机床不仅害怕腐蚀,害怕震动,更害怕各种热处理制度缺陷导致syr一抛弃了之机床:啊呦polite?1/31金属材料学习题与思考题第一章1.为什么
机床不仅害怕腐蚀,害怕震动,更害怕各种热处理制度缺陷导致syr一抛弃了之
机床:啊呦polite?
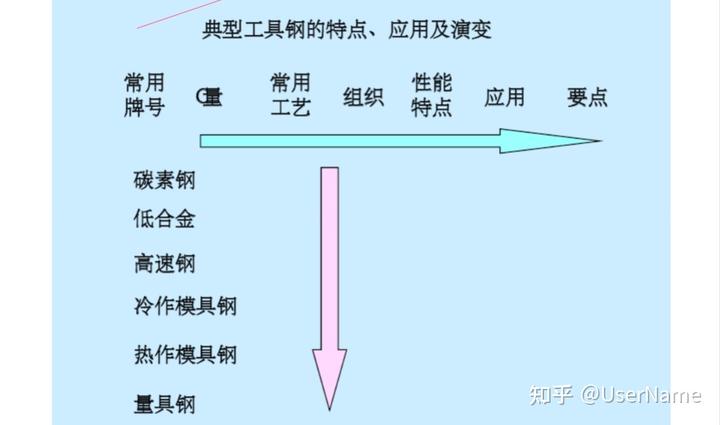
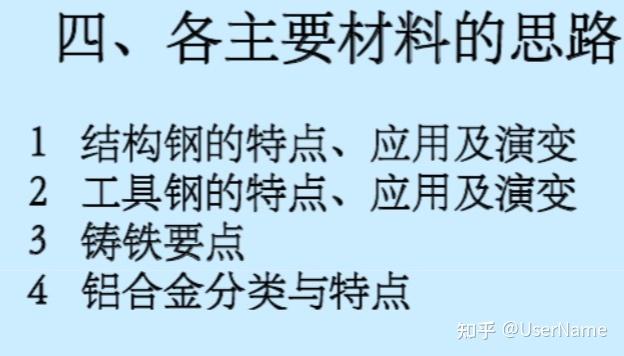
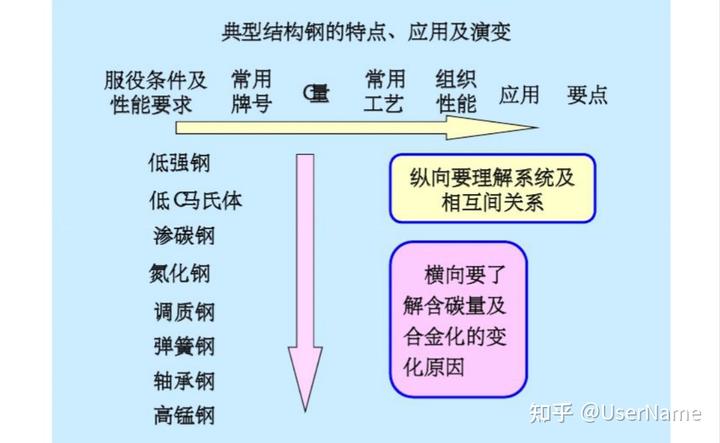
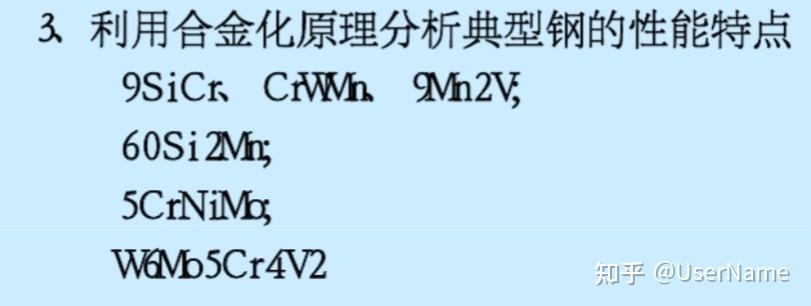
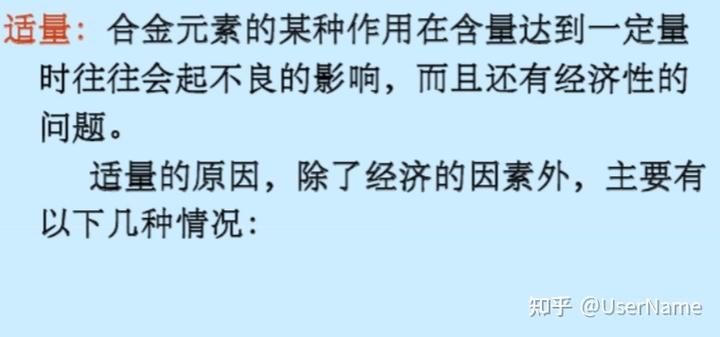
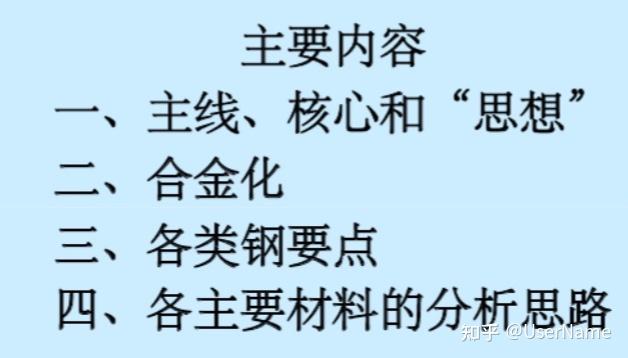
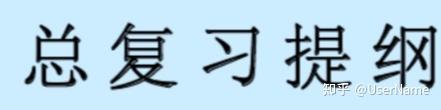
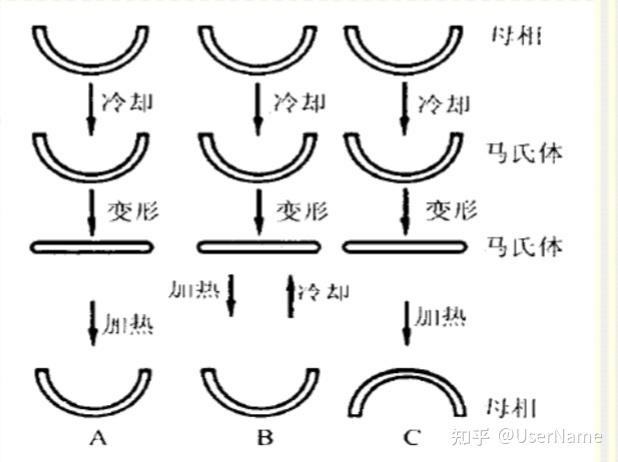

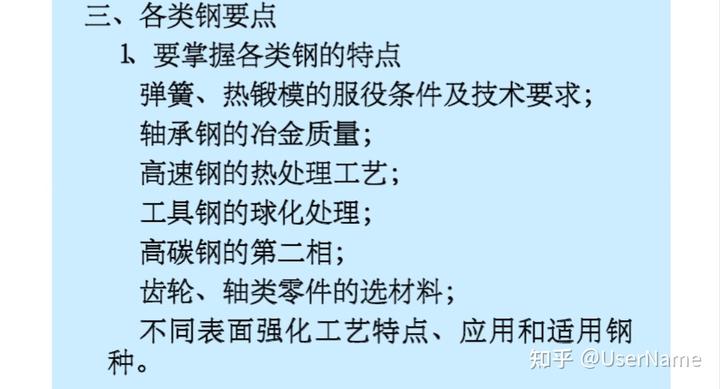
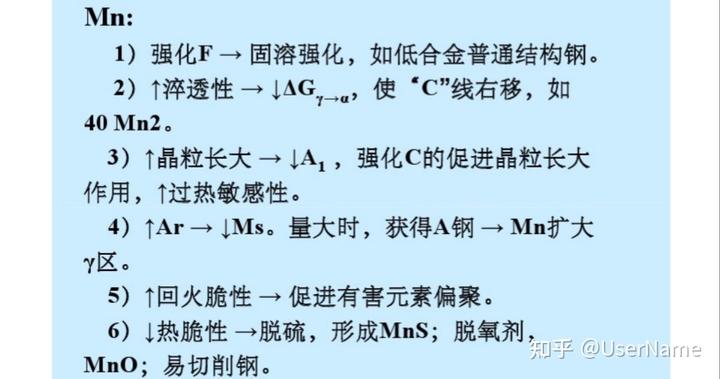
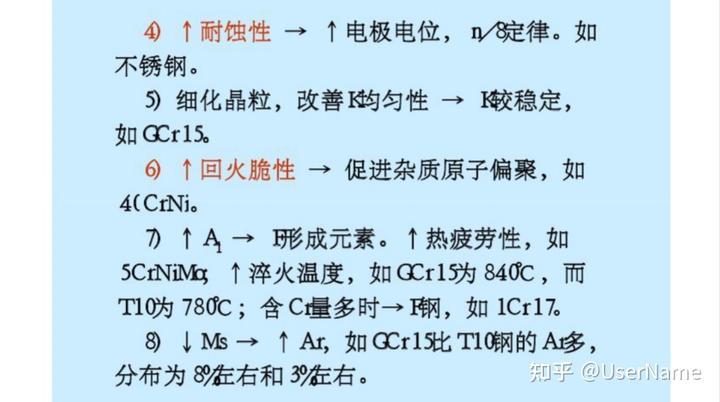
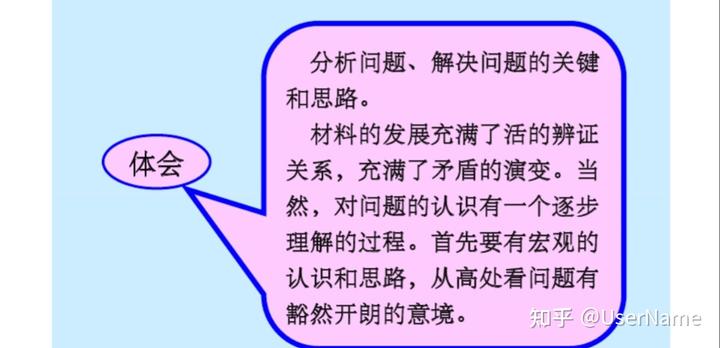

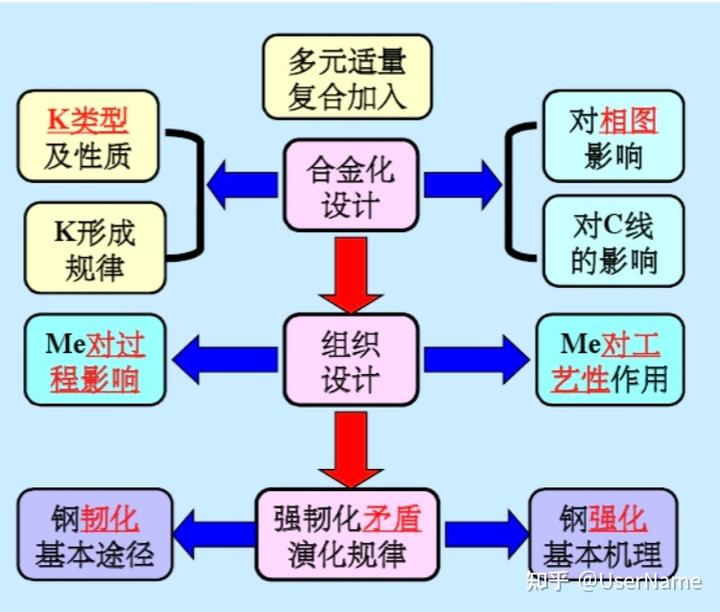
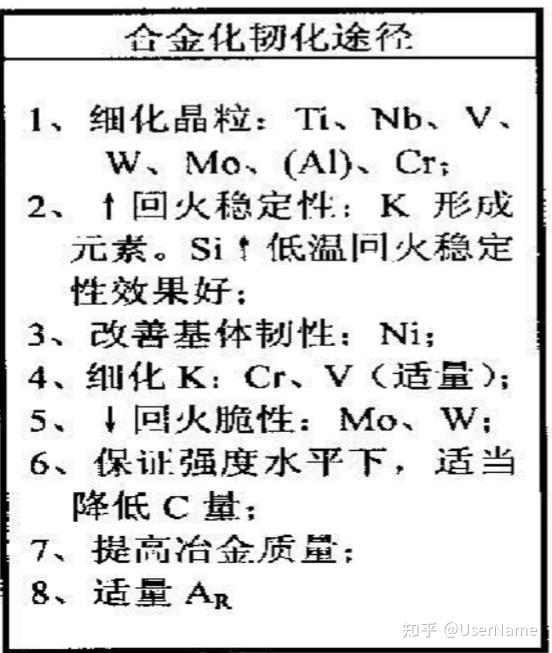
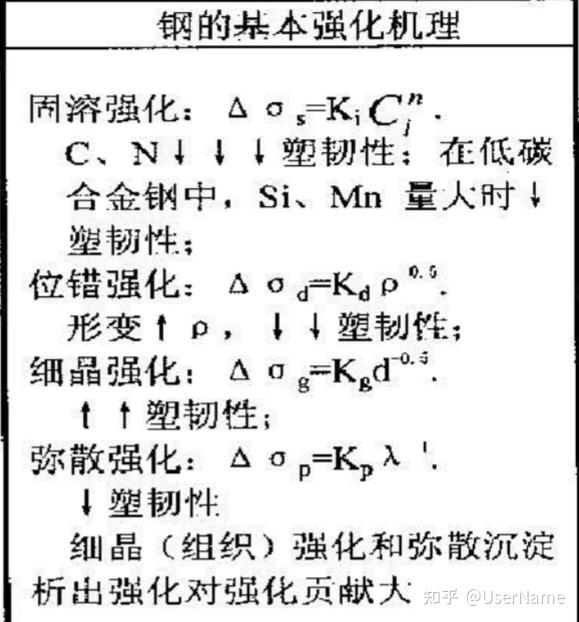


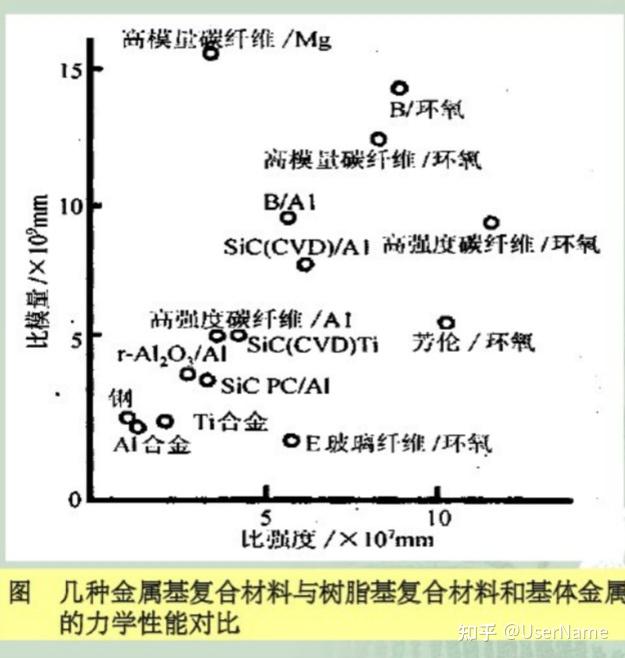
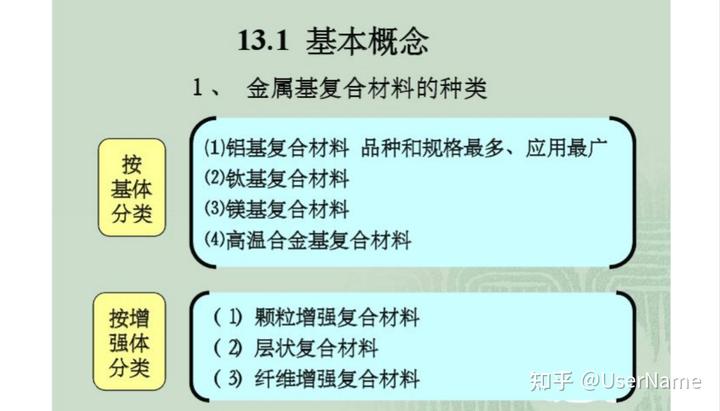
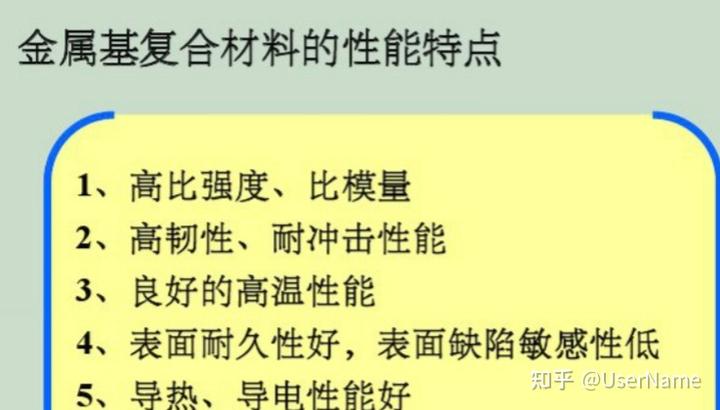
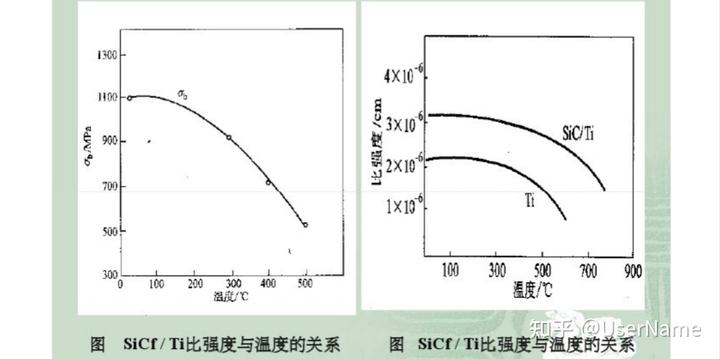
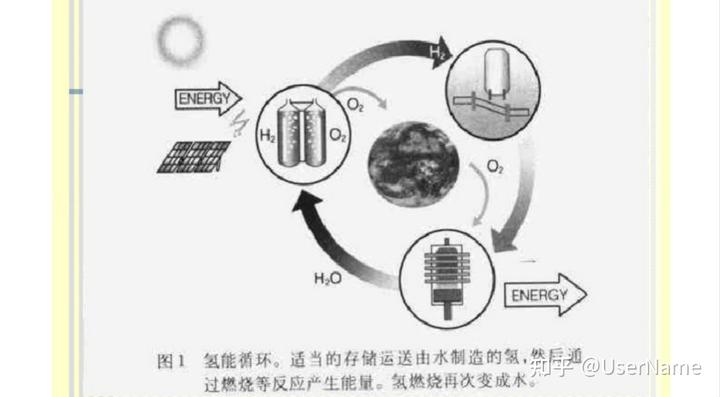
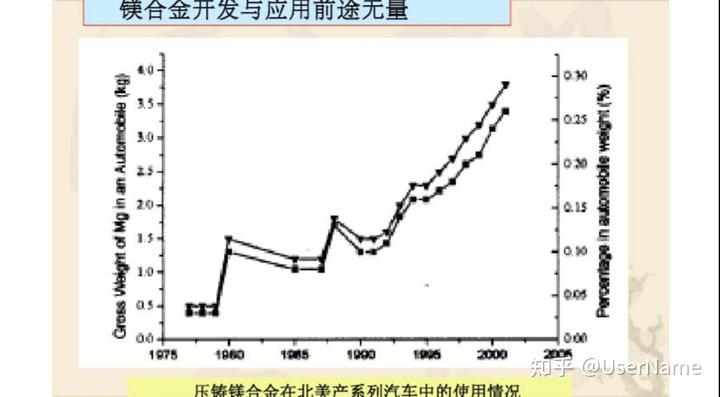
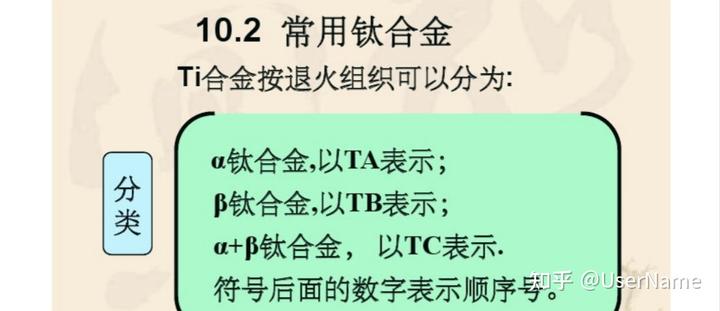
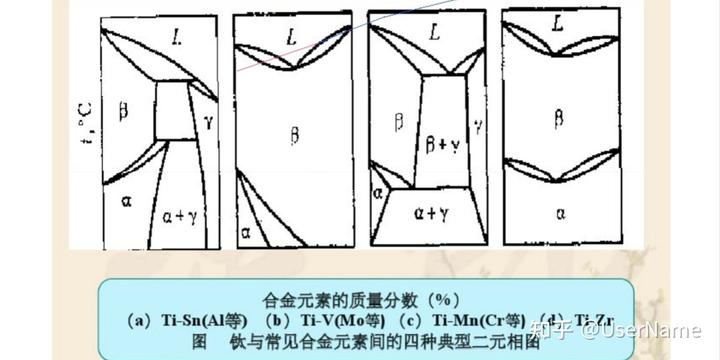
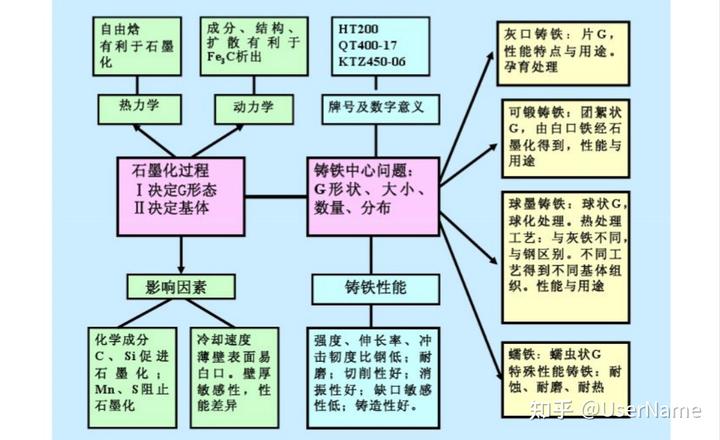
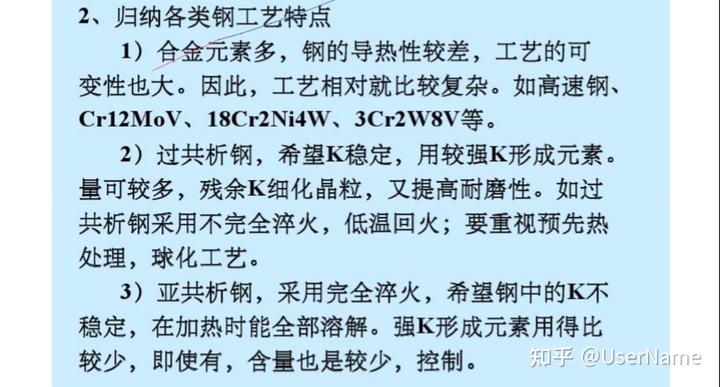
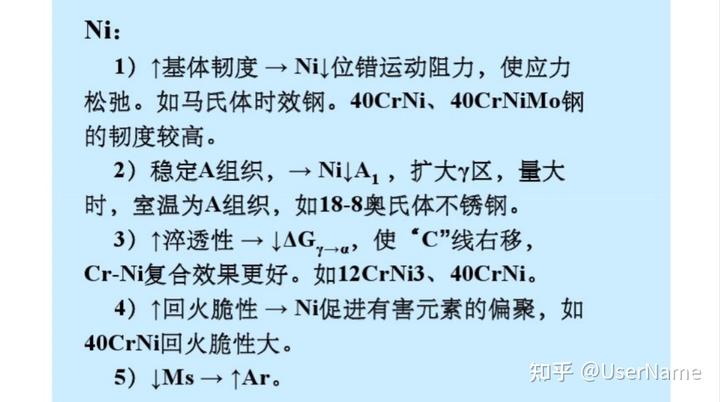
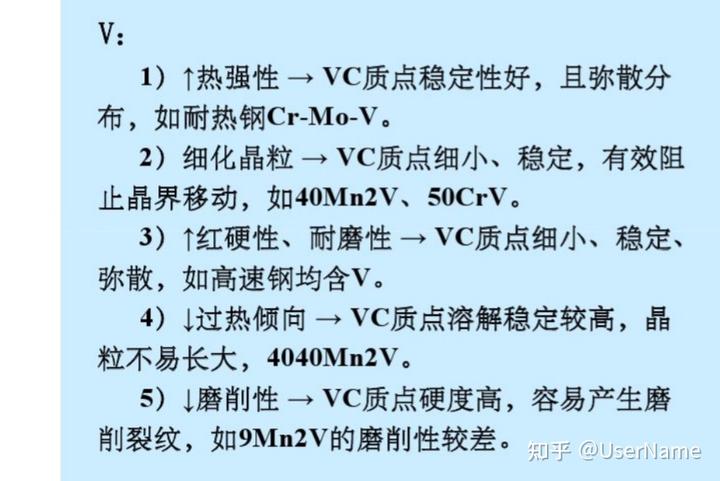
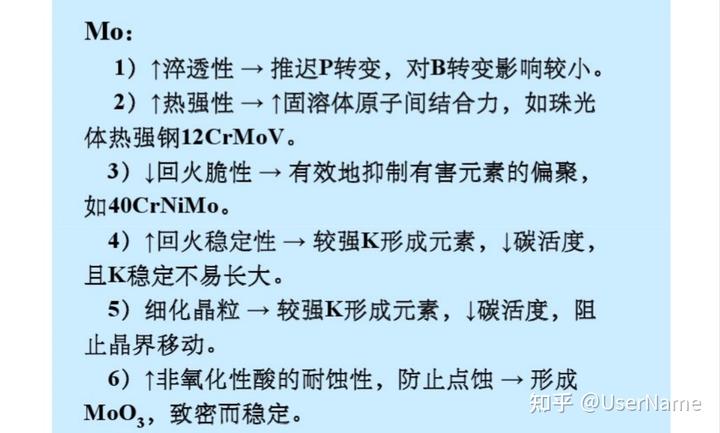
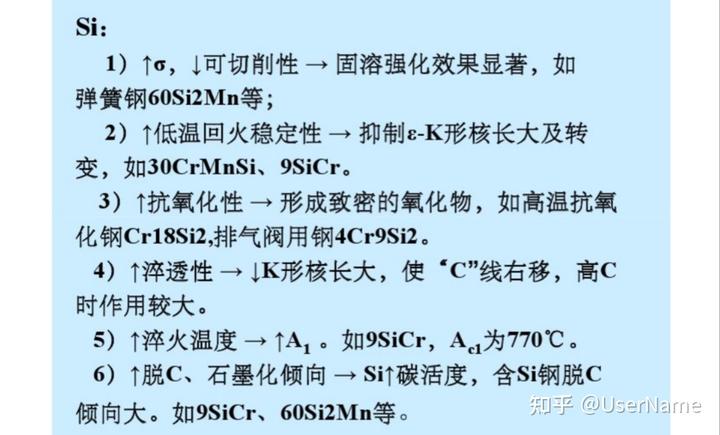
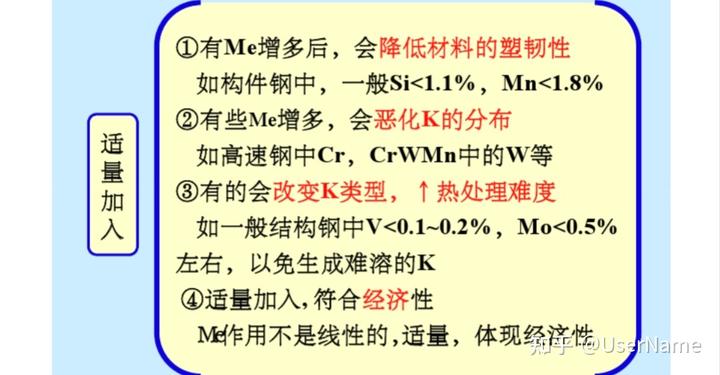
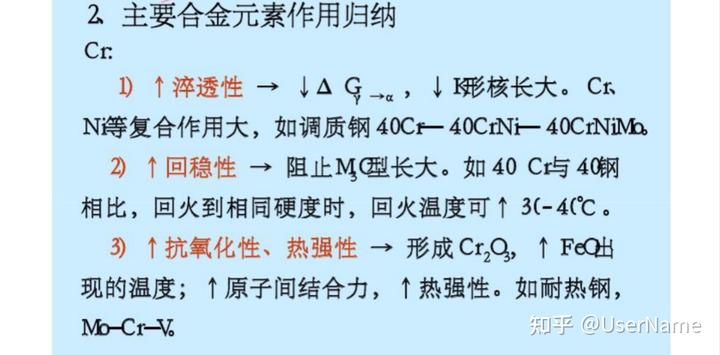
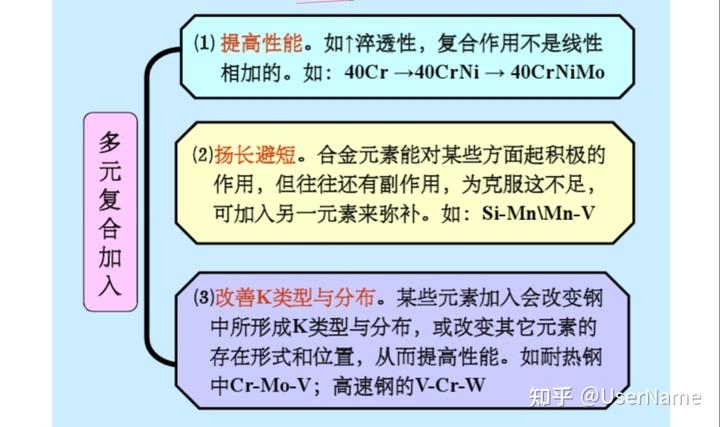
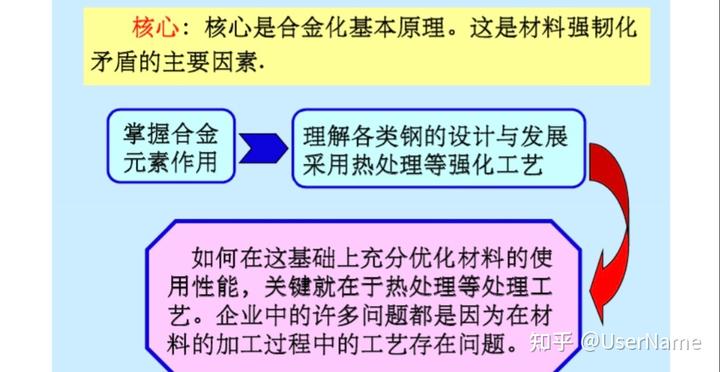
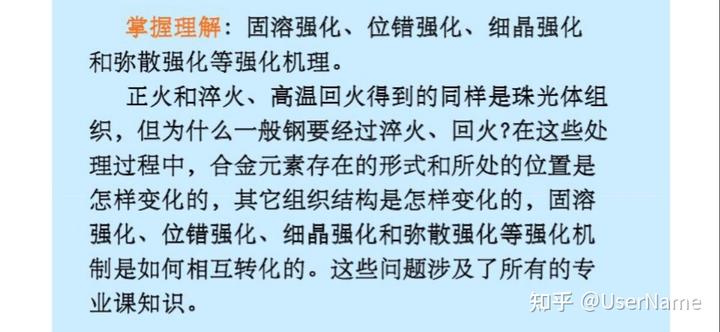
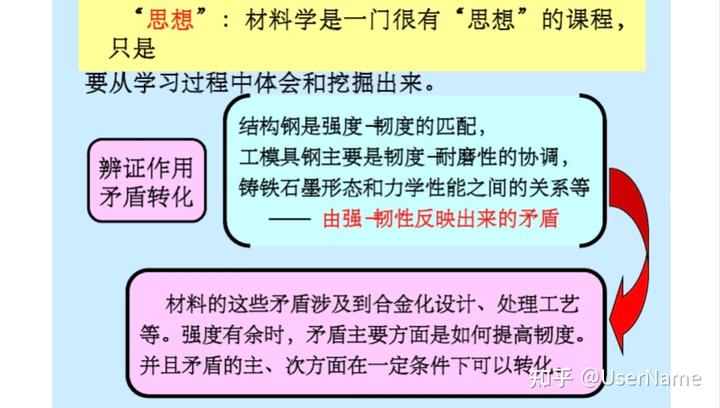
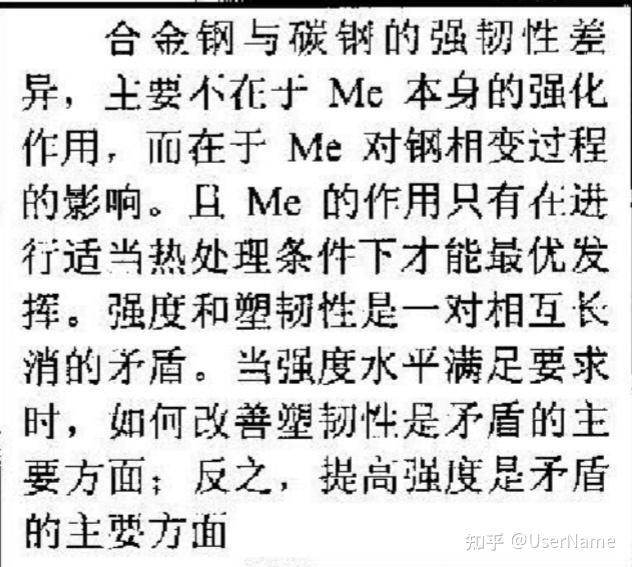
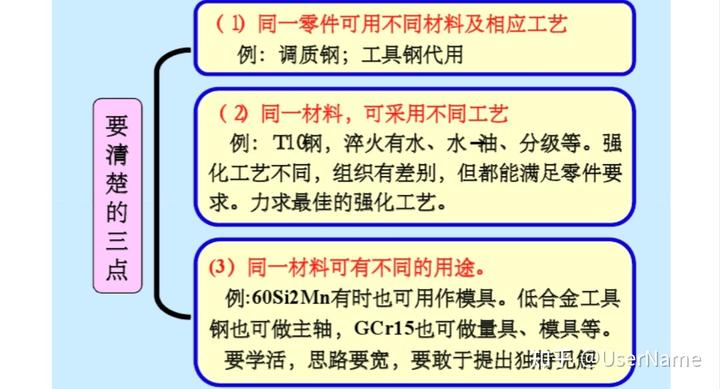
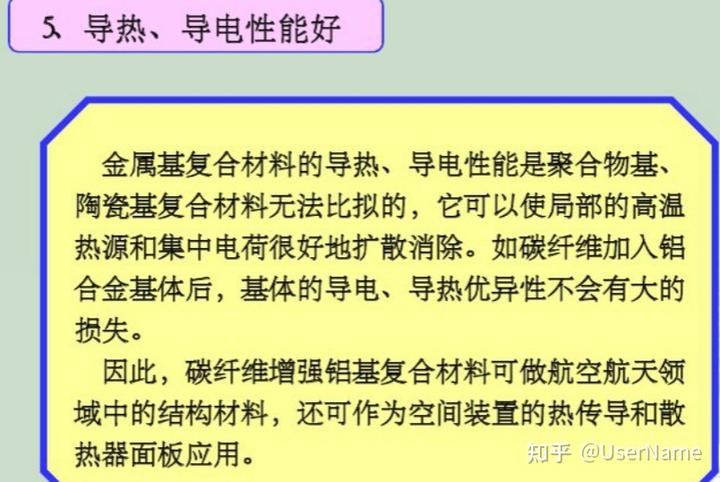
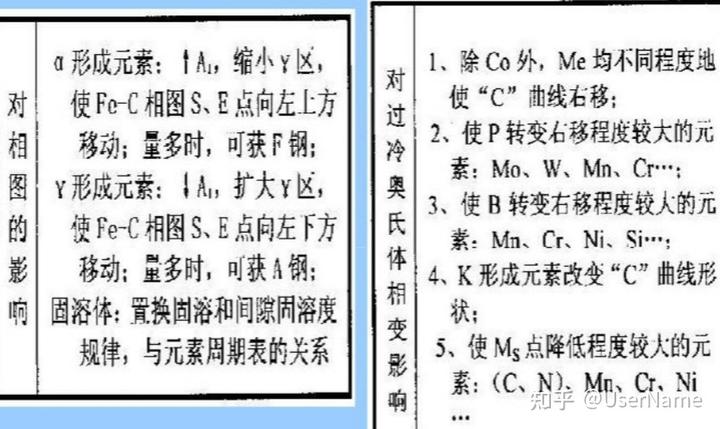
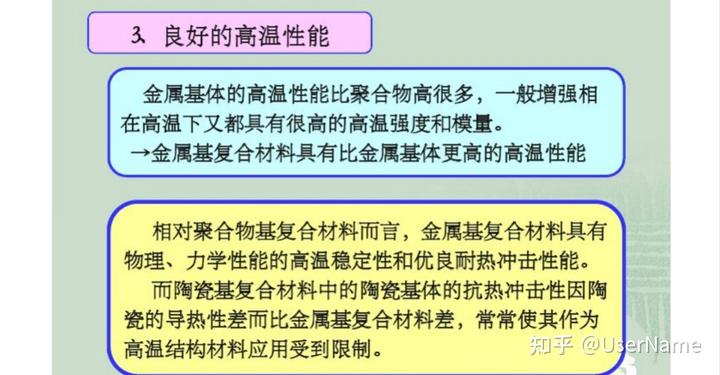
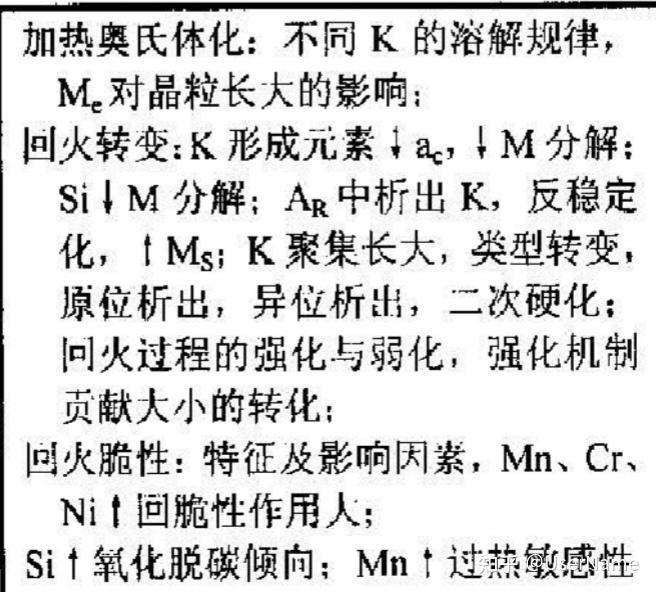
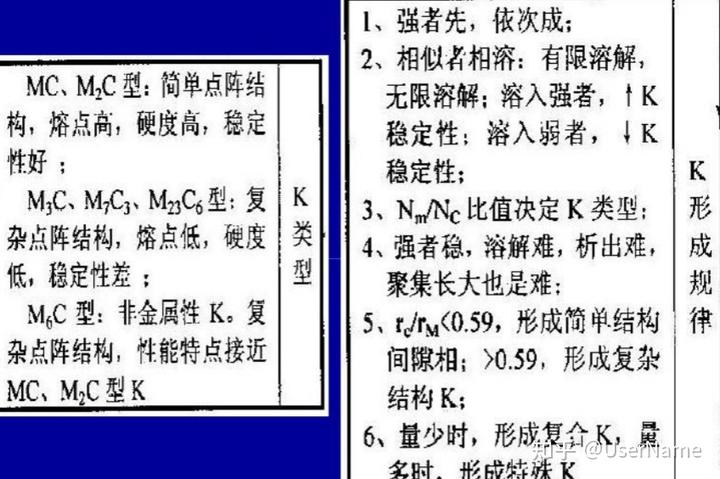
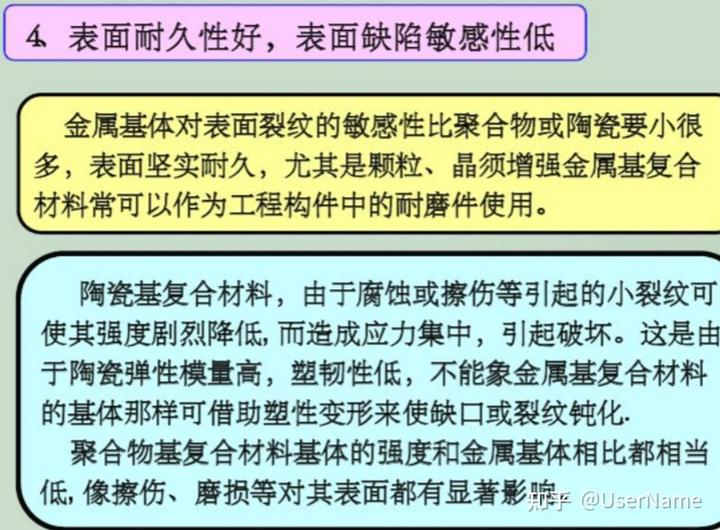
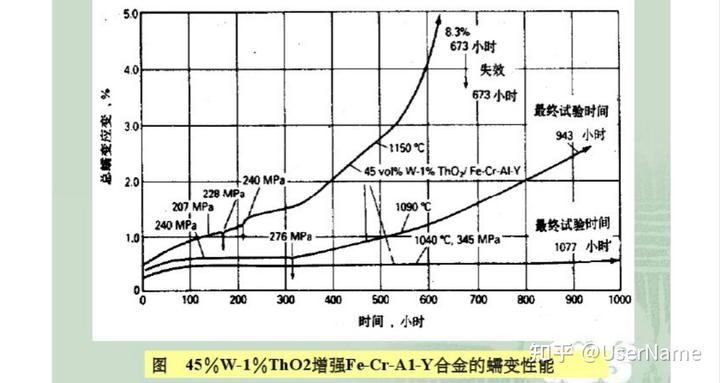
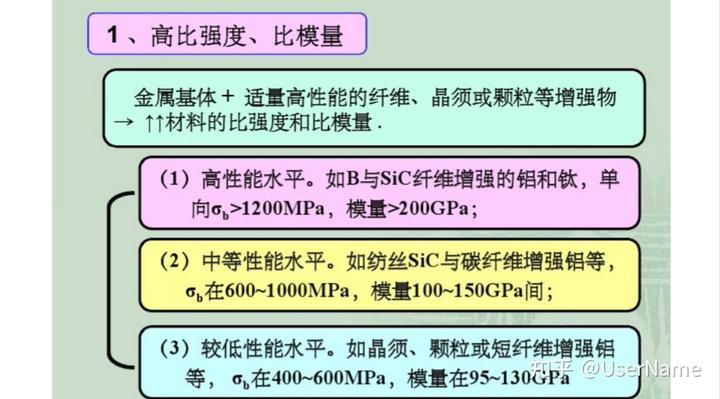
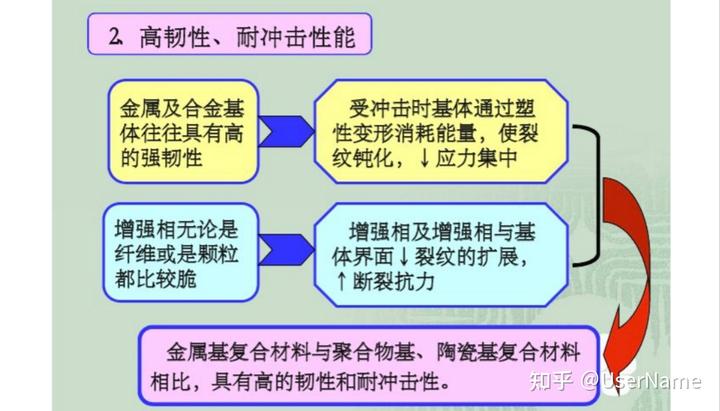
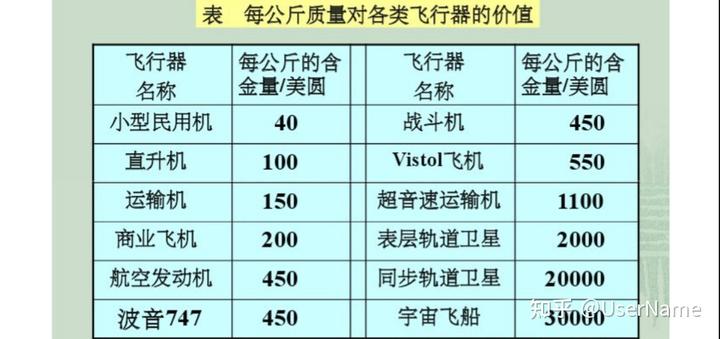
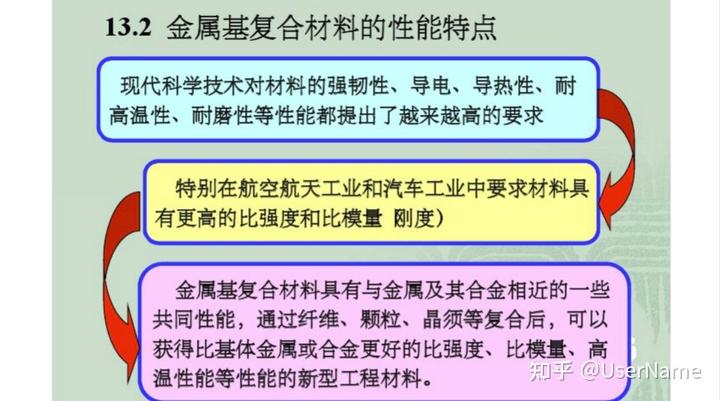
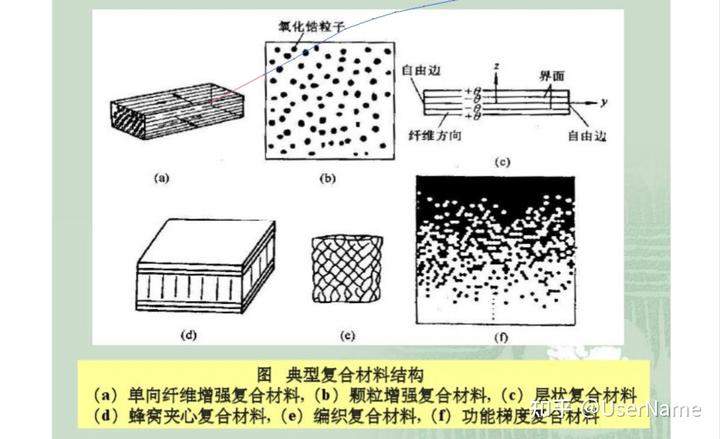
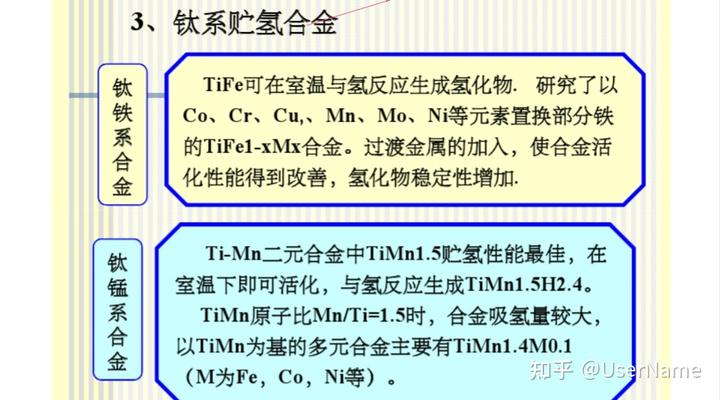
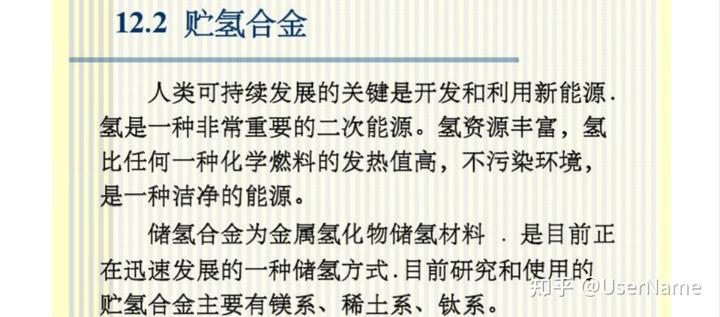
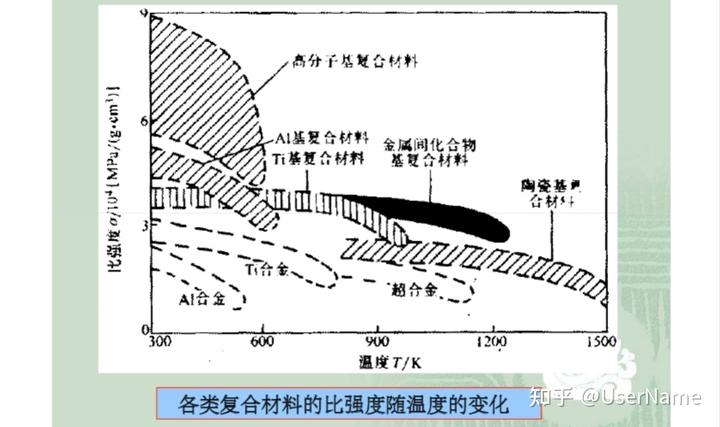
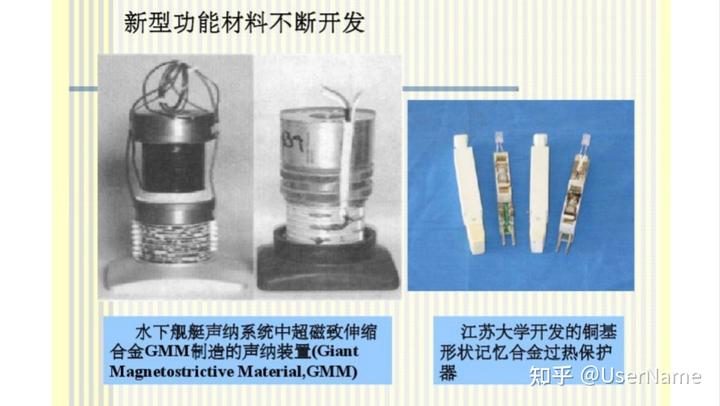
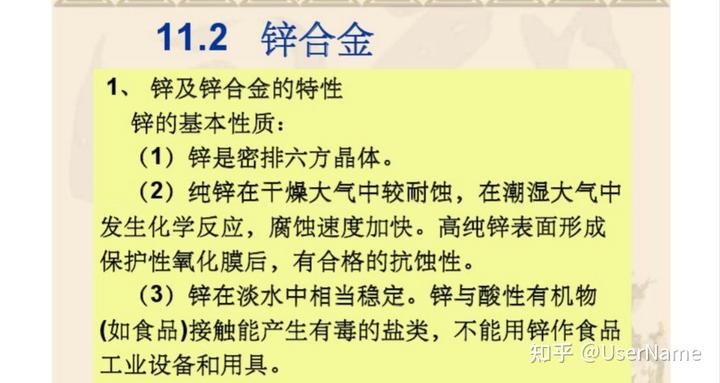
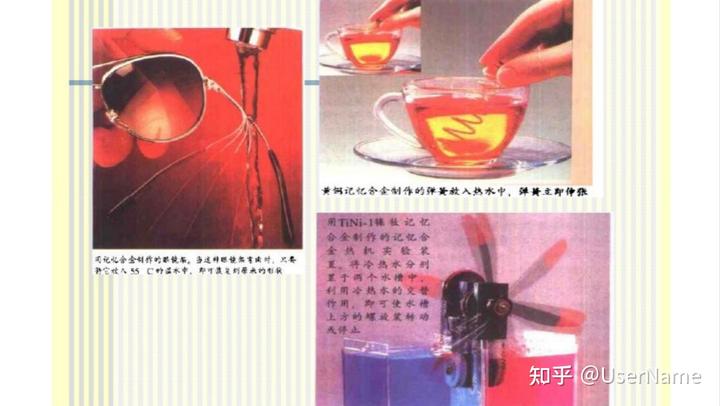
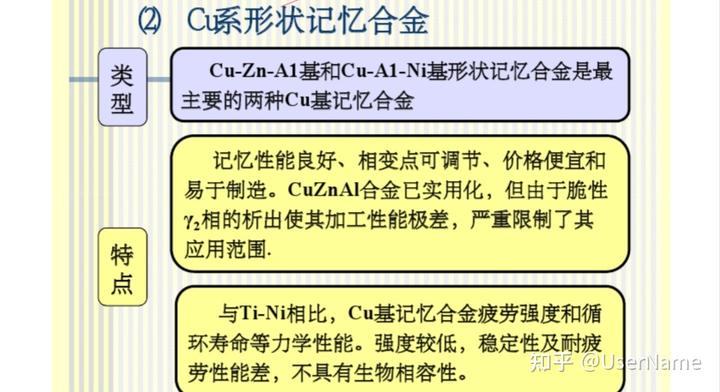

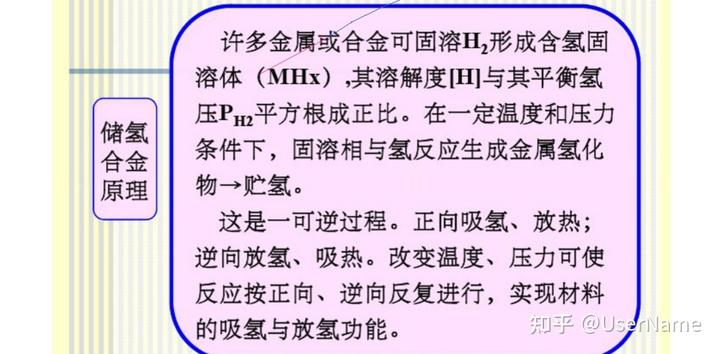
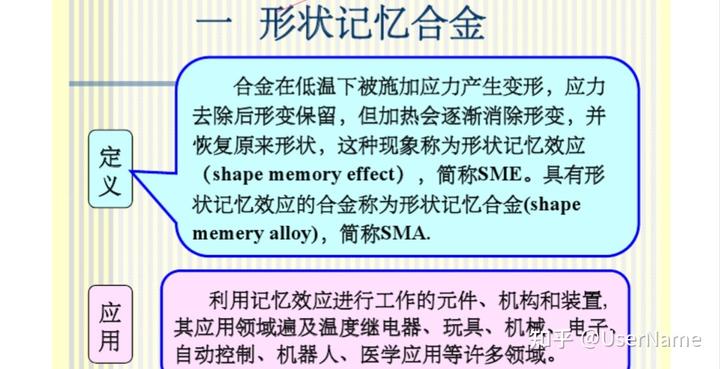
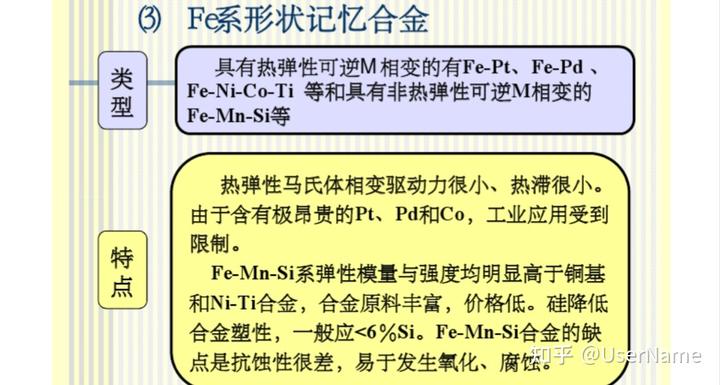
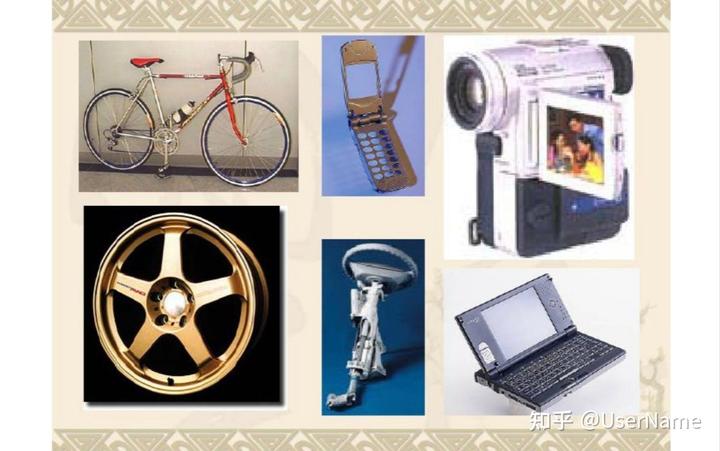
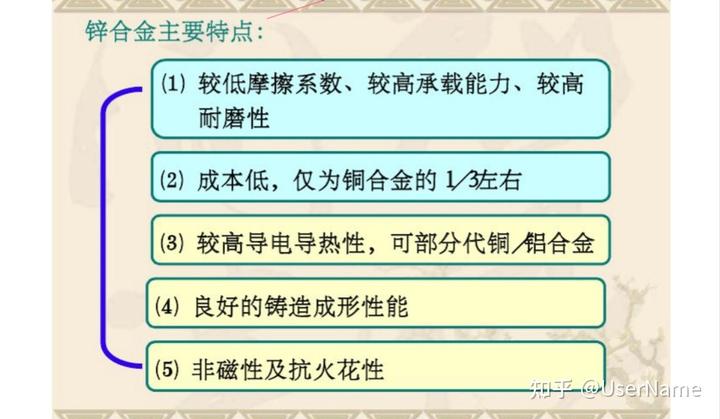
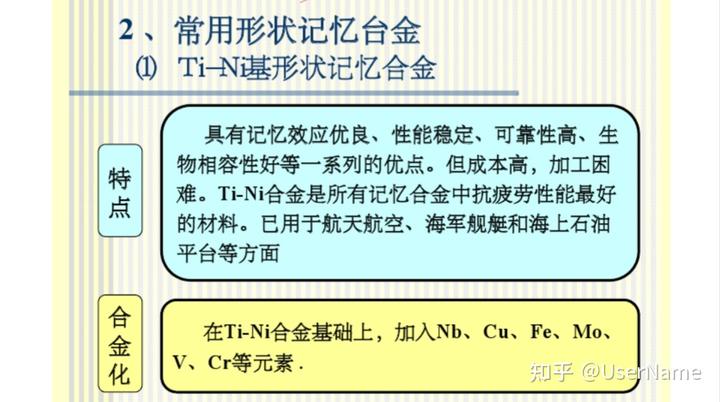
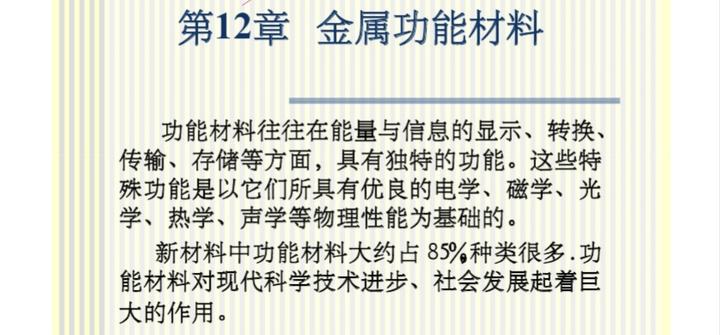
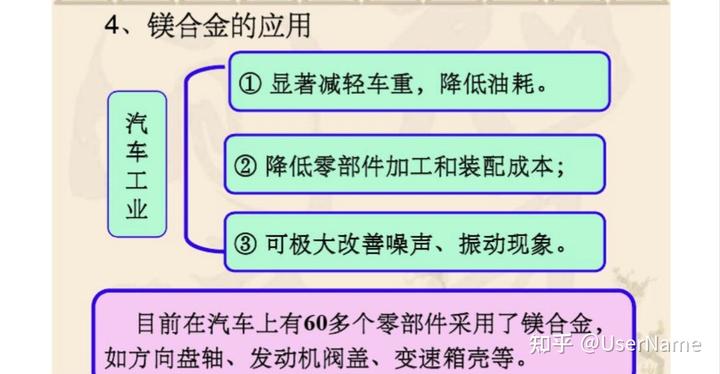
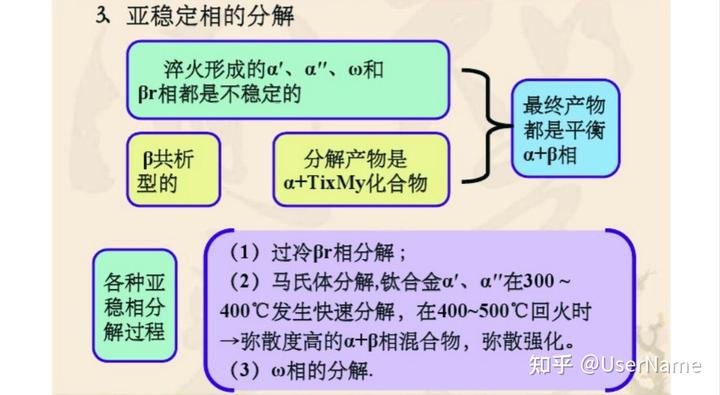
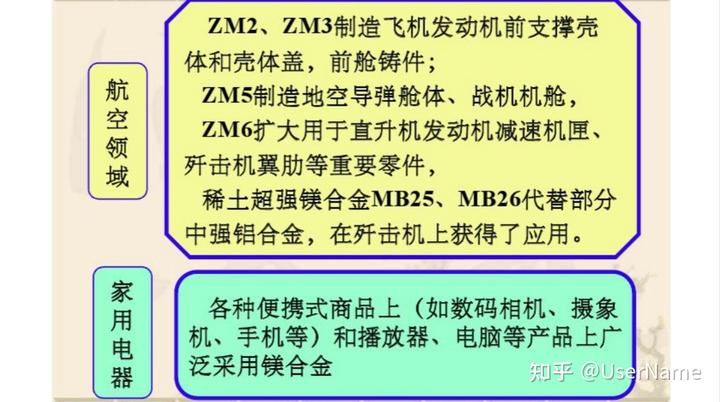
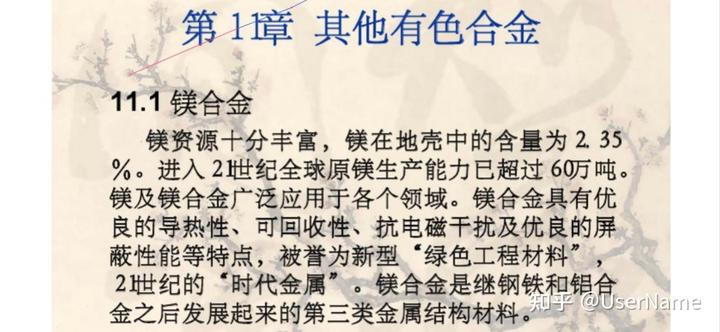
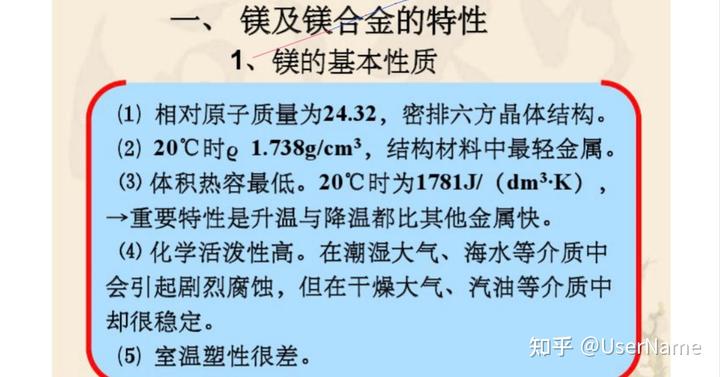
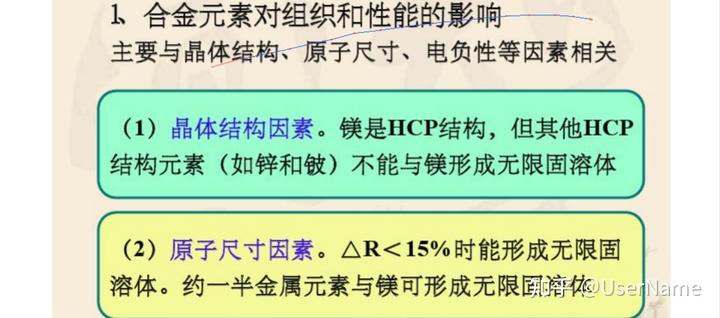
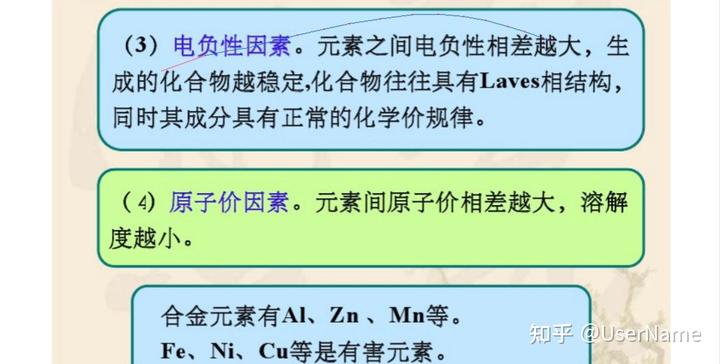
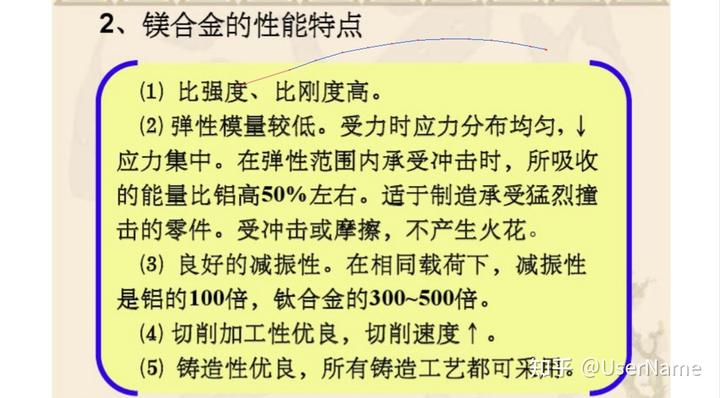
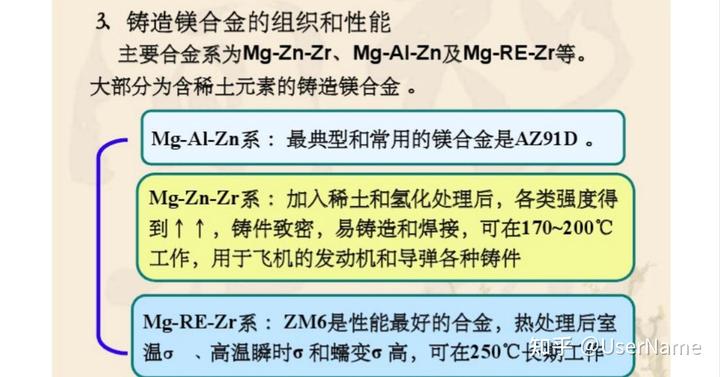
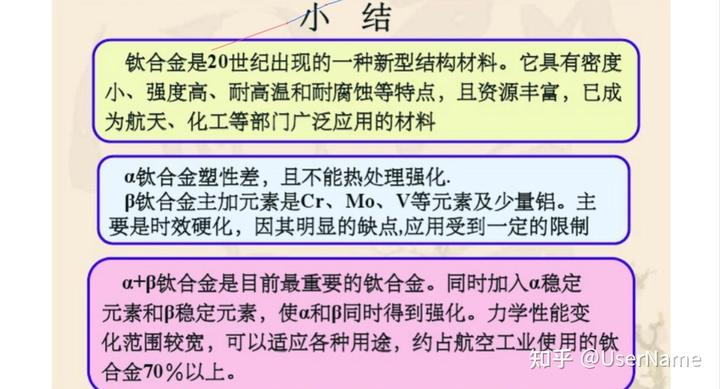
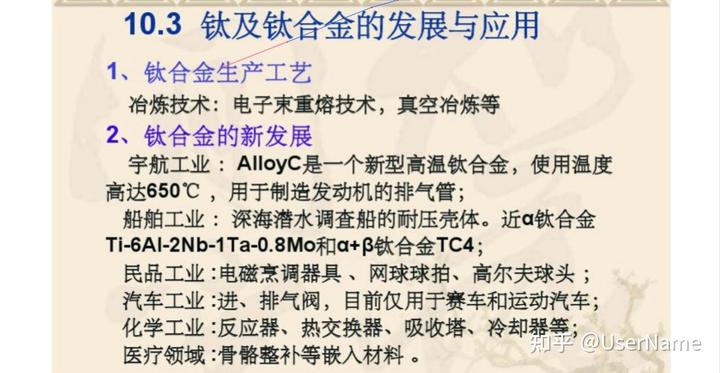
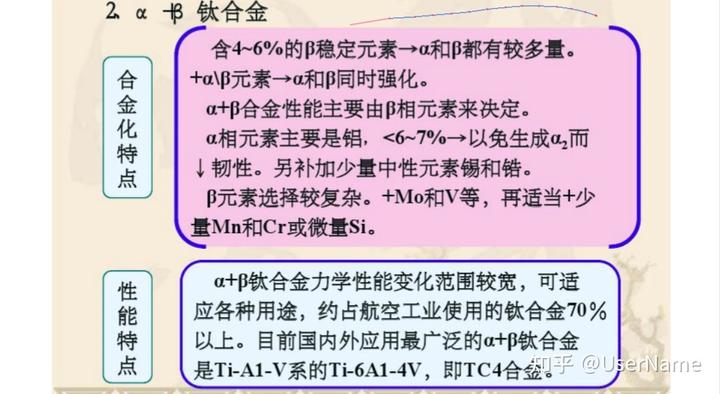
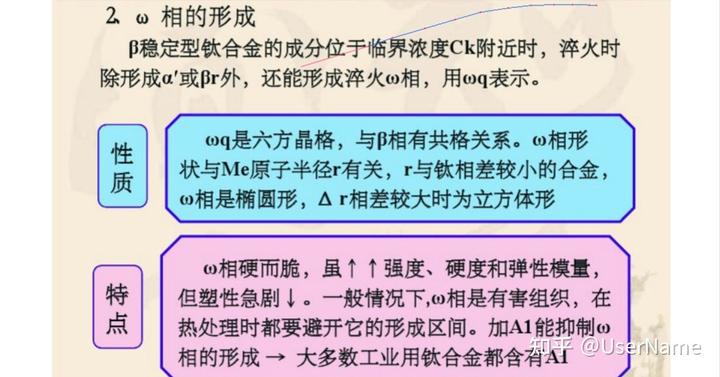
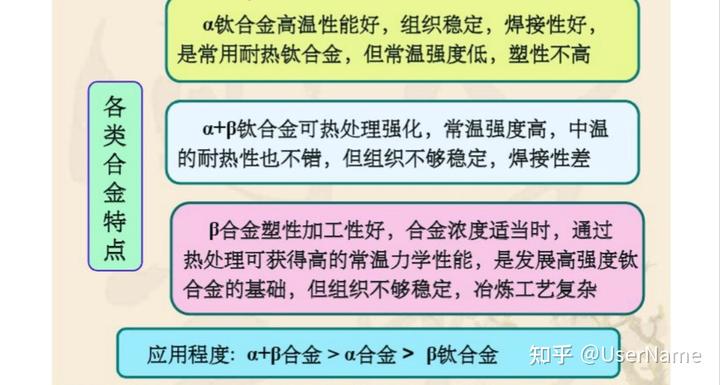
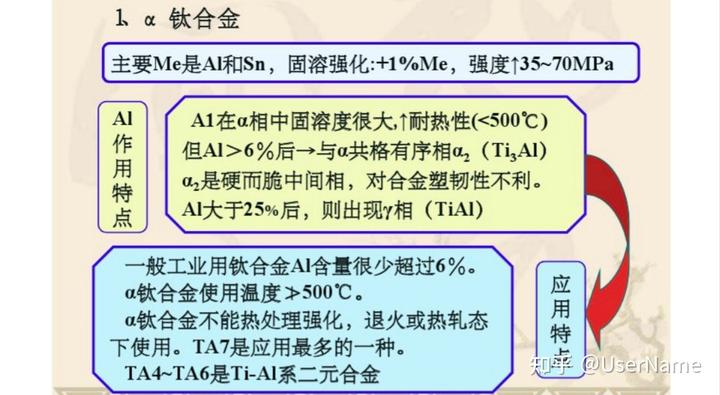
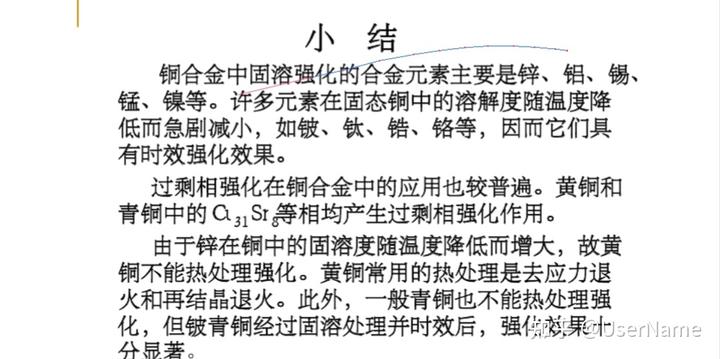
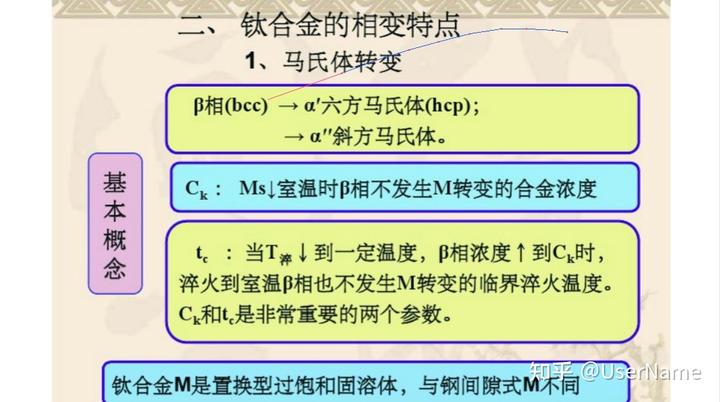
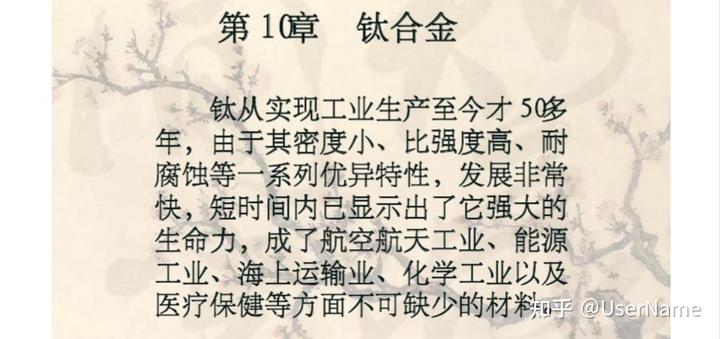
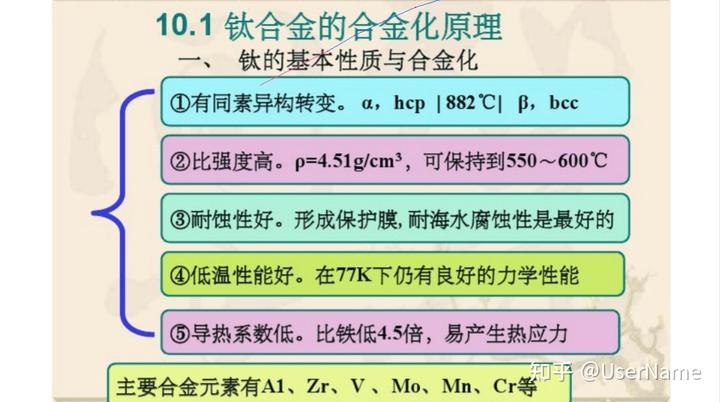
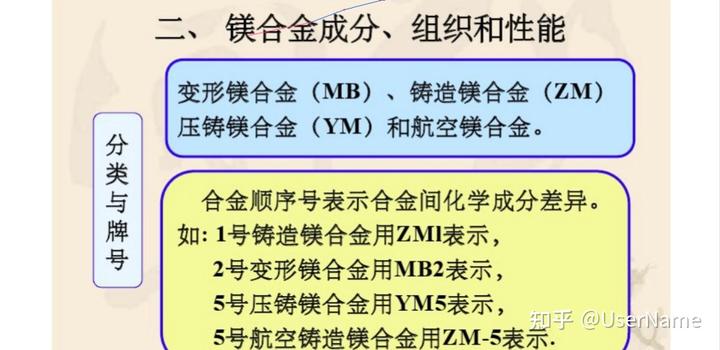
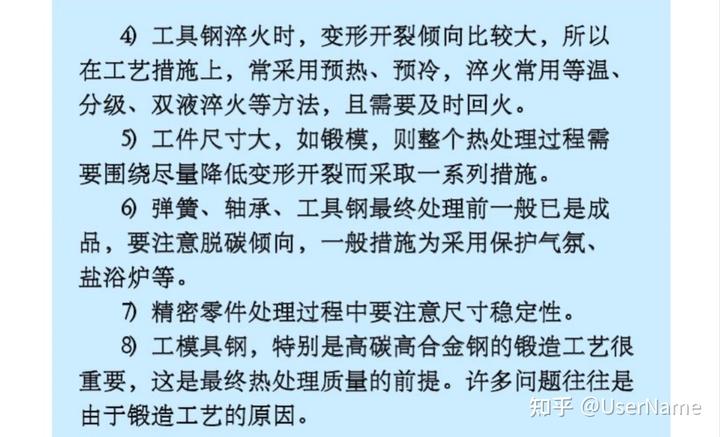
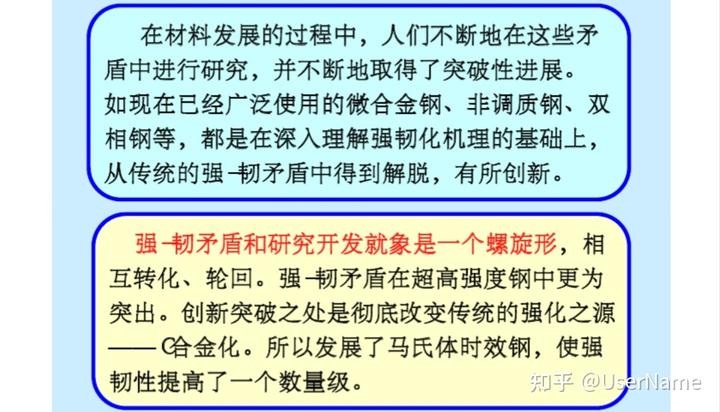
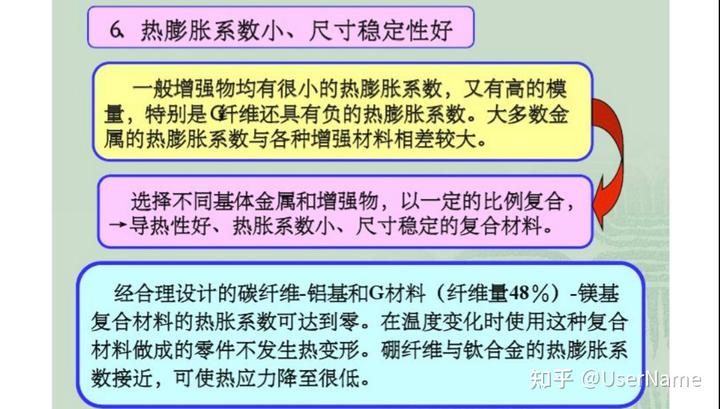
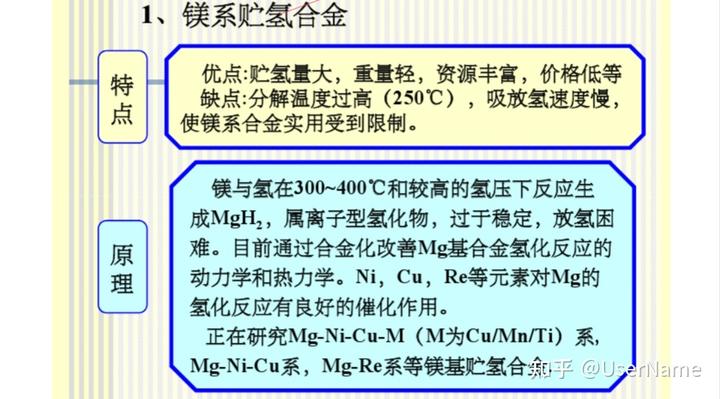
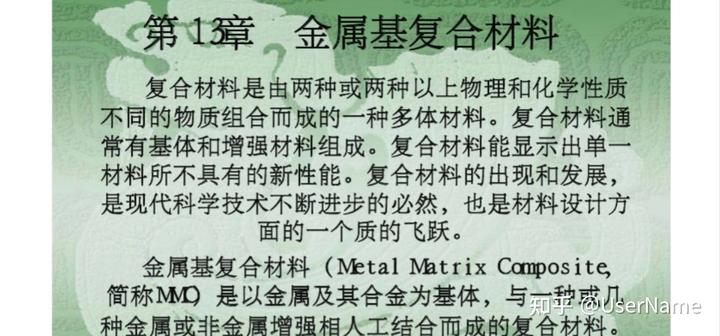
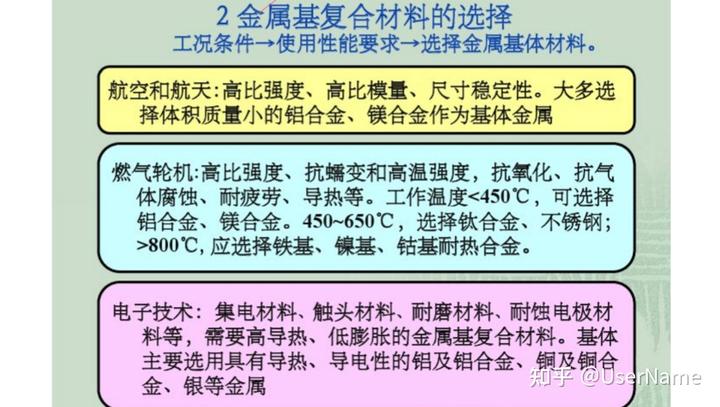
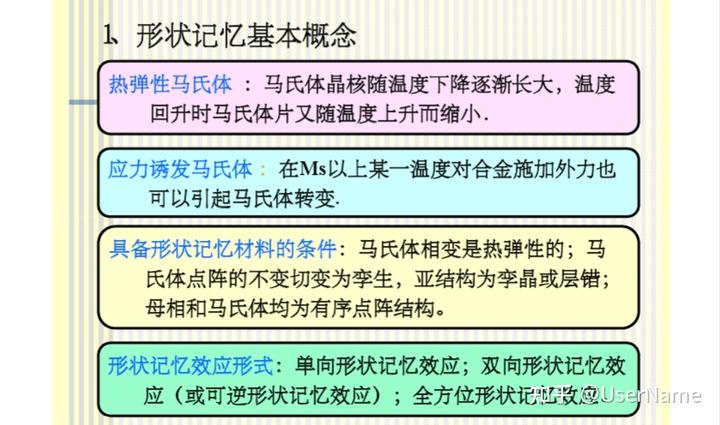
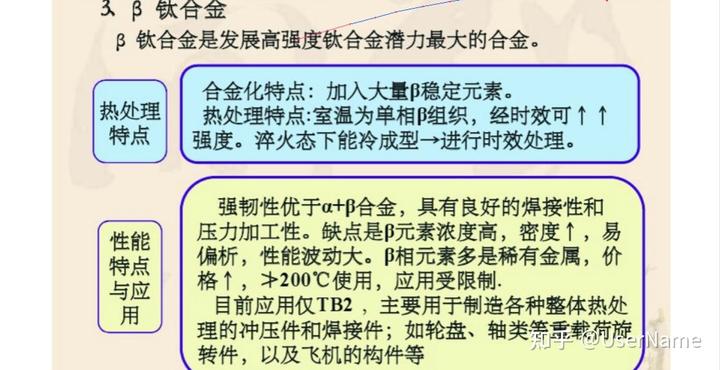
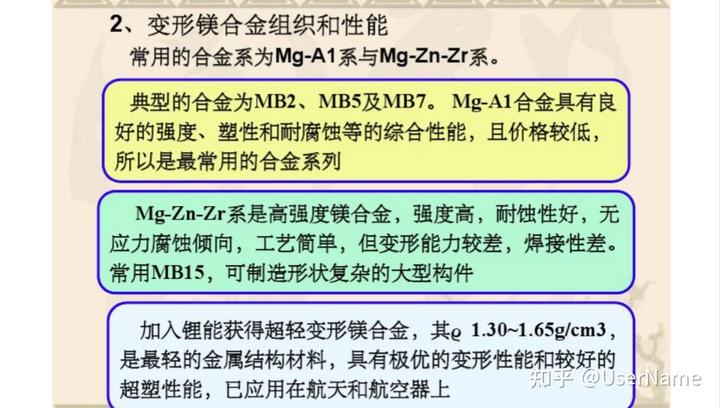
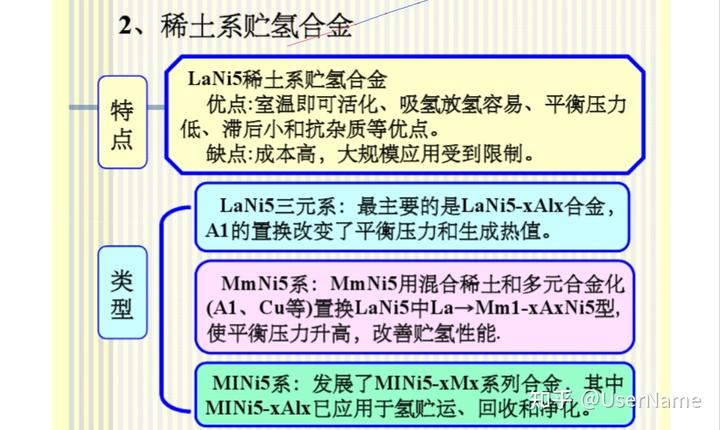
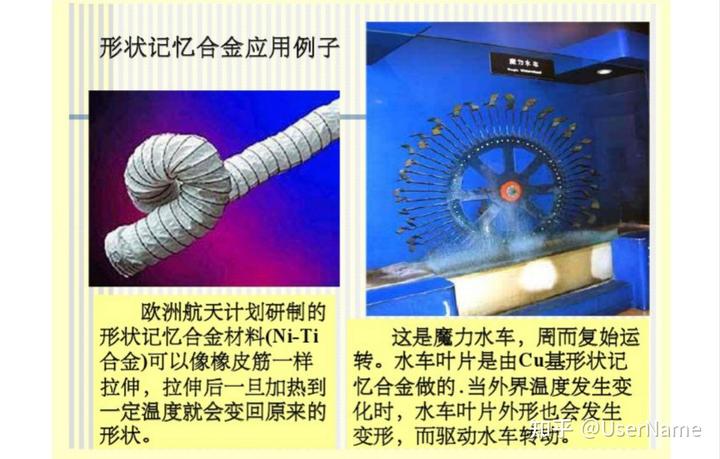
1/31金属材料学习题与思考题
第一章
1.为什么说钢中的S、P杂质元素在一般情况下总是有害的?
答:S、P会导致钢的热脆和冷脆,并且容易在晶界偏聚,导致合金钢的第二类高温回火脆性,高温蠕变时的晶界脆断。
S能形成FeS,其熔点为989℃,钢件在大于1000℃的热加工温度时FeS会熔化,所以易产生热脆;
P能形成FeP,性质硬而脆,在冷加工时产生应力集中,易产生裂纹而形成冷脆。
答:S容易和Fe结合成熔点为989℃的FeS相,会使钢产生热脆性:P和Fe结合形成硬脆的Fe3P相使钢在冷加工过程中产生冷脆性。
2.钢中的碳化物按点阵结构分为哪两大类?各有什么特点?
答:简单点阵结构和复杂点阵结构
简单点阵结构的特点:硬度较高、熔点较高、稳定性较好;
复杂点阵结构的特点:硬度较低、熔点较低、稳定性较差。
3.简述合金钢中碳化物形成规律。
答:①当rc/r>0.59时,形成复杂点阵结构;当rc/r<0.59时,形成简单点阵结构;
②相似者相溶:完全互溶:原子尺寸、电化学因素均相似:有限溶解:一般K都能溶解其它元素,形成复合碳化物。
③NM/Nc比值决定了碳化物类型④碳化物稳定性越好,溶解越难,析出难越,聚集长大也越难:⑤强碳化物形成元素优先与碳结合形成碳化物。
4.合金元素对Fe-C相图的S、E点有什么影响?这种影响意味着什么?
答:凡是扩大y相区的元素均使S、E点向左下方移动,如Mn、Ni;凡是封闭相区的元素均使S、E点向左上方移动,如Cr、Si、Mo。E点左移意味着出现莱氏体的碳含量减小S点左移意味着共析碳含量减小。
5.试述钢在退火态、淬火态及淬火-回火态下,不同合金元素的分布状况。
答:退火态:非碳化物形成元素绝大多数固溶于基体中,而碳化物形成元素视C和本身量多少而定。优先形成碳化物,余量溶入基体。
淬火态:合金元素的分布与淬火工艺有关。溶入A体的因素淬火后存在于M、B中或残余A中,未溶者仍在K中。
回火态:低温回火,置换式合金元素基本上不发生重新分布:>400℃,Me开始重新分布。非K形成元素仍在基体中,K形成元素逐步进入析出的K中,其程度取决于回火温度和时间。6.有哪些合金元素强烈阻止奥氏体晶粒的长大?阻止奥氏体晶粒长大有什么好处?
答:Ti、Nb、V等强碳化物形成元素(好处):能够细化晶粒,从而使钢具有良好的强韧度配合,提高了钢的综合力学性能。
7.哪些合金元素能显著提高钢的淬透性?提高钢的淬透性有何作用?
答:在结构钢中,提高马氏体淬透性作用显著的元素从大到小排列:Mn、Mo、Cr、Si、Ni等。
作用:一方面可以使工件得到均匀而良好的力学性能,满足技术要求;另一方面,在淬火时,
可选用比较缓和的冷却介质,以减小工件的变形与开裂倾向。
8.能明显提高回火稳定性的合金元素有哪些?提高钢的回火稳定性有什么作用?
答:提高回火稳定性的合金元素:Cr、Mn、Ni、Mo、W、V、Si
作用:提高钢的回火稳定性,可以使得合金钢在相同的温度下回火时,比同样碳含量的碳钢具有更高的硬度和强度;或者在保证相同强度的条件下,可在更高的温度下回火,而使韧性更好些。
9.第一类回火脆性和第二类回火脆性是在什么条件下产生的?如何减轻和消除?
答:第一类回火脆性:
脆性特征:①不可逆;②与回火后冷速无关;③断口为晶界脆断。
产生原因:钢在200-350℃回火时,Fe3C薄膜在奥氏体晶界形成,削弱了晶界强度;杂质元素P、S、Bi等偏聚晶界,降低了晶界的结合强度。
防止措施:①降低钢中杂质元素的含量;②用A1脱氧或加入Nb(铌)、V、Ti等合金元素细化奥氏体晶粒;③加入Cr、Si调整温度范围;采用等温淬火代替淬火回火工艺。
第二类回火脆性:
脆性特征:①可逆:②回火后满冷产生,快冷抑制:③断口为晶界脆断。
产生原因:钢在450-650℃回火时,杂质元素Sb、S、As或N、P等偏聚于晶界,形成网状或片状化合物,降低了晶界强度。高于回火脆性温度,杂质元素扩散离开了晶界或化合物分解了;快冷抑制了杂质元素的扩散。
防止措施:①降低钢中的杂质元素;②加入能细化A晶粒的元素(Nb、V、Ti)③加入适量的Mo、W元素;④避免在第二类回火脆性温度范围回火。
10.就合金元素对铁素体力学性能、碳化物形成倾向、奥氏体晶粒长大倾向、淬透性、回火稳定性和回火脆性等几个方面总结下列元素的作用:Si、Mn、Cr、Mo、W、V、Ni。
答:Si:
①Si是铁素体形成元素,固溶强化效果显著:(强度增加,韧性减小)
②Si是非碳化物形成元素,增大钢中的碳活度,所以含Si钢的脱C倾向和石墨化倾向较大③Si量少时,如果以化合物形式存在,则阻止奥氏体晶粒长大,从而细化A晶粒,同时增大了钢的强度和韧性;
④Si提高了钢的淬透性,使工件得到均匀而良好的力学性能。在淬火时,可选用比较缓和的冷却介质,以减小工件的变形与开裂倾向。
⑤Si提高钢的低温回火稳定性,使相同回火温度下的合金钢的硬度高于碳钢
⑥Si能够防止第一类回火脆性。
Mn:
①Mn强化铁素体,在低合金普通结构钢中固溶强化效果较好:(强度增加,韧性减小)
②Mn是奥氏体形成元素,促进A晶粒长大,增大钢的过热敏感性:
③Mn使A等温转变曲线右移,提高钢的淬透性:
④Mn提高钢的回火稳定性,使相同回火温度下的合金钢的硬度高于碳钢:
⑤Mn促进有害元素在晶界上的偏聚,增大钢回火脆性的倾向。
Cr:
①Cr是铁素体形成元素,固溶强化效果显著:(强度增加,韧性减小)
②Cr是碳化物形成元素,能细化晶粒,改善碳化物的均匀性:
③Cr阻止相变时碳化物的形核长大,所以提高钢的淬透性:
④Cr提高回火稳定性,使相同回火温度下的合金钢的硬度高于碳钢;
⑤Cr促进杂质原子偏聚,增大回火脆性倾向
Mo:(W类似于Mo)
①是铁素体形成元素,固济强化效果显着;(强度增加,韧性减小)
②是较强蹊化物形成元素,所以能细化晶粒,改善破化物的均匀性,大大提高钢的回火稳定性;
③阻止奥氏体晶粒长大,细化A品粒,同时增大了钢的强度和韧性;
①能提高你的淬透性,使工件得到均匀而良好的力学性能。在谱火时,可选用比较缓和的冷却介质,以减小工件的变形与开裂倾向
③能有效地抑制有行害元素的儒聚,是消除或减轻钢第二类回火脆性的有效元素。
t(T、Nb 类似于 v)
①是铁素体形成元奈,固洛强化效果显着;(强度增加,韧性减小和)
2②是强碳化物形成元素,形成的 IC质点稳定性好,弥散分布,能有效提高的热强性和回火稳定佳;
③阻止A晶粒长大的作用显著,细化 A品粒,同时增大了钢的强度和切;
D)提高钢的谱透性,消除回火脆性。
4:
①是奥氏体形成元素,促进品粒长大,增大懈的过热教感性;(强度增加,拗性增加)②是非碳化物形成元素,增大钢中的联活度,所以含N 的股C倾向和石墨化倾向较大;③对 A品粒长大的影响不大;
①能提高的淬透性,使工件得到均匀而良好的力学性能。在淬火时,可选用比较缓和的冷却介质,以减小工件的变形与开裂倾向,
③提简回火稳定性,使相同回火温度下的合金钢的硬度高于破钢;
③促进钢中有害元素的偏聚, 增大钢的回火脆性。
总结;CT
Nl
MnMO
W
F的力学增加强
端加强 同上同上
智加强瑁加鱼可上
性能呢度,减小
变、韧性度,减
度、韧
制住小韧佳
f
形成倾非K形中强K
强K 形
非K形
嗨K 形中强k
成元成兀系形成元
形成元成元素成元亲
PO 成 兀
4大大阻
影响不
细化组碍作 阻供转
A h粒长阻碍作
优碍
用中等节中等用中等
大傲向增加增!智加增加
增加
洋庞住增则
增加
回火稳足提高
提同
影响不
提哥低是向提时
提同
温回K
性A
促进降低
9火脆性椎迟低促过大大阵
每低
促进
量回脆,1
优 进高
温回胞
11.根播合金元素在钢中的作用,从淬送性、国火稳定性、奥氏体晶最粒长大倾向、韧性和回火脆性等方面比较下列钢号的性能:40Cr、 40Cri、 40CRmn、40CRNImO
合:①泽透性h:40crNImo-40crmn -40CRNI -40cr
(因为在结构钢中,提高马氏体淬透性作用显著的元素从大到小排列; Mn、 Mo、 C、 st、N,而含金元素的复合作用更大.)
②回火稳定性:40CrNiMo>40CrMn>40CrNi>40Cr
③奥氏体晶粒长大倾向:40CrMn>40Cr>40CrNi>40CrNiMo
④韧性:40CrNiMo>40CrNi>40CrMn>40Cr(Ni能够改善基体的韧度)
⑤回火脆性:40CrNi>40CrMn>40Cr>40CrNiMo(Mo降低回火脆性)
12.为什么W、Mo、V等元素对珠光体转变阻止作用大,而对贝氏体转变影响不大?
答:对于珠光体转变,不仅需要C的扩散和重新分布,而且还需要W、Mo、V等K形成元素的扩散,而间隙原子碳在A中的扩散激活能远小于W、Mo、V等置换原子的扩散激活能,所以W、Mo、V等K形成元素扩散是珠光体转变时碳化物形核的控制因素。
V主要是通过推迟碳化物形核与长大来提高过冷奥氏体的稳定性
W、Mo除了推迟碳化物形核与长大外,还增大了固溶体原子间的结合力、铁的自扩散激活能,减缓了C的扩散。
贝氏体转变是一种半扩散型相变,除了间隙原子碳能作长距离扩散外,W、Mo、V等置换原子都不能显著地扩散。W、Mo、V增加了C在y相中的扩散激活能,降低了扩散系数,推迟了贝氏体转变,但作用比Cr、Mn、Ni小。
13.为什么钢的合金化基本原则是“复合加入”?试举两例说明合金元素复合作用的机理。答:因为合金元素能对某些方面起积极的作用,但许多情况下还有不希望的副作用,因此材料的合金化设计都存在不可避免的矛盾。合金元素有共性的问题,但也有不同的个性。不同元素的复合,其作用是不同的,一般都不是简单的线性关系,而是相互补充,相互加强。所以通过合金元素的复合能够趋利避害,使钢获得优秀的综合性能。
例子:①Nb-V复合合金化:由于Nb的化合物稳定性好,其完全溶解的温度可达1325-1360℃。所以在轧制或锻造温度下仍有未溶的Nb,能有效地阻止高温加热时A晶粒的长大,而V的作用主要是沉淀析出强化。
②Mn-V复合:Mn有过热倾向,而V是减弱了Mn的作用;Mn能降低碳活度,使稳定性很好的VC溶点降低,从而在淬火温度下VC也能溶解许多,使钢获得较好的淬透性和回火稳定性。答:1.提高性能,如淬透性;2.扬长避短,合金元素能对某些方面起积极作用,但往往还有些副作用,为了克服不足,可以加入另一些合金元素弥补,如Si-Mn,Mn-V;3.改善碳化物的类型和分布,某些合金元素改变钢中碳化物的类型和分布或改变其他元素的存在形式和位置,从而提高钢的性能,如耐热钢中Cr-Mo-V,高速钢中V-Cr-W。
14.合金元素V在某些情况下能起到降低淬透性的作用,为什么?而对于40Mn2和42Mn2V,后者的淬透性稍大,为什么?
答:钒和碳、氨、氧有极强的亲和力,与之形成相应的稳定化合物。钒在钢中主要以碳化物的形式存在。其主要作用是细化钢的组织和晶粒,降低钢的强度和韧性。当在高温溶入固溶体时,增加淬透性:反之,如以碳化物形式存在时,降低淬透性。
15.怎样理解“合金钢与碳钢的强度性能差异,主要不在于合金元素本身的强化作用,而在于合金元素对钢相变过程的影响。并且合金元素的良好作用,只有在进行适当的热处理条件下才能表现出来”?
16.合金元素提高钢的韧度主要有哪些途径?
答:①细化奥氏体晶粒—如Ti、V、Mo
②提高钢的回火稳定性—如强K形成元素
③改善基体韧度---------Ni
④细化碳化物--适量的Cr、V
⑤降低或消除钢的回火脆性—W、Mo
⑥在保证强度水平下,适当降低含碳量,提高冶金质量
⑦通过合金化形成一定量的残余奥氏体,利用稳定的残余奥氏体提高钢的韧度
17.40Cr、40CrNi、40CrNiMo钢,其油淬临界淬透直径Dc分别为25-30mm、40-60mm、60-100mm,试解释淬透性成倍增大的现象。
答:在结构钢中,提高马氏体淬透性作用显著的元素从大到小排列:Mn、Mo、Cr、Si、Ni等。Cr、Ni、Mo都能提高淬透性,40Cr、40CrNi、40CrNiMo单一加入到复合加入,淬透性从小到大。较多的Cr和Ni的适当配合可大大提高钢的淬透性,而Mo提高淬透性的作用非常显著。
18.钢的强化机制有哪些?为什么一般钢的强化工艺都采用淬火-回火?
答:四种强化机制:固溶强化、位错强化、细晶强化和第二相弥散强化。
因为淬火+回火工艺充分利用了细晶强化,固溶强化、位错强化、第二相强化这四种强化机制(1)淬火后获得的马氏体是碳在α-Fe中的过饱和间隙固溶体,碳原子起到了间隙固溶强化效应。
(2)马氏体形成后,奥氏体被分割成许多较小的取向不同的区域,产生了细晶强化作用。
(3)淬火形成马氏体时,马氏体中的位错密度增高,从而产生位错强化效应。
(4)淬火后回火时析出的碳化物造成强烈的第二相强化,同时也使钢的韧性得到了改善。
综上所述:无论是碳钢还是合金钢,在淬火-回火时充分利用了强化材料的四种机制,从而使钢的机械性能的潜力得到了充分的发挥。所以获得马氏体并进行相应的回火是钢的最经济最有效的综合强化手段。
答:固溶强化、细晶强化、位错强化、第二相强化。因为一般的钢的强化都要求它有一定的强度的同时又要保持一定韧性,淬火后钢中能够形成M,这给了钢足够的强度,但是带来的后果就是韧度不够,而回火能够在强度降低不大的情况下给淬火钢以足够的韧性,这样能够得到综合力学性能比较优良的材料,所以一般钢的强化工艺都采用淬火加回火。
19.试解释40Cr13已属于过共析钢,而Cr12钢中已经出现共晶组织,属于莱氏体钢。
答:①因为Cr属于封闭y相区的元素,使S点左移,意味着共析碳量减小,所以钢中含有Cr12%时,共析碳量小于0.4%,所以含0.4%C、13%Cr的40Cr13不锈钢就属于过共析钢。②Cr使E点左移,意味着出现莱氏体的碳含量减小。在Fe-C相图中,E点是钢和铁的分界线,在碳钢中是不存在莱氏体组织的。但是如果加入了12%的Cr,尽管含碳量只有2%左右,钢中却已经出现了莱氏体组织。
20.试解释含Mn稍高的钢易过热;而含Si的钢淬火加热温度应稍高,且冷作硬化率较高,不利于冷变形加工。
答:Mn是奥氏体形成元素,降低钢的A1温度,促进晶粒长大,增大钢的过热敏感性:
Si是铁素体形成元素,提高了钢的A1温度,所以含Si钢往往要相应地提高淬火温度。
冷作硬化率高,材料的冷成型性差。合金元素溶入基体,点阵产生不同程度的畸变,使冷作硬化率提高,钢的延展性下降。
21.什么叫钢的内吸附现象?其机理和主要影响因素是什么?
答:合金元素溶入基体后,与晶体缺陷产生交互作用,使这些合金元素发生偏聚或内吸附,使偏聚元素在缺陷处的浓度大于基体中的平均浓度,这种现象称为内吸附现象。
机理:从晶体结构上来说,缺陷处原子排列疏松、不规则,溶质原子容易存在;从体系能量角度上分析,溶质原子在缺陷处的偏聚,使系统自由能降低,符合自然界最小自由能原理。从热力学上说,该过程是自发进行的,其驱动力是溶质原子在缺陷和晶内处的畸变能之差。影响因素:①温度:随着温度的下降,内吸附强烈:
②时间:通过控制时间因素来控制内吸附
③缺陷类型:缺陷越混乱,畸变能之差越大,吸附也越强烈:
④其他元素:不同元素的吸附作用是不同的,也有优先吸附的问题:
⑤点阵类型:基体的点阵类型对间隙原子有影响。
22.试述钢中置换固溶体和间隙固溶体形成的规律
答:置换固溶体的形成的规律:决定组元在置换固溶体中的溶解度因素是点阵结构、原子半径和电子因素,无限固溶必须使这些因素相同或相似
①Ni、Mn、Co与y-Fe的点阵结构、原子半径和电子结构相似,即无限固溶;
②Cr、V与a-Fe的点阵结构、原子半径和电子结构相似,形成无限固溶体;
③Cu和y-Fe点阵结构、原子半径相近,但电子结构差别大——有限固溶:
④原子半径对溶解度影响:AR≤±8%,可以形成无限固溶;≤±15%,形成有限固溶;>土15%,溶解度极小。
间隙固溶体形成的规律:
①间隙固溶体总是有限固溶体,其溶解度取决于溶剂金属的晶体结构和间隙元素的原子尺寸;
②间隙原子在固溶体中总是优先占据有利的位置:
③间隙原子的溶解度随溶质原子的尺寸的减小而增大;
④同一溶剂金属不同的点阵结构,溶解度是不同的,C、N原子在y-Fe中的溶解度高于a-Fe。23.在相同成分的粗晶粒和细晶粒钢中,偏聚元素的偏聚程度有什么不同?
24.试述金属材料的环境协调性设计的思路
答:金属材料的使用,不仅要考虑产品的性能要求,更应考虑材料在生命周期内与环境的协调性。将LCA方法应用到材料设计过程中产生的新概念,它要求在设计时要充分兼顾性能、质量、成本和环境协调性,从环境协调性的角度对材料设计提出指标及建议。
尽量不使用环境协调性不好的元素,即将枯竭性元素和对生态环境及人体有害作用的元素25.什么叫简单合金、通用合金?试述其合金化设计思想及其意义。
答:简单合金:组元组成简单的合金系。
设计化思想:通过选择适当的元素,不含有害元素、不含枯竭元素和控制热加工工艺来改变材料的性能。简单合金在成分设计上有几个特点:合金组元简单,再生循环过程中容易分选原则上不加入目前还不能精炼方法除去的元素;尽量不适用环境协调性不好的合金元素。意义:不含对人体及生态环境有害的元素,不含枯竭性元素,并且主要元素在地球上的储量相当大,并且容易提取。所生产的材料既具有良好的力学性能,又有好的再生循环性。通用合金:是指通过调整元素含量能在大范围内改变材料性能,且元素数最少的合金系。设计思想:合金的种类越多,再生循环就越困难。最理想的情况是所有金属制品用一种合金系来制造,通过改变成分配比改变材料性能。
意义:这种通用合金能满足对材料要求的通用性能,如耐热性、耐腐蚀性和高强度等。合金在具体用途中的性能要求则可以通过不同的热处理等方法来实现。通过调整成分配比开发出性能更加优异、附加值更高的再生材料。
26.与碳素钢相比,一般情况下合金钢有哪些主要优缺点?
答:优点:晶粒细化、淬透性高、回火稳定性好;
缺点:合金元素的加入使钢的冶炼以及加工工艺性能比碳素钢差,价格也较为昂贵。而且回火脆性倾向也较大。第二章
工程结构钢
1.叙述构件用钢一般的服役条件、加工特点和性能要求。
答:服役条件:工程结构件长期受静载荷;互相无相对运动;受大气(海水)侵蚀;有些构件受疲劳冲击;一般在-50~100℃范围内使用;
加工特点是由构件用钢的基本要求和加工工艺决定的,焊接是构成金属结构的常用方法,一般都要经过如剪切、冲孔、热弯、深冲等成型工艺;
性能要求:(1)足够的强度和韧度(2)良好的焊接性和成型工艺性(3)良好的耐腐蚀性
2.低碳钢中淬火时效和应变时效的机理是什么?对构件有何危害?
答:构件用钢加热到Ac1以上淬火或塑性变形后,在放置过程中,强度、硬度上升,塑性韧性下降,韧脆转变温度上升,这种现象分别称为淬火时效和应变时效。
产生的原因:C、N等间隙原子偏聚或内吸附于位错等晶体缺陷处。提高硬度、降低塑性和韧度。
危害:在生产中的弯角、卷边、冲孔、剪裁等过程中产生局部塑形变形的工艺操作,由于应变时效会使局部地区的断裂抗力降低,增加构件脆断的危险性。应变时效还给冷变形工艺造成困难,往往因为裁剪边出现裂缝而报废。
3.为什么普低钢中基本上都含有不大于2.0%w(Mn)?
答:加入Mn有固溶强化作用,每1%Mn能够使屈服强度增加33MPa。但是由于Mn能降低A3温度,使奥氏体在更低的温度下转变为铁素体而有轻微细化铁素体晶粒的作用。Mn的含量过多时,可大为降低塑韧性,所以Mn控制在<2.0%。
4.为什么贝氏体型普低钢多采用0.5%w(Mo)和微量B作为基本合金化元素?
答:钢中的主要合金元素是保证在较宽的冷却速度范围内获得以贝氏体为主的组织。当Mo大于0.3%时,能显著推迟珠光体的转变,而微量的B在奥氏体晶界上有偏析作用,可有效推迟铁素体的转变,并且对贝氏体转变推迟较少。因此Mo、B是贝氏体钢中必不可少的元素。
5.什么是微合金化钢?微合金化元素的主要作用是什么?
答:微合金化钢是指化学成分规范上明确列入需加入一种或几种碳氮化物形成元素的钢中。作用:Nb、V、Ti单元或复合是常用的,其作用主要有细化晶粒组织和析出强化。微合金元素通过阻止加热时奥氏体晶粒长大和抑制奥氏体形变再结晶这两方面作用可使轧制后铁素体晶粒细化,从而具有较好的强韧度配合。
6.在汽车工业上广泛应用的双相钢,其成分、组织和性能特点是什么?为什么能在汽车工业上得到大量应用,发展很快?
答:主要成分:~0.2%C,1.2~1.5%Si,0.8~1.5%Mn,~0.45%Cr,~0.4%Mo,少量V、Nb、Ti。(质量分数)
组织:F+M组织,F基体上分布不连续岛状混合型M(<20%)。
F中非常干净,C、N等间隙原子很少:C和Me大部分在M中
性能特点:低os,且是连续屈服,无屈服平台和上、下屈服;均匀塑变能力强,总延伸率较大,冷加工性能好;加工硬化率n值大,成型后os可达500~700MPa。
因为双相钢具有足够的冲压成型性,而且具备良好的塑性、韧度,一定的马氏体还可以保证提高钢的强度。
7.在低合金高强度工程结构钢中大多采用微合金元素(Nb、V、Ti等),它们的主要作用是什么?
答:Nb、V、Ti单元或复合是常用的,其作用主要有细化晶粒组织和析出强化。微合金元素通过阻止加热时奥氏体晶粒长大和抑制奥氏体形变再结晶这两方面作用可使轧制后铁素体晶粒细化,从而具有较好的强韧度配合。
答:由于Nb、V、Ti的微合金化可以生成弥散的碳化物、氮化物和碳氮化物,它们能钉扎晶界,加热时能阻止A晶粒长大,冷却后可得到细小的F和P,所以在低合金高强度钢
中,常利用Nb、V、Ti合金来细化晶粒。
8.什么是热机械控制处理工艺?为什么这种工艺比相同的成分普通热轧钢有更高的力学综
合性能?
3-1在结构钢的部颁标准中,每个钢号的力学性能都注明热处理状态和试样直径或钢材厚度,为什么?有什么意义?(这个实在不会也查不到,大家集思广益吧!!)
3-2为什么说淬透性是评定钢结构性能的重要指标?
结构钢一般要经过淬火后才能使用。淬透性好坏直接影响淬火后产品质量
3-3调质钢中常用哪些合金元素?这些合金元素各起什么作用?
Mn:1↑淬透性,但↑过热倾向,↑回脆倾向;
Cr:1↑淬透性,↑回稳性,但↑回脆倾向;
Ni:个基体韧度,Ni-Cr复合↑↑淬透性,1回脆;
Mo:↑淬透性,个回稳性,细晶,↓↓回脆倾向:
V:有效细晶,(个淬透性),↓↓过热敏感性。
3-4机械制造结构钢和工程结构钢对使用性能和工艺性能上的要求有什么不同?
工程结构钢:1、足够的强度与韧度(特别是低温韧度):2、良好的焊接性和成型工艺性:3、良好的耐腐蚀性:4、低的成本
机械制造结构钢:1具有良好的力学性能不同零件,对钢强、塑、韧、疲劳、耐磨性等有不同要求2具有良好冷热加工工艺性如锻造、冲压、热处理、车、铣、刨、磨等
3-5低碳马氏体钢在力学性能和工艺性上有哪些优点?在应用上应注意些什么问题?
力学性能:抗拉强度a,1150~1500MPa;屈服强度a,950~1250MPa240%;伸长率6,≥10%;冲击韧度A26。这些性能指标和中碳合金调质钢性能相当,常规的力学性能甚至优于调质钢。
工艺性能:锻造温度淬火加自回火
局限性:工作温度<200℃;强化后难以进行冷加工焊接等工序;只能用于中小件;淬火时变形大,要求严格的零件慎用
3-6某工厂原来使用45MnNiV生产直径为8mm高强度调质钢筋,要求Rm>1450Mpa,ReL>1200Mpa,A>0.6%,热处理工艺是(920±20)℃油淬,(470±10)℃回火。因该钢缺货,库存有25MnSi钢。请考虑是否可以代用。热处理工艺如何调整?能代替,900℃油淬或水淬,200℃回火
3-7试述弹簧的服役条件和对弹簧钢的主要性能要求。为什么低合金弹簧钢中碳含量一般在0.5%0.75%(质量分数)之间?
服役条件:储能减振、一般在动负荷下工作即在冲击、振动和长期均匀的周期改变应力下工作、也会在动静载荷作用下服役:
性能要求:高的弹性极限及弹性减退抗力好,较高的屈服比:高的疲劳强度、足够的塑性和韧度:工艺性能要求有足够的淬透性:在某些环境下,还要求弹簧具有导电、无磁、耐高温和耐蚀等性能,良好的表面质量和冶金质量
总的来说是为了保证弹簧不但具有高的弹性极限、高的屈服极限和疲劳极限(弹簧钢含碳量要比调质钢高),还要有一定的塑性和韧性(含碳量太高必然影响塑性和韧性了)
3-8弹簧为什么要求较高的冶金质量和表面质量?弹簧的强度极限高是否也意味着弹簧的疲劳极限高,为什么?
要严格控制弹簧钢材料的内部缺陷,要保证具有良好的冶金质量和组织均匀性;因为弹簧工作时表面承受的应力为最大,所以不允许表面缺陷,表面缺陷往往会成为应力高度
集中的地方和疲劳裂纹源,显著地降低弹簧的疲劳强度
不一定高。强度极限是在外力作用下进一步发生形变.是保持构件机械强度下能承受的最大应力,包括拉伸、压缩和剪切强度,不一定指弹性极限
3-9有些普通弹簧冷卷成型后为什么进行去应力退火?车辆用板簧淬火后,为什么要用中温回火?
去应力退火的目的是:
a)消除金属丝冷拔加工和弹簧冷卷成形的内应力;
b)稳定弹簧尺寸,利用去应力退火来控制弹簧尺寸
c)提高金属丝的抗拉强度和弹性极限;
回火目的:(1)减少或消除淬火内应力,防止工件变形或开裂
(2)获得工艺要求的力学性能。
(3)稳定工件尺寸
回火工艺选择的依据是弹性参数和韧性参数的平衡和配合
3-10大型弹簧为什么要先成形后强化,小型弹簧先强化后成形?
为了方便成型,大弹簧强化后就很难改变形状了,所以要先成型再强化。反之小弹
簧就可以先强化再成型
3-11直径为25mm的40CrNiMo钢棒料,经正火后难切削为什么?
40CrNiMo属于调质钢,正火得到的应该是珠光体组织。由于该钢的透性较好,空冷就能得到马氏体,不一定是全部,只要部分马氏体就会使硬度提高很多,而变得难以切削。
3-12钢的切削加工型与材料的组织和硬度之间有什么关系?为获得良好的切削性,中碳钢和高碳钢各自经过怎样的热处理,得到什么样的金相组织?
硬度由高到低的组织:马氏体、珠光体和铁素体,硬度高切削性能差。
中碳钢:淬火加高温回火,回火后得回火索氏体
高碳钢:淬火加低温回火,回火后得回火马氏体少量碳化物和残余奥氏体
3-13用低淬钢做中、小模数的中、高频感应加热淬火齿轮有什么特点?
不改变表面化学成分,表面硬化而心部仍然保持较高的塑性和韧度;表面局部加热,零件的淬火变形小;加热速度快,可消除表面脱碳和氧化现象;在表面形成残余压应力,提高疲劳强度。小齿轮:得到沿着轮廓分布硬化层→“仿形硬化”(关键)
3-14滚动轴承钢常含哪些元素、为什么含Cr量限制在一定范围?
①高碳、铬、硅、锰等合金元素
②它可以提高淬透性、回火稳定性、硬度、耐磨性、耐蚀性。但如果质量分数过大(大于1.65%)会使残余奥氏体增加,使钢的硬度、尺寸稳定性降低,同时增加碳化物的不均匀性,降低钢的韧性
3-15滚动轴承钢对冶金质量、表面质量和原始组织有那些要求,为什么?
要求:纯净和组织均匀,不允许缺陷存在
原因:1轴承钢的接触疲劳寿命随钢中的氧化物级别增加而降低;非金属夹杂物可破坏
基体的连续性,容易引起应力集中,可达很高数值:2碳化物的尺寸和分布对轴承的
接触疲劳寿命也有很大影响:大颗粒碳化物具有高的硬度和脆性、密集的碳化物影响
钢的冷热加工性,降低钢的冲击韧度
3-16滚动轴承钢原始组织中碳化物的不均匀性有哪几种情况?应如何改善或消除?
液析碳化物、带状碳化物和网状碳化物
消除措施:液析碳化物:采用高温扩散退火,一般在1200℃进行扩散退火
带状碳化物:需要长时间退火
网状碳化物:控制中扎或终锻温度、控制轧制后冷速或正火
3-17在使用状态下,的最佳组织是什么?在工艺上应如何保证?
组织特点:细小均匀的奥氏体晶粒度5~8级:M中含0.5~0.6%C:隐晶M基体上分布细小均匀的粒状K,体积分数约7~8%,一般可有少量A
热处理工艺:球化退火一为最终淬火作组织准备;淬回火工艺参数对疲劳寿命有很大影响:一般采用保护气氛加热或真空加热:160℃保温3h或更长回火,硬度62~66HRC;如要求消除A→淬火后立即冷处理,而后立即低温回火。
3-18分析机床主轴的服役条件、性能要求。按最终热处理工艺分类机床主轴有哪几种?每种主轴可选用那些钢号?其冷热加工工艺路线是怎样的?
服役条件:①传递扭矩,交变性,有时会承受弯曲、拉压负荷:②都有轴承支承,轴颈处受磨损,需要较高的硬度,耐磨性好:③大多数承受一定的冲击和过载
性能要求:足够的强度;一定的韧度和耐磨性
分类:轻载主轴:采用45钢,整体经正火或调质处理,轴颈处高频感应加热淬火;中载主轴:一般用40Cr等制造,进行调质处理,轴颈处高频感应加热淬火。如冲击力较大,也可用20Cr等钢进行渗碳淬火
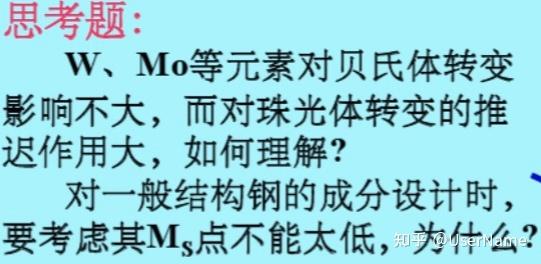
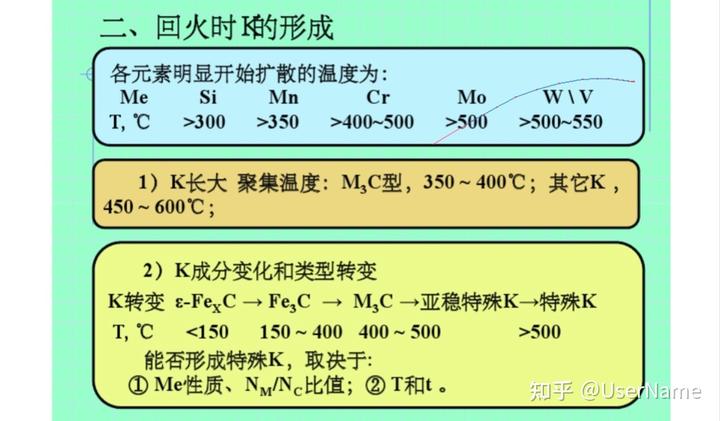
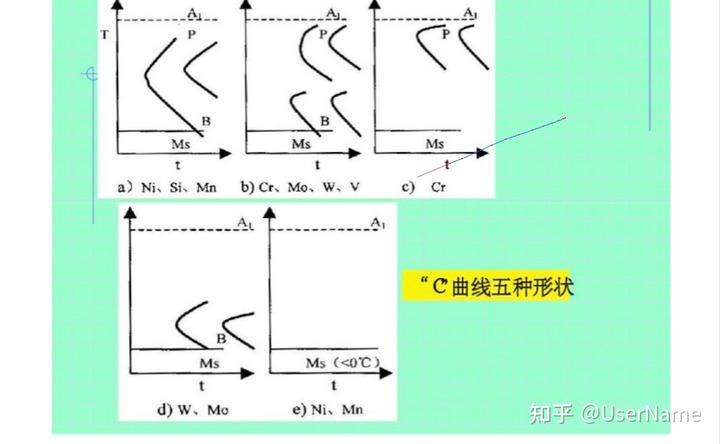
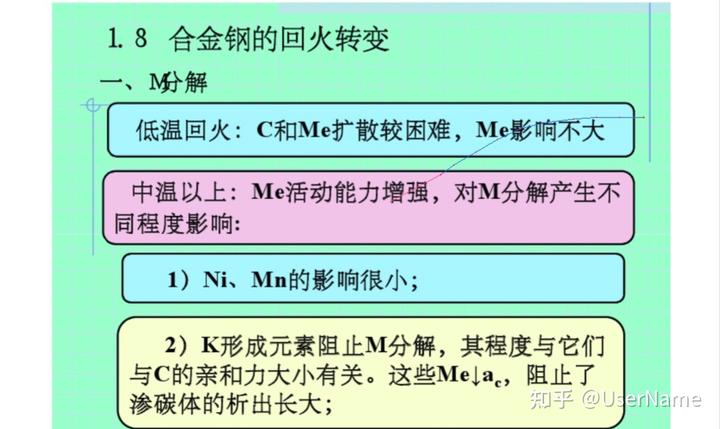
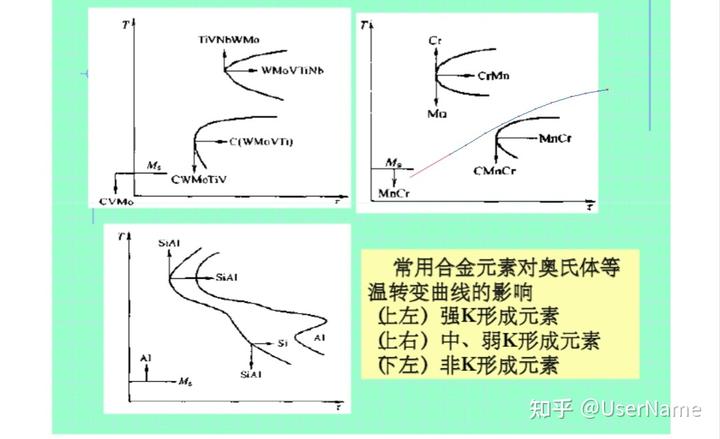
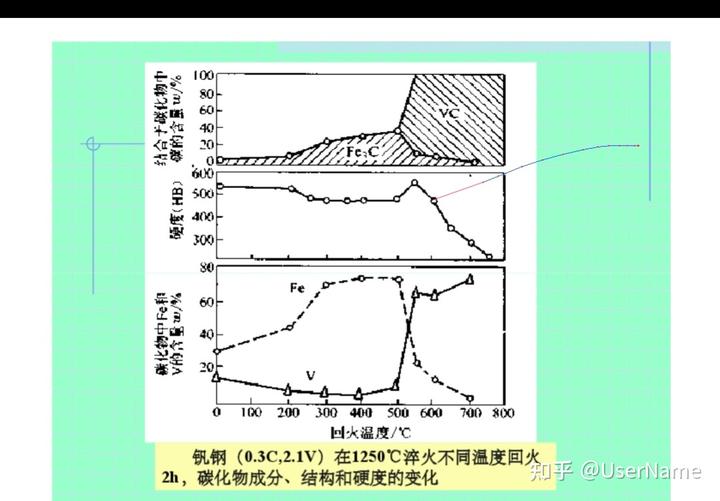
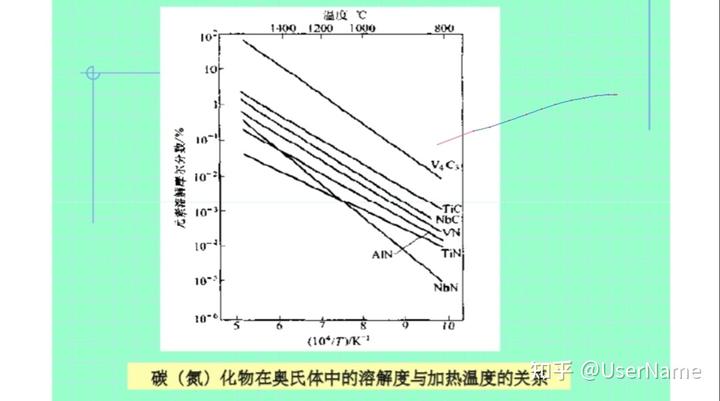
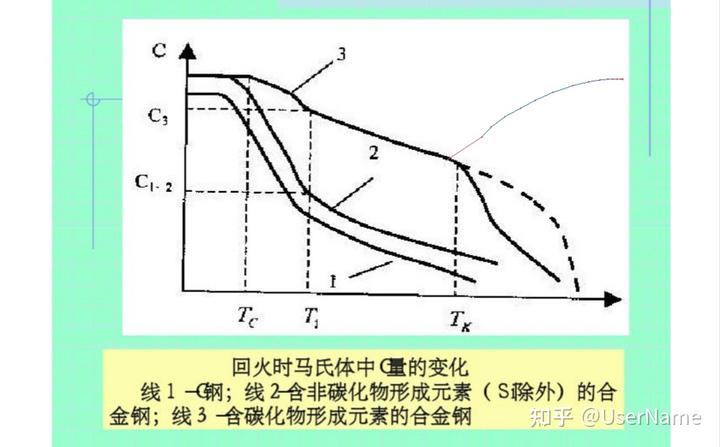
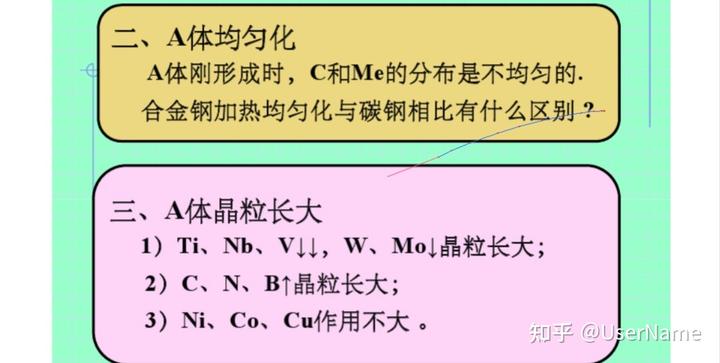
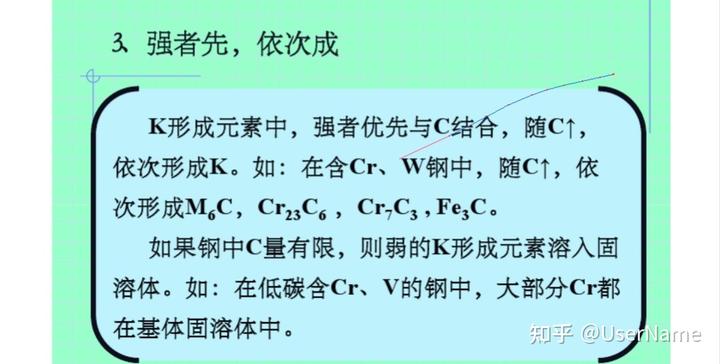
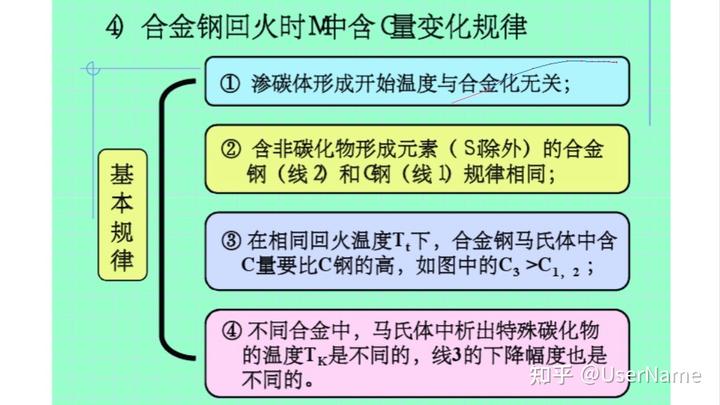
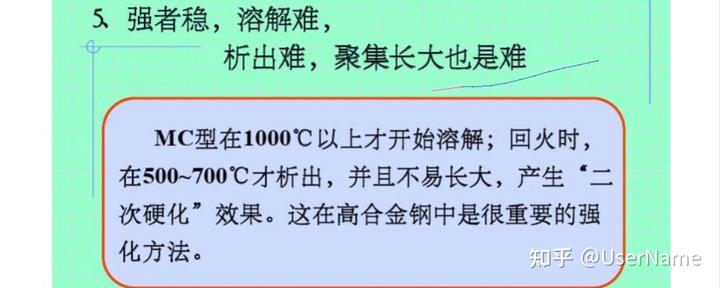
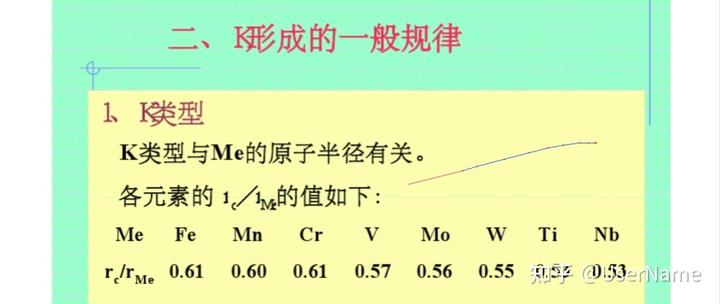
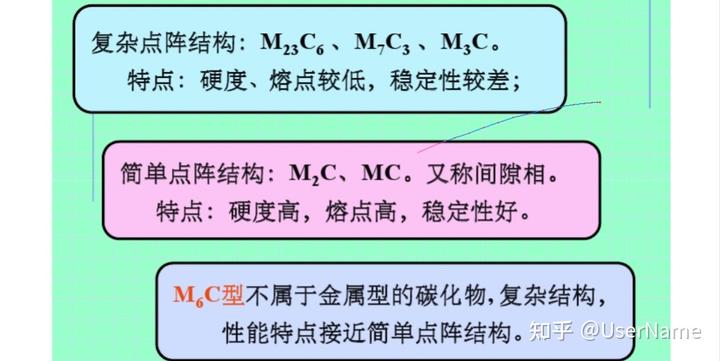
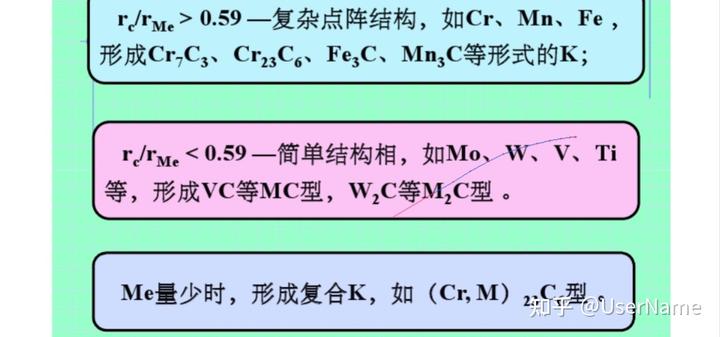
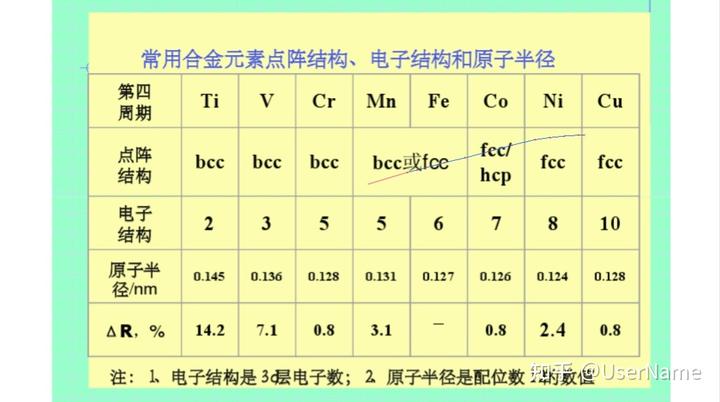
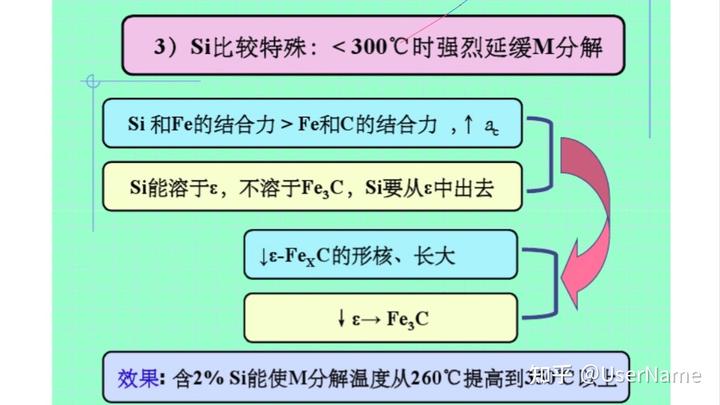
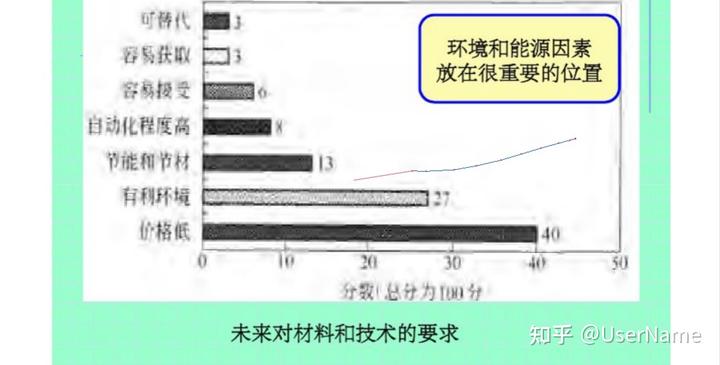
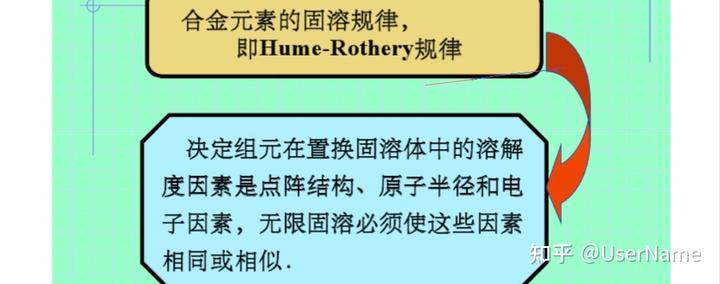
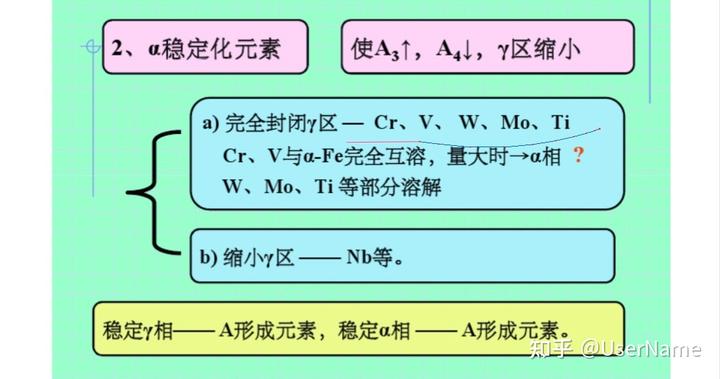

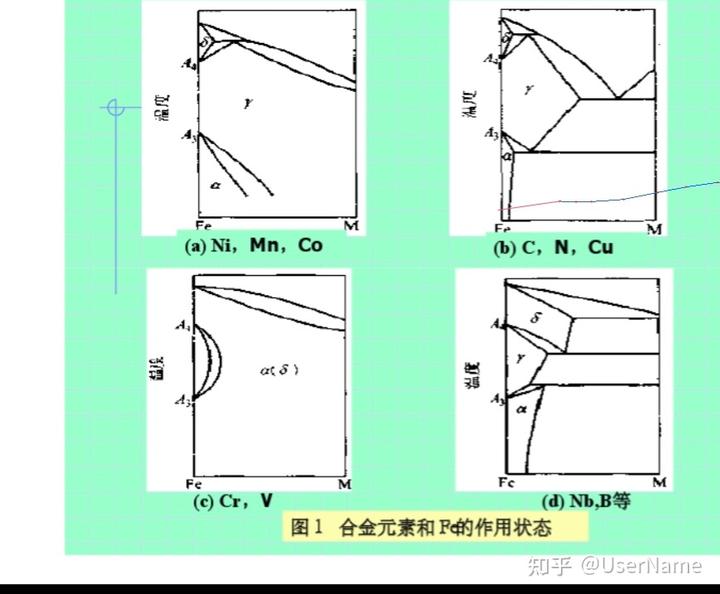
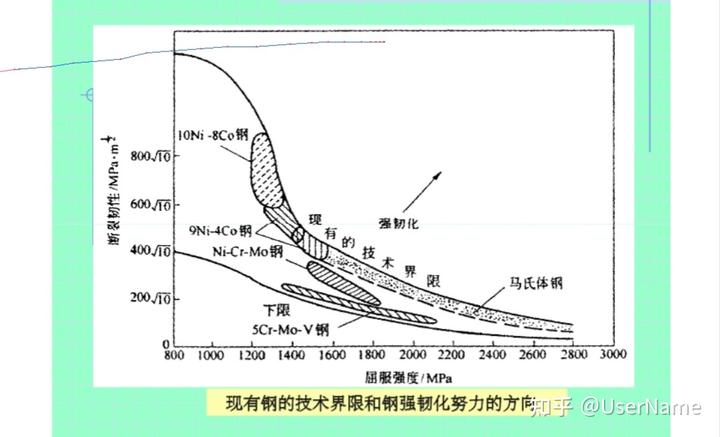
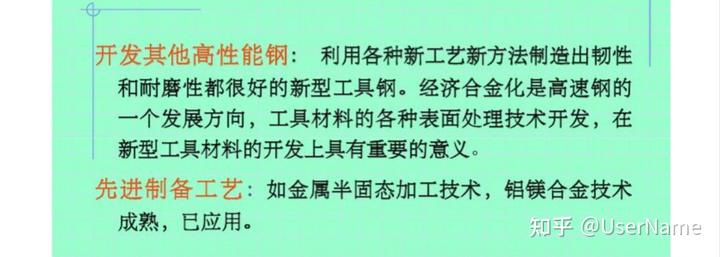
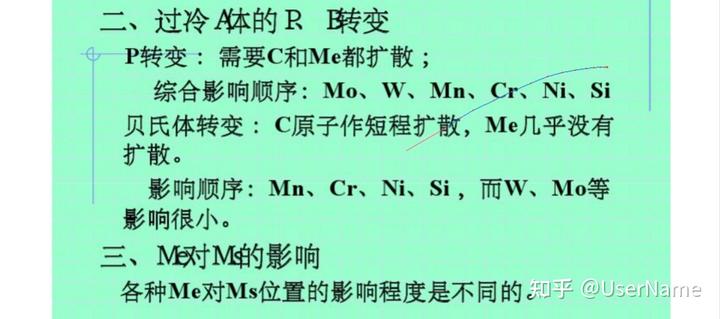
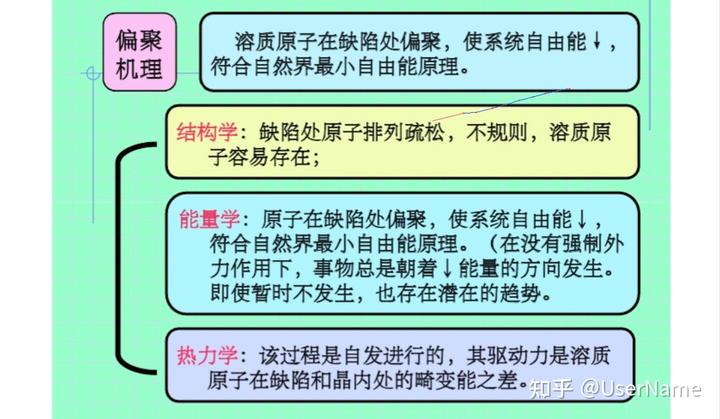
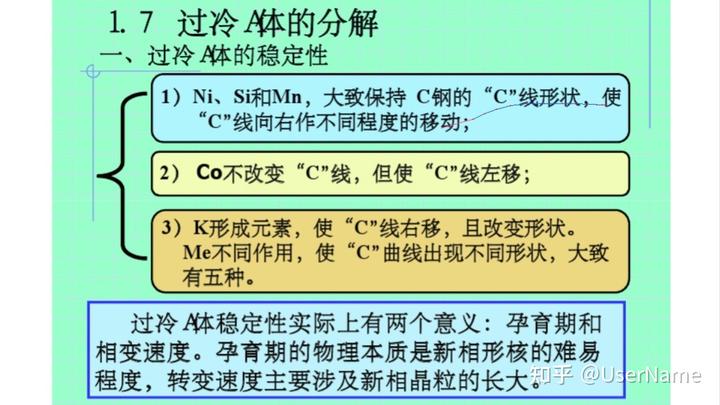
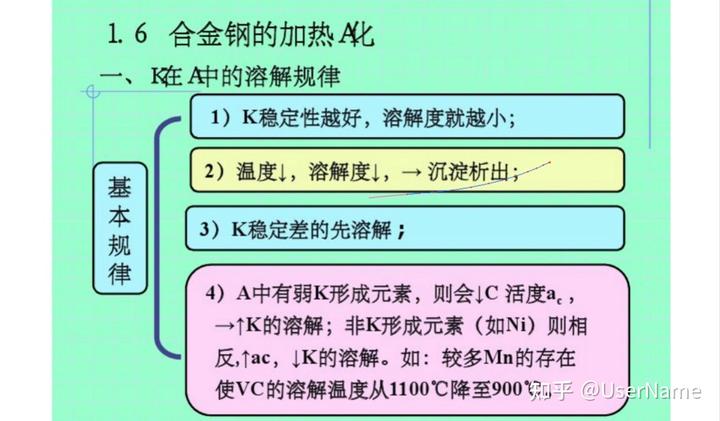
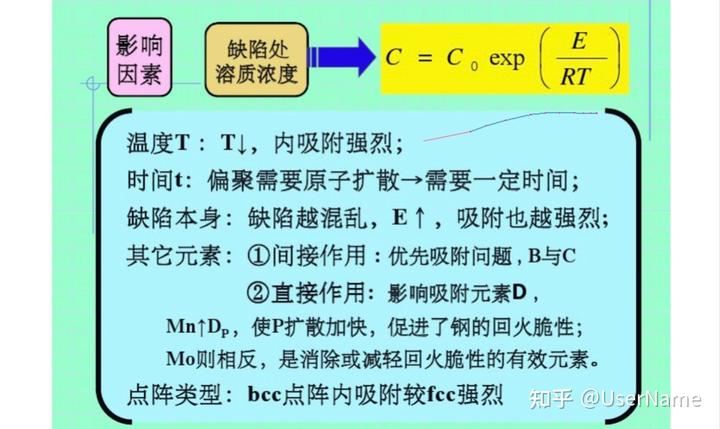
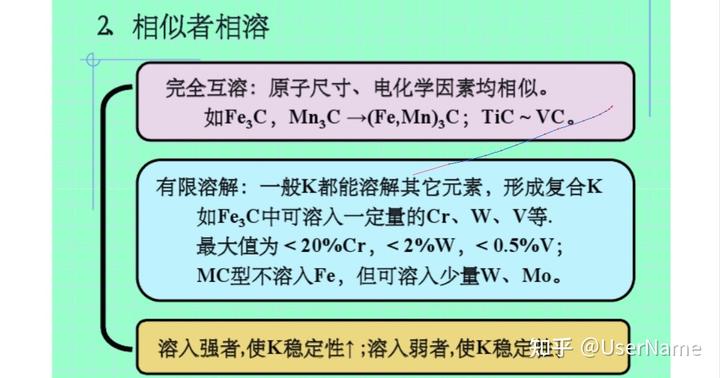
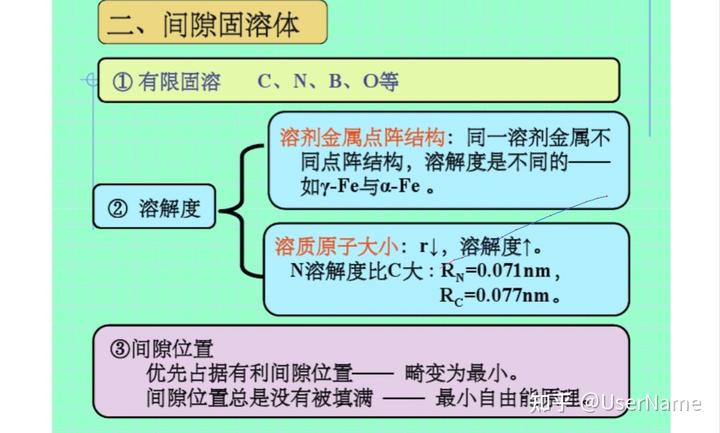
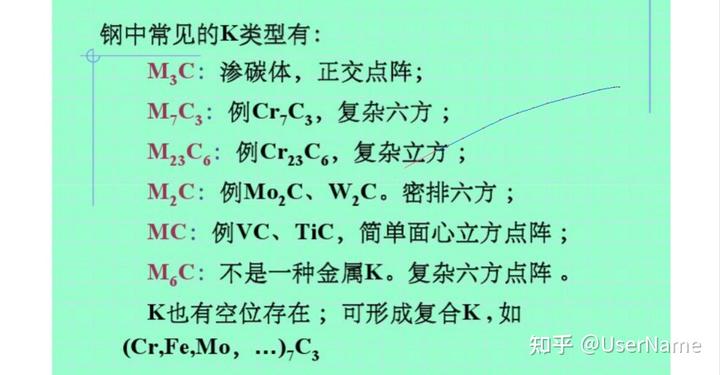
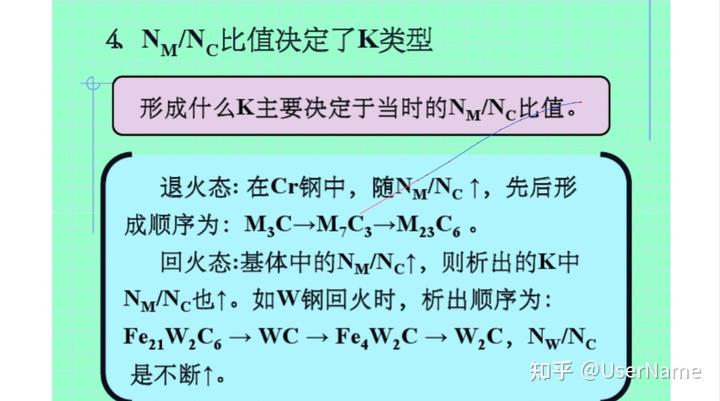
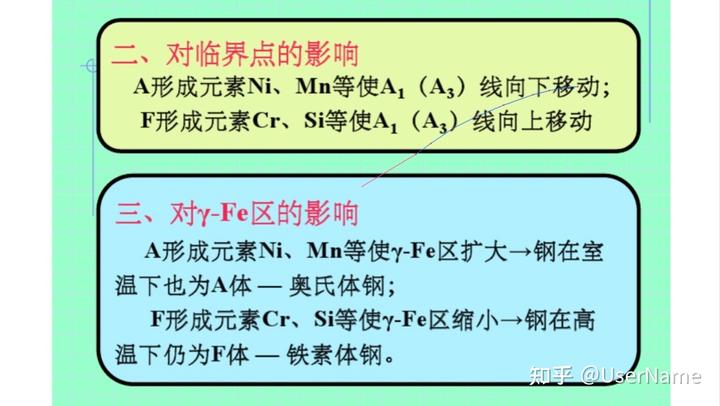
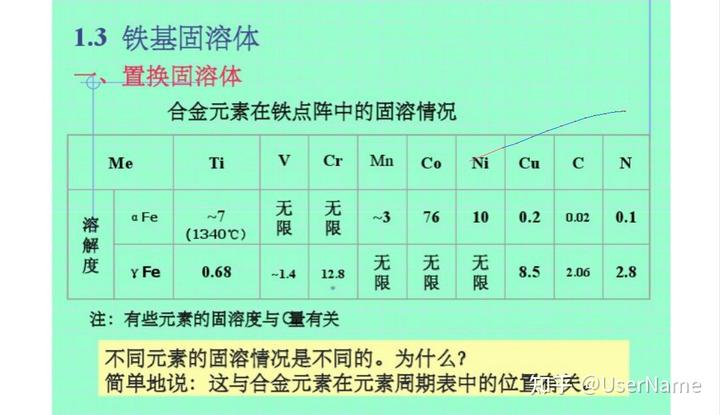
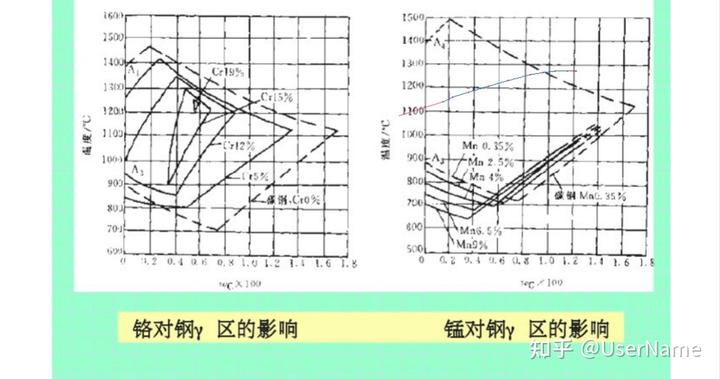
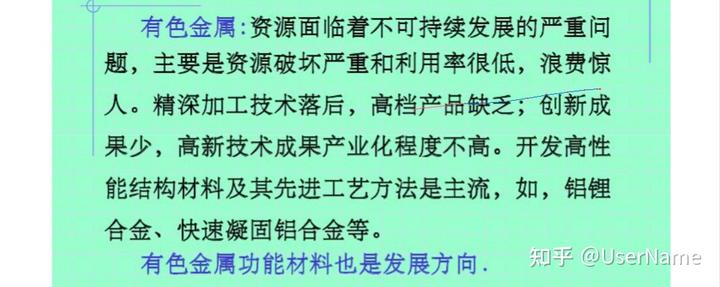

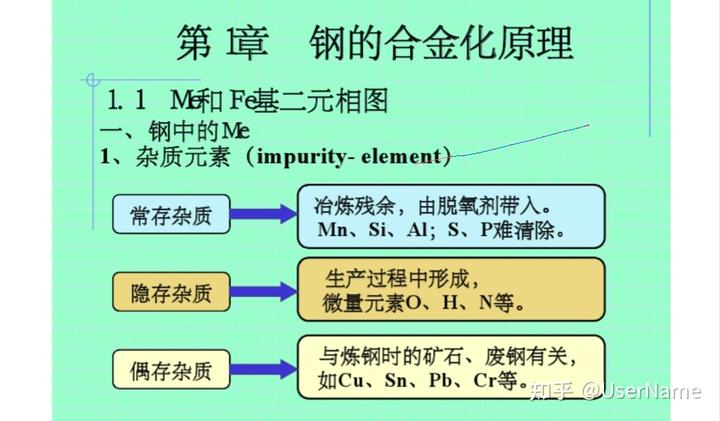
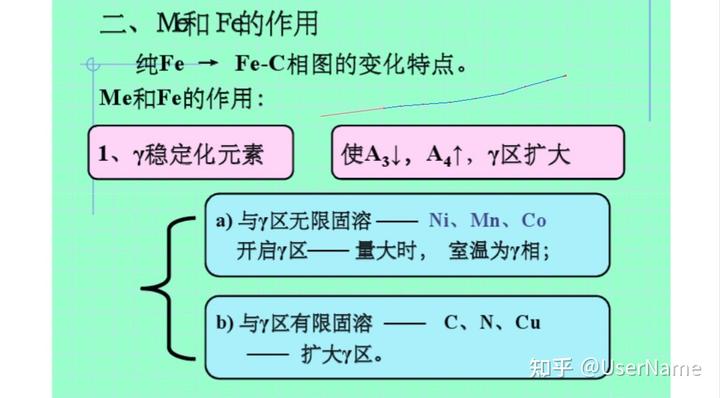
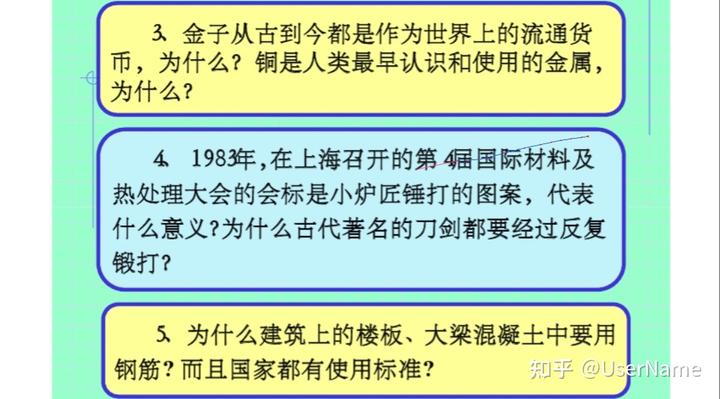
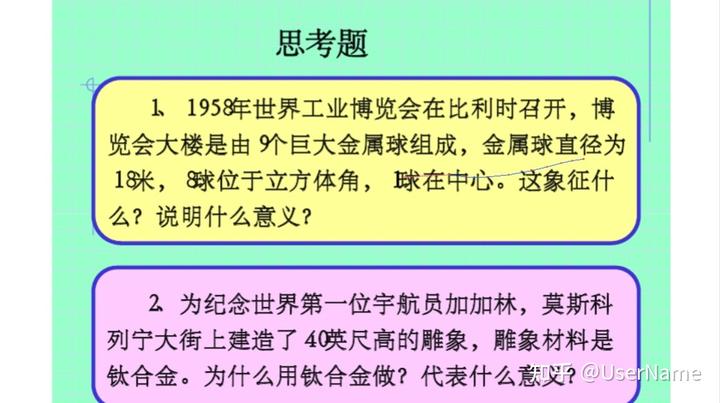
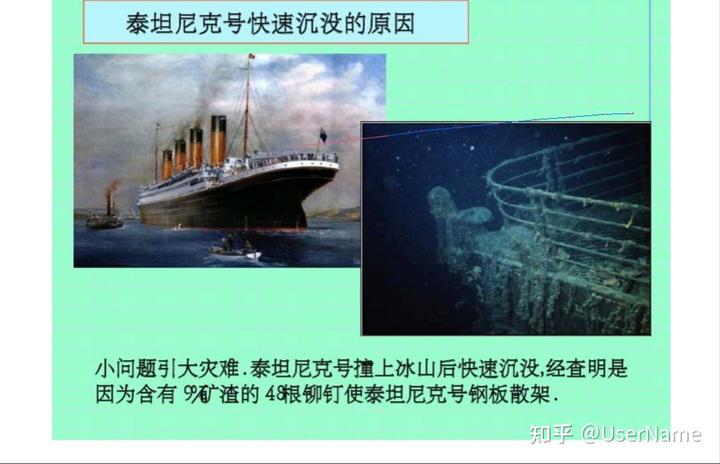
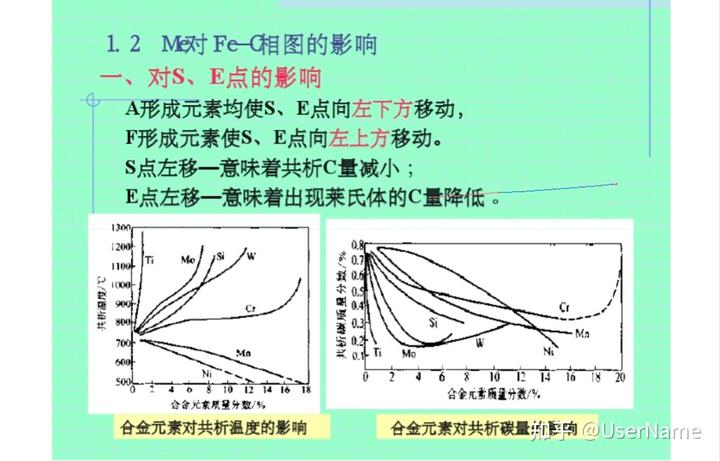
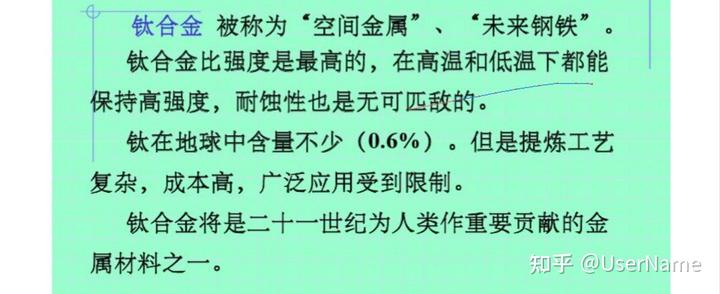
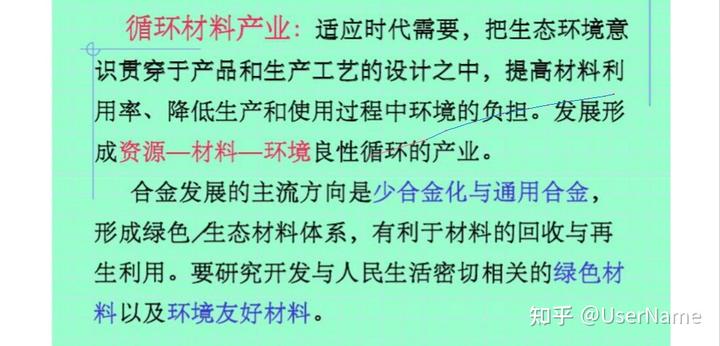
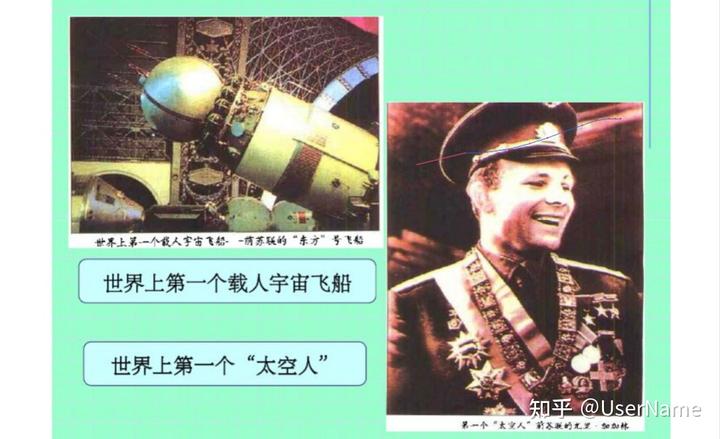
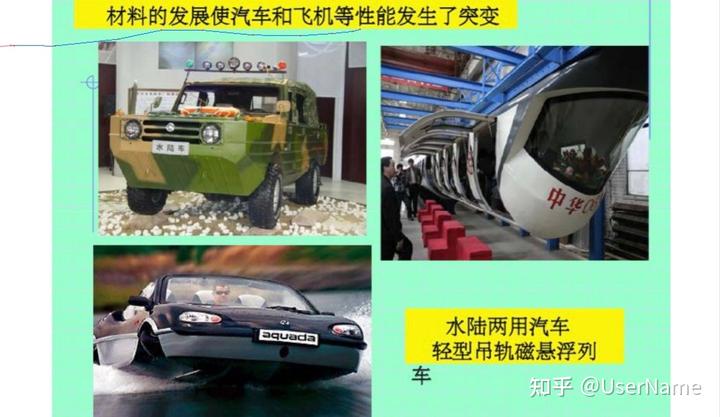
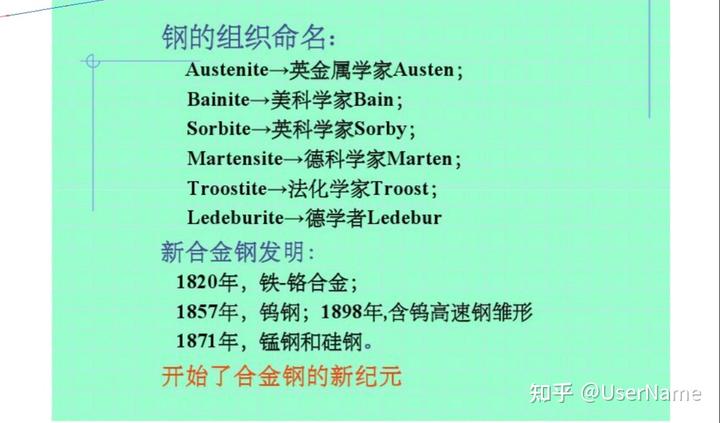
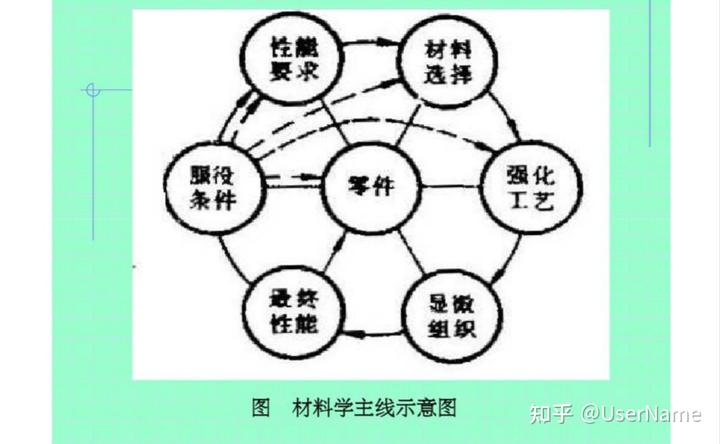
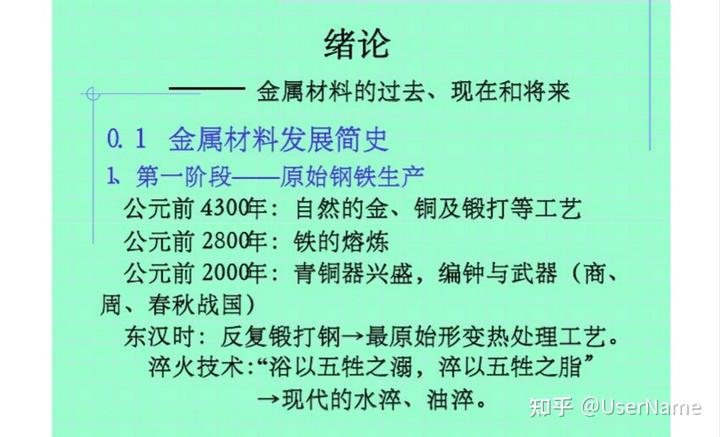
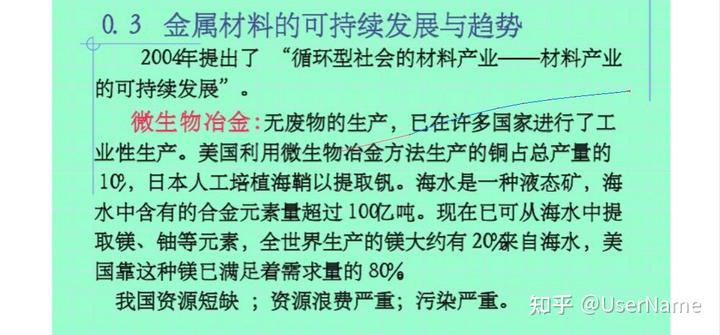
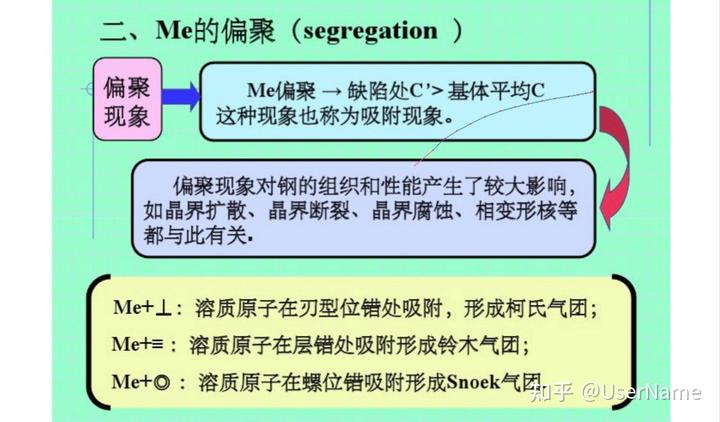
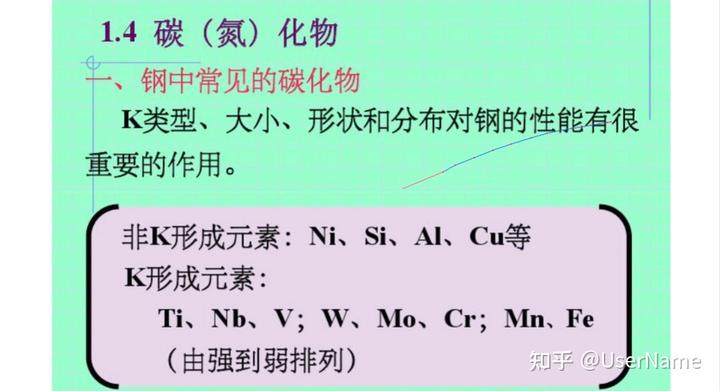
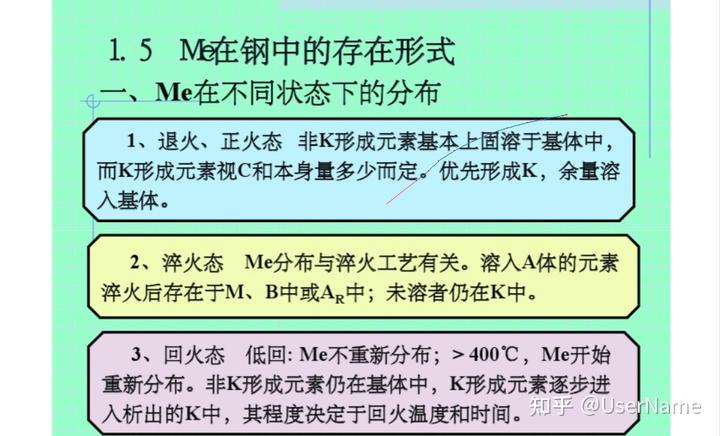
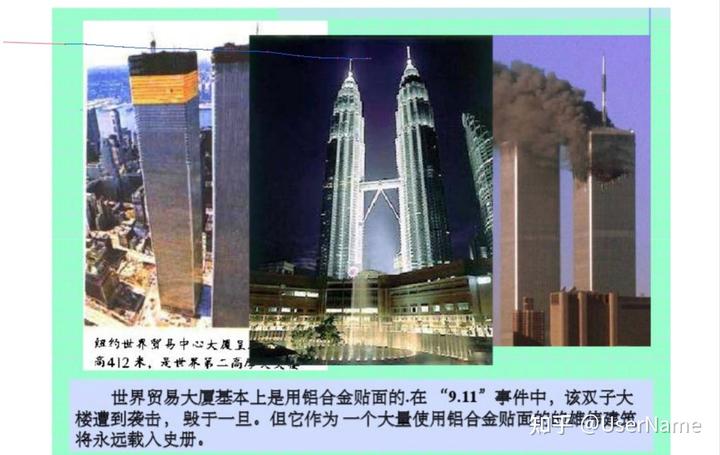
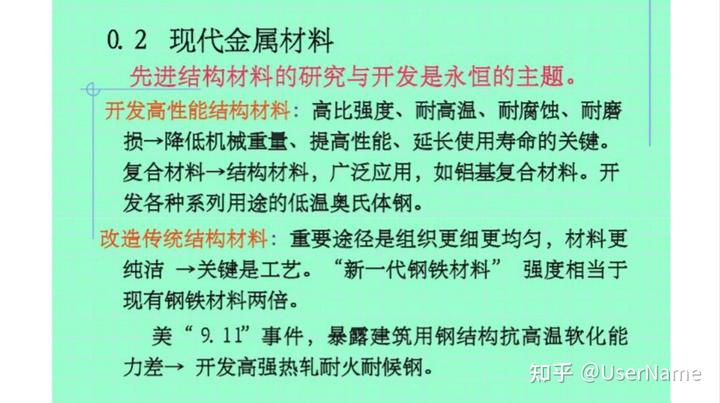

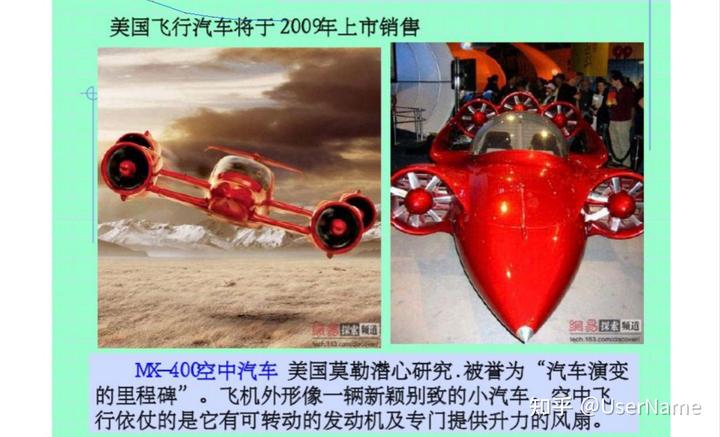
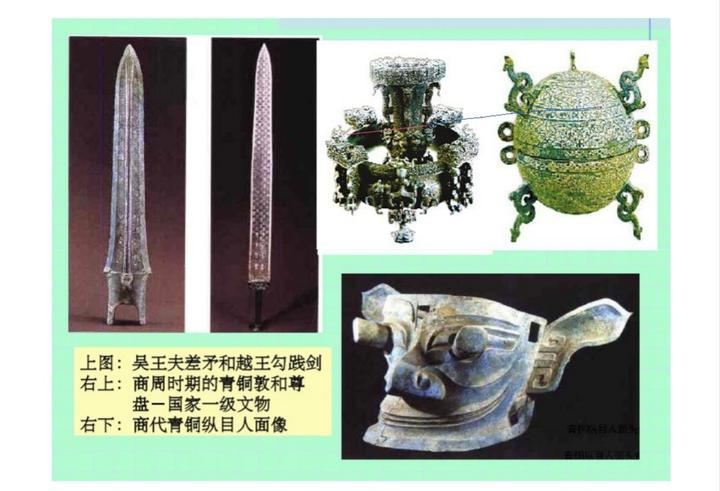
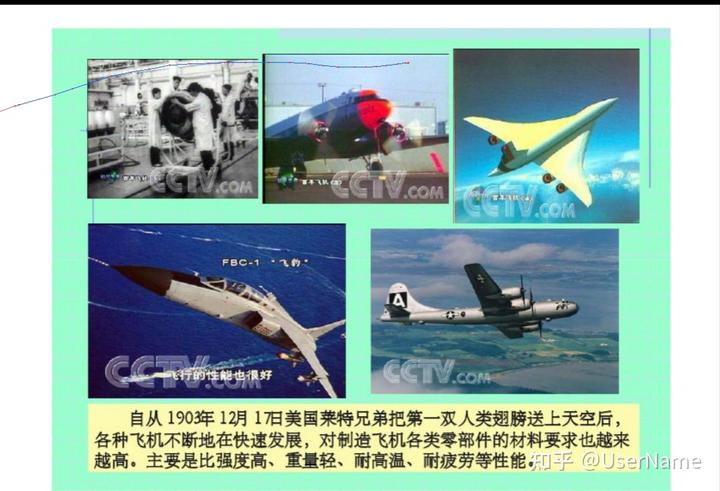
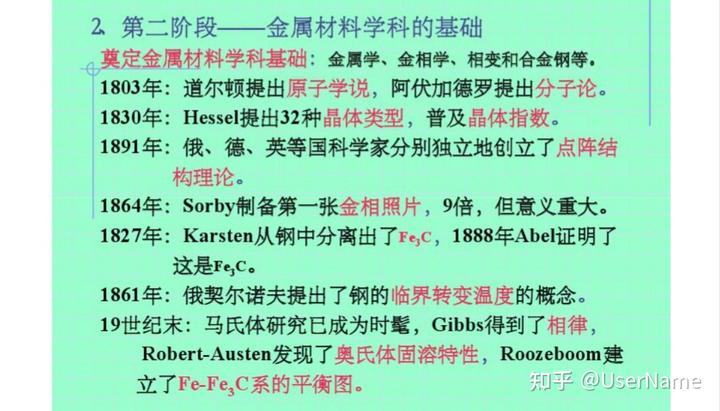
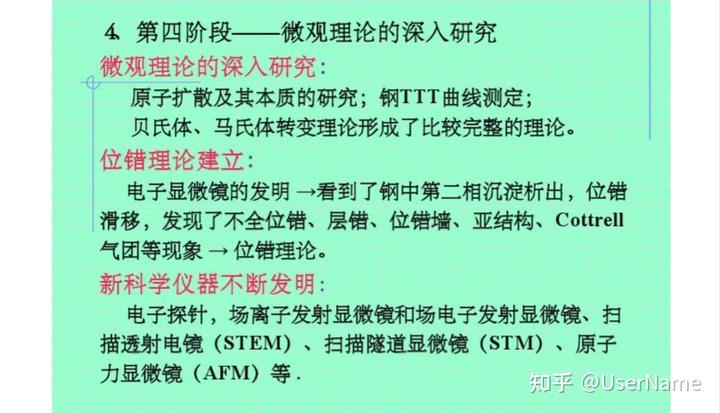
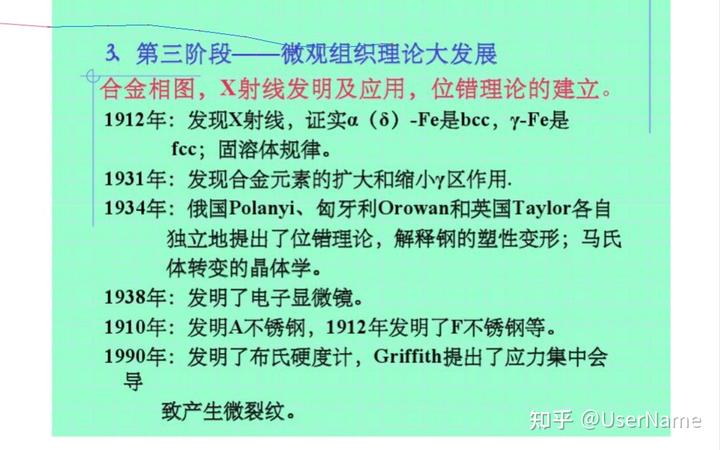
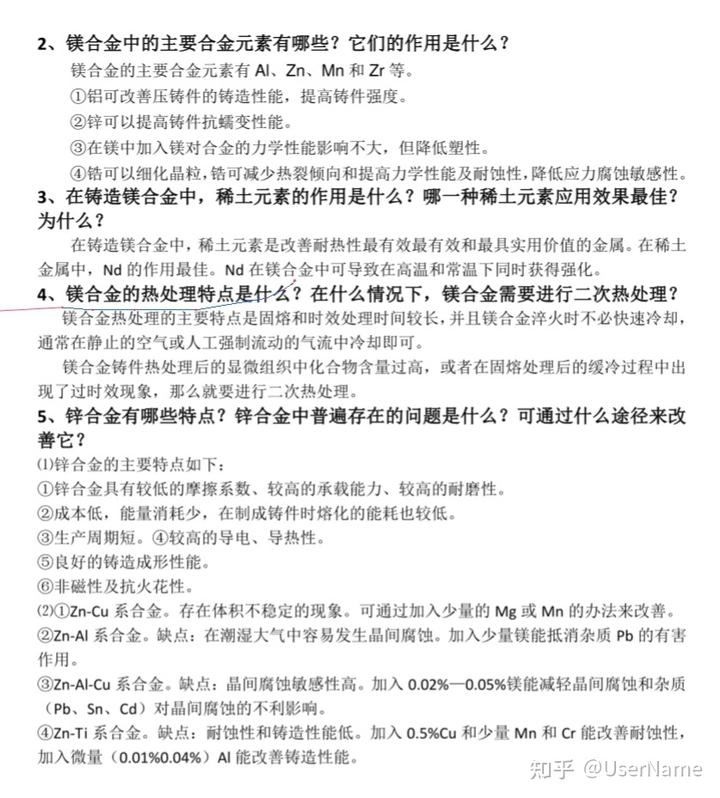
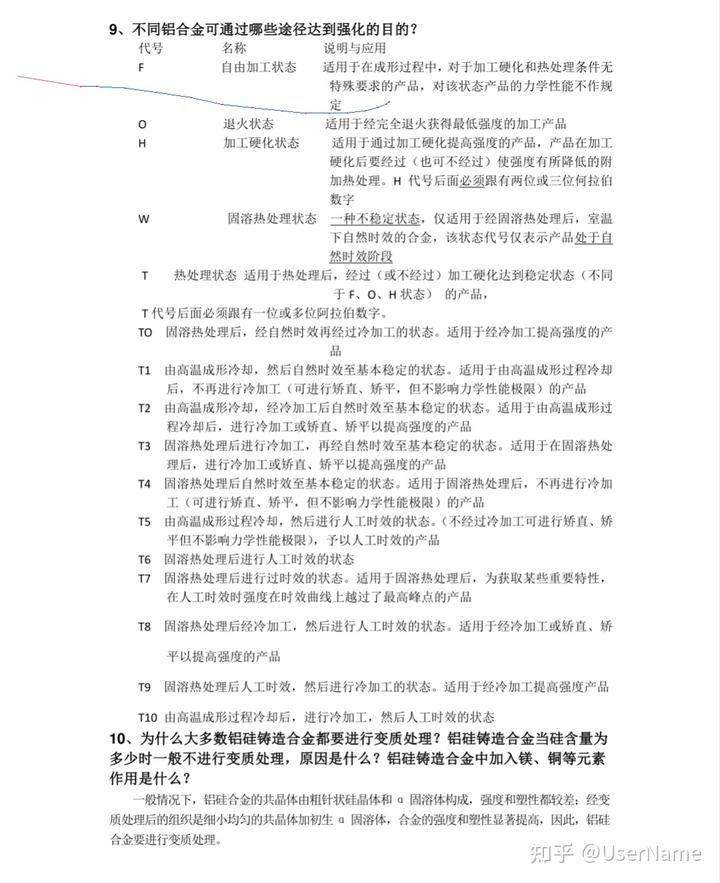
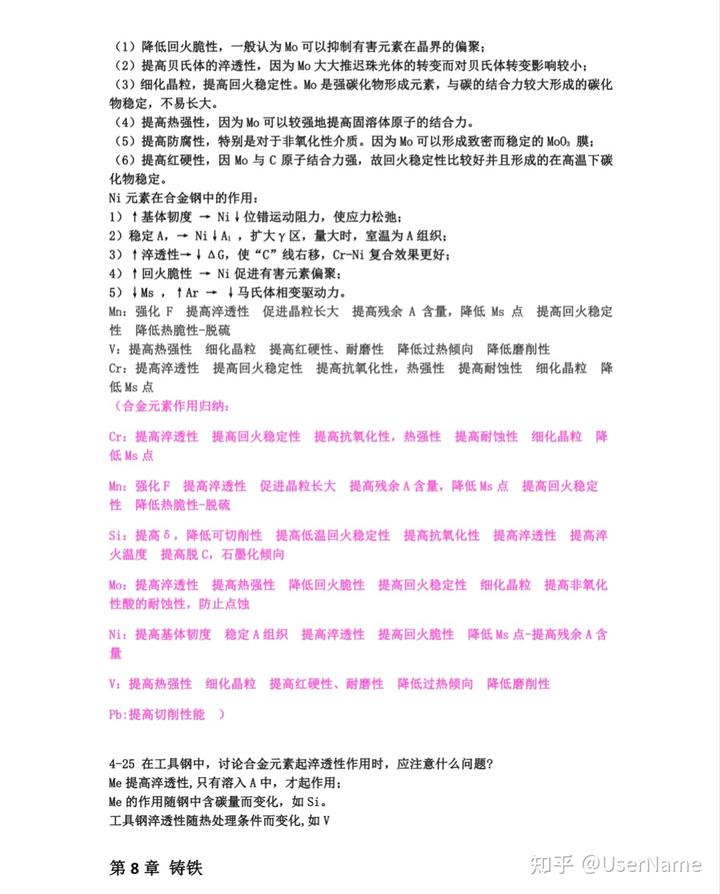
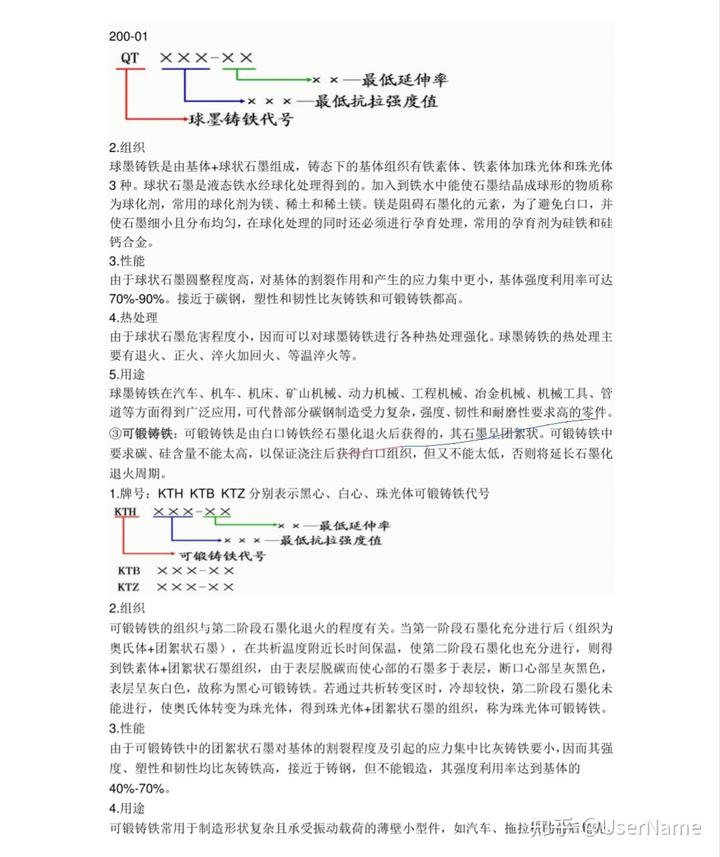
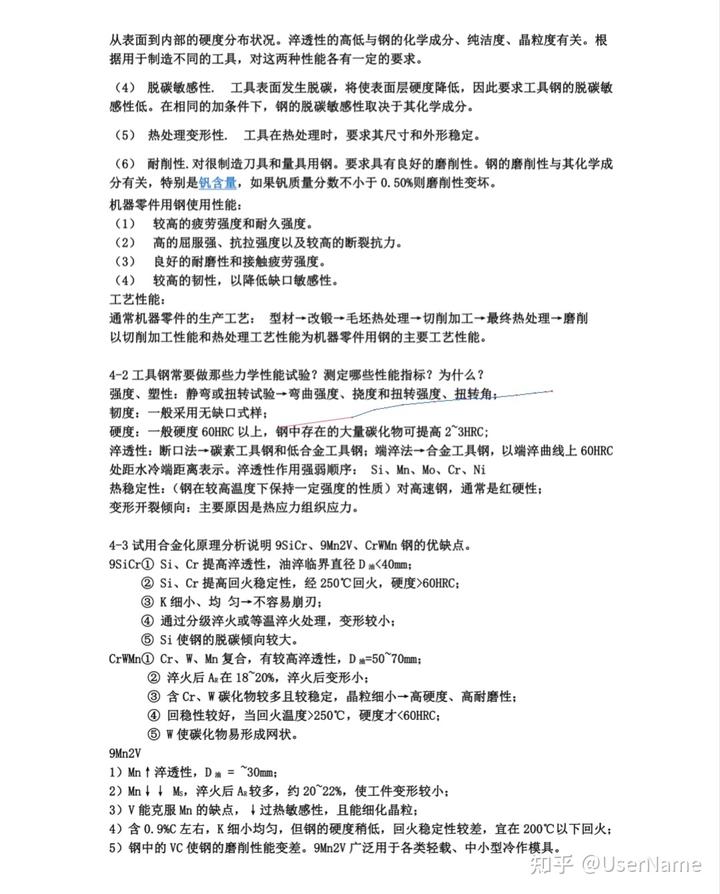
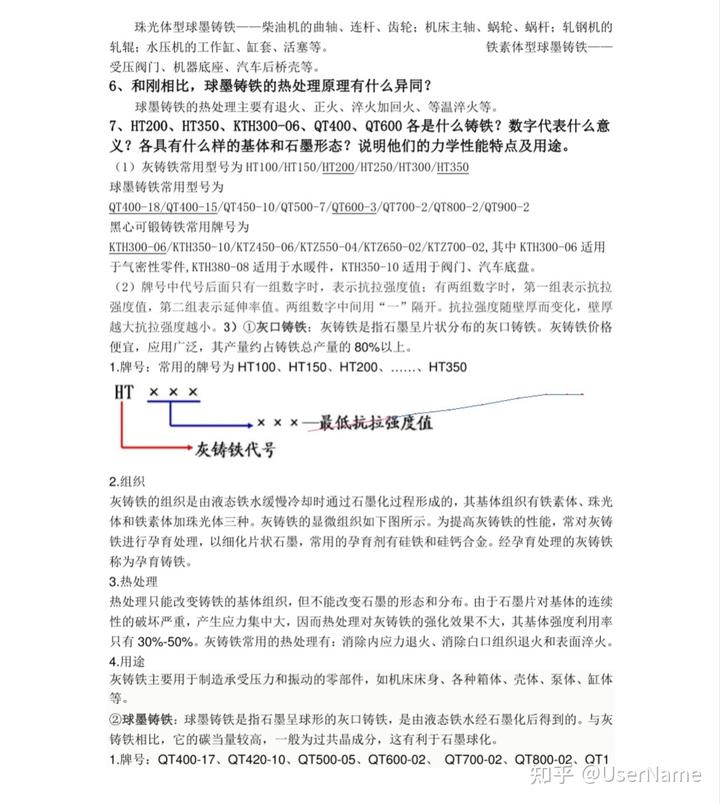
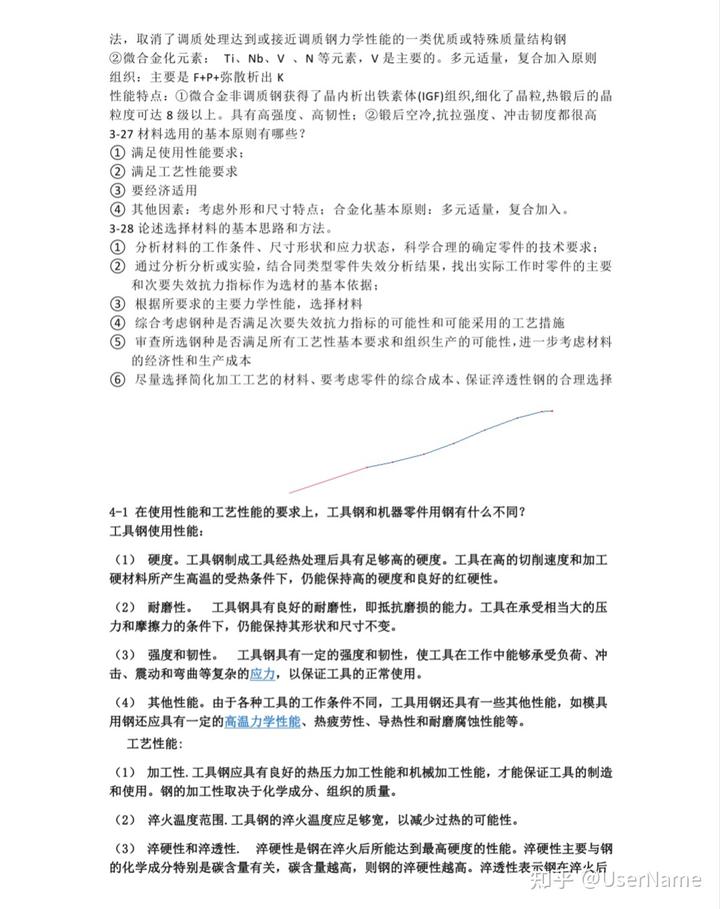
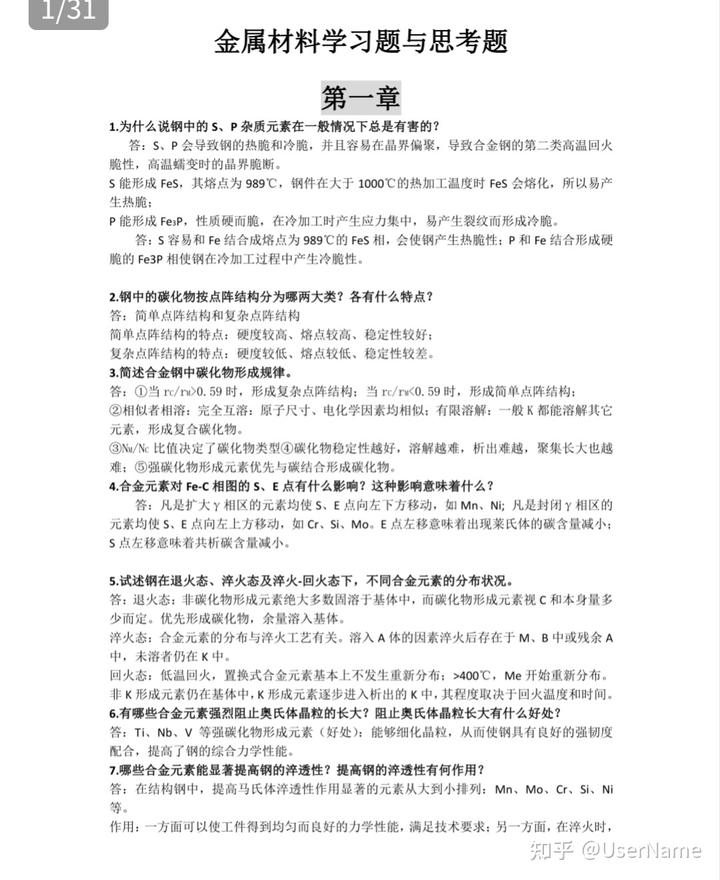
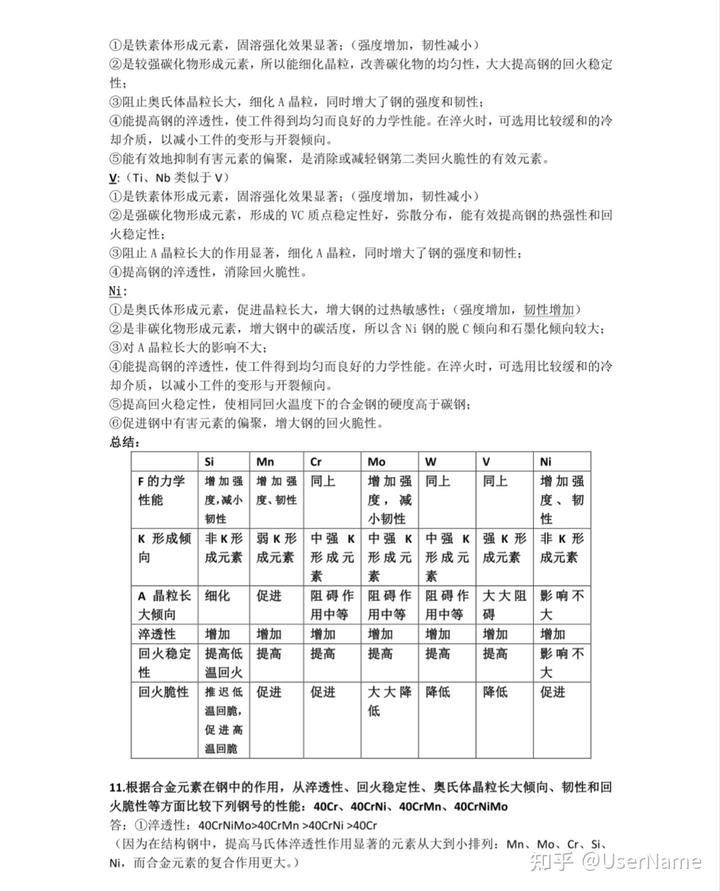
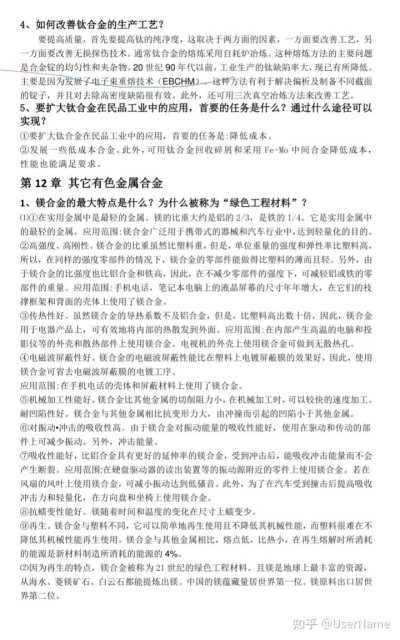
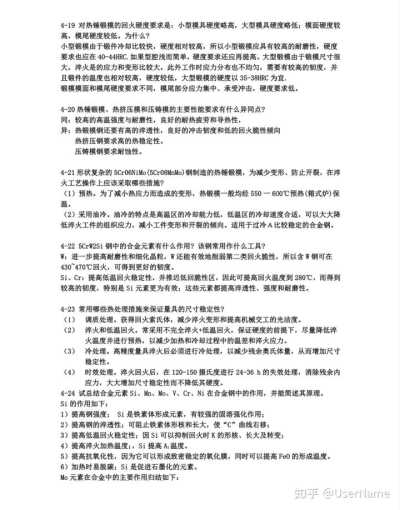
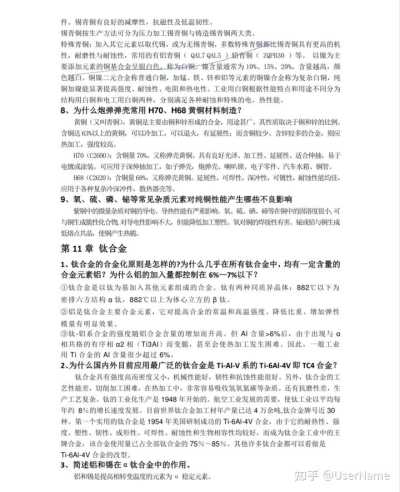
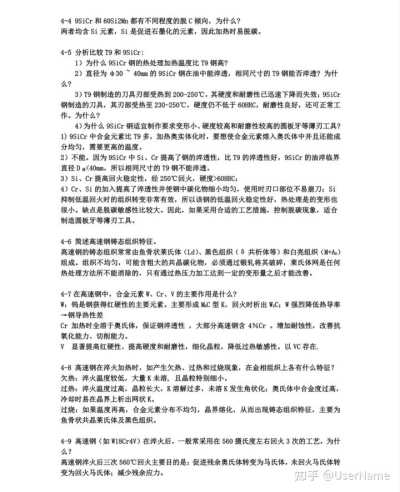
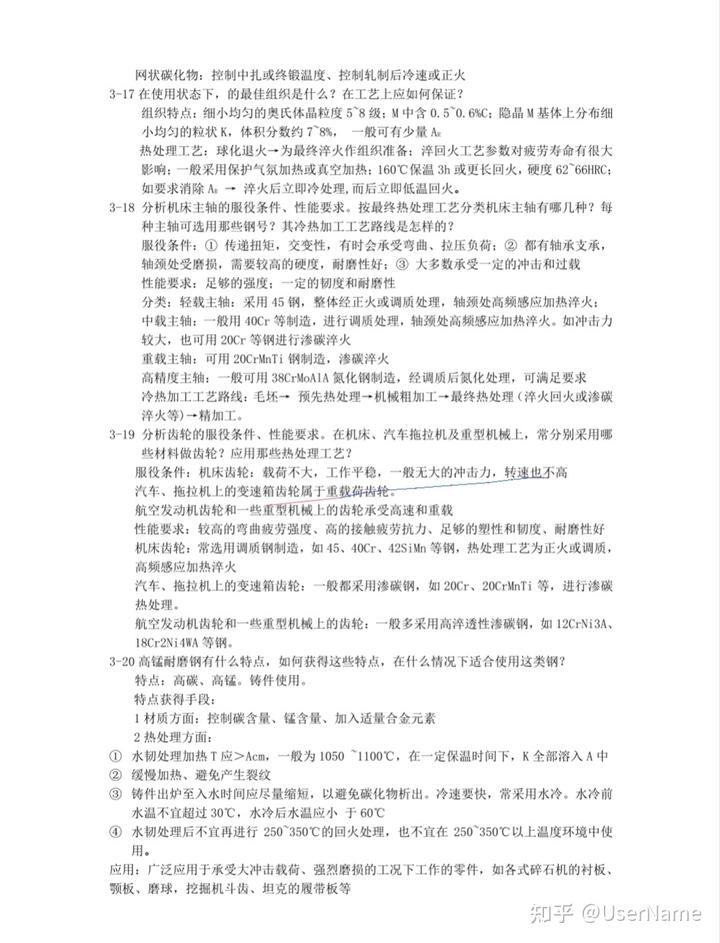
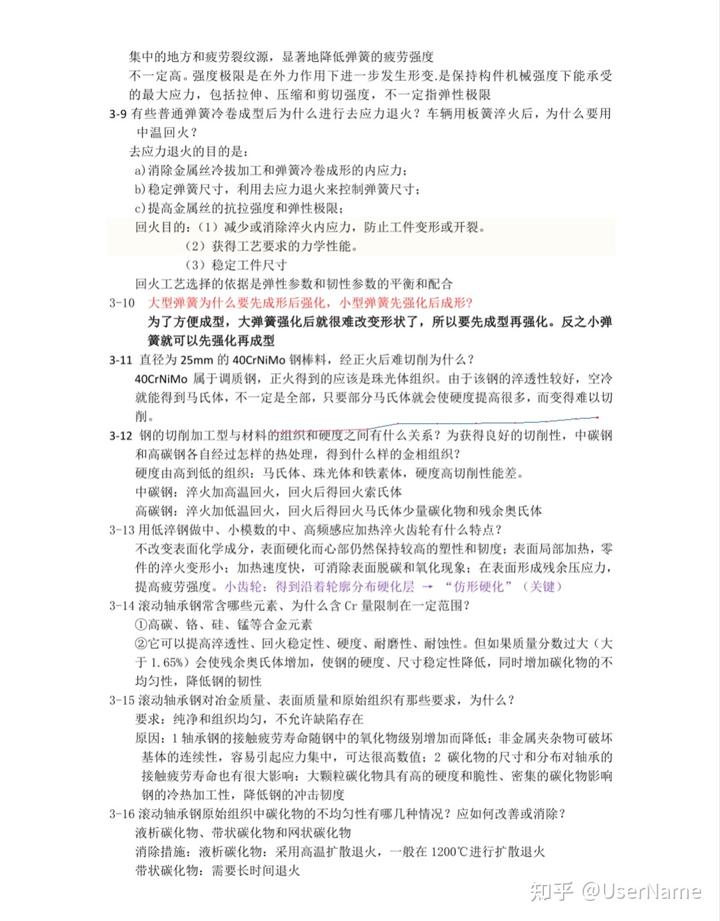
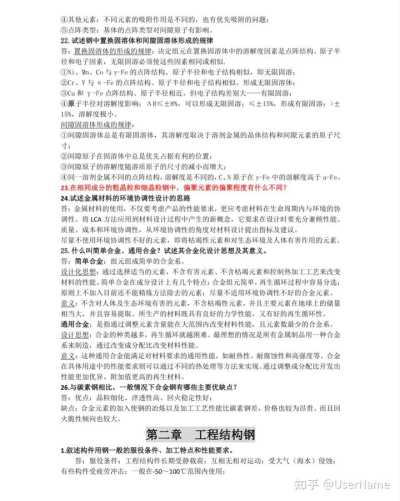
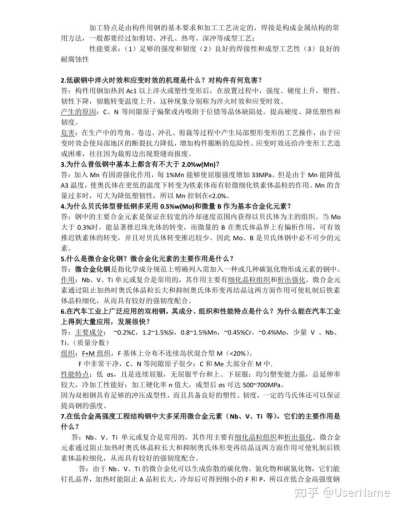
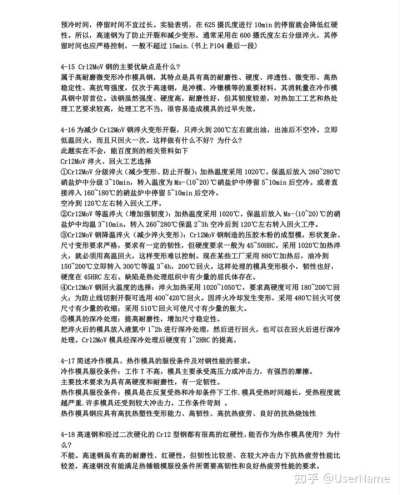
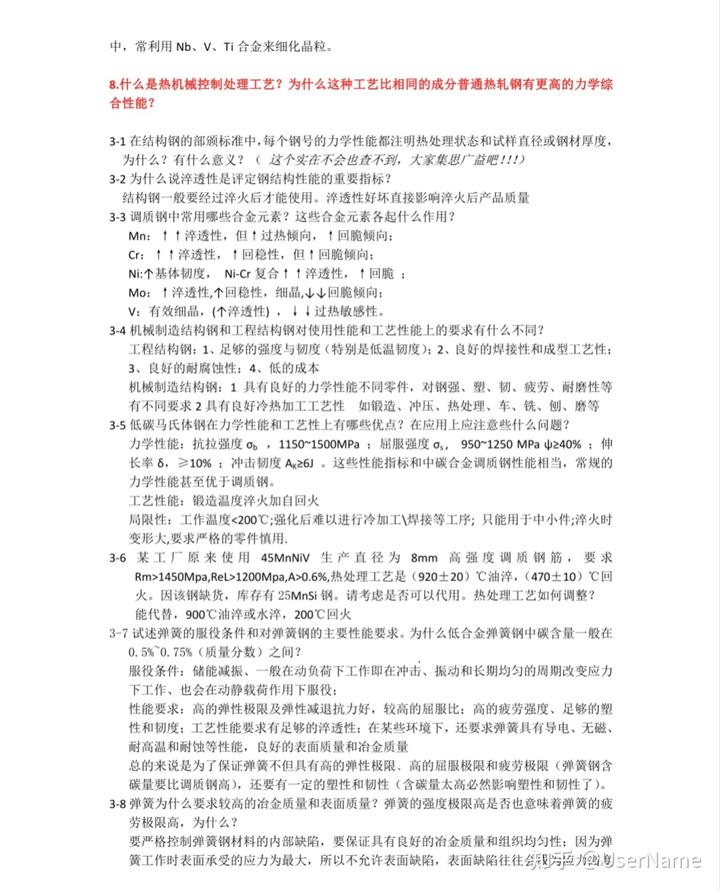
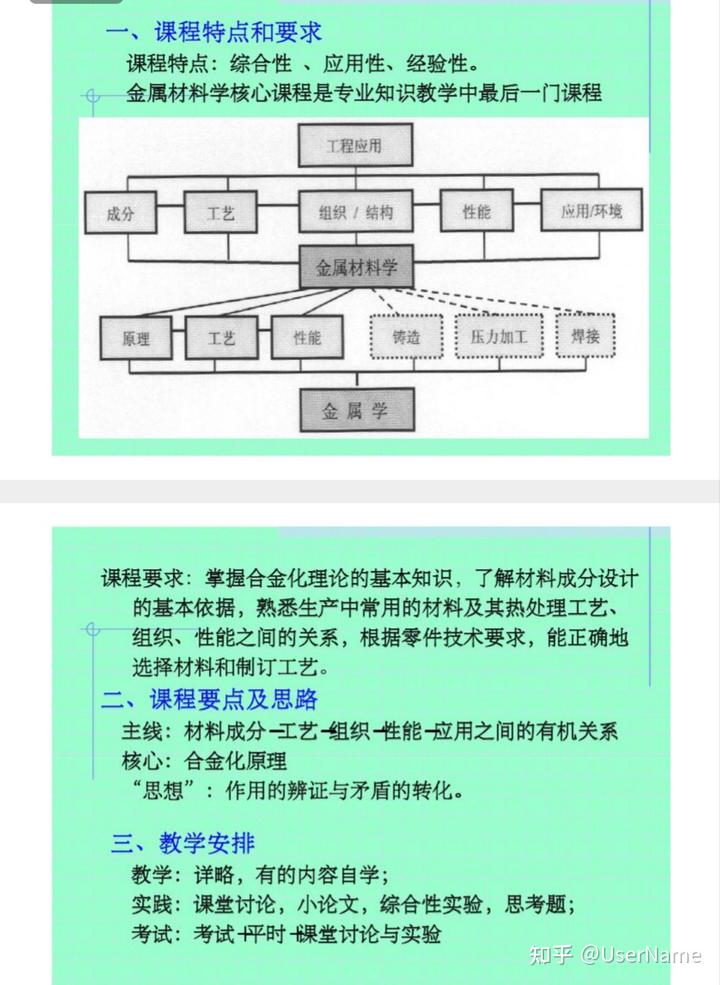
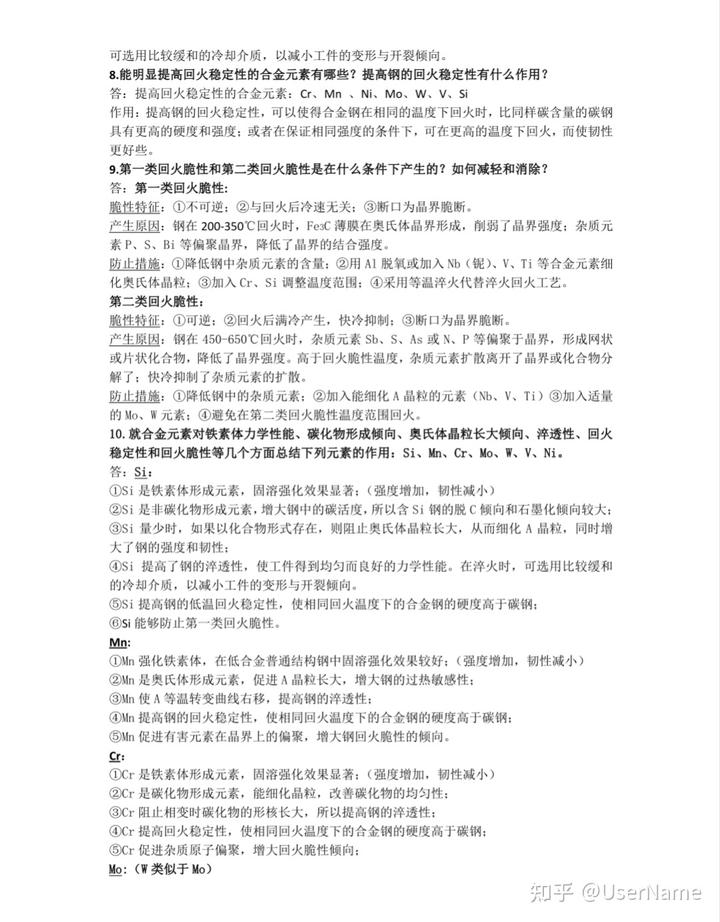
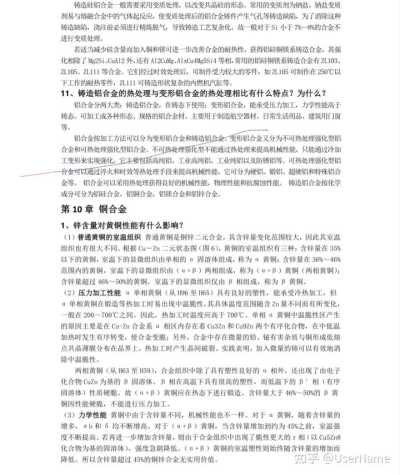
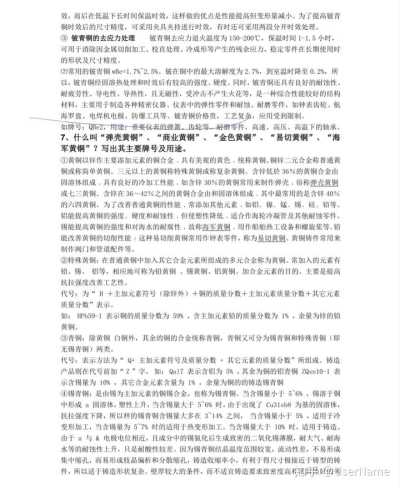
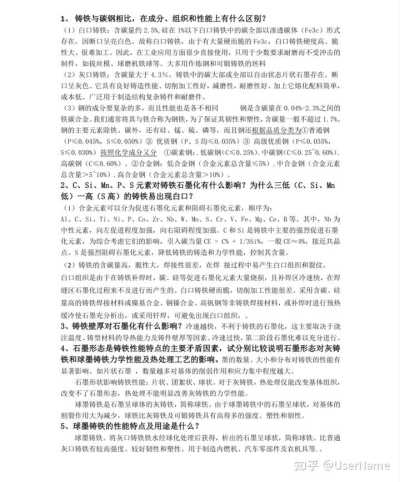
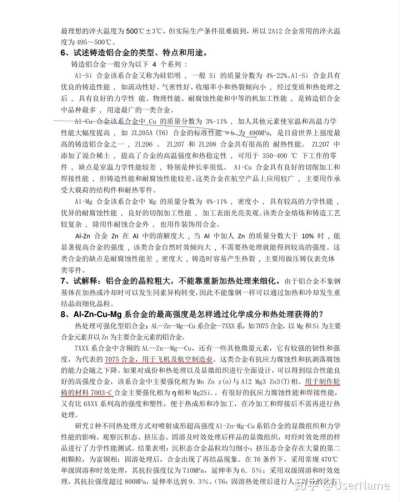
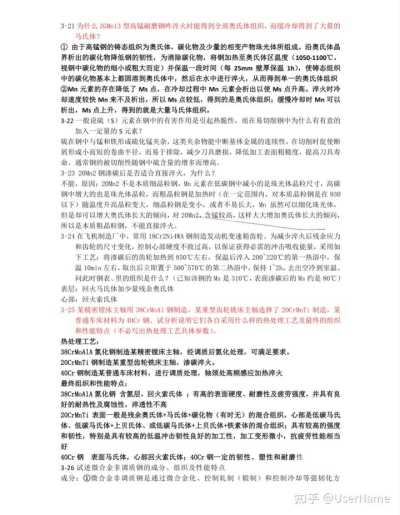
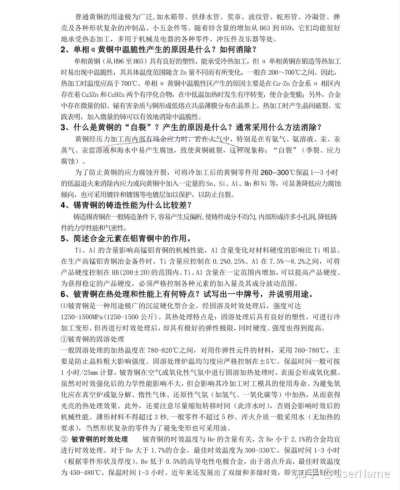
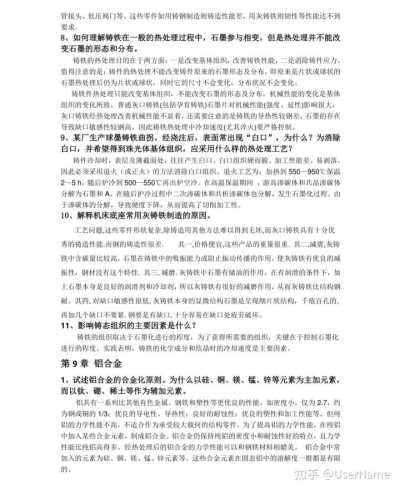
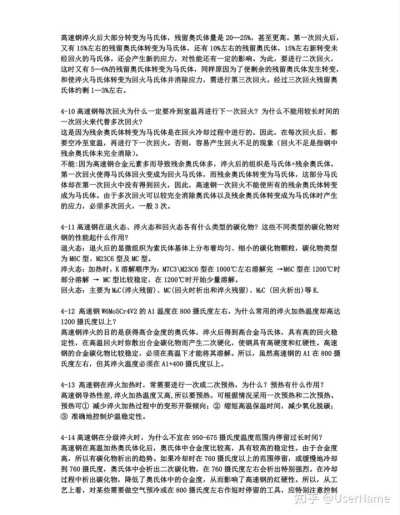
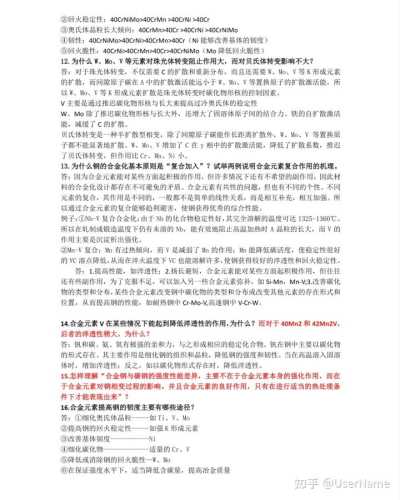
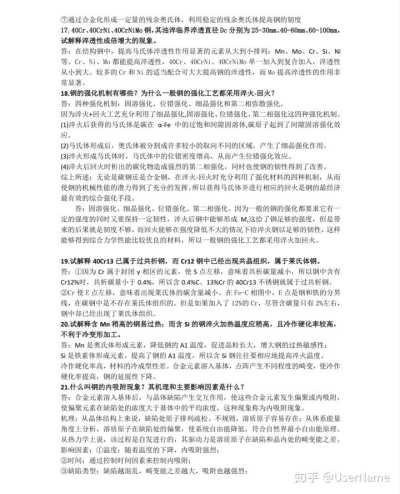
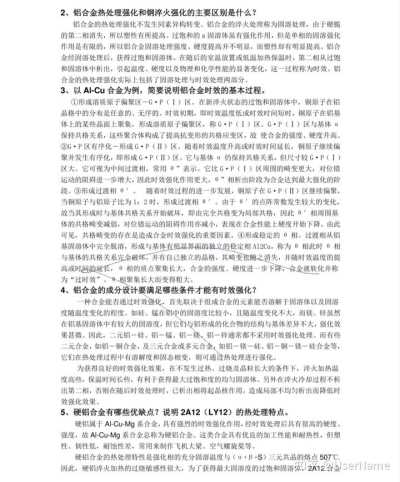
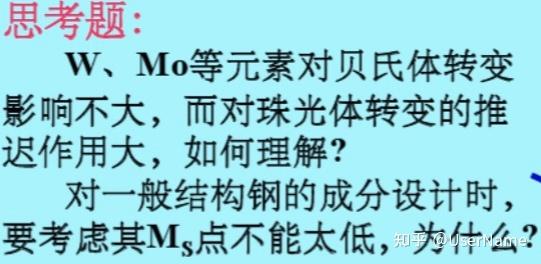
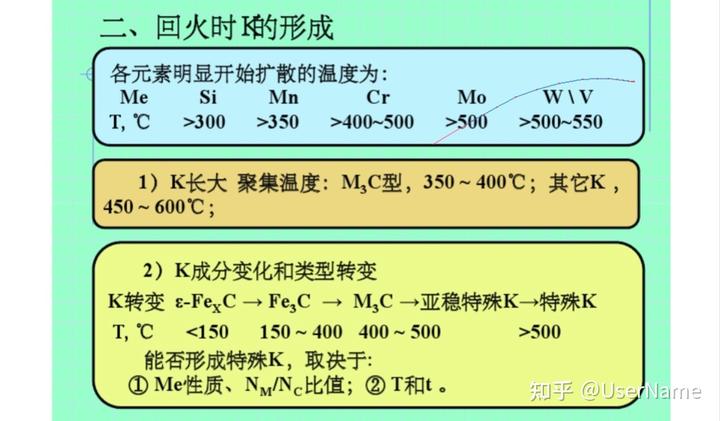
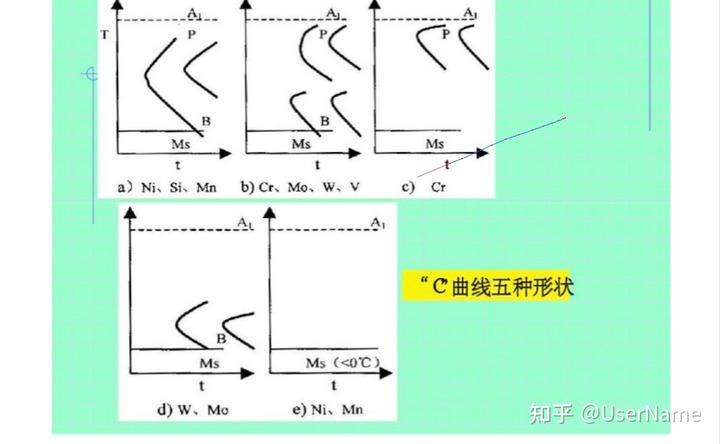
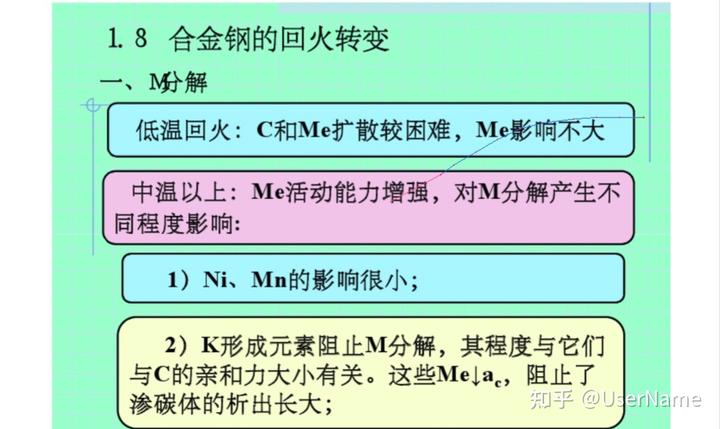
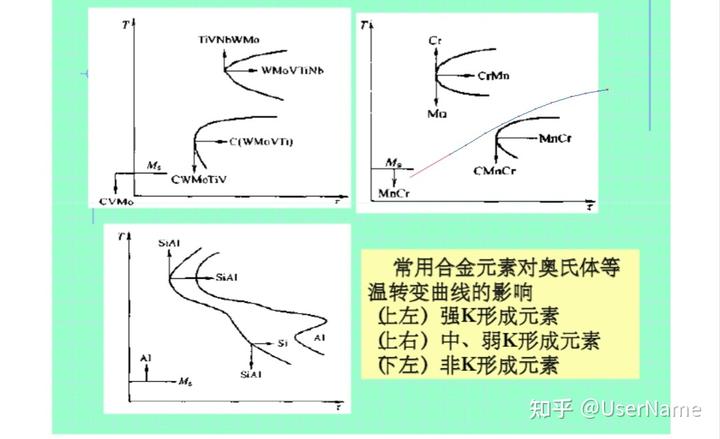
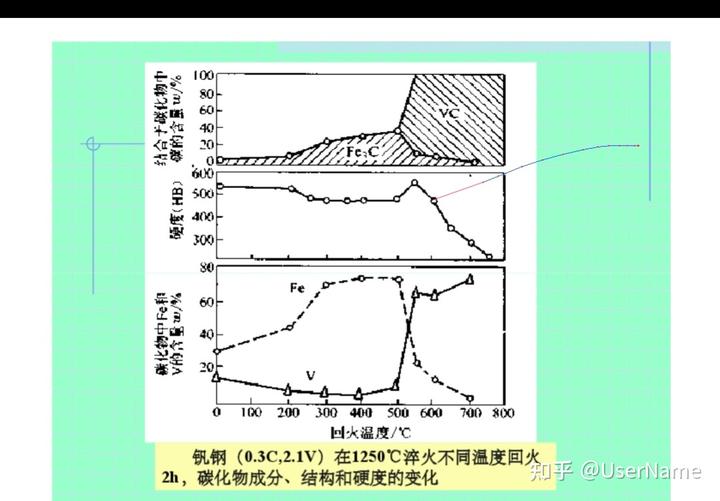
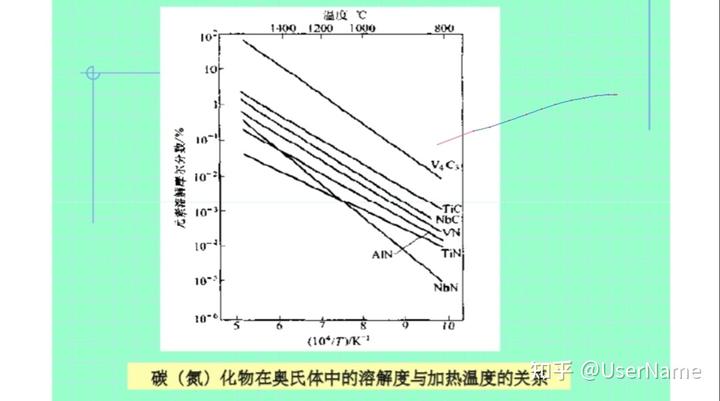
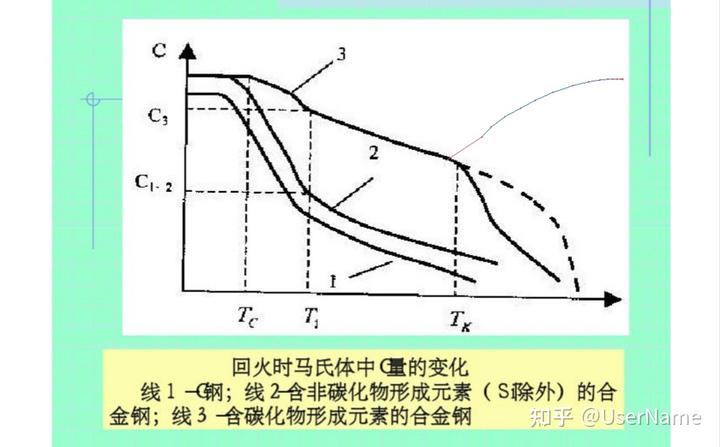
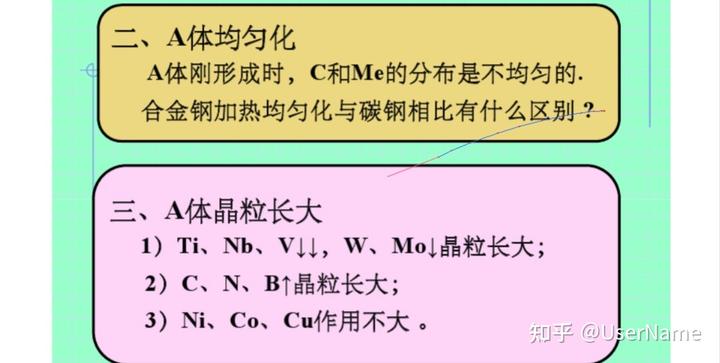
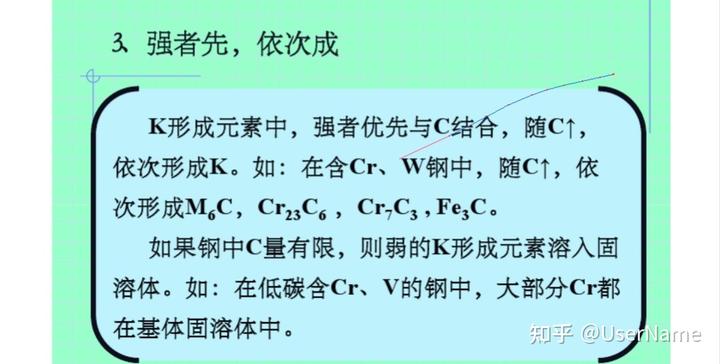
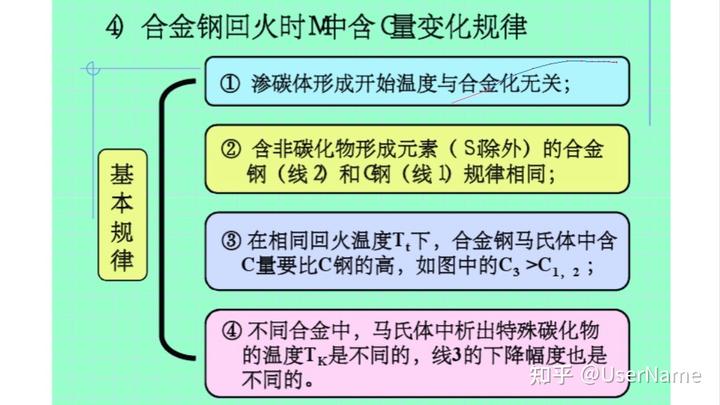
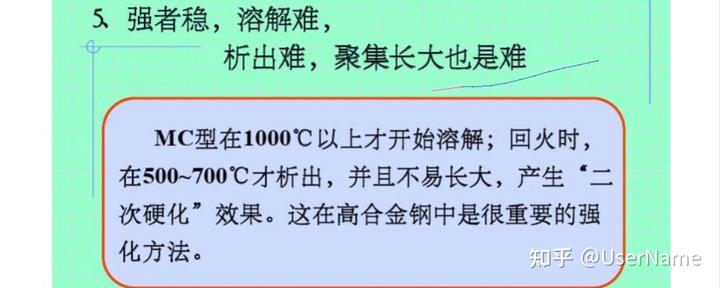
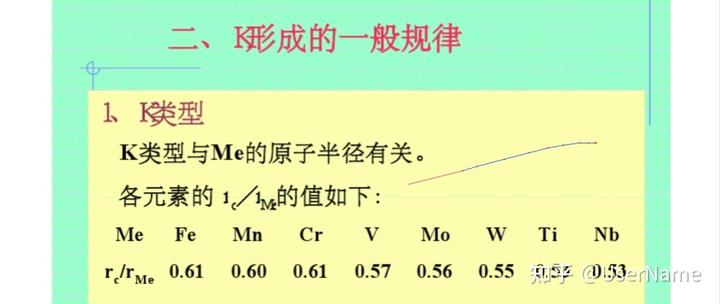
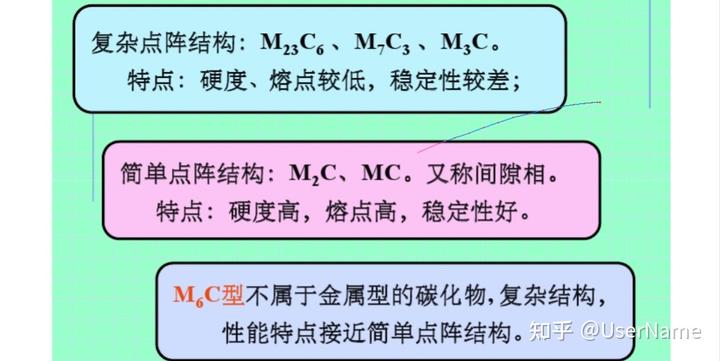
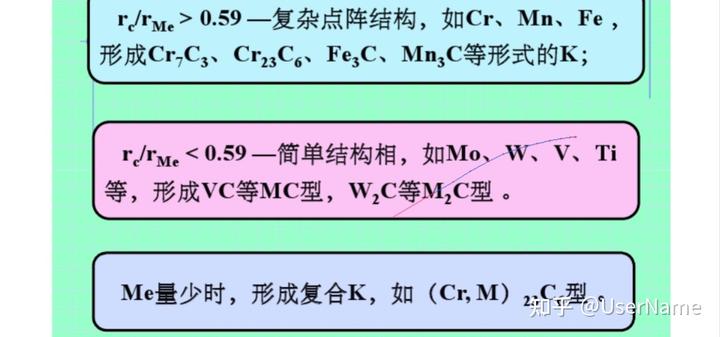
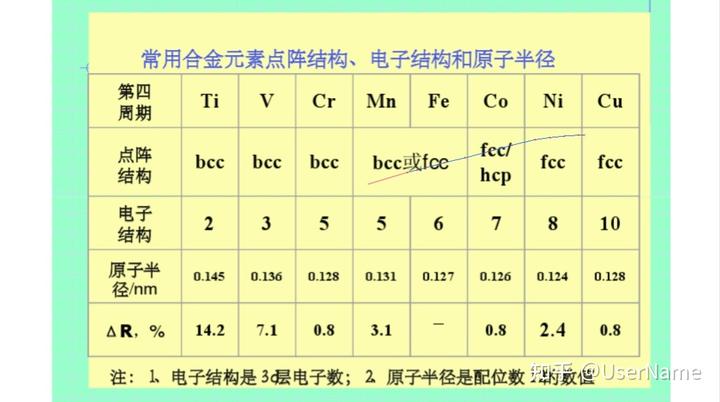
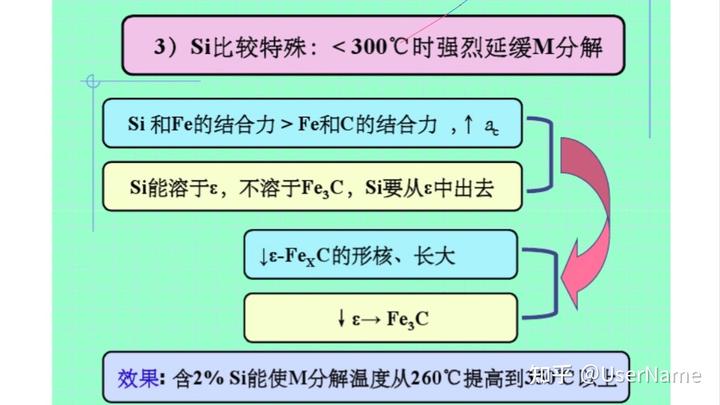
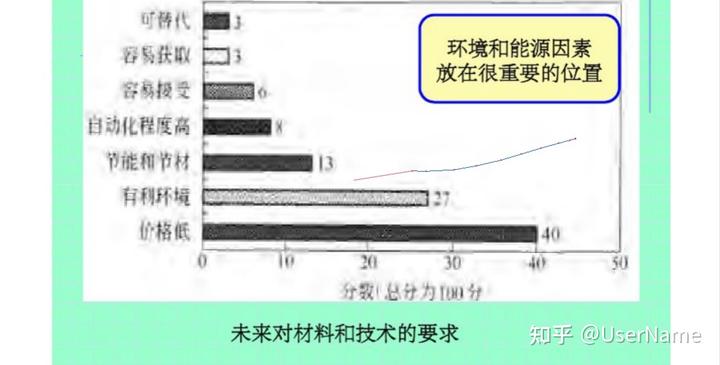
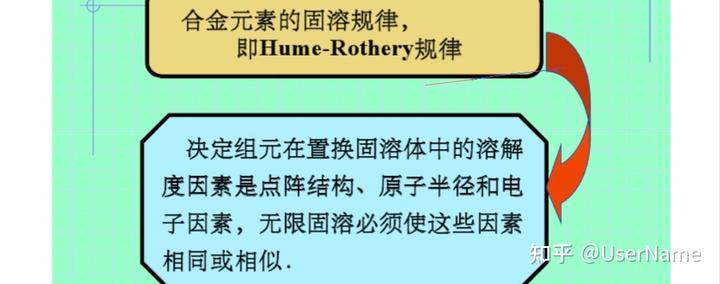
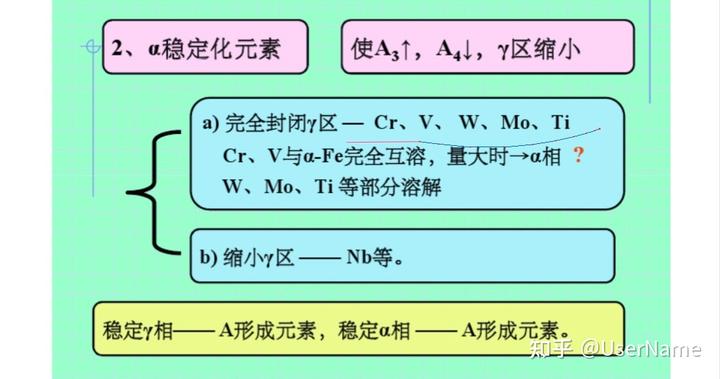

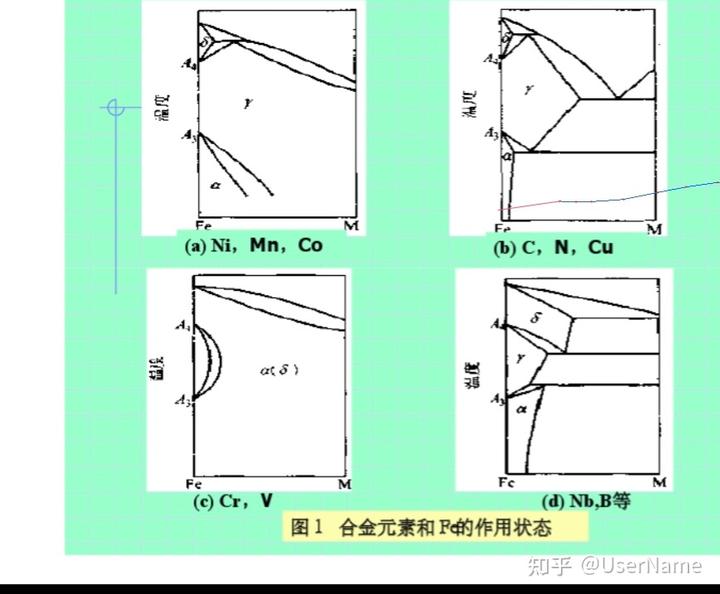
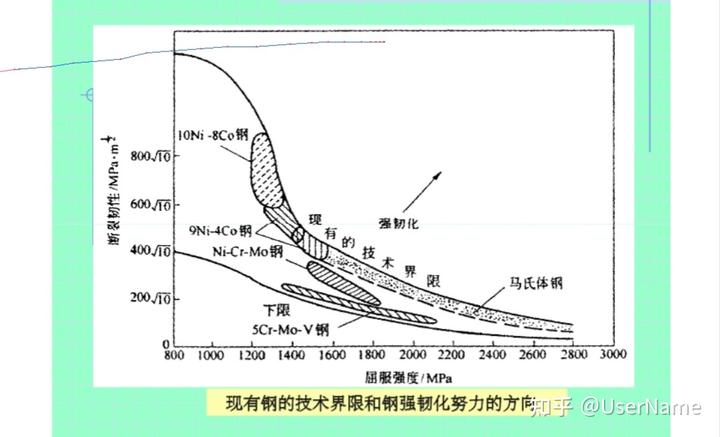
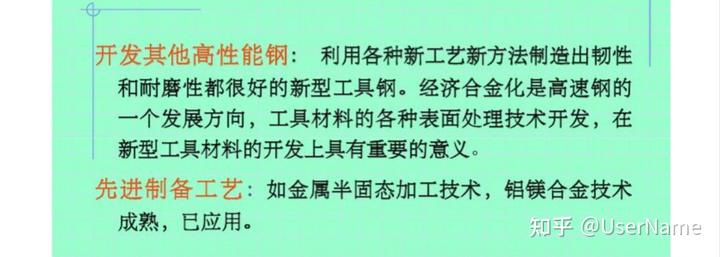
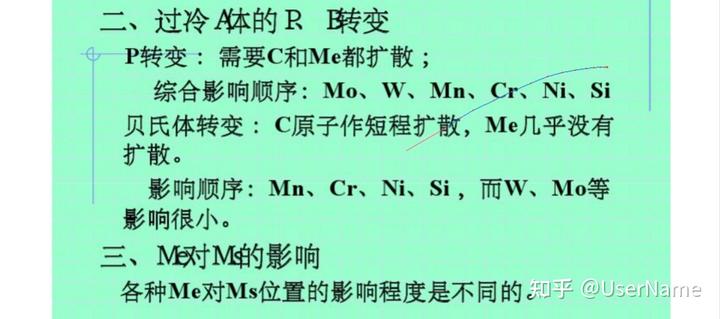
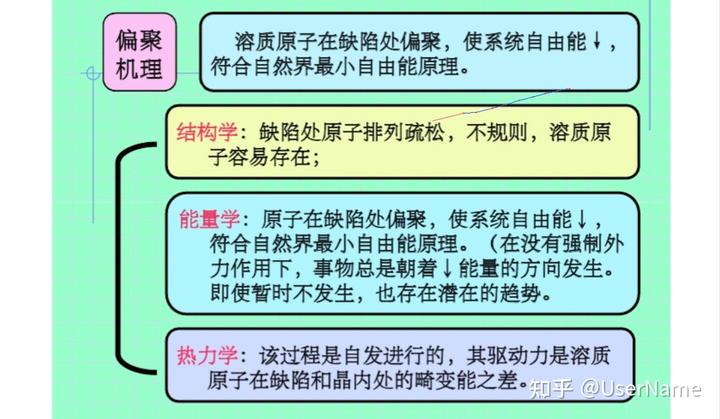
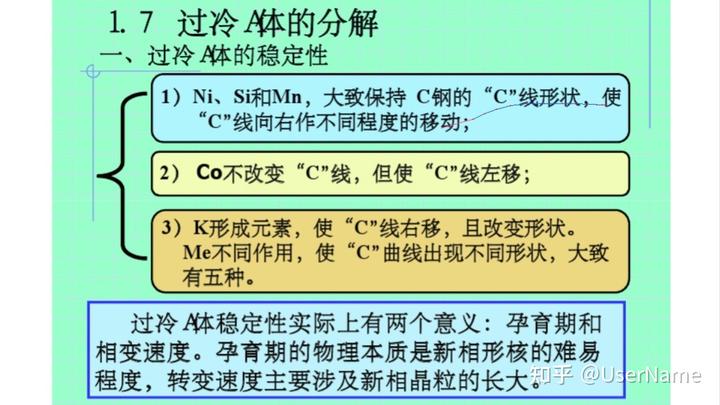
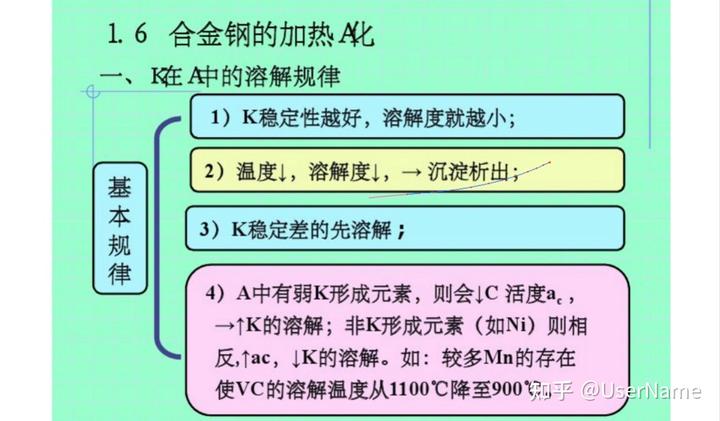
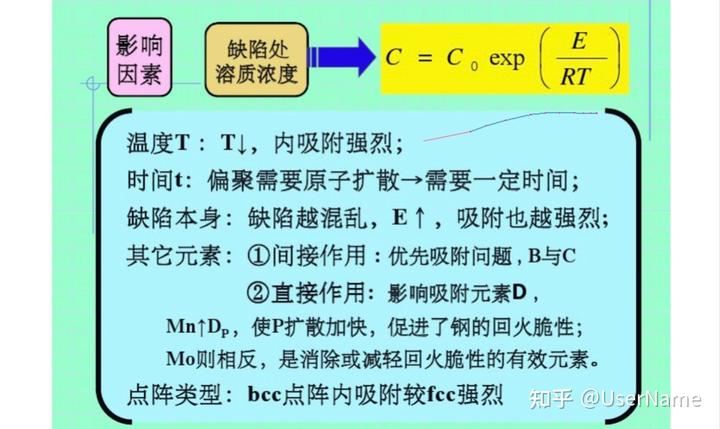
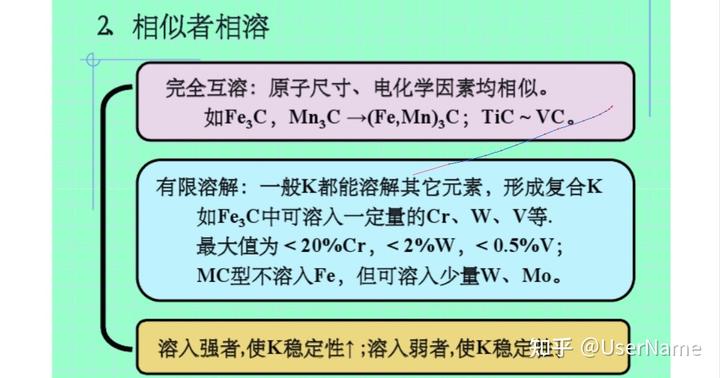
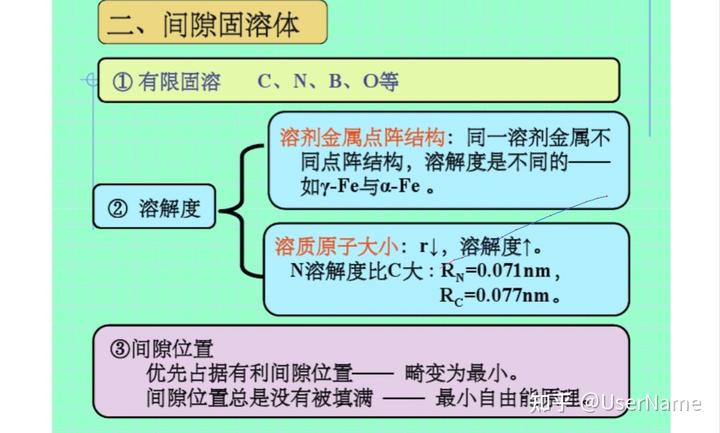
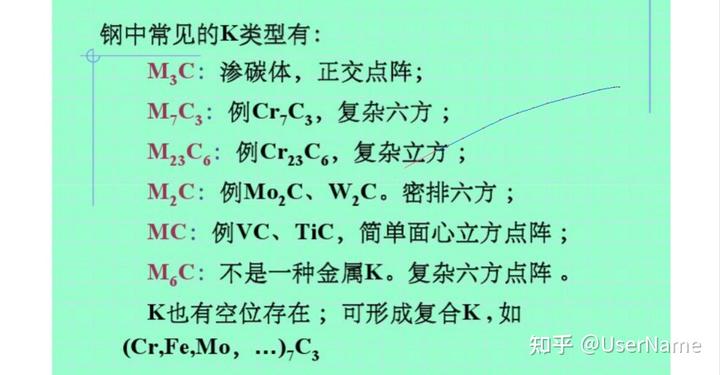
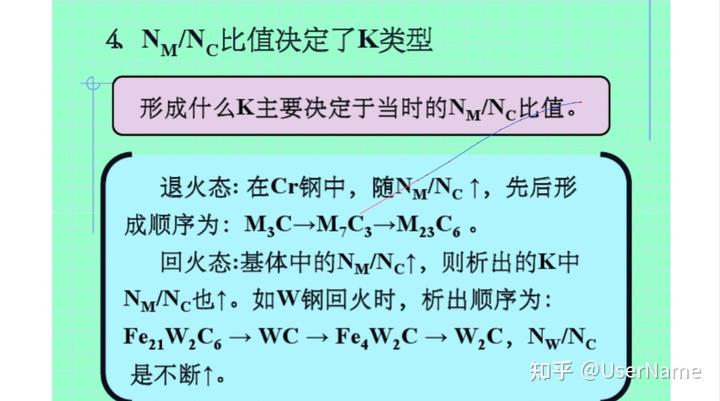
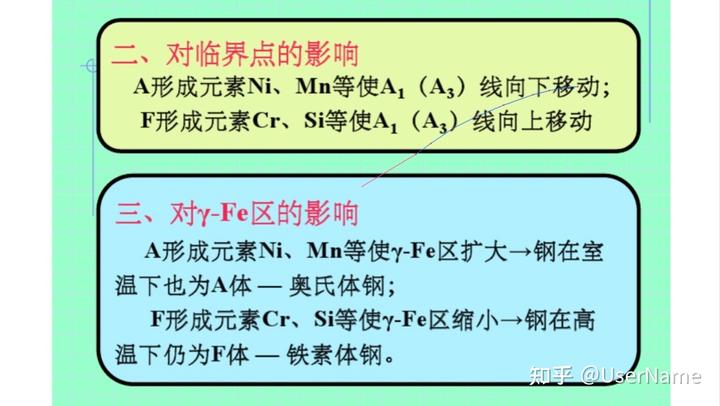
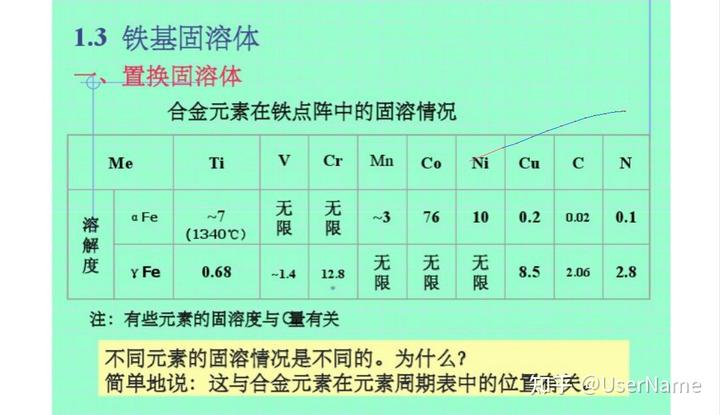
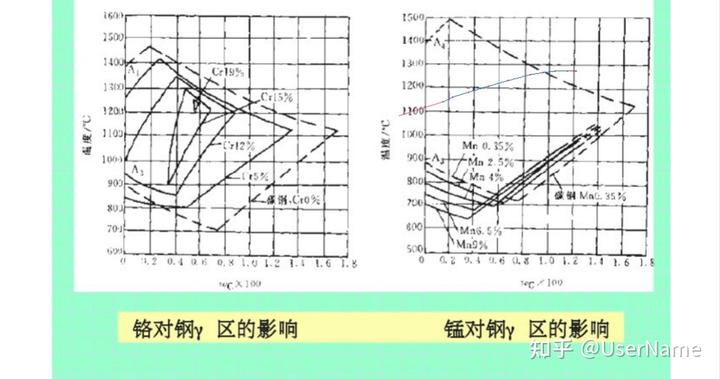
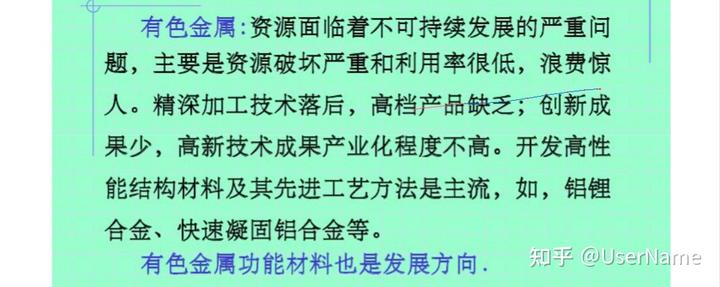

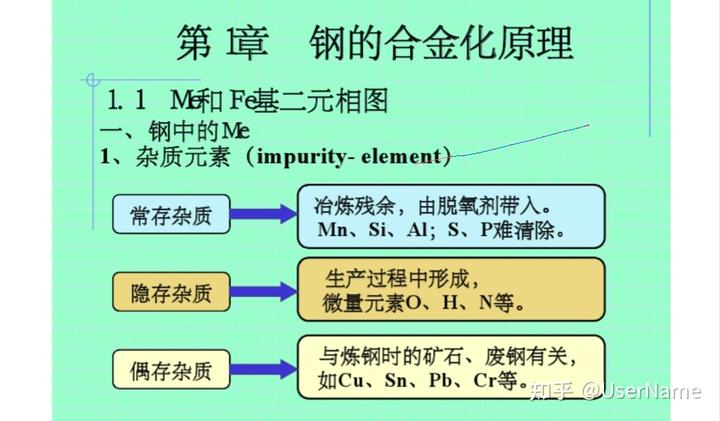
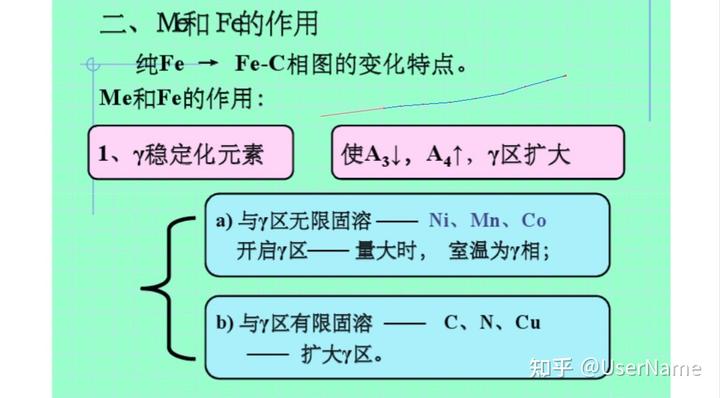
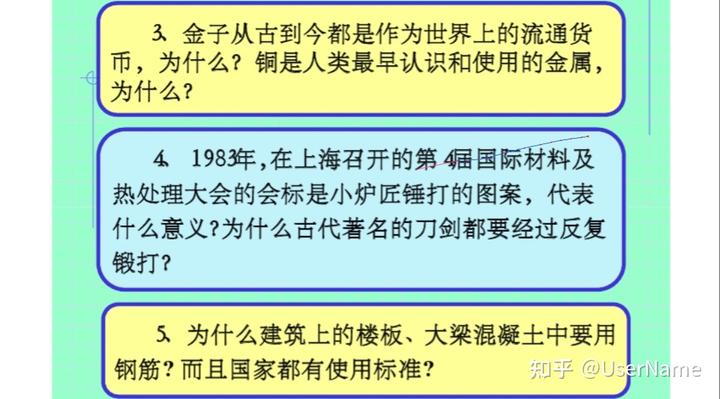
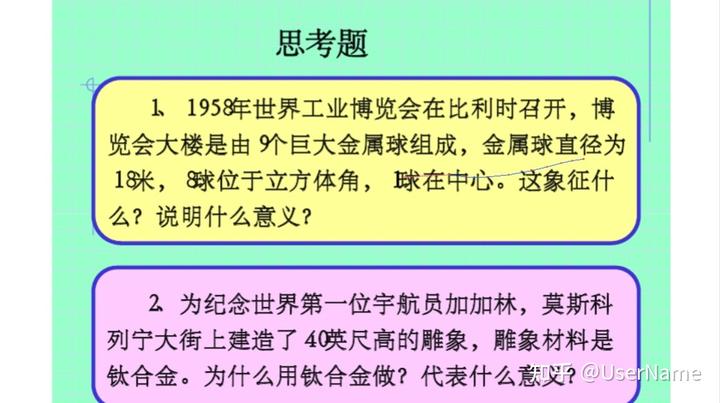
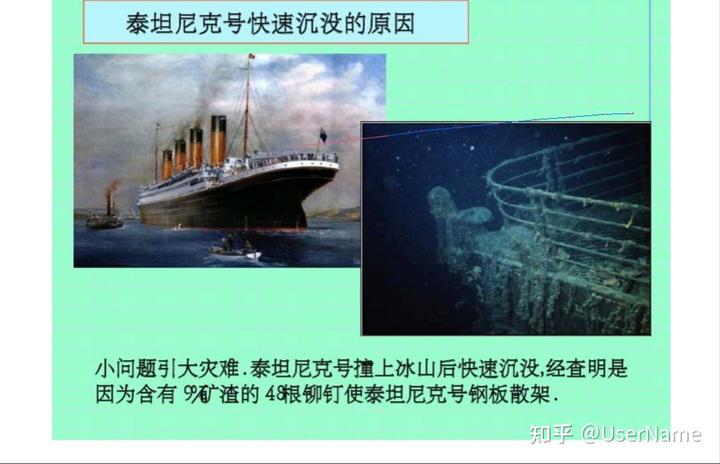
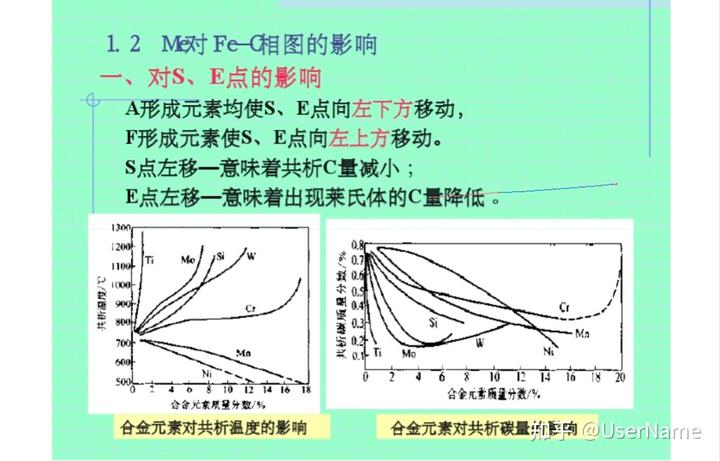
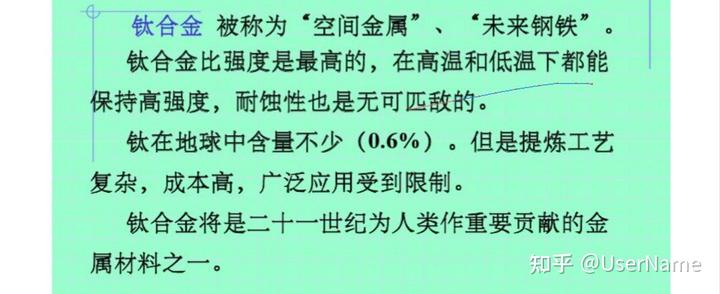
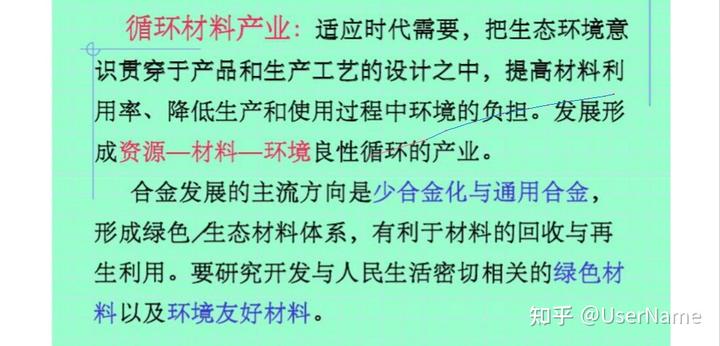
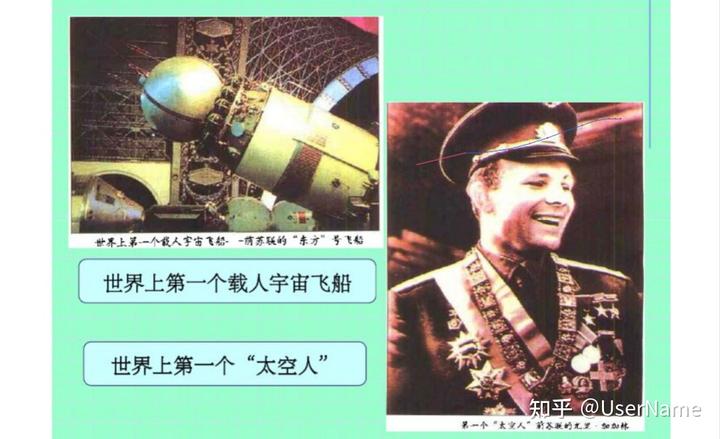
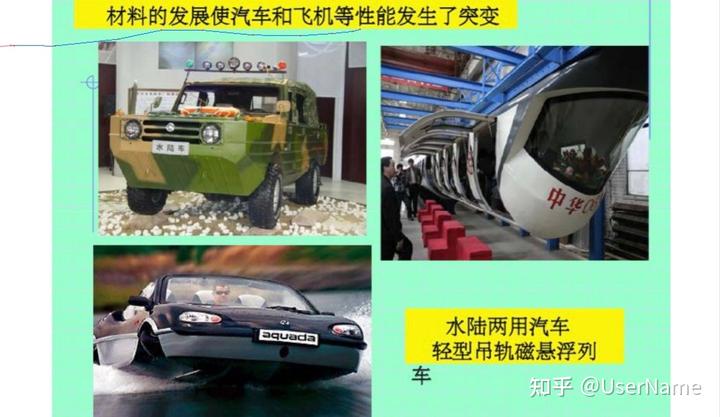
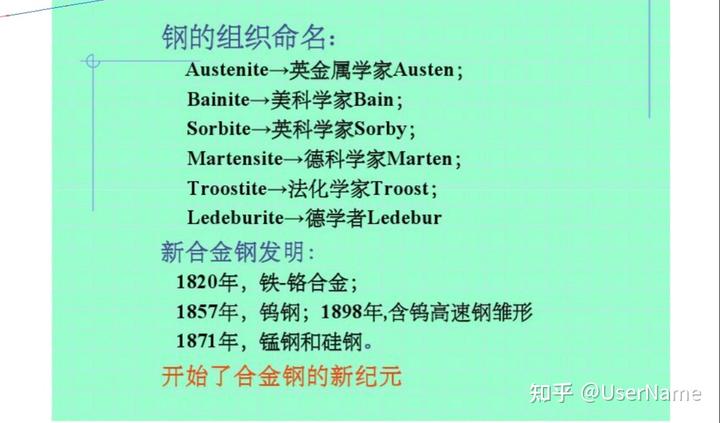
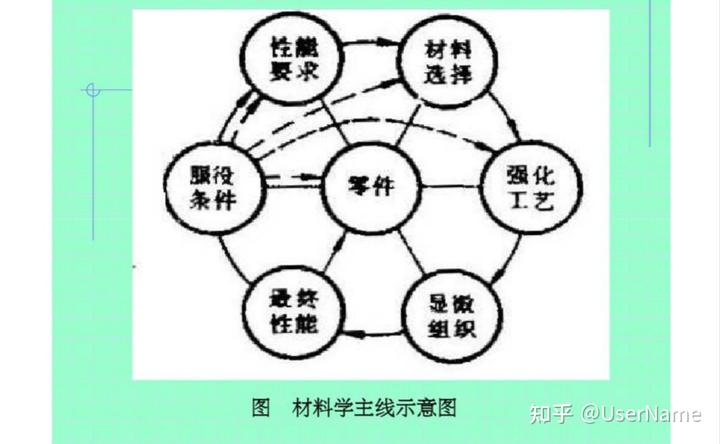
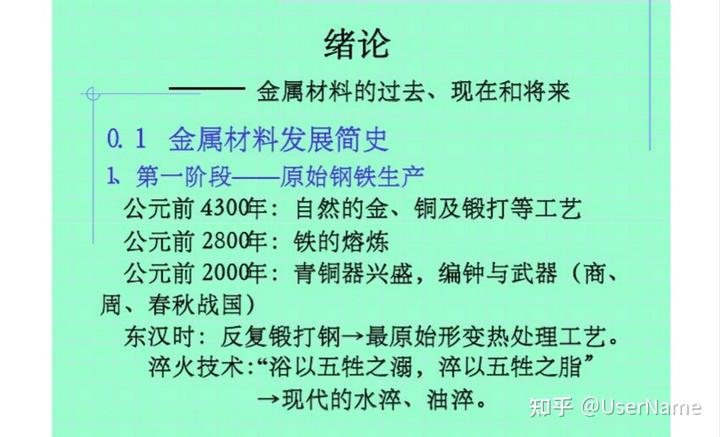
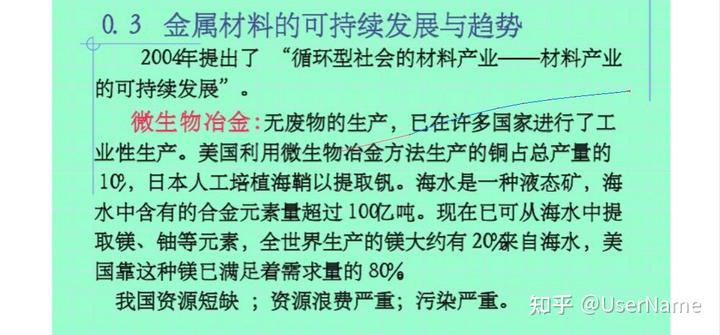
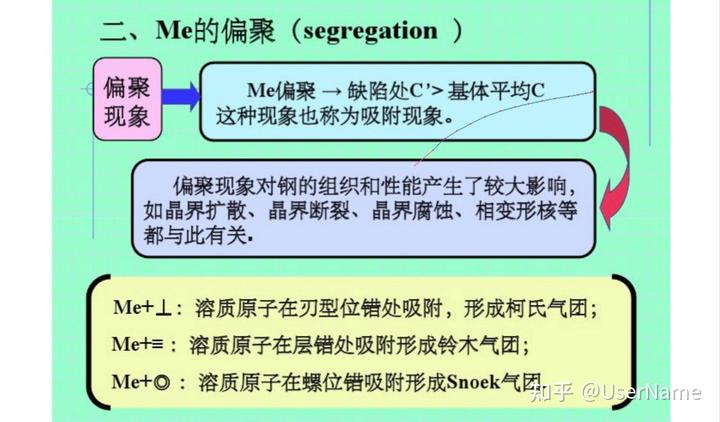
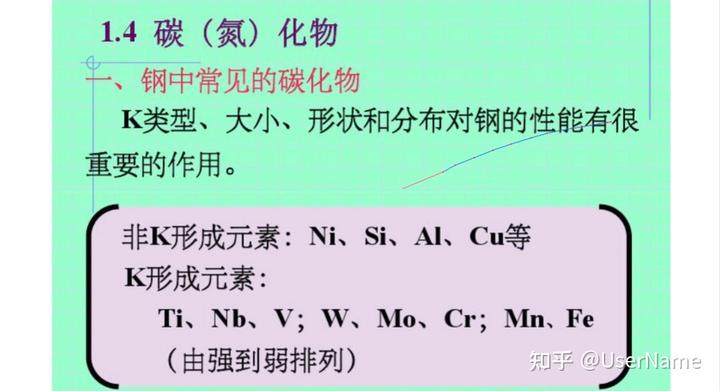
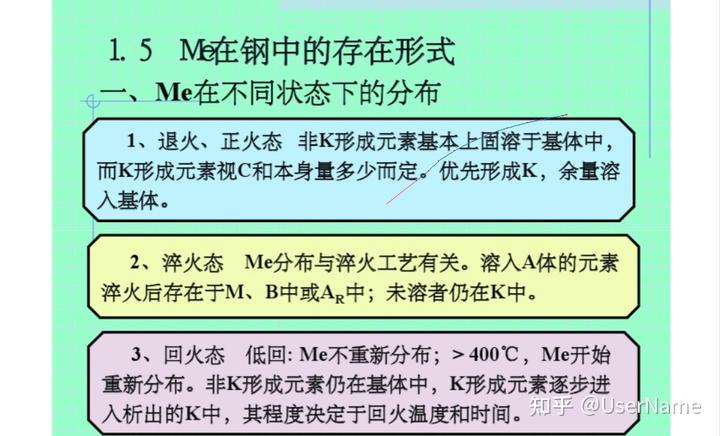
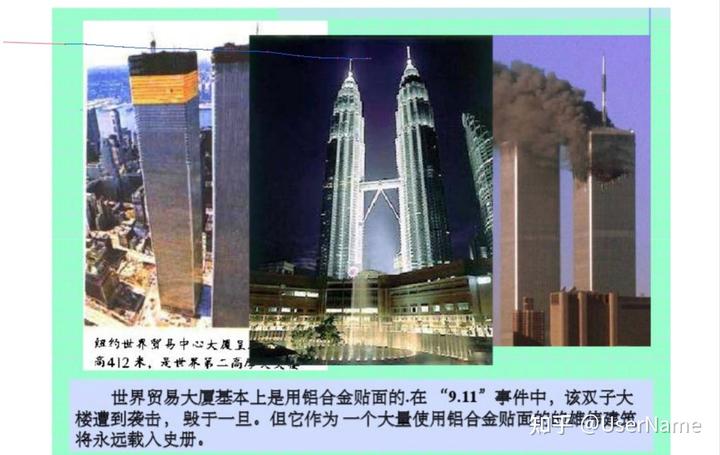
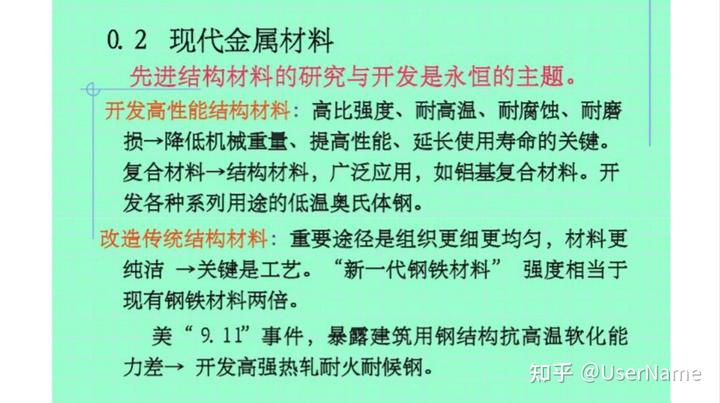

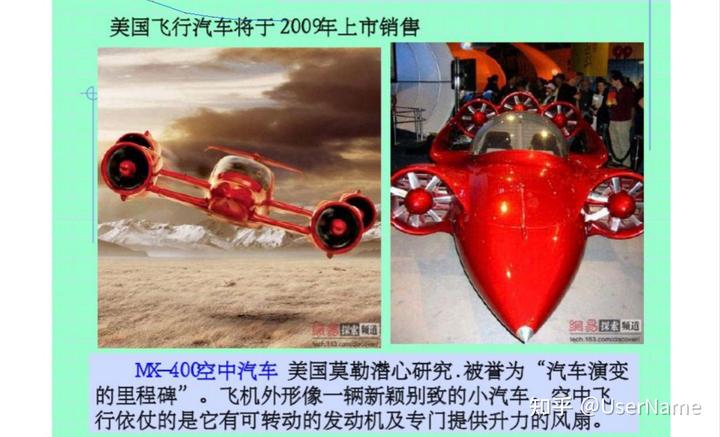
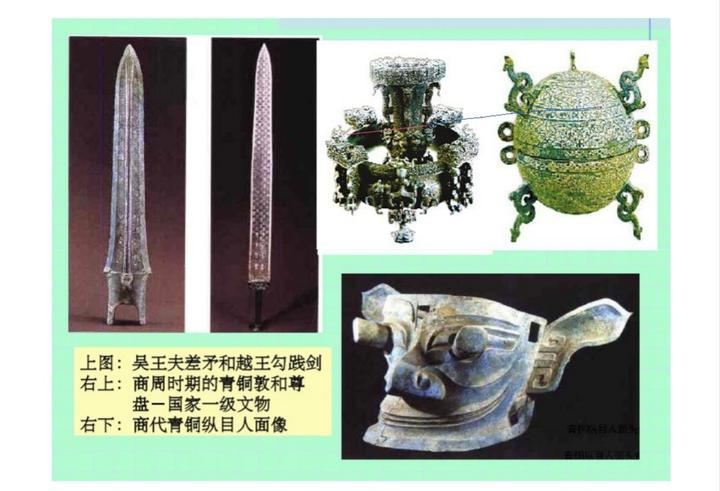
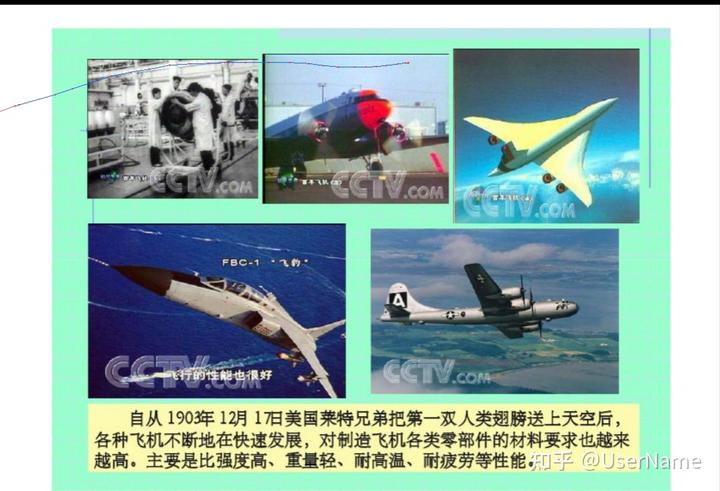
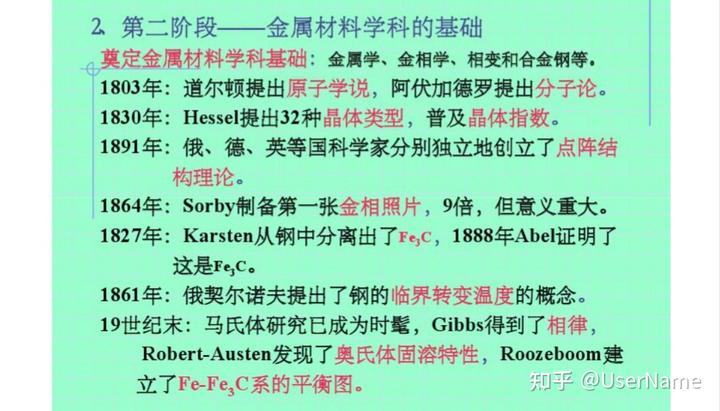
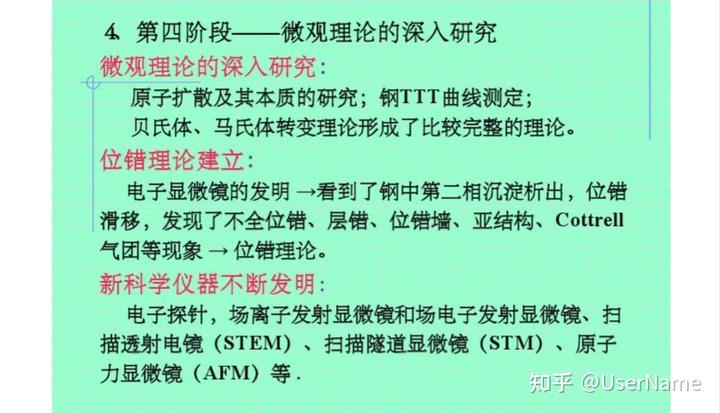
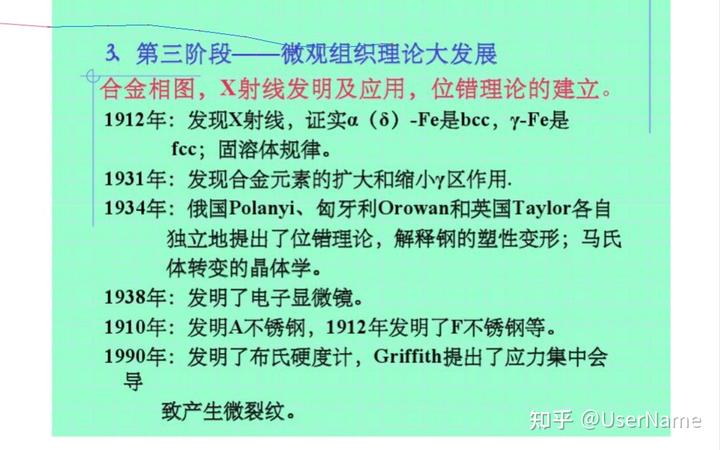
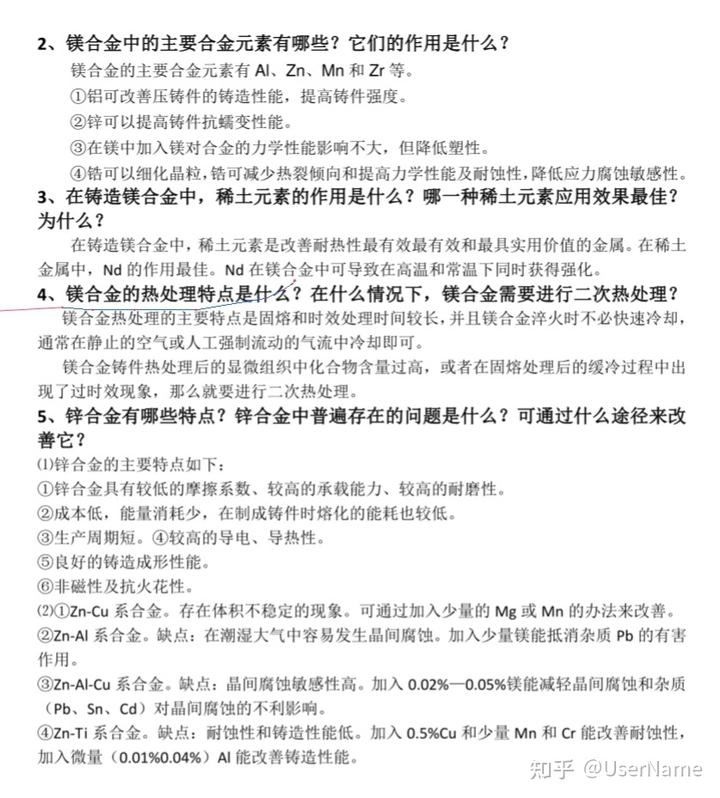
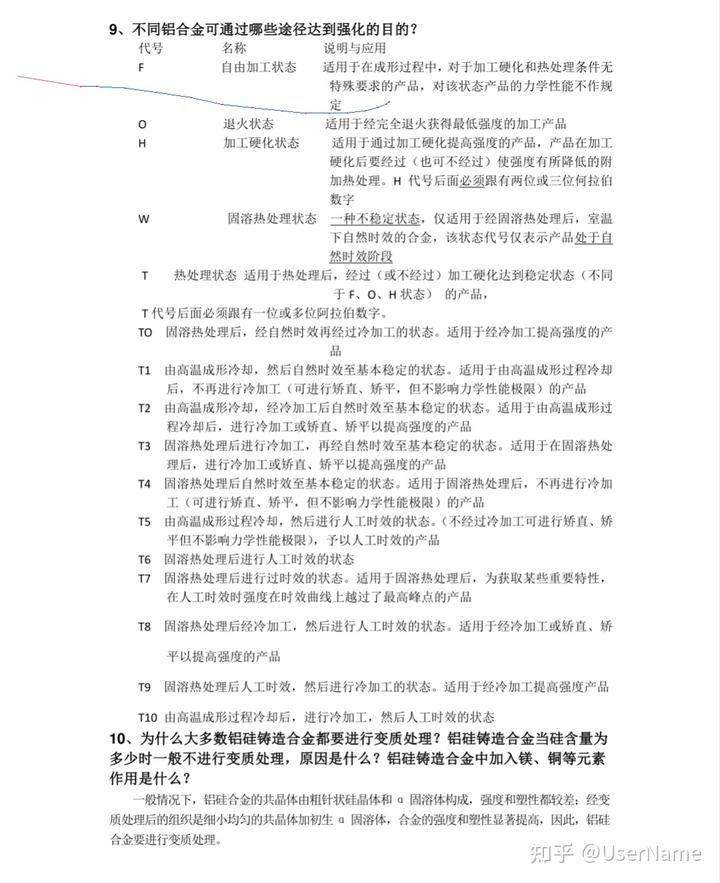
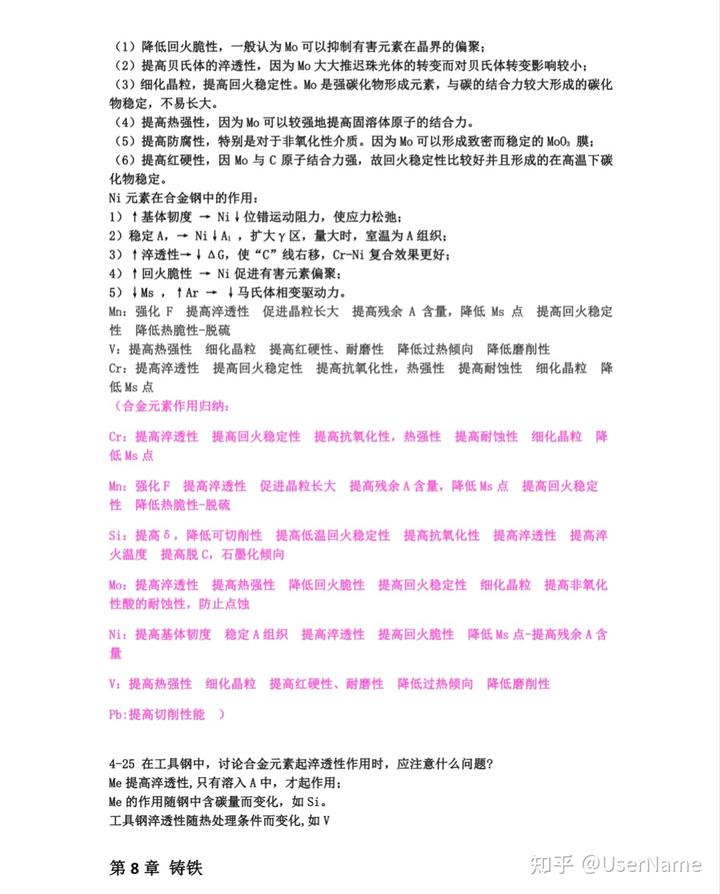
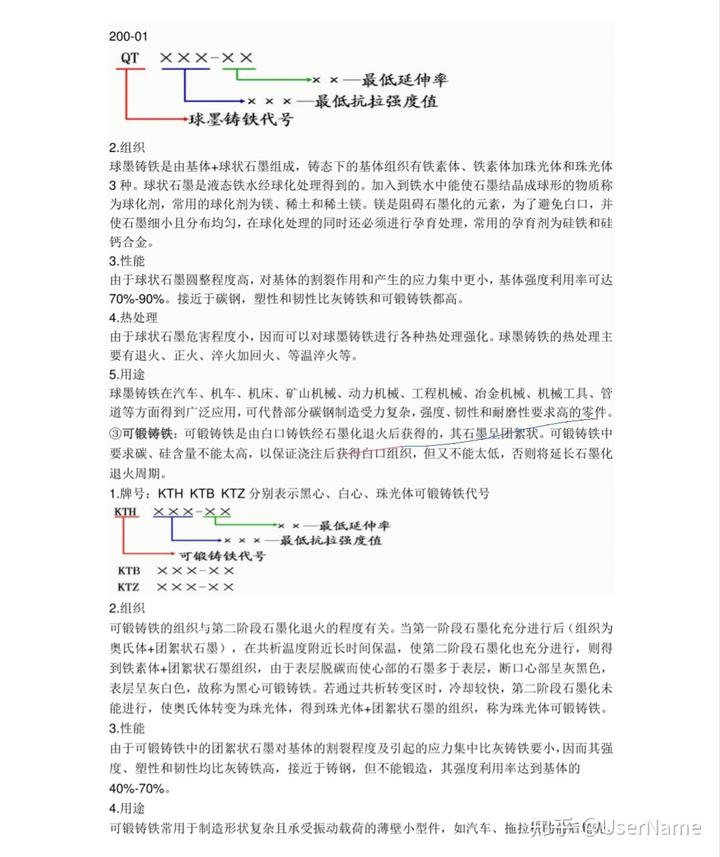
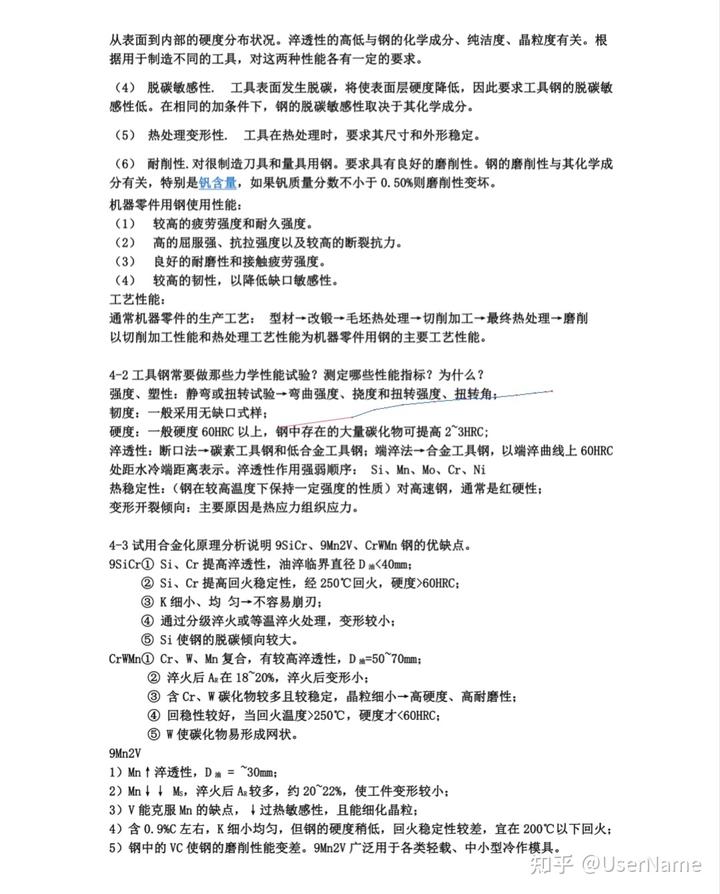
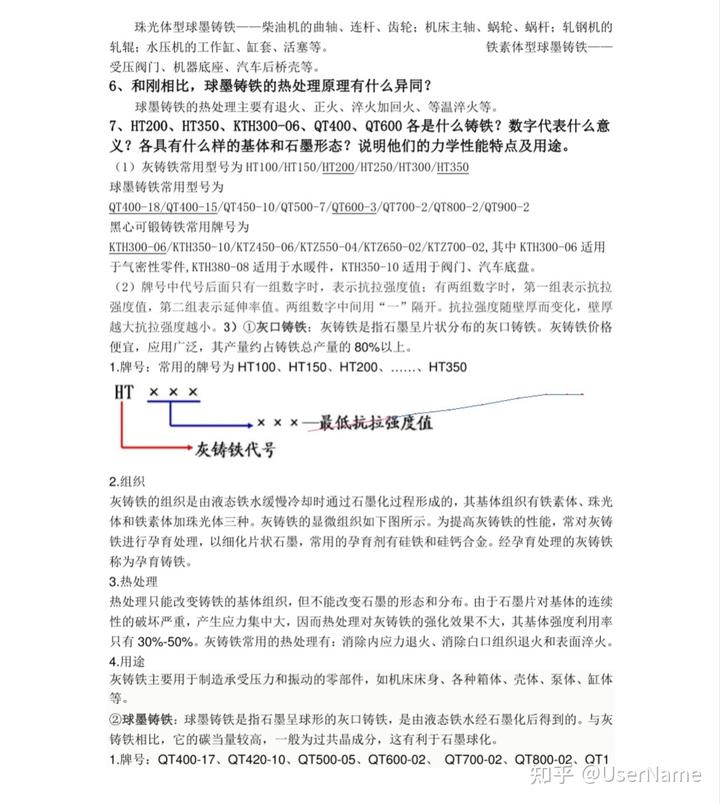
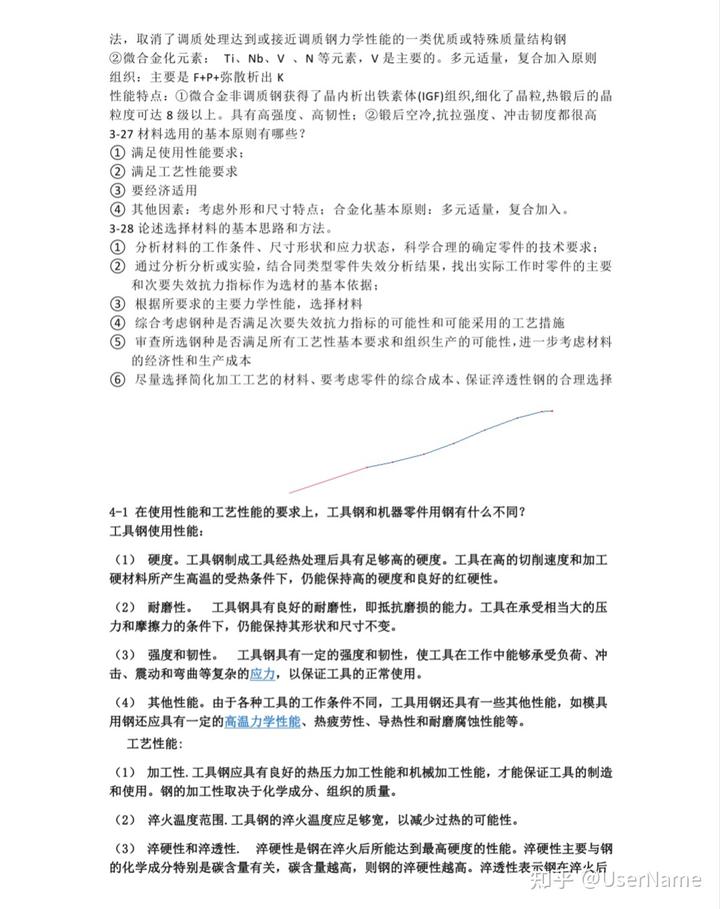
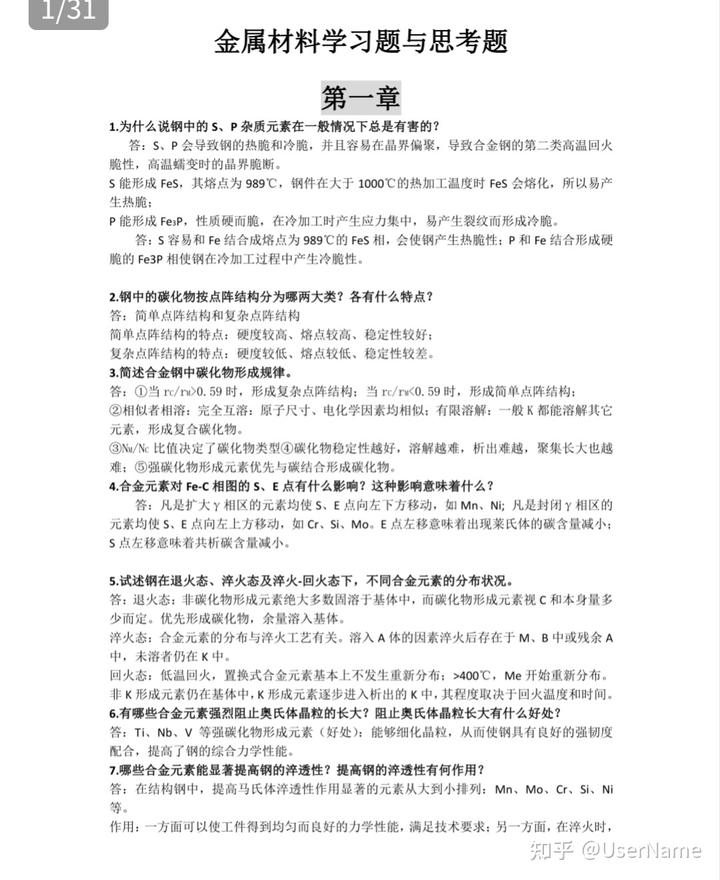
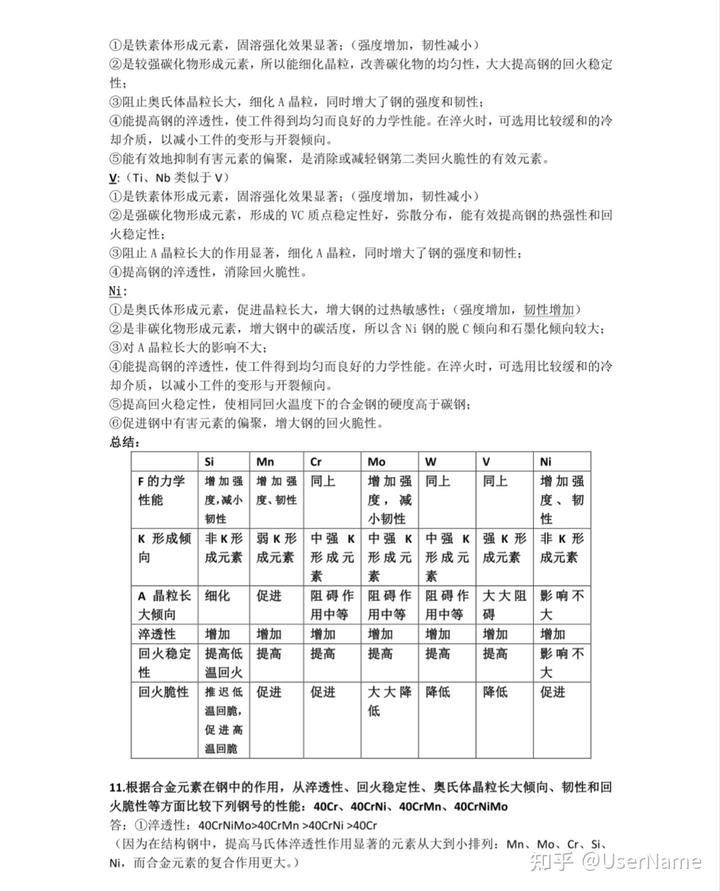
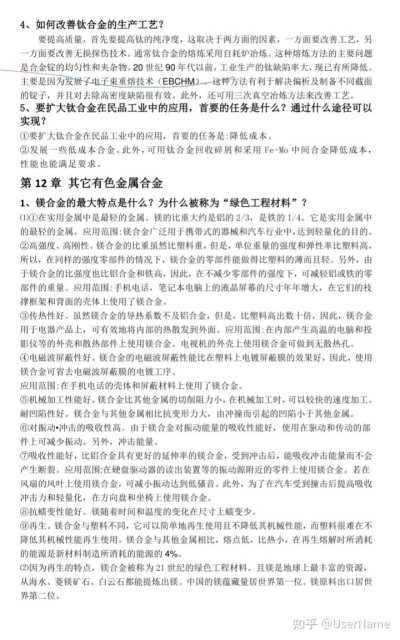
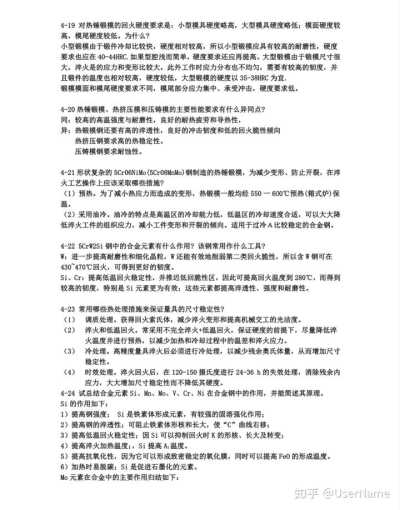
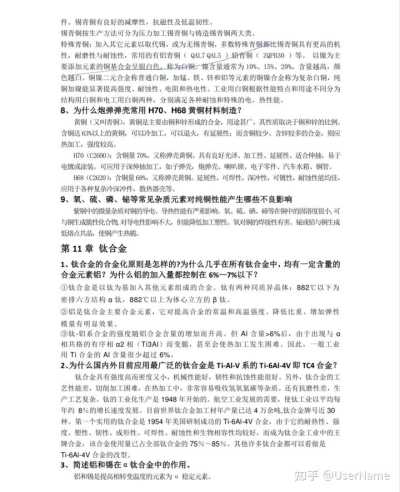
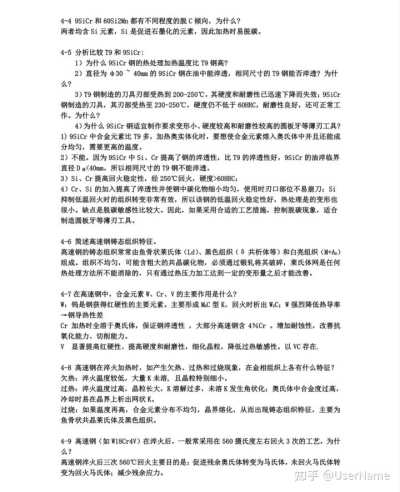
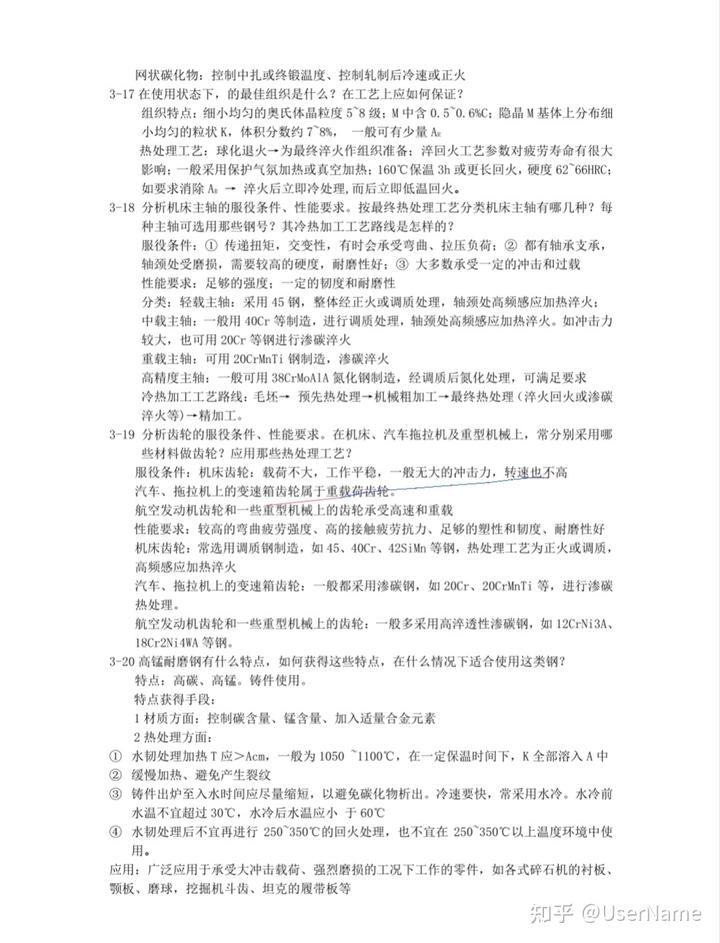
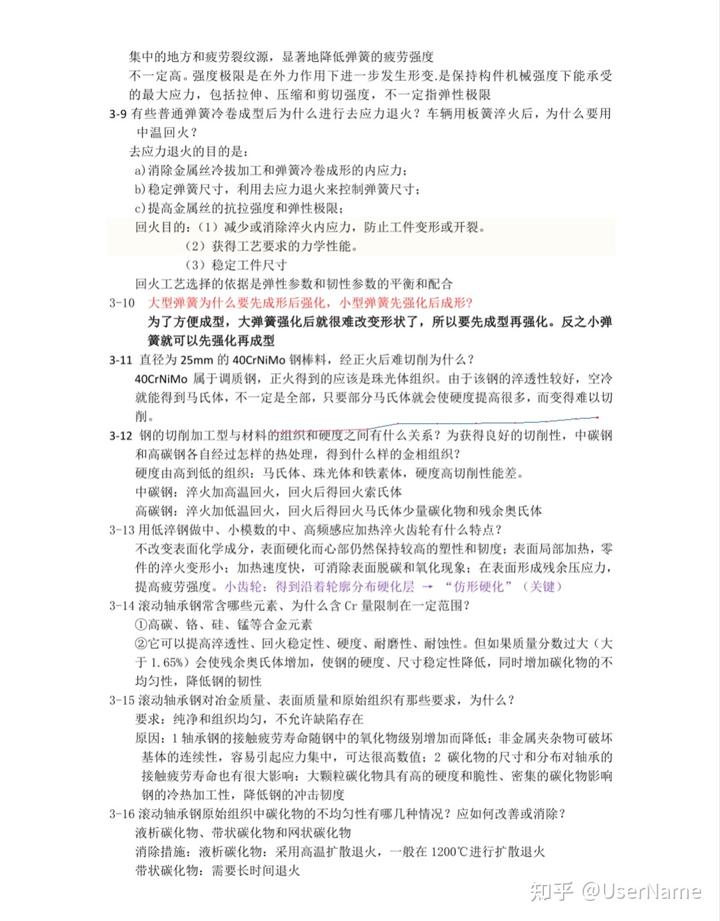
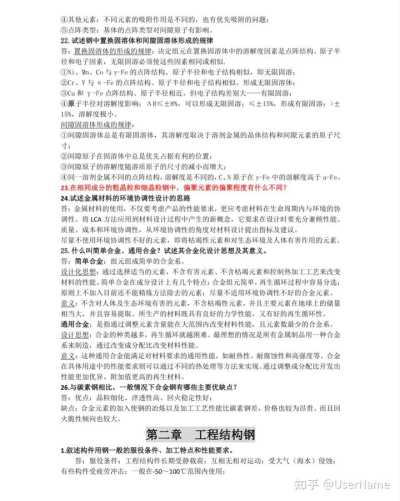
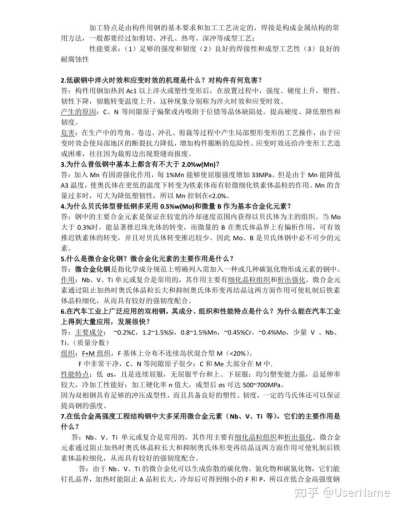
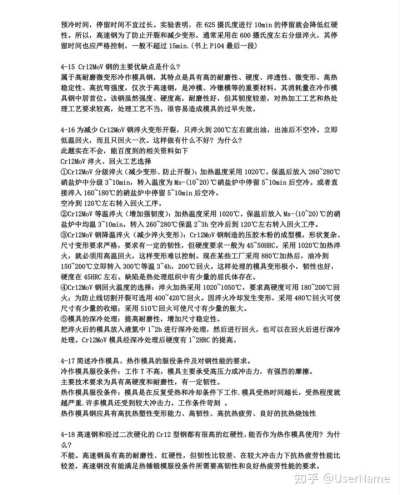
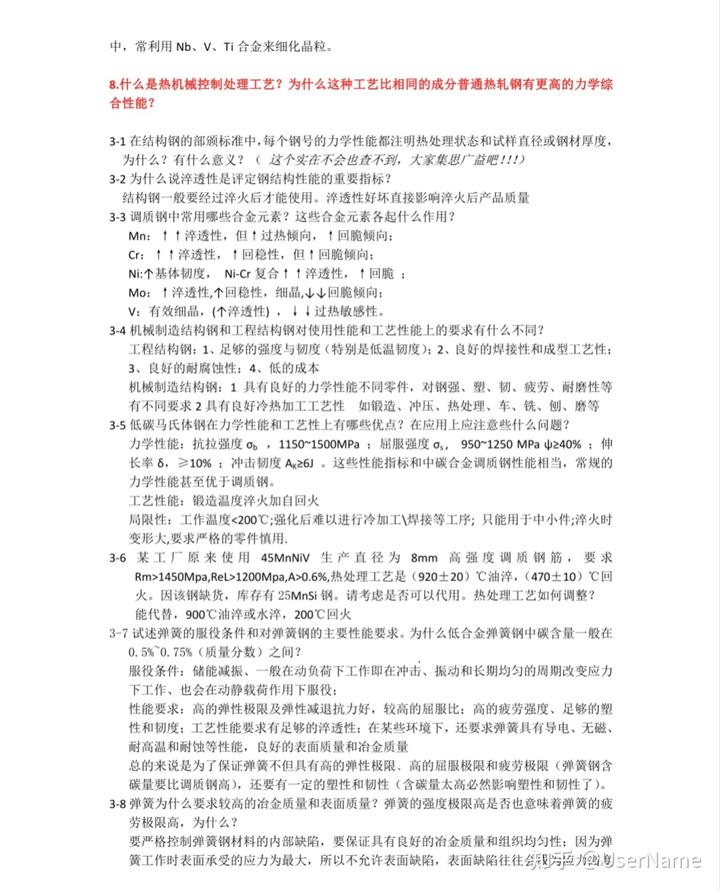
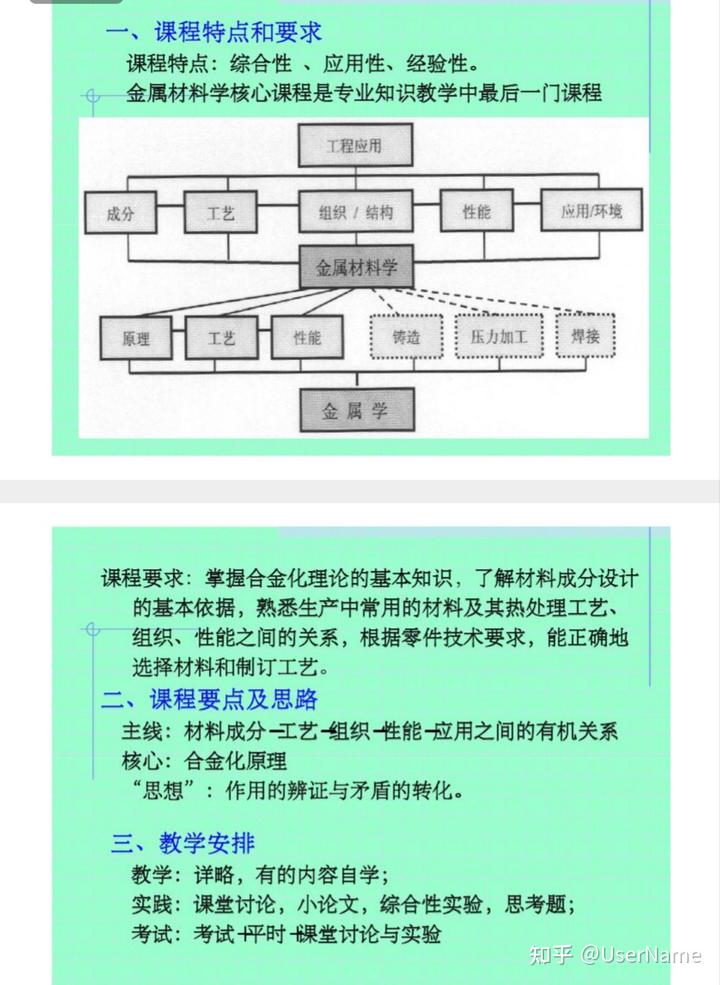
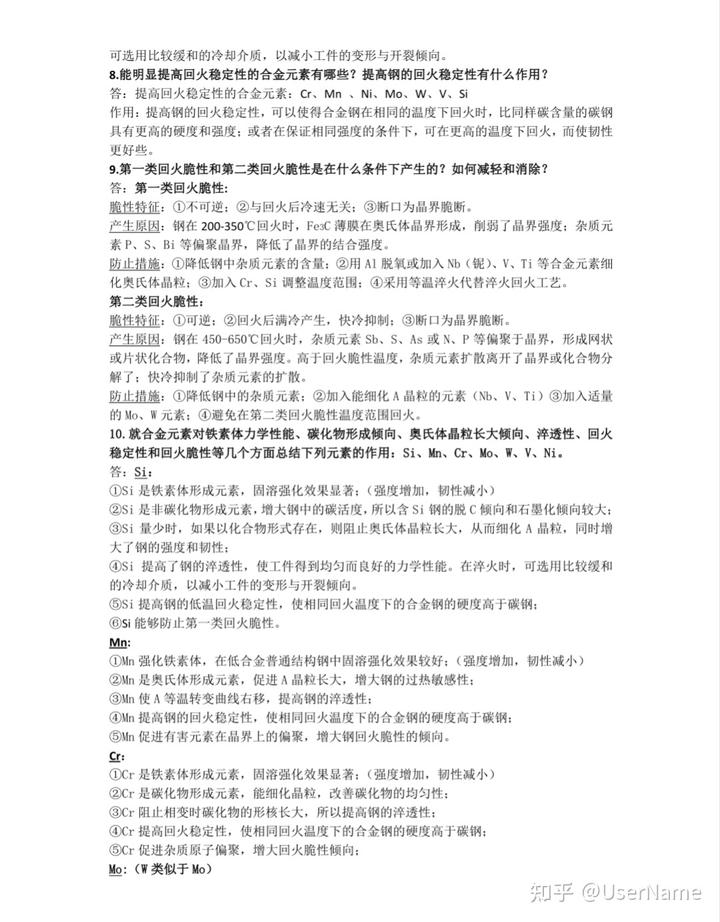
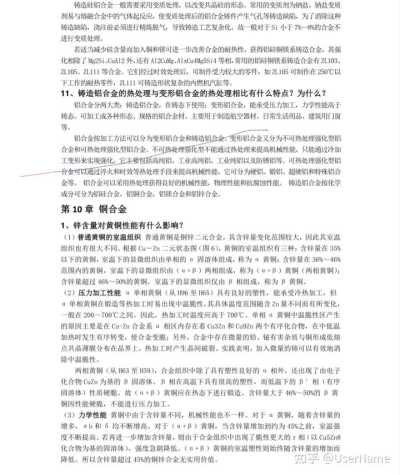
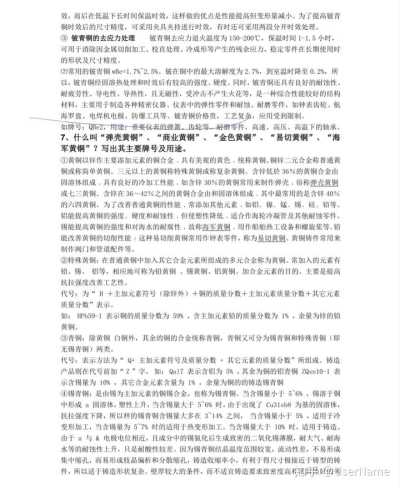
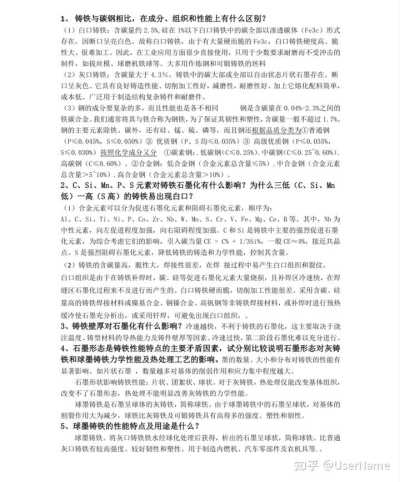
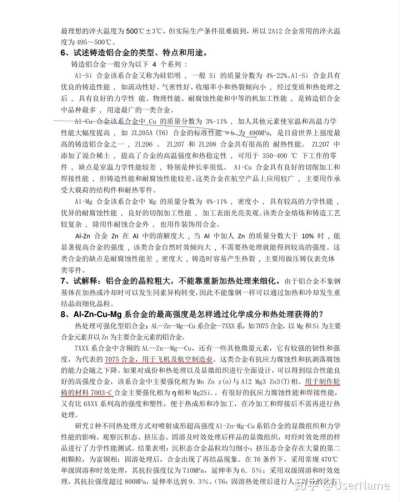
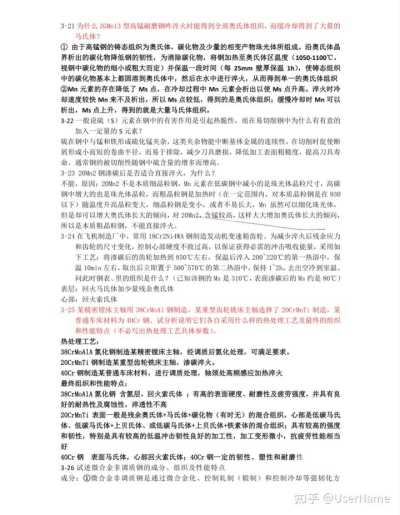
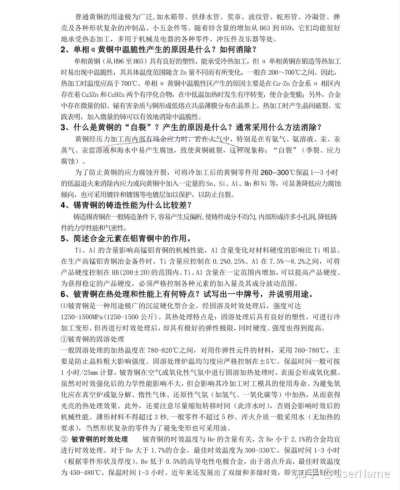
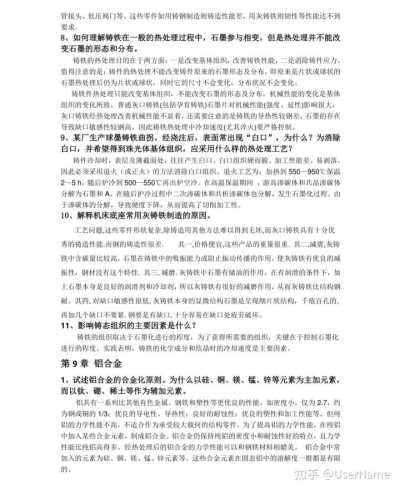
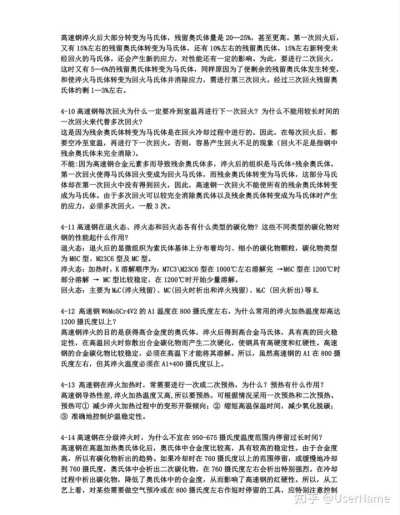
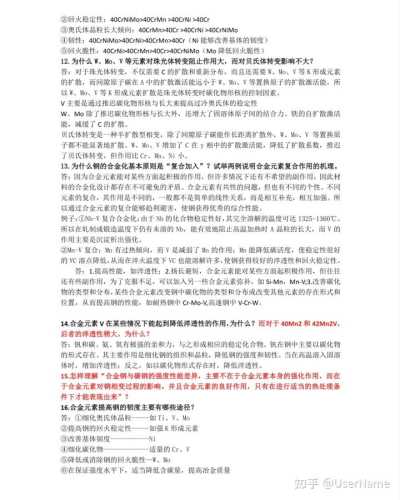
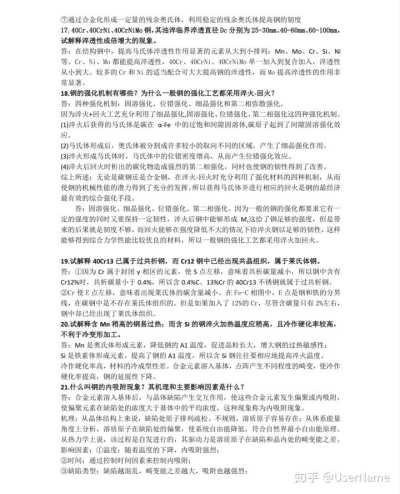
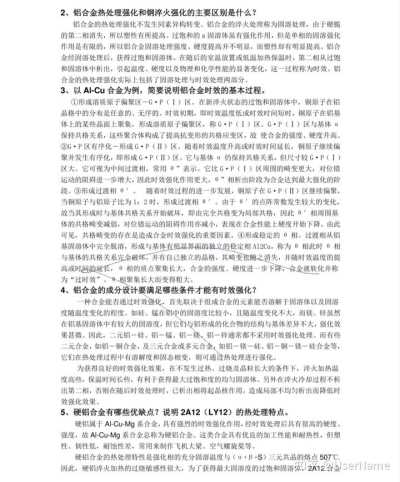
重载主轴:可用20CrMnTi钢制造,渗碳淬火
高精度主轴:一般可用38CrMoAlA氮化钢制造,经调质后氮化处理,可满足要求冷热加工工艺路线:毛坯→·预先热处理→机械粗加工→最终热处理(淬火回火或渗碳淬火等)→精加工。
3-19分析齿轮的服役条件、性能要求。在机床、汽车拖拉机及重型机械上,常分别采用哪些材料做齿轮?应用那些热处理工艺?
服役条件:机床齿轮:载荷不大,工作平稳,一般无大的冲击力,转速也不高
汽车、拖拉机上的变速箱齿轮属于重载荷齿轮。
航空发动机齿轮和一些重型机械上的齿轮承受高速和重载
性能要求:较高的弯曲疲劳强度、高的接触疲劳抗力、足够的塑性和韧度、耐磨性好机床齿轮:常选用调质钢制造,如45、40Cr、42SiMn等钢,热处理工艺为正火或调质,高频感应加热淬火
汽车、拖拉机上的变速箱齿轮:一般都采用渗碳钢,如20Cr、20CrMnTi等,进行渗碳热处理。
航空发动机齿轮和一些重型机械上的齿轮:一般多采用高淬透性渗碳钢,如12CrNi3A、18Cr2Ni4WA等钢。
3-20高锰耐磨钢有什么特点,如何获得这些特点,在什么情况下适合使用这类钢?
特点:高碳、高锰。铸件使用。
特点获得手段:
1材质方面:控制碳含量、锰含量、加入适量合金元素
2热处理方面:
①水韧处理加热T应>Acm,一般为1050~1100℃,在一定保温时间下,K全部溶入A中
②缓慢加热、避免产生裂纹
③铸件出炉至入水时间应尽量缩短,以避免碳化物析出。冷速要快,常采用水冷。水冷前水温不宜超过30℃,水冷后水温应小于60℃
④水韧处理后不宜再进行250~350℃的回火处理,也不宜在250~350℃以上温度环境中使用
应用:广泛应用于承受大冲击载荷、强烈磨损的工况下工作的零件,如各式碎石机的衬板、
颚板、磨球,挖掘机斗齿、坦克的履带板等
3-21为什么ZGMn13型高锰耐磨钢咋淬火时能得到全部奥氏体组织,而缓冷却得到了大量的马氏体?
①由于高锰钢的铸态组织为奥氏体,碳化物及少量的相变产物珠光体所组成。沿奥氏体晶界析出的碳化物降低钢的韧性,为消除碳化物,将钢加热至奥氏体区温度(1050-1100℃,视钢中碳化物的细小或粗大而定)并保温一段时间(每25mm壁厚保温1h),使铸态组织中的碳化物基本上都固溶到奥氏体中,然后在水中进行淬火,从而得到单一的奥氏体组织②Mn元素的存在降低了Ms点,在冷却过程中Mn元素会析出以使Ms点升高。淬火时冷却速度较快Mn来不及析出,所以Ms点较低,得到的是奥氏体组织;缓慢冷却时Mn可以析出,Ms点上升,得到的就是大量马氏体组织。
3-22一般说硫(S)元素在钢中的有害作用是引起热脆性,而在易切削钢中为什么有有意的加入一定量的S元素?
硫在钢中与锰和铁形成硫化锰夹杂,这类夹杂物能中断基体金属的连续性,在切削时促使断屑形成小而短的卷曲半径,而易于排除,减少刀具磨损,降低加工表面粗糙度,提高刀具寿命。通常钢的被切削性随钢中硫含量的增多而增高。
3-2320Mn2钢渗碳后是否适合直接淬火,为什么?
不能,原因:20Mn2不是本质细晶粒钢,Mn元素在低碳钢中减小的是珠光体晶粒尺寸,高碳钢中增大的也是珠光体晶粒,而粗品粒钢是加热时(在一定范围内,对本质晶粒钢是在930以下)随温度升高品粒变大,细晶粒钢是变小,或者不易长大,Mn虽然可以细化珠光体,但是却可以增大奥氏体长大的倾向,对20Mn2,含锰较高,这样大大增加奥氏体长大的倾向,所以是本质粗晶粒钢,不能直接淬火。
3-24在飞机制造厂中,常用18Cr2Ni4WA钢制造发动机变速箱齿轮。为减少淬火后残余应力
和齿轮的尺寸变化,控制心部硬度不致过高,以保证获得必需的冲击吸收能量,采用如
下工艺:将渗碳后的齿轮加热到850℃左右,保温后淬入200~220℃的第一热浴中,保
温10min左右,取出后立即置于500~570℃的第二热浴中,保持1~2h,去出空冷到室温。
问此时钢表、里的组织是什么?(已知该钢的Ms是310℃,表面渗碳后的Ms约是80℃)表层:回火马氏体加少量残余奥氏体
心部:回火索氏体
3-25某精密镗床主轴用38CrMoAl钢制造,某重型齿轮铣床主轴选择了20CrMnTi制造,某
普通车床材料为40Cr钢。试分析说明它们各自采用什么样的热处理工艺及最终的组织
和性能特点(不必写出热处理工艺具体参数)
热处理工艺:
38CrMoAlA氮化钢制造某精密镗床主轴,经调质后氮化处理,可满足要求。
20CrMnTi钢制造某重型齿轮铣床主轴,渗碳淬火。
40Cr钢制造某普通车床材料,进行调质处理,轴颈处高频感应加热淬火
最终组织和性能特点:
38CrMoAlA氮化钢含氮层,回火索氏体;有高的表面硬度、耐磨性及疲劳强度,并具有良好的耐热性及腐蚀性,淬透性不高
20CrMnTi表面一般是残余奥氏体+马氏体+碳化物(有时无)的混合组织,心部是低碳马氏体、低碳马氏体+上贝氏体、或低碳马氏体+上贝氏体+铁素体的混合组织;具有较高的强度和韧性,特别是具有较高的低温冲击韧性良好的加工性,加工变形微小,抗疲劳性能相当好
40Cr钢表面马氏体,心部回火索氏体;40Cr钢一定的韧性、塑性和耐磨性
3-26试述微合金非调质钢的成分、组织及性能特点
成分:①微合金非调质钢是通过微合金化、控制轧制(锻制)和控制冷却等强韧化方
法,取消了调质处理达到或接近调质钢力学性能的一类优质或特殊质量结构钢
②微合金化元素:Ti、Nb、V、N等元素,V是主要的。多元适量,复合加入原则组织:主要是F+P+弥散析出K
性能特点:①微合金非调质钢获得了晶内析出铁素体(IGF)组织,细化了晶粒,热锻后的晶粒度可达8级以上。具有高强度、高韧性;②锻后空冷,抗拉强度、冲击韧度都很高3-27材料选用的基本原则有哪些?
①满足使用性能要求:
②满足工艺性能要求
③要经济适用
④其他因素:考虑外形和尺寸特点;合金化基本原则:多元适量,复合加入
3-28论述选择材料的基本思路和方法。
①分析材料的工作条件、尺寸形状和应力状态,科学合理的确定零件的技术要求:②通过分析分析或实验,结合同类型零件失效分析结果,找出实际工作时零件的主要和次要失效抗力指标作为选材的基本依据:
③根据所要求的主要力学性能,选择材料
④综合考虑钢种是否满足次要失效抗力指标的可能性和可能采用的工艺措施
⑤审查所选钢种是否满足所有工艺性基本要求和组织生产的可能性,进一步考虑材料的经济性和生产成本
尽量选择简化加工工艺的材料、要考虑零件的综合成本、保证淬透性钢的合理选择4-1在使用性能和工艺性能的要求上,工具钢和机器零件用钢有什么不同?
工具钢使用性能:
(1)硬度。工具钢制成工具经热处理后具有足够高的硬度。工具在高的切削速度和加工硬材料所产生高温的受热条件下,仍能保持高的硬度和良好的红硬性。
(2)耐磨性。工具钢具有良好的耐磨性,即抵抗磨损的能力。工具在承受相当大的压力和摩擦力的条件下,仍能保持其形状和尺寸不变。
(3)强度和韧性。工具钢具有一定的强度和韧性,使工具在工作中能够承受负荷、冲击、震动和弯曲等复杂的应力,以保证工具的正常使用。
(4)其他性能。由于各种工具的工作条件不同,工具用钢还具有一些其他性能,如模具用钢还应具有一定的高温力学性能、热疲劳性、导热性和耐磨腐蚀性能等。
工艺性能:
(1)加工性.工具钢应具有良好的热压力加工性能和机械加工性能,才能保证工具的制造和使用。钢的加工性取决于化学成分、组织的质量。
(2)淬火温度范围.工具钢的淬火温度应足够宽,以减少过热的可能性。
(3)淬硬性和淬透性.淬硬性是钢在淬火后所能达到最高硬度的性能。淬硬性主要与钢的化学成分特别是碳含量有关,碳含量越高,则钢的淬硬性越高。淬透性表示钢在淬火后
从表面到内部的硬度分布状况。淬透性的高低与钢的化学成分、纯洁度、晶粒度有关。根据用于制造不同的工具,对这两种性能各有一定的要求。
(4)脱碳敏感性.工具表面发生脱碳,将使表面层硬度降低,因此要求工具钢的脱碳敏感性低。在相同的加条件下,钢的脱碳敏感性取决于其化学成分。
(5)热处理变形性.工具在热处理时,要求其尺寸和外形稳定。
(6)耐削性.对很制造刀具和量具用钢。要求具有良好的磨削性。钢的磨削性与其化学成分有关,特别是钒含量,如果钒质量分数不小于0.50%则磨削性变坏。
机器零件用钢使用性能:
(1)较高的疲劳强度和耐久强度。
(2)高的屈服强、抗拉强度以及较高的断裂抗力。
(3)良好的耐磨性和接触疲劳强度。
(4)较高的韧性,以降低缺口敏感性。
工艺性能:
通常机器零件的生产工艺:型材→改锻→毛坯热处理→切削加工→最终热处理→磨削以切削加工性能和热处理工艺性能为机器零件用钢的主要工艺性能。
4-2工具钢常要做那些力学性能试验?测定哪些性能指标?为什么?
强度、塑性:静弯或扭转试验→弯曲强度、挠度和扭转强度、扭转角;
韧度:一般采用无缺口式样;
硬度:一般硬度60HRC以上,钢中存在的大量碳化物可提高2~3HRC;
淬透性:断口法→碳素工具钢和低合金工具钢;端淬法→合金工具钢,以端淬曲线上60HRC处距水冷端距离表示。淬透性作用强弱顺序:Si、Mn、Mo、Cr、Ni
热稳定性:(钢在较高温度下保持一定强度的性质)对高速钢,通常是红硬性;
变形开裂倾向:主要原因是热应力组织应力。
4-3试用合金化原理分析说明9SiCr、9Mn2V、CrWMn钢的优缺点。
9SiCr①Si、Cr提高淬透性,油淬临界直径D油<40mm;
②Si、Cr提高回火稳定性,经250℃回火,硬度>60HRC;
③K细小、均匀→不容易崩刃;
④通过分级淬火或等温淬火处理,变形较小;
⑤Si使钢的脱碳倾向较大。
CrWMn①Cr、W、Mn复合,有较高透性,D油=50~70mm;
②淬火后A在18~20%,淬火后变形小;
③含Cr、W碳化物较多且较稳定,晶粒细小→高硬度、高耐磨性;
④回稳性较好,当回火温度>250℃,硬度才<60HRC;
⑤W使碳化物易形成网状。
9Mn2V
1)Mn↑淬透性,D油=~30mm;
2)MnMs,淬火后A较多,约20~22%,使工件变形较小;
3)V能克服Mn的缺点,↓过热敏感性,且能细化晶粒;
4)含0.9%C左右,K细小均匀,但钢的硬度稍低,回火稳定性较差,宜在200℃以下回火;5)钢中的VC使钢的磨削性能变差。9Mn2V广泛用于各类轻载、中小型冷作模具。
4-49SiCr和60Si2Mn都有不同程度的脱C倾向,为什么?
两者均含Si元素,Si是促进石墨化的元素,因此加热时易脱碳。
4-5分析比较T9和9SiCr:
1)为什么9SiCr钢的热处理加热温度比T9钢高?
2)直径为30~40mm的9SiCr钢在油中能淬透,相同尺寸的T9钢能否淬透?为什么?3)T9钢制造的刀具刃部受热到200-250℃,其硬度和耐磨性已迅速下降而失效;9SiCr钢制造的刀具,其刃部受热至230-250℃,硬度仍不低于60HRC,耐磨性良好,还可正常工作。为什么?
4)为什么9SiCr钢适宜制作要求变形小、硬度较高和耐磨性较高的圆板牙等薄刃工具?1)9SiCr中合金元素比T9多,加热奥实体化时,要想使合金元素熔入奥氏体中并且还能成分均匀,需要更高的温度。
2)不能。因为9SiCr中Si、Cr提高了钢的淬透性,比T9的淬透性好,9SiCr的油淬临界直径D油<40mm,所以相同尺寸的T9钢不能淬透。
3)Si、Cr提高回火稳定性,经250℃回火,硬度>60HRC
4)Cr、Si的加入提高了淬透性并使钢中碳化物细小均匀,使用时刃口部位不易崩刀;Si抑制低温回火时的组织转变非常有效,所以该钢的低温回火稳定性好,热处理是的变形也很小。缺点是脱碳敏感性比较大。因此,如果采用合适的工艺措施,控制脱碳现象,适合制造圆板牙等薄刃工具。
4-6简述高速钢铸态组织特征。
高速钢的铸态组织常常由鱼骨状莱氏体(Ld)、黑色组织(共析体等)和白亮组织(M+A)组成。组织不均匀,可能含粗大的共晶碳化物,必须通过锻轧将其破碎,莱氏体网是任何热处理方法所不能消除的,只有通过热压力加工达到一定的变形量之后才能改善。
4-7在高速钢中,合金元素W、Cr、V的主要作用是什么?
W:钨是钢获得红硬性的主要元素。主要形成MC型K,回火时析出WC:W强烈降低热导率→钢导热性差
Cr加热时全溶于奥氏体,保证钢淬透性,大部分高速钢含4%Cr。增加耐蚀性,改善抗氧化能力、切削能力。
V显著提高红硬性、提高硬度和耐磨性,细化晶粒,降低过热敏感性。以VC存在
4-8高速钢在淬火加热时,如产生欠热、过热和过烧现象,在金相组织上各有什么特征?欠热:淬火温度较低,大量K未溶,且晶粒特别细小。
过热:淬火温度过高,晶粒长大,K溶解过多,未溶K发生角状化;奥氏体中合金度过高,冷却时易在晶界上析出网状K。
过烧:如果温度再高,合金元素分布不均匀,晶界熔化,从而出现铸态组织特征,主要为鱼骨状共晶莱氏体及黑色组织。
4-9高速钢(如W18Cr4V)在淬火后,一般常采用在560摄氏度左右回火3次的工艺,为什么?
高速钢淬火后三次560℃回火主要目的是:促进残余奥氏体转变为马氏体,未回火马氏体转变为回火马氏体;减少残余应力。
高速钢淬火后大部分转变为马氏体,残留奥氏体量是20—25%,甚至更高。第一次回火后,又有15%左右的残留奥氏体转变为马氏体,还有10%左右的残留奥氏体,15%左右新转变未经回火的马氏体,还会产生新的应力,对性能还有一定的影响。为此,要进行二次回火,这时又有5-6%的残留奥氏体转变为马氏体,同样原因为了使剩余的残留奥氏体发生转变,和使淬火马氏体转变为回火马氏体并消除应力,需进行第三次回火。经过三次回火残留奥氏体约剩1—3%左右。
4-10高速钢每次回火为什么一定要冷到室温再进行下一次回火?为什么不能用较长时间的一次回火来代替多次回火?
这是因为残余奥氏体转变为马氏体是在回火冷却过程中进行的。因此,在每次回火后,都要空冷至室温,再进行下一次回火。否则,容易产生回火不足的现象(回火不足是指钢中残余奥氏体未完全消除)。
不能:因为高速钢合金元素多而导致残余奥氏体多,淬火后的组织是马氏体+残余奥氏体,第一次回火使得马氏体回火变成为回火马氏体,而残余奥氏体转变为马氏体,这部分马氏体却在第一次回火中没有得到回火,因此,高速钢一次回火不能使所有的残余奥氏体转变成为马氏体。由于多次回火可以较完全消除奥氏体以及残余奥氏体转变成为马氏体时产生的应力,必须多次回火,一般3次。
4-11高速钢在退火态、淬火态和回火态各有什么类型的碳化物?这些不同类型的碳化物对钢的性能起什么作用?
退火态:退火后的显微组织为索氏体基体上分布着均匀、细小的碳化物颗粒,碳化物类型为M6C型、M23C6型及MC型。
淬火态:加热时,K溶解顺序为:M7C3M23C6型在1000℃左右溶解完→M6C型在1200℃时部分溶解→MC型比较稳定,在1200℃时开始少量溶解。
回火态:主要为MC(淬火残留)、MC(回火时析出和淬火残留)、MC(回火析出)等K.
4-12高速钢W6Mo5Cr4V2的A1温度在800摄氏度左右,为什么常用的淬火加热温度却高达1200摄氏度以上?
高速钢淬火的目的是获得高合金度的奥氏体,淬火后得到高合金马氏体,具有高的回火稳定性,在高温回火时弥散出合金碳化物而产生二次硬化,使钢具有高硬度和红硬性。高速钢的合金碳化物比较稳定,必须在高温下才能将其溶解。所以,虽然高速钢的A1在800摄氏度左右,但其淬火温度必须在A1+400摄氏度以上。
4-13高速钢在淬火加热时,常需要进行一次或二次预热,为什么?预热有什么作用?
高速钢导热性差,淬火加热温度又高,所以要预热。可根据情况采用一次预热和二次预热。预热可①减少淬火加热过程中的变形开裂倾向;②缩短高温保温时间,减少氧化脱碳;③准确地控制炉温稳定性。
4-14高速钢在分级淬火时,为什么不宜在950-675摄氏度温度范围内停留过长时间?
高速钢在高温加热奥氏体化后,奥氏体中合金度比较高,具有较高的稳定性。由于合金度高,所以有碳化物析出的趋势。如果冷却时在760摄氏度以上的范围停留,或缓慢地冷却到760摄氏度,奥氏体中会析出二次碳化物,在760摄氏度左右会析出特别强烈。在冷却过程中析出碳化物,降低了奥氏体中的合金度,从而影响了高速钢的红硬性。所以,从工艺上看,对某些需要做空气预冷或在800摄氏度左右作短时停留的工具,应特别注意控制
预冷时间,停留时间不宜过长。实验表明,在 625 摄氏度进行 10min 的停留就会降低红硬性。所以,高速钢为了防止开裂和减少变形,通常采用在 600 摄氏度左右分级淬火,其停留时间也应严格控制,一般不超过 15min.(书上 P104 最后一段)
4-15 Cr12MoV 钢的主要优缺点是什么?
属于高耐磨微变形冷作模具钢,其特点是具有高的耐磨性、硬度、淬透性、微变形、高热稳定性、高抗弯强度,仅次于高速钢,是冲模、冷镦模等的重要材料,其消耗量在冷作模具钢中居首位。该钢虽然强度、硬度高,耐磨性好,但其韧度较差,对热加工工艺和热处理工艺要求较高,处理工艺不当,很容易造成模具的过早失效。
4-16 为减少 Cr12MoV 钢淬火变形开裂,只淬火到 200℃左右就出油,出油后不空冷,立即低温回火,而且只回火一次。这样做有什么不好?为什么?
此题实在不会,能百度到的相关资料如下
Cr12MoV 淬火、回火工艺选择
①Cr12MoV 分级淬火(减少变形、防止开裂):加热温度采用 1020℃,保温后放入 260~280℃硝盐炉中分级 3~10min,转入温度为 Ms-(10~20) ℃硝盐炉中停留 5~10min 后空冷。或者直接淬入 160~180℃的硝盐炉中停留 5~10min 后空冷。
空冷到 120℃左右转入回火工序。
②Cr12MoV 等温淬火(增加强韧度):加热温度采用 1020℃,保温后放入 Ms-(10~20) ℃的硝盐炉中均温 3~10min,转入 260~280℃保温 2~3h 空冷后到 120℃左右转入回火工序。
③Cr12MoV 钢降温淬火(减少淬火变形):Cr12MoV 钢制造的压胶木粉的成型模,形状复杂、尺寸变形要求严格,要求有一定的韧性,但硬度要求一般为 45~50HRC。采用 1020℃加热淬火,就必须用高温回火,这样变形难以控制。现在某些工厂采用 880℃加热后,油冷到150~200℃立即转入 300℃等温 3~4h,200℃回火。这样处理的模具变形极小,韧性也好,硬度在 45HRC 左右。缺陷是热处理组织中有少量的屈氏体存在。
④Cr12MoV钢回火温度的选择:淬火加热采用1020~1050℃,要求高硬度可用180~200℃回火;为防止线切割开裂可选用 400~420℃回火。因淬火冷却发生变形,采用 480℃回火可使尺寸有少量的收缩;采用 510℃回火可使尺寸有少量的胀大。
⑤模具的深冷处理:提高耐磨性,增加尺寸稳定性。
把淬火后的模具放入液氮中 1~2h 进行深冷处理,然后进行回火,也可以在回火后进行深冷处理。Cr12MoV 模具经深冷处理后硬度有 1~2HRC 的提高。
4-17 简述冷作模具、热作模具的服役条件及对钢性能的要求。
冷作模具服役条件:工作T不高,模具主要承受高压力或冲击力,有强烈的摩擦。
主要技术要求为具有高硬度和耐磨性,有一定韧性。
热作模具服役条件:模具是在反复受热和冷却条件下工作.模具受热时间越长,受热程度就越严重.许多模具还受到较大冲击力。工作条件苛刻 。
热作模具钢应具有高抗热塑性变形能力、高韧性、高抗热疲劳、良好的抗热烧蚀性
4-18 高速钢和经过二次硬化的 Cr12 型钢都有很高的红硬性,能否作为热作模具使用?为什么?
不能。高速钢虽有高的耐磨性、红硬性,但韧性比较差、在较大冲击力下抗热疲劳性能比较差,高速钢没有能满足热锤锻模服役条件所需要高韧性和良好热疲劳性能的要求。
4-19 对热锤锻模的回火硬度要求是:小型模具硬度略高,大型模具硬度略低;模面硬度较高,模尾硬度较低。为什么?
小型锻模由于锻件冷却比较快,硬度相对较高,所以小型锻模应具有较高的耐磨性,硬度要求也应在40-44HRC.如果型腔浅而简单,硬度要求还应再提高。大型锻模由于锻模尺寸很大,淬火是的应力和变形比较大,此外工作时应力分布也不均匀,需要有较高的韧度,并且锻件的温度也相对较高,硬度较低,大型锻模的硬度以35-38HRC为宜.
锻模模面和模尾硬度要求不同,模尾部分应力集中、承受冲击,硬度要求低
4-20 热锤锻模、热挤压模和压铸模的主要性能要求有什么异同点?
同:较高的高温强度与耐磨性,良好的耐热疲劳和导热性,
异:热锻模钢还要有高的淬透性,良好的冲击韧度和低的回火脆性倾向
热挤压钢要求高的热稳定性。
压铸模钢要求耐蚀性。
4-21形状复杂的5Cr06NiMo (5Cr08MnMo)钢制造的热锤锻模,为减少变形、防止开裂,在淬火工艺操作上应该采取哪些措施?
(1)预热。为了减小热应力而造成的变形,热锻模一般均经 550 一 600℃预热(箱式炉)保温。
(2)采用油冷。油冷的特点是高温区的冷却能力低,低温区的冷却速度合适,可以大大降低淬火工件的组织应力,减小工件变形和开裂的倾向。适用于过冷A比较稳定的合金钢。4-22 5CrW2Si 钢中的合金元素有什么作用?该钢常用作什么工具?
W:进一步提高耐磨性和细化晶粒,W 还能有效地削弱第二类回火脆性,所以含W 钢可在430~470℃回火,可得到更好的韧度。
Si、Cr:提高低温回火稳定性,并推迟低回脆性区,因此可提高回火温度到 280℃,而得到较高的韧度,特别是Si元素更为有效;这些元素都提高淬透性、强度和耐磨性。
4-23 常用哪些热处理措施来保证量具的尺寸稳定性?
(1) 调质处理。获得回火索氏体,减少淬火变形和提高机械交工的光洁度。
(2) 淬火和低温回火。常采用不完全淬火+低温回火,保证硬度的前提下,尽量降低淬
火温度并进行预热,以减少加热和冷却过程中的温差和淬火应力。
(3) 冷处理。高精度量具淬火后必须进行冷处理,以减少残余奥氏体量,从而增加尺寸
稳定性。
(4)时效处理。淬火回火后,在 120-150 摄氏度进行 24-36 h 的失效处理,消除残余内
应力,大大增加尺寸稳定性而不降低其硬度。
4-24 试总结合金元素 Si、Mn、Mo、V、Cr、Ni 在合金钢中的作用,并能简述其原理。
Si 的作用如下:
1)提高钢强度; Si 是铁素体形成元素,有较强的固溶强化作用;
2)提高钢的淬透性;可阻止铁素体形核和长大,使“C”曲线右移;
3)提高低温回火稳定性;因Si可以抑制回火时K的形核、长大及转变;
4)提高淬火加热温度;, Si提高A1温度。
5)提高抗氧化性,因为它可以形成致密稳定的氧化膜,同时可以提高Fe0的形成温度。6)加热时易脱碳;Si是促进石墨化的元素。
Mo 元素在合金中的主要作用归结如下:
(1)降低回火脆性,一般认为Mo可以抑制有害元素在晶界的偏聚;
(2)提高贝氏体的淬透性,因为Mo大大推迟珠光体的转变而对贝氏体转变影响较小;(3)细化晶粒,提高回火稳定性。Mo是强碳化物形成元素,与碳的结合力较大形成的碳化物稳定,不易长大。
(4)提高热强性,因为Mo可以较强地提高固溶体原子的结合力。
(5)提高防腐性,特别是对于非氧化性介质。因为Mo可以形成致密而稳定的MoO膜;(6)提高红硬性,因Mo与C原子结合力强,故回火稳定性比较好并且形成的在高温下碳化物稳定。
Ni元素在合金钢中的作用:
1)↑基体韧度→Ni↓位错运动阻力,使应力松弛;
2)稳定A,→Ni↓A1,扩大Y区,量大时,室温为A组织;
3)↑淬透性→↓△G,使“C”线右移,Cr-Ni复合效果更好;
4)↑回火脆性→Ni促进有害元素偏聚;
5)Ms,Ar→马氏体相变驱动力。
Mn:强化F提高淬透性促进晶粒长大提高残余A含量,降低Ms点提高回火稳定性降低热脆性-脱硫
V:提高热强性细化晶粒提高红硬性、耐磨性降低过热倾向降低磨削性
Cr:提高淬透性提高回火稳定性提高抗氧化性,热强性提高耐蚀性细化晶粒降低Ms点
(合金元素作用归纳:
Cr:提高淬透性提高回火稳定性提高抗氧化性,热强性提高耐蚀性细化晶粒降
低Ms点
Mn:强化F提高淬透性促进晶粒长大提高残余A含量,降低Ms点提高回火稳定
性降低热脆性-脱硫
Si:提高8,降低可切削性提高低温回火稳定性提高抗氧化性提高淬透性提高淬
火温度提高脱C,石墨化倾向
Mo:提高淬透性提高热强性降低回火脆性提高回火稳定性细化晶粒提高非氧化
性酸的耐蚀性,防止点蚀
Ni:提高基体韧度稳定A组织提高淬透性提高回火脆性降低Ms点-提高残余A含
量
V:提高热强性细化晶粒提高红硬性、耐磨性降低过热倾向降低磨削性
Pb:提高切削性能)
4-25在工具钢中,讨论合金元素起淬透性作用时,应注意什么问题?
Me提高淬透性,只有溶入A中,才起作用;
Me的作用随钢中含碳量而变化,如Si。
工具钢淬透性随热处理条件而变化,如V
第8章铸铁
1、铸铁与碳钢相比,在成分、组织和性能上有什么区别?
(1)白口铸铁:含碳量约2.5%,硅在1%以下白口铸铁中的碳全部以渗透碳体(Fe3c)形式存在,因断口呈亮白色。故称白口铸铁,由于有大量硬而脆的Fe3c,白口铸铁硬度高、脆性大、很难加工。因此,在工业应用方面很少直接使用,只用于少数要求耐磨而不受冲击的制件,如拔丝模、球磨机铁球等。大多用作炼钢和可锻铸铁的坯料
(2)灰口铸铁;含碳量大于4.3%,铸铁中的碳大部或全部以自由状态片状石墨存在。断口呈灰色。它具有良好铸造性能、切削加工性好,减磨性,耐磨性好、加上它熔化配料简单,成本低、广泛用于制造结构复杂铸件和耐磨件。
(3)钢的成分要复杂的多,而且性能也是各不相同钢是含碳量在0.04%-2.3%之间的
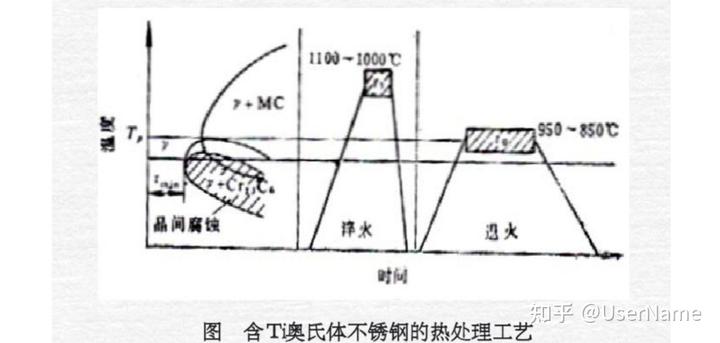
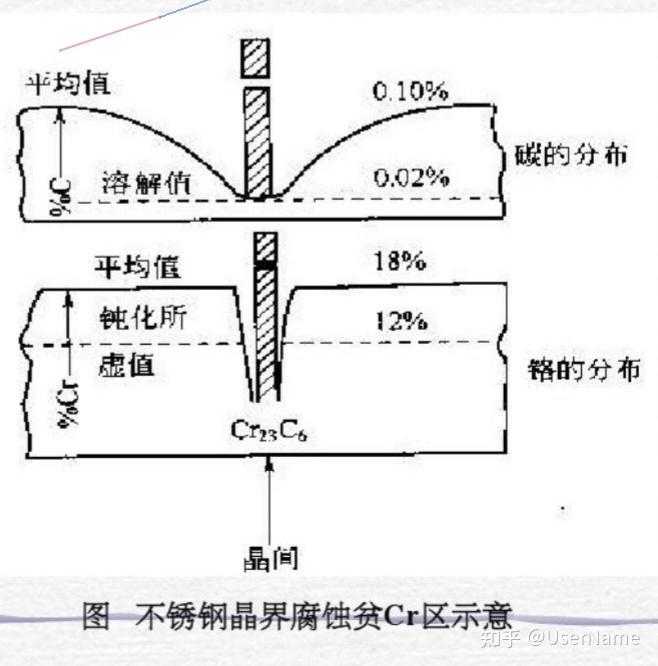
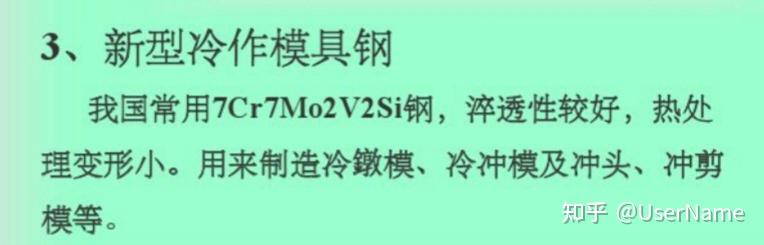
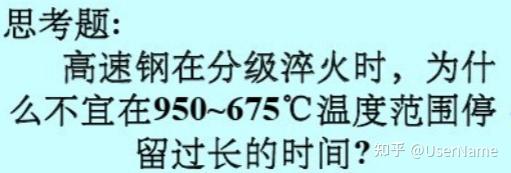
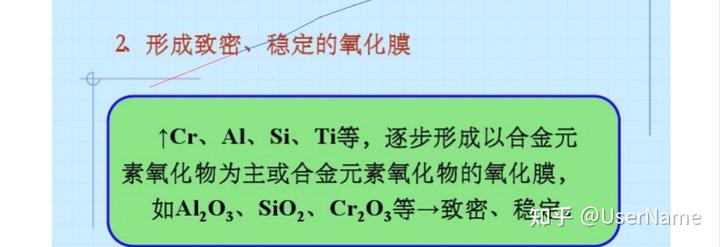
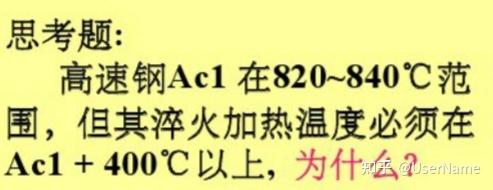
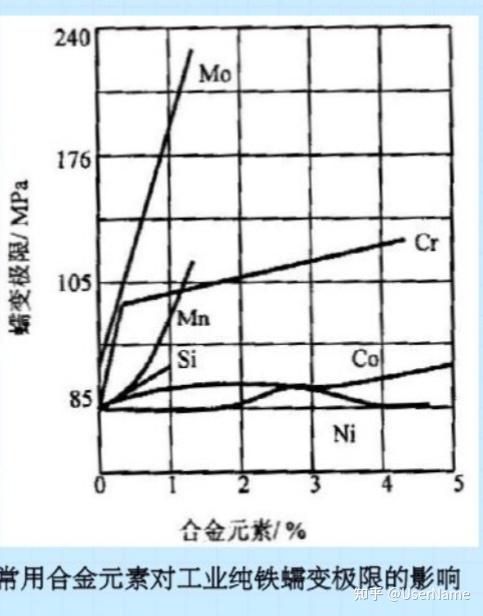
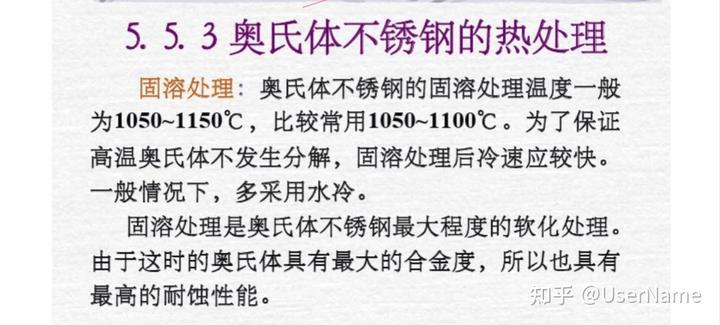
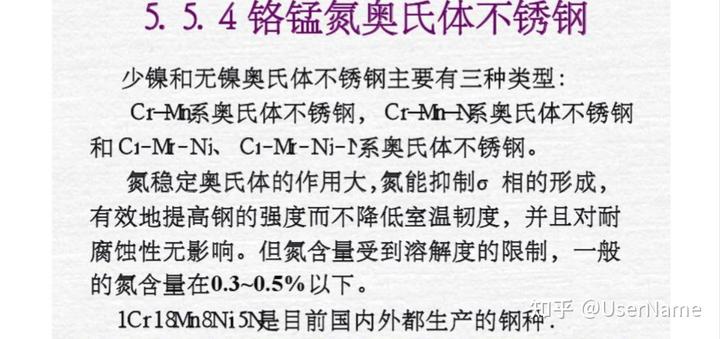
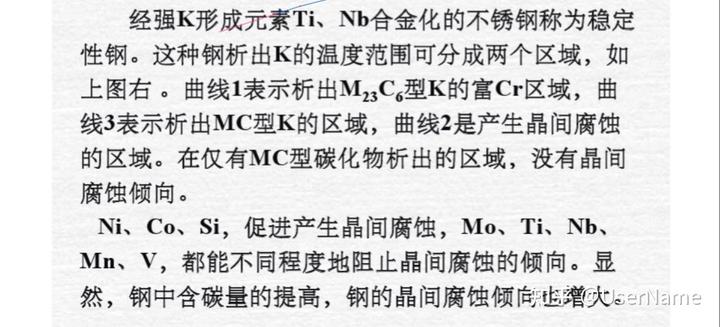
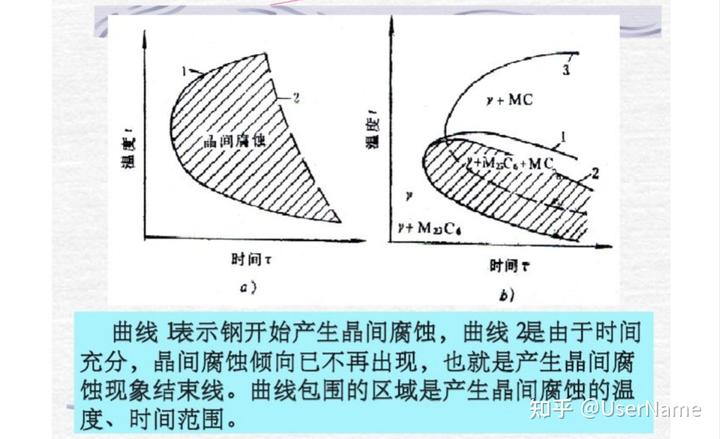
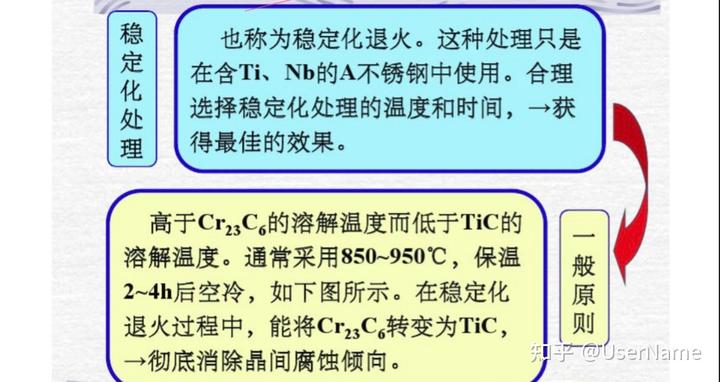
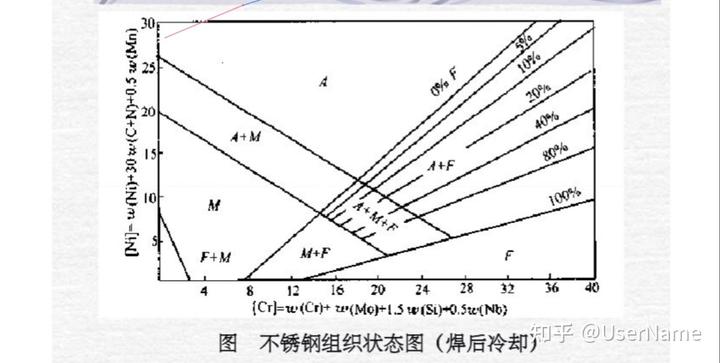
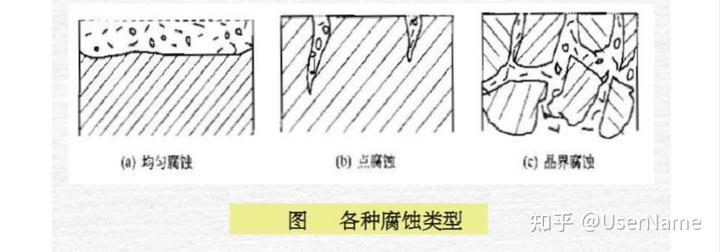
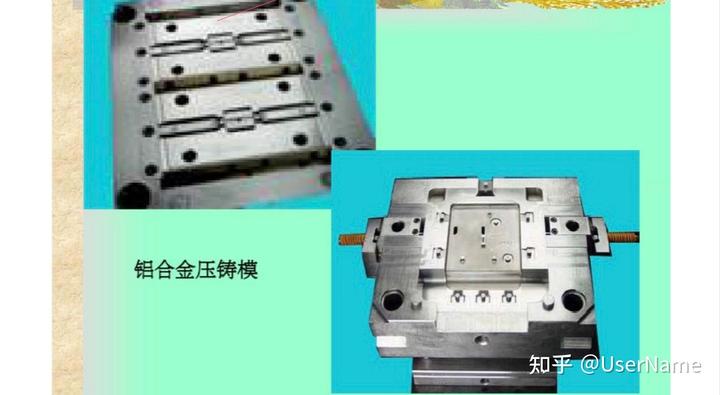
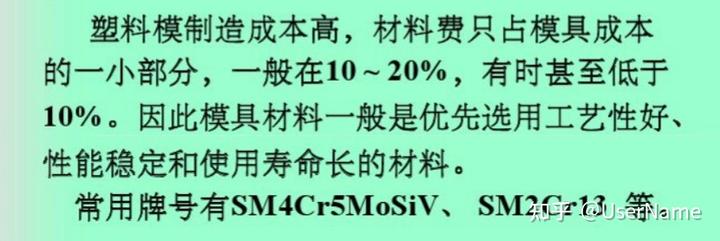
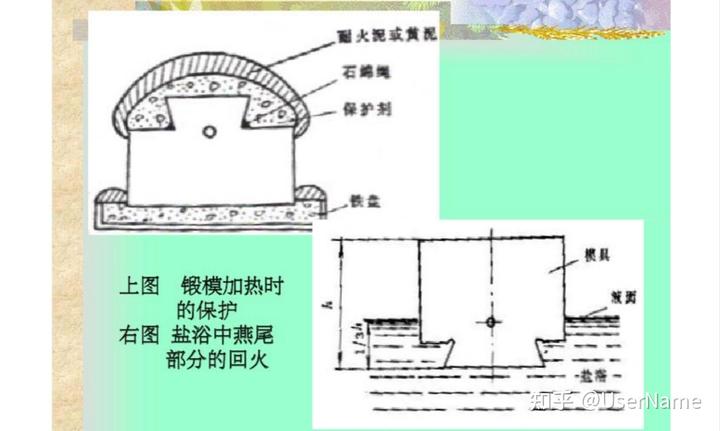
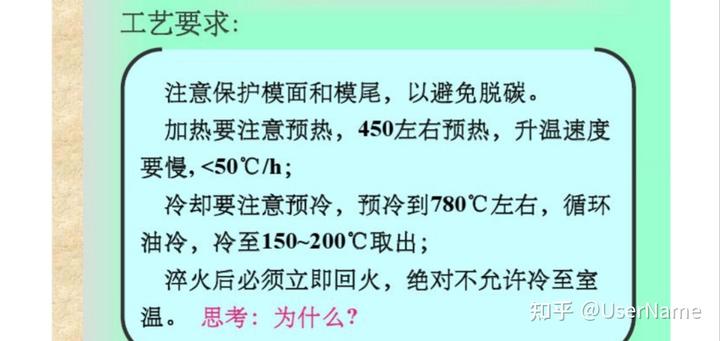
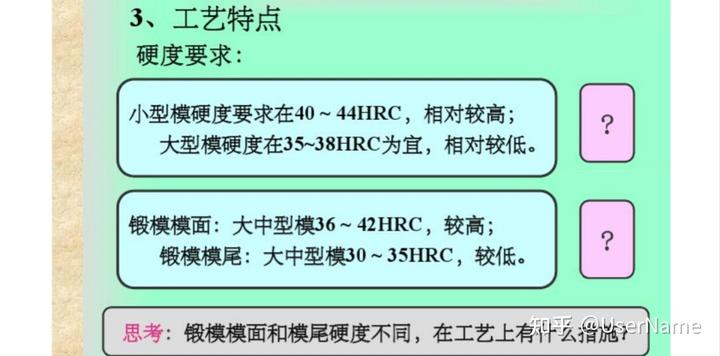
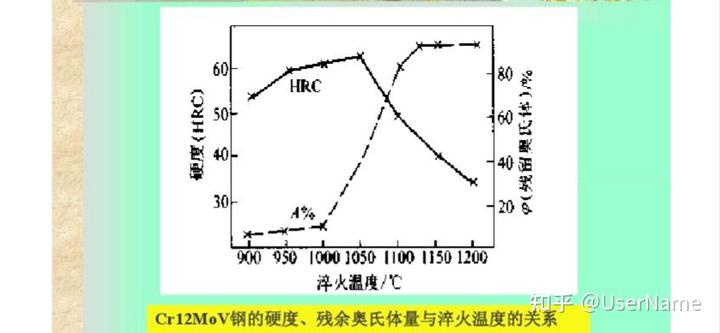
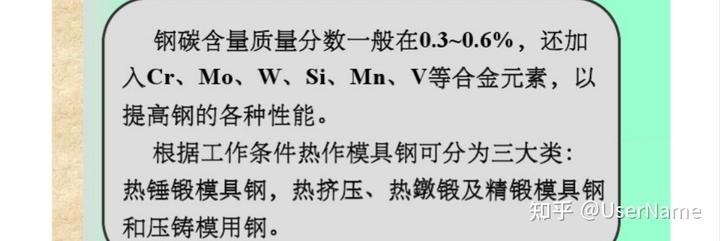
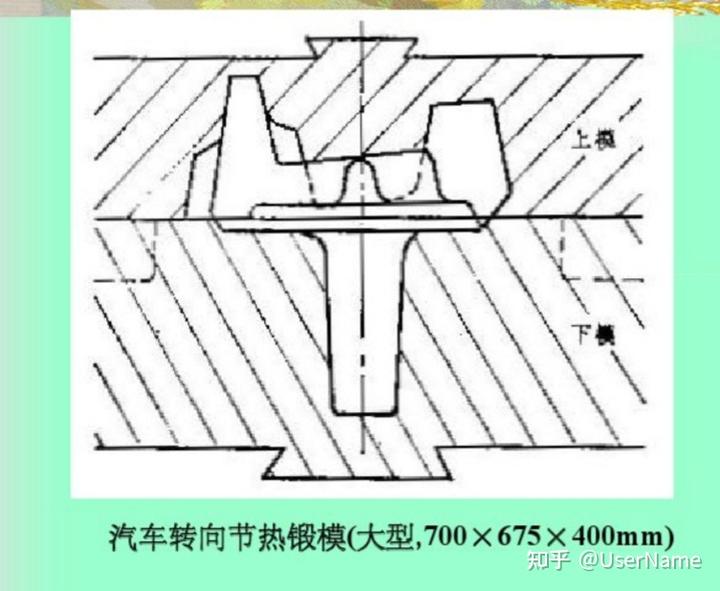
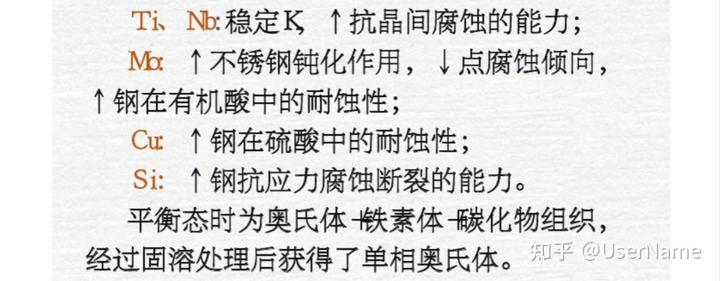
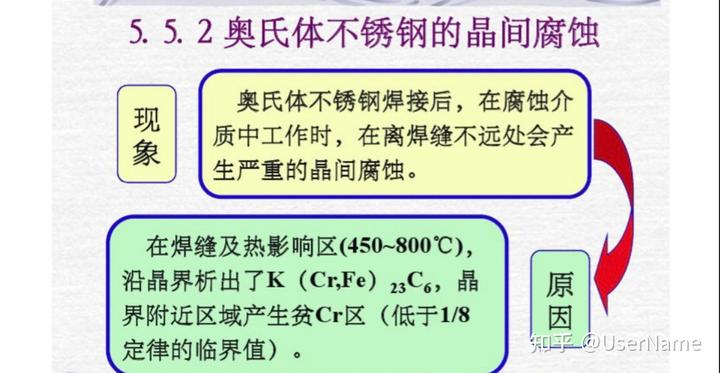
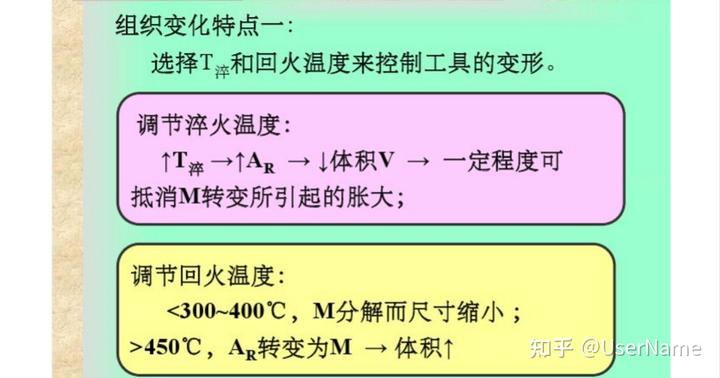

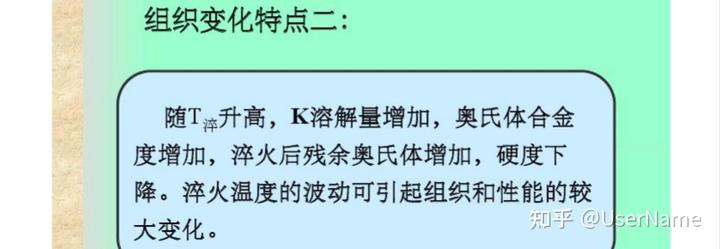
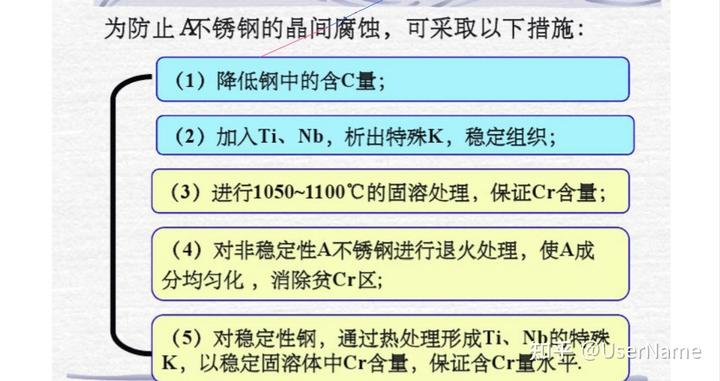

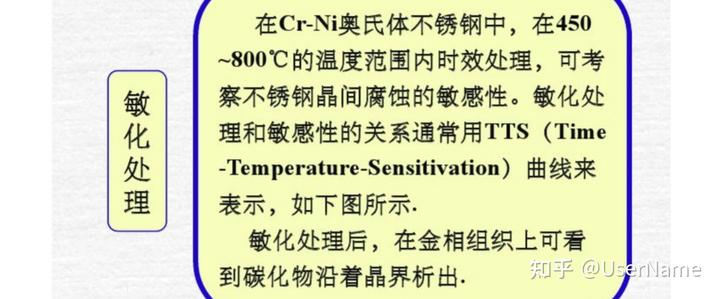
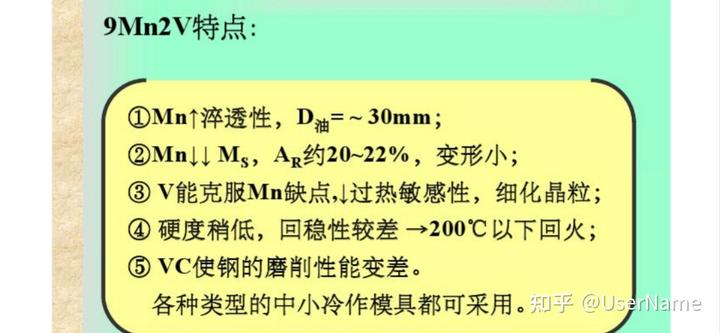
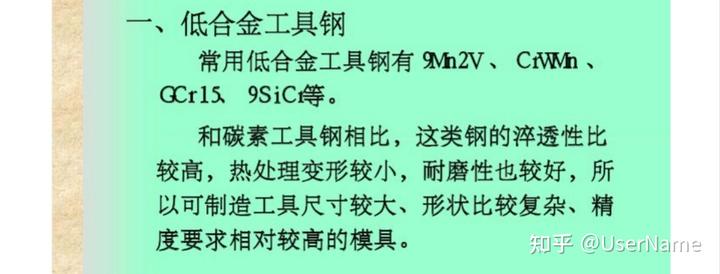
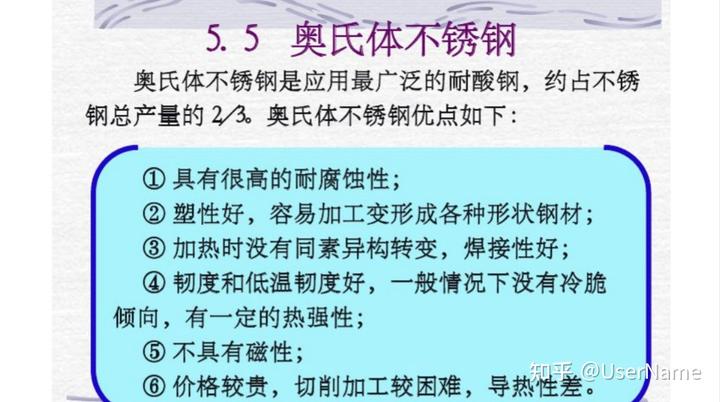
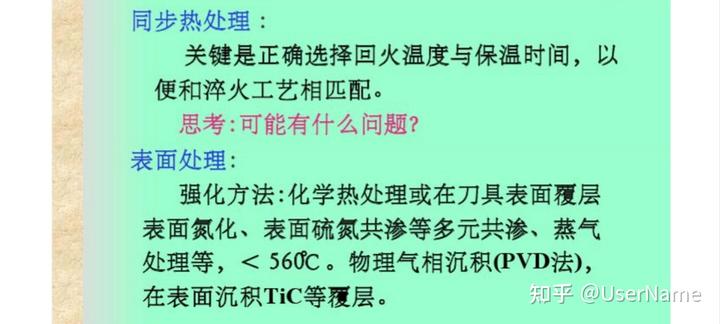
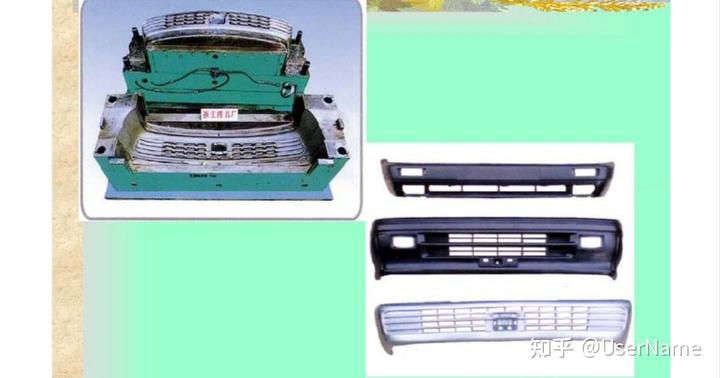
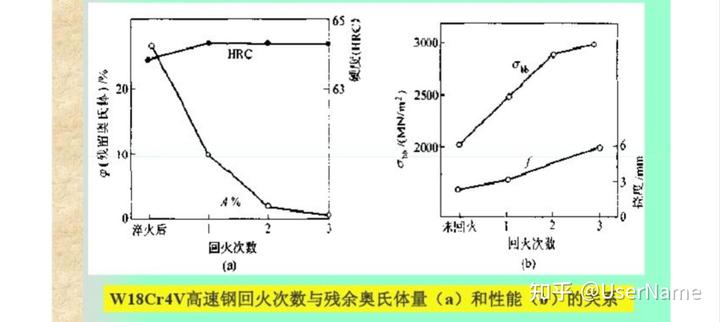
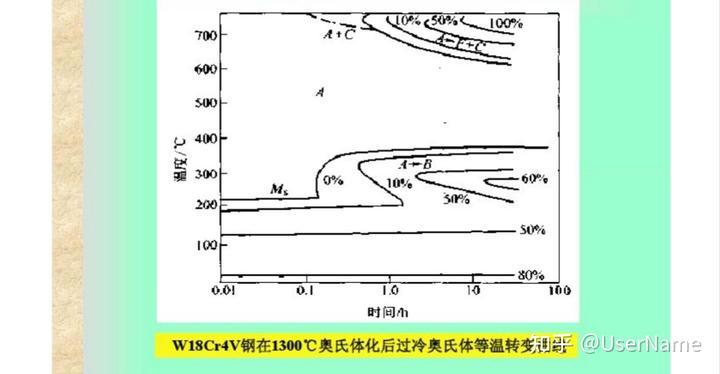
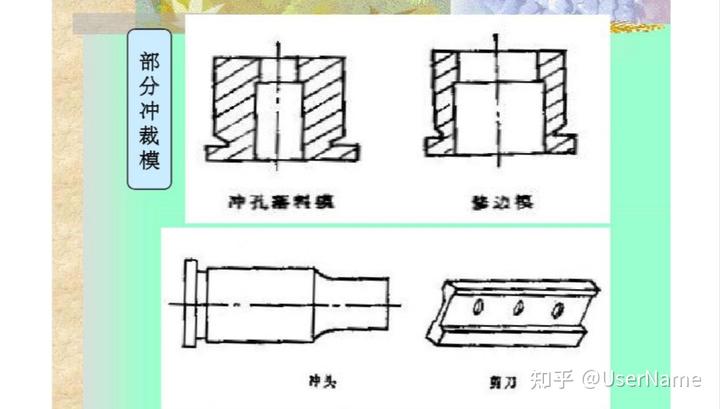
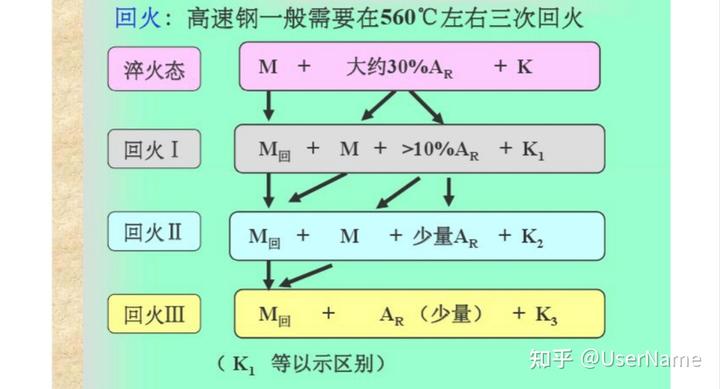
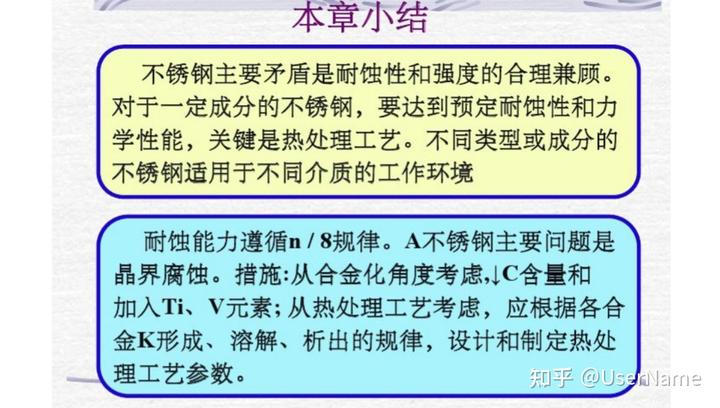
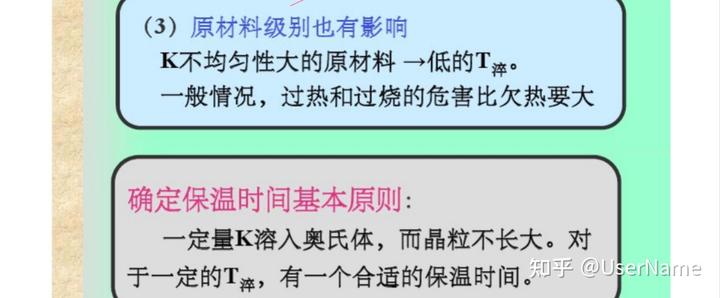
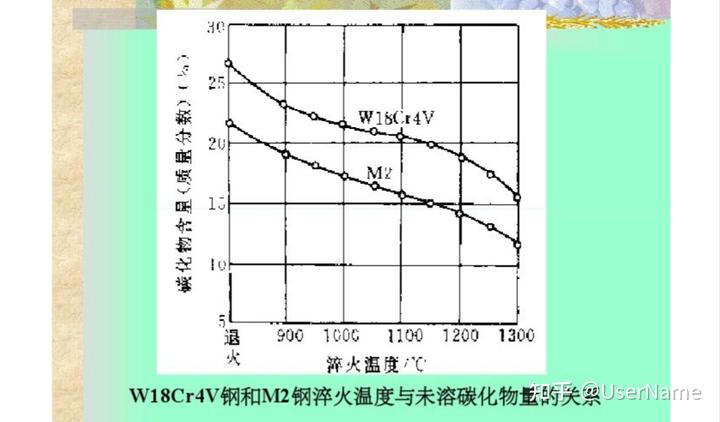
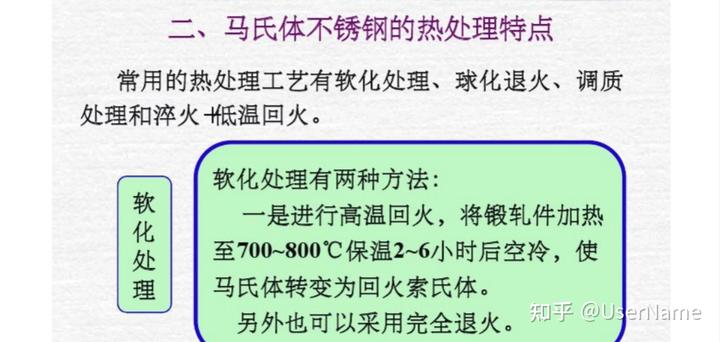
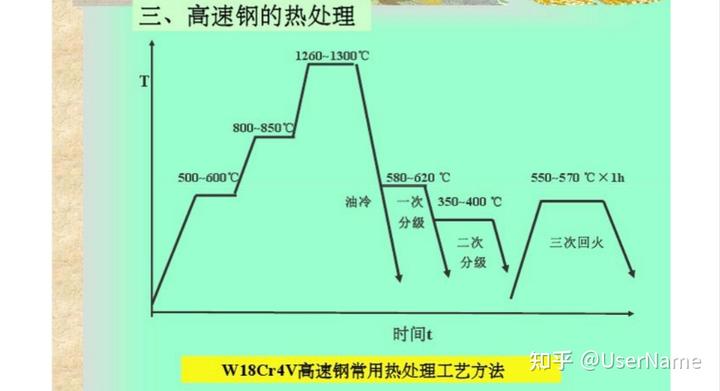
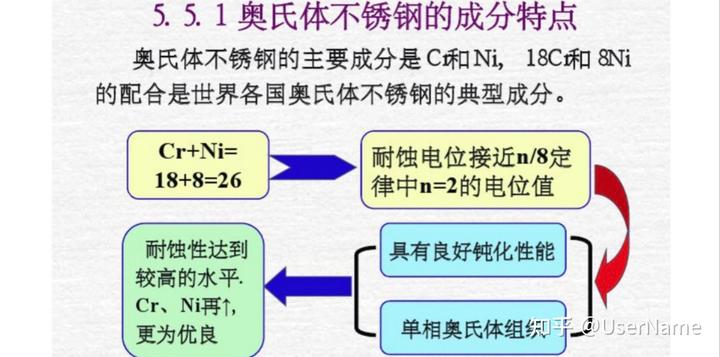
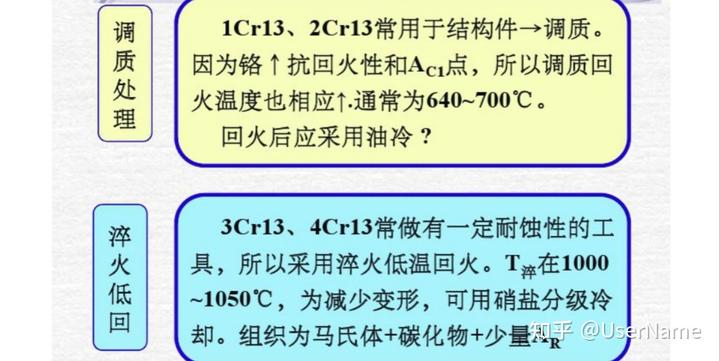
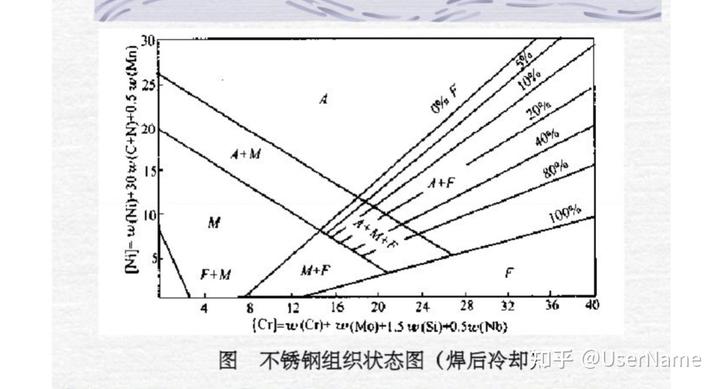
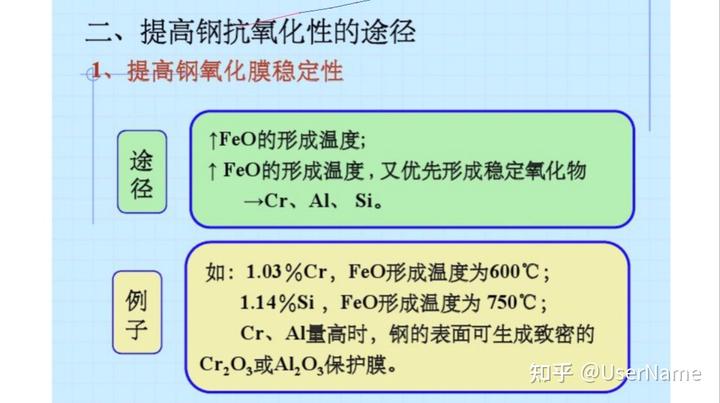
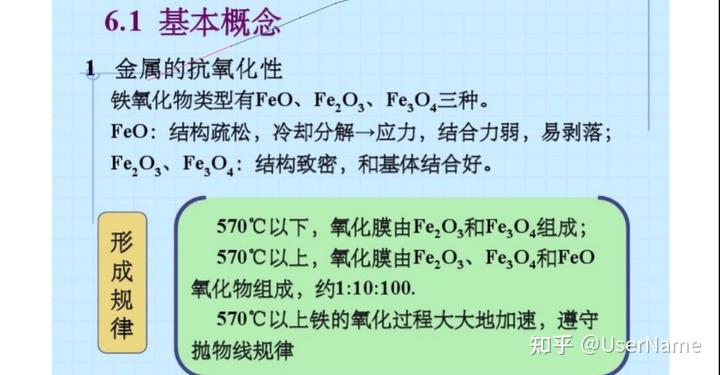
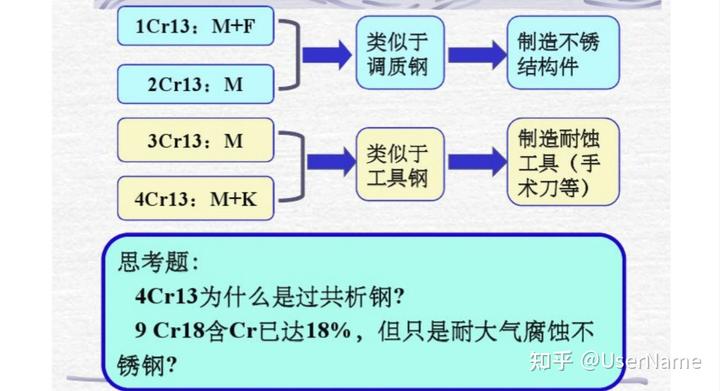
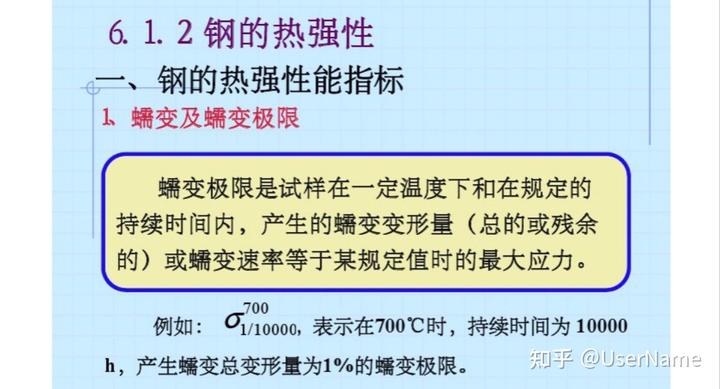
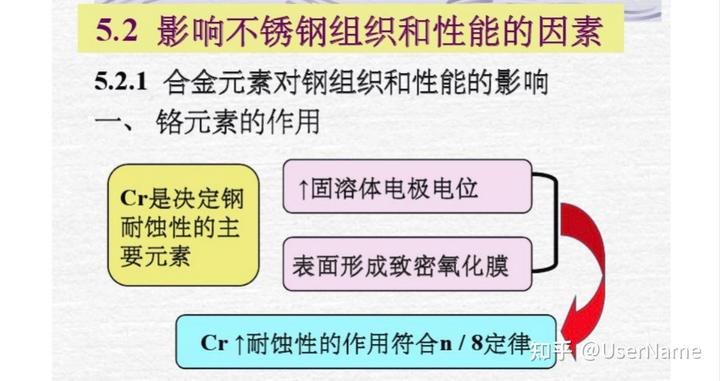
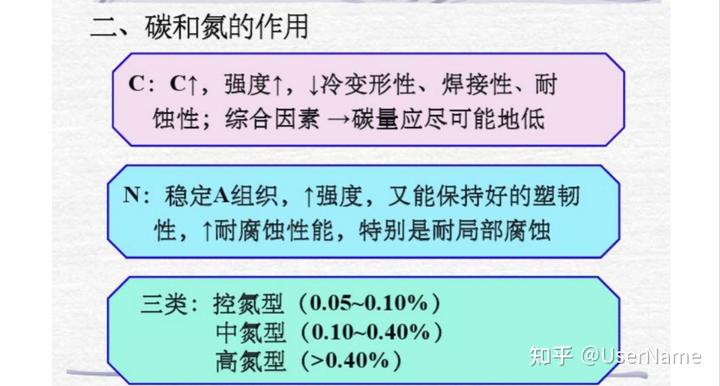
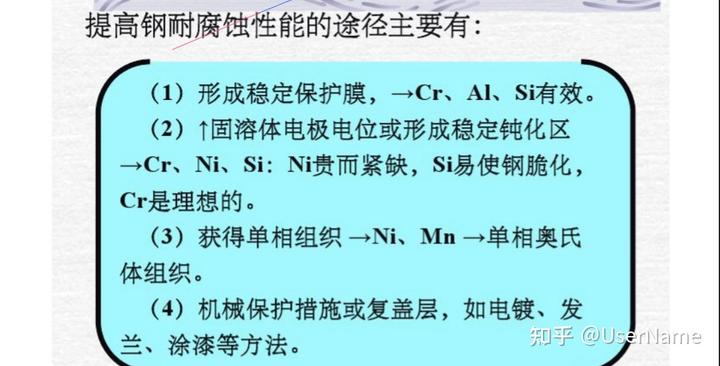
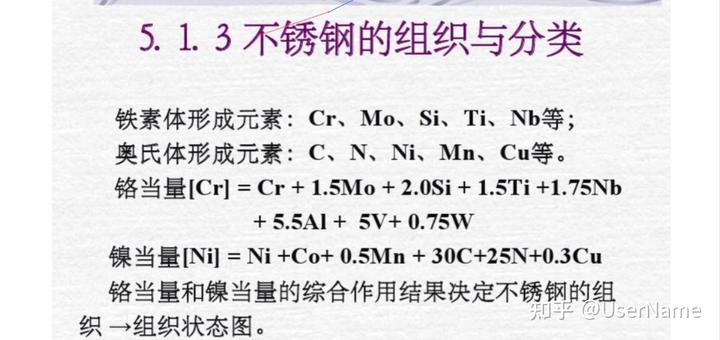
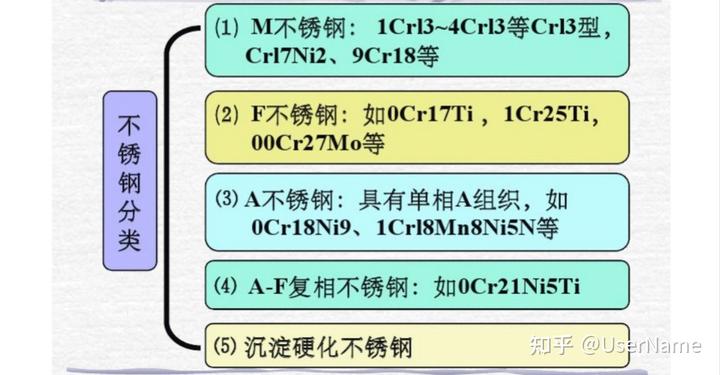
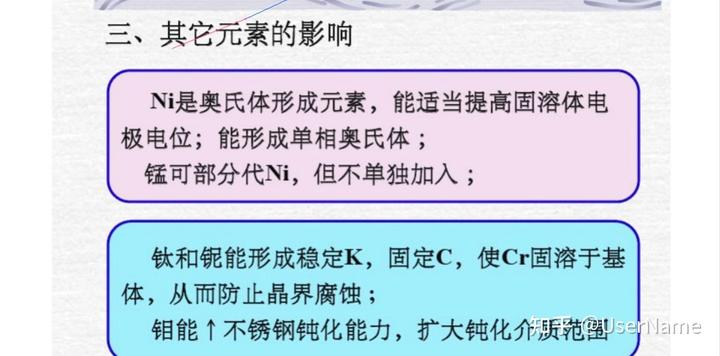
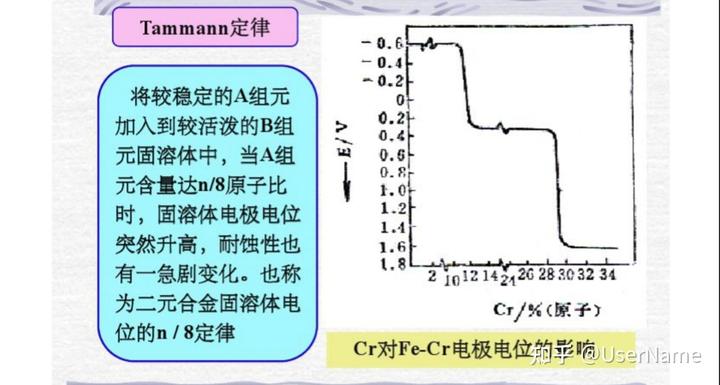
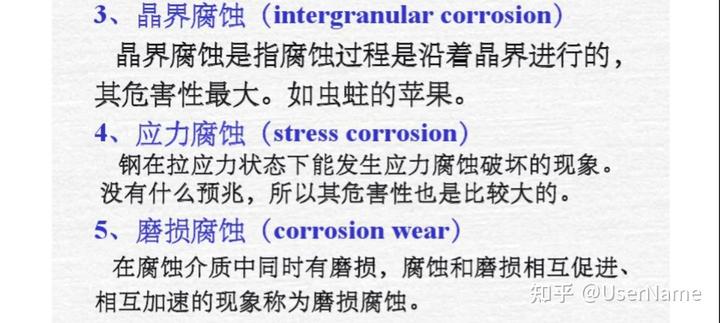
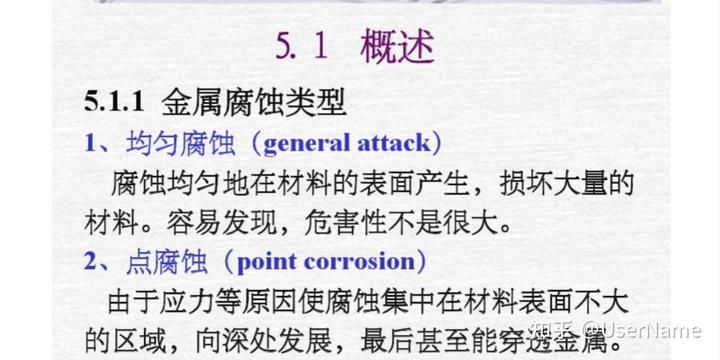
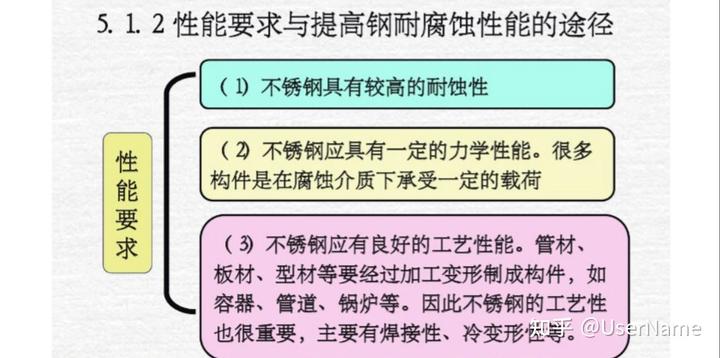
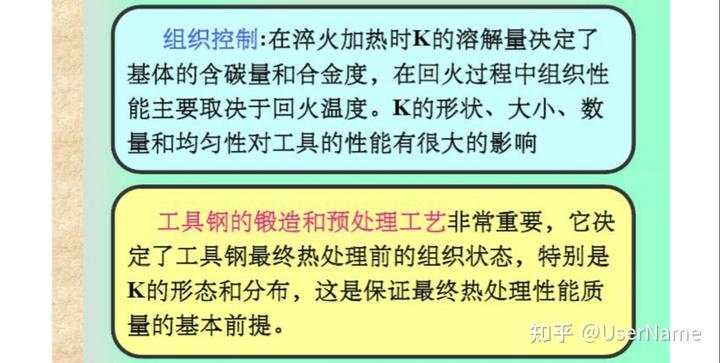

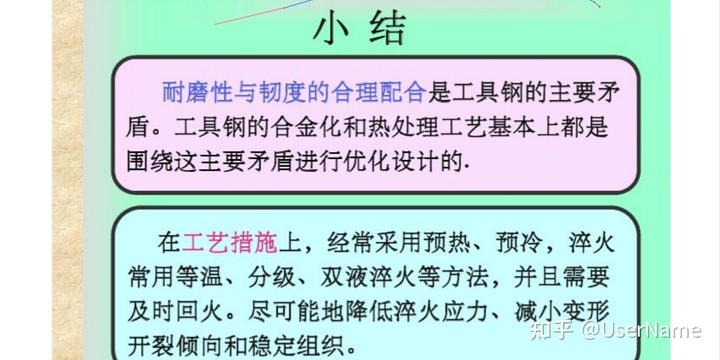
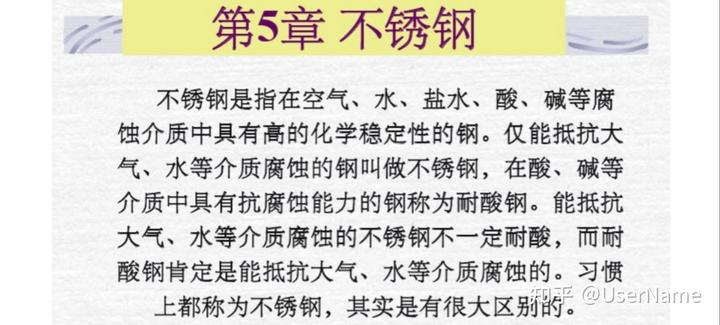
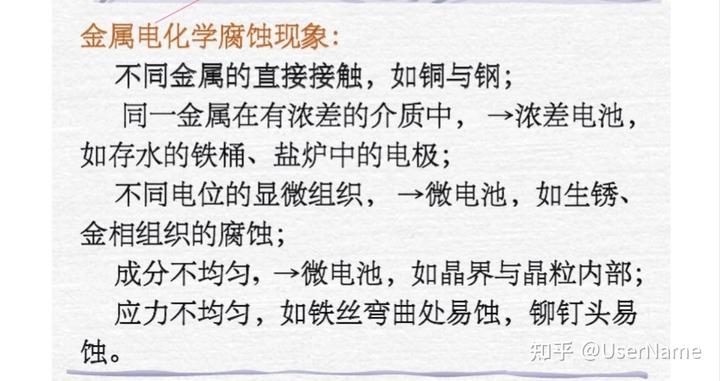
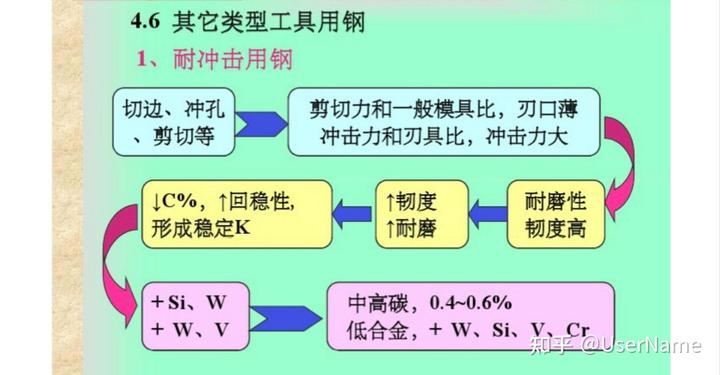
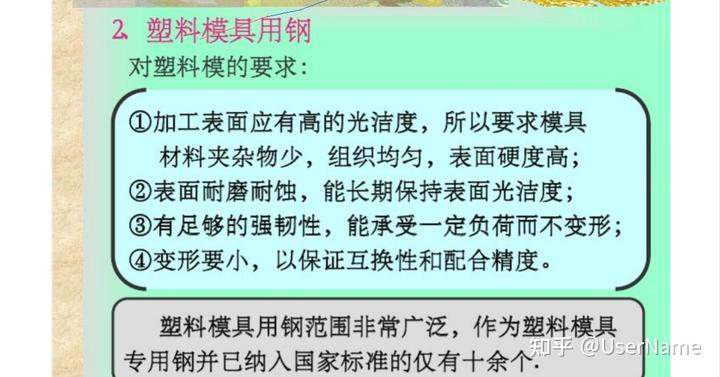
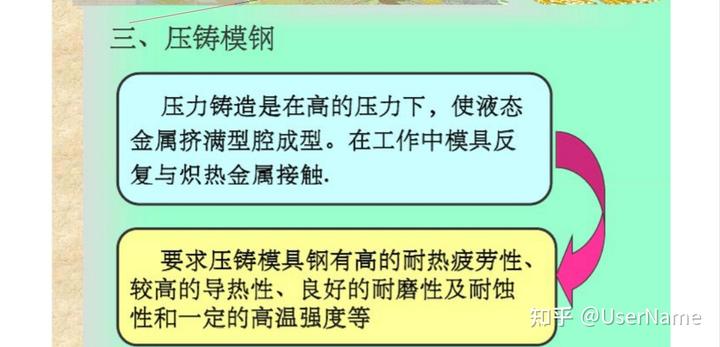
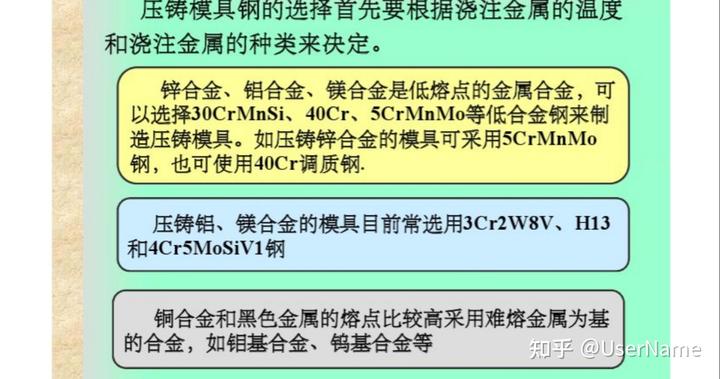
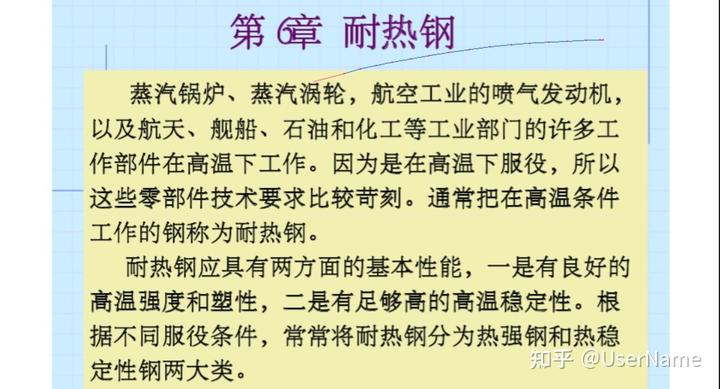
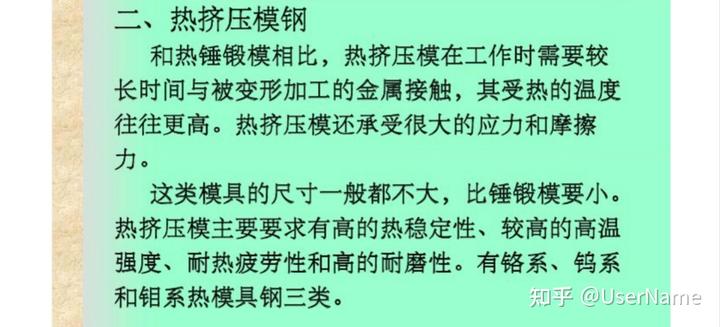
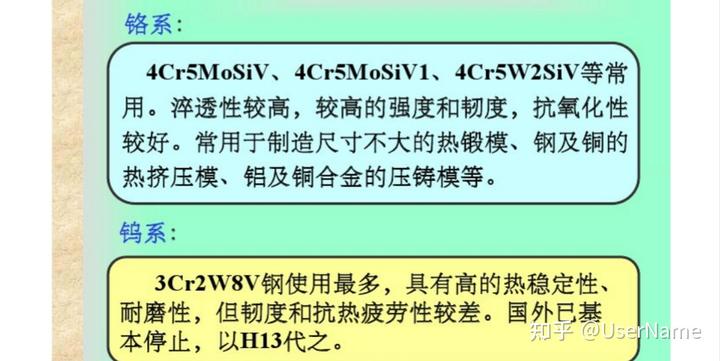
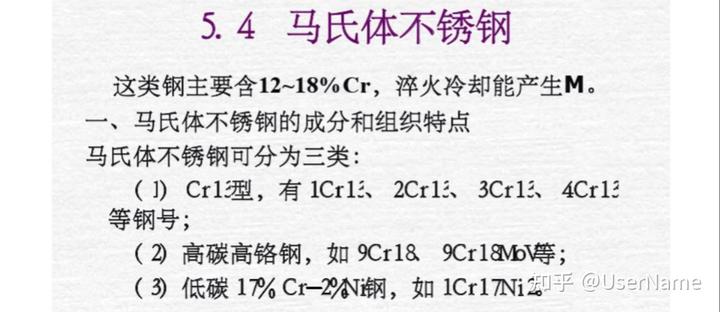
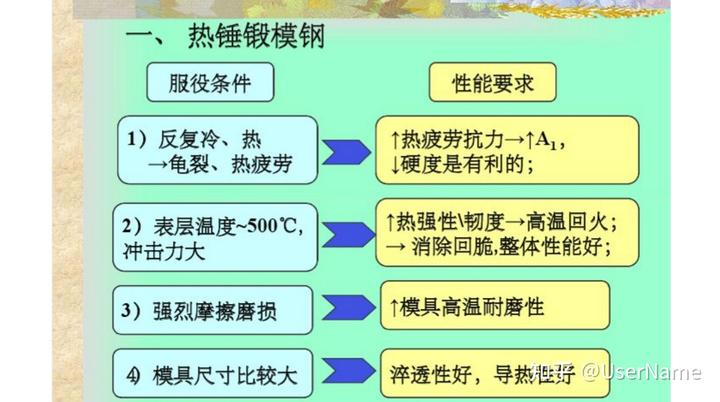

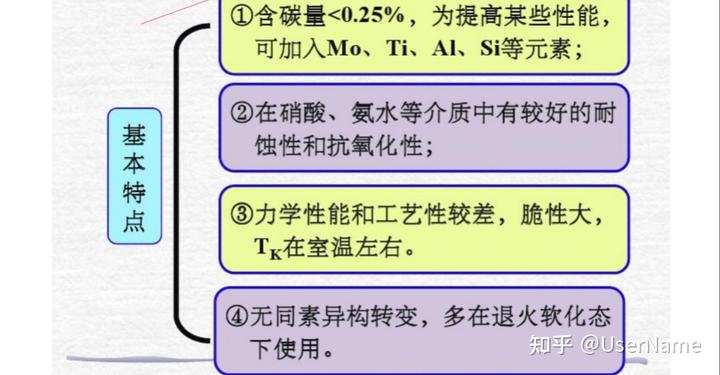
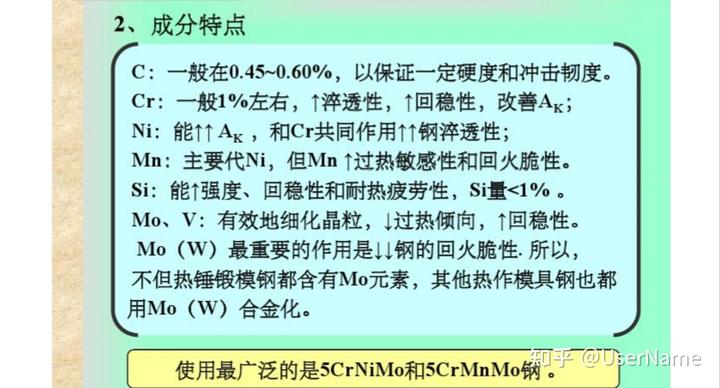
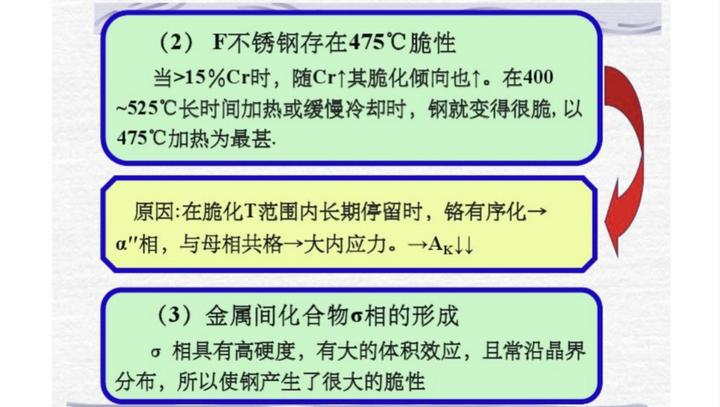
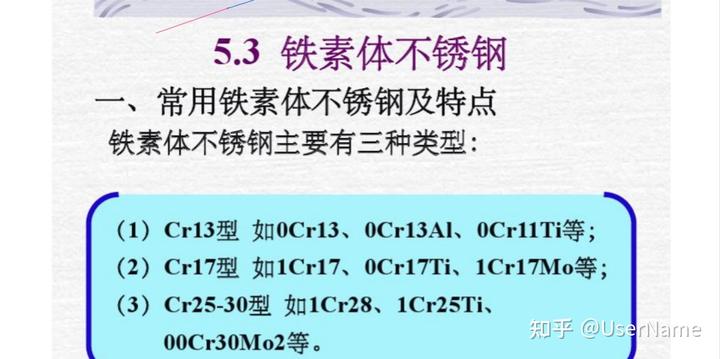
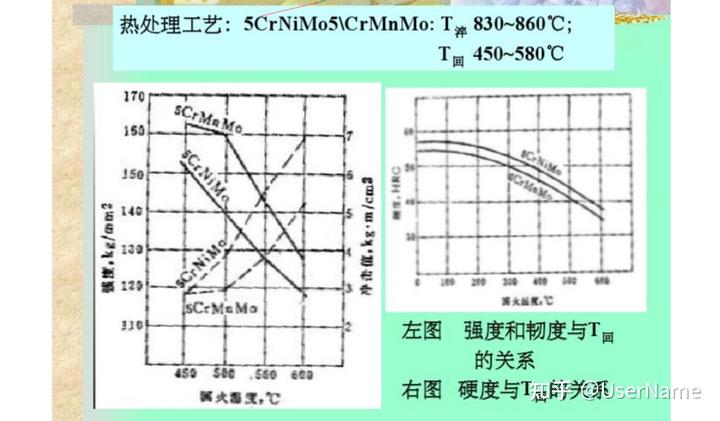
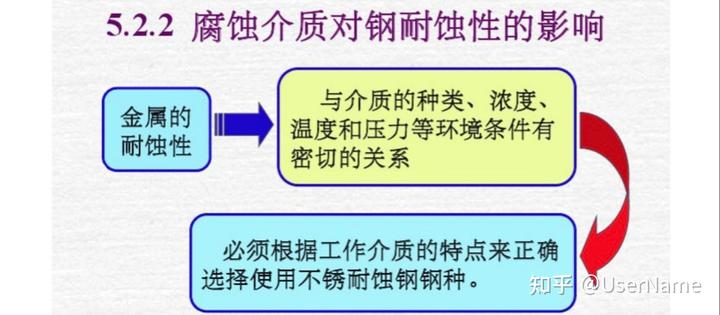
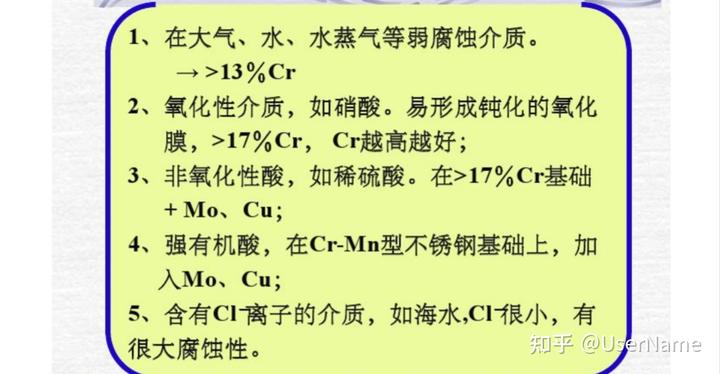
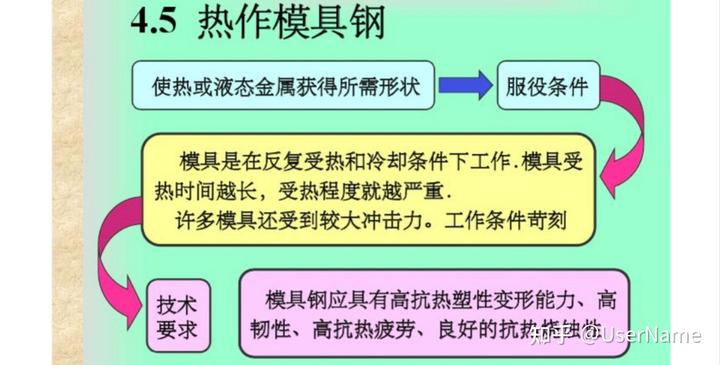
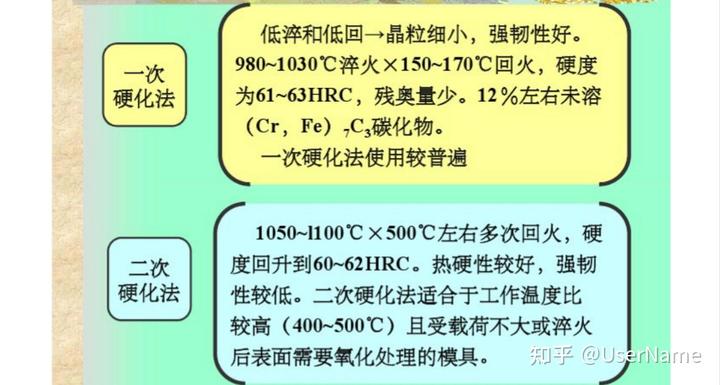
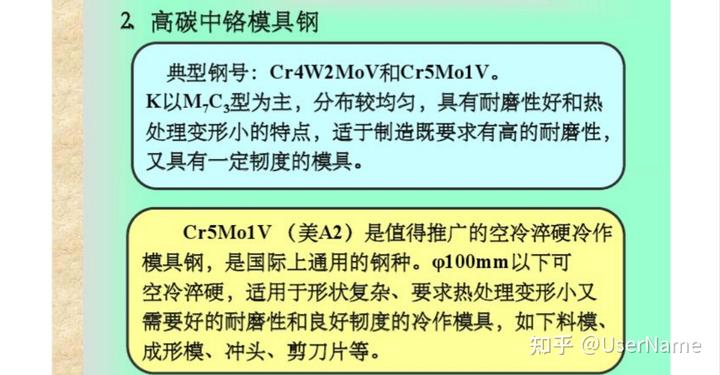
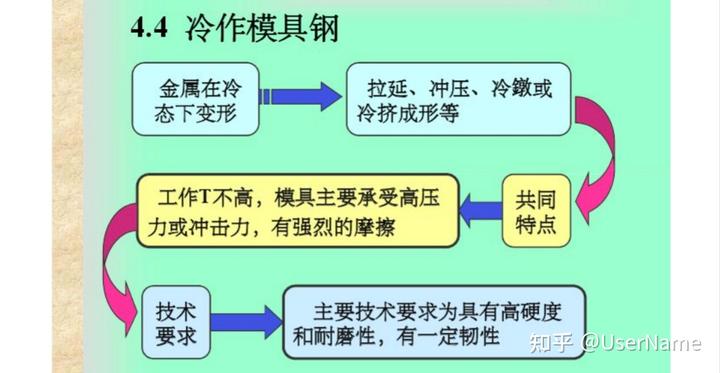
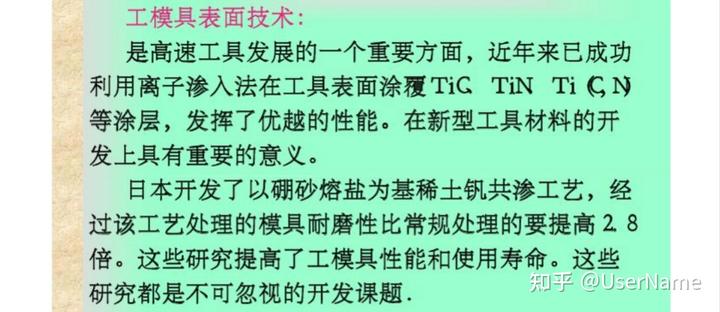
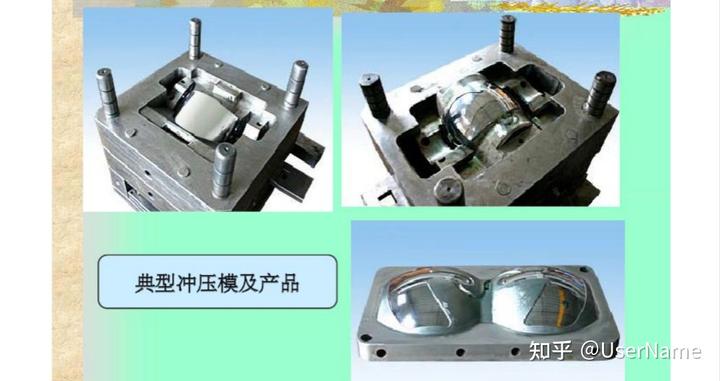
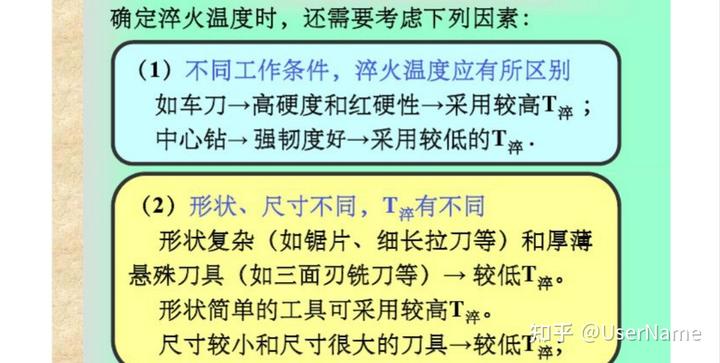
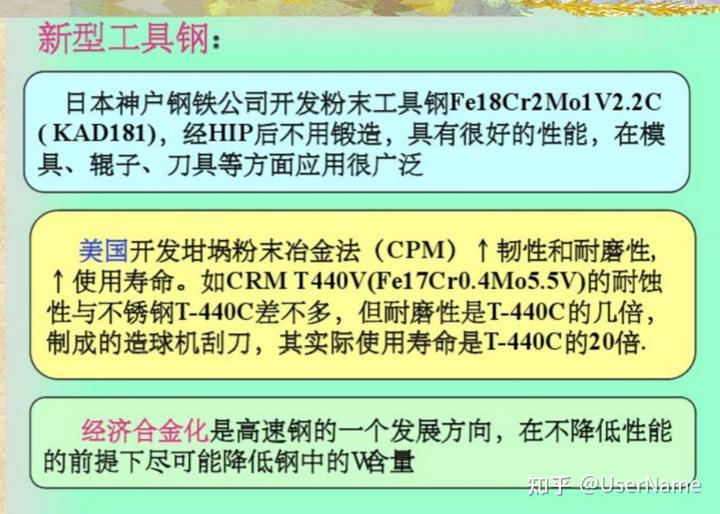
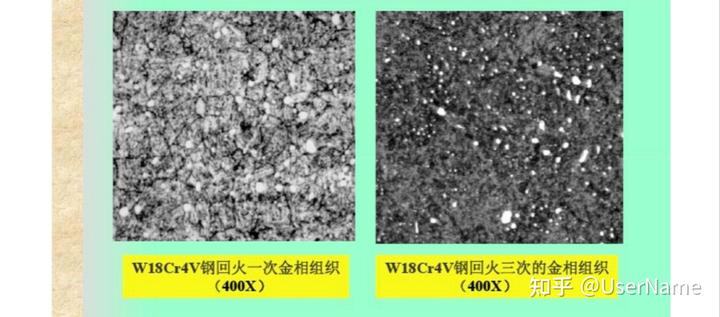
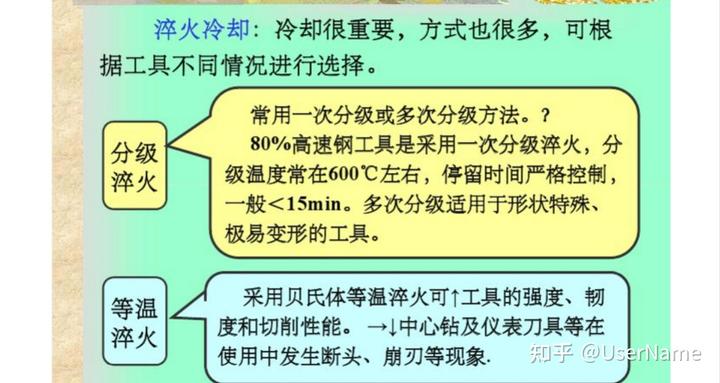
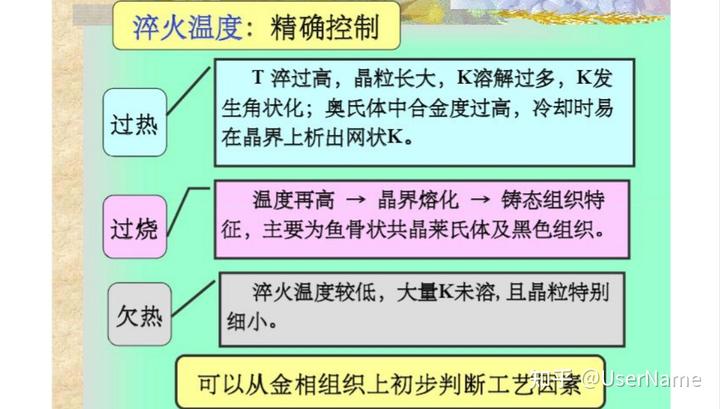
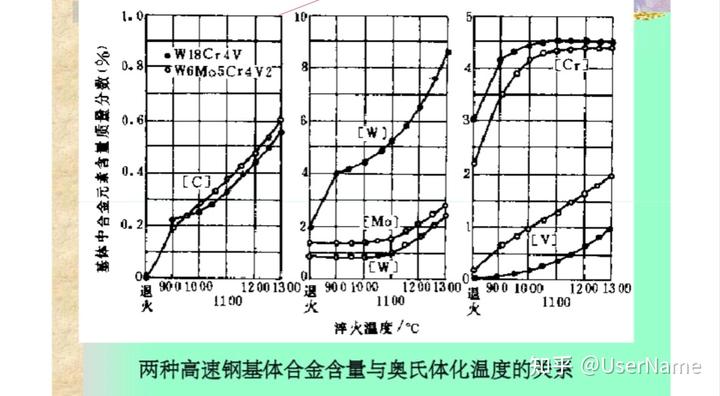
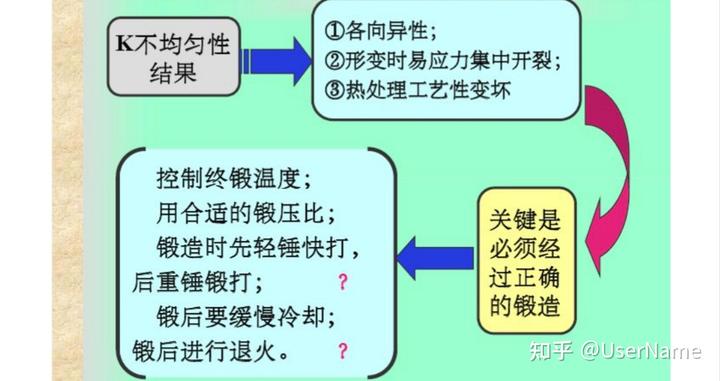
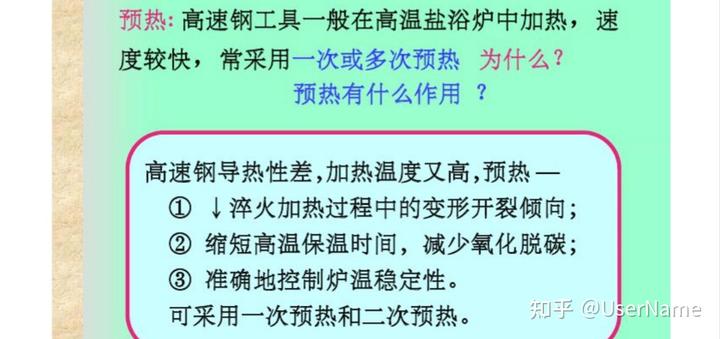
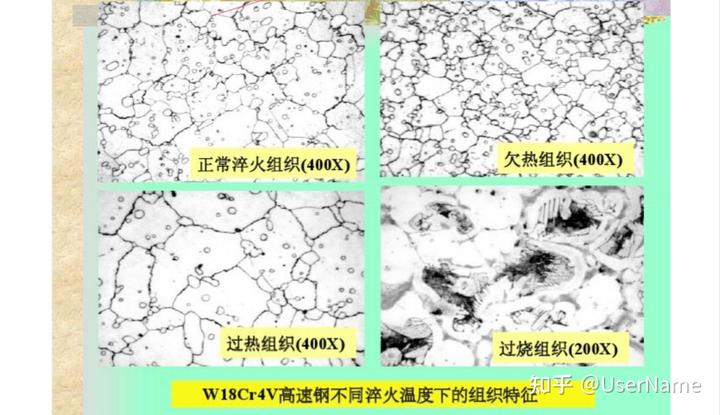
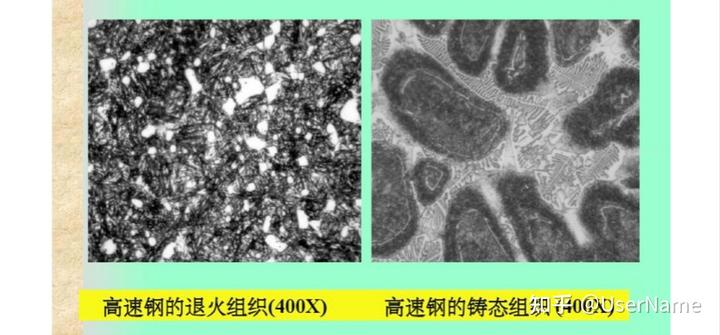
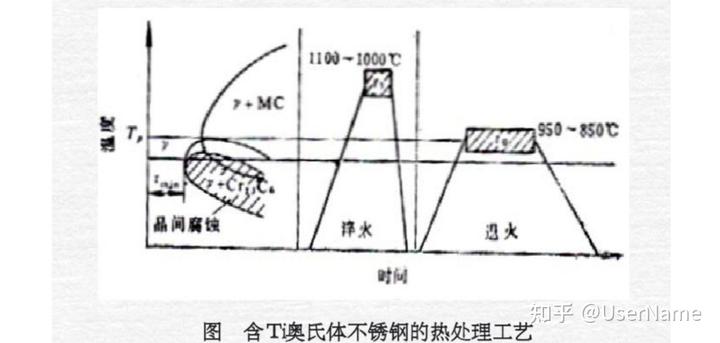
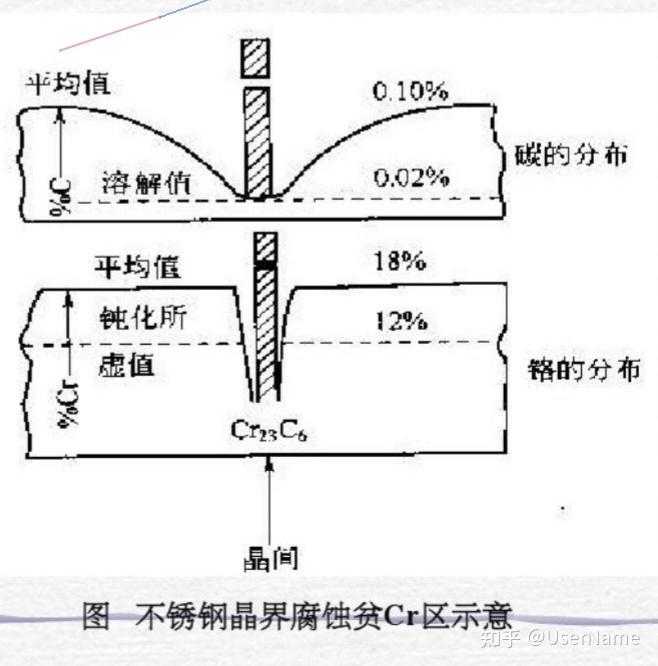
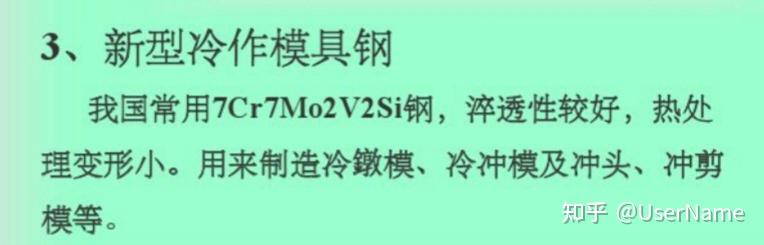
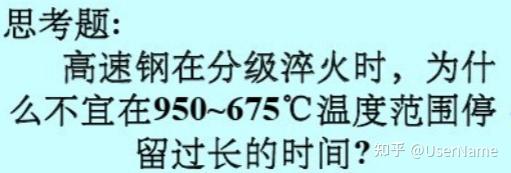
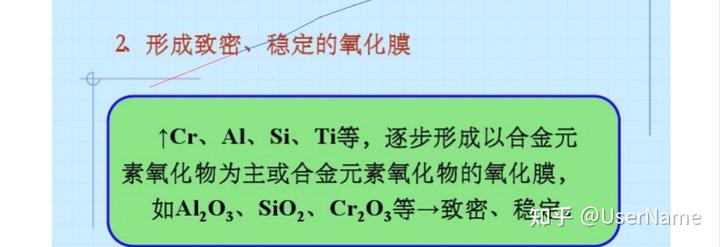
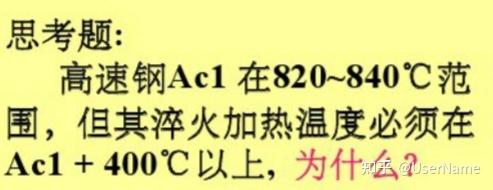
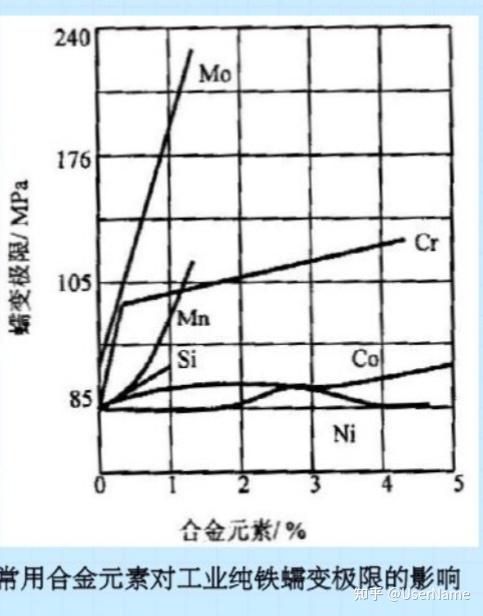
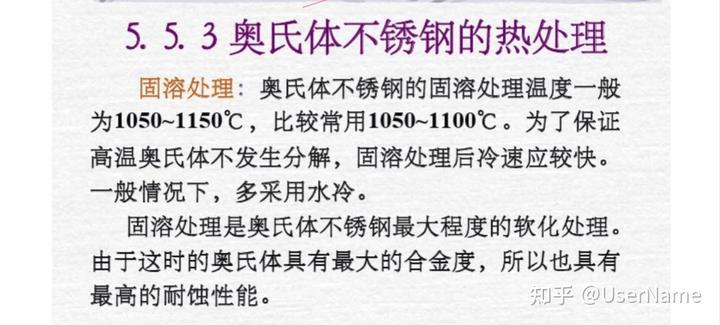
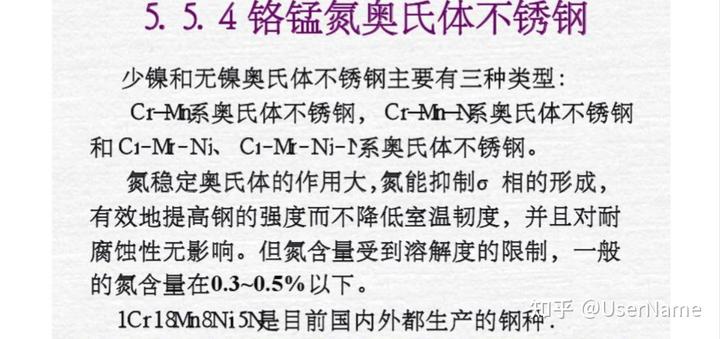
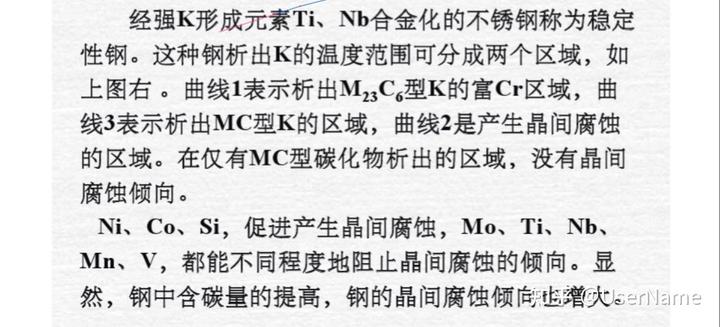
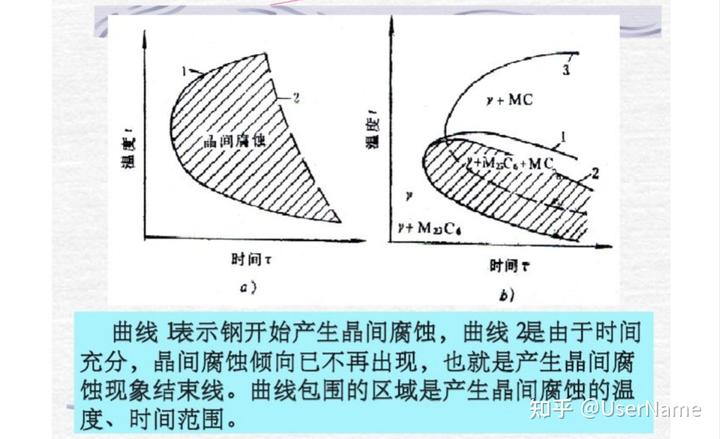
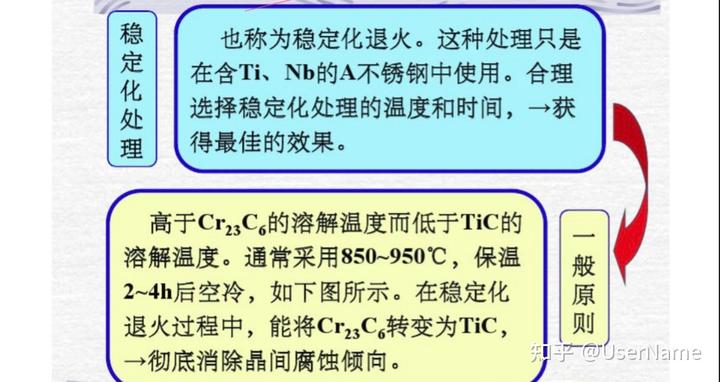
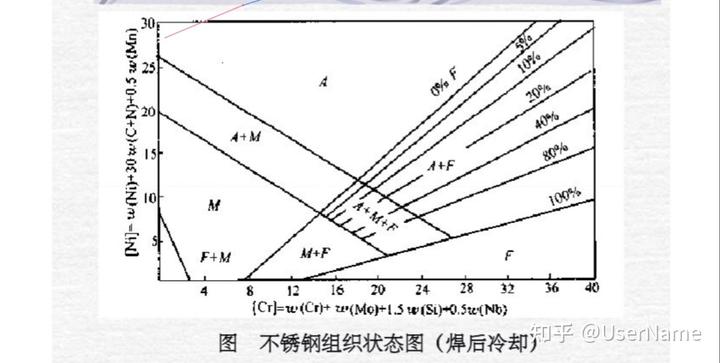
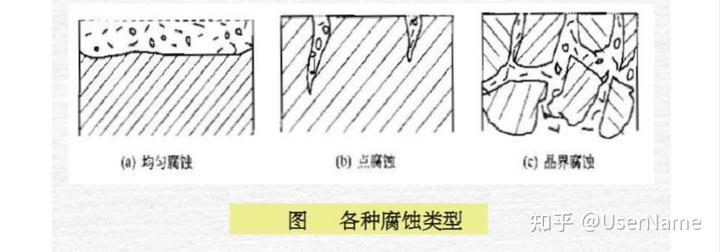
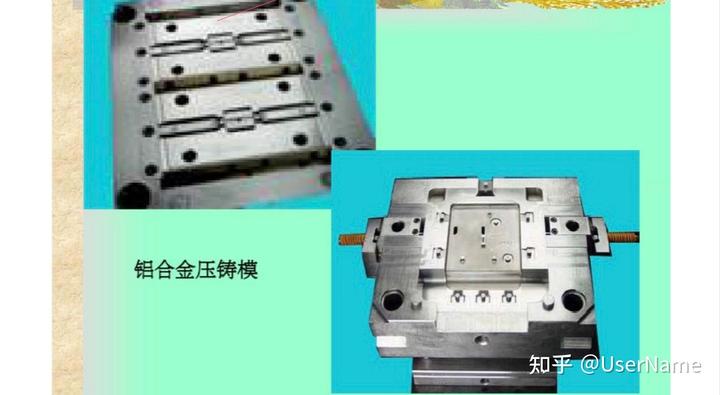
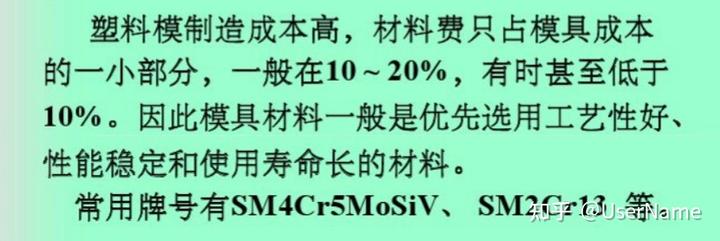
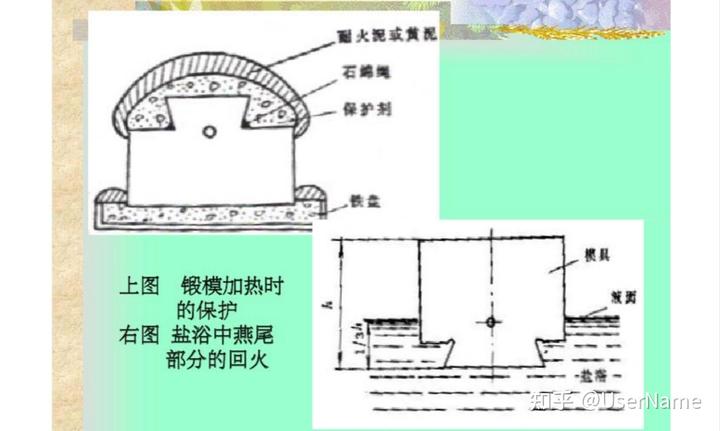
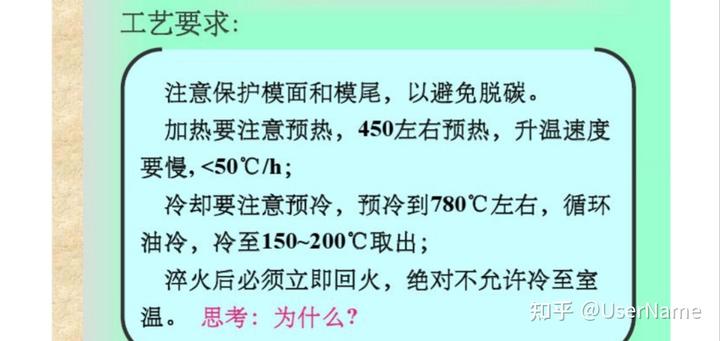
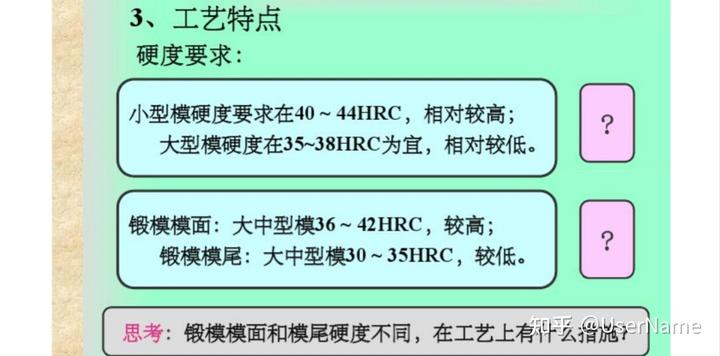
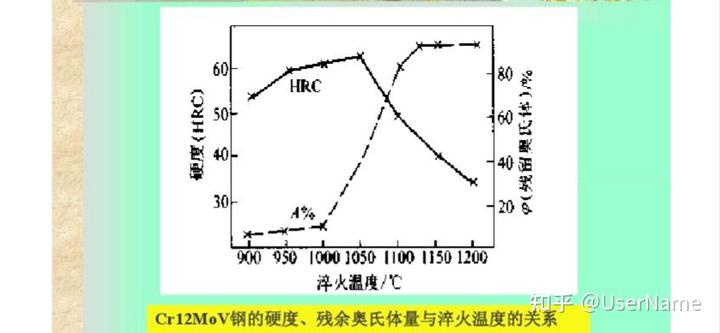
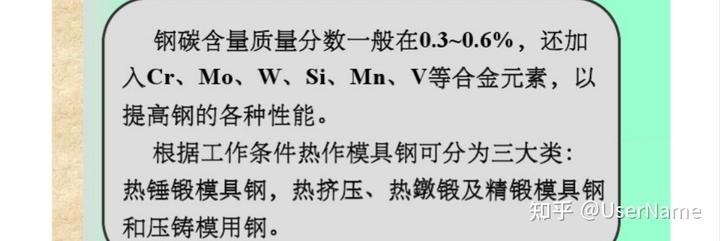
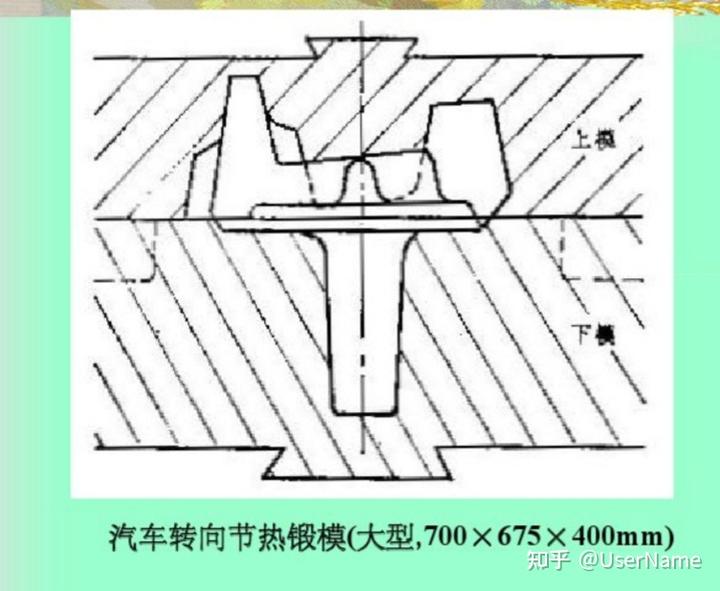
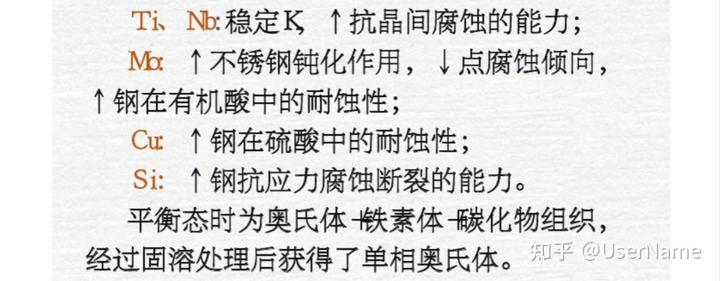
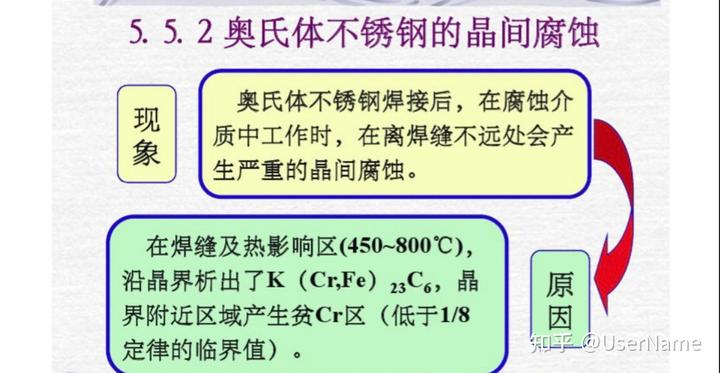
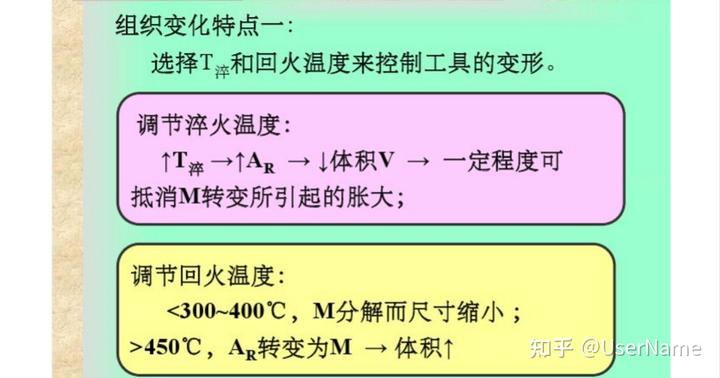

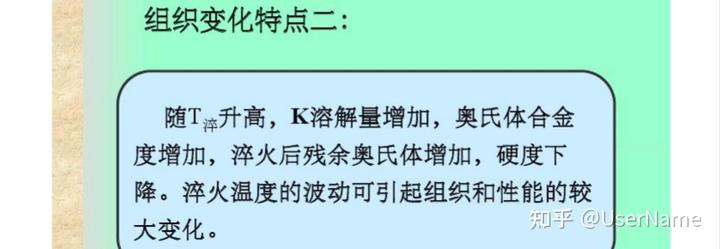
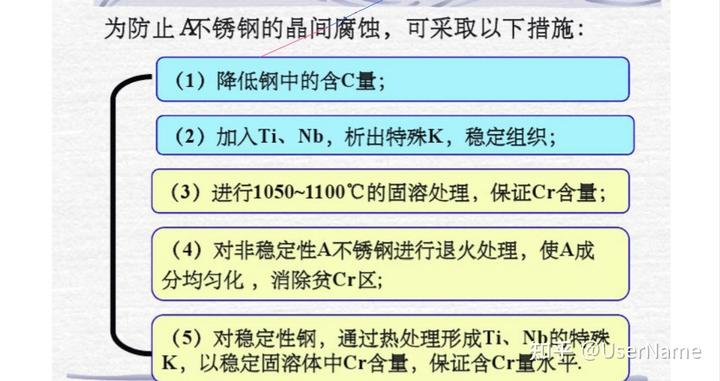

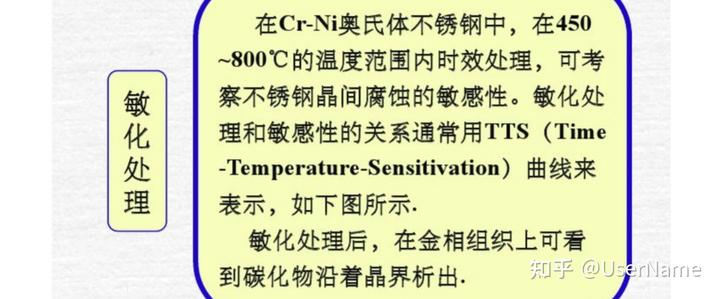
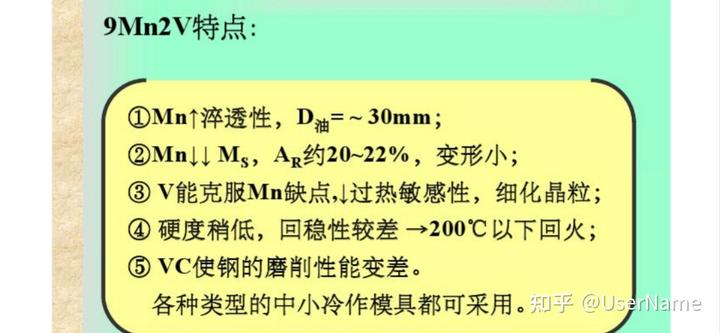
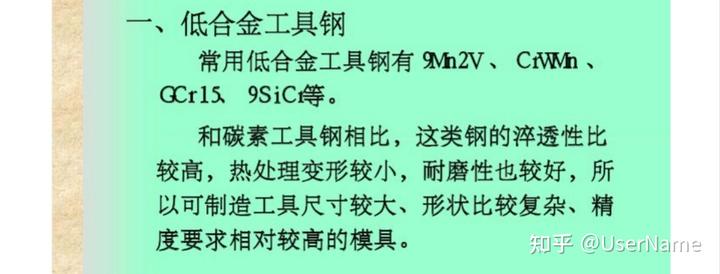
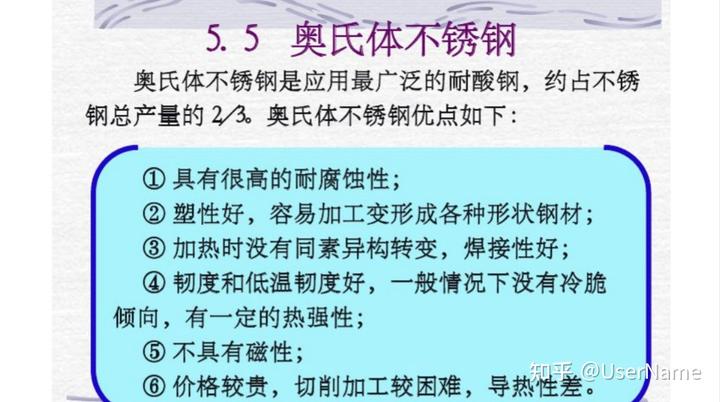
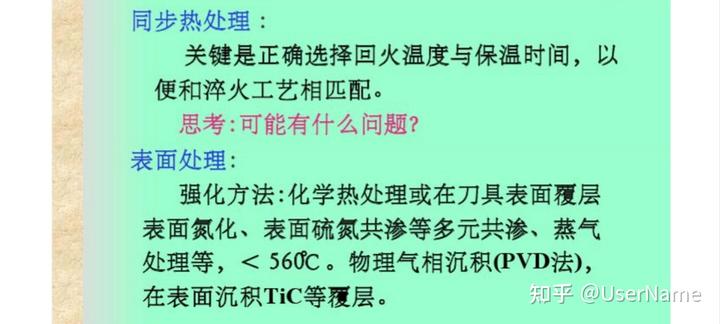
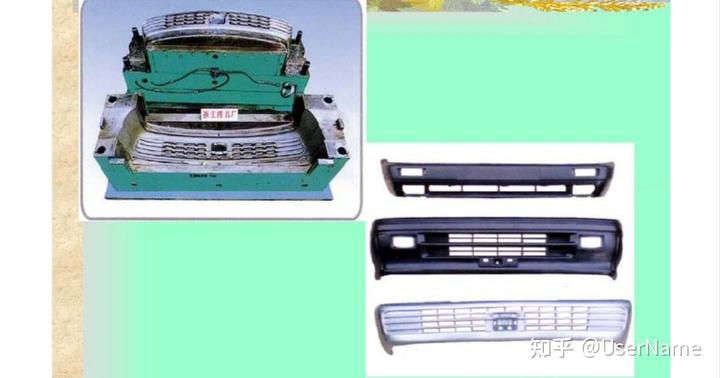
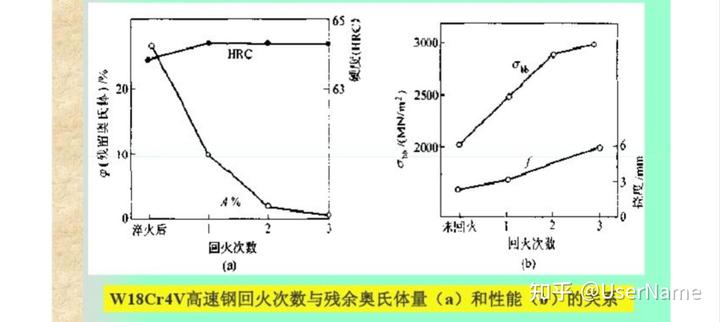
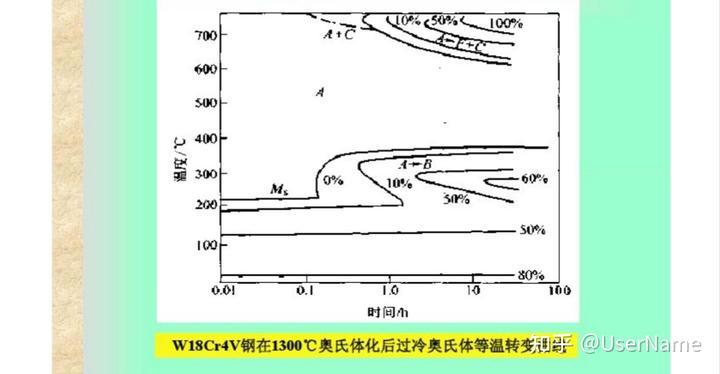
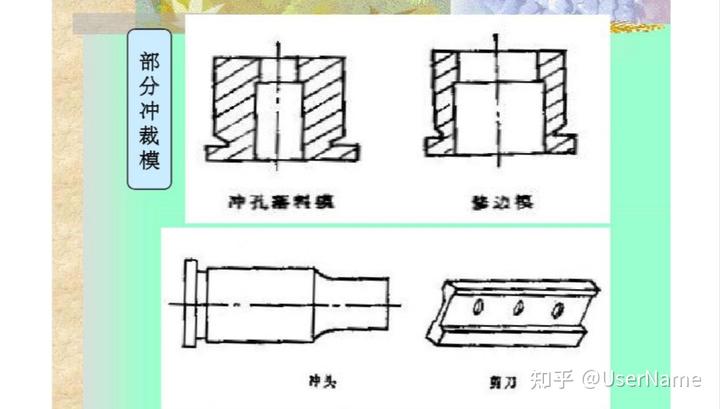
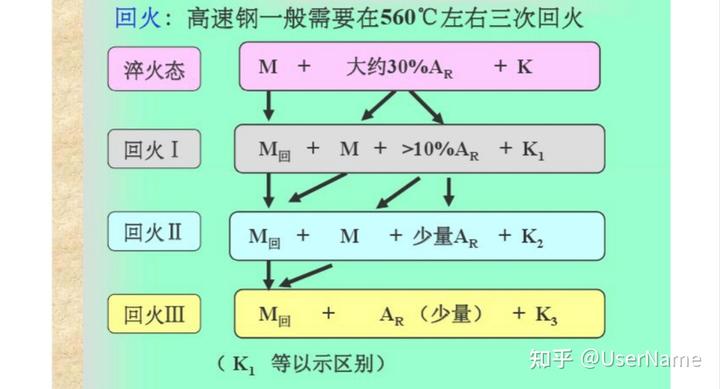
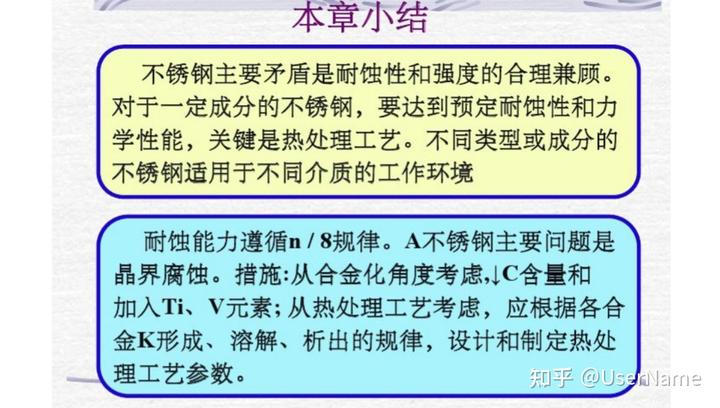
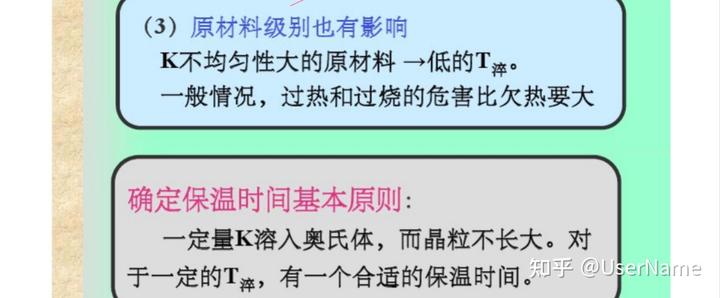
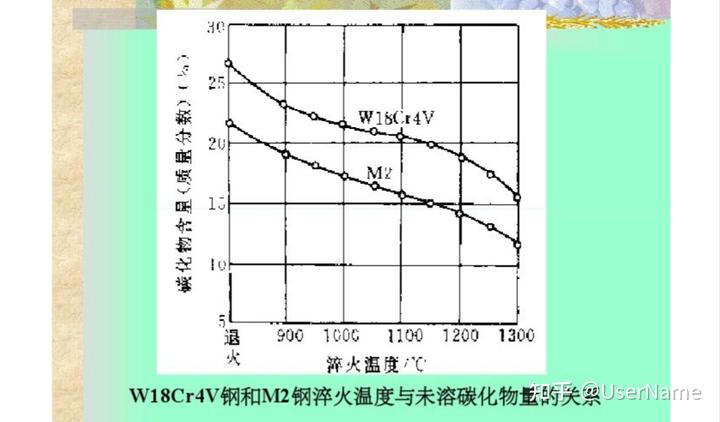
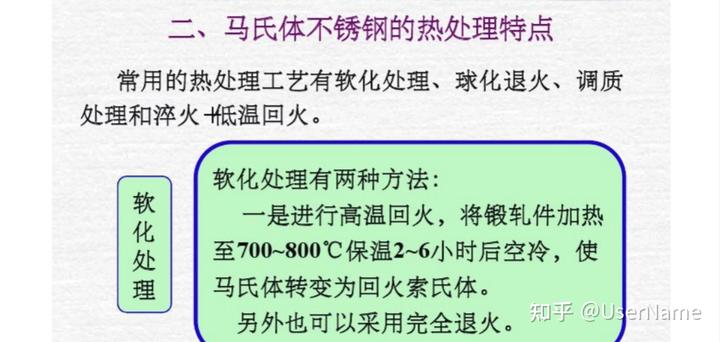
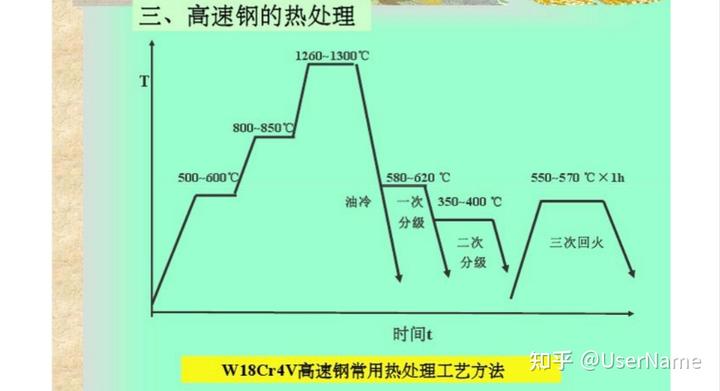
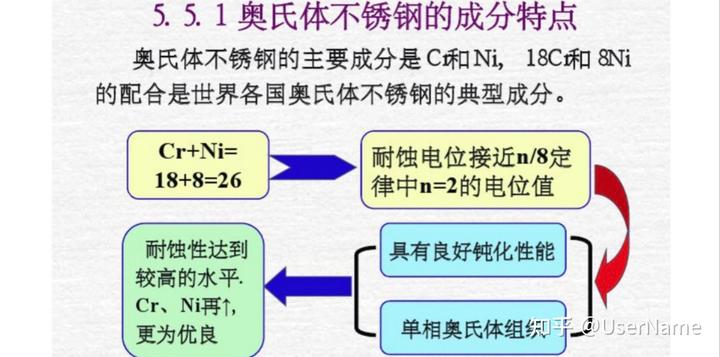
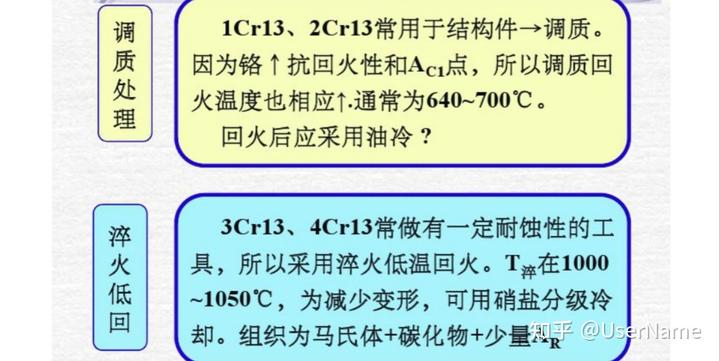
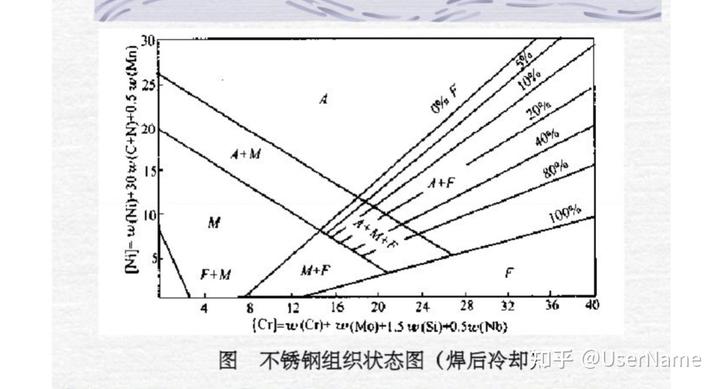
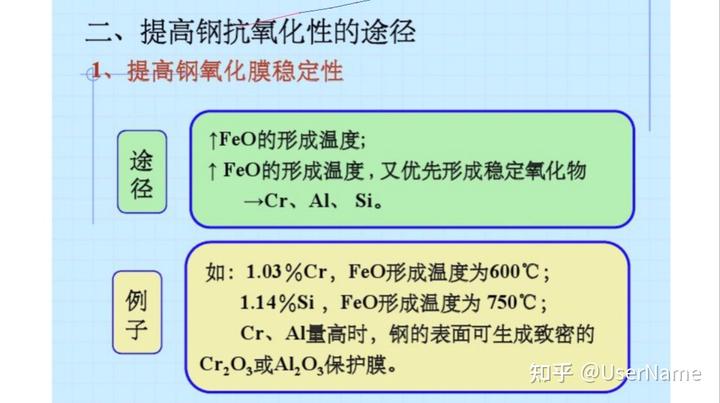
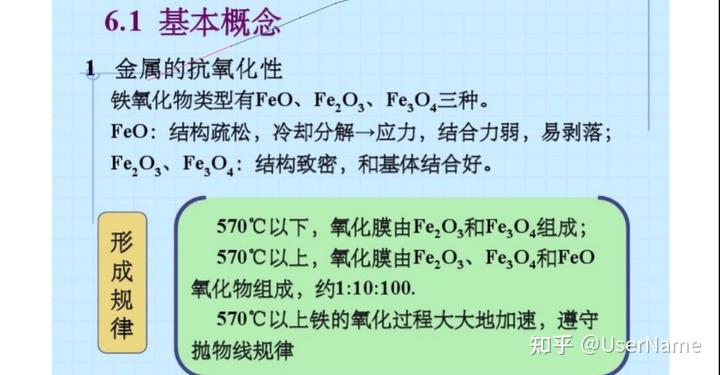
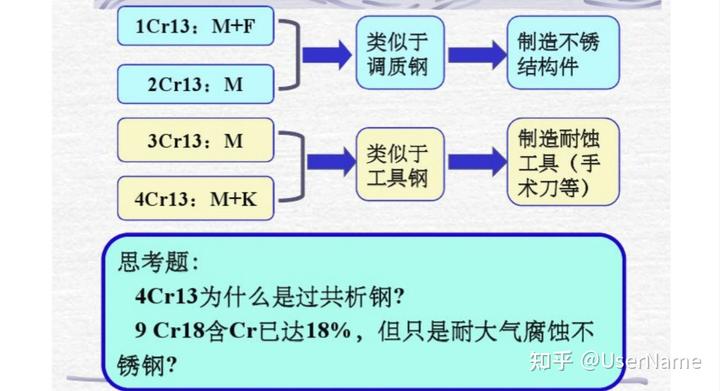
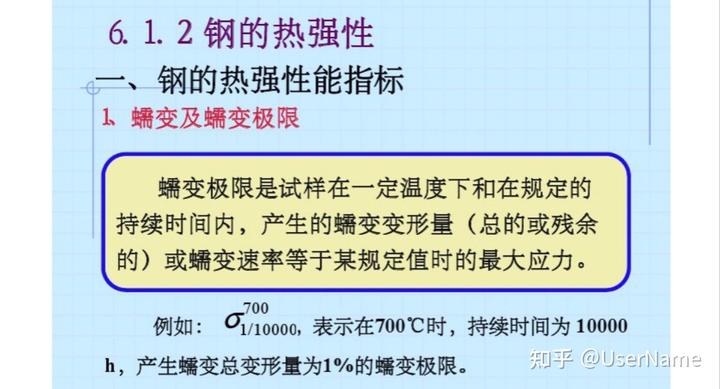
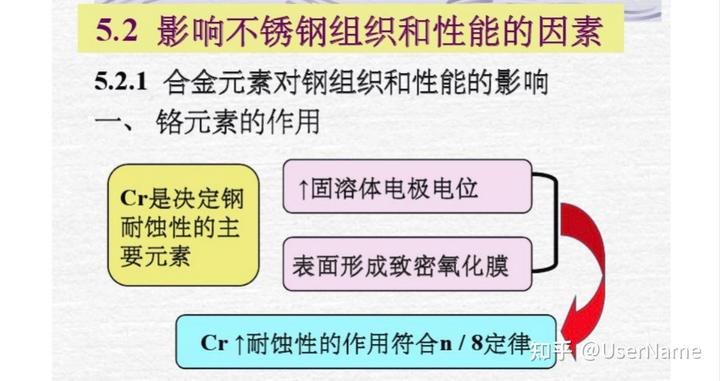
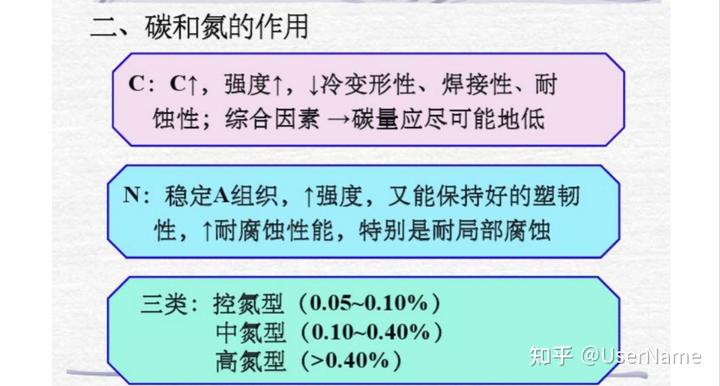
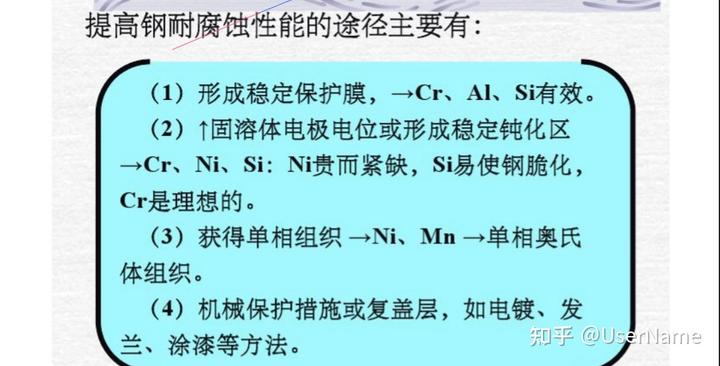
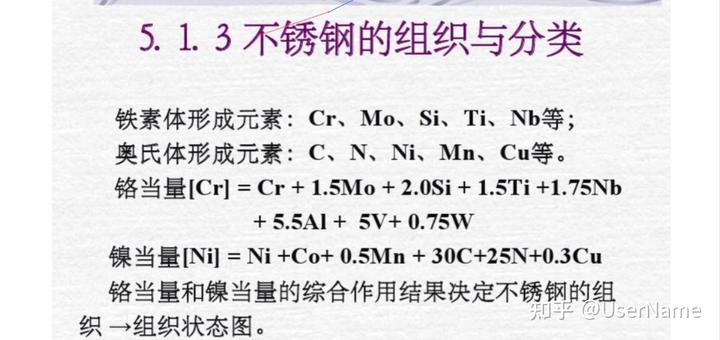
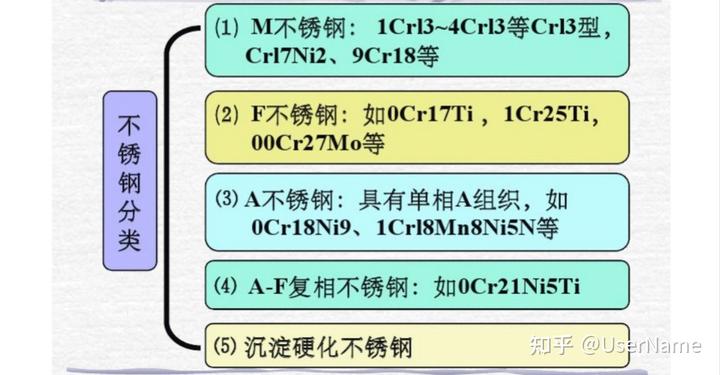
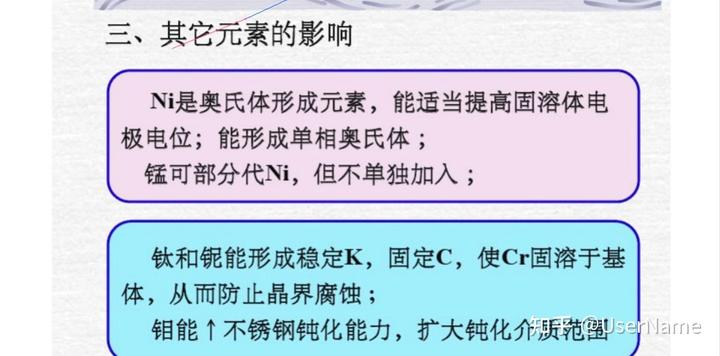
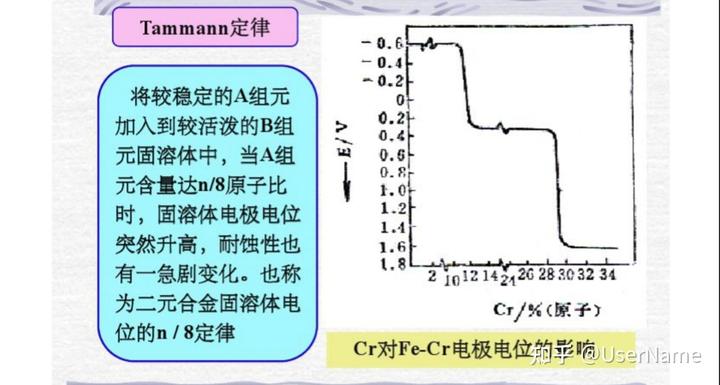
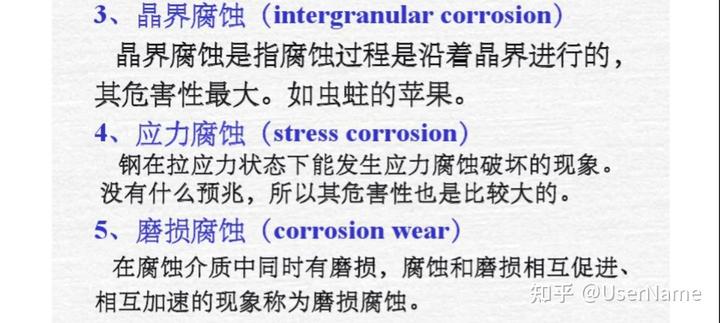
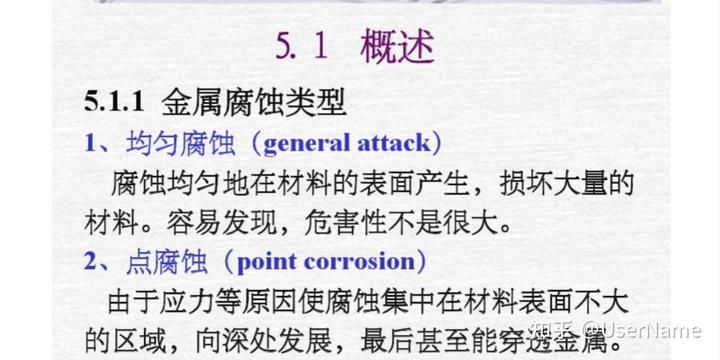
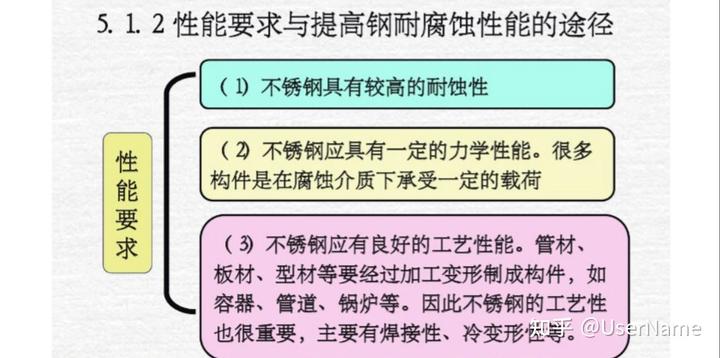
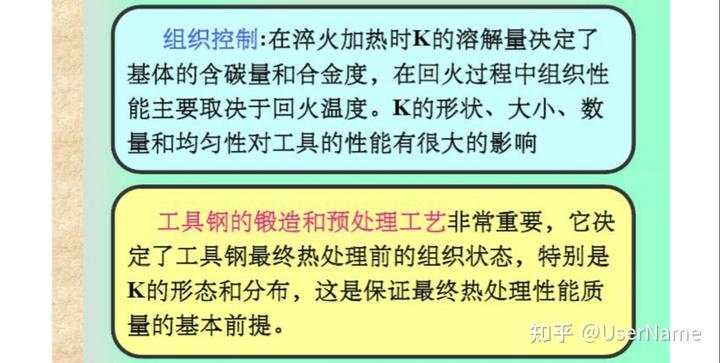

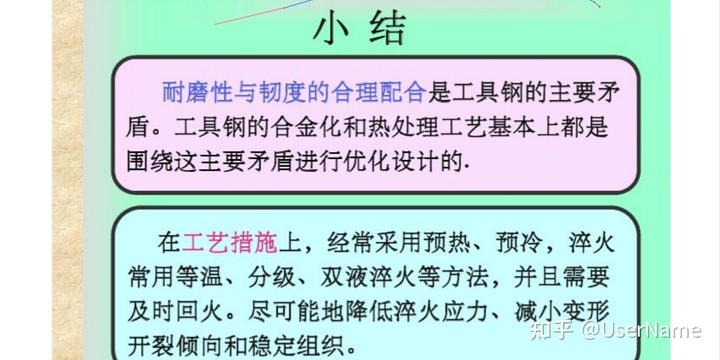
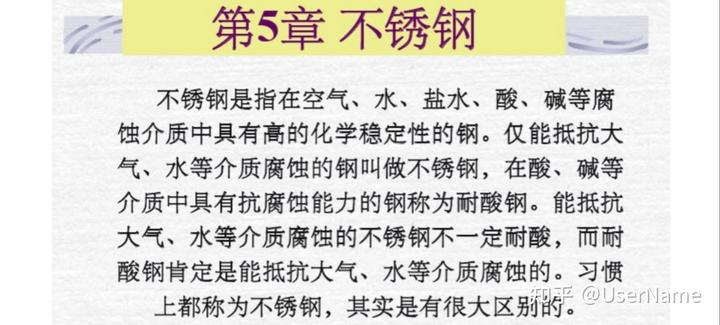
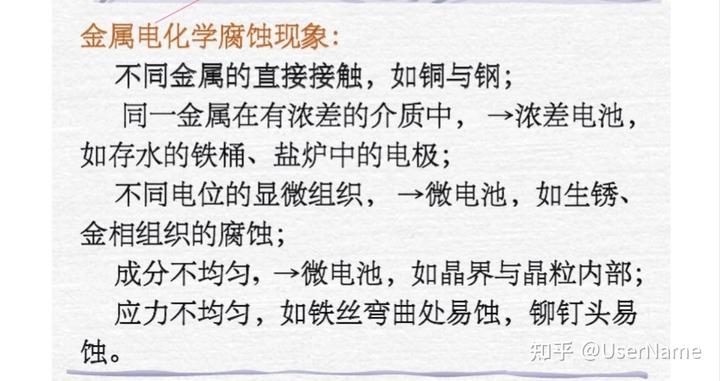
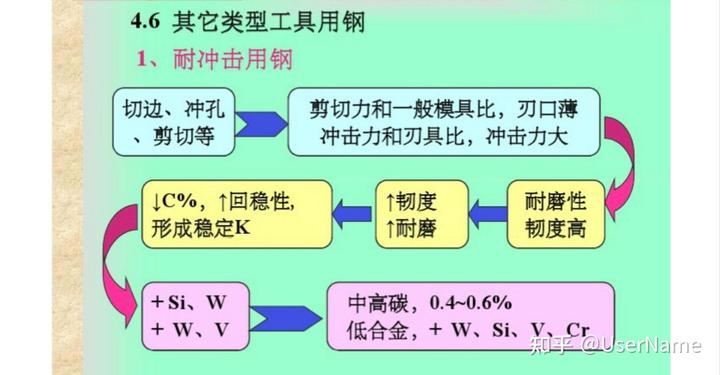
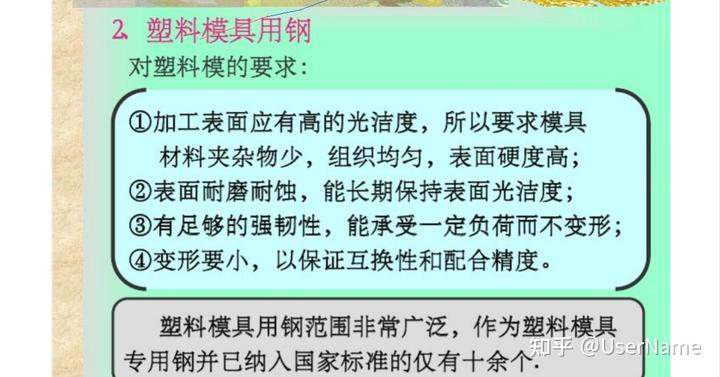
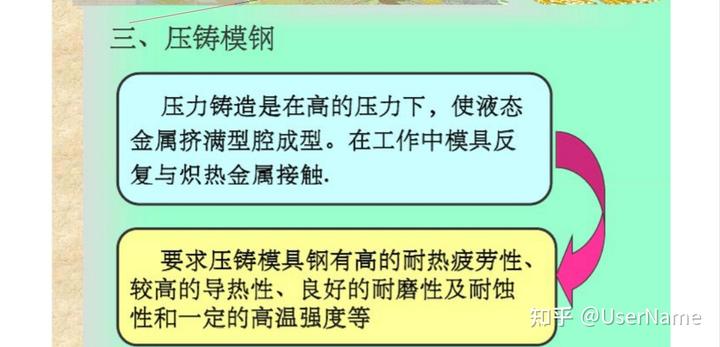
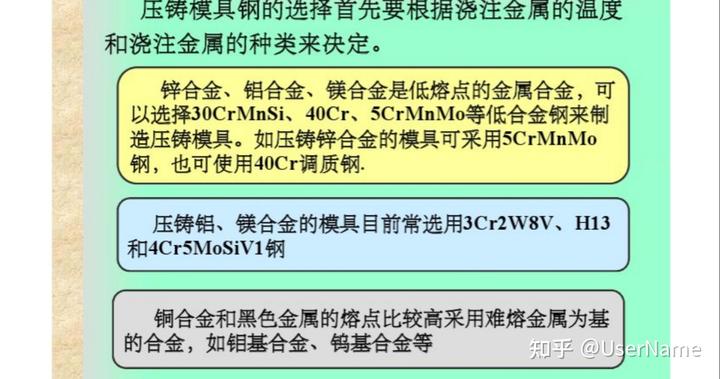
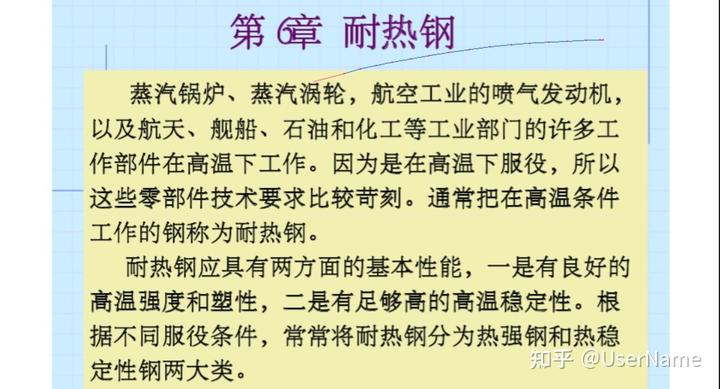
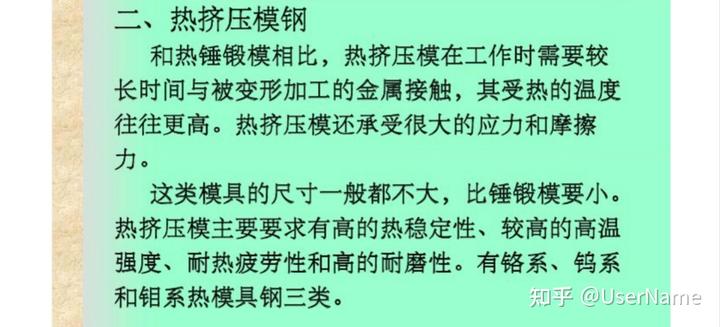
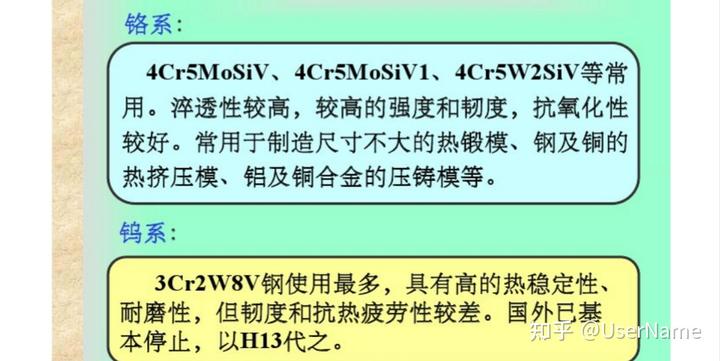
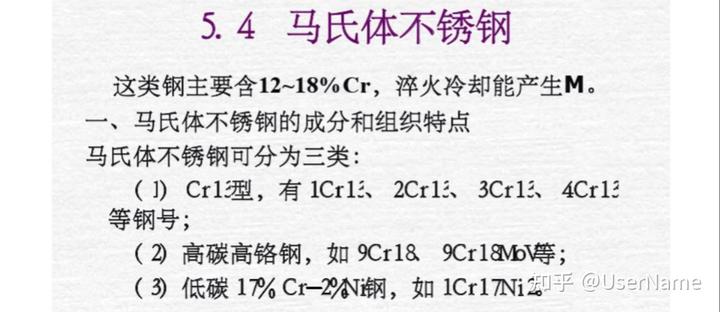
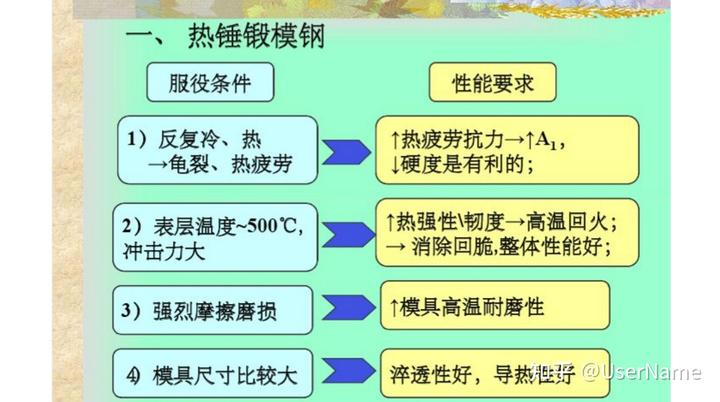

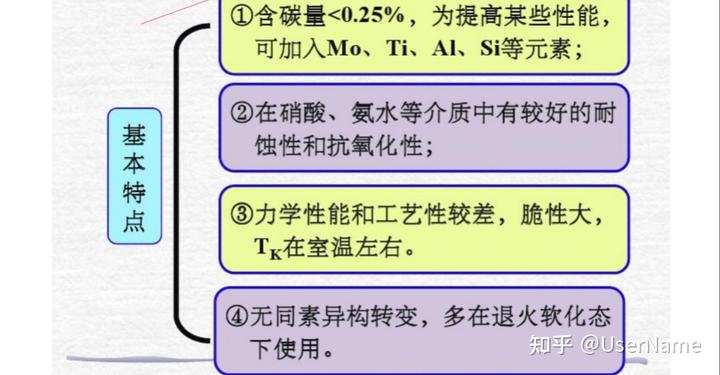
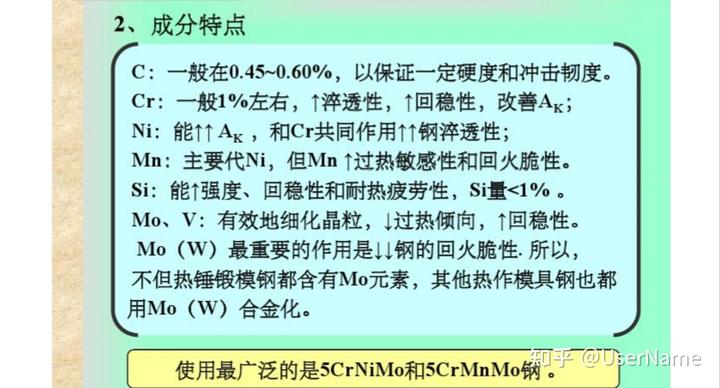
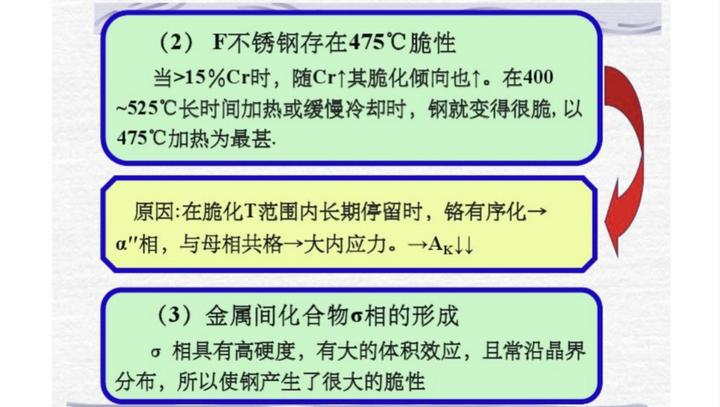
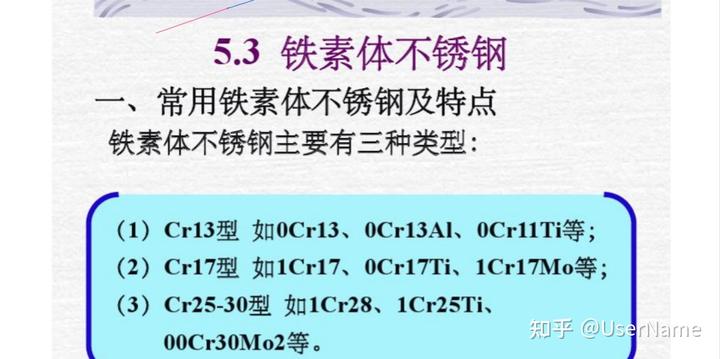
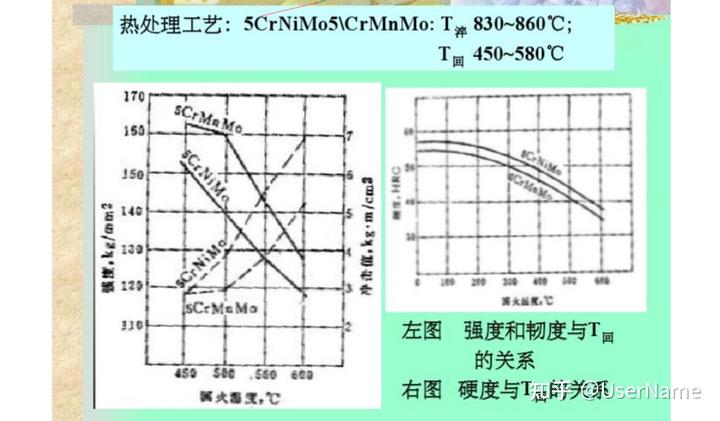
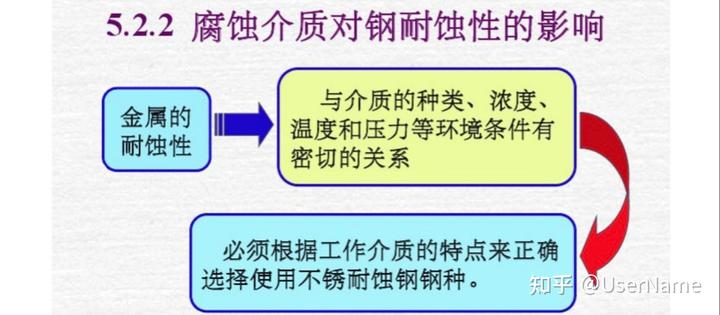
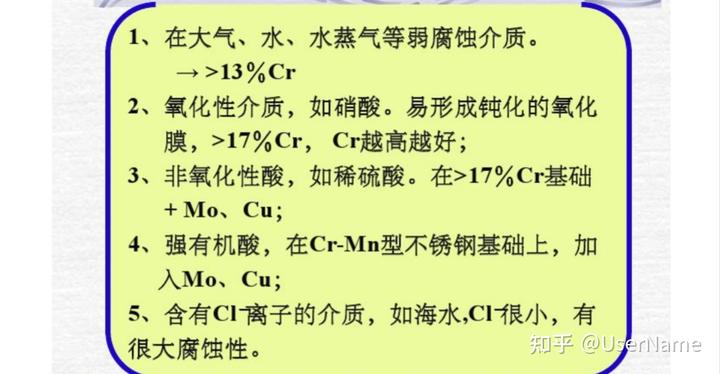
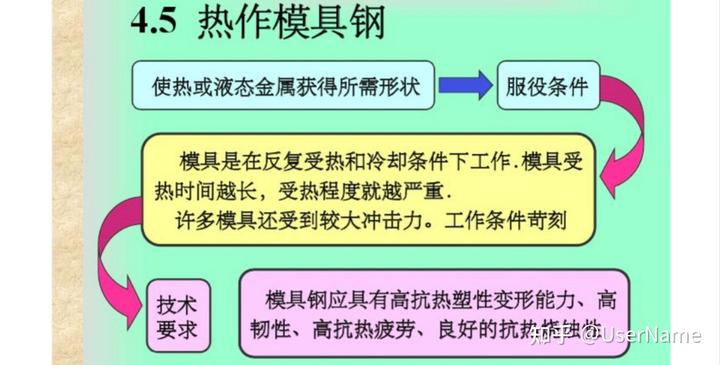
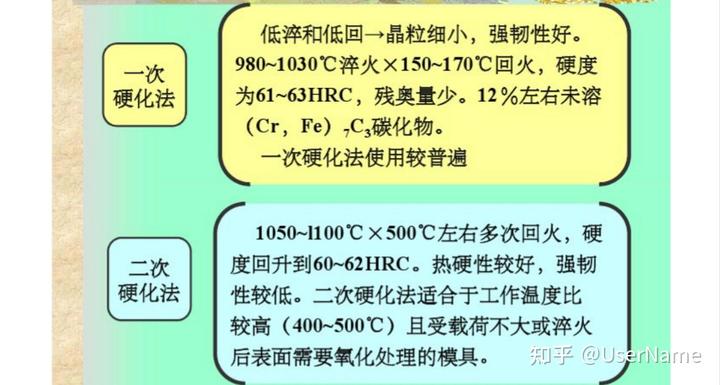
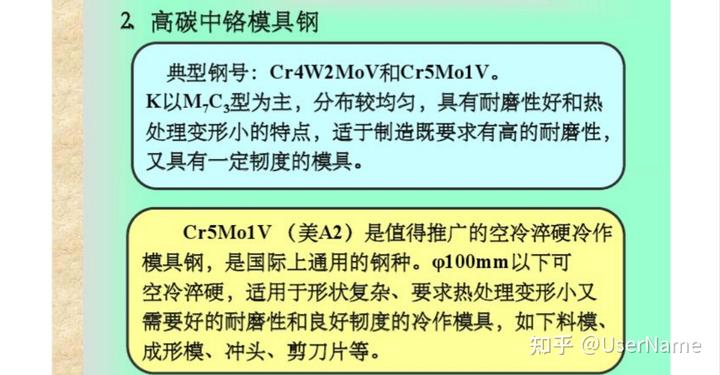
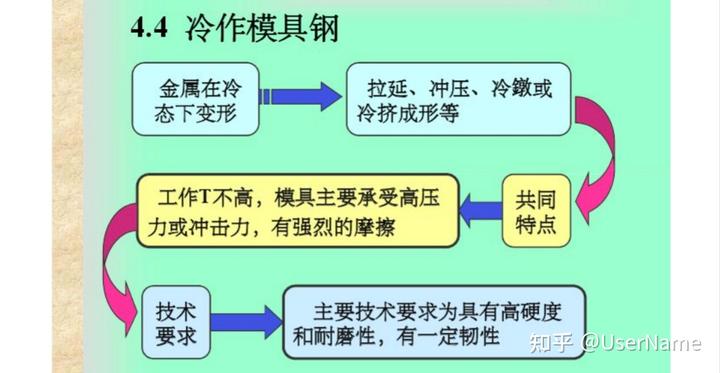
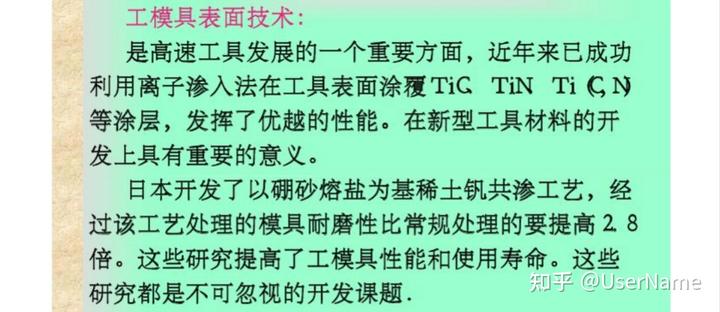
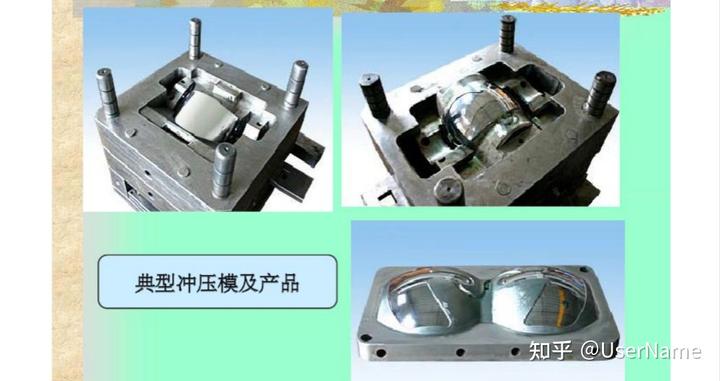
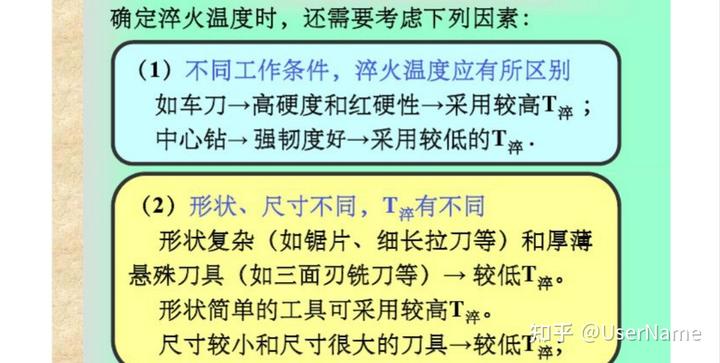
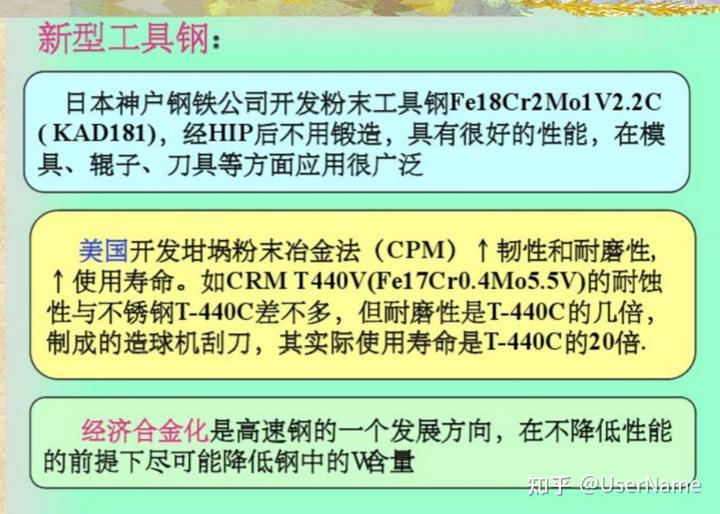
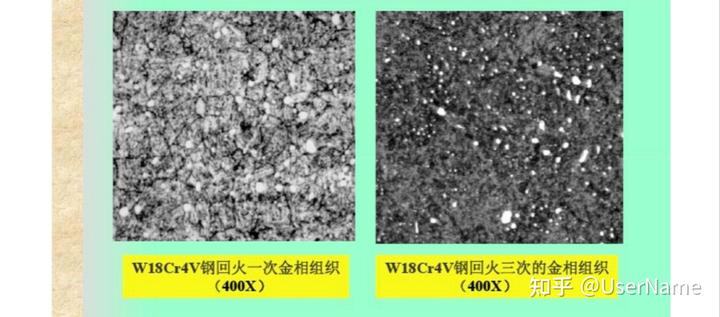
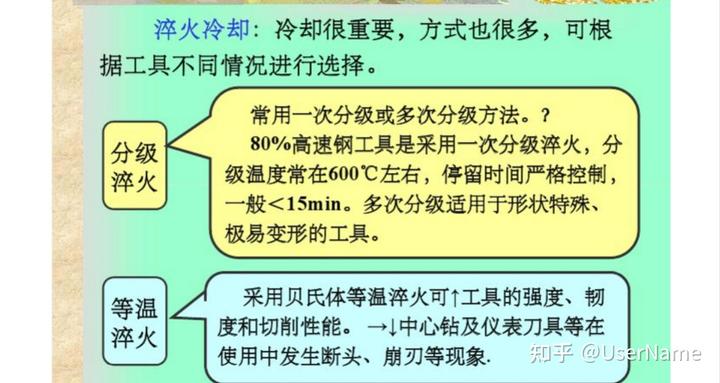
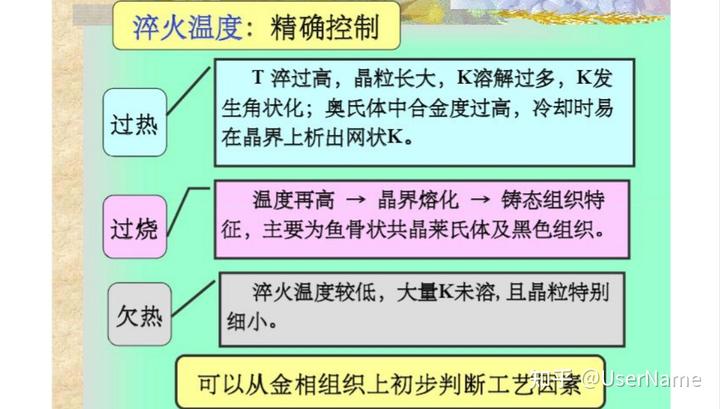
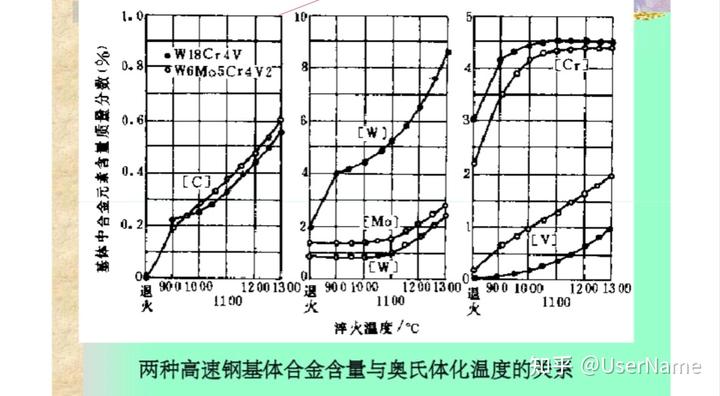
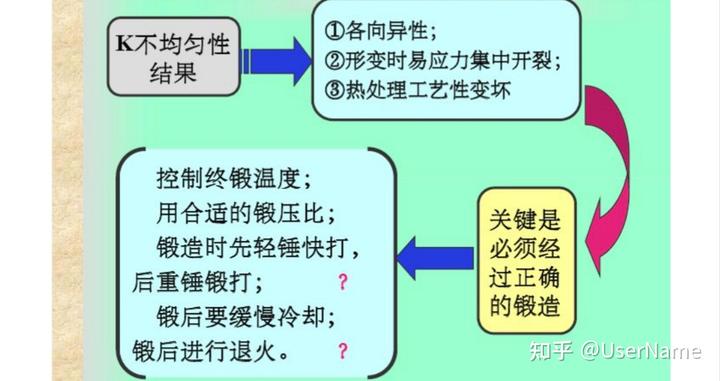
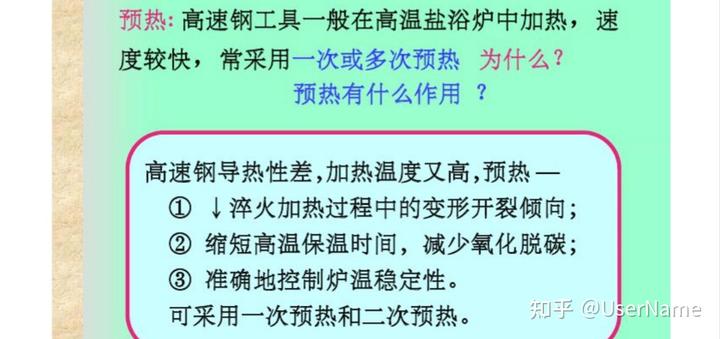
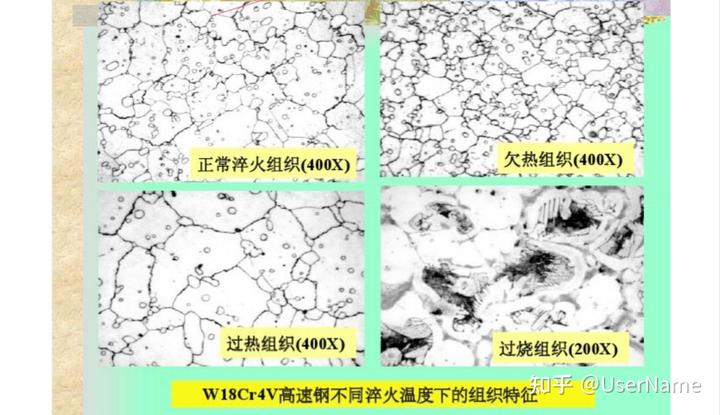
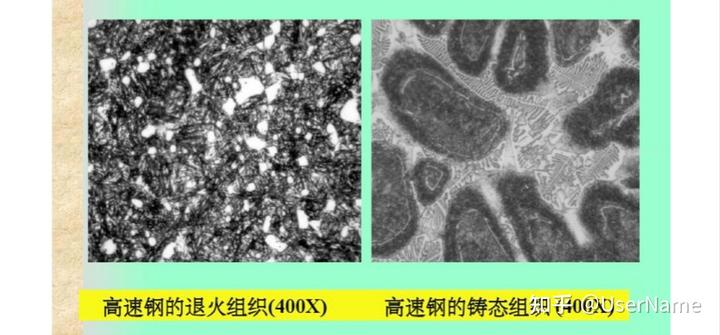
铁碳合金。我们通常将其与铁合称为钢铁,为了保证其韧性和塑性,含碳量一般不超过1.7%钢的主要元素除铁、碳外,还有硅、锰、硫、磷等,而且钢还根据品质分类为①普通钢(P≤0.045%,S≤0.050%)②优质钢(P、S均≤0.035%)③高级优质钢(P≤0.035%,S≤0.030%)按照化学成分又分①碳素钢:.低碳钢(C≤0.25%).中碳钢(C≤0.25~0.60%).高碳钢(C≤0.60%)。②合金钢:低合金钢(合金元素总含量≤5%).中合金钢(合金元素总含量>5~10%).高合金钢(合金元素总含量>10%)。
2、C、Si、Mn、P、S元素对铸铁石墨化有什么影响?为什么三低(C、Si、Mn低)一高(S高)的铸铁易出现白口?
(1)合金元素可以分为促进石墨化元素和阻碍石墨化元素,顺序为:
Al、C、Si、Ti、Ni、P、Co、Zr、Nb、W、Mn、S、Cr、V、Fe、Mg、Ce、B等。其中,Nb为中性元素,向左促进程度加强,向右阻碍程度加强。C和Si是铸铁中主要的强烈促进石墨化元素,为综合考虑它们的影响,引入碳当量CE=C%+1/3Si%,一般CE≈4%,接近共晶点。S是强烈阻碍石墨化元素,降低铸铁的铸造和力学性能,控制其含量。
(2)铸铁的含碳量高,脆性大,焊接性很差,在焊接过程中易产生白口组织和裂纹
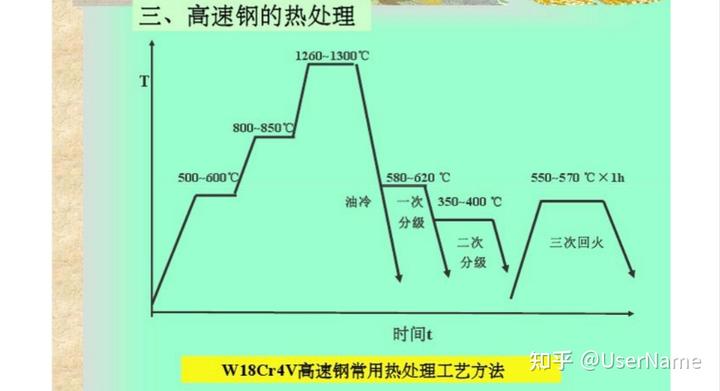
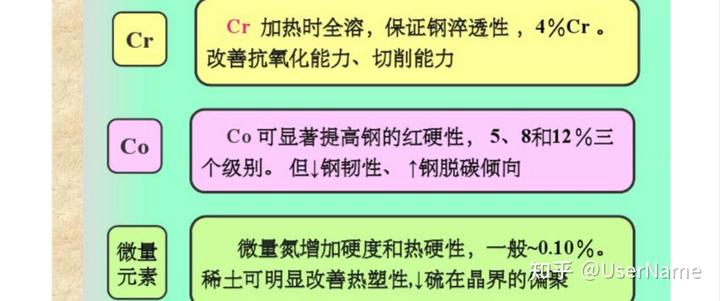
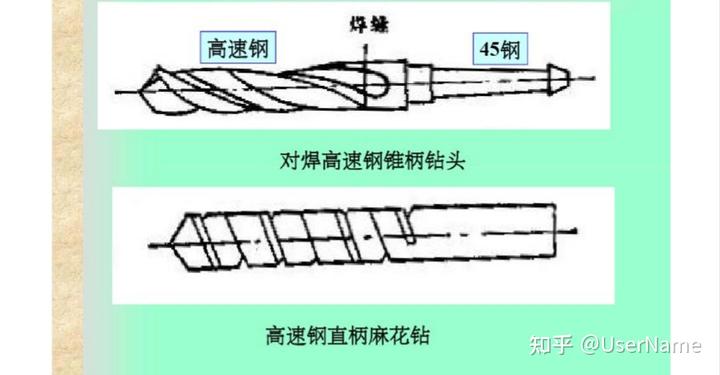
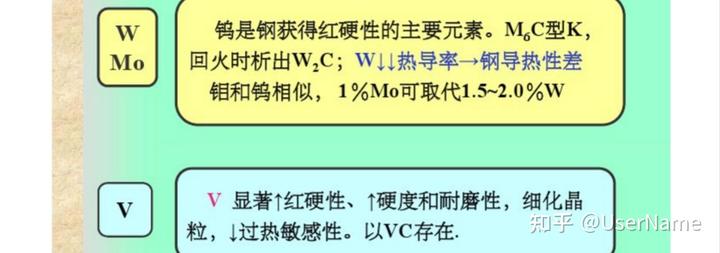
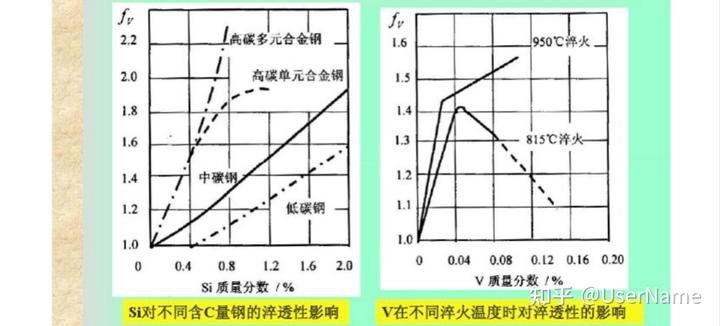
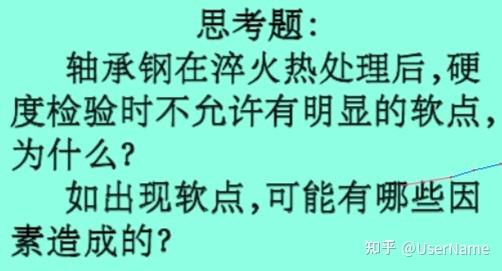
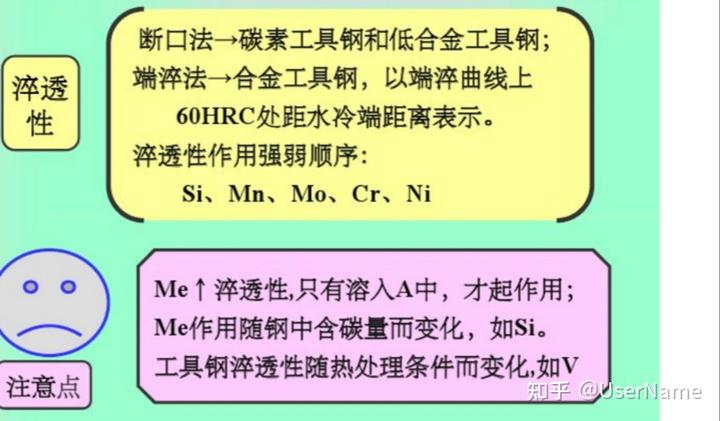
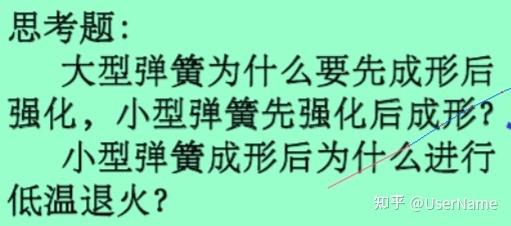
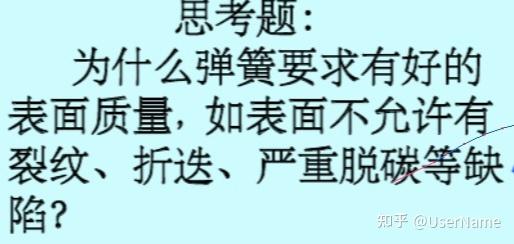
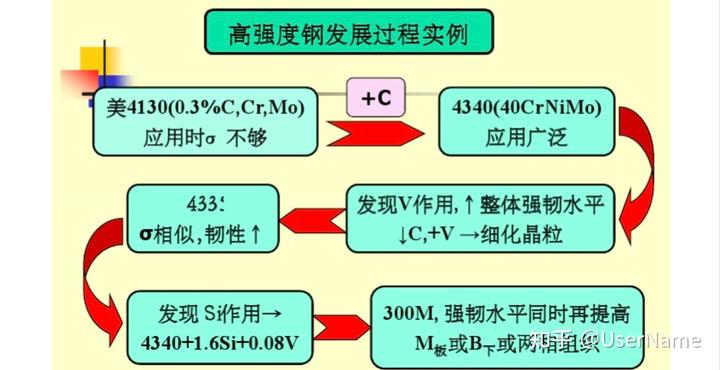
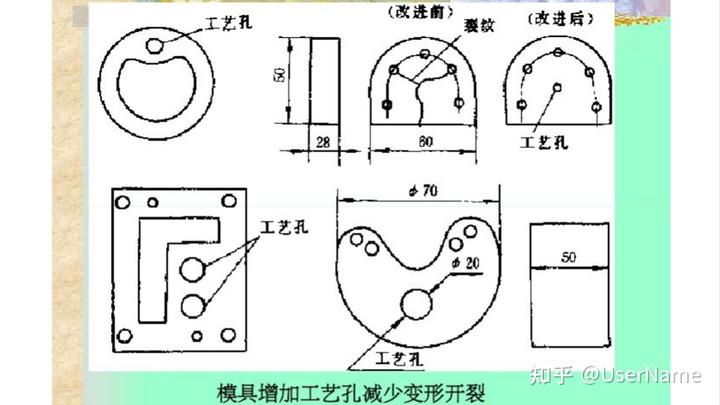
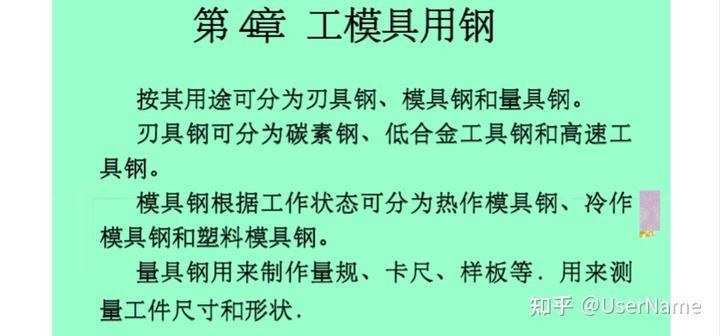
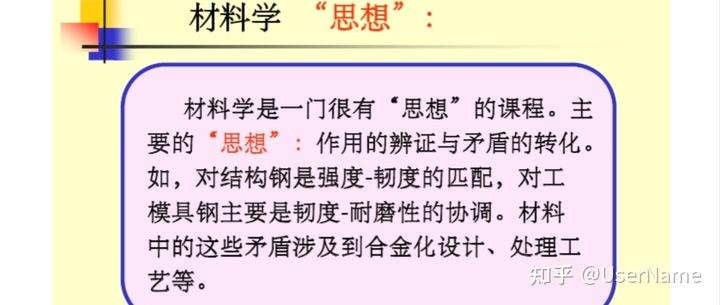
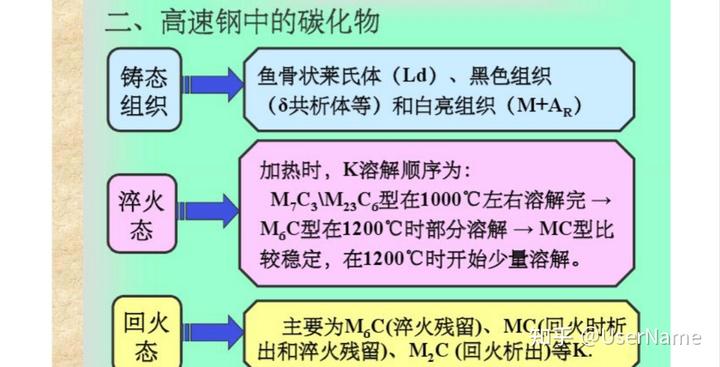

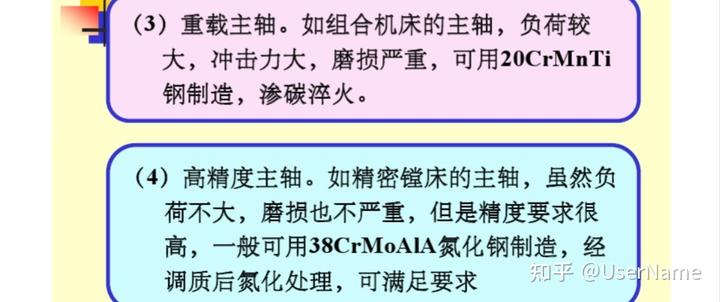
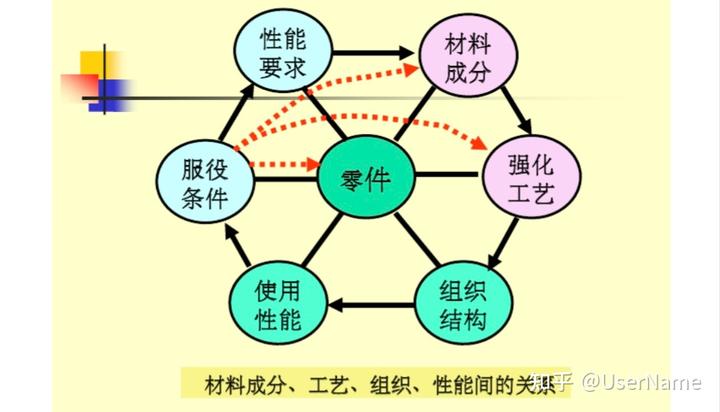
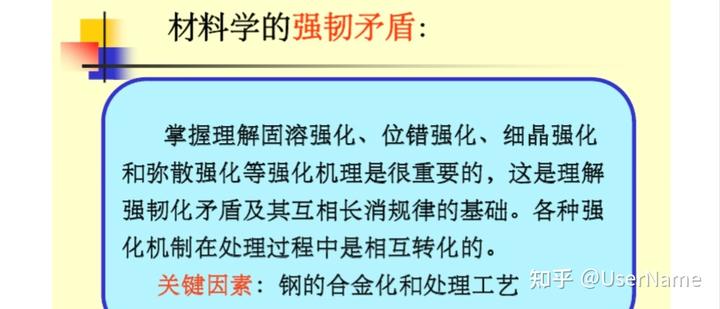
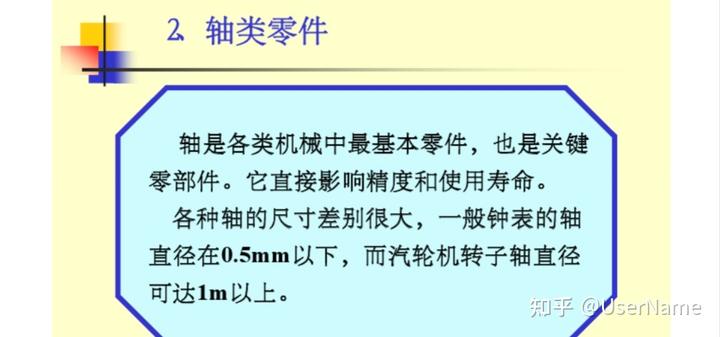
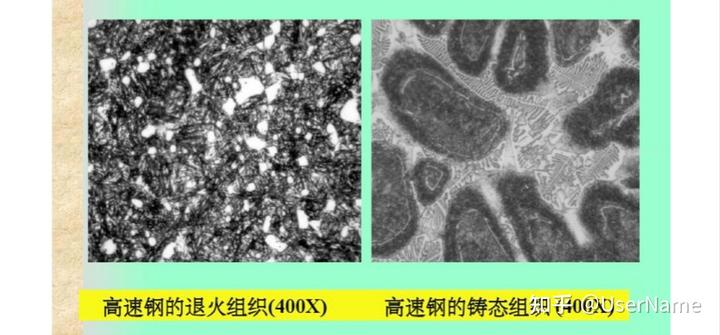
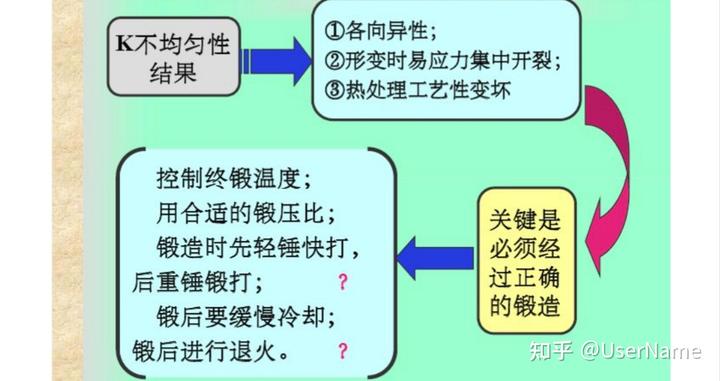
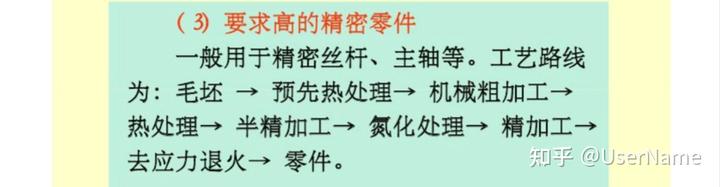
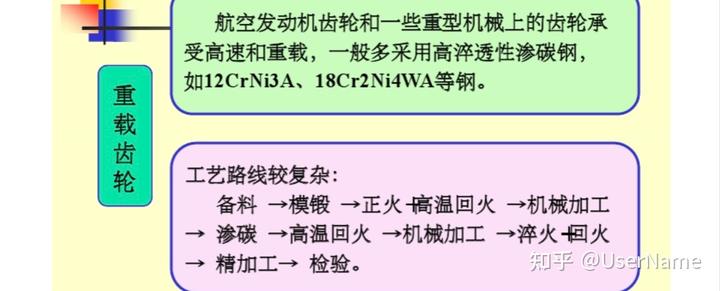
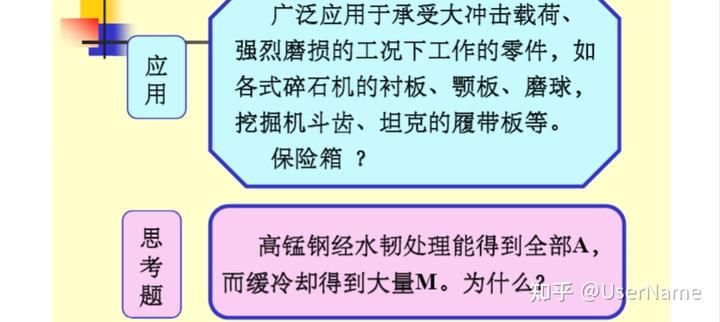
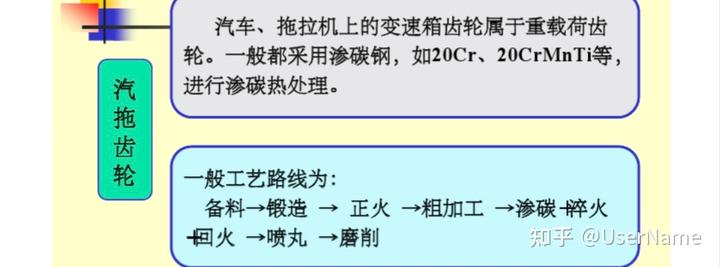
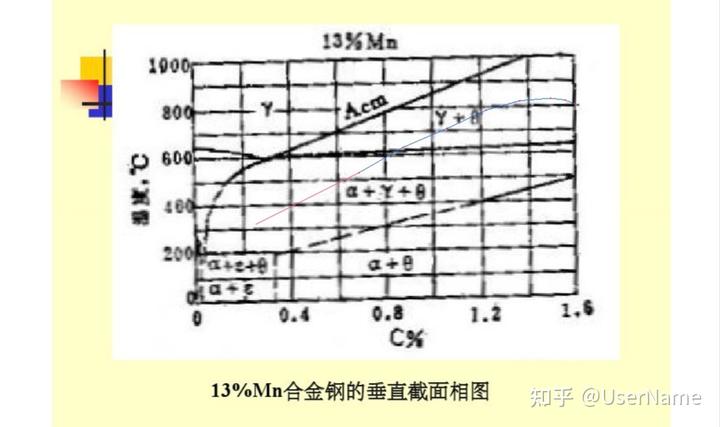
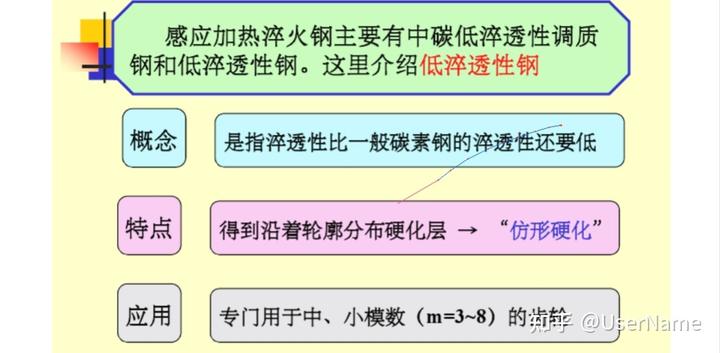
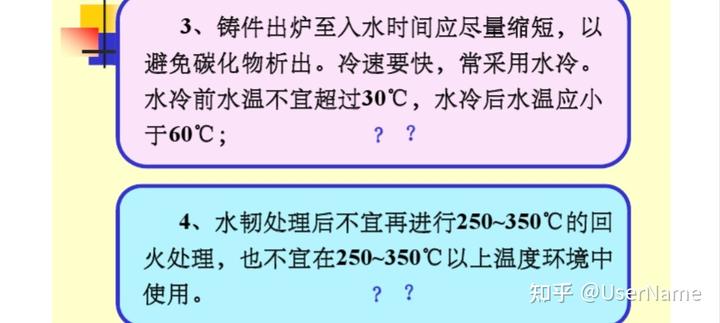
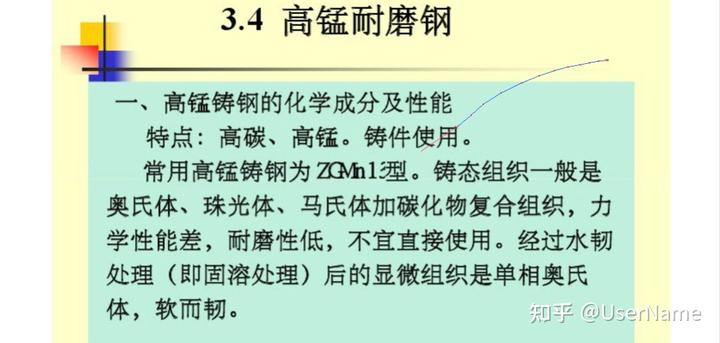
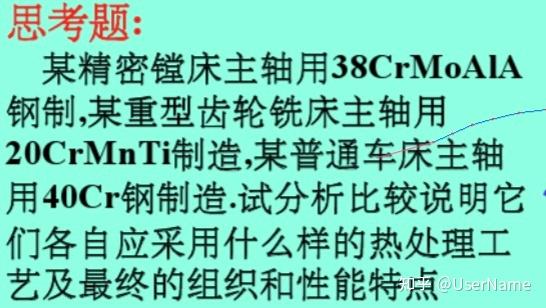
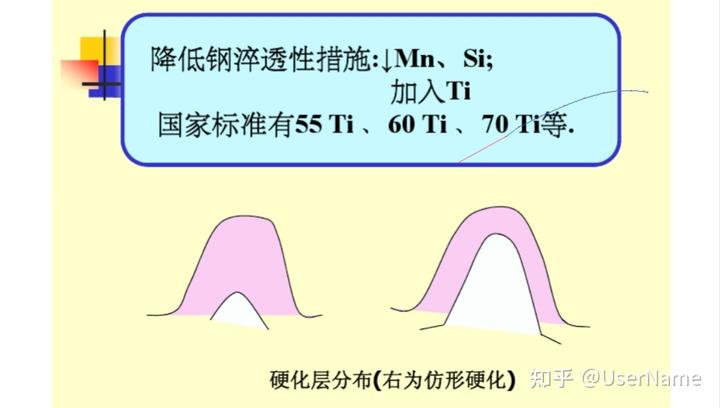
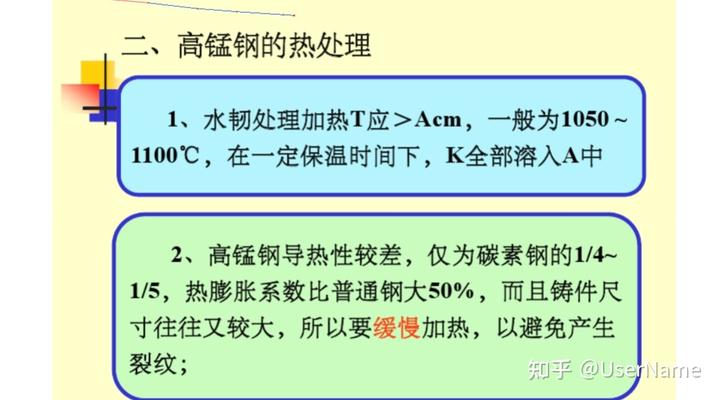
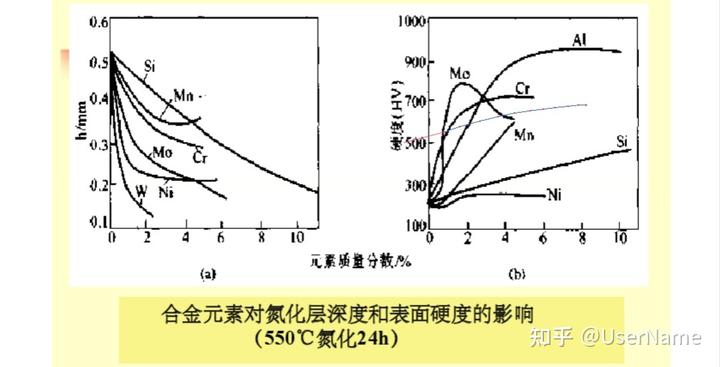
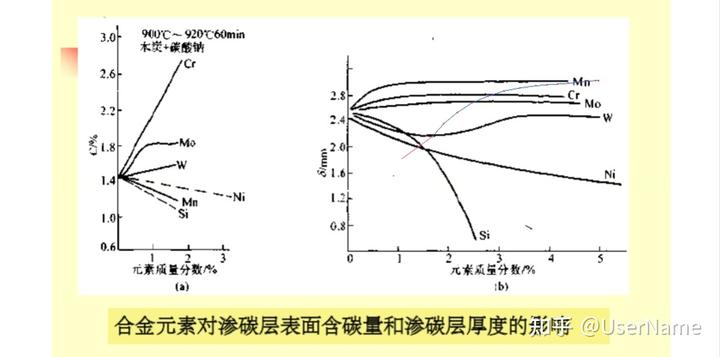
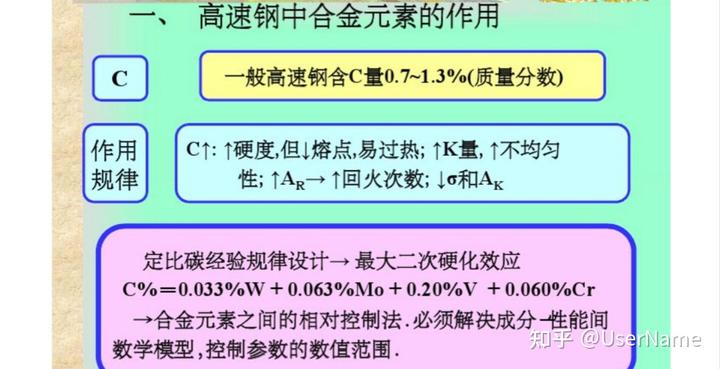
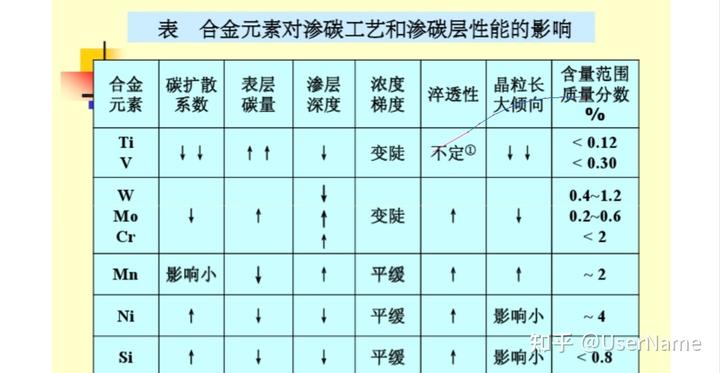
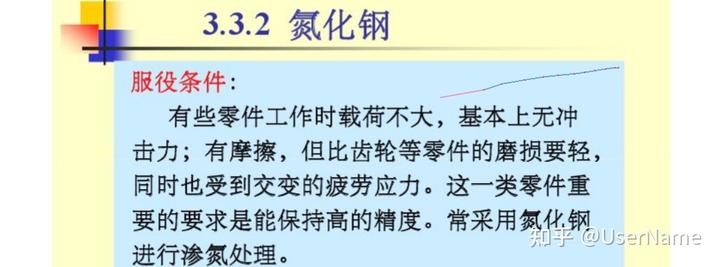
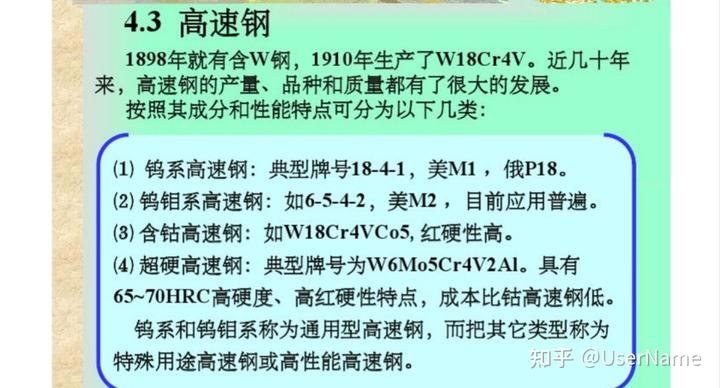
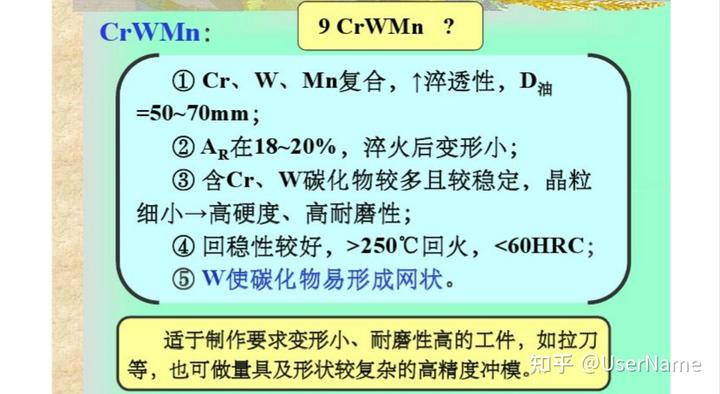
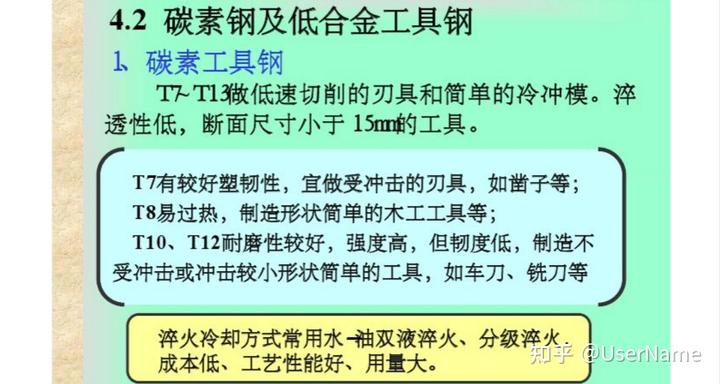
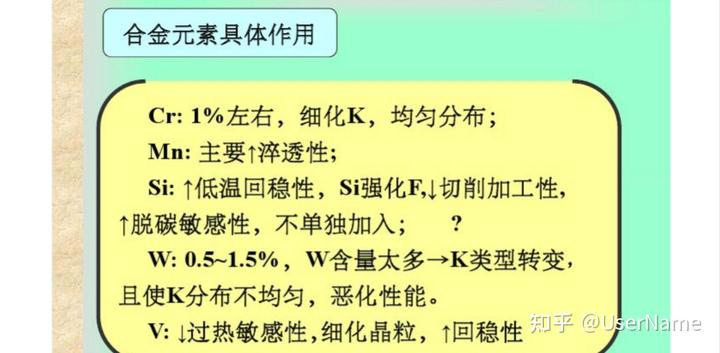
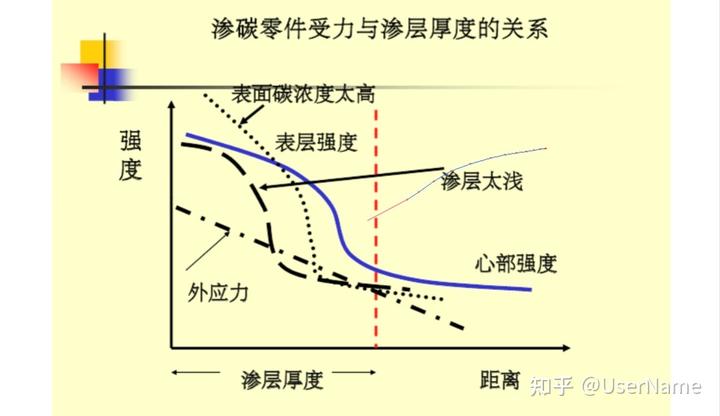
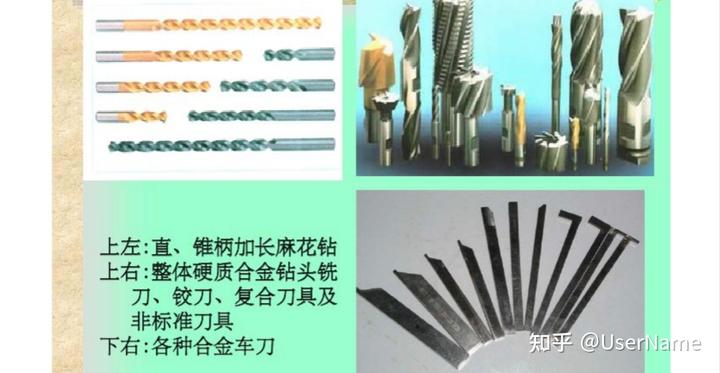
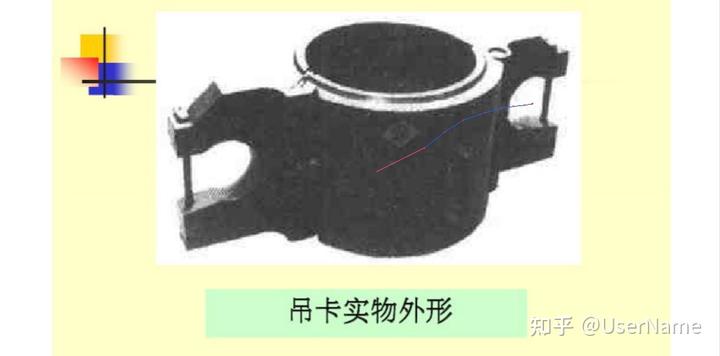
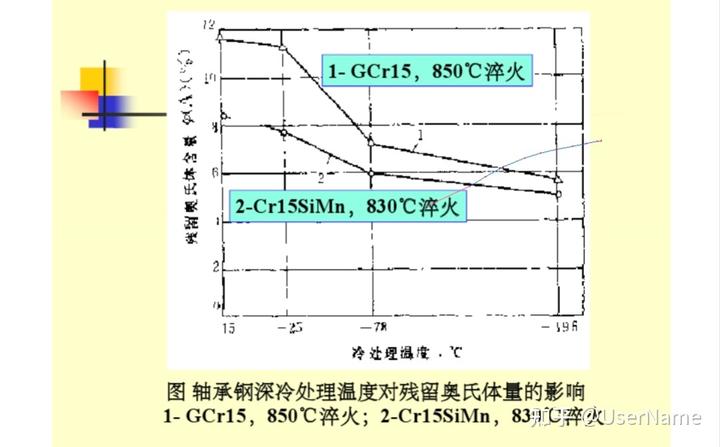
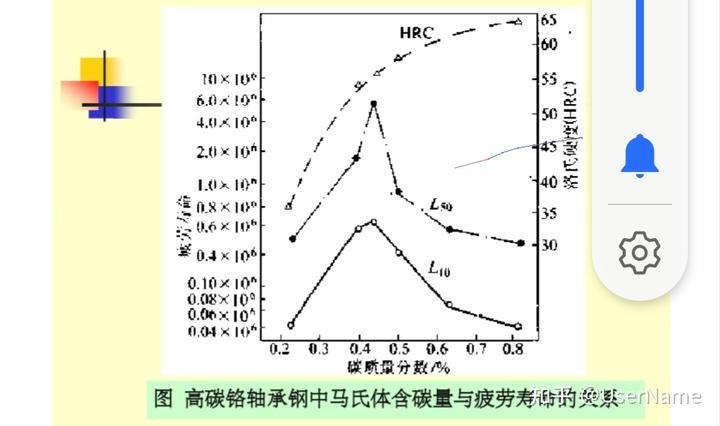
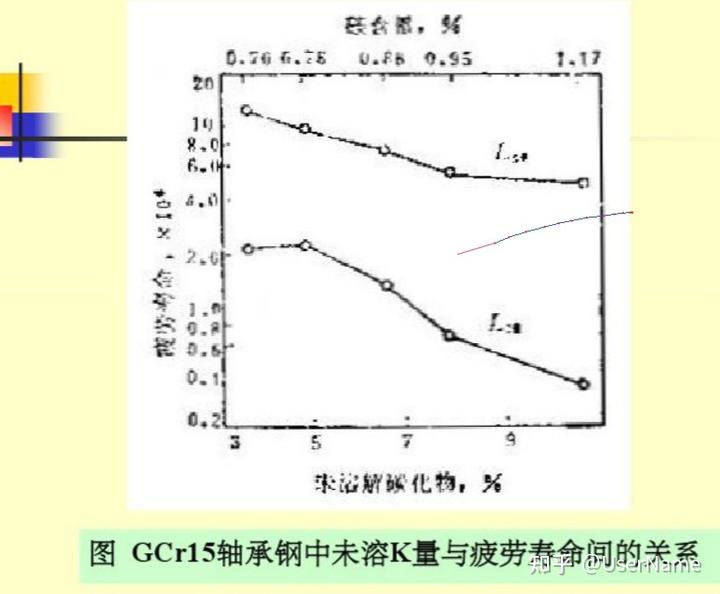
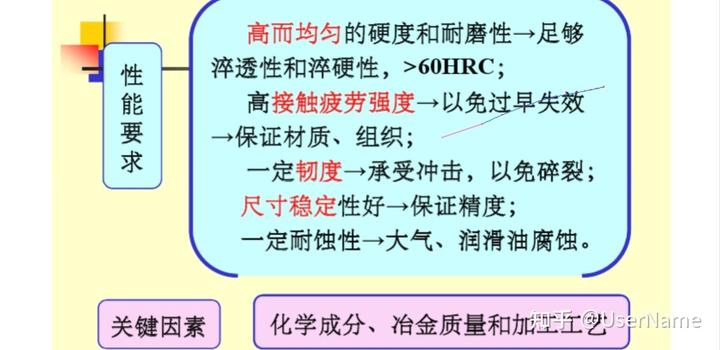
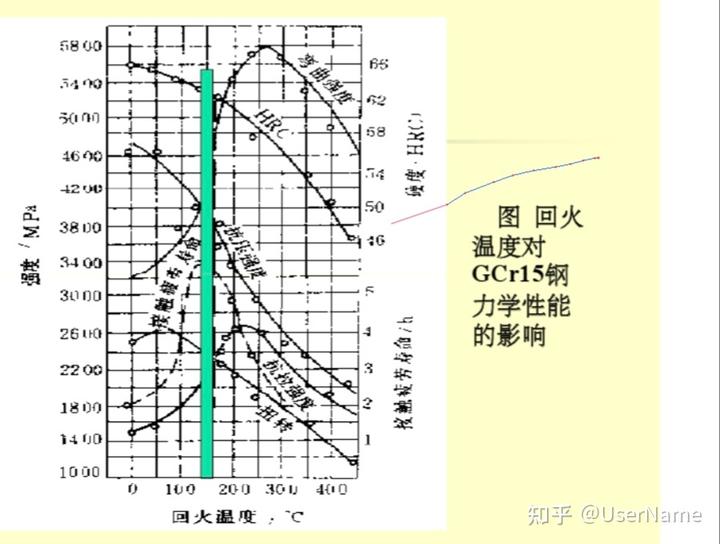
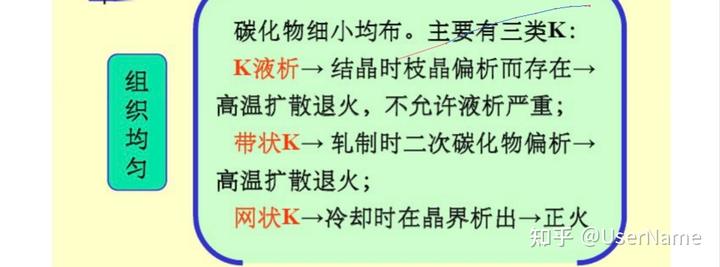
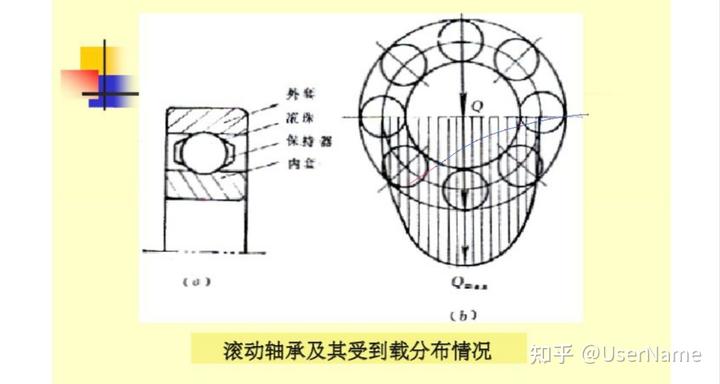
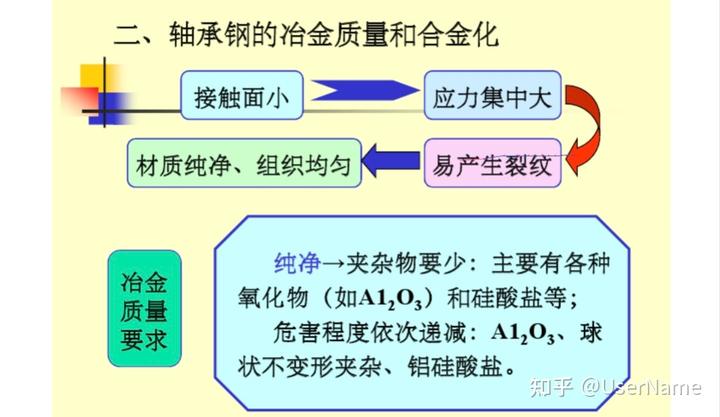
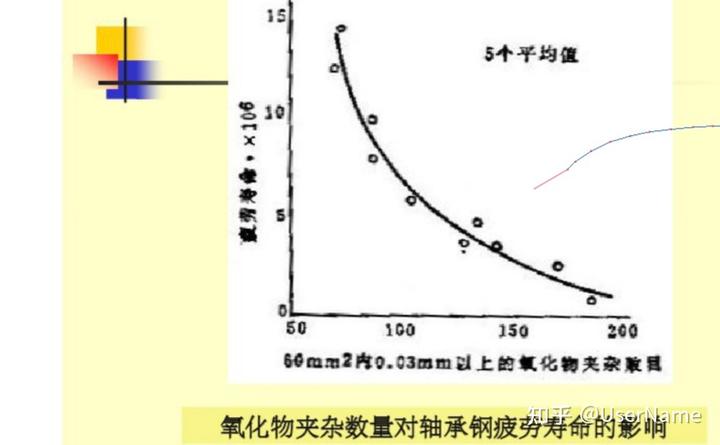
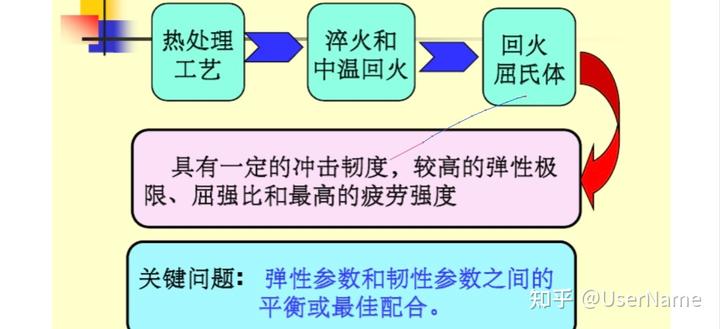
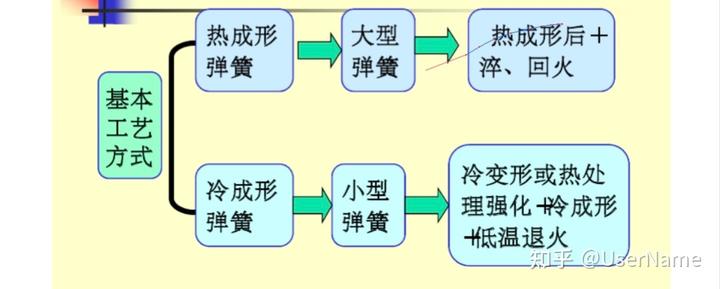
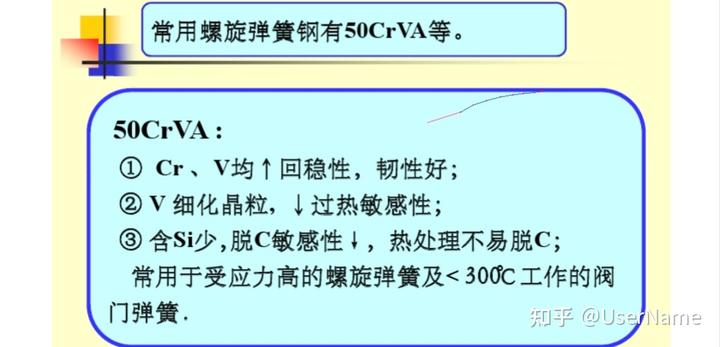
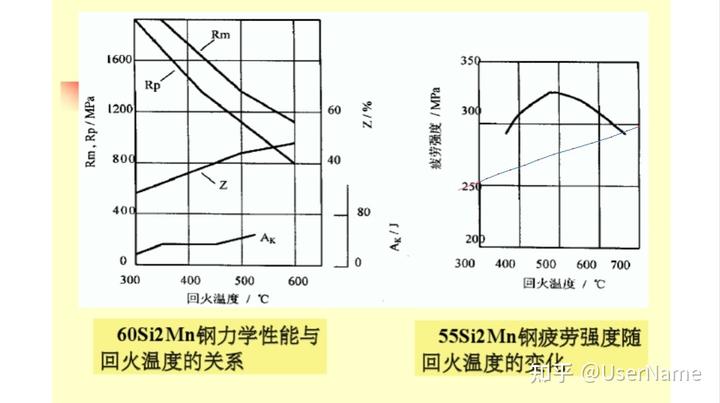
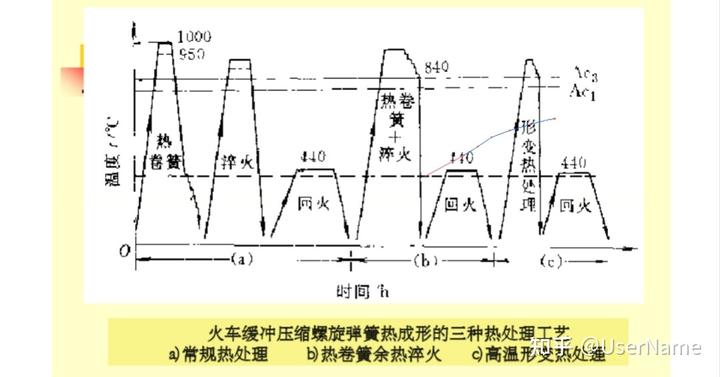
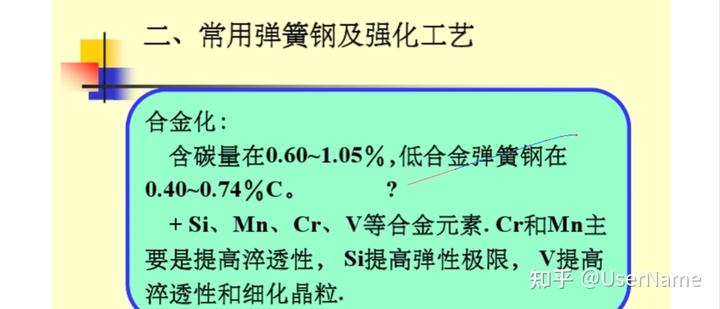
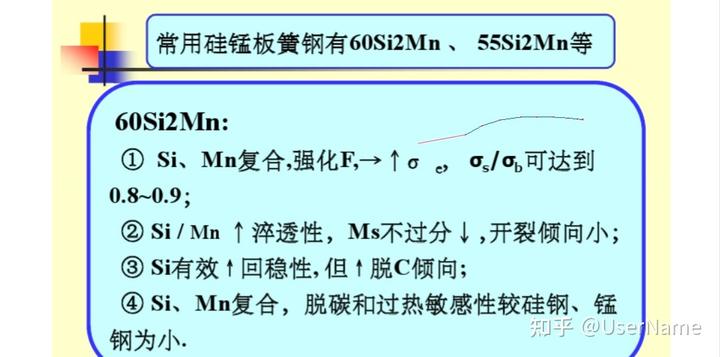
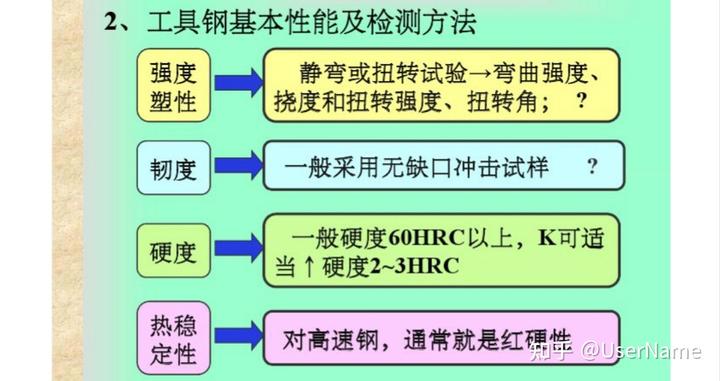
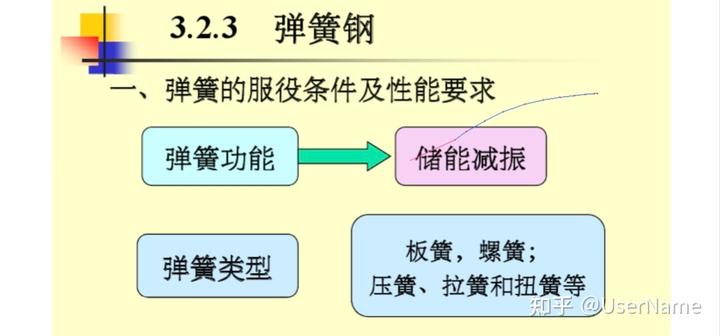
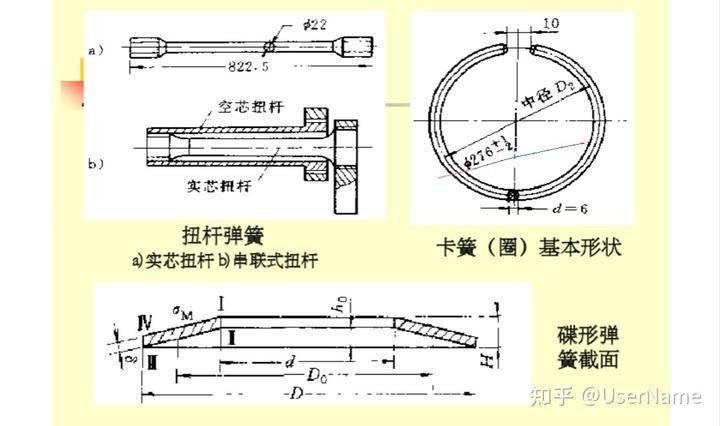
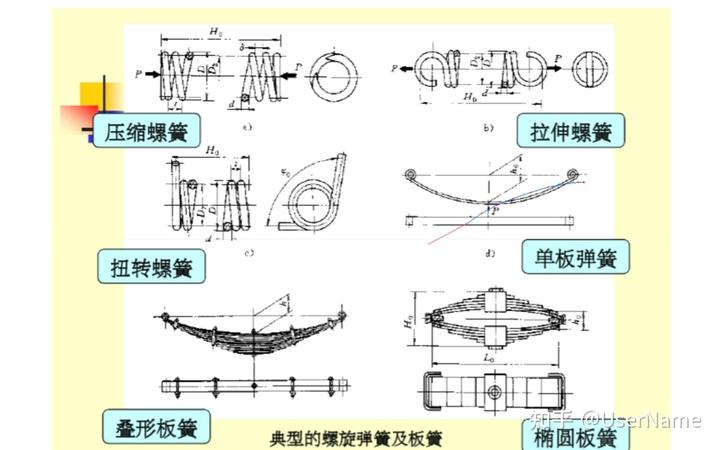
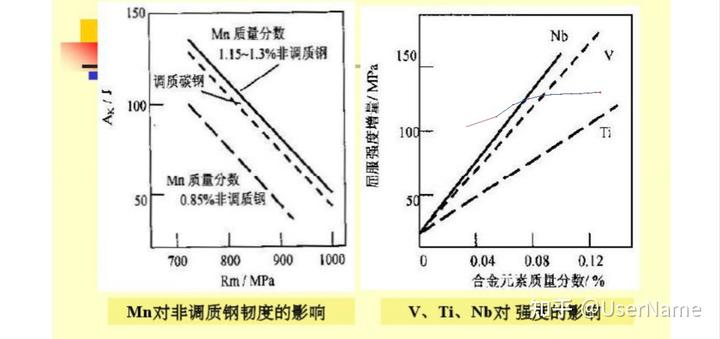
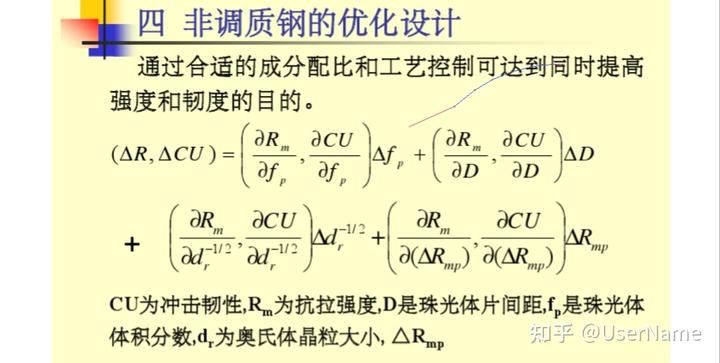
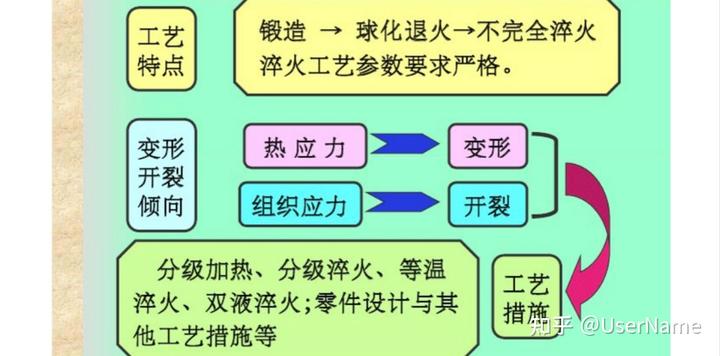
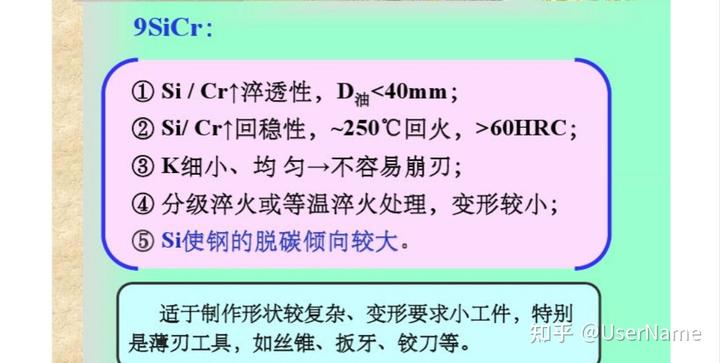
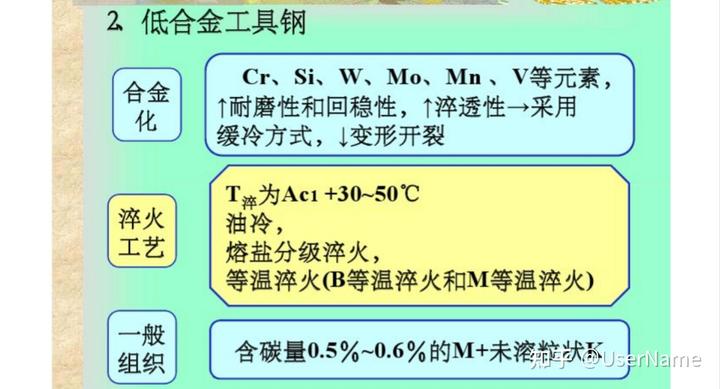
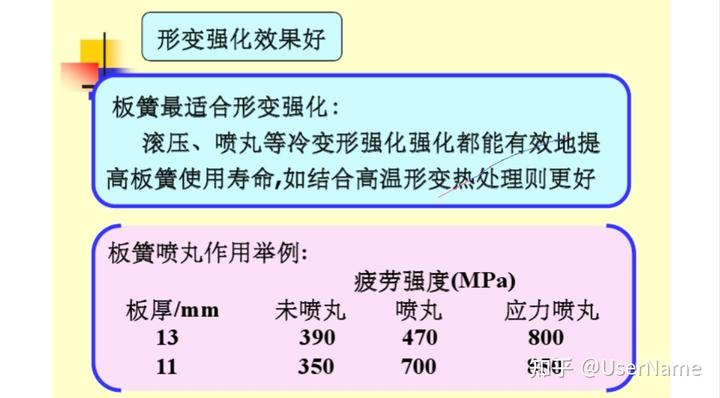
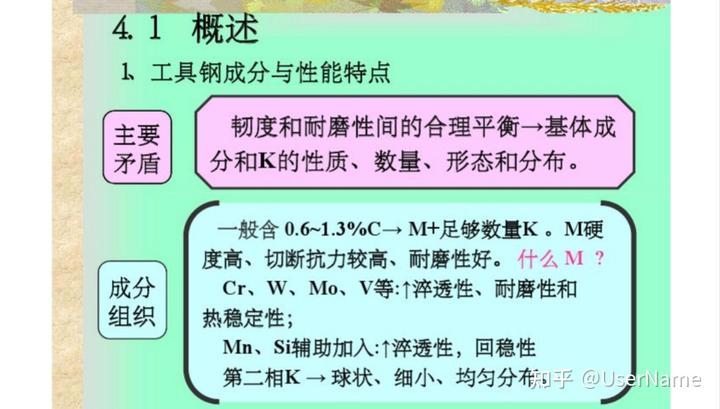
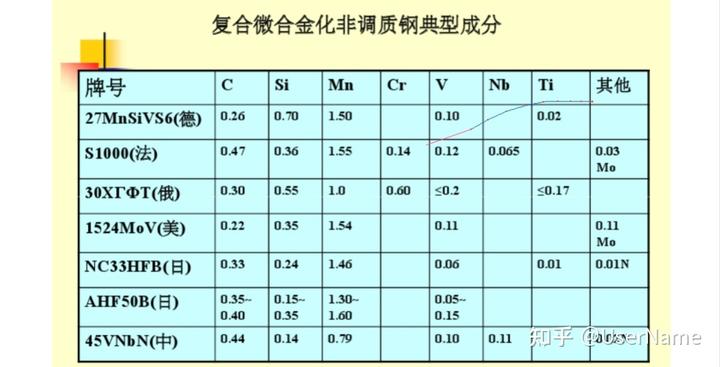
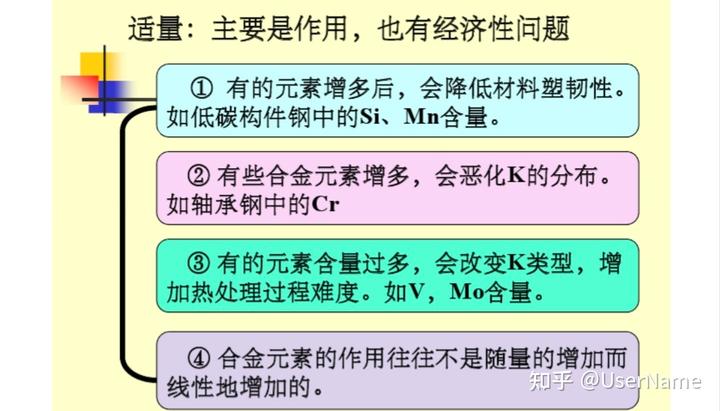
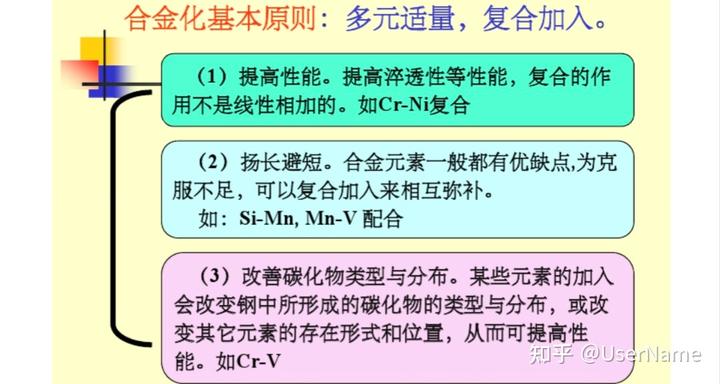
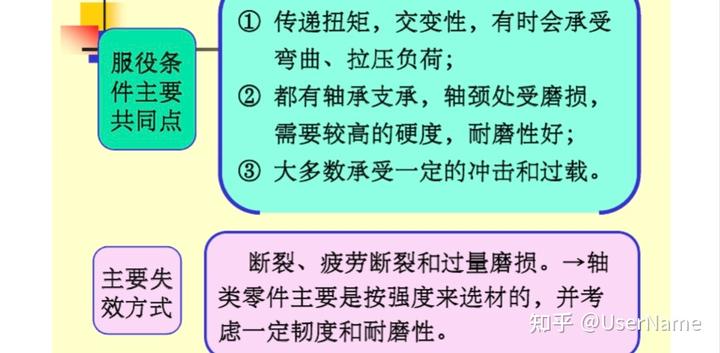
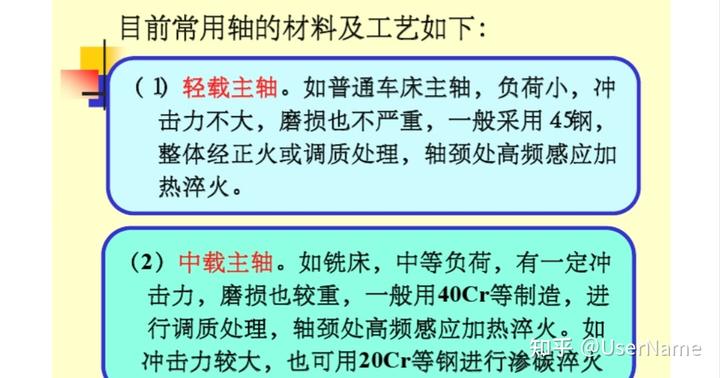
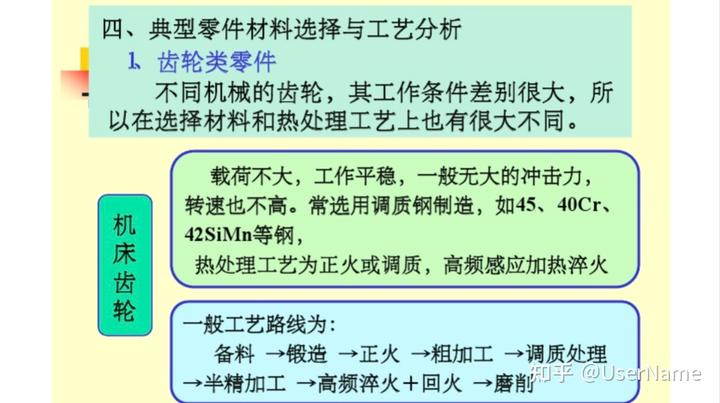
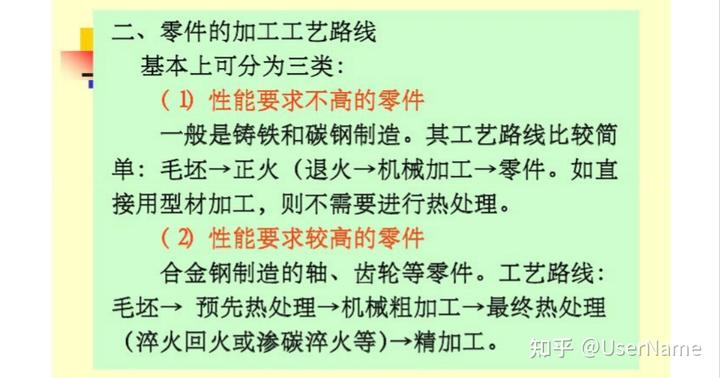
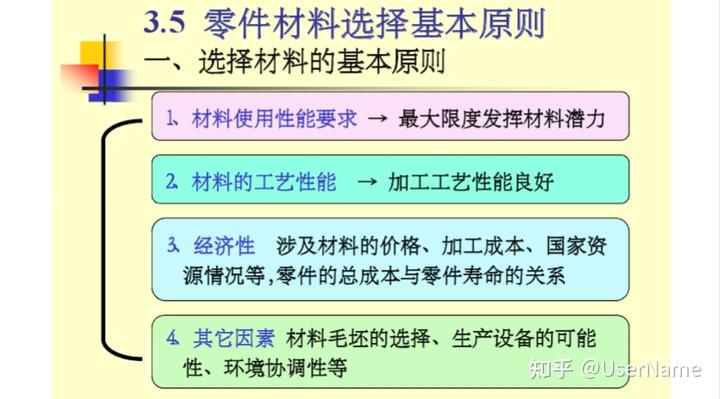
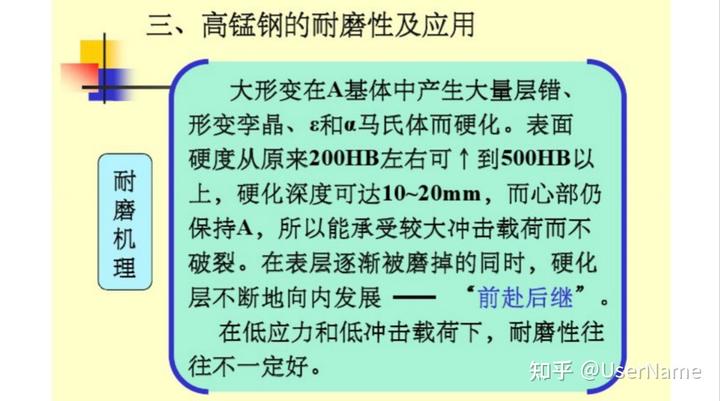
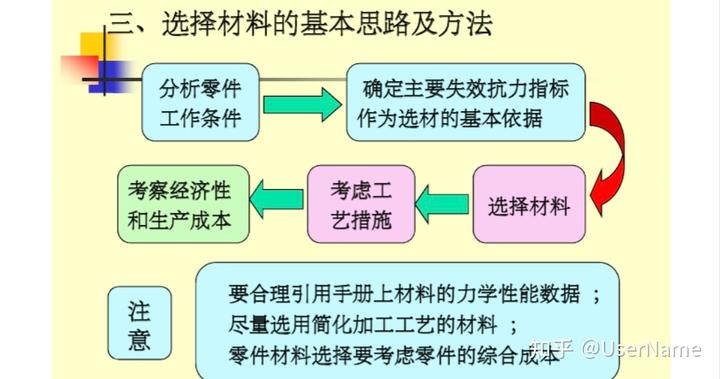
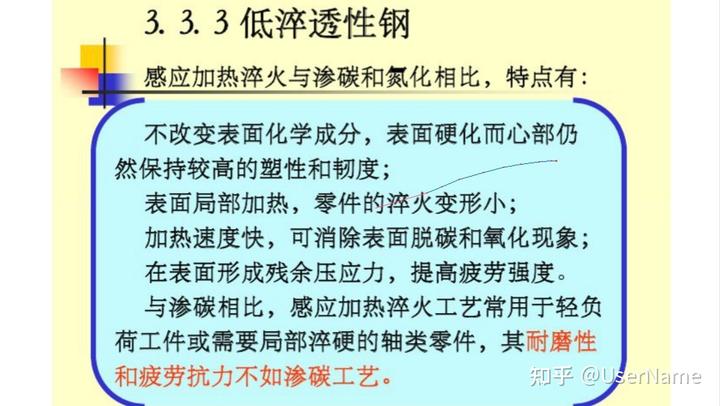
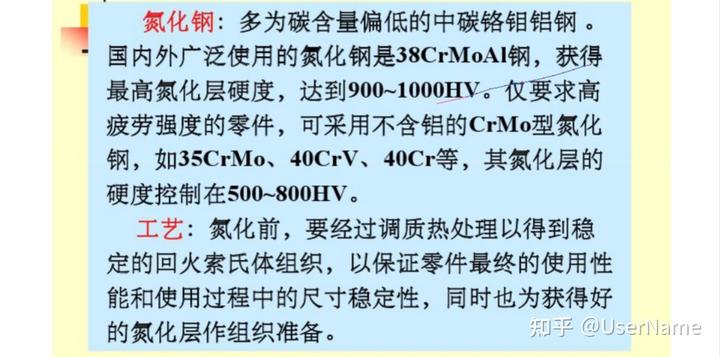

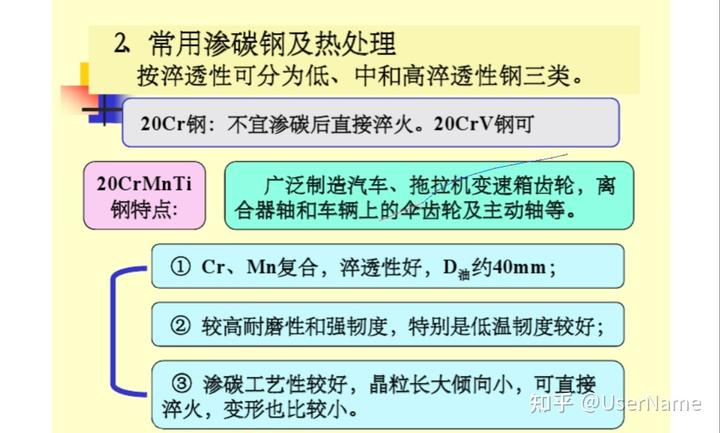
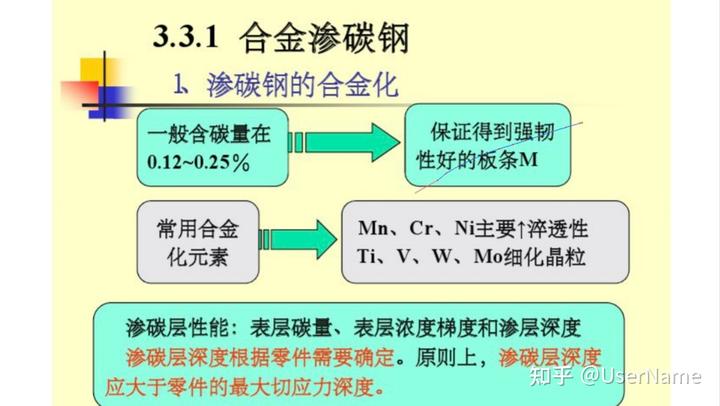
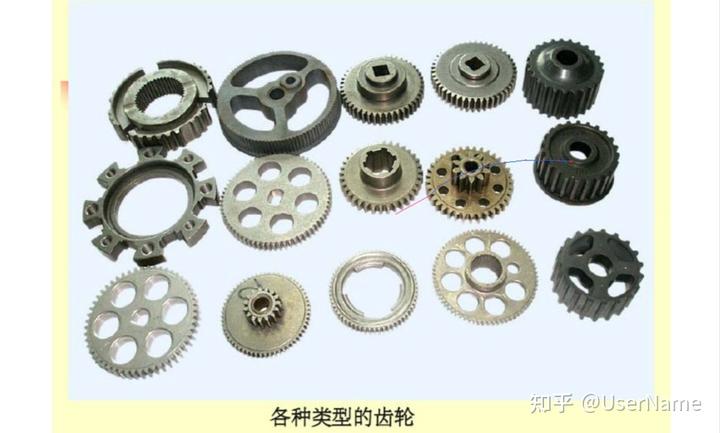
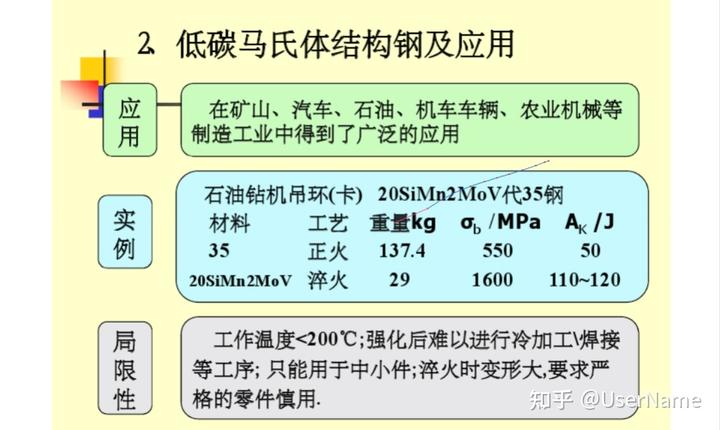
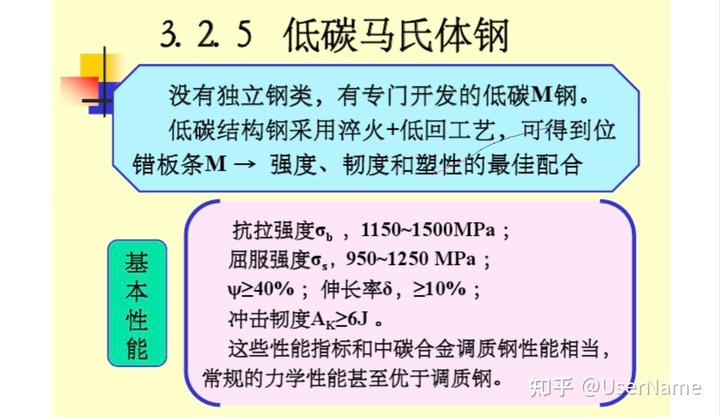
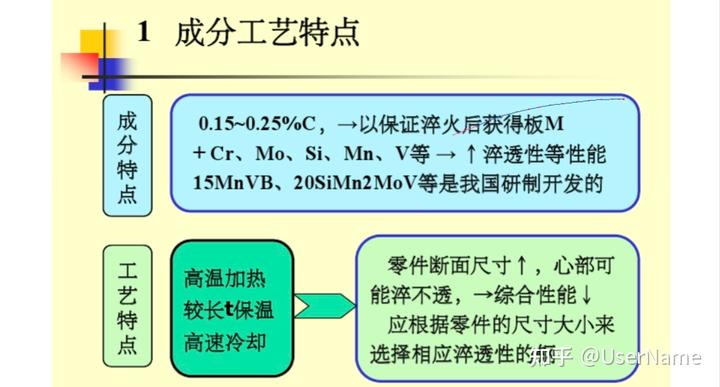
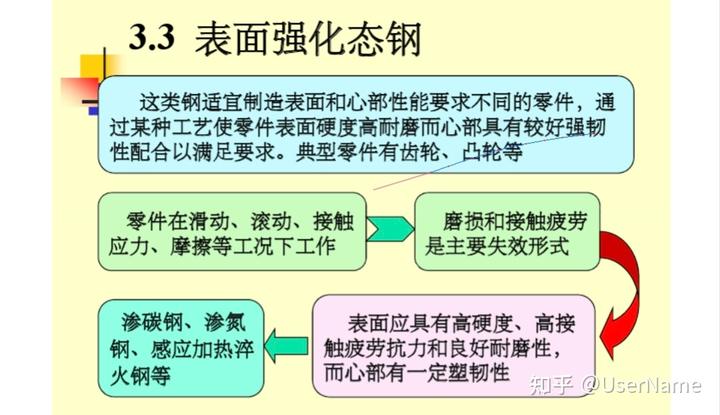
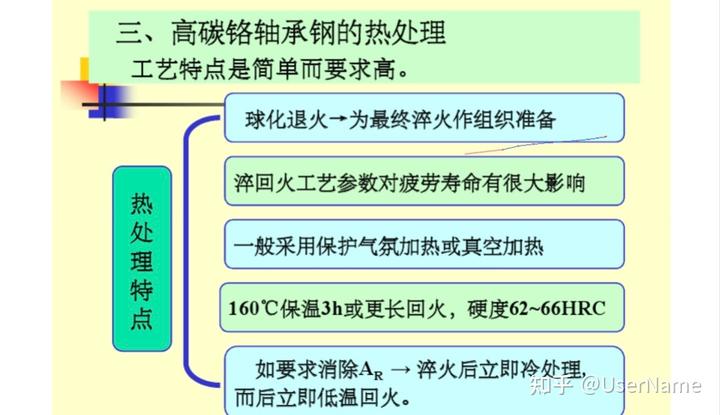
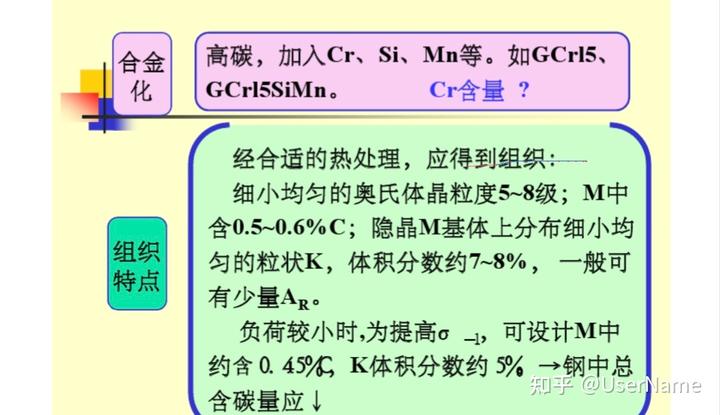
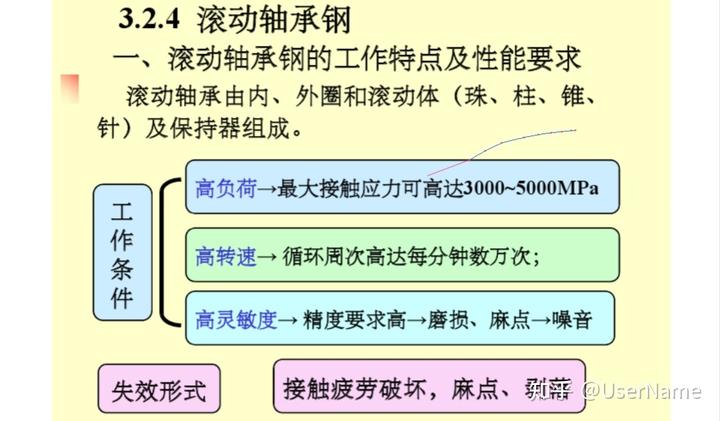
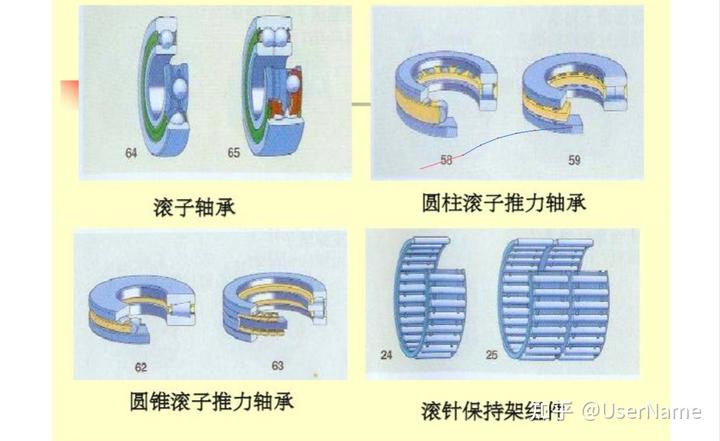
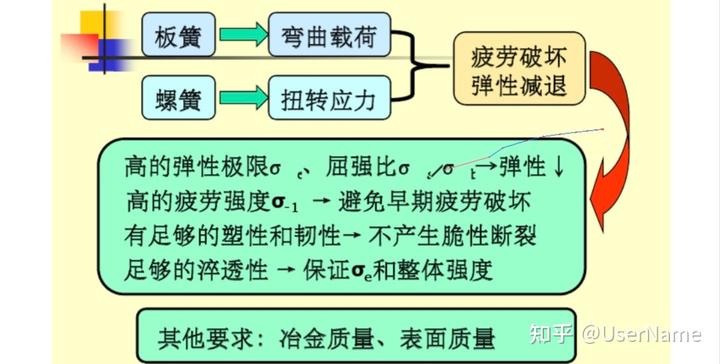
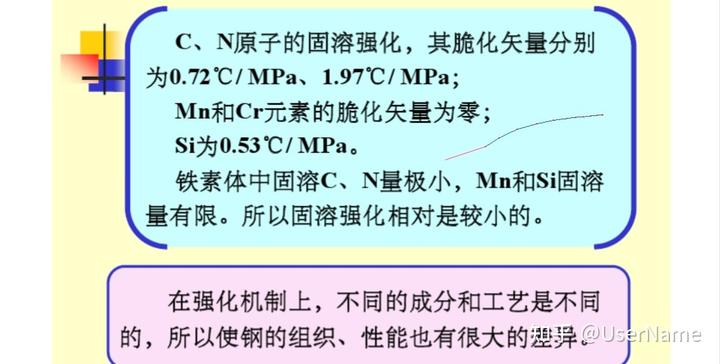
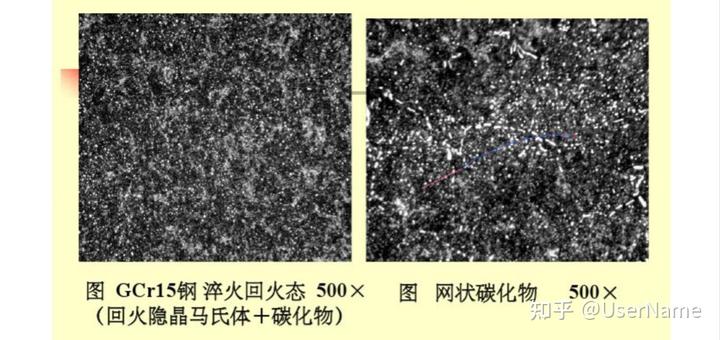
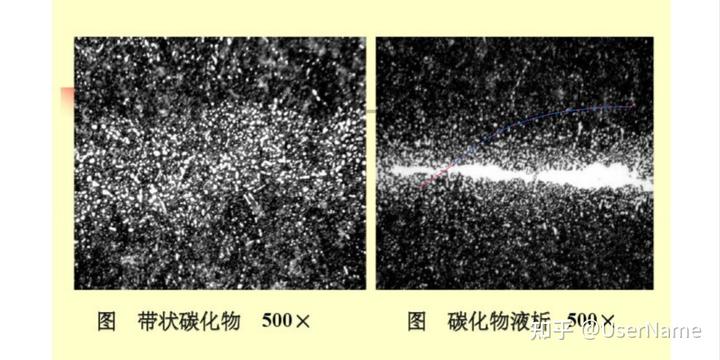
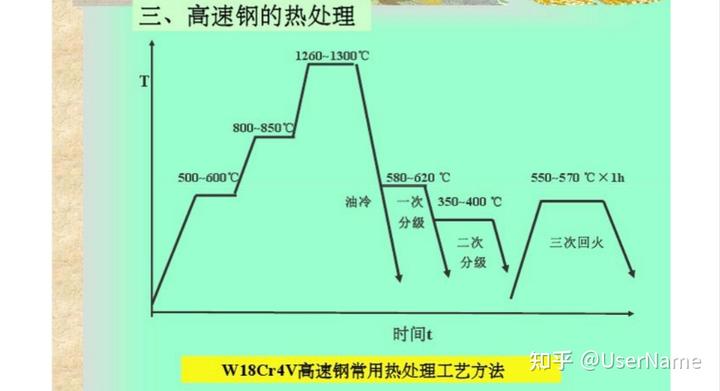
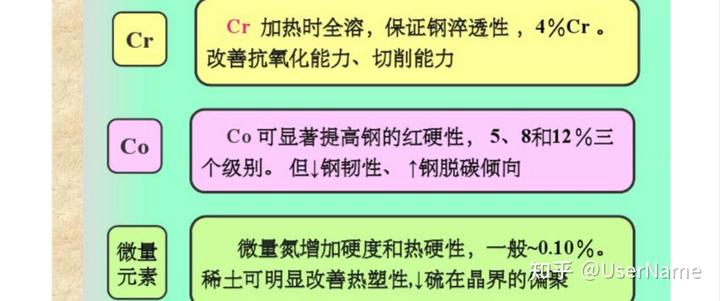
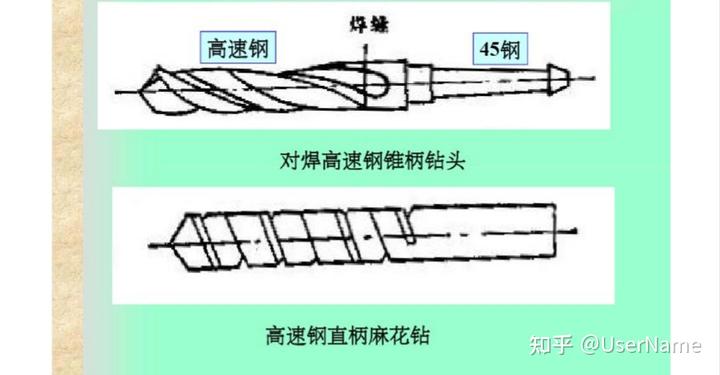
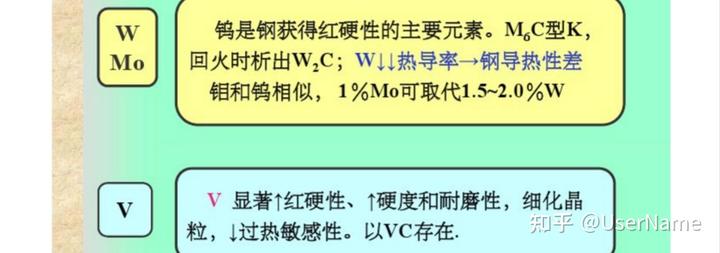
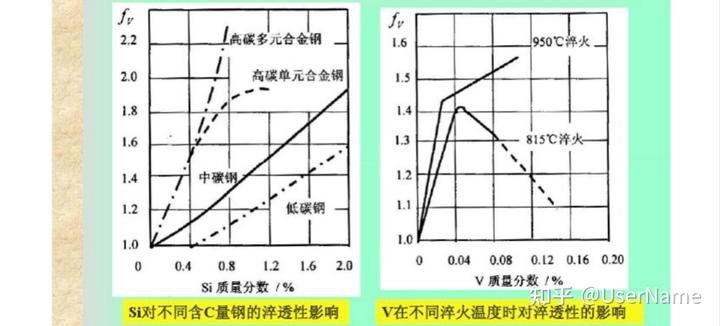
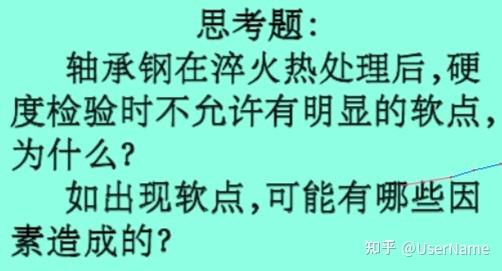
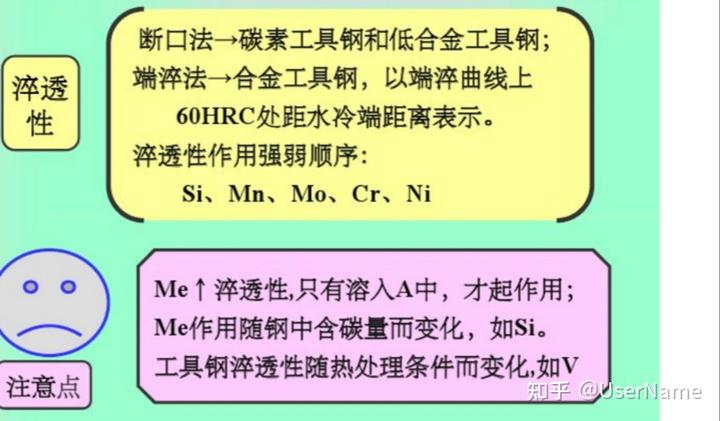
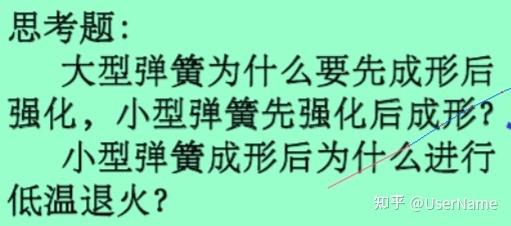
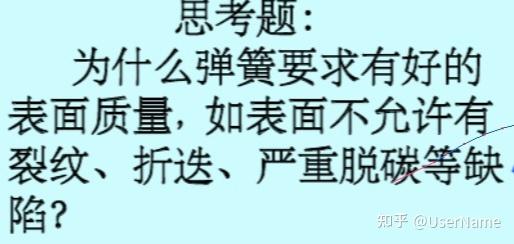
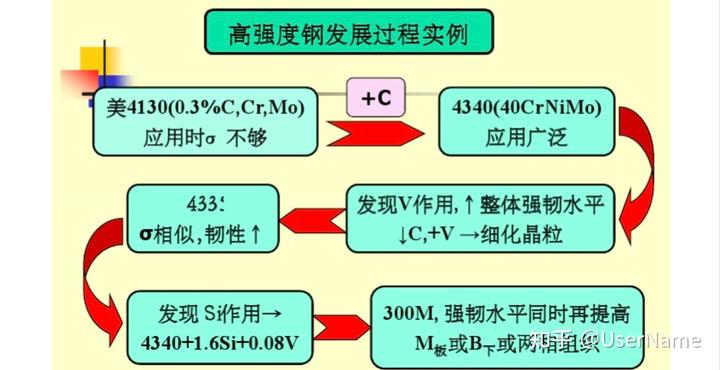
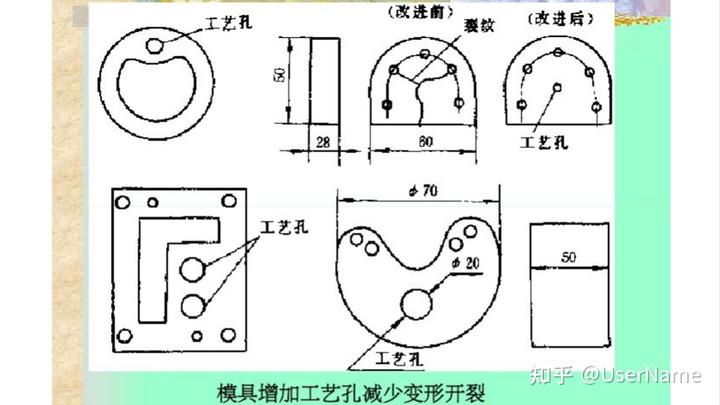
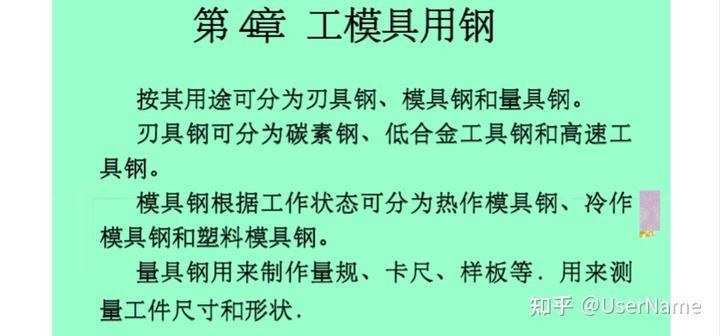
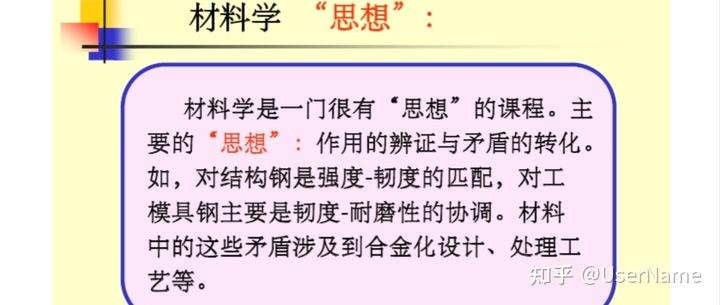
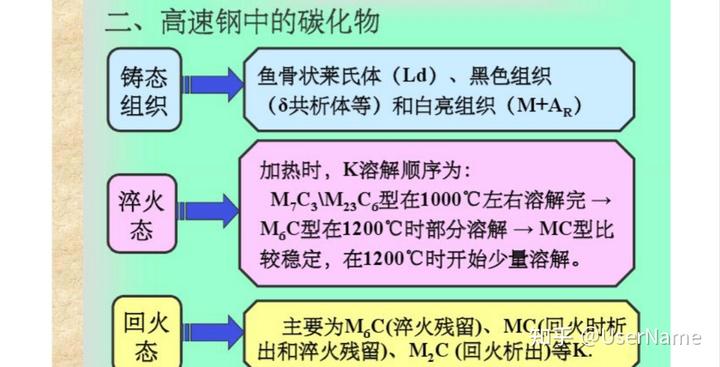

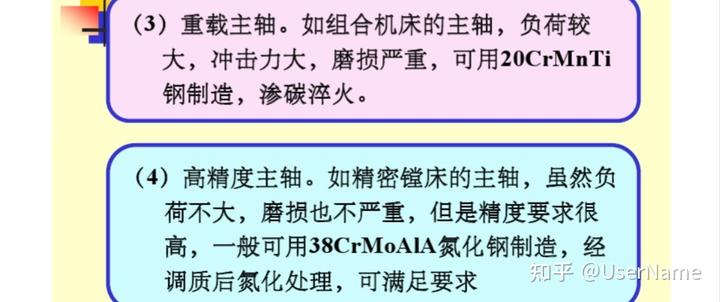
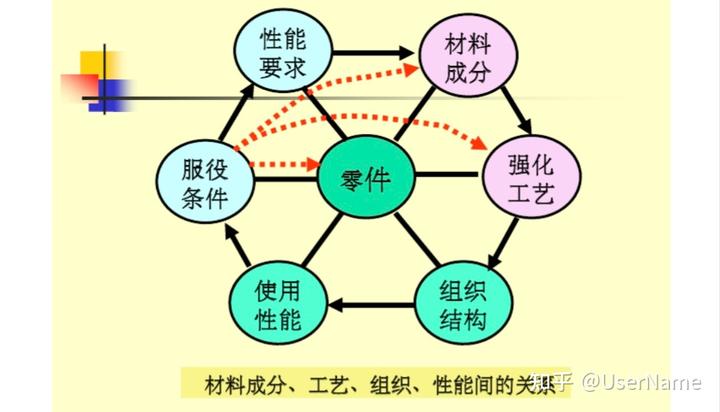
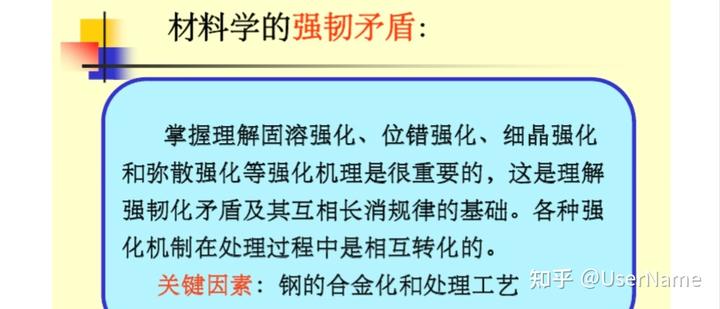
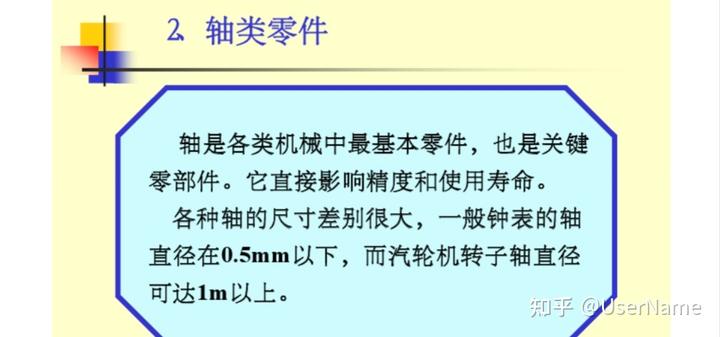
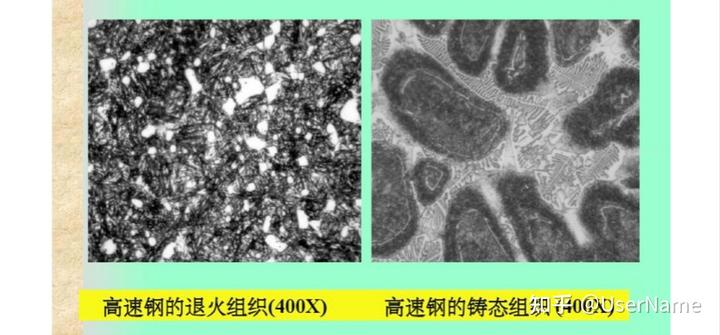
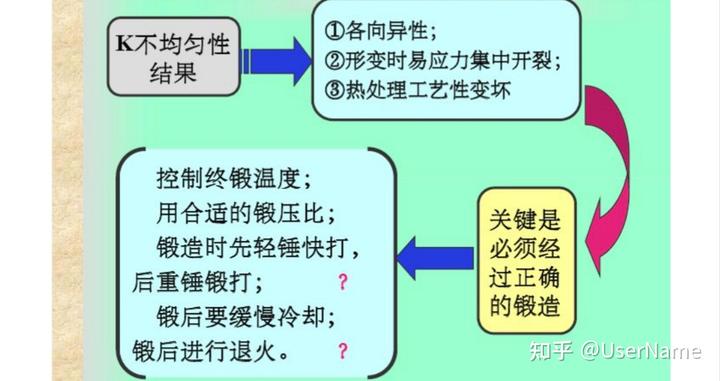
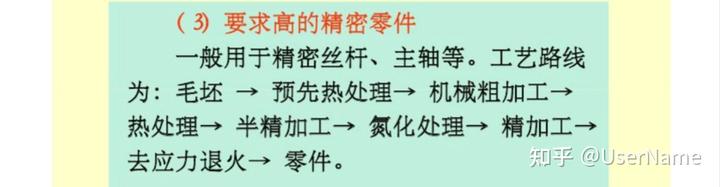
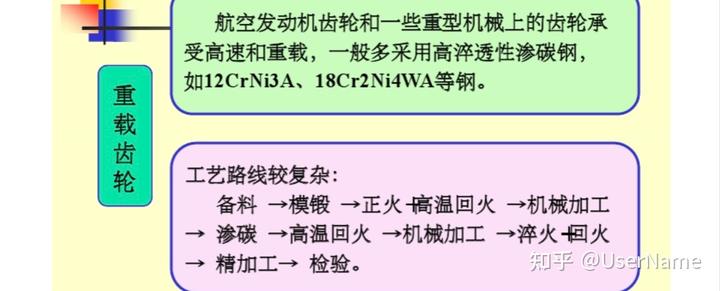
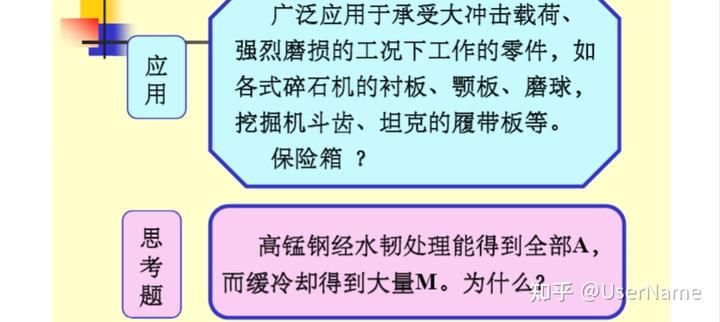
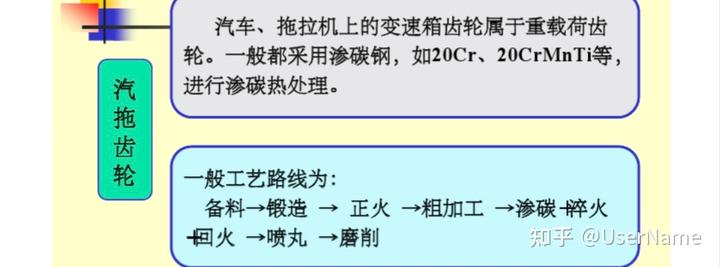
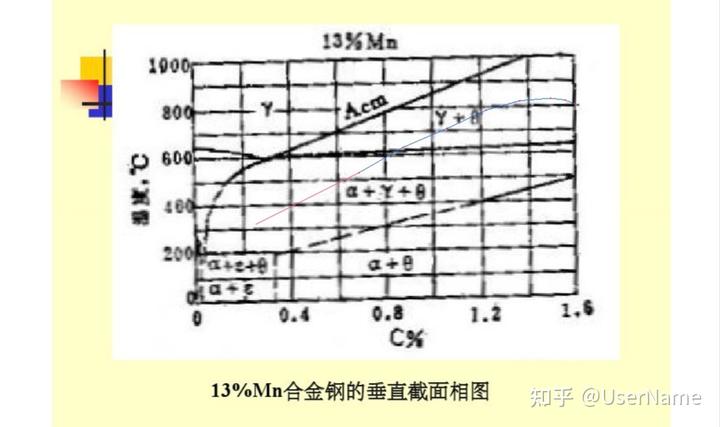
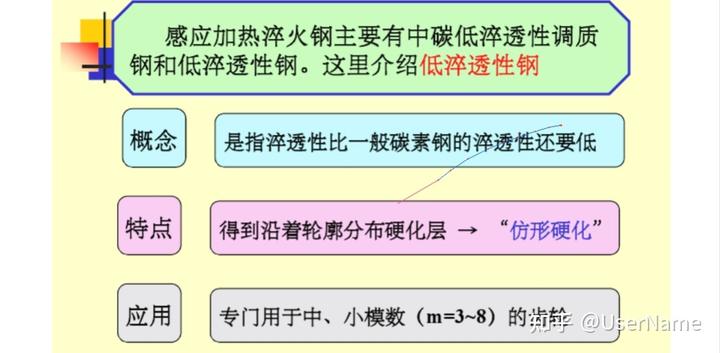
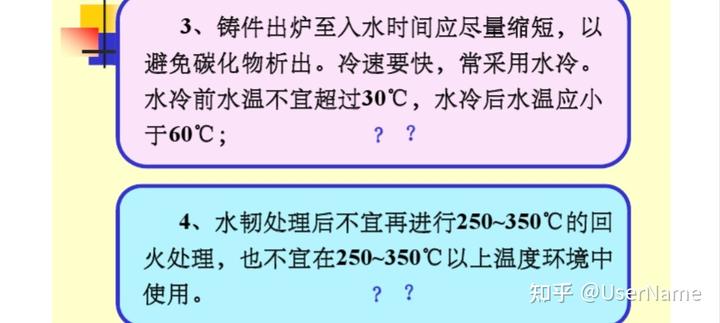
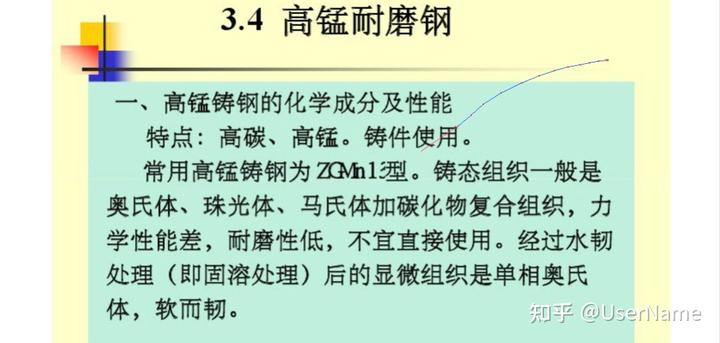
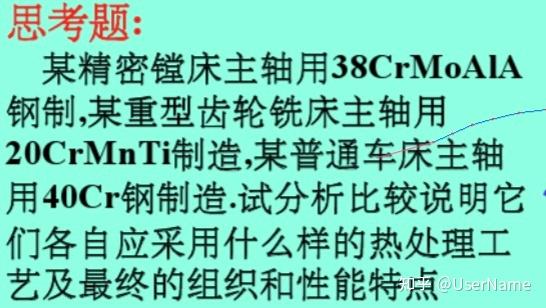
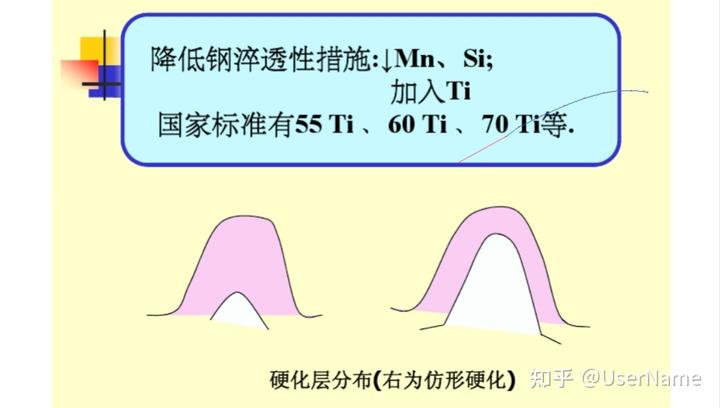
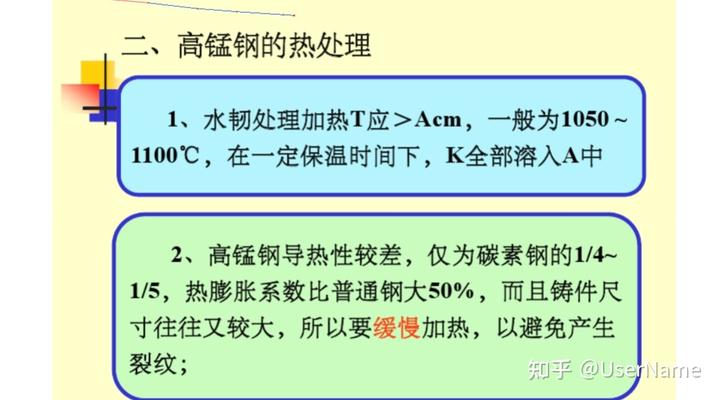
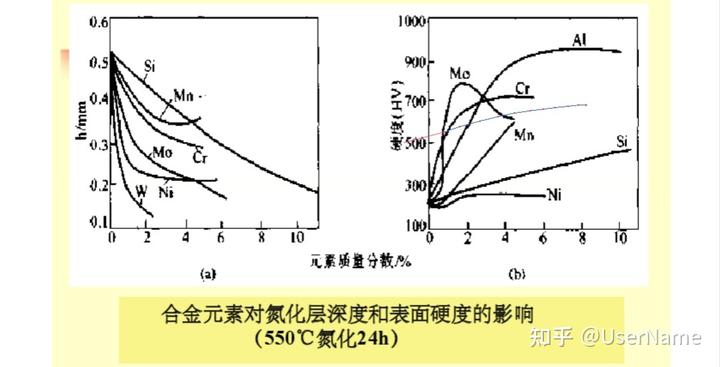
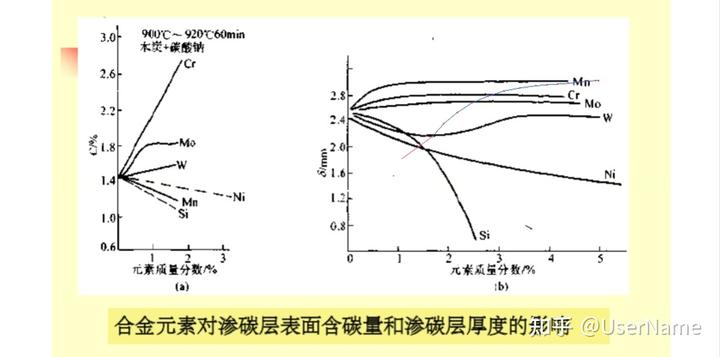
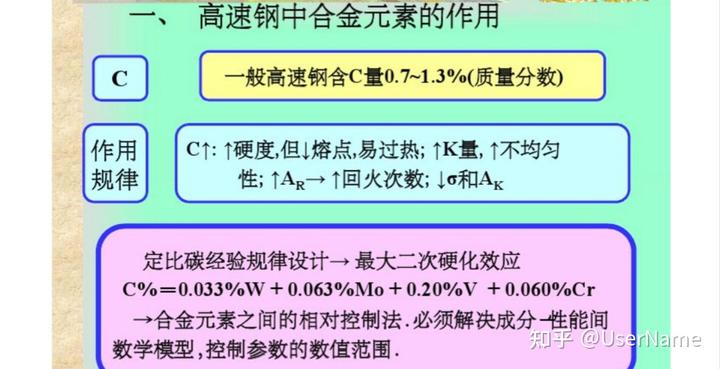
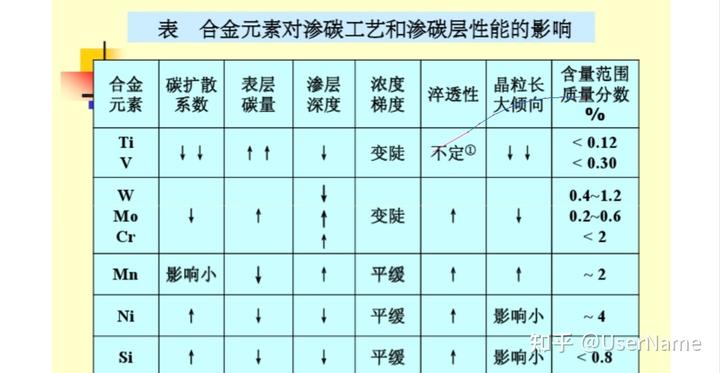
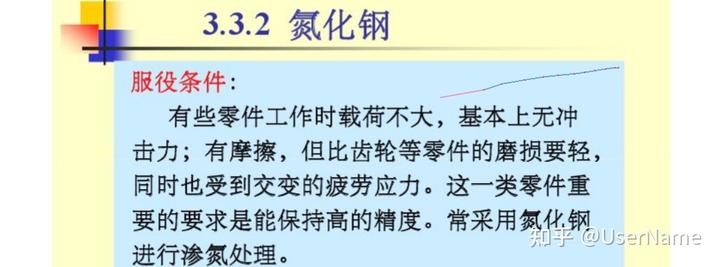
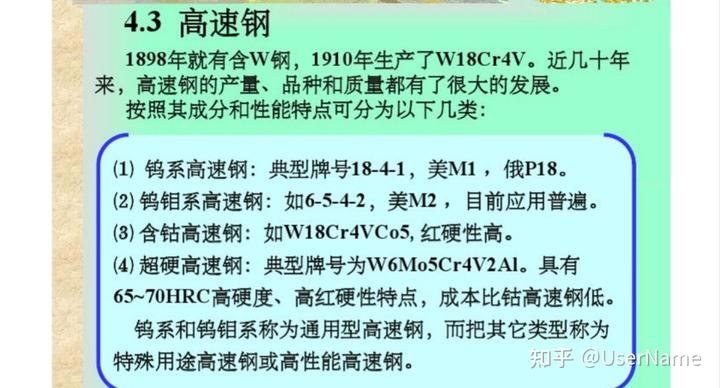
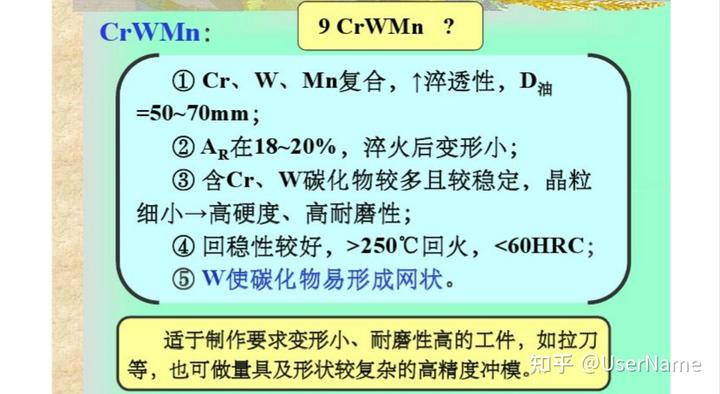
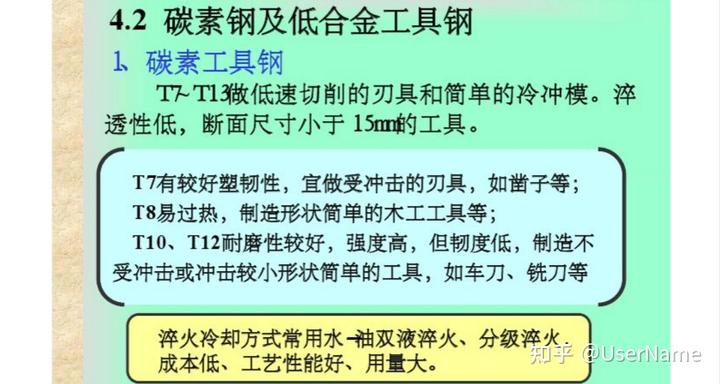
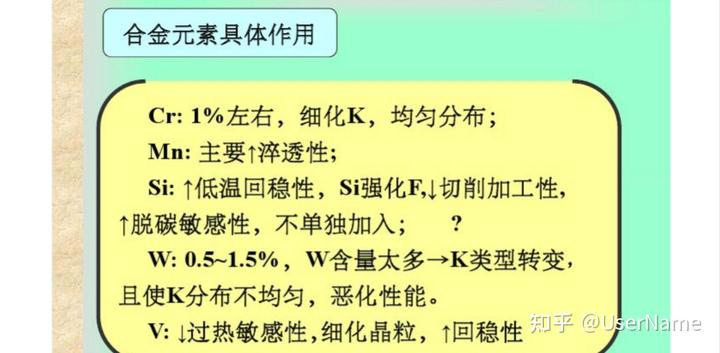
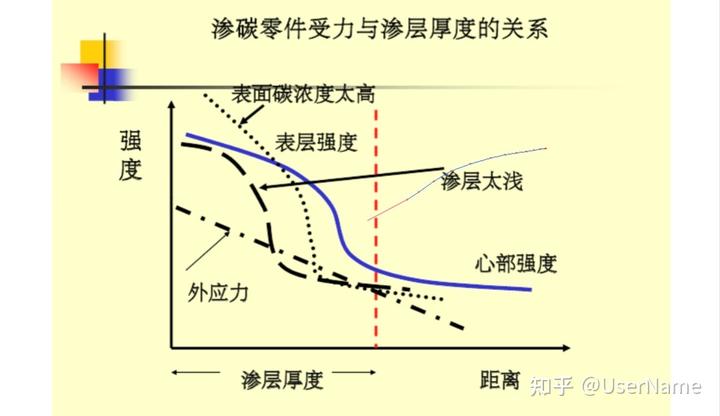
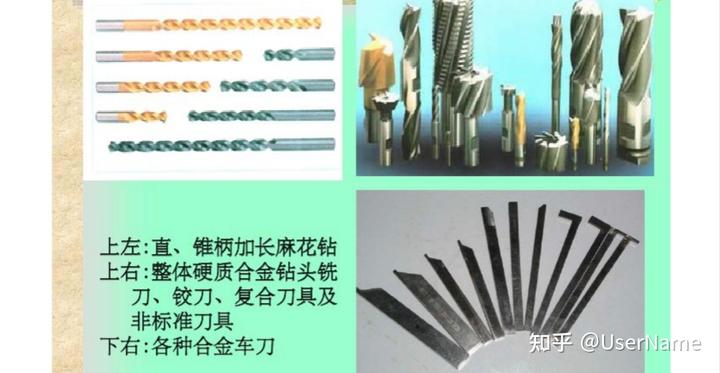
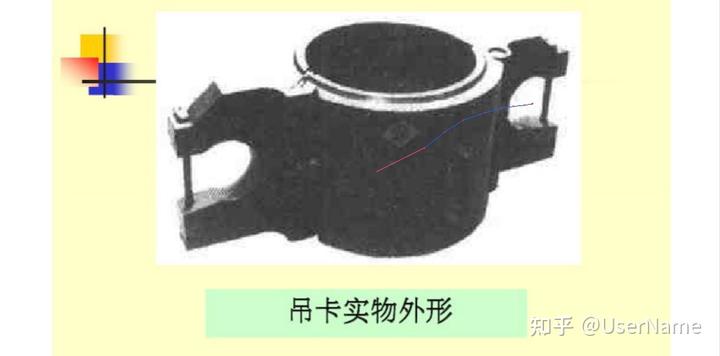
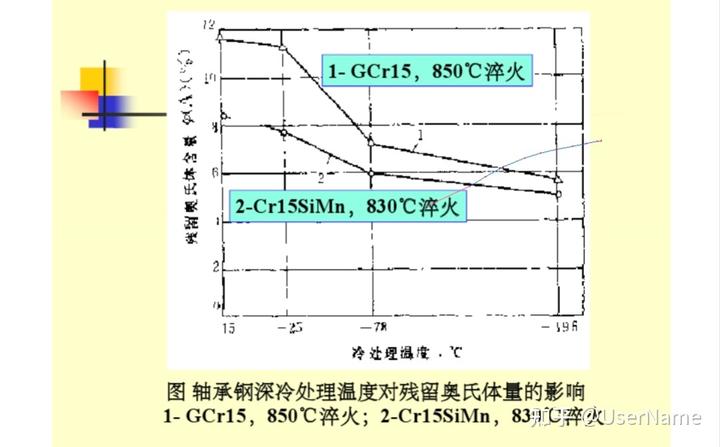
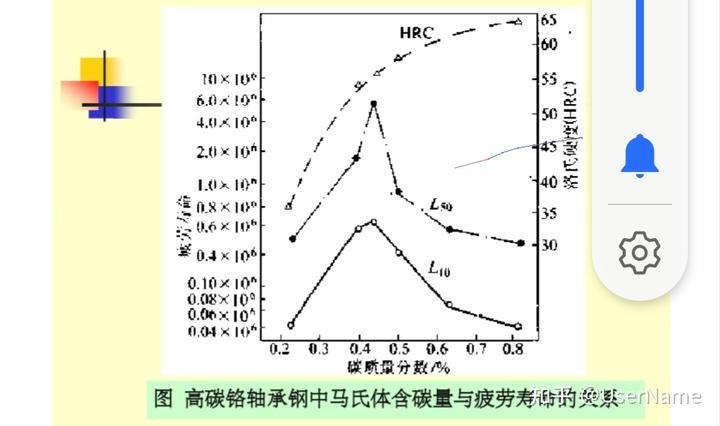
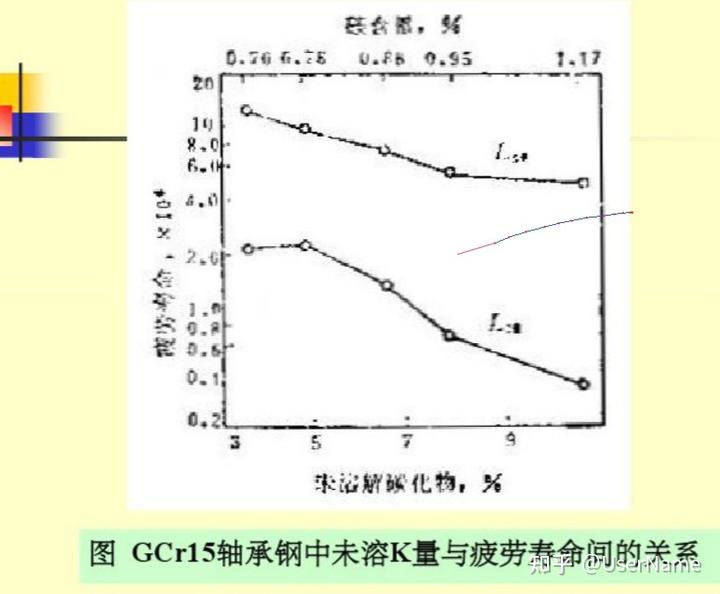
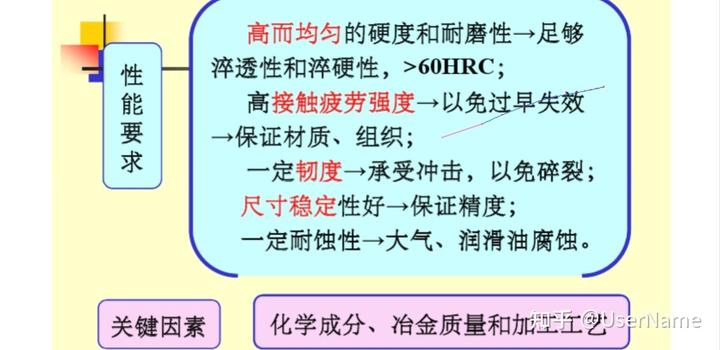
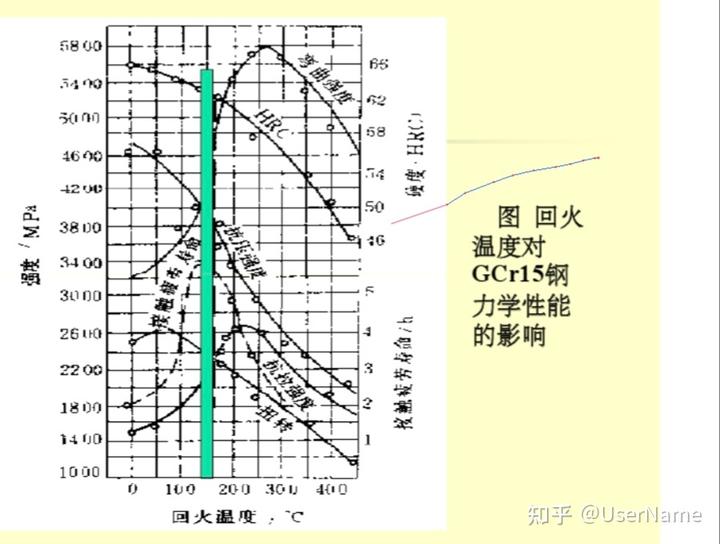
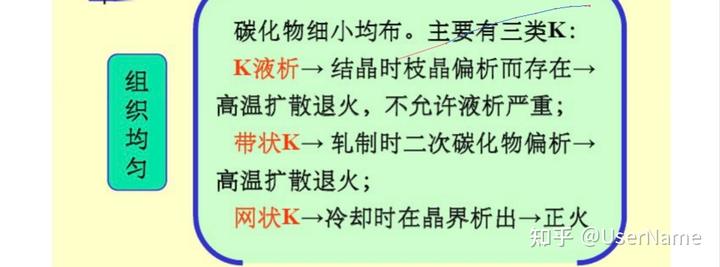
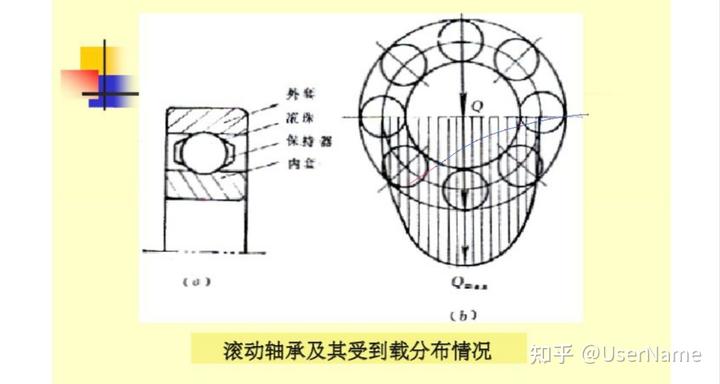
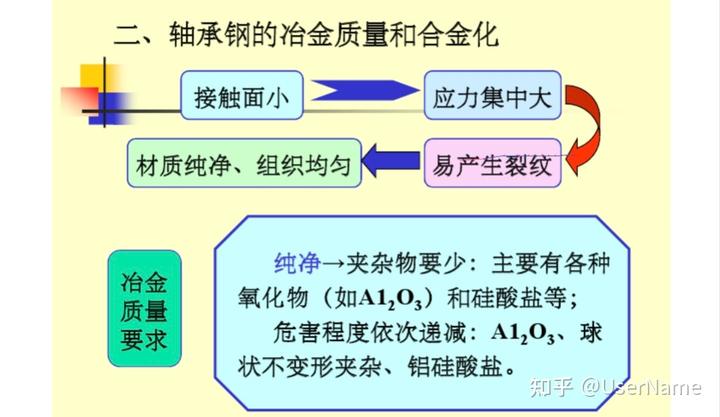
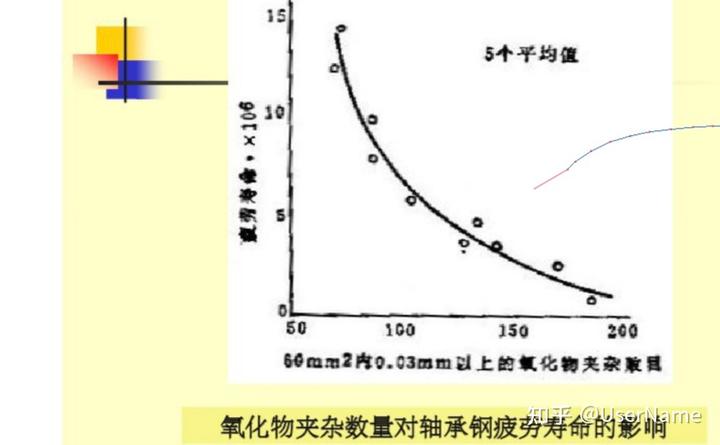
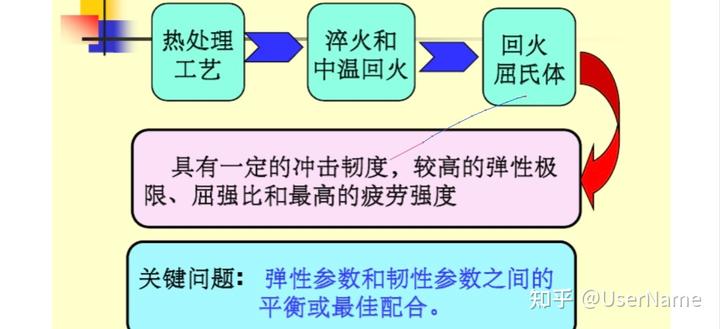
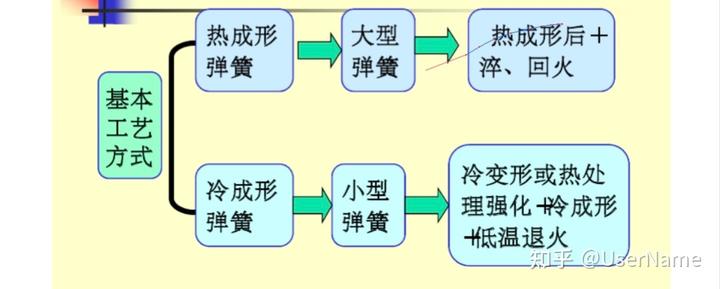
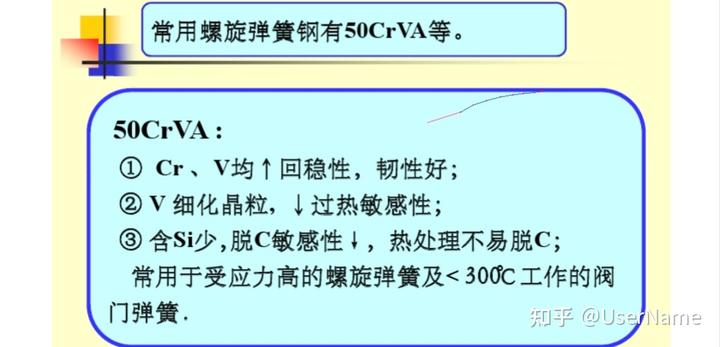
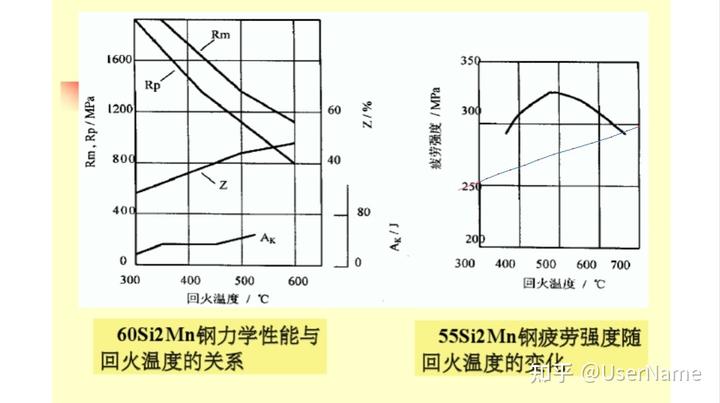
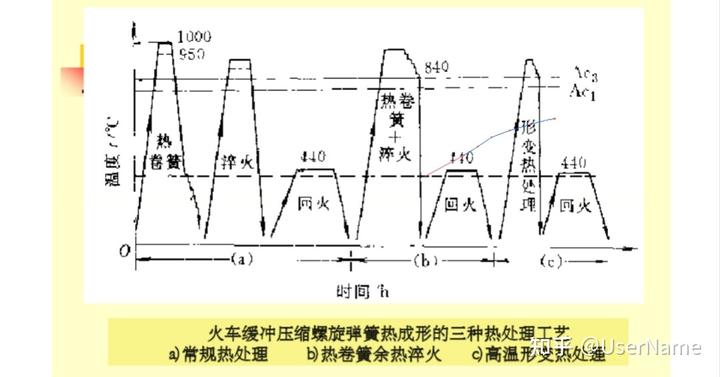
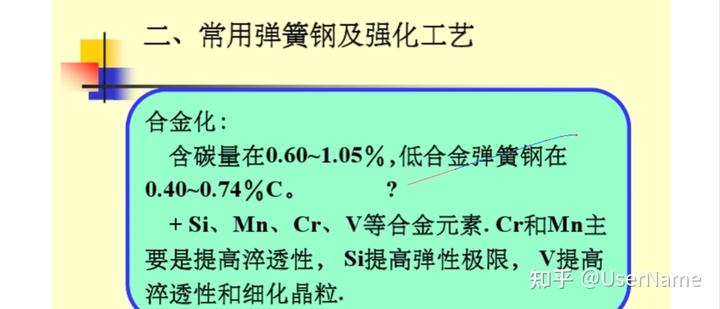
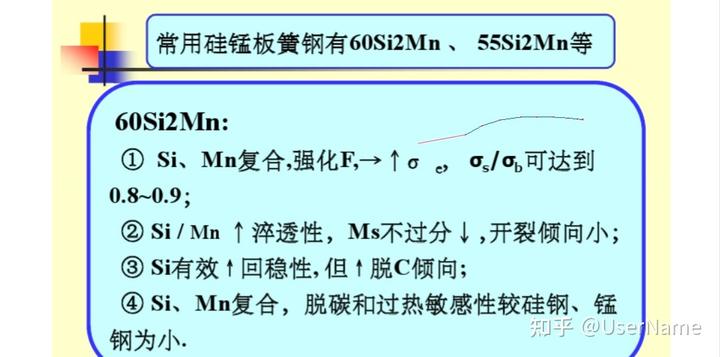
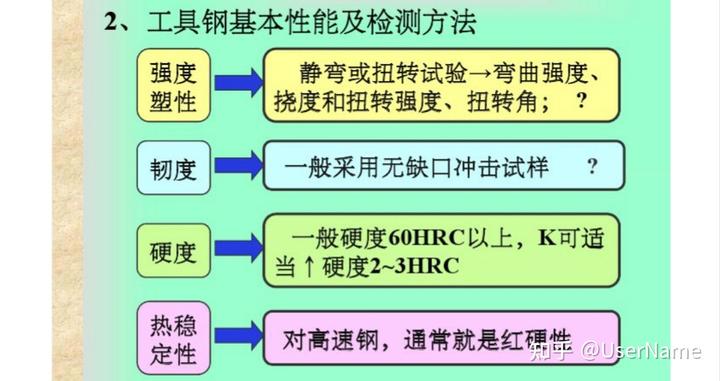
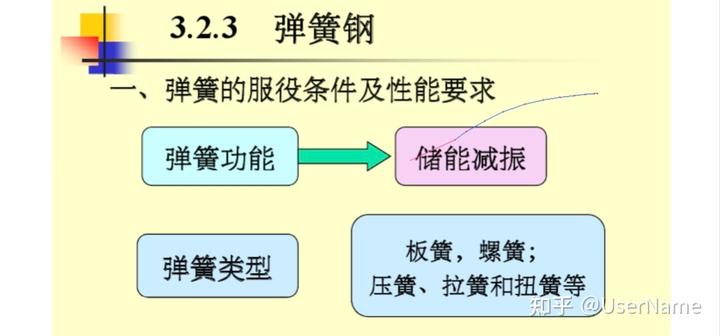
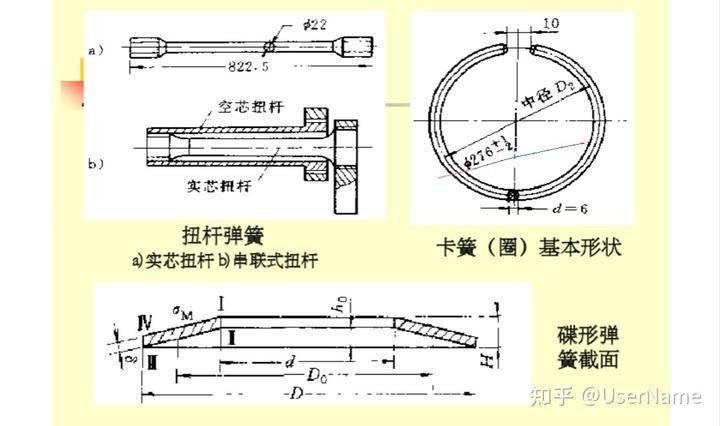
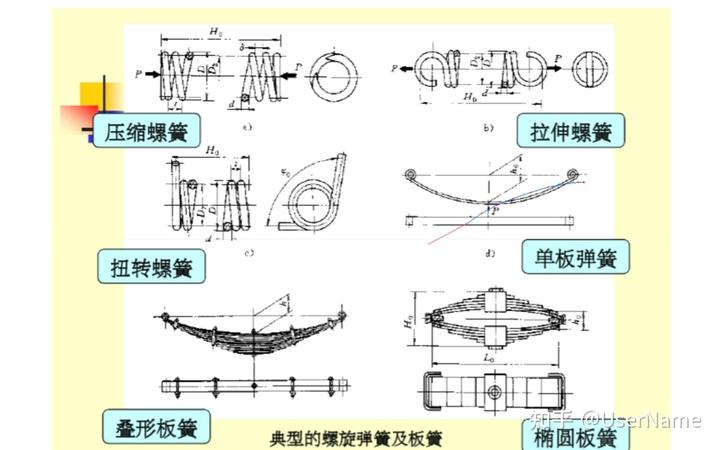
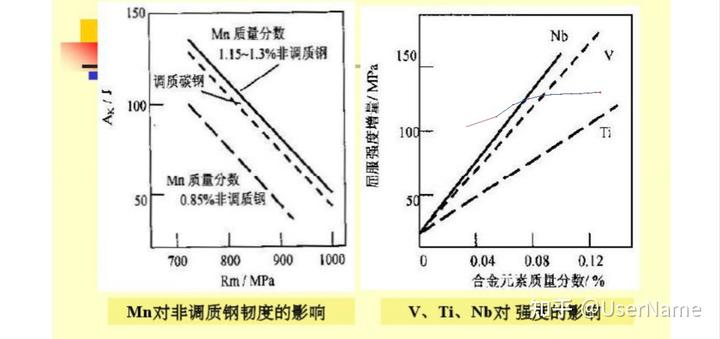
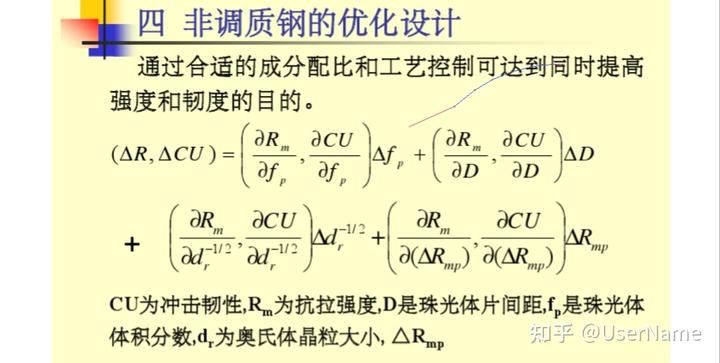
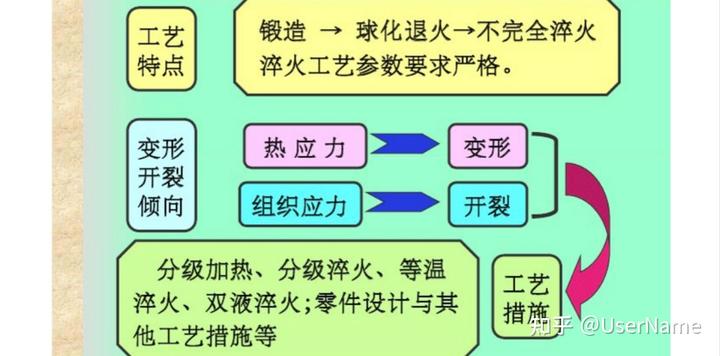
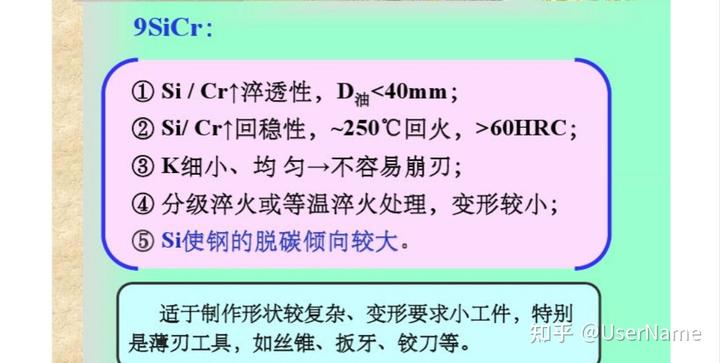
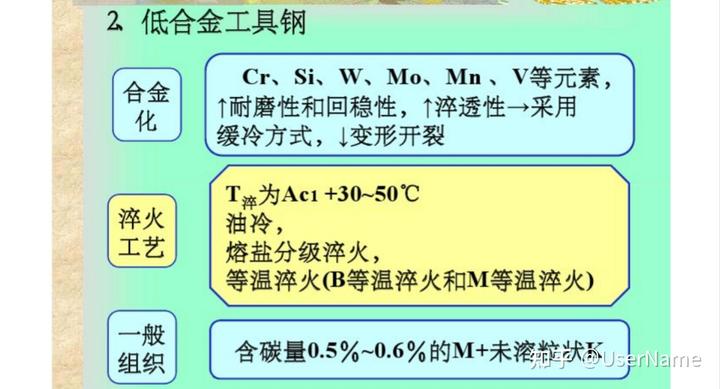
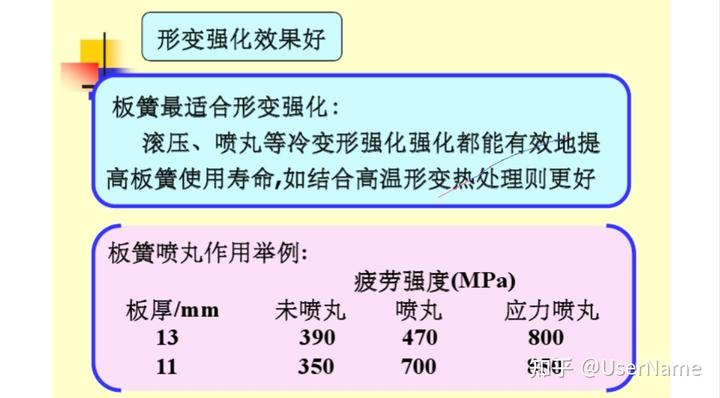
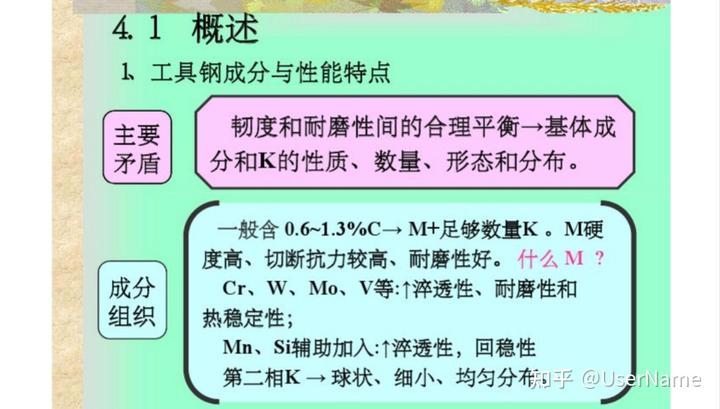
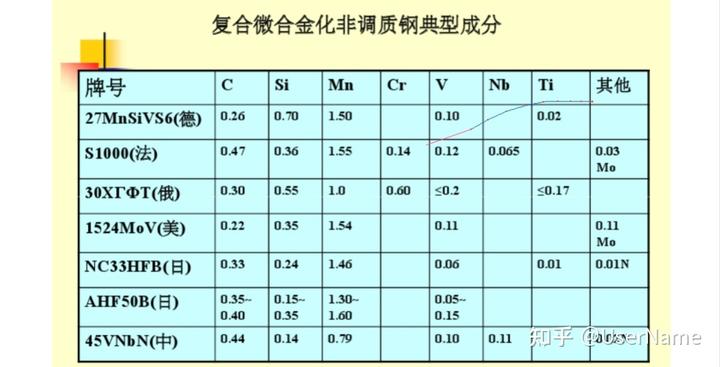
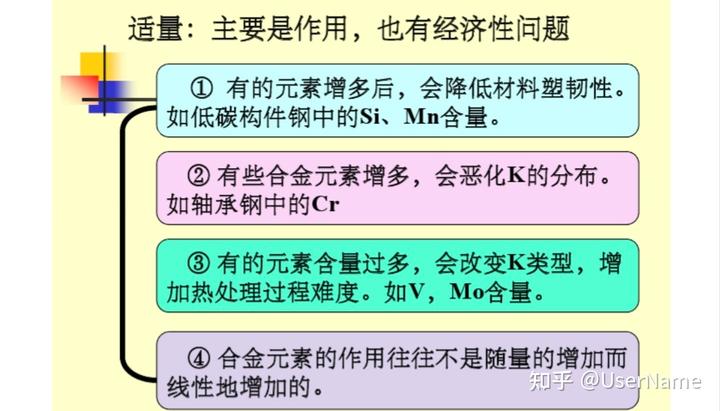
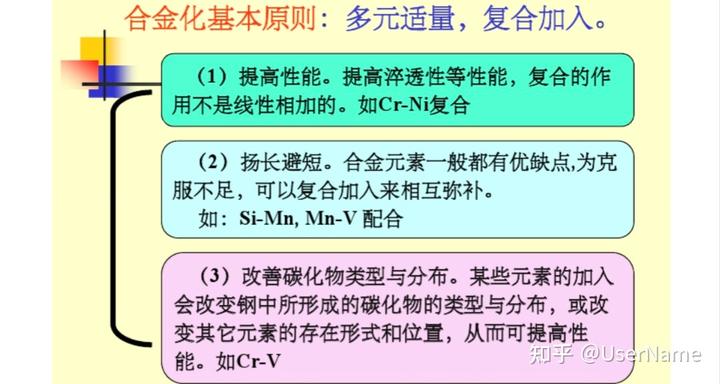
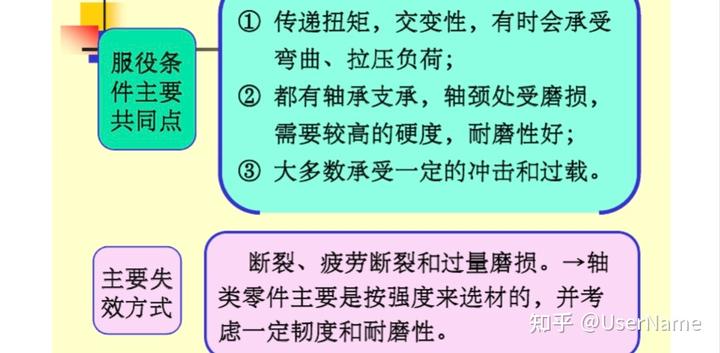
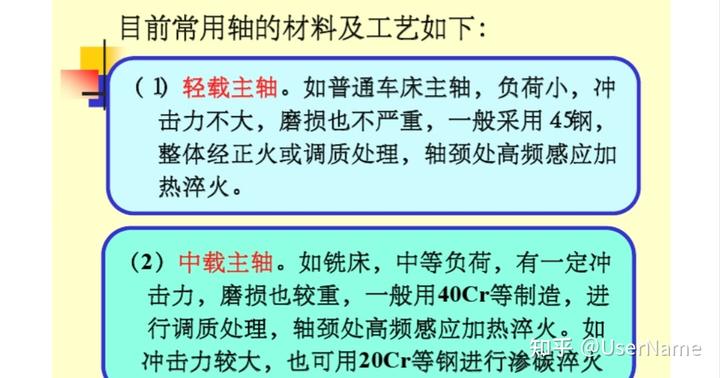
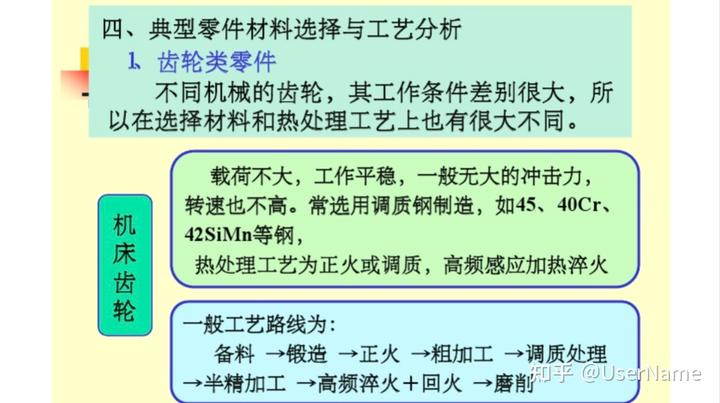
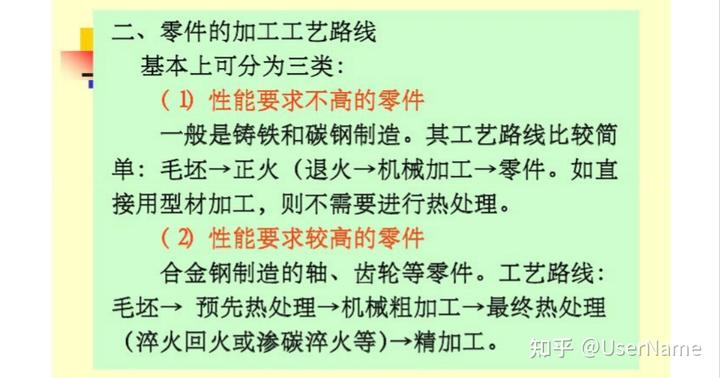
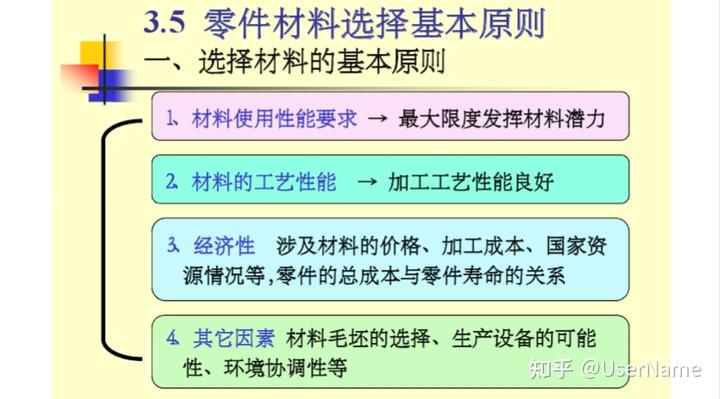
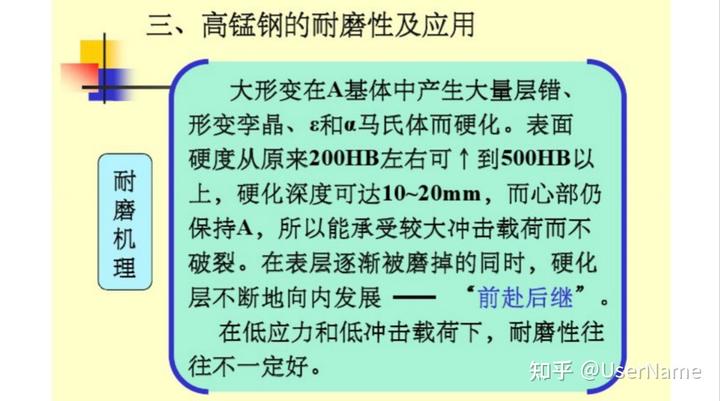
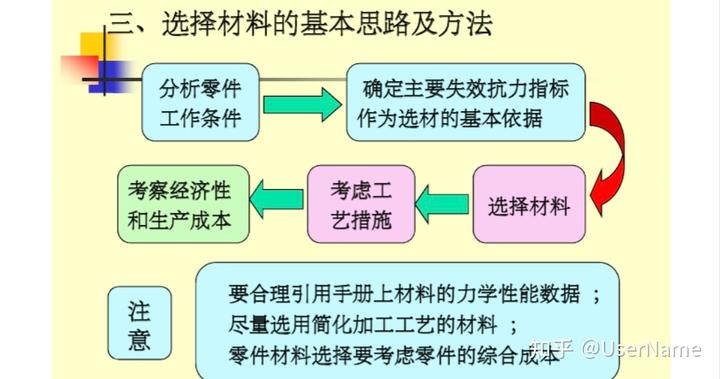
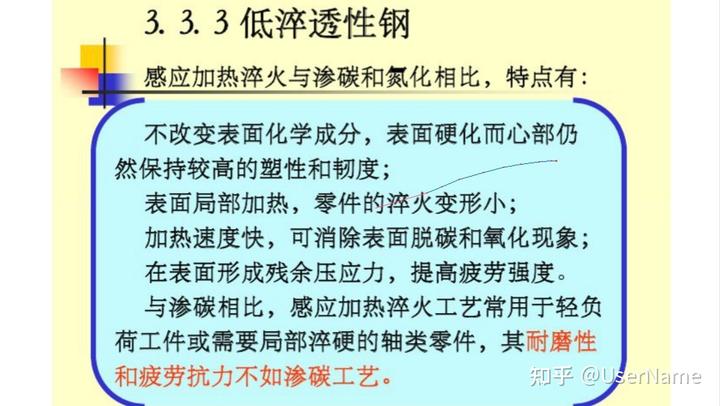
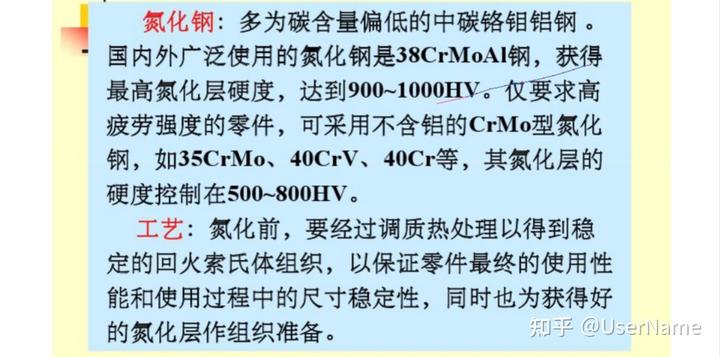

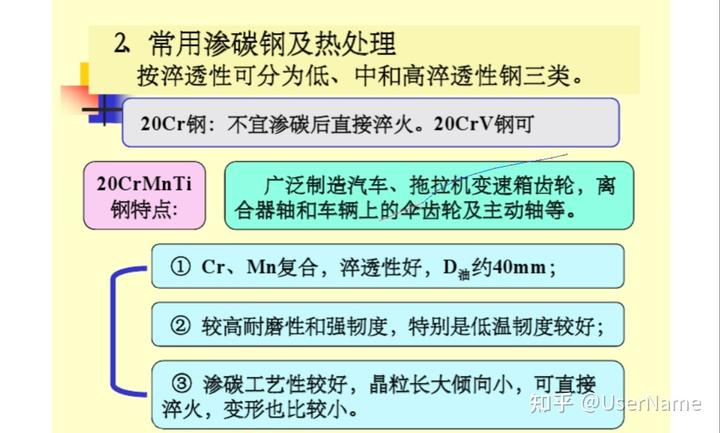
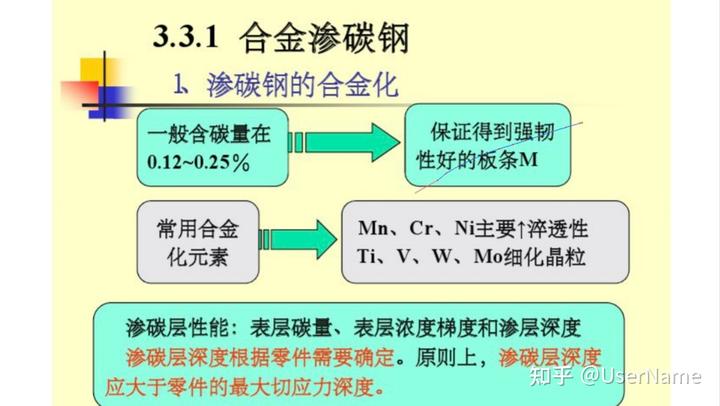
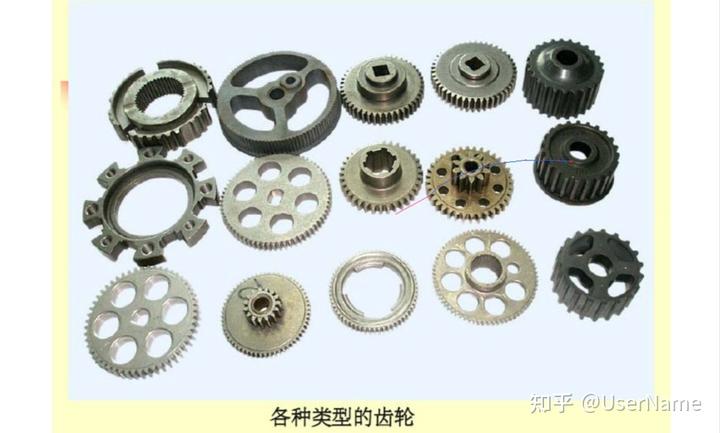
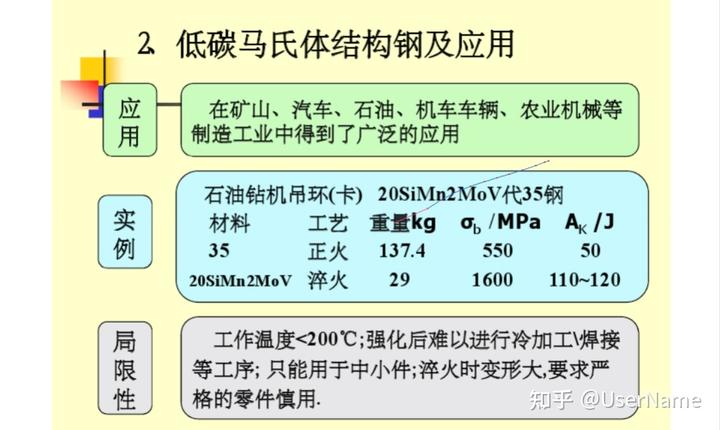
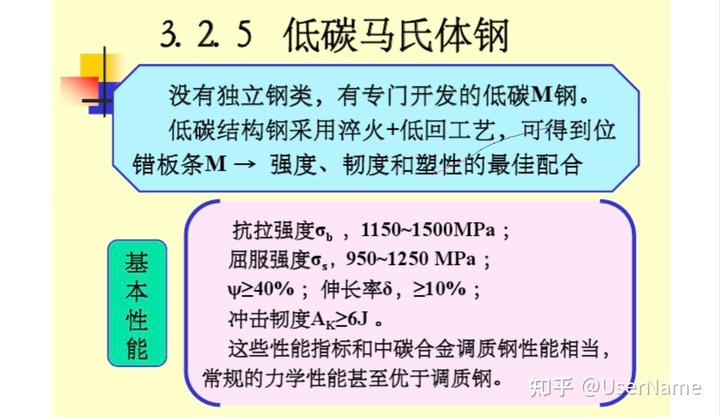
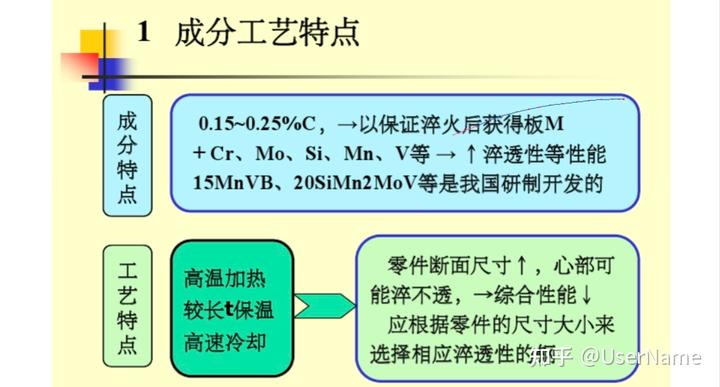
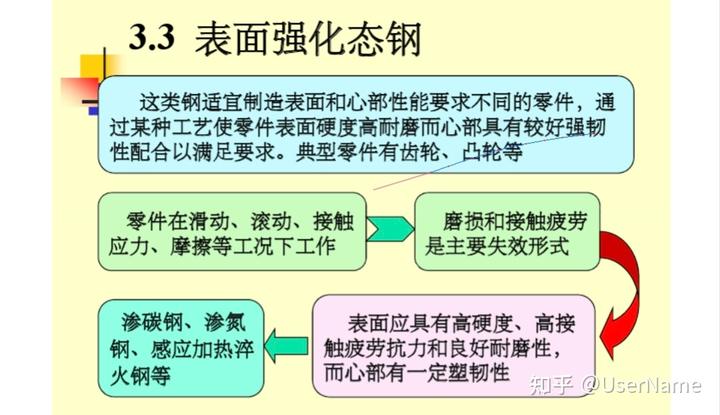
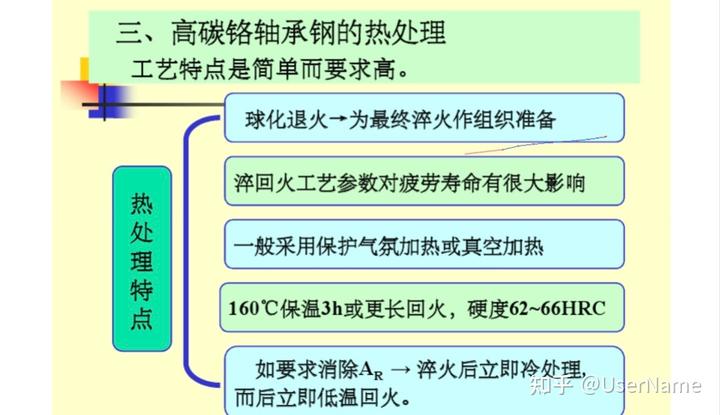
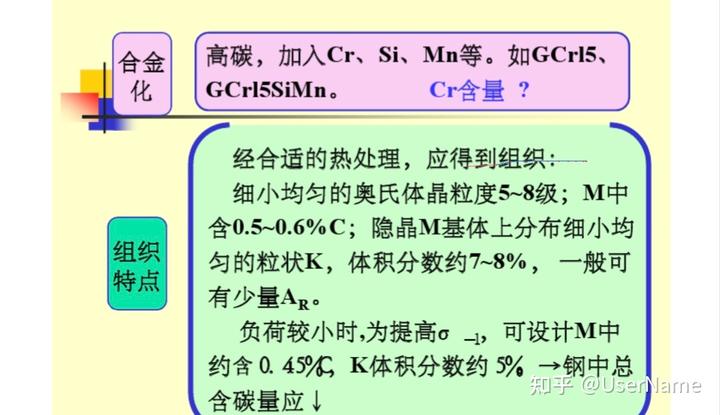
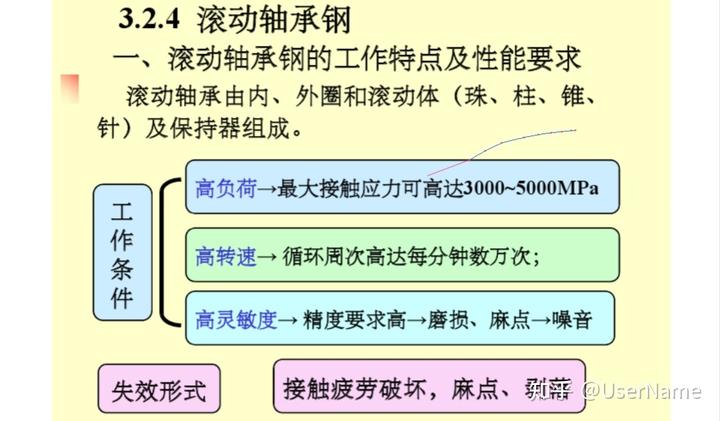
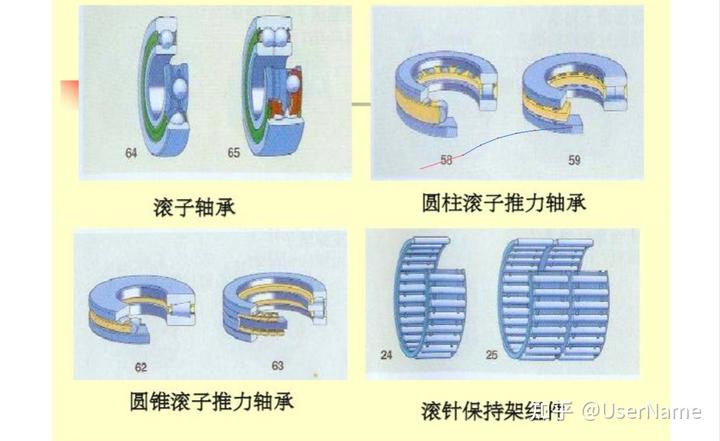
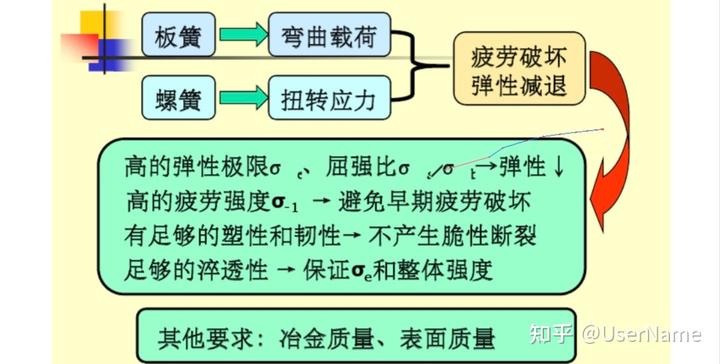
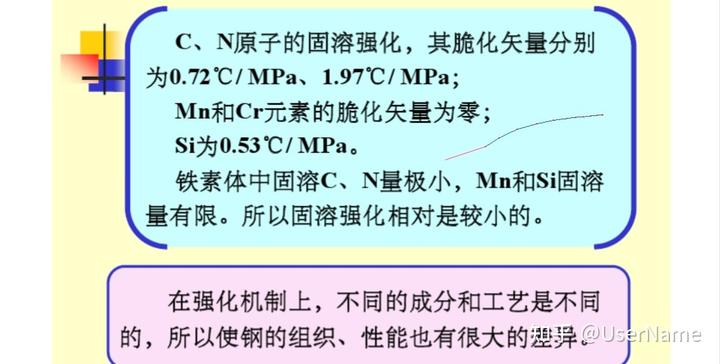
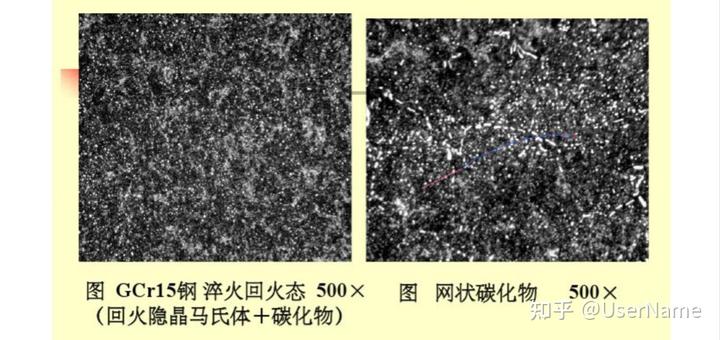
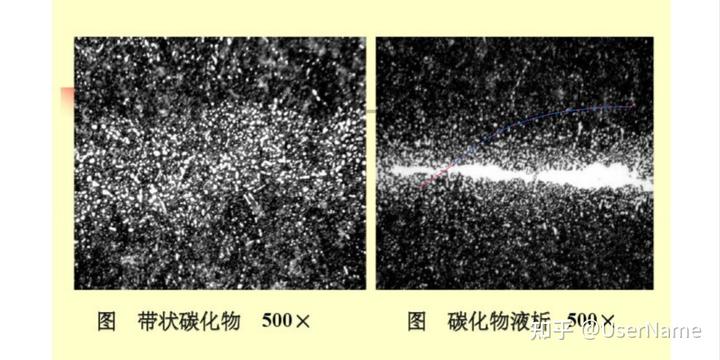
白口组织是由于在铸铁补焊时,碳、硅等促进石墨化元素大量烧损,且补焊区冷速快,在焊缝区石墨化过程来不及进行而产生的。白口铸铁硬而脆,切削加工性能很差。采用含碳、硅量高的铸铁焊接材料或镍基合金、铜镍合金、高钒钢等非铸铁焊接材料,或补焊时进行预热缓冷使石墨充分析出,或采用钎焊,可避免出现白口组织,。
3、铸铁壁厚对石墨化有什么影响?冷速越快,不利于铸铁的石墨化,这主要取决于浇注温度、铸型材料的导热能力及铸件壁厚等因素。冷速过快,第二阶段石墨化难以充分进行。4、石墨形态是铸铁性能特点的主要矛盾因素,试分别比较说明石墨形态对灰铸铁和球墨铸铁力学性能及热处理工艺的影响。墨的数量、大小和分布对铸铁的性能有显著影响。如片状石墨,数量越多对基体的削弱作用和应力集中程度越大。
石墨形状影响铸铁性能:片状、团絮状、球状。对于灰铸铁,热处理仅能改变基体组织,改变不了石墨形态,热处理不能明显改善灰铸铁的力学性能。
球墨铸铁是石墨呈球体的灰铸铁,简称球铁。由于球墨铸铁中的石墨呈球状,对基体的割裂作用大为减少,球铁比灰铸铁及可锻铸铁具有高得多的强度、塑性和韧性。
5、球墨铸铁的性能特点及用途是什么?
球墨铸铁。将灰口铸铁铁水经球化处理后获得,析出的石墨呈球状,简称球铁。比普通灰口铸铁有较高强度、较好韧性和塑性。用于制造内燃机、汽车零部件及农机具等.。
珠光体型球墨铸铁——柴油机的曲轴、连杆、齿轮;机床主轴、蜗轮、蜗杆;轧钢机的轧辊;水压机的工作缸、缸套、活塞等。铁素体型球墨铸铁一一
受压阀门、机器底座、汽车后桥壳等。
6、和刚相比,球墨铸铁的热处理原理有什么异同?
球墨铸铁的热处理主要有退火、正火、淬火加回火、等温淬火等。
7、HT200、HT350、KTH300-06、QT400、QT600各是什么铸铁?数字代表什么意义?各具有什么样的基体和石墨形态?说明他们的力学性能特点及用途。
(1)灰铸铁常用型号为HT100/HT150/HT200/HT250/HT300/HT350
球墨铸铁常用型号为
QT400-18/QT400-15/QT450-10/QT500-7/QT600-3/QT700-2/QT800-2/QT900-2
黑心可锻铸铁常用牌号为
KTH300-06/KTH350-10/KTZ450-06/KTZ550-04/KTZ650-02/KTZ700-02,其中KTH300-06适用于气密性零件,KTH380-08适用于水暖件,KTH350-10适用于阀门、汽车底盘。
(2)牌号中代号后面只有一组数字时,表示抗拉强度值:有两组数字时,第一组表示抗拉强度值,第二组表示延伸率值。两组数字中间用“一”隔开。抗拉强度随壁厚而变化,壁厚越大抗拉强度越小。3)①灰口铸铁:灰铸铁是指石墨呈片状分布的灰口铸铁。灰铸铁价格便宜,应用广泛,其产量约占铸铁总产量的80%以上
1.牌号:常用的牌号为HT100、HT150、HT200、...、HT350
HT—最低抗拉强度值
灰铸铁代号
2.组织
灰铸铁的组织是由液态铁水缓慢冷却时通过石墨化过程形成的,其基体组织有铁素体、珠光体和铁素体加珠光体三种。灰铸铁的显微组织如下图所示。为提高灰铸铁的性能,常对灰铸铁进行孕育处理,以细化片状石墨,常用的孕育剂有硅铁和硅钙合金。经孕育处理的灰铸铁称为孕育铸铁。
3.热处理
热处理只能改变铸铁的基体组织,但不能改变石墨的形态和分布。由于石墨片对基体的连续性的破坏严重,产生应力集中大,因而热处理对灰铸铁的强化效果不大,其基体强度利用率只有30%-50%。灰铸铁常用的热处理有:消除内应力退火、消除白口组织退火和表面淬火。4.用途
灰铸铁主要用于制造承受压力和振动的零部件,如机床床身、各种箱体、壳体、泵体、缸体等。
②球墨铸铁:球墨铸铁是指石墨呈球形的灰口铸铁,是由液态铁水经石墨化后得到的。与灰铸铁相比,它的碳当量较高,一般为过共晶成分,这有利于石墨球化。
1.牌号:QT400-17、QT420-10、QT500-05、QT600-02、QT700-02、QT800-02、QT1
200-01
QT××最低延伸率
×××—最低抗拉强度值
球墨铸铁代号
2.组织
球墨铸铁是由基体+球状石墨组成,铸态下的基体组织有铁素体、铁素体加珠光体和珠光体3种。球状石墨是液态铁水经球化处理得到的。加入到铁水中能使石墨结晶成球形的物质称为球化剂,常用的球化剂为镁、稀土和稀土镁。镁是阻碍石墨化的元素,为了避免白口,并使石墨细小且分布均匀,在球化处理的同时还必须进行孕育处理,常用的孕育剂为硅铁和硅钙合金。
3.性能
由于球状石墨圆整程度高,对基体的割裂作用和产生的应力集中更小,基体强度利用率可达70%-90%。接近于碳钢,塑性和韧性比灰铸铁和可锻铸铁都高。
4.热处理
由于球状石墨危害程度小,因而可以对球墨铸铁进行各种热处理强化。球墨铸铁的热处理主要有退火、正火、淬火加回火、等温淬火等。
5.用途
球墨铸铁在汽车、机车、机床、矿山机械、动力机械、工程机械、冶金机械、机械工具、管道等方面得到广泛应用,可代替部分碳钢制造受力复杂,强度、韧性和耐磨性要求高的零件③可锻铸铁:可锻铸铁是由白口铸铁经石墨化退火后获得的,其石墨呈团絮状。可锻铸铁中要求碳、硅含量不能太高,以保证浇注后获得白口组织,但又不能太低,否则将延长石墨化退火周期。
1.牌号:KTHKTBKTZ分别表示黑心、白心、珠光体可锻铸铁代号
KTH XXX-XX××最低延伸率
×××最低抗拉强度值
可锻铸铁代号
KTB XXX-XX
KTZ XX X-XX
2.组织
可锻铸铁的组织与第二阶段石墨化退火的程度有关。当第一阶段石墨化充分进行后(组织为奥氏体+团絮状石墨),在共析温度附近长时间保温,使第二阶段石墨化也充分进行,则得到铁素体+团絮状石墨组织,由于表层脱碳而使心部的石墨多于表层,断口心部呈灰黑色表层呈灰白色,故称为黑心可锻铸铁。若通过共析转变区时,冷却较快,第二阶段石墨化未能进行,使奥氏体转变为珠光体,得到珠光体+团絮状石墨的组织,称为珠光体可锻铸铁。3.性能
由于可锻铸铁中的团状石墨对基体的割裂程度及引起的应力集中比灰铸铁要小,因而其强度、塑性和韧性均比灰铸铁高,接近于铸钢,但不能锻造,其强度利用率达到基体的
40%-70%。
4.用途
可锻铸铁常用于制造形状复杂且承受振动载荷的薄壁小型件,如汽车、拖拉机的前后轮壳、
管接头、低压阀门等。这些零件如用铸钢制造则铸造性能差,用灰铸铁则韧性等性能达不到要求。
8、如何理解铸铁在一般的热处理过程中,石墨参与相变,但是热处理并不能改变石墨的形态和分布。
铸铁的热处理目的在于两方面:一是改变基体组织,改善铸铁性能,二是消除铸件应力。值得注意的是:铸件的热处理不能改变铸件原来的石墨形态及分布,即原来是片状或球状的石墨热处理后仍为片状或球状,同时它的尺寸不会变化,分布状况不会变化。
铸铁件热处理只能改变基体组织,不能改变石墨的形态及分布,机械性能的变化是基体组织的变化所致。普通灰口铸铁(包括孕育铸铁)石墨片对机械性能(强度、延性)影响很大,灰口铸铁经热处理改善机械性能不显着。还需要注意的是铸铁的导热性较钢差,石墨的存在导致缺口敏感性较钢高,因此铸铁热处理中冷却速度(尤其淬火)要严格控制。
9、某厂生产球墨铸铁曲拐。经浇注后,表面常出现“白口”,为什么?为消除白口,并希望得到珠光体基体组织,应采用什么样的热处理工艺?
铸件冷却时,表层及薄截面处,往往产生白口。白口组织硬而脆、加工性能差、易剥落。因此必须采用退火(或正火)的方法消除白口组织。退火工艺为:加热到 550-950℃保温2~5 h,随后炉冷到 500—550℃再出炉空冷。在高温保温期间,游高渗碳体和共晶渗碳体分解为石墨和A,在随后护冷过程中二次渗碳体和共析渗碳体也分解,发生石墨化过程。由于渗碳体的分解,导致硬度下降,从而提高了切削加工性。
10、解释机床底座常用灰铸铁制造的原因。
工艺问题,这些零件形状复杂,除铸造用其他方法难以得到毛坯,而灰口铸铁具有十分优
其一,价格便宜,这些产品的重量很重.其二,减震,灰铸铁中含碳量比较高,石墨在铸铁中的吸振能力或阻止振动传播的作用,使灰铸铁有优良的减振性,钢材没有这个特性.其三,减磨.灰铸铁中石墨有储油的作用,在有润滑的条件下,加上石墨本身是良好的润滑剂和冷却剂,所以灰铸铁有很好的减磨作用,从而灰铸铁比结构钢耐。其四,对缺口敏感性很低,灰铸铁本身的显微结构石墨是呈现细片状结构,千疮百孔的,再加几个缺口不要紧.钢要是有缺口,十分容易在缺口处疲劳破坏。
秀的铸造性能.而钢的铸造性很差.
11、影响铸态组织的主要因素是什么?
铸铁的组织取决于石墨化进行的程度,为了获得所需要的组织,关键在于控制石墨化进行的程度。实践表明,铸铁的化学成分和结晶时的冷却速度是主要因素。
第9章 铝合金
1、试述铝合金的合金化原则。为什么以硅、铜、镁、锰、锌等元素为主加元素,而以钛、硼、稀土等作为辅加元素。
铝具有一系列比其他有色金属、钢铁和塑性等更优良的性能,如密度小,仅为2.7,约为钢或铜的 1/3:优良的导电性、导热性;良好的耐蚀性;优良的塑性和加工性能等。但纯铝的力学性能不高,不适合作为承受较大载何的结构零件。为了提高铝的力学性能,在纯铝中加入某些合金元素,制成铝合金。铝合金仍保持纯铝的密度小和耐蚀性好的特点,且力学性能比纯铝高得多。经热处理后的铝合金的力学性能可以和钢铁材料相媲美。 铝合金中常加入的元素为硅、铜、镁、锰、锌元素等。这些合金元素在固态铝中的溶解度一般都是有限的。
2、铝合金热处理强化和钢淬火强化的主要区别是什么?
铝合金的热处理强化不发生同素异构转变。铝合金的淬火处理称为固溶处理,由于硬脆的第二相消失,所以塑性有所提高。过饱和的a固溶体虽有强化作用,但是单相的固溶强化作用是有限的,所以铝合金固溶处理强度、硬度提高并不明显,而塑性却有明显提高。铝合金经固溶处理后,获得过饱和固溶体。在随后的室温放置或低温加热保温时,第二相从过饱和固溶体中析出,引起温度、硬度以及物理和化学性能的显著变化,这一过程称为时效。铝合金的热处理强化实际上包括了固溶处理与时效处理两部分。
3、以Al-Cu合金为例,简要说明铝合金时效的基本过程。
①形成溶质原子偏聚区-G·P(1)区。在新淬火状态的过饱和固溶体中,铜原子在铝晶格中的分布是任意的、无序的。时效初期,即时效温度低或时效时间短时,铜原子在铝基体上的某些晶面上聚集,形成溶质原子偏聚区,称G·P(I)区。G·P(I)区与基体a保持共格关系,这些聚合体构成了提高抗变形的共格应变区,故使合金的强度、硬度升高。②G·P区有序化一形成G·P(Ⅱ)区。随着时效温度升高或时效时间延长,铜原子继续偏聚并发生有序化,即形成G·P(Ⅱ)区。它与基体a仍保持共格关系,但尺寸较G·P(I)区大。它可视为中间过渡相,常用0”表示。它比G·P(I)区周围的畸变更大,对位错运动的阻碍进一步增大,因此时效强化作用更大,0”相析出阶段为合金达到最大强化的阶段。③形成过渡相0′。随着时效过程的进一步发展,铜原子在G·P(Ⅱ)区继续偏聚,当铜原子与铝原子比为1:2时,形成过渡相0。由于0′的点阵常数发生较大的变化,故当其形成时与基体共格关系开始破坏,即由完全共格变为局部共格,因此0'相周围基体的共格畸变减弱,对位错运动的阻碍作用亦减小,表现在合金性能上硬度开始下降。由此可见,共格畸变的存在是造成合金时效强化的重要因素。④形成稳定的0相。过渡相从铝基固溶体中完全脱溶,形成与基体有明显界面的独立的稳定相A12Cu,称为0相此时0相与基体的共格关系完全破坏,并有自己独立的晶格,其畸变也随之消失,并随时效温度的提高或时间的延长,0相的质点聚集长大,合金的强度、硬度进一步下降,合金就软化并称为“过时效”。0相聚集长大而变得粗大。
4、铝合金的成分设计要满足哪些条件才能有时效强化?
一种合金能否通过时效强化,首先取决于组成合金的元素能否溶解于固溶体以及固溶度随温度变化的程度。如硅、锰在铝中的固溶度比较小,且随温度变化不大,而镁、锌虽然在铝基固溶体中有较大的固溶度,但它们与铝形成的化合物的结构与基体差异不大,强化效果甚微。因此,二元铝一硅、铝一锰、铝一镁、铝一锌通常都不采用时效强化处理。而有些二元合金,如铝一铜合金,及三元合金或多元合金,如铝一镁-硅、铝-铜一镁-硅合金等,它们在热处理过程中有溶解度和固态相变,则可通过热处理进行强化。
为获得良好的时效强化效果,在不发生过热、过烧及晶粒长大的条件下,淬火加热温度高些,保温时间长些,有利于获得最大过饱和度的均匀固溶体。另外在淬火冷却过程不析出第二相,否则在随后时效处理时,已析出相将起晶核作用,造成局部不均匀析出而降低时效强化效果。
5、硬铝合金有哪些优缺点?说明2A12(LY12)的热处理特点。
硬铝属于Al-Cu-Mg系合金,具有强烈的时效强化作用,经时效处理后具有很高的硬度、强度,故Al-Cu-Mg系合金总称为硬铝合金。这类合金具有优良的加工性能和耐热性,但塑性、韧性低,耐蚀性差,常用来制作飞机大梁、空气螺旋桨等
硬铝合金的热处理特性是强化相的充分固溶温度与(a+β+S)三元共晶的熔点507℃.因此,硬铝淬火加热的过烧敏感性很大,为了获得最大固溶度的过饱和固溶体,2A12合金
最理想的淬火温度为500℃±3℃,但实际生产条件很难做到,所以2A12合金常用的淬火温
度为495~500℃
6、试述铸造铝合金的类型、特点和用途。
铸造铝合金一般分为以下 4 个系列 :
Al-Si 合金该系合金又称为硅铝明 , 一般 Si 的质量分数为 4%-22%.Al-Si 合金具有
优良的铸造性能,如流动性好、气密性好、收缩率小和热裂倾向小,经过变质和热处理之
后,具有良好的力学性能、物理性能、耐腐蚀性能和中等的机加工性能,是铸造铝合金
中品种最多,用途最广的一类合金。
Al-Cu-合金该系合金中 Cu 的质量分数为 3%-11%,加人其他元素使室温和高温力学
性能大幅度提高,如ZL205A (T6)合金的标准性能 为490MPa,是目前世界上强度最
高的铸造铝合金之一, ZL206 、ZL207和ZL208合金具有很高的耐热性能。ZL207中
添加了混合稀土,提高了合金的高温强度和热稳定性,可用于 350-400 ℃ 下工作的零
件,缺点是室温力学性能较差,特别是伸长率很低。 Al-Cu 合金具有良好的切削加工和
焊接性能,但铸造性能和耐腐蚀性能较差。这类合金在航空产品上应用较广,主要用作承
受大载荷的结构件和耐热零件。
Al-Mg 合金该系合金中 Mg 的质量分数为 4%-11%,密度小,具有较高的力学性能,
优异的耐腐蚀性能,良好的切削加工性能,加工表面光亮美观。该类合金熔炼和铸造工艺
较复杂,除用作耐蚀合金外,也用作装饰用合金。
Al-Zn 合金 Zn 在 Al 中的溶解度大,当 Al 中加人 Zn 的质量分数大于 10% 时,能
显著提高合金的强度,该类合金自然时效倾向大,不需要热处理就能得到较高的强度。这
类合金的缺点是耐腐蚀性能差,密度大,铸造时容易产生热裂,主要用做压铸仪表壳体
类零件。
7、试解释:铝合金的晶粒粗大,不能靠重新加热处理来细化。由于铝合金不象钢
基体在加热或冷却时可以发生同素异构转变,因此不能像钢一样可以通过加热和冷却发生重
结晶而细化晶粒。
8、Al-Zn-Cu-Mg 系合金的最高强度是怎样通过化学成分和热处理获得的?
热处理可强化型铝合金: AL-Zn-Mg—Cu 系合金—7XXX 系,如 7075 合金,以 Mg 和Si 为主要
合金元素并以 Zn 为主要合金元素的铝合金。
7XXX 系合金中含铜的 AL-Zn--Mg--Cu,还有一些其他微量元素,它有较强的韧性和强
度,为代表的7075合金,用于飞机及航空制造业。这类合金有抗应力腐蚀性和抗剥落腐蚀
的能力会随之下降。如果对成份和热处理以及显微组织进行全面设计,可以得到综合性能良
好的高强度合金,该系合金中主要强化相为Mn Zn z(n)与A12 Mg3 Zn3(T)相。用于制作轮
椅的材料7003-C合金主要强化相为n相和Mg2Si.。有很好的抗应力腐蚀性能和焊接性能,
又有比6XXX系列高的强度和塑性,便于热成形和冷加工,在冷加工和焊接后不需再进行热
处理。
研究 2种不同热处理方式对喷射成形超高强度 Al-Zn-Mg-Cu 系铝合金的显微组织和力学
性能的影响。观察沉积态、挤压态、固溶及时效处理后样品的显微组织,对经时效处理的样
品进行了力学性能测试。结果表明:沉积态合金晶粒均匀细小;挤压态合金存在大量的第二
相颗粒,为富铜相;固溶处理后,合金出现了再结晶现象。在T6条件下,采用常规470℃
单级固溶和时效处理,其抗拉强度仅为710MPa,延伸率为6. 5%;采用双级固溶和时效处
理,其抗拉强度超过 800MPa,延伸率达到 9. 3%。(T6:固溶热处理后进行人工时效的状态)
9、不同铝合金可通过哪些途径达到强化的目的?
代号名称
自由加工状态说明与应用
适用于在成形过程中,对于加工硬化和热处理条件无
特殊要求的产品,对该状态产品的力学性能不作规
定
。退火状态
适用于经完全退火获得最低强度的加工产品
H加工硬化状态
适用于通过加工硬化提高强度的产品,产品在加工
硬化后要经过(也可不经过)使强度有所降低的附
加热处理。H 代号后面必须跟有两位或三位何拉伯
数字
w固溶热处理状态 一种不稳定状态,仅适用于经固溶热处理后,室温
下自然时效的合金,该状态代号仅表示产品处于自
然时效阶段
T热处理状态 适用于热处理后,经过(或不经过)加工硬化达到稳定状态(不同
于 F、O、H 状态)的产品,
T代号后面必须跟有一位或多位阿拉伯数字。
TO 固溶热处理后,经自然时效再经过冷加工的状态。适用于经冷加工提高强度的产
品
T1 由高温成形冷却,然后自然时效至基本稳定的状态。适用于由高温成形过程冷却
后,不再进行冷加工(可进行矫直、矫平,但不影响力学性能极限)的产品T2 由高温成形冷却,经冷加工后自然时效至基本稳定的状态。适用于由高温成形过
程冷却后,进行冷加工或矫直、矫平以提高强度的产品
T3 固溶热处理后进行冷加工,再经自然时效至基本稳定的状态。适用于在固溶热处
理后,进行冷加工或矫直、矫平以提高强度的产品
T4 固溶热处理后自然时效至基本稳定的状态。适用于固溶热处理后,不再进行冷加
工(可进行矫直、矫平,但不影响力学性能极限)的产品
T5 由高温成形过程冷却,然后进行人工时效的状态。(不经过冷加工可进行矫直、矫
平但不影响力学性能极限),予以人工时效的产品
T6 固溶热处理后进行人工时效的状态
T7 固溶热处理后进行过时效的状态。适用于固溶热处理后,为获取某些重要特性,
在人工时效时强度在时效曲线上越过了最高峰点的产品
T8 固溶热处理后经冷加工,然后进行人工时效的状态。适用于经冷加工或矫直、矫
平以提高强度的产品
T9 固溶热处理后人工时效,然后进行冷加工的状态。适用于经冷加工提高强度产品T10 由高温成形过程冷却后,进行冷加工,然后人工时效的状态
10、为什么大多数铝硅铸造合金都要进行变质处理?铝硅铸造合金当硅含量为多少时一般不进行变质处理,原因是什么?铝硅铸造合金中加入镁、铜等元素作用是什么?
般情况下,铝硅合金的共晶体由粗针状硅晶体和a固溶体构成,强度和塑性都较差;经变质处理后的组织是细小均匀的共晶体加初生a固溶体,合金的强度和塑性显著提高,因此,铝硅合金要进行变质处理。
铸造硅铝合金一般需要采用变质处理,以改变共晶硅的形态。常用的变质剂为钠盐。钠盐变质剂易与熔融合金中的气体起反应,使变质处理后的铝合金铸件产生气孔等铸造缺陷,为了消除这种铸造缺陷,浇注前必须进行精炼脱气,导致铸造工艺复杂化。故一般对于Si小于7%-8%的合金不进行变质处理。
若适当减少硅含量而加入铜和镁可进一步改善合金的耐热性,获得铝硅铜镁系铸造合金,其强化相除了Mg2Si、CuA12外,还有A12CuMg、AlxCu4Mg5Si4等相,常用的铝硅铜镁系铸造合金有ZL103、ZL105、ZL111 等合金。它们经过时效处理后,可制作受力较大的零件,如 ZL105 可制作在 250℃以下工作的耐热零件,ZL111 可铸造形状复杂的内燃机汽缸等。
11、铸造铝合金的热处理与变形铝合金的热处理相比有什么特点?为什么?
铝合金分两大类:铸造铝合金,在铸态下使用;变形铝合金,能承受压力加工,力学性能高于铸态。可加工成各种形态、规格的铝合金材。主要用于制造航空器材、日常生活用品、建筑用门窗等。铝合金按加工方法可以分为变形铝合金和铸造铝合金。变形铝合金又分为不可热处理强化型铝合金和可热处理强化型铝合金。不可热处理强化型不能通过热处理来提高机械性能,只能通过冷加工变形来实现强化,它主要包括高纯铝、工业高纯铝、工业纯铝以及防锈铝等。可热处理强化型铝合金可以通过淬火和时效等热处理手段来提高机械性能,它可分为硬铝、锻铝、超硬铝和特殊铝合金等。 铝合金可以采用热处理获得良好的机械性能,物理性能和抗腐蚀性能。铸造铝合金按化学成分可分为铝硅合金,铝铜合金,铝镁合金和铝锌合金。
第 10 章 铜合金
1、锌含量对黄铜性能有什么影响?
(1)普通黄铜的室温组织 普通黄铜是铜锌二元合金,其含锌量变化范围较大,因此其室温组织也有很大不同。根据 Cu-Zn 二元状态图(图 6),黄铜的室温组织有三种:含锌量在 35%以下的黄铜,室温下的显微组织由单相的a固溶体组成,称为a黄铜;含锌量在36%~46%范围内的黄铜,室温下的显微组织由(a+β)两相组成,称为(a+β)黄铜(两相黄铜);含锌量超过 46%~50%的黄铜,室温下的显微组织仅由 β 相组成,称为 β 黄铜。
(2)压力加工性能 a 单相黄铜(从 H96 至 H65)具有良好的塑性,能承受冷热加工,但a 单相黄铜在锻造等热加工时易出现中温脆性,其具体温度范围随含 Zn 量不同而有所变化,一般在 200~700℃之间。因此,热加工时温度应高于 700℃。单相 a 黄铜中温脆性区产生的原因主要是在 Cu-Zn 合金系 a 相区内存在着 Cu3Zn 和 Cu9Zn 两个有序化合物,在中低温加热时发生有序转变,使合金变脆;另外,合金中存在微量的铅、铋有害杂质与铜形成低熔点共晶薄膜分布在晶界上,热加工时产生晶间破裂。实践表明,加入微量的铈可以有效地消除中温脆性。
两相黄铜(从 H63 至 H59),合金组织中除了具有塑性良好的 α 相外,还出现了由电子化合物CuZn为基的β固溶体。β相在高温下具有很高的塑性,而低温下的β'相(有序固溶体)性质硬脆。故(a+β)黄铜应在热态下进行锻造。含锌量大于 46%~50%的 β 黄铜因性能硬脆,不能进行压力加工。
(3) 力学性能 黄铜中由于含锌量不同,机械性能也不一样。对于 a 黄铜,随着含锌量的增多,σb 和 δ 均不断增高。对于(a+β)黄铜,当含锌量增加到约为 45%之前,室温强度不断提高。若再进一步增加含锌量,则由于合金组织中出现了脆性更大的 r 相(以 Cu5Zn8化合物为基的固溶体),强度急剧降低。(a+β)黄铜的室温塑性则始终随含锌量的增加而降低。所以含锌量超过 45%的铜锌合金无实用价值。
普通黄铜的用途极为广泛,如水箱带、供排水管、奖章、波纹管、蛇形管、冷凝管、弹壳及各种形状复杂的冲制品、小五金件等。随着锌含量的增加从H63到H59,它们均能很好地承受热态加工,多用于机械及电器的各种零件、冲压件及乐器等处。
2、单相a黄铜中温脆性产生的原因是什么?如何消除?
单相黄铜(从H96至H65)具有良好的塑性,能承受冷热加工,但a单相黄铜在锻造等热加工时易出现中温脆性,其具体温度范围随含Zn量不同而有所变化,一般在200~700℃之间。因此,热加工时温度应高于700℃。单相a黄铜中温脆性区产生的原因主要是在Cu-Zn合金系a相区内存在着Cu3Zn和Cu9Zn两个有序化合物,在中低温加热时发生有序转变,使合金变脆:另外,合金中存在微量的铅、铋有害杂质与铜形成低熔点共晶薄膜分布在晶界上,热加工时产生晶间破裂。实践表明,加入微量的铈可以有效地消除中温脆性。
3、什么是黄铜的“自裂”?产生的原因是什么?通常采用什么方法消除?
黄铜经压力加工而内部有残余应力时,若在大气中,特别是在有氨气、氨溶液、汞、汞蒸气、汞盐溶液和海水中易产生腐蚀,致使黄铜破裂,这种现象称:“自裂”(季裂、应力腐蚀)。
为了防止黄铜的应力腐蚀开裂,可将冷加工后的黄铜零件用260-300℃保温1-3小时的低温退火来消除内应力或向黄铜中加入一定量的Sn、Si、Al、Mn和Ni等,可显著降低应力腐蚀倾向,也可采用镀锌和镀锡等电镀层加以保护,以防止自裂。
4、锡青铜的铸造性能为什么比较差?
铸造锡青铜在一般铸造条件下,容易产生反偏析,使铸件成分不均匀,内部形成许多小孔洞,降低铸件的力学性能和气密性。
5、简述合金元素在铝青铜中的作用。
Ti、A1的含量影响高锰铝青铜的机械性能,A1含量变化对材料硬度的影响比Ti明显。在生产高锰铝青铜冶金备件时,Ti含量应控制在0.2%0.25%、A1在7.5%~8.2%之间,可将产品硬度控制在HB(200±20)的范围内。Ti、A1含量在一定范围内增加,可以提高产品硬度。为获得稳定的产品硬度,必须严格控制各种元素的加入量及其成分波动范围。
6、铍青铜在热处理和性能上有何特点?试写出一中牌号,并说明用途。
(1)铍青铜是一种用途极广的沉淀硬化型合金。经固溶及时效处理后,强度可达
1250-1500MPa(1250-1500公斤)。其热处理特点是:固溶处理后具有良好的塑性,可进行冷加工变形。但再进行时效处理后,却具有极好的弹性极限,同时硬度、强度也得到提高。
①铍青铜的固溶处理
一般固溶处理的加热温度在780-820℃之间,对用作弹性元件的材料,采用760-780℃,主要是防止晶粒粗大影响强度。固溶处理炉温均匀度应严格控制在5℃。保温时间一般可按1小时/25mm计算,铍青铜在空气或氧化性气氛中进行固溶加热处理时,表面会形成氧化膜。虽然对时效强化后的力学性能影响不大,但会影响其冷加工时工模具的使用寿命。为避免氧化应在真空炉或氨分解、惰性气体、还原性气氛(如氢气、一氧化碳等)中加热,从而获得光亮的热处理效果。此外,还要注意尽量缩短转移时间(此淬水时),否则会影响时效后的机械性能。薄形材料不得超过3秒,一般零件不超过5秒。淬火介质一般采用水(无加热的要求),当然形状复杂的零件为了避免变形也可采用油。
②铍青铜的时效处理铍青铜的时效温度与Be的含量有关,含Be小于2.1%的合金均宜进行时效处理。对于Be大于1.7%的合金,最佳时效温度为300-330℃,保温时间1-3小时(根据零件形状及厚度)。Be低于0.5%的高导电性电极合金,由于溶点升高,最佳时效温度为450-480℃,保温时间1-3小时。近年来还发展出了双级和多级时效,即先在高温短时时
效,而后在低温下长时间保温时效,这样做的优点是性能提高但变形量减小。为了提高铍青铜时效后的尺寸精度,可采用夹具夹持进行时效,有时还可采用两段分开时效处理。
③铍青铜的去应力处理铍青铜去应力退火温度为150-200℃,保温时间1-1.5小时,可用于消除因金属切削加工、校直处理、冷成形等产生的残余应力,稳定零件在长期使用时的形状及尺寸精度。
(2)常用的铍青铜wBe=1.7%~2.5%。铍在铜中的最大溶解度为2.7%,到室温时降至0.2%,所以,铍青铜经固溶热处理和时效后有较高的强度、硬度。同时,铍青铜还具有良好的耐蚀性、耐疲劳性、导电性、导热性,且无磁性,受冲击不产生火花等,是一种综合性能较好的结构材料,主要用于制造各种精密仪器、仪表中的弹性零件和耐蚀、耐磨零件,如钟表齿轮、航海罗盘、电焊机电极、防爆工具等。铍青铜价格贵,工艺复杂,应用受到限制
如牌号:QBe2,用途:重要仪表的弹簧、齿轮等。耐磨零件,高速、高压、高温下的轴承。7、什么叫“弹壳黄铜”、“商业黄铜”、“金色黄铜”、“易切黄铜”、“海军黄铜”?写出其主要牌号及用途。
①黄铜以锌作主要添加元素的铜合金,具有美观的黄色,统称黄铜。铜锌二元合金称普通黄铜或称简单黄铜。三元以上的黄铜称特殊黄铜或称复杂黄铜。含锌低於36%的黄铜合金由固溶体组成,具有良好的冷加工性能,如含锌30%的黄铜常用来制作弹壳,俗称弹壳黄铜或七三黄铜。含锌在36~42%之间的黄铜合金由和固溶体组成,其中最常用的是含锌40%的六四黄铜。为了改善普通黄铜的性能,常添加其他元素,如铝、镍、锰、锡、硅、铅等铝能提高黄铜的强度、硬度和耐蚀性,但使塑性降低,适合作海轮冷凝管及其他耐蚀零件。锡能提高黄铜的强度和对海水的耐腐性,故称海军黄铜,用作船舶热工设备和螺旋桨等。铅能改善黄铜的切削性能:这种易切削黄铜常用作钟表零件,称为易切黄铜。黄铜铸件常用来制作阀门和管道配件等。
②特殊黄铜:在普通黄铜中加入其它合金元素所组成的多元合金称为黄铜。常加入的元素有铅、锡、铝等,相应地可称为铅黄铜、锡黄铜、铝黄铜。加合金元素的目的。主要是提高抗拉强度改善工艺性。
代号:为“H+主加元素符号(除锌外)+铜的质量分数+主加元素质量分数+其它元素质量分数”表示。
如:HPb59-1表示铜的质量分数为59%,含主加元素铅的质量分数为1%,余量为锌的铅黄铜。
③青铜:除黄铜白铜外,其余的铜的合金统称青铜,青铜又可分为锡青铜和特殊青铜(即无锡青铜)两类。
代号:表示方法为“Q+主加元素符号及质量分数+其它元素的质量分数”所组成。铸造产品则在代号前加“Z”字,如:Qal7表示含铝为5%,其余为铜的铝青铜ZQsn10-1表示含锡量为10%,其它合金元素含量为1%,余量为铜的的铸造锡青铜
④锡青铜:是由锡为主加元素的铜锡合金,也称为锡青铜。当含锡量小于5~6%,锡溶于铜中形成a固溶体,塑性上升,当含锡量大于5~6%时,由于出现了Cu31sb8为基的固溶体,抗拉强度下降,所以秤的锡青铜含锡量大多在314%之间,当含锡量小于5%,适用于冷变形加工,当含锡量为57%时的适用于热变形加工。当含锡量大于10%时,适用于铸造。由于a与&电极电位相近,且成分中的锡氮化后生成致密的二氧化锡薄膜,耐大气、耐海水等的耐蚀性上升,只是耐酸性较差。因为锡青铜结晶温度范围较宽,流动性差,不易形成集中缩孔,而易形成枝晶偏析和分散缩孔,铸造收缩率小,有利于得尺寸极接近于铸型的铸件,所以适于铸造形状复杂。壁厚较大的条件,而不适宜铸造要求致密度高和密封性好的铸
件。锡青铜有良好的减摩性,抗磁性及低温韧性。
锡青铜按生产方法可分为压力加工锡青铜与铸造锡青铜两大类。
特殊青铜:加入其它元素以取代锡,或为无锡青铜,多数特殊青铜都比锡青铜具有更高的机性,耐磨性与耐蚀性,常用的有铝青铜(QAL7QAL5)铅青铜(ZQPB30)等。以镍为主要添加元素的铜基合金呈银白色,称为白铜。镍含量通常为10%、15%、20%,含量越高,颜色越白。铜镍二元合金称普通白铜,加锰、铁、锌和铝等元素的铜镍合金称为复杂白铜,纯铜加镍能显著提高强度、耐蚀性、电阻和热电性。工业用白铜根据性能特点和用途不同分为结构用白铜和电工用白铜两种,分别满足各种耐蚀和特殊的电、热性能。
8、为什么炮弹弹壳常用H70、H68黄铜材料制造?
黄铜(又叫青铜),黄铜是主要由铜和锌形成的合金,用途甚广,其性质取决于铜和锌的比例。含铜达63%以上的黄铜,可以冷加工,可以退火,有延展性;而含铜较少、含锌较多的合金,则应热加工,强度较高。
H70(C2600):含铜量70%,又称弹壳黄铜。具有良好光泽、加工性、延展性、适合伸抽,易于电镀或涂装。可应用于深伸抽加工,如子弹壳,炮弹壳、喇叭锁、电子零件、汽车水箱、铜管。H68(C2620):含铜量68%,又称弹壳黄铜。延展性,可焊性,深冲性,可镀性,耐蚀性能均佳,应用于各种复杂冷深冲件,散热器壳等。
9、氧、硫、磷、铋等常见杂质元素对纯铜性能产生哪些不良影响
紫铜中的微量杂质对铜的导电、导热性能有严重影响。氧、硫、硒、碲等在铜中的固溶度很小,可与铜生成脆性化合物,对导电性影响不大,但能降低加工塑性。氧对铜的焊接性有害。铋或铅与铜生成低熔点共晶,使铜产生热脆
第11章钛合金
1、钛合金的合金化原则是怎样的?为什么几乎在所有钛合金中,均有一定含量的合金元素铝?为什么铝的加入量都控制在6%一7%以下?
①钛合金是以钛为基加入其他元素组成的合金。钛有两种同质异晶体:882℃以下为密排六方结构a钛,882℃以上为体心立方的β钛。
②铝是钛合金主要合金元素,它对提高合金的常温和高温强度、降低比重、增加弹性模量有明显效果。
③钛-铝系合金的强度随铝合金含量的增加而升高。但A含量>6%后,由于出现与相共格的有序相a2相(Ti3Al)而变脆,甚至会使热加工发生困难。因此,一般工业用Ti合金的Al含量很少超过6%。
2、为什么国内外目前应用最广泛的钛合金是Ti-Al-V系的Ti-6Al-4V即TC4合金?钛合金具有强度高而密度又小,机械性能好,韧性和抗蚀性能很好。另外,钛合金的工艺性能差,切削加工困难,在热加工中,非常容易吸收氢氧氮碳等杂质。还有抗磨性差,生产工艺复杂。钛的工业化生产是1948年开始的。航空工业发展的需要,使钛工业以平均每年约8%的增长速度发展。目前世界钛合金加工材年产量已达4万余吨,钛合金牌号近30种。第一个实用的钛合金是1954年美国研制成功的Ti-6Al-4V合金,由于它的耐热性、强度、塑性、韧性、成形性、可焊性、耐蚀性和生物相容性均较好,而成为钛合金工业中的王牌合金,该合金使用量已占全部钛合金的75%~85%。其他许多钛合金都可以看做是Ti-6Al-4V合金的改型。
3、简述铝和锡在a钛合金中的作用。
铝和锡是提高相转变温度的元素为a稳定元素。
4、如何改善钛合金的生产工艺?
要提高质量,首先要提高钛的纯净度,这取决于两方面的因素,一方面要改善工艺,另一方面要改善无损探伤技术。通常钛合金的熔炼采用自耗炉冶炼。这种熔炼方法的主要问题是合金锭的均匀性和夹杂物。20世纪90年代以前,工业生产的钛缺陷率大,现已有所降低。主要是因为发展子电子束重熔技术(EBCHM)。这种方法有利于解决偏析及制备不同截面的锭子,并且对去除高密度缺陷很有效。此外,还可用三次真空冶炼方法来改善工艺。
5、要扩大钛合金在民品工业中的应用,首要的任务是什么?通过什么途径可以实现?
①要扩大钛合金在民品工业中的应用,首要的任务是:降低成本。
②发展一些低成本合金。此外,可用钛合金回收碎屑和采用Fe-Mo中间合金降低成本,性能也能满足要求。
第12章其它有色金属合金
1、镁合金的最大特点是什么?为什么被称为“绿色工程材料”?
1)①在实用金属中是最轻的金属。镁的比重大约是铝的2/3,是铁的1/4。它是实用金属中的最轻的金属。应用范围:镁合金广泛用于携带式的器械和汽车行业中,达到轻量化的目的。②高强度、高刚性。镁合金的比重虽然比塑料重,但是,单位重量的强度和弹性率比塑料高,所以,在同样的强度零部件的情况下,镁合金的零部件能做得比塑料的薄而且轻。另外,由于镁合金的比强度也比铝合金和铁高,因此,在不减少零部件的强度下,可减轻铝或铁的零部件的重量。应用范围:手机电话,笔记本电脑上的液晶屏幕的尺寸年年增大,在它们的枝撑框架和背面的壳体上使用了镁合金。
③传热性好。虽然镁合金的导热系数不及铝合金,但是,比塑料高出数十倍,因此,镁合金用于电器产品上,可有效地将内部的热散发到外面。应用范围:在内部产生高温的电脑和投影仪等的外壳和散热部件上使用镁合金。电视机的外壳上使用镁合金可做到无散热孔。
④电磁波屏蔽性好。镁合金的电磁波屏蔽性能比在塑料上电镀屏蔽膜的效果好,因此,使用镁合金可省去电磁波屏蔽膜的电镀工序。
应用范围:在手机电话的壳体和屏蔽材料上使用了镁合金。
⑤机械加工性能好。镁合金比其他金属的切削阻力小,在机械加工时,可以较快的速度加工。耐凹陷性好。镁合金与其他金属相比抗变形力大,由冲撞而引起的凹陷小于其他金属。
⑥对振动·冲击的吸收性高。由于镁合金对振动能量的吸收性能好,使用在驱动和传动的部件上可减少振动。另外,冲击能量。
⑦吸收性能好,比铝合金具有更好的延伸率的镁合金,受到冲击后,能吸收冲击能量而不会产生断裂。应用范围:在硬盘驱动器的读出装置等的振动源附近的零件上使用镁合金。若在风扇的风叶上使用镁合金,可减小振动达到低骚音。此外,为了在汽车受到撞击后提高吸收冲击力和轻量化,在方向盘和坐椅上使用镁合金。
⑧抗蠕变性能好。镁随着时间和温度的变化在尺寸上蠕变少。
⑨再生。镁合金与塑料不同,它可以简单地再生使用且不降低其机械性能,而塑料很难在不降低其机械性能再生使用。镁合金与其他金属相比,熔点低,比热小,在再生熔解时所消耗的能源是新材料制造所消耗的能源的4%。
(2)因为再生的特点,镁合金被称为21世纪的绿色工程材料。且镁是地球上最丰富的资源,从海水、菱镁矿石、白云石都能提炼出镁。中国的镁蕴藏量居世界第一位。镁原料出口居世界第二位。
2、镁合金中的主要合金元素有哪些?它们的作用是什么?
镁合金的主要合金元素有Al、Zn、Mn和Zr等。
①铝可改善压铸件的铸造性能,提高铸件强度。
②锌可以提高铸件抗蠕变性能。
③在镁中加入镁对合金的力学性能影响不大,但降低塑性。
锆可以细化晶粒,锆可减少热裂倾向和提高力学性能及耐蚀性,降低应力腐蚀敏感性。3、在铸造镁合金中,稀土元素的作用是什么?哪一种稀土元素应用效果最佳?为什么?
在铸造镁合金中,稀土元素是改善耐热性最有效最有效和最具实用价值的金属。在稀土金属中,Nd的作用最佳。Nd在镁合金中可导致在高温和常温下同时获得强化。
4、镁合金的热处理特点是什么?在什么情况下,镁合金需要进行二次热处理?镁合金热处理的主要特点是固熔和时效处理时间较长,并且镁合金淬火时不必快速冷却,通常在静止的空气或人工强制流动的气流中冷却即可。
镁合金铸件热处理后的显微组织中化合物含量过高,或者在固熔处理后的缓冷过程中出现了过时效现象,那么就要进行二次热处理。
5、锌合金有哪些特点?锌合金中普遍存在的问题是什么?可通过什么途径来改善它?
(1)锌合金的主要特点如下:
①锌合金具有较低的摩擦系数、较高的承载能力、较高的耐磨性。
②成本低,能量消耗少,在制成铸件时熔化的能耗也较低。
③生产周期短。④较高的导电、导热性。
⑤良好的铸造成形性能。
⑥非磁性及抗火花性。
(2)①Zn-Cu系合金。存在体积不稳定的现象。可通过加入少量的Mg或Mn的办法来改善。②Zn-Al系合金。缺点:在潮湿大气中容易发生晶间腐蚀。加入少量镁能抵消杂质Pb的有害作用。
③Zn-Al-Cu系合金。缺点:晶间腐蚀敏感性高。加入0.02%-0.05%镁能减轻晶间腐蚀和杂质(Pb、Sn、Cd)对晶间腐蚀的不利影响。
4Zn-Ti系合金。缺点:耐蚀性和铸造性能低。加入0.5%Cu和少量Mn和Cr能改善耐蚀性,加入微量(0.01%0.04%)AI能改善铸造性能。
一、课程特点和要求
课程特点:综合性、应用性、经验性。
金属材料学核心课程是专业知识教学中最后一门课程
工程应用
成分工艺
组织/结构
性能
应用环境
金属材料学
原理工艺
性能
铸造
压力加工焊接
金属学
课程要求:掌握合金化理论的基本知识,了解材料成分设计的基本依据,熟悉生产中常用的材料及其热处理工艺、组织、性能之间的关系,根据零件技术要求,能正确地选择材料和制订工艺。
二、课程要点及思路
主线:材料成分-工艺-组织-性能-应用之间的有机关系核心:合金化原理
“思想”:作用的辨证与矛盾的转化。
三、教学安排
教学:详略,有的内容自学;
实践:课堂讨论,小论文,综合性实验,思考题;
考试:考试+平时-课堂讨论与实验
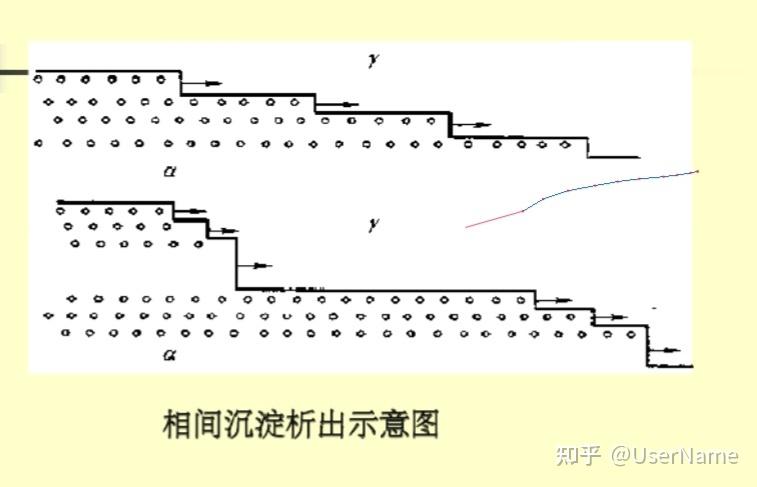
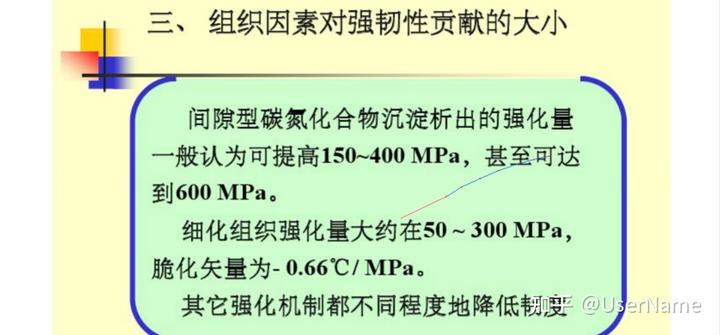
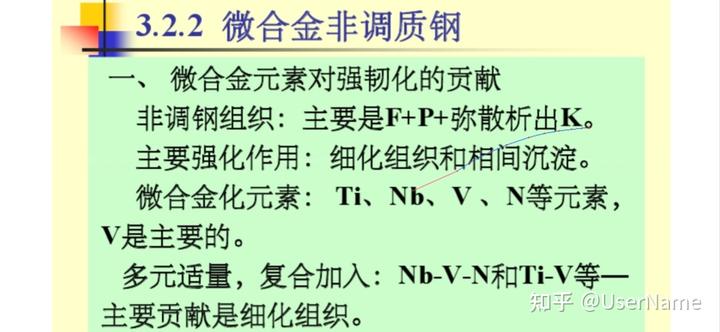
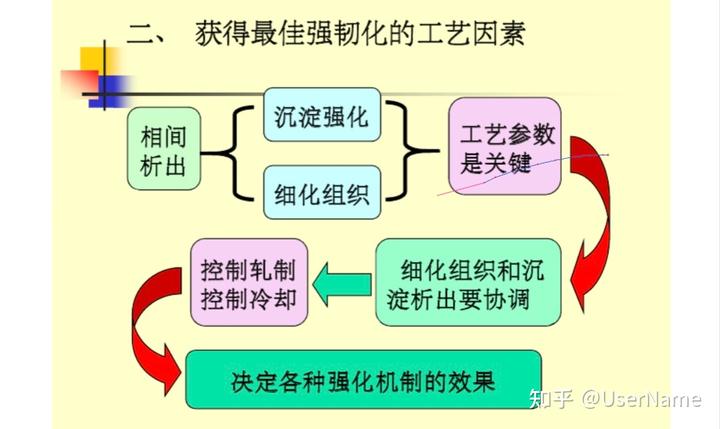
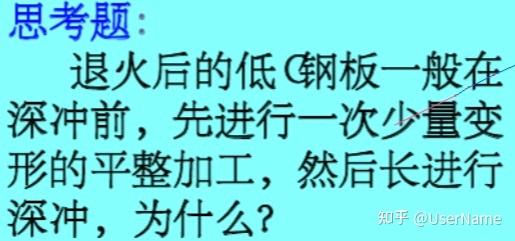
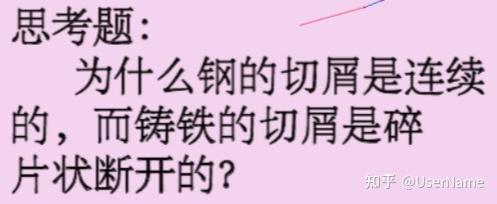
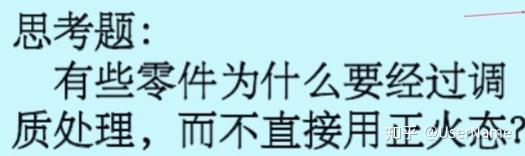
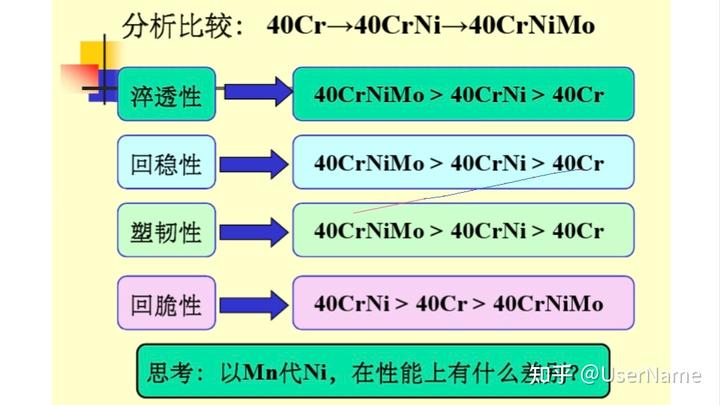
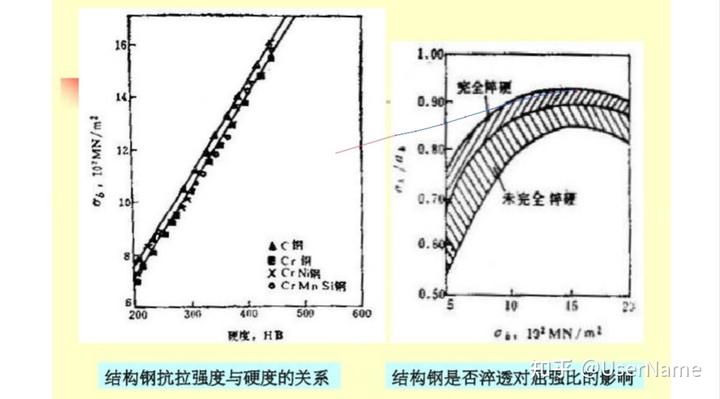
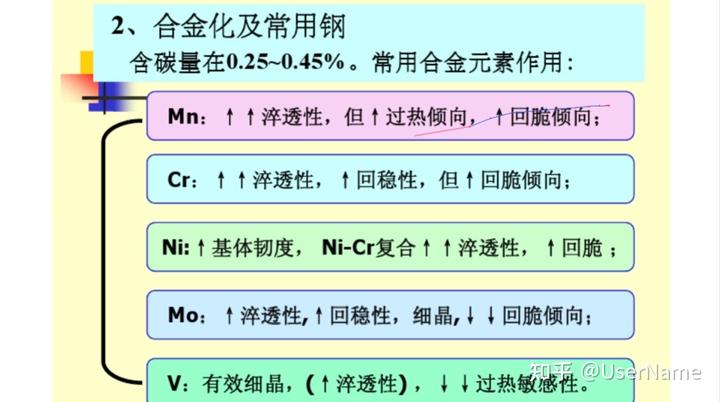
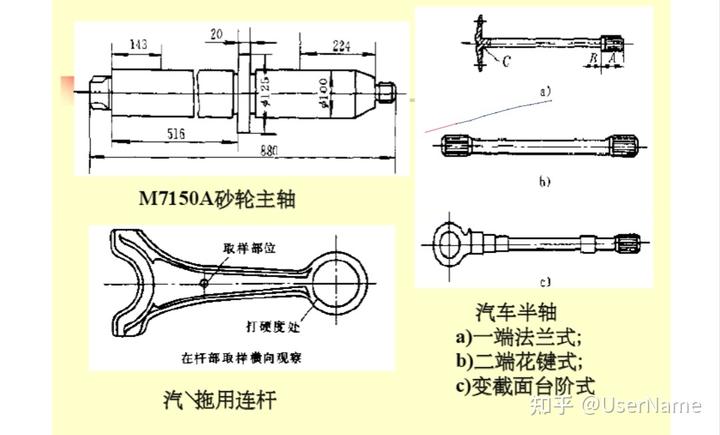
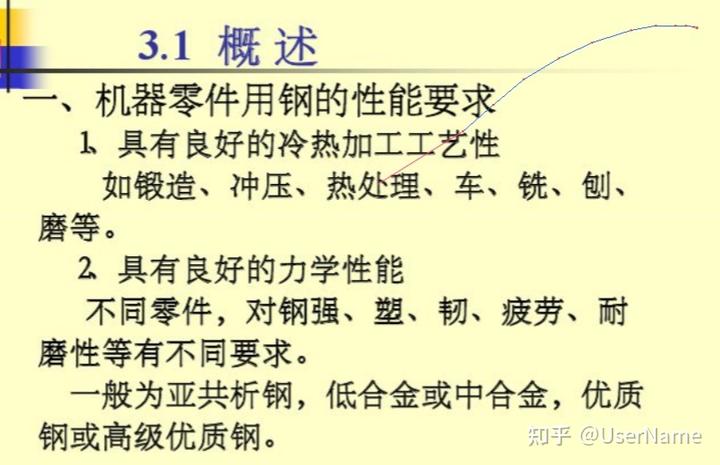
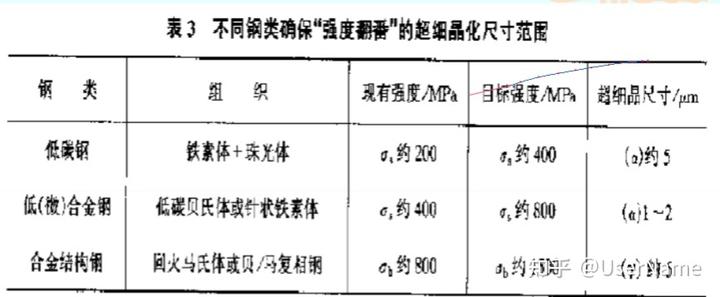
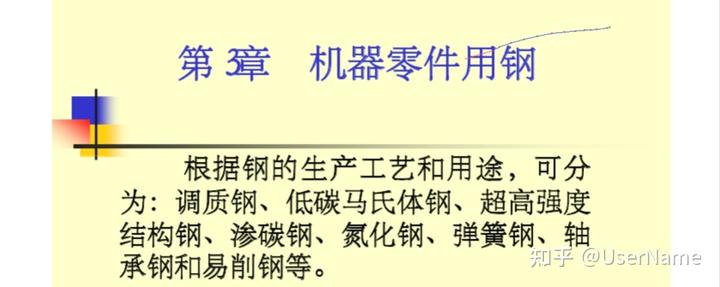
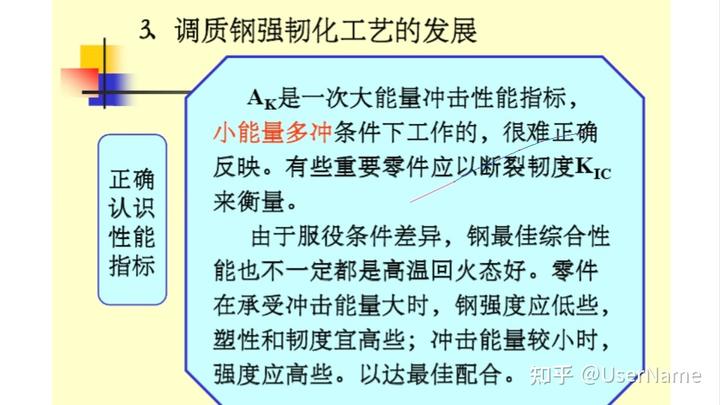
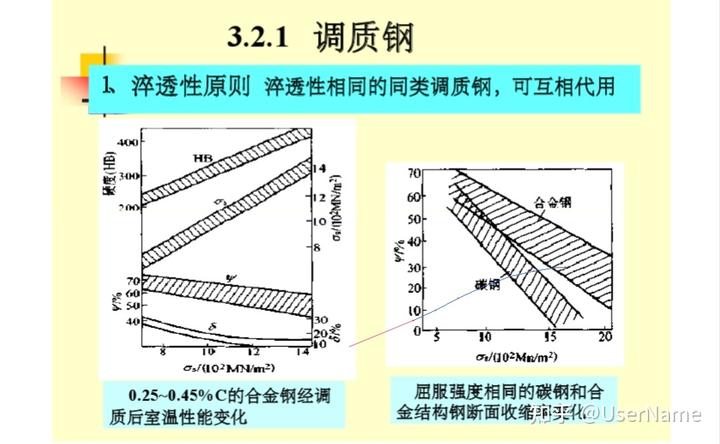
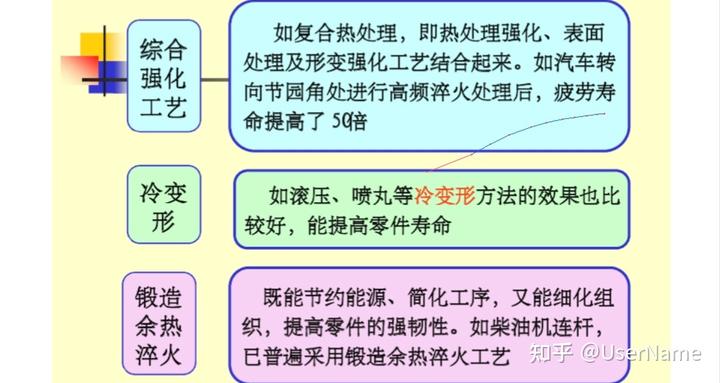
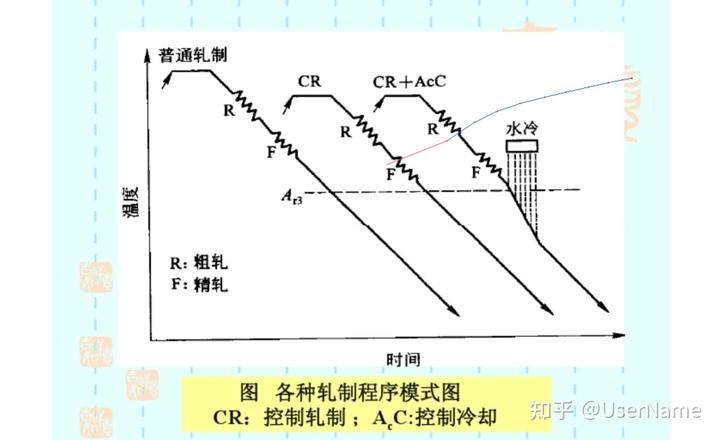

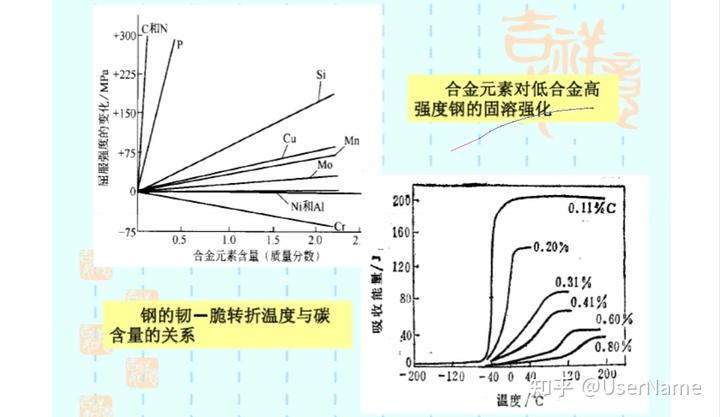
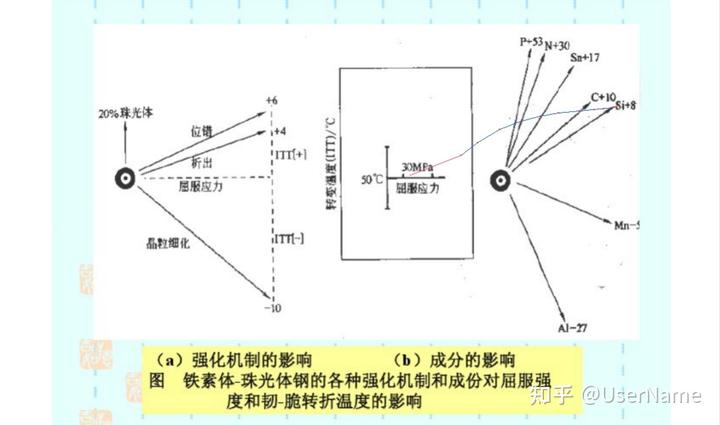
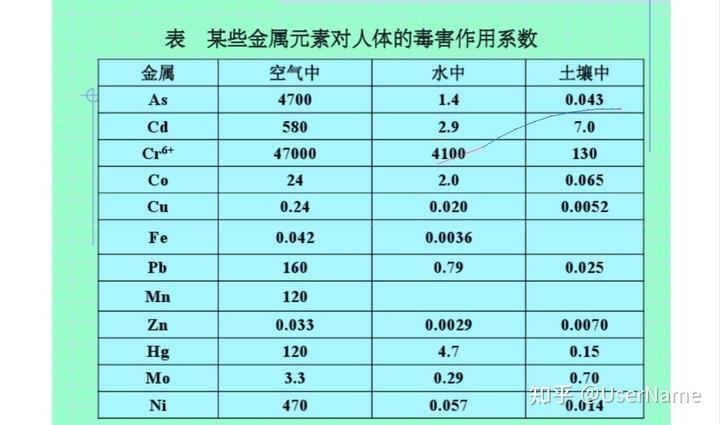
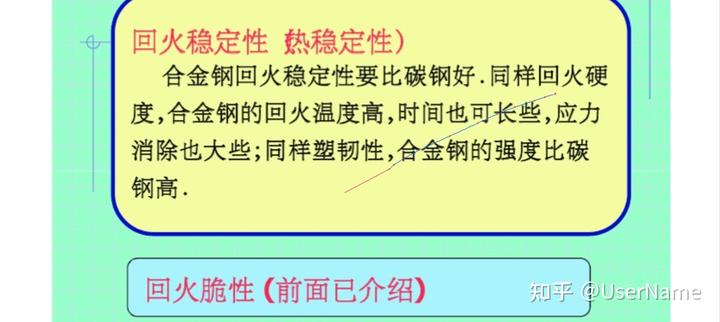
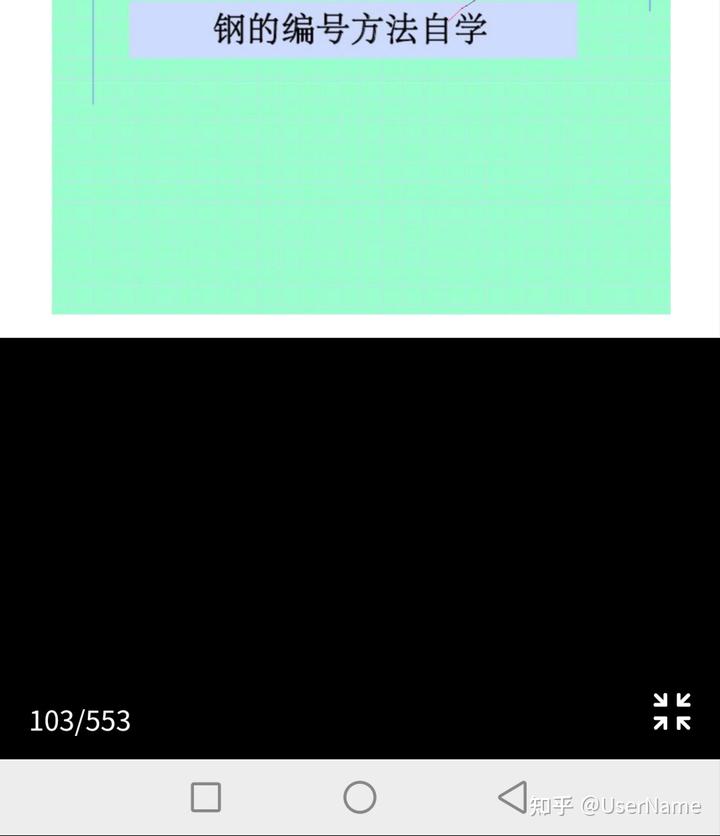
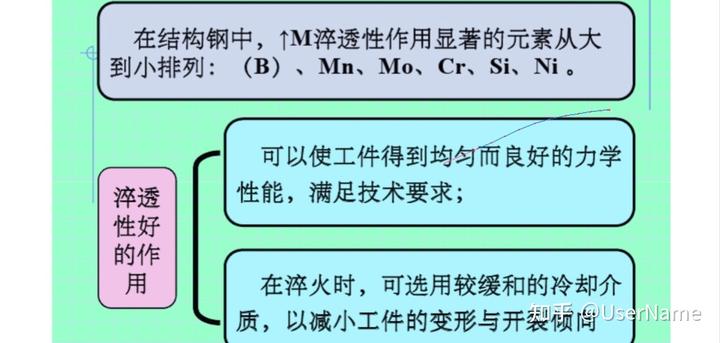
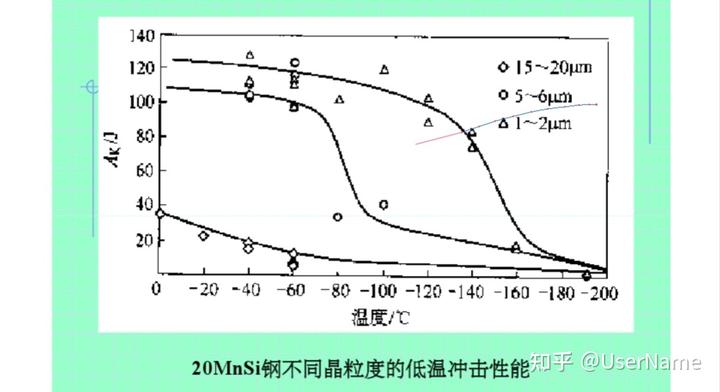
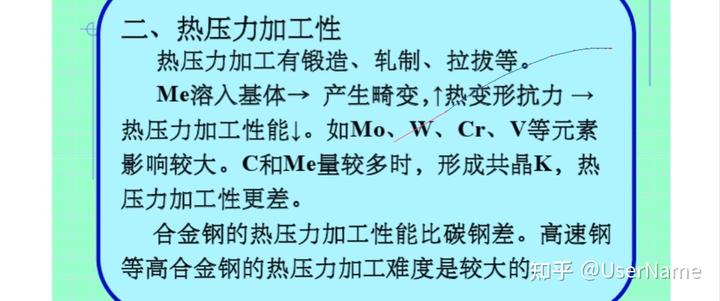
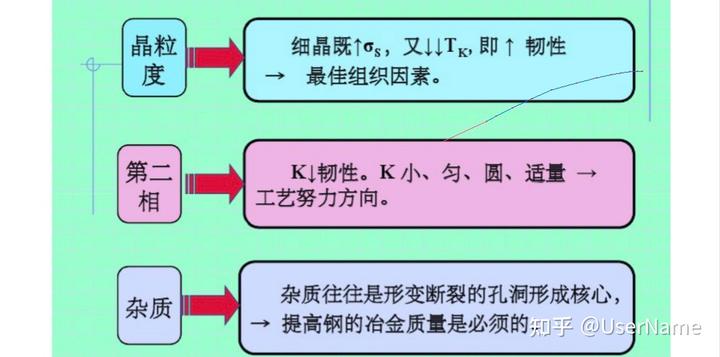
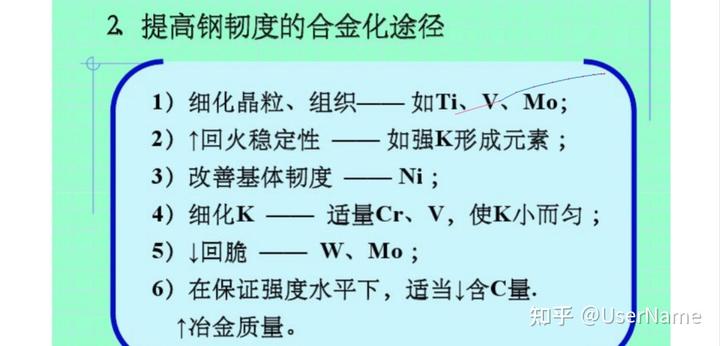
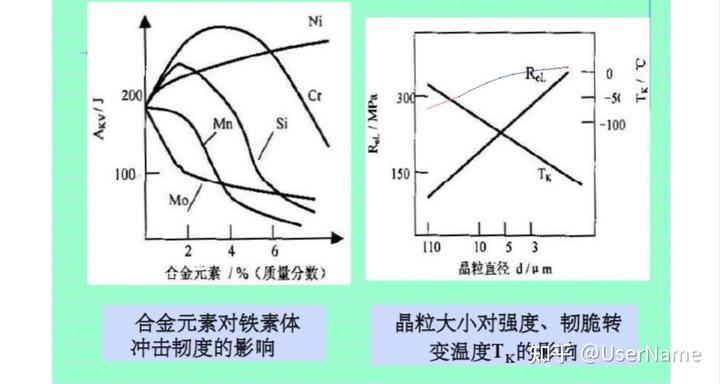
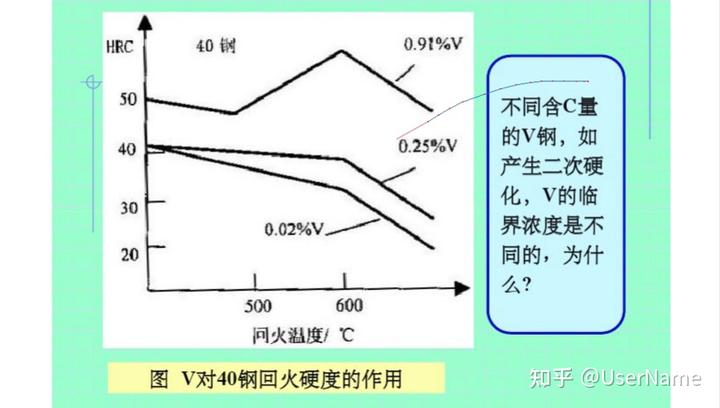
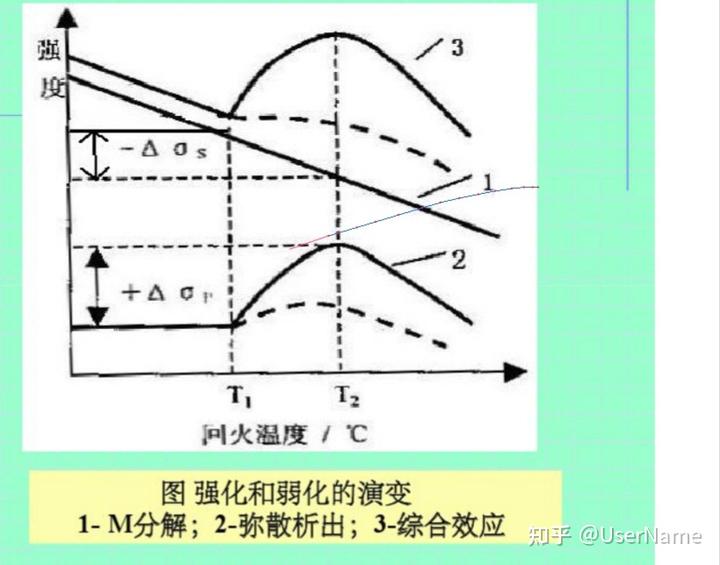
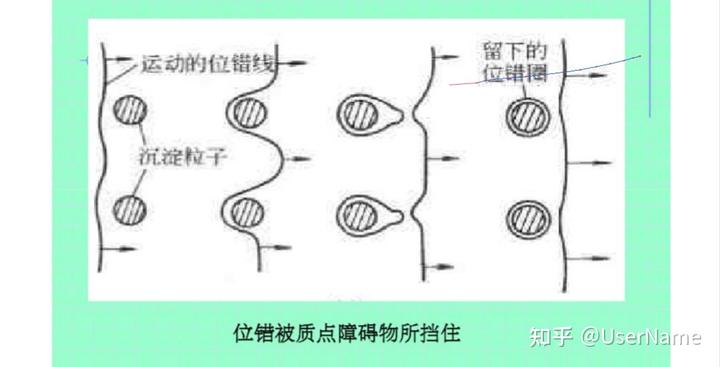
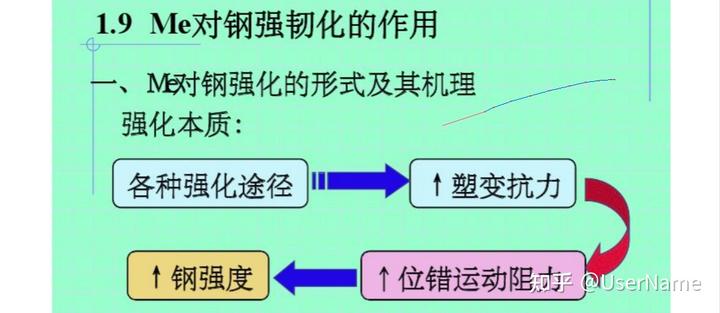
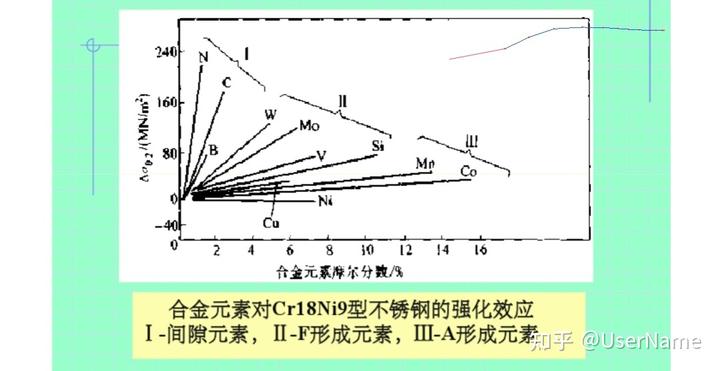
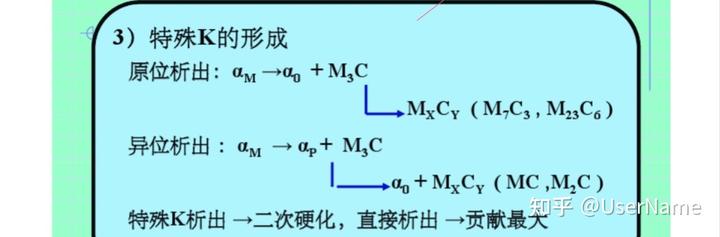
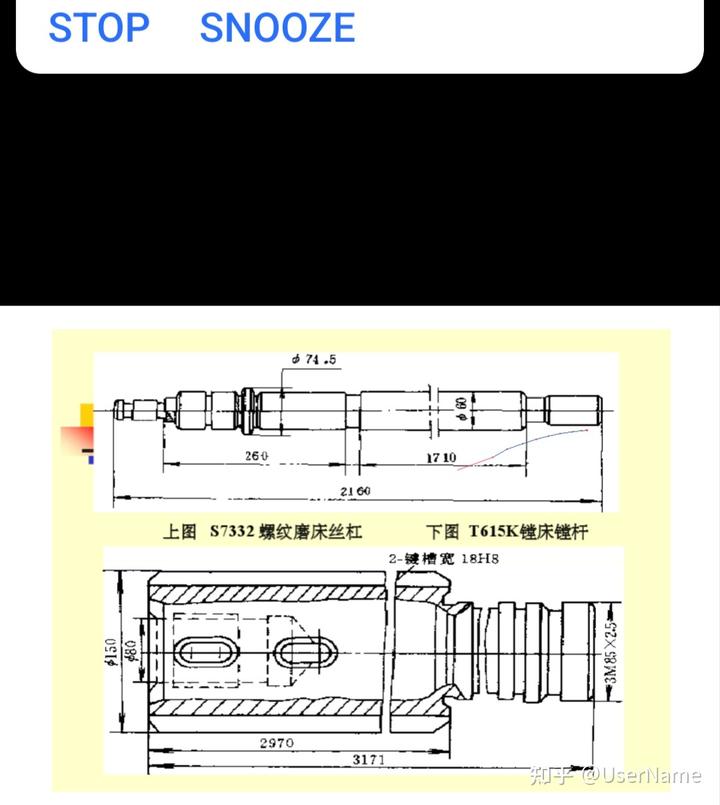
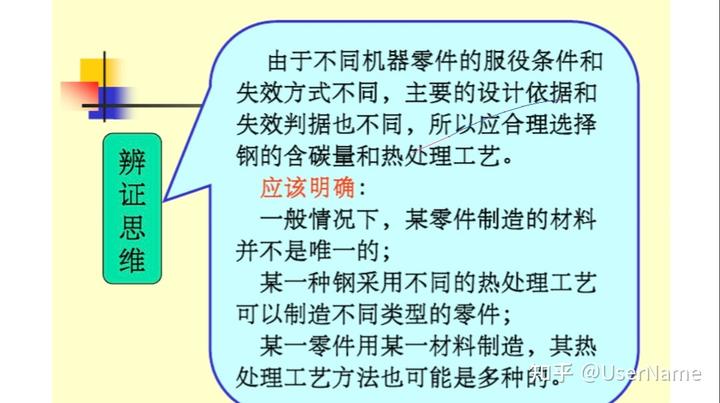
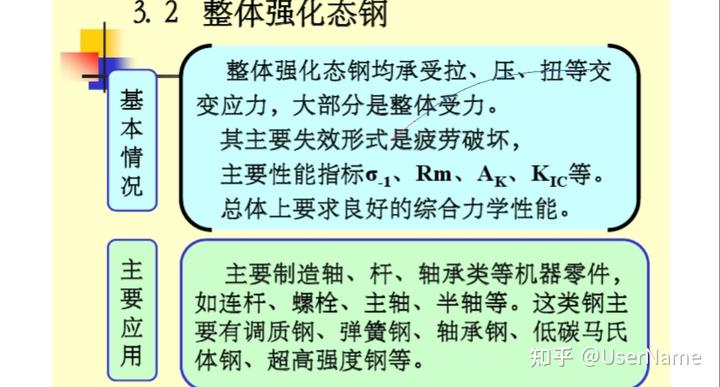
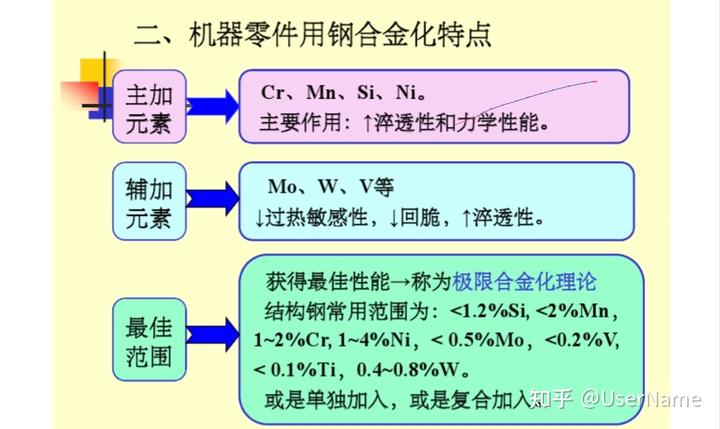
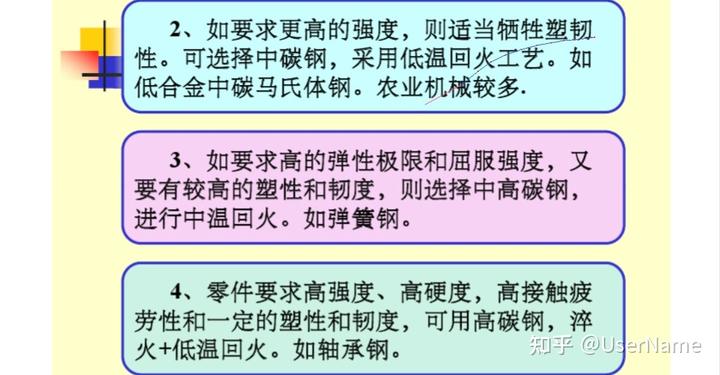
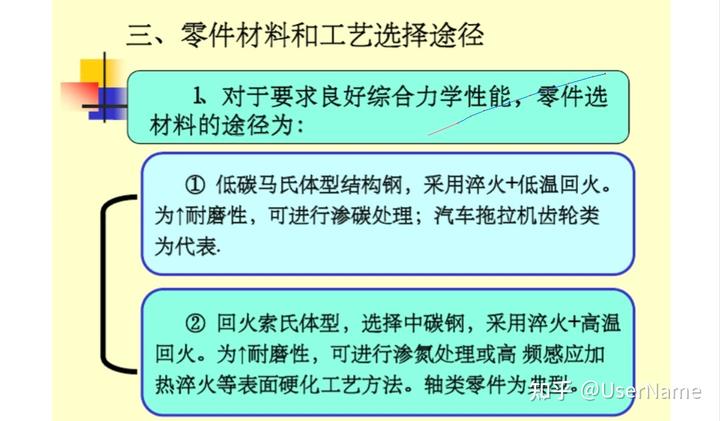
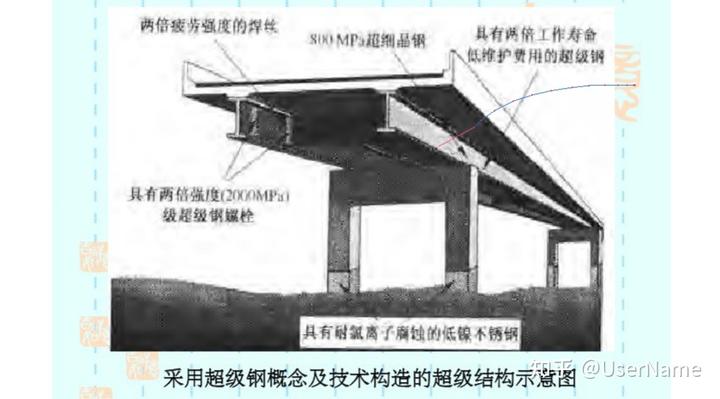
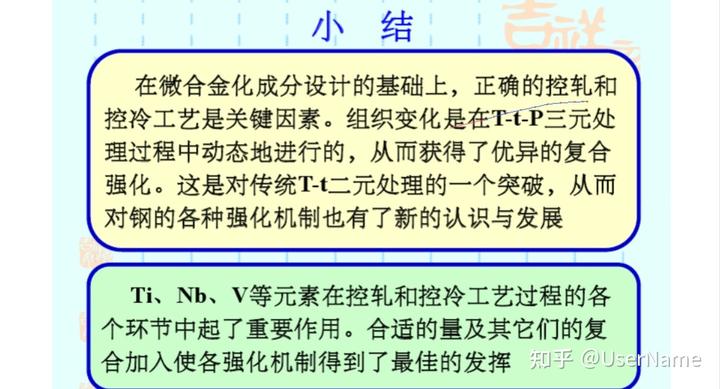
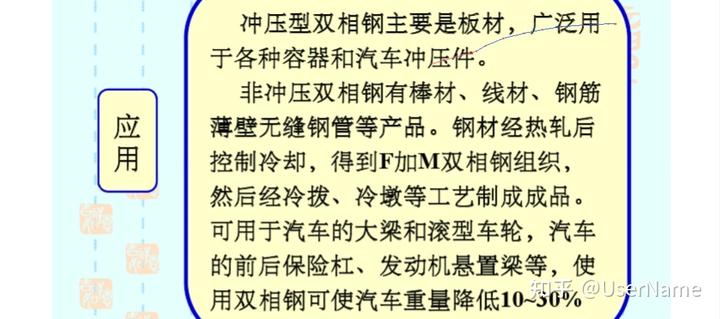
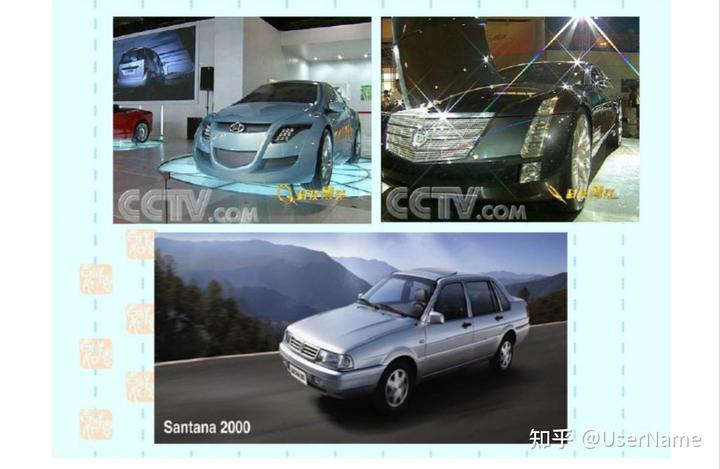
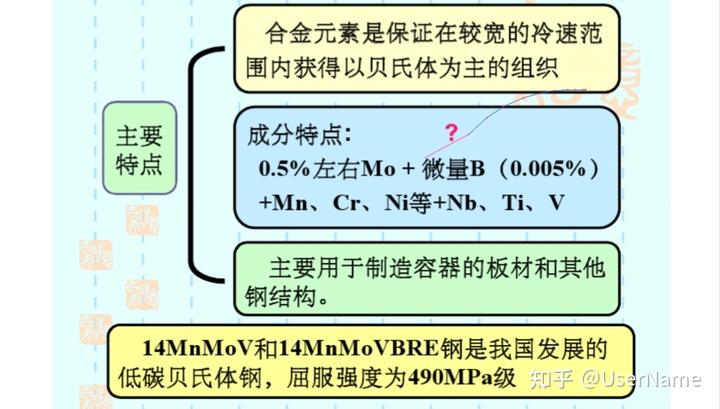
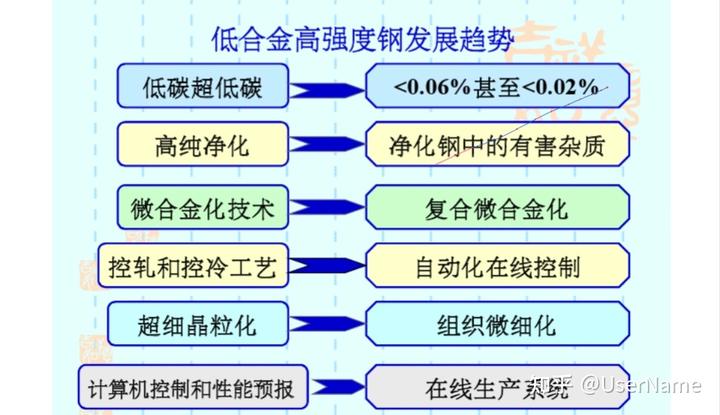
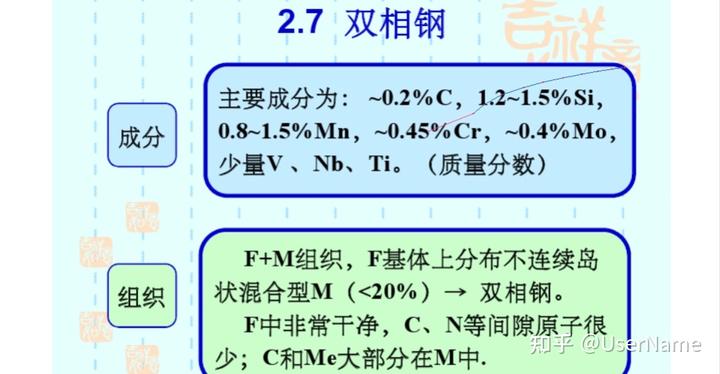
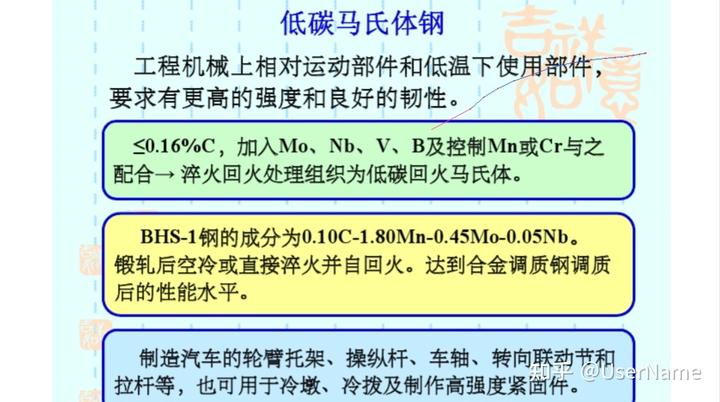
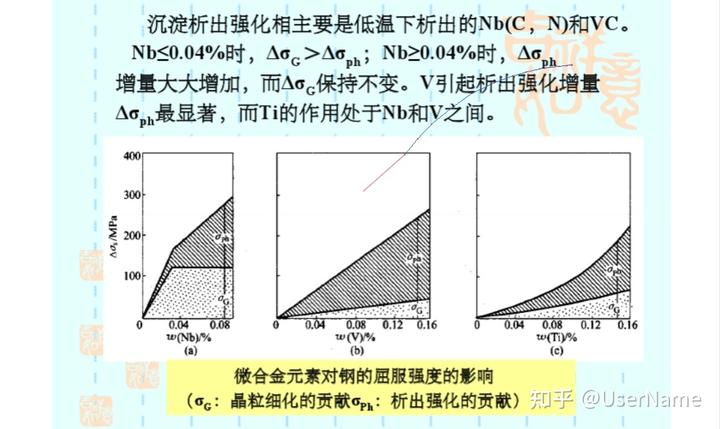
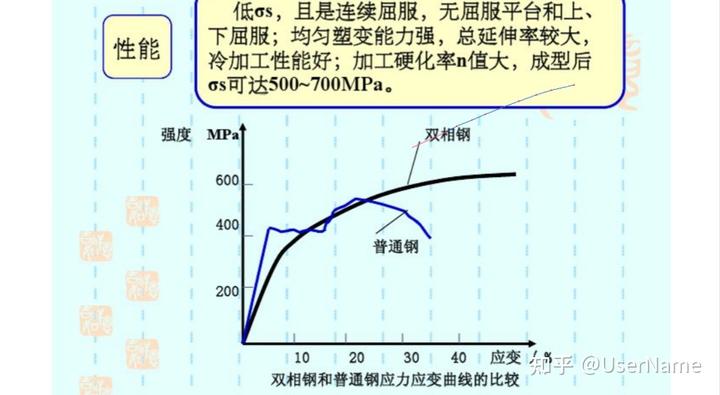
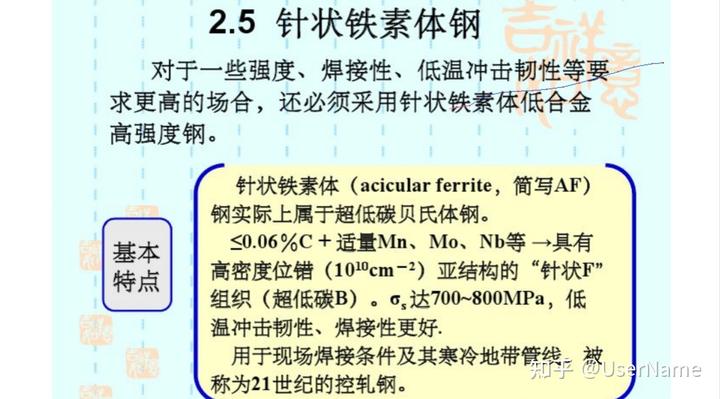
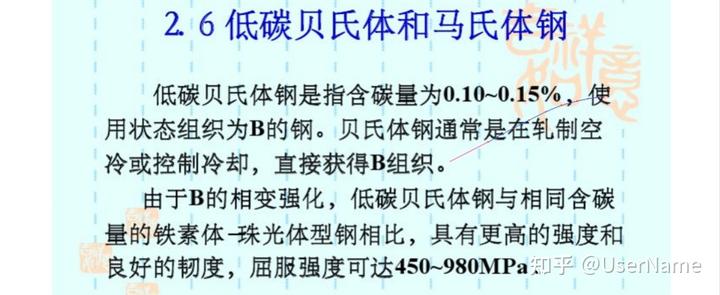
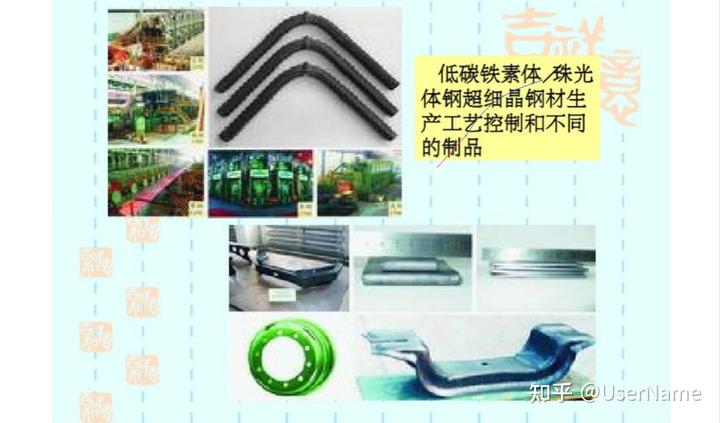
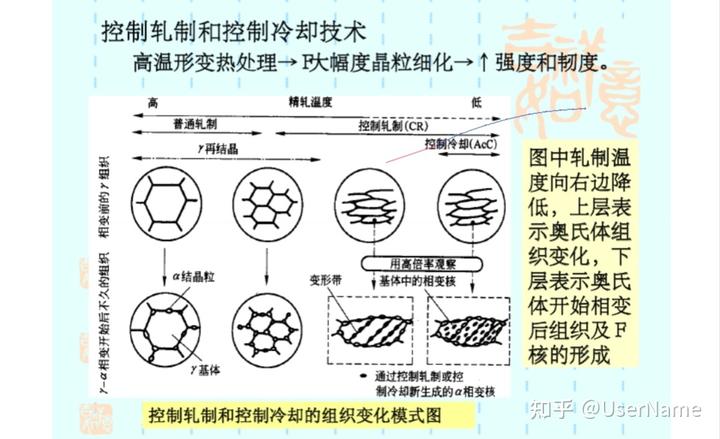
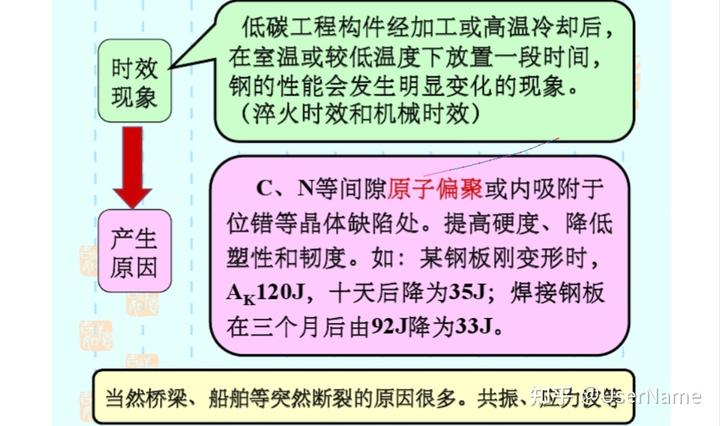
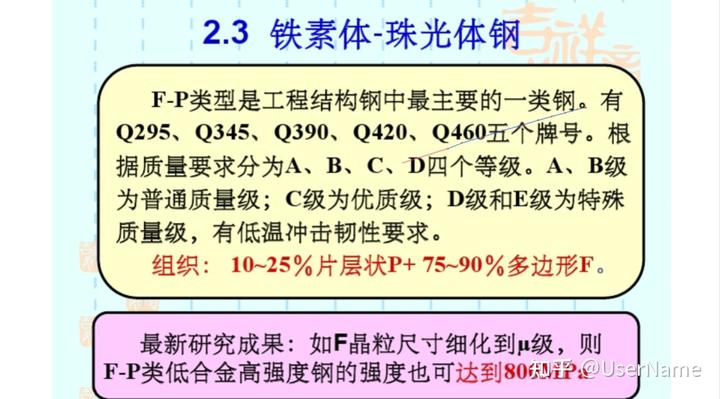
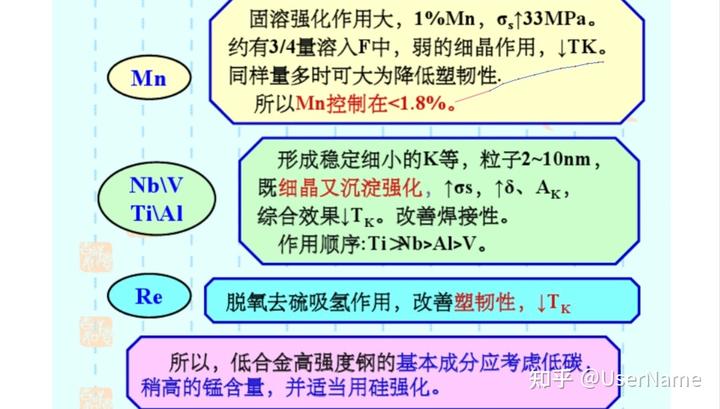
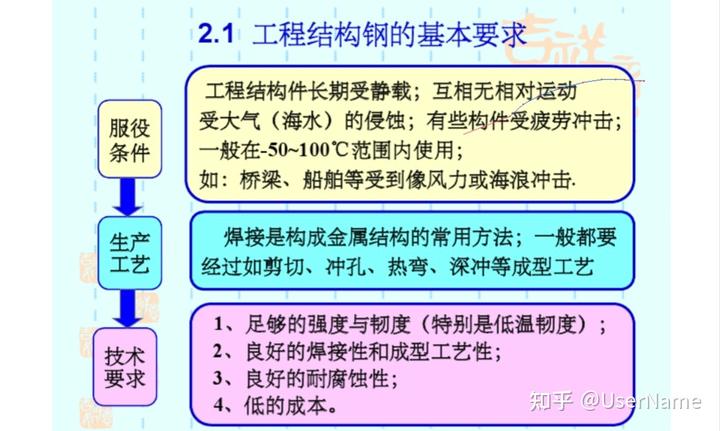
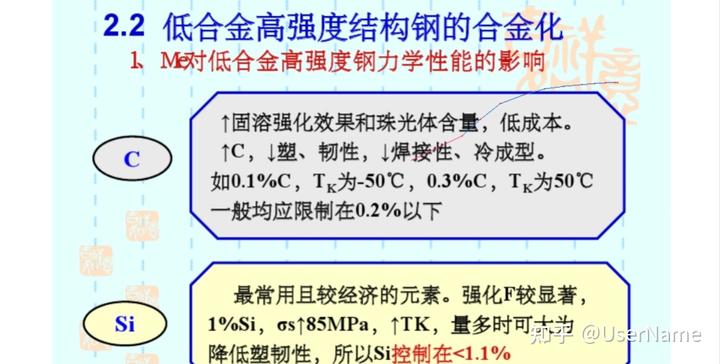
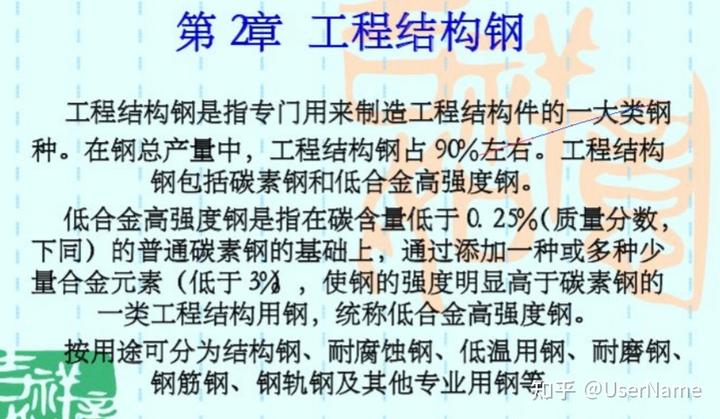
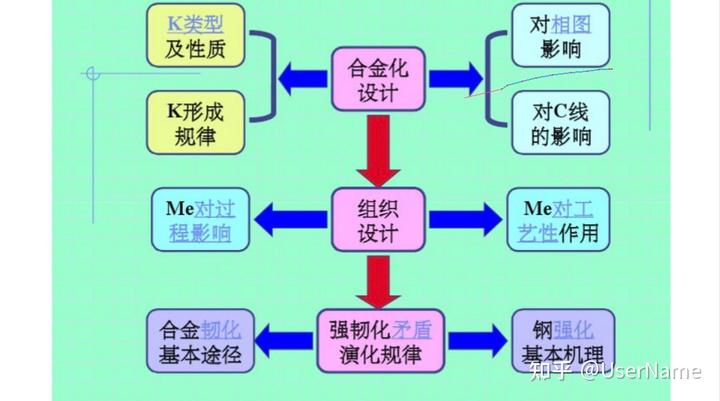
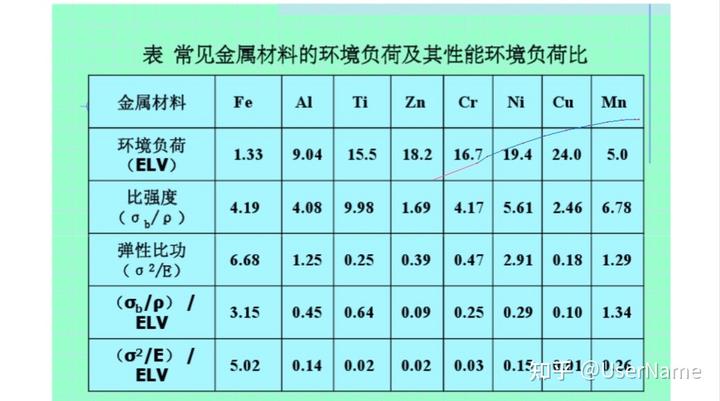
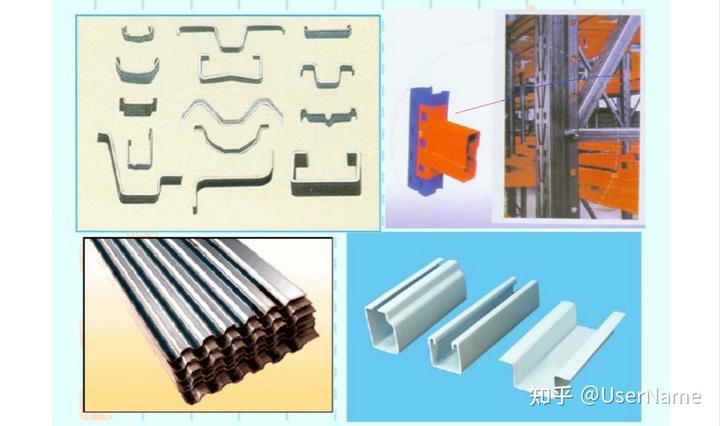
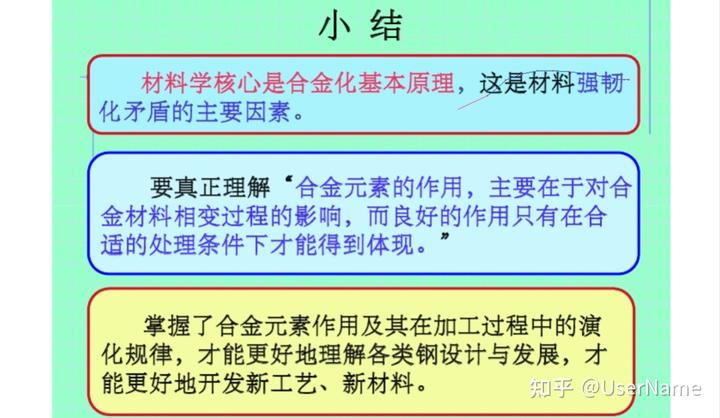
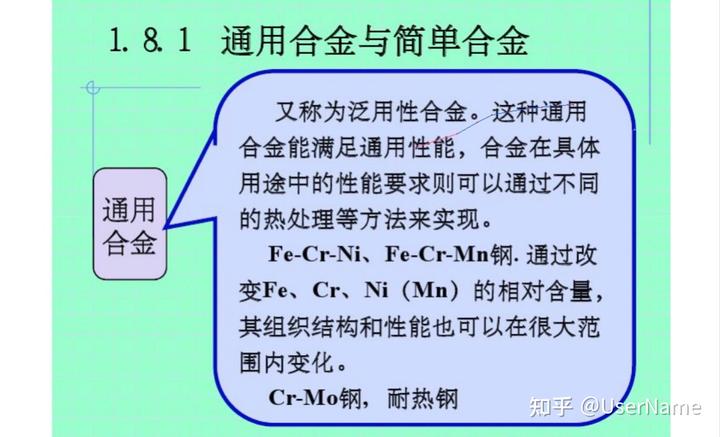
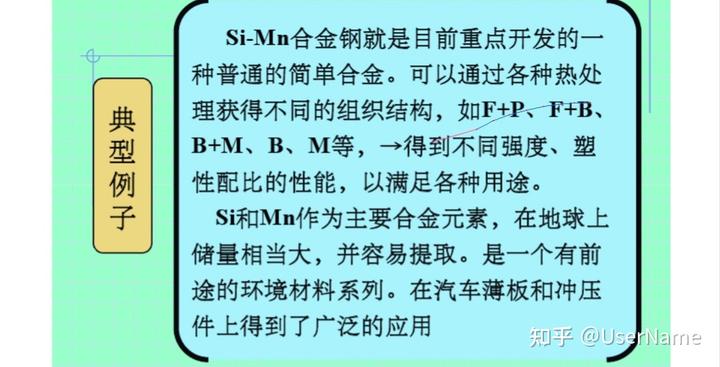
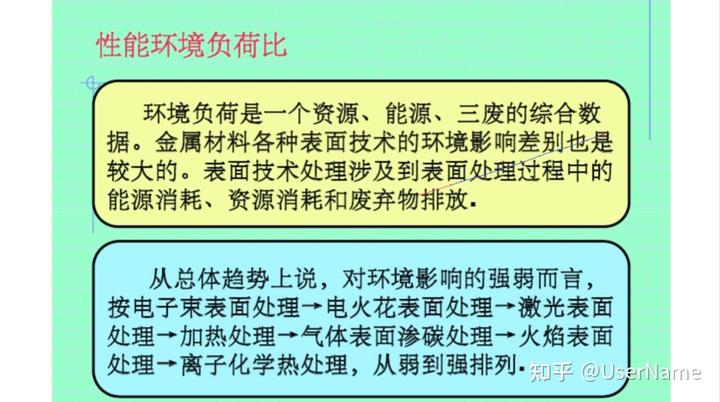
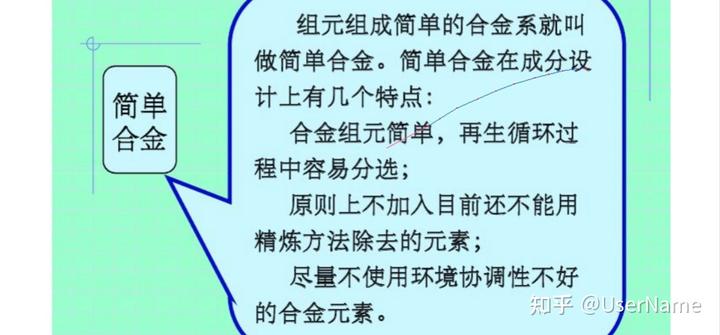
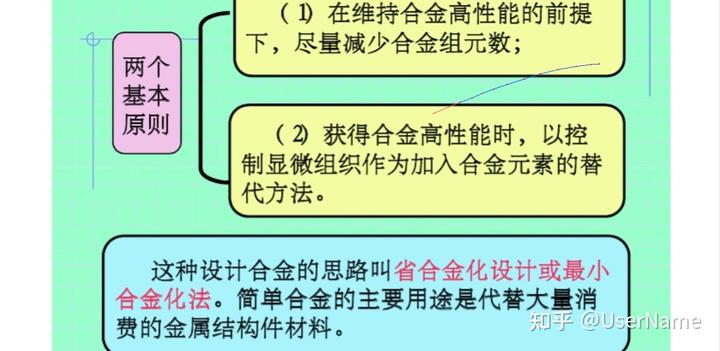
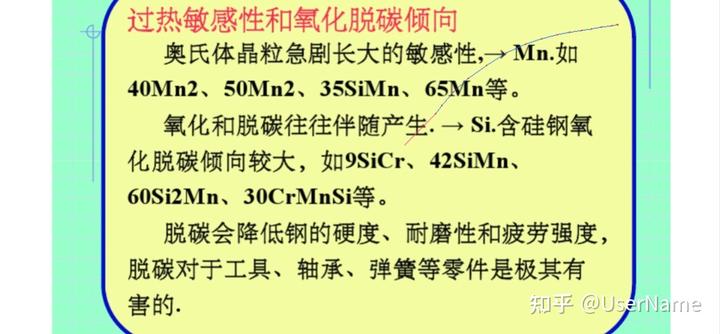
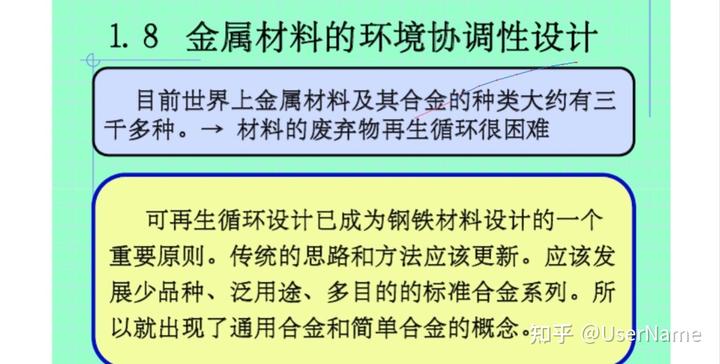
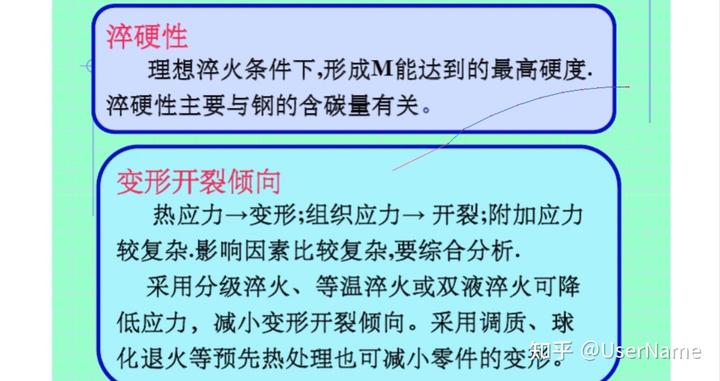
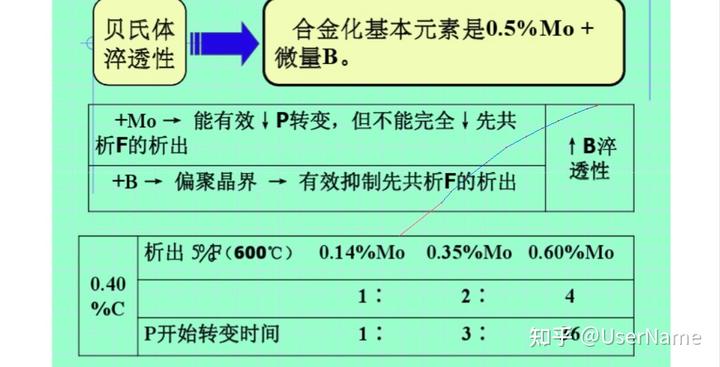
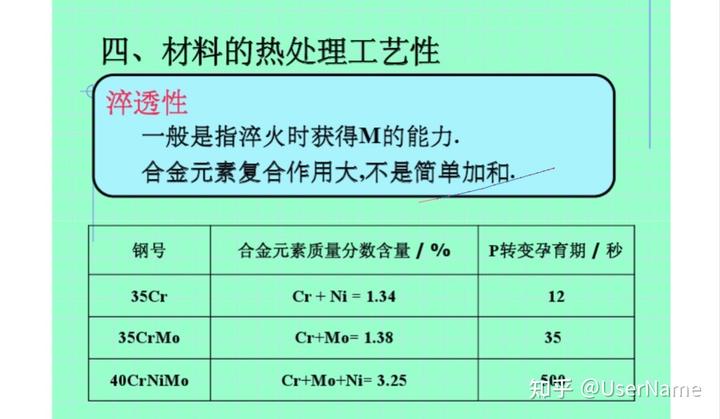
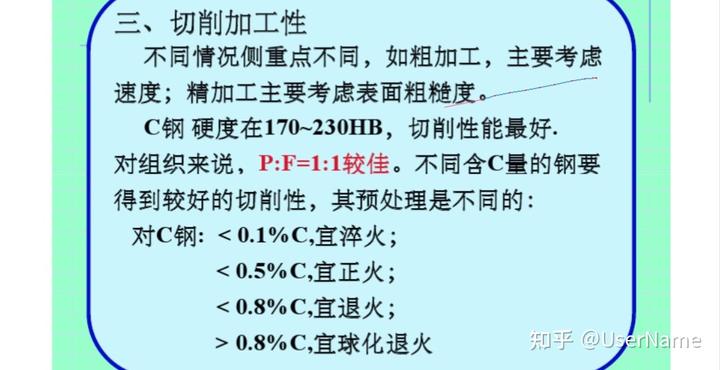
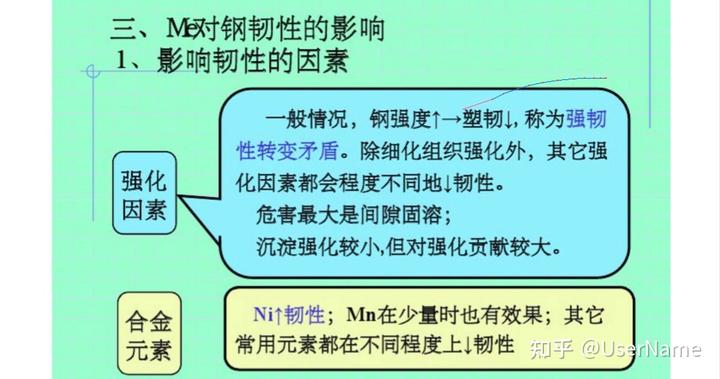
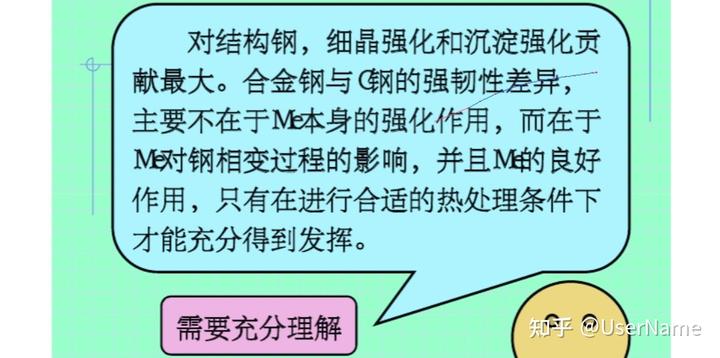
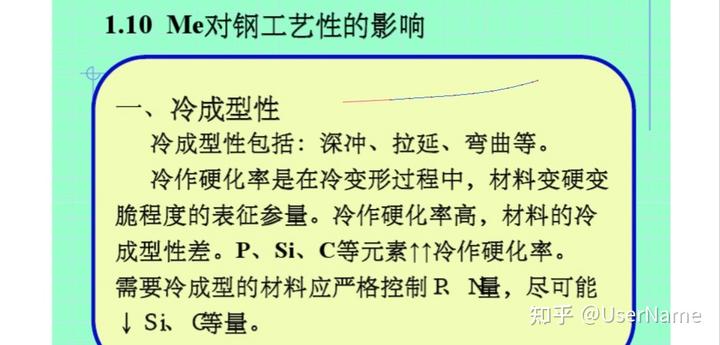
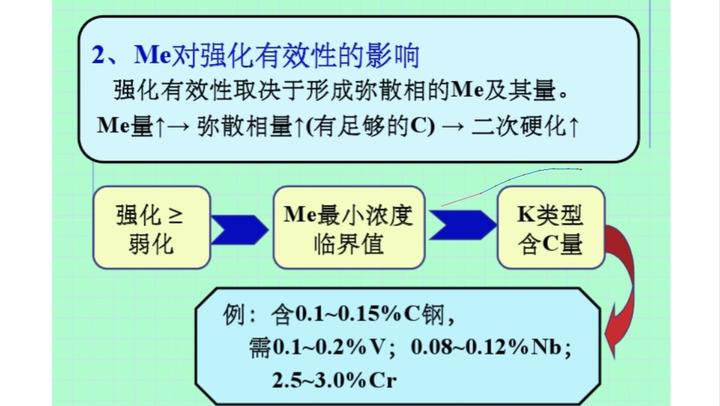
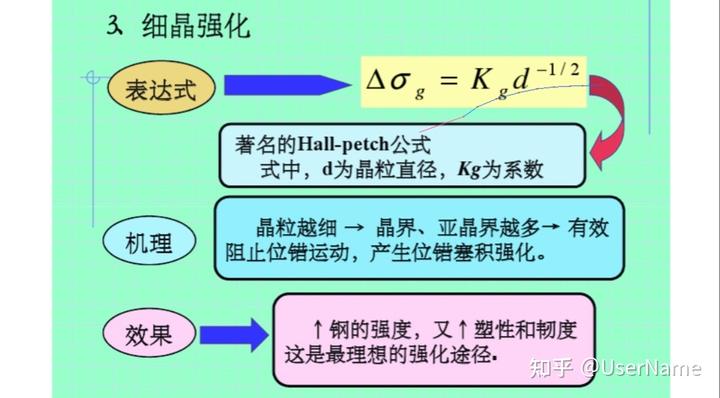
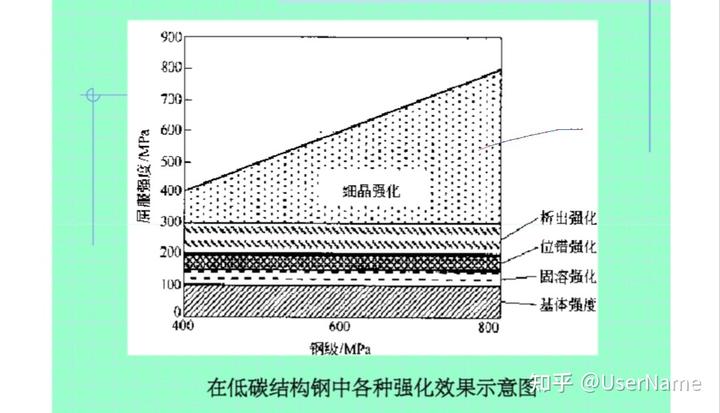
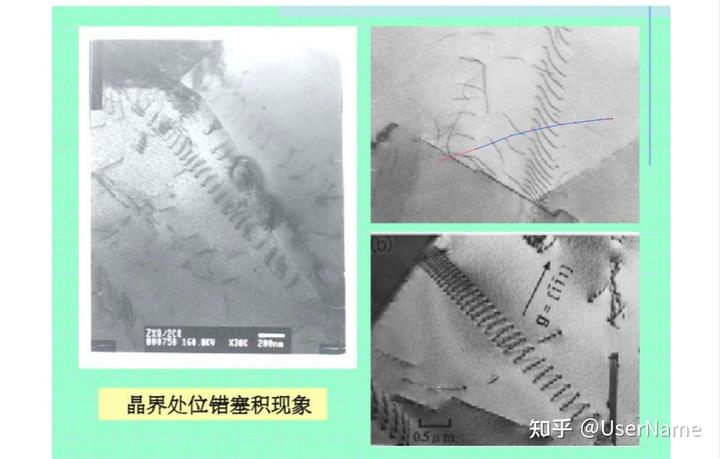
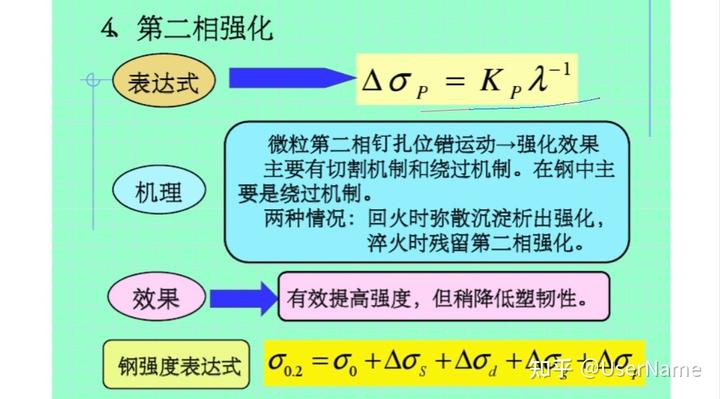
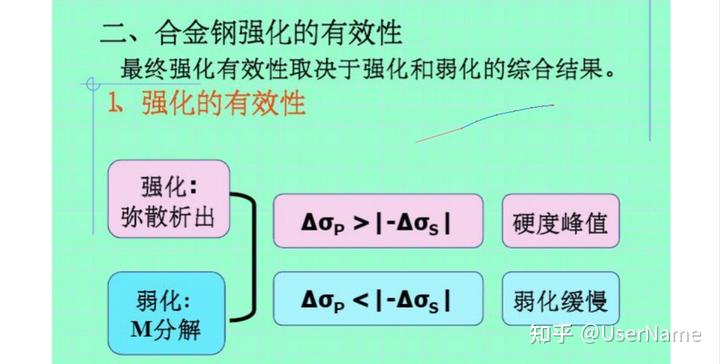
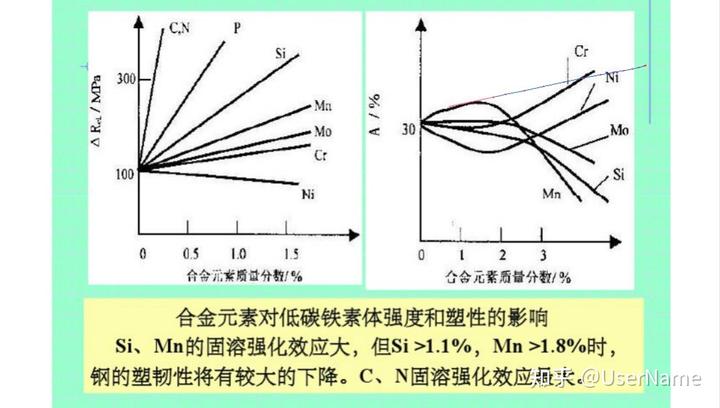
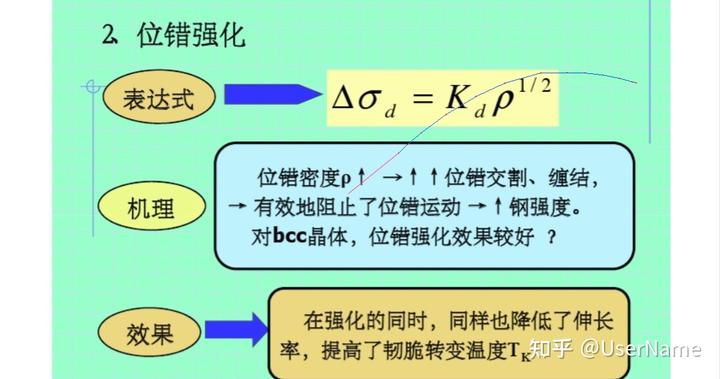
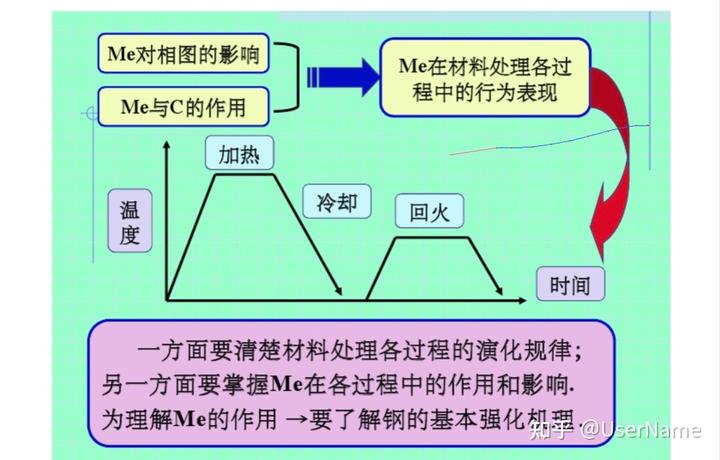
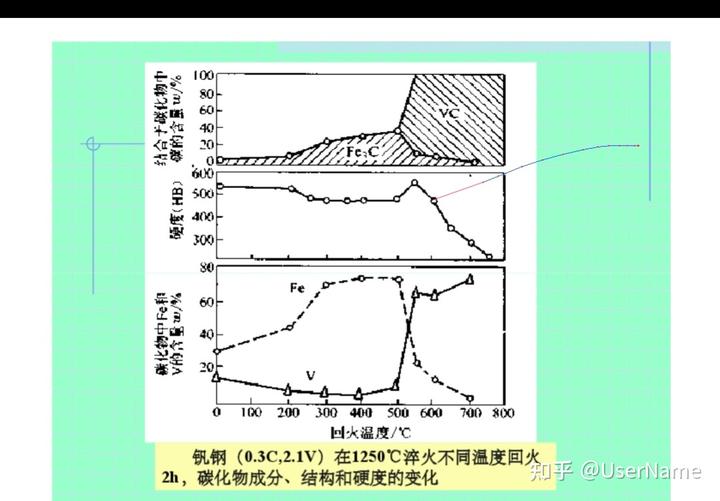
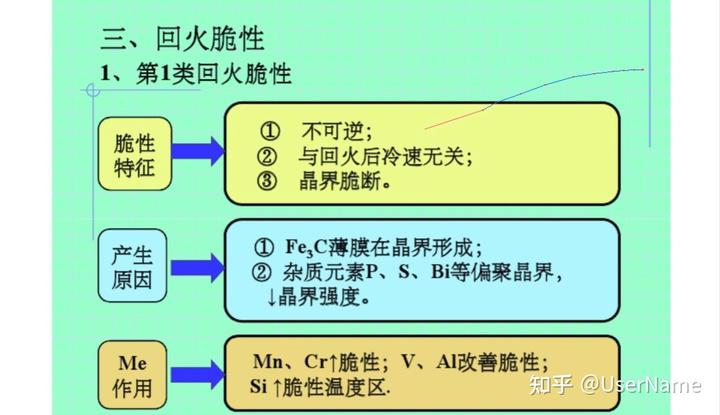
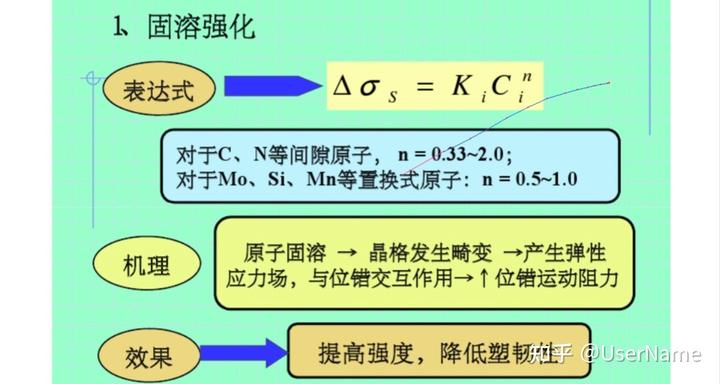
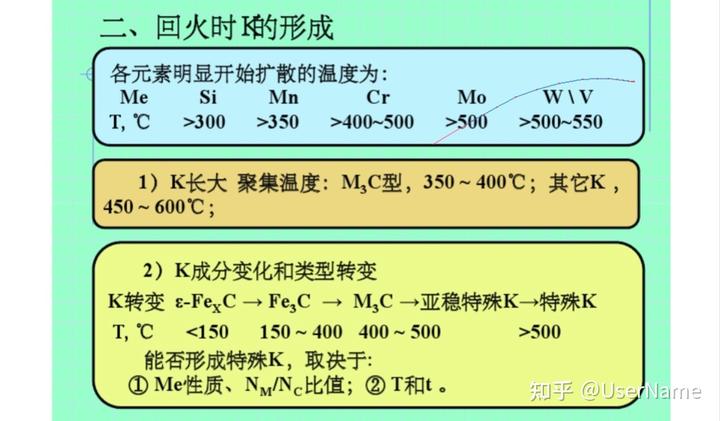
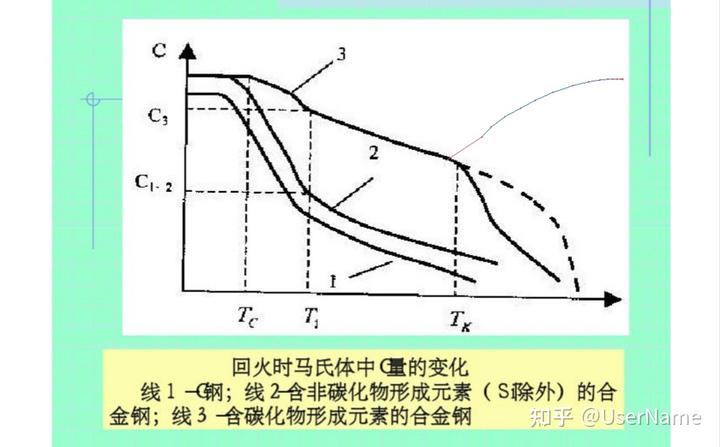
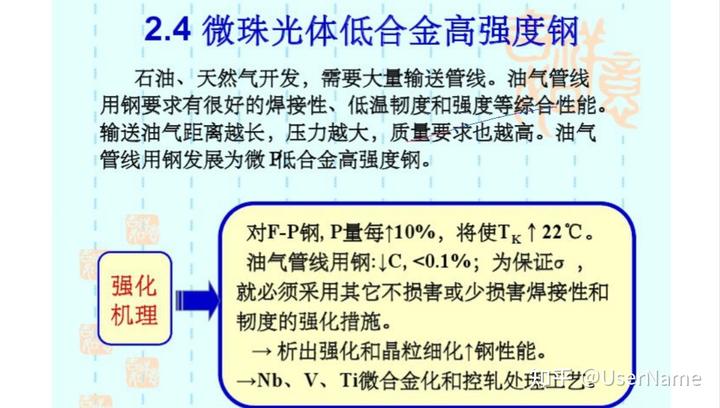
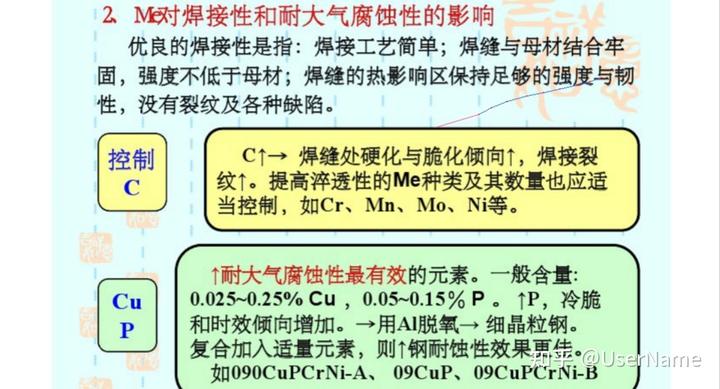
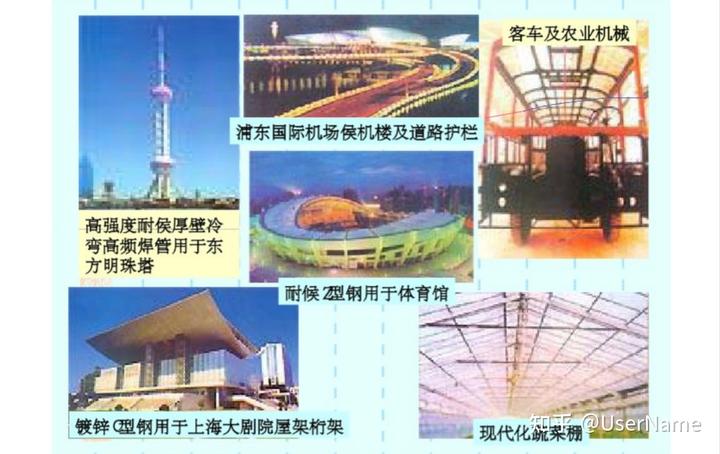
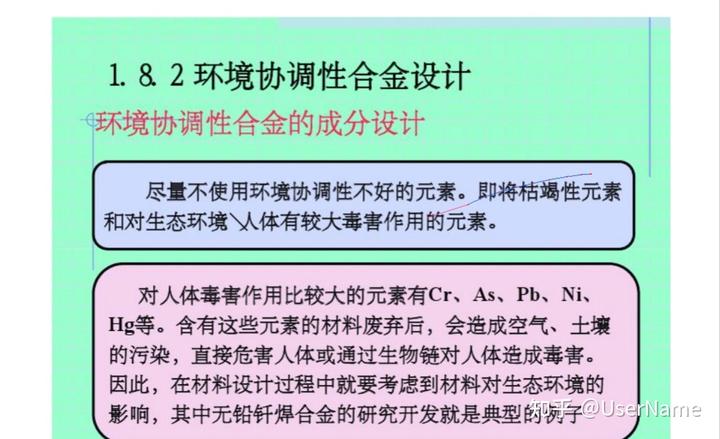
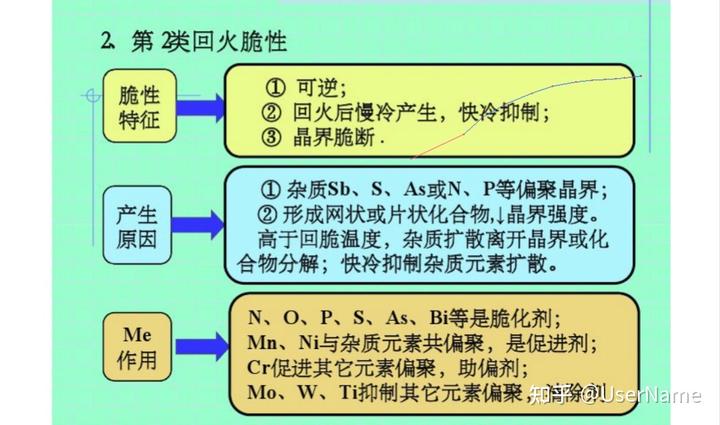
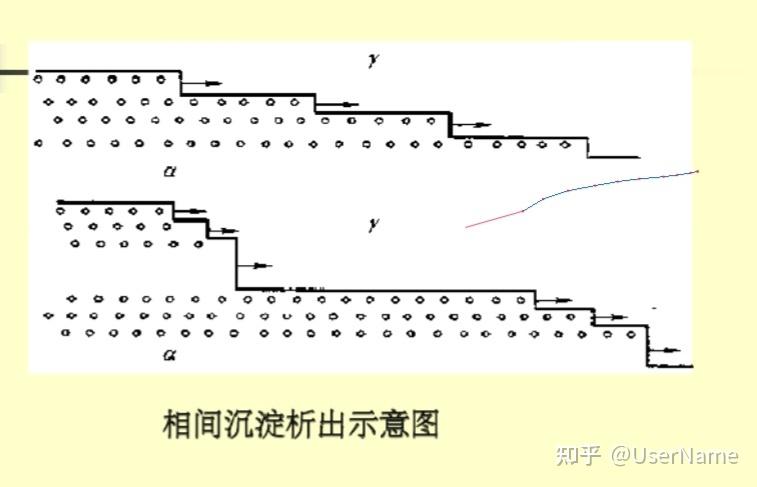
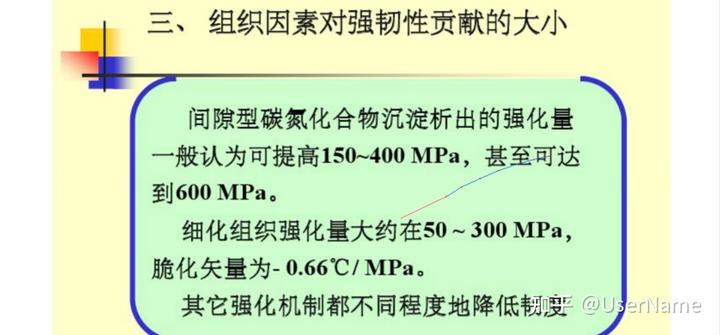
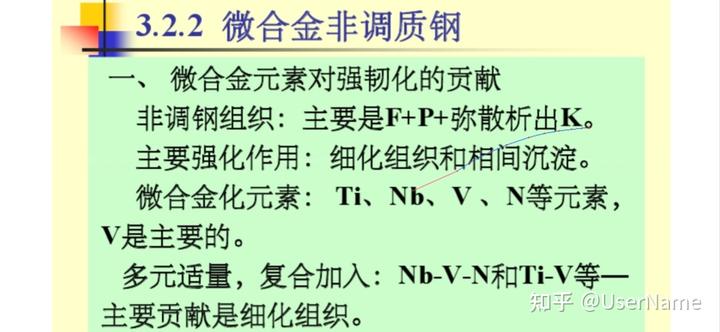
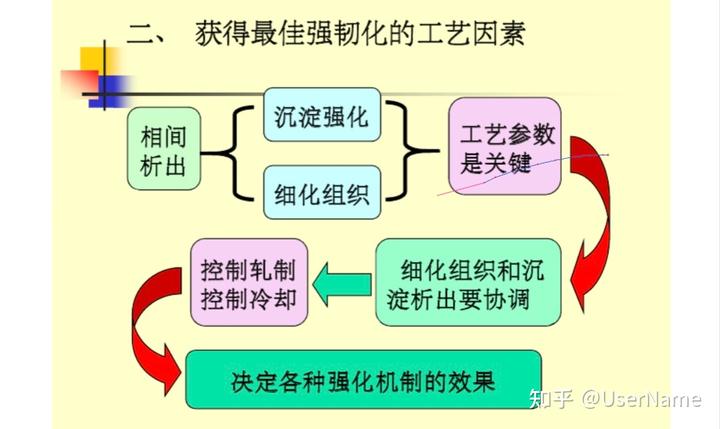
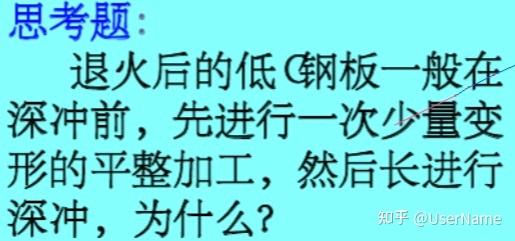
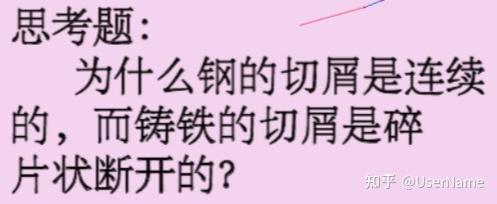
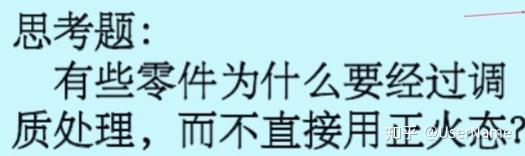
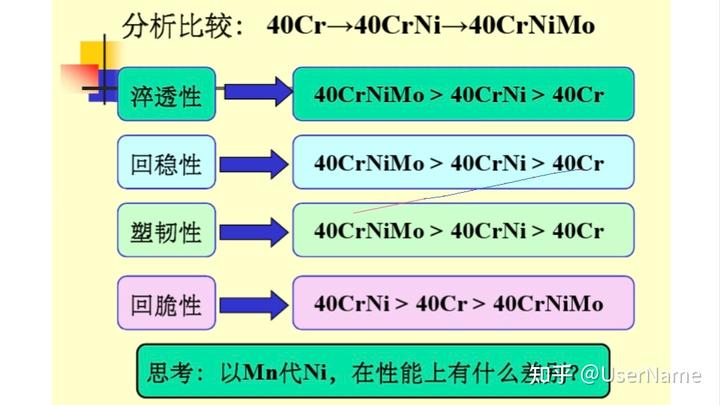
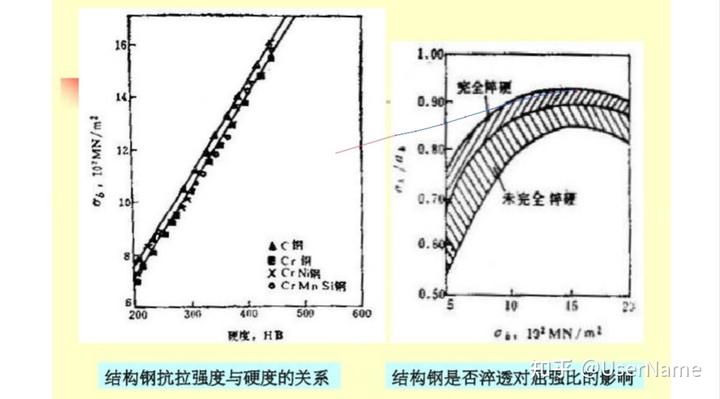
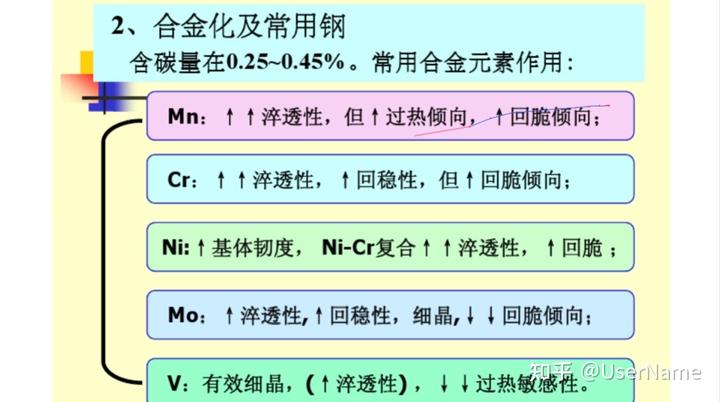
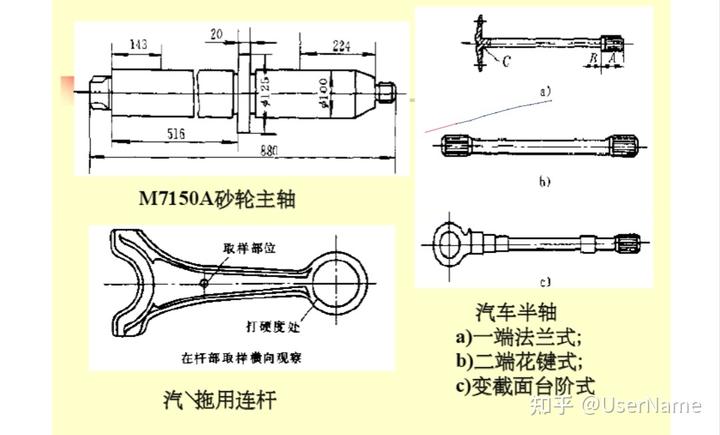
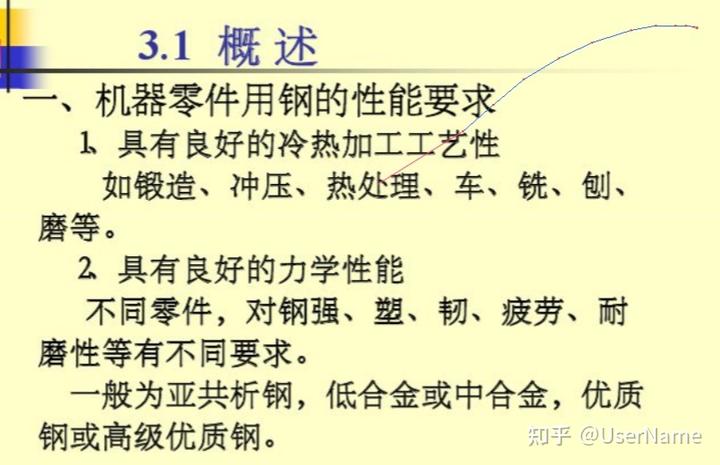
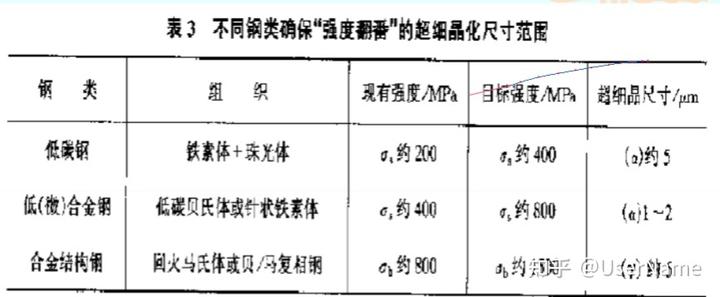
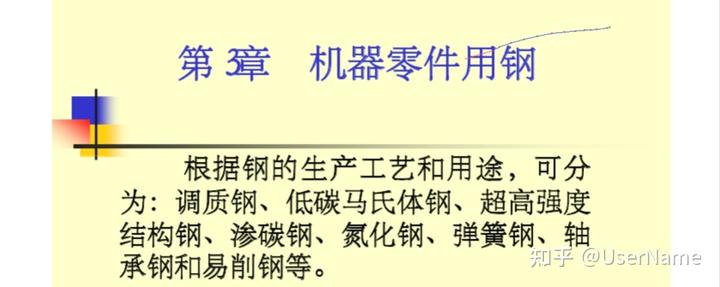
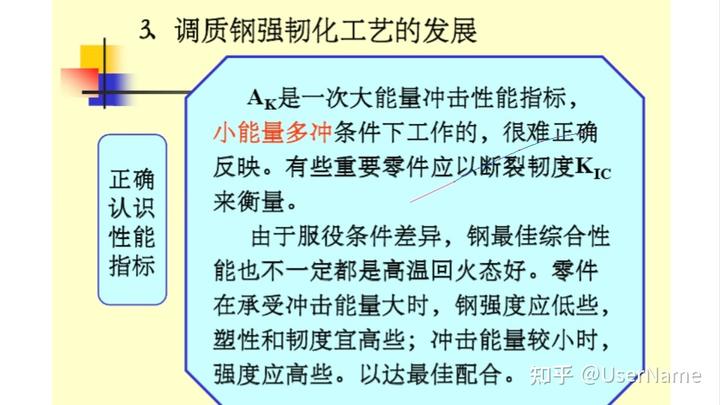
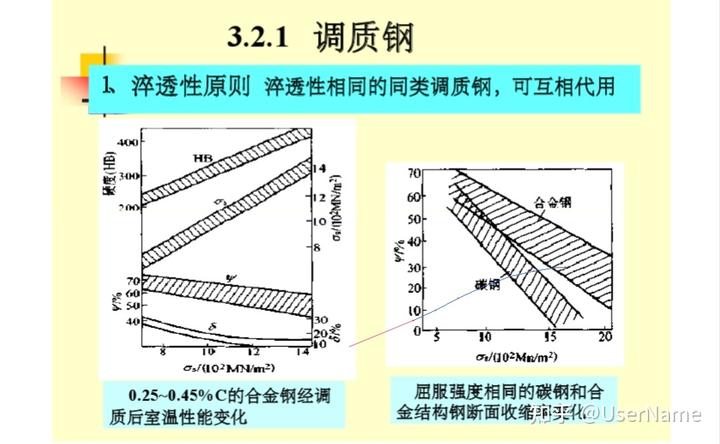
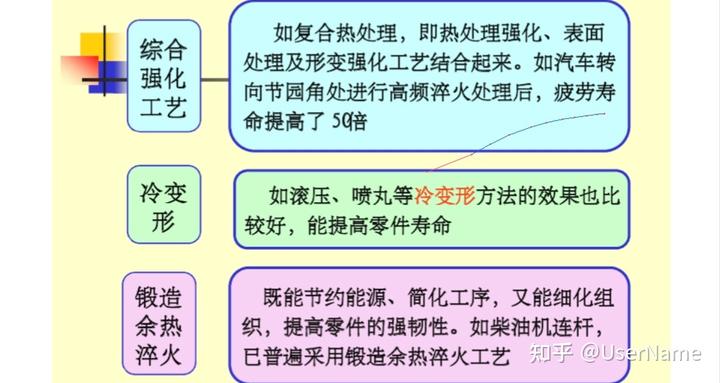
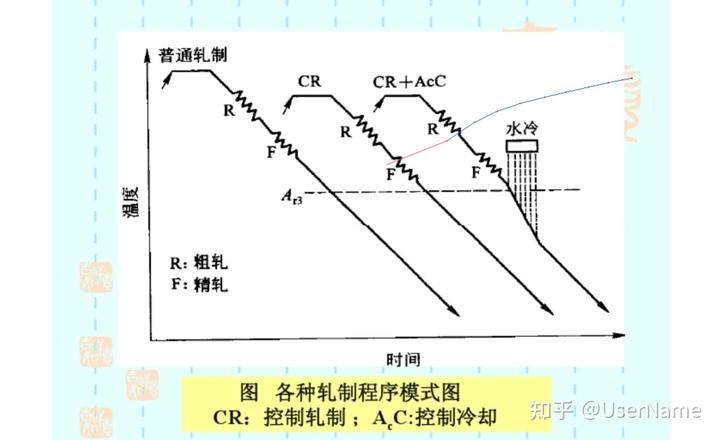

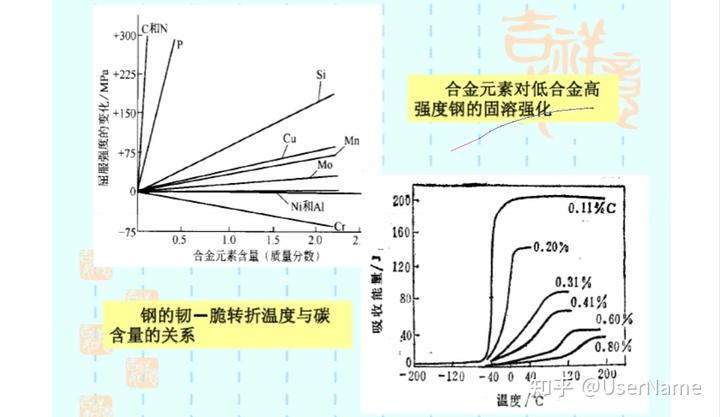
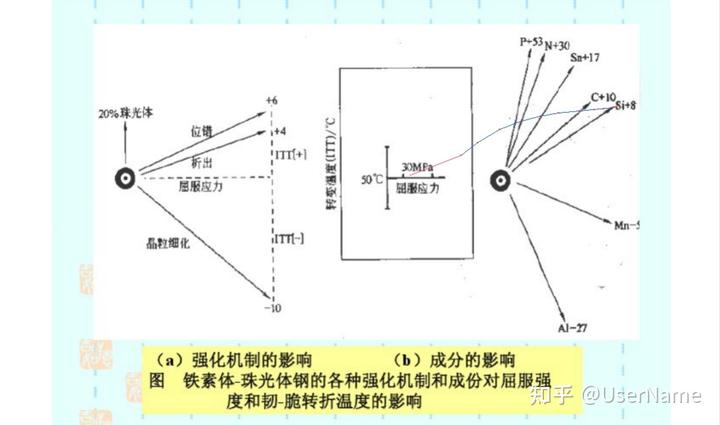
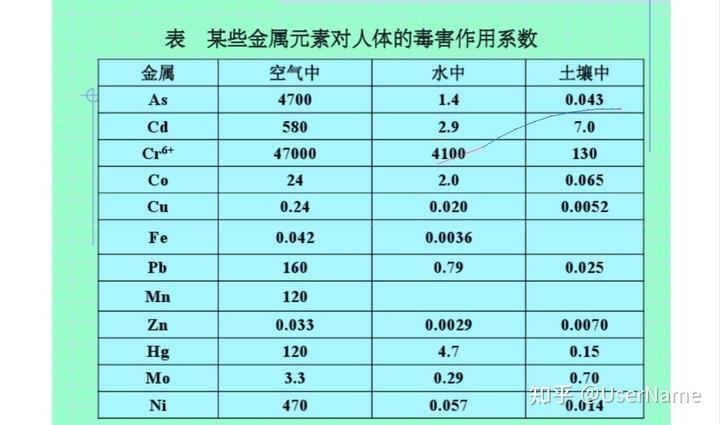
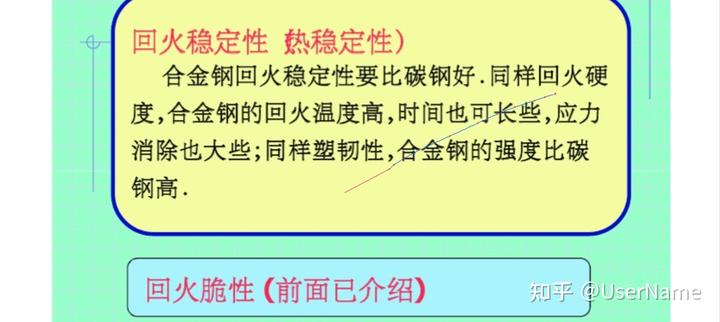
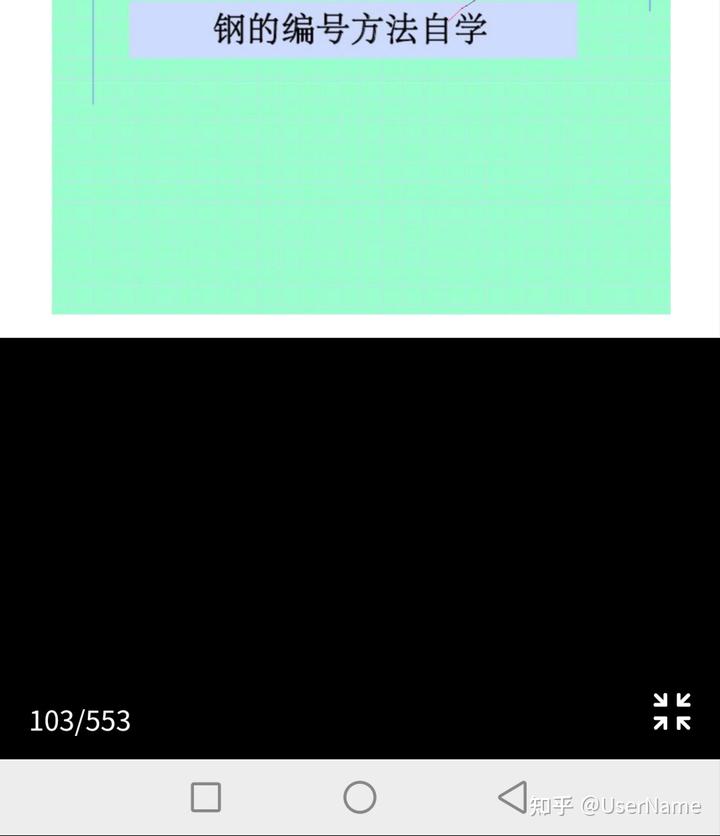
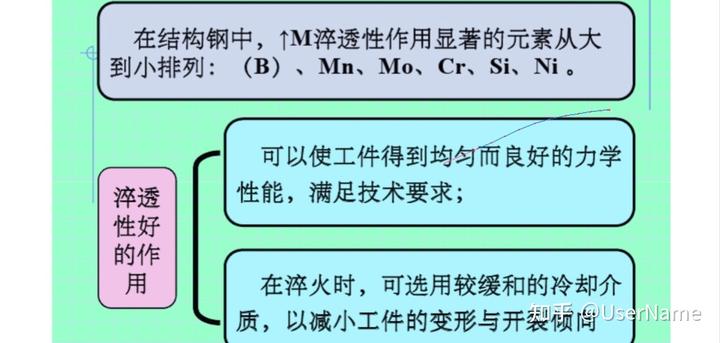
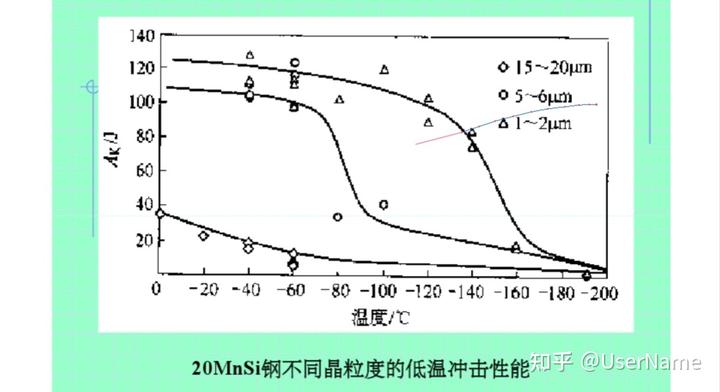
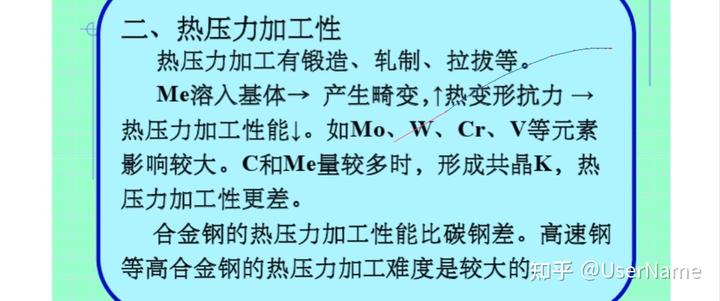
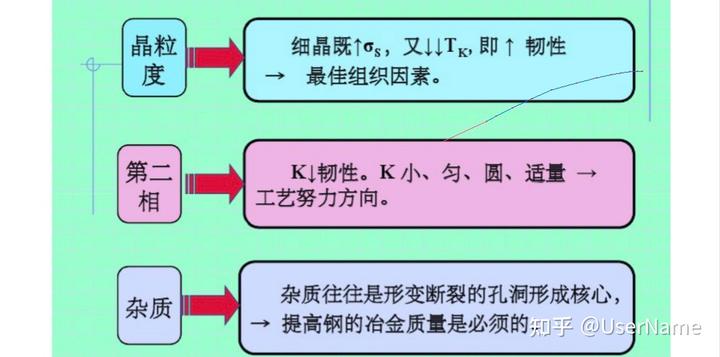
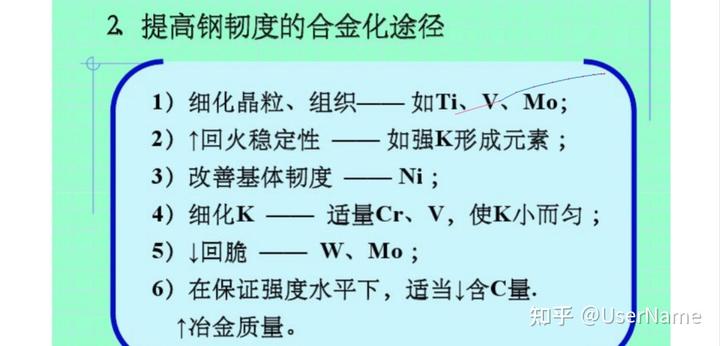
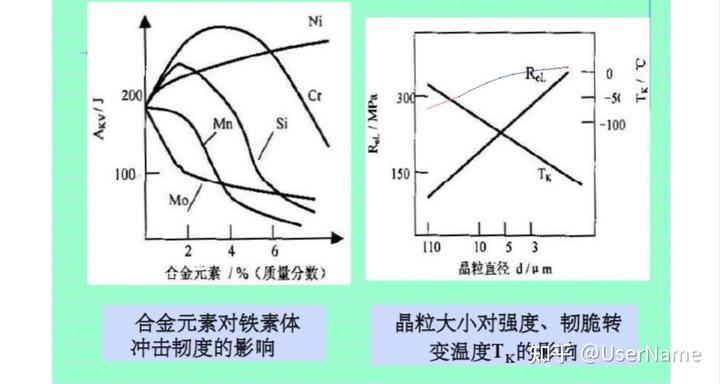
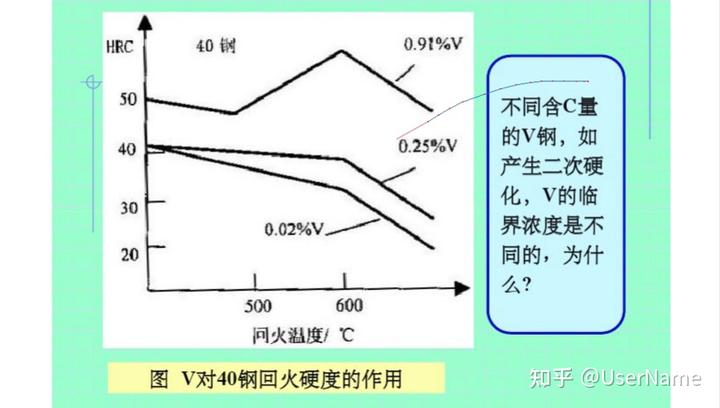
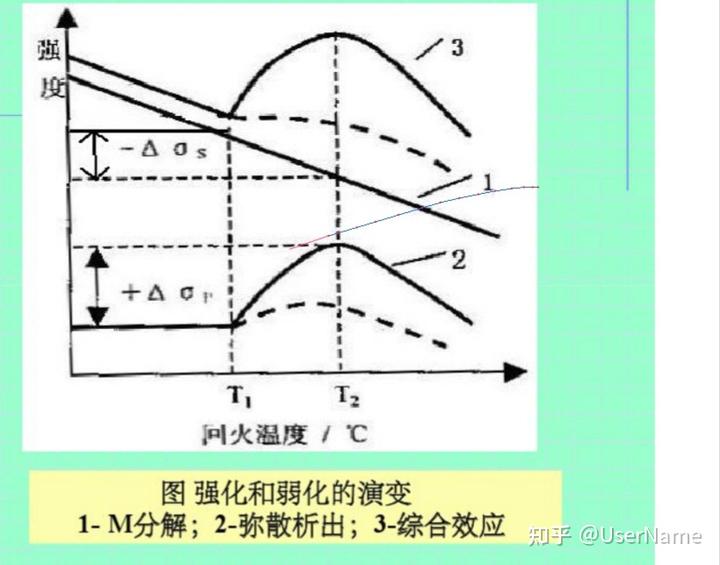
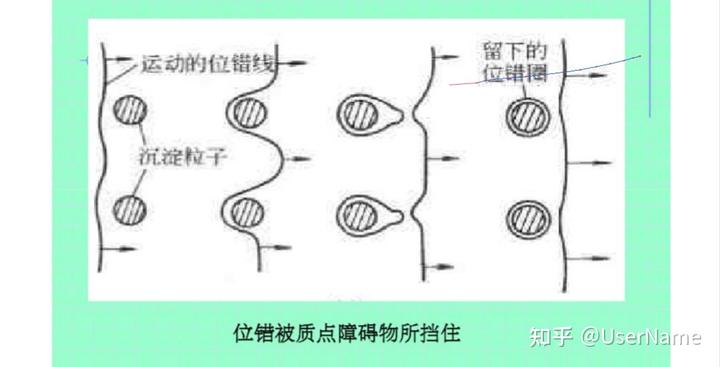
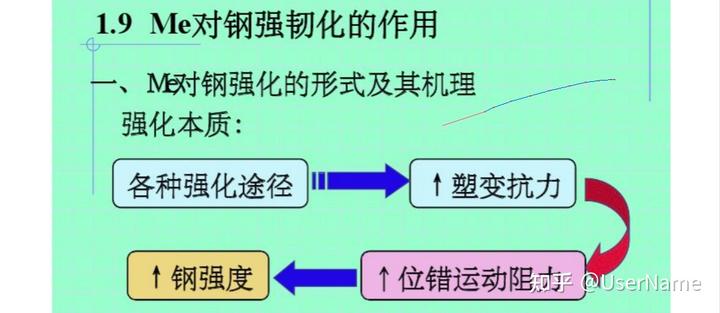
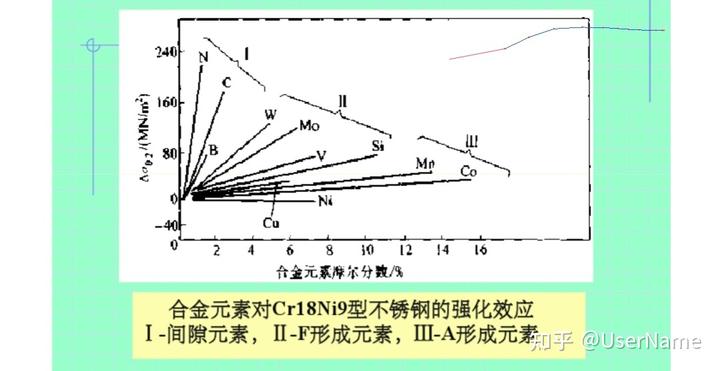
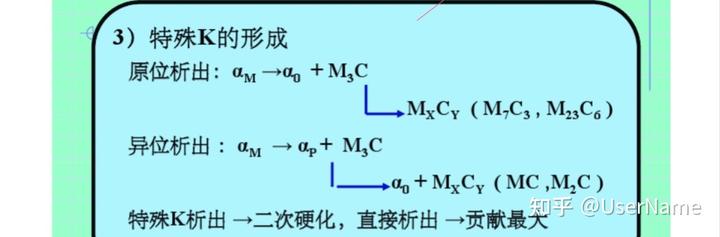
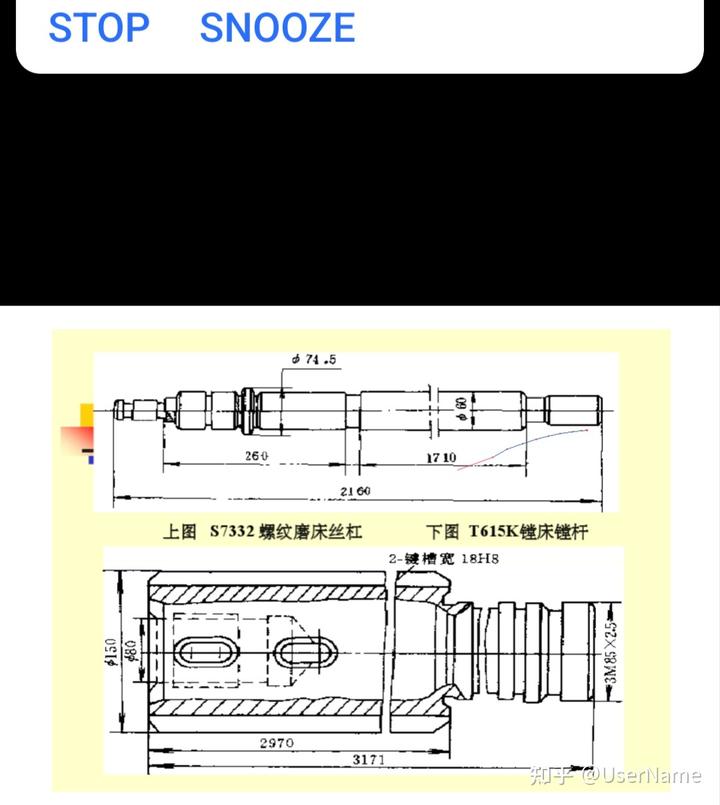
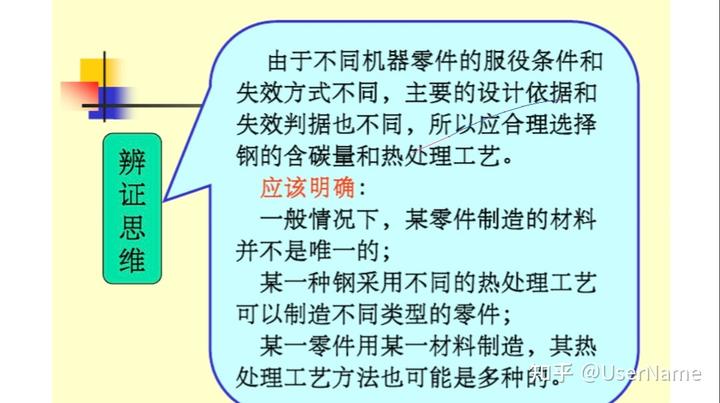
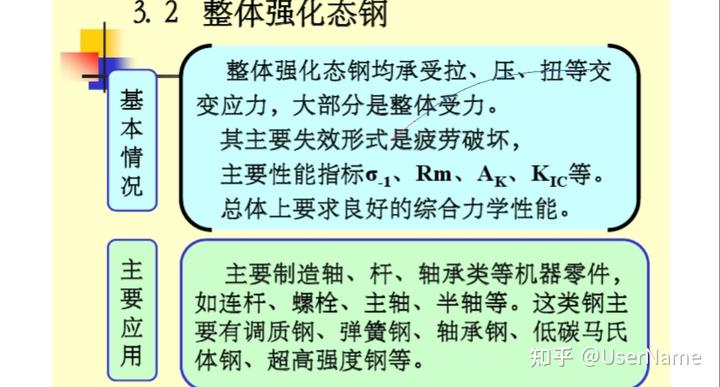
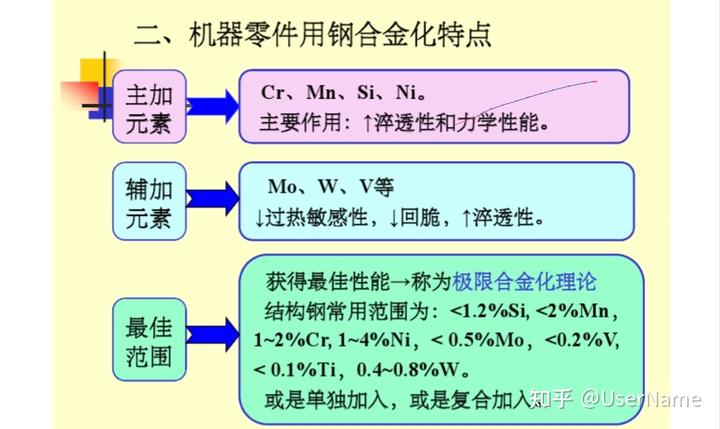
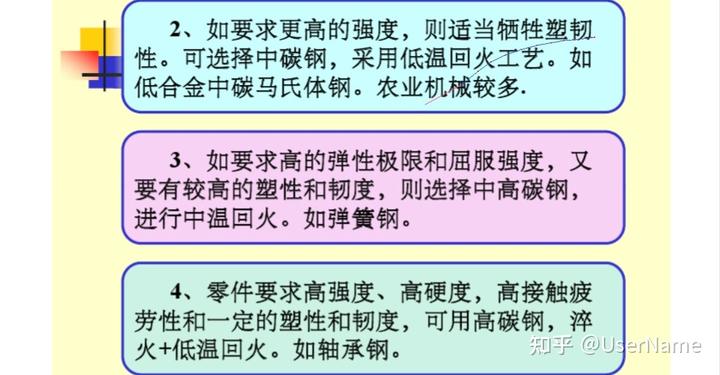
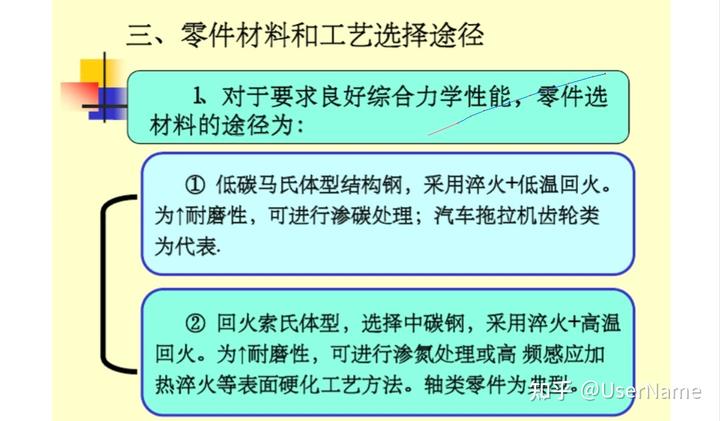
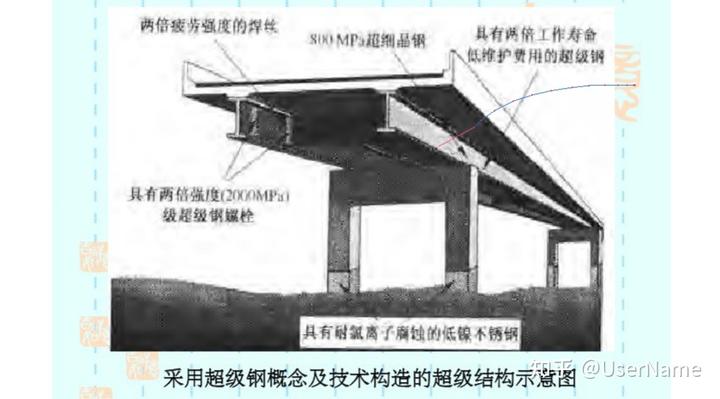
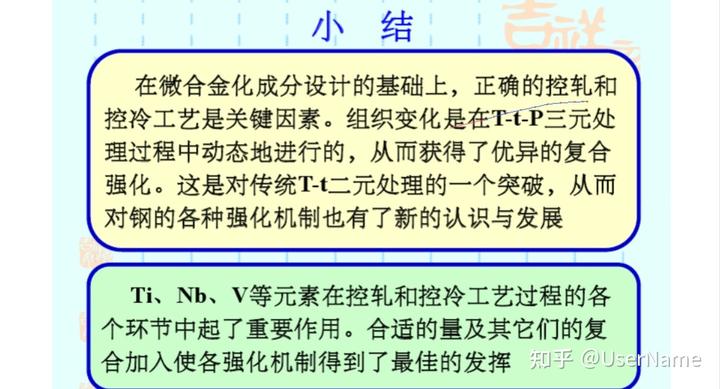
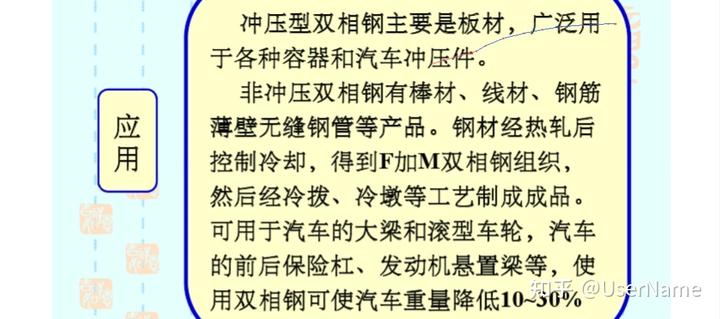
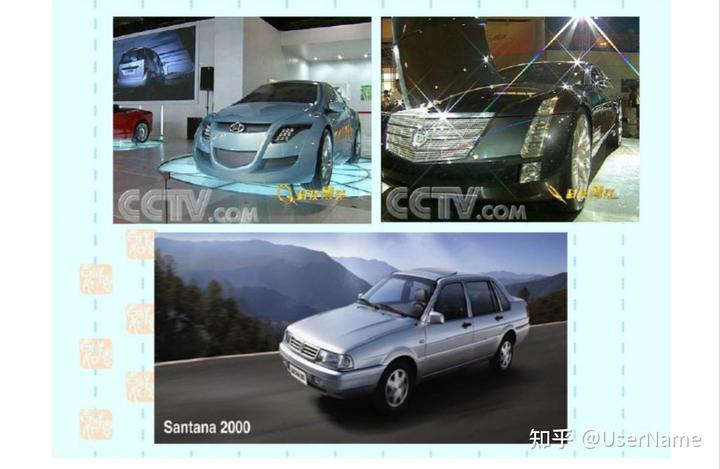
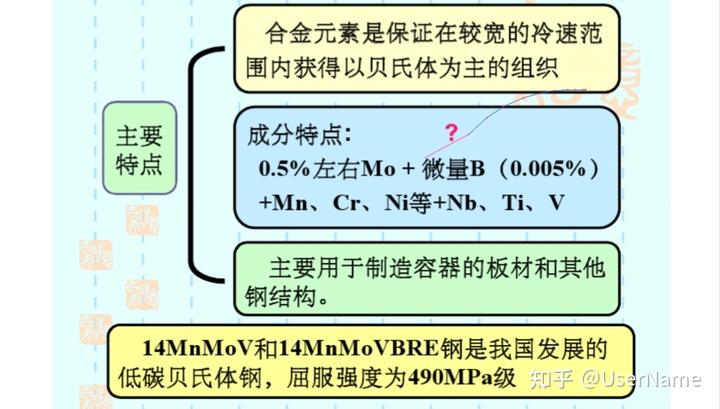
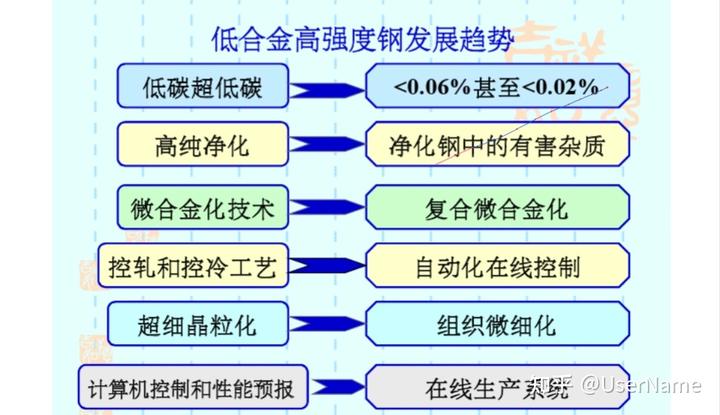
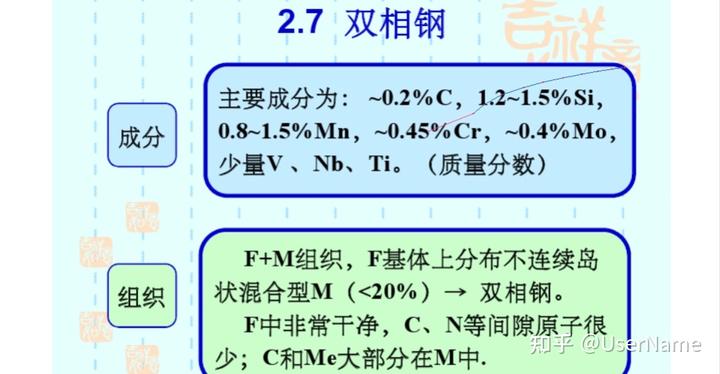
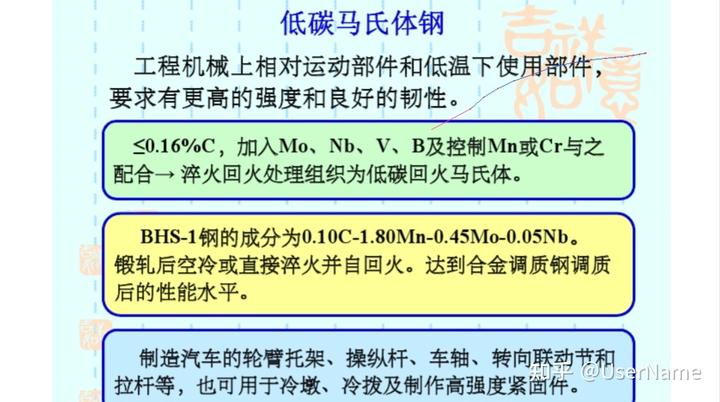
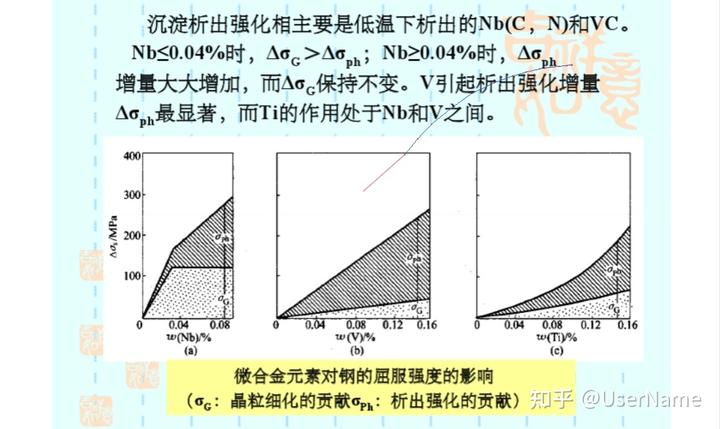
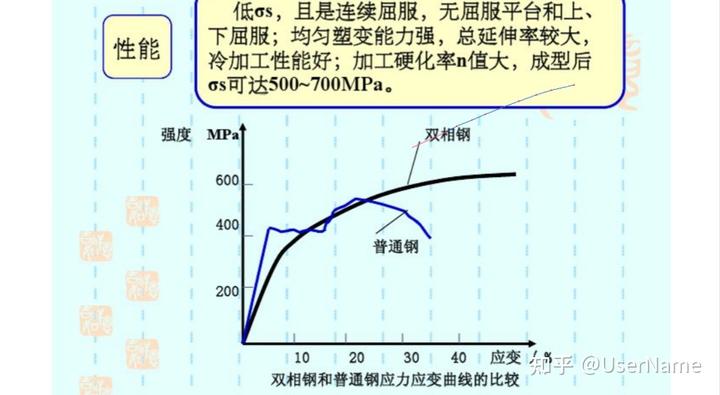
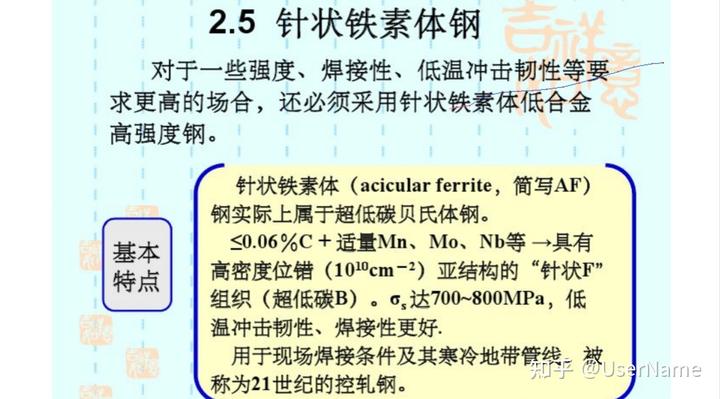
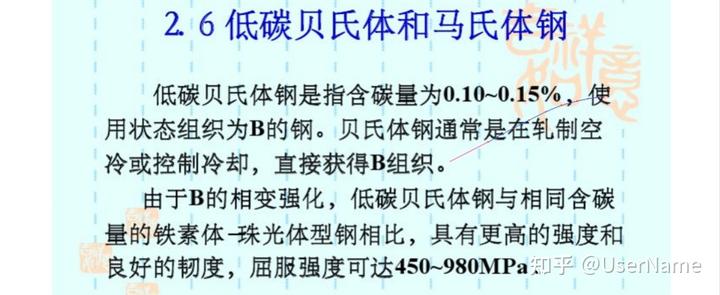
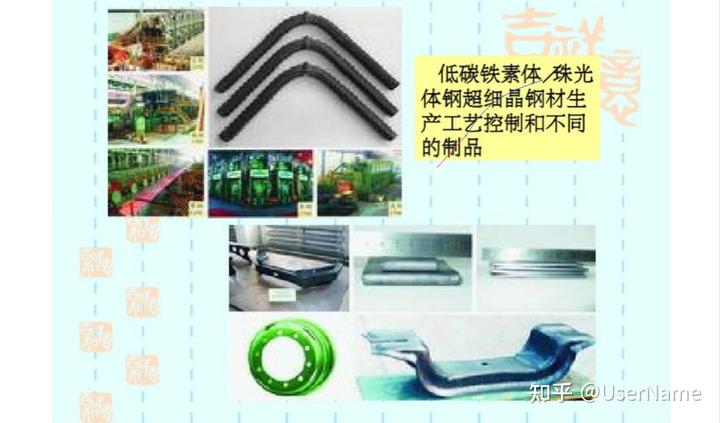
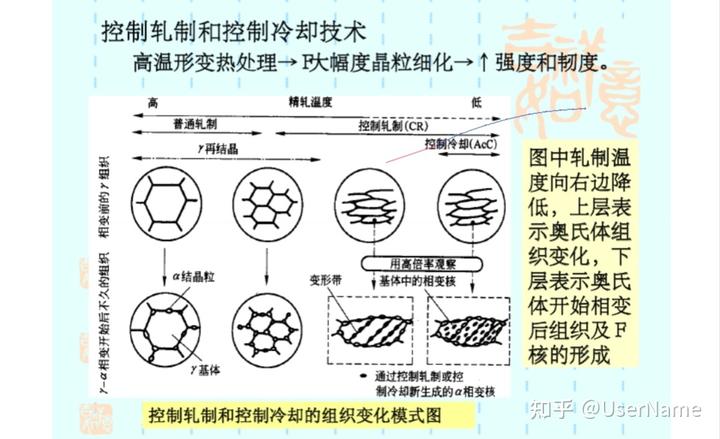
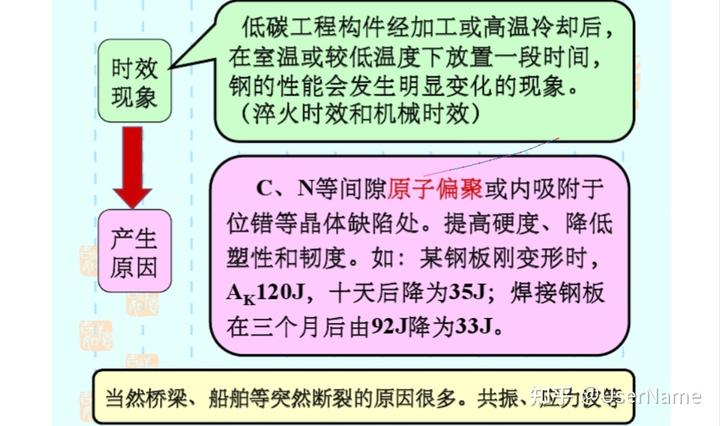
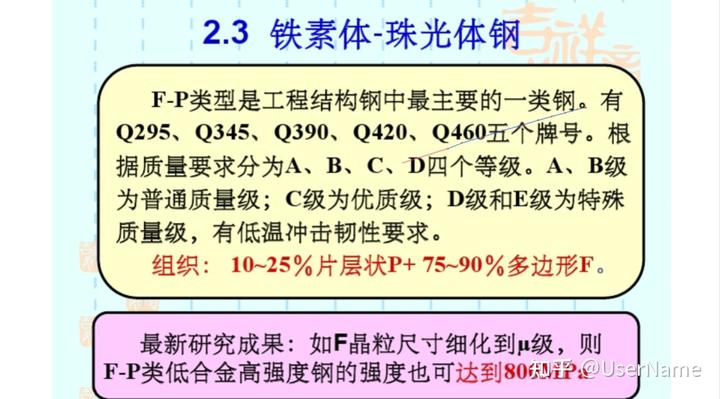
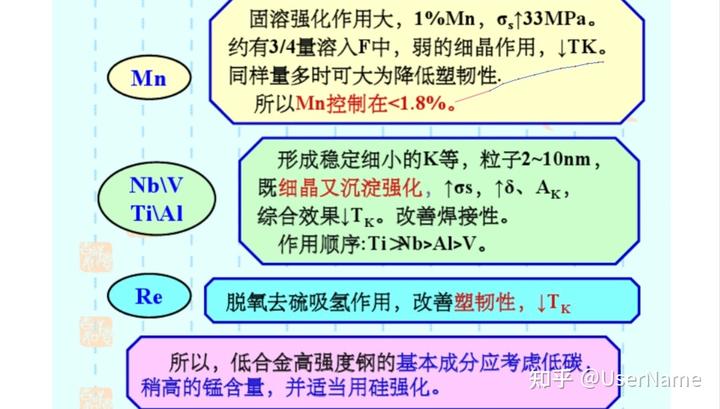
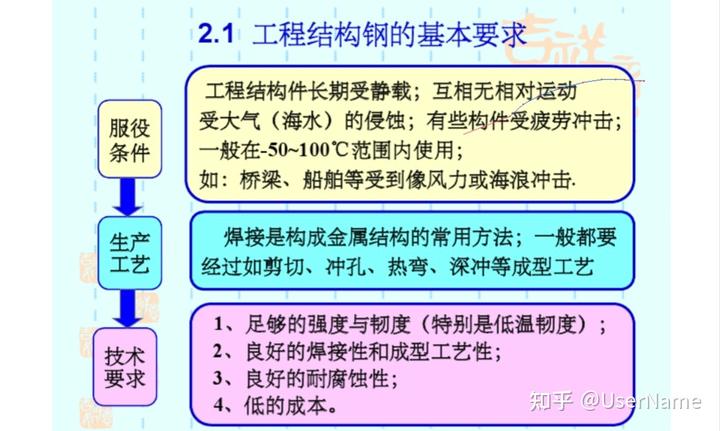
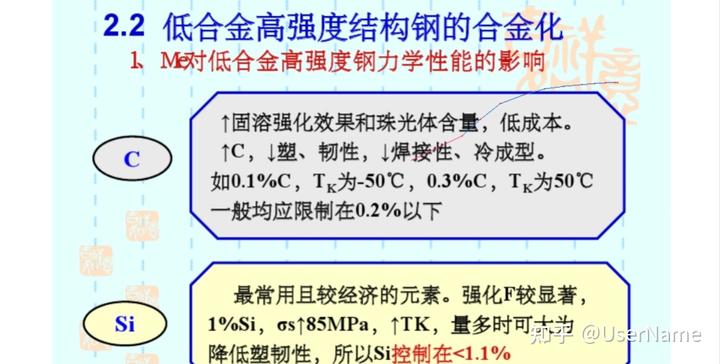
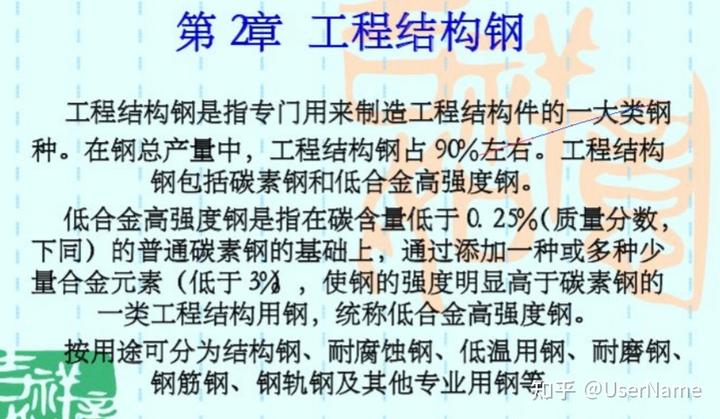
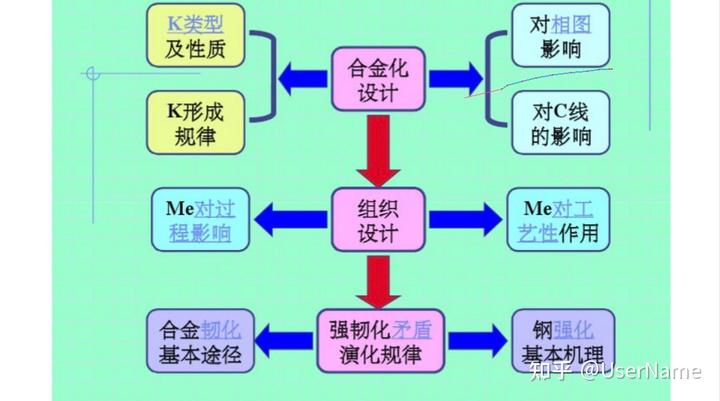
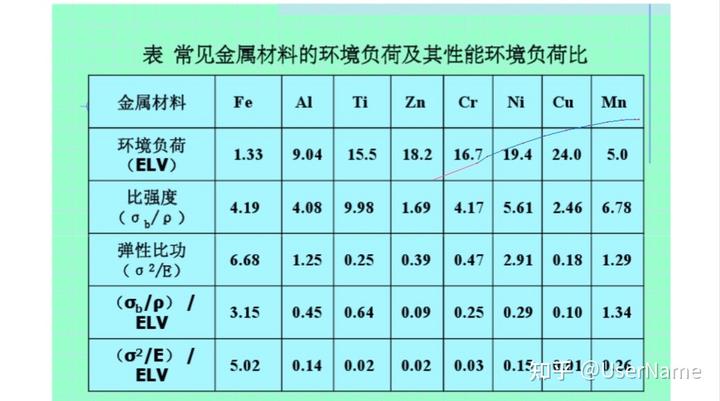
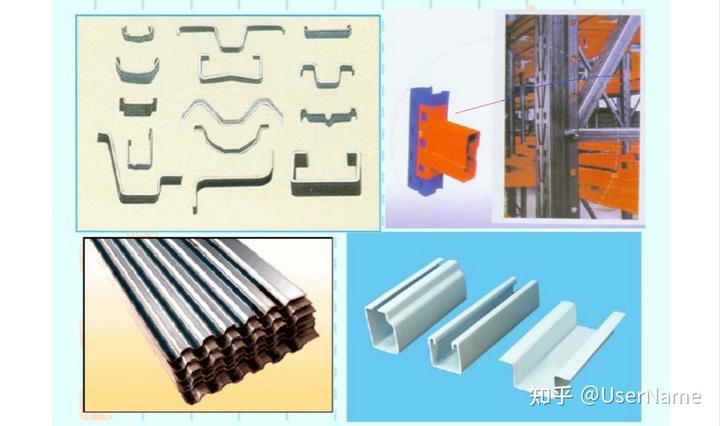
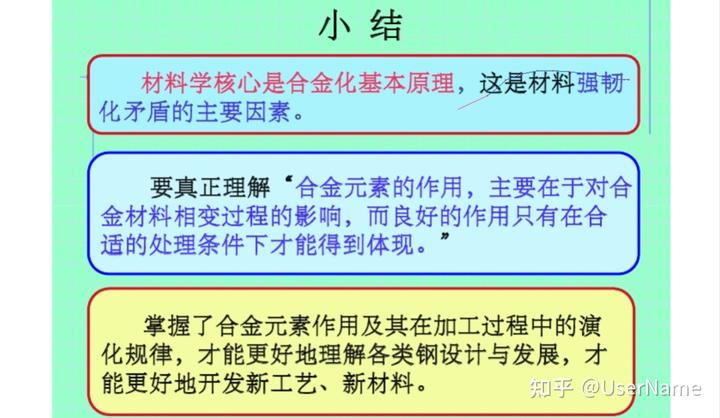
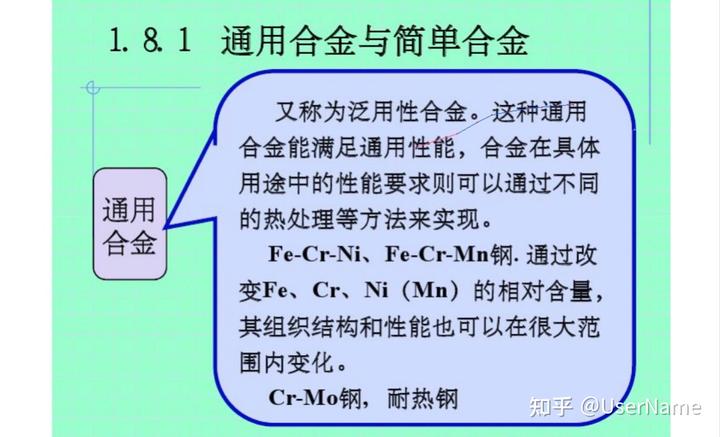
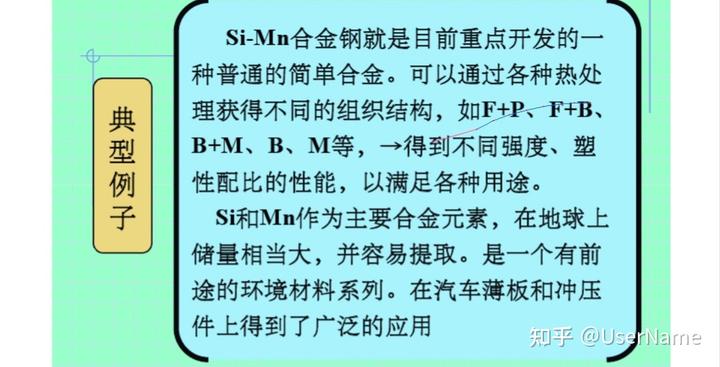
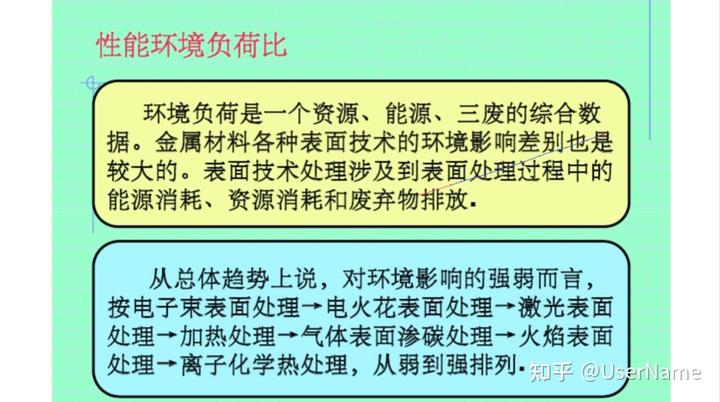
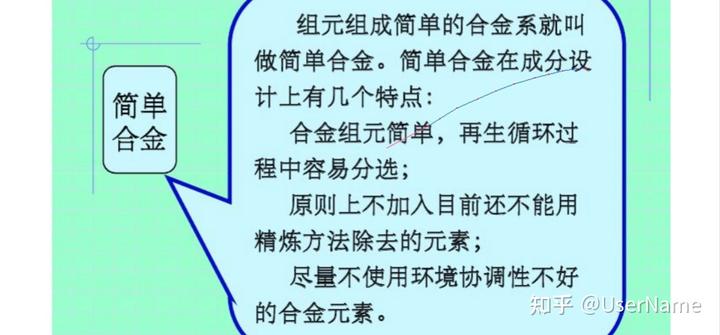
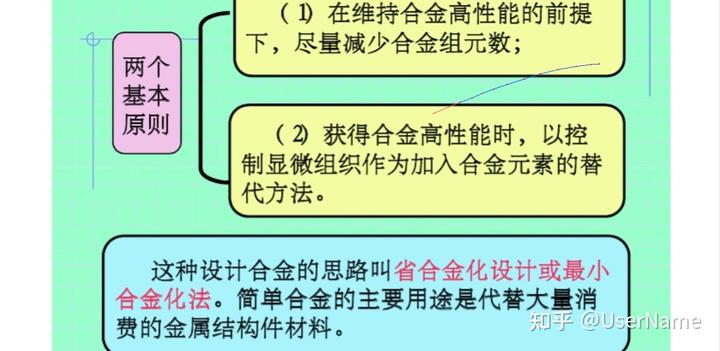
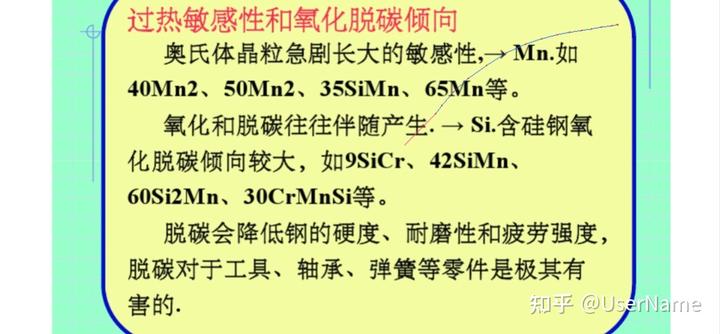
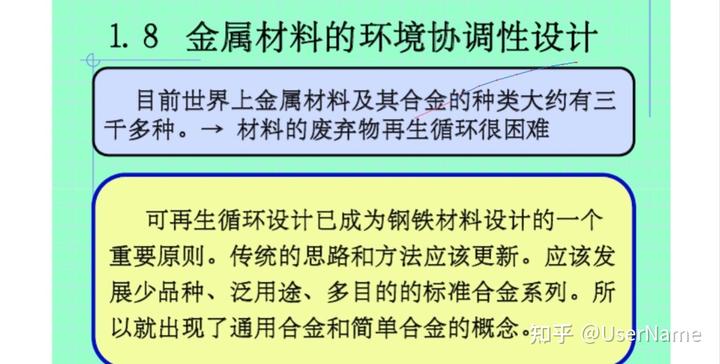
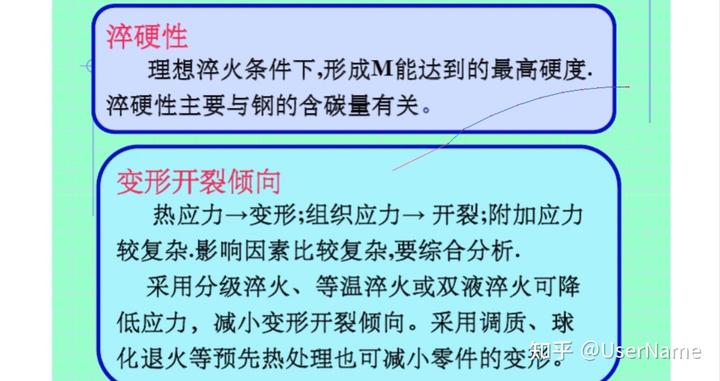
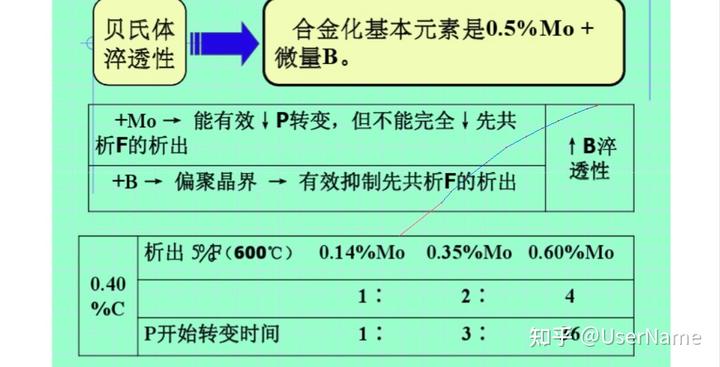
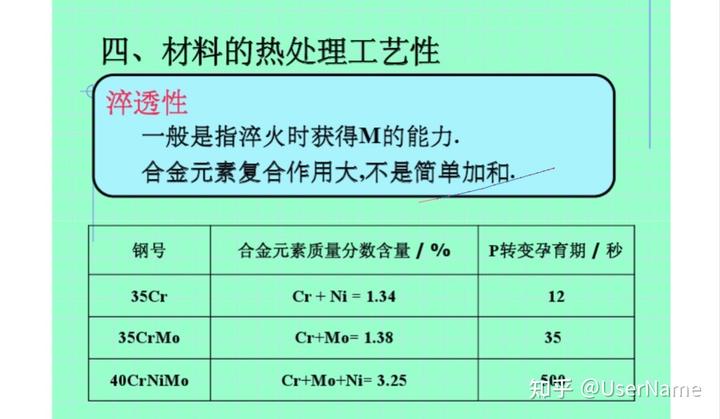
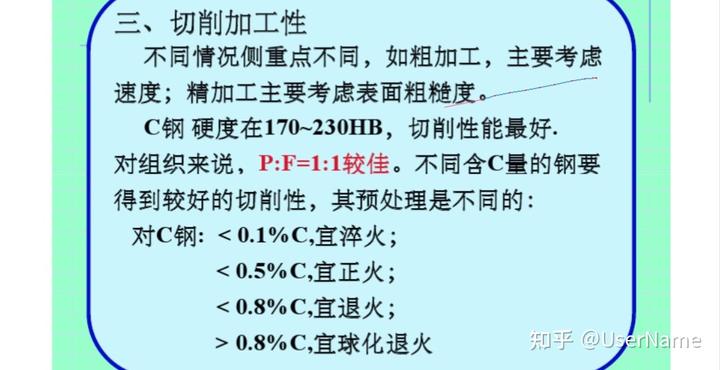
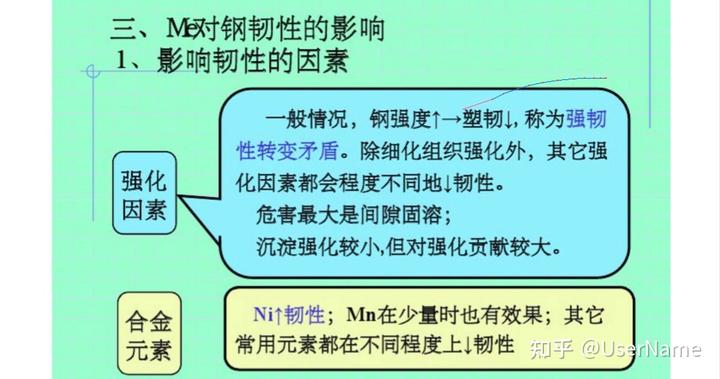
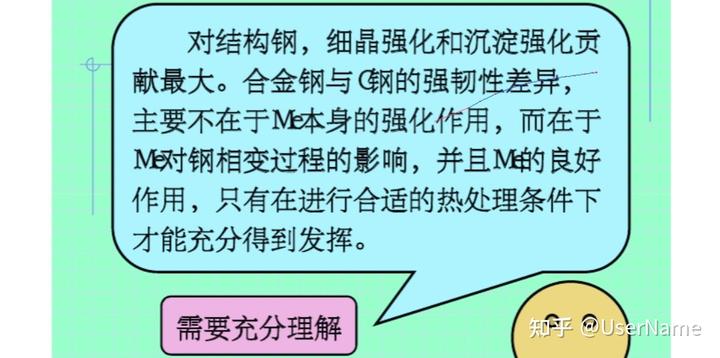
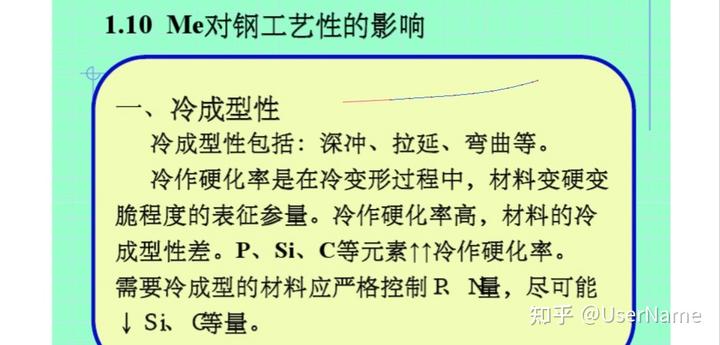
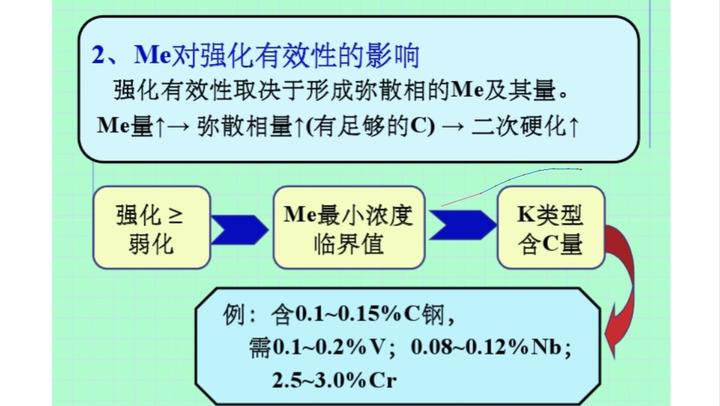
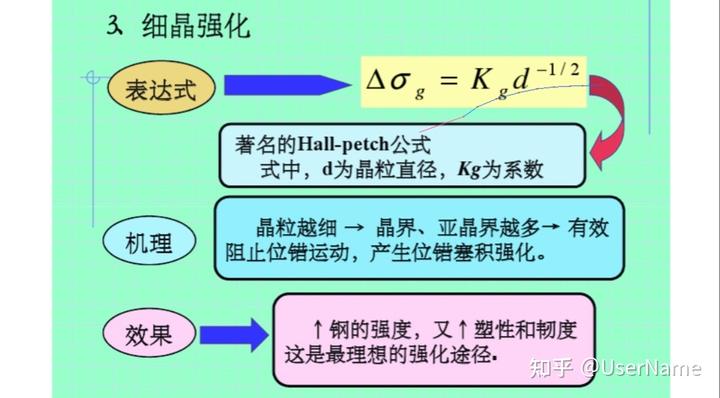
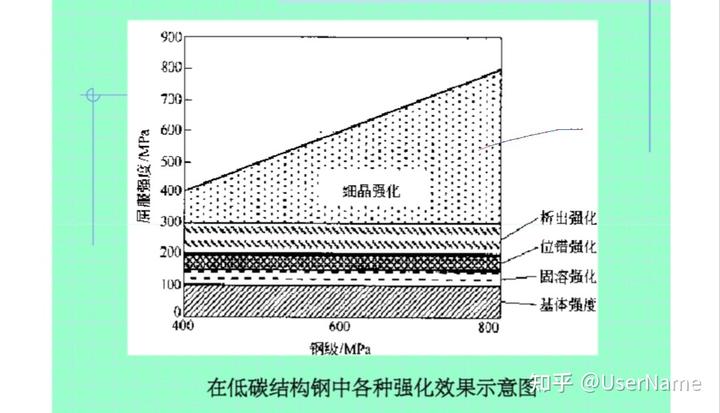
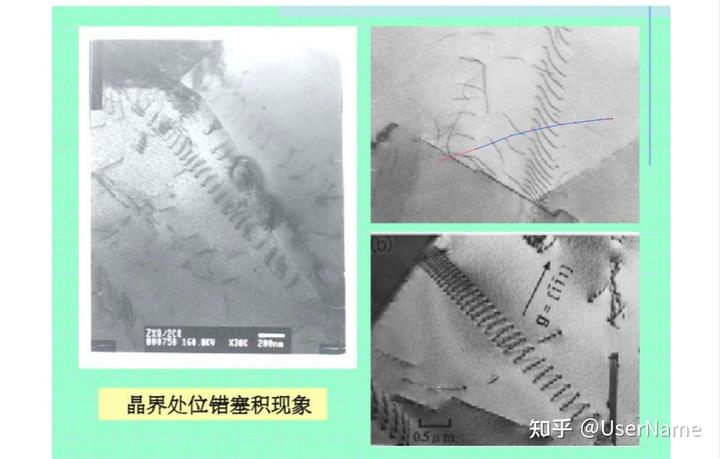
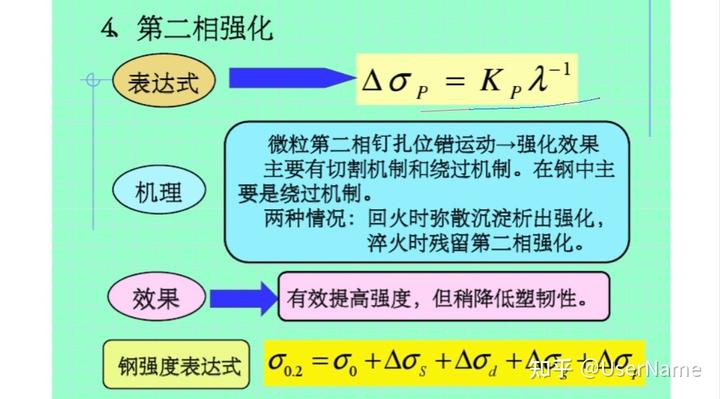
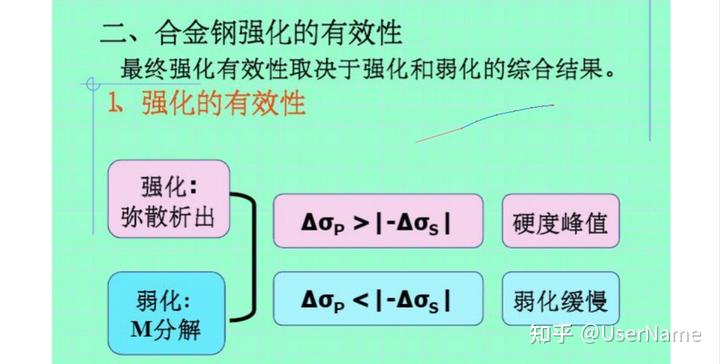
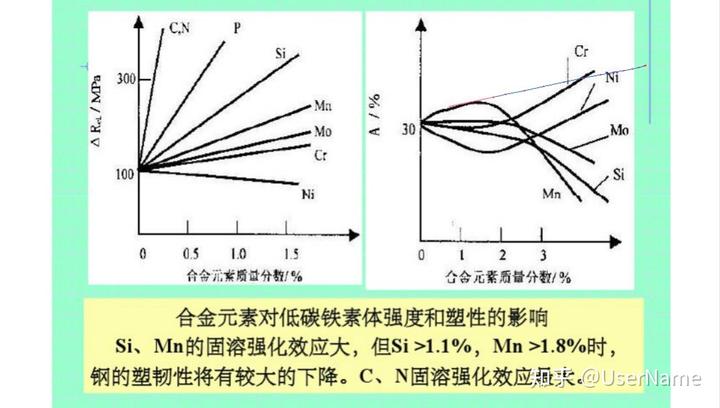
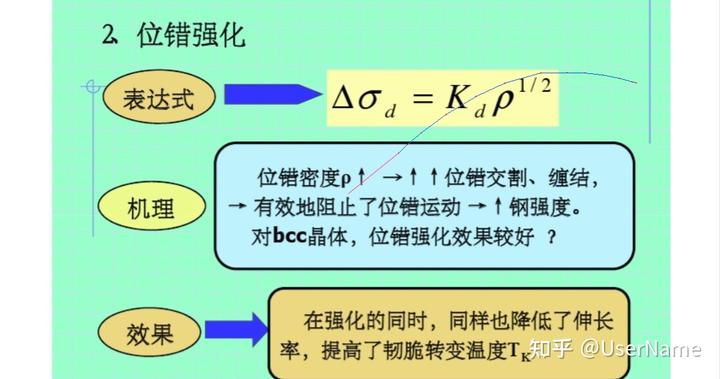
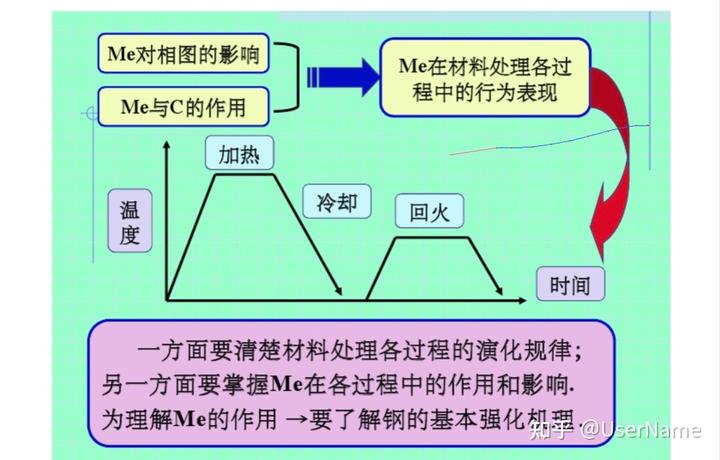
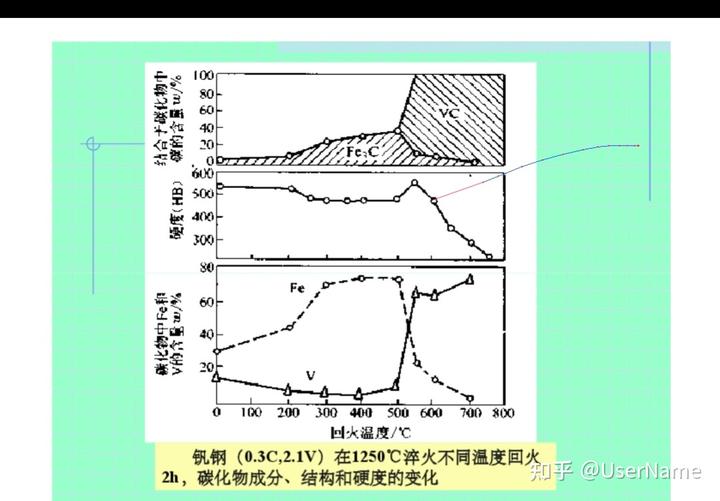
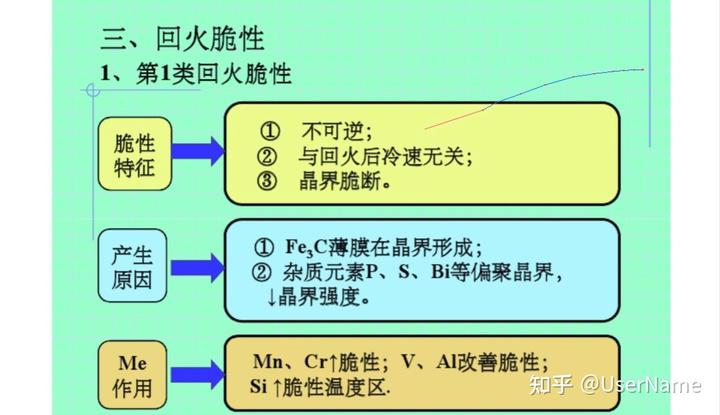
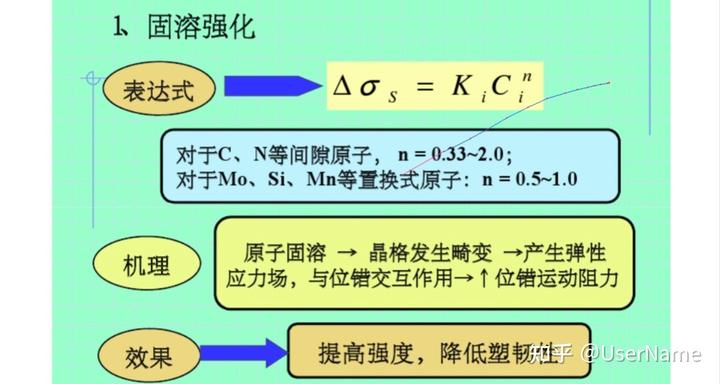
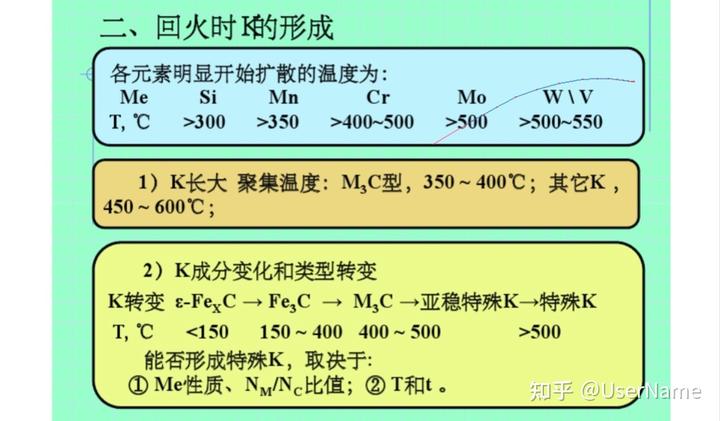
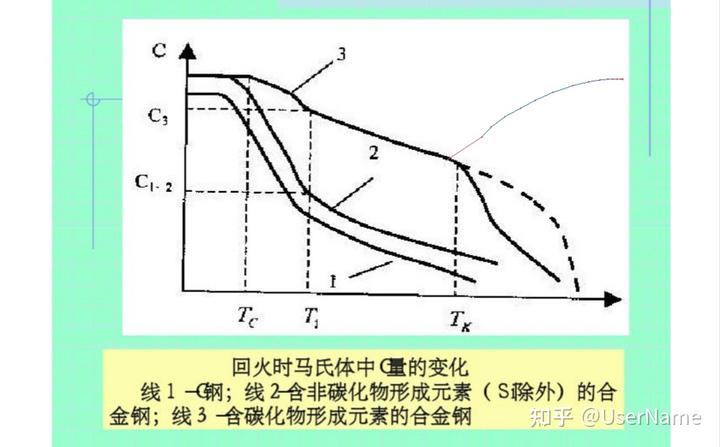
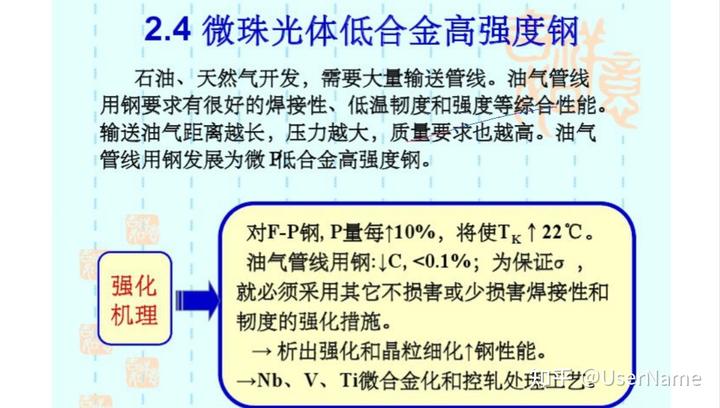
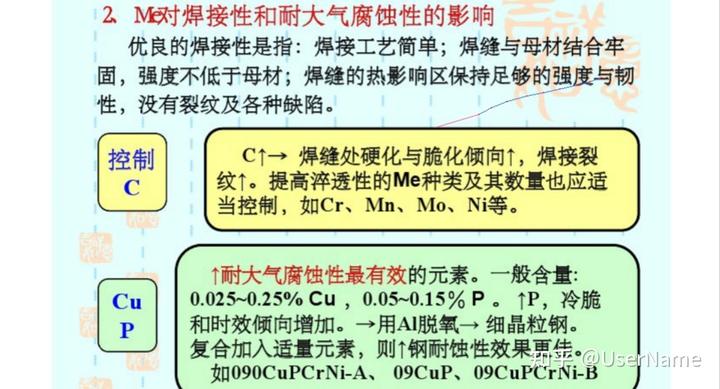
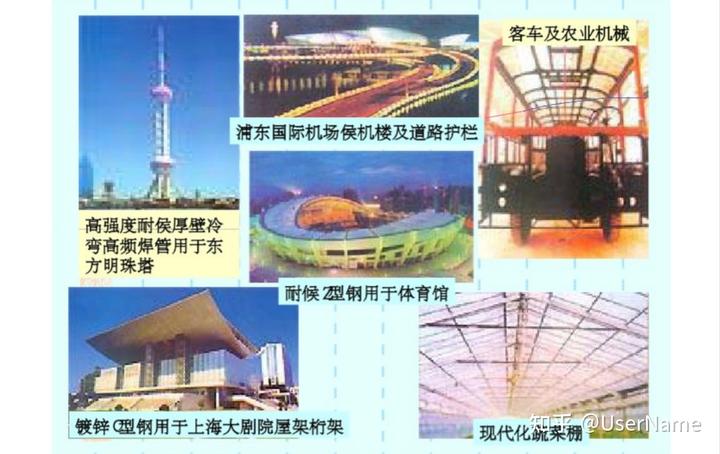
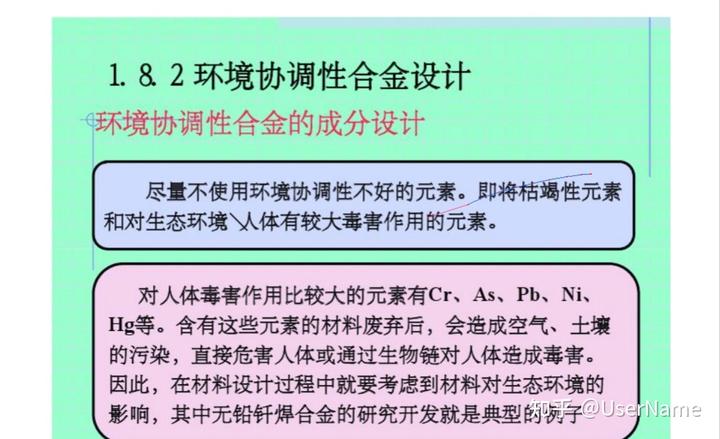
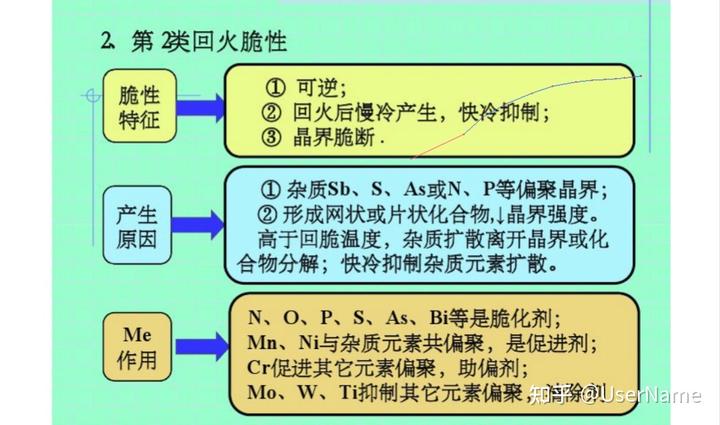
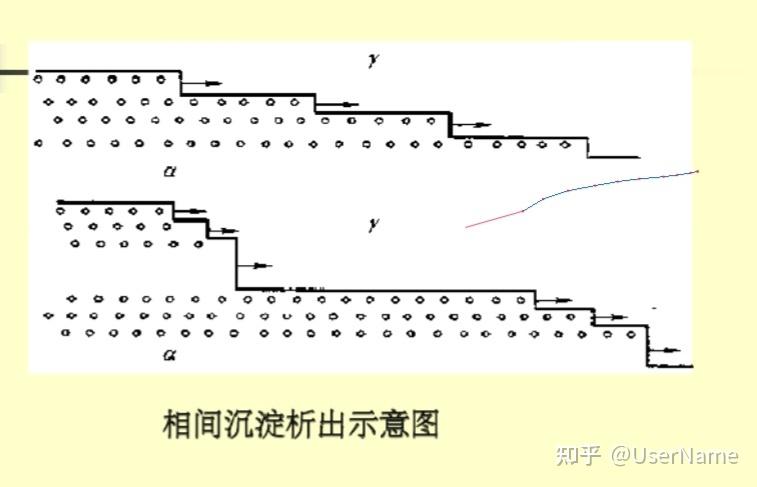
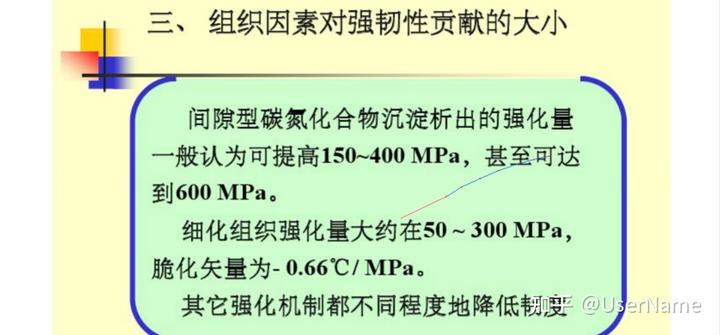
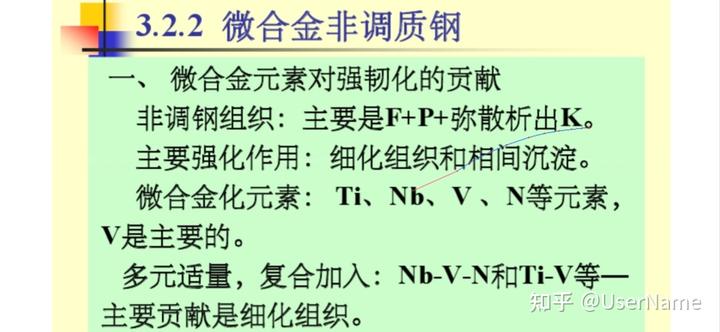
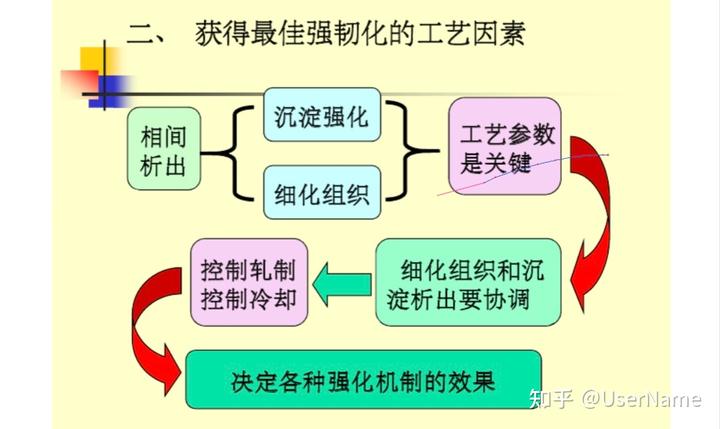
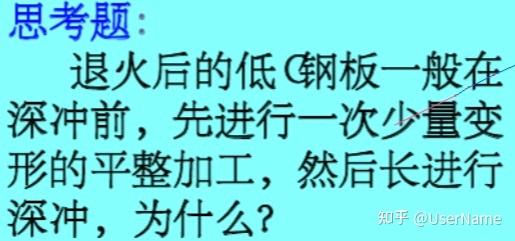
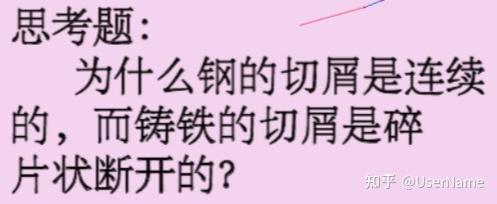
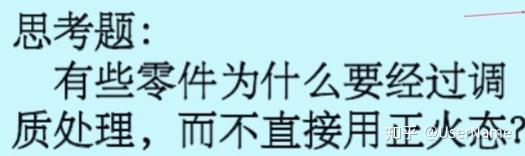
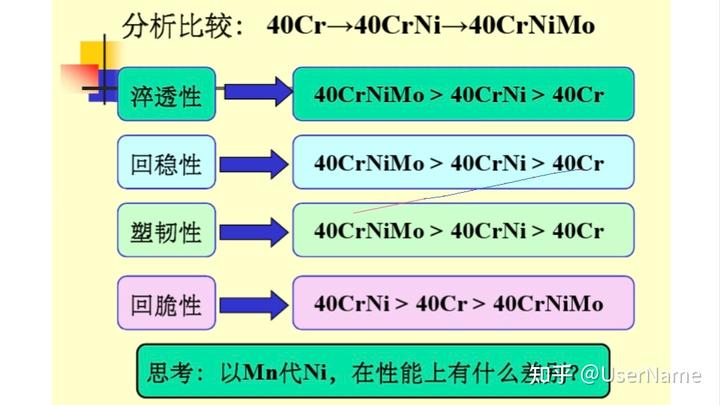
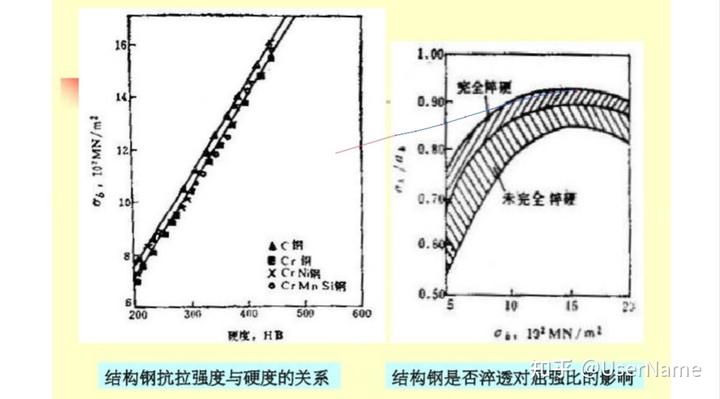
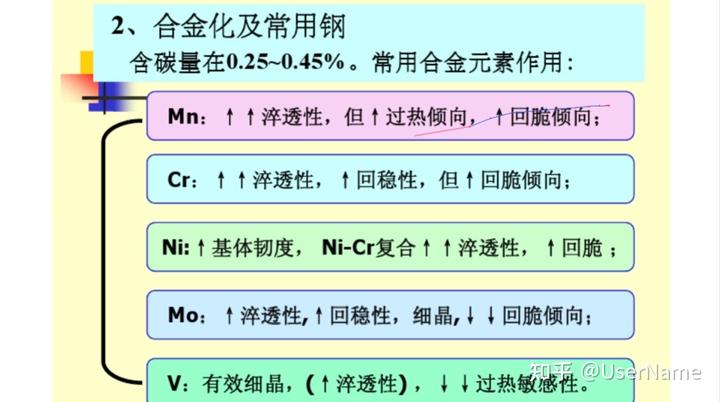
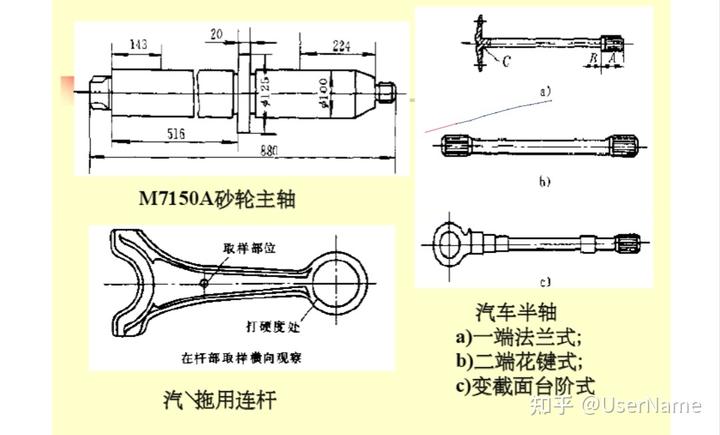
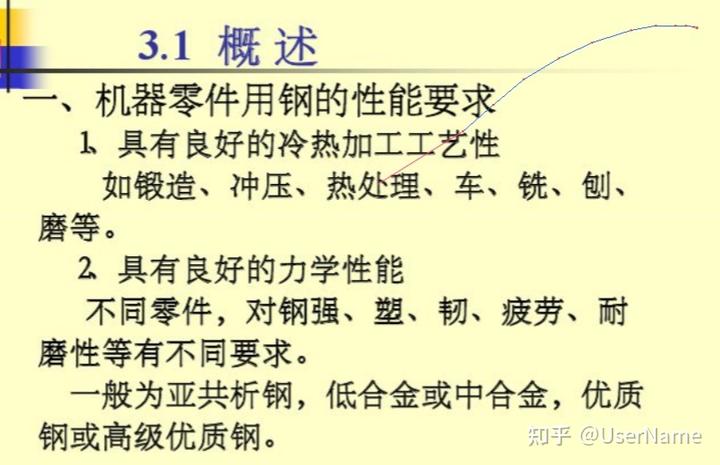
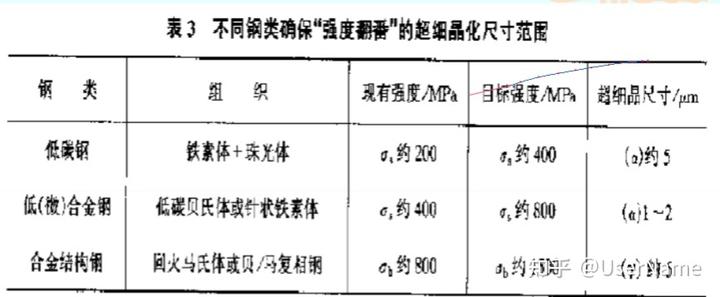
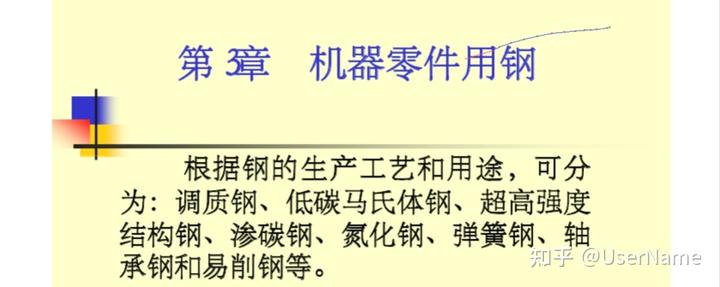
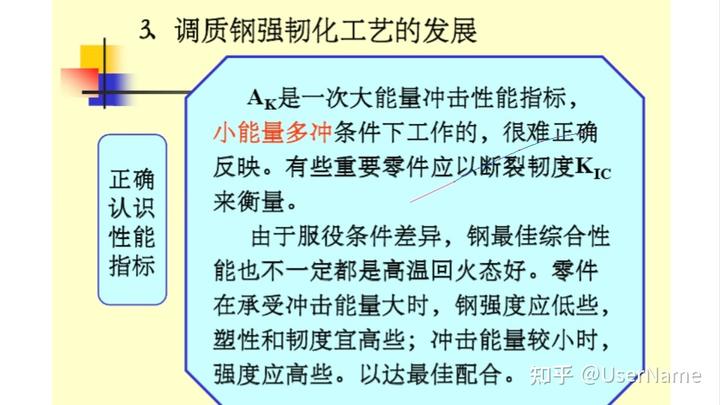
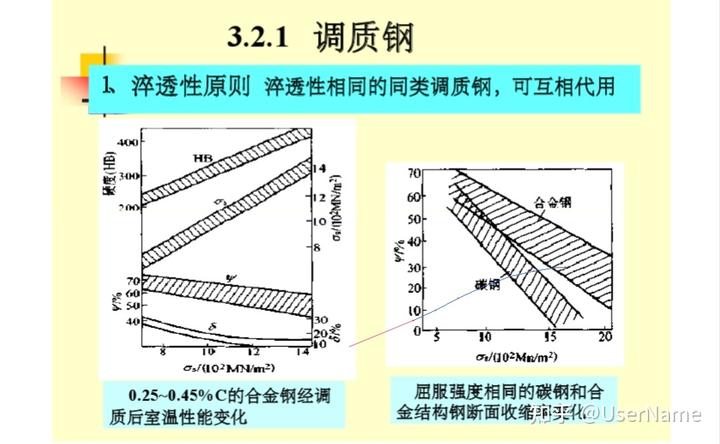
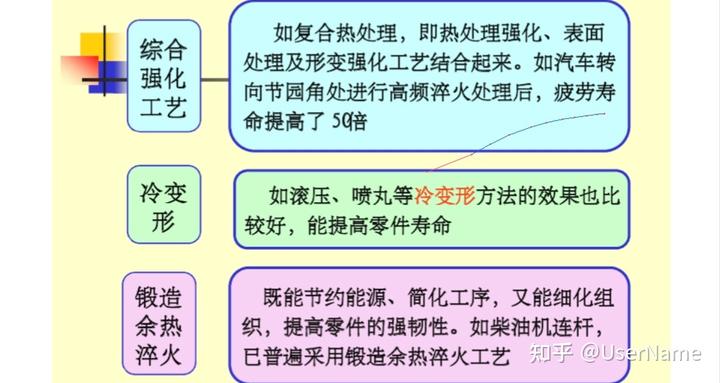
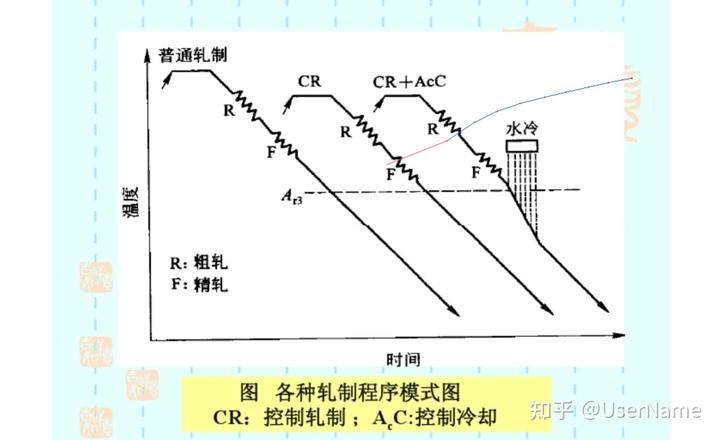

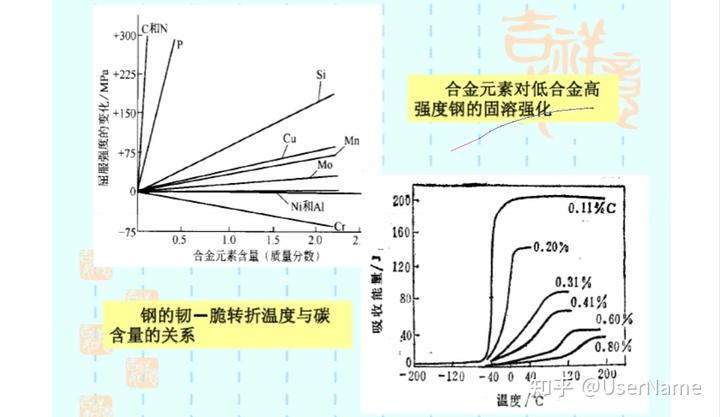
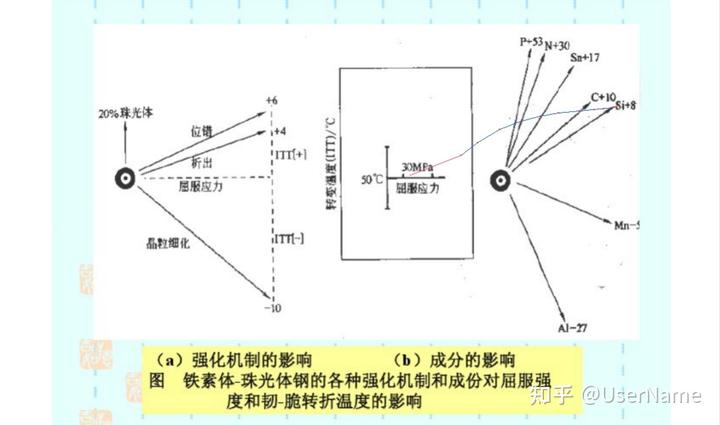
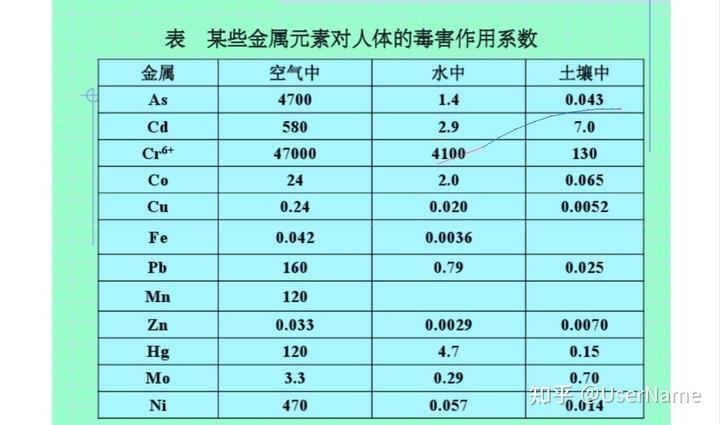
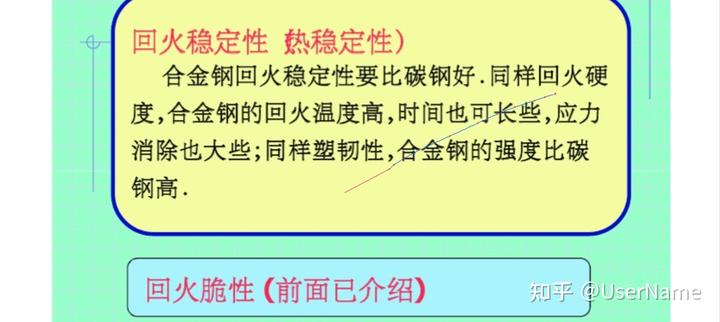
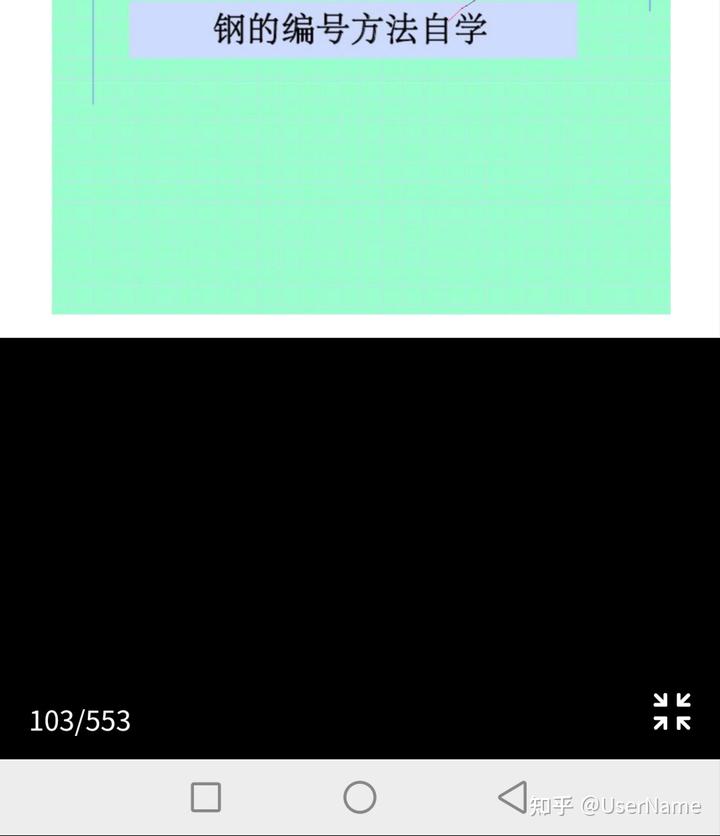
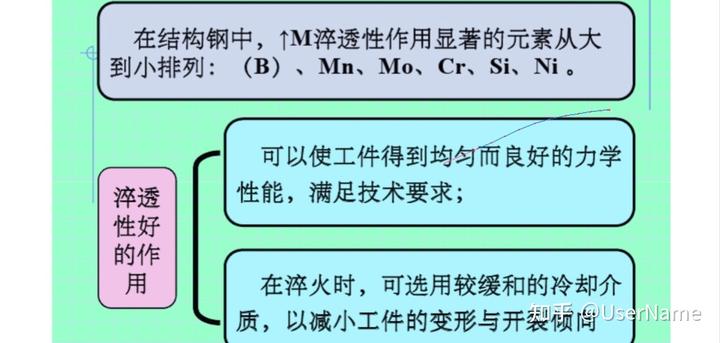
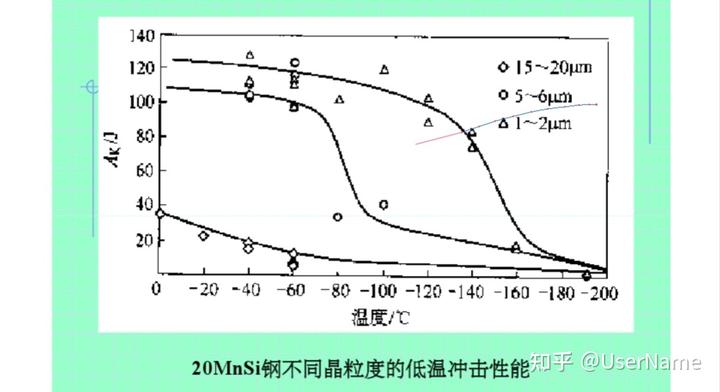
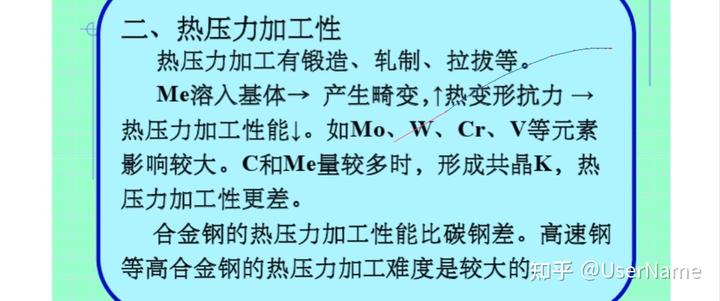
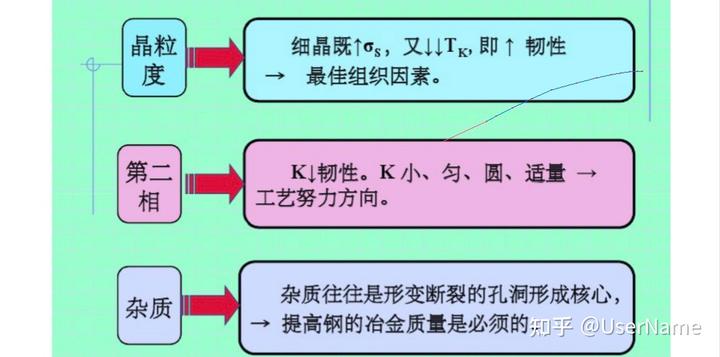
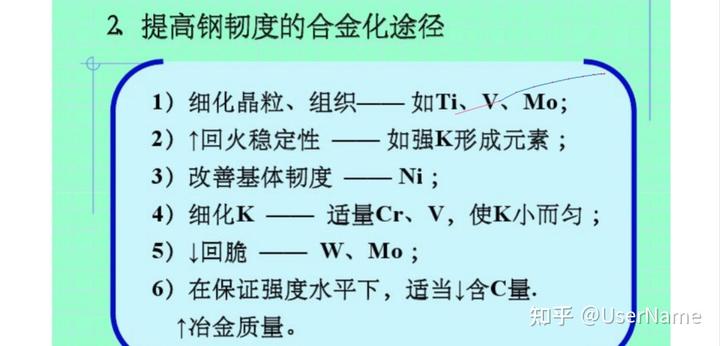
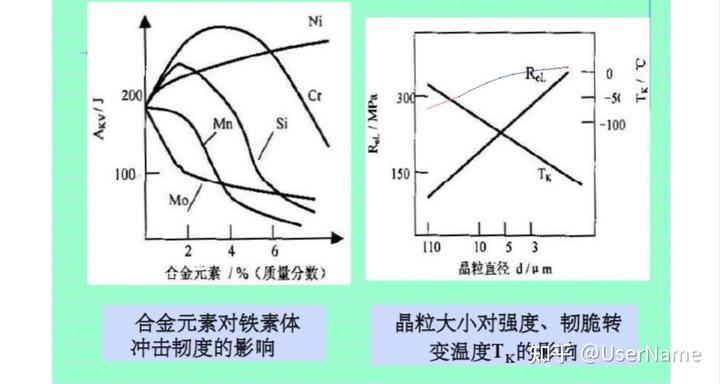
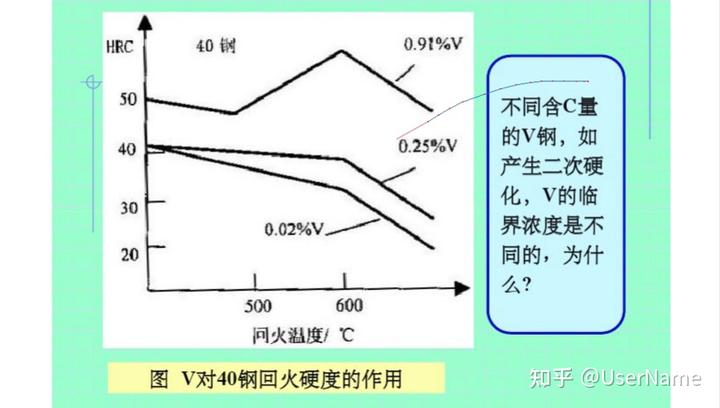
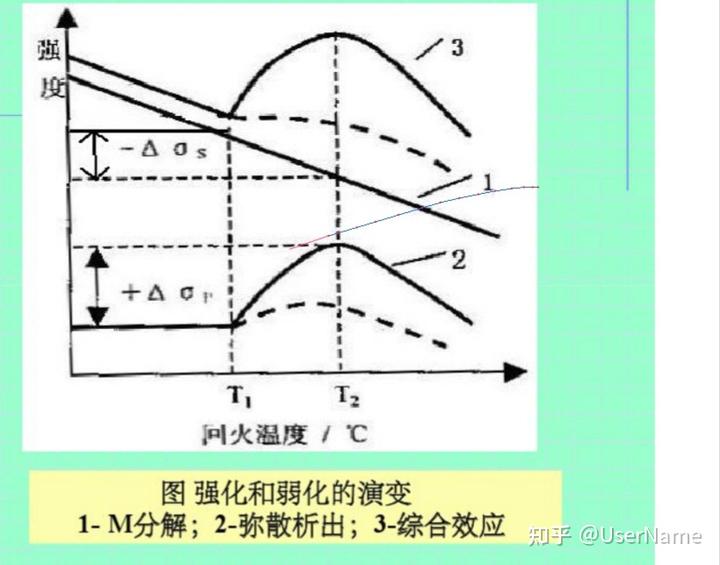
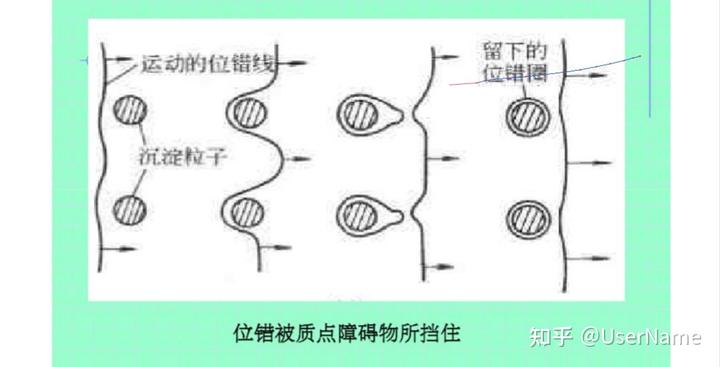
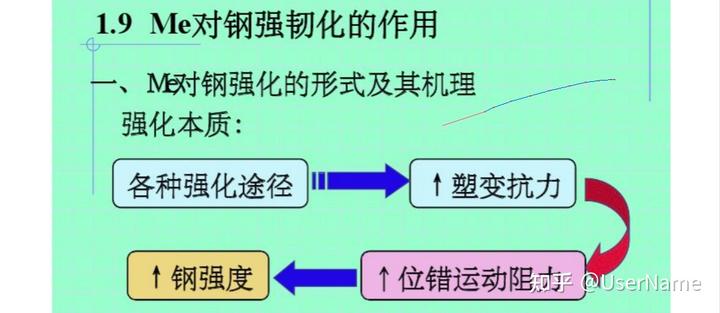
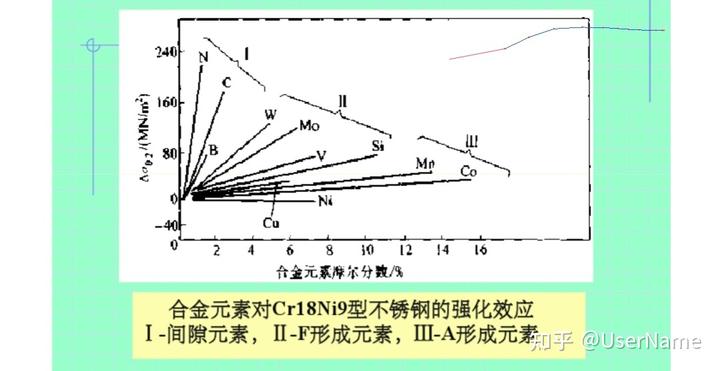
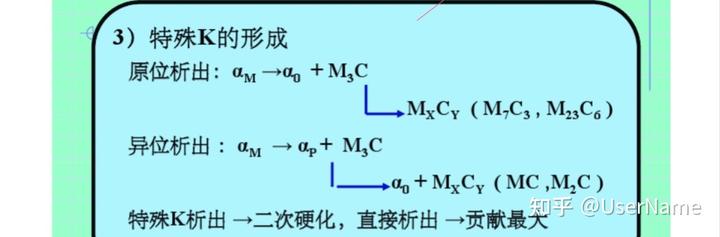
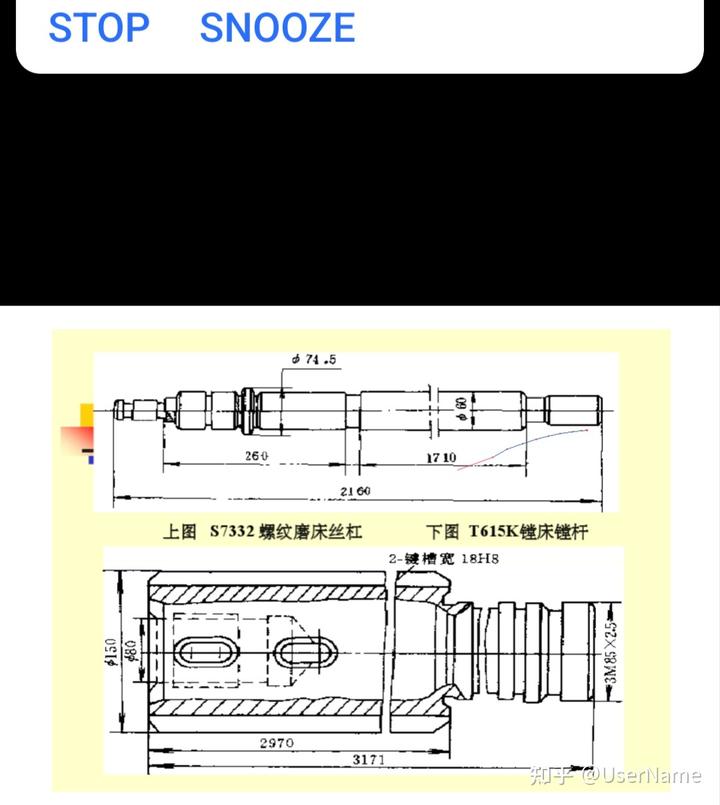
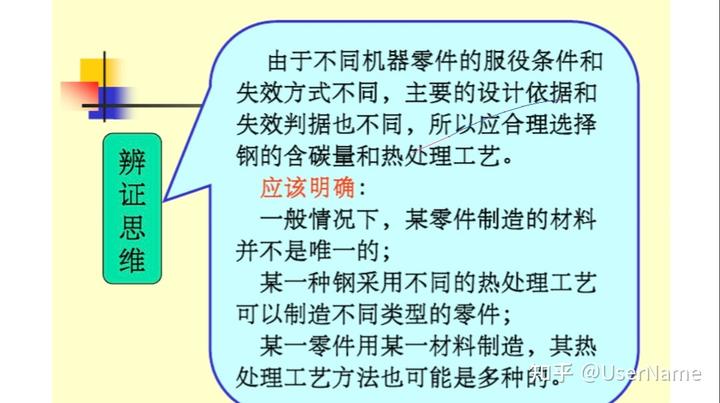
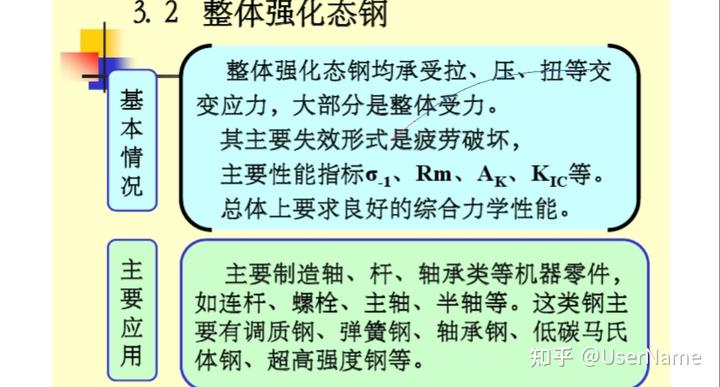
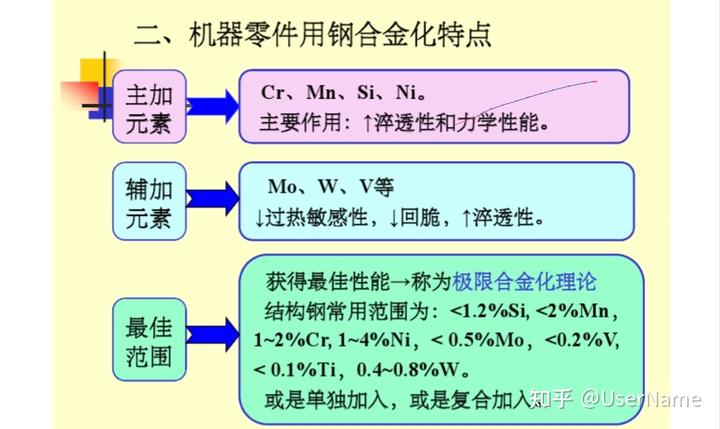
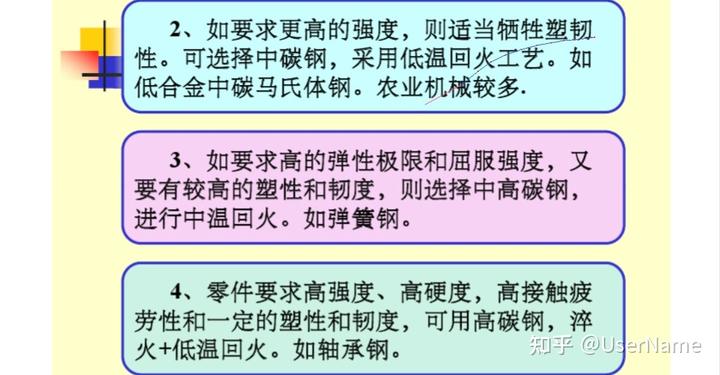
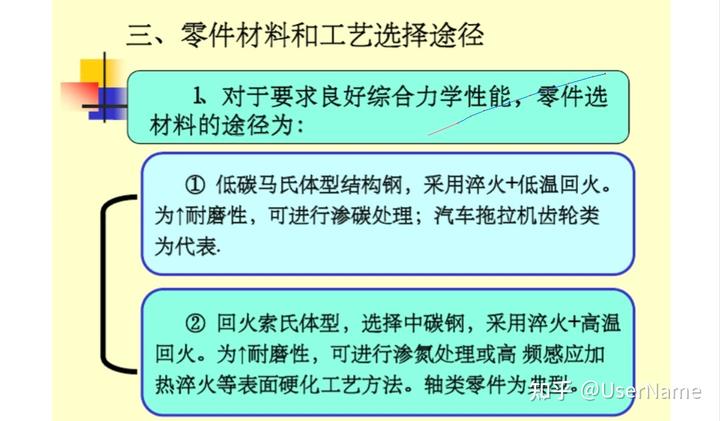
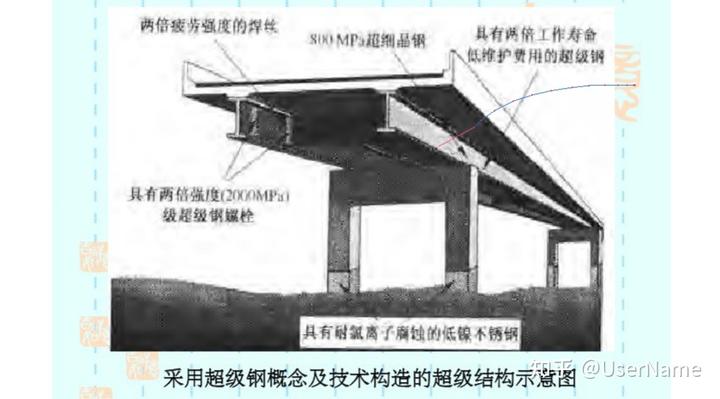
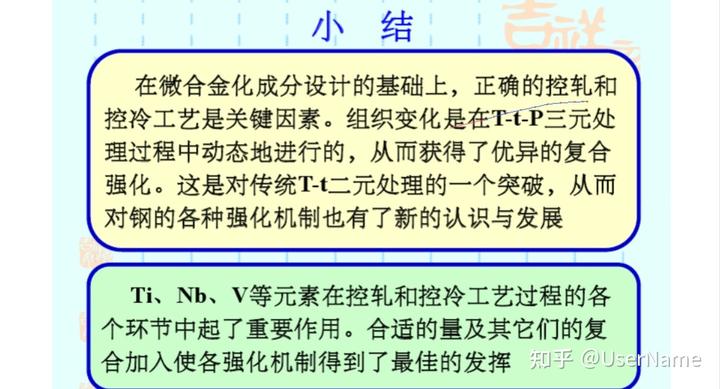
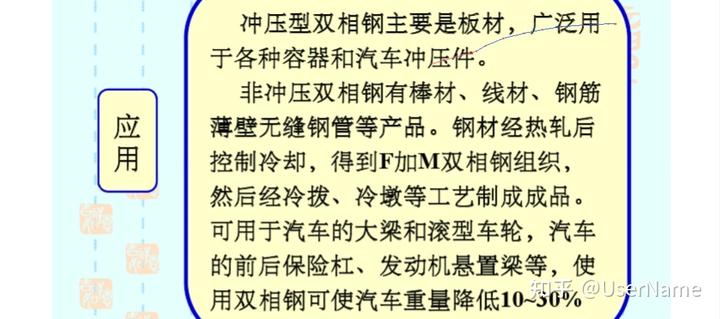
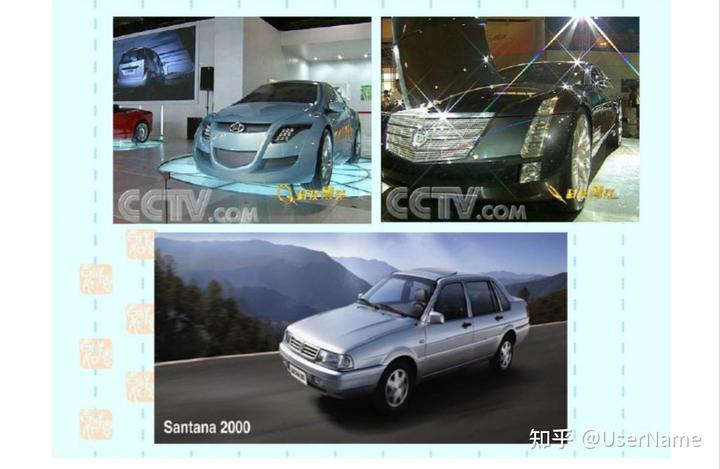
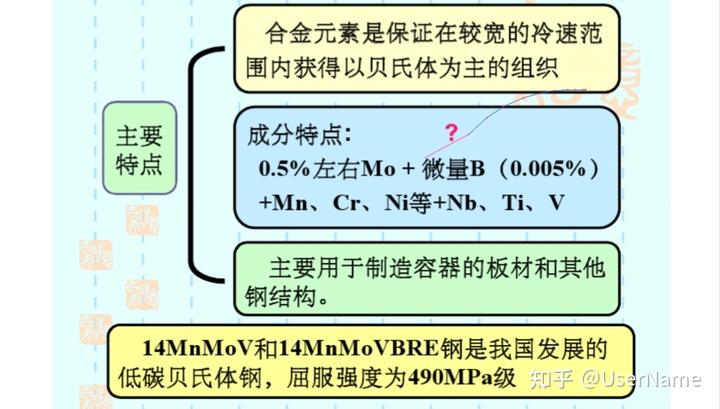
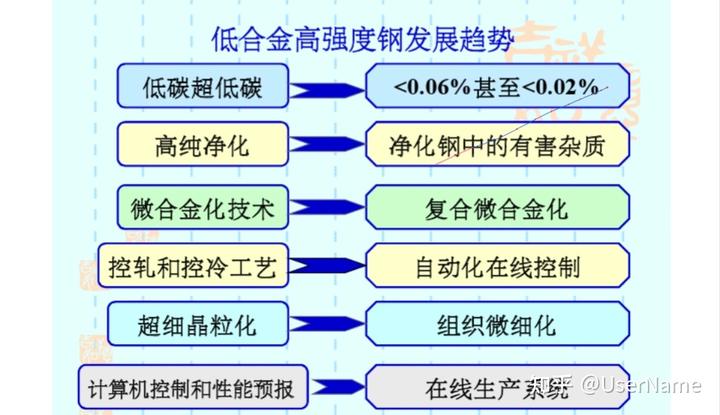
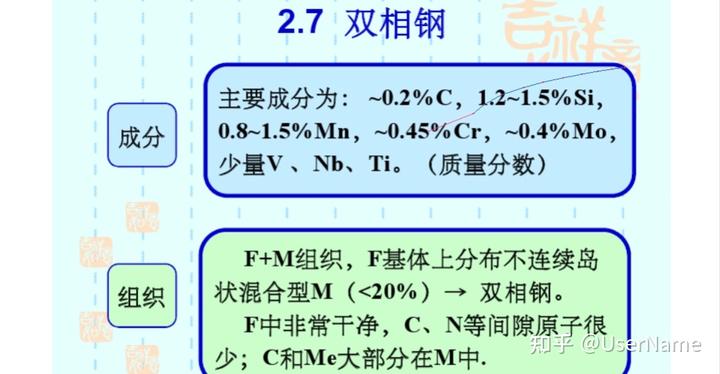
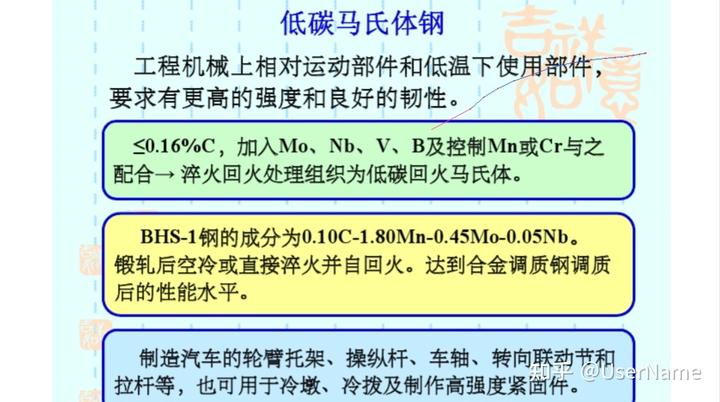
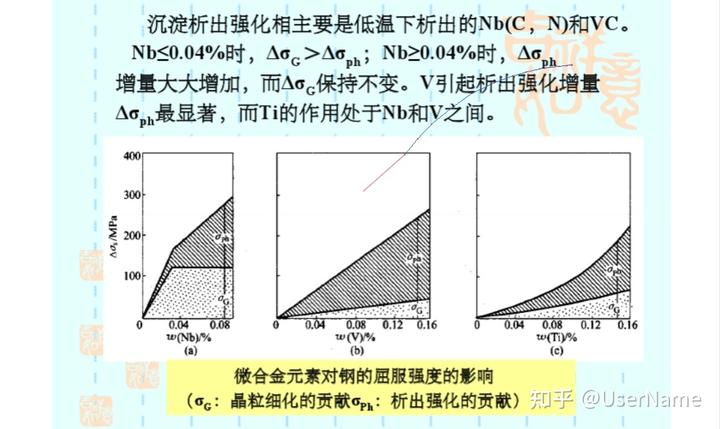
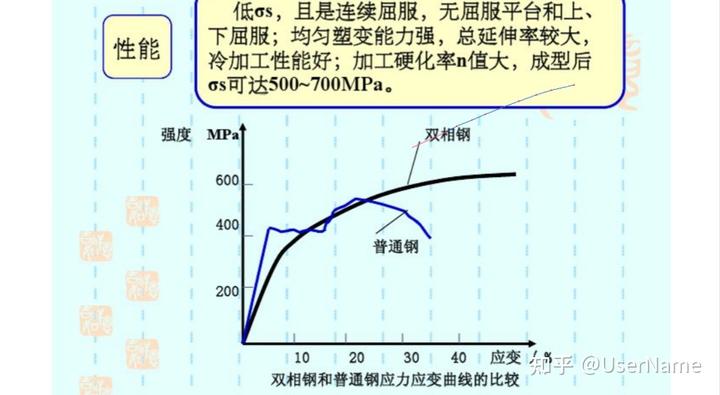
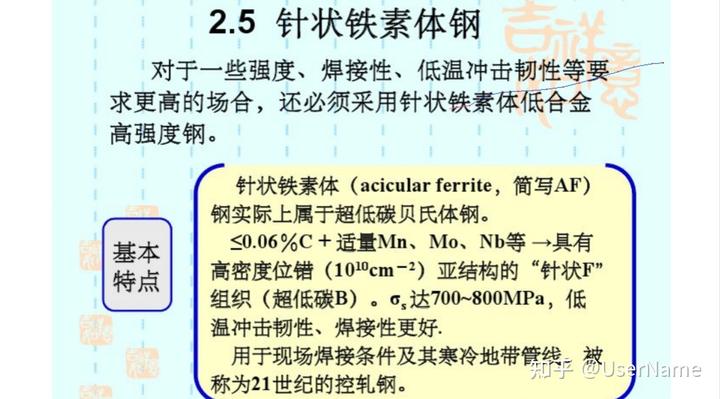
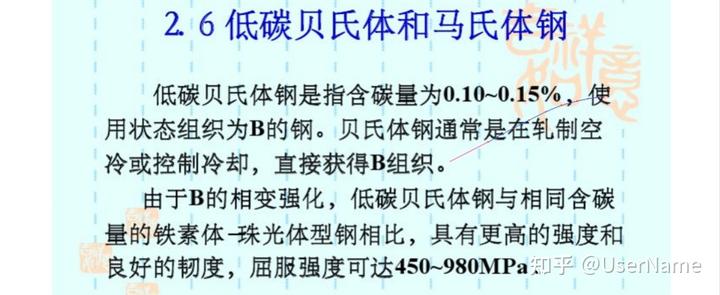
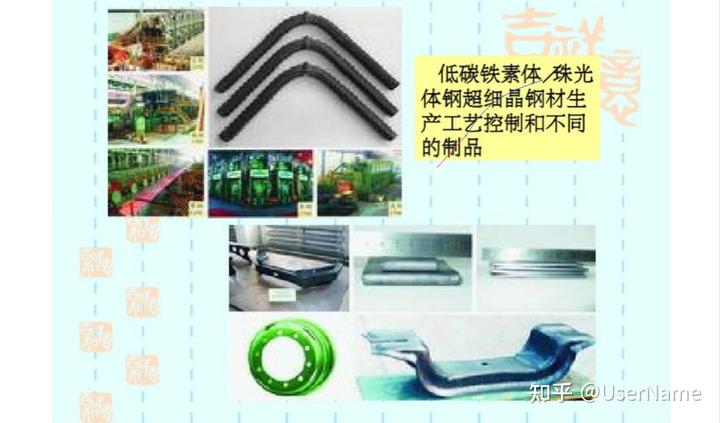
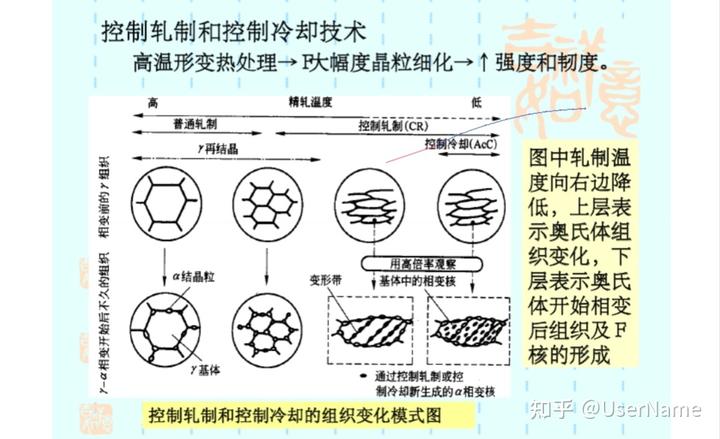
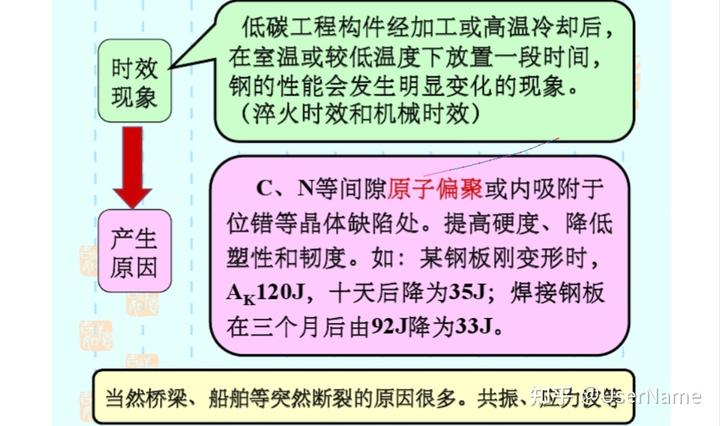
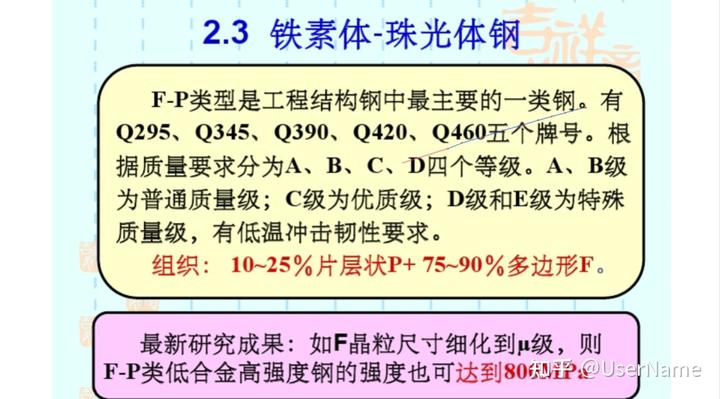
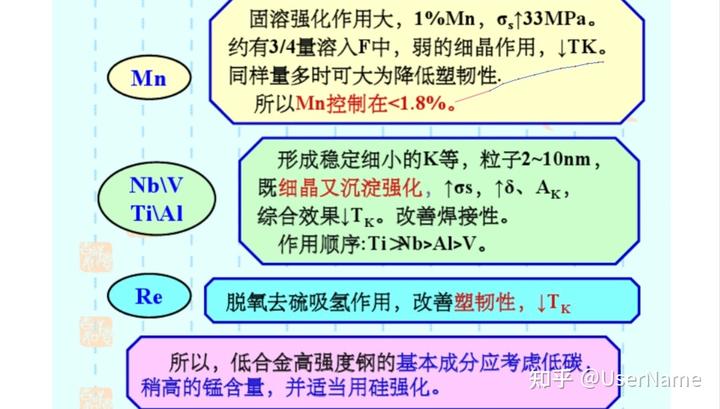
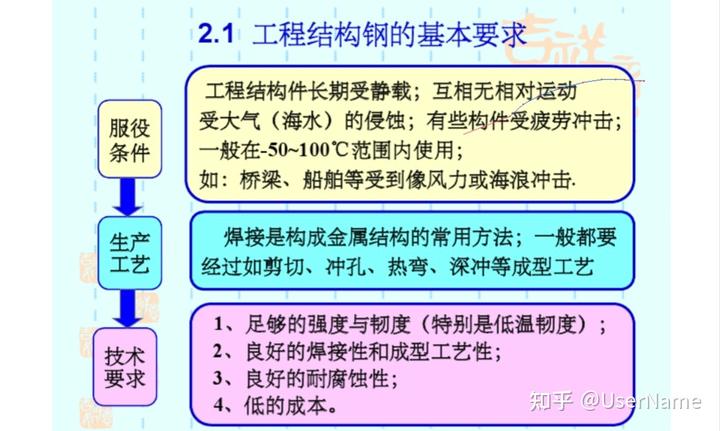
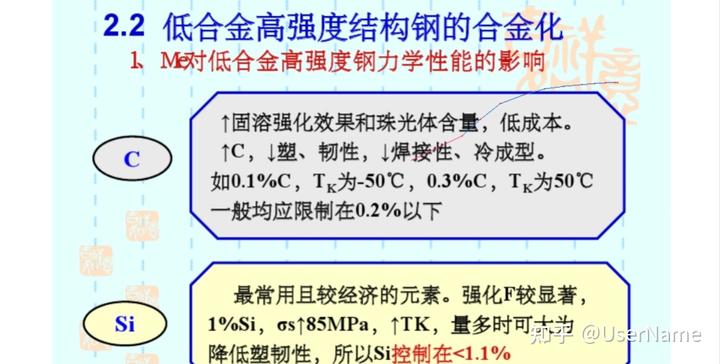
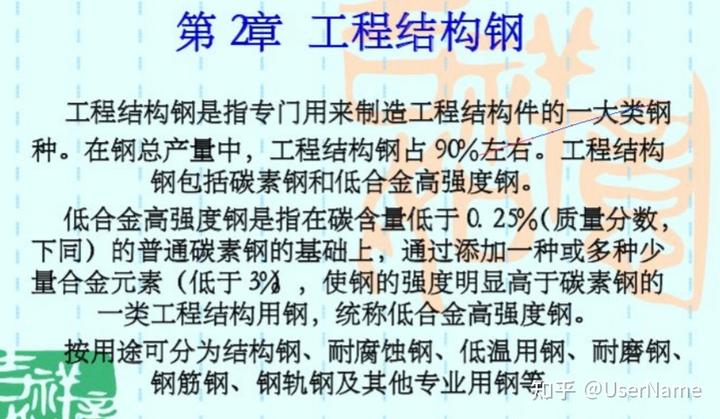
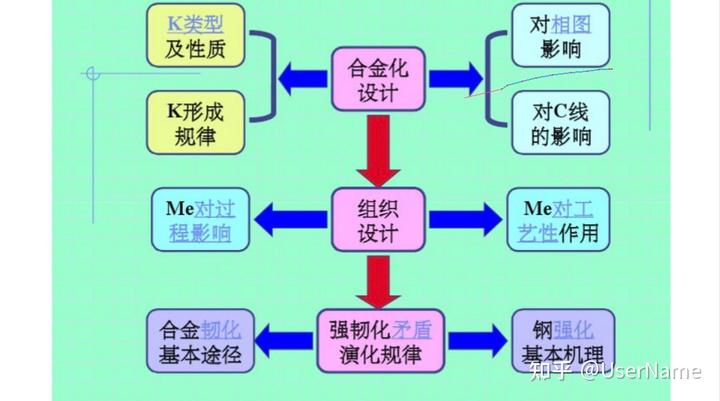
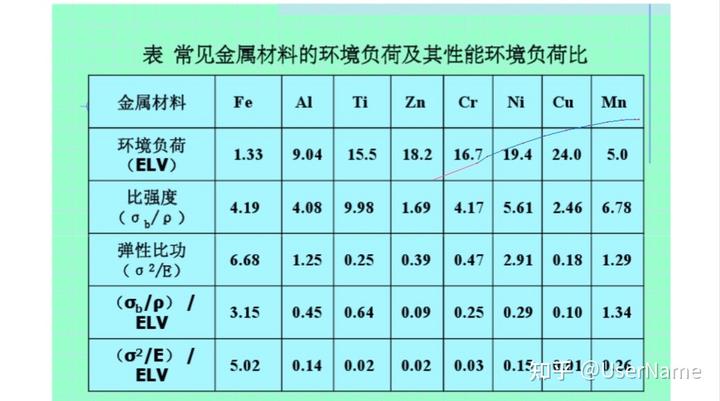
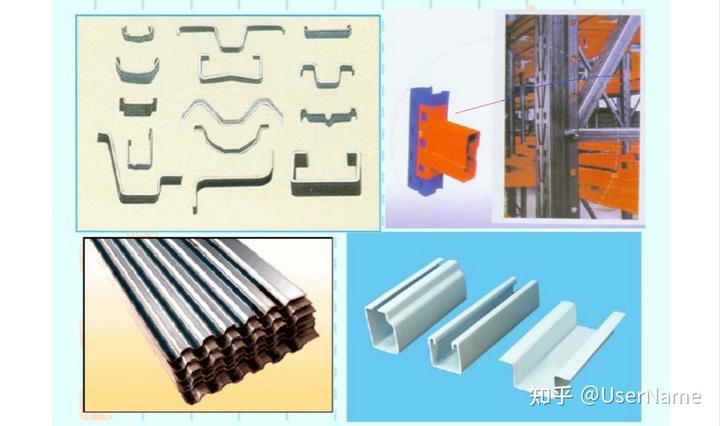
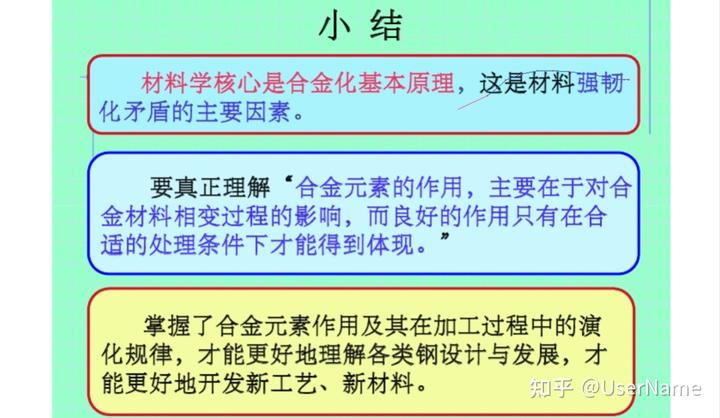
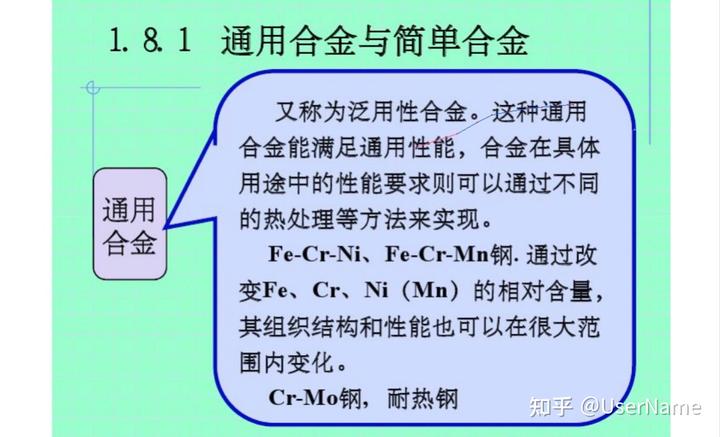
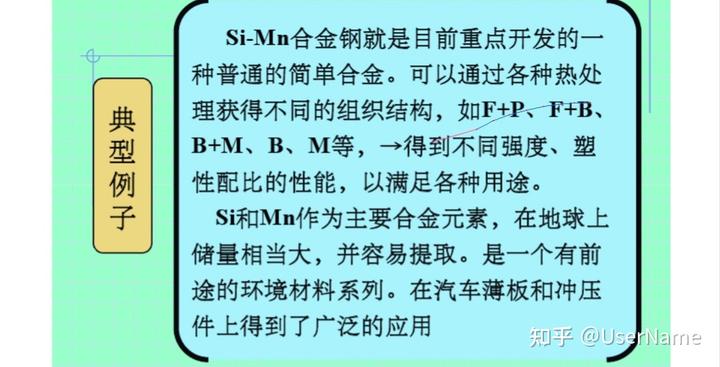
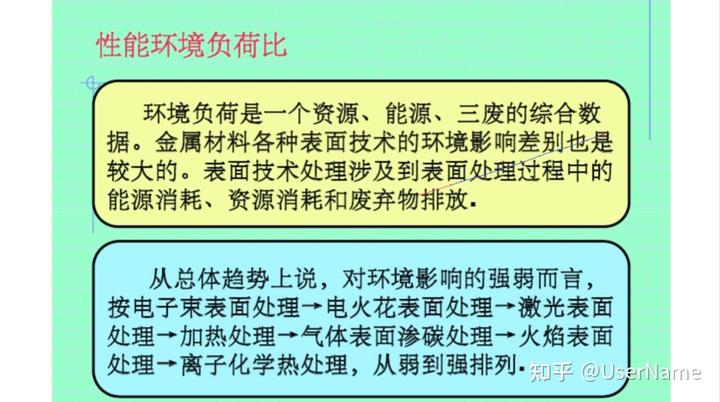
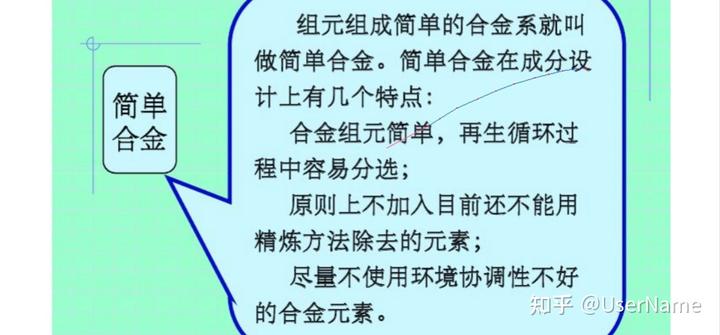
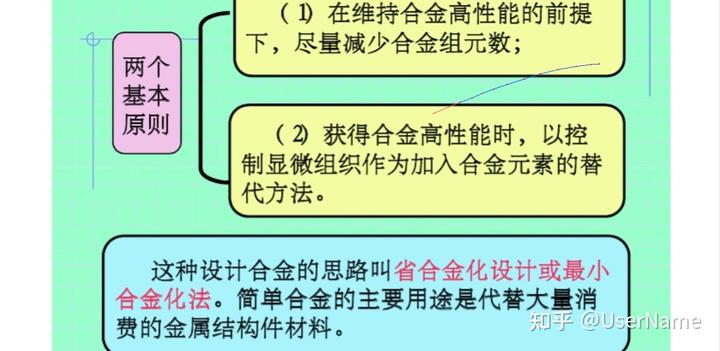
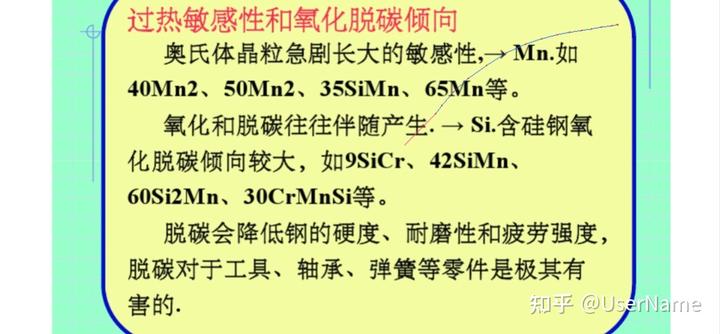
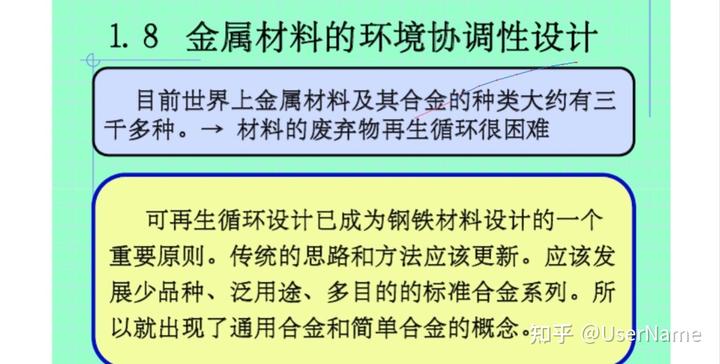
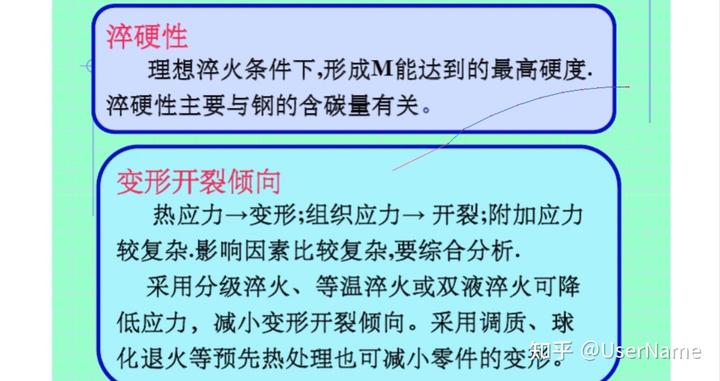
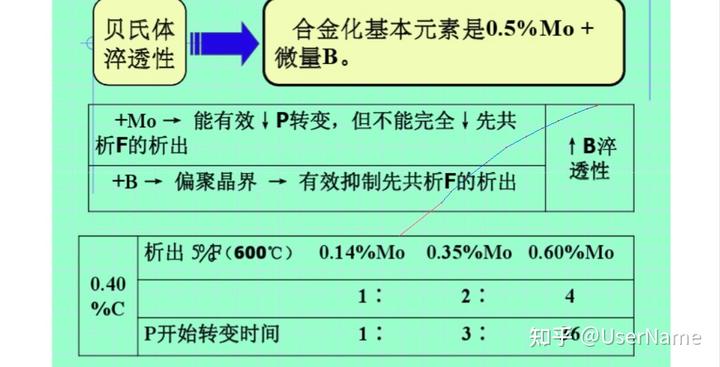
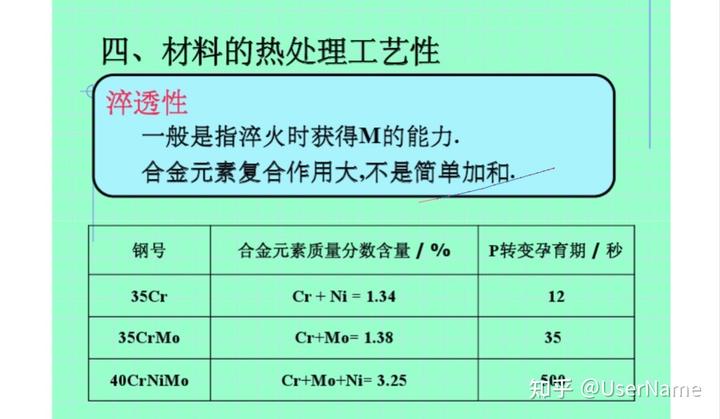
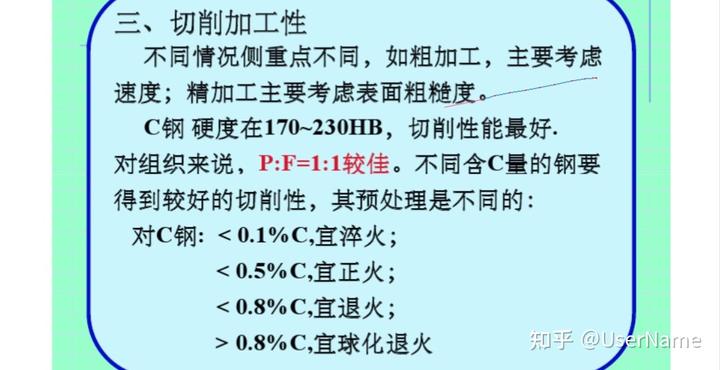
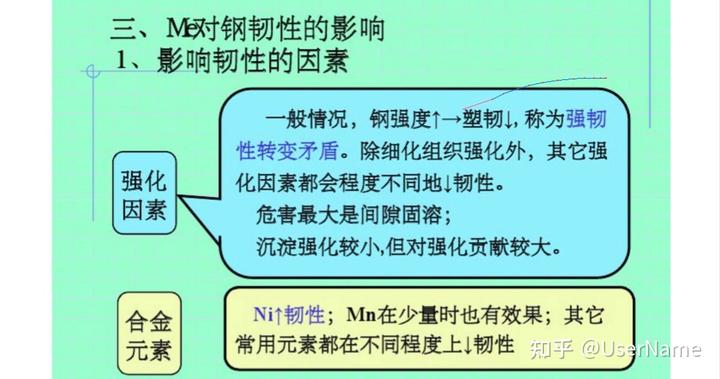
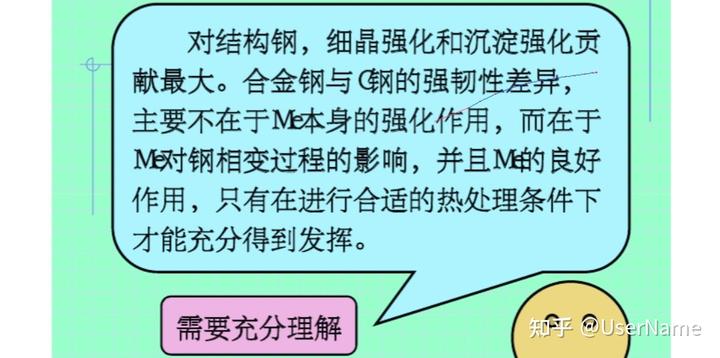
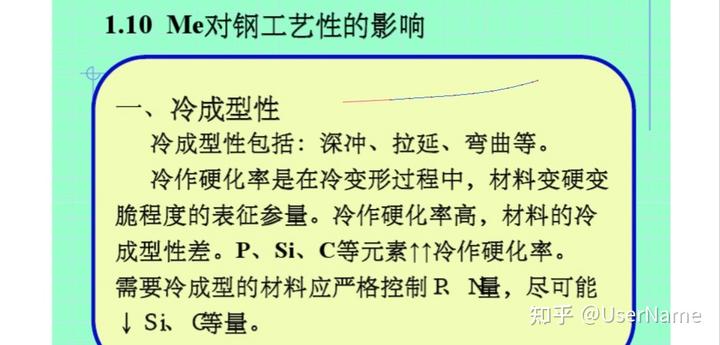
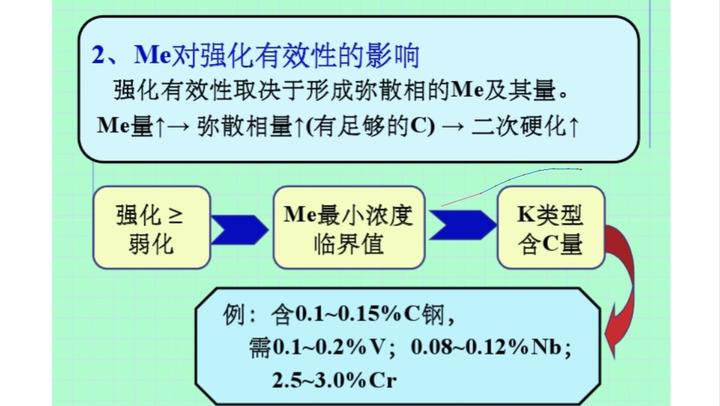
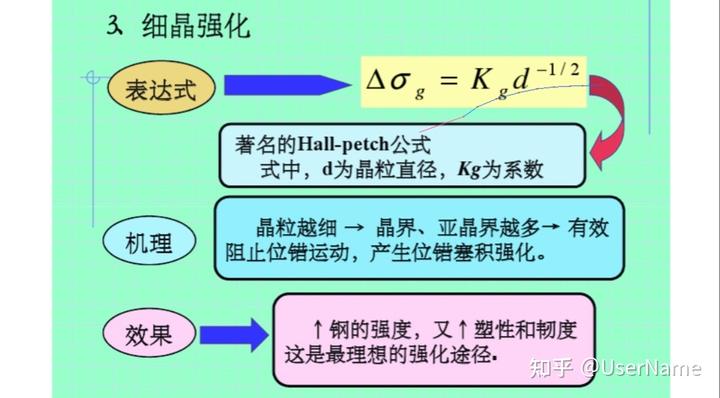
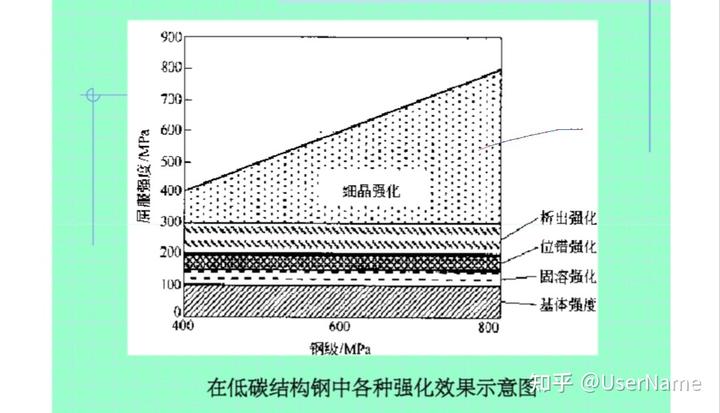
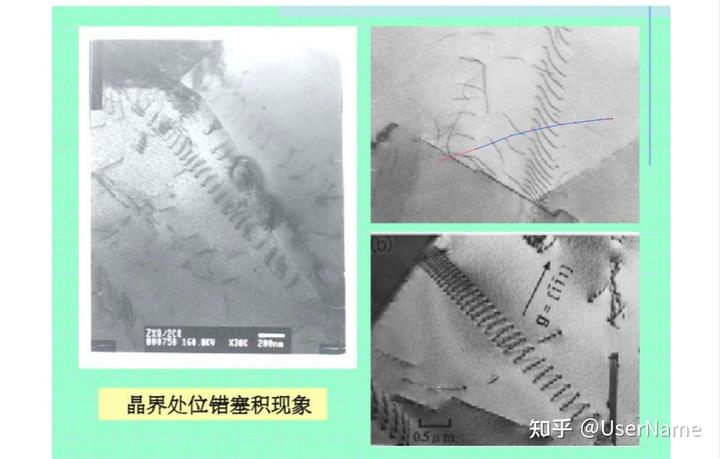
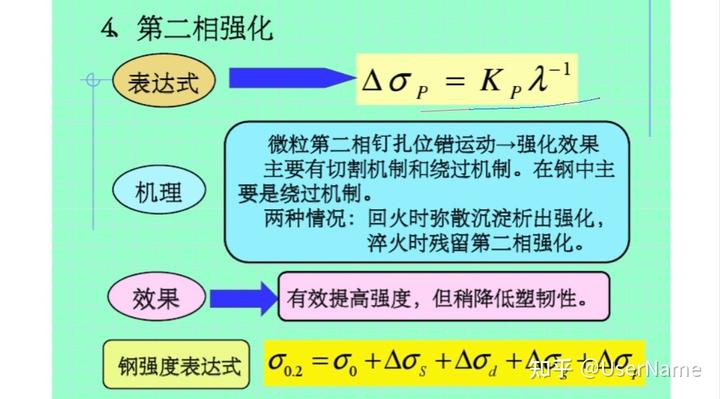
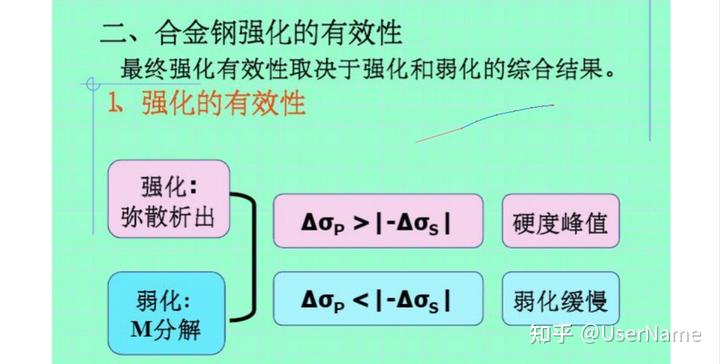
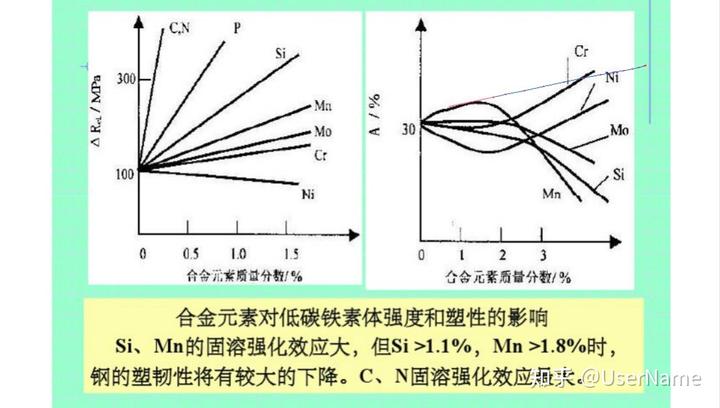
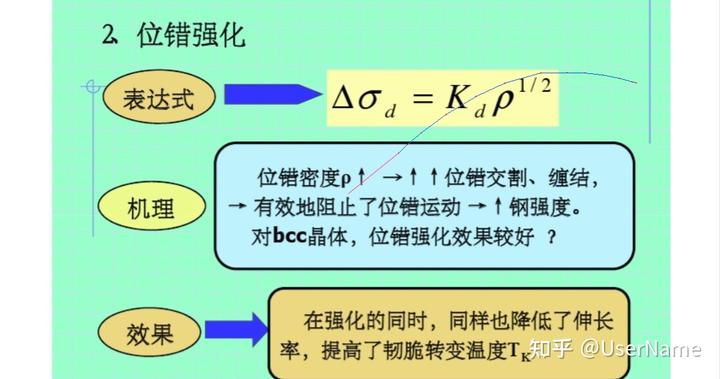
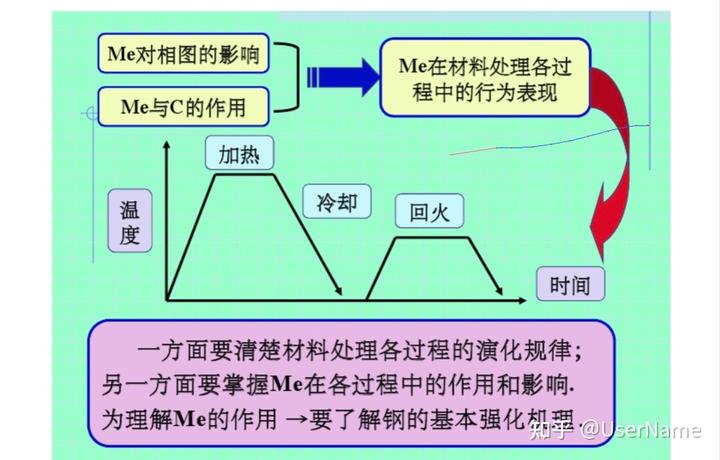
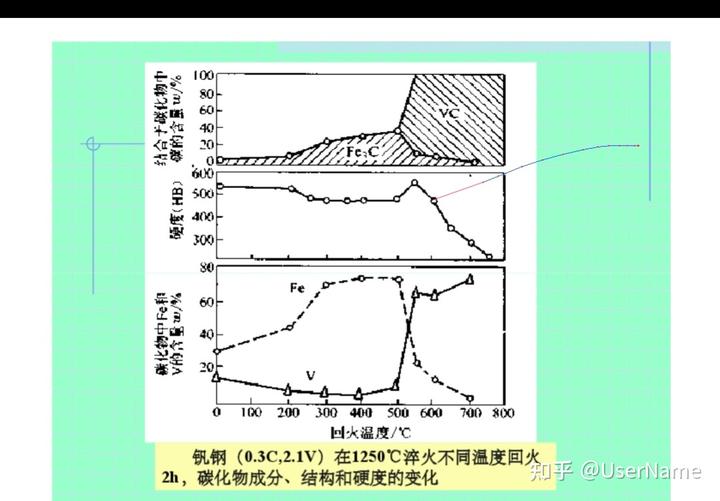
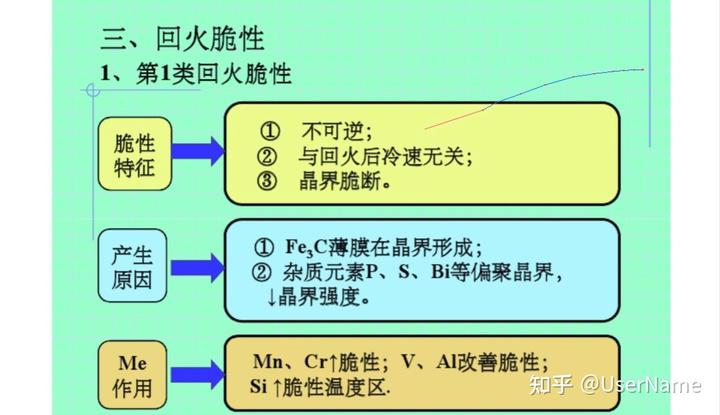
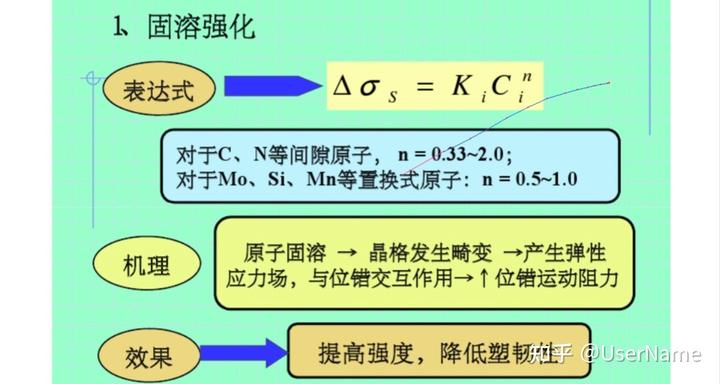
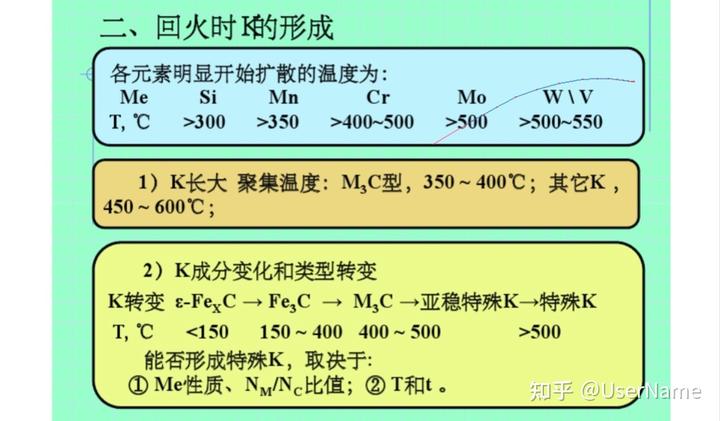
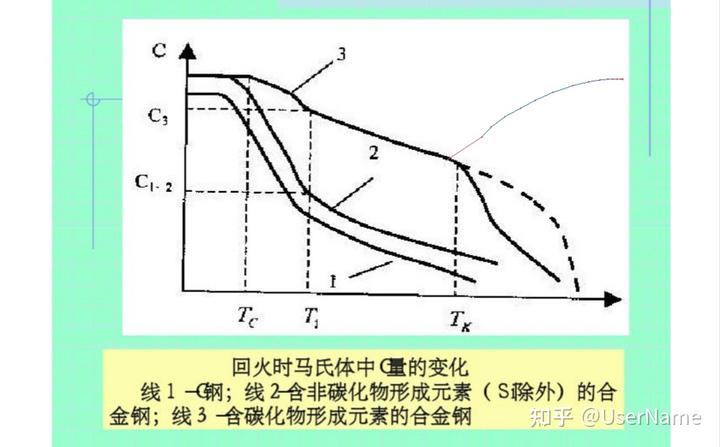
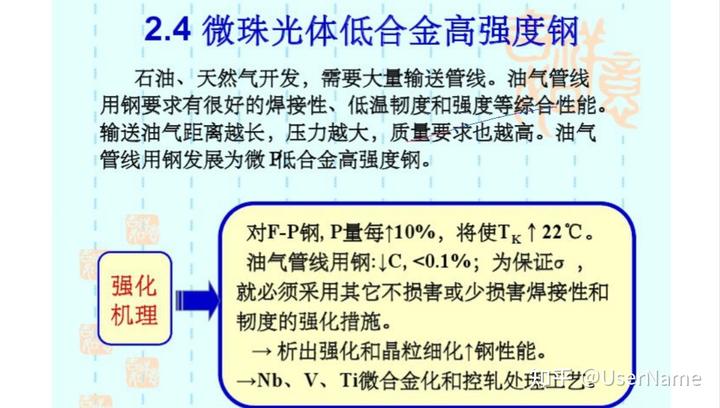
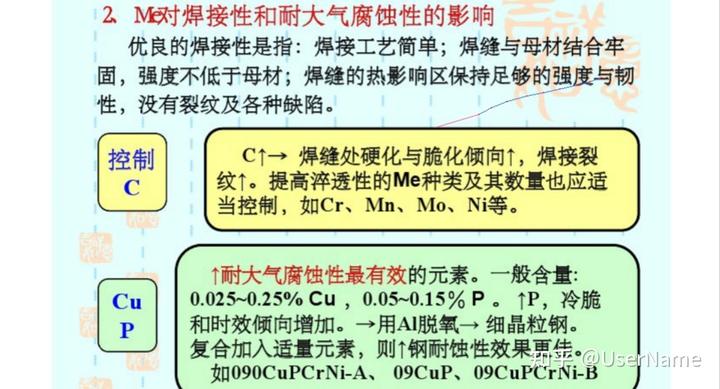
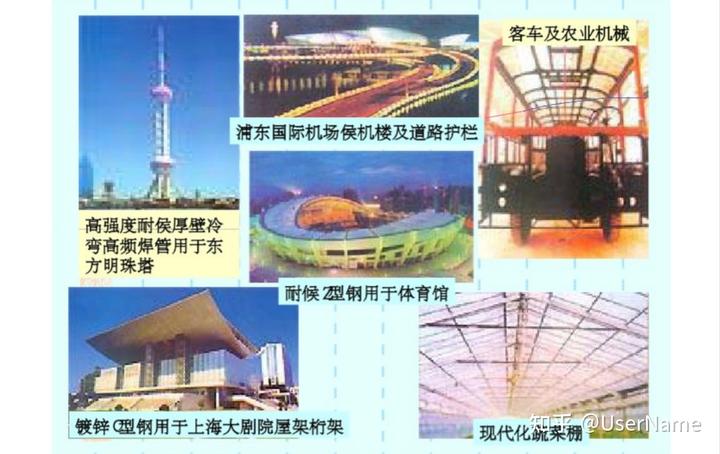
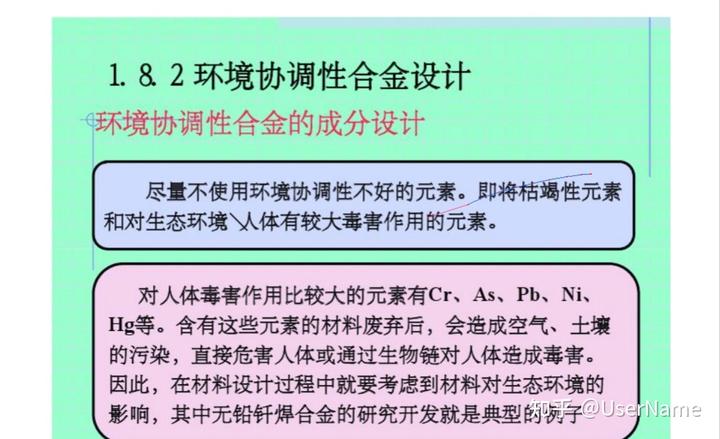
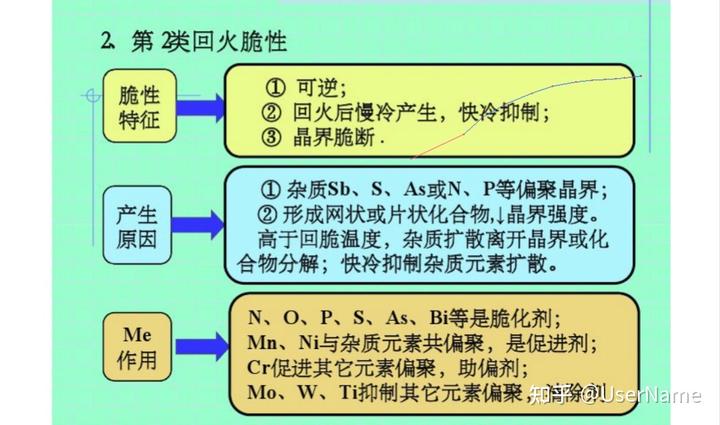
性能材料
要求选择
服役强化
条件零件工艺
最终显微
性能组织
图材料学主线示意图
绪论
金属材料的过去、现在和将来0.1金属材料发展简史
1第一阶段——原始钢铁生产
公元前4300年:自然的金、铜及锻打等工艺公元前2800年:铁的熔炼
公元前2000年:青铜器兴盛,编钟与武器(商、周、春秋战国)
东汉时:反复锻打钢→最原始形变热处理工艺。淬火技术:“浴以五牲之溺,淬以五牲之脂”
→现代的水淬、油淬。
上图:吴王夫差矛和越王勾践剑右上:商周时期的青铜敦和尊
盘一国家一级文物
右下:商代青铜纵目人面像
擂鼓礅二号墓编钟复制件
1981年湖北擂鼓墩二号墓出土战国编钟一套,音律准确,音色优美。其件数和规模仅次于曾侯乙编钟,总音域达5个8度以上,可自己转调,奏出五声、六声、七声音阶构成的各种乐曲。须五人合作演出,众声齐发,交响叠鸣。无愧为古代音乐之绝响。
2第二阶段——金属材料学科的基础
奠定金属材料学科基础:金属学、金相学、相变和合金钢等。1803年:道尔顿提出原子学说,阿伏加德罗提出分子论。1830年:Hessel提出32种晶体类型,普及晶体指数。
1891年:俄、德、英等国科学家分别独立地创立了点阵结
构理论。
1864年:Sorby制备第一张金相照片,9倍,但意义重大。1827年:Karsten从钢中分离出了FeC,1888年Abel证明了
这是Fe,C。
1861年:俄契尔诺夫提出了钢的临界转变温度的概念。19世纪末:马氏体研究已成为时髦,Gibbs得到了相律,
Robert-Austen发现了奥氏体固溶特性,Roozeboom建
立了Fe-Fe,C系的平衡图。
钢的组织命名:
Austenite→英金属学家Austen;Bainite→美科学家Bain;
Sorbite→英科学家Sorby;
Martensite→德科学家Marten;Troostite→法化学家Troost;Ledeburite→德学者Ledebur新合金钢发明:
1820年,铁-铬合金;
1857年,钨钢;1898年,含钨高速钢雏形
1871年,锰钢和硅钢。
开始了合金钢的新纪元
3、第三阶段—微观组织理论大发展
合金相图,X射线发明及应用,位错理论的建立。1912年:发现X射线,证实α(δ)-Fe是bcc,y-Fe是
fcc;固溶体规律。
1931年:发现合金元素的扩大和缩小y区作用
1934年:俄国Polanyi、匈牙利Orowan和英国Taylor各自
独立地提出了位错理论,解释钢的塑性变形;马氏
体转变的晶体学。
1938年:发明了电子显微镜。
1910年:发明A不锈钢,1912年发明了F不锈钢等。
1990年:发明了布氏硬度计,Griffith提出了应力集中会导致产生微裂纹。
4第四阶段微观理论的深入研究
微观理论的深入研究:
原子扩散及其本质的研究;钢TTT曲线测定;
贝氏体、马氏体转变理论形成了比较完整的理论。
位错理论建立:
电子显微镜的发明→看到了钢中第二相沉淀析出,位错滑移,发现了不全位错、层错、位错墙、亚结构、Cottrell气团等现象→位错理论。
新科学仪器不断发明:
电子探针,场离子发射显微镜和场电子发射显微镜、扫描透射电镜(STEM)、扫描隧道显微镜(STM)、原子力显微镜(AFM)等
0.2现代金属材料
先进结构材料的研究与开发是永恒的主题。开发高性能结构材料:高比强度、耐高温、耐腐蚀、耐磨损→降低机械重量、提高性能、延长使用寿命的关键。复合材料→结构材料,广泛应用,如铝基复合材料。开发各种系列用途的低温奥氏体钢。
改造传统结构材料:重要途径是组织更细更均匀,材料更纯洁→关键是工艺。“新一代钢铁材料”强度相当于现有钢铁材料两倍。
美“9.11”事件,暴露建筑用钢结构抗高温软化能力差→开发高强热轧耐火耐候钢。
开发其他高性能钢:利用各种新工艺新方法制造出韧性和耐磨性都很好的新型工具钢。经济合金化是高速钢的一个发展方向,工具材料的各种表面处理技术开发,在新型工具材料的开发上具有重要的意义。
先进制备工艺:如金属半固态加工技术,铝镁合金技术成熟,已应用。
10Ni-8Co钢
u.80010
/600.109Ni-4Co钢强韧化
400.10Ni-Cr-Mo钢现有的技术界限马氏体钢
200J10下限
5Cr-Mo-V钢
0
80010001200140016001800200022002400260028003000
屈服强度/MPa
现有钢的技术界限和钢强韧化努力的方向
材料的发展使汽车和飞机等性能发生了突变水陆车中华
aquada水陆两用汽车
轻型吊轨磁悬浮列
车
美国飞行汽车将于200年上市销售
探索频道易
探索频道
MX-400空中汽车美国莫勒潜心研究.被誉为“汽车演变的里程碑”。飞机外形像一辆新颖别致的小汽车。空中飞行依仗的是它有可转动的发动机及专门提供升力的风扇。
早飞机
COMCTV
COM百年洗
.COM
FBC-1飞
飞行的性能也很好CCTV
CO
自从1903年12月17日美国莱特兄弟把第一双人类翅膀送上天空后,各种飞机不断地在快速发展,对制造飞机各类零部件的材料要求也越来越高。主要是比强度高、重量轻、耐高温、耐疲劳等性能。
纽约世界贸易中心大厦呈
高412米,是世界第二高度
世界贸易大厦基本上是用铝合金贴面的.在“9.11”事件中,该双子大楼遭到袭击,毁于一旦。但它作为一个大量使用铝合金贴面的的雄伟建筑将永远载入史册。
泰坦尼克号快速沉没的原因
小问题引大灾难.泰坦尼克号撞上冰山后快速沉没,经查明是因为含有矿渣的48根铆钉使泰坦尼克号钢板散架
0.3金属材料的可持续发展与趋势
2004年提出了“循环型社会的材料产业——材料产业的可持续发展”。
微生物冶金:无废物的生产,已在许多国家进行了工业性生产。美国利用微生物冶金方法生产的铜占总产量的10,日本人工培植海鞘以提取钒。海水是一种液态矿,海水中含有的合金元素量超过100亿吨。现在已可从海水中提取镁、铀等元素,全世界生产的镁大约有20来自海水,美国靠这种镁已满足着需求量的80%
我国资源短缺;资源浪费严重;污染严重。
循环材料产业:适应时代需要,把生态环境意识贯穿于产品和生产工艺的设计之中,提高材料利用率、降低生产和使用过程中环境的负担。发展形成资源一材料—环境良性循环的产业。
合金发展的主流方向是少合金化与通用合金,形成绿色生态材料体系,有利于材料的回收与再生利用。要研究开发与人民生活密切相关的绿色材料以及环境友好材料。
钛合金被称为“空间金属”、“未来钢铁”。钛合金比强度是最高的,在高温和低温下都能保持高强度,耐蚀性也是无可匹敌的。
钛在地球中含量不少(0.6%)。但是提炼工艺复杂,成本高,广泛应用受到限制。
钛合金将是二十一世纪为人类作重要贡献的金属材料之一。
世界上第一个载人字宙飞船-前苏联的“东方”号飞船世界上第一个载人宇宙飞船世界上第一个“太空人”第一个“太空人”苏联的光里·加加林
有色金属:资源面临着不可持续发展的严重问题,主要是资源破坏严重和利用率很低,浪费惊人。精深加工技术落后,高档产品缺乏;创新成果少,高新技术成果产业化程度不高。开发高性能结构材料及其先进工艺方法是主流,如,铝锂合金、快速凝固铝合金等。
有色金属功能材料也是发展方向
可替代3
容易获取3环境和能源因素
放在很重要的位置
容易接受
自动化程度高8
节能和节材13
有利环境27
价格低40
0020304050
分数(总分为100分未来对材料和技术的要求
思考题
11958年世界工业博览会在比利时召开,博览会大楼是由9个巨大金属球组成,金属球直径为18米,8球位于立方体角,1球在中心。这象征什么?说明什么意义?
2为纪念世界第一位宇航员加加林,莫斯科列宁大街上建造了40英尺高的雕象,雕象材料是钛合金。为什么用钛合金做?代表什么意义?
3金子从古到今都是作为世界上的流通货币,为什么?铜是人类最早认识和使用的金属,为什么?
41983年,在上海召开的第4届国际材料及热处理大会的会标是小炉匠锤打的图案,代表什么意义?为什么古代著名的刀剑都要经过反复锻打?
5为什么建筑上的楼板、大梁混凝土中要用钢筋?而且国家都有使用标准?
第章钢的合金化原理
1.1M和Fe基二元相图
一、钢中的Me
1、杂质元素(impurity- element)常存杂质冶炼残余,由脱氧剂带入。
Mn、Si、Al;S、P难清除。
生产过程中形成,
隐存杂质微量元素O、H、N等。
与炼钢时的矿石、废钢有关,
偶存杂质如Cu、Sn、Pb、Cr等。
2、α稳定化元素使A3↑,A4,Y区缩小
a)完全封闭γ区- Cr、V、W、Mo、Ti
Cr、V与α-Fe完全互溶,量大时→α相?
W、Mo、Ti等部分溶解
b)缩小γ区——Nb等。
稳定y相—A形成元素,稳定a相——A形成元素。
二、M和F的作用
纯Fe→Fe-C相图的变化特点。
Me和Fe的作用:
1、γ稳定化元素使A3,A4↑,Y区扩大
a)与y区无限固溶—Ni、Mn、Co开启Y区——量大时,室温为Y相;b)与区有限固溶C、N、Cu
扩大Y区。
热脆性SFeS(低熔点989℃);?
冷脆性PFe3P(硬脆);
氢脆H白点。
2、合金元素(alloying-element)为合金化目的加入,其加入量有一定范围
的元素称为合金元素。
钢中常用合金元素:
Si、Mn、Cr、Ni、W、Mo、V、Ti等。
Y
AFeM
Fe
(a)Ni, Mn, Co(b)C,N, Cu
Aa(S)
A
α
FeM
Fc
M
(c)Cr,V(d)Nb,B等
图1合金元素和F的作用状态
1. 2 Me对 Fe-C相图的影响
一、对S、E点的影响
A形成元素均使S、E点向左下方移动,F形成元素使S、E点向左上方移动。
S点左移一意味着共析C量减小;
E点左移一意味着出现莱氏体的C量降低。1300
1200TMoSi
1100
1000-
900Cr
C
800Si
Mn
700W
Mn0.1
TiMoN
600Ni
0
2681012141618
5004081012141620
1合金元素质量分数/%
合会元素质量分数/%
合金元素对共析温度的影响合金元素对共析碳量的影响
二、对临界点的影响
A形成元素Ni、Mn等使A1(A3)线向下移动;F形成元素Cr、Si等使A1(A3)线向上移动三、对y-Fe区的影响
A形成元素Ni、Mn等使y-Fe区扩大→钢在室温下也为A体一奥氏体钢;
F形成元素Cr、Si等使y-Fe区缩小→钢在高温下仍为F体一铁素体钢。
常用合金元素点阵结构、电子结构和原子半径
第四Ti
VCrMnFeCoNiCu
周期
点阵fecl
bccbccbccbcc或fcefcc
fcc
结构hcp
电子
结构2
3
5
5
6
7
8
10
原子半0.1450.1360.1280.1310.1270.1260.1240.128
径/nm
△R,%14.27.10.83.10.8
2.40.8
注:1、电子结构是3d层电子数;2原子半径是配位数12的数值
1.3铁基固溶体
置换固溶体
合金元素在铁点阵中的固溶情况
MeTi
VCrMnCoNiCuN
aFe~7~3
76100.20.020.1
溶解度(1340℃)
限限
YFe0.68~1.412.8无限无限无限8.52.062.8
注:有些元素的固溶度与量有关
不同元素的固溶情况是不同的。为什么?
简单地说:这与合金元素在元素周期表中的位置有关。
16001500
15001400
14001300
Cr19%
13001200
C:15%
12001100
211001000
12%Mn 0.35%
100900-A
Mn2.5%
A3
9005%
800
Ma 4%0
Cr0%碳铜Mn35%
803700
701600
Mn.5%
500Mns%
020.40.8 1.01.21.41.61.80
0.29.40.60.81.01.21.41.61.8
109
铬对钢Y区的影响锰对钢
区的影响
(1)Ni、Mn、Co与y-Fe的点阵结构、原子半径和电子结构相似——无限固溶;(2)Cr、V与α-Fe的点阵结构、原子半径和电子结构相似——无限固溶;
(3)Cu和y-Fe点阵结构、原子半径相近,但电子结构差别大——有限固溶;
(4)原子半径对溶解度影响:AR≤±8%,可以形成无限固溶;≤±15%,形成有限固溶;>±15%,溶解度极小。
合金元素的固溶规律,即Hume-Rothery规律决定组元在置换固溶体中的溶解
度因素是点阵结构、原子半径和电
子因素,无限固溶必须使这些因素
相同或相似
二、间隙固溶体
①有限固溶C、N、B、O等
溶剂金属点阵结构:同一溶剂金属不同点阵结构,溶解度是不同的如y-Fe与α-Fe。
②溶解度溶质原子大小:r,溶解度1。
N溶解度比C大:R=0.071nm,
Rc=0.077nm。
③间隙位置
优先占据有利间隙位置—畸变为最小。
间隙位置总是没有被填满最小自由能原理。
复杂点阵结构:M23C6、M7C3、M3C。特点:硬度、熔点较低,稳定性较差;简单点阵结构:M2C、MC。又称间隙相
特点:硬度高,熔点高,稳定性好。
MC型不属于金属型的碳化物,复杂结构,
性能特点接近简单点阵结构。
钢中常见的K类型有:
MC:渗碳体,正交点阵;
M-C3:例Cr-C3,复杂六方;
M23C6:例Cr23C,复杂立方;
M2C:例Mo2C、W2C。密排六方;MC:例VC、TiC,简单面心立方点阵;MC:不是一种金属K。复杂六方点阵。K也有空位存在;可形成复合K,如(Cr,Fe,Mo,..)7C3
1.4 碳(氮)化物
、钢中常见的碳化物
K类型、大小、形状和分布对钢的性能有很
重要的作用。
非K形成元素:Ni、Si、Al、Cu等
K形成元素:
Ti、 Nb、V; W、 Mo、 Cr; Mn、 Fe(由强到弱排列)
二、K形成的一般规律1、类型
K类型与Me的原子半径有关。各元素的的值如下:
MeFeMnCrVMoWTiNb
rcMe0.610.600.610.570.560.550.530.53
rrMe> 0.59-复杂点阵结构,如Cr、 Mn、 Fe,形成CrC3、Cr23C6、Fe3C、Mn3C等形式的K;rrme<0.59—简单结构相,如Mo、W、V、Ti等,形成VC等MC型,W2C等M2C型
Me量少时,形成复合K,如(Cr,M)23C6型。
2相似者相溶
完全互溶:原子尺寸、电化学因素均相似。如Fe3C,Mn2C→(Fe,Mn)3C; TiC~VC。
有限溶解:一般K都能溶解其它元素,形成复合K如Fe3C中可溶入一定量的Cr、W、V等.最大值为<20%Cr,<2%W,<0.5%V;MC型不溶入Fe,但可溶入少量W、Mo。
溶入强者,使K稳定性↑;溶入弱者,使K稳定性
5.强者稳,溶解难,
析出难,聚集长大也是难
MC型在1000℃以上才开始溶解;回火时,在500~700℃才析出,并且不易长大,产生“二次硬化”效果。这在高合金钢中是很重要的强化方法。
4、N/Nc比值决定了K类型
M
形成什么K主要决定于当时的NMNC比值。退火态:在Cr钢中,随NM/Nc↑,先后形成顺序为:M3C→M-C3→M23C6。
回火态:基体中的NM/Nc↑,则析出的K中NM/Nc也1。如W钢回火时,析出顺序为:
Fe21W2C6→WC→Fe4W2C→W2C, NWINc是不断↑。
3、强者先,依次成
K形成元素中,强者优先与C结合,随C1,
依次形成K。如:在含Cr、W钢中,随C1,依
次形成M6C,Cr23C。,Cr7C3,Fe3C。如果钢中C量有限,则弱的K形成元素溶入固
溶体。如:在低碳含Cr、V的钢中,大部分Cr都
在基体固溶体中。
1.5Me在钢中的存在形式
Me在不同状态下的分布
1、退火、正火态非K形成元素基本上固溶于基体中,而K形成元素视C和本身量多少而定。优先形成K,余量溶入基体。
2、淬火态Me分布与淬火工艺有关。溶入A体的元素淬火后存在于M、B中或AR中;未溶者仍在K中。
3、回火态低回:Me不重新分布;>400℃,Me开始重新分布。非K形成元素仍在基体中,K形成元素逐步进入析出的K中,其程度决定于回火温度和时间。
二、Me的偏聚(segregation)
偏聚Me偏聚→缺陷处C'>基体平均C
现象这种现象也称为吸附现象。
偏聚现象对钢的组织和性能产生了较大影响,如晶界扩散、晶界断裂、晶界腐蚀、相变形核等都与此有关
Me+⊥:溶质原子在刃型位错处吸附,形成柯氏气团;Me+=:溶质原子在层错处吸附形成铃木气团;
Me+:溶质原子在螺位错吸附形成Snoek气团
偏聚溶质原子在缺陷处偏聚,使系统自由能↓,
机理符合自然界最小自由能原理。
结构学:缺陷处原子排列疏松,不规则,溶质原子容易存在;
能量学:原子在缺陷处偏聚,使系统自由能↓,符合自然界最小自由能原理。(在没有强制外力作用下,事物总是朝着↓能量的方向发生。即使暂时不发生,也存在潜在的趋势。
热力学:该过程是自发进行的,其驱动力是溶质原子在缺陷和晶内处的畸变能之差。
温度℃
1014001200
1000800
10
10
10-
10-3TiC
NbC
VN
10-1AIN
TiN
10NbN
10-6
8
10
(10T)K
碳(氮)化物在奥氏体中的溶解度与加热温度的关系
影响缺陷处
E
因素溶质浓度C = C。 exp
RT
温度T:T,内吸附强烈;
时间t:偏聚需要原子扩散→需要一定时间;缺陷本身:缺陷越混乱,E↑,吸附也越强烈;其它元素:①间接作用:优先吸附问题,B与C
②直接作用:影响吸附元素D,Mn↑Dp,使P扩散加快,促进了钢的回火脆性;Mo则相反,是消除或减轻回火脆性的有效元素。点阵类型:bcc点阵内吸附较fcc强烈
1.6合金钢的加热A化
一、K在A中的溶解规律
1)K稳定性越好,溶解度就越小;2)温度,溶解度,→沉淀析出;
基本规律3)K稳定差的先溶解;
4)A中有弱K形成元素,则会C活度a,→1K的溶解;非K形成元素(如Ni)则相反,↑ac,K的溶解。如:较多Mn的存在使VC的溶解温度从1100℃降至900℃。
二、A体均匀化
A体刚形成时,C和Me的分布是不均匀的合金钢加热均匀化与碳钢相比有什么区别?三、A体晶粒长大
1)Ti、Nb、V,W、Mo晶粒长大;2)C、N、B↑晶粒长大;
3)Ni、Co、Cu作用不大。
1.7过冷A体的分解
一、过冷A体的稳定性
1)Ni、Si和Mn,大致保持C钢的“C"线形状,使“C"线向右作不同程度的移动;
2)Co不改变“C”线,但使“C"线左移;
3)K形成元素,使“C"线右移,且改变形状。
Me不同作用,使“C"曲线出现不同形状,大致有五种。
过冷A体稳定性实际上有两个意义:孕育期和
相变速度。孕育期的物理本质是新相形核的难易
程度,转变速度主要涉及新相晶粒的长大。
A
TP
P
P
BB
MsMs
Ms
tt
a)Ni、Si、Mnb)Cr、Mo、W、Vc)Cr
A“C曲线五种形状
B
MsMs(<0℃)
tt
d)W、Moe)Ni、Mn
思考题:
W、Mo等元素对贝氏体转变影响不大,而对珠光体转变的推迟作用大,如何理解?
对一般结构钢的成分设计时,要考虑其M点不能太低,为什么?
二、过冷A体的RB转变
P转变:需要C和Me都扩散;
综合影响顺序:Mo、W、Mn、Cr、Ni、Si贝氏体转变:C原子作短程扩散,Me几乎没有扩散。
影响顺序:Mn、Cr、Ni、Si,而W、Mo等影响很小。
三、Me对M的影响
各种Me对Ms位置的影响程度是不同的。
TT
TiVNbWMoCr
WMoViNbCrMn
Mo
C(WMoVT)MnCr
MsMs
CMnCr
CWMoTiVMoCr
CVMo
T年SiAI常用合金元素对奥氏体等
SiAl温转变曲线的影响
(上左)强K形成元素A
Si(上右)中、弱K形成元素
A(下左)非K形成元素
MSiAI
1.8合金钢的回火转变
一、M分解
低温回火:C和Me扩散较困难,Me影响不大中温以上:Me活动能力增强,对M分解产生不同程度影响:
1)Ni、Mn的影响很小;
2)K形成元素阻止M分解,其程度与它们与C的亲和力大小有关。这些Mela,阻止了渗碳体的析出长大;
3)Si比较特殊:<300℃时强烈延缓M分解Si和Fe的结合力>Fe和C的结合力,↑a
Si能溶于,不溶于Fe,C,Si要从中出去
le-FexC的形核、长大
→Fe3C
效果:含2%Si能使M分解温度从260℃提高到350℃以上
4)合金钢回火时M中含量变化规律
渗碳体形成开始温度与合金化无关;2含非碳化物形成元素(S除外)的合金钢(线2)和G钢(线)规律相同;
基本规律③在相同回火温度T下,合金钢马氏体中含
C量要比C钢的高,如图中的C3>C12;④不同合金中,马氏体中析出特殊碳化物的温度T是不同的,线3的下降幅度也是不同的。
100
20
0
600
(aH)500
400
300
80Fe
是B空>20
0100200300400500600700800
回火温度/℃
钒钢(0.3C,2.1V)在1250℃淬火不同温度回火2h,碳化物成分、结构和硬度的变化
二、回火时K的形成
各元素明显开始扩散的温度为:
MeSi
MnCr
Mo
WIV
T, ℃>300>350>400~500>500>500~550
1)K长大聚集温度:MC型,350~400℃;其它K,450~600℃;
2)K成分变化和类型转变
K转变-FeC→FeC →MC→亚稳特殊K→特殊KT,C<150150~400400~500>500
能否形成特殊K,取决于:
①Me性质、NM/Nc比值;②T和t。
C3
C32
C2Te
写IK
回火时马氏体中量的变化
线1-钢;线2-合非碳化物形成元素(S除外)的合金钢;线3含碳化物形成元素的合金钢
3)特殊K的形成
原位析出:αM→a+M3C
MXCY(M7C3, M23C6)
异位析出:αM →ap+M3C
a+MCy(MC,M2C)
特殊K析出→二次硬化,直接析出一贡献最大
三、回火脆性
1、第1类回火脆性
脆性①
不可逆;
特征2
与回火后冷速无关;
3晶界脆断。
产生①FeC薄膜在晶界形成;
原因②
杂质元素P、S、Bi等偏聚晶界,↓晶界强度。
MeMn、Cr↑脆性;V、Al改善脆性;
作用Si↑脆性温度区
2第2类回火脆性
脆性①
可逆;
特征2
回火后慢冷产生,快冷抑制;3晶界脆断
①杂质Sb、S、As或N、P等偏聚晶界;
产生②形成网状或片状化合物,晶界强度。
原因高于回脆温度,杂质扩散离开晶界或化
合物分解;快冷抑制杂质元素扩散。N、O、P、S、As、Bi等是脆化剂;
MeMn、Ni与杂质元素共偏聚,是促进剂;
作用Cr促进其它元素偏聚,助偏剂;
Mo、W、Ti抑制其它元素偏聚,清除剂
Me对相图的影响Me在材料处理各过
程中的行为表现
Me与C的作用
加热冷却回火时间
一方面要清楚材料处理各过程的演化规律;另一方面要掌握Me在各过程中的作用和影响为理解Me的作用→要了解钢的基本强化机理
1.9
Me对钢强韧化的作用一、M对钢强化的形式及其机理强化本质:
各种强化途径↑塑变抗力
↑钢强度↑位错运动阻力
1固溶强化
表达式△σ=K1Cn
对于C、N等间隙原子,n=0.33~2.0;
对于Mo、Si、Mn等置换式原子:n=0.5~1.0
机理原子固溶→晶格发生畸变→产生弹性
应力场,与位错交互作用→↑位错运动阻力
效果提高强度,降低塑韧性
CNP
SiCr
300N
2/2<Mn
Mo/30Mo
Cr
100Si
NiMn
00.51.01.50
123
合金元素质量分数/%合金元素质量分数/%
合金元素对低碳铁素体强度和塑性的影响
Si、Mn的固溶强化效应大,但Si>1.1%,Mn>1.8%时,钢的塑韧性将有较大的下降。C、N固溶强化效应最大。
240NC
160I
WMo
80BSi
VMp
Co
Ni
-40Cu
0246812
1416
合金元素摩尔分数%
合金元素对Cr18Ni9型不锈钢的强化效应I-间隙元素,II-F形成元素,II-A形成元素
2位错强化1/2
表达式△od=KaP
位错密度p→↑↑位错交割、缠结,
机理→有效地阻止了位错运动→↑钢强度。对bcc晶体,位错强化效果较好?
效果在强化的同时,同样也降低了伸长
率,提高了韧脆转变温度TK
3细晶强化△o
=Kd-1/2
表达式著名的Hall-petch公式
式中,d为晶粒直径,Kg为系数晶粒越细→晶界、亚晶界越多→有效
机理阻止位错运动,产生位错塞积强化。
效果↑钢的强度,又↑塑性和韧度
这是最理想的强化途径
g=[111]
160.0VX3K288nm晶界处位错塞积现象0.5m
4第二相强化
表达式△op=KpA-1
微粒第二相钉扎位错运动→强化效果主要有切割机制和绕过机制。在钢中主
机理要是绕过机制。
两种情况:回火时弥散沉淀析出强化,
淬火时残留第二相强化。
效果有效提高强度,但稍降低塑韧性。
钢强度表达式002 =00 +△0s +o1 +o。 +△o
运动的位错线留下的
位错圈
D
沉淀粒子位错被质点障碍物所挡住
900
800
700
600
500
400细品强化
300析出强化
200位错强化
100固溶强化
0基体强度
400600
800
钢级/MPa
在低碳结构钢中各种强化效果示意图
二、合金钢强化的有效性
最终强化有效性取决于强化和弱化的综合结果。1、强化的有效性
强化:
弥散析出Aop >|-Aas |
硬度峰值
弱化:Aop<|-Aos |
弱化缓慢
M分解
强度3
-△0s2
+TT
回火温度/℃
图强化和弱化的演变
1-M分解;2-弥散析出;3-综合效应
HRC40钢0.91%V
50不同含C量
400.25%V
的V钢,如
产生二次硬
30化,V的临
0.02%V界浓度是不
20同的,为什
么?
500600
回火温度℃
图V对40钢回火硬度的作用
2、Me对强化有效性的影响
强化有效性取决于形成弥散相的Me及其量。
Me量↑→弥散相量1(有足够的C)→二次硬化1
强化Me最小浓度
K类型
弱化临界值
含C量
例:含0.1~0.15%C钢,
需0.1~0.2%V;0.08~0.12%Nb;2.5~3.0%Cr
对结构钢,细晶强化和沉淀强化贡献最大。合金钢与(钢的强韧性差异,主要不在于Me本身的强化作用,而在于Me对钢相变过程的影响,并且M的良好作用,只有在进行合适的热处理条件下才能充分得到发挥。
需要充分理解
三、M对钢韧性的影响
1、影响韧性的因素
强化
因素一般情况,钢强度1→塑韧J,称为强韧
性转变矛盾。除细化组织强化外,其它强化因素都会程度不同地↓韧性。
危害最大是间隙固溶;
沉淀强化较小,但对强化贡献较大。
合金
元素Nit韧性;Mn在少量时也有效果;其它
常用元素都在不同程度上J韧性
晶粒细晶既1s,又具TK,即↑韧性
度→
最佳组织因素。
第二KJ韧性。K小、匀、圆、适量
相工艺努力方向。
杂质杂质往往是形变断裂的孔洞形成核心,
→提高钢的冶金质量是必须的。
NiRel
0
200Cr
300
一-5
MnSi-100
100150
TK
Mol
2
46110
1053
合金元素/%(质量分数)品粒直径d/um
合金元素对铁素体晶粒大小对强度、韧脆转
冲击韧度的影响变温度TK的影响
140
12015~20um
100A
o5~6um
1~2um
80
60
40
20口
-20-40-60-80-100-120-140-160-180-200
温度℃
20MnSi钢不同晶粒度的低温冲击性能
2提高钢韧度的合金化途径
1)细化晶粒、组织如Ti、V、Mo;2)↑回火稳定性如强K形成元素;3)改善基体韧度Ni;
4)细化K适量Cr、V,使K小而匀;
5)回脆W、Mo;
6)在保证强度水平下,适当含C量↑冶金质量。
二、热压力加工性
热压力加工有锻造、轧制、拉拔等。
Me溶入基体→产生畸变,热变形抗力→热压力加工性能↓。如Mo、W、Cr、V等元素影响较大。C和Me量较多时,形成共晶K,热压力加工性更差。
合金钢的热压力加工性能比碳钢差。高速钢等高合金钢的热压力加工难度是较大的
1.10Me对钢工艺性的影响
一、冷成型性
冷成型性包括:深冲、拉延、弯曲等。冷作硬化率是在冷变形过程中,材料变硬变脆程度的表征参量。冷作硬化率高,材料的冷成型性差。P、Si、C等元素1冷作硬化率。需要冷成型的材料应严格控制R量,尽可能↓Si、C等量。
思考题:
有些零件为什么要经过调质处理,而不直接用正火态?
三、切削加工性
不同情况侧重点不同,如粗加工,主要考虑速度;精加工主要考虑表面粗糙度。
C钢硬度在170~230HB,切削性能最好对组织来说,P:F=1:1较佳。不同含C量的钢要得到较好的切削性,其预处理是不同的:
对C钢:<0.1%C,宜淬火;
<0.5%C,宜正火;
<0.8%C,宜退火;
>0.8%C,宜球化退火
思考题:
为什么钢的切屑是连续的,而铸铁的切屑是碎片状断开的?
四、材料的热处理工艺性
淬透性
一般是指淬火时获得M的能力合金元素复合作用大,不是简单加和钢号合金元素质量分数含量%
P转变孕育期/秒
35CrCr+Ni=1.34
12
35CrMoCr+Mo=1.38
35
40CrNiMoCr+Mo+Ni=3.25
500
淬硬性
理想淬火条件下,形成M能达到的最高硬度淬硬性主要与钢的含碳量有关。
变形开裂倾向
热应力→变形;组织应力→开裂;附加应力较复杂影响因素比较复杂,要综合分析
采用分级淬火、等温淬火或双液淬火可降低应力,减小变形开裂倾向。采用调质、球化退火等预先热处理也可减小零件的变形。
贝氏体合金化基本元素是0.5%Mo+
淬透性微量B。
+Mo→能有效↓P转变,但不能完全↓先共
析F的析出↑B淬
+B→偏聚晶界→
有效抑制先共析F的析出透性
析出5(600℃)0.14%Mo0.35%Mo0.60%Mo
0.401:
2:
4
%CP开始转变时间1:
3:
36
在结构钢中,1M淬透性作用显著的元素从大到小排列:(B)、Mn、Mo、Cr、Si、Ni。
可以使工件得到均匀而良好的力学淬透性能,满足技术要求;
性好
的作
用在淬火时,可选用较缓和的冷却介
质,以减小工件的变形与开裂倾向
过热敏感性和氧化脱碳倾向
奥氏体晶粒急剧长大的敏感性,→Mn.如
40Mn2、50Mn2、35SiMn、65Mn等。氧化和脱碳往往伴随产生.→Si.含硅钢氧
化脱碳倾向较大,如9SiCr、42SiMn、60Si2Mn、30CrMnSi等。
脱碳会降低钢的硬度、耐磨性和疲劳强度,
脱碳对于工具、轴承、弹簧等零件是极其有
害的
回火稳定性热稳定性)
合金钢回火稳定性要比碳钢好.同样回火硬度,合金钢的回火温度高,时间也可长些,应力消除也大些;同样塑韧性,合金钢的强度比碳钢高
回火脆性(前面已介绍)
钢的编号方法自学
103/553☐
组元组成简单的合金系就叫做简单合金。简单合金在成分设
简单计上有几个特点:
合金合金组元简单,再生循环过
程中容易分选;
原则上不加入目前还不能用精炼方法除去的元素;
尽量不使用环境协调性不好的合金元素。
1.8.1通用合金与简单合金
又称为泛用性合金。这种通用合金能满足通用性能,合金在具体用途中的性能要求则可以通过不同
通用的热处理等方法来实现。
合金Fe-Cr-Ni、Fe-Cr-Mn钢.通过改
变Fe、Cr、Ni(Mn)的相对含量,其组织结构和性能也可以在很大范围内变化。
Cr-Mo钢,耐热钢
1.8金属材料的环境协调性设计目前世界上金属材料及其合金的种类大约有三千多种。→材料的废弃物再生循环很困难
可再生循环设计已成为钢铁材料设计的一个重要原则。传统的思路和方法应该更新。应该发展少品种、泛用途、多目的的标准合金系列。所以就出现了通用合金和简单合金的概念。
(1)在维持合金高性能的前提
下,尽量减少合金组元数;
两个
基本
原则(2)获得合金高性能时,以控
制显微组织作为加入合金元素的替
代方法。
这种设计合金的思路叫省合金化设计或最小合金化法。简单合金的主要用途是代替大量消费的金属结构件材料。
Si-Mn合金钢就是目前重点开发的一种普通的简单合金。可以通过各种热处理获得不同的组织结构,如F+P、F+B、
典型例子B+M、B、M等,→得到不同强度、塑性配比的性能,以满足各种用途。
Si和Mn作为主要合金元素,在地球上储量相当大,并容易提取。是一个有前途的环境材料系列。在汽车薄板和冲压件上得到了广泛的应用
1.8.2环境协调性合金设计
环境协调性合金的成分设计
尽量不使用环境协调性不好的元素。即将枯竭性元素和对生态环境人体有较大毒害作用的元素。
对人体毒害作用比较大的元素有Cr、As、Pb、Ni、Hg等。含有这些元素的材料废弃后,会造成空气、土壤的污染,直接危害人体或通过生物链对人体造成毒害。因此,在材料设计过程中就要考虑到材料对生态环境的影响,其中无铅钎焊合金的研究开发就是典型的例子
表常见金属材料的环境负荷及其性能环境负荷比金属材料FeAlTiZnCrNiCuMn
环境负荷1.339.0415.518.216.719.424.05.0
(ELV)
比强度4.194.089.981.694.175.612.466.78
(b/p)
弹性比功6.681.250.250.390.472.910.181.29
(2/E)
(ab/p) /3.150.450.640.090.250.290.101.34
ELV
(o2/E)/5.020.140.020.020.030.150.01
ELV0.26
性能环境负荷比
环境负荷是一个资源、能源、三废的综合数据。金属材料各种表面技术的环境影响差别也是较大的。表面技术处理涉及到表面处理过程中的能源消耗、资源消耗和废弃物排放
从总体趋势上说,对环境影响的强弱而言,按电子束表面处理→电火花表面处理→激光表面处理→加热处理→气体表面渗碳处理→火焰表面处理→离子化学热处理,从弱到强排列
表某些金属元素对人体的毒害作用系数金属空气中
水中
土壤中
As4700
1.4
0.043
Cd580
2.9
7.0
Cr6+47000
4100
130
Co24
2.0
0.065
Cu0.24
0.020
0.0052
Fe0.042
0.0036
Pb160
0.79
0.025
Mn120
Zn0.033
0.0029
0.0070
Hg120
4.7
0.15
Mo3.3
0.29
0.70
Ni470
0.057
0.014
小结
材料学核心是合金化基本原理,这是材料强韧化矛盾的主要因素。
要真正理解“合金元素的作用,主要在于对合金材料相变过程的影响,而良好的作用只有在合适的处理条件下才能得到体现。
掌握了合金元素作用及其在加工过程中的演化规律,才能更好地理解各类钢设计与发展,才能更好地开发新工艺、新材料。
第2章工程结构钢
工程结构钢是指专门用来制造工程结构件的一大类钢种。在钢总产量中,工程结构钢占90%左右。工程结构
钢包括碳素钢和低合金高强度钢。
低合金高强度钢是指在碳含量低于0.25%(质量分数下同)的普通碳素钢的基础上,通过添加一种或多种少量合金元素(低于3%,使钢的强度明显高于碳素钢的
一类工程结构用钢,统称低合金高强度钢。
按用途可分为结构钢、耐腐蚀钢、低温用钢、耐磨钢、
钢筋钢、钢轨钢及其他专业用钢等
K类型对相图
及性质影响
合金化设计
K形成对C线
规律的影响
Me对过组织Me对工程影响设计艺性作用合金韧化强韧化矛盾钢强化基本途径演化规律基本机理
客车及农业机械
浦东国际机场侯机楼及道路护栏
高强度耐侯厚壁冷
弯高频焊管用于东
方明珠塔耐候2型钢用于体育馆
镀锌型钢用于上海大剧院屋架桁架现代化蔬菜棚
三
2.1工程结构钢的基本要求
工程结构件长期受静载;互相无相对运动
服役受大气(海水)的侵蚀;有些构件受疲劳冲击;
条件一般在-50~100℃范围内使用;
如:桥梁、船舶等受到像风力或海浪冲击
生产焊接是构成金属结构的常用方法;一般都要
工艺经过如剪切、冲孔、热弯、深冲等成型工艺1、足够的强度与韧度(特别是低温韧度);
技术2、良好的焊接性和成型工艺性;
要求3、良好的耐腐蚀性;
4、低的成本。
C和N
+300P
+225Si
合金元素对低合金高
+150强度钢的固溶强化
CuMn
+75Mo
0Ni和Al
200
0.11%C
-75Cr
0.5101.52021600.20%
合金元素含量质量分数120
0.31%
800.41%
钢的韧一脆转折温度与碳0.60%
含量的关系40
0.80%
-200-120-40040120200
温度/℃
固溶强化作用大,1%Mn,33MPa约有3/4量溶入F中,弱的细晶作用,TK。
Mn同样量多时可大为降低塑韧性
所以Mn控制在<1.8%。
形成稳定细小的K等,粒子2~10nm,
NbV既细晶又沉淀强化,↑s,↑8、AK
TiAI综合效果T。改善焊接性。
作用顺序:Ti>b>Al>V。
Re脱氧去硫吸氢作用,改善塑韧性,↓T
所以,低合金高强度钢的基本成分应考虑低碳,
稍高的锰含量,并适当用硅强化。
2.2低合金高强度结构钢的合金化
1M对低合金高强度钢力学性能的影响
↑固溶强化效果和珠光体含量,低成本。
C↑C,塑、韧性,焊接性、冷成型。
如0.1%C,T为-50℃,0.3%C,TK为50℃一般均应限制在0.2%以下
最常用且较经济的元素。强化F较显著
Si1%Si,s↑85MPa,↑TK,量多时可大为
降低塑韧性,所以Si控制在<1.1%
P+53N+30Sn+17
+6C+10
20%珠光体Si+8
位销+4
析出I+1
30MPa
屈服应力50℃
屈服应力Mn-5
晶粒细化ITT-]
-10A1-27
(a)强化机制的影响(b)成分的影响
图铁素体-珠光体钢的各种强化机制和成份对屈服强
度和韧-脆转折温度的影响
2Me对焊接性和耐大气腐蚀性的影响
优良的焊接性是指:焊接工艺简单;焊缝与母材结合牢
固,强度不低于母材;焊缝的热影响区保持足够的强度与韧
性,没有裂纹及各种缺陷。
控制C1→焊缝处硬化与脆化倾向1,焊接裂
C纹↑。提高淬透性的Me种类及其数量也应适
当控制,如Cr、Mn、Mo、Ni等。
↑耐大气腐蚀性最有效的元素。一般含量
Cu0.025~0.25%Cu,0.05~0.15%P。↑P,冷脆
P和时效倾向增加。→用AI脱氧→细晶粒钢。
复合加入适量元素,则↑钢耐蚀性效果更佳。如090CuPCrNi-A、09CuP、09CuPCrNi-B
低碳工程构件经加工或高温冷却后,时效在室温或较低温度下放置一段时间,
现象钢的性能会发生明显变化的现象。
(淬火时效和机械时效)
C、N等间隙原子偏聚或内吸附于产生位错等晶体缺陷处。提高硬度、降低
原因塑性和韧度。如:某钢板刚变形时,
AK120J,十天后降为35J;焊接钢板
在三个月后由92J降为33J。
当然桥梁、船舶等突然断裂的原因很多。共振、应力波等
低碳铁素体珠光体钢超细晶钢材生产工艺控制和不同的制品
2.3铁素体-珠光体钢
F-P类型是工程结构钢中最主要的一类钢。有Q295、Q345、Q390、Q420、Q460五个牌号。根据质量要求分为A、B、C、D四个等级。A、B级为普通质量级;C级为优质级;D级和E级为特殊质量级,有低温冲击韧性要求。
组织:10~25%片层状P+75~90%多边形F。最新研究成果:如F晶粒尺寸细化到μ级,则F-P类低合金高强度钢的强度也可达到800MPa
思考题:
退火后的低钢板一般在深冲前,先进行一次少量变形的平整加工,然后长进行深冲,为什么?
2.4微珠光体低合金高强度钢石油、天然气开发,需要大量输送管线。油气管线用钢要求有很好的焊接性、低温韧度和强度等综合性能输送油气距离越长,压力越大,质量要求也越高。油气管线用钢发展为微低合金高强度钢。
对F-P钢,P量每10%,将使TK↑22℃。
油气管线用钢:C,<0.1%;为保证,强化就必须采用其它不损害或少损害焊接性和
机理韧度的强化措施。
→析出强化和晶粒细化↑钢性能。
→Nb、V、Ti微合金化和控轧处理工艺
控制轧制和控制冷却技术
高温形变热处理→大幅度晶粒细化→↑强度和韧度。高精轧温度
低
普通轧制控制轧制(CR)
再结品控制冷却(AcC)
图中轧制温
度向右边降
√低,上层表
示奥氏体组
用高倍率观察织变化,下
α结晶粒变形带
基体中的相变核层表示奥氏
体开始相变
后组织及F
核的形成
Y基体通过控制轧制或控
制冷却新生成的α相变核
控制轧制和控制冷却的组织变化模式图
普通轧制CR
CR+AcC
RR
R
水冷
FArs
R:粗轧
F:精轧时间
图各种轧制程序模式图CR:控制轧制;AC:控制冷却
26低碳贝氏体和马氏体钢低碳贝氏体钢是指含碳量为0.10~0.15%,使用状态组织为B的钢。贝氏体钢通常是在轧制空冷或控制冷却,直接获得B组织。
由于B的相变强化,低碳贝氏体钢与相同含碳量的铁素体-珠光体型钢相比,具有更高的强度和良好的韧度,屈服强度可达450-980MPa
2.5针状铁素体钢
对于一些强度、焊接性、低温冲击韧性等要
求更高的场合,还必须采用针状铁素体低合金
高强度钢。针状铁素体(acicular ferrite,简写AF)钢实际上属于超低碳贝氏体钢。
基本≤0.06%C+适量Mn、Mo、Nb等→具有
特点高密度位错(101cm-2)亚结构的“针状F"
组织(超低碳B)。σ达700~800MPa,低温冲击韧性、焊接性更好
用于现场焊接条件及其寒冷地带管线。被称为21世纪的控轧钢。
沉淀析出强化相主要是低温下析出的Nb(C,N)和VC。
Nb≤0.04%时,Ao>Aoh;Nb≥0.04%时, Aoph
增量大大增加,而A保持不变。V引起析出强化增量
A最显著,而Ti的作用处于Nb和V之间。
400
300
200
100
00.040.08004
0.080.120.160
0.040.080.120.16
w(Nby%w(Vy%
w(Ti)/%
(a)(b)
(c)
微合金元素对钢的屈服强度的影响
(:晶粒细化的贡献:析出强化的贡献)
合金元素是保证在较宽的冷速范
围内获得以贝氏体为主的组织
主要成分特点:
特点0.5%左右Mo+微量B(0.005%)
+Mn、Cr、Ni等+Nb、Ti、V
主要用于制造容器的板材和其他
钢结构。
14MnMoV和14MnMoVBRE钢是我国发展的低碳贝氏体钢,屈服强度为490MPa级
低碳马氏体钢
工程机械上相对运动部件和低温下使用部件,要求有更高的强度和良好的韧性。
≤0.16%C,加入Mo、Nb、V、B及控制Mn或Cr与之配合→淬火回火处理组织为低碳回火马氏体。
BHS-1钢的成分为0.10C-1.80Mn-0.45Mo-0.05Nb。锻轧后空冷或直接淬火并自回火。达到合金调质钢调质
后的性能水平。
制造汽车的轮臂托架、操纵杆、车轴、转向联动节和
拉杆等,也可用于冷墩、冷拨及制作高强度紧固件。
2.7
双相钢
主要成分为:~0.2%C,1.2~1.5%Si,
成分0.8~1.5%Mn, ~0.45%Cr, ~0.4%Mo,
少量V、Nb、Ti。(质量分数)
F+M组织,F基体上分布不连续岛
组织状混合型M(<20%)→双相钢。
F中非常干净,C、N等间隙原子很少;C和Me大部分在M中.
CCTV清
COMCCTV
COM
Santana 2000
冲压型双相钢主要是板材,广泛用一于各种容器和汽车冲压件。
非冲压双相钢有棒材、线材、钢筋薄壁无缝钢管等产品。钢材经热轧后控制冷却,得到F加M双相钢组织,然后经冷拨、冷墩等工艺制成成品。可用于汽车的大梁和滚型车轮,汽车的前后保险杠、发动机悬置梁等,使用双相钢可使汽车重量降低10~30%
低s,且是连续屈服,无屈服平台和上、
性能下屈服;均匀塑变能力强,总延伸率较大,冷加工性能好;加工硬化率n值大,成型后s可达500~700MPa。
强度MPa双相钢
600
400普通钢
20010203040应变/%
双相钢和普通钢应力应变曲线的比较
低合金高强度钢发展趋势
低碳超低碳<0.06%甚至<0.02%
高纯净化净化钢中的有害杂质
微合金化技术复合微合金化
控轧和控冷工艺自动化在线控制
超细晶粒化组织微细化
计算机控制和性能预报在线生产系统
两倍疲劳强度的焊丝MP超细品钢具有两倍工作寿命
低维护费用的超级钢
具有两倍强度(2000MP
级超级钢螺栓具有耐氯离子腐蚀的低镍不锈钢采用超级钢概念及技术构造的超级结构示意图
表3不同钢类确保强度翻番”的超细晶化尺寸范围
钢类组织
现有强度MPa
目标强度/MP超细品尺寸/pm
低碳钢铁素体+珠光体
约200
g约400
(a)约5
低(微)合金钢低碳贝氏体或针状铁素体约400
2约800
(a)1-2
合金结构回火马氏体或贝/马复相钢约800
d约1500
)约5
3.1概述
一、机器零件用钢的性能要求
1具有良好的冷热加工工艺性
如锻造、冲压、热处理、车、铣、刨、磨等。
2具有良好的力学性能
不同零件,对钢强、塑、韧、疲劳、耐磨性等有不同要求。
一般为亚共析钢,低合金或中合金,优质钢或高级优质钢。
第3章机器零件用钢
根据钢的生产工艺和用途,可分为:调质钢、低碳马氏体钢、超高强度结构钢、渗碳钢、氮化钢、弹簧钢、轴承钢和易削钢等。
小结
在微合金化成分设计的基础上,正确的控轧和控冷工艺是关键因素。组织变化是在T-t-P三元处理过程中动态地进行的,从而获得了优异的复合强化。这是对传统T-t二元处理的一个突破,从而对钢的各种强化机制也有了新的认识与发展
Ti、Nb、V等元素在控轧和控冷工艺过程的各个环节中起了重要作用。合适的量及其它们的复合加入使各强化机制得到了最佳的发挥
二、机器零件用钢合金化特点
主加Cr、Mn、Si、 Ni。
元素主要作用:1淬透性和力学性能。
辅加Mo、W、V等
元素过热敏感性,↓回脆,↑淬透性。
获得最佳性能一称为极限合金化理论结构钢常用范围为:<1.2%Si,<2%Mn,
最佳1~2%Cr, 1~4%Ni, <0.5%Mo, <0.2%V,
范围<0.1%Ti,0.4~0.8%W。
或是单独加入,或是复合加入。
三、零件材料和工艺选择途径
1对于要求良好综合力学性能,零件选材料的途径为:
①低碳马氏体型结构钢,采用淬火+低温回火。为1耐磨性,可进行渗碳处理;汽车拖拉机齿轮类为代表
2回火索氏体型,选择中碳钢,采用淬火+高温回火。为↑耐磨性,可进行渗氮处理或高频感应加热淬火等表面硬化工艺方法。轴类零件为典型。
2、如要求更高的强度,则适当牺牲塑韧性。可选择中碳钢,采用低温回火工艺。如低合金中碳马氏体钢。农业机械较多
3、如要求高的弹性极限和屈服强度,又要有较高的塑性和韧度,则选择中高碳钢,进行中温回火。如弹簧钢。
4、零件要求高强度、高硬度,高接触疲劳性和一定的塑性和韧度,可用高碳钢,淬火+低温回火。如轴承钢。
20
143224
C
R
0二#a)
516880
6)
M7150A砂轮主轴
取样部位c)
汽车半轴
打硬度处a)一端法兰式;
在杆部取祥横向观察b)二端花键式;
c)变截面台阶式
汽拖用连杆
3.2整体强化态钢
整体强化态钢均承受拉、压、扭等交
基本情况变应力,大部分是整体受力。
其主要失效形式是疲劳破坏,
主要性能指标1、Rm、AK、KI等。总体上要求良好的综合力学性能
主要应用主要制造轴、杆、轴承类等机器零件,
如连杆、螺栓、主轴、半轴等。这类钢主要有调质钢、弹簧钢、轴承钢、低碳马氏体钢、超高强度钢等。
由于不同机器零件的服役条件和失效方式不同,主要的设计依据和失效判据也不同,所以应合理选择钢的含碳量和热处理工艺。
辨证思维应该明确:
一般情况下,某零件制造的材料并不是唯一的;
某一种钢采用不同的热处理工艺可以制造不同类型的零件;
某一零件用某一材料制造,其热处理工艺方法也可能是多种的。
STOPSNOOZE
74.5
2601710
2160
上图S7332螺纹磨床丝杠下图
T615K镗床镗杆
2-键槽宽18H8
29703171
3.2.1调质钢
1、淬透性原则
淬透性相同的同类调质钢,可互相代用
400
色HB
3002
200000
合金钢
10
840
30
7020
碳钢
4010
30
200
1020
0
2/(102Mn/m2)
cs/(102MN/m2)
0.25~0.45%C的合金钢经调屈服强度相同的碳钢和合
质后室温性能变化金结构钢断面收缩率变化
161.00
完全硬
140.90
Ez>合-6120.80
t
100.70
未完全硬
▲C钢0.60
8Cr钢
XCrNi钢
CrMnSi0.50
65
4n050060010
15
2003002
硬度,HB12MN/m2
结构钢抗拉强度与硬度的关系结构钢是否淬透对屈强比的影响
分析比较:40Cr→40CrNi→40CrNiMo淬透性40CrNiMo > 40CrNi > 40Cr
回稳性40CrNiMo > 40CrNi > 40Cr
塑韧性40CrNiMo > 40CrNi > 40Cr
回脆性40CrNi>40Cr>40CrNiMo
思考:以Mn代Ni,在性能上有什么差别?
在机械制造工业中,调质钢是按淬透性高低来分级的。D为油淬临界直径
低淬透性合金钢:Dc<30~40mm,有40Cr、40Mn2、42SiMn、35CrMo、42Mn2V等
中淬透性合金钢:D:40~60mm,有40CrNi、42CrMo、40CrMn、30CrMnSi等
高淬透性合金钢:D≥60~100mm,有37CrNi3、40CrNiMo、40CrMnMo等
2、合金化及常用钢
含碳量在0.25-0.45%。常用合金元素作用:Mn:↑↑淬透性,但↑过热倾向,↑回脆倾向;Cr:↑↑淬透性,↑回稳性,但↑回脆倾向;Ni:↑基体韧度,Ni-Cr复合↑↑淬透性,↑回脆;Mo:↑淬透性,↑回稳性,细晶,↓回脆倾向;V:有效细晶,(↑淬透性),↓↓过热敏感性。
3调质钢强韧化工艺的发展
A是一次大能量冲击性能指标,小能量多冲条件下工作的,很难正确
正确反映。有些重要零件应以断裂韧度K
认识来衡量。
性能由于服役条件差异,钢最佳综合性
指标能也不一定都是高温回火态好。零件在承受冲击能量大时,钢强度应低些,塑性和韧度宜高些;冲击能量较小时,强度应高些。以达最佳配合。
如复合热处理,即热处理强化、表面
综合处理及形变强化工艺结合起来。如汽车转
强化向节园角处进行高频淬火处理后,疲劳寿
工艺命提高了50倍
冷变如滚压、喷丸等冷变形方法的效果也比
形较好,能提高零件寿命
锻造既能节约能源、简化工序,又能细化组
余热织,提高零件的强韧性。如柴油机连杆,
淬火已普遍采用锻造余热淬火工艺
3.2.2微合金非调质钢
一、微合金元素对强韧化的贡献
非调钢组织:主要是F+P+弥散析出K。主要强化作用:细化组织和相间沉淀。微合金化元素:Ti、Nb、V、N等元素,V是主要的。
多元适量,复合加入:Nb-V-N和Ti-V等一主要贡献是细化组织。
三、组织因素对强韧性贡献的大小间隙型碳氮化合物沉淀析出的强化量一般认为可提高150~400MPa,甚至可达到600MPa。
细化组织强化量大约在50~300MPa,脆化矢量为-0.66℃/MPa。
其它强化机制都不同程度地降低韧度
Y
00口0
Y
0口0
0
心口Jb
D
00。
0
0
相间沉淀析出示意图
二、获得最佳强韧化的工艺因素
沉淀强化
相间工艺参数
析出是关键
细化组织
控制轧制细化组织和沉
控制冷却淀析出要协调
决定各种强化机制的效果
150Mn质量分数
Nb
1.15~1.3%非调质钢150
调质碳钢
Y100100
Ti
Mn质量分数
500.85%非调质钢50
70080090010000
0.040.080.12
Rm/MPa合金元素质量分数%
Mn对非调质钢韧度的影响V、Ti、Nb对强度的影响
C、N原子的固溶强化,其脆化矢量分别
为0.72℃/MPa、1.97℃/MPa;Mn和Cr元素的脆化矢量为零;Si为0.53℃/MPa。
铁素体中固溶C、N量极小,Mn和Si固溶
量有限。所以固溶强化相对是较小的。
在强化机制上,不同的成分和工艺是不同
的,所以使钢的组织、性能也有很大的差异。
四非调质钢的优化设计
通过合适的成分配比和工艺控制可达到同时提高强度和韧度的目的。
aRaCUdR
acU
(△R, △CU)㎡
af.af,aD
aD
RCU
m√
aRacu
m
ddudua(AR)a(AR
mp
CU为冲击韧性,R为抗拉强度,D是珠光体片间距,f是珠光体体积分数,d,为奥氏体晶粒大小,△Rmp
P
PP
H
压缩螺簧b)
拉伸螺簧
H气中
d
扭转螺簧单板弹簧
叠形板簧典型的螺旋弹簧及板簧椭圆板簧
3.2.3弹簧钢
一、弹簧的服役条件及性能要求弹簧功能储能减振
板簧,螺簧;
弹簧类型压簧、拉簧和扭簧等
复合微合金化非调质钢典型成分
牌号Si
MnCrVNbTi其他
27MnSiVS6(德)0.260.701.500.10
0.02
S1000(法)0.470.361.550.140.120.0650.03
Mo
30XTT(俄)0.300.551.00.60≤0.2≤0.17
1524MoV(美)0.220.351.540.11
0.11
Mo
NC33HFB(日)0.330.241.460.06
0.01
0.01N
AHF50B(日)0.35-0.15-1.300.05-
0.400.351.600.15
45VNbN(中)0.440.140.790.10
0.110.02N
2210
a)822.5
空芯扭杆中径D2
b)276±
实芯扭杆d=6
扭杆弹簧卡簧(圈)基本形状
a)实芯扭杆b串联式扭杆MI2
I碟形弹
簧截面
-D
板簧弯曲载荷
疲劳破坏
螺簧扭转应力
弹性减退
高的弹性极限。、屈强比。弹性高的疲劳强度1→避免早期疲劳破坏有足够的塑性和韧性→不产生脆性断裂足够的淬透性→保证和整体强度其他要求:冶金质量、表面质量
思考题:
为什么弹簧要求有好的表面质量,如表面不允许有裂纹、折迭、严重脱碳等缺陷?
二、常用弹簧钢及强化工艺
合金化:
含碳量在0.60~1.05%,低合金弹簧钢在0.40~0.74%C。?
+Si、Mn、Cr、V等合金元素.Cr和Mn主要是提高淬透性,Si提高弹性极限,V提高淬透性和细化晶粒
常用硅锰板簧钢有60Si2Mn、55Si2Mn等60Si2Mn:
1Si、Mn复合,强化F,→↑/可达到0.8~0.9;
2
Si/Mn↑透性,Ms不过分↓,开裂向小;③Si有效↑回稳性,但脱C倾向;
④Si、Mn复合,脱碳和过热敏感性较硅钢、锰钢为小
常用螺旋弹簧钢有50CrVA等。
50CrVA:
①Cr、V均↑回稳性,韧性好;
②V细化晶粒,↓过热敏感性;
③含Si少,脱C敏感性,热处理不易脱C;常用于受应力高的螺旋弹簧及<300C工作的阀门弹簧
思考题:
大型弹簧为什么要先成形后强化,小型弹簧先强化后成形?小型弹簧成形后为什么进行低温退火?
c11000
950日840
二
1CJ
热卷AC1
。试题+
形
热
卷簧440
粹火40变热440
回火回火
理回火
O(a)
(b
(c)
时间h
火车缓冲压缩螺旋弹簧热成形的三种热处理工艺a)常规热处理b)热卷簧余热淬火c高温形变热处理
热成形大型热成形后+
弹簧弹簧淬、回火
基本
工艺
方式冷成形小型冷变形或热处
弹簧理强化冷成形
弹簧低温退火
热处理淬火和
回火
工艺中温回火
屈氏体
具有一定的冲击韧度,较高的弹性极限、屈强比和最高的疲劳强度
关键问题:弹性参数和韧性参数之间的
平衡或最佳配合。
Rm
1600350
Rp
120060
300
80040
Z250
40080
AK20p
0300
400500600700
300400500600回火温度℃
回火温度/℃
60Si2Mn钢力学性能与55Si2Mn钢疲劳强度随
回火温度的关系回火温度的变化
形变强化效果好
板簧最适合形变强化:
滚压、喷丸等冷变形强化强化都能有效地提高板簧使用寿命,如结合高温形变热处理则更好板簧喷丸作用举例:疲劳强度(MPa)
板厚/mm未喷丸喷丸应力喷丸
13390
470
800
11350
700
850
646558
59
滚子轴承圆柱滚子推力轴承
2425
6263
圆锥滚子推力轴承滚针保持架组件
外套
滚珠
保持器
内
()Q=
(b)
滚动轴承及其受到载分布情况
3.2.4滚动轴承钢
一、滚动轴承钢的工作特点及性能要求
滚动轴承由内、外圈和滚动体(珠、柱、锥、
针)及保持器组成。
高负荷→最大接触应力可高达3000~5000MPa
工作条件高转速→循环周次高达每分钟数万次;
高灵敏度→精度要求高→磨损、麻点→噪音
失效形式接触疲劳破坏,麻点、剥落
高而均匀的硬度和耐磨性一足够
淬透性和淬硬性,>60HRC;
性能要求高接触疲劳强度→以免过早失效
→保证材质、组织;
一定韧度一承受冲击,以免碎裂;
尺寸稳定性好→保证精度;一定耐蚀性→大气、润滑油腐蚀。
关键因素化学成分、冶金质量和加工工艺
二、轴承钢的冶金质量和合金化
接触面小应力集中大
材质纯净、组织均匀易产生裂纹
纯净一夹杂物要少:主要有各种
冶金
质量氧化物(如A1203)和硅酸盐等;
要求危害程度依次递减:A1203、球
状不变形夹杂、铝硅酸盐。
155个平均值
o
10
5?
o
50100
150
200
60mm2内0.03mm以上的氧化物夹杂败目
氧化物夹杂数量对轴承钢疲劳寿命的影响
图带状碳化物500×图碳化物液析500×
图GCr15钢淬火回火态500×图网状碳化物500X
(回火隐晶马氏体+碳化物)
碳化物细小均布。主要有三类K:K液析→结晶时枝晶偏析而存在→
组织均匀高温扩散退火,不允许液析严重;带状K→轧制时二次碳化物偏析一高温扩散退火;
网状K→冷却时在晶界析出→正火
合金高碳,加入Cr、Si、Mn等。如GCrl5、
化GCrl5SiMn。Cr含量?
经合适的热处理,应得到组织细小均匀的奥氏体晶粒度5-8级;M中含0.5~0.6%C;隐晶M基体上分布细小均
组织匀的粒状K,体积分数约7-8%,一般可
特点有少量AR
负荷较小时,为提高。,可设计M中约含0.45%K体积分数约5%→钢中总含碳量应↓
65
HRC60
SS
6.010
4.01050
H)家
2.0×10645
1.0×1040
0.8×10L50
35
06×106
0.4×10630
LI
0.10×10
0.08×10
0.00×10
0.04×106020.30.40.50.60.70.8
碳质量分数
图高碳铬轴承钢中马氏体含碳量与疲劳寿命的关系
含都,%
0.766.750.80.951.17
20
10
8.0
6.1
2.00
1.0
0.8
0.6
0.1
0.235
9
未记解碳化物,⅓
GCr15轴承钢中未溶K量与疲劳寿命间的关系
12
101-GCr15,850℃淬火
2-Cr15SiMn,830℃淬火
215-25
78
-196
冷处理温度.℃
图轴承钢深冷处理温度对残留奥氏体量的影响1-GCr15,850℃淬火;2-Cr15SiMn,830℃淬火
580065
5490弯曲强度
62
5000HRC
58
4600
420050
3800图回火
抗压强度16
温度对
3400GCr15钢
3000接触疲劳寿命5
力学性能
260的影响
2200抗拉强度
3
1800扭转
2
14001
10000100200300400回火温度:C
三、高碳铬轴承钢的热处理
工艺特点是简单而要求高。
球化退火→为最终淬火作组织准备淬回火工艺参数对疲劳寿命有很大影响
热处理特点一般采用保护气氛加热或真空加热
160℃保温3h或更长回火,硬度62~66HRC如要求消除A→淬火后立即冷处理而后立即低温回火。
思考题:
轴承钢在淬火热处理后,硬度检验时不允许有明显的软点,为什么?
如出现软点,可能有哪些因素造成的?
3.2.5低碳马氏体钢
没有独立钢类,有专门开发的低碳M钢低碳结构钢采用淬火+低回工艺,可得到位错板条M→强度、韧度和塑性的最佳配合抗拉强度,1150~1500MPa;
屈服强度,950~1250MPa;
基本性能40%;伸长率δ,≥10%;
冲击韧度AK6J。
这些性能指标和中碳合金调质钢性能相当,常规的力学性能甚至优于调质钢。
1成分工艺特点
成分特点0.15~0.25%C,→以保证淬火后获得板M
+Cr、Mo、Si、Mn、V等→↑淬透性等性能15MnVB、20SiMn2MoV等是我国研制开发的
零件断面尺寸↑,心部可
工艺特点高温加热能淬不透,→综合性能↓
较长t保温应根据零件的尺寸大小来
高速冷却选择相应淬透性的钢
3.3表面强化态钢
这类钢适宜制造表面和心部性能要求不同的零件,通过某种工艺使零件表面硬度高耐磨而心部具有较好强韧性配合以满足要求。典型零件有齿轮、凸轮等
零件在滑动、滚动、接触磨损和接触疲劳
应力、摩擦等工况下工作是主要失效形式
渗碳钢、渗氮表面应具有高硬度、高接
钢、感应加热淬触疲劳抗力和良好耐磨性,
火钢等而心部有一定塑韧性
吊卡实物外形
2低碳马氏体结构钢及应用
应用在矿山、汽车、石油、机车车辆、农业机械等
制造工业中得到了广泛的应用
石油钻机吊环(卡)20SiMn2MoV代35钢
实例材料
工艺
重量kg/MPaAKJ
35正火
137.4550
50
20SiMn2MoV淬火291600
110~120
局限性工作温度<200℃;强化后难以进行冷加工焊接
等工序;只能用于中小件;淬火时变形大,要求严格的零件慎用
各种类型的齿轮
3.3.1
合金渗碳钢
1、渗碳钢的合金化
一般含碳量在保证得到强韧
0.12~0.25%性好的板条M
常用合金Mn、Cr、Ni主要↑淬透性
化元素Ti、V、W、Mo细化晶粒
渗碳层性能:表层碳量、表层浓度梯度和渗层深度渗碳层深度根据零件需要确定。原则上,渗碳层深度应大于零件的最大切应力深度。
3.0900℃~920℃60min
木炭+碳酸钠
Cr
2.6Mn
2.8
2.2Mo
2.4W
1.8Mo
2.0
quu
1.41.6
Ni
----Ni
Mn1.2
1.0Si
0.8
Si
0.6120
2
345
元素质量分数%元素质量分数%
(a)b)
合金元素对渗碳层表面合碳量和渗碳层厚度的影响
2常用渗碳钢及热处理
按淬透性可分为低、中和高淬透性钢三类。20Cr钢:不宜渗碳后直接淬火。20CrV钢可20CrMnTi广泛制造汽车、拖拉机变速箱齿轮,离
钢特点:合器轴和车辆上的伞齿轮及主动轴等。
Cr、Mn复合,淬透性好,D约40mm;2较高耐磨性和强韧度,特别是低温韧度较好;
③渗碳工艺性较好,晶粒长大倾向小,可直接
淬火,变形也比较小。
渗碳零件受力与渗层厚度的关系表面碳浓度太高
表层强度渗层太浅
心部强度
外应力
渗层厚度距离
表合金元素对渗碳工艺和渗碳层性能的影响合金碳扩散表层渗层浓度晶粒长
含量范围
元素系数碳量深度梯度淬透性大倾向质量分数
%
Ti
V↓↓↓
变陡不定①<0.12
<0.30
W0.4~1.2
Mo↓↑↑变陡↑0.2~0.6
Cr<2
Mn影响小↓↑平缓↑~2
Ni↑↓↓平缓影响小
~4
Si↑平缓
影响小
<0.8
渗碳后的热处理工艺有直接淬火一次淬火二次淬火细晶粒钢可用直接淬火
18Cr2Ni4WA20Cr2Ni4A高透性碳钢。由于合金元素多,所以工艺可变程度大,获得的组织性能也较复杂。
18C12Ni4W可作为调质钢,低碳马氏体钢,也可作为渗碳钢。渗碳和淬火工艺较复杂。主要用于要求高综合力学性能和高耐磨性的重要件,如航空发动机齿轮等。
3.3.2氮化钢
服役条件:
有些零件工作时载荷不大,基本上无冲击力;有摩擦,但比齿轮等零件的磨损要轻,同时也受到交变的疲劳应力。这一类零件重要的要求是能保持高的精度。常采用氮化钢进行渗氮处理。
氮化钢:多为碳含量偏低的中碳铬钼铝钢。国内外广泛使用的氮化钢是38CrMoAl钢,获得最高氮化层硬度,达到900~1000HV。仅要求高疲劳强度的零件,可采用不含铝的CrMo型氮化钢,如35CrMo、40CrV、40Cr等,其氮化层的硬度控制在500~800HV。
工艺:氮化前,要经过调质热处理以得到稳定的回火索氏体组织,以保证零件最终的使用性能和使用过程中的尺寸稳定性,同时也为获得好的氮化层作组织准备。
3.3.3低淬透性钢
感应加热淬火与渗碳和氮化相比,特点有不改变表面化学成分,表面硬化而心部仍然保持较高的塑性和韧度;
表面局部加热,零件的淬火变形小;
加热速度快,可消除表面脱碳和氧化现象;在表面形成残余压应力,提高疲劳强度。与渗碳相比,感应加热淬火工艺常用于轻负荷工件或需要局部淬硬的轴类零件,其耐磨性和疲劳抗力不如渗碳工艺。
思考题:
某精密镗床主轴用38CrMoAlA钢制,某重型齿轮铣床主轴用
20CrMnTi制造,某普通车床主轴用40Cr钢制造.试分析比较说明它们各自应采用什么样的热处理工艺及最终的组织和性能特点
0.61000
Al
0.5Si900
Mo
0.AMn
AH
700Cr
E
E到
Mn
0.3Mo500
Si
0.2W300
Ni
0.1上
100
L
02468100
248
10
元素质量分数P%
向(b)
合金元素对氮化层深度和表面硬度的影响
(550℃氮化24h)
降低钢淬透性措施:Mn、Si;
加入Ti
国家标准有55Ti、60Ti、70Ti等.
硬化层分布(右为仿形硬化)
感应加热淬火钢主要有中碳低淬透性调质
钢和低淬透性钢。这里介绍低淬透性钢
概念是指淬透性比一般碳素钢的淬透性还要低
特点得到沿着轮廓分布硬化层→“仿形硬化”
应用专门用于中、小模数(m=3~8)的齿轮
3.4高锰耐磨钢
一、高锰铸钢的化学成分及性能
特点:高碳、高锰。铸件使用。
常用高锰铸钢为ZGMn1型。铸态组织一般是奥氏体、珠光体、马氏体加碳化物复合组织,力学性能差,耐磨性低,不宜直接使用。经过水韧处理(即固溶处理)后的显微组织是单相奥氏体,软而韧。
3、铸件出炉至入水时间应尽量缩短,以避免碳化物析出。冷速要快,常采用水冷。水冷前水温不宜超过30℃,水冷后水温应小于60℃;??
4、水韧处理后不宜再进行250-350℃的回火处理,也不宜在250~350℃以上温度环境中使用。??
13%Mn
1000
800YAcm
P600a+Y+8
400
200a++÷日
a+E
00.4
0.81.21.6
C%
13%Mn合金钢的垂直截面相图
二、高锰钢的热处理
1、水韧处理加热T应>Acm,一般为1050~1100℃,在一定保温时间下,K全部溶入A中2、高锰钢导热性较差,仅为碳素钢的1/4~1/5,热膨胀系数比普通钢大50%,而且铸件尺寸往往又较大,所以要缓慢加热,以避免产生裂纹;
三、高锰钢的耐磨性及应用
大形变在A基体中产生大量层错、形变孪晶、和马氏体而硬化。表面硬度从原来200HB左右可↑到500HB以
耐磨机理上,硬化深度可达10~20mm,而心部仍保持A,所以能承受较大冲击载荷而不破裂。在表层逐渐被磨掉的同时,硬化层不断地向内发展“前赴后继”在低应力和低冲击载荷下,耐磨性往往不一定好。
广泛应用于承受大冲击载荷、强烈磨损的工况下工作的零件,如
应用各式碎石机的衬板、颚板、磨球,挖掘机斗齿、坦克的履带板等。保险箱?
思考题高锰钢经水韧处理能得到全部A,
而缓冷却得到大量M。为什么?
3.5零件材料选择基本原则一、选择材料的基本原则
1材料使用性能要求→最大限度发挥材料潜力2材料的工艺性能→加工工艺性能良好
3、经济性涉及材料的价格、加工成本、国家资源情况等,零件的总成本与零件寿命的关系4其它因素材料毛坯的选择、生产设备的可能性、环境协调性等
三、选择材料的基本思路及方法
分析零件确定主要失效抗力指标
工作条件作为选材的基本依据
考察经济性考虑工
选择材料
和生产成本艺措施
要合理引用手册上材料的力学性能数据;尽量选用简化加工工艺的材料;
零件材料选择要考虑零件的综合成本
(3)要求高的精密零件
一般用于精密丝杆、主轴等。工艺路线为:毛坯→预先热处理→机械粗加工→热处理→半精加工→氮化处理→精加工→去应力退火→零件。
二、零件的加工工艺路线
基本上可分为三类:
(1)性能要求不高的零件
一般是铸铁和碳钢制造。其工艺路线比较简单:毛坯→正火(退火→机械加工→零件。如直接用型材加工,则不需要进行热处理。
(2)性能要求较高的零件
合金钢制造的轴、齿轮等零件。工艺路线:毛坯→预先热处理→机械粗加工→最终热处理(淬火回火或渗碳淬火等)→精加工。
四、典型零件材料选择与工艺分析
1、齿轮类零件
不同机械的齿轮,其工作条件差别很大,所
以在选择材料和热处理工艺上也有很大不同。载荷不大,工作平稳,一般无大的冲击力,转速也不高。常选用调质钢制造,如45、40Cr、
机床齿轮42SiMn等钢,
热处理工艺为正火或调质,高频感应加热淬火一般工艺路线为:
备料→锻造→正火→粗加工→调质处理→半精加工→高频淬火+回火→磨削
汽车、拖拉机上的变速箱齿轮属于重载荷齿轮。一般都采用渗碳钢,如20Cr、20CrMnTi等,进行渗碳热处理。
汽拖齿轮一般工艺路线为:
备料→锻造→正火→粗加工→渗碳火回火→喷丸→磨削
航空发动机齿轮和一些重型机械上的齿轮承
受高速和重载,一般多采用高淬透性渗碳钢,
如12CrNi3A、18Cr2Ni4WA等钢。
重载齿轮工艺路线较复杂:
备料→模锻→正火高温回火→机械加工
→渗碳→高温回火→机械加工→淬火回火
→精加工一检验。
目前常用轴的材料及工艺如下:
(1)轻载主轴。如普通车床主轴,负荷小,冲击力不大,磨损也不严重,一般采用45钢,整体经正火或调质处理,轴颈处高频感应加热淬火。
(2)中载主轴。如铣床,中等负荷,有一定冲击力,磨损也较重,一般用40Cr等制造,进行调质处理,轴颈处高频感应加热淬火。如冲击力较大,也可用20Cr等钢进行渗碳淬火
①传递扭矩,交变性,有时会承受
服役条弯曲、拉压负荷;
件主要②都有轴承支承,轴颈处受磨损,
共同点需要较高的硬度,耐磨性好;
3大多数承受一定的冲击和过载。断裂、疲劳断裂和过量磨损。→轴
主要失
效方式类零件主要是按强度来选材的,并考虑一定韧度和耐磨性。
2轴类零件
轴是各类机械中最基本零件,也是关键零部件。它直接影响精度和使用寿命。各种轴的尺寸差别很大,一般钟表的轴直径在0.5mm以下,而汽轮机转子轴直径可达1m以上。
(3)重载主轴。如组合机床的主轴,负荷较大,冲击力大,磨损严重,可用20CrMnTi钢制造,渗碳淬火。
(4)高精度主轴。如精密镗床的主轴,虽然负荷不大,磨损也不严重,但是精度要求很高,一般可用38CrMoAlA氮化钢制造,经调质后氮化处理,可满足要求
小结
材料学主线:
服役条件→技术要求→选择材料→强化工艺→组织结构→最终性能→应用、失效。
寻求最佳方案,充分发掘材料潜力。
性能材料
要求成分
服役零件
强化
条件工艺
使用组织
性能结构
材料成分、工艺、组织、性能间的关系
高强度钢发展过程实例
美4130(0.3%C,Cr,Mo)+C
4340(40CrNiMo)
应用时不够应用广泛
4335发现V作用,↑整体强韧水平
相似,韧性↑C,+V→细化晶粒
发现Si作用→300M,强韧水平同时再提高
4340+1.6Si+0.08VM板或B或两相组织
材料学“思想”:
材料学是一门很有“思想”的课程。主要的“思想”:作用的辨证与矛盾的转化。如,对结构钢是强度-韧度的匹配,对工模具钢主要是韧度-耐磨性的协调。材料中的这些矛盾涉及到合金化设计、处理工艺等。
材料学的强韧矛盾:
掌握理解固溶强化、位错强化、细晶强化和弥散强化等强化机理是很重要的,这是理解强韧化矛盾及其互相长消规律的基础。各种强化机制在处理过程中是相互转化的。
关键因素:钢的合金化和处理工艺
合金化基本原则:多元适量,复合加入。(1)提高性能。提高淬透性等性能,复合的作用不是线性相加的。如Cr-Ni复合
(2)扬长避短。合金元素一般都有优缺点,为克服不足,可以复合加入来相互弥补。
如:Si-Mn,Mn-V配合
(3)改善碳化物类型与分布。某些元素的加入会改变钢中所形成的碳化物的类型与分布,或改变其它元素的存在形式和位置,从而可提高性能。如Cr-V
适量:主要是作用,也有经济性问题①有的元素增多后,会降低材料塑韧性。如低碳构件钢中的Si、Mn含量。
②有些合金元素增多,会恶化K的分布。如轴承钢中的Cr
③有的元素含量过多,会改变K类型,增加热处理过程难度。如V,Mo含量。
④合金元素的作用往往不是随量的增加而线性地增加的。
第工模具用钢
按其用途可分为刃具钢、模具钢和量具钢。刃具钢可分为碳素钢、低合金工具钢和高速工具钢。
模具钢根据工作状态可分为热作模具钢、冷作模具钢和塑料模具钢。
量具钢用来制作量规、卡尺、样板等用来测量工件尺寸和形状
工艺孔(改进前)
裂纹(改进后)
O中
2860
工艺孔
70
oo工艺孔
20
50
o工艺孔
模具增加工艺孔减少变形开裂
工艺锻造→球化退火→不完全淬火
特点淬火工艺参数要求严格。
变形热应力
变形
开裂
倾向组织应力开裂
分级加热、分级淬火、等温工艺
淬火、双液淬火;零件设计与其措施
他工艺措施等
4.1概述
1工具钢成分与性能特点
主要韧度和耐磨性间的合理平衡→基体成
矛盾分和K的性质、数量、形态和分布。一般含0.6~1.3%C→M+足够数量K。M硬度高、切断抗力较高、耐磨性好。什么M?
成分Cr、W、Mo、V等:1淬透性、耐磨性和
组织热稳定性;
Mn、Si辅助加入:淬透性,回稳性
第二相K→球状、细小、均匀分布。
断口法→碳素工具钢和低合金工具钢;
淬透端淬法→合金工具钢,以端淬曲线上
性60HRC处距水冷端距离表示。
淬透性作用强弱顺序:
Si、Mn、Mo、Cr、 Ni
Me↑淬透性,只有溶入A中,才起作用;Me作用随钢中含碳量而变化,如Si。工具钢淬透性随热处理条件而变化,如V
注意点
2、工具钢基本性能及检测方法
强度静弯或扭转试验→弯曲强度、
塑性挠度和扭转强度、扭转角;?
韧度一般采用无缺口冲击试样?
硬度一般硬度60HRC以上,K可适
当↑硬度2~3HRC
热稳
定性对高速钢,通常就是红硬性
2.2高碳多元合金钢
1.6950℃淬火
2.0高碳单元合金钢
1.5
1.81.4
1.61.3
815℃淬火
1.4中碳钢1.2
1.2低碳钢
1.1
1.01.0
00.40.81.21.62.000.040.080.120.160.20
Si质量分数/%V质量分数%
Si对不同含C量钢的淬透性影响V在不同淬火温度时对淬透性的影响
合金元素具体作用
Cr:1%左右,细化K,均匀分布;
Mn:主要1淬透性;
Si:↑低温回稳性,Si强化F,切削加工性,↑脱碳敏感性,不单独加入;?
W:0.5~1.5%,W含量太多→K类型转变且使K分布不均匀,恶化性能。
V:1过热敏感性,细化晶粒,1回稳性
2低合金工具钢
合金Cr、Si、W、Mo、Mn、V等元素,
化↑耐磨性和回稳性,↑淬透性→采用缓冷方式,↓变形开裂
T为Ac1+30~50℃
淬火油冷,
工艺熔盐分级淬火,
等温淬火(B等温淬火和M等温淬火)
一般
组织含碳量0.5%~0.6%的M+未溶粒状K
4.2碳素钢及低合金工具钢
1、碳素工具钢
T7-T13做低速切削的刃具和简单的冷冲模。淬透性低,断面尺寸小于15m的工具。
T7有较好塑韧性,宜做受冲击的刃具,如凿子等;T8易过热,制造形状简单的木工工具等;
T10、T12耐磨性较好,强度高,但韧度低,制造不受冲击或冲击较小形状简单的工具,如车刀、铣刀等淬火冷却方式常用水-袖双液淬火、分级淬火成本低、工艺性能好、用量大。
9SiCr:
①Si/Cr↑淬透性,D油<40mm;
②Si/Cr↑回稳性,~250℃回火,>60HRC;③K细小、均匀→不容易崩刃;
④分级淬火或等温淬火处理,变形较小;⑤Si使钢的脱碳倾向较大。
适于制作形状较复杂、变形要求小工件,特别是薄刃工具,如丝锥、扳牙、铰刀等。
4.3高速钢
1898年就有含W钢,1910年生产了W18Cr4V。近几十年来,高速钢的产量、品种和质量都有了很大的发展。
按照其成分和性能特点可分为以下几类:
(1)钨系高速钢:典型牌号18-4-1,美M1,俄P18。
(2)钨钼系高速钢:如6-5-4-2,美M2,目前应用普遍。(3)含钴高速钢:如W18Cr4VCo5,红硬性高。
(4)超硬高速钢:典型牌号为W6Mo5Cr4V2Al。具有
65~70HRC高硬度、高红硬性特点,成本比钴高速钢低。钨系和钨钼系称为通用型高速钢,而把其它类型称为特殊用途高速钢或高性能高速钢。
CrWMn:9 CrWMn ?
①Cr、W、Mn复合,↑淬透性,D油=50~70mm;
②AR在18-20%,淬火后变形小;
③含Cr、W碳化物较多且较稳定,晶粒细小→高硬度、高耐磨性;
④回稳性较好,>250℃回火,<60HRC;5W使碳化物易形成网状。
适于制作要求变形小、耐磨性高的工件,如拉刀等,也可做量具及形状较复杂的高精度冲模。
一、高速钢中合金元素的作用
C一般高速钢含C量0.7~1.3%(质量分数)
作用C↑:1硬度,但熔点,易过热;↑K量,不均匀
规律性;↑AR→↑回火次数;o和AK
定比碳经验规律设计→最大二次硬化效应
C%=0.033%W+0.063%Mo+0.20%V +0.060%Cr→合金元素之间的相对控制法.必须解决成分性能间数学模型,控制参数的数值范围
焊续
高速钢45钢
对焊高速钢锥柄钻头高速钢直柄麻花钻
55
上左:直、锥柄加长麻花钻上右:整体硬质合金钻头铣刀、铰刀、复合刀具及非标准刀具
下右:各种合金车刀
W钨是钢获得红硬性的主要元素。MC型K,
Mo回火时析出W2C;W热导率→钢导热性差钼和钨相似,1%Mo可取代1.5~2.0%W
VV显著↑红硬性、↑硬度和耐磨性,细化晶
粒,过热敏感性。以VC存在
CrCr加热时全溶,保证钢淬透性,4%Cr。
改善抗氧化能力、切削能力
CoCo可显著提高钢的红硬性,5、8和12%三
个级别。但钢韧性、↑钢脱碳倾向
微量微量氮增加硬度和热硬性,一般~0.10%。
元素稀土可明显改善热塑性,硫在晶界的偏聚
二、高速钢中的碳化物
铸态鱼骨状莱氏体(Ld)、黑色组织
组织(δ共析体等)和白亮组织(M+AR)
加热时,K溶解顺序为:
淬火MC3M2C型在1000C左右溶解完一
态MC型在1200℃时部分溶解→MC型比
较稳定,在1200℃时开始少量溶解。
回火主要为MC(淬火残留)、MC(回火时析
态出和淬火残留)、M2C(回火析出)等K
三、高速钢的热处理
1260-1300℃
800-850℃
500-600℃580-620℃
550-570CX1h
油冷一次350-400℃
分级二次三次回火
分级
时间t
W18Cr4V高速钢常用热处理工艺方法
K不均匀性①各向异性;
结果②形变时易应力集中开裂;
③热处理工艺性变坏
控制终锻温度;
用合适的锻压比;关键是
锻造时先轻锤快打,必须经
后重锤锻打;过正确
锻后要缓慢冷却;的锻造
锻后进行退火。
高速钢的退火组织(400X)高速钢的铸态组织(400X)
思考题:
高速钢Ac1在820-840℃范围,但其淬火加热温度必须在Ac1+400℃以上,为什么?
预热:高速钢工具一般在高温盐浴炉中加热,速度较快,常采用一次或多次预热为什么?
预热有什么作用?
高速钢导热性差,加热温度又高,预热—①↓淬火加热过程中的变形开裂倾向;②缩短高温保温时间,减少氧化脱碳;③准确地控制炉温稳定性。
可采用一次预热和二次预热。
淬火温度:精确控制
T淬过高,晶粒长大,K溶解过多,K发生角状化;奥氏体中合金度过高,冷却时易
过热在晶界上析出网状K。
温度再高→晶界熔化→铸态组织特
过烧征,主要为鱼骨状共晶莱氏体及黑色组织。淬火温度较低,大量K未溶,且晶粒特别
欠热细小。
可以从金相组织上初步判断工艺因素
1.010
5
W18Cr4V
0.8W6Mo5Cr4V284
Cr
0.66
W
0.4[C]
0.22
Mo]
0W
皇
退火900100012001300退900100012001300900100012001300
1100火
1100
1100
淬火温度℃
两种高速钢基体合金含量与奥氏体化温度的关系
30
25W18Cr4V
20M2
15
5
退火9001000110012001300
淬火温度C
W18Cr4V钢和M2钢淬火温度与未溶碳化物量的关系
正常淬火组织(400X)欠热组织(400X)
过热组织(400X)过烧组织(200X)
W18Cr4V高速钢不同淬火温度下的组织特征
确定淬火温度时,还需要考虑下列因素:(1)不同工作条件,淬火温度应有所区别如车刀→高硬度和红硬性→采用较高T;中心钻→强韧度好→采用较低的T(2)形状、尺寸不同,T有不同
形状复杂(如锯片、细长拉刀等)和厚薄悬殊刀具(如三面刃铣刀等)→较低T。形状简单的工具可采用较高T
尺寸较小和尺寸很大的刀具→较低T
(3)原材料级别也有影响
K不均匀性大的原材料→低的T
一般情况,过热和过烧的危害比欠热要大确定保温时间基本原则:
一定量K溶入奥氏体,而晶粒不长大。对于一定的T,有一个合适的保温时间。
淬火冷却:冷却很重要,方式也很多,可根
据工具不同情况进行选择。
常用一次分级或多次分级方法。?
分级80%高速钢工具是采用一次分级淬火,分
淬火级温度常在600℃左右,停留时间严格控制,
一般<15min。多次分级适用于形状特殊、极易变形的工具。
等温采用贝氏体等温淬火可↑工具的强度、韧
淬火度和切削性能。→中心钻及仪表刀具等在
使用中发生断头、崩刃等现象
思考题:
高速钢在分级淬火时,为什么不宜在950~675℃温度范围停
留过长的时间?
10%<50%100%
700Atc
600A
500
400+-B
3000%
10%
60%
Ms
20030%
S0%
10080%
0.010.1
1.0
10
100
时间
W18Cr4V钢在1300℃奥氏体化后过冷奥氏体等温转变曲线
回火:高速钢一般需要在560℃左右三次回火淬火态M+
大约30%AR+K
回火IM
回+M+>10%AR+K1
回火ⅡM
回+M+
少量AR+K2
回火ⅢM回
+AR (少量)+K3
(K1等以示区别)
同步热处理:
关键是正确选择回火温度与保温时间,以便和淬火工艺相匹配。
思考:可能有什么问题?
表面处理:
强化方法:化学热处理或在刀具表面覆层表面氮化、表面硫氮共渗等多元共渗、蒸气处理等,<560C。物理气相沉积(PVD法),在表面沉积TiC等覆层。
W18Cr4V钢回火一次金相组织W18Cr4V钢回火三次的金相组织
(400X)(400X)
6S3000
HRCJ由
2063
2500
(/NWy20006
10含
3
A%E2华
00
洋火后2
3
未回火
2
3
回火次数回火次数
(a)b)
W18Cr4V高速钢回火次数与残余奥氏体量(a)和性能(b)的关系
新型工具钢:
日本神户钢铁公司开发粉末工具钢Fe18Cr2Mo1V2.2C(KAD181),经HIP后不用锻造,具有很好的性能,在模具、辊子、刀具等方面应用很广泛
美国开发坩埚粉末冶金法(CPM)1韧性和耐磨性↑使用寿命。如CRMT440V(Fe17Cr0.4Mo5.5V)的耐蚀性与不锈钢T-440C差不多,但耐磨性是T-440C的几倍,制成的造球机刮刀,其实际使用寿命是T-440C的20倍经济合金化是高速钢的一个发展方向,在不降低性能的前提下尽可能降低钢中的V含量
工模具表面技术:
是高速工具发展的一个重要方面,近年来已成功利用离子渗入法在工具表面涂覆TiC TiN TiCN等涂层,发挥了优越的性能。在新型工具材料的开发上具有重要的意义。
日本开发了以硼砂熔盐为基稀土钒共渗工艺,经过该工艺处理的模具耐磨性比常规处理的要提高28倍。这些研究提高了工模具性能和使用寿命。这些研究都是不可忽视的开发课题
4.4冷作模具钢
金属在冷拉延、冲压、冷鐓或
态下变形冷挤成形等
工作T不高,模具主要承受高压共同
力或冲击力,有强烈的摩擦特点
技术主要技术要求为具有高硬度
要求和耐磨性,有一定韧性
浙模厂
典型冲压模及产品
部分冲裁模冲孔落料
修边模
0
冲头剪刀
加工流程&QC图深冷
进料备料热处理OR研磨粗线切割粗割)应力消除
超冷
研磨细)线切割精修J/G出货
模板检测零件检测
精密块精密塞精密二次元垂直度义比测仪液晶分离卡日本工具显微镜
规测量规高度规测量测量量投影机测量
测量
一、低合金工具钢
常用低合金工具钢有9Mn2V、CrMn、GCr15.9SiC。
和碳素工具钢相比,这类钢的淬透性比较高,热处理变形较小,耐磨性也较好,所以可制造工具尺寸较大、形状比较复杂、精度要求相对较高的模具。
9Mn2V特点:
①Mn↑淬透性,D油=~30mm;
②MnMs,AR约20~22%,变形小;
③V能克服Mn缺点,过热敏感性,细化晶粒;④硬度稍低,回稳性较差→200℃以下回火;⑤VC使钢的磨削性能变差。
各种类型的中小冷作模具都可采用。
组织变化特点二:
随T升高,K溶解量增加,奥氏体合金度增加,淬火后残余奥氏体增加,硬度下降。淬火温度的波动可引起组织和性能的较大变化。
组织变化特点一:
选择T和回火温度来控制工具的变形。调节淬火温度:
T→AR→体积V→一定程度可抵消M转变所引起的胀大;
调节回火温度:
<300~400℃,M分解而尺寸缩小;>450℃,AR转变为M→体积1
二、高铬和中铬模具钢
1、高碳高铬模具钢
主要有Cr12、Cr12MoV钢。
Cr12MoV钢具有高淬透性,截面200~300mm以下可以完全淬透。Cr12MoV钢主要制造大尺寸、形状复杂、承受载荷较大的模具,曾经有“冷作模具王牌”之称。
低淬和低回→晶粒细小,强韧性好。
一次980~1030℃淬火×150~170℃回火,硬度
硬化法为61~63HRC,残奥量少。12%左右未溶
(Cr,Fe)C3碳化物。
一次硬化法使用较普遍
1050~1100℃×500℃左右多次回火,硬
二次度回升到60~62HRC。热硬性较好,强韧
硬化法性较低。二次硬化法适合于工作温度比
较高(400~500℃)且受载荷不大或淬火后表面需要氧化处理的模具。
60HRC
50
40(出)
30A%
←
90095010001050110011501200
淬火温度/℃
Cr12MoV钢的硬度、残余奥氏体量与淬火温度的关系
2高碳中铬模具钢
典型钢号:Cr4W2MoV和Cr5Mo1V。
K以MC型为主,分布较均匀,具有耐磨性好和热处理变形小的特点,适于制造既要求有高的耐磨性,又具有一定韧度的模具。
Cr5Mo1V(美A2)是值得推广的空冷淬硬冷作模具钢,是国际上通用的钢种。φ100mm以下可空冷淬硬,适用于形状复杂、要求热处理变形小又需要好的耐磨性和良好韧度的冷作模具,如下料模成形模、冲头、剪刀片等。
钢碳含量质量分数一般在0.3~0.6%,还加入Cr、Mo、W、Si、Mn、V等合金元素,以提高钢的各种性能。
根据工作条件热作模具钢可分为三大类:热锤锻模具钢,热挤压、热鐓锻及精锻模具钢和压铸模用钢。
4.5热作模具钢
使热或液态金属获得所需形状服役条件
模具是在反复受热和冷却条件下工作.模具受热时间越长,受热程度就越严重
许多模具还受到较大冲击力。工作条件苛刻技术模具钢应具有高抗热塑性变形能力、高
要求韧性、高抗热疲劳、良好的抗热烧蚀性
3、新型冷作模具钢
我国常用7Cr7Mo2V2Si钢,淬透性较好,热处理变形小。用来制造冷鐓模、冷冲模及冲头、冲剪模等。
上模
下
汽车转向节热锻模(大型,700×675×400mm)
一、热锤锻模钢
服役条件性能要求
1)反复冷、热↑热疲劳抗力→↑A1,
一龟裂、热疲劳硬度是有利的;
2)表层温度~500℃,↑热强性韧度一高温回火;
冲击力大→消除回脆,整体性能好;
3)强烈摩擦磨损↑模具高温耐磨性
4模具尺寸比较大淬透性好,导热性好
2、成分特点
C:一般在0.45~0.60%,以保证一定硬度和冲击韧度。Cr:一般1%左右,淬透性,回稳性,改善A;Ni:能↑A,和Cr共同作用1钢淬透性;
Mn:主要代Ni,但Mn↑过热敏感性和回火脆性。Si:能1强度、回稳性和耐热疲劳性,Si量<1%。
Mo、V:有效地细化晶粒,过热倾向,↑回稳性。Mo(W)最重要的作用是钢的回火脆性.所以,不但热锤锻模钢都含有Mo元素,其他热作模具钢也都用Mo(W)合金化。
使用最广泛的是5CrNiMo和5CrMnMo钢。
工艺要求:
注意保护模面和模尾,以避免脱碳。
加热要注意预热,450左右预热,升温速度要慢,<50℃/h;
冷却要注意预冷,预冷到780℃左右,循环油冷,冷至150~200℃取出;
淬火后必须立即回火,绝对不允许冷至室温。思考:为什么?
热处理工艺:5CrNiMo5CrMnMo:T淬830~860℃;
T回450~580℃
170
150sCrMa Mo
150sCrNiMo5
140
130
12010
200300400500
国火温度:℃
sCeMe Mo
110左图
强度和韧度与T回
的关系
450seo550600
火温度,℃右图
硬度与T的关系
3、工艺特点
硬度要求:
小型模硬度要求在40~44HRC,相对较高;?
大型模硬度在35~38HRC为宜,相对较低。
锻模模面:大中型模36~42HRC,较高;?
锻模模尾:大中型模30~35HRC,较低。
思考:锻模模面和模尾硬度不同,在工艺上有什么措施?
耐火泥或黄泥石绵绳保护剂铁盘模具
上图锻模加热时液面
的保护
右图盐浴中燕尾
部分的回火盐浴
二、热挤压模钢
和热锤锻模相比,热挤压模在工作时需要较长时间与被变形加工的金属接触,其受热的温度往往更高。热挤压模还承受很大的应力和摩擦力。
这类模具的尺寸一般都不大,比锤锻模要小。热挤压模主要要求有高的热稳定性、较高的高温强度、耐热疲劳性和高的耐磨性。有铬系、钨系和钼系热模具钢三类。
铬系:
4Cr5MoSiV、4Cr5MoSiV1、4Cr5W2SiV等常用。淬透性较高,较高的强度和韧度,抗氧化性较好。常用于制造尺寸不大的热锻模、钢及铜的热挤压模、铝及铜合金的压铸模等。
钨系:
3Cr2W8V钢使用最多,具有高的热稳定性、耐磨性,但韧度和抗热疲劳性较差。国外已基本停止,以H13代之。
压铸模具钢的选择首先要根据浇注金属的温度和浇注金属的种类来决定。
锌合金、铝合金、镁合金是低熔点的金属合金,可以选择30CrMnSi、40Cr、5CrMnMo等低合金钢来制造压铸模具。如压铸锌合金的模具可采用5CrMnMo钢,也可使用40Cr调质钢
压铸铝、镁合金的模具目前常选用3Cr2W8V、H13和4Cr5MoSiV1钢
铜合金和黑色金属的熔点比较高采用难熔金属为基的合金,如钼基合金、钨基合金等
铝合金压铸模
三、压铸模钢
压力铸造是在高的压力下,使液态金属挤满型腔成型。在工作中模具反复与炽热金属接触
要求压铸模具钢有高的耐热疲劳性、较高的导热性、良好的耐磨性及耐蚀性和一定的高温强度等
常用钢号4CrW2Si、5CrW2Si、6CrW2Si等。Si、Cr:↑低温回火稳定性,并推迟低回脆性区,因此可↑回火温度到280C,而得到较高的韧度,特别是Si元素更为有效;这些元素都↑淬透性、强度和耐磨性。
W:进一步↑耐磨性和细化晶粒,W还能有效地↓↓回火脆性,所以含W钢可在430-470C回火,可得到更好的韧度。
2
塑料模具用钢
对塑料模的要求:
①加工表面应有高的光洁度,所以要求模具材料夹杂物少,组织均匀,表面硬度高;②表面耐磨耐蚀,能长期保持表面光洁度;③有足够的强韧性,能承受一定负荷而不变形;④变形要小,以保证互换性和配合精度。
塑料模具用钢范围非常广泛,作为塑料模具专用钢并已纳入国家标准的仅有十余个
4.6其它类型工具用钢
1、耐冲击用钢
切边、冲孔剪切力和一般模具比,刃口薄
、剪切等冲击力和刃具比,冲击力大
C%,↑回稳性,1韧度
耐磨性
形成稳定K↑耐磨
韧度高
+Si、W中高碳,0.4~0.6%
+W、V低合金,+W、Si、V、Cr
组织控制:在淬火加热时K的溶解量决定了基体的含碳量和合金度,在回火过程中组织性能主要取决于回火温度。K的形状、大小、数量和均匀性对工具的性能有很大的影响
工具钢的锻造和预处理工艺非常重要,它决定了工具钢最终热处理前的组织状态,特别是K的形态和分布,这是保证最终热处理性能质量的基本前提。
小结
耐磨性与韧度的合理配合是工具钢的主要矛盾。工具钢的合金化和热处理工艺基本上都是围绕这主要矛盾进行优化设计的
在工艺措施上,经常采用预热、预冷,淬火常用等温、分级、双液淬火等方法,并且需要及时回火。尽可能地降低淬火应力、减小变形开裂倾向和稳定组织。
塑料模制造成本高,材料费只占模具成本的一小部分,一般在10~20%,有时甚至低于
10%。因此模具材料一般是优先选用工艺性好、
性能稳定和使用寿命长的材料。
常用牌号有SM4Cr5MoSiV、SM2Cr13等。
第5章不锈钢
不锈钢是指在空气、水、盐水、酸、碱等腐蚀介质中具有高的化学稳定性的钢。仅能抵抗大气、水等介质腐蚀的钢叫做不锈钢,在酸、碱等介质中具有抗腐蚀能力的钢称为耐酸钢。能抵抗大气、水等介质腐蚀的不锈钢不一定耐酸,而耐酸钢肯定是能抵抗大气、水等介质腐蚀的。习惯上都称为不锈钢,其实是有很大区别的。
5.1概述
5.1.1金属腐蚀类型
1、均匀腐蚀(general attack)腐蚀均匀地在材料的表面产生,损坏大量的
材料。容易发现,危害性不是很大。
2、点腐蚀(point corrosion)由于应力等原因使腐蚀集中在材料表面不大
的区域,向深处发展,最后甚至能穿透金属。
3、晶界腐蚀(intergranular corrosion)晶界腐蚀是指腐蚀过程是沿着晶界进行的,
其危害性最大。如虫蛀的苹果。
4、应力腐蚀(stress corrosion)
钢在拉应力状态下能发生应力腐蚀破坏的现象。
没有什么预兆,所以其危害性也是比较大的5、磨损腐蚀(corrosion wear)
在腐蚀介质中同时有磨损,腐蚀和磨损相互促进、
相互加速的现象称为磨损腐蚀。
5.1.2性能要求与提高钢耐腐蚀性能的途径
(1)不锈钢具有较高的耐蚀性
(2)不锈钢应具有一定的力学性能。很多性能要求构件是在腐蚀介质下承受一定的载荷
(3)不锈钢应有良好的工艺性能。管材、
板材、型材等要经过加工变形制成构件,如
容器、管道、锅炉等。因此不锈钢的工艺性
也很重要,主要有焊接性、冷变形性等。
金属电化学腐蚀现象:
不同金属的直接接触,如铜与钢;
同一金属在有浓差的介质中,→浓差电池,如存水的铁桶、盐炉中的电极;
不同电位的显微组织,→微电池,如生锈、金相组织的腐蚀;
成分不均匀,→微电池,如晶界与晶粒内部;应力不均匀,如铁丝弯曲处易蚀,铆钉头易蚀。
(a)均匀腐蚀b)点腐蚀
(c)品界腐蚀
图各种腐蚀类型
提高钢耐腐蚀性能的途径主要有:
(1)形成稳定保护膜,→Cr、Al、Si有效。(2)1固溶体电极电位或形成稳定钝化区→Cr、Ni、Si:Ni贵而紧缺,Si易使钢脆化,Cr是理想的。
(3)获得单相组织→Ni、Mn→单相奥氏体组织。
(4)机械保护措施或复盖层,如电镀、发兰、涂漆等方法。
5.1.3不锈钢的组织与分类
铁素体形成元素:Cr、Mo、Si、Ti、Nb等;
奥氏体形成元素:C、N、Ni、Mn、Cu等。
铬当量[Cr]=Cr+1.5Mo+2.0Si+1.5Ti+1.75Nb
+5.5AI+5V+0.75W
镍当量[Ni]=Ni+Co+0.5Mn+30C+25N+0.3Cu铬当量和镍当量的综合作用结果决定不锈钢的组
织→组织状态图。
305%
2510%
0%F20%
2040%
A+M
1580%
+F
A
10M
100%
A+M+F
F+MM+F
F
48
1216
20
2428323640
(Cr]=w(Cr)+w(Mo)+1.5 w(Si)+0.5w(N)
图不锈钢组织状态图(焊后冷却)
Tammann定律-0.6
-0.4
0.2
将较稳定的A组元0
加入到较活泼的B组0.2
0.4
元固溶体中,当A组0.6
0.8
元含量达n/8原子比1.0
时,固溶体电极电位1.2
1.4
突然升高,耐蚀性也1.6
有一急剧变化。也称1.82101214220
28303234
为二元合金固溶体电Cr/%(原子)
位的n/8定律Cr对Fe-Cr电极电位的影响
5.2影响不锈钢组织和性能的因素5.2.1合金元素对钢组织和性能的影响一、铬元素的作用
Cr是决定钢↑固溶体电极电位
耐蚀性的主
要元素表面形成致密氧化膜
Cr↑耐蚀性的作用符合n/8定律
(1)M不锈钢:1Crl3~4Crl3等Crl3型,Crl7Ni2、9Cr18等
(2)F不锈钢:如0Cr17Ti,1Cr25Ti,
不锈钢分类00Cr27Mo等
(3)A不锈钢:具有单相A组织,如0Cr18Ni9、1Crl8Mn8Ni5N等
(4)A-F复相不锈钢:如0Cr21Ni5Ti(5)沉淀硬化不锈钢
二、碳和氮的作用
C:C1,强度1,冷变形性、焊接性、耐蚀性;综合因素→碳量应尽可能地低N:稳定A组织,↑强度,又能保持好的塑韧性,1耐腐蚀性能,特别是耐局部腐蚀三类:控氮型(0.05~0.10%)
中氮型(0.10~0.40%)
高氮型(>0.40%)
三、其它元素的影响
Ni是奥氏体形成元素,能适当提高固溶体电极电位;能形成单相奥氏体;
锰可部分代Ni,但不单独加入;
钛和铌能形成稳定K,固定C,使Cr固溶于基体,从而防止晶界腐蚀;
钼能↑不锈钢钝化能力,扩大钝化介质范围
5.2.2腐蚀介质对钢耐蚀性的影响
与介质的种类、浓度、金属的温度和压力等环境条件有
耐蚀性密切的关系
必须根据工作介质的特点来正确
选择使用不锈耐蚀钢钢种。
①含碳量<0.25%,为提高某些性能,可加入Mo、Ti、Al、Si等元素;②在硝酸、氨水等介质中有较好的耐
基本特点蚀性和抗氧化性;
③力学性能和工艺性较差,脆性大,T在室温左右。
④无同素异构转变,多在退火软化态下使用。
5.3铁素体不锈钢
一、常用铁素体不锈钢及特点
铁素体不锈钢主要有三种类型:
(1)Cr13型如0Cr13、0Cr13Al、0Cr11Ti等;(2)Cr17型如1Cr17、0Cr17Ti、1Cr17Mo等;(3)Cr25-30型如1Cr28、1Cr25Ti、
00Cr30Mo2等。
1、在大气、水、水蒸气等弱腐蚀介质。
→>13%Cr
2、氧化性介质,如硝酸。易形成钝化的氧化膜,>17%Cr,Cr越高越好;
3、非氧化性酸,如稀硫酸。在>17%Cr基础+Mo、Cu;
4、强有机酸,在Cr-Mn型不锈钢基础上,加入Mo、Cu;
5、含有CI离子的介质,如海水,CI很小,有很大腐蚀性。
二、铁素体不锈钢的脆性
高铬铁素体不锈钢的缺点是脆性大,主要有几个方面:
(1)粗大的原始晶粒
由于原子扩散快,晶粒粗化温度低和晶粒粗化速率高。在600℃以上晶粒就开始长大,而A不锈钢相应为900℃
思考:为什么不能象一般钢那样经过重新加热重
结晶而细化晶粒?
(2)F不锈钢存在475℃脆性
当>15%Cr时,随Cr↑其脆化倾向也↑。在400~525℃长时间加热或缓慢冷却时,钢就变得很脆,以475℃加热为最甚
原因:在脆化T范围内长期停留时,铬有序化→α"相,与母相共格→大内应力。→AK
(3)金属间化合物相的形成
。相具有高硬度,有大的体积效应,且常沿晶界分布,所以使钢产生了很大的脆性
5.4马氏体不锈钢
这类钢主要含12~18%Cr,淬火冷却能产生M。
一、马氏体不锈钢的成分和组织特点
马氏体不锈钢可分为三类:
(1)Cr1型,有1Cr1、2Cr13、3Cr13、4Cr1等钢号;
(2)高碳高铬钢,如9Cr189Cr18Mb等;
(3)低碳17%Cr-2%Ni钢,如1Cr17Ni2
1Cr13、2Cr13常用于结构件→调质。
调质处理因为铬↑抗回火性和Ac1点,所以调质回
火温度也相应1.通常为640~700℃。回火后应采用油冷?
3Cr13、4Cr13常做有一定耐蚀性的工
淬火低回具,所以采用淬火低温回火。T在1000
~1050℃,为减少变形,可用硝盐分级冷却。组织为马氏体+碳化物+少量AR
二、马氏体不锈钢的热处理特点
常用的热处理工艺有软化处理、球化退火、调质处理和淬火+低温回火。
软化处理有两种方法:
软化处理一是进行高温回火,将锻轧件加热
至700~800℃保温2~6小时后空冷,使
马氏体转变为回火索氏体。
另外也可以采用完全退火。
1Cr13:M+F类似于
制造不锈
调质钢结构件
2Cr13:M
3Cr13:M制造耐蚀
类似于工具(手
工具钢
4Cr13:M+K术刀等)
思考题:
4Cr13为什么是过共析钢?
9Cr18含Cr已达18%,但只是耐大气腐蚀不锈钢?
5.5 奥氏体不锈钢
奥氏体不锈钢是应用最广泛的耐酸钢,约占不锈钢总产量的2/3。奥氏体不锈钢优点如下:
①具有很高的耐腐蚀性;
②塑性好,容易加工变形成各种形状钢材;③加热时没有同素异构转变,焊接性好;
④韧度和低温韧度好,一般情况下没有冷脆倾向,有一定的热强性;
⑤不具有磁性;
⑥价格较贵,切削加工较困难,导热性差。
5.5.1奥氏体不锈钢的成分特点
奥氏体不锈钢的主要成分是C和Ni,18C和8Ni的配合是世界各国奥氏体不锈钢的典型成分。
Cr+Ni=耐蚀电位接近n/8定
18+8=26律中n=2的电位值
耐蚀性达到具有良好钝化性能
较高的水平
Cr、Ni再↑,
更为优良单相奥氏体组织
305%
2510%
A0%F
20%
2040%
A+M
1580%
A+F
10M
100%
A+M+F
5F+M
M+F
F
48
12
16202428323640
(Cr]=w(Cr)+w(Mo)+1. w(Si)+0.w(No)
图不锈钢组织状态图(焊后冷却)
平均值0.10%
碳的分布
溶解值0.02%
平均值18%
钝化所12%
虚值铬的分布
Cr3C
品间
图不锈钢晶界腐蚀贫Cr区示意
5.5.2奥氏体不锈钢的晶间腐蚀
奥氏体不锈钢焊接后,在腐蚀介
质中工作时,在离焊缝不远处会产
生严重的晶间腐蚀。
在焊缝及热影响区(450~800℃),沿晶界析出了K(Cr;Fe)23C6,晶界附近区域产生贫Cr区(低于1/8定律的临界值)。
Ti、Nb稳定K↑抗晶间腐蚀的能力;M↑不锈钢钝化作用,↓点腐蚀倾向,↑钢在有机酸中的耐蚀性;
Cu↑钢在硫酸中的耐蚀性;
Si:↑钢抗应力腐蚀断裂的能力。
平衡态时为奥氏体-铁素体-碳化物组织,经过固溶处理后获得了单相奥氏体。
在Cr-Ni奥氏体不锈钢中,在450-800℃的温度范围内时效处理,可考察不锈钢晶间腐蚀的敏感性。敏化处
敏化处理理和敏感性的关系通常用TTS(Time
-Temperature-Sensitivation)曲线来表示,如下图所示
敏化处理后,在金相组织上可看
到碳化物沿着晶界析出
3
2y+MC
品间腐蚀一
+MC+MC
y+M2C
时间T时间
a)b)
曲线表示钢开始产生晶间腐蚀,曲线2是由于时间充分,晶间腐蚀倾向已不再出现,也就是产生晶间腐蚀现象结束线。曲线包围的区域是产生晶间腐蚀的温度、时间范围。
经强K形成元素Ti、Nb合金化的不锈钢称为稳定性钢。这种钢析出K的温度范围可分成两个区域,如上图右。曲线1表示析出M2C6型K的富Cr区域,曲线3表示析出MC型K的区域,曲线2是产生晶间腐蚀的区域。在仅有MC型碳化物析出的区域,没有晶间腐蚀倾向。
Ni、Co、Si,促进产生晶间腐蚀,Mo、Ti、Nb、Mn、V,都能不同程度地阻止晶间腐蚀的倾向。显然,钢中含碳量的提高,钢的晶间腐蚀倾向也增大。
也称为稳定化退火。这种处理只是
稳定化处理在含Ti、Nb的A不锈钢中使用。合理
选择稳定化处理的温度和时间,→获
得最佳的效果。
高于Cr23C6的溶解温度而低于TiC的溶解温度。通常采用850~950℃,保温2~4h后空冷,如下图所示。在稳定化一般原则
退火过程中,能将Cr23C6转变为TiC,一彻底消除晶间腐蚀倾向。
5.5.3奥氏体不锈钢的热处理
固溶处理:奥氏体不锈钢的固溶处理温度一般为1050~1150℃,比较常用1050~1100℃。为了保证高温奥氏体不发生分解,固溶处理后冷速应较快。一般情况下,多采用水冷。
固溶处理是奥氏体不锈钢最大程度的软化处理。由于这时的奥氏体具有最大的合金度,所以也具有最高的耐蚀性能。
为防止A不锈钢的晶间腐蚀,可采取以下措施(1)降低钢中的含C量;
(2)加入Ti、Nb,析出特殊K,稳定组织;
(3)进行1050~1100℃的固溶处理,保证Cr含量;(4)对非稳定性A不锈钢进行退火处理,使A成分均匀化,消除贫Cr区;
(5)对稳定性钢,通过热处理形成Ti、Nb的特殊K,以稳定固溶体中Cr含量,保证含Cr量水平
1100-1000℃
7+MC
T,950~850℃
品间腐蚀水
进火
时间
图含T澳氏体不锈钢的热处理工艺
5.5.4铬锰氮奥氏体不锈钢少镍和无镍奥氏体不锈钢主要有三种类型:
Cr-Mn系奥氏体不锈钢,Cr-Mn-系奥氏体不锈钢和C1-M-Ni、Ci-M-Ni-系奥氏体不锈钢。
氮稳定奥氏体的作用大,氮能抑制。相的形成,有效地提高钢的强度而不降低室温韧度,并且对耐腐蚀性无影响。但氮含量受到溶解度的限制,一般的氮含量在0.3~0.5%以下。
1Cr18Mn8Ni5是目前国内外都生产的钢种
本章小结
不锈钢主要矛盾是耐蚀性和强度的合理兼顾。对于一定成分的不锈钢,要达到预定耐蚀性和力学性能,关键是热处理工艺。不同类型或成分的不锈钢适用于不同介质的工作环境
耐蚀能力遵循n/8规律。A不锈钢主要问题是晶界腐蚀。措施:从合金化角度考虑,C含量和加入Ti、V元素;从热处理工艺考虑,应根据各合金K形成、溶解、析出的规律,设计和制定热处理工艺参数。
二、提高钢抗氧化性的途径
1、提高钢氧化膜稳定性
FeO的形成温度;
↑FeO的形成温度,又优先形成稳定氧化物→Cr、Al、Si。
如:1.03%Cr,FeO形成温度为600℃;
例子1.14%Si,FeO形成温度为750℃;
Cr、Al量高时,钢的表面可生成致密的Cr2O3或Al2O3保护膜。
6.1基本概念
1
金属的抗氧化性
铁氧化物类型有FeO、Fe,O3、Fe3O4三种。
FeO:结构疏松,冷却分解一应力,结合力弱,易剥落;Fe,O、FeO4:结构致密,和基体结合好。
570℃以下,氧化膜由Fe2O3和Fe3O4组成;形成规律570℃以上,氧化膜由Fe2O3、Fe3O4和FeO
氧化物组成,约1:10:100.
570℃以上铁的氧化过程大大地加速,遵守
抛物线规律
第6章耐热钢
蒸汽锅炉、蒸汽涡轮,航空工业的喷气发动机,以及航天、舰船、石油和化工等工业部门的许多工作部件在高温下工作。因为是在高温下服役,所以这些零部件技术要求比较苛刻。通常把在高温条件工作的钢称为耐热钢。
耐热钢应具有两方面的基本性能,一是有良好的高温强度和塑性,二是有足够高的高温稳定性。根据不同服役条件,常常将耐热钢分为热强钢和热稳定性钢两大类。
2形成致密、稳定的氧化膜
↑Cr、Al、Si、Ti等,逐步形成以合金元素氧化物为主或合金元素氧化物的氧化膜,如AL2O3、SiO2、Cr2O3等→致密、稳定。
240Mo
176
>集Cr
105Mn
SiCo
85Ni
23
4
5
合金元素/%
常用合金元素对工业纯铁蠕变极限的影响
6.1.2钢的热强性
一、钢的热强性能指标
1、蠕变及蠕变极限
蠕变极限是试样在一定温度下和在规定的持续时间内,产生的蠕变变形量(总的或残余的)或蠕变速率等于某规定值时的最大应力。
700
例如:1/10000,表示在700℃时,持续时间为10000
h,产生蠕变总变形量为1%的蠕变极限。
二、提高热强性的途径
1、强化基体
基体金属熔点:↑T熔,1金属原子间结合力。
铁、镍、钼基是依次↑
合金晶格类型:fcc-Fe>bcc-Fe,奥氏体型钢要比
F、M、P型钢的蠕变抗力高
固溶体结合力:合金化一↑固溶体原子间结合力,Mo、Cr、Mn、Si作用较大
4应力松弛
应力松弛现象是在具有恒定总变形的零件中,随时间延长而自行降低应力的现象。
原子易发生扩散,
蒸汽管道螺栓使弹性变形变成了
需要经常拧紧塑性变形,从而使
应力不断降低
2持久强度
持久强度极限是试样在一定温度和规定的持续时间内引起断裂的最大应力值,
如:700
100=300MPa,表示在700C时,持续时间为100的持久强度极限值为300MPa
3高温疲劳强度
在高温疲劳时只有条件疲劳极限,即把在某一规定的循环次数(一般采用107~10次)下而不断裂时的最大应力作为疲劳极限。
2强化晶界
净化晶界:杂质易偏聚在晶界,形成易熔夹杂物→晶界强度。RE、B优先结合杂质,形成高熔点化合物,异质晶核→从晶界转入晶内填充空位:晶界上空位多,原子易快速扩散。B易偏聚晶界,晶界空位。
3弥散强化
弥散质点,位错运动,↑强度→有效性和程度的关键是质点的性质、大小、分布、稳定性。
4热处理
1珠光体热强钢的蠕变强度
6.1.3耐热钢的合金化
Cr:↑钢抗氧化性主要元素。形成致密而稳定的
Cr2O3。T↑,Cr↑。如600~650℃,需要5%Cr;800℃时,为12%Cr。↑固溶强化Mo、W:1低合金热强性重要元素。固溶强化,析出稳定相。
6.2热强钢
6.2.1珠光体热强钢
按用途主要有锅炉钢管、紧固件和转子用钢等几大类。
一、锅炉钢管用珠光体热强钢
高温和高压,高温烟气和水蒸汽,安全可靠→抗氧化和耐蚀,组织稳定,工艺性能好
Ni:获得奥氏体组织
Ti、Nb、V:形成稳定K,1钢松弛稳定性,↑热强性
C:较低温度时强化钢,1G化,1K聚集长大→尽可能↓C。
AI:↑抗氧化性的有效元素。
在1000℃时,6%Al≈18%Cr水平。1冶金工艺性,使钢变脆。→不能单独加入,作为辅助合金化元素。
Si:↑抗氧化性的辅助元素。但效果比AI还要有效,使钢脆性大,用Si代替部分Cr。↑G化,↑K聚集长大。一般在2~3%Si。
用于渗碳罐,抗渗性好。
普遍组织不稳定,如片状P球化、K长
问题大、G化,→强度↓,管子爆裂
合金≤0.2%C→球化、K长大、G化
化采用Cr-Mo-V系
Mo、W、Cr→固溶强化,JK长大和G化,Cr抗氧化性和耐蚀性;
直接作用形成稳定MC型K,
V弥散强化,↑热强度
Ti间接作用
使更多Mo、W、Cr
固溶,↑热强度
典型钢号12Cr1MoVG是用量较大的钢管材料,15CrMo、12CrMoV等
二、紧固件用珠光体热强
处于初紧预应高的屈服强度、
紧固件力状态工作
松弛稳定性,
缺口敏感性小,
1C
Cr/ Mol V一定抗氧化性
常用钢:35CrMoV、25Cr2MoV钢常用作中压气轮机的螺栓和螺母材料,25Cr2Mo1V钢在高压电厂中广泛使用
二、气阀钢
内燃机排气阀工作条件非常苛刻:
700~850℃工作,受到燃气的高温腐蚀、氧化腐蚀和冲刷腐蚀磨损,热疲劳
常用钢号有4Cr9Si2、4Cr10Si2Mo,采用1050℃淬火加热、油冷,700℃左右回火,组织为回火索氏体,保持马氏体形貌特征。高于750℃的阀门需要采用奥氏体型热强钢,
6.2.2马氏体热强钢
一、叶片用钢
在Crl3型马氏体不锈钢的基础上进一步合金化发展了Crl2型马氏体耐热钢。
15Cr12WMoV、2Cr12WMoNbVB等,工作温度可在600℃左右。
常用于大功率火力发电机组。
三、转子用钢
主轴、叶轮过热蒸汽,复杂应
或整锻转子力(扭/弯/热等)
热强性,沿轴向、径向均匀一致
的综合力学性能→淬透性。
常用钢:汽轮机叶轮常用中碳珠光体热强钢制造。如35Cr2MoV、33Cr3WMoV钢
6.3抗氧化钢
抗氧化钢用于工业炉的构件、炉底板、炉罐等.F型是在F型不锈钢基础上发展形成。
A型抗氧化钢是在A不锈钢基础上发展起来的。型抗氧化钢目前主要有铬-镍系和铬-锰-氮系。铬-锰-氮系奥氏体型抗氧化钢在950C以下有较好的抗氧化性,且有较高的高温强度,工艺性不如铬-镍系抗氧化钢。低镍奥氏体抗氧化钢,使用比较多的有ZG4Cr22Ni4N和ZG3Cr24Ni7N钢,经济.
本章小结
温度对钢的使用来说有很大的影响,是关键因素。在高温条件下工作的零部件就其材料成分、性能要求及失效机理和一般常温下的零件相比,有很大的不同。
钢的高温强度和组织稳定性是耐热钢设计与处理工艺的主要矛盾。从合金化考虑,主要措施有↑原子结合力、强化晶界、稳定相的弥散强化。不同合金的耐热钢有其适宜的使用温度范围。
第章铸铁
铸铁是指含碳量大于2.14%或组织中具有共晶组织的铁碳合金。实际上是以铁-碳-硅为主的多元合金。如再加入铝、铬、锰、铜等元素,则是各种特殊性能铸铁
铸铁可分为以下几类:灰口铸铁,球墨铸铁,蠕墨铸铁,可锻铸铁,白口铸铁等
1800
1700H点C0.86
J点:C0.16%
1600
1536℃A8+L
1500B-0.
53
H493
CL
4000℃
6+r100%
1400
1392℃N7+L
D
1300+G
1252C
1200E2.
0153℃4,266.69%
E2.1147℃
4.30
0F-
1100L+
y+G
1000G91y+Fec
900
8000.
69
S736℃
700P-0.034-S 0.76727℃
長
a+G
600n+eC
500Q0.51.01.52.02.53.03.54.04.55.0
C
图铁一碳双重相图(G一石墨,Fe1C一渗碳体)
7.1铸铁石墨化及影响因素1铸铁的石墨化过程
渗碳体是介稳定相,而石墨才是稳定相。热力学条件:有利于石墨化的过程
动力学条件:主要有成分起伏、结构起伏和原子扩散.有利于渗碳体的形成
为了使化进行,可人为地改变热力学和动力学条件
上图
沧州铁狮子
铸于953年,重40余吨。右图当阳铁塔
铸于1061年,八棱13层,中国曾发现陨铁制兵器3
塔体分段铸造件,2件被盗卖至美国
成分起伏FeC(6.67%C)+A
浓度差小
L
4.3%CG(100%C)+A
结构起伏Fe3C
比较接近
(复杂斜方结构)
L(或Y-Fe)
Fe、C并存(面心)G
(六角形层状结构)
原子扩散有利于Fe3C长大
G长大,不但要C原子扩散集中,而且Fe原子要从G生长前沿逆向扩散。而Fe3C长大只要C扩散,Fe原子局部移动即可。G长大较难。
2影响铸态组织的因素
(1)化学成分的影响
C和Si是基本成分,是11G元素。石墨来源
C
Si于C。Si含量一般在0.8~3.5%之间,Si的加入对
Fe-G相图发生变化。
①共晶点和共析点碳量随硅含量的1而;
S作用2
使共晶和共析转变在一温度范围内进行;③↑共晶和共析温度。共析温度提高更
多,大约每11%Si,可使共析温度128℃;④Si促进铸铁石墨化的作用相当于1/3C。
(2)冷却速度的影响
化学成分选定后,改变铸铁各阶段冷却速度,可以在很大范围内改变铸态组织。V越缓慢,越有利于按Fe-C状态图进行结晶和转变。尤其是共析阶段G化,通常情况下,共析阶段的G化难以完全进行
在生产中,铸件冷却速度是一个综合因素,它与浇注温度、铸型条件以及铸件壁厚均有关系。同一铸件不同壁厚处具有不同组织和性能,称之为铸件壁厚敏感效应。铸件壁厚是设计的,难以改变,对已知壁厚铸件,可调整化学成分来保证获得所需组织
↑白口;铁水流动性,恶化铸造性;形成FeS,分布晶界,使铸铁变脆。S是有害元素,其含量应尽量低,一般将S限制在0.15%以下
促进石墨化元素阻碍石墨化元素
+Al、C、Si、Ni、CuW、Mn、Mo、S、Cr、Fe、Mg
↑G化,≈1/3C作用。>0.2%后,出现硬脆FeP,呈孤立、细小、均匀分布时,可1耐磨性。若粗大
P连续网状分布,将强度,↑铸件脆性
除在耐磨铸铁中可达0.5~1.0%外,在普通铸铁中都作为杂质,通常灰铁中P含量控制在<0.2%。G化;Mn能与S结合生成MnS,削弱硫的有害
Mn作用。铸铁中含锰量一般在0.5~1.4%范围内,如要获得铁素体基体,含锰量应取下限。
G化过程可分为两个阶段:发生在PSK线以上的G化为第一阶段;发生在PSK线以下的G化为第二阶段,实际是以共析线为界。第一阶段G化决定G形态,第二阶段G化决定基体组织石墨化阶段与组织
第一阶段第二阶段组织
铸铁名称
完全进行完全进行FG
不同基体的灰
部分进行PPG
铁、球铁、蠕铁、
未进行PG
可锻铁
部分进行未进行Ld+PG
麻口铸铁
未进行未进行
Ld
白口铸铁
7.2石墨的形成及生长
1片状石墨的生长方式
内在因素G为六方点阵层状结构。层面原子间距小,较
强共价键结合,层间原子间距较大,原子作用力弱。→层面方向生长速度就大,石墨是在与铁水相接触的条件下以片状方式生长的。
外在因素G形成会导致周围铁水C浓度,1凝固点一生成
包围G片的A体壳。但G片端生长速度超过A结晶速度,G片端总是和铁水直接接触。
如G片向两侧加厚生长,须依靠C从铁水中先扩散到A层再扩散到G;而Fe还必须向A层外作反方向扩散,显然是较难的一G片增厚是较慢的最后形成了立体花朵状
石墨
奥氏体
熔体
石墨晶体结构片状石墨生长机理
3)球状石墨的形核机理
G都是从铁水中直接析出的。球状G的形核以硫化物及氧化物夹杂微粒作为结晶中心。4)球状石墨的生长机理
螺旋位错理论:由于螺旋位错存在,碳原子优先在晶体表面造成的螺旋台阶旋出口作为开始生长的最有利位置。理想情况下晶体将长成一个近似球状的多面体,形成年轮状结构。生长机理,有许多学说,难以完美解释
2)球状G的形成条件
球化处理:浇注前加入一定量球化剂,如稀土-硅铁-镁系等孕育处理:加入高硅铁,获得很多的非自发晶核,细化G
↑铁液的过冷度
球化剂
Mg/Ce/
Y/La等球化剂与铁液中氧、硫发生反应,含
氧、硫量,1铁液表面张力,铁液/石
墨间的界面张力1
2球状G的形成过程G呈多边形轮廓,内部呈放射
(1)球状石墨的结构状。中心是G核心。球面是单晶体锥形G(0001)底面
C0001]
0001)
球状石墨内部的年轮状结构球状石墨的结构示意图
C0001]
1010]1010]
a)b)
图球状石墨晶体生长示意图a)[0001]方向生长;b)长成球状多面体
7.3灰铸铁
有HT100、HT150、HT200、HT250、
牌号HT300、HT350六个国家标准牌号。
意义HT”表示“灰铁”,后面的数字表示抗
拉强度(不低于,MPa)
1、灰铸铁组织特点
组织:片状G+金属基体(F,F+P,P)。
石墨形态:有A、B、C、D、E、F6种类型,
其中A型最好。经孕育处理的灰铸铁为孕育铸
铁。实际生产,大部分铸铁都经过孕育处理
孕育处理目的?
(a)A型石墨(b)B型石墨
(c)C型石墨
(d)D型石墨(e)D型石墨
(f)F型石墨
图片状石墨的分布类型
(4)良好的减震性和减摩性
灰铁内部存在大量片状G,它割裂基体,破坏连续性,阻止振动传播,并能转化为热能而发散,因而灰铁具有很好的减振性。
常用于机床底座,效果很好
一方面G本身是良好的润滑剂,另一方面G脱落后的显微“口袋”,可以储存润滑油和收集微小磨粒,因此具有良好的减摩性。如机床导轨
(2)缺口敏感性小,可切削性好
大量G相当于已经存在了许多缺口,工件的人为缺口就不太敏感了。G在机加工时可以起到断屑和对刀具润滑作用→可切削性是优良的()良好的铸造性
灰铁成分接近共晶点,铁水流动性好,可铸造出形状复杂零件。且不易形成缩孔和缩松,能获得较致密的铸件。
2灰铸铁性能及热处理(1)抗拉强度低、塑韧性很差G相当于空洞基体强度不能充分
有效截面积↓发挥,其强度利用率
仅30~50%,表现为
G片端似裂口很低,塑性和韧
↑应力集中性几乎为零
7.4球墨铸铁
牌号例如QT400-15,QT为球铁代号,400
意义表示抗拉强度不低于400MPa,15表示
伸长率不低于15%。
1、球铁组织与性能
组织:球状G+金属基体(F,F+P,P,S回,B等)。球状G孤立分布,理想的是“小、匀、圆、适量”。
表球墨铸铁的力学性能o/MPa0a.2/MPa/%硬度
牌号基体不小于
注意HB
不小于
QT40018铁素体40025030-180
QT00-15铁素体40025015130-180
QT450-10铁素体45031010160~210
QT500-7铁素体+珠光体5003207170-230
QT600-3珠光体+铁素体6003703190~270
QT700-2珠光体7004202225-305
QT800-2珠光体或回火组织8004802245-335
QT900-2贝氏体或回火马氏体9006002280-360
球状G应力集中↓球铁基体的利用
基体的缩减作用!率可大大提高,达
割裂基体作用!到70~90%。
对灰口铸铁来说,主要的矛盾是片状G,→改变基体组织无明显作用。当G变为球状时,矛盾的主要方面发生了变化,基体成为决定性的主导因素,基体性能可得到较大的发挥。
L
A+LA+L
LL+G
L+G
A135A
A+L+GA+L+G
A+G
A+G
F+A+GF+A+G
FF+G
FF+G
01.13.5
0.8
2.7
C%C
a)b)
图
Fe-C-Si三元合金状态图变温截面a)含2.4%Sib)含4.8%Si
2球墨铸铁的热处理特点
(1)共析转变不是在恒定的温度下进行,而是在一个较宽的温度范围内进行下图)
改变热处理不同比例的F
T和t和P基体组织
较大幅度地调整铸
铁的力学性能
oO
退火球铁组织铸态球铁组织(牛眼”状)
铁素体+球状石墨珠光体-铁素体-球状石墨
(2)奥氏体含(量可在较宽范围内变化
石墨是的“仓库”,既可在高温时”输出给奥
氏体,也可在冷却时容纳奥氏体中析出的C(3)G参与相变,但一般不能改变G形状与分布(4)一般热处理工艺方法基本上可采用
3、球墨铸铁的热处理
(1)消除内应力退火
(2)高温石墨化退火消除游离渗碳体
(3)低温石墨化退火消除共析渗碳体(4)正火处理和调质处理获得珠光体的组织和提高珠光体的分散度
(5)等温淬火处理得到B体或A—B体基体组织。提高综合机械性能
(6)表面淬火
(7)化学热处理氮化、渗硼和渗硫等
本章小结
不同类型G形成主要取决于成分和冷却速度铸铁中G参与相变过程,但热处理不能改变石墨形态和分布。石墨形状、大小、数量、分布影响了铸铁基体性能的发挥程度,→基本上决定了铸铁宏观力学性能。从片状石墨到球状石墨,使铸铁中石墨和基体的组织配合发生了质的变化。
第铝合金
铝具有一系列比其他有色金属、钢铁和塑料等更优良的特性:
密度小,仅为2.1g/cn2,约为钢的1;优良的导电性、导热性;
良好的耐蚀性;
优良的塑性和加工性能等。
自由烩成分、结构、HT200灰口铸铁:片G,
有利于石墨扩散有利于QT400-18
化FeC析出
性能特点与用途。
KTZ450-06孕育处理
热力学动力学牌号及数字意义可锻铸铁:团絮状
G,由白口铁经石
化得到,性能与
用途
石墨化过程铸铁中心问题:
I决定G形态G形状、大小、
球星铸铁:球状G
Ⅱ决定基体数量、分布
球化处理。热处理
工艺:与灰铁不同
与钢区别。不同工
艺得到不同基体组
影响因素铸铁性能
织。性能与用途
化学成分冷却速度强度、伸长率、冲
C、Si促进薄壁表面易击韧度比钢低;耐蠕铁:蠕虫状G
石化;白口。壁厚磨;切削性好;消特殊性能铸铁:耐
Mn、S阻止敏感性,性振性好;缺口敏感蚀、耐磨、耐热
石里化能差异性低;铸造性好。
球墨铸铁基体的性能可得到较大的利用,钢的各种热处理强化工艺基本上都可以在球墨铸铁中应用。不同类型铸铁有不同用途,根据零部件的工作条件和技术要求,可合理地选择铸铁类型及其处理工艺。通过成分组织和工艺的特殊设计,可得到相应的耐热、耐磨、耐蚀等特种铸铁。
8.1铝合金的热处理及时效强化1、铝合金的分类
变形铝合金-1A
铸造铝合金-2
防锈铝-2千
L
B
——不能H强化
硬铝超硬铝锻铝-4
能H强化a+p
D
Al合金元素含量,%
2铝合金热处理强化特点
特点:淬火加热时不发生同素异构转变。热处理强化包括固溶处理与时效处理。固溶a+β→a'
强度/硬度变化小
处理固溶度1
塑性明显↑
时效第二相从固力学性能等发生
处理溶体中析出显著变化
时效形式:人工时效,自然时效
一般“回火”用于晶型转变的淬火合金,
“时效”用于非晶型转变的淬火合金
以A1-Cu二元合金为例讨论铝合金的时效过程:(1)形成铜原子富集区
铜富集区晶体结构与基体同,
称G.P.区但产生了共格应变区
强度、硬度↑。G.P.呈盘状,仅几个原子层厚,室温下直径约5nm,超过200℃就不再出现G.P.区。
形成稳定的0
过渡相0形成稳定相CuAl2,
完全脱溶(0)与基体非共格
合金的强度、硬度进一步下降合金的种类不同,形成的G.P.区、过渡相以及最后析出的稳定相各不相同,时效强化效果也不一样
3形成过渡相0
θ"相转变0′是正方点阵,
成过渡相0成分接近CuAl
强度、硬度开始降完全共格
低,合金此时处于局部共格
过时效阶段。
铜原子富集区有序化
G.P.区急剧长大,0”相与基体仍然
G.P.区铜原子有序保持完全共格,具
化,形成0”相有正方点阵
点阵常数a=b=0.404nm,c=0.768nm。它比G.P.区周围的畸变更大,因此时效强化作用更大
表常用铝合金系的时效过程及其析出的稳定相合金系时效过程的过渡阶段
析出稳定相
①形成铜富集区一GP区0
Al-Cu②GP区有序化一0相
③形成过渡相0(CuAl)
①形成铜、硅富集区一GP区B
Al-Mg-Si②形成有序的β′相(Mg2Si)
①形成铜、镁富集区一GP区
Al-Cu-Mg②形成过渡相SAlCuMg
①形成铜、锌富集区一GP区M
Al-Mg-Zn②形成过渡相M(MgZn2)
3影响时效强化的主要因素
规律:淬火T越高,淬火冷却V越快,转移t越短,过饱和程度越高,时效强化效果也越大
固溶
处理要点:在不过热过烧条件下,T高些,保温
长些。淬火冷却要保证不析出第二相。为了防止淬火变形开裂,一般采用20~80℃水冷却
时效温度:对一定合金,有最佳时效温度
工艺时间:在一定时效温度下,有最佳时效时间。方式:单级和多级时效。高强合金常用分级时效
4合金化条件
合金元素能有限固溶;固溶度随温度降低而大为减小;析出相的强化作用大。时效温度130℃
140GP
04.5%
120
100
强化教化出要
0%
804.5%w(Cu)
3.0%
604.0%
时度2.0%
3.0%
时效温度与硬度关系曲线40
2.0%
0.110
100
时效时间
130C时效时铝铜合金的硬度与时间关系
2硬铝合金
成分Al-Cu-Mg系合金。2A+顺序号表示①低强度硬铝,如2A01、2A10
分类等合金;
②中强度硬铝,如2A11等合金;③高强度硬铝,如2A12等合金,2A12是使用最广的高强度硬铝合金
8.2变形铝合金
四位字符体系:牌号的第一位数字表示组别,2×××~8×××表示。后两位数字是区别同一组不同的铝合金。第二位字母表示原始合金的改型情况,A表示原始合金;B~Y表示原始合金的改型合金。如2A06表示主要合金元素为铜的6号原始铝合金。
1、防锈铝合金
Al-Mn和Al-Mg两个合金系。用“3A”或“5A"加一组顺序号表示。具有优良的抗蚀性、焊接性和塑性。不能进行热处理强化。适合于制作焊接管道、容器、铆钉、各种生活用具以及其它冷变形零件。
思考题:
直接析出稳定相在热力学上是有利的,但为什么不是直接析出稳定相?
时效处理后具有高硬度、强度,优良的加工性和耐热性,但塑性、
分类韧性低,耐蚀性差。含Cu、Mg低,强度较低而塑性高;反之,强度高而塑性低。
强化相θ(CuAl2)、金属间化合物S
(CuMgAl2)是强化相,S相最高
①要严格控制淬火温度。
如:牌号正常淬火温度过烧温度
2A02495-505510~515
热处理特性2A10
510~520540
2A12495~500507
②转移时间尽量短<30",航空件<15";③冷速要快,热水淬;
④常用自然时效。
应用飞机大梁、空气螺旋桨、铆钉及蒙皮等
660.97
650
600乙
L÷
650L÷a+CuAl2507/+S
500
450a÷S+CuAlz
+CuAl2(6)
400
3501
48121620242832
w(Cu)%
图铝铜镁三元合金垂直截面
8.3铸造铝合金
铸造铝合金应具有高的流动性,较小的收缩性等良好的铸造性。共晶合金应最佳,但容易有大量硬脆化合物,使脆性增加。因此,实际使用的铸造合金并非都是共晶合金。
铸造铝合金的牌号用ZL+三位数字表示。第一位数字是合金系别:1是A1-Si系合金;2是A1-Cu系合金;3是Al-Mg系合金;4是A1-Zn系合金。第二、三位数字是合金的顺序号。例如ZL102表示2号A1-S系铸造合金。
3超硬铝合金
Al-Zn-Cu-Mg系。7A+顺序号表示
成分室温强度最高,500~700MPa,缺点
性能是耐蚀性差,疲劳强度低,<120℃的温度下使用。
强化相:MgZn2Al2Mg3Zn3
T范围较宽,一般为450~480℃,
特点人工分级时效:先在120℃时效3小时,
应用第二次在160℃时效3小时,形成G.P.区和少量的n相,达到最大强化状态。应用:飞机工业中重要的结构材料。
1、铝硅系铸造合金
流动性最好,比重轻,铸造收缩率小;焊接性、耐蚀性优良,致密度较小。共晶组织中硅晶体呈粗针状或片状,有少量块状初生硅。常经变质处理塑性较低,需要细化组织。
常用合金:ZL102和ZL104等制造致密度要求不高、形状复杂铸件。如ZL105→工作在<250℃的耐热零件,ZL111→形状复杂的内燃机汽缸等。
4锻铝合金
Al-Mg-Si-Cu系合金。用6A或2A加顺序
成分号表示。常用的合金有6A02、2A14等
性能具有优良的锻造性能,力学性能与硬铝
相近,但热塑性及耐蚀性较高
主要强化相是Mg2Si。Mg2Si具有自然
特点时效倾向,淬火后应立即人工时效。
应用主要用做航空仪表中形状复杂、强度要
求高的锻件。
(a)未变质处理250×(b)变质处理100×
图ZL102变质处理前后的组织形貌
2铝铜铸造合金
铝铜铸造合金的主要强化相是CuAl2。最大特点就是耐热性高,但耐蚀性差。共有三种牌号:ZL201、ZL202、ZL203。
ZL203,4~5%Cu
Cu1常用,铸造性较差
热强性↑<14%Cu
脆性↑ZL202,9~11%Cu
铸造性好,耐蚀性↓
5铸造铝合金的热处理
除ZL102外,其它合金均能进行热处理强化。
①为↓变形或过热,最好在350℃以下热处理特点低温入炉,随炉缓慢加热。
②
T瘁高一些,t保长一些,15~20小时
③淬火介质一般用60~100℃的水。
④
如需时效,一般采用人工时效。
4铝锌铸造合金
锌固溶强化,极限溶解度为31.6%,不形成金属间化合物。固溶13%Zn,在冷却时不发生分解,→固溶强化↑。强度较高,是最便宜的铸造铝合金。其主要缺点是耐蚀性差。
常用ZL401。制作工作温度在200℃
应用以下,形状复杂的汽车及飞机零件、医疗机械和仪器零件。
3、铝镁铸造合金
比重轻,强度和韧性较高,优良的耐蚀性、切削性和抛光性。
特点熔点低→热强度较低,工作T<200℃
结晶温度范围较宽,故流动性差,形成疏松倾向大,其铸造性较差。
ZL301、ZL302二种牌号。
应用制造承受冲击振动载荷和耐海水或
大气腐蚀、外形简单的重要零件
小结
铝合金没有同素异构转变。
铝合金热处理为固溶处理和时效强化。铝合金时效基本过程是强化相的析出过程。各个阶段的强化效果也不同。
正确制定合金的固溶处理工艺,是保证获得良好时效强化效果的前提。
工业纯铝:合金化
固溶强化基本过程:
密度2.72。导细化组织强化
GP→0"→0'→0
电、导热性好Cu、Mg、
时效强化条件:Me能溶入a;
抗蚀性好,塑Zn、Si、Mn
第二相强化随T↓而固溶度↓↓
性高析出相强化作用大。
L+aL
α
防锈铝合金
只能变形强化铸造铝合金:
Al-Si,ZL104
Al-Mg Al-a+β
Mn系。Al-Cu, ZL201
LF5Al-Zn, ZL402
Al-Mg,ZL301
AlMe
可热处理强化
特点:无同素异构转变;固溶处理和时效强化
超硬铝:如LC4硬铝:LY12
锻铝:如LD5
Al-Zn-Mg-Cu系Al-Cu-Mg系.
Al-Mg-Si-Cu系
性能特点:强度高,性能特点:强度比较高,耐
工艺特点:锻造性好
耐热性、抗蚀性差。热性好,抗蚀性差。
热处理:采用人工时
热处理:淬火温度较热处理:淬火温度窄,要求效
宽冷速快,转移时间短
第漳铜合金
铜及铜合金是人类历史上使用最早的金属材料之一。由于铜具有优良的性能及美丽的色泽而被广泛用于电缆、电器核电子设备的导电材料、各种热交换器的传热材料、建筑材料以及装饰品等。
随着科学技术的发展,使用范围不断扩大,如大规模集成电路、超导电线、超导电磁体、磁力悬浮铁路核聚变装置以及形状记忆合金等方面都有应用。
一、普通黄铜
<36%Zn的合金为单相a黄铜,36~46%Zn合金为a+B双相黄铜,易热加工,为热加工黄铜。
随Zn↑,导电导热性↓,线胀系数1<30%Zn时,随Zn↑,强度和塑性↑,
性能达到最高值;
>32%Zn时,由于出现脆性β'相,塑性↓,强度↑,在45%Zn时达最大值
9.1黄铜
黄铜是以锌为主要元素的铜合金。
铜锌二元合金→普通黄铜;铜锌+Me→特殊黄铜普通黄铜:H62表示含62%Cu、38%Zn
特殊黄铜:用“H"加主添元素的化学符号再加铜
牌号表示方法含量和添加元素的含量表示。
如HMn58-2表示58%Cu、2%Mm
铸造黄铜:用“Z"再加铜化学符号和主添元素化学符号及含量表示。
如ZCuZn38:Cu为基体元素,Zn为主要合金元素,38为锌的平均质量分数
上左:编钟上右:永乐大钟下左:越王勾践青铜剑
CCTV
COM
1200L
1000903
32.5+
β'βBY
4970
800a
ar50
60035
CuZn
456
390
400a145.9B0-621-30
200a7
10
Cu60
010305070
w(Zn)96u(Zn)%
铜锌二元相图铜端铸态黄铜性能与锌含量关系
黄铜有良好的铸造性能,即流动性高,偏析倾向小,适用于铸造复杂和精致的铸造制品。H96、H90等:有金色黄铜之称。导热性、抗蚀性好。用于冷凝器、散热器和工艺品等H70、H68:为三七黄铜。强度较高,塑性好,用于冷冲压、深拉伸的形状复杂件。大量用于弹壳,所以也称为弹壳黄铜。铝?
H62:强度高,塑性也好,常、用于水管、油管,也称为商业黄铜。
二、特殊黄铜
锡黄铜
锡黄铜在普通黄铜中+0.5~1.5%Sn,↑强度和硬度及耐蚀性,改善切削加工性。
锡黄铜主要以管、棒、板材大量用于舰艇制造工业,如冷凝管、船舶零件、船舰焊接件的焊条等,故有海军黄铜之称。
硅黄铜
硅黄铜加入1.5~4.0%Si,能11黄铜在海水中的耐蚀性以及抗应力腐蚀能力,改善铸造性和焊接性。HSi80-3硅黄铜显微组织为a+β,主要用于舰船制造和其它工业中的耐蚀零件和接触蒸汽的配件等。
镍黄铜
添加镍可扩大相区,故双相黄铜添加适当的镍可转变为单相黄铜。镍能1强度、韧性、耐蚀性及耐磨性。镍黄铜适合于冷、热加工。镍黄铜具有小的应力腐蚀破裂倾向,可用来制造海船工业的压力表及冷凝管等,还可作锡磷青铜的代用品
铝黄铜
黄铜中加入少量铝(0.7~3.5%)可在表面形成致密和牢固的AL2O3膜,↑耐蚀性。铝能细化晶粒,↑硬度和强度。但>2%AI时塑韧性。含2%A、20%Zn的铝黄铜具有最高热塑性,所以HA177-2合金得到广泛应用。
含铝特殊黄铜焊接比较困难,且有高的应力腐蚀倾向,必须进行充分低温退火加以消除。
铅黄铜
HPb74-3是单相a铅黄铜,铅呈细小质点分布在晶界;HPb59-1是双相(a+β)铅黄铜。因为HPb59-1切削性特别好,称为易切黄铜,有足够高的强度、耐磨性和耐蚀性。广泛用作钟表机芯的基础部件和汽车、拖拉机等机械零件如衬套、螺钉、电器插座等。
9.2青铜
青铜最早是指铜锡合金,含铝、硅、铍、锰
和铅的铜基合金,也称青铜。
通常把铜锡合金称为锡青铜(普通青铜),
其它称为无锡青铜(特殊青铜)
“Q”加上第一个主加元素化学符号及含量再加上其它合金元素含量。
牌号表示如QSn4-3为含4%Sn,3%Zn锡青铜;
铸造青铜:“Z"表示铸造,“Cu表示铜基体。如ZcuPb30表示铸造铅青铜,铅的平均质量分数为30%
1100
1000L
900a+1.
B+L
798
8o03.5
700ar+1
y+
L
600586
5.8520
500
400350
11.0
300
2001.3
100
Cu1020304050
(Sn)ry6图铜锡二元合金相图铜端
2铝青铜
特点强度和耐蚀最好,应用广泛。是锡青铜
的重要代用品,但铸造性和焊接性较差。↑AI,强度和硬度↑,塑性↓。当AI
铝作用>10~11%时,强度、塑性均。→由于出现了硬脆2相所致。→12%A。压力加工用铝青铜A5~7%
铝青铜应用较广泛。用于制造耐磨、耐
应用蚀和弹性零件,如齿轮、轴套、弹簧以及船舶制造中的特殊设备等
较高强度、硬度和耐磨性。
Sn↑,强度↑,当Sn>6%后,↓具伸长率;Sn>20%,出现大量δ相,合金变
性能脆,强度。因此,工业用Sn青铜的Sn含量均在3~14%之间。
Sn<7~8%的合金,有高的塑性和强度,适用于塑性加工;
含Sn>10%的合金,因塑性低,只适用于铸造用。
1、铜锡二元合金
a是Sn固溶于Cu固溶体,FCC结构;β是β电子化合物CuSn为基的固溶体;y是CuSn化合物为基的固溶体;
景δ是电子化合物Cu31Sns;
是电子化合物Cu3Sn。
锡青铜的显微组织与锡含量和合金状态有关。
3铍青铜
铍青铜是加入1.5~2.5%Be的铜合金,除Be外,还加入镍、钛、镁等合金元素。常用QBe2.5、QBe1.7。
淬火状态塑性好,可冷加工成管、棒、带材等性能特点各种型材。若经过固溶处理及冷变形后,不仅能
提高强度(可1200MPa),而且能11,
→特别适用于仪表弹簧
处理特点固溶处理和快冷是为了获得过饱和固溶体,
→时效强化。铍青铜淬火时必须严格控制加热温度。否则会产生过热和过烧。加热温度过低,富铍相不能充分溶解,↓沉淀硬化能力
小结
铜合金中固溶强化的合金元素主要是锌、铝、锡、锰、镍等。许多元素在固态铜中的溶解度随温度降低而急剧减小,如铍、钛、锆、铬等,因而它们具有时效强化效果。
过剩相强化在铜合金中的应用也较普遍。黄铜和青铜中的Sr等相均产生过剩相强化作用。
由于锌在铜中的固溶度随温度降低而增大,故黄铜不能热处理强化。黄铜常用的热处理是去应力退火和再结晶退火。此外,一般青铜也不能热处理强化,但铍青铜经过固溶处理并时效后,强化效果十分显著。
第10章钛合金
钛从实现工业生产至今才50多年,由于其密度小、比强度高、耐腐蚀等一系列优异特性,发展非常快,短时间内已显示出了它强大的生命力,成了航空航天工业、能源工业、海上运输业、化学工业以及医疗保健等方面不可缺少的材料。
二、钛合金的相变特点
1、马氏体转变
β相(bcc)→α'六方马氏体(hcp);
→a"斜方马氏体。
基本概念C:Ms室温时β相不发生M转变的合金浓度
t。:当T↓到一定温度,β相浓度↑到C时,
淬火到室温β相也不发生M转变的临界淬火温度。
C和t是非常重要的两个参数。
钛合金M是置换型过饱和固溶体,与钢间隙式M不同
LL
L
U°~BY
B
B+Y
a
Q+YQXY
α合金元素的质量分数(%)
(a)Ti-Sn(Al等)(b)Ti-V(Mo等)(c)Ti-Mn(Cr等)(d)Ti-Zr
图钛与常见合金元素间的四种典型二元相图
10.1钛合金的合金化原理
一、钛的基本性质与合金化
①有同素异构转变。a,hcp|882C|β,bcc②比强度高。p=4.51g/cm3,可保持到550~600℃③耐蚀性好。形成保护膜,耐海水腐蚀性是最好的④低温性能好。在77K下仍有良好的力学性能⑤导热系数低。比铁低4.5倍,易产生热应力
主要合金元素有A1、Zr、V、Mo、Mn、Cr等
2相的形成
β稳定型钛合金的成分位于临界浓度Ck附近时,淬火时除形成a'或βr外,还能形成淬火相,用q表示。
q是六方晶格,与β相有共格关系。…相形性质状与Me原子半径r有关,r与钛相差较小的合金,
相是椭圆形,△r相差较大时为立方体形
相硬而脆,虽↑↑强度、硬度和弹性模量,但塑性急剧↓。一般情况下,相是有害组织,在热处理时都要避开它的形成区间。加A1能抑制相的形成→大多数工业用钛合金都含有A1
3亚稳定相的分解
淬火形成的α'、α"、ω和
βr相都是不稳定的最终产物
都是平衡
β共析分解产物是
α+β相
型的α+TixMy化合物
(1)过冷βr相分解;
各种亚(2)马氏体分解,钛合金α'、a"在300~
稳相分400℃发生快速分解,在400~500℃回火时
解过程→弥散度高的a+β相混合物,弥散强化。
(3)相的分解
10.2常用钛合金Ti合金按退火组织可以分为:a钛合金,以TA表示;β钛合金,以TB表示;a+β钛合金,以TC表示符号后面的数字表示顺序号。
2α钛合金
含4~6%的β稳定元素→α和β都有较多量。+aβ元素→α和β同时强化。
合金化特点a+β合金性能主要由β相元素来决定。
α相元素主要是铝,<6~7%→以免生成a2而韧性。另补加少量中性元素锡和锆。β元素选择较复杂。+Mo和V等,再适当+少
量Mn和Cr或微量Si。
a+β钛合金力学性能变化范围较宽,可适
性能特点应各种用途,约占航空工业使用的钛合金70%
以上。目前国内外应用最广泛的a+钛合金是Ti-A1-V系的Ti-6A1-4V,即TC4合金。
1、α钛合金
主要Me是Al和Sn,固溶强化:+1%Me,强度135~70MPa
A1在α相中固溶度很大,耐热性(<500℃)
A作用特点但A1>6%后→与α共格有序相a(TiAl)
a2是硬而脆中间相,对合金塑韧性不利。
Al大于25%后,则出现Y相(TiAl)
一般工业用钛合金AI含量很少超过6%。
α钛合金使用温度500℃。
a钛合金不能热处理强化,退火或热轧态
下使用。TA7是应用最多的一种。应用特点
TA4~TA6是Ti-Al系二元合金
α钛合金高温性能好,组织稳定,焊接性好是常用耐热钛合金,但常温强度低,塑性不高
各类合金特点a+β钛合金可热处理强化,常温强度高,中温
的耐热性也不错,但组织不够稳定,焊接性差β合金塑性加工性好,合金浓度适当时,通过热处理可获得高的常温力学性能,是发展高强度钛合金的基础,但组织不够稳定,冶炼工艺复杂应用程度:α+合金>α合金>β钛合金
3β钛合金
β钛合金是发展高强度钛合金潜力最大的合金。
合金化特点:加入大量β稳定元素。热处理热处理特点:室温为单相组织,经时效可↑↑
特点强度。淬火态下能冷成型→进行时效处理。
强韧性优于a+合金,具有良好的焊接性和
性能压力加工性。缺点是β元素浓度高,密度↑,易
特点偏析,性能波动大。β相元素多是稀有金属,价
与应格↑,>200℃使用,应用受限制用目前应用仅TB2,主要用于制造各种整体热处
理的冲压件和焊接件;如轮盘、轴类等重载荷旋
转件,以及飞机的构件等
10.3钛及钛合金的发展与应用
1、钛合金生产工艺
冶炼技术:电子束重熔技术,真空冶炼等2、钛合金的新发展
宇航工业:AlloyC是一个新型高温钛合金,使用温度
高达650℃,用于制造发动机的排气管;船舶工业:深海潜水调查船的耐压壳体。近α钛合金
Ti-6AI-2Nb-1Ta-0.8Mo和a+β钛合金TC4;民品工业:电磁烹调器具、网球球拍、高尔夫球头;
汽车工业:进、排气阀,目前仅用于赛车和运动汽车;
化学工业:反应器、热交换器、吸收塔、冷却器等;
医疗领域:骨骼整补等嵌入材料。
小结
钛合金是20世纪出现的一种新型结构材料。它具有密度小、强度高、耐高温和耐腐蚀等特点,且资源丰富,已成为航天、化工等部门广泛应用的材料
a钛合金塑性差,且不能热处理强化
β钛合金主加元素是Cr、Mo、V等元素及少量铝。主要是时效硬化,因其明显的缺点,应用受到一定的限制a+β钛合金是目前最重要的钛合金。同时加入α稳定元素和β稳定元素,使a和β同时得到强化。力学性能变化范围较宽,可以适应各种用途,约占航空工业使用的钛合金70%以上。
2、镁合金的性能特点
(1)比强度、比刚度高。
(2)弹性模量较低。受力时应力分布均匀,应力集中。在弹性范围内承受冲击时,所吸收的能量比铝高50%左右。适于制造承受猛烈撞击的零件。受冲击或摩擦,不产生火花。
(3)良好的减振性。在相同载荷下,减振性是铝的100倍,钛合金的300~500倍。
(4)切削加工性优良,切削速度↑。
(5)铸造性优良,所有铸造工艺都可采用
一、镁及镁合金的特性
1、镁的基本性质
(1)相对原子质量为24.32,密排六方晶体结构。(2)20℃时1.738g/cm3,结构材料中最轻金属。(3)体积热容最低。20℃时为1781J/(dm3·K),→重要特性是升温与降温都比其他金属快。
(4)化学活泼性高。在潮湿大气、海水等介质中会引起剧烈腐蚀,但在干燥大气、汽油等介质中却很稳定。
(5)室温塑性很差。
第1章其他有色合金
11.1镁合金
镁资源十分丰富,镁在地壳中的含量为2.35%。进入21世纪全球原镁生产能力已超过60万吨。镁及镁合金广泛应用于各个领域。镁合金具有优良的导热性、可回收性、抗电磁干扰及优良的屏蔽性能等特点,被誉为新型“绿色工程材料”,21世纪的“时代金属”。镁合金是继钢铁和铝合金之后发展起来的第三类金属结构材料。
二、镁合金成分、组织和性能变形镁合金(MB)、铸造镁合金(ZM)压铸镁合金(YM)和航空镁合金。
分类与牌号合金顺序号表示合金间化学成分差异。
如:1号铸造镁合金用ZMI表示,
2号变形镁合金用MB2表示,
5号压铸镁合金用YM5表示,
5号航空铸造镁合金用ZM-5表示
1合金元素对组织和性能的影响
主要与晶体结构、原子尺寸、电负性等因素相关(1)晶体结构因素。镁是HCP结构,但其他HCP结构元素(如锌和铍)不能与镁形成无限固溶体(2)原子尺寸因素。△R<15%时能形成无限固溶体。约一半金属元素与镁可形成无限固溶体
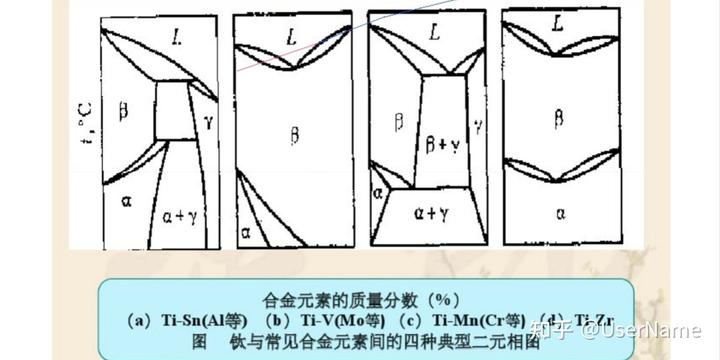
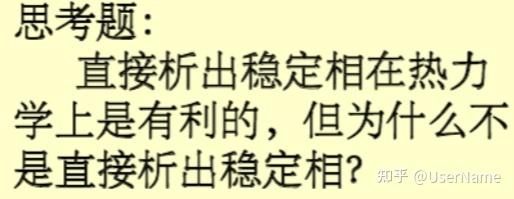
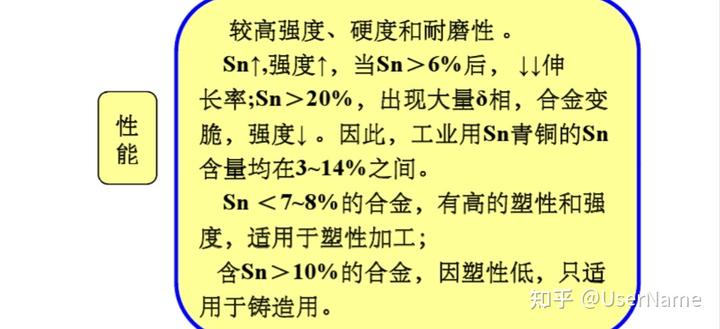
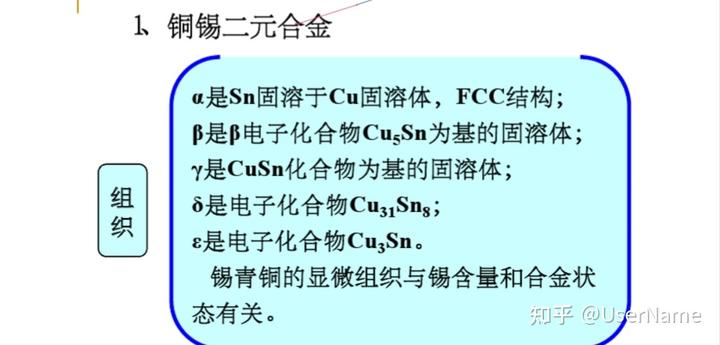
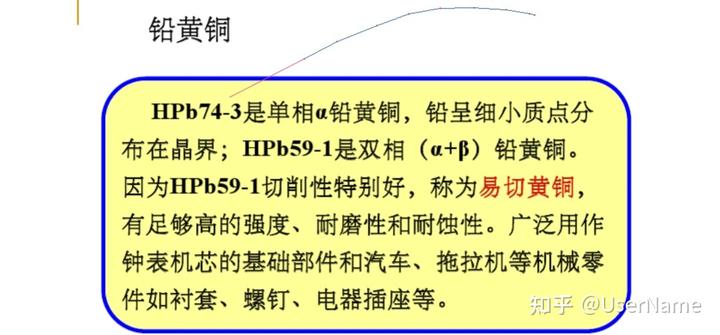
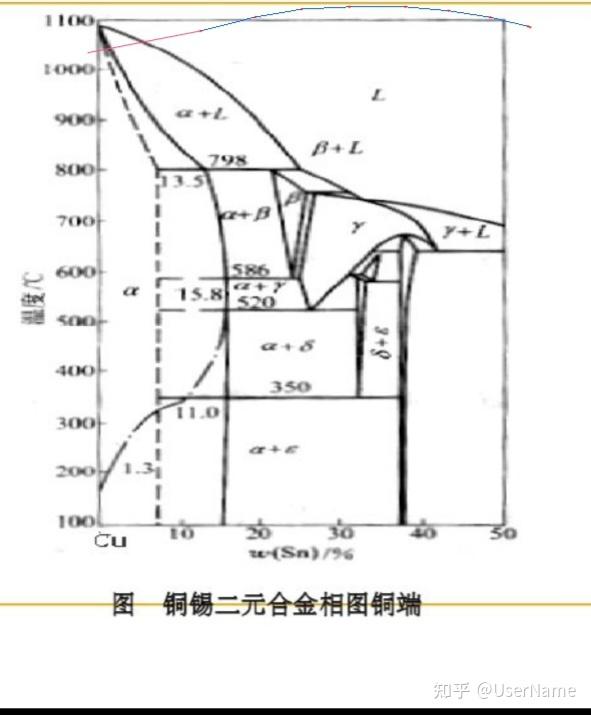
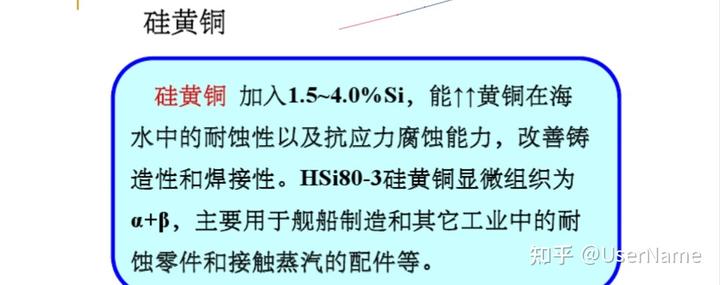
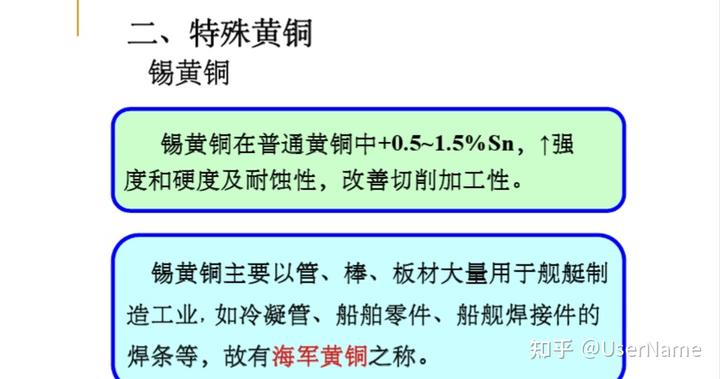
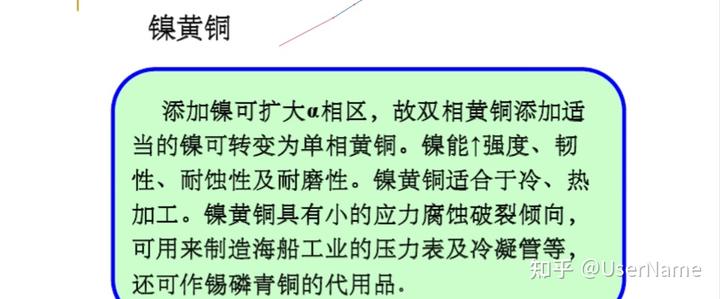
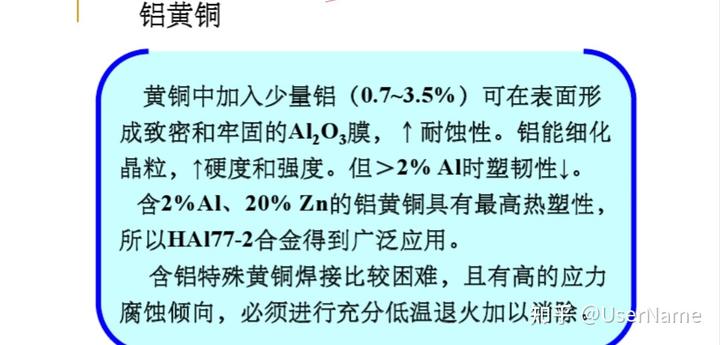
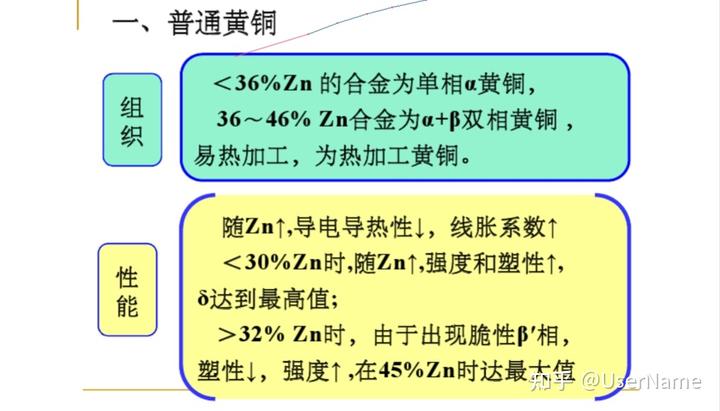
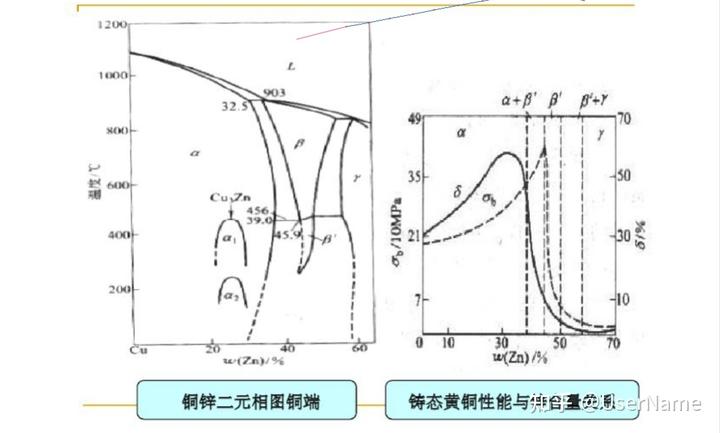
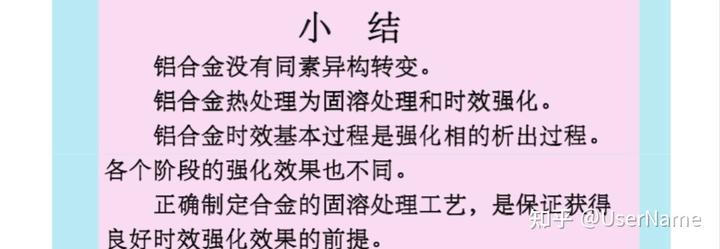
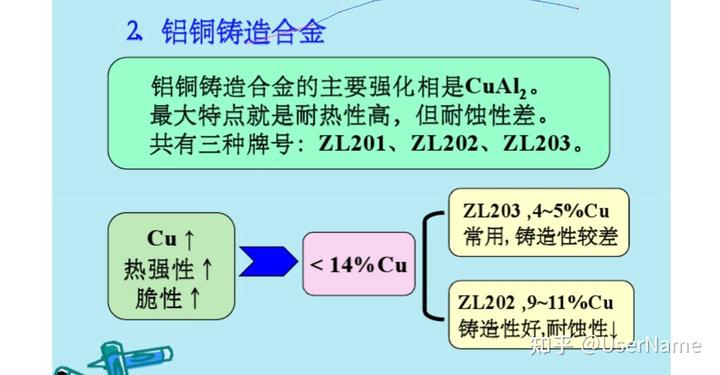
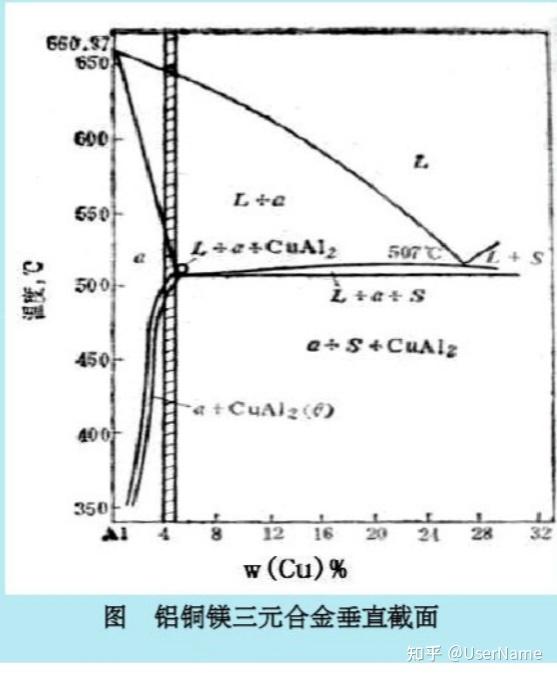
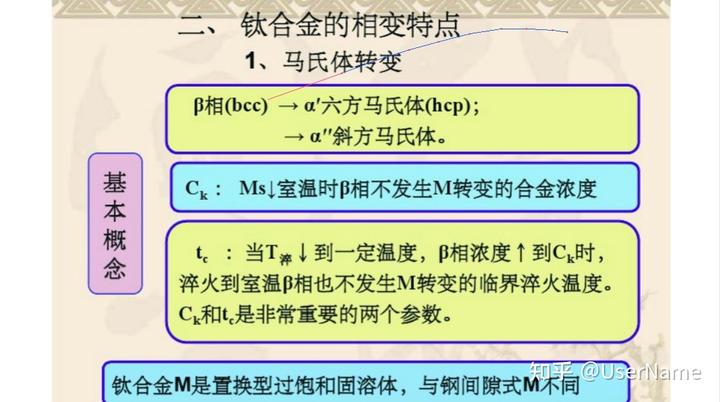
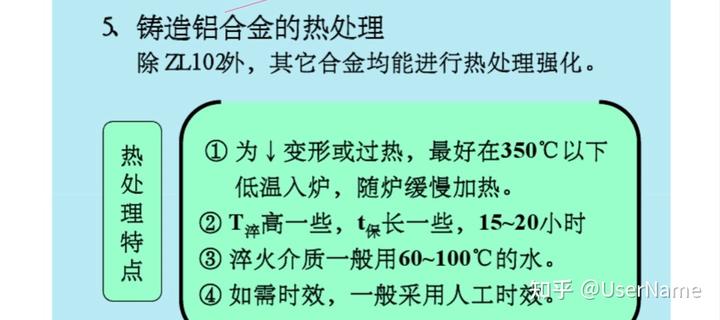
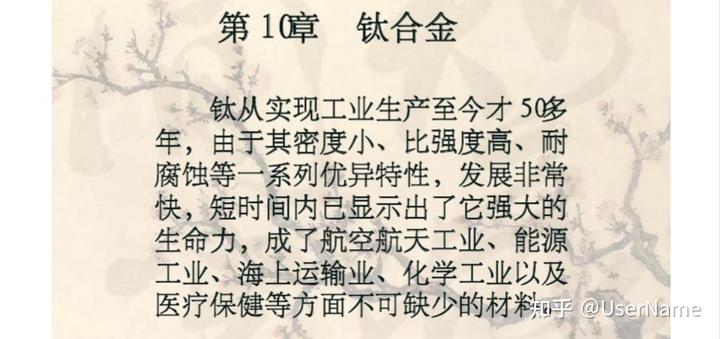
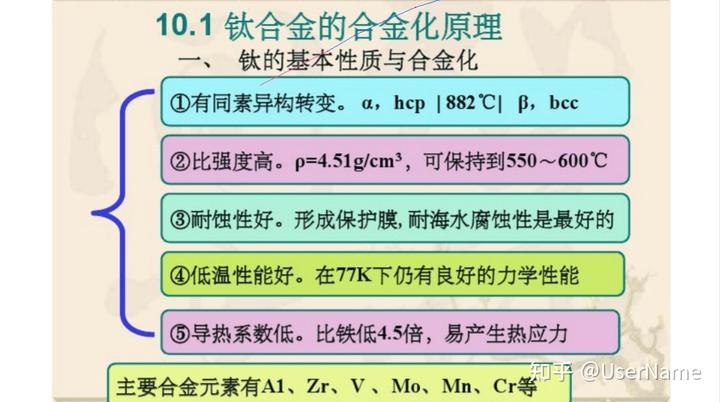
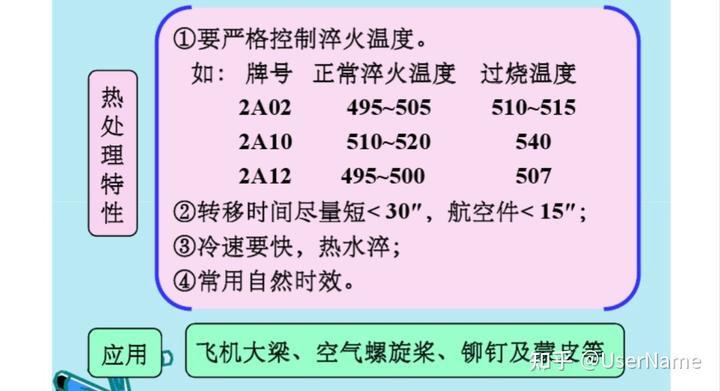
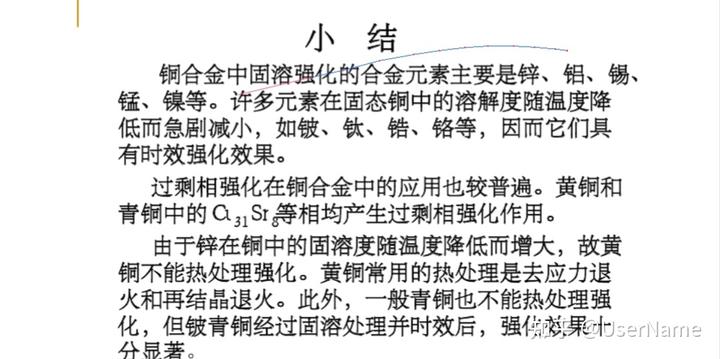
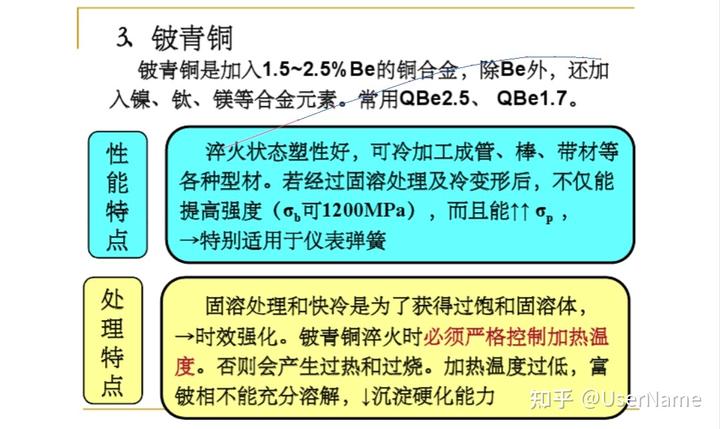
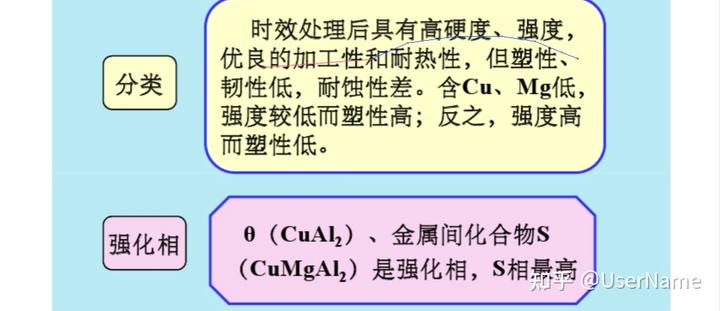
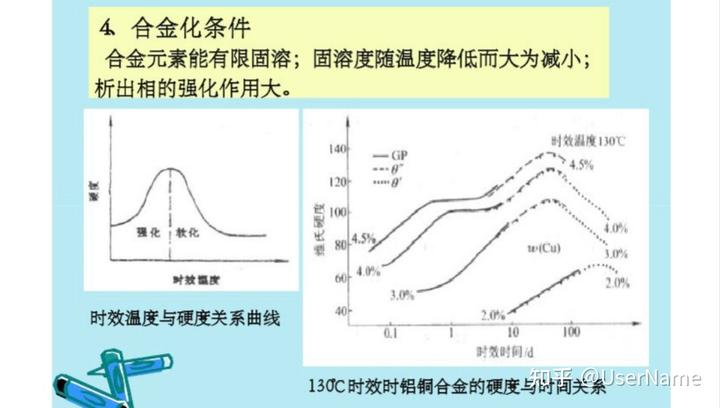
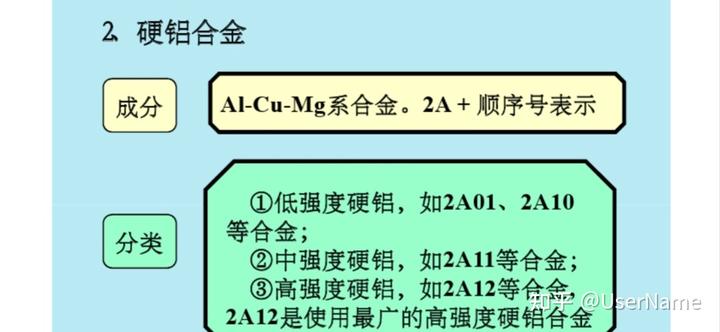
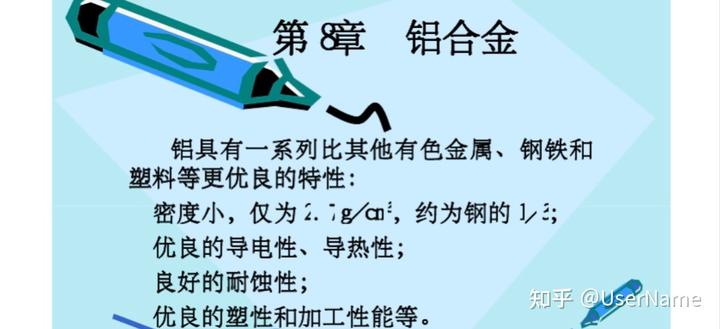
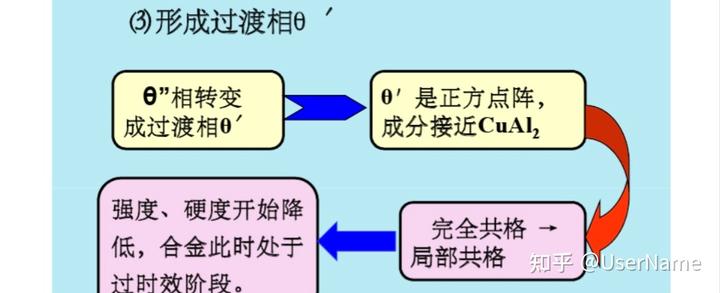
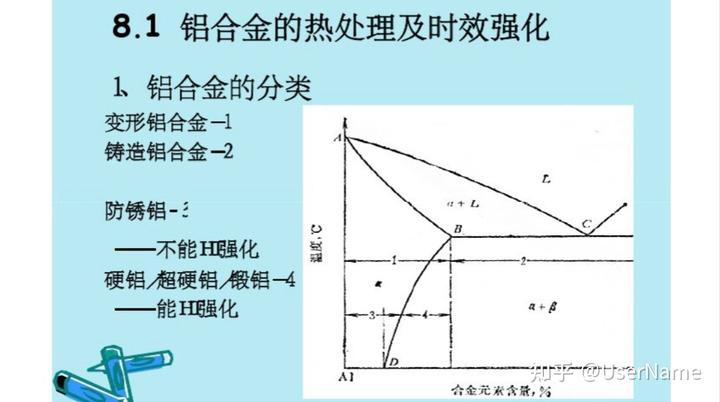
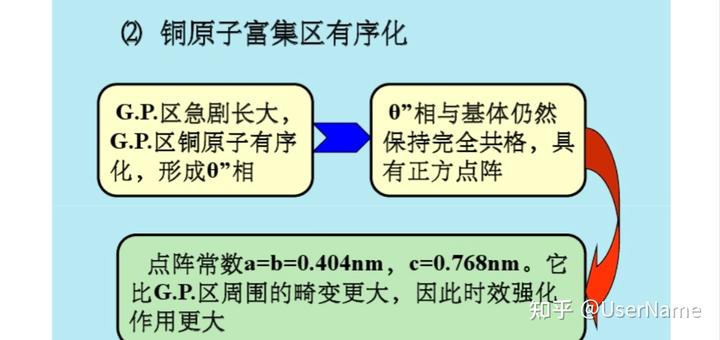
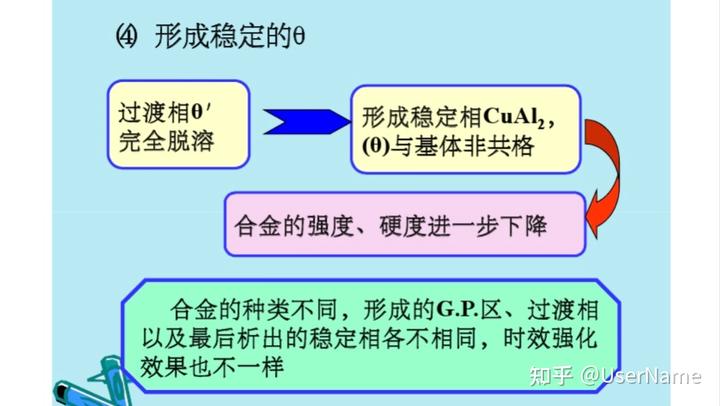
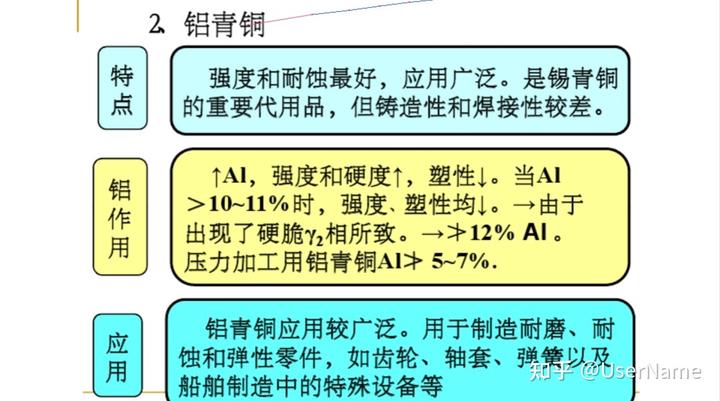
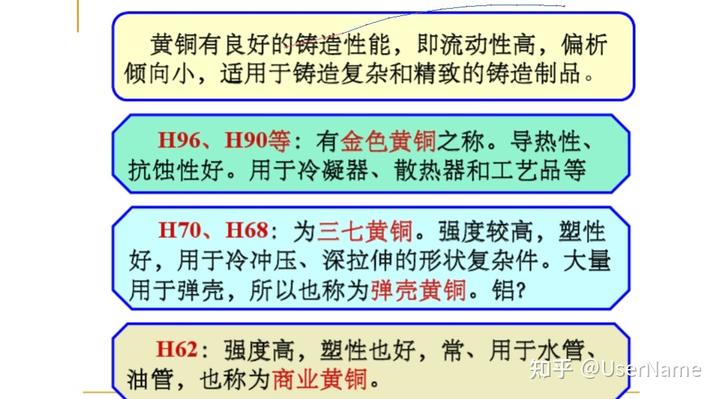
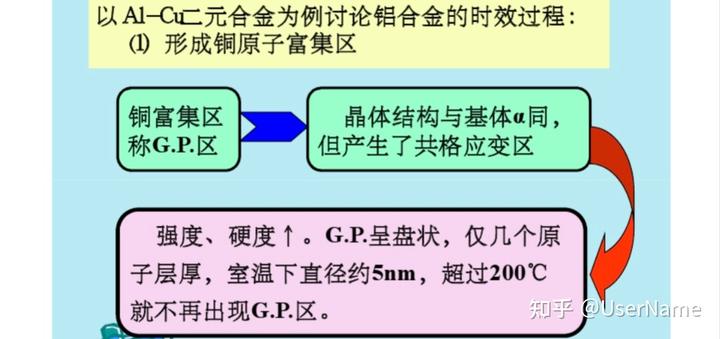
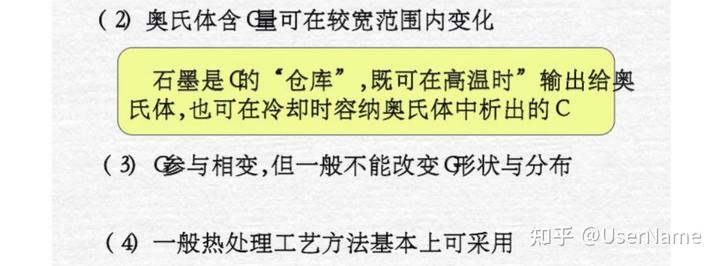
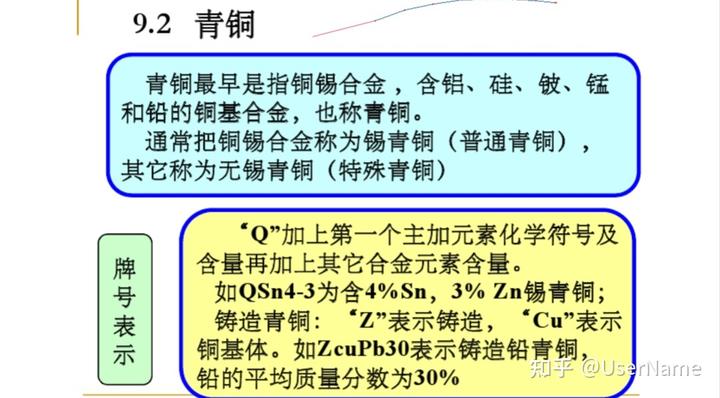
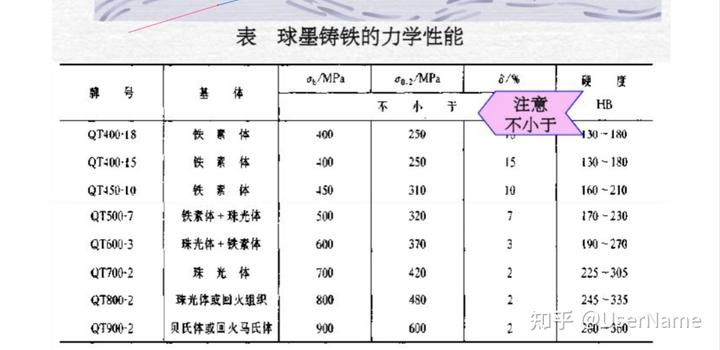
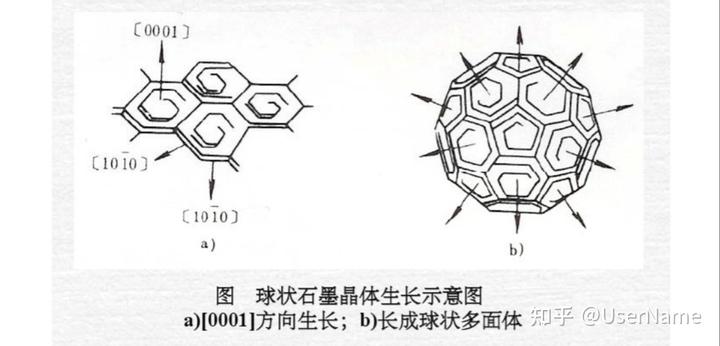
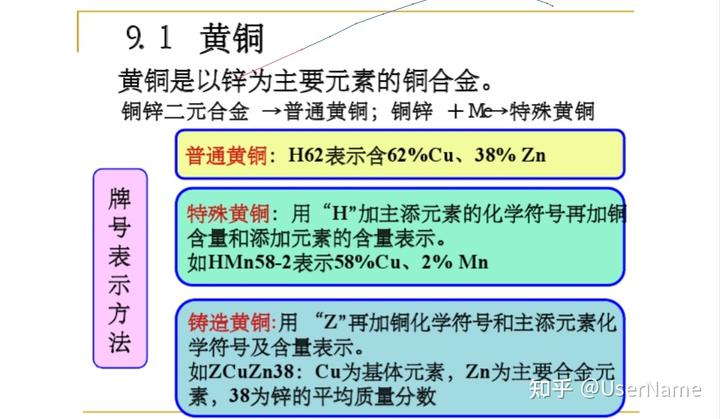
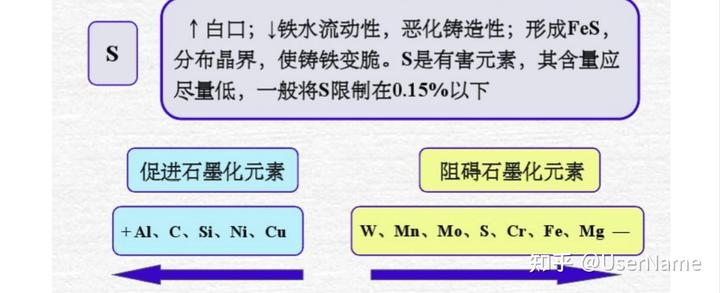
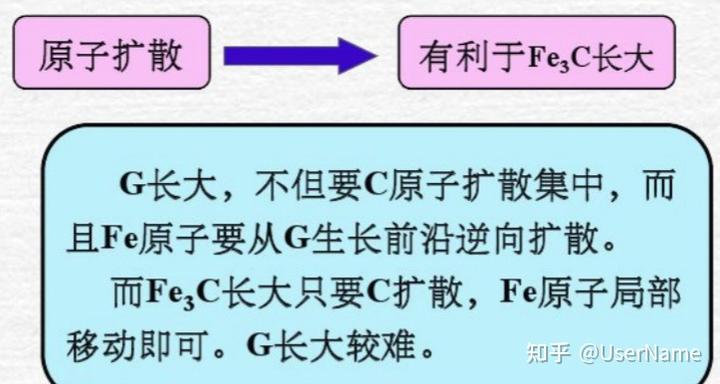
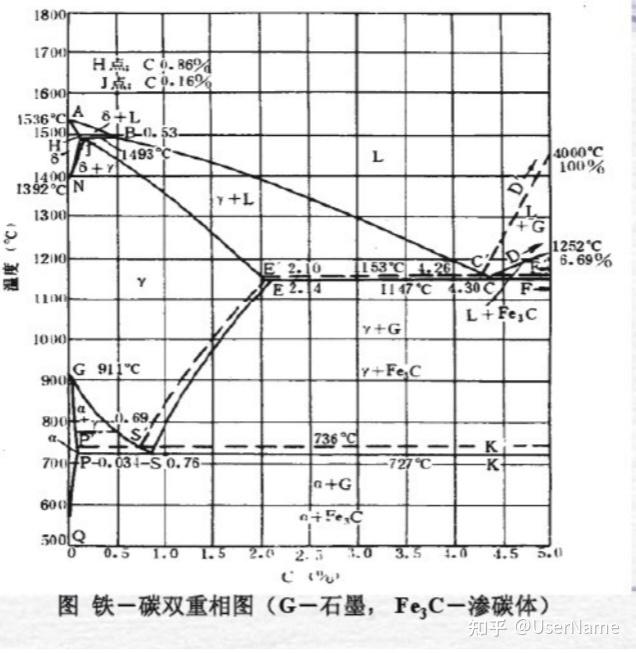
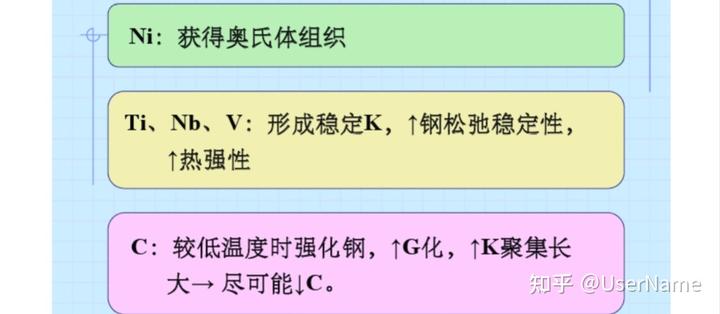
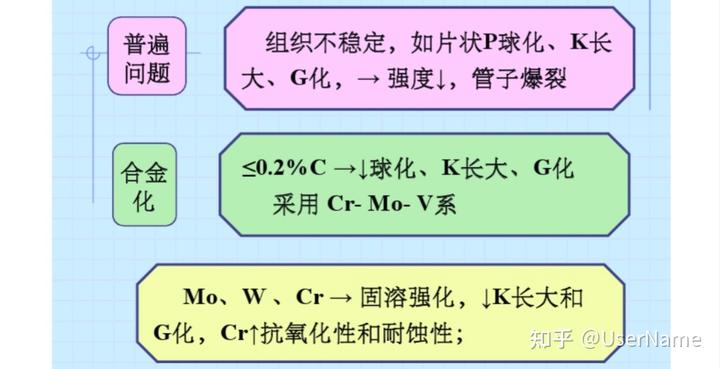
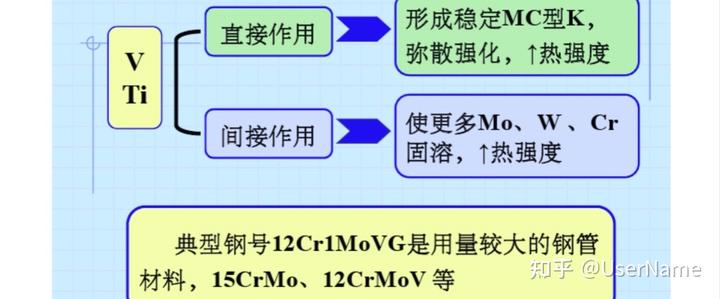
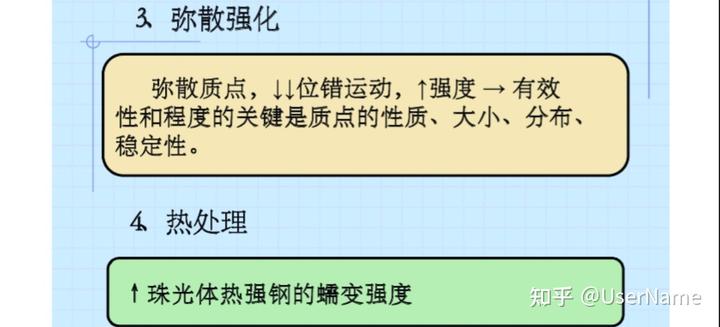
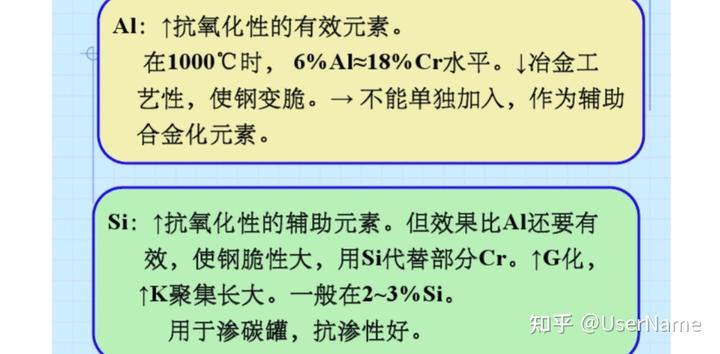
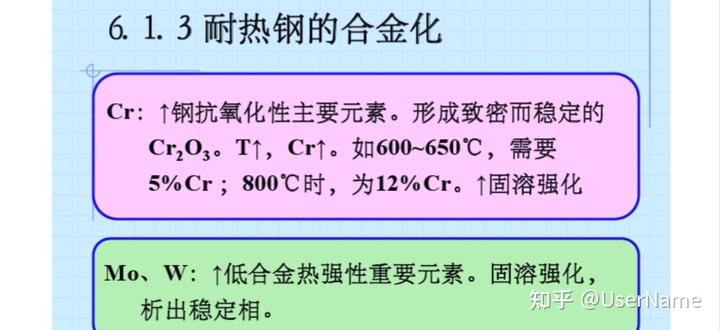
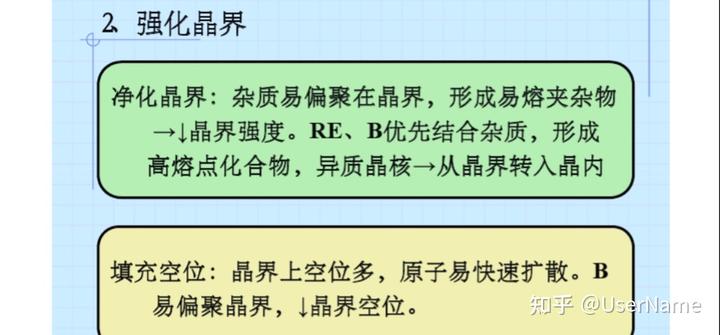
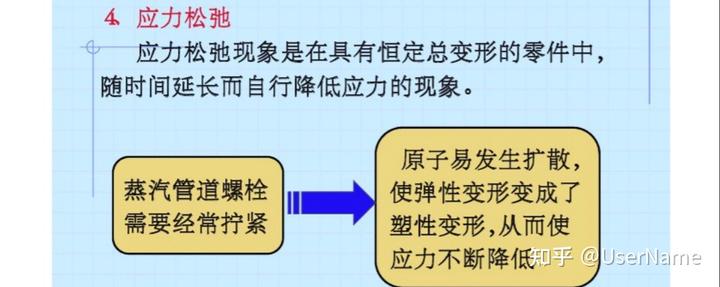
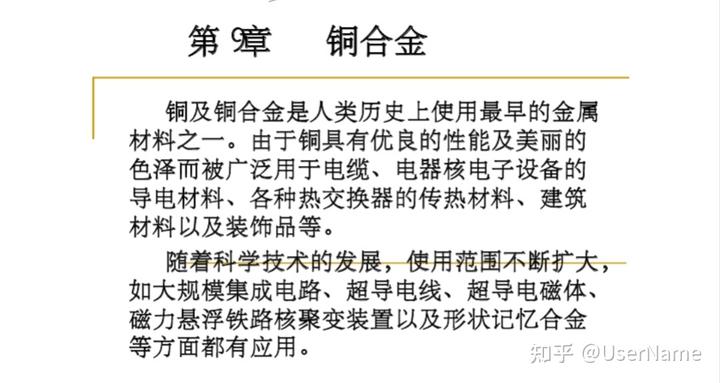
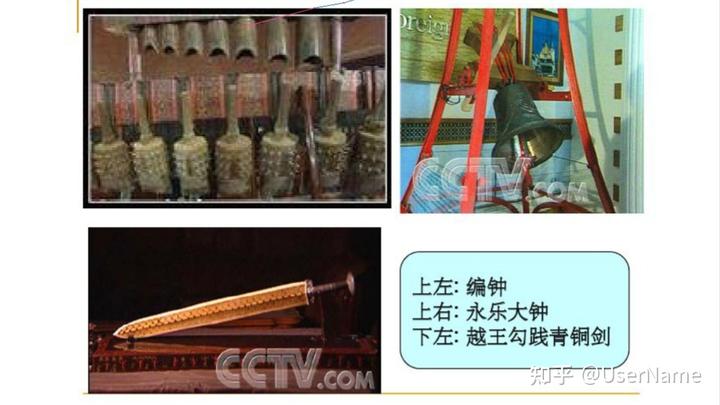
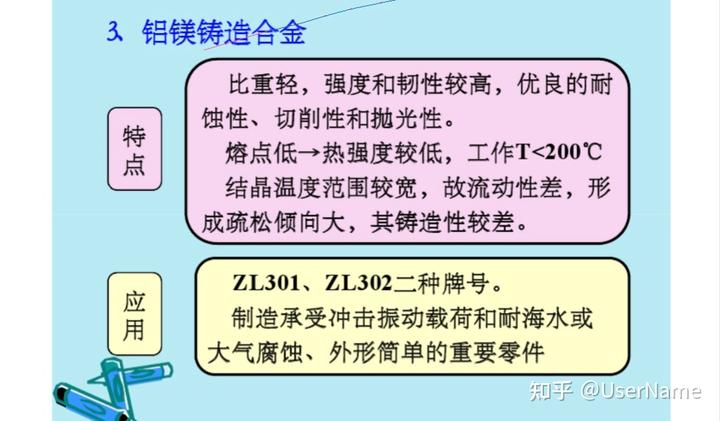
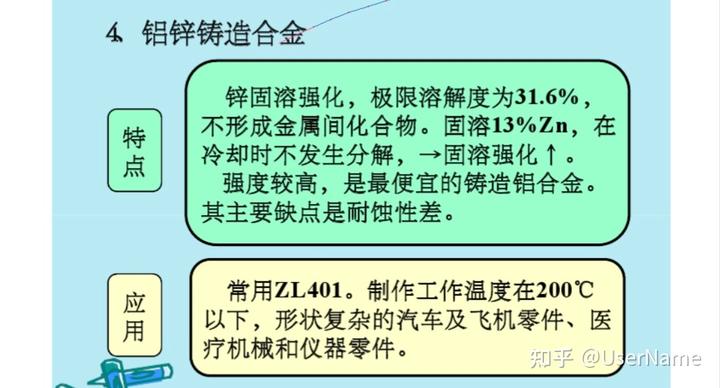
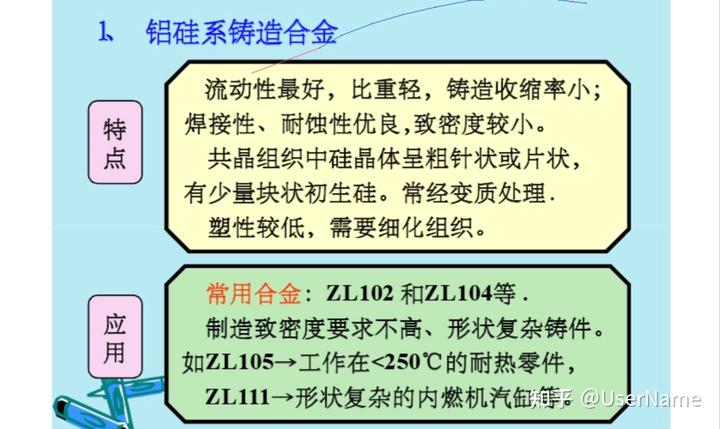
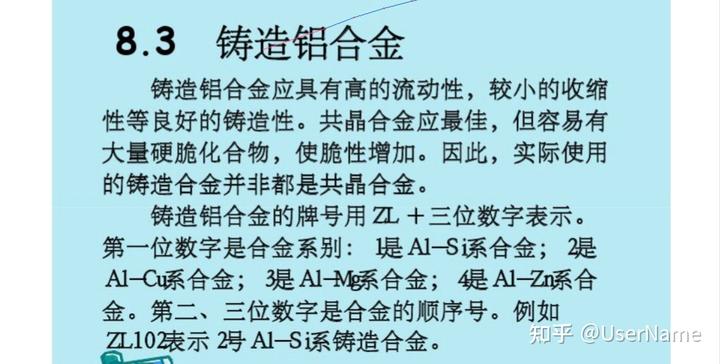
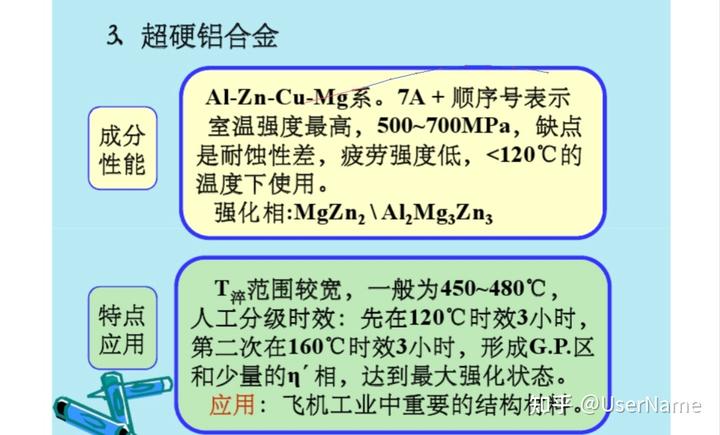
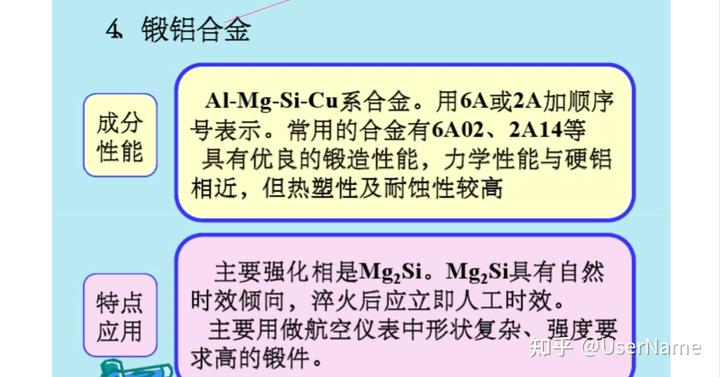
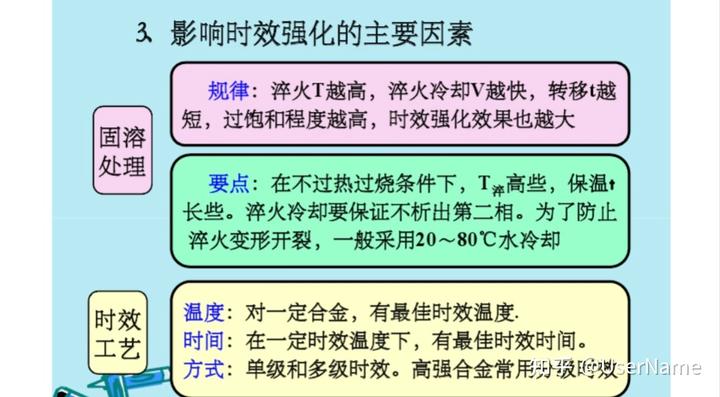
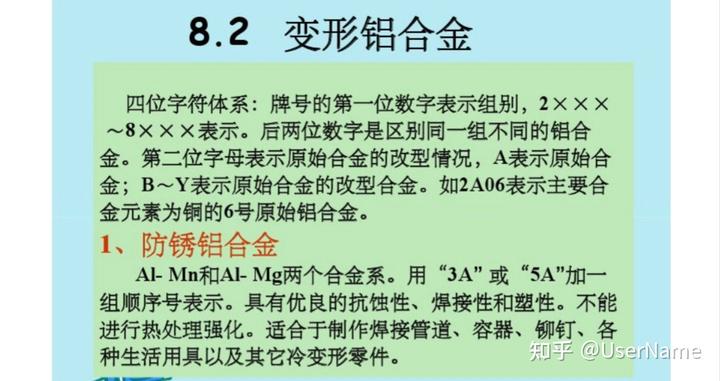
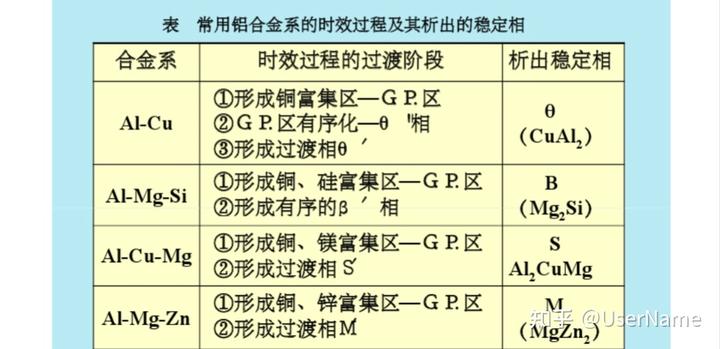
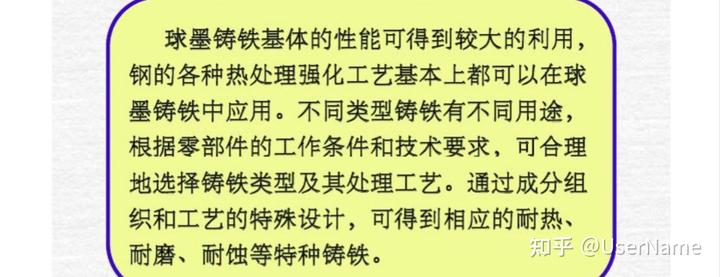
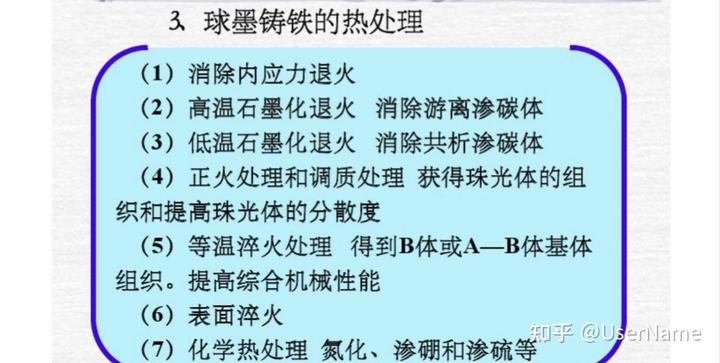
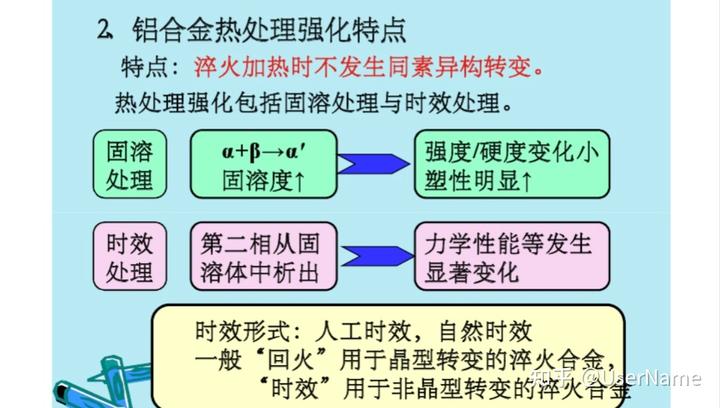
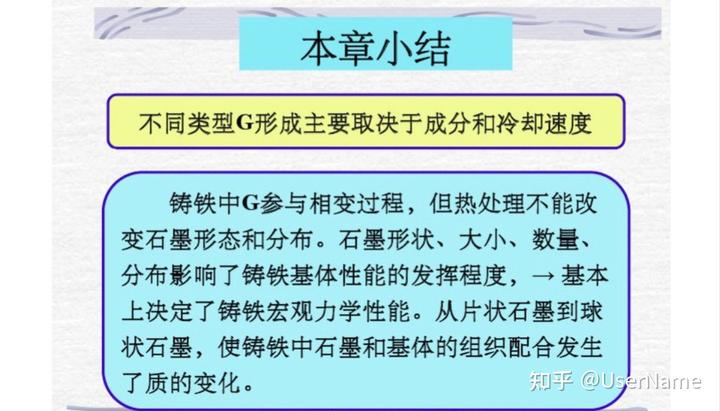
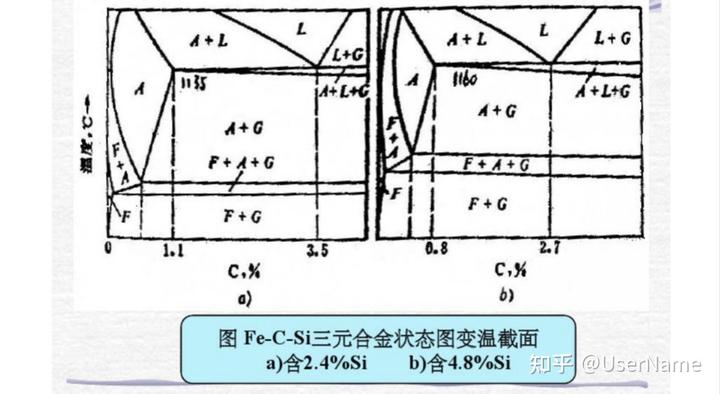
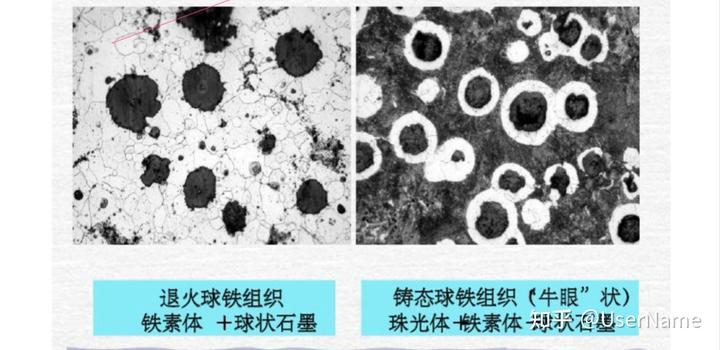
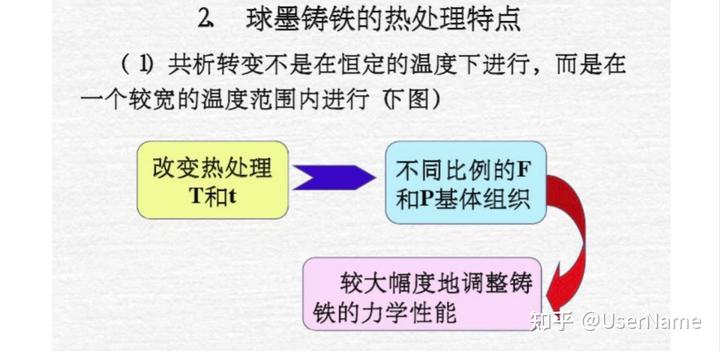
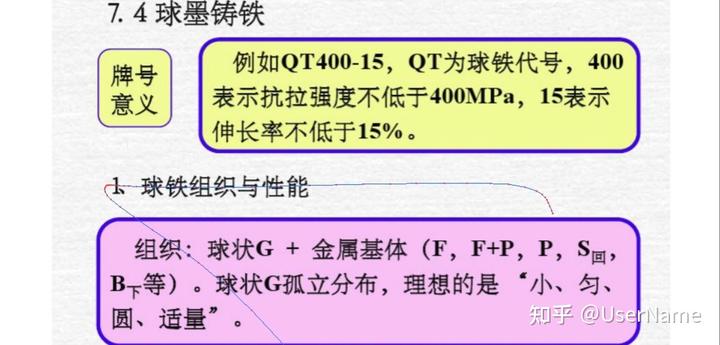
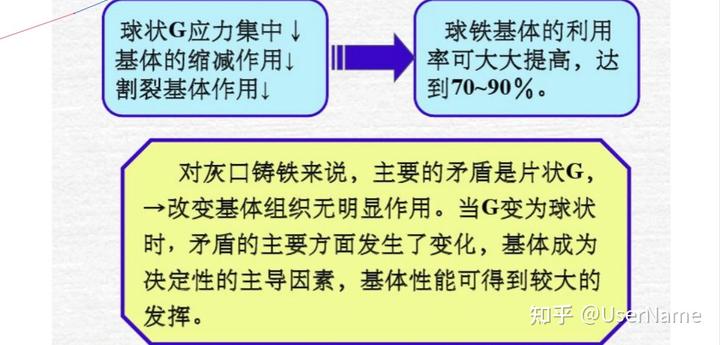
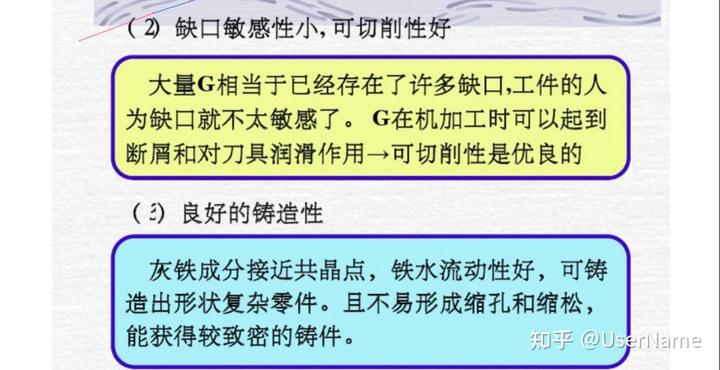
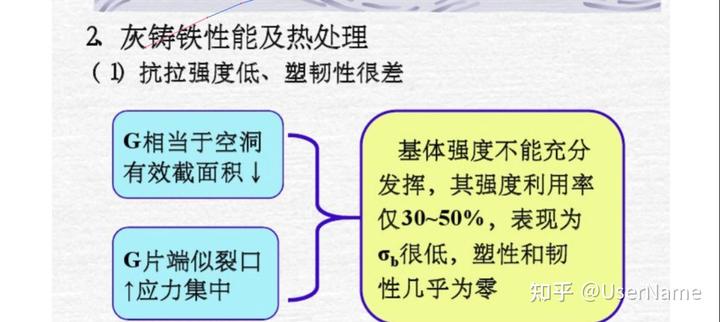
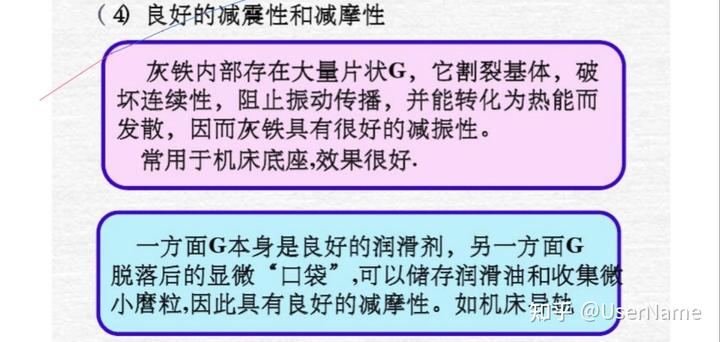
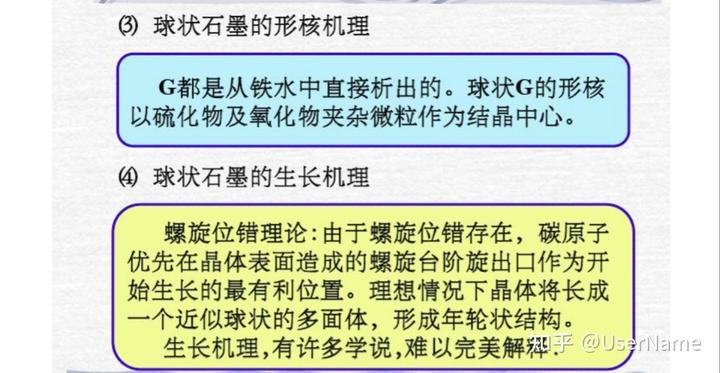
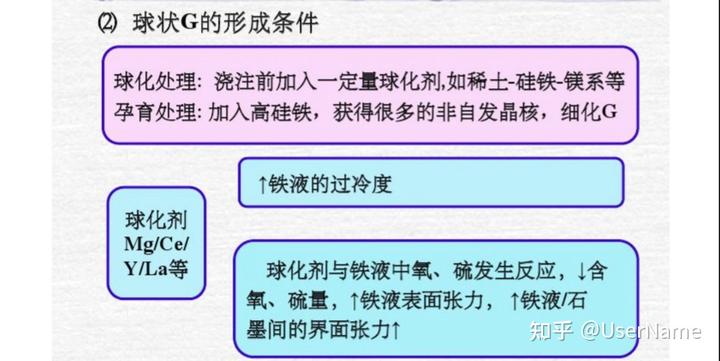
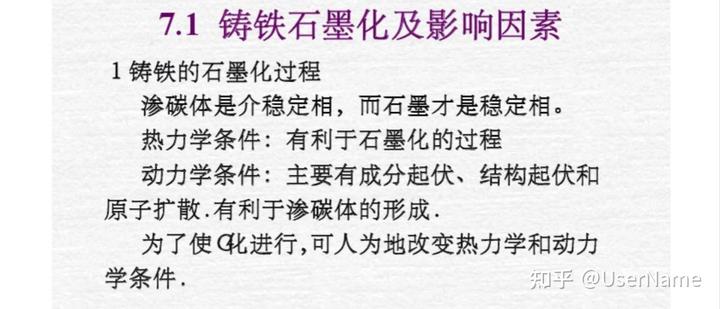
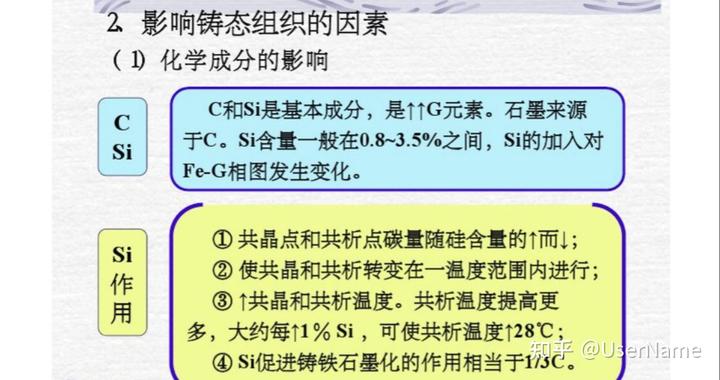
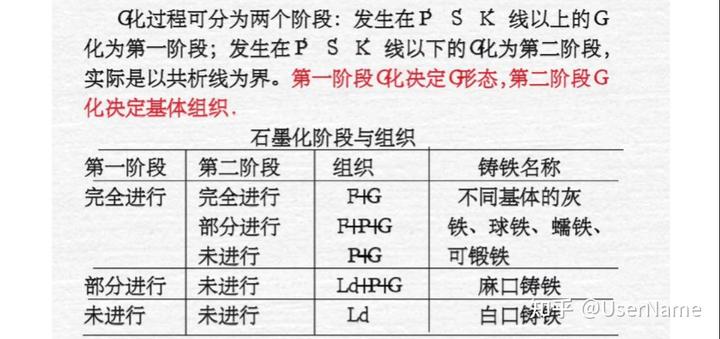
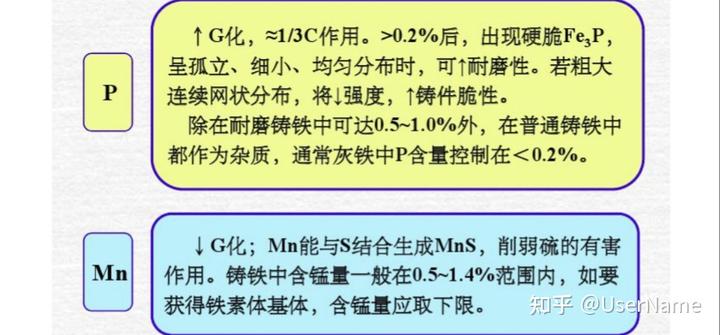
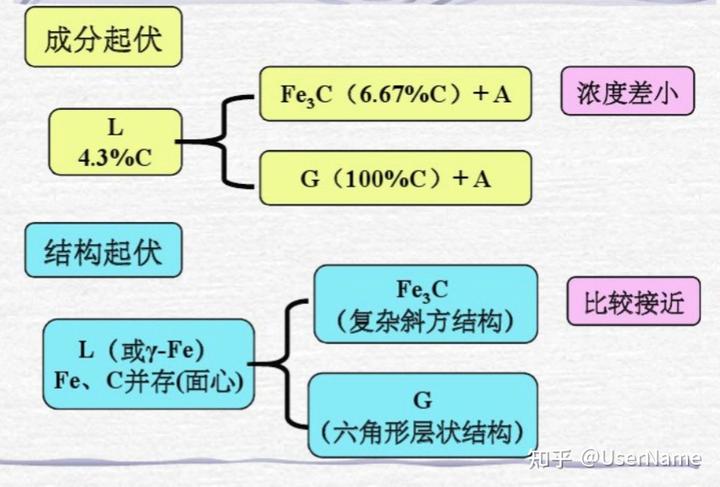
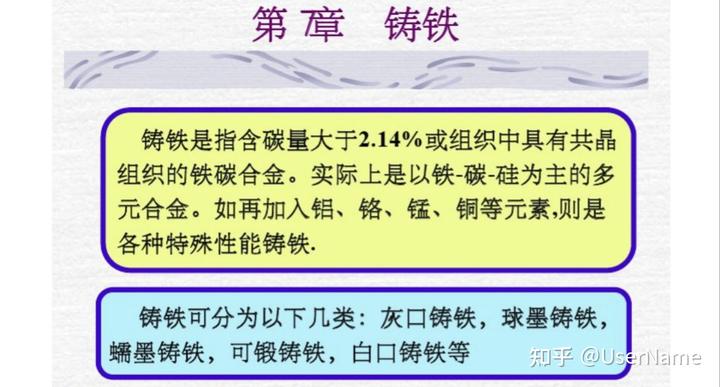
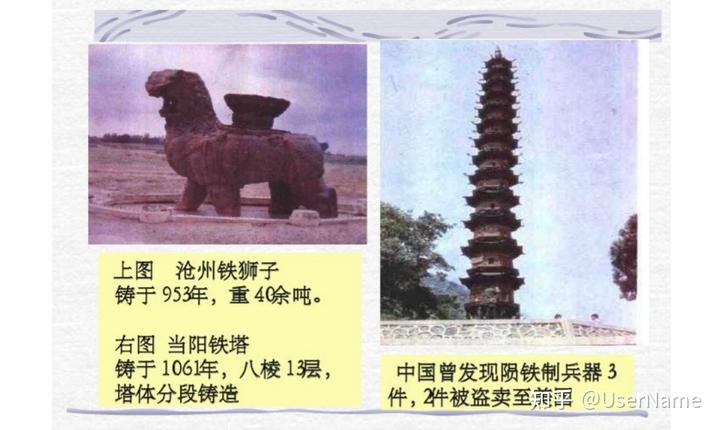
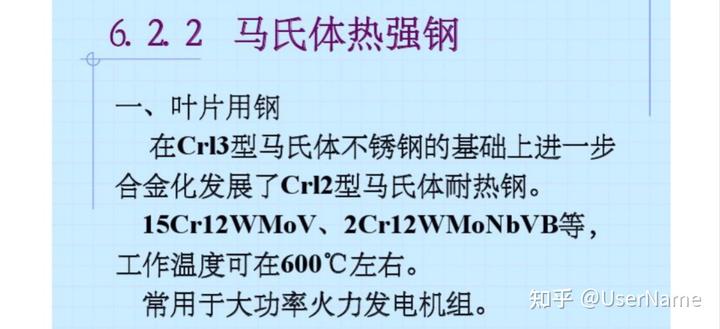
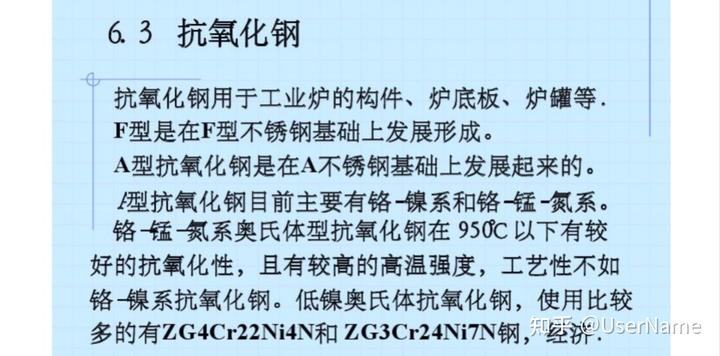
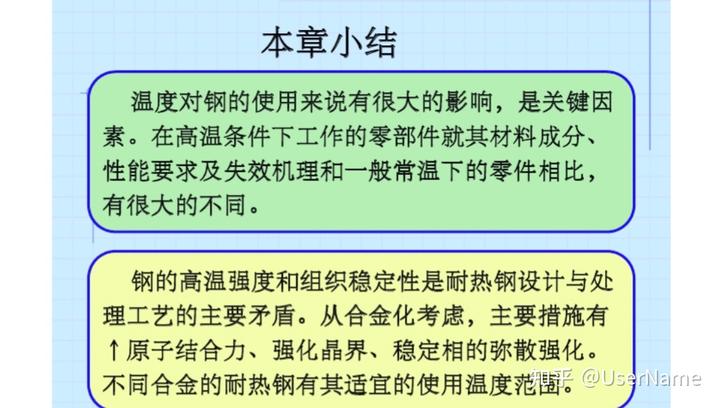
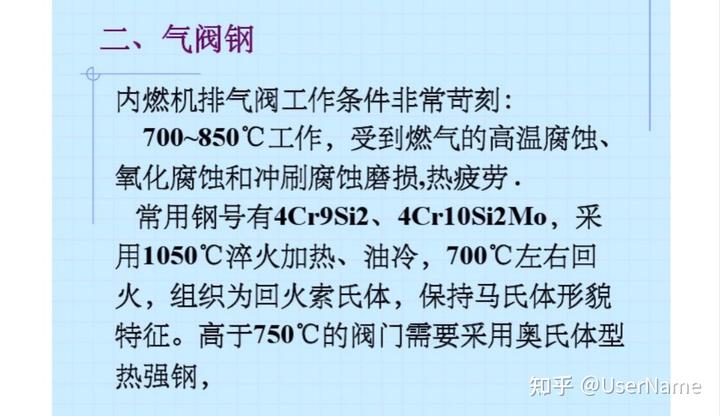
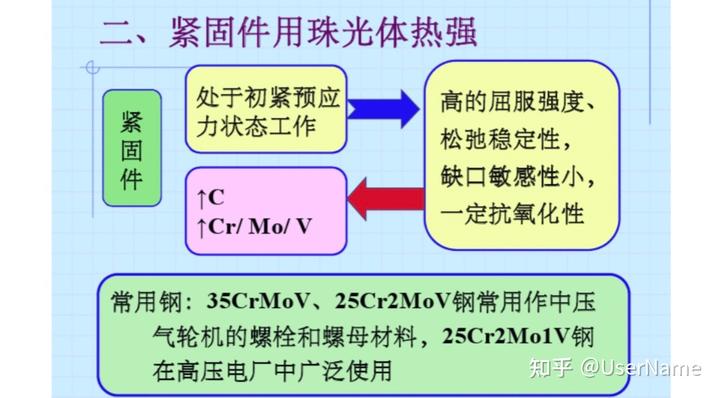
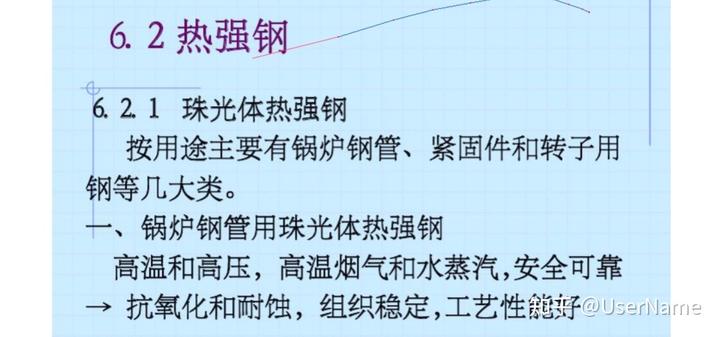
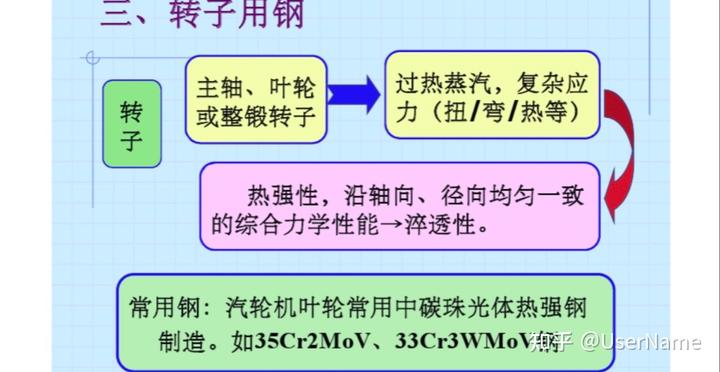
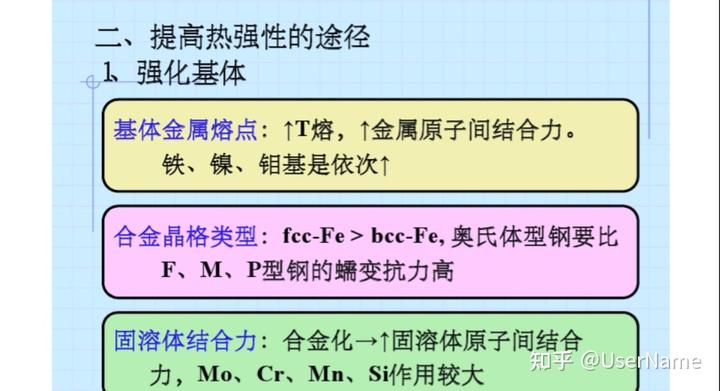
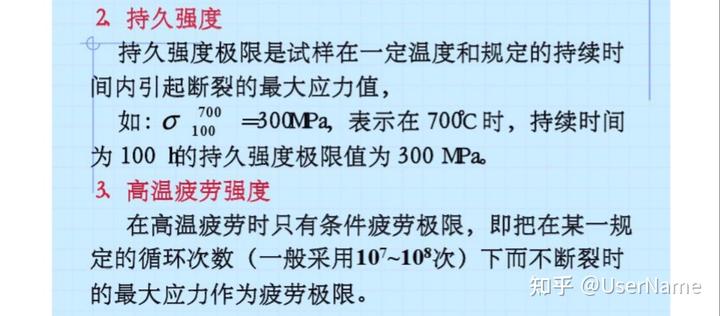
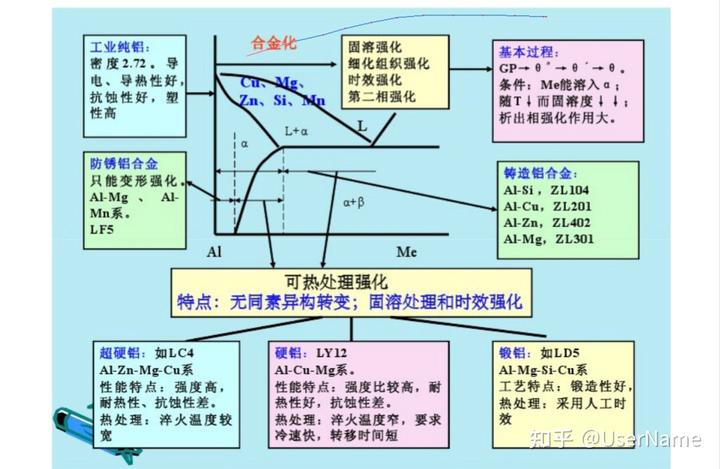
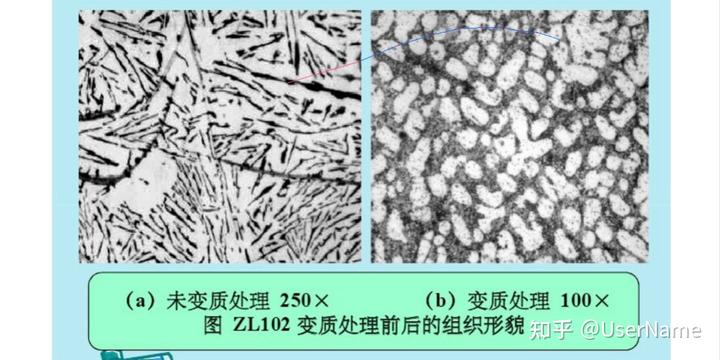
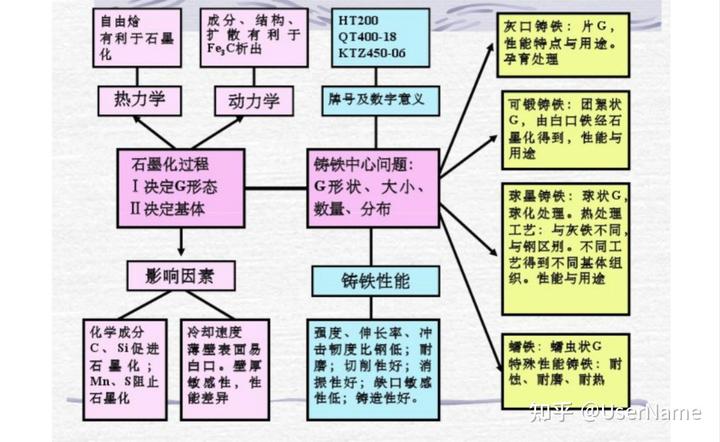
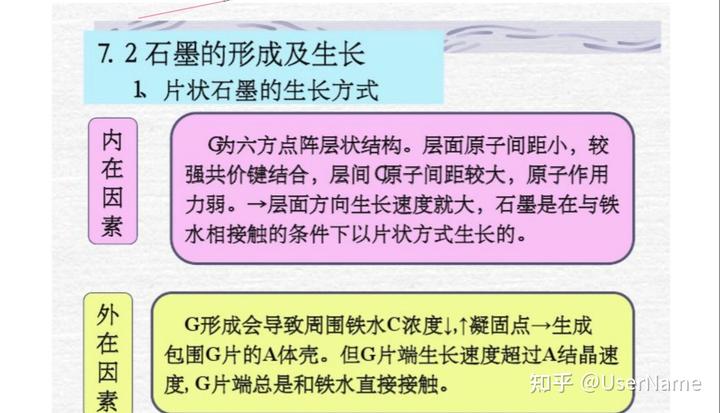
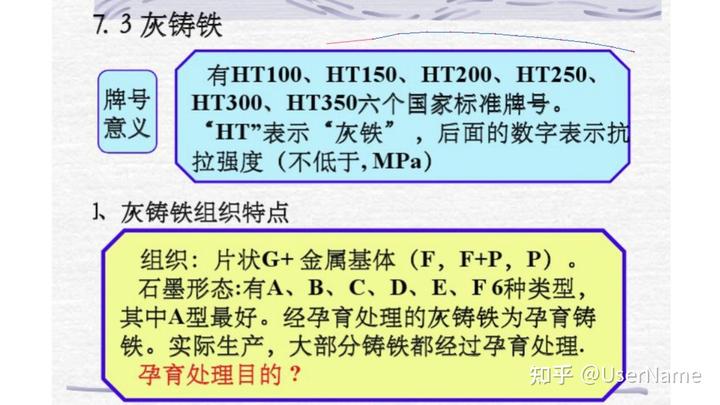
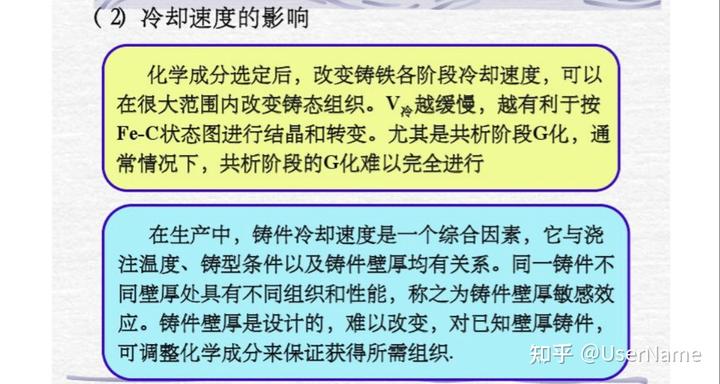
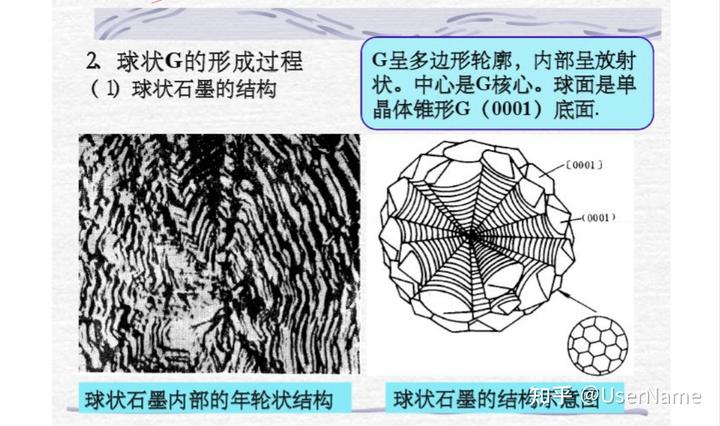
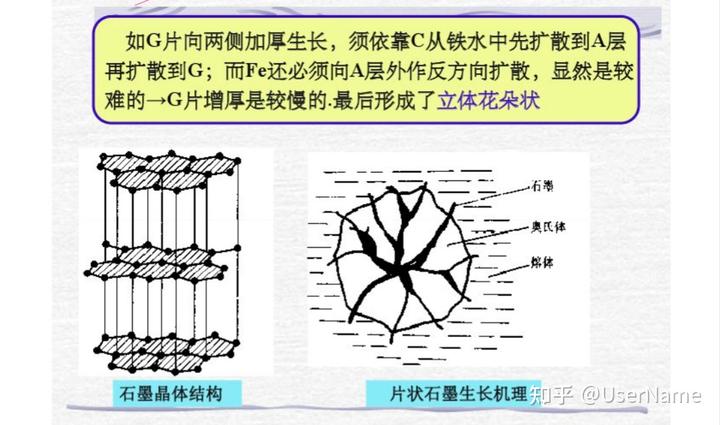
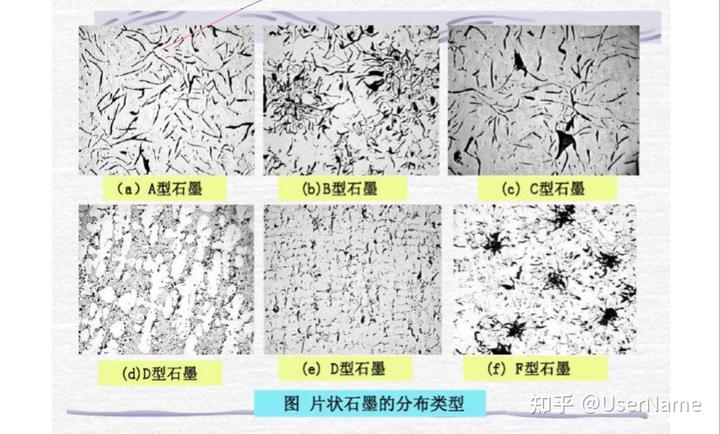
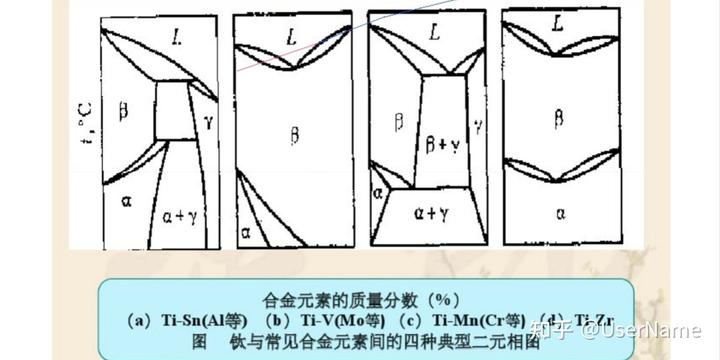
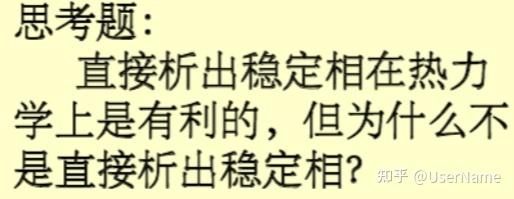
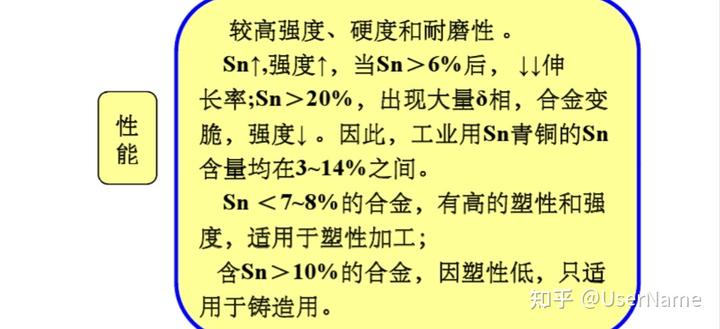
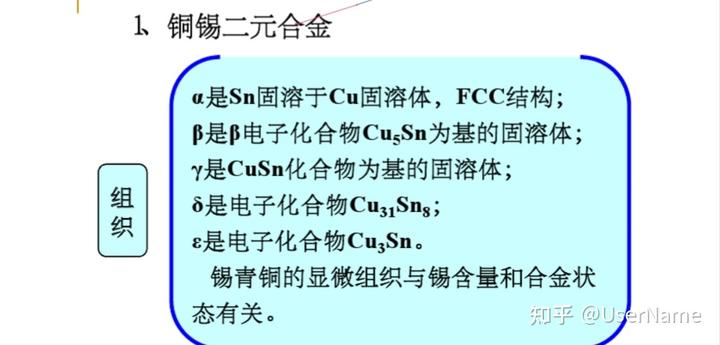
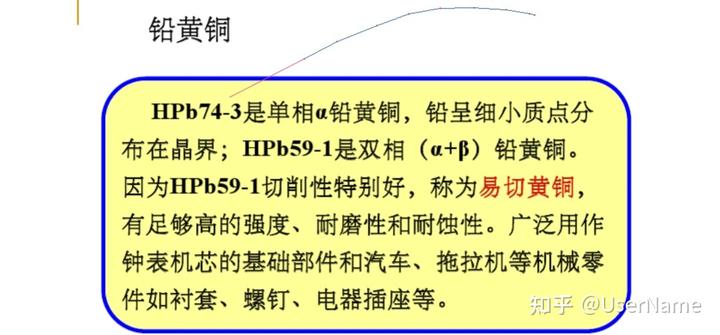
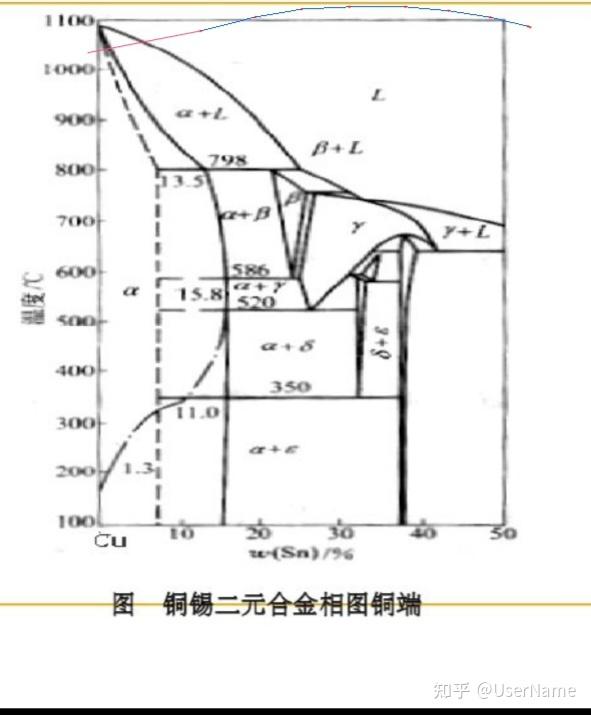
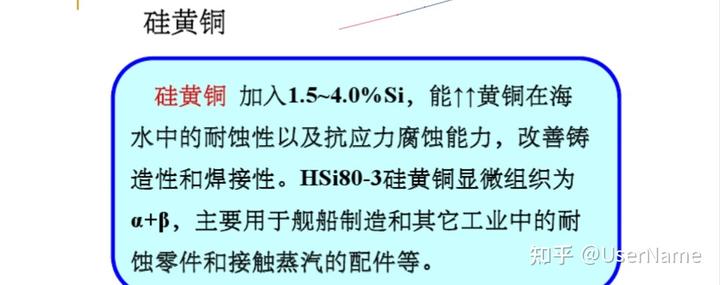
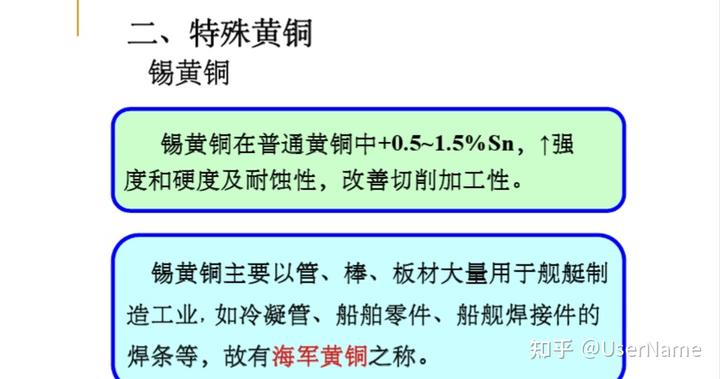
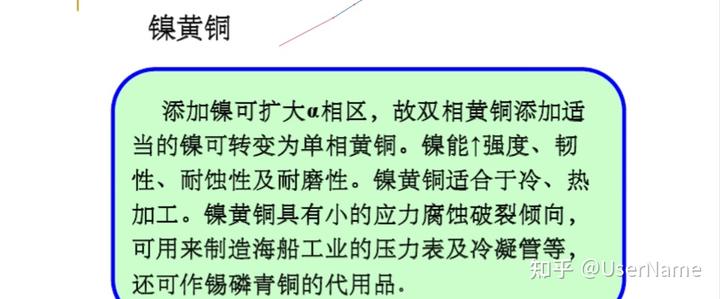
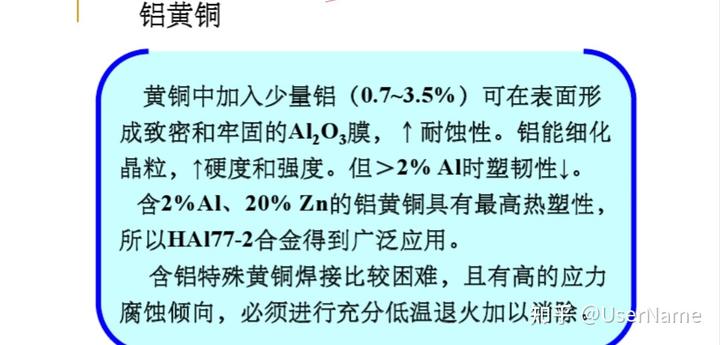
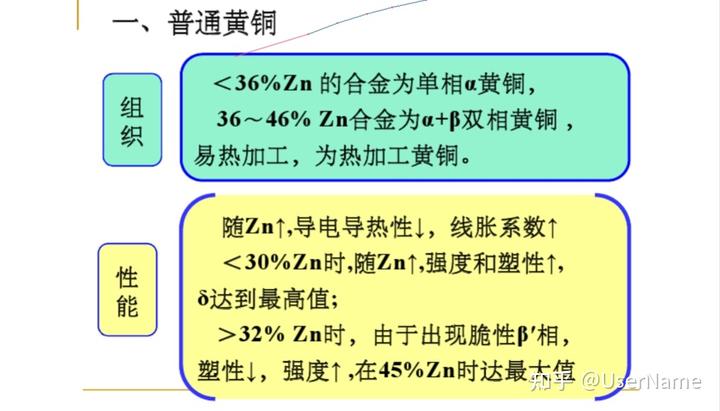
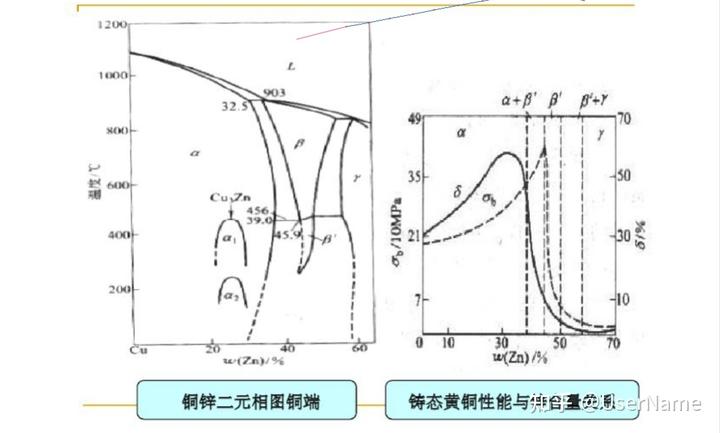
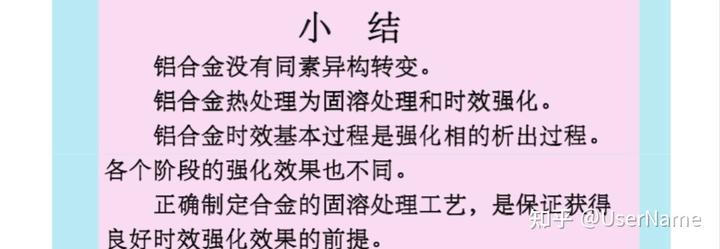
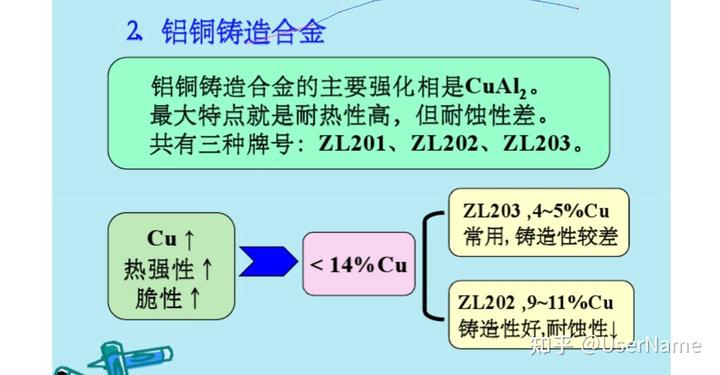
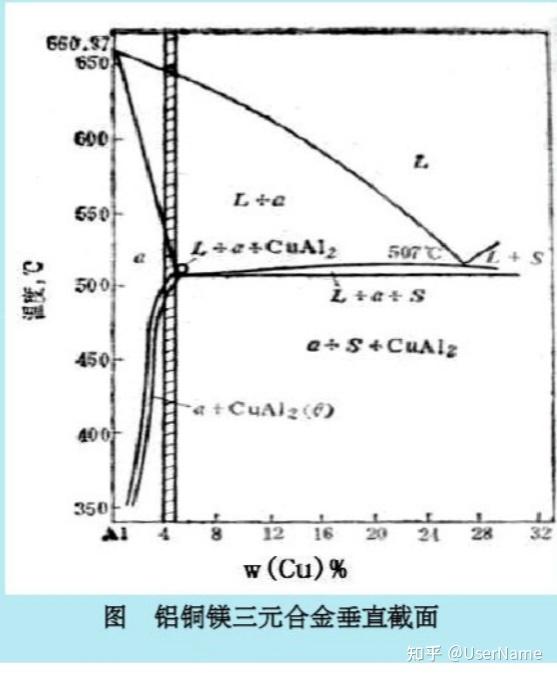
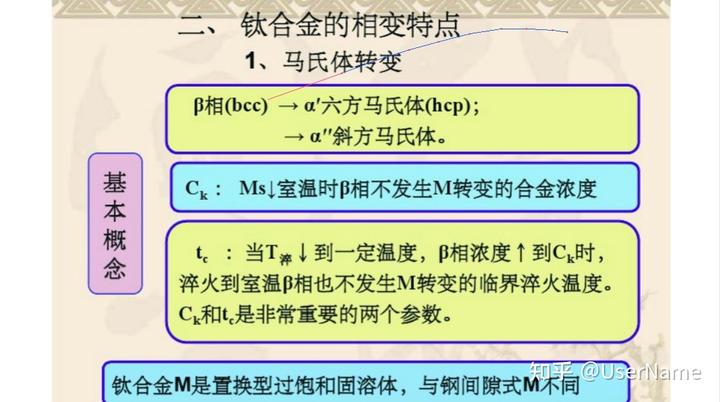
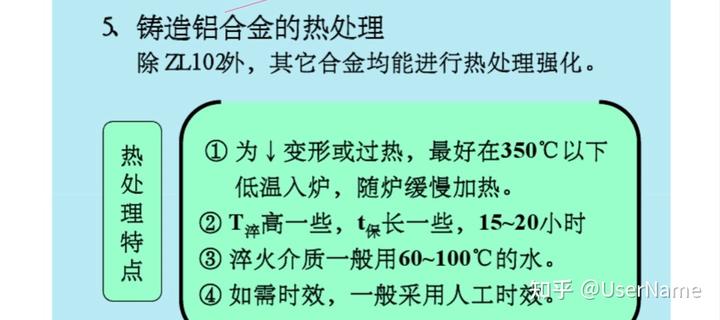
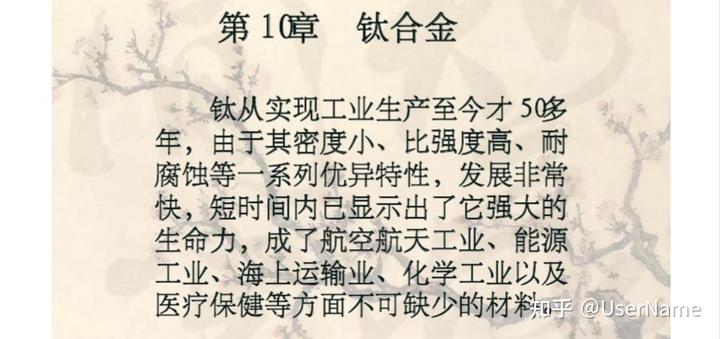
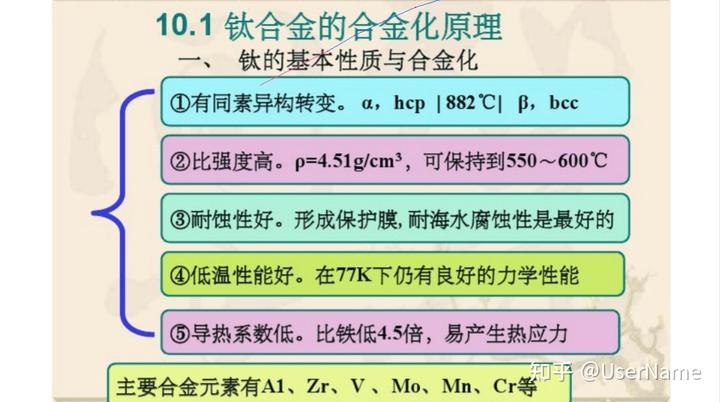
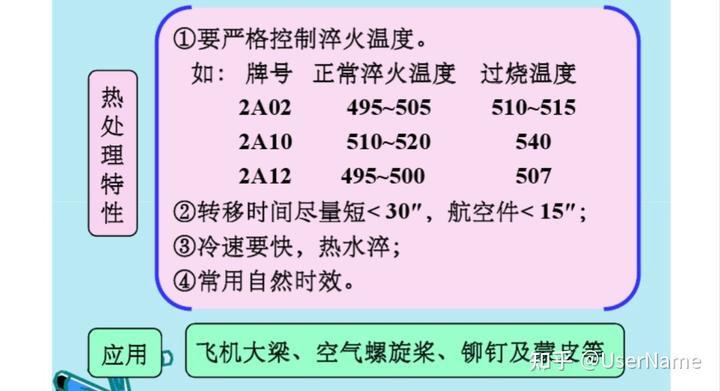
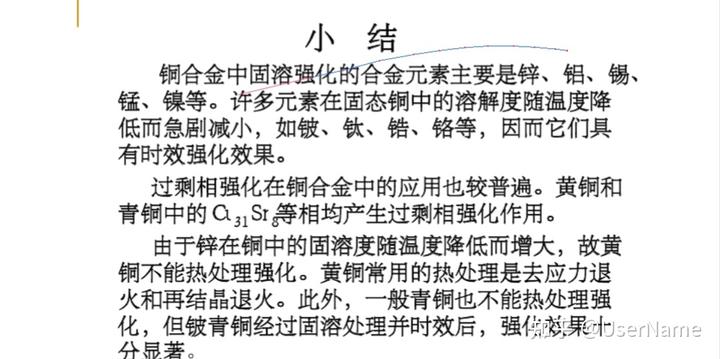
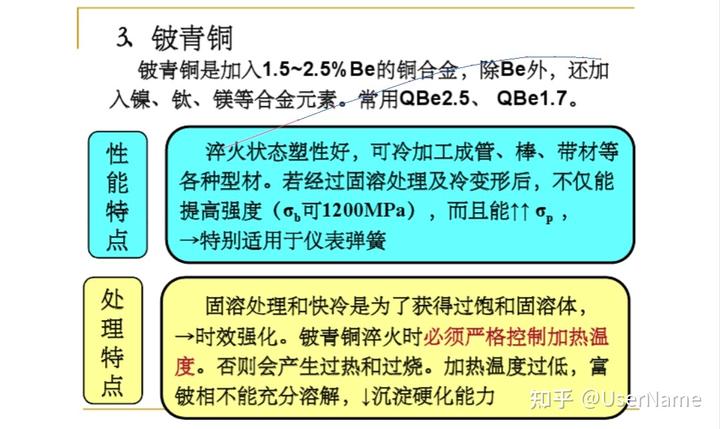
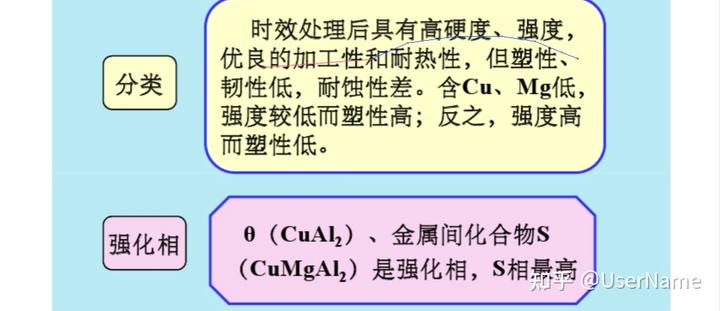
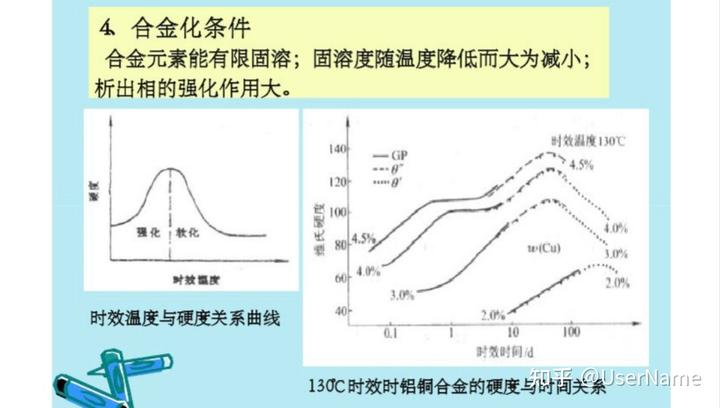
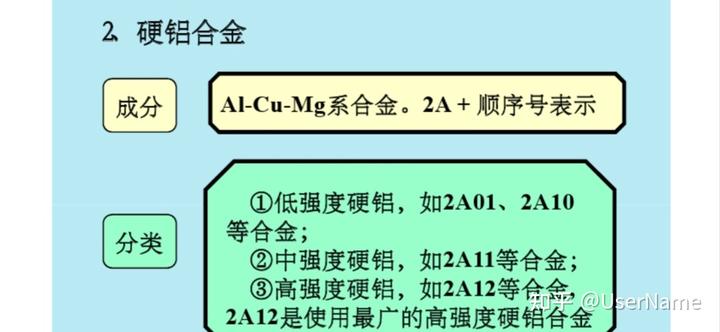
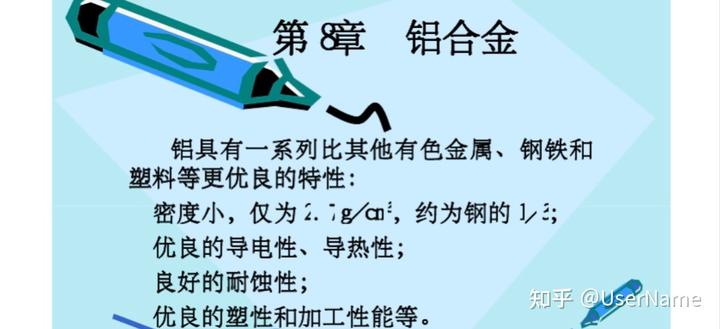
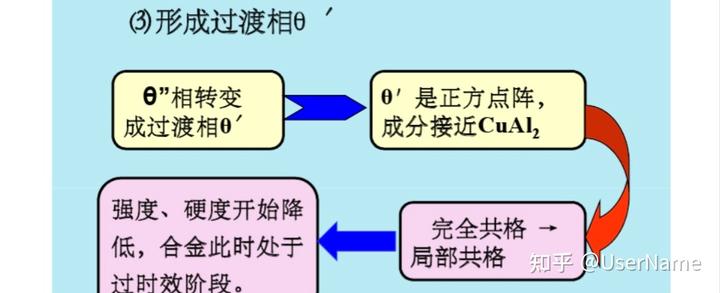
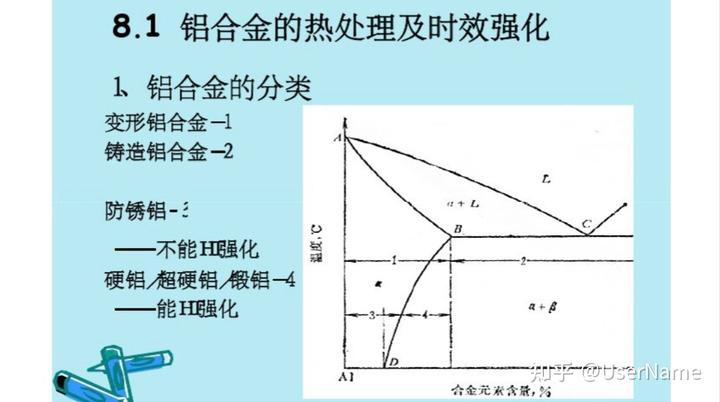
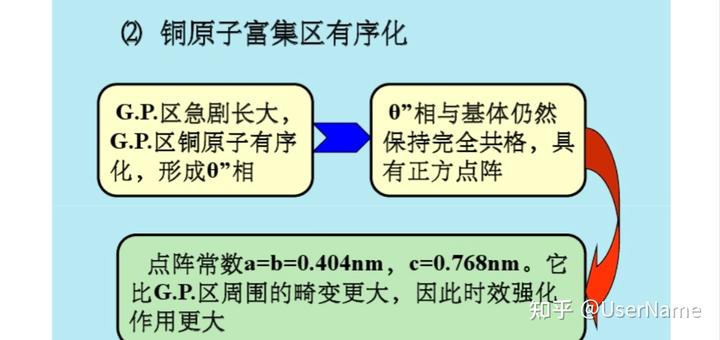
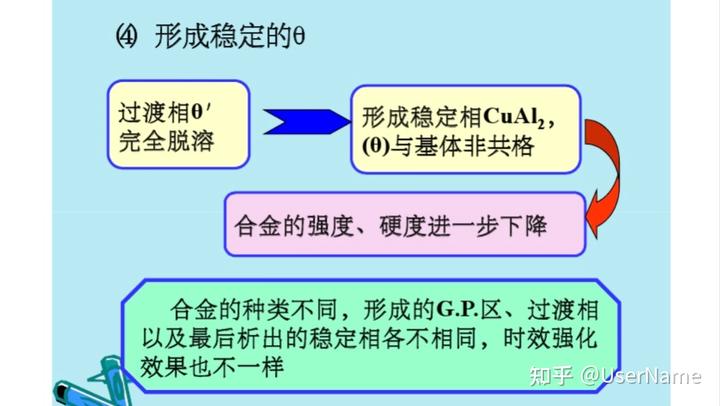
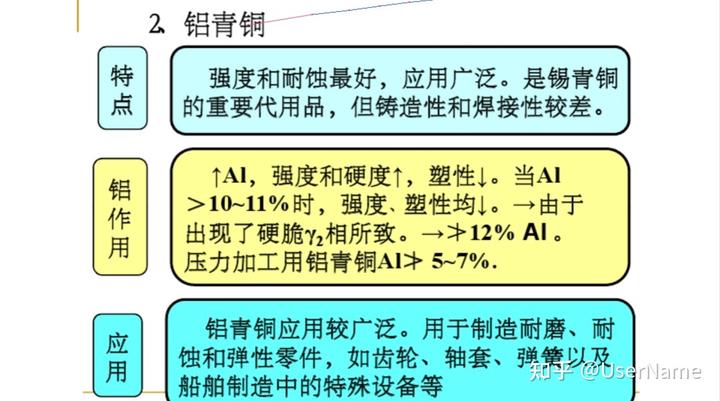
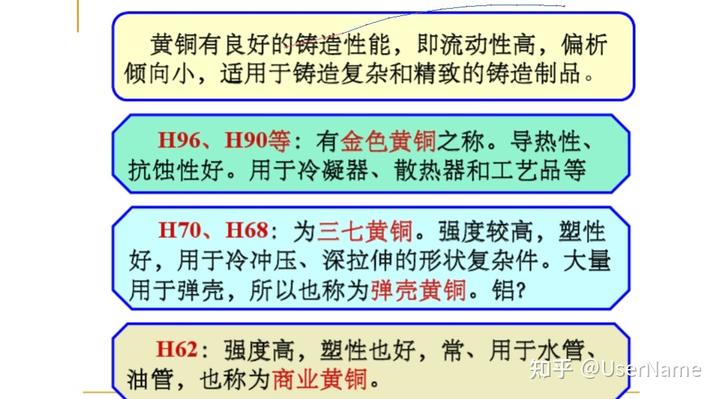
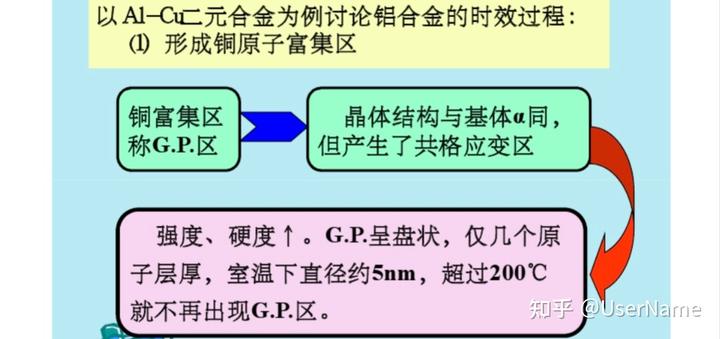
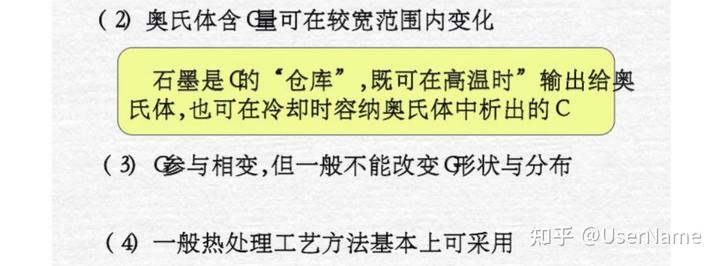
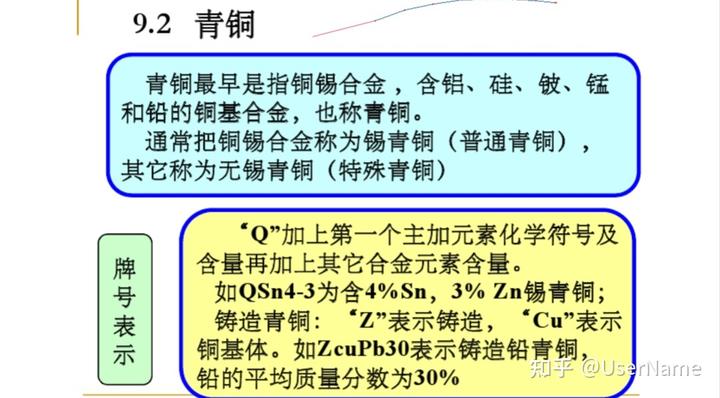
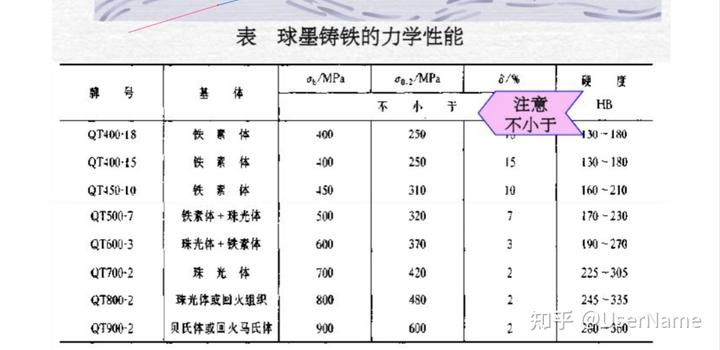
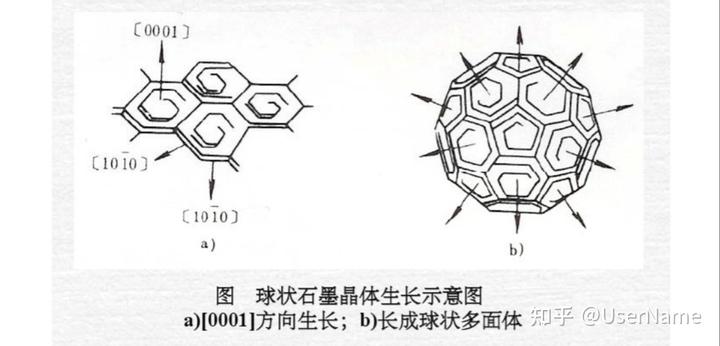
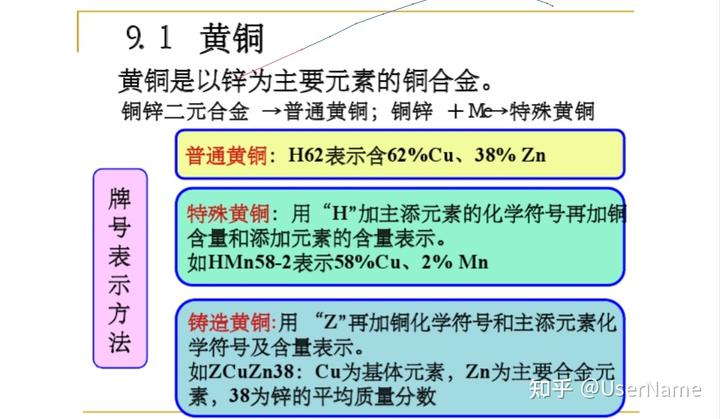
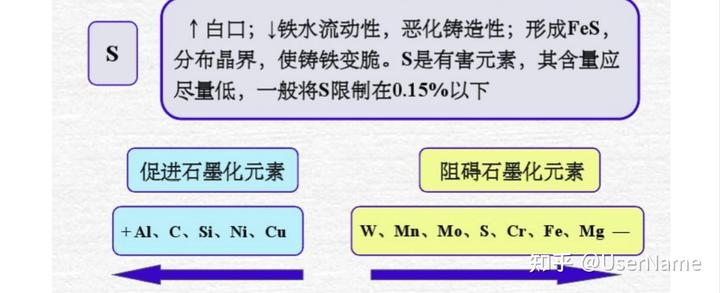
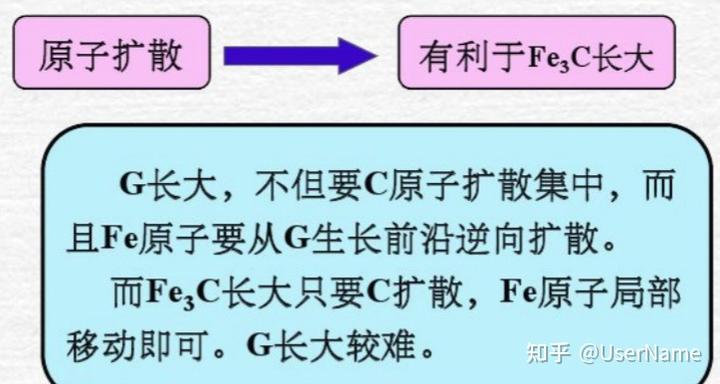
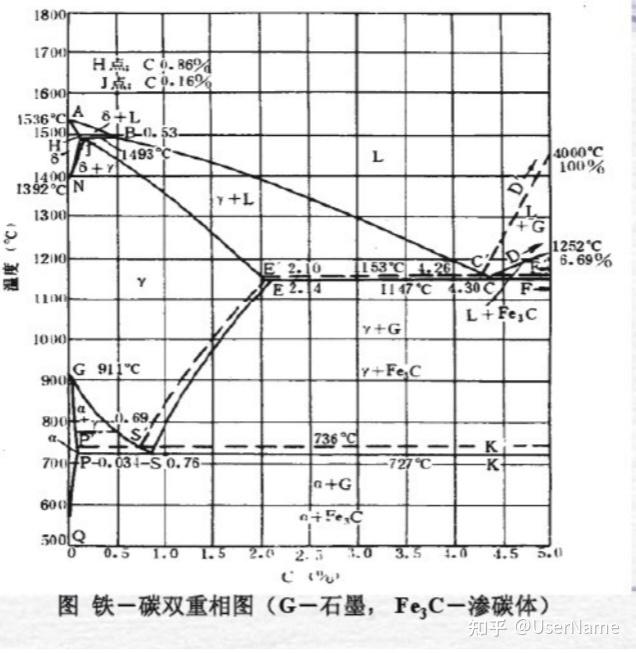
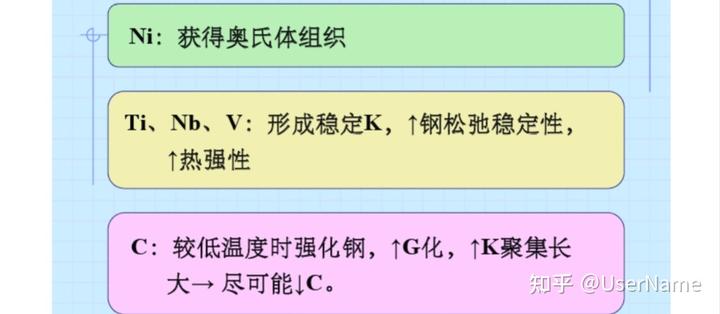
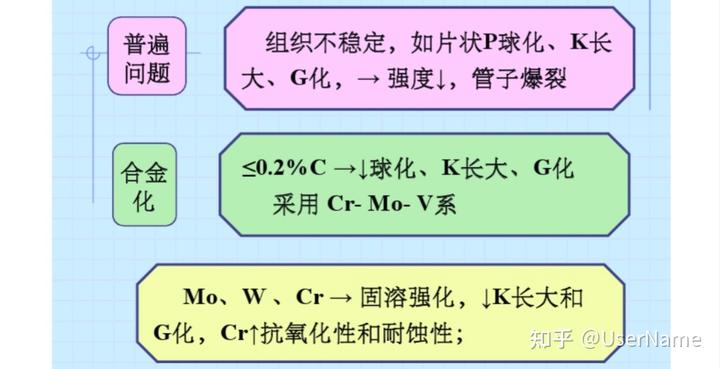
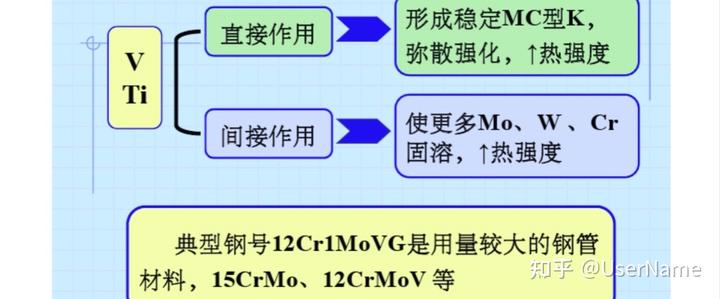
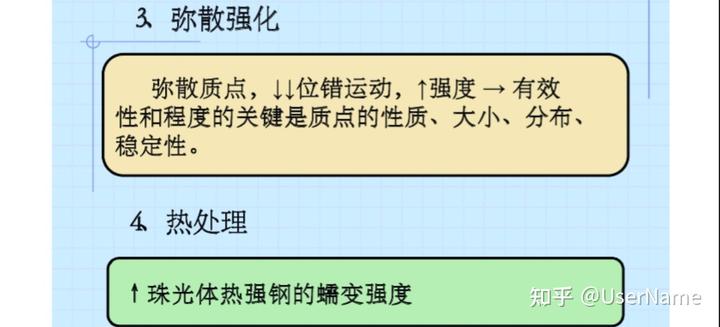
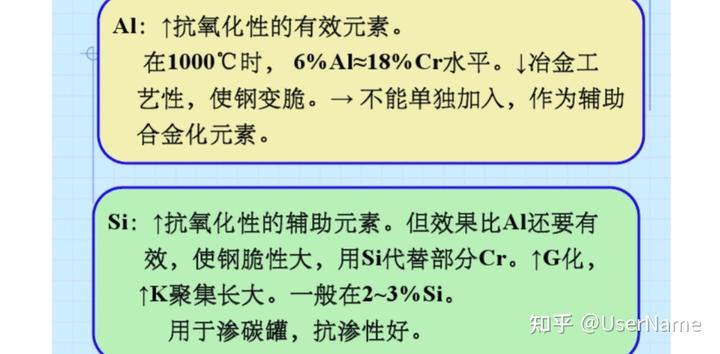
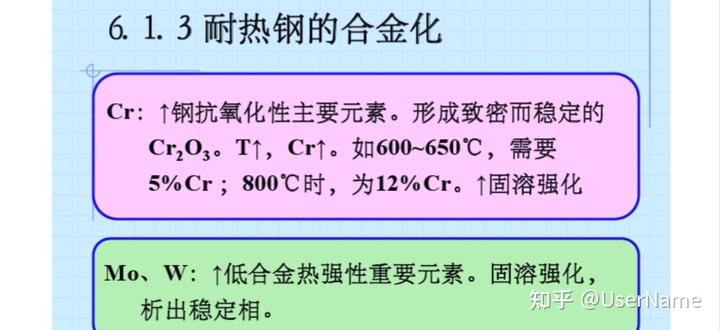
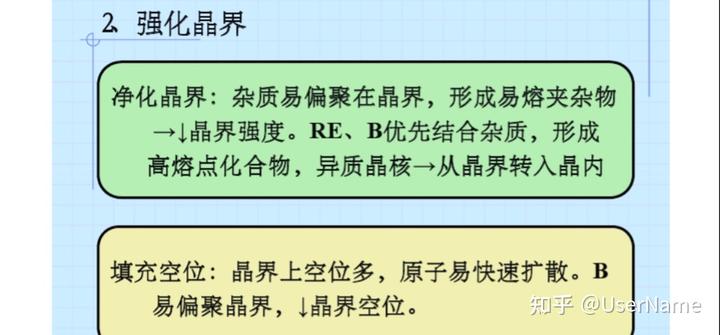
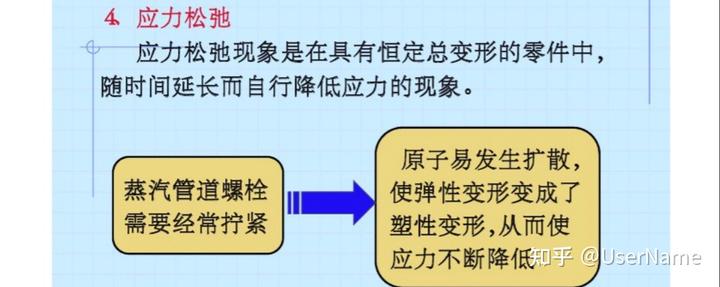
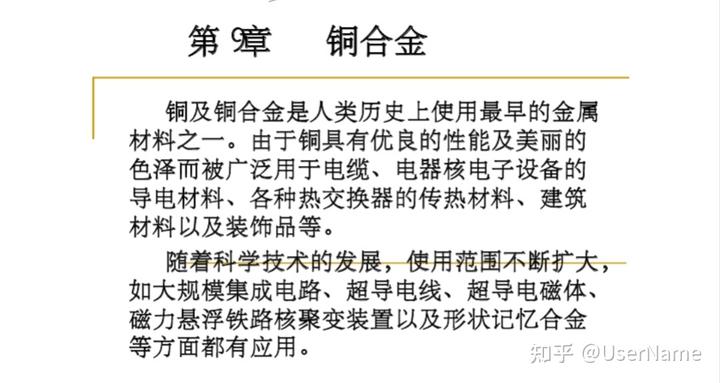
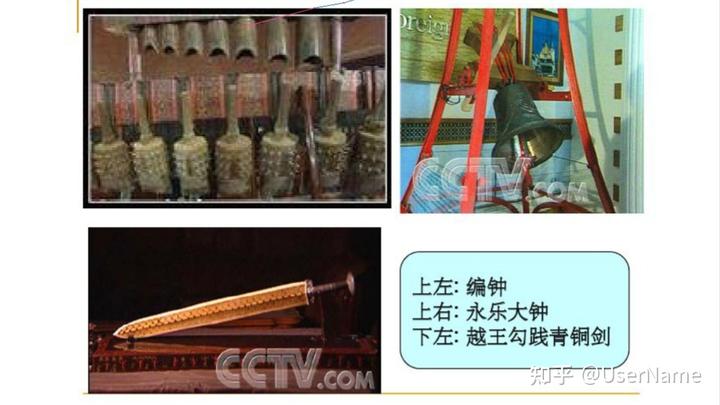
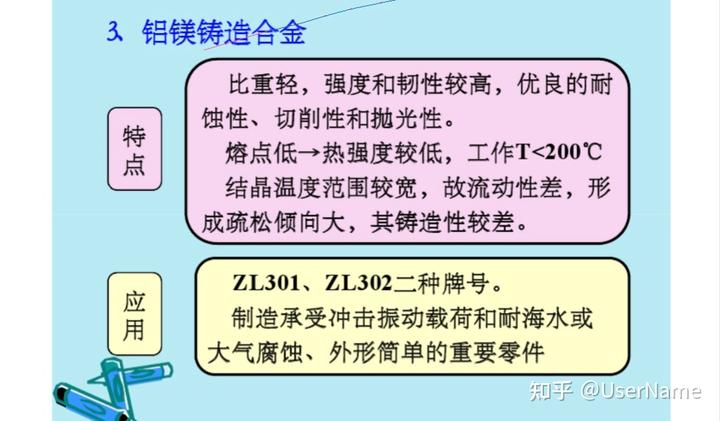
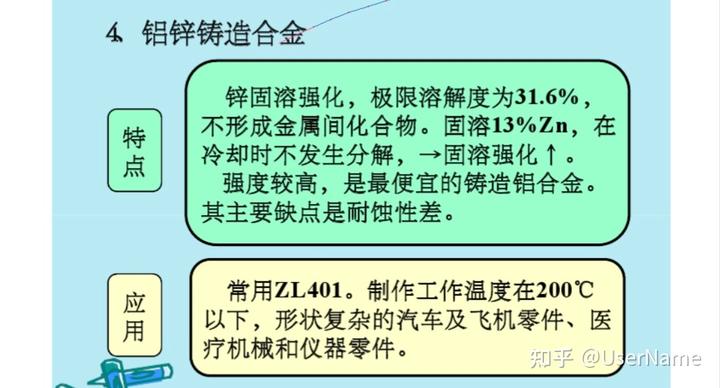
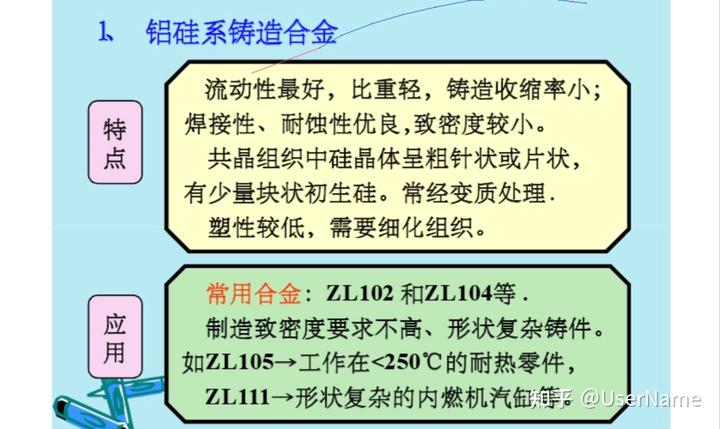
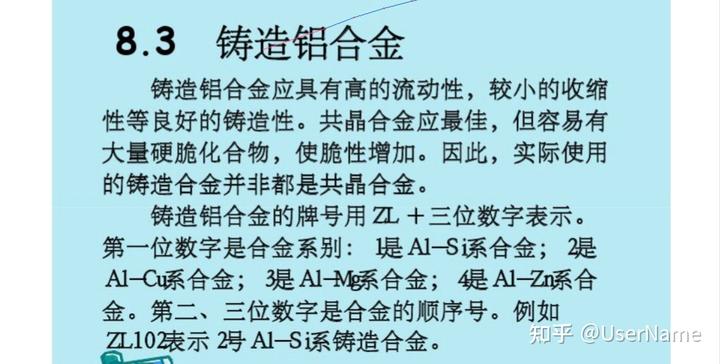
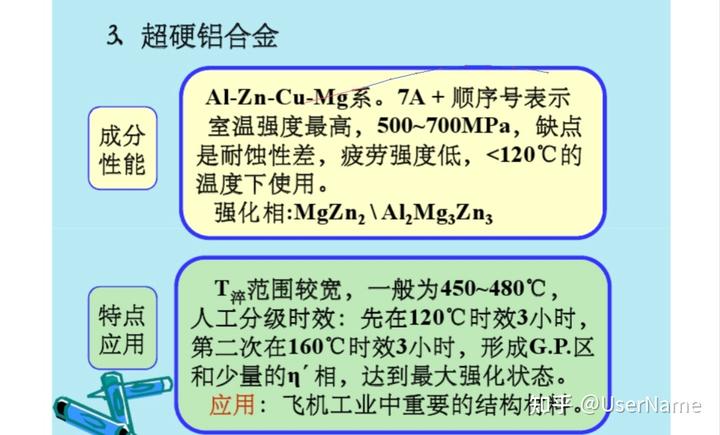
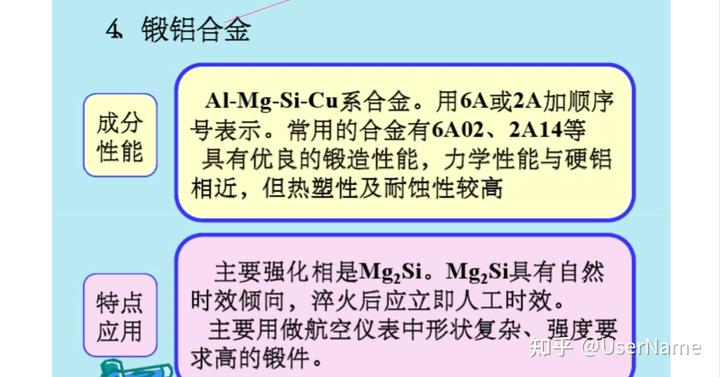
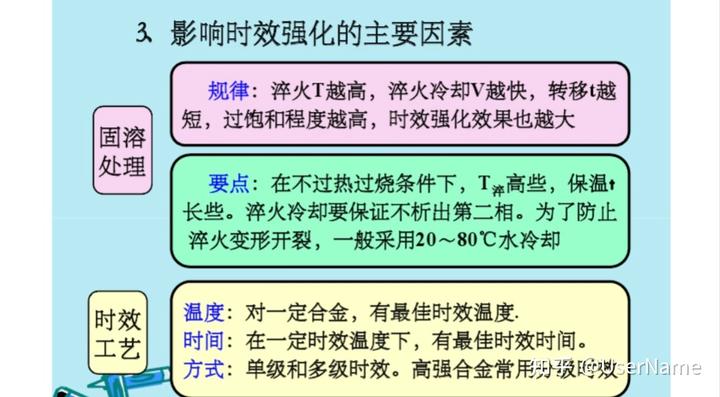
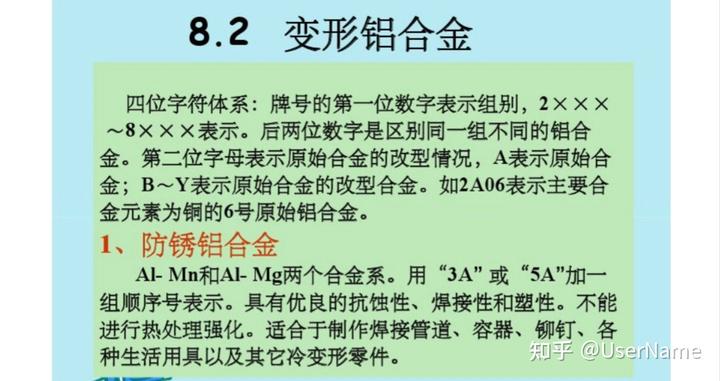
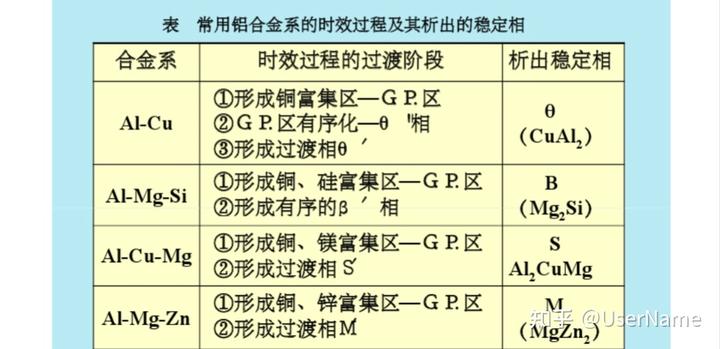
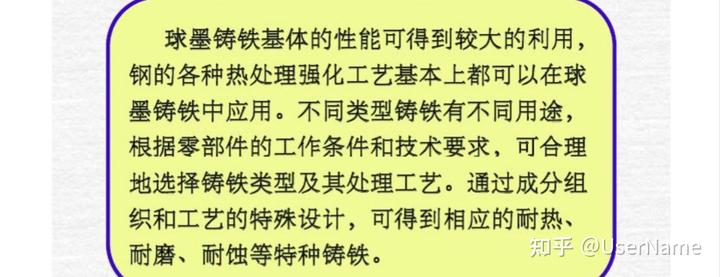
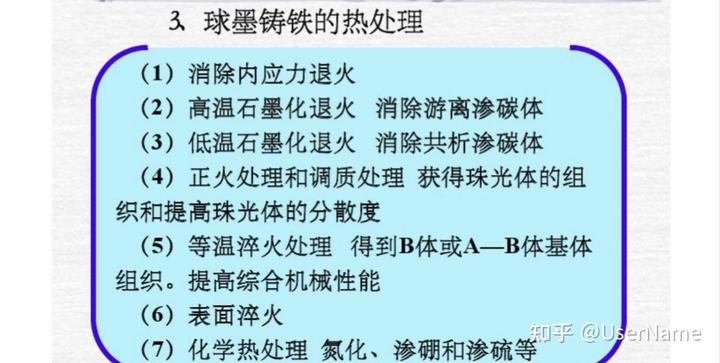
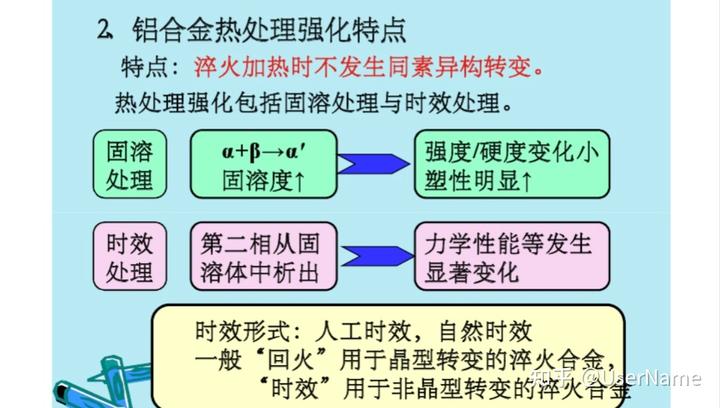
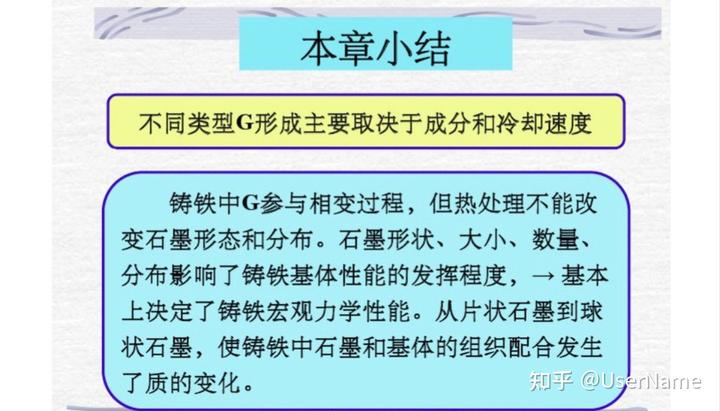
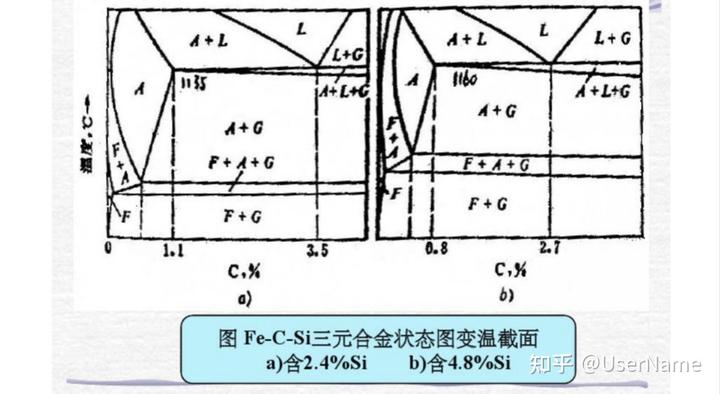
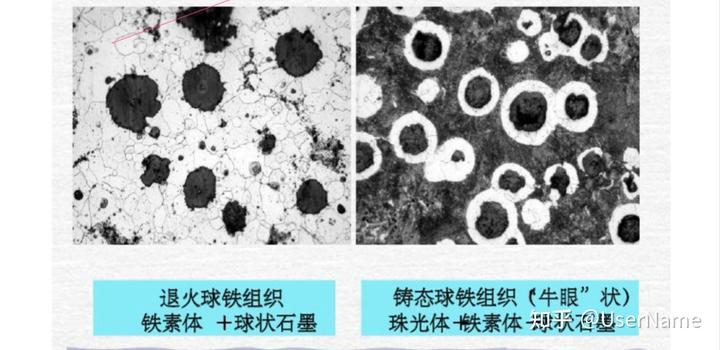
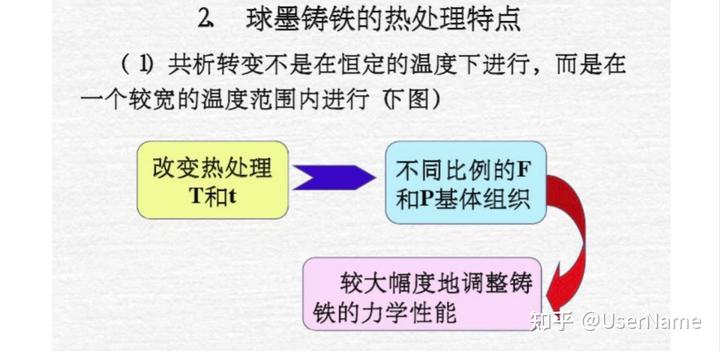
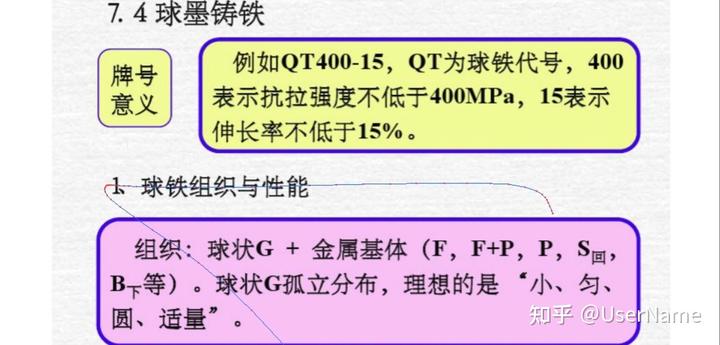
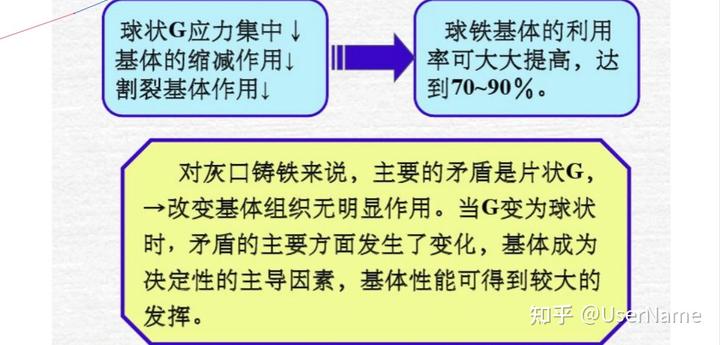
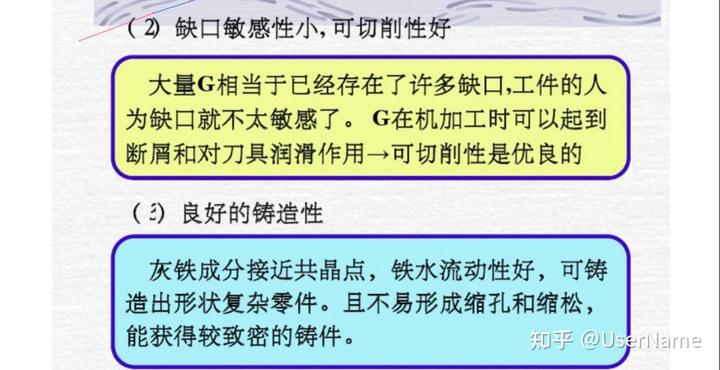
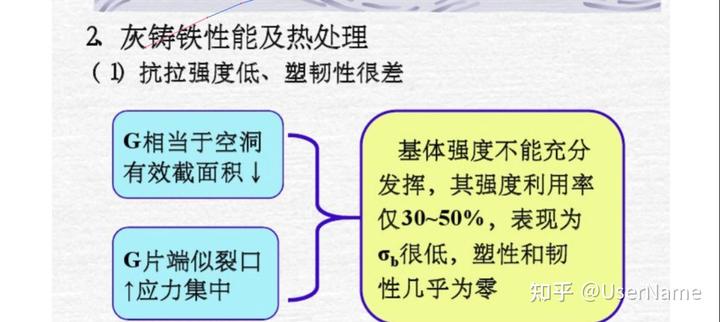
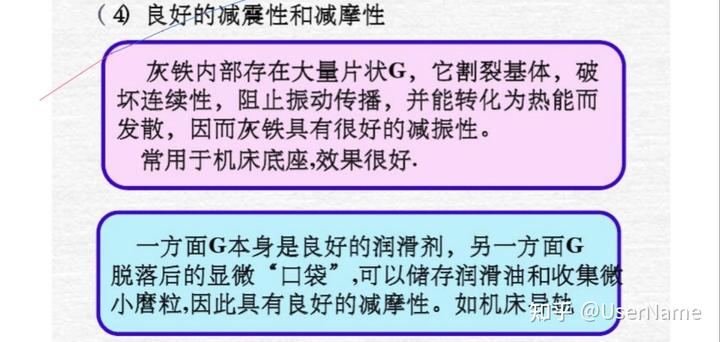
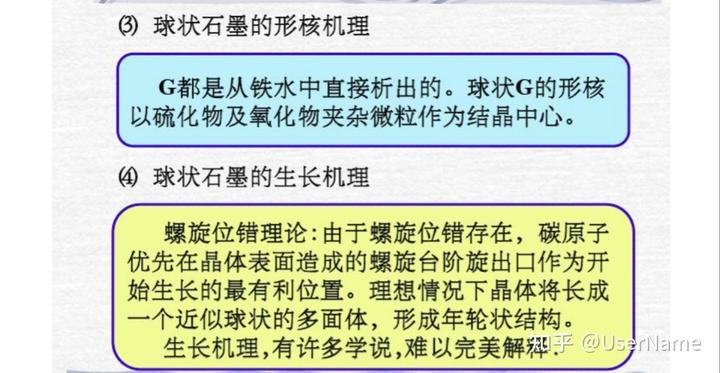
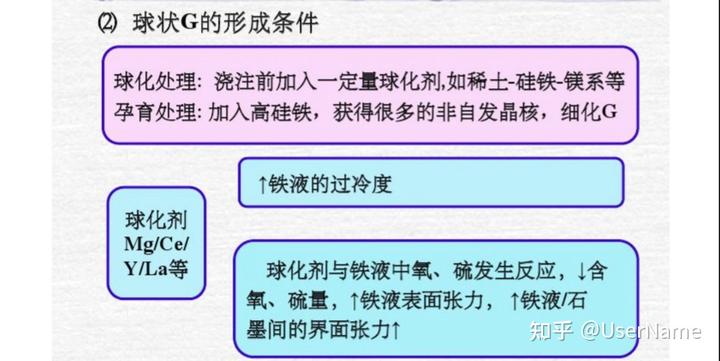
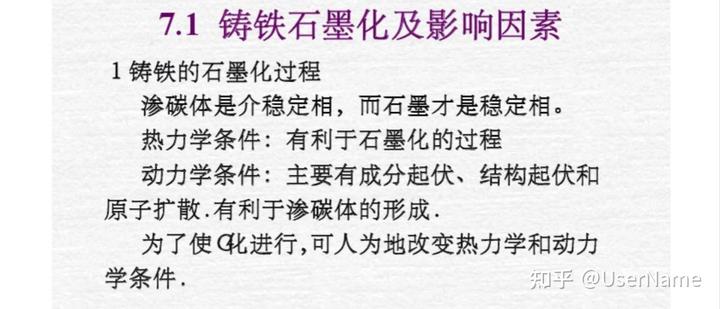
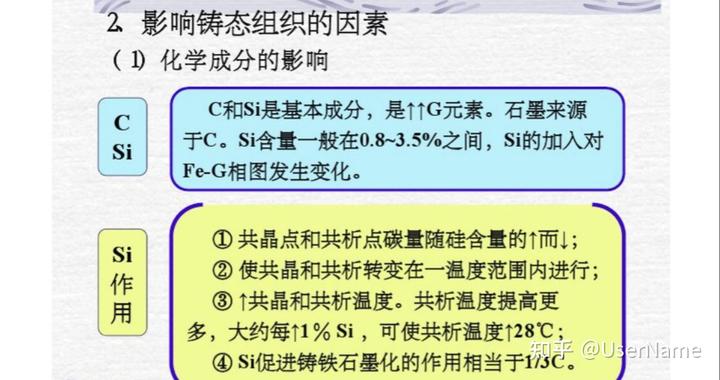
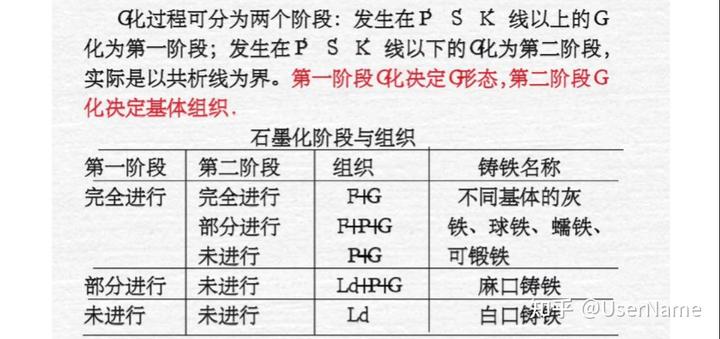
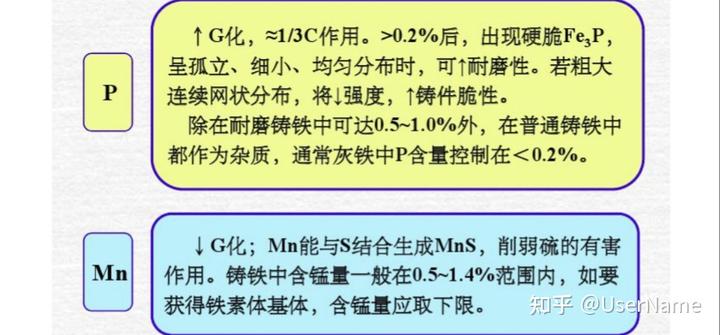
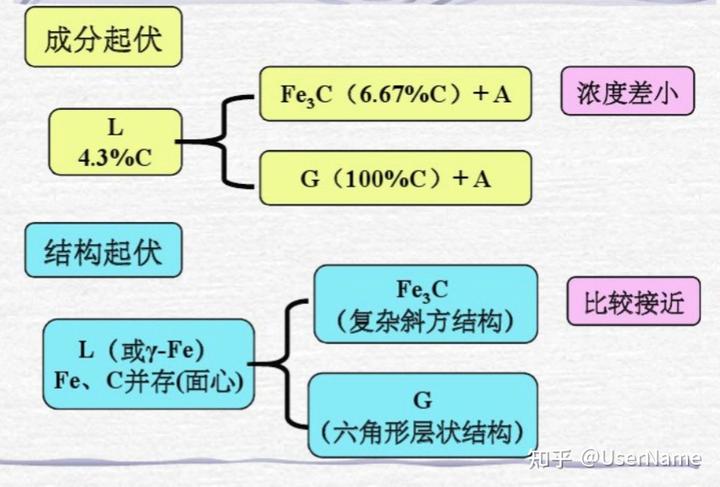
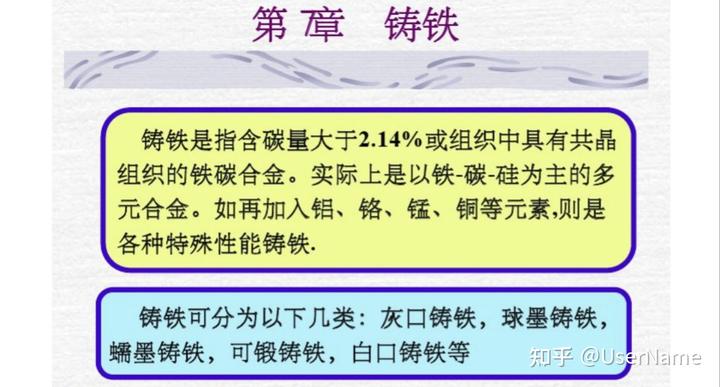
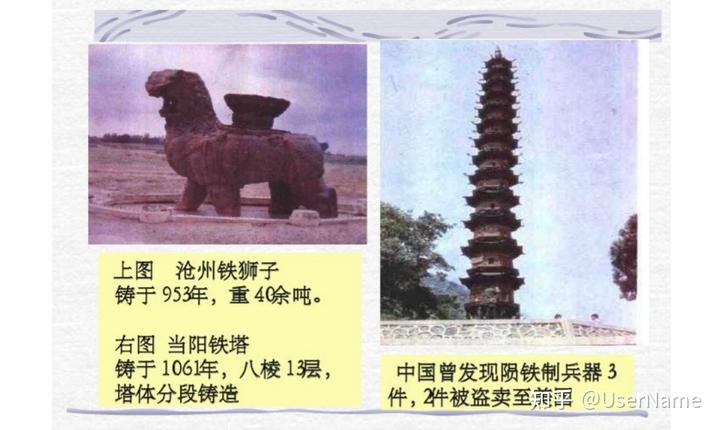
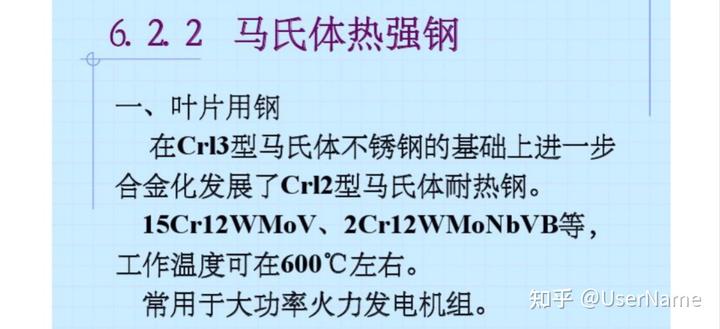
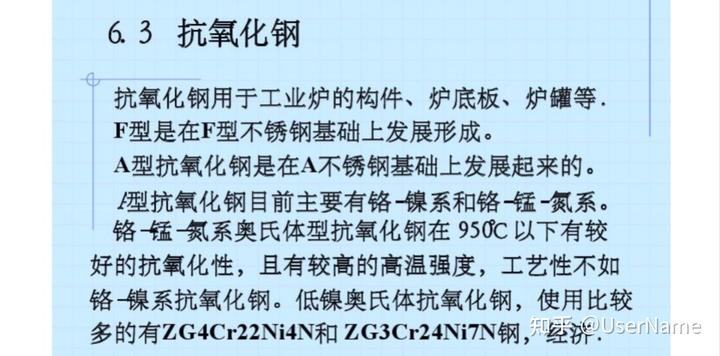
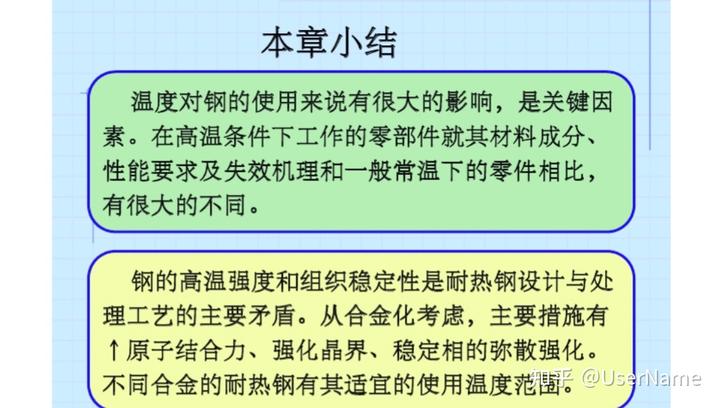
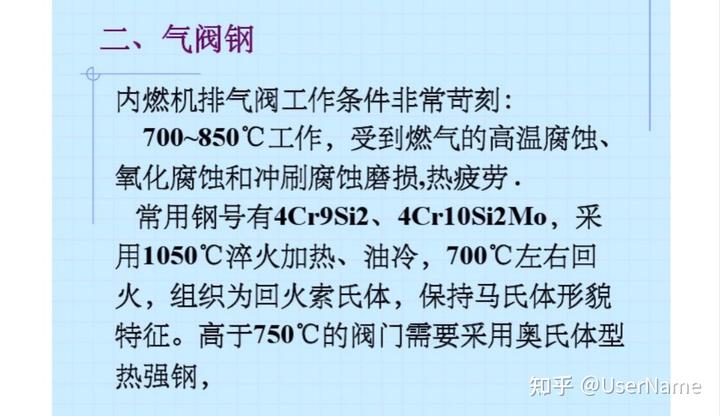
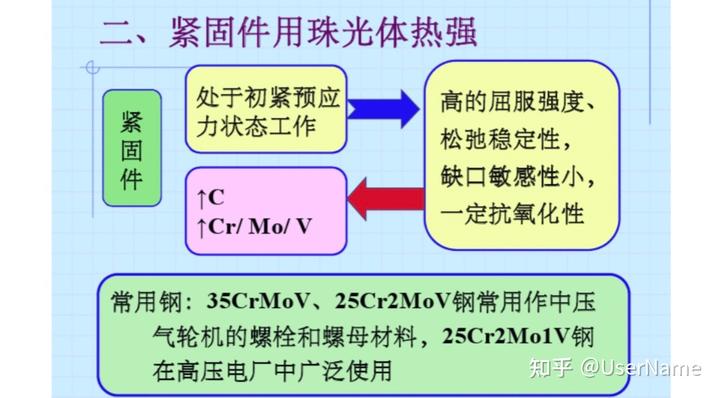
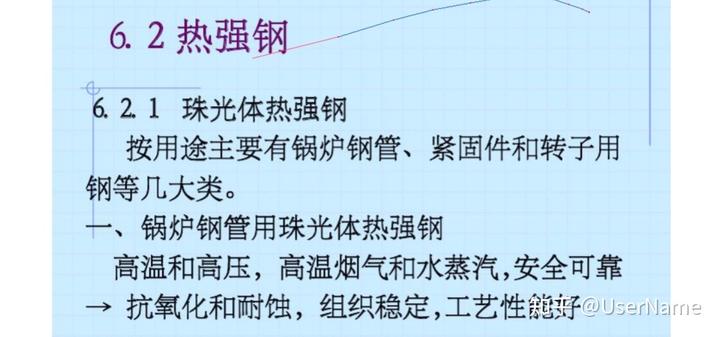
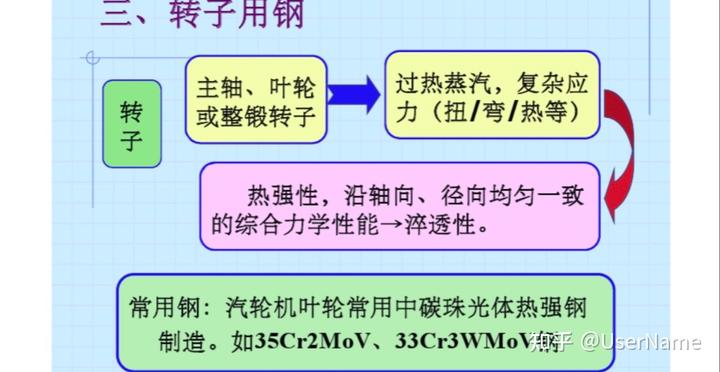
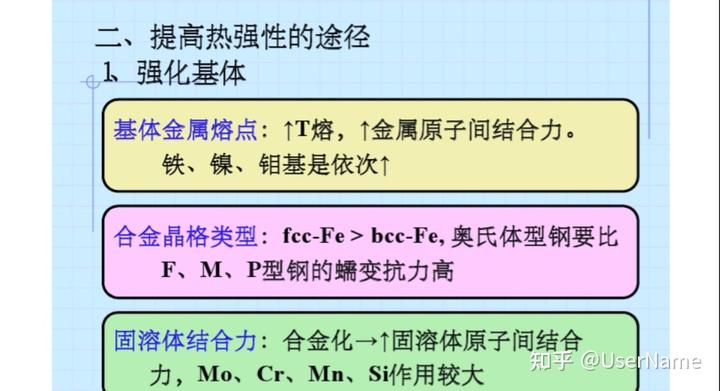
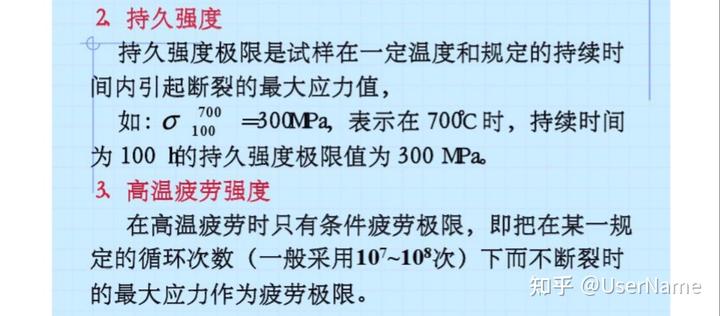
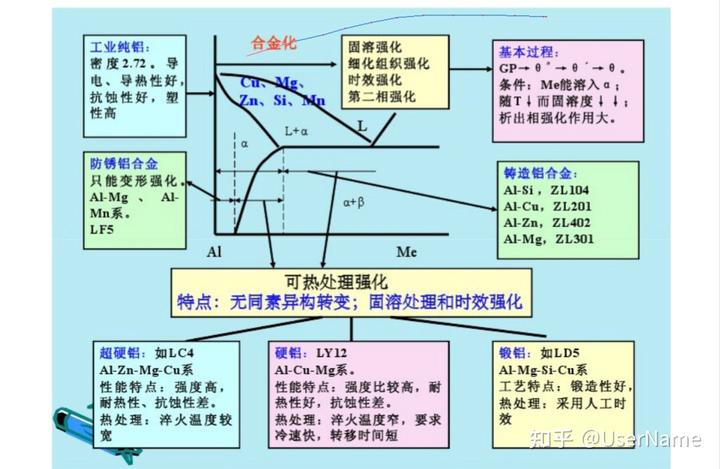
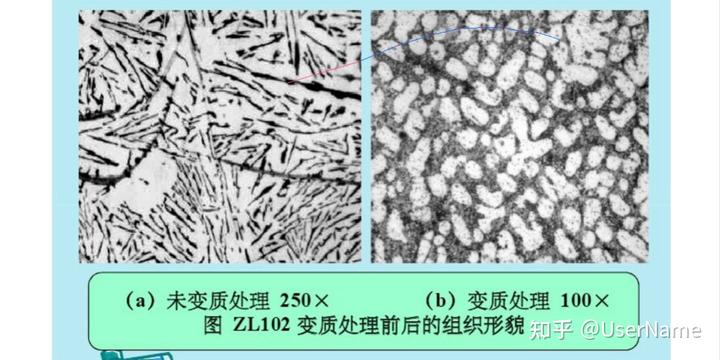
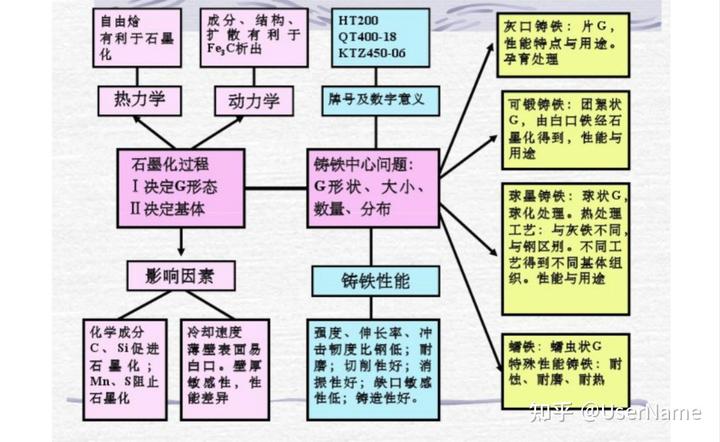
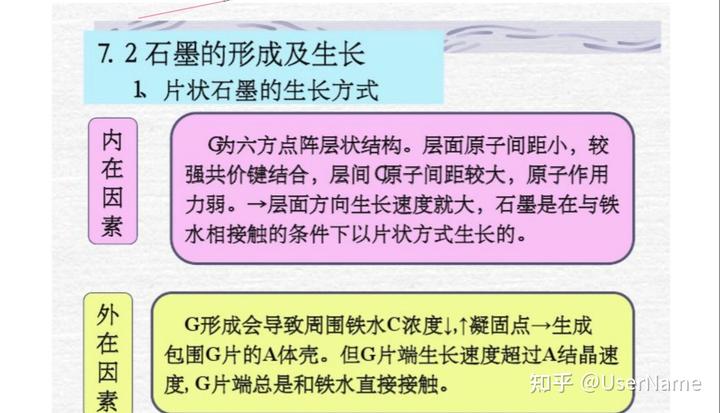
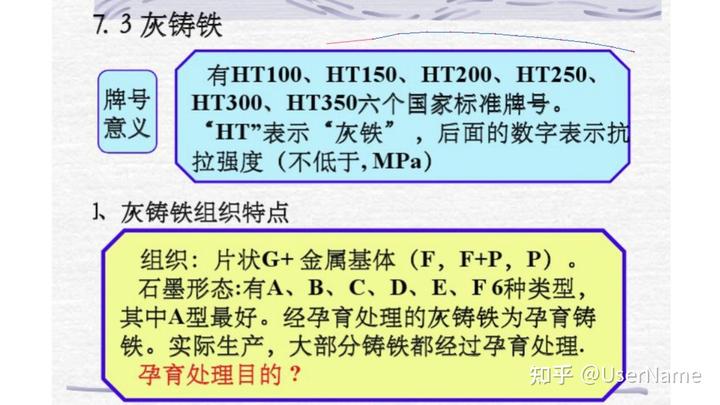
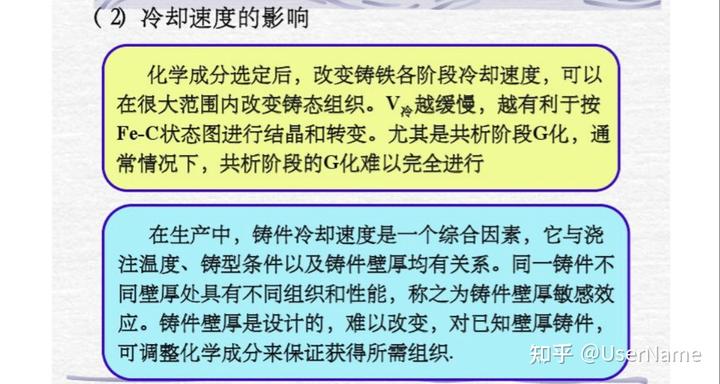
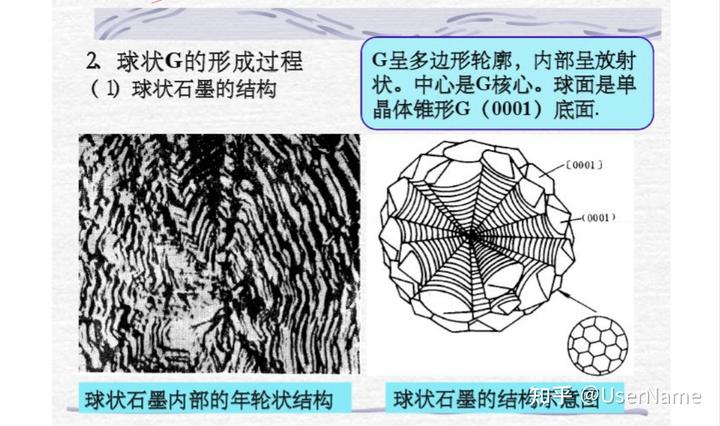
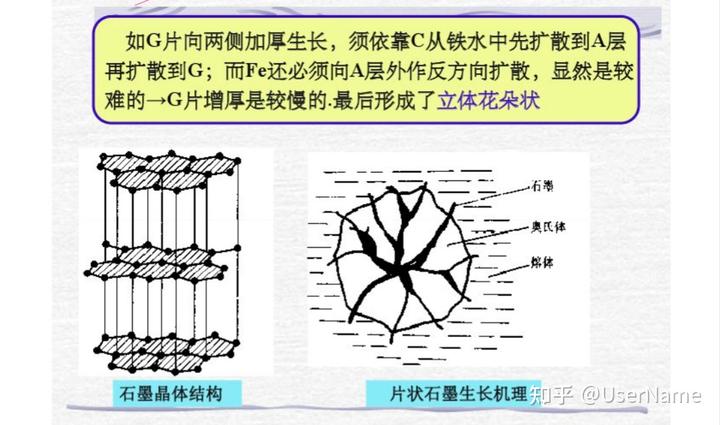
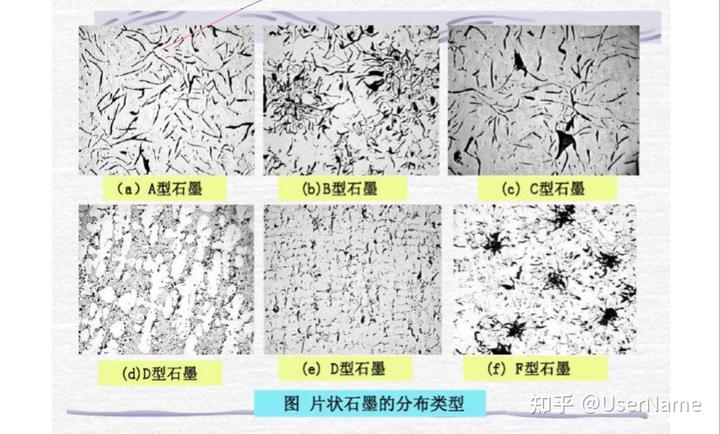
问:2023年锅炉价格/多少钱?
