1 电站锅炉行业基本状况为适应电力建设发展和满足大型电站机组生产需要,我国自“六五”计划开始就引进美国C-E公司300MW、600MW锅
1 电站锅炉行业基本状况
为适应电力建设发展和满足大型电站机组生产需要,我国自“六五”计划开始就引进美国C-E公司300MW、600MW锅炉全部设计和制造技术,并成功地试制出国内首台600MW考核机组,为我国大型火电机组的制造奠定了基础。
“七五”、“八五”期间,锅炉行业所属主导企业以蛇形管和水冷壁为重点,率先引进了国外先进焊接设备和技术,如直管对接MIG焊、热丝机械TIG焊和管屏角焊缝脉冲MAG焊设备等,填补了国内该领域的空白。
目前,以TIG/MIG熔化焊为主的蛇形管生产线,已在国内各锅炉压力容器行业得到了广泛的应用。“七五”期间吸收引进了膜式壁管屏生产线,即双生法埋弧焊和一次成型MAG焊,为锅炉水冷壁产品达到世界水平打下坚实的基础。
到目前为止,我国锅炉行业已相继为国内和国外生产电站锅炉300MW级200余台,600MW级约10余台,主导企业电站锅炉年生产能力均达到和超过3000MW/年,最大为4500MW/年,这对我国西部大开发和西电东送发展战略提供了极其有利的发电设备条件。
2 压力容器行业基本状况
国内各主要压力容器制造厂,通过“七五”、“八五”、“九五”几个五年计划的改造,在焊接生产能力方面都得到了极大的提高。这种发展大致可以分为两个阶段。
第一阶段在“七五”期间,各容器厂纷纷进行焊接设备的更新改造,引进了一大批国外先进的焊接设备,如窄间隙焊机、多功能氩弧焊机、小口径管内壁堆焊机等。金州重型机械厂将容器车间近70%的焊接设备更新为进口设备;兰石厂一次就引进了30台埋弧焊机。
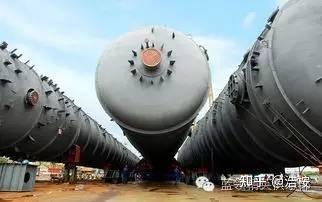
这种批量地引进国外设备,不但极大地增强了焊接实力,更主要的是随着先进设备的引进,先进的焊接工艺技术也在国内得到了广泛地推广应用,为压力容器焊接技术水平上一个新台阶奠定了坚实的基础,使我国压力容器行业的焊接机械化水平达到60%以上。
第二阶段以“八五”、“九五”期间为重点,为了容器大型化和国产化的需要,各厂分别以自己的主导产品为目标,有针对性的增加焊接生产能力,如上海锅炉厂有限公司为制造重量达560T的大型加氢反应器,增加了一批先进焊接设备;兰石厂经过改造后,焊接实力大大加强,自80年代末生产出国产化第一台高压螺纹锁紧式换热器以来,已生产了近50台同类产品。
以美国UOP专利技术著称,焊接、制造、安装难度极大的四合一连续重整反应器,近十年来该厂已生产了6台,完全替代了进口。中国第一重型机械集团公司近十年来,相继生产出了一批大直径、大壁厚、大吨位的锻焊式热壁加氢反应器,最大壁厚达281mm,单台总重近1000T;南京化工机械厂为30万吨/年合成氨和52万吨/年尿素装置制造出了核心设备—氨合成塔和尿素合成塔,并生产了直径达7m的大型卧式贮罐。
这些不但标志着我国压力容器制造行业焊接技术发展的突飞猛进,同时也使各类压力容器的国产化水平进一步提高,为中国加入WTO后,压力容器制造业进一步打进国际市场做好了充分准备。
在国际上,以日本和欧洲为代表,在压力容器焊接方面,主要以容器大型化为目标,开发相关的技术,特别是一些新材料、新钢种的焊接技术得到越来越广泛的应用,同时在提高焊接质量方面,无论从工艺设备上和焊接材料的研制方面,都取得了长足的进展。而这些新材料、新技术的出现,正在不断地被国内各有关企业加以引进,这无疑会更加促进我国压力容器焊接技术的进一步发展。
3 大型受压部件焊接工艺与装备
3.1 水冷壁焊接趋向大型化和多头化
膜式水冷壁管屏实际上是锅炉炉墙的主要受压部件,为降低产品成本,现代化大型锅炉的膜式水冷壁管屏均采用光管加扁钢焊接而成。而且从保证密封和传热的目的考虑,必须采用双面焊接,将光管和扁钢用连续焊缝拼接方法达到成品宽度的管屏。
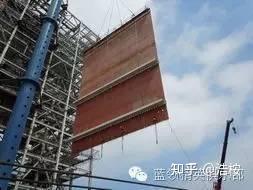
一台300MW电站锅炉膜式水冷壁部件管屏总面积约4000平方米、焊缝总长度达27万米。因此不采用高效率的专用成套设备是很难完成上述生产任务的。以德国BABCOCK公司开发的膜式水冷壁系列专用成套埋弧自动焊装置,采用“双生法”技术,最早用于生产。
其中KOMESMA800型和1600型焊接设备能通过最大管屏宽度为800mm和1600mm的单元膜式水冷壁管屏。该设备属于固定框架式焊接工作站,机床具有钢管和扁钢定位、夹紧、送进、焊接和焊剂自动回收等功能,一般都装有四个或八个焊头同时完成水平位置四条或八条角焊缝的焊接。此技术操作简单,对管子和扁钢表面要求不高。
上海锅炉厂有限公司和武汉锅炉集团公司等单位从德国引进了KOMESMA800型、1600型、P3200膜式水冷壁专用成套设备,取得了较好的应用效果和经济效益。
膜式壁光管加扁钢结构生产是一种高精度自动焊接系统,制造质量尤其是管屏加工精度不仅影响厂内组装焊接,而且也影响工地安装。为此,日本三菱重工在八十年代初开发和研制了一种气体保护焊膜式水冷壁管屏自动焊机,在出口模块式锅炉水冷壁生产上得到成功应用。
该种管屏焊机采用新型脉冲电源,提供了最佳熔滴过渡和十分稳定的焊接过程,获得了理想的焊接效果和满意的焊缝质量--无飞溅、无缺陷、接头致密、成型美观、补焊量极小(不到1‰);
利用气体保护焊可远距离送丝,焊枪体积小和脉冲电弧全位置技术,可随意进行上下、前后和分焊枪群对称布置焊枪,根据设备能力和生产需要选择和确定每台设备的焊枪头数,一般4头、8头焊接专用机用于管屏组装,12头、20头(最多日本三菱重工近几年开发的44头设备,利用率可达最大,焊接生产效率最高)焊接专用机用于管屏单元件焊接,设备机械部分的加工精度相当高,装配质量精确,管子扁钢分别定位,互不影响。
在每群焊枪前方设有上下对称双驱动U型滚轮,压紧和移动管子。滚轮的压紧力可根据管子的直径和壁厚进行调整。扁钢对中装置采用耐磨导向滑块定位和滚轮托动,根据管子外径调整中心位置。
管子节距采用轴套粗调和垫片精调,保证装配间隙符合节距要求,工艺上采用全对称焊接方式即焊接程序、焊接热输入量及焊接结构等上下焊枪同时焊接一次成型,无需校正,使焊接变形最小,管屏几何尺寸精度较高。
1988年,哈尔滨锅炉厂有限责任公司和东方锅炉(集团)股份公司相继从日本三菱重工引进此类膜式水冷壁管屏双面MAG焊专用成套装置,单元管屏专用焊机规格为1600mm屏宽×12头,成品管屏专用机规格为3200mm屏宽×4焊头。
这两套专用焊机的投产,使两厂膜式水冷壁生产能力翻了一番,取得了显著的经济效益,同时标志着我国膜式水冷壁焊接技术跃居世界最先进行列。这两台MAG管屏自动焊机与抛丸清理机、扁钢校正和精整机、管屏输送辊道、管子扁钢组装机等辅助设备配套,形成了一条膜式壁管屏生产线。
“九五”期间哈尔滨锅炉厂有限责任公司、东方锅炉(集团)股份公司根据需要,通过自主开发和技术改造等措施进行调整,新近增加了不同种类(宽度)的MPM主机,增加了焊接头数。目前哈锅经调整后已拥有五台MPM主机设备,共44头。投产运行两条膜式壁生产线,一条为窄扁钢,一条为宽扁钢。
在气体供应方面,选用日本大型气体配比装置,具有容量1.2立方米配比精度±3%。半自动焊及MPM设备焊接用保护气体全部采用管道输送方式,具有气体流畅、安全和使用方便等特点。MPM设备焊接用气体保护焊丝,为进口250kg筒装层绕镀铜焊丝,即提高了焊材利用率,又减少了焊缝接头。
至此,该厂的水冷壁生产完全实现了大型化和机械化,技术装备达到国际一流水平,而且气体保护焊方法已成为水冷壁制造中不可缺少的主导工艺,应用率达到80%以上。东锅通过改造,使水冷壁的焊接能力显著增加,管屏焊接头数已超过30头,这标志着气体保护焊工艺的应用范围已经逐渐扩大,
在水冷壁生产中很有发展前途,许多工业锅炉制造厂已全部采用国内生产的MPM设备和制造技术,扩大了气体保护焊的应用领域。近几年来,通过生产实践,已经掌握了MPM设备和MAG技术,积累了许多成功经验。
3.2 蛇形管焊接质量稳定工艺灵活
蛇形管是锅炉的心脏,管子部件不仅材料复杂、规格多、焊接量大,而且是工作温度最高、材质级别最高的受压元件。近年来,随着大型机组生产任务不断增加,焊口数量及管子壁厚成倍增加,蛇行管制造尤其是厚壁管的直管接长焊已成为影响锅炉受热面生产能力的关键,促使开发了各种新型高效自动焊接工艺。
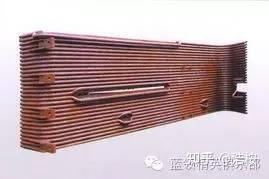
其中MIG焊技术是美国C-E公司的成功经验,国内在亚临界锅炉生产中最先应用并引进了全套焊接设备即MIG/MAG直管对接自动焊接装置。
MIG/MAG焊是一种高电流密度的焊接方法,可获得较高的熔敷效率和较高的焊接速度,可以以不同的熔滴过渡形式进行焊接,采用细丝、脉冲电弧、射流过渡可实现管子单面焊双面成型并达到无飞溅的稳定焊接过程,MIG焊工艺对焊接设备的要求很高,尤其是引弧性能,设备应具有脉冲频率自动优化,焊接程序设定和各层焊接参数设定(最多六层)等功能,以此保证焊缝质量达到理想状态。
目前,TIG/MIG自动焊接系统已成为锅炉蛇行管生产的关键工艺,得到了国内同行业的普遍应用。新型的TIG/MIG管子接长专用焊接设备,采用现代实用性PLC程控器,能对TIG/MIG焊等各层参数进行设定和预置、查询,
首层TIG焊封底参数可分区设定和分角度控制,焊接电流分脉冲和直流两种可任意选择。设备具有快速定位夹紧和对中功能及焊接过程自动程序控制,各锅炉制造厂已引进多台此类专用设备安装在生产线上。
具有相当于MIG焊熔敷效率的热丝TIG焊在中厚壁合金钢管焊接中应用日益广泛,与冷丝TIG焊相比可提高效率3-4倍。传统的钨极氩弧焊(GTAW),由于其保护效果好,焊缝金属纯净,焊接质量好,焊接过程稳定,易于实现单面焊双面成形等优点,被广泛用于航空航天、原子能、化工、纺织、锅炉、压力容器等领域。
但是,电极的载流能力有限,电弧功率受到限制,焊缝熔深浅,焊接速度低,只能用于焊接厚度较薄的工件。为此开发了一种新方法──自动热丝钨极氩弧焊。它的填充金属可借肋于电阻热熔化,不受电弧热影响,电弧主要用于熔化母材金属,焊丝经加热后送入熔池,形成焊缝。
这样在相同焊接电流下能获得高的熔敷率,从而提高焊接速度。自动热丝钨极氩弧焊的特点:⑴增加钨极氩弧焊的工艺灵活性。焊丝加热到一定温度后送入焊接熔池,可显著地增加钨极氩弧焊的工艺灵活性。
由于电弧功率和送丝速度是分别控制的,焊接规范选择范围较广,允许采用接近于零到任何焊接电流时最大的熔敷速度。⑵具有在较宽熔敷率范围内焊接高质量焊缝的能力。当焊丝接近焊接熔池时,其伸长量部份的电阻热已将焊丝表面的易挥发物去除干净了。
由于焊丝表面的水份、油锈等是造成焊缝中产生气孔的主要原因,因此自动热丝钨极氩弧焊还能有效地消除焊缝中的气孔,从而提高焊接质量。通常情况下,增加送丝速度会加剧气孔产生,但是,对于自动热丝钨极氩弧焊而言,在较宽的焊接范围内,使用同样的焊材却不会出现气孔。
所以说,自动热丝钨极氩弧焊具有在较宽熔敷率范围内焊接高质量焊缝的能力。⑶提高经济效益和生产效率。因为自动热丝钨极氩弧焊焊接电弧的能量主要用于熔化母材,形成熔池。而焊丝靠本身的热丝电源加热,热丝熔化所需能量的85%是由热丝系统提供的,其余部分则由电弧供给。
因此在较低的焊接线能量下,其焊接速度已达到或超过普通的熔化极气体保护焊的水平。焊接过程中,熔池的热输入相对减少,因此,焊接热影响区变窄,这对某些热输入敏感的材料焊接具有较为重要的意义,有利于提高这些材料的接头质量。
在锅炉蛇行管部件中,有些管件必须先弯成U形管,然后再组焊成所要求的形状。在这种情况下必须在管子固定不转的条件下完成全位置焊接。各锅炉厂从国外引进了各种管子全位置TIG自动焊机,为适应不同管径规格,配备了系列焊接机头,并成功地用于生产。
3.3 厚壁集箱生产发生新变化
随着电站锅炉容量的不断增大,集箱的壁厚和直径也逐渐加大,例如亚临界锅炉集箱的壁厚已达到148mm,外径已达914mm,由于集箱数量较多,故焊接工作量并不亚于锅炉汽包筒体,而且材料等级已上升为9Cr1MoV钢(P91)。
集箱壳体上通常有大量与省煤器、过热器和再热器等部件相连接的管座,管座上需要连接的接管长度分别为200mm以下短接管和弯成一定形状的长接管两种规格。
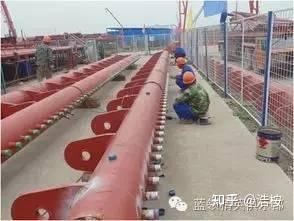
管接头角焊缝在锅炉本体制造中,手工焊接量大,也是产品质量最容易出现问题的环节,因此许多制造厂已将非焊透或局部焊透式管接头(插入式)坡口改变为全焊透式结构,采用自动或半自动气体保护焊或埋弧焊工艺进行焊接,取得了显著的效果,从根本上提高了管接头焊接的内在质量。
例如,短管接头内孔自动脉冲TIG焊封底,外侧手工电弧焊盖面,以及内孔自动脉冲TIG焊封底,外侧细丝埋弧自动焊盖面焊工艺,不仅提高了集箱生产的自动化程度和生产效率,而且焊缝质量优良,生产过程稳定。采用内孔TIG焊封底和外侧自动焊盖面的管接头角焊缝,厂内可以免做水压试验。
对于大口径管接头焊接,哈尔滨锅炉厂有限责任公司通过试验证明,药芯焊丝气体保护焊工艺由于具有熔敷效率高、熔深大、气渣联合保护、工艺稳定、焊接飞溅少、适于全位置、大电流以及连续焊接等特点,完全可以取代传统的药皮焊条手工电弧焊,尤其是在大口径厚壁马鞍形接管角焊缝焊接中,其优点将会更加显露出来。
目前,该工艺方法已正式用于200MW锅炉集箱全焊透结构马鞍形接管的焊接生产中,焊接效率比手工焊高3——4倍,焊缝成型美观,接头少,便于操作,深受工人喜欢,是一种有发展前途的新工艺。
为进一步提高集箱生产能力和制造水平,适应大型机组特殊钢种焊接要求,上海锅炉厂有限公司,哈尔滨锅炉厂有限责任公司相继从日本KKK公司分别引进了三台集箱管接头焊接机器人工作站,采用细丝脉冲电弧自动焊工艺,用来焊接各种材质管接头焊缝,机器人焊接工作站系统具有精确探测测量和自动纠正等功能,可准确测定和纠正管座位置和焊接变形引起的偏差。
该机器人具有六个自由度,能焊接直段长度400mm的管接头,焊缝成型美观、均匀。目前哈尔滨锅炉厂有限责任公司的焊接机器人,经过调试和工艺试验后已用于生产,为机器人的实际应用取得了良好的开端。东方锅炉(集团)股份公司与哈尔滨工业大学联合研制了短管接头焊接机械手,采用光电装置定位,机器人与焊接转胎联动使用。这说明我国锅炉集箱制造水平正在迅速提高,机械化、自动化程度逐渐上升。
4 焊接新工艺、新技术
4.1 厚璧壳体窄间隙埋弧焊技术
随着电站锅炉和石化压力容器的大型化和高参数化,锅炉筒体和压力容器壳体的壁厚不断增加,例如600MW锅炉筒体采用美国钢种SA-299(C-Mn钢)壁厚达到182mm;400T和560T热壁加氢反应器壳体采用2.25Cr-1Mo钢,壁厚分别达到200和210mm;300MW和600MW核电站压力壳的壁厚达到250——300mm。
从80年代中期,主要锅炉和压力容器厂相继从瑞典伊萨公司和意大利安萨多公司等国外厂家引进了窄间隙埋弧自动焊接技术和成套设备,从此在厚壁高压锅炉和压力容器壳体制造中优先采用窄间隙埋弧焊工艺。
实践证明,窄间隙焊接不但在焊接时间和焊接材料上比普通埋弧焊节省1/3——1/2,而且接头综合力学性能良好,焊接效率高。窄间隙埋弧自动焊作为一种优质、高效、低消耗的焊接技术在厚板焊接方面日趋成熟。
该方法的最大优点是:最小焊缝金属填充量和自动分道(每层两道)焊技术,可获得性能优良、致密性高的焊缝接头;采用带有侧壁光电跟踪和自动防偏的焊接转胎,能提供最佳焊接操作和产品焊接质量的可重复性,因此该方法在大型锅炉和容器产品生产中越来越广泛地得以应用。
窄间隙埋弧焊工艺的应用,为压制筒体提供了加工条件。在300MW、600MW等亚临界锅炉设计上,工业发达国家均采用锅筒上、下两部分不等厚结构,从而达到了合理使用钢材、节约原材料、减轻机组重量和降低制造成本的目的。
我国从600MW锅炉开始采用了8000吨油压机压制汽包筒体瓦瓣片和窄间隙埋弧自动焊工艺焊接筒体纵缝,实现了厚壁长筒节(单节最大长度7000mm,最大厚度250mm)压制工艺自动化和焊接工艺高效率化,开辟了大型机组制造工艺的新途径。
压制成型方法不仅解决了不等厚筒体的加工困难,而且克服了热卷成形和常规焊接方法(埋弧焊和电渣焊)存在的自身局限性和诸多弊端。例如,热卷筒体需要二次高温正火校圆,表面氧化严重,产生凹坑,影响外观质量,使壁厚减薄;
电渣焊时需要提高焊材强度等级,从而降低了接头性能特别是冲击韧性,而窄间隙埋弧焊焊缝的冲击韧性比常规埋弧焊方法还要高;压制成型工艺对不锈钢复合板加工最适合,可进行中温、低温或冷态压制和校正,而不影响复合板贴合强度及产生表面缺陷,采用窄间隙埋弧焊能够解决电渣焊方法难以实现的焊接难题。
窄间隙埋弧焊接工艺的广泛应用必将促使窄间隙焊接设备朝着实用可靠、系统配套和精度高、功能先进的方向发展。近年来,为满足生产需要,国内自行开发了多种专用纵环缝窄间隙焊机例如纵缝双丝埋弧自动焊机已用于300MW、600MW亚临界锅炉筒体纵缝焊接,可焊接筒体纵缝最大长度7000mm,现已成为压制筒体纵缝焊接的关键设备。
中国第一重型机械集团公司自行研制的龙门式和悬臂式窄间隙埋弧焊装置,在板拼接和筒体纵缝焊接生产中占据重要地位。随着产品结构的不断变化,对焊接设备要求逐渐提高,功能单一的窄间隙焊机尚不能适应特殊结构的焊接要求,如锥体纵缝、封头上接管和法兰环缝的焊接。
因此迫切需要开发新型窄间隙焊设备,即HED型焊接工作站,它由焊接转胎、埋弧焊接系统(机头、送丝机及电源)、焊接操作架以及焊接变位器等配套设备为一体,构成所谓窄间隙自动焊接系统,从而进一步扩大其应用空间,为生产提供方便。
近年来,在厚壁管道生产中,窄间隙MAG焊、窄间隙热丝TIG焊等工艺的应用范围日趋扩大,因此为窄间隙设备发展提供了有利的条件。
4.2 壳体内璧带极堆焊技术
在石化行业的一些加氢设备和核容器及尿素设备中,内壁往往要求堆焊奥氏体不锈钢。对于大面积堆焊而言,手工电弧焊和丝极自动堆焊不但效率低、堆焊层内部和表面质量差,而且在堆焊层与基层母材结合处往往易产生缺陷,因此带极自动堆焊技术应运而生,被广泛地用于容器内壁大面积堆焊之中。
带极自动堆焊具有效率高、堆焊层内部质量均匀、堆焊表面平整光滑等特点,而且由于稀释率较低,堆焊金属与基体母材之间的结合面处不易产生焊接缺陷和发生质量问题。从堆焊方法原理上讲,带极堆焊可以分为埋弧自动堆焊和电渣堆焊两种。
电渣堆焊具有焊接熔深浅、稀释率低、堆焊层表面更加平整光滑等优点。若焊带尺寸较宽时必须加磁控头,否则堆焊难以成型。另外由于其焊接熔深浅,热输入量大,在容器使用时,堆焊层产生氢剥离的机率也较大。
一般来讲当焊带尺寸为0.4×75(厚×宽)及更小时,电渣堆焊层不会产生氢剥离。因此,为确保堆焊层质量和容器运行中不出现问题,当采用大尺寸焊带堆焊时,推荐过渡层采用熔深较大的埋弧自动焊,而为使堆焊层表面平整光滑,表层堆焊时易采用电渣堆焊。
堆焊使用的焊带尺寸,国内已使用到最大达75mm宽的焊带,而国外最大已使用到150mm宽。容器内壁堆焊层一般采用过渡层加表层的双层或多层堆焊,但对某些容器,根据需要,也已成功开发出单层浅熔深电渣堆焊技术。
堆焊用的材料大多使用进口焊带和焊剂,现在国产焊带和焊剂的质量也在逐步提高,已接近进口堆焊焊材的质量水平,并在一些容器制造厂广泛应用。
4.3 小直径管内壁氩弧堆焊技术
过去,小口径管内壁不锈钢堆焊都采用手工电弧焊方法,不但效率低、堆焊质量不易保证,而且对于直径小、长度较长的接管无法实现内壁堆焊。
80年代中期,兰石厂首先从日本爱知公司购置了一台小接管内壁丝极氩弧焊设备,随着这一先进技术的开发,彻底解决了细而长且直径较小的接管内壁无法进行不锈钢堆焊的难题,它可以实现内径φ50mm以上的接管内壁堆焊,其堆焊效率高,堆焊质量好,堆焊层表面平整美观,完全达到国外小接管内壁堆焊的工艺水平。
其缺点是只能堆直管,不能堆弯管。为此,哈尔滨焊接研究所研制出了小直径接管及弯管内壁堆焊机,即将90°弯管分割成3段,分别实现30°弯管的内壁堆焊,然后再组装焊接成一90°整体弯管,其焊接质量与进口设备不相上下。
4.4 接管、法兰药芯焊丝气体保护堆焊技术
药芯焊丝气体保护焊,由于芯部焊剂的作用,焊缝表面生成薄层渣壳,使焊缝光滑平整,成型不亚于埋弧焊。在富氩混合气体保护下,电弧能量高,熔深大,即使焊道搭接量50%也能保证道间和层间熔合良好。
药芯焊丝焊接时,电流通过药芯周围的薄层铁皮导电,电流密度大,熔敷效率比实芯焊丝高。此外药芯焊丝焊接可以连续送丝不断弧,无飞溅,无需特殊清理,适合多道、自动和半自动焊接作业,因此近年来已被广泛用于不锈钢堆焊,特别是接管内壁及法兰密封面不锈钢堆焊结构。
哈尔滨锅炉厂有限责任公司在陕西渭河大化厂产品—气化炉生产中,为了提高生产效率,采用药芯焊丝MAG焊工艺进行了内径Φ175-370mm的接管自动堆焊,并且自行研制了1.5吨和25吨的自动MAG药芯焊丝堆焊装置(适应直径分别为Φ375-800mm及Φ800-1600mm的接管和法兰堆焊的专用焊接设备)成功的完成了与气化炉壳体相焊的各种接管与法兰(近百只)的堆焊生产。
兰石厂也将药芯焊丝CO2气体保护不锈钢堆焊工艺成功的应用于加氢反应器接管的内壁焊接。该项技术的应用,节约了大批不锈钢锻件,降低了生产成本,具有可观的经济效益,同时为压力容器焊接开发出了一项新的工艺技术。
4.5 管子--管板全位置焊接技术
对于换热器产品,换热管与管板间的焊缝质量是一个至关重要的因素,它直接影响到产品的质量和使用寿命。最早管端角焊缝均采用手工电弧焊,这种焊接方法焊缝外观质量差,容易产生气孔、未熔合等焊接缺陷,焊接质量不稳定,在出厂前的水压试验或使用过程中容易泄漏。
经过工艺改进,采用手工钨极氩弧焊(TIG)方法焊接,焊缝质量明显提高。但由于是手工操作,焊缝质量不稳定。为进一步提高管端角焊缝质量,提高焊接自动化水平,各厂逐步开发应用了管子--管板全位置自动氩弧焊工艺,采用专机来完成管端焊接,从而改变了换热器管端手工焊接的落后局面。
4.6 接管马鞍型管座自动焊技术
厚壁锅炉锅筒、核电站压力壳体及其他石化容器上的大直径接管的焊接,也是厚壁容器制造技术关键之一。这种大直径管管座的焊接不仅工作量大,劳动条件差(高温焊接),技术难度高,而且质量要求也十分严格。以560T热壁加氢反应器接管管座为例,管座焊接壁厚为210mm、直径达690mm,材质为2.25Cr-1Mo,若采用手工焊接是不堪设想的。
郑州机械研究所、中国电工设备总公司与上海锅炉厂有限公司合作研制了一种大直径接管马鞍型焊缝专用埋弧自动焊机,并在厚壁锅炉锅筒下降管和560T热壁加氢反应器等化工高压容器接管管座焊接中得到实际应用,焊接质量优良,并取得可观的经济效益。
该焊机具有机械式马鞍跟踪机构,并具有上坡焊和下坡焊接速度补偿功能,以保证焊道在上坡焊和下坡焊时熔池金属处于不同流动方向情况下能获得相同厚度。现这一专用设备又在武汉锅炉、东方锅炉、北京巴威及中国一重得到推广应用。
接管直径大小决定马鞍落差量,最近生产的新型焊机马鞍落差最大为170mm,可焊接管最大直径Φ1700mm,可满足600MW核电产品和压力容器大型管座焊接要求。
5 新材料的开发、研制与应用
5.1 P91大直径管的应用
随着T91材料的成熟应用,大口径P91钢在集箱部件中的应用日趋增多,一些锅炉厂结合生产实际,对该材料进行了全面的焊接性和工艺性试验,掌握了该钢材焊接特性和工艺特点。9Cr1MoV钢是在9Cr1Mo钢基础上加入了V、Nb等合金元素,高温回火后的组织为回火马氏体加稳定的碳化物。
9Cr1MoV钢具有较高的抗蠕变断裂强度,抗热疲劳性能和抗氢脆性能,可用于温度高达650℃过热器、再热器以及600℃以下的集箱和导管部件,在一个较宽的冷却速度范围内可得到单一马氏体结构,且具有很好的韧性和强度。在625℃时的持久强度与TP304和1Cr18Ni9Ti钢等强,用于代替奥氏体不锈钢时,可避免与奥氏体不锈钢管焊接制成的异种金属接头早期失效的问题。
5.2 16MnR(HIC)—抗氢诱导裂纹用钢的应用
在炼油厂、化工厂中,许多壳体材质为16MnR的容器都是在含有H2S介质的条件下工作。以往为抵御H2S介质所造成的应力腐蚀开裂,往往是控制16MnR材质的含Mn量,焊后进行整体消除应力热处理和控制其产品焊接接头的最高硬度≤200HB。
即使是这样,在容器使用中,焊接接头及母材上还不时有由于H2S应力腐蚀作用产生的裂纹,有的甚至因此而导致容器报废。为此,近年来国内设计院和钢厂共同设计和研制开发出一种在H2S介质条件下工作能抗应力腐蚀开裂的新钢种—抗氢诱导裂纹用钢,即16MnR(HIC)钢,
该钢主要特点是在控制其含Mn量的同时,严格控制其S、P含量(P≤0.015,S≤0.004),为改善钢材性能,还添加了部分微量合金元素,钢板的硬度≤200HB,对该钢制造的压力容器其焊缝也作出了相应的要求:其焊缝的S≤0.010%,P≤0.020%。
焊接接头部位的硬度值经SR处理后≤200HB。这一新钢种现已被广泛地使用在压力容器制造上。国内哈尔滨焊接研究所、江南焊丝厂等也相继开发出满足该钢种焊接工艺要求的焊接材料。
这种钢在国外80年代就已开发并成熟的用于生产,其名为抗氢蚀脆裂性能钢,例如,欧州迪林格钢铁公司就生产出DICREST系列压力容器用钢,它在化学成份方面控制更严,Mn含量≤1.20%,P≤0.010%,S≤0.0010%,而实际生产的钢板P含量仅为0.007%,S为0.0006%,因此其抗氢蚀脆裂性能更为优越。
5.3 双相不锈钢的开发和应用
由于现代工业技术的飞跃发展,传统的奥氏体不锈钢经常受到应力腐蚀、点蚀、缝隙腐蚀等各种局部腐蚀的破坏。双相不锈钢(即铁素体—奥氏体双相不锈钢)得到开发,这类钢在上述各类局部腐蚀中表现了优于普通奥氏体不锈钢的特点,正受到日益广泛的重视。
所以,近年来在压力容器行业中,用该钢制作的容器越来越多,如西安524厂已用该钢制作过几台大型塔器。这类钢制作容器的关键在于焊接工艺的制定和实施。由于国内的相应焊材还不十分成熟,故多使用进口焊材,尤以瑞典焊材为优。
5.4 镍基耐蚀合金的焊接
近年来,根据需要,蒙乃尔合金(Ni-Cu合金)、因科镍合金(Ni-Cr-Fe合金)、因科洛依合金(N-Fe-Cr合金,如Incoloy800、Incoloy825)及哈斯特洛依合金(Ni-Cr-Mo合金)在压力容器中应用的越来越多,但容器整个壳体应用上述合金的还是少数,主要都是用来制作某一容器部件。
这类合金应用的关键是焊接时最易产生热裂纹 ,所以如何保证压力容器中这部分零件的焊接质量是最为重要的。哈尔滨焊接研究所生产的HT—103低氢型药皮镍基合金焊条,由于含有一定的Mo元素,具有优良的抗热裂性能,在镍基合金焊接以及异种钢焊接生产中,取得了良好的效果,解决了热裂问题。
5.5 高强度耐热抗氢钢的开发和应用
在石化行业中,相当一部分容器是在高温高压临氢介质下工作。长期以来,人们大量使用被称之为王牌抗氢钢的2.25Cr-1Mo钢来制作临氢设备。但随着加氢工艺技术,尤其是渣油加氢改质和煤加氢液化工艺的不断发展,加氢装置的规模越来越大,反应器的尺寸和壁厚也越来越大,设备的设计条件也更加苛刻,
若仍采用一般的2.25Cr-1Mo钢来制造,往往会造成壁厚太厚,单台容器金属重量过大,不但增加成本,而且给制造、运输和安装都会带来极大的困难。为此有必要开发强度更高、使用温度更高、抗氢性能更好的新型Cr-Mo钢种。
国外近20年来在这方面已做了大量的工作,相继开发出了3Cr-1Mo-0.25V和2.25Cr-1Mo-0.25V钢并应用于反应器的制造。这两种新型Cr-Mo钢与普通的2.25Cr-1Mo钢相比,各方面都有明显的优越性。
国内第一重型机械集团公司于1994年开始了3Cr-1Mo-0.25V钢的开发研究试验工作,经过几年的努力,已将该钢用于压力容器产品实际生产中。近两年来,国内几家主要生产临氢设备的容器厂又在进行2.25Cr-1Mo-0.25V钢的开发研究工作,并已取得一定的成绩。相信随着工业技术的不断发展,这些新型的Cr-Mo钢会越来越得到广泛的应用。
5.6 背面自保护不锈钢钨极氩弧焊丝的应用
多年来,不锈钢氩弧焊焊接时背面金属氧化一直是焊接工艺上一大难题。一般采用背面充氩保护,但是当容器较大,管道较长或背面无法实施氩气保护时,将大量浪费氩气,且仍出现保护不好,或根本无法进行背面保护的问题。
为解决这一工艺难题,日本油脂公司焊接事业部开发制造了一种背面自保护不锈钢TIG焊丝,这是一种具有特殊涂层的焊丝,涂层(即药皮)熔化后会渗透到熔池背面,形成一层致密的保护层,相当于焊条药皮的熔渣覆盖在焊缝表面,使背面金属不受氧化。
冷却后这层渣壳会自动脱落,用压缩空气或水冲的方法极易清除。这种焊丝的使用方法与普通的TIG焊丝完全相同,涂层不会影响正面的电弧和熔池形态。兰石厂从珠海雅各臣发展有限公司购置了该种焊丝,使用效果相当满意,大大降低了不锈钢氩弧焊的综合成本。
不过要提醒的是,该焊丝为单面焊双面成型打底焊专用焊丝,不宜用于第二层以上的焊道,否则易造成夹渣。目前国内的一些焊材厂也相应的开发并生产了此类焊丝。
5.7 丙烷、丙烯气体在热切割加工中的应用
在热切割方面,氧-丙烷(丙烯)火焰切割技术的应用已经取得了实际效果。丙烷、丙烯等气体在安全特性、燃烧特性及经济性等综合技术性能上均优越于乙炔气体。
氧-丙烷火焰柔和,体积发热量比乙炔高,切割面精度高,尤其是切割厚板时不塌边不回火(体积热量大、后劲足)等优点更优于乙炔,而氧-乙炔火焰猛烈,火焰集中温度高,致使切割面硬化,热影响区宽以及合金钢切割面易产生淬硬和裂纹等弊病,不利于机械加工和焊接,由此看来丙烷等气体的推广使用已经势在必行。
哈锅通过多次试验并经生产实践验证后逐步推广了氧-丙烯火焰切割。目前该厂已彻底停止了乙炔气体的生产和供应,并建立了气体供应站,将瓶装气体串联后通过管道(原乙炔气体管道)输送到各生产分厂,进而全部实现了氧-丙烯火焰切割,
应用实践证明,使用乙烯等石油气体代替乙炔用于火焰切割,不仅使用安全,切割质量得到提高,而且与乙炔气体相比,价格便宜,成本低,具有显著的经济效益。尤其是减少了乙炔气体制备的能源浪费(煤、水、电)和环境污染,具有广泛的社会效益。
本文编辑:糖糖
本文由焊割在线整理发布,转载请注明
问:2023年锅炉价格/多少钱?

上一篇:脱硫脱硝厂家供应锅炉脱硝设备
下一篇:模块锅炉的一些基本常识