随着低温制冷技术的不断发展,低温工艺及装备设计制造技术日趋完善,在工业、农业、国防及科研等领域内的作用日益突显,尤其在石油化工
随着低温制冷技术的不断发展,低温工艺及装备设计制造技术日趋完善,在工业、农业、国防及科研等领域内的作用日益突显,尤其在石油化工、煤化工、天然气、空分等大型成套装备技术领域具有重要地位,已广泛应用于大型液化天然气(LNG)、百万吨化肥、百万吨甲醇、大型气体液化分离等重大系统装备技术工艺流程中。
在LNG工业领域,大力发展LNG产业,提高天然气能源在消费中的比例是调整我国能源结构的重要途径。LNG既是天然气远洋运输的唯一方法,又是天然气调峰的重要手段。随着国内众多LNG工厂的相继投产及沿海LNG接收终端的建设,我国LNG工业进入了高速发展时期,与之相关联的LNG低温制冷装备技术也得到快速发展。LNG液化工艺主要包括天然气预处理、液化、储存、运输、接收、再气化等工艺单元,其中,液化工艺为核心工艺流程,主要应用低温制冷工艺技术制取-162℃低温环境并将天然气液化。根据不同的LNG液化工艺,可设计并加工制造不同的制冷装备,主要包括天然气压缩机、制冷剂压缩机、天然气冷箱、BOG压缩机、气液分离器、大型空冷器、LNG膨胀机、四级节流阀及各种过程控制装备等。储运工艺技术中还包括大型LNG储罐、LNG立式储罐、LNG气化器、LNG潜液泵等。近年来,30万立方米以上LNG系统多采用混合制冷剂板翅式主换热装备及液化工艺技术,60万立方米以上大型LNG系统多采用混合制冷剂缠绕管式主换热装备及液化工艺技术,这两种混合制冷剂LNG液化工艺技术具有集约化程度高、制冷效率高、占地面积小及非常便于自动化管理等优势,已成为大型LNG液化工艺装备领域内的标准性主流选择,在世界范围内已广泛应用。目前,国内的大型LNG装备一般随着成套工艺技术整体进口,包括工艺技术包及主设备专利技术使用费等,造价非常昂贵,后期维护及更换设备的费用同样巨大。由于大型LNG系统装备及主设备大多仍未国产化,即还没有成型的设计标准,因此给LNG制冷装备的设计计算带来了难题。
《液化天然气装备设计技术:液化换热卷》主要围绕LNG混合制冷剂液化工艺及换热工艺中所涉及的主要低温装备,研究开发LNG液化工艺流程中核心主液化装备的设计计算技术,主要包括LNG低温液化混合制冷剂多股流缠绕管式主换热装备、LNG低温液化混合制冷剂多股流板翅式主换热装备、天然气进气压缩机及混合制冷剂压缩机用表面蒸发空冷器、LNG开架式气化器等装备的设计计算技术,为LNG液化、LNG储运、LNG接收及LNG气化等关键环节中所涉及主要设备的设计计算提供可参考样例,并推进LNG系列装备及LNG系统工艺技术的标准化及国产化研究开发进程。此外,近年来由于低温液氮洗、低温甲醇洗等系统工艺技术在低温气体液化分离领域内占比越来越大,应用越来越广泛,而这两套工艺系统内最具特色的装备为大型多股流缠绕管式主换热装备,是目前世界上设计计算难度最大的系列主设备之一,尤其低温液氮用多股流缠绕管式换热器,内含扩散制冷工艺技术且有10股以上低温流体同时进行低温多股流、多相流换热过程,设计计算难度极大,在换热领域内,同LNG低温液化混合制冷剂多股流缠绕管式主换热装备并列为设计计算难度最大的换热装备,本书作者通过多年研究开发,已系统掌握这两种主换热装备的设计计算技术,并通过本书一并呈送相关领域同行借鉴参考。
(1)LNG缠绕管式主换热装备
以目前最流行的MCHE型混合制冷剂LNG液化工艺为例,MCHE主换热器为多股流缠绕管式换热器,主要用于100×104m3/d以上大型LNG液化系统,是整个LNG液化工艺流程中的核心设备,可一次性将36℃天然气冷却至-162℃,并液化。由于MCHE主换热器为工艺型换热器,内含液化工艺,有5种以上混合制冷剂分凝预冷并同时制冷,是一种多股流回热型换热器,也是目前换热器中体积最大、缠绕过程最复杂、设计计算难度最大的换热器。MCHE型缠绕管式换热器管内介质以螺旋方式流动,壳程介质逆流横向交叉通过绕管,换热器层与层之间换热管反向缠绕,管、壳程介质以纯逆流方式进行传热,即使在较低的雷诺数下其流动形态也为湍流,换热系数较高,其结构相对紧凑、耐高压且密封可靠、热膨胀可自行补偿,易实现大型LNG液化作业。美国APCI是LNG领域MCHE最大的供货商,在1977~2013年间,生产了120套LNG装置,其液化能力累计达到4.3×108t/a。此外,德国Linde公司在近5年内一共生产了累计金属重量达到3120t的多股流缠绕管式换热器应用于LNG工厂。自2010年以来,由兰州交通大学张周卫等主持研究开发LNG缠绕管式换热器等项目,目前,已出版《缠绕管式换热器》专著一部,开发MCHE专用软件一套,申报发明专利12项,发表论文14篇,涉及12类不同温区的缠绕管式换热器,并系统开发了缠绕管式换热器设计计算方法,可用于设计计算LNG专用系统缠绕管式换热器、低温甲醇洗系列缠绕管式换热器、低温液氮洗系列缠绕管式换热器等各种类型缠绕管式换热器。本书给出了专用于计算MCHE型LNG混合制冷剂用缠绕管式换热器的一个计算事例,供相关行业的同行参考。
(2)LNG板翅式换热器
LNG板翅式换热器主要用于30×104m3/d以上大型LNG液化系统,是该系统中的核心设备,一般达到60×104m3/d以上时,采用并联两套的模块化办法,实现LNG系统的大型化。基于板翅式换热器的LNG液化工艺也是目前非常流行的中小型LNG液化系统的主液化工艺。从2013年开始,由兰州交通大学张周卫等开始研究开发大型LNG混合制冷剂用多股流板翅式换热器,并前后开发了LNG混合制冷剂板翅式换热器、LNG一级三股流板翅式换热器、LNG二级四股流板翅式换热器、LNG三级五股流板翅式换热器等系列LNG板翅式换热器,申报发明专利4项。本文根据项目开发情况,给出了LNG混合制冷剂多股流板翅式换热器设计计算模型,供相关行业的同行参考。
(3)表面蒸发空冷器
表面蒸发空冷器常用于天然气压缩机、混合制冷剂压缩机等出口高温气体的冷却过程,其利用管外水膜的蒸发过程进一步强化管外传热过程,从而达到空冷的效果。基本工作原理是用泵将设备下部水池中的循环冷却水输送到位于水平放置的光管管束上方的喷淋水分配器,由分配器将冷却水向下喷淋到传热管表面,使管外表面形成连续均匀的薄水膜;同时用风机将空气从设备下部空气入口吸入,使空气自下而上流动,横掠水平放置的光管管束。此时传热管的管外换热除依靠水膜与空气流间的显热传递外,管外表面水膜的迅速蒸发吸收了大量的热量,强化了管外传热。由于水具有较高的汽化潜热(1atm时为2386kJ/kg),因此管外表面水膜的蒸发大大强化了管外传热,使设备总体传热效率明显提高。本书根据表面蒸发空冷器强化换热原理,给出了一种表面蒸发空冷器的设计计算方法,仅供参考。
(4)LNG开架式气化器
LNG开架式气化器是用海水作为热媒将液态LNG气化为气体。开架式气化器结构简单,外部接口有LNG入口、气化后的LNG出口以及海水进出口、换热管安装在框架结构内。气化器的基本单元是传热管,由若干传热管组成板状排列,两端与集气管或集液管焊接形成一个管束板,再由若干个管束板组成气化器。LNG从下部总管进入,然后分配到每个小的换热管内,在换热管束内由下向上流动。气化器顶部装有海水分布装置,海水由顶部进入,经分布器分配成薄膜状均匀沿管束外壁下降,同时将热量传递给管内液化天然气,使其加热并气化。本书根据LNG开架式气化器工作原理,给出了一种LNG开架式气化器的设计计算方法,仅供参考。
(5)低温液氮洗用多股流缠绕管式换热器
与LNG缠绕管式换热器设计相关联的低温液氮洗用多股流缠绕管式换热器主要应用于液氮洗工艺,主换热工艺流程主要包括三个阶段,由三个不同换热温区的换热器组成,其中,第一个阶段是将压缩后的高压氮气进行预冷,将42℃高压氮气预冷至-63.6℃;第二个阶段是将高压氮气及低温甲醇工艺来的净化气从-63.6℃冷却至-127.2℃,为低温液化做准备;第三个阶段是将-127.2℃高压氮气冷却至-188℃并液化及将-127.2℃净化气冷却至-188.2℃,三个过程连续运行并连接成为一个整体式低温液氮回热换热装备。本书给出了低温液氮洗用多股流缠绕管式换热器设计计算模型,供相关行业的同行参考。
本书共分6章,第1章、第2章、第3章由张周卫、郭舜之负责撰写并编辑整理,第4章、第5章、第6章由汪雅红、赵丽负责撰写并编辑整理;全书最后由张周卫统稿。
本书受国家自然科学基金(编号:51666008)、甘肃省财政厅基本科研业务费(编号:214137)、甘肃省自然科学基金(编号:1208RJZA234)等支持,在此表示感谢!
本书按照目前所列装备设计计算开发进度,重点针对5项装备进行研究开发,总结设计计算方法,并与相关行业内的研究人员共同分享。由于水平有限、时间有限及其他原因,本书难免存在不足之处,希望同行及广大读者批评指正。
兰州交通大学
张周卫 郭舜之 汪雅红 赵丽
2017年12月1日
第1章 绪论
液化天然气(LNG)是将天然气冷却至-162℃并液化后得到的液态天然气,常压下储存,经远洋运输至LNG接收站,再气化打入天然气管网,或在LNG陆基工厂将陆地开采的天然气直接液化,经LNG槽车运输至接收站,再气化后打入天然气管网,供城镇居民或工业燃气使用。LNG作为继石油、煤炭、天然气之后的第四类新能源,来源于天然气并成为当今世界能源消耗中的重要部分,是天然气经脱水、脱硫、脱CO2之后的无色透明低温液体,其体积约为气态天然气体积的1/630,重量仅为同体积水的45%左右,通常储存在-162℃、0.1MPa左右的低温储存罐内。天然气由甲烷、乙烷、丙烷及其他杂质气体等主要成分构成,不同产地的天然气所含气体成分不同,所用的LNG液化工艺及装备依据产量及成分不同而有较大差别。
1.1 LNG应用领域
LNG是天然气脱除杂质并液化后的产物,作为燃料主要应用于城镇燃气、工业燃料、燃气发电及LNG汽车等领域。由于LNG为低温液体,具有自增压功效,在常温常压下直接将LNG打入自增压容器,并将自增压容器连入管网后,在天然气应用高峰期起到管网增压调峰的作用。
(1)城镇燃气
LNG是一种非常理想的清洁燃料,燃烧后的产物几乎没有环境污染。近年来,随着国家能源结构的不断调整,LNG作为替代煤炭、石油等的主要能源,已广泛应用于城镇燃气等领域。LNG燃烧后产生的二氧化碳和氮氧化合物仅为煤的50%和20%,污染为液化石油气的1/4,煤的1/800。LNG作为管道天然气的调峰气源,可对城市燃气系统进行调峰,保证城市天然气管网安全平稳供气。LNG自增压调峰装置已广泛用于天然气输配系统中,并对民用和工业用气的波动性进行调峰,尤其针对冬季采暖用气调峰具有非常重要的作用。
(2)LNG发电
LNG具有燃烧清洁的特性,已经成为全球新建电厂的主要能源。与煤电相比,LNG发电具有污染少、运行灵活、占地小、消耗低、投资省等优势。日本一直是世界上LNG进口最多的国家,其LNG进口量的75%以上用于发电,用作城市燃气的占20%~23%。韩国也是LNG进口大国,其电力工业是韩国天然气公司的最大客户,所消费的LNG占该国LNG进口总量的50%以上。
(3)工业燃料
应用以LNG作为工业燃料燃气系统,可有效替代燃煤、燃油锅炉等供热设备,节约除尘、脱硫、脱氮等工艺成本,有利于环境保护,提高产品质量、减轻劳动强度,为企业带来良好的经济、社会和环境效益。LNG可应用于造纸、冶金、陶瓷、玻璃等能源消耗较大的行业,上述行业企业往往距离城市或天然气管线较远,或者根本无法连接管道天然气时,使用LNG的优势更加明显。
(4)化工原料
LNG也是一种优质的化工原料。以LNG为原料的一次加工产品主要有合成氨、甲醇、炭黑等近20种,经二次或三次加工后的重要化工产品则包括甲醛、乙酸、碳酸二甲酯等50种以上。与用其他原料相比,以LNG为原料的化工产品装置投资省、能耗低、占地少、人员少、环保性好、运营成本低。
(5)LNG汽车
LNG汽车燃烧排出的一氧化碳、氮氧化物与烃类化合物水平都大大低于汽油、柴油发动机汽车,排放过程不积炭、不磨损,而且具有续驶里程长、燃烧效率高等特点,运营费用很低,是一种环保型汽车,目前国内外都在大力发展LNG汽车。
(6)LNG冷能利用
-162℃低温LNG在1atm(1atm=101325Pa)时转变为常温气态的过程中可提供大量的冷能。LNG在常温下约有836J/kg的冷能,将这些冷能回收,还可以用于多种低温用途上,如使空气分离而制造液态氧、液态氮;液化二氧化碳并制取干冰;制造冷冻食品或为冷冻仓库提供冷量等。
1.2 LNG工厂国内外发展现状
LNG液化装置具有投资费用大、配套要求严格、操作条件特殊(如操作压力从高压到低压,操作温度由环境温度到-162℃等)的特点。LNG液化装置按其生产性质一般分为基本负荷型、调峰型、终站型和卫星站型四种。基本负荷型是指所生产的LNG主要供远离气源的用户使用或出口外运的大型液化装置;调峰型主要建在远离天然气气源的地区,用于液化管输来的天然气;终站型接收站用于接收油轮从基地型LNG生产厂运来的LNG,在站内加以储存和气化后分配给用户;LNG卫星站是一种小型的LNG接收和气化站,用于接收从LNG终端接收站或液化装置用专用汽车槽车来的LNG。
1.2.1 国外发展及现状
世界上第一个基本负荷型LNG生产厂于1964年建于阿尔及利亚,之后一批新的基本负荷型LNG生产厂在亚洲、非洲、大洋洲、北美洲等地相继建成。世界上LNG调峰型生产装置约有70多个,美国和加拿大有50多个,欧洲和澳大利亚10多个,这些调峰型装置可储存1.7×106t的LNG,能液化13.2×106m3/d的天然气,能气化13.2×106m3/d的天然气。经过40多年的发展,LNG接收站已遍及日本各地和英国、法国、意大利、西班牙、韩国等国家,世界现有40多个LNG接收站,日本拥有最多,多达30个,美国包括在建的终端站有17个。欧美各国和俄罗斯是通过建全国天然气管网而实现全国城镇燃气化的,而日本基本上是用LNG接收站加LNG卫星站实现全国城镇燃气天然气化的。采用LNG卫星站供应天然气的城镇比例在日本已达20%左右,美国在20世纪80年代初约有22个卫星调峰装置。
1.2.2 国内发展及现状
为了推动能源结构变革,改善生态环境、发展经济,近十年来,中国LNG产业开始迅速发展。目前中国已建成运营的LNG工厂有50多座,总液化能力2300×104m3/d,正在建设或调试的有60多座,全部建成后年产能可达208×108m3/d。2001年,我国第一座10×104m3/d小型天然气液化装置—中原LNG工厂在中原油田试运行成功,虽然规模不大,但标志着我国在生产LNG方面迈开了关键的一步。之后,2004年新疆广汇50×106m3/d LNG工厂建成投产,以及2008年宁夏哈纳斯200×104m3/d LNG工厂的建设等项目,标志着我国大规模工业生产LNG的开始,并对国家“西气东输”主干管网以外的广阔市场进行供气。国内LNG工厂大多建在西北及华北地区,其中,西北地区目前已建成LNG工厂13座,产能1110×104m3/d;华北地区目前已建成LNG工厂22座,产能745×104m3/d;华东地区目前已建成LNG工厂3座,产能29×104m3/d;西南地区目前已建成LNG工厂8座,产能272×104m3/d;华南地区目前已建成LNG工厂3座,产能100×104m3/d;东北地区目前已建成LNG工厂3座,产能52×104m3/d。
2000年始建于上海的LNG事故调峰站是我国第一座调峰型天然气液化装置,生产能力为30×104m3/d,储存能力为2×104m3/d,再气化能力为120m3/d,主要用于东海天然气中上游工程因不可抗拒的因素造成停产、冬季调峰时向管网提供可靠的天然气供应等。上海调峰站的建成,开启了我国LNG城镇燃气调峰之路。近些年来,国内陆续建成30×104m3/d LNG调峰站30多座。我国西北部天然气储量丰富,人口稀少;东南沿海天然气储量较少,人口密集,经济发达,因而较西部有更大的LNG需求,仅依靠“西气东输”显然不能满足东南部发展的需要,还需要大量进口海洋LNG。目前,国内沿东南沿海各个省份已建成投运大型LNG接收站6座,总接收能力2.42 ´107t/a,其中深圳大鹏600万吨/a LNG站是中国第一座投入商业运行的LNG接收站。地处福建、上海、江苏、大连、浙江的5座LNG接收站也相继投产。此外,我国已在青岛等地建有LNG卫星站,我国LNG卫星站设计、建造及陆上运输技术已基本成熟,相关装备可国产化,且价格便宜,具有一定的竞争力。
1.3 LNG产业链
LNG产业链是一条贯穿天然气产业全过程的投资巨大且技术密集的完整产业链条,主要由天然气勘探开采、天然气预处理、LNG液化、LNG储运、LNG接收、LNG再气化等工艺流程链条组成。除了LNG生产链条外,还包括LNG装备制造业产业链,主要包括LNG系列换热器、天然气压缩机、混合制冷剂压缩机、LNG系列储罐、LNG系列低温阀门等。由陆地或海洋开采的天然气在LNG工厂经过预处理后再进行液化,生产的LNG按照国际贸易流程,通过船运或槽车运输到LNG接收站储存,再气化后经天然气管网送至不同用户。从LNG生产流程来讲,整个LNG产业链主要包括上、中、下游三个环节(图1-1)。
(1)LNG上游产业链
上游产业链主要包括天然气勘探、开发、净化、分离、液化等几个环节。其中,天然气液化是LNG产业链上游中的关键环节。液化的主要作用是持续不断地把原料气液化成为LNG,其主要步骤包括:①预处理工艺,即从天然气原料气中脱水、脱碳、脱硫、脱杂质等;②脱重烃工艺,即脱除天然气中的冷凝温度较高的重烃馏分;③LNG液化工艺,即用深冷剂将原料气冷却并冷凝到-162℃,使其成为液态LNG产品。
(2)LNG中游产业链
中游主要包括LNG储存、装卸、运输、接收等环节,包括LNG储罐和再气化设施及供气主干管网的建设等环节。LNG储存是指LNG被储存在接近1atm的LNG储罐中,最常见的大型LNG储罐有单包容储罐、双包容储罐、全包容储罐等,LNG储罐是LNG液化末端或接收终端的关键设备;LNG运输是指通过LNG槽车或LNG运输船将LNG运送到终端站;LNG接收站是连接终端市场及用户的关键环节。在LNG接收站,LNG通过码头从运输船卸载、储存LNG,然后再气化后变成普通管道气输送至LNG发电厂或通过当地分销网络作为燃料气输送至LNG终端用户。
(3)LNG下游产业链
LNG下游产业链即LNG终端市场用户,主要包括LNG联合循环电站、城市燃气公司、工业锅炉用户、分布式能源站、天然气加气站,以及其他工业燃料或化工原料用户等。另外,可向下延伸至LNG卫星站、LNG加注站及冷能利用等与LNG相关的所有产业。
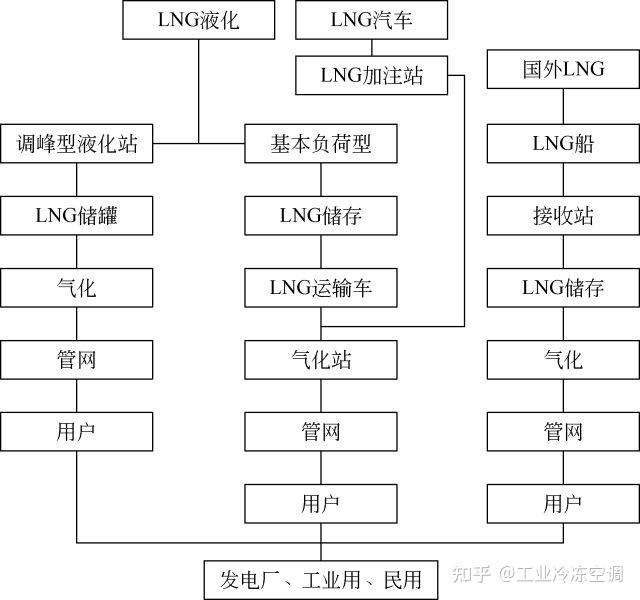
图1-1 LNG产业链示意
1.4 LNG产业链各环节主要工艺概述
1.4.1 LNG净化工艺
预处理前的天然气在进入长输管线时,其中含有有害杂质及深冷过程中可能凝固的物质,如CO2、H2S、H2O、重烃、汞等,这些杂质气体应在天然气液化之前进行工艺分离,以免在冷却过程中冷凝并堵塞管道及产生严重管路腐蚀。一般工艺流程中,首先,应脱除重烃,然后用醇胺法除去CO2和H2S;其次,用分子筛吸附天然气中的H2O;接着,用脱氧工艺脱除天然气中的O2;最后,在需要的情况下脱汞。
天然气脱水工艺方法主要有变压吸附法,一般采用两个分子筛干燥塔切换吸附与再生流程,交替吸附及脱吸过程,从而达到连续脱除的目的。固体干燥剂种类很多,还可采用氯化钙、硅胶、活性炭、分子筛等。吸附法脱水工艺流程如图1-2所示。
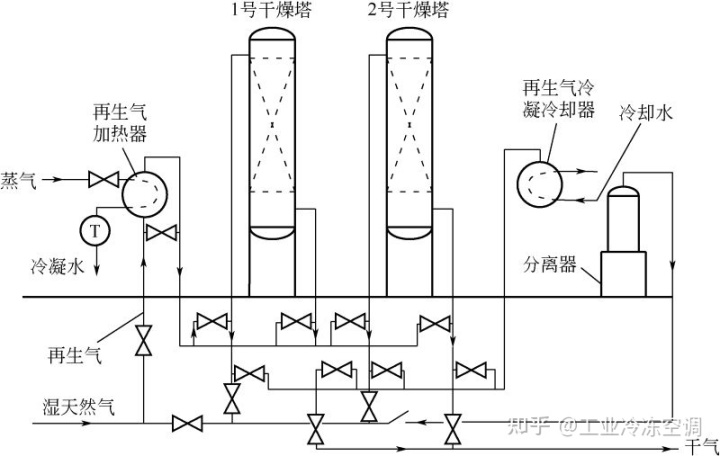
图1-2 吸附法天然气脱水典型工艺流程示意
在天然气预处理过程中,脱除酸性气体CO2、H2S、COS等过程常称为脱硫脱碳过程。常用的脱硫方法有醇胺法、热钾碱法、砜胺法等,其中,醇胺法是利用以胺为溶剂的水溶液,以乙醇胺、二乙醇胺为溶剂,与原料天然气中的酸性气体发生化学反应来脱除酸性气体,其工艺流程见图1-3。
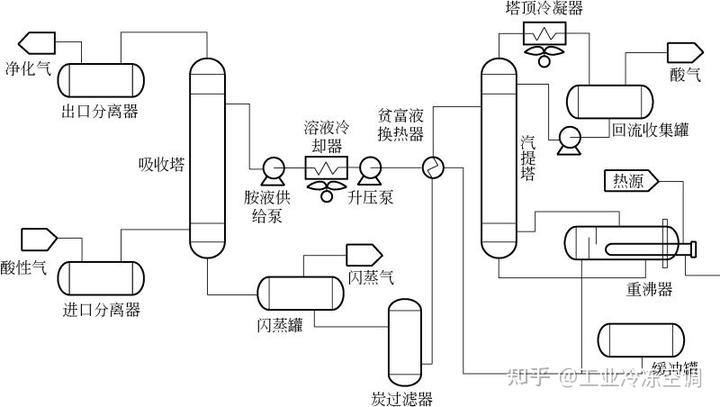
图1-3 醇胺法脱硫装置的典型工艺流程
当汞存在于铝制设备时,铝会与水反应生成白色粉末状的腐蚀产物,严重破坏铝制设备,而且汞还会造成环境污染等危害,所以汞的含量应受到严格的限制,脱除汞的方法是汞与硫在催化反应器中反应。重烃是指C5以上的烃类,在烃类中,分子量由小到大时,其沸点是由低到高变化的,所以在冷凝天然气的循环中,重烃总是先被冷凝,如果未把重烃先分离掉,或在冷凝后分离掉,则重烃将可能冻结从而堵塞设备。重烃在脱水时被分子筛等吸附剂部分脱除,其余的采用深冷分离。天然气是氦的最主要来源,应加以分离利用。采用膜分离和深冷分离相结合的方式脱除,有很高的利用价值。氮气的含量增加会使天然气液化更困难,一般采用最终闪蒸法从LNG中选择性脱除。
1.4.2 LNG液化工艺
由于天然气临界温度较低,在常温下不能用压缩的方法使其液化,只有在低温深冷下才能使其变为液体,即原料天然气经净化预处理后,进入换热器进行低温冷冻循环,并冷却至-162℃液化。液化是LNG生产的核心,目前成熟的天然气液化工艺有级联式液化工艺、混合制冷剂液化工艺、带膨胀机的液化工艺等。近年来,大型LNG系统大多采用以混合制冷剂多股流缠绕管式主换热装备作为主液化装备的MCHE型液化流程,主要应用于60×104m3/d以上大型液化系统。30×104m3/d以上大型液化系统一般采用混合制冷剂多股流板翅式主换热装备作为主液化设备。
(1)级联式液化流程
级联式天然气液化工艺(图1-4)是利用低温制冷剂常压下沸点不同,逐级降低制冷温度达到天然气液化目的,一般采用三级制冷,液化流程中各级所用制冷剂分别为丙烷(大气压下沸点-42.3℃)、乙烯(大气压下沸点-104℃)、甲烷(大气压下沸点-162℃),每个制冷循环设置三个换热器。该液化流程由三级独立的制冷循环组成,第一级丙烷制冷循环为天然气、乙烯和甲烷提供冷量;第二级乙烯制冷循环为天然气和甲烷提供冷量;第三级甲烷制冷循环为天然气提供冷量。
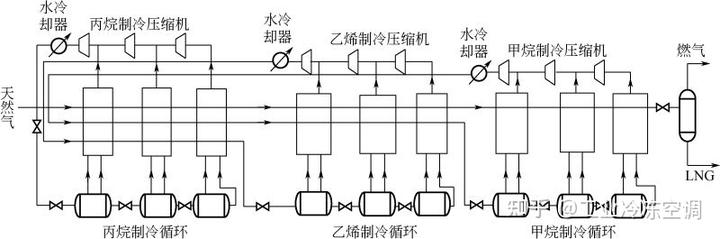
图1-4 级联式天然气液化工艺流程
(2)混合制冷剂液化流程
混合制冷剂制冷循环(MRC)是以C1~C5的烃类化合物及氮气等组分的混合制冷剂为工质,进行逐级冷凝、蒸发、节流制冷,从而得到不同温区的制冷量,使天然气逐步冷却直至液化。混合制冷剂由氮、甲烷、乙烷、丙烷、丁烷、戊烷及氮气等组成。
混合制冷剂液化流程主要分为闭式混合制冷剂液化流程(图1-5)、开式混合制冷剂液化流程(图1-6)、丙烷预冷混合制冷剂液化流程(图1-7)、MCHE型混合制冷剂液化流程(图1-8)等多种流程。在闭式液化流程中,制冷循环与天然气液化过程分开并形成独立封闭的制冷循环;在开式液化流程中,天然气既是制冷剂又是需要液化的对象;丙烷预冷液化流程由混合制冷剂循环、丙烷预冷循环、天然气液化回路三部分组成,其中丙烷预冷循环用于混合制冷剂和天然气,混合制冷循环用于深冷和液化天然气;MCHE型混合制冷剂液化流程中,混合制冷剂制冷循环为封闭循环,主液化设备只有一台多股流缠绕管式主换热器(MCHE),天然气从主液化设备MCHE底部进入,从顶部出来时已液化为LNG。MCHE型混合制冷剂液化天然气流程是目前世界范围内最流行的大型LNG液化工艺流程,具有经济节能、能效比高、便于管理、占地面积小等优点。
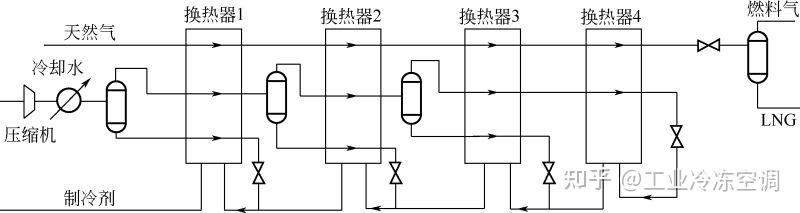
图1-5 闭式混合制冷剂液化流程
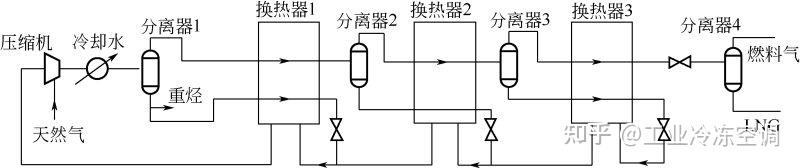
图1-6 开式混合制冷剂液化流程
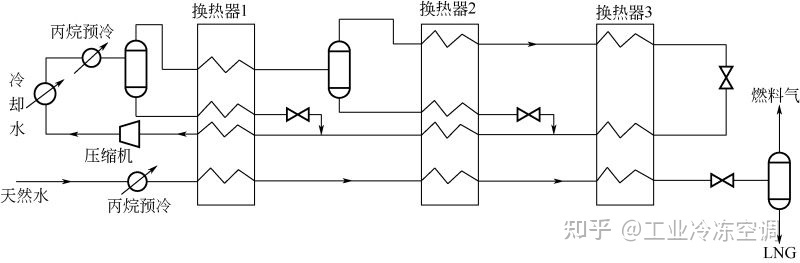
图1-7 丙烷预冷混合制冷剂液化流程
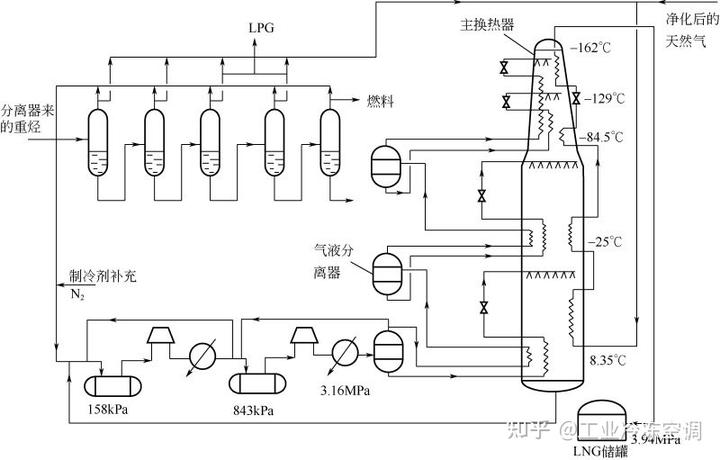
图1-8 MCHE型混合制冷剂液化工艺流程
(3)带膨胀机的液化工艺
带膨胀机液化是利用高压制冷剂通过透平膨胀机绝热膨胀的克劳特循环制冷并实现天然气液化的目的。气体在膨胀机中膨胀降温的同时,能够输出功,可用于驱动流程中的压缩机。带膨胀机的液化流程分为氮气膨胀液化流程(图1-9)、天然气膨胀液化流程(图1-10)、氮-甲烷膨胀液化流程等。
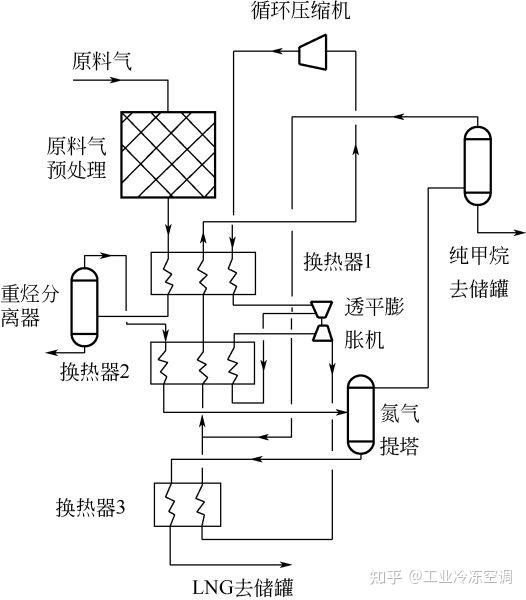
图1-9 氮气膨胀液化流程
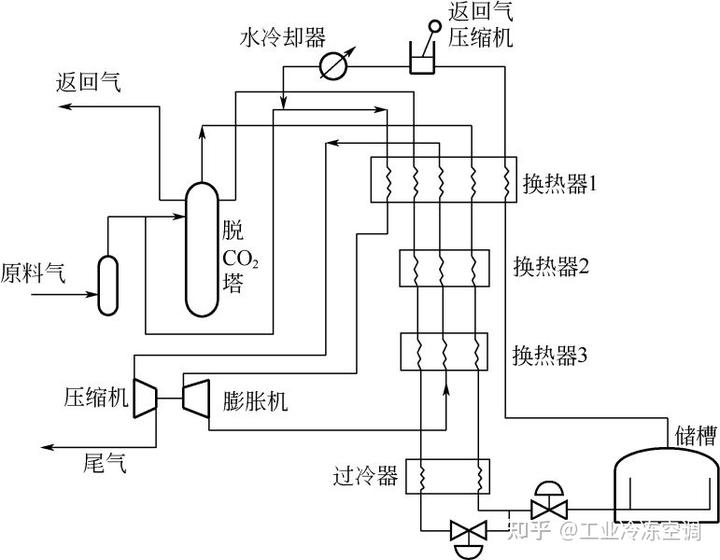
图1-10 天然气膨胀液化流程
1.4.3 LNG接收站工艺
LNG接收站主要由数十个大型LNG全包容式储罐、LNG码头、LNG卸料臂等组成,是一项投资十分巨大、上下游各环节联系十分紧密的系
....
问:2023年锅炉价格/多少钱?
