大概率2021-2030间CCUS项目更多的是示范工程。全国目前已经建立近十个二氧化碳捕集与利用的电力行业示范工程。水泥、钢铁企业也
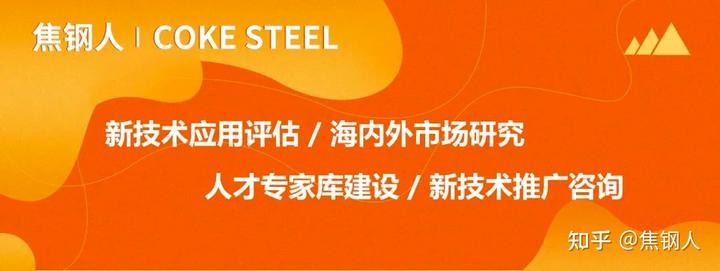
大概率2021-2030间CCUS项目更多的是示范工程。全国目前已经建立近十个二氧化碳捕集与利用的电力行业示范工程。水泥、钢铁企业也在尝试对接CCUS需求中。印染、液晶、电解铝行业也在持续推进。但预测各行业大规模实施、部署CCUS技术为:煤电和钢铁行业2030-2040,水泥2035-2050,生物质能2040-2060。
CCUS技术背景
国家生态环境部环境规划院对CCUS进行了定位,首先CCUS技术是实现化石能源低碳化利用的唯一选择。2050年化石能源仍扮演重要角色,占中国能源消费比例10%-15%。
其次CCUS是保持电力系统灵活性的主要技术手段。火电来加装CCUS实现近零排放可以保证电力系统的灵活性、可靠性、且平衡可再生能源发电的波动性。
第三,CCUS是钢铁、水泥等难减排行业低碳转型的可行技术。钢铁行业即使利用氢还原铁技术也将持续排放剩余二氧化碳。水泥行业采取减排措施后也将排放剩余二氧化碳。因此加装CCUS来实现钢铁和水泥行业的净零排放是重要的。
第四,CCUS可以进行新能源耦合实现负排放技术,比如将CCUS与生物质能进行有机结合实现负碳排放。
中科院山西煤炭化学研究所陆诗建教授称:
CCUS示范项目截止到2020年,国外拥有65个商业化CCUS设施,34个示范项目,8个CCUS技术测试中心,每年整体利用和封存4000万吨二氧化碳。
而我国有35个CCUS示范项目,6个商业化设施。目前主要示范项目集中在化工和电力工程,体量为每年300万吨,与国外相比仍有差距。
我国碳排放和CCUS技术现状
从燃烧的角度,CCUS捕集技术分为燃烧前、燃烧中、和燃烧后。
燃烧前是化工过程中的煤气化和天然气净化技术。燃烧中指的是包括富氧燃烧和化学链的化学热技术。而燃烧后技术是指电厂、钢铁厂烟囱排放的燃烧后尾气的二氧化碳捕集。
我国二氧化碳排放目前最大为燃煤锅炉烟气。
其中电厂排放40亿吨二氧化碳,燃煤锅炉的烟气二氧化碳浓度为11%-15%。钢铁厂排放18亿吨二氧化碳,二氧化碳浓度为12%-30%。水泥厂排放15亿吨二氧化碳,烟气二氧化碳浓度为30%-40%。
以上烟气均为常压。电厂、水泥厂、钢铁厂是碳排放大户并每年排放七十亿吨二氧化碳。
化工行业排放6亿吨二氧化碳,且拥有高压高浓度二氧化碳。
燃油锅炉厂、生物质锅炉烟气、船舶排气、天然气联合循环电厂的碳排放规模相对较小,且浓度较低。
从技术角度捕集方法分为固体吸收法、溶剂吸附法、膜法、和低温精馏法。
固体吸附法分为变压吸附和变温吸附。变压吸附技术已经成熟,低温的钠基吸附剂和固态胺吸附剂可以用于小型示范项目,但高温钙剂和镁剂吸附剂还处于实验室阶段。变压吸附采用固定床,而变温吸附采用循环流化床。
变压吸附法应用于中浓度40%-60%二氧化碳的天然气净化场景。但缺点是产品的纯度低,一般为95%且能耗较大。
整体固体吸附法需要高性能吸附剂,主要体现在孔容大、吸附容量大、吸附分离度高、再生过程性能好、颗粒均匀、机械程度好。
尤其变温吸附剂的关键是较好的机械耐磨度。反应器的循环流化床需要来回循环,机械强度差会磨碎并失效。变压吸附和循环流化床的变温吸附工艺一般采用吸附塔和解吸附塔的工艺。
溶剂吸收法包括化学吸收、物理吸收、以及物理化学吸收。三个方法都相对成熟,且化学吸收法正持续改良中。
化学吸收剂第一代的典型代表是1950年美国开发的一乙醇胺法MEA,主要用于脱除二氧化碳和硫化氢。吸收能力相对稳定、价格便宜又环保、五级反应二氧化碳吸收速度快,但能耗较高。
目前工业应用由于高能耗的原因开始使用混合胺吸收剂。典型代表为混合胺KS系列、MA系列、多元胺PZ系列等等。
能耗指标从MEA吸收剂的3.8-4.5GJ/tCO2降低至2.8-3.2GJ/tCO2,大约每捕集一吨二氧化碳消耗1.5吨蒸汽。
物理吸收主要应用于化工、化肥、沼气、高压天然气等场景。物理吸收法的典型溶剂是聚乙二醇二甲醚。
物理化学吸收的典型代表是天然气脱碳。天然气含有低浓度二氧化碳且适合物理化学吸收法。物理化学吸收剂的典型代表为MDEA甲基二乙醇胺,并已实现规模化应用。
膜分离法的原理是利用膜材料性能分离二氧化碳。它一般含有二氧化碳和其他成分,而二氧化碳更容易渗透穿过。比如甲烷在高压侧而二氧化碳在渗透侧渗透从而通过物理方法实现甲烷和二氧化碳的分离。
膜法适用于商业化项目,天然气净化和化工厂尾气处理都有应用。它的优点是适合模块化设计。
缺点是膜对于预处理要求严格,气体分离膜容易堵塞,气源中如果有水、重烃或固体颗粒会对膜组件造成较大伤害。
此次国外的膜寿命能达到十年,而国内的膜寿命为5-8年,使用年限较短。
小规模项目将用到10-20根膜管,但百万吨规模项目的膜管需求量会加大。小规模应用占地面积小是优势,但当规模变大后反而占地面积会成为劣势。
此外膜的纯度有限,一般中浓度二氧化碳可以提纯95%,如果进气是10%的低浓度二氧化碳烟气,能耗高且纯度一般小于80%。
低温精馏法也是物理方法,它主要是利用二氧化碳和其他气体凝点的不同来分离。
基本方法是对气源进行降温,降温后的二氧化碳首先变成液态,而其他气体从塔顶排出达到分离效果,但实际会有未液化的二氧化碳一并排出。
一般低温精馏法回收率在85-90%之间。剩余二氧化碳一般采用低温精馏加膜法或加吸附法的组合工艺继续分离。
它适合高浓度二氧化碳场景。低温煤化工、低温甲醇洗的尾气中二氧化碳浓度为80%。但缺点是只适合于高浓度的进气。如果气源二氧化碳浓度为20%-50%,能耗及成本会十分昂贵。
总体来说:
燃烧中的富氧和化学链技术仍在开发中,且工业运用不多。
胺溶剂的化学吸附法和低温精馏法已应用于工业化装置并往大型规模发展。
膜分离法在天然气净化和化工厂已有工业化的示范装置。但低浓度的烟气气源更多处于中试阶段。固定吸附法也处于中试阶段,对于化工厂的气源也刚刚拥有成熟化的装置。
最后,燃煤燃油锅炉烟气、水泥厂&钢铁厂烟气、天然气联合循环电厂等应用场景目前大多使用化学吸收技术。
化学吸收技术路径分析
化学吸收法主要分为两种:热钾碱法和有机胺法。
热钾碱法主要用于化肥尾气二氧化碳的回收利用。化肥厂的蒸汽余热未被利用起来,因此蒸汽的余热可以加热溶液。化学原理是在低温下吸收,而在之后的加热中发生解吸。
热钾碱以碳酸钾为主。此体系在低温下与二氧化碳发生反应生成碳酸氢钾,加热的情况下碳酸氢钾又发生分解,并成为碳酸钾和二氧化碳。
技术缺点是碳酸钾容易结晶,解吸温度较高,且温度要求严格。反应温度区间是70℃,解吸温度是120℃。如果温度低于65°C容易发生结晶并产生危害和受阻。
有机胺法最广泛的应用场景是烟气二氧化碳捕集,且毒性较低。有机胺体系的缺点是容易氧化。烟气中含有氧,在加热和带氧的情况下胺液会发生氧化并降解。
有机胺法的基本原理也是酸碱反应。烟气采用的是二氧化碳和有机胺在低温下反应生成氨基甲酸酯,并在高温下解吸分解为二氧化碳和有机胺体系。
整个流程后端是在低温下吸收,吸收后解吸,解吸的过程中需要加热。加热使用蒸汽作为热源,因此耗热的能耗是核心。
另外消耗层面主要是消费蒸汽和溶剂。溶剂价格昂贵,且可能产生降解和损耗。额外添加的溶剂也是成本。吸收剂吸收容量越大、能耗越低、循环量越低,性能越好。
装备层面是三个规整的填料塔:前端是碱洗塔、中间的是吸收塔、后端是再生塔。一般工业锅炉排放烟气中的二氧化碳首先经过预处理冷却至40度,预处理包括脱除硫等杂质气体再进入吸收塔。
预处理后烟气进入吸收塔中二氧化碳与喷顶的碱性胺吸收液产生化学反应并吸收,再通过换热器送到再生塔。
再生塔底部利用蒸汽加热废气至100度,吸收液将分解并制成二氧化碳。随后二氧化碳经过冷凝压缩通过管道装罐运输。
目前研究的重点是在大规模项目中是否采用方塔或圆塔、是否用水泥替换钢材、水泥塔的防腐性能、以及填料中的气液分布器优化等课题。
工艺层面是利用碱洗塔底的贫富液换热器回收贫液热量,没有完全回收的余热则用热泵回收。
化学吸收技术的工艺特点是烟气适应性好,烟气构成复杂及排量大的问题都能很好应用,技术相对成熟。
我国目前80%-90%的二氧化碳捕集技术都采用化学吸收法。
化学吸收技术开发情况
目前我国各方正在持续研发化学吸收剂用于降低投资成本。其中降低蒸汽的能耗、吸收剂的损耗、以及电费是核心。
吸收剂的性能由多维度指标评判。较低的降解挥发、较小的腐蚀、较快的反应速度、较大的容量、较小的粘度密度,都会降低吸收剂的损耗,而最后是价格因素。
混合胺有上百种类别,而常用的有十多种,主要分为一级、二级、三级胺。典型的MEA吸收剂为一级胺,它反应快但能耗高。
二级胺的代表PZ、DEA反应更快、容量大但再生性不好,因此需要更高的温度。
三级胺的典型为MDEA,它的特性是反应慢但能耗低。
因此我国各大院校正在混合不同胺来兼顾平衡吸收性、再生性、能耗、粘度等各项指标开发合适的配方。
现在的研究重点是相变吸收剂,混合胺吸收剂在吸收塔中吸收二氧化碳后进入分相器。分相器中一项胺会抢夺二氧化碳,结果是分相器下方二氧化碳浓度非常高且溶液量较少而上方几乎没有二氧化碳。
溶液量少意味着再生能耗的大幅降低。分相的过程需要寻找控制点,而最优情况下可降至2.2GJ/tCO2。能耗相比MEA吸收剂降低45%。
各方院校单位正在积极研究两相吸收剂的配方。
此外市场正在研究新型离子液体、触发性吸收剂、和无水吸收剂等技术。
浙江大学能源工程学院方梦祥教授团队已经开展相变吸收剂的中式研究并落地相应工程示范,2022年有望实现工业化。
中科院山西煤化所陆诗建教授团队研发的低分压二氧化碳吸收剂主要针对低浓度二氧化碳排放应用场景,包括电厂、钢铁、水泥、和冶金行业的烟道气。
目前提升后的性能为再生能耗小于等于2.7GJ/tCO2。采用方式是吸收剂配方的优化,利用组合工艺实现吸收剂的回收降低夹带,吸收剂负载相比MEA提高33%。
化学吸收剂降解挥发问题
烟气中一般含有氧气、二氧化硫、氮氧化物、和粉尘。气体会造成吸收剂的氧化降解,而再生塔温度较高会发生热降解。
通常氧化降解占到70%,热降解占到30%。氧化降解通常发生脱烷基化反应、加成反应并生成热稳定性。热降解反应通常发生去甲基化反应、二聚反应、环化反应并产生氨和尿素等污染物的增加。
解决的办法是抗降解剂,通常加入氧化膜型缓蚀剂、金属捕获剂、和氧气捕获剂。目前吸收剂的改良工作正由各大校方及机构大力推进中。
中科院山西煤化所陆诗建教授团队已经开发抗氧化剂降低溶剂降解损耗,而吸收剂损耗小于等于0.7kg/tCO2。
目前市场已知吸收剂损耗最理想能够达到0.5kg/tCO2的水平。
关键设备和技术研发
设备研发主要包括吸收塔、再生塔、板式换热器、再沸器、以及压缩系统。
吸收塔和再生塔目前使用不锈钢填料塔。不锈钢填料可以满足速率性能要求,其中也包括了气体和液体的均匀分布器设备开发。
浙江大学能源工程学院方梦祥教授团队研发了低成本塑料填料。
塑料的问题是亲水性大,因此添加聚丙烯的亲水改性剂可以提高成膜率来达到不锈钢填料的性能。目前浙大正在进行工业化研究。
其次是换热器研发。吸收塔和再生塔中的温差在40度到100度之间,大量热量需要换热。目前正在根据吸收性和传热性研发板式换热器,而不易泄漏和腐蚀也是换热器的研发关键。
第三是节能工艺。吸收系统中的吸收剂会发生放热反应并造成吸收剂的吸收容量下降。回收工艺包括级间冷却、分布式换热、MVR热泵、压缩式热泵、分级流解吸、直接换热、增压换热等等。
级间冷却的工艺可以吸收一定的二氧化碳后冷却再回到塔中恢复吸收容量,然后再使用富液分级流的工艺利于再生塔中的再生过程。最后再用MVR工艺把能耗回收。
级间冷却+MVR热泵+分级流解吸的三种工艺结合可以降低总能耗20%。
浙江大学能源工程学院方梦祥教授团队通过200Nm3/h的实验设备结合以上技术、材料、和工艺可达成2.8GJ/tCO2的指标。
第四,中科院山西煤化所陆诗建教授团队开发了预处理碱洗旋流烟气脱水脱硫技术。
烟气构成很复杂,除了二氧化碳、氮气、氧气外还有二氧化硫等杂质气体,和重金属。二氧化硫进入吸收系统后首先与氨液反应,它的酸性比二氧化碳强并与氨液反应后在解吸塔的温度下无法解吸,因此溶液降解了。需要采用预处理技术的碱洗把氧化硫提前去除。
其次电厂、钢厂烟气的特点是50-60°C的饱和气,但进塔温度要求40°C,且过程中需要降温脱水。不排水的结果是在运行中将产生水雾并稀释溶液,所以预处理也可以调节水平衡。
最后吸收过程中也含有氨气、亚硝胺、气溶胶等环境污染物,多级水洗等工艺也在开发中。
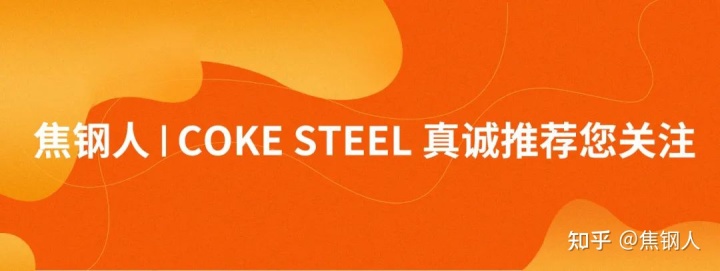
焦钢人CokeSteel
问:2023年锅炉价格/多少钱?
