工程实训指导书(金工实习)工业机器人或可换工作台数控机床单元控制器0第十一章现代制造技术工作台架☐CNC第一节概述检测装置监控装
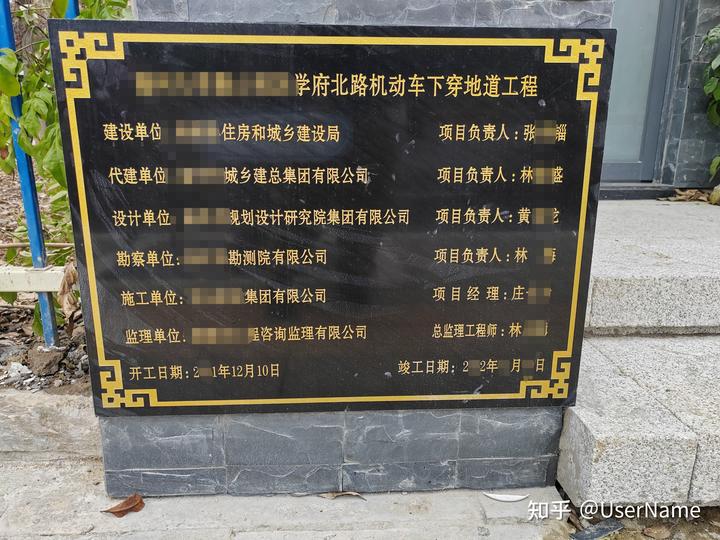
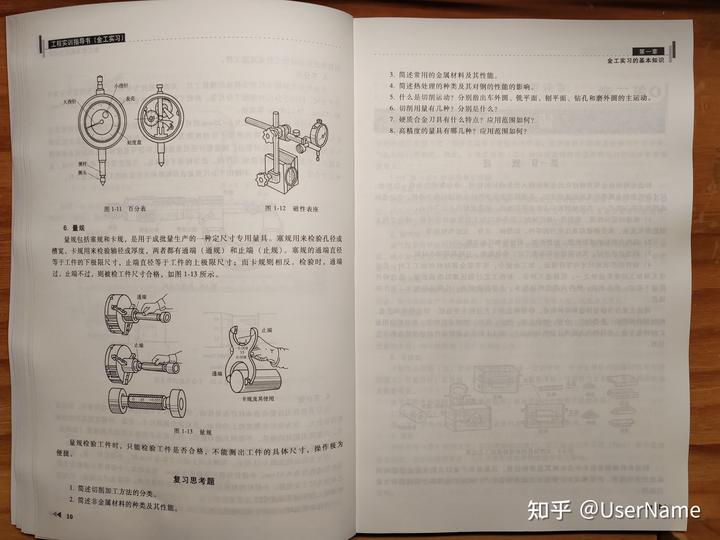
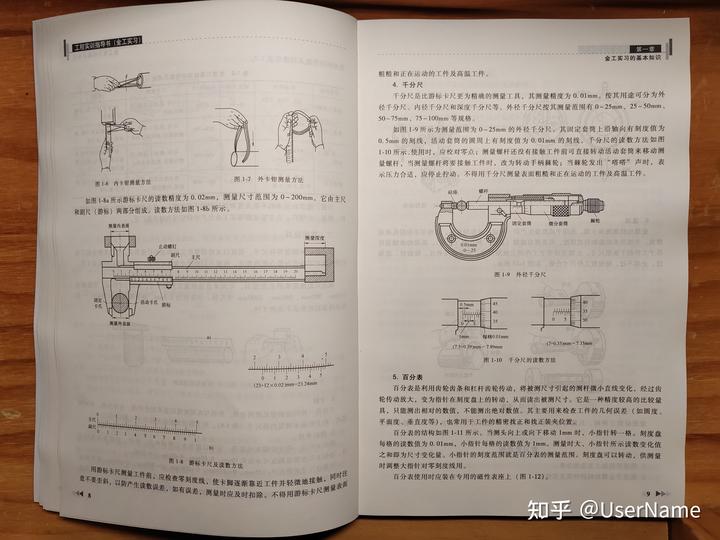

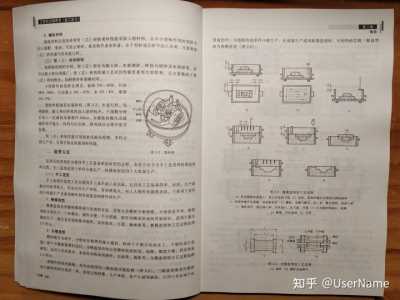
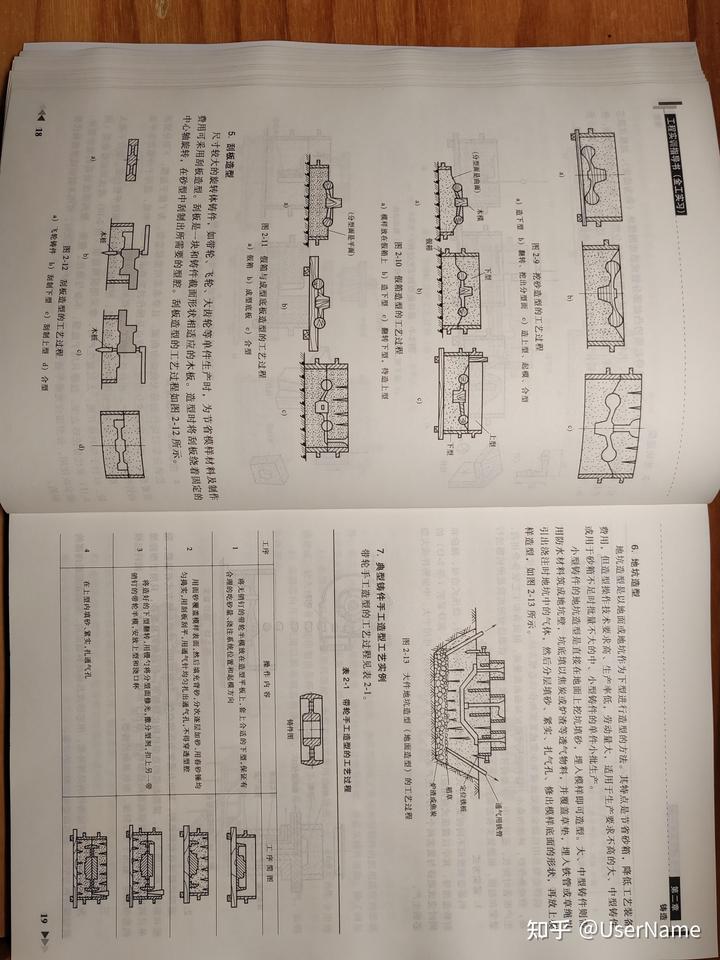
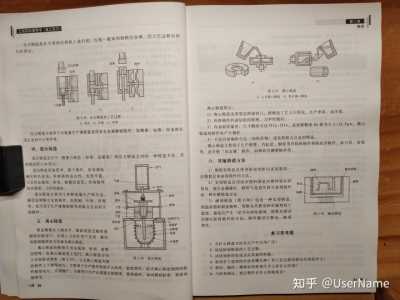
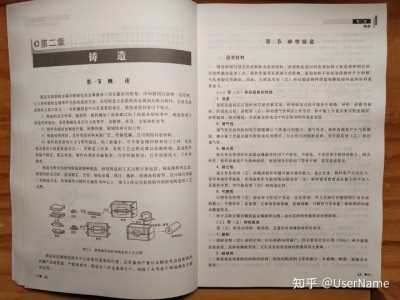
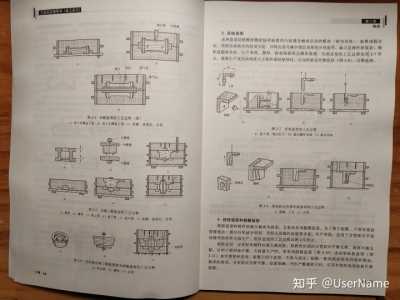
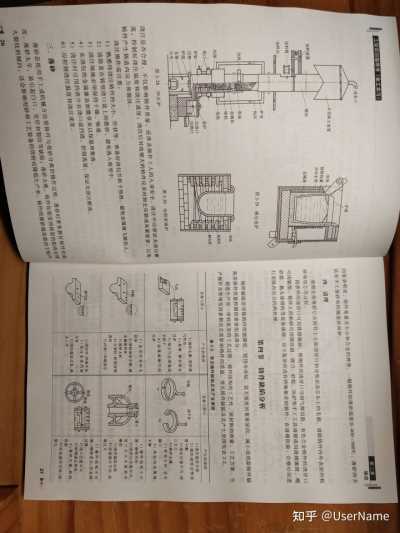
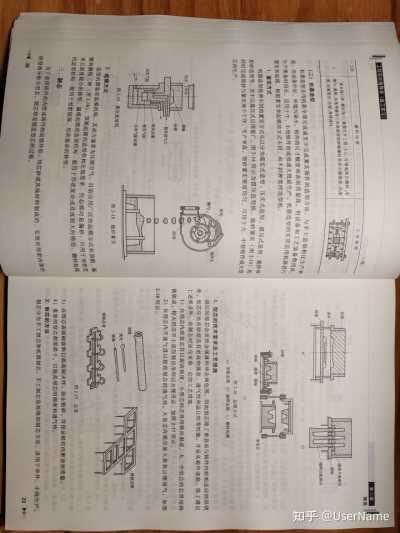
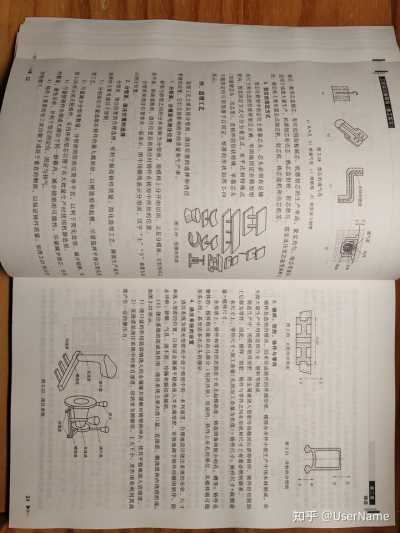
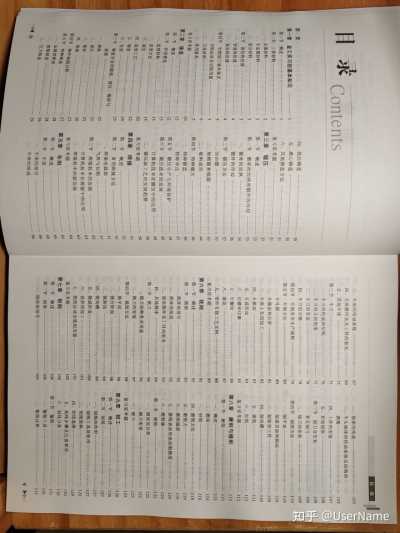
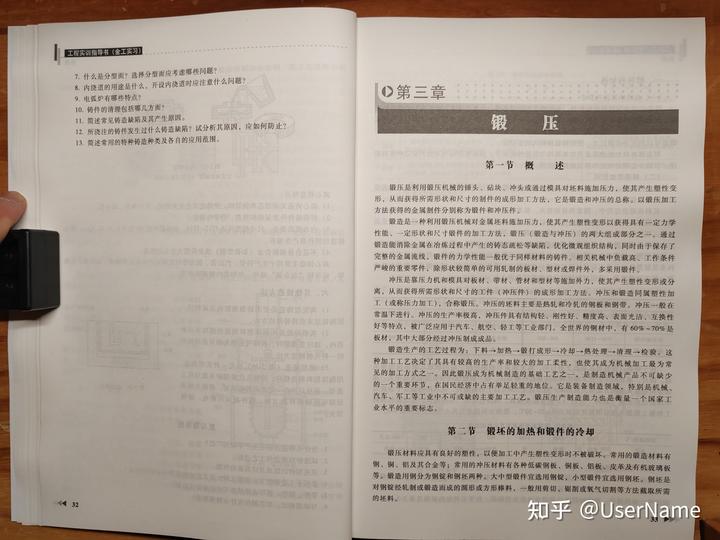
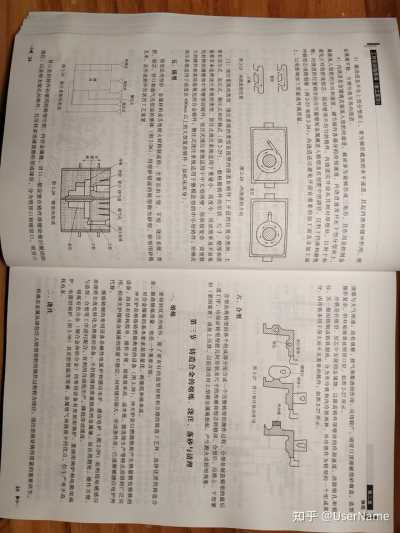
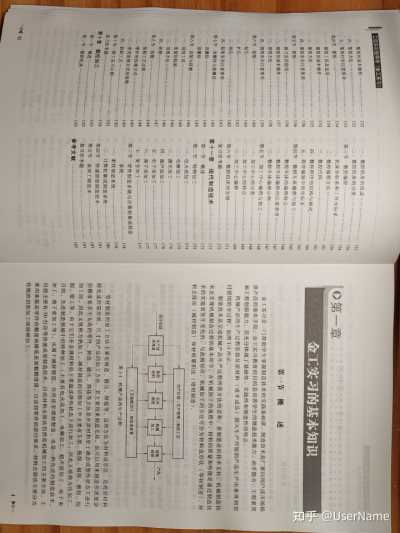
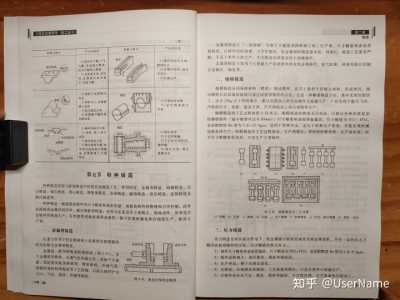
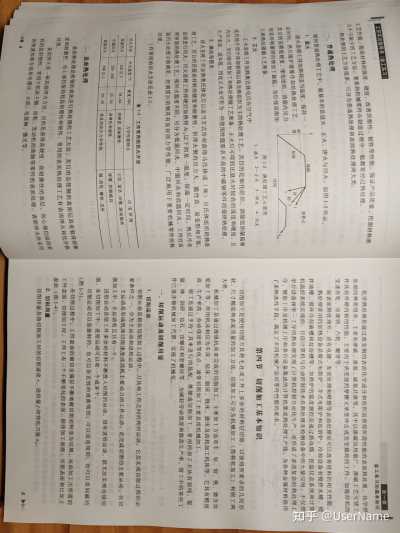
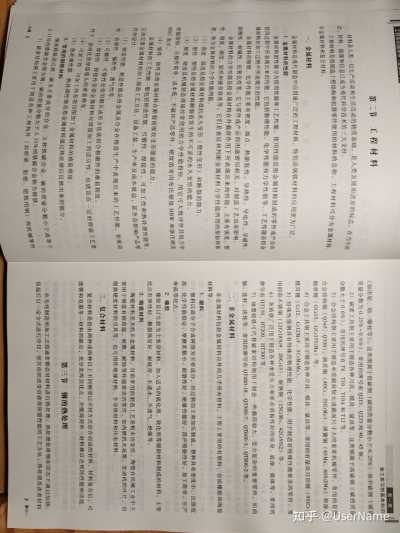
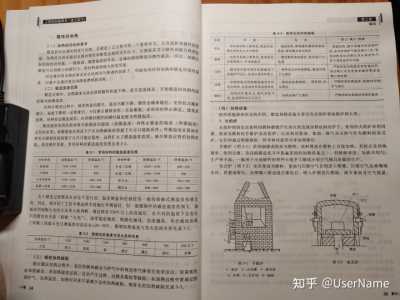
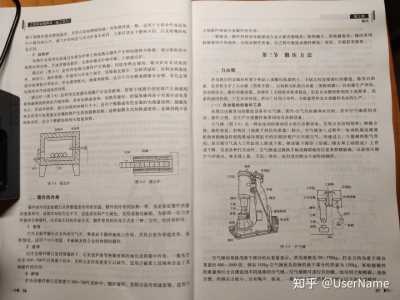
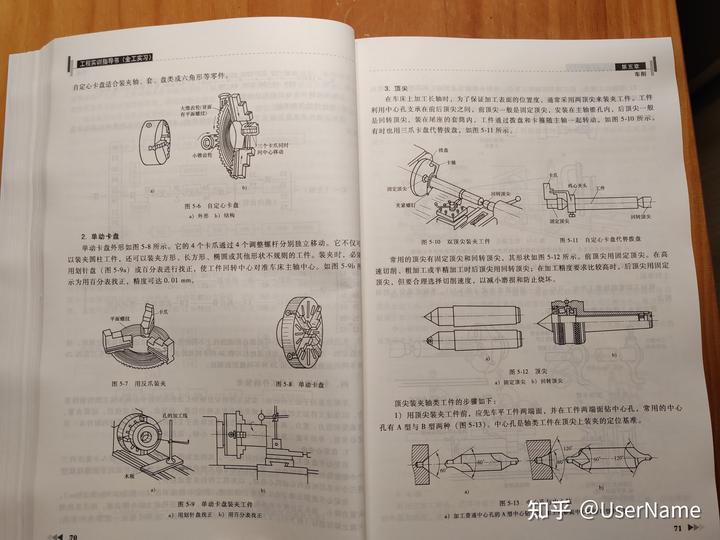
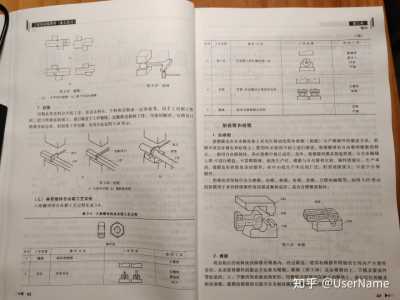
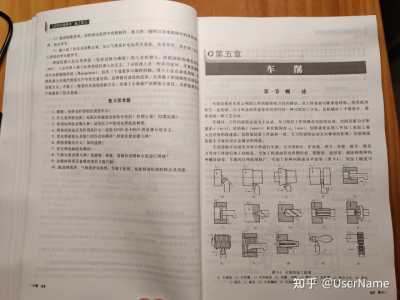
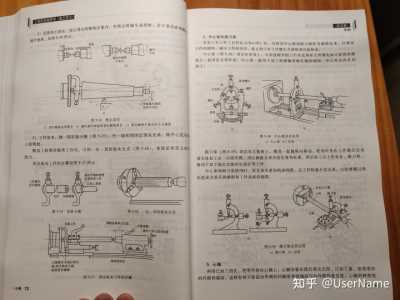
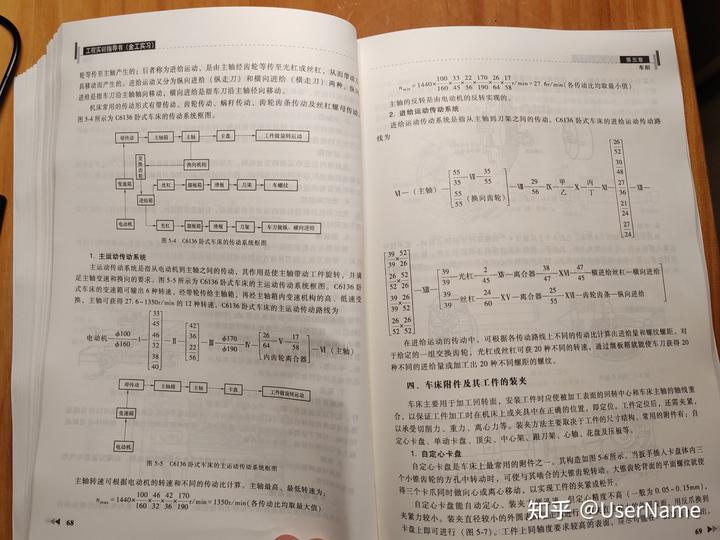
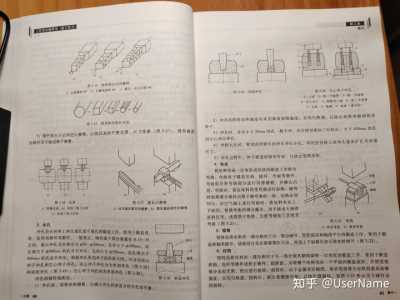
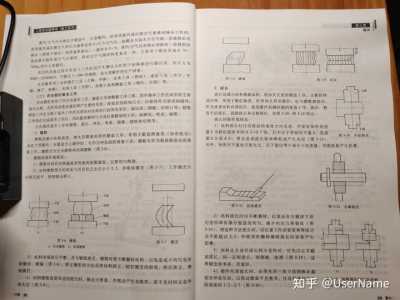
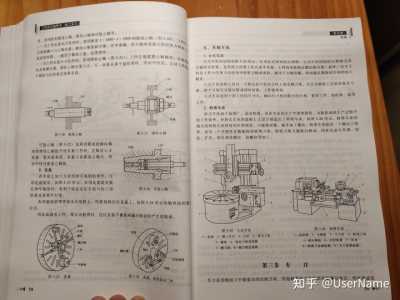
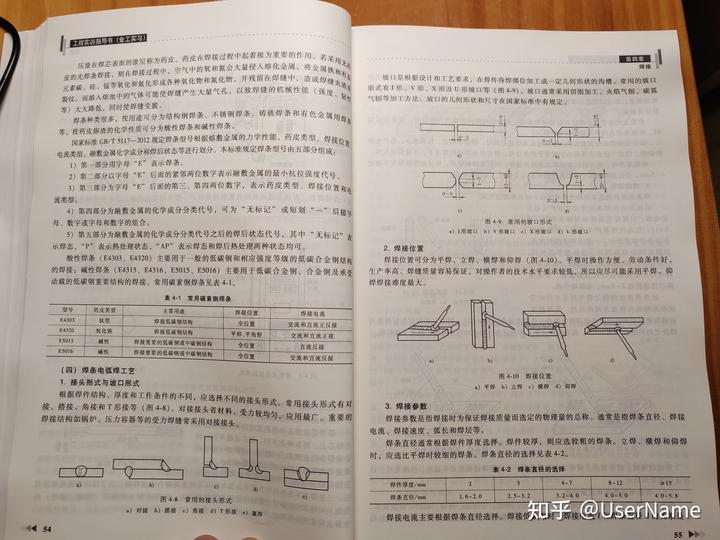
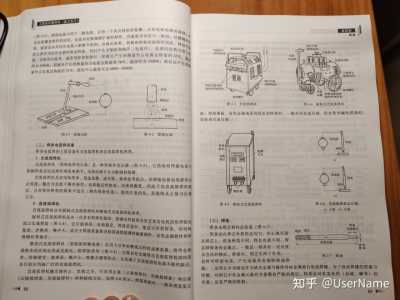
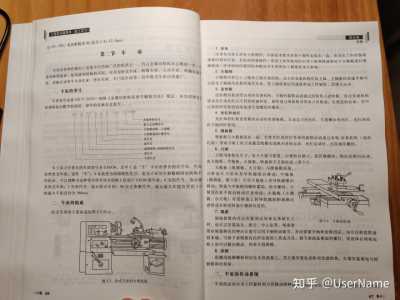
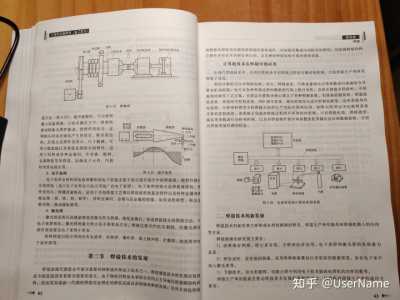
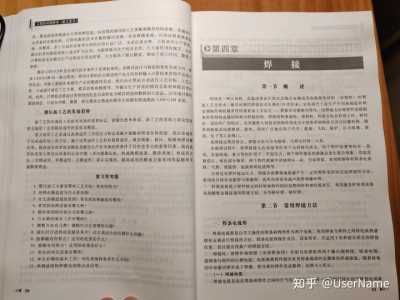
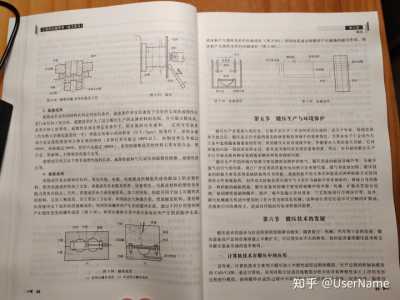
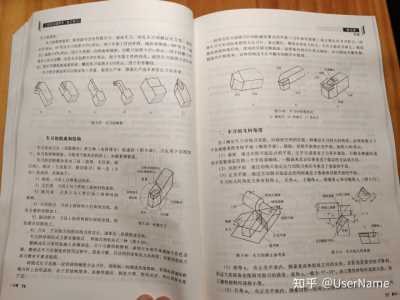
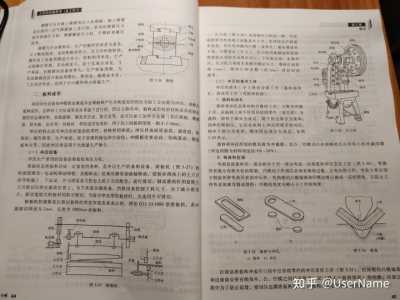
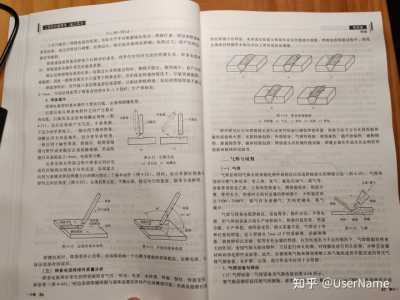
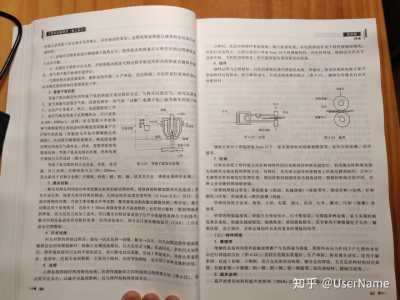
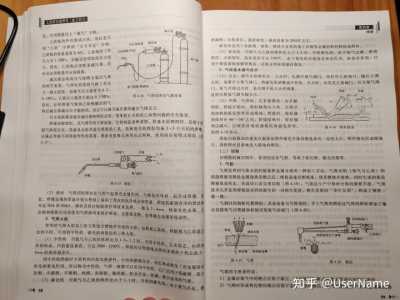
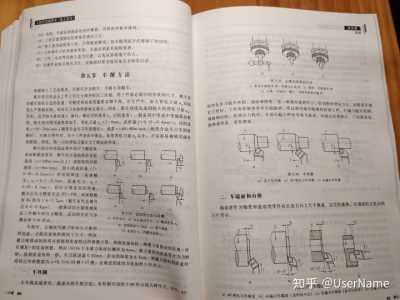
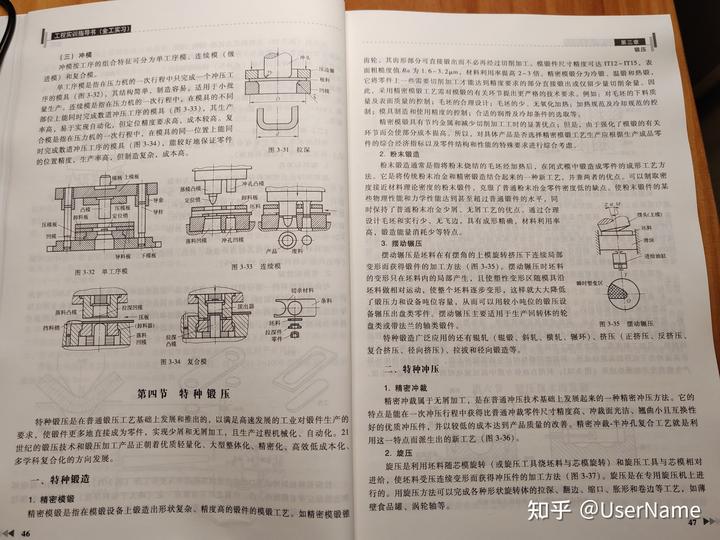
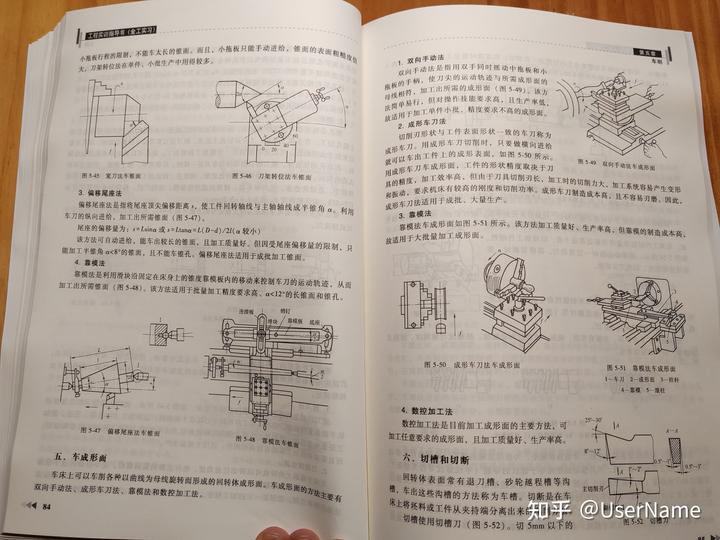
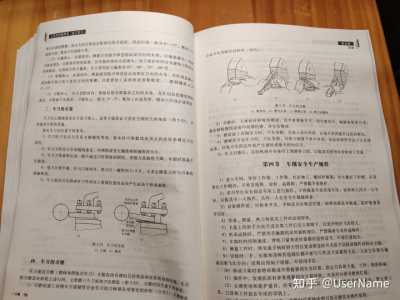
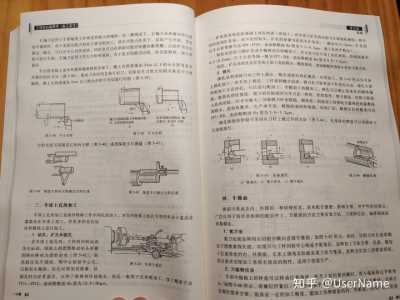
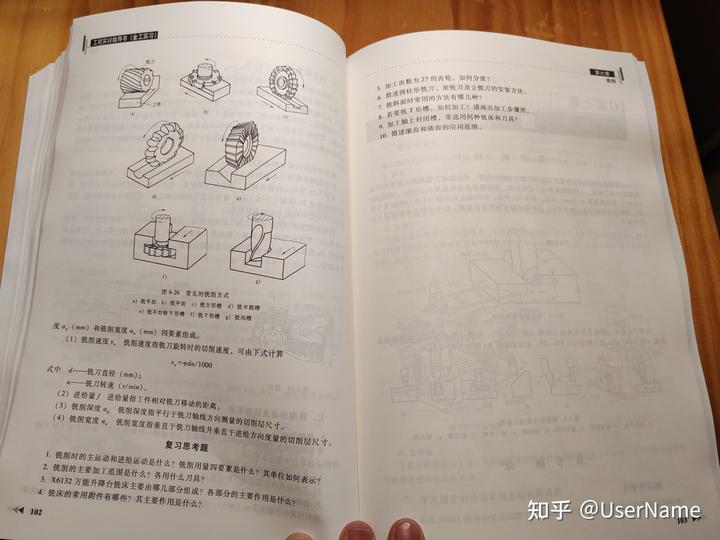
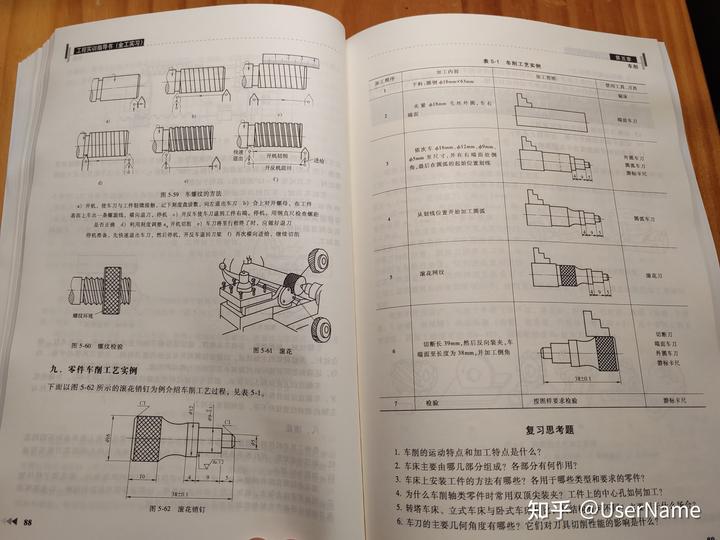
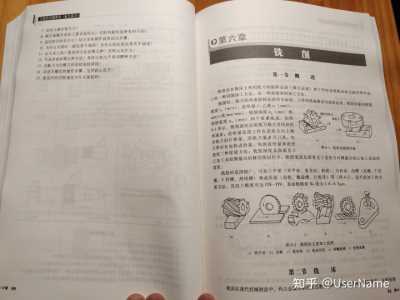
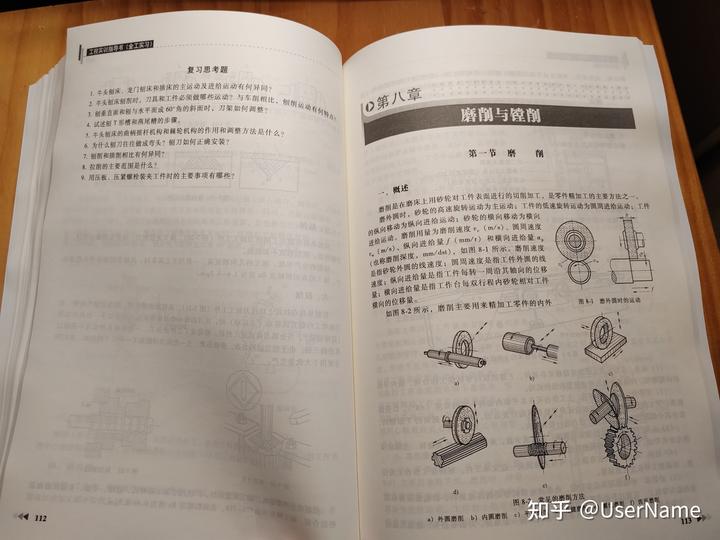
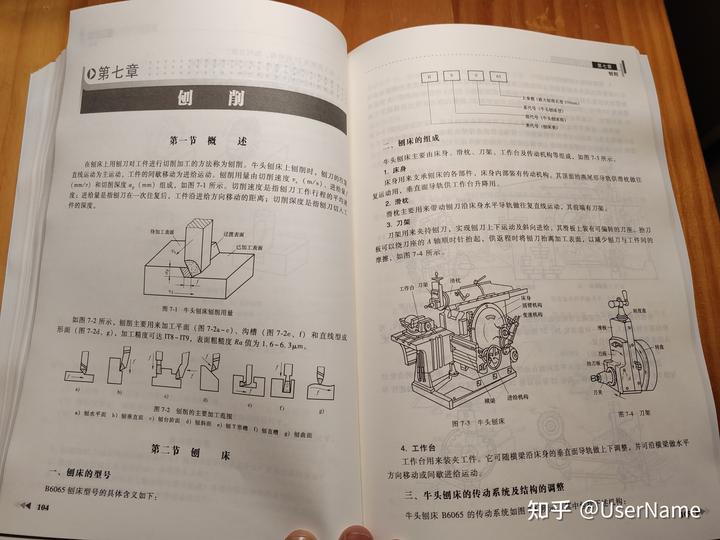
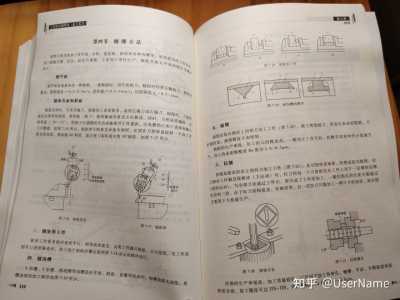
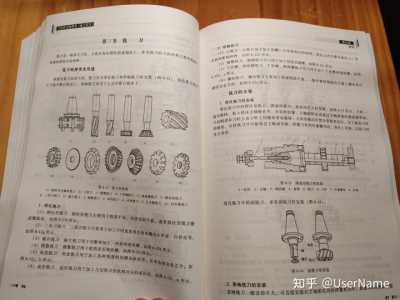
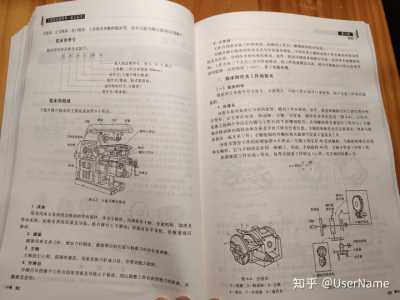
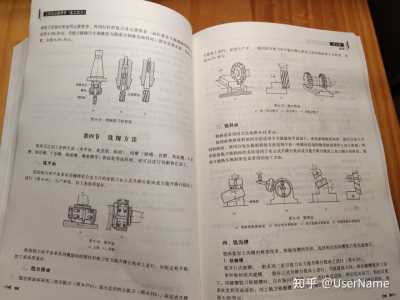
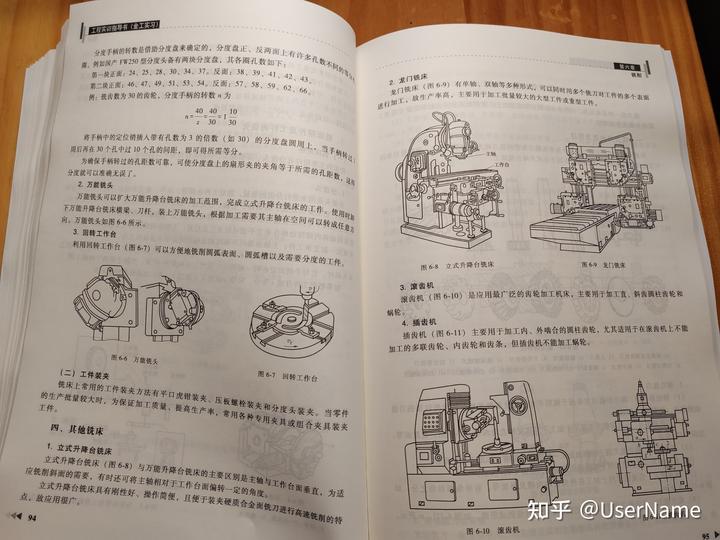
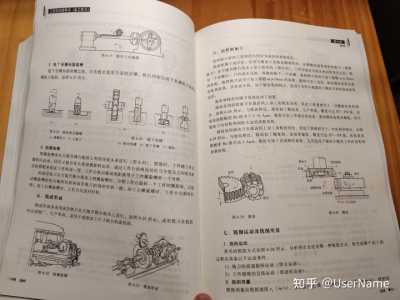
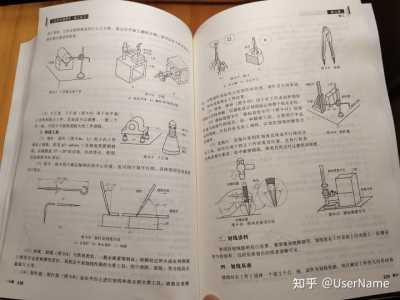
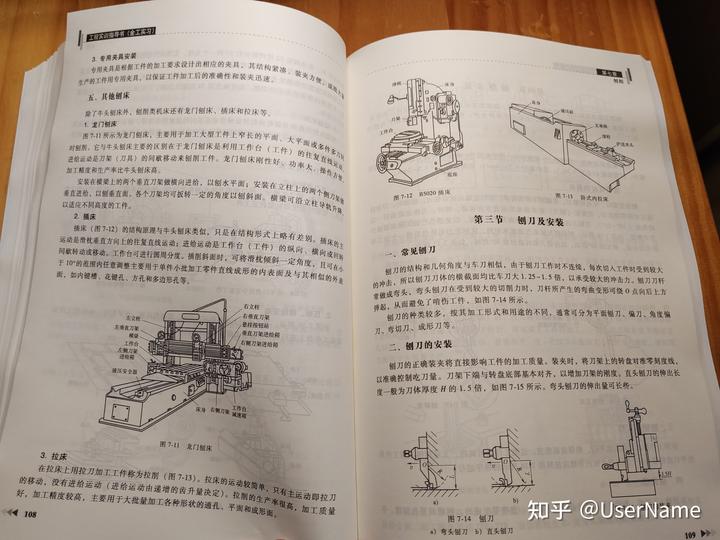
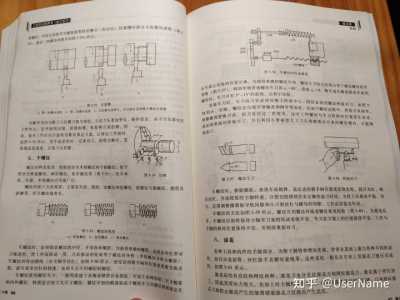
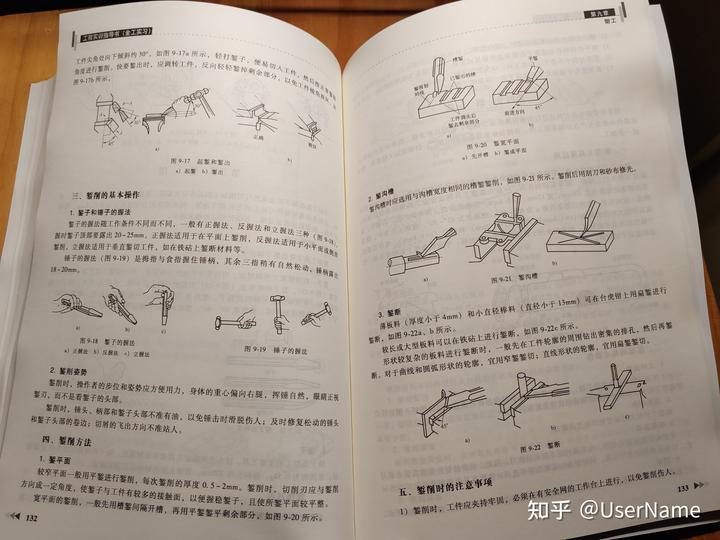

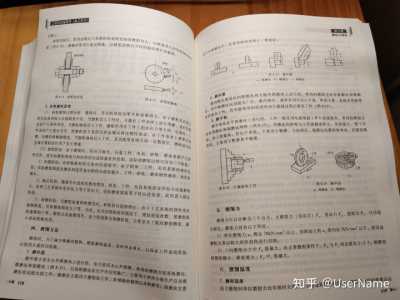
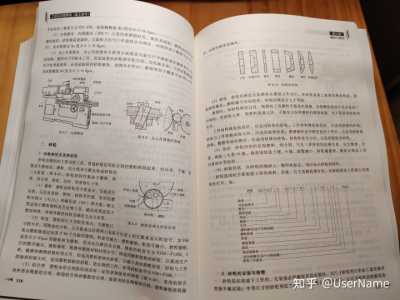
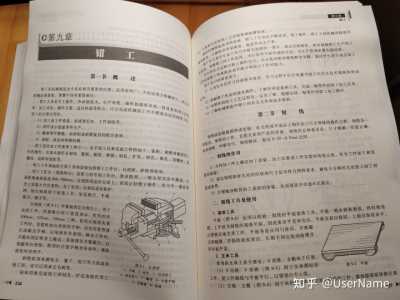
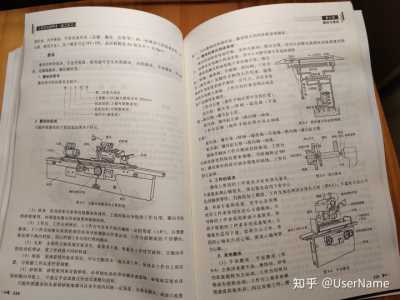
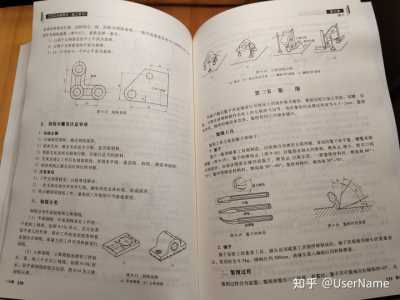
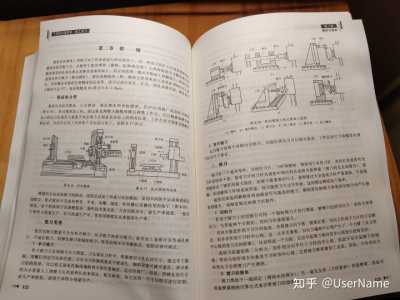
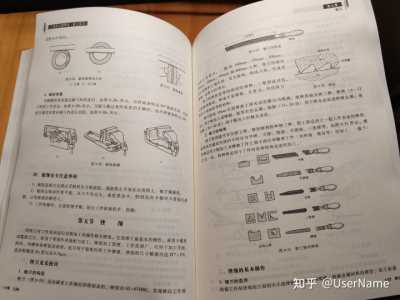
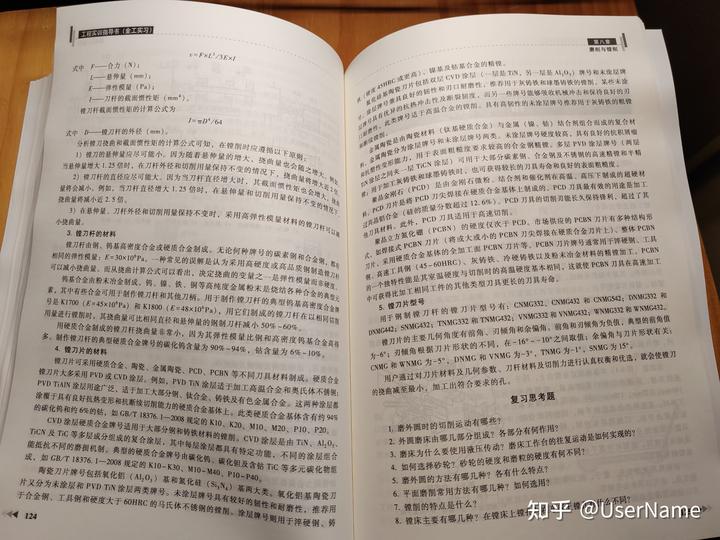
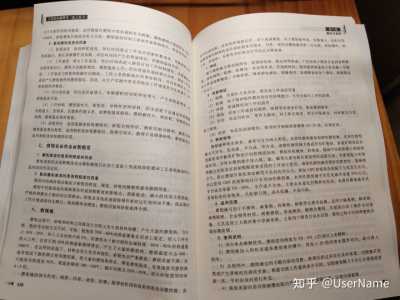
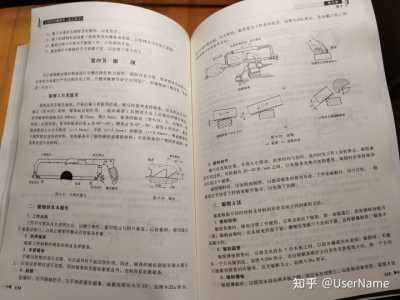
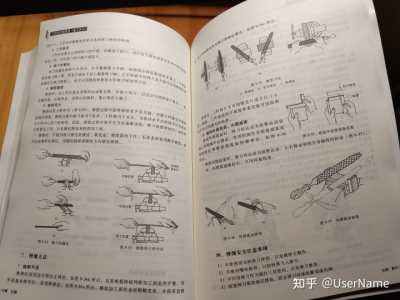
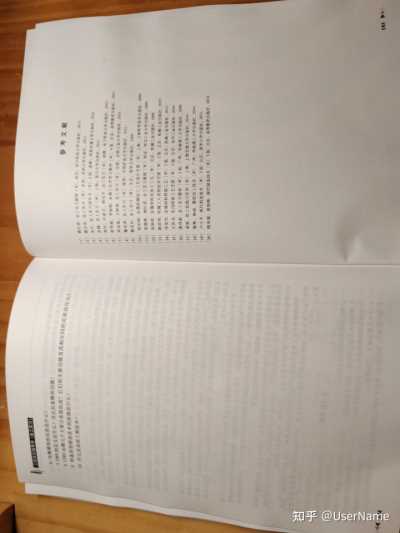
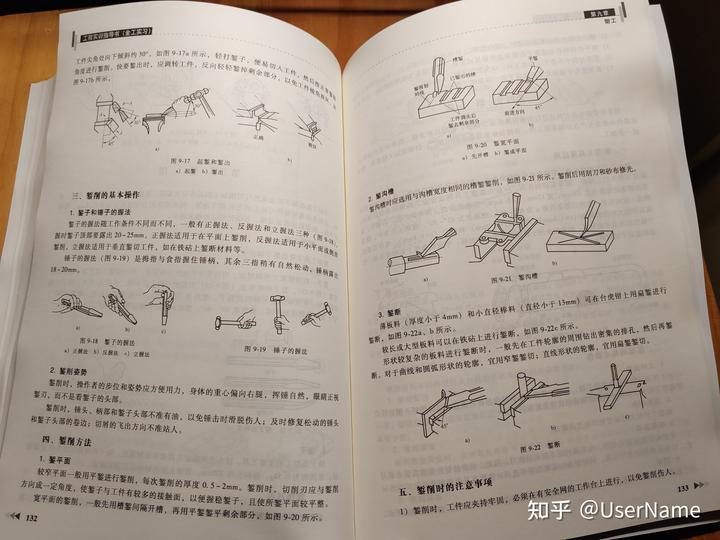
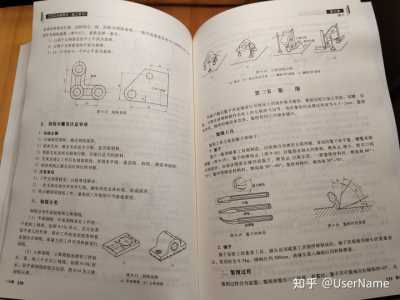
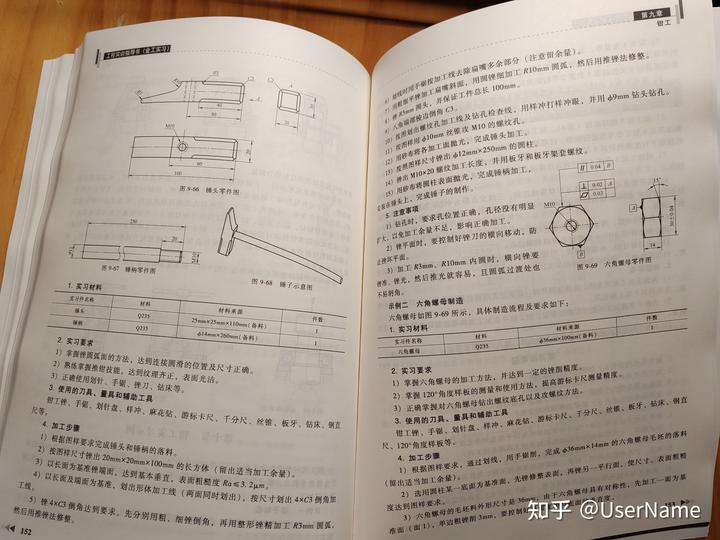
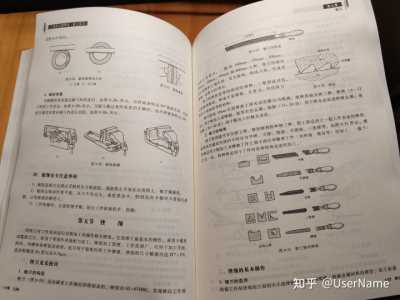
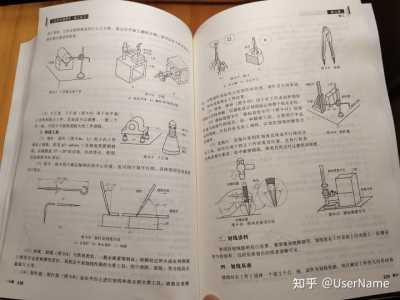
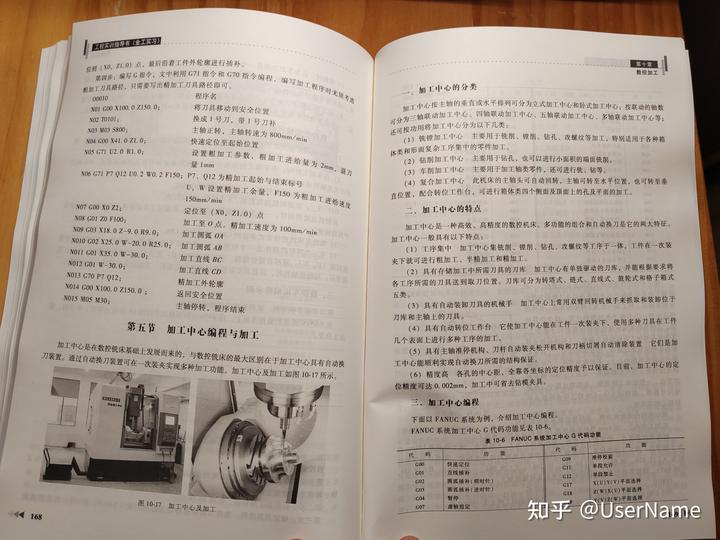
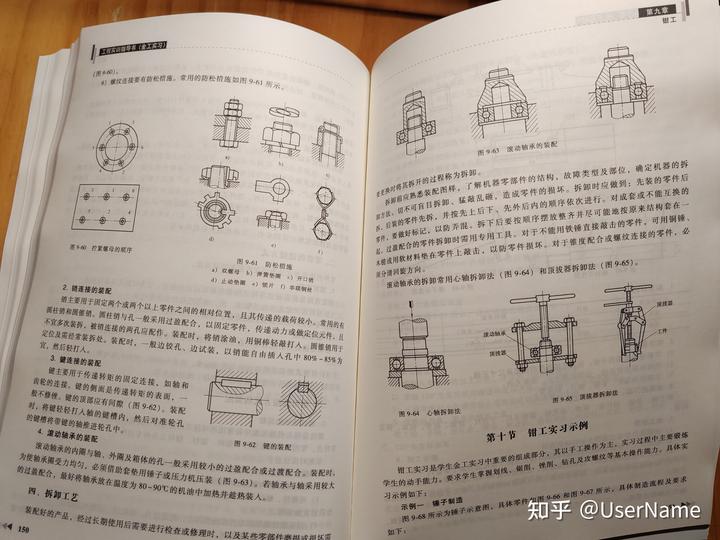
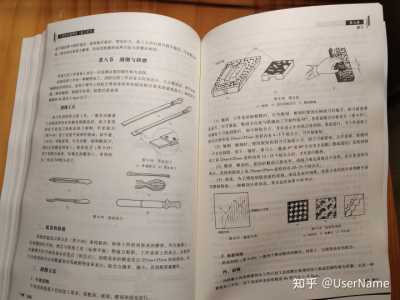
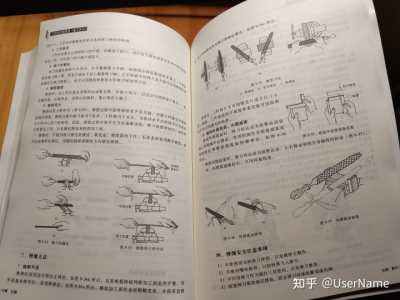
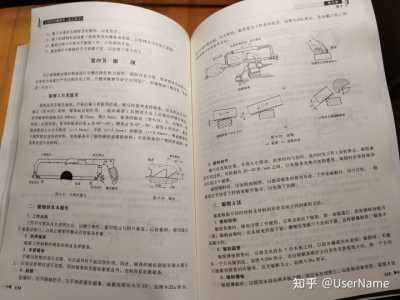
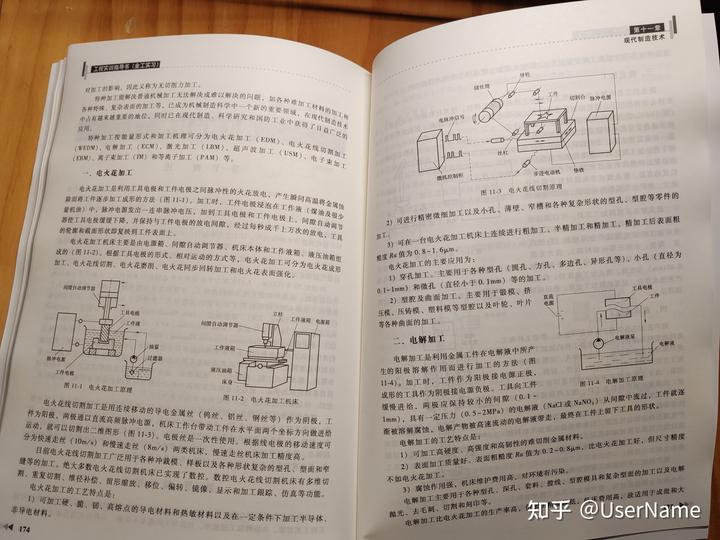
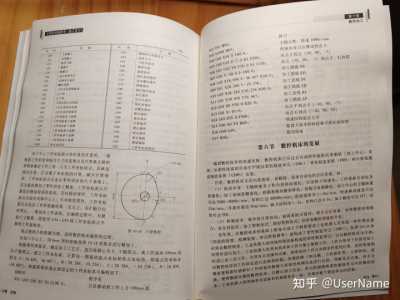
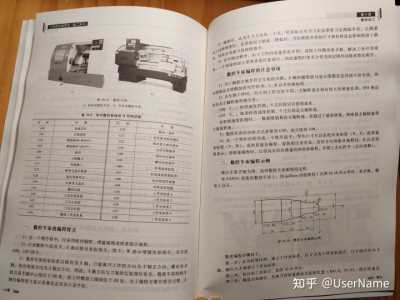
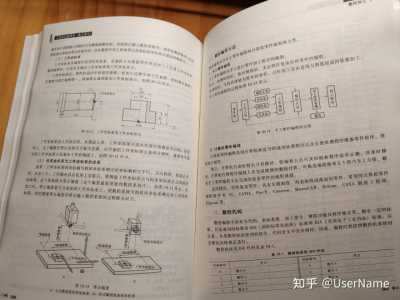
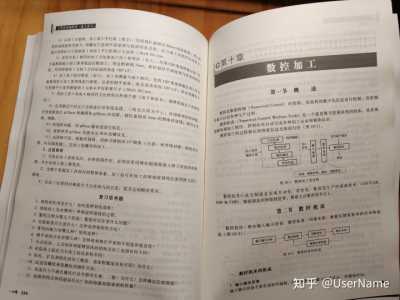
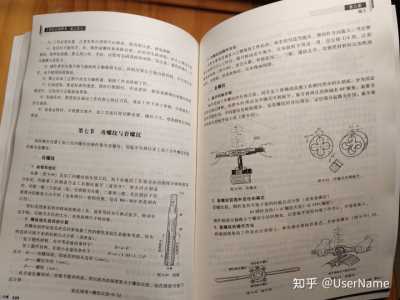
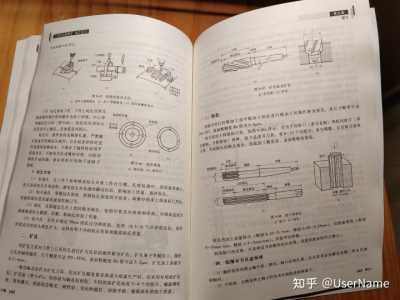
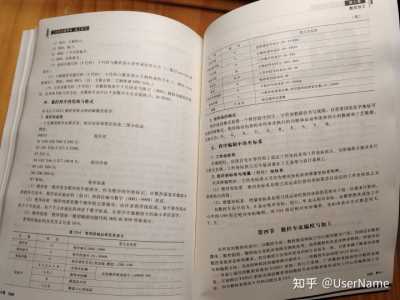
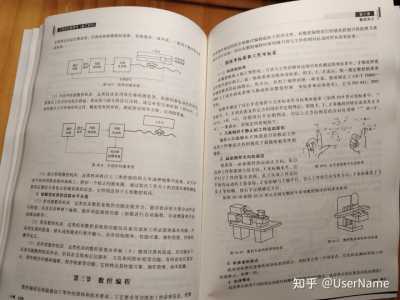
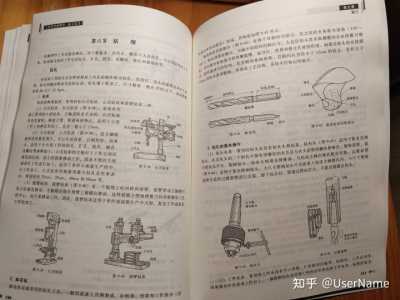
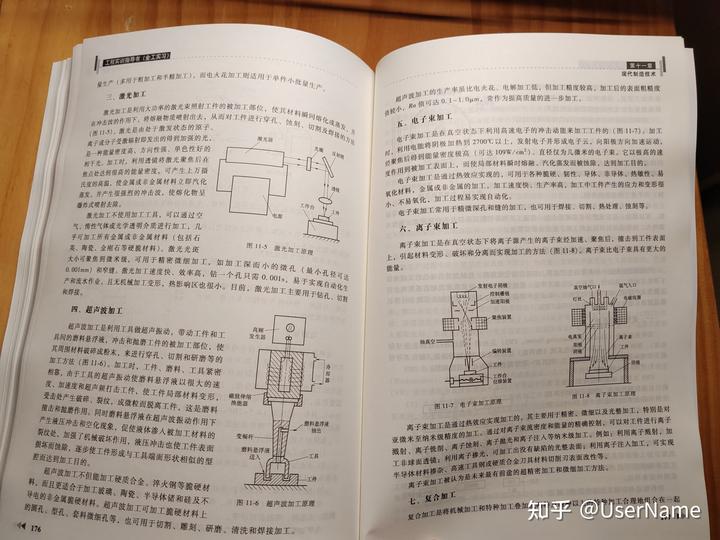
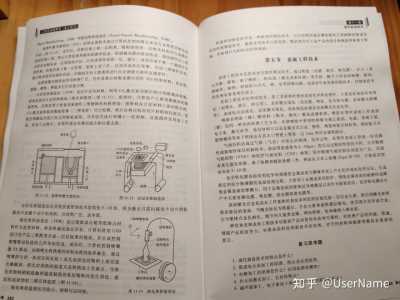
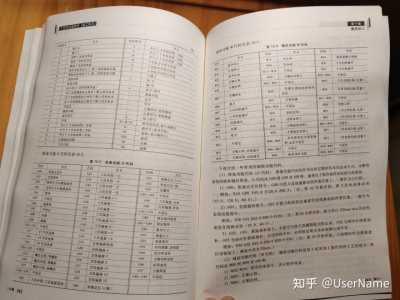
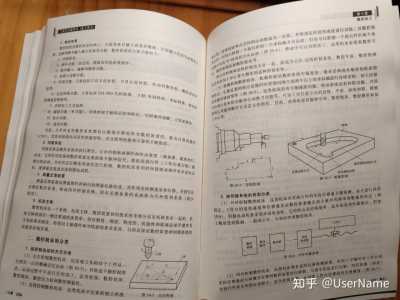
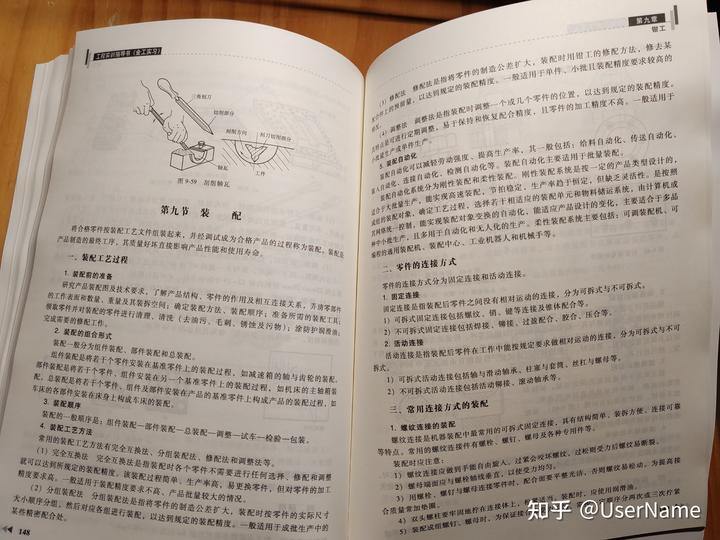
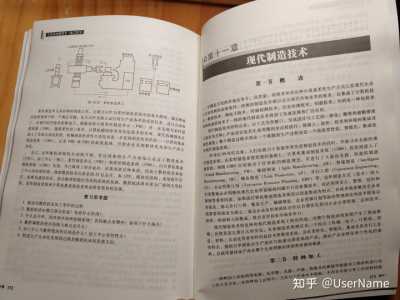
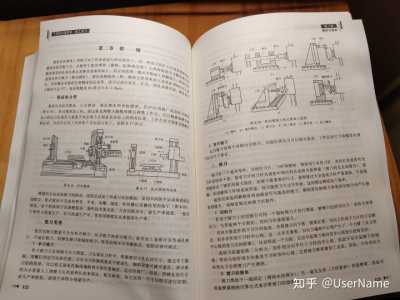
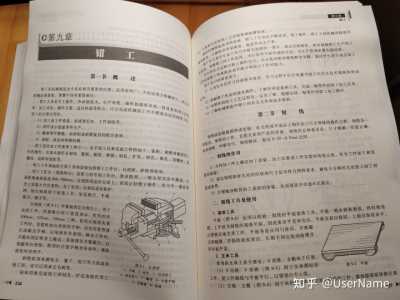
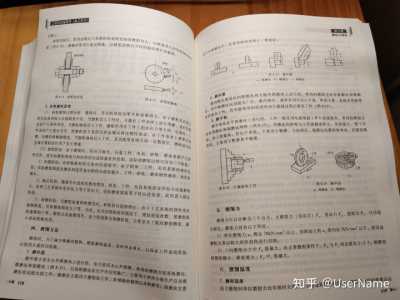
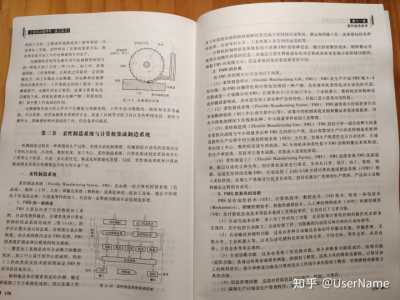
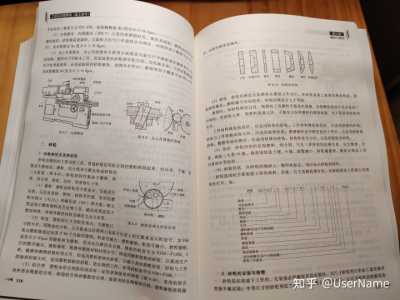
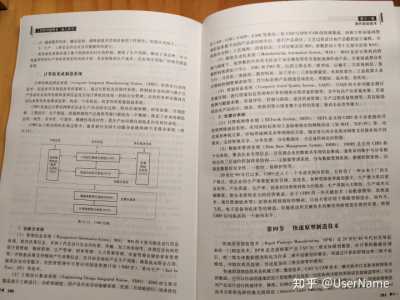
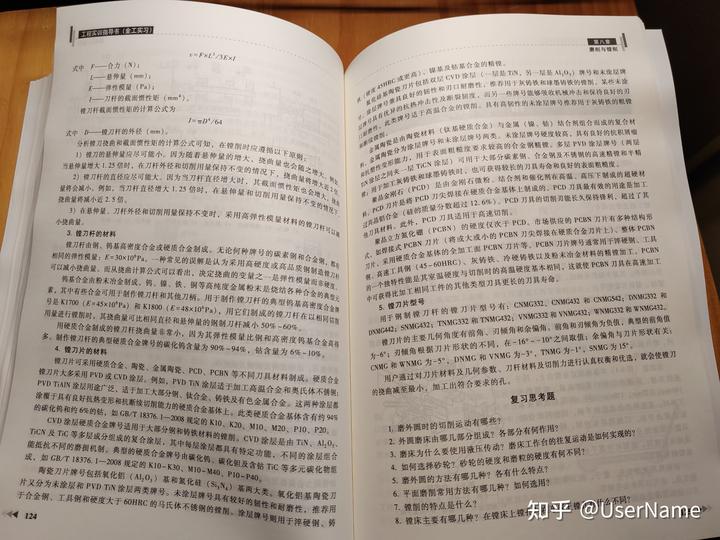
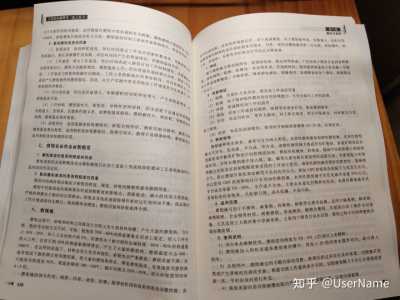
工程实训指导书(金工实习)工业机器人或可换工作台数控机床单元控制器0第十一章现代制造技术工作台架☐CNC第一节概述检测装置监控装置图10-19柔性制造单元在瞬息万变的市场竞争下,高质量、高效率和多品种小批量柔性生产方式已是现代企业柔性制造单元具有相对的独立性,它既可以作为柔性制造系统中的基本模块,能完整地生存和发展的必要条件。传统的制造技术难以适应现代市场竞争的要求,以集成了计算机技完成该系统中的一个规定功能;也可以作为独立运行的生产设备单独承担任务,进行自动加术、数控技术、微电子技术、传感检测技术、信息处理技术、伺服技术、光机电一体化技术工。在现代科学技术的推动下,根据需要可将柔性制造单元(FMC)进一步发展为柔性制和网络通信技术于一体的现代制造技术得到了迅速发展和广泛应用。现代制造技术的特点是:以工艺为突破口,形成设计与工艺的一体化;精密和超精密加造系统(FMS)。随着柔性加工技术、计算机辅助技术及信息技术的发展,现代机械制造业进入了全面自动化阶段,机械制造的柔性自动化也进一步发展到更高的阶段——计算机集成工技术为主体;产品设计是其生命周期的全过程设计;强调人、组织、技术和环境的集成及制造系统(CIMS)。它是FMC和FMS的高度发展,可使企业实现整体优化和生产的自绿色制造;整个制造过程不再是一个离散的生产过程而是一个高度柔性化、智能化、集成化动化。20世纪90年代以来,人们在致力于发展单项先进制造技术的同时,开始寻求全新的现代制造系统。在柔性制造系统发展的基础上,计算机集成制造系统(CIMS)的发展进入了的现代制造系统。总之,从单能机和刚性自动线开始,发达国家的生产自动化已走过了数控机床(CNC)、加工中心(MC)、柔性制造单元(FMC)和柔性制造系统(FMS),向计算机集成制造系统(CIMS)发展,并已取得了初步成功。而我国就总体来讲,仍处于数控机床和加新阶段。围绕CIMS应用提出了许多新的制造理念,并进行了大量的实践,如虚拟制造工中心的发展阶段。随着数控技术向着采用32位芯片、多CPU、模块化结构、通用程序语(VisualManufacturing,VM)、敏捷制造(AgileManufacturing,AM)、智能制造(Intelligent言、标准化通信协议、多功能和智能化等高档系统的发展,数控机床将有更为广阔的应用前Manufacturing,IM)、精良制造(LeanProduction,LP)、并行工程(ConcurrentEngineering,景,柔性制造系统和计算机集成制造系统也将有更快的发展CE)、企业资源计划(EnterpriseResourcePlanning,ERP)等。这些制造方式(技术)使人们清楚地认识到解决现代企业所面临的问题不只是依靠技术,而必须涉及人、管理、组织和复习思考题体制等重要因素。如果说计算机集成制造系统是以信息集成为特点,从技术角度解决企业竞1.叙述用数控机床加工零件的过程。争需求,那么并行工程、精良生产、敏捷制造、企业资源计划等新的管理理论和技术则是以2.数控机床由哪几部分组成?各有什么作用?消费者的需求为核心,通过企业组织和团队合作以合理优化使用企业全部资源,达到技术、3.什么是开环、闭环和半闭环控制系统?其优缺点有哪些?各用于什么场合?4.数控编程的程序结构与格式是什么?现代制造技术的发展和现代制造系统工程的形成,对整个制造业的发展产生了深远影组织、体制和人的集成,使企业更具有市场竞争力。5.加工中心与数控铣床的区别是什么?加工中心有何特点?响,并使其发生着巨大的变化。未来制造系统理应是一个综合了机械、电子、计算机、信6.简述生产自动化发展的过程及数控机床的发展方向。息、材料、自动化等多学科的高技术密集型系统,具有柔性化、智能化、集成化和并行工作的特点,能按订单制造出生产成本与批量关联度低的产品,满足产品多样化和个性化的要求,且高质量保证产品在整个生命周期内使消费者感到满意。第二节特种加工特种加工是指利用电能、化学能、光能、声能、热能及机械能等能量对工程材料进行加工的工艺方法。在特种加工过程中,刀具与工件基本不接触,不存在切削力和工件材料性能173172第十章数控加工工程实训指导书(金工实习)换刀主轴正转,转速1000r/min代码功能代码NO2T01MO6;快速由对刀点移动到点S寸制输入G61功能精确停止校验方式(续)G20NO3S1000M03;G64G21米制输入连续方式G65NO4G0OX50.0Y80.0;由点S到点(50,80,-7)G22脉冲当量子程序调用镜像开G68旋转变换NO5G00G43Z-7.0H1F500;由点(50,80,-7)到点F,右补偿G24镜像关G69G25旋转取消N06G01G42XOY50.0D1F200;加工圆弧FEG73G28返回到参考点G74深孔钻削循环NO7G03Y-50.0J-180.0;加工圆弧EDG29由参考点返回加工直线DCG33螺纹切削G76逆攻螺纹循环N08G03X18.856Y-36.667R20.0;精镗循环刀具半径补偿取消G80N09G01X28.284Y-10.236;N10G03X28.284Y10.236R30.0;加工圆弧CBG40固定循环取消G41左刀补G81钻孔循环加工直线BAG42右刀补G82沉头孔循环加工圆弧AFG43刀具长度正向补偿G83N11G01X18.856Y36.667;深孔钻循环G44刀具长度负向补偿G84N12GO3XOY50.0R20.0;由点F到点G(-10,50,-7)G49刀具长度补偿取消攻螺纹循环G85镗孔循环N13G01X-10.0;由点G到点(-10,50,35)G54工件坐标系1选择G86工件坐标系2选择镗孔循环G55N14G01Z35.0F500:快速回到原点上方G87G56工件坐标系3选择反镗循环G88镗孔循环N15GOOXOYOMO5:取消刀具半径补偿和刀具长度补偿G57工件坐标系4选择G89N16G40G49;程序结束G58工件坐标系5选择镗孔循环G90G59工件坐标系6选择绝对编程N17M30;G91G60单方向定位增量编程G92工件坐标系设定第六节数控机床的发展加工中心工件坐标原点的位置是任意的,一般根据工件形状和标注尺寸的基准以及计算最方便的Y原则来确定工件上某一点为工件坐标原点,具体选S(50,80)随着数控技术的迅速发展,数控机床已从过去自动的单能机向多能机(加工中心)发展,从刚性连接的自动生产线向柔性制造单元(FMC)、柔性制造系统(FMS)和计算机集择应注意:①为便于坐标值的计算,减少计算错GFR20误,工件坐标原点应选在零件固有的尺寸基准上;目前,数控机床正在向高速度、高精度、高度自动化的方向发展,即:成制造系统(CIMS)发展。②为提高被加工零件的加工精度,工件坐标原点尽(1)机床本身主轴转速及工作台进给高速化;自动换刀快速化;工件装卸自动化及量选在精度较高的表面;③对称的零件,工件坐标快速化;加工表面高精度化;控制系统功能多样化;切削刀具强硬化。加工中心的主轴转速原点应设在对称中心上;不对称的零件,工件坐标20R30可达5000~6000r/min,有的已达40000r/min;进给速度为1~2m/min,快速移动速度可达原点应设在工件外轮廓的某一交点上;④Z轴方向033m/min,并逐步靠近50m/min;换刀时间为1~2s,有的已达0.5s;加工精度可达IT7,有的零点,一般设在工件表面。在编程过程中,为避免尺寸换算,需使用G54-G59将工件坐标原点平D的可达IT6。移到工件基准处。E(2)控制技术程序设计简易化;提高系统可靠性;增大记忆容量、加快数据处理能力;交互对话式、加工资料库式、图形资料库式;经济型数控系统的开发。现以铣削凸轮轮廓为例,说明数控铣床编程的过程。图10-18凸轮铣削近年来,在数控机床的基础上配备自动上下料装置或工业机器人及其他一些外围设备在加工中心上,用6mm厚的铝板按图10-18的要求进行精加工。(如监控装置、检测装置、单元控制器等)就构成了柔性制造单元(FMC)。如图10-19所根据零件图要求,确定加工工艺后,选凸轮圆心为X、Y轴零点,离工件表面100mm处示是由数控机床、工业机器人和其他外围设备构成的柔性制造单元。它以数控机床为主体,为Z轴零点,建立工件坐标系。计算每一圆弧的起点坐标和终点坐标值,即基点的坐标分对零件进行加工,工业机器人负责从机床和工作台架上装卸工件。工作台架用于存放待加工别为A(18.856,36.667)、B(28.284,10.236)、C(28.284,-10.236)、D(18.856,的或已加工的工件,并具有自动循环功能,将堆放的工件自动移至所需的位置。监控装置则-36.667)。根据算得的基点和设定的工件坐标系可编程如下:对数控机床的工作状态进行监视和控制,发现故障(如过载、刀具损坏等)立即停机。检00010测装置根据传感器对工件检验的数据与系统的检测信息进行比较,判断是否合格,若不合格,便将数据反馈给数控机床,以修正加工信息。单元控制器将柔性制造单元中的数控机171NO1G90G0OXOYOZ100.0;程序名床、工业机器人和其他有关设备有机地联系在一起,实现对整个制造单元的控制。刀具移动到工件上方100mm处170第十章数控加工4)编程时,认为车刀刀尖是一个点,但实际上车刀刀尖总带有刀尖圆弧半径,且随着加工过程的进行,尤其是加工斜面、圆弧时,刀尖圆弧半径的尺寸和形状还会影响到加工精5)在车削过程中,由于工件的余量各处不同,或按工件精度要求粗、精加工分开等原度,因此应考虑刀具补偿指令。,一个表面的加工常需多次反复进行,因此编程时要充分使用固定循环功能来简化程序。二、数控车床编程的注意事项1)为了编程方便并符合车床的习惯,X轴的编程值与显示值都是直径而不是半径。但在圆弧定义的附加语句中的R、I、K以半径值标明。b)2)在车削工件时,由于加工的方法不同,主轴转速必须有很大的调速范围。ISO规定图10-15数控车床a)斜床身数控车床b)平床身数控车床的有关主轴转速的指令有:C96S_;恒线速度控制,S之后指定切削线速度。表10-5华中数控系统的G代码功能G97S_;取消恒线速度控制,S之后指定主轴转速。代码功能在恒线速度控制时,一般要限制最高主轴转速。若超过了最高转速,则要使主轴转速等代码G0O快速定位G70功能于最高转速。GO1直线插补精加工循环3)数控车床的进给方式多使用G99,也可使用G98。G71G02圆弧插补(顺时针)4)在一个零件的程序或一个程序段中,零件尺寸可以是绝对坐标值(X、Z)或增量G72直径复合粗切循环G03圆弧插补(逆时针)端面复合粗切循环G90坐标值(U、W),或两者混合编程。要特别注意的是:直径方向用绝对编程时,X以直径G04延时直径切削循环G94值表示;用增量编程时,以径向实际位移量的两倍值编程,并附上方向符号(正向省略)。G20寸制输入端面切削循环G92G21米制输入螺纹切削循环三、数控车床编程示例G96G27参考点返回检查恒线速度控制G97现以车削手柄为例,说明数控车床编程的过程。G28返回到参考点恒线速度控制取消G98在FANUC系统的数控车床上,用40mm的铝棒加工出图10-16所示零件,要求粗、精G29由参考点返回每分钟进给设置G99G32螺纹切削每转进给设置加工分开。G54G40刀具补偿取消工件坐标系12G55G41刀尖左补偿工件坐标系2G42G56刀尖右补偿工件坐标系3G5798号9O(0,0)G50修改工件坐标系工件坐标系4G58A(18,-9)工件坐标系5B(25,-29)C(35,-59)一、数控车床的编程特点D(35.-89)3020301)在一个程序段中,可采用绝对编程、增量编程或两者混合编程。图10-16数控车床编程示例2)许多数控车床用X、Z表示绝对坐标指令,用U、W表示增量坐标指令,而不用G90、G91指令。第一步:在分析零件图,建立工件坐标系,以O点为工件坐标原点,以手柄径向为X数控编程步骤如下。3)数控车床的坐标系以纵向为X轴,刀架离开工件的方向为X轴正方向,横向为Z轴,指向尾座方向为Z轴正方向。因此,X轴方向与刀架的安装部位有关。数控车床的程序轴、轴向为Z轴建立工件坐标系。原点是主轴中心线位于XO处,而工件精加工端面位于ZO处。为了编程方便并符合习惯,X第二步:标注加工坐标点,如图10-16所示。轴的编程值与显示值都是直径而不是半径。第三步:确定刀具路径,先将刀具快速移动至起始位置(X41.0,Z1.0),然后快速定167166第十章数控加工(续)工程实训指导书(金工实习)意义及范围4)M05:主轴停止。5)M06:换刀。地址进给速度的指定:FO~F150006)M08:1号切削液开。F主轴转速的指定:S0~S99997)M09:切削液关。功能8刀具编号的指定:TO~T99(3)进给功能代码(F代码)F代码与数值表示进给速度的大小(一般以mm/min来进给功能T主轴起停的指定:M03~M05表示)。主轴速度功能刀具功能M刀具补偿号的指定:00~99(4)主轴速度功能代码(S代码)S代码与数值表示主轴转速的大小(一般以r/min来表示)。例如:S600M03;(注:主轴正转,主轴转速600r/min。)辅助功能H、D暂停时间的指定:秒子程序号的指定:P1-P9999(5)刀具功能代码(T代码)在数控铣床中T代码常与换刀(MO6)辅助功能同时使补偿号用,也用来为新刀具寻址。在数控车床中以T加数字方式直接换刀,如T0101。暂停P子程序的重复次数,固定循环的重复次数:L2-L9999四、数控程序的结构与格式子程序号的指定L固定循环的参数重复次数P、Q、R本书以FANUC数控系统为例讲解数控程序。参数1.程序的结构2.程序段的格式一个完整的程序由程序名、程序内容和程序结束三部分组成。程序段的格式是指一个程序段中的字、字符和数据的书写规则。目前常用的是字地址可例如:变程序段格式。程序段应包括机床所要求执行的功能和运动所需要的几何数据和工艺数据,00015程序名其格式为:NG_X_Y_Z_RF_S_TM_。N1G90G00X60.0Z40.0;N2G01X30.0Z37.0F300;五、程序编制中的坐标系N3Z25.0;在编程时,应该首先在零件图上设定工件坐标系和工件坐标原点。为使编程方便及各尺1.工件坐标系N4G02X46.0Z17.0R18.0;程序内容N5G01X60.0;寸较为直观,工件坐标原点应尽量设置在工艺基准与设计基准上。N6G00Z40.0;2.绝对坐标系与增量(相对)坐标系N7M30;程序结束在具体编程时,工件坐标系又可分为绝对坐标系和增量坐标系两种。(1)程序名程序名为程序的开始部分,作为程序的开始标记,在数控装置存储器中(1)绝对坐标系绝对坐标系是指刀具运动位置的坐标值是以设定的工件坐标原点为的程序目录中。程序名由地址码(如0)和四位编号数字(0001-9999)组成。(2)增量坐标系增量坐标系是指刀具运动位置的坐标值是相对于前一位置来计算的。基准给出的值。(2)程序内容程序内容是整个程序的主要部分,由许多程序段组成。每个程序段由若干个字组成。每个字又由地址码和若干数字组成。在程序中能做指令的最小单位是字。在数控车床中用X、Z表示绝对坐标,用U、W表示相对坐标。在数控铣床或加工中(3)程序结束程序结束一般用辅助功能代码MO2和M30等来表示。心中用G90指定绝对坐标编程,用C91指定相对坐标编程,坐标的表示方式都是用X、常用的地址码及其含义见表10-4。Y、Z。功能表10-4常用的地址码及其含义第四节数控车床编程与加工地址程序名意义及范围在所有的数控机床中,以数控车床、数控铣床和加工中心使用最为广泛。其他还有数控程序段号程序编号:0001-9999N准备功能程序段编号:N1-N9999磨床、数控刨床、数控电火花机床和线切割机床等。虽然数控机床是多种多样的,所使用的G指令动作方式(如直线、圆弧):G00-G99数控系统更是种类繁多,但其编程方法和所使用的指令却基本一致,只要掌握了最基本的指X、Y、Z、U、V、W直线坐标轴令和编程方法,无论何种机床的编程都不难学习。一些数控车床如图10-15所示。坐标字A、B、C市面上流行的数控系统有FANUC系统、西门子系统、广州数控系统和华中数控系统旋转坐标轴坐标轴的移动命令:±99999.999165◆◆R等。下面将以FANUC系统为例讲解常用的数控车床和数控铣床或加工中心的编程加工方圆弧的半径IJ、K圆弧中心的坐标法。华中数控系统的G代码功能见表10-5。164第十一章现代制造技术工程实训指导书(金工实习)2)编制数控机床、输送装置、储料装置及其他设备的工作程序,实现自动加工。CAD、CAE、CAPP、CAM等部分,是CAD/CAPP/CAM的集成。具体工作是接到管3)生产、工程信息的论证及其数据库的建立。理信息系统下达的产品设计指令后,进行产品设计、工艺过程设计和产品数控加工编程,并柔性制造系统实现了集中控制和实时在线控制,缩短了生产周期,解决了多品种、中小将设计文档、工艺规程、设备信息、工时定额送给MIS,将数控加工等工艺指令送给MAS。批量零件的生产率和系统柔性间的矛盾,具有较低的生产成本,是发展应用最广的现代制造(3)制造自动化系统(ManufacturingAutomationSystem,,MAS)MAS是在计算机的控系统。制与调度下,按照数控代码将毛坯加工成合格的零件并装配成部件或产品。主要组成部分有二、计算机集成制造系统数控机床或加工中心、FMC和FMS等,包括立体仓库、缓冲站、运输车、刀具预调仪、装、刀台、刀具库、清洗机、数控机床、加工中心、三坐标测量仪、夹具组装台、工业机器人及计算机集成制造系统(ComputerIntegratedManufacturingSystem,CIMS)是指在自动化计算机控制管理系统等。其目标是使产品制造活动优化、周期短、成本低、柔性高。技术、信息技术及制造技术的基础上,通过计算机及其软件系统,将制造企业内部与整个生(4)质量保证系统(ComputerAidedQualitySystem,CAQS)CAQS的主要功能是制订产活动有关的所有物料流和信息流实现计算机高度统一的综合化管理,从而把各种分散的自质量计划,进行质量信息管理和计算机辅助在线质量控制等,其中包括产品质量决策、质量动化系统有机地集成起来,构成一个高效益、高柔性的智能制造系统。CIMS是通过计算机网络把企业生产活动的全过程,即从市场预测、经营决策、计划控检测与数据采集、质量评价、控制与跟踪、量具质量管理、生产过程质量管理等。其目标是制、工程设计、生产制造、质量控制到产品销售等部门联结为一个整体,保证了企业内部信保证从产品设计、制造、检验到售后服务整个过程的质量,提高企业竞争能力。息的一致性、共享性、可靠性、精确性和及时性,使生产由局部自动化走向全局自动化。2.支撑分系统(1)计算机网络系统(NETworkSystem,NETS)NETS是支持CIMS各个分系统的开CIMS在工程应用的实现过程中,通常划分为四个功能分系统和两个支撑分系统(图11-11)。放型网络通信系统,采用国际标准和工业标准规定的网络协议(如MAP、TCP/IP)等,可实现异种机互联,异构周域网及多种网络的互联,满足各应用分系统对网络支持服务的不同市场信息技术信息售后服务信息需求,支持资源共享、分布处理、分布数据库、分层递阶和实时控制。(2)数据库管理系统(DataBaseManagementSystem,DBMS)DBMS是支持CIMS各个分系统,覆盖企业全部信息,以实现企业的数据共享和信息集成。通常采用集中与分布相经营管工程设计集成分系统(EDIS)理信息结合的三层递阶控制体系结构——主数据管理系统、分布数据管理系统、数据控制系统,以服务质量分系统保证(MIS)分系统保证数据的安全性、一致性、易维护性等。制造自动化分系统(MAS)(CAQ)20世纪90年代以来,CIMS进入了一个迅速发展的阶段。它提供了一种未来工厂的生功能分系统产模式,使企业的生产要素配置更合理、更优化,各种资源浪费减到最少,生产潜力得以更好发挥,产品质量、生产率、设备利用率得到极大的提高,生产周期大大缩短,生产成本大数据库管理分系统(DBMS)幅降低,使企业获得更大的经济效益。由于CIMS的一些关键技术(如数据模型、系统技支撑分系统术、现代管理技术等)还没有得到很好的解决,目前主要应用于离散型制造业,如汽车、计算机网络分系统(NETS)飞机、电子设备和机床等的制造。但随着这些关键技术的解决和新制造思想的实现,将使CIMS应用提高到一个新的水平。图11-11CIMS结构1.功能分系统第四节快速原型制造技术(1)管理信息系统(ManagementInformationSystem,MIS)MIS的主要功能是进行信息处理,提供决策信息。具体工作是进行信息的收集、传输、加工和查询等,处理信息包括经快速原型制造技术(RapidProtoypeManufacturing,RPM)是20世纪80年代初发展起营计划管理、物料管理、生产管理、财务管理、人力资源管理、质量管理及辅助事务管理来的一门制造技术。RPM是直接根据产品CAD的三维实体模型数据,经计算机数据处理等,并根据决策支持模块产生决策信息。其目标是缩短产品生产周期,降低流动资金占用,后,将三维实体数据模型转化为许多二维平面模型的叠加,再通过计算机控制这些二维平面提高企业应变能力。在经营管理中主要应用制造资源计划(MRPⅡ)、准时生产(JustIn模型,并顺次将其连接,形成复杂的三维实体零件模型。Time,JIT)等技术。快速原型制造技术是机械工程、数控技术、CAD与CAM技术、激光技术以及新型材料技术(2)工程设计集成系统(EngineeringDesignIntegratedSystem,EDIS)EDIS的主要功的集成。它可以自动迅速地把设计思想物化为具有一定结构和功能的原型或直接制造零件,可以能是进行工程设计、分析和制造,使产品开发活动能够高效、优质、自动地进行。该系统包对产品设计进行快速评价、修改,以响应市场需求,提高企业的竞争能力。目前,快速原型制造180技术主要有选择性激光烧结法((SelectiveLaserSintering,IS)、分层实体制造法((Laminated181工程实训指导书(金工实习)第十一量生产(多用于粗加工和半精加工),而电火花加工则适用于单件小批量生产。现代制造技术三、激光加工声波加工的生产率虽比电火花、电解加工低,但加工精度较高,加工后的表面粗糙度激光加工是利用大功率的激光束照射工件的被加工部位,使其材料瞬间熔化或蒸发,#值较小,Ra值可达0.1-1.0μm,常作为提高质量的进一步加工。在冲击波的作用下,将熔融物质喷射出去,从而对工件进行穿孔、蚀刻、切割及焊接的方法(图11-5)。激光是由处于激发状态的原子、五、电子束加工离子或分子受激辐射即发出的得到加强的光,激光器电子束加工是在真空状态下利用高速电子的冲击动能来加工工件的(图11-7)。加工是一种能量密度高、方向性强、单色性好的光圈反射镜时,利用电能将阴极加热到2700℃以上,发射电子并形成电子云,向阳极方向加速运动,相干光。加工时,利用透镜将激光聚焦后在焦点处达到很高的能量密度,可产生上万摄T经聚焦后得到能量密度极高(可达109W/cm2)、直径仅为几微米的电子束。它以极高的速度作用到被加工表面上,而使局部材料瞬时熔融、汽化蒸发而被蚀除,达到加工目的。氏度的高温,使金属或非金属材料立即汽化、电子束加工是通过热效应实现的,可用于各种脆硬、韧性、导体、非导体、热敏性、易蒸发,并产生很强烈的冲击波,使熔化物呈透镜氧化材料,金属或非金属的加工,加工速度快、生产率高,加工中工件产生的应力和变形很爆炸式喷射去除。工作台小、不易氧化,加工过程易实现自动化。激光加工不使用加工工具,可以通过空电源工件电子束加工常用于精微深孔和缝的加工,也可用于焊接、切割、热处理、蚀刻等。气、惰性气体或光学透明介质进行加工,几六、离子束加工乎可加工所有金属或非金属材料(包括石英、陶瓷、金刚石等硬脆材料)。激光光斑图11-5激光加工原理离子束加工是在真空状态下将离子源产生的离子束经加速、聚焦后,撞击到工件表面上,引起材料变形、破坏和分离而实现加工的方法(图11-8)。离子束比电子束具有更大的大小可聚焦到微米级,可用于精密微细加工,如加工深而小的微孔(最小孔径可达能量。0.001mm)和窄缝。激光加工速度快、效率高,钻一个孔只需0.001s,易于实现自动化生产和流水作业,且无机械加工变形,热影响区也很小。目前,激光加工主要用于钻孔、切割发射电子阴极和焊接。真空抽气口氩气入口999控制栅极加速阳极灯丝、电磁线圈四、超声波加工聚焦装置。⊙超声波加工是利用工具做超声振动,带动工件和工18高频具间的磨料悬浮液,冲击和抛磨工件的被加工部位,使发生器电离室离子束抽真空阳极其周围材料破碎成粉末,来进行穿孔、切割和研磨等的偏转装置工件阴极加工方法(图11-6)。加工时,工件、磨料、工具紧密工件阴极相靠,由于工具的超声振动使磨料悬浮液以很大的速冷却器~工作台度、加速度和超声频打击工件,使工件局部材料变形,位移装置受击处产生破碎、裂纹,成微粒而脱离工件,这是磨料磁致伸缩图11-8离子束加工原理换能器撞击和抛磨作用。同时磨料悬浮液在超声波振动作用下图11-7电子束加工原理产生液压冲击和空化现象,促使液体渗入被加工材料的磨料悬浮液离子束加工是通过热效应实现加工的,其主要用于精密、微细以及光整加工,特别是对裂纹处,加强了机械破坏作用,液压冲击也使工件表面抽出变幅杆亚微米至纳米级精度的加工。通过对离子束流密度和能量的精确控制,可以对工件进行离子损坏而蚀除,逐步使工件形成与工具端面形状相似的型磨料悬浮液溅射、离子铣削、离子蚀刻、离子抛光和离子注入等纳米级加工。例如:利用离子溅射,加腔而达到加工目的。送入工具工非球面透镜;利用离子掺光,可加工出没有缺陷的光整表面;利用离子注入加工,可实现超声波加工不但能加工硬质合金、淬火钢等脆硬材半导体材料掺杂、高速工具钢或硬质合金刀具材料切削刃表面改性等。工件料,而且更适合于加工玻璃、陶瓷、半导体锗和硅及不离子束加工被认为是未来最有前途的超精密加工和微细加工方法。导电的非金属脆硬材料。超声波加工可加工脆硬材料上图11-6超声波加工原理七、复合加工的圆孔、型孔、套料微细孔等,也可用于切割、雕刻、研磨、清洗和焊接加工。复合加工是将机械加工和特种加工叠加或两种及两种以上的特种加工合理地组合在一起177◆176第十一章现代制造技术工程实训指导书(金工实习)的加工方法。它能成倍地提高加工效率和进一步导电结合剂及工夹具的自动供给和装卸以及完成工序间的自动传送、调运和存储工作。该系统包括各种砂轮改善加工质量,是特种加工发展的重要方向。现传送带、自动导引小车、工业机器人及专用吊运送机等。绝缘磨料将典型复合加工中的电解磨削介绍如下:(金刚石、刚玉)计算机控制的信息系统是用于处理FMS的各种信息、输出控制数控机床、物料搬运系电解磨削是利用电解作用与机械磨削相结合等自动操作所需的信息,是通过主控计算机或分布式计算机系统来实现主要控制功能的。的一种复合加工方法(图11-9)。加工时,砂轮阴极一根据FMS的规模大小,信息系统的复杂程度将有所不同。接阴极,工件接阳极,且两者之间保持一定的接2.FMS的分类触应力,加工区域送入电解液,在电解和机械磨按FMS的规模大小可分为以下四类:阳极~削的双重作用下,工件很快达到加工要求。在电(1)柔性制造单元(FlexibleManufacturingCell,FMC)FMC在生产中比FMS晚6~8电解液解磨削中,电解作用是主要的,金属主要靠电化年出现,是FMS向廉价化和小型化发展的一种产物,是实现单机柔性化及自动化的代表,工件学腐蚀下来,砂轮起着磨去电解产物(阳极钝化氧化膜腐蚀物可看成是一个规模小的FMS,它通常由1~2台加工中心、工业机器人、数控机床和物料运物)和平整工件表面的作用。图11-9电解磨削原理送存储设备构成,具有适应加工多品种产品的特性,目前已进入普及应用阶段。电解磨削在加工时几乎不产生磨削力和磨削热,工件不会出现裂纹、烧伤和变形等缺(2)柔性制造系统(FlexibleManufacturingSystem,FMS)FMS通常有4台或更多台全陷,可以高效、高质地磨削各类硬质合金、高速工具钢等切削刀具以及各种强度高、韧性与自动数控机床(加工中心或车削中心等),由集中的控制系统及物料搬运系统连接起来,可脆性大、热敏感材料所制成的工件。但设备费用较高。在不停机的情况下实现多品种、中小批量零件的加工及管理。(3)柔性制造线(FlexibleManufacturingLine,FML)FML是处于单一或少品种大批量第三节柔性制造系统与计算机集成制造系统非柔性自动线与中小批量多品种FMS之间的生产线,是以离散型生产中的柔性制造系统和连接性生产过程中的分散型控制系统(DCS)为代表,实现生产线柔性化及自动化的。它通机械制造过程是一种离散的生产过程,实现自动化较困难。机械制造自动化的发展经历常由加工中心、数控机床或专用机床、NC专用机床和柔性低于FMS的物料搬运系统构成,了单机自动化、自动线、数控机床、加工中心、柔性制造系统、计算机集成制造系统和并行但生产率更高。其技术已基本成熟,目前进入实用化阶段。工程等几个阶段,并进一步向柔性化、集成化和智能化发展。目前,柔性制造系统和计算机(4)柔性制造工厂(FlexibleManufacturingFactory,FMF)FMF是将多条FMS连接起集成制造系统在机械制造中的应用日益广泛。来,配以自动化立体仓库,用计算机系统进行联系,采用从订货、设计、加工、装配、检一、柔性制造系统验、运送至发货的完整FMS。它也包括了CAD/CAM并使计算机集成制造系统(CIMS)投人实际使用,实现生产系统并行化及自动化,进而实现全厂范围的生产管理、产品加工及物柔性制造系统(FlexibleManufacturingSystem,FMS)是由统一的计算机控制系统(信料储运过程的自动化。息流)、物料(工件、刀具)和输送系统(物料流)连接起来的一组加工设备,能在不停情况下实现多品种、小批量零件的加工,并具有一定管理功能的自动化制造系统。3.FMS应具有的功能1.FMS的一般组成FMS是在成组技术(GT)、计算机技术、数控技术、CAD技术、机电一体化技术FMS主要是由多工位的数控加工系(Mechatronics)、模糊控制技术、智能传感器技术、人工神经网络技术(ANN)和虚拟现实统、自动化物料输送、存储系统和计算机(VR)及计算机仿真技术等技术基础上发展起来的,它具有以下主要功能:控制的信息系统组成的(图11-10)。图程序编制(1)自动完成多品种、多工序工件的加工功能这是依靠计算机控制的数控机床群来加工约束条件中空心箭头表示信息流,实线箭头表示物实现的,其中包括自动换刀、自动安装工件、切削液的自动供应和切屑的自动处理等。料流,双点画线框内表示FMS范围。FMS老动迎中央数据处理K-监控和记录(2)自动输送和储料功能这是由各种自动输送设备如环形输送托板、传输装置、无的系统扩展必须以模块结构为基础。轨小车、工业机器人等,以及自动化储料仓库如毛坯仓库、中间仓库、零件仓库、夹具仓数控加工系统是由可自动换刀的数控储料机床机床机床测量机床、加工中心或车削中心组成的。待加(3)自动诊断功能这是由系统工况监视功能、指令和恢复功能组成的。监视功能库、刀具仓库等来实现的。√工工件的类别及技术要求将决定FMS所运送系统(监控功能)是通过各类传感器来测量、控制加工精度,监视刀具的磨损或破损,以保证加采用的设备形式。毛坯上料工的顺利进行。指令和恢复功能是计算机发出工作指令来补偿加工精度、更换磨损或破损刀物料流物料输送和存储系统是由存储、输送输入卸料零件具的功能。输出和装卸三个子系统组成的,用以实现工件(4)信息处理功能这是对所需信息进行综合、控制,主要有:图11-10柔性制造系统组成原理1)编制生产计划及生产管理程序,实现可变加工而又均衡生产179178第九章钳工头指导书(金工实习三角刮刀(3)修配法修配法是指将零件的制造公差扩大,装配时用钳工的修配方法,修去某切削部分配合件上的预留量,以达到规定的装配精度。一般适用于单件、小批且装配精度要求较高的(4)调整法调整法是指装配时调整一个或几个零件的位置,以达到规定的装配精度。刮削方向情况。刮刀切削部分其特点是可进行定期调整,易于保持和恢复配合精度,且零件的加工精度不高。一般适用于装配自动化可以减轻劳动强度、提高生产率,其一般包括:给料自动化、传送自动化、小批量生产或单件生产。轴瓦5.装配自动化工件图9-59刮削轴瓦装人自动化、连接自动化、检测自动化等。装配自动化主要适用于批量装配。装配自动化系统分为刚性装配和柔性装配。刚性装配系统是按一定的产品类型设计的,第九节装配适合于大批量生产,能实现高速装配,节拍稳定,生产率趋于恒定,但缺乏灵活性。是按照成组的装配对象,确定工艺过程,选择若干相适应的装配单元和物料储运系统,由计算机或其网络统一控制,能实现装配对象变换的自动化,能适应产品设计的变化,主要适合于多品将合格零件按装配工艺文件组装起来,并经调试成为合格产品的过程称为装配。装配是产品制造的最终工序,其质量好坏直接影响产品性能和使用寿命。种中小批生产,且多用于自动化和无人化的生产。柔性装配系统主要包括:可调装配机、可编程的通用装配机、装配中心、工业机器人和机械手等。一、装配工艺过程二、零件的连接方式1.装配前的准备研究产品装配图及技术要求,了解产品结构、零件的作用及相互连接关系,弄清零部件零件的连接方式分为固定连接和活动连接。的工作表面和数量、重量及其装拆空间;确定装配方法、装配顺序;准备所需的装配工具;固定连接是指装配后零件之间没有相对运动的连接,分为可拆式与不可拆式。1.固定连接领取零件并对装配的零件进行清理、清洗(去油污、毛刺、锈蚀及污物);涂防护润滑油;完成需要的修配工作。1)可拆式固定连接包括螺纹、销、键等连接及锥体配合等。2.装配的组合形式2)不可拆式固定连接包括焊接、铆接、过盈配合、胶合、压合等。装配一般分为组件装配、部件装配和总装配。活动连接是指装配后零件在工作中能按规定要求做相对运动的连接,分为可拆式与不可2.活动连接组件装配是将若干个零件安装在基准零件上的装配过程,如减速箱的轴与齿轮的装配。部件装配是将若于个零件、组件安装在另一个基准零件上的装配过程,如机床的主轴箱装1)可拆式活动连接包括轴与滑动轴承、柱塞与套筒、丝杠与螺母等。拆式。配。总装配是将若干个零件、组件及部件安装在产品的基准零件上构成产品的装配过程,如车床的各部件安装在床身上构成车床的装配。2)不可拆式活动连接包括活动铆接、滚动轴承等。3.装配顺序三、常用连接方式的装配装配的一般顺序是:组件装配一部件装配一总装配一调整一试车一检验一包装。4.装配工艺方法螺纹连接是机器装配中最常用的可拆式固定连接,具有结构简单、装拆方便、连接可靠1.螺纹连接的装配常用的装配工艺方法有完全互换法、分组装配法、修配法和调整法等。特点。常用的螺纹连接件有螺栓、螺钉、螺母及各种专用件等(1)完全互换法完全互换法是指装配时各个零件不需要进行任何选择、修配和调整就可以达到所规定的装配精度。该装配过程简单、生产率高,易更换零件,但对零件的加工1)螺纹连接应做到手能自由旋人。过紧会咬坏螺纹,过松则受力后螺纹易断裂。装配时应注意:精度要求高。一般适用于装配精度要求不高、产品批量较大的情况。(2)分组装配法分组装配法是指将零件的制造公差扩大,装配时按零件的实际尺寸3)用螺栓、螺钉与螺母连接零件时,配合面要平整光洁,否则螺纹易松动。为提高接2)螺母端面应与螺栓轴线垂直,以使受力均匀。大小顺序分组,然后对应各组进行装配,以达到规定的装配精度。一般适用于成批生产中的某些精密配合处。4)双头螺柱要牢固地拧在连接体上,松紧适当。装配时,应使用润滑油。5)装配成组螺钉、螺母时,为保证接合面受力均匀,需按一定顺序分两次或三次拧紧合质量常加垫圈。149148第九章钳工工程实训指导书(金工实习)如图9-27所示。工作部分锉柄图9-29锉刀的构造切削方向锉刀存屑槽a)b)图9-26锯削圆管的方法分的长度表示,一般有100mm、150mm、200mm、a)正确b)不正确图9-27锯削薄板250mm、300mm、350mm和400mm七种。锉刀的锉齿是在剁机上剁出的,交叉排列,构成刀齿,形成存工件4.锯削深缝刀的锉纹有单纹和双纹两种,一般制成双纹,屑槽,如图9-30所示。图9-30锉齿当锯缝的深度超过锯弓的高度时,如图9-28a所示,应将锯条转过90重新安装,把以便锉屑断碎,锉面不易堵塞,且省力。单纹锉刀一弓转到工件旁边,如图9-28b所示,当锯弓横过来的高度仍不够时,也可将锯条转过180°使其锯齿安装在锯弓内进行切削,如图9-28c所示。刀按每10mm长的锉面上锉齿的齿数分为粗锉、细锉和油光锉三种。粗(4-12)用于粗加工或锉铜、铝等有色金属;细(13-24齿)用于锉光表面或硬金属;油般用于锉削铝等软材料。锉刀按用途可分为钳工锉、整形锉和特种锉三种。钳工锉适用于一般工件表面的锉削,光(30~40齿)用于精加工时修光表面。通常按其截面形状的不同分为平锉、方锉、圆锉、半圆锉、三角锉等,如图9-31所示。整形适用于精加工及修整工件上细小部位和精密工件(如样板、模具等)的加工,一般5~2.锉刀的种类b)12支一组。特种锉适用于工件的各种特殊表面的加工。0平锉图9-28锯削深缝四、锯削安全注意事项半圆钟1)锯削起锯后应将左手轻扶在弓架前段,谨防将左手放在台虎钳上,被手锯锯伤。2)锯削过程动作要平稳,压力不宜过大,速度要适中,特别是在卡锯时不要强行推锯,以免锯条折断伤人。方锉3)工件快断时,注意控制手锯,防止工件掉落伤手、伤脚。第五节锉削三角锉H用锉刀对工件表面进行切削加工的操作称为锉削。它是钳工最基本的操作,多用于锯削或錾削之后,常用于零部件的装配与加工。锉削加工简便,工作范围广,可用于加工平面、圆锉曲面、沟槽和各种复杂表面,也可用于装配时的工件修整。锉削的尺寸精度可达IT7-IT8,应用示例表面粗糙度Ra值可达0.8μm。图9-31钳工锉的种类一、刀及其使用1.锉刀的构造二、锉削的基本操作刀(图9-29)是由碳素工具钢经淬硬制成的,硬度达62-67HRC。其规格以工作部根据工件形状和加工面的大小选择锉刀的形状和规格;根据金属材料的硬度、加工余量1.锉刀的选用137136工程实训指导书(金工实习)第八章磨削与镗削v=F×L3/3E×I式中F——合力(N);L——悬伸量(mm);E——弹性模量(Pa);I——刀杆的截面惯性矩(mm4)。(硬度45HRC或更高)、镍基及钴基合金的精镗。氮化硅基陶瓷刀片包括双层CVD涂层(一层是TiN,另一层是Al2O3)牌号和未涂层牌镗刀杆截面惯性矩的计算公式为号。涂层牌号兼具良好的韧性和刃口耐磨性,推荐用于灰铸铁和球墨铸铁的镗削。某些未涂I=πD4/64层牌号具有优异的抗热冲击性及断裂韧度,而另一些牌号能够吸收机械冲击和保持良好的刃式中D——镗刀杆的外径(mm)。口耐磨性,此类牌号适于高温合金的镗削。具有高韧性的未涂层牌号推荐用于灰铸铁的粗镗分析镗刀挠曲和截面惯性矩的计算公式可知,在镗削时应遵循以下原则:金属陶瓷是由陶瓷材料(钛基硬质合金)与金属(镍、钴)结合剂组合而成的复合材1)镗刀的悬伸量应尽可能小。因为随着悬伸量的增大,挠曲量也会随之增大。例加料。金属陶瓷分为涂层牌号和未涂层牌号两类。未涂层牌号硬度较高,具有良好的抗积屑瘤和断续镗削。当悬伸量增大1.25倍时,在刀杆外径和切削用量保持不变的情况下,挠曲量将增大近2和抗塑性变形能力,用于表面粗糙度要求较高的合金钢精镗。多层PVD涂层牌号(两层2)镗刀杆的直径应尽可能大。因为当刀杆直径增大时,其截面惯性矩也会增大,挠TEN涂层之间夹一层TiCN涂层)可用于大部分碳素钢、合金钢及不锈钢的高速精镗和半精量将会减小。例如,当刀杆直径增大1.25倍时,在悬伸量和切削用量保持不变的情况下;用于加工灰铸铁和球墨铸铁时,也可获得较长的刀具寿命和良好的表面粗糙度。挠曲量将减小近2.5倍。聚晶金刚石(PCD)是由金刚石微粉、结合剂和催化剂在高温、高压下制成的超硬材料。PCD刀片是将PCD刀尖焊接在硬质合金基体上制成的。PCD刀具最有效的用途是加工3)在悬伸量、刀杆外径和切削用量保持不变时,采用高弹性模量材料的镗刀杆可以小挠曲量。过共晶铝合金(硅的质量分数超过12.6%)。PCD刀具的切削刃能长久保持锋利,超过了其3.镗刀杆的材料他刀具材料。此外,PCD刀具适用于高速切削。聚晶立方氮化硼(PCBN)的硬度仅次于PCD。市场供应的PCBN刀片有多种结构形镗刀杆由钢、钨基高密度合金或硬质合金制成。无论何种牌号的碳素钢和合金钢,都有式,如焊接式PCBN刀片(将或大或小的PCBN刀尖焊接在硬质合金刀片上)、整体PCBN相同的弹性模量:E=30×10Pa。一种常见的误解是认为采用高硬度或高品质钢制造镗刀杆刀片、采用硬质合金基体的全加工面PCBN刀片等。PCBN刀片牌号通常用于淬硬钢、工具可以减小挠曲量。而从挠曲计算公式可以看出,决定挠曲的变量之一是弹性模量而非硬度。钢、高速工具钢(45-60HRC)、灰铸铁、冷硬铸铁以及粉末冶金材料的精镗加工。PCBN钨基合金由粉末冶金制成。钨、镍、铁、铜等高纯度金属粉末是烧结各种合金的典型元的一个独特性能是其室温硬度与切削时的高温硬度基本相同,这就使PCBN刀具在高速加工素,其中有些合金可用于制作镗刀杆和其他刀柄。用于制作镗刀杆的典型钨基高密度合金牌中可获得比加工相同工件的其他类型刀具更长的刀具寿命。号是K1700(E=45×10Pa)和K1800(E=48×10Pa),用它们制成的镗刀杆在以相同切削用量进行镗削时,其挠曲量可比相同直径和悬伸量的钢制刀杆减小50%~60%。用于钢制镗刀杆的镗刀片型号有:CNMG332、CNMG432和CNMG542;DNMG332和5.镗刀片型号用硬质合金制成的镗刀杆挠曲量非常小,因为其弹性模量比钢和高密度钨基合金高得DNMG442;SNMG432;TNMG332和TNMG432;VNMG332和VNMG432;WNMG332和WNMG432。多。制作镗刀杆的典型硬质合金牌号的碳化钨含量为90%~94%,钴含量为6%~10%。镗刀片的主要几何角度有前角、刃倾角和余偏角。前角和刃倾角为负值,典型的前角值4.镗刀片的材料为-6°;刃倾角根据刀片形状的不同,在-16°~-10°之间取值;余偏角与刀片形状有关:镗刀片可采用硬质合金、陶瓷、金属陶瓷、PCD、PCBN等不同刀具材料制成。硬质合金CNMG和WNMG为-5°,DNMG和VNMG为-3°,TNMG为-1°,SNMG为15°。镗刀片大多采用PVD或CVD涂层。例如,PVDTiN涂层适于加工高温合金和奥氏体不锈钢;用户通过对刀片材料及几何参数、刀杆材料及切削力进行认真权衡和优选,就会使镗刀PVDTiAIN涂层用途广泛,适于加工大部分钢、钛合金、铸铁及有色金属合金。这两种涂层都的挠曲减至最小,加工出符合要求的孔。涂覆于具有良好抗热变形和抗断续切削能力的硬质合金基体上。此类硬质合金基体含有约94%复习思考题的碳化钨和约6%的钴,如GB/T18376.1-2008规定的K10、K20、M10、M20、P10、P20。CVD涂层硬质合金牌号适用于大部分钢和铸铁材料的镗削。CVD涂层是由TiN、Al203、1.磨外圆时的切削运动有哪些?TiCN及TiC等多层成分组成的复合涂层,其中每层涂层都具有特定功能,不同的涂层组合2.外圆磨床由哪几部分组成?各部分有何作用?能抵抗不同的磨损机制。典型的硬质合金牌号由碳化钨、碳化钽及含钴TiC等多元碳化物组3.磨床为什么要使用液压传动?磨床工作台的往复运动是如何实现的?成,如GB/T18376.1-2008规定的K10-K30、M10-M40、P10-P40。4.如何选择砂轮?砂轮的硬度和磨粒的硬度有何不同?陶瓷刀片牌号包括氧化铝(Al2O3)基和氮化硅(Si3N)基两大类。氧化铝基陶瓷刀片又分为未涂层和PVDTiN涂层两类牌号。未涂层牌号具有较好的韧性和耐磨性,推荐用5.磨外圆的方法有哪几种?各有什么特点?于合金钢、工具钢和硬度大于60HRC的马氏体不锈钢的镗削。涂层牌号则用于淬硬钢、铸6.平面磨削常用方法有哪几种?如何选用?8.镗床主要有哪几种?在镗床上镗孔与在车床上镗孔有什么不同?7.镗削的特点是什么?124125工程实训指导书(金工实习)第八章大于车削所消耗的能量。这些能量在磨削中将迅速转变为热能,磨粒磨削点温度高达10%磨削与镗削1400℃,砂轮磨削区温度也有几百度。磨削温度对加工表面质量影响很大,需设法控制2.影响磨削温度的因素(1)砂轮速度提高砂轮速度,单位时间通过工件表面的磨粒数增多,单颗磨粒切好的抗泡性能,良好的环境稳定性。对于高速磨削,由于磨除效率高,发热量大,因此对高厚度减小,挤压和摩擦作用加剧,单位时间内产生的热量增加,使磨削温度升高磨削液的润滑性及冷却性能要求很高。另外,还应对磨削液的第二层功能,即防腐性、防(2)工件速度增大工件速度,单位时间内进入磨削区的工件材料增加,单颗磨粒火性、消泡性、无害性及抗氧化性等加以足够重视。钢片磨削液主要由润滑剂、防锈添加剂、稳定剂等组成,广泛应用于硬质合金的各种磨1.构成切削厚度加大,磨削力及能耗增加,磨削温度上升;但从热量传递的观点分析,提高工件度,工件表面与砂轮的接触时间缩短,工件上受热影响区的深度较浅,可以有效防止削,具有润滑、防锈、防腐蚀、冷却等作用。其润滑性佳,使用效果明显优于乳化液,可提表面产生磨削烧伤和磨削裂纹。因此,在生产实践中常采用提高工件速度的方法来减少工表面烧伤和裂纹。工件表面粗糙度,不粘砂轮,降低砂轮磨损。溶液透明,易观察表面加工情况。防锈期达7天以上。(3)径向进给量径向进给量增大,单颗磨粒的切削厚度增大,产生的热量增多,2.性能特征磨削温度升高。(1)润滑可延长刀具寿命,提高加工件表面质量。(2)防锈对于钢和铸件都有较好的防锈能力,可完全取代工序间防锈。(4)工件材料磨削韧性大、强度高、导热性差的材料,因为消耗于金属变形和摩(3)冷却快速降低加工件的温度。的能量大、发热多,而散热性能又差,故磨削温度较高;磨削脆性大、强度低、导热性好的材料,磨削温度相对较低。(4)清洗对加工件遗留的钢屑、铁屑等有清洗作用,提高磨削效率。本品对机床、零件无腐蚀,对人体无毒害,符合环保要求,对环境无污染,(5)砂轮特性选用低硬度砂轮磨削时,砂轮自锐性好,磨粒切削刃锋利,磨削力和(5)安全磨削温度都比较低。选用粗粒度砂轮磨削时,容屑空间大,磨屑不易堵塞砂轮,磨削温度比选用细粒度砂轮磨削时低。(6)经济本品是高浓缩的,使用时可根据需要稀释10~25倍,非常经济。易于排放。磨削液种类非常多,通常可分为两大类型:水溶性磨削液和油溶性磨削液。水溶性磨削3.种类特性七、磨削表面的表面粗糙度液又可分为:乳化液、半合成、全合成。油溶性磨削液主要成分为矿物油。普通矿物油是在1.磨削表面的表面粗糙度的形成低黏度或中黏度矿物油中加防锈添加剂。例如在机械油、轻柴油、煤油中加脂肪酸以增强润磨削表面的表面粗糙度是由磨粒磨削后在加工表面上形成残留轮廓和工艺系统振动所引滑作用。另外在磨削液中加入硫、氯、磷等元素的极压添加剂形成极压油,其渗透能力和润起的波纹所决定的。滑能力会更适宜表面粗糙度要求低的工序加工使用。油溶性磨削液有较好的附着性,能隔绝2.影响磨削表面的表面粗糙度的因素空气,防止磨削区氧化和水解等不良的化学反应。例如CBN砂轮易在高温下与水发生反应,磨削时的残留部分取决于砂轮的粒度、硬度、砂轮的修整质量及磨削用量。所以使用CBN高速磨削时应采用油性磨削液。水溶性磨削液中的乳化液含油量50%左右,磨削中的振动远比残留部分对表面粗糙度的影响大。消除振动,减小波纹的主要措施:半合成含油量5%-40%,全合成不含油,主要由水基化合物和水组成;水溶性磨削液其具严格控制磨床主轴的径向圆跳动;砂轮及其他高速旋转部件要经过仔细的动平衡;保证磨床有很好的冷却效果,且配制方便、成本低廉、不易污染。工作台慢进给时无爬行;提高磨床动刚度;磨削用量和砂轮选择合理。4.适用范围八、磨削液磨削液可用于不锈钢、碳素钢、高镍钢、铸铁等大部分金属,适用于碳素钢、轴承钢、球墨铸铁、合金钢等材质,调整磨削、普通磨削、精磨及磨削、车削混合加工线作为切削磨削过程中,砂轮和材料之间既发生切削又发生刻划和划擦,产生大量的磨削热。与车液,尤其适用于大循环集中供液系统。主要用于硬质合金在切削、磨削过程中的润滑散热并削、铣削等切削方式不同,车削、铣削有70%-80%的热量聚集在切屑上流走,传人工件的能短期防锈。占10%-20%,传人刀具的则不到5%,但磨削由于被切削的金属较薄,60%~90%的热量被1)用自来水稀释使用,磨削使用浓度为3%-4%(25倍以上水稀释)。5.使用说明传人工件,仅有不到10%的热量被磨屑带走,产生了大量的磨削热,磨削温度可达400-1000℃,在这样的高温下,材料会发生变形和烧伤,砂轮也会严重磨损,磨削质量下降。在2)磨削液加入到机床盛装磨削液的槽中,再加入20倍的清水搅拌均匀,即可投入通常情况下磨削都会使用磨削液,将大量的磨削热带走,降低磨削温度。有效地使用磨削液可提高切削速度30%,将温度降到100~150℃,减少切削力10%-30%,延长砂轮使用寿命黑或产生异味时应排放更新。根据切削工作量的多少不同,切削液每隔3个月左右需排放更使用。4-5倍。3)在使用中,磨削液会因不断污染而变脏,铁屑沉积过多时应及时清理,切削液若变磨削液的四大作用:润滑、冷却、清洗、防锈。附带的作用有良好的乳化分散性能,良1204)排放更新时若切削液槽底脏污严重,应及时清理干净,以免污染新液。新一次,平时应及时进行补充。1工程实训指导书(金工实习)平面的加工精度可达IT5-IT6,表面粗糙度Ra值为0.2-0.4μm(2)内圆磨床内圆磨床(图8-7)主要用来磨圆柱孔、锥孔及端面。磨削运动和外磨削与镗削磨床相同。砂轮做高速旋转,且旋转方向与工件旋转方向相反。内圆的加工精度可达IT7,表面粗糙度Ra值为0.2~0.8μm。牢,砂轮的硬度就越高。(3)无心外圆磨床无心外圆磨床主要用于成批及大量生产中磨削细长轴和无中心的短轴。磨削时不用装夹工件,而是放置在砂轮和导轮之间,用托板支承,工件由低速旋的导轮带着旋转,由高速旋转的砂轮磨削,如图8-8所示。磨削的加工精度可达ITS-表面粗糙度Ra值为0.2~0.8μm。砂轮修整器平形单面凹形薄型筒形碗形碟形双斜边形头架砂轮砂轮架图8-10砂轮的形状工作台e导轮(4)硬度砂轮的硬度是指磨粒在磨削力作用下,从砂轮表面上脱落的难易程度。砂床身砂轮轮硬度越高,磨粒越不容易脱落。砂轮的硬度分七个等级。导轮操纵砂轮架手轮磨削时,如砂轮硬度过高,则磨钝了的磨粒不能及时脱落,会使磨削温度升高而造成工则磨粒脱落过快,不能充分发挥磨粒的磨削效能,操纵工作台手轮外形。图8-7内圆磨床、工件材料硬度较高时,应选用较软的砂轮;工件材料硬度较低时,应选用较硬的砂轮;砂轮图8-8无心外圆磨床原理托板砂轮与工件接触面较大时,应选用较软砂轮;磨薄壁件及导热性差的工件时,应选用较软的三、砂轮砂轮;精磨和成形磨时,应选用较硬的砂轮;砂轮粒度号大时,应选用较软的砂轮。(5)组织砂轮的组织是指磨粒、结合剂、气孔三者体积的比例关系,分为紧密、中1.砂轮特性及选择原则等、疏松三大类16级,最常用的是5级、6级,级数越小,砂轮越紧密。磨淬火钢及工具砂轮是磨削的主要切削工具。普通砂轮是用结合剂把磨粒粘结起来,经压坯、干燥、焙烧及车整制成。磨粒、结合剂和空隙是构成砂轮的时常用中等组织。(6)砂轮形状在砂轮的端面上一般印有标志,用以标示砂轮的特性。三大要素(图8-9)。砂轮的特性取决于磨粒、粒砂轮选用时主要根据工件的材料、形状、尺寸及热处理方法。在砂轮的非工作面上印有度、结合剂、硬度、组织、形状和尺寸等。(1)磨粒磨粒是砂轮的主要成分,直接进行特性代号,如:待加工表面砂轮砂轮GB/T41271N-300×50×76.2-A/F36L5V--50m/s切削,应具有坚韧、锋利、耐热等性能。常用的磨已加工表面粒有刚玉(Al2O3)和碳化硅(SiC)两大类。刚玉空隙砂轮一类适用于磨削钢料及合金钢刀具,碳化硅类适用于切削表面工件对应标准号磨削铸铁、青铜等脆性材料及硬质合金刀具等。型号1-给合剂圆周型面(2)粒度磨粒的尺寸用粒度表示,当磨粒尺磨粒外径厚度寸较大时,用筛选法分级,以其能通过的筛网上每英寸长度上的孔数来表示粒度号,如F60图8-9磨削原理及砂轮结构孔径磨料牌号(四个空格间隔)表示磨粒能通过每英寸60个孔眼的筛网。粒度号越大,磨粒越细;粒度号越小,磨粒越粗。磨粒种类直径小于63μm的磨粒称为微粉,用光电沉降仪法分级。微粉的粒度号为F230~F1200,F粒度一后的数字越大,微粉越细。粗磨和磨软材料时用小号,即选用磨粒较粗的砂轮,以提高生产硬度等级组织一率;精磨和磨硬材料时用大号,即选用磨粒较细的砂轮,以减小表面粗糙度值。砂轮与工件结合剂种类结合剂牌号(四个空格间隔)接触面积较大时,选用磨粒较粗的砂轮,防止烧伤工件。常用的粒度号为F30~F100。最高工作速度(3)结合剂磨粒由结合剂粘结成具有一定形状和强度的砂轮(图8-10)。常用的结合剂种类有陶瓷结合剂、树脂结合剂和橡胶结合剂,最常用的是陶瓷结合剂。磨粒被粘结得越2.砂轮的安装与修整116砂轮是在高速下工作的,安装前必须确保其没有裂纹。大尺寸砂轮用台阶法兰盘安装并需做平衡试验;中等尺寸的砂轮用法兰盘安装在主轴上(图8-11);小尺寸砂轮直接黏固在117◆第九章钳工第九章作,主要有台式钻床、立式钻床和摇臂钻床。钳工着机械制造技术的发展,钳工工艺也在不断改进,钳工操作、钳工工具机械化程度不断地提高,以减轻其劳动强度、提高劳动生产率。是学生金工实习中最为基础的一部分,通过实践操作,初步接触工生产的作性质,掌握钳工的工作范围,为后续学习提供感性认识,为生产管理积累实践经验。学生的实习过程以独立操作为主,以示范讲解和现场教学为辅,通过学生亲自动手加工第一节概述工件和装配工件来提高动手能力和独立工作的能力。)人身安全是实习的最根本要求,实习过程中应自觉遵守钳工的安全技术规则和劳动钳工实习的要求如下:钳工在机械制造业中具有相当重要的位置,适用范围广,不仅适用于机械加工,而且机械设备装配、维修中具有重要地位。)握工作业的基本操作,了解所用设备和工具,完成一般零件的工加工任务。纪律。钳工大多是手工操作,劳动强度大,生产率低,操作技能要求高,但具有所用工具3)对零件的加工工艺过程有一定的了解,能够安排一般零件的钳工加工顺序。单、加工灵活、操作方便、适应性强等特点,可以完成机械加工中不便或无法完成的工作钳工的主要应用有:4)了解机械制造中钳工的有关文件和技术资料。第二节划线1)加工前工件准备,如清理毛坯、工件划线等。2)单件或小批量零件生产。3)精密零件修整,如刮削或研磨量具的配合表面。划线就是根据图样或实物,在毛坯或半成品上划出加工尺寸界线的操作过程。划线是一4)装配、调试和维修机械。项复杂、细致的工作,直接关系到产品的质量。划线的总体要求是:尺寸准确、位置正确、钳工是冷加工的重要工种之一,是手持工具来完成工件的加工、装配、调整和修理等工线条清晰、冲眼均匀。划线精度一般在0.25~0.5mm之间。作的操作。其基本操作有划线、錾削、锯削、锉削、钻孔、扩孔、铰孔、孔、攻螺纹、套螺纹、刮研和装配等。钳工工作场地的主要工具和设备包括钳工工作台、台虎钳、砂轮和钻床。1)在待加工件上确定加工余量、加工位置或工件安装时的找正线,作为工件加工和安一、划线的作用钳工工作台(简称钳台)是钳工的专用工作台,要求稳固,一般由坚实杂木做成,台装的依据。面距离地面高度800-900mm,台虎钳固定在台面上,高度正好便于操作。实习中一般在钳2)通过划线检查毛坯的形状和尺寸是否符合图样要求,避免不合格的毛坯投入加工而台上安装4台台虎钳,为了安全,台面应设有防护3)合理地分配各加工表面的余量,从而保证少出或不出废品。造成浪费。网。钳台抽屉用于放置工具,如直角尺、手锯、锉刀、锤子等。台虎钳(图9-1)牢靠地固定在钳台上,用于二、划线工具及使用夹持工件,其规格以钳口宽度表示,常用的有100mm、125mm、150mm三种。使用台虎钳夹紧平板(图9-2)是用以检验、划线的平面基准工具。平板一般由铸铁制成,经时效处1.基准工具工件时,直接转动台虎钳的手柄,切勿用套管接理。上平面为划线的基准平面,因此要求平直和光洁。平板安放应稳固,上面应保持水平,长或敲击手柄,以免损坏台虎钳;锤击工件时,2以便稳定地支承工件。平板各处应均匀使用,不准敲只能在固定钳身上敲击,其他部位不能敲打,以击和碰撞,并保持表面清洁,长期不用应涂油防锈并免破坏台虎钳。使用时注意手柄为活动件,谨防放松时夹到手。用木板护盖。砂轮机用来磨钻头、錾子、刮刀等刀具或其2.支承工具他工具,还可以用来去毛刺等。常用的支承工具主要有:V形铁、方箱和千斤顶。图9-1台虎钳(1)V形铁V形铁(图9-3)用于支承圆柱形图9-2平板钻床用来完成钳工的钻孔、扩孔和铰孔等工1一手柄2一丝杠3一活动钳口1264一固定钳口5一螺母6一夹紧手柄7一夹紧盘8底座(2)方箱方箱(图9-4)用于夹持尺寸较小而加工面多的工件,能根据需要转换位置工件,使工件轴线与平板平行,以便划出中心线。127第八章程实训指导书(金工实习磨削与镗削工件镗刀第二节镗削镗刀工件镗杆2√A钟削是在镗床上用镗刀对工件表面进行的切削加工,是一种用刀具扩大孔或其他圆形镗刀工件目√廊的内径切削工艺。主要用于复杂零件(箱体、缸体和支架)上具有较高尺寸精度和位精度要求的孔和孔系以及相关表面的加工,其应用范围一般从半粗加工到精加工,所用刀"b)μ工件螺纹镗刀通常为单刃镗刀(称为镗杆)。镗孔是镗削的一种。镗削主要用来加工直径在80mm以上的铣刀孔,环形槽及有较高位置精度的孔系等,还可以进行钻孔、扩孔、铰孔及铣平面。镗孔的尺a)寸精度可达IT7,表面粗糙度Ra值为0.8~1.6um。工件端面镗刀工件一、镗床的分类凸凸凸镗床分为卧式镗床、立式镗床、深孔镗床和坐标镗床,其中应用最广的是卧式镗庆凸凸凸f)(图8-16)。卧式镗床加工时,通过垂直调整主轴箱和横向调整工作台,可以精确地确定被e)加工的孔与孔或孔与基准平面在两个互相垂直坐标上的相对位置。工作台还可绕垂直轴做转运动,从而可以对工件的各个方向进行加工,如图8-17所示。d)图8-18卧式镗床上的主要加工范围a)镗孔b)镗同轴孔c)镗大孔d)加工端面e)铣平面f)加工螺纹后立柱雕前立柱变速箱前立柱尾座、转盘主轴田主轴箱双刃镗刀有两个对称的切削刃,切削时背向力可以相互抵消,工件孔径尺寸和精度由镗2.双刃镗刀工作台尾座主轴刀径向尺寸保证。工作台三、镗刀床身10镗刀有三个基本零件:可转位刀片、刀杆和镗座。镗座用于夹持刀杆,夹持长度通常约为一床身上拖板刀杆直径的4倍。装有刀片的刀杆从镗座中伸出的长度称为悬伸量(镗刀的无支承部分)。悬下拖板图8-16卧式镗床伸量决定了镗孔的最大深度,是镗刀最重要的尺寸。悬伸量过大会造成刀杆严重挠曲,引起振图8-17卧式镗床的运动颤,从而破坏工件的表面质量,还可能使刀片过早失效。这些都会降低加工效率。镗削的主运动是镗刀的转动,进给运动是工件或刀具的移动。采用不同的主运动和进给运通常应该选用静刚度和动刚度尽可能高的镗刀。静刚度反映镗刀承受因切削力而产生挠动配合,卧式镗床可完成各种孔、平面、沟槽、端面、环形槽以及螺纹等的加工(图8-18)。但是,由于机床和刀具调整复杂,操作技术要求高,刀具切削刃少,故生产率较低,一般用曲的能力,动刚度则反映镗刀抗振性。于单件小批量生产。在大批量生产中,需要用镗模夹具来提高生产率。作用于镗刀上的切削力可用一个旋转测力计进行测量。被测力包括切向力、进给力和背1.切削力二、镗刀类型切向力垂直作用于刀片的前面,并将镗刀向下推。需要注意:切向力作用于刀片的刀尖附向力。与其他两个力相比,切向力的量值最大。按其切削刃数量可分为单刃镗刀、双刃镗刀和多刃镗刀;按其加工表面可分为通孔镗刀、不通孔镗刀、阶梯孔镗刀和端面镗刀;按其结构可分为整体式、装配式和可调式。近,而并非作用于刀杆中心线,这一点至关重要。切向力偏离中心线产生了一个力臂(从刀杆1.单刃镗刀中心线到受力点的距离),从而形成一个力矩,它会引起镗刀相对其中心线发生扭转变形。单刃镗刀刀头结构与车刀类似,刀头装在刀杆中,根据被加工孔孔径尺寸,通过手工操进给力是量值第二大的力,其作用方向平行于刀杆的中心线,因此不会引起镗刀的挠纵,用螺钉固定刀头的位置。刀头与刀杆轴线垂直可镗通孔,倾斜安装可镗不通孔。单刃镗曲。背向力的作用方向垂直于刀杆的中心线,它将镗刀推离被加工表面。因此,只有切向力刀结构简单,可以校正原有孔轴线偏斜和小的位置偏差,适应性较广。但是,所镗孔径尺寸镗刀类似于一端固定(镗座夹持部分)、另一端无支承(刀杆悬伸)的悬臂梁,因此可和背向力会使镗刀产生挠曲。的大小要靠人工调整刀头的悬伸长度来保证,较为麻烦,加之仅有一个主切削刃进行切削,2.镗刀的挠曲故生产率较低,多用于单件小批量生产。123122用悬臂梁挠曲计算公式来计算镗刀的挠曲量第八章磨削与镗削工程实训指导书(金工实习)圆柱面、内外锥面、平面及成形面(花键、螺纹、齿轮等)和一些难加工的高硬材料(火钢、硬质合金),加工精度可达IT5-IT6,表面粗糙度Ra值为0.1-0.8μm。二、磨床广,可以磨削内外圆柱面、锥度较大的内外锥面和端面。液压传动具有传动平稳、无冲击振动、换向方便,且可以在较大范围内无级调速的特3.磨床的液压传动系统挡块—工作台挡块磨床的种类很多,专业性很强,按用途可分为外圆磨床、内圆磨床、平面磨床、无心床、花键轴磨床、螺纹磨床等。点,故磨床采用液压传动系统。图8-4为磨床液压传动原理图。磨床的液压传动系统主要由液压泵、液压do缸、转阀、溢流阀、节流阀、换向阀、工作介液压缸1.磨床的型号磨床型号的具体含义如下:质(液压油)及操作手柄等元件组成。溢流=2:=换向阀M1432B第二次重大改进阀的作用是使系统中维持一定压力,并把多余的高压油排入油池。工作台的往复直线运动是100操纵手柄节流阀1主参数1/10(最大磨削直径320mm)机床型别(万能外圆磨床型)工作台左移(操作手柄在图中实线位置)。按下述循环实现的。机床组别(外圆磨床组)高压油:液压泵→转阀→溢流阀→节流液压泵转阀油池类代号(磨床类)2.磨床的组成阀→换向阀→液压缸右腔。低压油:液压缸左腔→换向阀→油池。图8-4磨床液压传动原理图万能外圆磨床的主要组成如图8-3所示。工作台右移(操作手柄在图中双点画线高压油:液压泵→转阀→溢流阀→节流阀→换向阀→液压缸左腔。固定磨头砂轮架位置)。低压油:液压缸右腔→换向阀→油池。鸡心夹头拨杆砂轮顶尖尾座套筒头架、砂轮头架主轴工作台尾座操纵手柄由工作台侧面挡块推动。工作台行程由改变挡块位置来调整,当转阀转过90%固定顶尖+时,液压泵中的高压油全部流回油池,工作台工件拨盘停止运动。4.工件的装夹图8-5顶尖装夹床身回磨床上常用的工件装夹方法有顶尖装夹、横向进给手轮孔的轴类零件。为提高加工精度,工件支承在两固定顶尖之间(图8-5);卡盘有自定心卡卡盘装夹和心轴装夹。顶尖装夹适用于有中心拖板轴向进给手轮转台图8-3万能外圆磨床的主要组成盘、单动卡盘和花盘。无中心孔的圆砂轮修整器(1)床身床身用来支承和连接磨床各部件,上部的纵向导轨供工作台用,横向导轨柱形工件多采用自定心卡盘装夹,不磨头×立柱供砂轮架用,内部装有液压传动装置和操纵机构。对称的工件多采用单动卡盘装夹,形行程挡块工作台(2)工作台工作台有两层,上工作台可在水平面内偏转一定的角度(±8°),以便磨状不规则的工件多采用花盘装夹;心锥面;下工作台由液压系统控制沿床身导轨做纵向往复运动。工作台前侧面的T形槽内,轴装夹适用于盘、套类空心工件,常驱动工作台手轮径向进给手轮装有两个换向挡块,用以控制工作台的行程和换向。(3)头架头架的主轴前端安装顶尖、拨盘或卡盘,来装夹工件使其旋转。主轴由单用的心轴有台肩心轴、锥度心轴和胀床身独电动机带动,使工件获得不同的转速。力心轴。(4)尾座尾座套筒内装有顶尖,可与主轴顶尖一起支承工件。尾座在工作台上的位5.其他磨床置,可根据工件长度任意调整。(1)平面磨床平面磨床(图(5)砂轮架砂轮架用来安装砂轮,由单独电动机带动做高速旋转。砂轮架安装在床8-6)主要用来磨平面。磨削时,砂轮图8-6平面磨床身的横向导轨上,可通过手动或液压传动实现横向进给。的高速旋转为主运动,工作台的纵向万能外圆磨床的头架和砂轮架都可在水平面内回转一定角度,并装有磨头,故加工范围移动为进给运动。工作台上装有电磁114吸盘或其他夹具,用以安装工件。磨第七章工程实训指导书(金工实习)刨削第四节刨削方法机创削主要用来加工水平面、台阶、垂直面、斜面和各种沟槽等。刨削使用的刀具简d加工调整方便、灵活,但生产率低,主要用于单件生产、修配及狭长平面和较长沟槽图7-18刨矩形工件加工。一、刨平面刨平面是最基本的一种刨削。一般粗刨时,用平面刨刀;精刨时用圆头精刨刀。刨削用量为:刨削速度v=0.2-0.5m/s;进给量f=0.3~1mm/r;切削深度an=0.5~2mm。二、刨垂直面和斜面图7-19刨沟槽的顺序刨垂直面时,可采用偏刀,根据加工表面要求,选用左偏刀或右偏刀。刨削时,刀架转盘应对准零刻度线,使滑板(刨刀)能准确地沿垂直方向移动。同时,刀座还需偏转一定的角度(10°-15°),使刨刀在返程时可自由地离开工件表面,以免擦伤已加工表面和减少刀刃磨损,如图7-16所示。刨斜面与刨垂直面基本相同,区别在刀架转盘扳转一个加工所插削是指在插床上用插刀加工工件(图7-20)。插刀类似刨刀,但受内表面的限制,刀五、插削要求的角度。例如刨60°斜面,就应使刀架转盘对准30°刻线,如图7-17所示。插削的生产率低,加工的几何精度高,一般用于工具车间、机修车间和单件小批量生杆刚性差,插削精度不如刨削。产,加工的表面粗糙度Ra值为1.6~6.3μm。滑板刀座505拉削是指在拉床上用拉刀加工工件(图7-21)。从切削性质来看,拉削近似为刨削。拉六、拉削转盘准确10一对准零刻度线刀相对工件做直线移动(主运动)时,拉刀的每一个刀齿依次从工件上切下一层薄的切屑转盘对(进给运动)。当全部刀齿通过工件后,即完成了工件的加工。一般拉削孔的长度不能超过准30°孔径的三倍。由于拉刀结构复杂,价格昂贵,且一把拉刀只能加工一种尺寸的表面,故拉削2凸60主要用于大批量生产。氏球面垫板图7-16刨垂直面拉刀图7-17三、刨矩形工件刨斜面矩形工件要求相对表面平行,相邻表面垂直。这类工件既可铣削,又可刨削。当工件采用平口虎钳装夹时,加工四个面的步骤应按照图7-18所示的顺序进行。工件四、刨沟槽图7-21拉削圆孔V形槽、T形槽、燕尾槽等沟槽是由平面、斜面、直槽等组成的。刨槽前要先划线。各槽表面的加工顺序如图7-19所示。拉削的生产率很高,加工质量较好,广泛用于加工各种孔、键槽、平面、半圆弧面和某图7-20插销方孔110些组合面,加工精度可达IT6~IT8,表面粗糙度Ra值为0.4-0.8μm。111第七章第七章0B6刨削刨削主参数(最大刨削长度650mm)系代号(牛头刨床型)组代号(牛头刨床组)类代号(创床类)第一节概述二、刨床的组成牛头刨床主要由床身、滑枕、刀架、工作台及传动机构等组成,如图7-3所示。在刨床上用刨刀对工件进行切削加工的方法称为刨削。牛头刨床上刨削时,刨刀的往1.床身直线运动为主运动,工件的间歇移动为进给运动。刨削用量由切削速度v。(m/s)、进给证;、床身用来支承刨床的各部件,床身内部装有传动机构。其顶面的燕尾形导轨供滑枕做往(mm/r)和切削深度a(mm)组成,如图7-1所示。切削速度是指刨刀工作行程的平均度;进给量是指刨刀在一次往复后,工件沿进给方向移动的距离;切削深度是指刨刀切人复运动用,垂直面导轨供工作台升降用。件的深度。2.滑枕滑枕主要用来带动刨刀沿床身水平导轨做往复直线运动,其前端有刀架。3.刀架待加工表面过渡表面刀架用来夹持刨刀,实现刨刀上下运动及斜向进给,其滑板上装有可偏转的刀座。抬刀已加工表面板可以绕刀座的A轴顺时针抬起,供返程时将刨刀抬离加工表面,以减少刨刀与工件间的摩擦,如图7-4所示。滑枕of工作台刀架床身图7-1牛头刨床刨削用量摇臂机构男刻度盘变速机构如图7-2所示,刨削主要用来加工平面(图7-2a~c)、沟槽(图7-2e、f)和直线型成形面(图7-2d、g),加工精度可达IT8-IT9,表面粗糙度Ra值为1.6~6.3μm。滑板o男转盘刀座一、抬刀板-四四a)b)9横梁进给机构刀夹图7-2刨削的主要加工范围f)a)刨水平面b)刨垂直面g)图7-4刀架c)刨台阶面d)刨斜面e)刨T形槽f)刨直槽g)刨曲面图7-3牛头刨床第二节刨床工作台用来装夹工件。它可随横梁沿床身的垂直面导轨做上下调整,并可沿横梁做水平4.工作台一、刨床的型号方向移动或间歇进给运动。B6065刨床型号的具体含义如下:三、牛头刨床的传动系统及结构的调整104牛头刨床B6065的传动系统如图7-5所示,其中包括下述机构:105◆◆工程实训指导书(金工实习)3.专用夹具安装专用夹具是根据工件的加工要求设计出相应的夹具,其结构紧凑、装夹方便。成批大生产的工件用专用夹具,以保证工件加工后的准确性和装夹迅速。滑枕刨削床身五、其他刨床口除了牛头刨床外,刨削类机床还有龙门刨床、插床和拉床等。▣。床身b液压缸1.龙门刨床刀架支承座工作台图7-11所示为龙门刨床,主要用于加工大型工件上窄长的平面、大平面或多件多刀滚柱护送夹头时刨削。它与牛头刨床主要的区别在于龙门刨床是利用工作台(工件)的往复直线运动给运动是刀架(刀具)的间歇移动来刨削工件。龙门刨床刚性好、功率大、操作方加工精度和生产率比牛头刨床高。底座安装在横梁上的两个垂直刀架做横向进给,以刨水平面;安装在立柱上的两个侧刀架垂直进给,以刨垂直面。各个刀架均可扳转一定的角度以刨斜面。横梁可沿立柱导轨升降图7-12B5020插床图7-13卧式内拉床以适应不同高度的工件。2.插床第三节刨刀及安装插床(图7-12)的结构原理与牛头刨床类似,只是在结构形式上略有差别。插床的主运动是滑枕垂直方向上的往复直线运动;进给运动是工作台(工件)的纵向、横向或回转间歇转动或移动。工作台可进行圆周分度。插削斜面时,可将滑枕倾斜一定角度,且可在小一、常见刨刀于10°的范围内任意调整主要用于单件小批加工零件直线成形的内表面及与其相似的外表面,如内键槽、花键孔、方孔和多边形孔等。刨刀的结构和几何角度与车刀相似,由于刨刀工作时不连续,每次切人工件时受到较大的冲击,所以刨刀刀体的横截面均比车刀大1.25-1.5倍,以承受较大的冲击力。刨刀刀杆常做成弯头,弯头刨刀在受到较大的切削力时,刀杆所产生的弯曲变形可绕O点向后上方右立柱弹起,从而避免了啃伤工件,如图7-14所示。左立柱右垂直刀架刨刀的种类较多,按其加工形式和用途的不同,通常可分为平面刨刀、偏刀、角度偏左垂直刀架悬挂按钮站刀、弯切刀、成形刀等。横梁垂直刀架进给箱工作台右侧刀架进给箱左侧刀架二、刨刀的安装进给箱刨刀的正确装夹将直接影响工件的加工质量。装夹时,将刀架上的转盘对准零刻度线,液压安全器以准确控制吃刀量。刀架下端与转盘底部基本对齐,以增加刀架的刚度。直头刨刀的伸出长0度一般为刀体厚度H的1.5倍,如图7-15所示。弯头刨刀的伸出量可长些。床身右侧刀架减速箱工作台图7-11龙门刨床3.拉床在拉床上用拉刀加工工件称为拉削(图7-13)。拉床的运动较简单,只有主运动即拉刀15H的移动,没有进给运动(进给运动由递增的齿升量决定)。拉削的生产率很高,加工质量好,加工精度较高,主要用于大批量加工各种形状的通孔、平面和成形面。b)图7-15刨刀的装夹108图7-14刨刀a)弯头刨刀b)直头刨刀109工程实训指导书(金工实习)第五章槽时,可用主切削刃与槽宽相等的切槽刀一次切出;切宽槽时需分几次横向进给(图s.车削主轴53)。最后一次精车的顺序如图5-53c所示。工件交换齿轮进给箱丝杠∧∧∧∧对开螺母图5-56车螺纹的传动路线×+在车床上安装的位置正确。为获得准确的螺纹牙型,螺纹车刀的刀尖角应等于被切螺纹的牙b)c)型角(图5-57)。例如米制普通螺纹车刀的e,=60°,前角y。=0。粗车或车精度要求不高的螺纹时,车刀可有5°~15°的前角,以利于切削。图5-53切宽槽安装车刀时,车刀的刀尖必须对准工件的中心,同时必须用螺纹样板对刀,如图5-a)第一次横向进给b)第二次横向进给c)末次横向进给后,再以纵向进给精车槽底切宽槽58所示。否则,螺纹会出现牙型偏差和倒牙等误差。在加工螺纹过程中,若因刀具损坏,切断所用的切断刀与切槽刀极为相似,只是刀头更加窄长,刚性更差。由于刀具要切至要修磨或更换刀具,使刀具经过二次装夹,这时工件螺纹与车刀的相对位置发生变动,工件中心,呈半封闭切削,排屑困难,容易将刀具折断。因故必须重新用样板对刀,并且利用小滑板使车刀刀尖准确落在后来的螺纹槽内,才能继此,装夹工件时应尽量将切断处靠近卡盘,以增加工件刚性。续加工。如图5-54所示。用手动进给时一定要均匀,即将切断时,需x6-0放慢进给速度,以免刀头折断。七、车螺纹√样板螺纹的种类很多,按制别分为米制螺纹和寸制螺纹;按牙E-60°型分为普通螺纹、梯形螺纹、矩形螺纹等(图5-55)。其中单图5-54切断线、右旋、米制螺纹应用最广泛。图5-57螺纹车刀图5-58样板对刀螺纹的加工方法很多,主要有车削、铣削、攻螺纹和套螺纹、搓螺纹与滚螺纹、磨削及研磨等,但车螺纹最常见。车螺纹时,根据螺距,查找车床铭牌,选定进给箱手柄位置或更换齿轮,脱开光杠,啮合丝杠,并选较低的主轴转速,以使切削顺利并有足够的退刀时间。为使刀具移动平稳、均匀,还需调整横溜板导轨间隙和小刀架丝杠与螺母的间隙。工件必须装夹牢固。车螺纹的方法如图5-59所示。螺纹可用螺纹环规或螺纹塞规检验(图5-60)。为避免乱a)b)牙,车螺纹应始终保持主轴至刀架的传动系统不变、车刀在刀架上的位置保持不变、工件与图5-55螺纹的类型主轴的相对位置保持不变,否则需重新对刀。a)普通螺纹b)矩形螺纹c)梯形螺纹八、滚花车螺纹时,必须保证螺纹的中径、牙型角和螺距。为获得准确的螺距,必须由丝杠带动各种工具和机件的手握部分,为便于握持和增加美观,常常在表面上滚出各种不同的花刀架进给,使工件每转动一周,刀具移动的距离等于螺纹的导程(单线螺纹导程为螺距)。车螺纹的传动路线(由主轴至丝杠)如图5-56所示。改变进给箱手柄的位置或更换交换齿纹,如百分表套管、丝杠扳手及螺纹量规等。这些花纹一般是在车床上用滚花刀滚压而成轮,就可改变丝杠的转速,从而车出不同螺距的螺纹。的,如图5-61所示。车螺纹使用螺纹车刀,一般用高速工具钢或硬质合金制造,可加工各种形状、尺寸精度滚花花纹有直纹和网纹两种,滚花刀也分直纹滚花刀和网纹滚花刀。滚花属于挤压加的内外螺纹,特别适合加工大尺寸螺纹。螺纹牙型的精度取决于螺纹车刀刃磨后的形状及其工,因此其背向力很大,在加工时主轴转速要低些,还需要提供充足的切削液,以免损坏滚86花刀和防止滚花产生的细屑堵塞滚花刀纹路而产生乱纹。工程实训指导书(金工实习)小拖板行程的限制,不能车太长的锥面。而且,小拖板只能手动进给,锥面的表面粗糙度值1.双向手动法第五章大。刀架转位法在单件、小批生产中用得较多。车削双向手动法是指用双手同时摇动中拖板和小拖板的手柄,使刀尖的运动轨迹与所需成形面的母线相符,加工出所需的成形面(图5-49)。该方0、法简单易行,但对操作技能要求高,且生产率低,故适用于加工单件小批、精度要求不高的成形面。2.成形车刀法60切削刃形状与工件表面形状一致的车刀称为4020成形车刀。用成形车刀切削时,只要做横向进给就可以车出工件上的成形表面,如图5-50所示。图5-49双向手动法车成形面图5-45宽刀法车锥面图5-46刀架转位法车锥面用成形车刀车成形面,工件的形状精度取决于刀具的精度,加工效率高,但由于刀具切削刃长,加工时的切削力大,加工系统容易产生变形3.偏移尾座法和振动,要求机床有较高的刚度和切削功率。成形车刀制造成本高,且不容易刃磨。因此,偏移尾座法是指将尾座顶尖偏移距离s,使工件回转轴线与主轴轴线成半锥角α。利用成形车刀法适用于成批、大量生产。车刀的纵向进给,加工出所需锥面(图5-47)。3.靠模法尾座的偏移量为:s=Lsina或s=Ltana=L(D-d)/2l(a较小)靠模法车成形面如图5-51所示。该方法加工质量好、生产率高,但靠模的制造成本高,该方法可自动进给,能车出较长的锥面,且加工质量好。但因受尾座偏移量的限制,只故适用于大批量加工成形面。能加工半锥角a<8°的锥面,且不能车锥孔。偏移尾座法适用于成批加工锥面。4.靠模法靠模法是利用滑块沿固定在床身上的锥度靠模板内的移动来控制车刀的运动轨迹,从而加工出所需锥面(图5-48)。该方法适用于批量加工精度要求高、a<12°的长锥面和锥孔。0连接板销钉由⊙甲滑块靠模板底座图0图5-50成形车刀法车成形面图5-51靠模法车成形面1一车刀2一成形面3一拉杆4一靠模5滚柱++4.数控加工法〤数控加工法是目前加工成形面的主要方法,可25~30°|A图5-47偏移尾座法车锥面A-A图5-48靠模法车锥面加工任意要求的成形面,且加工质量好、生产率高。五、车成形面8~12°六、切槽和切断).5~0.5°~1°|A~2°车床上可以车削各种以曲线为母线旋转而形成的回转体成形面。车成形面的方法主要有双向手动法、成形车刀法、靠模法和数控加工法。回转体表面常有退刀槽、砂轮越程槽等沟槽,车出这些沟槽的方法称为车槽。切断是在车主切削刃84床上将坯料或工件从夹持端分离出来的车削方法。副切削刃~2°切槽使用切槽刀(图5-52)。切5mm以下的图5-52切槽刀工程实训指导书(金工实习)第五章右偏刀适用于车削轴类工件和直径较小的端面。在一般情况下,右偏从外缘向中心扩孔是在钻孔的基础上对孔的进一步加工。在车床上扩孔的方法与车床钻孔相似,所不车削车面时,由是副切主要切加工,在切作用,。为同的是用扩孔钻,而不是用钻头。扩孔的余量与孔径大小有关,一般为0.5~2mm。扩孔的服这一缺点,可以从中心向外进给,同时也可以在原副切削刃处磨出断屑槽,以此作为主切尺寸公差等级可达IT9-IT10,表面粗糙度Ra值为3.2~6.3μm,属于孔的半精加工。削刃进行车削。左偏刀适用于车左台阶和端面。由于是主切削切削,故切削顺利,加工质孔是用铰刀做扩孔或半精镗孔后的精加工,其方法与在车床上钻孔相似。铰削余量为0.1~0.2mm,尺寸公差等级一般为IT7~IT8,表面粗糙度Ra值为0.8-1.6um。量好。车台阶实际上是车外圆和端面的组合加工。轴上台阶高度在5mm以下的小台阶可在车钻孔、扩孔及铰孔是在车床上加工直径较小、精度较高、表面粗糙度值较小孔的主要方法。外圆时同时车出(图5-38)。装夹刀具时用直角尺对刀,以保证车刀的主切削刃垂直于工件2.镗孔轴线。轴上台阶高度在5mm以上的大台阶可分层进行切削(图5-39)。镗孔是利用镗刀对工件上铸出、锻出或钻出的孔做进一步的加工。图5-43所示为车床上镗孔加工。在车床上镗孔,工件旋转做主运动,镗刀在刀架带动下作进给运动。镗孔主要√出出用来加工大直径孔,可以进行粗加工、半精加工和精加工。镗孔可以修正原来孔的轴线偏斜,提高孔的位置度。镗刀的切削部分与车刀是一样的,形状简单,便于制造。但镗刀要进人孔内切削,尺寸不能大,导致镗刀杆比较细,刚性差,因此加工时背吃刀量和进给量都选约95得较小,进给次数多,生产率不高。镗削的通用性很强,应用广泛。精镗后孔的精度可达在末次纵向进给后,横IT7-IT8,表面粗糙度Ra值为1.6~3.2μm。90主切削刃偏刀主切削刃和工件轴线约成90分多次纵向进给向退刀,车出90°台阶镗孔深度的控制可采用在刀杆上做记号的方法(图5-44)。孔深度的测量可以用游标卡a)b)尺或深度尺。图5-38车小台阶图5-39车大台阶台阶长度可用钢直尺和内卡钳(图5-40)或用深度卡尺测量(图5-41)。刻线记号a)b)c)图5-43车床镗孔图5-44测量孔深a)镗通孔b)镗台阶孔c)镗不通孔图5-40钢直尺和内卡钳确定台阶长度图5-41深度卡尺确定台阶长度四、车锥面三、车床上孔的加工锥面可看成是内、外圆的一种特殊形式,具有配合紧密、拆卸方便、对中性好的特点,车床上孔的加工是指回转体工件中间孔的加工。对非回转体上的孔可利用单动卡盘或花广泛应用于需经常拆卸的配合件上。车锥面的方法主要有宽刀法、刀架转位法、偏移尾座法盘装夹在车床上加工,但更多的是在钻和靠模法。床和镗床上进行加工。1.宽刀法1.钻孔、扩孔和铰孔在车床上钻孔时,工件的回转运动宽刀法就是利用主切削刃横向直接车锥面,如图5-45所示。此时,切削刃的长度要略为主运动,尾座上的套筒推动钻头所做长于圆锥素线长度,切削刃与工件回转中心线成半锥角仪。这种加工方法方便、迅速,能加的纵向移动为进给运动(图5-42)。钻工任意角度的内、外圆锥。车床上倒角实际就是宽刀法车锥面。此种方法加工的锥面很短,孔前应先车端面、用中心钻钻中心孔,图5-42车床上钻孔而且要求切削加工系统有较高的刚性,适用于批量生产。以防钻头偏斜;钻孔时需加切削液,钻2.刀架转位法深孔时应经常退出,以利于排屑和冷却钻头。钻孔一般用于孔的粗加工,加工精度可达车床中拖板上的转盘可以转动任意角度,松开上面的紧固螺钉,使小拖板转过半锥角IT11~IT12,表面粗糙度Ra值为12.5~50μm。a,如图5-46所示,将螺钉拧紧后,转动小拖板手柄,沿斜向进给,便可以车锥面。这种方82法操作简单方便,能保证一定的加工精度,能加工各种锥度的内、外锥面,应用广泛。但受83工程实训指导书(金工实习)和主后面的摩擦,但过大的后角也会削弱切削刃强度。因此后角一般为6°-12°,精加工第五章车削选较大值,粗加工时选较小值。(3)主偏角x,在基面内,测量主切削刃和进给运动方向的夹角。主偏角减小,切合金刀头用碳化硅砂轮(绿色)。刃强度增加,切削条件得到改善,但车削时背向力会增大。加工细长杆件时为避免工件的形和振动,应选较大的主偏角。车刀常用的主偏角有45°、60°、75°、90°等。(4)副偏角在基面内,测量副切削刃和进给运动相反方向的夹角。其作用是减副切削刃和已加工表面之间的摩擦,以改善加工表面的表面粗糙度。一般副偏角'为5°-15°。(5)刃倾角A,在主切削面内,测量切削刃和基面之间的夹角。其作用是控制切屑的流向,并影响刀头强度。刃倾角A,一般为-5°~5°。粗加工时选负值,精加工时选正或零值b)0图5-33车刀的刃磨三、车刀的安装a)磨前面b)磨主后面c)磨副后面d)磨刀尖圆弧车刀应正确地装夹在车床刀架上,这样才能保证刀具有合理的几何角度(图5-32),从而提高车削的质量。2)刃磨时,人要站在砂轮的侧面,双手要拿稳车刀,用力要均匀,倾斜角度要合适;装夹车刀应注意下列事项:要在砂轮圆周表面中间部位磨,并左右移动。3)磨高速工具钢车刀时,刀头发热,应放入水中冷却,以免刀具因温升过高而软化。高度。1)车刀的刀尖应与车床主轴轴线等高。装夹时可根据尾座顶尖的高度来确定刀尖4)磨硬质合金车刀时,刀头发热,可将刀柄置于水中冷却;切忌将硬质合金刀头直接2)车刀刀杆应与车床轴线垂直,否则将改变主偏角和副偏角的大小。沾水,以免刀头因急冷而产生裂纹或极大的内应力。3)车刀刀体悬伸长度一般不超过刀杆厚度的两倍,否则刀具刚性下降,车削时容易产5)车刀刃磨后,应加机油并在油石上细磨各刀面,以提高其使用寿命和加工质量。生振动。第四节车削安全生产规程4)垫刀片要平整,并与刀架对齐。垫刀片一般使用2~3片,太多会降低刀杆与刀架的接触刚度。5)车刀装好后应检查在工件的加工极限位置时是否产生运动干涉或碰撞。1)进入车间,穿好工作服、工作鞋,扎好袖口,戴好护眼镜;女生戴好工作帽,头发罩在工作帽内;不准穿拖鞋、凉鞋、高跟鞋;严禁戴手套操作。2)实习学生应在指定车床上进行操作,不得随意开动其他车床;如果两人同开一台车刀尖与工件床,只能其中一人操作,另外一人在安全区域做准备。轴线不等高3)设备操作前,应检查开关、手柄是否在规定位置,润滑油路是否畅通,防护装置是否完好。车刀伸4)变速、测量、换刀和装夹工件时必须停机。出过长5)卡盘上的扳手在松开或夹紧工件后应立即取下,以免开机时飞出伤人。垫刀片放置a)不平整6)机床运转时,严禁用手触摸机床的旋转部位。严禁隔着车床传递物件。b7)车削时的切削速度、背吃刀量和进给量都应选择适当,不得任意加大。图5-32车刀的安装a)正确b)错误8)测量工件时,将变速手柄转到空档位置或将急停开关按下以防误操作而转动主轴。9)切削时,手、头部和身体其他部位都不要与工件及刀具靠得太近;人站立位置应偏四、车刀的刃磨离切屑飞出方向;切屑应用钩子清除,不得用手拉。10)转动刀架时要将床鞍或中滑板移到安全位置,防止刀具和卡盘、工件、尾座相碰。车刀通过刃磨(整体和焊接式车刀)才能保持合理的几何角度和良好的切削性能。车刀的刃磨是在砂轮上进行的,主要磨三个刀面和刀尖圆弧(图5-33)。刃磨时应注意下列事项:11)操作中,发现机床有异常现象时应立即停机,并及时向指导教师汇报。1)刃磨高速工具钢车刀或硬质合金车刀的刀体部分用氧化铝砂轮(白色);刃磨硬12)正确使用和爱护量具,经常保持量具清洁,用后及时擦净并放入盒内。禁止将工78具、刀具和工件放在车床的导轨上。应严格按照刀具刃磨安全操作规程。工程实训指导书(金工实习)多,常用的有锥度心轴、圆柱心轴和可胀心轴等。第五章车削当工件长度大于孔径时,常用锥度1:1000-1:5000的锥度心轴(图5-20)。工件压后靠摩擦力与心轴夹紧。锥度心轴装卸方便、对中准确,但不能承受较大的切削力和加工五、其他车床直径的外圆,一般用于精加工盘、套类零件。当工件长度小于孔径时,常用圆柱心轴(图5-21)。工件左端紧靠心轴轴肩,右端用1.立式车床母及垫圈压紧。圆柱心轴夹紧力大,可一次装夹多个盘形零件,但对中性差,且对工件的立式车床的结构如图5-25所示,分单柱式和双柱式两种。立式车床结构的主要特点是主轴竖直布置,直径很大的圆工作台水平布置,工件的安装找正都比较方便。此外,由于工个端面与孔的垂直度要求高。件及工作台的重力由床身导轨推力轴承承担,减小了主轴负载,因而能长期保证车床的加工工件精度。立式车床结构上的另一个特点是不但在立柱上装有侧刀架,而且在横梁上还装有垂直刀心轴架,两个刀架可分别切削或同时切削,工作效率高。工件螺母立式车床适用于加工径向尺寸大,轴向尺寸相对较小的大型、重型工件,如机架、盘等轴工件。2.转塔车床卧式车床加工范围广,适应性强,但在专业化生产中效率较低。为提高成批生产过程中垫圈的工作效率,在卧式车床的基础上又设计制造出了转塔车床,如图5-26所示。转塔车床的最大结构特点是没有丝杠和尾座,只能靠丝锥、板牙加工螺纹。转塔车床除有一个横向刀架图5-20锥度心轴图5-21圆柱心轴外,还有一个可绕竖直轴旋转的转塔刀架,转塔刀架只能纵向移动,用来完成车外圆、钻孔、扩孔、铰孔和攻螺纹、套螺纹等加工。可胀心轴(图5-22)是利用锥面的轴向移主轴工件动使弹性心轴胀开而夹紧工件的。它既定心又夹紧,装夹效率高,夹紧力比锥度心轴大,但对中性比锥度心轴低。6.花盘在车床上加工大而形状不规则的零件,可3用花盘装夹,如图5-23所示。采用花盘装夹镗孔和车端面时,有利于保证定位平面与加工面图5-22可胀心轴的垂直度和平行度。8率8有些复杂的零件装夹在角铁上,再将角铁压在花盘上。如图5-24所示的轴承座的装8④8方式。用花盘装夹工件,找正比较费时,还应安装平衡铁来减小转动时产生的振动。垫铁压板图5-25立式车床图5-26转塔车床花盘一螺钉一平衡铁1一底座2-圆工作台3-立柱4-垂直刀架1一进给箱2-主轴箱3一方刀架4一转塔刀架螺钉槽5一横梁6一垂直刀架进给箱5一纵向溜板6一定程装置7一床身7一侧刀架8一侧刀架进给箱8一转塔刀架溜板箱9一方刀架溜板箱工件螺钉槽工件安装基面平衡铁角铁第三节车刀图5-23花盘图5-24花盘、角铁装夹工件车刀是切削加工中最基本的切削刀具,其他种类的刀具就其切削部分而言,均可看成是7475工程实训指导书(金工实习)第五章轮等传至主轴产生的;后者称为进给运动,是由主轴经齿轮等传至光杠或丝杠,从而带动车削具移动而产生的。进给运动又分为纵向进给(纵走刀)和横向进给(横走刀)两种。纵10033221702617r/min=27.6r/min(各传动比均取最小值)进给是指车刀沿主轴轴向移动,横向进给是指车刀沿主轴径向移动。nmin=1440×16045561906458机床常用的传动形式有带传动、齿轮传动、蜗杆传动、齿轮齿条传动及丝杠螺母传动主轴的反转是由电动机的反转实现的。图5-4所示为C6136卧式车床的传动系统框图。2.进给运动传动系统进给运动传动系统是指从主轴到刀架之间的传动。C6136卧式车床的进给运动传动路带传动主轴箱主轴卡盘工件做旋转运动线为子52交换齿换向机构30553548变速箱丝杠溜板箱滑板刀架车螺纹355529甲丙3M一(主轴)I区56乙Xr一XI5536进给箱(换向齿轮)5521目。24电动机光杠溜板箱滑板刀架车刀做纵、横向进给2724]图5-4C6136卧式车床的传动系统框图1.主运动传动系统3952主运动传动系统是指从电动机到主轴之间的传动,其作用是使主轴带动工件旋转,并满3926265239238足主轴变速和换向的要求。图5-5所示为C6136卧式车床的主运动传动系统框图。C6136卧光杠XW离合器一横进给丝杠一横向进给39457-XM4747的式车床的变速箱可输出6种转速,经带轮传给主轴箱,再经主轴箱内变速机构的高、低速变5226一Ⅷ3926392425丝杠XV-离合器X一齿轮齿条一纵向进给换,主轴可获得27.6~1350r/min的12种转速。C6136卧式车床的主运动传动路线为3952396055337452626电动机1004626265252中17026-Ⅱ1716032Ⅲ64在进给运动的传动中,可根据各传动路线上不同的传动比计算出进给量和螺纹螺距。对190-(主轴)38内齿轮离合器于给定的一组交换齿轮,光杠或丝杠可获20种不同的转速,通过溜板箱就能使车刀获得2040种不同的进给量或加工出20种不同螺距的螺纹。带传动主轴箱主轴卡盘四、车床附件及其工件的装夹工件做旋转运动车床主要用于加工回转面,安装工件时应使被加工表面的回转中心和车床主轴的轴线重变速箱合,以保证工件加工时在机床上或夹具中在正确的位置,即定位。工件定位后,还需夹紧,以承受切削力、重力、离心力等。装夹方法主要取决于工件的尺寸结构。常用的附件有:自定心卡盘、单动卡盘、顶尖、中心架、跟刀架、心轴、花盘及压板等。电动机1.自定心卡盘图5-5C6136卧式车床的主运动传动系统框图自定心卡盘是车床上最常用的附件之一。其构造如图5-6所示。当扳手插入卡盘体内三个小锥齿轮的方孔中转动时,可使与其啮合的大锥齿轮转动。大锥齿轮背面的平面螺纹就使主轴转速可根据电动机的转速和不同的传动比计算。主轴最高、最低转速为:1004642170得三个卡爪同时做向心或离心移动,以实现工件的夹紧或松开。nmax=1440×x1r/min=1350r/min(各传动比均取最大值)1603236190自定心卡盘能自动定心、装夹方便迅速,但定心精度不高(一般为0.05-0.15mm),夹紧力较小。装夹直径较小的外圆表面用正爪进行,装夹直径较大的外圆表面,用反爪换到68卡盘上即可进行(图5-7)。工件上同轴度要求较高的表面,应尽可能在一次装夹中车出。69工程实训指导书(金工实习)1)提高熔敷效率,如焊条电弧焊中的铁粉焊、重力焊、躺焊以及埋弧焊中的多丝地焊、热丝焊等。2)减小坡口角度及熔敷金属,如以气体保护电弧焊为基础,采用单丝、双丝或三经行焊接的窄间隙焊等。第五章焊接机器人是从事焊接(包括切割与喷涂)的工业机器人。根据国际标准化组(IS0),工业机器人属于标准焊接机器人的定义,工业机器人是一种多用途的、可重复编的自动控制操作机(Manipulator),具有三个或更多可编程的轴,用于工业自动化领域。车削接机器人在现代焊接生产中的大量应用,是焊接自动化的进步。它突破了焊接刚性自动化传统方式,开拓了一种柔性自动化的新方式,实现了小批量产品焊接自动化,为焊接柔性产线提供了技术基础。第一节概述复习思考题车削是指在车床上利用工件的旋转和刀具的移动,从工件表面切除多余材料,使其成为1.熔焊、压焊及钎焊的区别是什么?符合一定形状、尺寸和表面质量要求的零件的一种切削加工方法,是机械加工中最基本、最2.什么是焊接电弧?电弧区的温度是如何分布的?何谓正接?何谓反接?常用的一种工艺方法。3.常用电焊机有哪几种?说明实习中使用电焊机的种类。车削时,工件的旋转运动为主运动,车刀相对工件的移动为进给运动。切削用量为切削4.焊条的组成及其作用是什么?说明E4303和E5015焊条牌号的含义。速度v(m/s)、进给量f(mm/r)和切削深度a。(mm)。切削速度是指工件加工表面上最5.常见焊接接头及坡口的形式有哪些?焊接位置有哪几种?大直径处的线速度;进给量是指工件旋转一周,车刀沿进给运动方向移动的距离;切削深度6.焊接参数是什么?如何选择?是指车刀每次切去金属层的厚度。7.常见焊接缺陷有哪些?车床是既可以用车刀对工件进行车削,又可用钻头、扩孔钻、铰刀、丝锥、板牙、滚花8.气焊火焰有哪几种?低碳钢、铸铁、黄铜各用哪种火焰进行焊接?刀等对工件进行加工的机床。可加工的表面有内外圆柱面、圆锥面、成形面、端面和各种内9.金属材料要具备哪些条件才能气割?外螺纹面等。车削的应用范围较广,可加工各种回转面及平面等(图5-1)。其加工精度可10.叙述埋弧焊、气体保护电弧焊、等离子弧焊、电阻焊和钎焊的特点及用途。n0c)g)h)i)j)k))m)n)图5-1车削的加工范围a)车端面b)车外圆c)车外锥面d)切槽、切断e)镗孔f)切内槽g)钻中心孔h)钻孔i)铰孔j)孔k)车外螺纹1)车内螺纹m)攻螺纹n)车成形面o)滚花6465◆工程实训指导书(金工实习)第五章达IT1-IT6;表面粗糙度Ra值为1.6~12.5μm。车削第二节车床1.床身床身是用来支承各主要部件,并按技术要求把各个部件连接在一起,使其在工作时保持准确的相对位置,是机床的基础件。床身上的导轨用以引导刀架和尾座相对于主轴箱进行准车床是各种机械加工设备中应用最广泛的机床之一,约占金属切削机床总数的一半。车确移动。床身结构的紧固性和精度对车床的加工精度有很大影响。床的种类很多,按用途和结构的不同,可分为卧式车床、转塔车床、立式车床、单轴自动车2.主轴箱床、多轴自动和半自动车床、仿形车床、专门化车床等。其中卧式车床应用最广。主轴箱内装空心主轴和主轴变速机构。动力经变速机构传给主轴,主轴箱的变速手柄可以改变主轴箱内齿轮的啮合关系,使主轴按规定的速度带动工件旋转,实现主运动。一、车床的型号3.进给箱车床型号是按GB/T15375-2008《金属切削机床型号编制方法》规定,由汉语拼音进给箱内装进给运动的变速机构,主轴的旋转运动通过齿轮传人进给箱,经过变速机构带动光杠或丝杠以不同的转速转动,最终通过溜板箱而带动刀具移动,实现进给运动,并可母和阿拉伯数字组成的。型号的具体含义如下:以获得所需要的进给量或车削螺纹的螺距。(A)(Q)(x)(O)/()4.光杠和丝杠其他特性代号光杠和丝杠将进给箱的运动传给溜板箱。自动走刀用光杠,车削螺纹用丝杠,光杠和丝重大改进顺序号杠不能同时使用。主轴数或第二主参数5.溜板箱主参数或设计顺序号系代号溜板箱与大拖板连在一起。它将光杠或丝杠传来的旋转运动通过齿轮-齿条机构(或丝组代号杠副)带动刀架上的刀具做直线横向或纵向进给运动。丝杠运动时,可实现车螺纹。通用特性、结构特性代号6.刀架类代号分类代号刀架用来装夹车刀,有4个装刀装置,以便转位换刀。使其做横向、纵向及斜向运动,由大拖板、中拖板、小拖板、转盘和方刀架组成(图5-3)。车工实习中常见的车床型号为CA6136,其中C是“车”字汉语拼音的首字母,代表大拖板(纵溜板、大刀架)与溜板箱连接,床类型为车床,读作“车”;A在此处为结构特性代号,是为了区分主参数相同而机构不可带动车刀沿床身导轨做纵向移动;中拖板的机床,可以理解为这种型号的车床在结构上区别于C6136型车床;6为组代号,表示落(横溜板、横刀架)可沿大拖板上的导轨做横向及卧式车床;1为系代号,表示卧式车床;36为主参数代号,表示最大车削直径的1/1移动;转盘与中拖板用螺栓紧固,松开螺母,可即最大车削直径为360mm。使其在水平面内转动任意角度;小拖板(小溜板、小刀架)可沿转盘上的导轨做短距离纵向二、车床的组成进给或在转动转盘后做斜向进给。卧式车床的主要组成如图5-2所示。7.尾座尾座套筒内可以安装顶尖用来支承较长工图5-3刀架的组成件,也可以安装钻头、铰刀、中心钻等。尾座套筒在尾架体壳的伸出长度可以用手柄转动调节,并由锁紧手柄将套筒固定,也可以将套筒退到末端,可卸下套筒锥孔内所安装的工具或刀具。调节尾座底侧面的螺钉,尾座体在尾架底板上还可以横向移动,用来车削圆锥。8.床脚床脚用地脚螺栓固定在水泥地基上,其左端安装电动机和变速机构,右端安装着电气控制箱和冷却泵。0三、车床的传动系统图5-2卧式车床的主要组成车床的运动分为工件旋转和刀具移动两种运动。前者为主运动,是由电动机经带轮和齿6667◆工程实训指导书(金工实习)第四章的熔点必须低于该金属本身的熔点,同时流动性要好,这样的氧化物能以液体状态从切口处焊接点焊时,先加压使焊件紧密接触,随后接通电流,在电阻热的作用下焊件接触处熔化,3)金属在切割氧射流中燃烧属于放热反应,使所放出的热量足以维持切割过程继续进被吹除。冷却后形成焊点。点焊主要用于厚度4mm以下的薄板构件、冲压件焊接,特别适合汽车车身和车厢、飞机机身的焊接;但不能焊接有密封要求的容器。4)金属的导热性不应太高,否则预热火焰及气割过程中氧化所析出的热量会被传导散行而不中断。6.缝焊失,使气割不能开始或中途停止。缝焊过程与点焊相似,只是用滚轮电极代替熔化电极。焊接时,转动的滚轮电极压紧并气割的特点是设备简单、操作灵活方便、生产率高、适应性强,可在任意位置和任意方带动焊件向前移动,配合断续通电,形成连续重叠的焊点(图4-23)。缝焊的焊缝具有良好的密封性。向切割任意形状和任意厚度的工件。2.等离子弧切割夹紧力等离子弧切割是利用等离子弧的热能实现切割的方法。气体可以是空气,也可以是复气、氩气和氮气的混合气体。高频电弧使一些气体“分解”或离子化,成为基本的原子粒滚轮电极压力O子,从而产生等离子。然后,电弧跳跃到工件焊件钨极上,高压气体把等离子从割嘴吹出,出口速度Ar或N2开关焊点U重叠焊点为800~1000m/s。这样,结合等离子中的各高频振荡冷却水O种气体恢复到正常状态时所释放的高能量产生直流电源。器冷却水熔化电极2700℃的高温(该温度几乎是不锈钢熔点的两倍),从而使不锈钢快速熔化,熔化的金属喷嘴图4-22点焊图4-23缝焊由喷出的高压气流吹走。因此,需要用排烟和等离子弧缝焊主要用于焊接厚度3mm以下、要求密封性的容器和管道等,如汽车的油箱、消声除渣设备。等离子弧是电弧经机械、热和电磁器等。工件压缩效应后形成的(图4-21)。7.钎焊等离子弧切割的特点是高速、高效、高质图4-21等离子弧发生装置钎焊是指低于焊件熔点的钎料和焊件同时加热到钎料熔化温度后,利用液态钎料填充接量,切口光滑,切割厚度可达150~200mm。头间隙使金属连接的焊接方法。钎焊时,首先要去除母材接触面上的氧化膜和油污,以利于其主要用于切割合金钢、不锈钢、铸铁、铜、铝、镍、钛及其合金、难熔金属和非金属。毛细管在钎料熔化后发挥作用,增加钎料的润湿性和毛细流动性。根据钎料熔点的不同,钎3.激光切割焊又分为硬钎焊和软钎焊。激光切割是利用高功率密度激光束照射被切割材料,使材料很快被加热至汽化温度,蒸钎焊的焊接过程是:焊前准备(除油、机械清理)→装配零件、填放钎料→加热、钎料发形成孔洞,随着光束对材料的移动,孔洞连续形成宽度很窄的(0.1mm左右)切口,完熔化→冷却、形成接头→焊后清理→检验。成对材料的切割。目前主要有激光升华切割、激光熔化切割和激光燃烧切割三种方法。激光钎焊的加热方法有:烙铁、火焰、电阻、感应、盐浴、红外、激光、气相(凝聚)加切割适用于易氧简单、直径小于20mm和强度要求不高的焊件,也可用于棒材、管材和板材热等。的焊接。因为没有刀具加工成本,所以激光切割设备适用于生产小批量的各种尺寸的部件钎焊的焊接温度低、焊接应力和变形小、尺寸精度高,可焊接异种金属,易于实现机械激光切割设备通常采用数控装置。采用该装置后,即可从计算机辅助设计(CAD)工作站化和自动化,但接头强度较低、耐热性差,多用搭接接头。其主要用于焊接微电子元件、精接收切割数据。密仪器、真空器件、异种金属构件及某些复杂的薄板结构等。4.闪光对焊(三)特种焊接闪光对焊的焊接过程是:通电一闪光加热→顶锻、断电→去压。闪光加热是焊件端面逐1.摩擦焊渐移近达到局部接触时,接触点金属迅速熔化,以火花形式飞溅,形成闪光。多次闪光加热摩擦焊是指利用焊件接触面摩擦产生的热量为热源,使焊件在压力作用下产生塑性变形后,焊件端面就均匀达到半熔化状态,然后断电加压顶锻,形成了焊接接头。该接头质量较而进行焊接的方法(图4-24)。其特点是接头质量好,生产率高,易实现自动化,适用于碳高、强度好,但接头表面粗糙,主要用于棒料、型材等的焊接,也可用于异种金属的对接。素钢、高速工具钢、不锈钢、低合金高强度结构钢、镍合金的焊接,尤其是异种材料间的焊5.点焊接,如碳素钢一不锈钢、铝一铜、铝一钢、铝一陶瓷等,如石油钻杆、圆柄刀具等。点焊是指焊接时利用熔化电极,在焊件接触面之间形成焊点的焊接方法(图4-22)。焊2.超声波焊点距不应太小,以减少分流的影响,且与焊件材料和厚度有关。超声波焊是指利用超声波频率(20kHz以上)的机械振动能量连接金属的一种特殊焊6061工程实训指导书(金工实习)模锻可分为锤上模锻和压力机模锻。锤上模锻第三章是在蒸汽一空气模锻锤上进行的,常用的模锻压力楔铁锤头锻压机有曲柄压力机、摩擦螺旋压力机、平锻机和液压模膛上模压力机(图3-28)是曲柄压力机的一种,可完分模面飞边槽机等。成除剪切外的绝大多数基本工序,是冲压生产的基带轮模锻与自由锻相比,生产的锻件形状更为复杂,离合器楔铁下模本设备。冲压时冲模的凸模(或冲头)装在滑块的轴尺寸精度较高,表面粗糙度值小,且力学性能较高;紧固楔铁模垫下端,凹模装在工作台上,压力机的曲柄连杆机构制动器锻件加工余量和锻造公差小,材料利用率高;生产将旋转运动转变成滑块的上、下往复运动,实现冲过程操作简便,劳动强度小,易于实现自动化,生压。压力机主要技术参数有额定压力、滑块行程距连杆产率高。但模锻的设备投资大;生产准备周期,尤离(mm)、滑块行程次数(次/min)和封闭高电动机其是锻模的设计制造周期长,费用高;锻模成本高;度等。0图3-26锻模(二)冲压的基本工序床身工艺灵活性差,适用于中小锻件的大批量生产。胶带导轨冲压的基本工序主要有分离工序(落料和冲滑块三、板料成形孔)和变形工序(弯曲和拉深)。工作台1.落料和冲孔利用冲压设备和冲模使金属或非金属板料产生分离或变形的压力加工方法称为冲压,也称为板料成形。这种加工方法通常是在常温下进行的,所以又称冷冲。板料成形的原材料是具有较高落料和冲孔是使坯料分离的工序,又称为冲裁工序。从板料上冲下所需形状的零件(或毛坯)为踏板塑性的金属材料,如低碳钢、铜及其合金、镁合金等。还可以加工某些非金属(如石棉板、硬落料,即冲下部分为成品,剩下周边部分为废料;胶、胶木板、皮革等)的板材、带材或其他型材。用于加工的板料厚度一般小于6mm。而冲孔则相反,它是在板料上冲出所需形状的孔,冲压的特点是可冲出形状复杂的零件,材料利用率高;冲压件表面质量高,强度高,刚即冲下部分为废料,剩余周边部分为成品,如图图3-28压力机性好;操作简单,生产率高,易于实现机械化和自动化;冲模精度要求高,结构复杂,制造3-29所示。成本大等,因此冲压常适用于大批量生产场合。落料和冲孔所用的模具称为冲裁模,其凸、凹模刃口必须锋利且应有很小的冲裁间隙(一)冲压设备(单边间隙为材料厚度的5%~10%)。冲压生产常用的设备是剪板机和压力机。2.弯曲和拉深剪板机是将板料切成一定宽度的条料,是冲压生产的备料设备。剪板机(图3-27)的弯曲是使板料的一部分相对于另一部分弯成一定角度的冲压变形工序(图3-30)。弯曲传动原理为:电动机带动带轮、齿轮转动,经离合器带动曲轴转动,使装在滑块上的上刀刃件有最小弯曲半径的限制,凹模的工作部位必须有圆角过渡,以免拉伤工件。弯曲主要应用沿导轨做上、下运动,并与固定在工作台上的下刀刃配合,进行剪切。制动器的作用是使上于制造各种弯曲形状的冲压件。弯曲模的凸模端部和凹模边缘应做成一定的圆角,以防止工件外表面被弯裂或划伤;凹模的角度应略小于工件的角度。刀刃剪切后停在最高位置上,为下次剪切做准备,挡铁用来控制下料尺寸。为了减小剪切力,剪切宽度大的板材用斜刃剪切,当剪切窄而厚的板材时,应选用平刃剪切。剪板机的规格是以剪切板料的厚度和宽度来表示的。例如Q11-2×1000型剪板机,表示废料冲头工件能剪切厚度为2mm、长度为1000mm的板料。制动器带轮齿轮工件废料曲轴下模电动机离合器(凹模)安滑块0导轨滑块图3-29落料与冲孔图3-30弯曲0上刀刃挡铁上刀刃a)落料b)冲孔板料下刀刃板料工作台下刀刃拉深是将板料冲成开口的中空形状零件的冲压变形工序(图3-31)。拉深模的凸模端部工作台和边缘除应带有圆角外,凸、凹模之间还应留有一定(略大于板料厚度)的间隙;拉深过图3-27剪板机程中为了防止起皱,要用压边圈将板料压紧,凹模和凸模必须有圆角过渡。4445第一章金工实习的基本知识第二节工程材料(如齿轮、轴、螺栓等)。这类钢属于低碳钢(碳的质量分数小于0.25%)和中碳钢(碳的质量分数为0.25%~0.6%)、常用的牌号有Q215、Q235和40、45钢。材料是人类一切生产活动和生活活动的物质基础,是人类发展和进步的标志。在当今社2)碳素工具钢主要用于制造各种刀具、模具、量具等。这类钢属于高碳钢(碳的质量会,材料、能源和信息已成为现代科学技术的三大支柱。分数大于0.6%)。常用的牌号有T8、T10、T10A和T12等。工程材料是指制造工程结构和机器零件使用的材料的总称。工程材料可分为金属材料、3)合金结构钢主要用于制造承受载荷较大或截面尺寸大的重要机械零件。常用的有低非金属材料和复合材料。合金结构钢(Q345、Q390)、调质钢(40Cr、35CrMo)、弹簧钢(65Mn、60Si2Mn)和滚动轴承钢(GCr15、GCr15SiMn)等。一、金属材料4)合金工具钢主要用于制造各种刀具、模具、量具等。常用的有量具刃具钢(9SiCr)、金属材料是现代制造中应用最广泛的工程材料,特别是钢铁材料的应用更为广泛。模具钢(Cr12、Cr12MoV、5CrMnMo)。5)特殊性能钢具有特殊的物理性能、化学性能,用于制造有特殊性能要求的零件。常1.金属材料的性能金属材料的性能分为使用性能和工艺性能。使用性能是指金属材料制成的零件或产品在用的有不锈钢(12Cr18Ni9、20Cr13)、耐热钢(15CrMo、42Cr9Si2)等。6)灰铸铁广泛用于制造各种承受压力和要求消振性好的床身、底座、箱体等。常用的使用过程中所表现出来的性能。它包括物理性能、化学性能和力学性能等。工艺性能是指金牌号有HT150、HT200、HT300等。属材料在加工过程中所表现出的性能。7)球墨铸铁可代替碳素结构钢用于制造一些载荷较大、受力复杂的重要零件,如曲金属材料的物理、化学性能主要有密度、熔点、热膨胀性、导热性、导电性、导磁性、轴、连杆、齿轮等。常用的牌号有QT400-18、QT500-7、QT600-3、QT800-2等。耐酸性、耐碱性、抗氧化性等。它与零件或产品的用途密切相关,对制造工艺也有影响。金属材料的力学性能是指金属材料在外载荷作用下所表现出来的性能,主要有强度、塑二、非金属材料性、刚度、硬度、韧性和疲劳强度等,它们是表征和判断金属材料力学性能所用的指标和依非金属材料包括金属材料以外的几乎所有材料,工程上常用的有塑料、合成橡胶和陶瓷据,称为金属材料的力学性能判据。材料等。(1)强度强度是指金属材料抵抗永久变形(塑性变形)和断裂的能力。1.塑料(2)塑性塑性是指金属材料断裂前发生的不可逆的永久变形的能力。塑料以高分子合成树脂为主要成分,经过热加工和加压制成。塑料具有密度小、比强度(3)硬度硬度是机械制造现场经常使用的力学性能指标,用它可大致评价其他力学高、化学性能稳定、摩擦系数小、耐磨性好、绝缘性能好、消声吸振性好、加工简单、生产性能指标,且操作简单、成本低、不破坏产品零件。硬度值常用布氏硬度HBW和洛氏硬度率高等优点。HRC表示。2.橡胶(4)韧性韧性是指金属材料在断裂前吸收变形能量的能力。橡胶是以生胶为主要原材料,加入适当的硫化剂、软化剂等辅助材料制成的材料。主要金属材料的工艺性能一般包括铸造性能、可锻性、焊接性、可加工性和热处理性能等。优点有弹性好、撕裂强度好、耐疲劳、不透水、不透气、绝缘等。它决定着金属材料的加工制造工艺方法、设备工装、生产率及成本效益,甚至会影响产品零3.陶瓷材料件的设计。陶瓷材料是无机非金属材料,目前常用的制造工艺是粉末冶金法。陶瓷在机械工业中主(1)铸造性能铸造性能是指金属及合金在铸造生产中表现出来的工艺性能,如流动要用于制造有耐高温、耐磨、耐蚀等性能要求的零件,如内燃机火花塞、发动机的叶片、切性、收缩性、偏析性、透气性等。削高硬度材料的刃具等,也可用作绝缘材料、半导体材料和压电材料。(2)可锻性可锻性是指用锻压成形方法获得合格锻件的难易程度。三、复合材料(3)焊接性焊接性是指金属材料对焊接加工的适应性,也就是在一定的焊接工艺条件下,获得优质焊接接头的难易程度。复合材料是指由两种或两种以上不同物质以不同方式组合而成的材料,材料复合后,可(4)可加工性可加工性是指切削加工金属材料的难易程度。改善和克服单一材料的缺点,充分发挥其优点,并能得到单一材料难以达到的性能和功能。(5)热处理性能热处理性能是指金属材料通过热处理后反映出来的能力。2.常用的钢铁材料第三节钢的热处理钢和铸铁是以铁、碳为主要成分的合金,又称铁碳合金。碳的质量分数小于或等于2.11%的铁碳含金称为钢;碳的质量分数大于2.11%的铁碳合金称为铸铁。在毛坯制造和加工之前通常都会对材料进行热处理,热处理是将钢在固态下通过加热、)碳素结构钢主要用于制造各种工程构件(如桥梁、船舶、建筑用钢)和机械零件保温后以一定方式进行冷却,使其组织改变而获得所需性能的工艺方法。热处理是改善材料23工程实训指导书(金工实习)第一章金工实习的基本知识工艺性能、提高材料的强度、硬度,改善其塑性、韧性等性能,保证产品质量,挖掘材料潜力不可缺少的工艺方法。重要的机械零件在制造过程中一般都要经过热处理。化学热处理是通过改变钢的表面化学成分和组织而获得所需性能的表面热处理。化学热热处理的工艺方法很多,可分为普通热处理和表面热处理两大类。处理的种类很多,主要有渗碳、渗氮、碳氮共渗等,其中以渗碳应用最广。渗碳工艺可使工件具有外硬内韧的性能,主要用于承受强烈摩擦又承受冲击或交变载荷的工件,如拖拉机的变速齿轮、活塞销、凸轮、履带等。一、普通热处理除表面热处理外,还有电镀、发蓝处理和喷塑等表面处理也可以改善材料的相关性能。钢的普通热处理工艺中,最基本的是退火、正火、淬火与回火,如图1-2所示。热处理常用的加热设备是箱式电阻炉、井式电阻炉和盐浴炉;冷却设备有搅拌水槽、搅1.退火保温拌油槽、循环冷却液槽和盐浴槽等。加热炉的温度测控是通过热电偶、控温仪表系统和计算退火是将工件加热到适当温度,保持一临界点机温控系统实现的。目前计算机与自动控制技术在热处理及检测设备中的大量应用,不仅使定时间,然后随炉缓慢冷却的热处理工艺。加热冷单台设备和单一工序的热处理实现了计算机控制自动化生产,还形成了多道复杂的热处理工却其目的是降低硬度、细化组织、消除内应力序、辅助工序及检测工序和多台设备集成的计算机集成热处理生产线,为各种金属材料提供和某些铸锻焊的热加工缺陷,为后续切削加时间了多种改性手段,满足了不同机械产品对零件性能的要求。工和热处理做工艺准备。图1-2热处理工艺示意图2.正火1一退火2—正火3淬火4—回火第四节切削加工基本知识正火是将工件加热奥氏体化后在空气中或其他介质中冷却获得以珠光体组织为主的热处理工艺。其目的是细化组织、消除组织缺陷和切削加工是使用切削刀具将毛坯或工件上多余的材料层切除,以获得所要求的几何形内应力,为后续切削加工和热处理做工艺准备。正火后可得到比退火时较高的强度和硬度,且状、尺寸精度和表面质量的加工方法。切削加工可分为机械加工(简称机加工)和钳工两生产率高、成本低,因此正火也可作为一些使用性能要求不高的中碳钢零件的最终热处理。大类。机械加工是通过操纵机床来完成的切削加工,主要加工方法有车、钻、刨、铣、磨及齿3.淬火与回火淬火是将工件加热奥氏体化后以适当方式冷却获得马氏体或(和)贝氏体组织的热处轮加工等,所用机床相应为车床、钻床、刨床、铣床、磨床及齿轮加工机床等。它具有精度理工艺。其目的是提高材料的硬度和耐磨性。但淬火钢内应力大、脆性高、易变形和开裂,高、生产率高、劳动强度低等优点。通常切削加工主要是指机械加工。必须进行回火。回火是将工件淬硬后加热到Ac1以下的某一温度,保温一定时间,然后冷却钳工是通过手持工具来进行的装配、维修或切削加工,常用的加工方法有划线、錾、到室温的热处理工艺。按回火温度不同,可分为低温回火、中温回火和高温回火。工件经高锯、锉、刮研、钻孔、攻螺纹和套螺纹等。为减轻劳动强度和提高生产率,钳工中的某些工温回火处理又称调质,经调质后的钢具有良好的力学性能,广泛地用于重要机械零件的热作已逐步被机械加工代替,实现了机械化处理。一、切削运动及切削用量工件常用的回火方法见表1-1。1.切削运动表1-1工件常用的回火方法切削运动是指在切削加工过程中,刀具和工件之间的相对运动。它是实现切削过程的必回火方法回火温度/℃硬度HRC力学性能特点应用举例要条件之一,分为主运动和进给运动。低温回火250以下58-64高硬度、高耐磨性刃具、量具、冲模、滚动轴承主运动是形成机床切削速度或消耗主要动力的工作运动,是完成切割的主要运动。在切中温回火250-50035-50高弹性和韧性弹簧、热锻模具削加工中,主运动有且只有一个。高温回火500以上20-30优良的综合力学性能轴、齿轮、螺栓、连杆进给运动是使工件多余的材料不断投入切削的运动。没有进给运动,就无法实现连续切削。在切削加工中,进给运动可以有一个或多个。二、表面热处理切削运动可以是旋转的,也可以是直线的或曲线的;可以是连续的,也可以是间歇的(图1-3)。表面热处理是将钢的表面进行热处理的工艺方法。其目的是使钢的表面层具有较高的硬在切削过程中,工件表面的被切金属层不断地被切削而转变为切屑,从而加工出所需的度和耐磨性,而心部仍保持较高的塑性和韧性。常用的表面热处理工艺有表面淬火和化学热处理。工件表面。切削加工时,工件上有三个不断变化的表面,即待加工表面、切削表面和已加工表面(图1-4)。表面淬火是一种局部淬火方法,目的是获得高硬度、高耐磨性的表层,而心部仍保持原2.切削用量有的良好韧性,常用于机床主轴、齿轮、发动机的曲轴等零件的表面处理。表面淬火所采用切削用量是指切削加工时的切削速度v、进给量f和背吃刀量an。的快速加热方法有电感应、火焰、电接触、激光等。←4
问:2023年锅炉价格/多少钱?

上一篇:高温导热油泵的工作原理
下一篇:横轴搅拌炒锅好用的原因