Si3N44703.7-4.5热压法玻璃-陶瓷2002.0石英玻璃60013.3.1.3陶瓷纤维(晶须)与陶瓷基体复合过程中的匹配原则大量实验表明:要制备高强
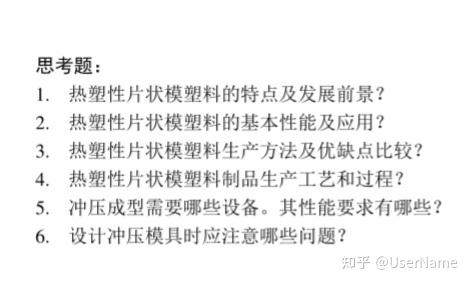
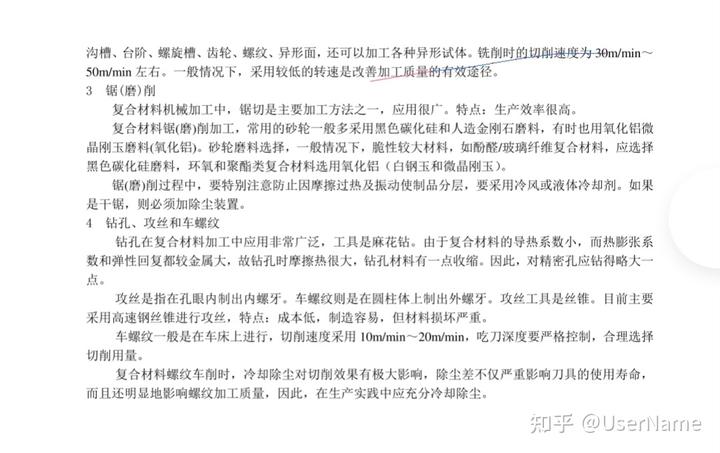
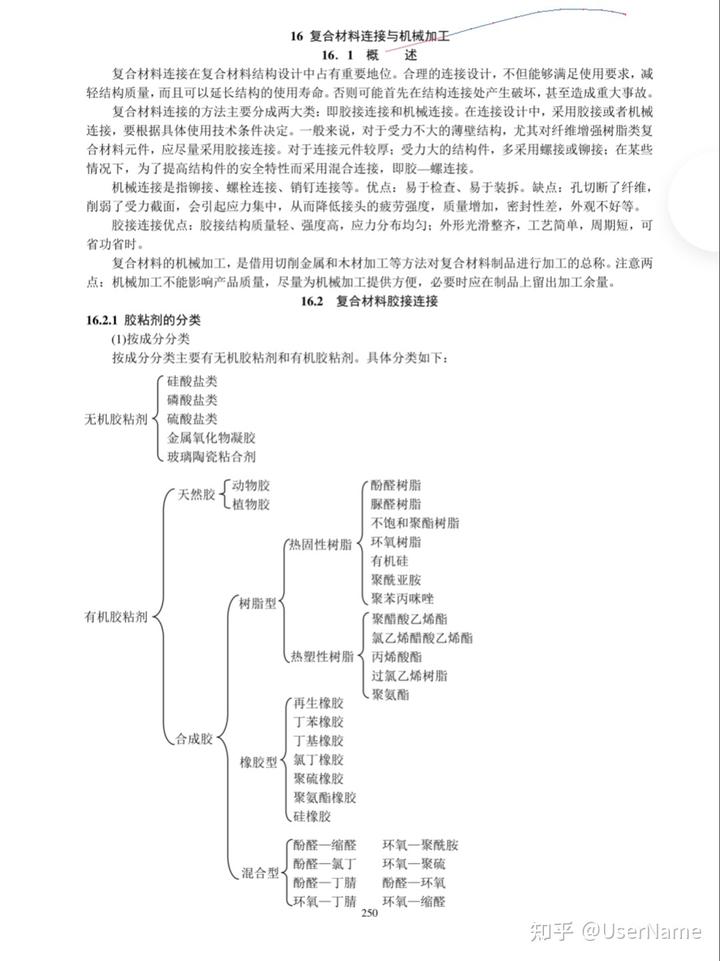
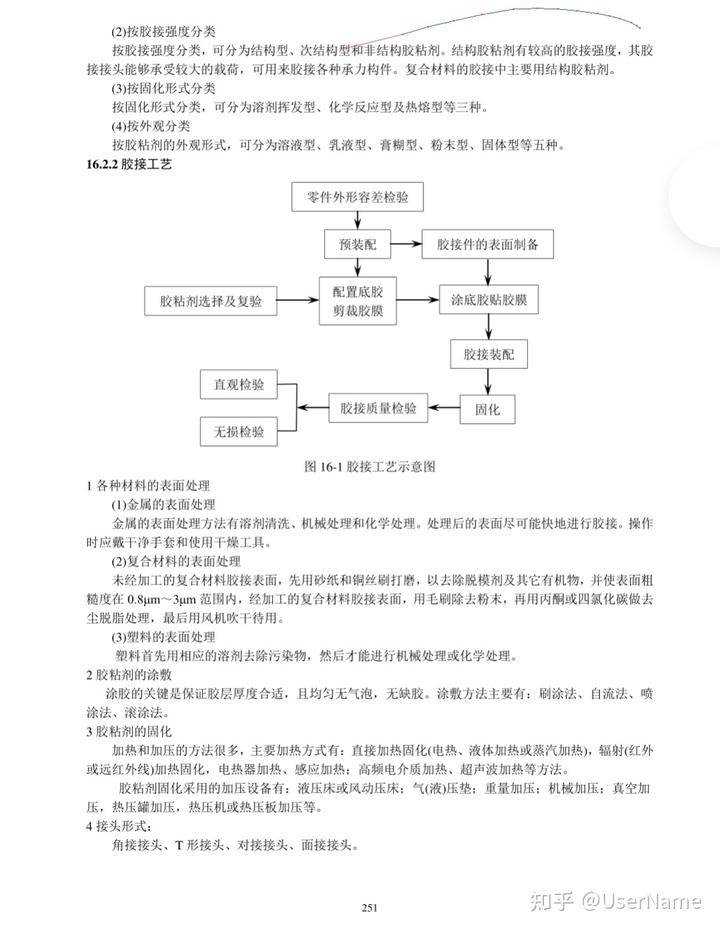
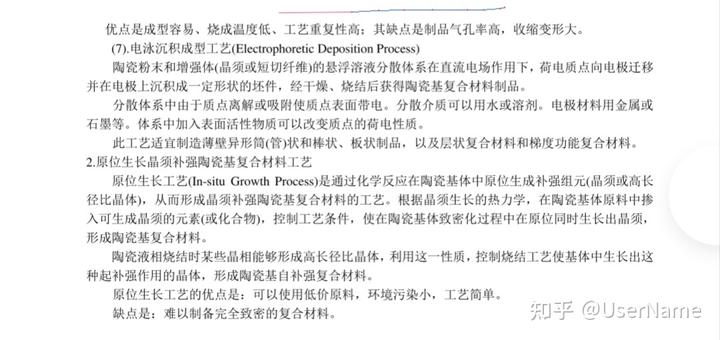
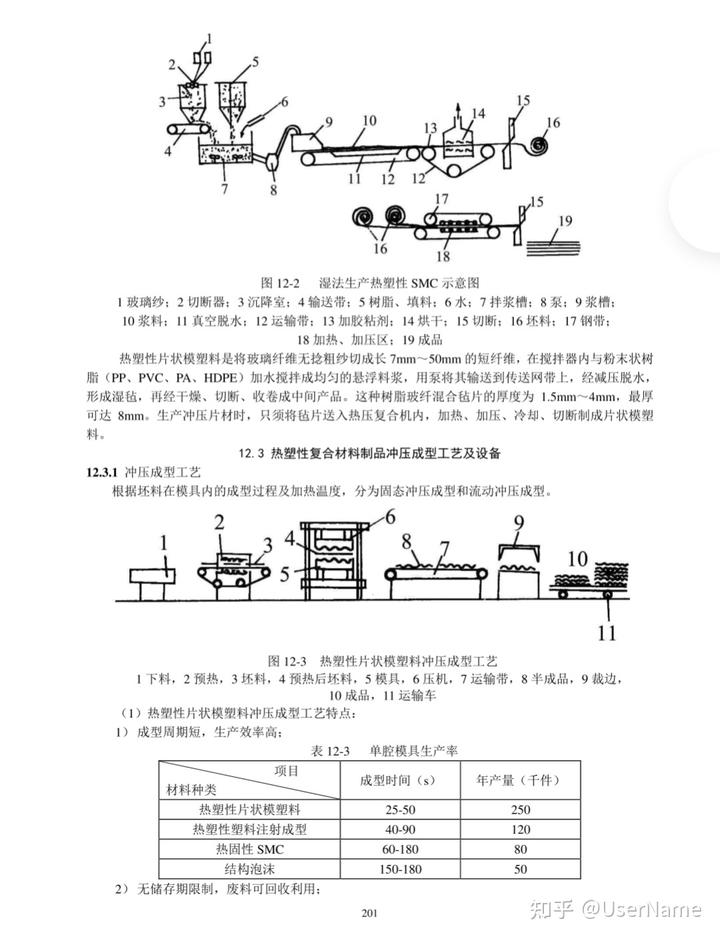
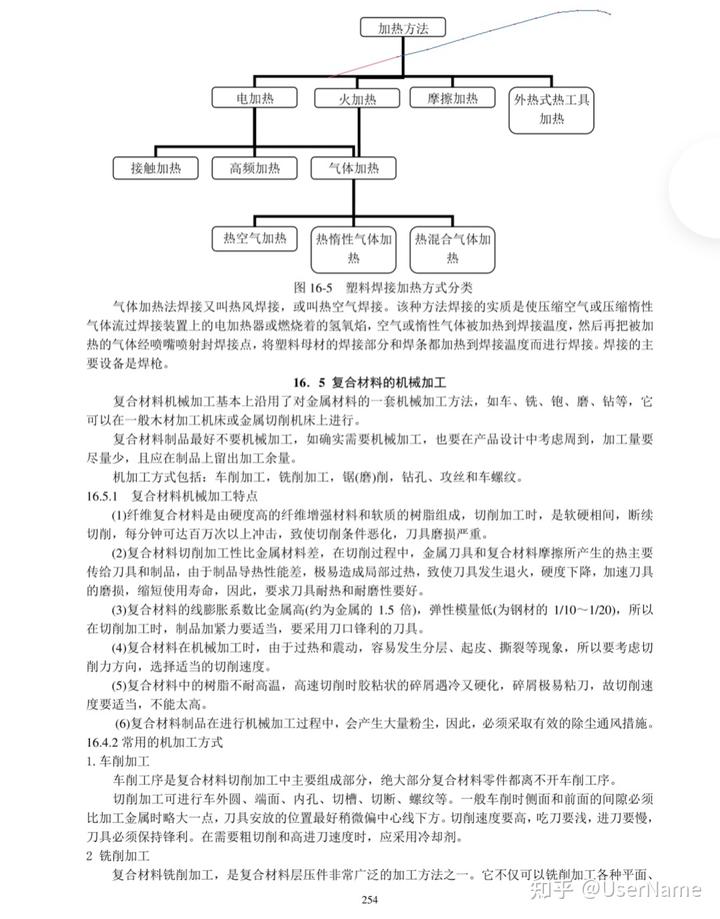
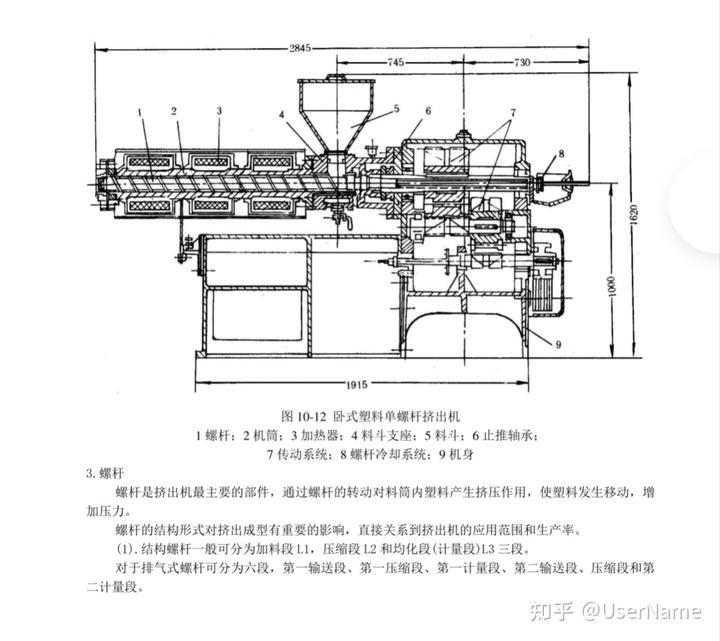
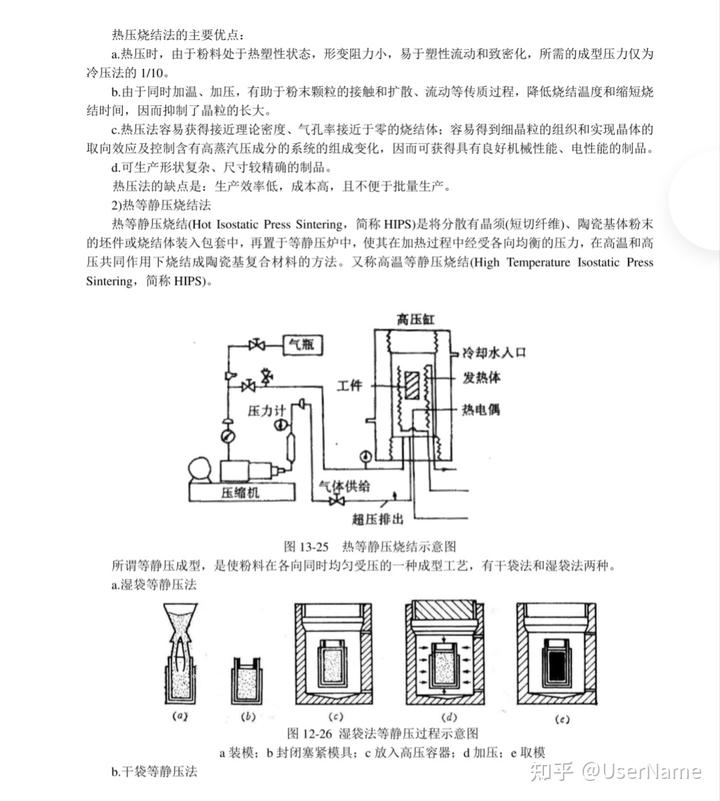
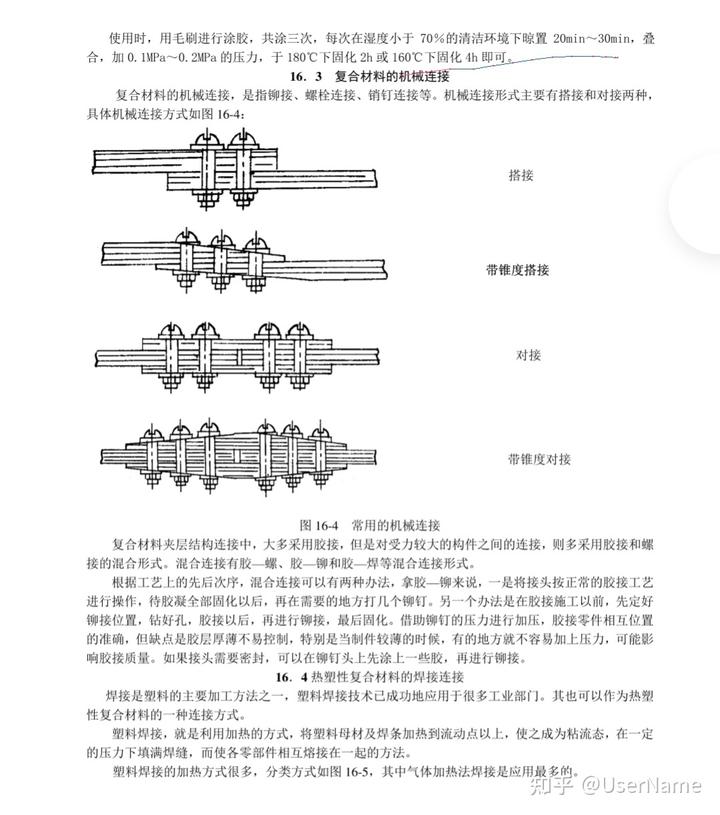
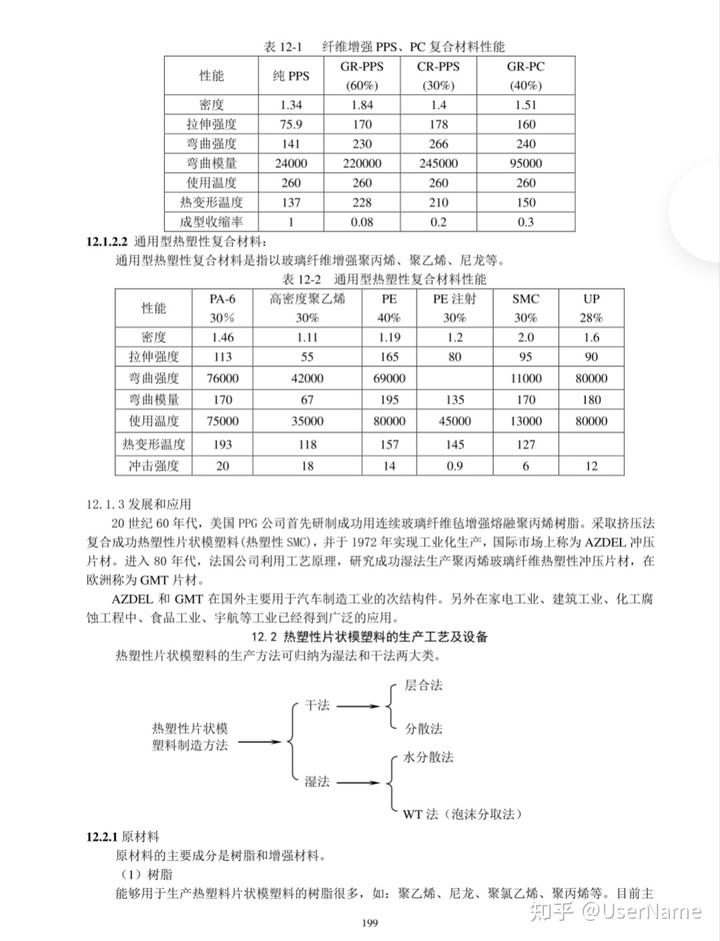
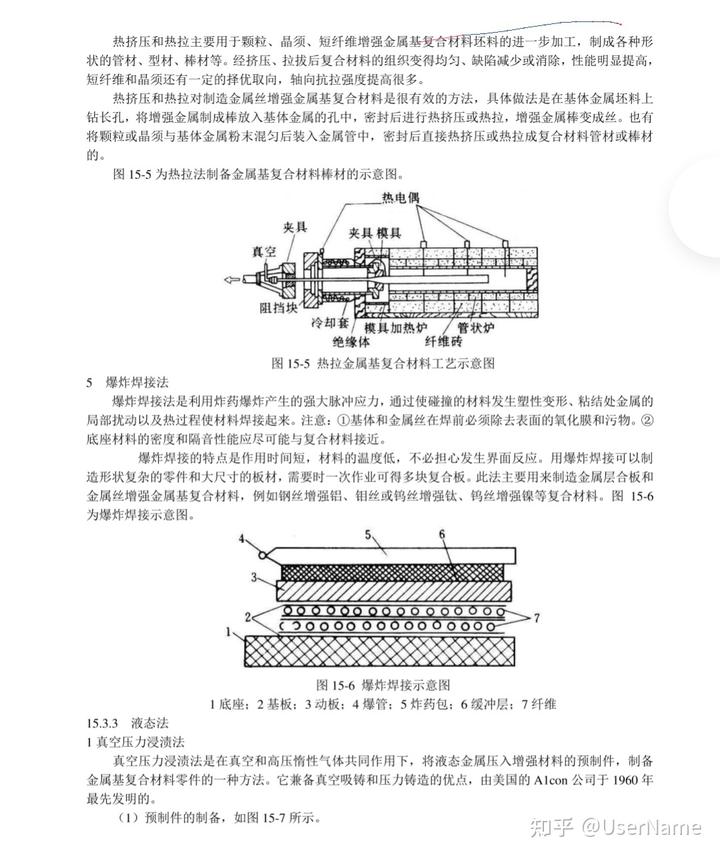
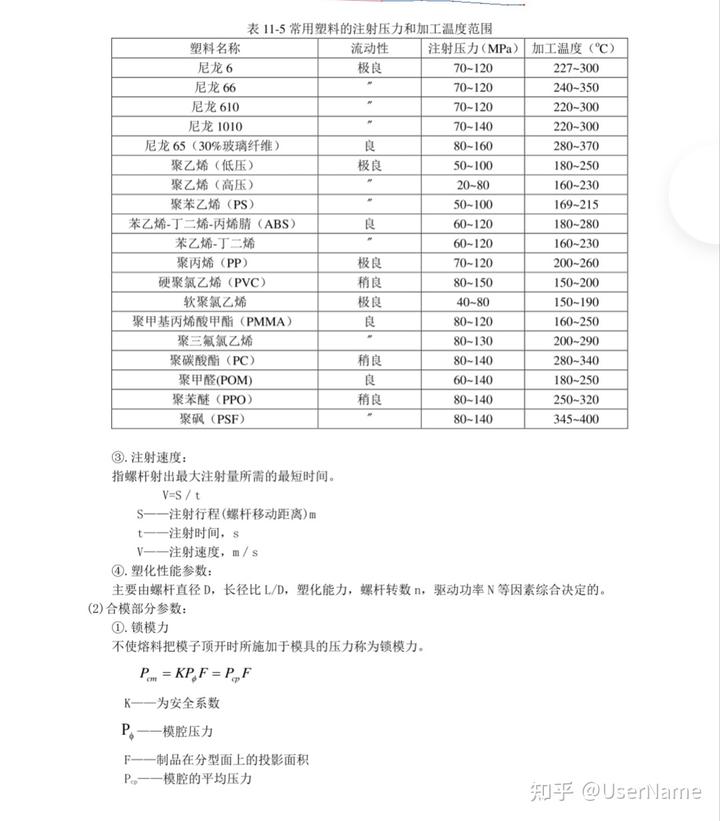
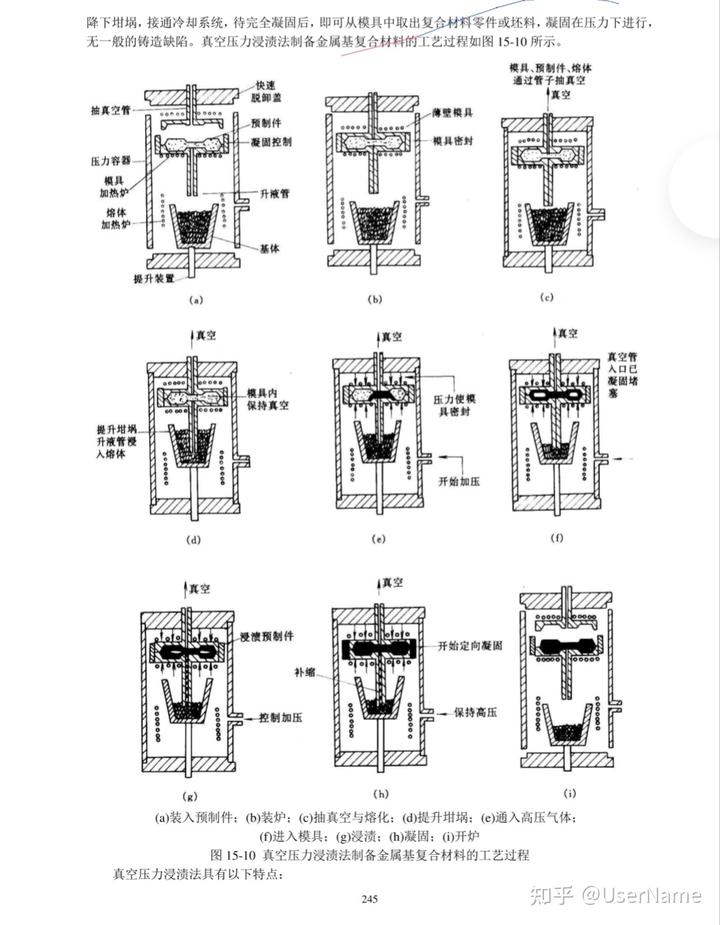
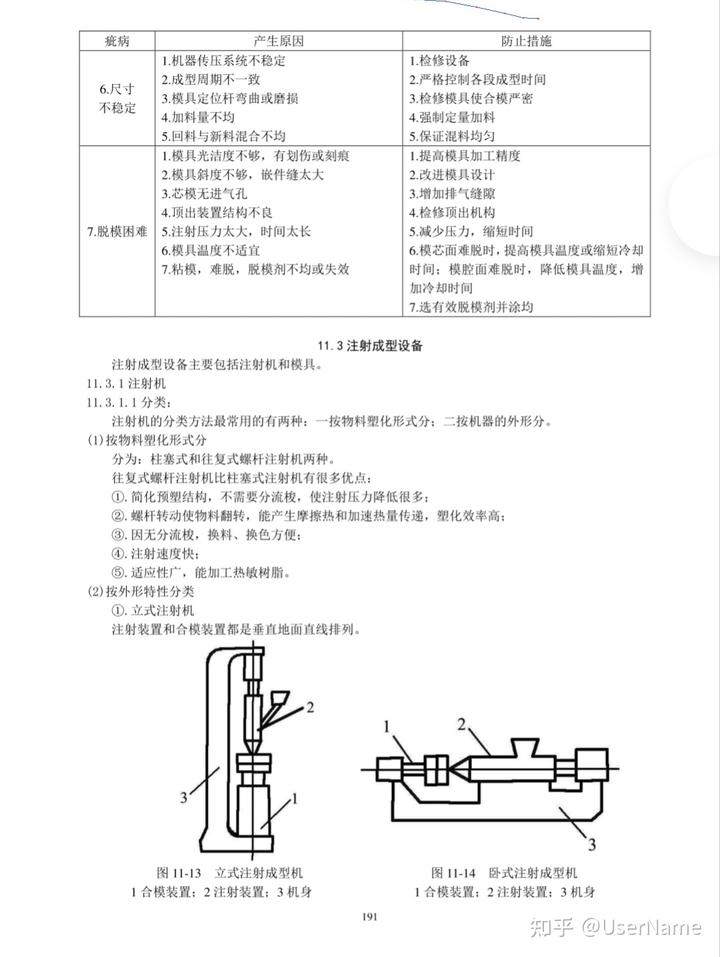
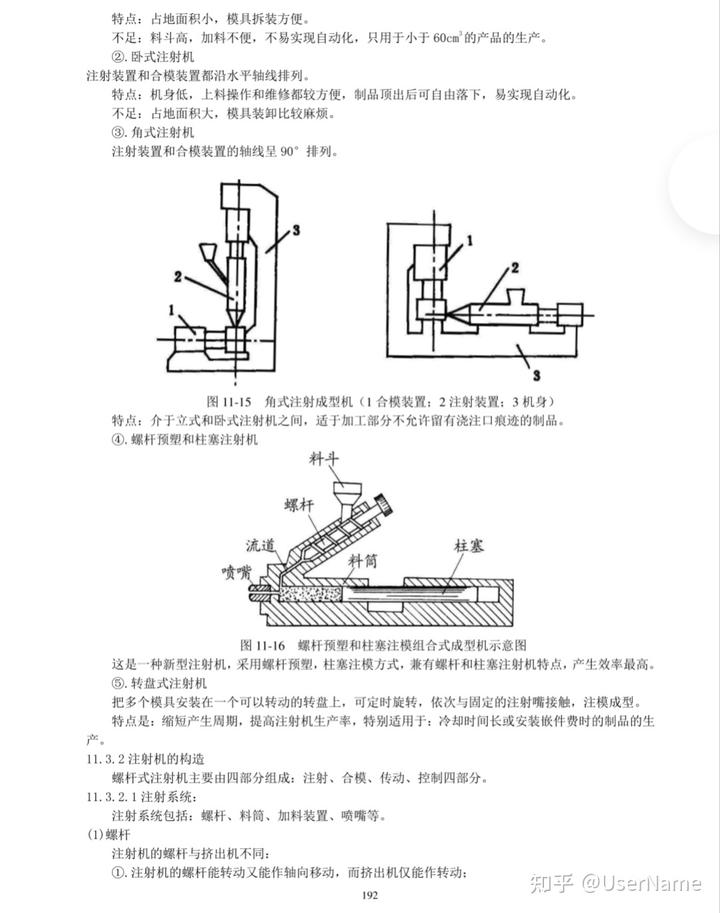
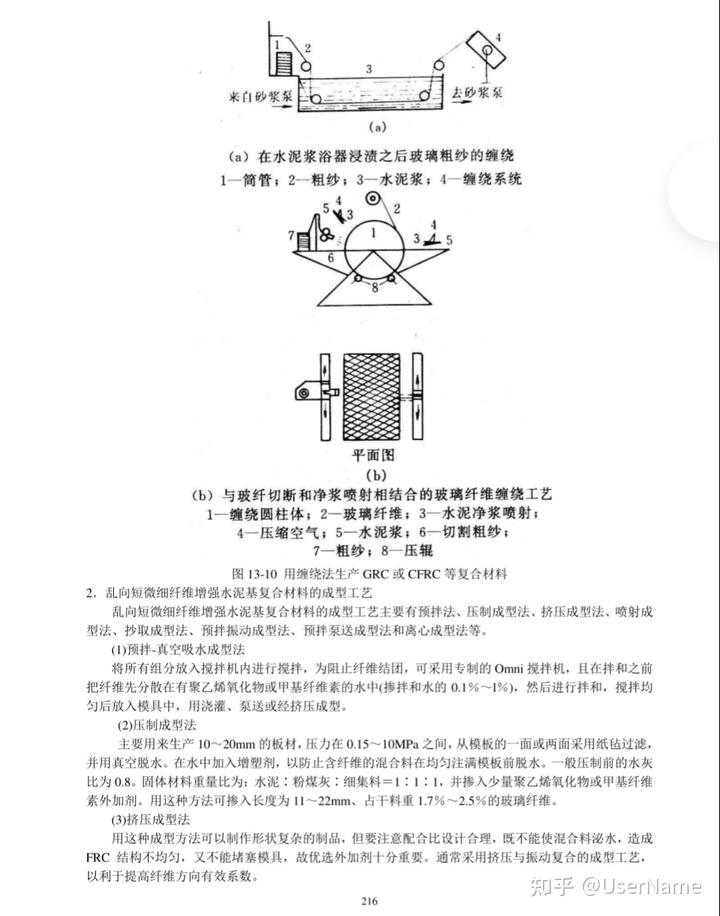
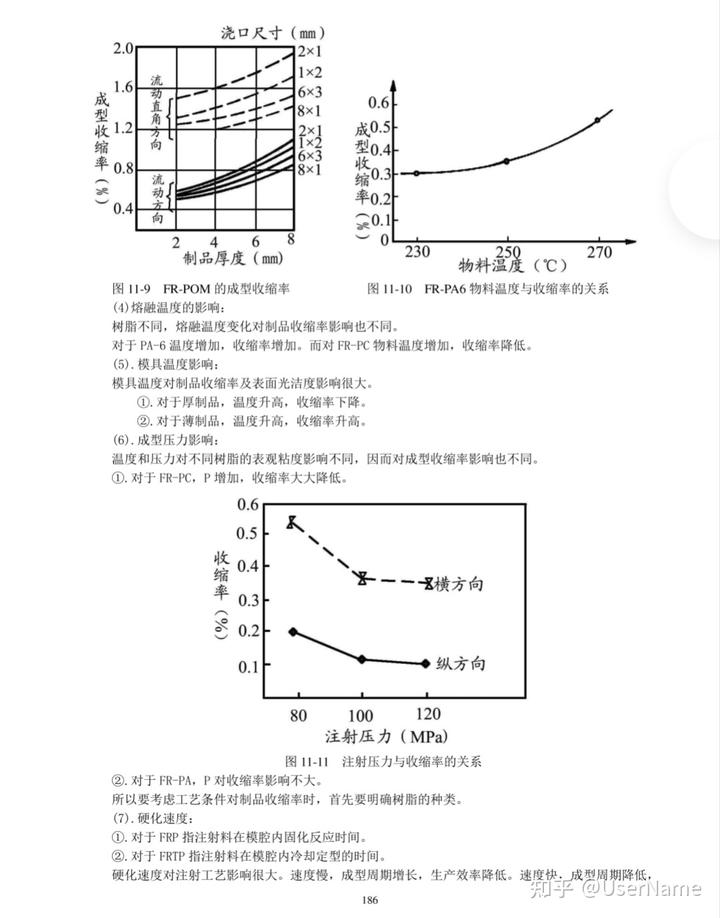
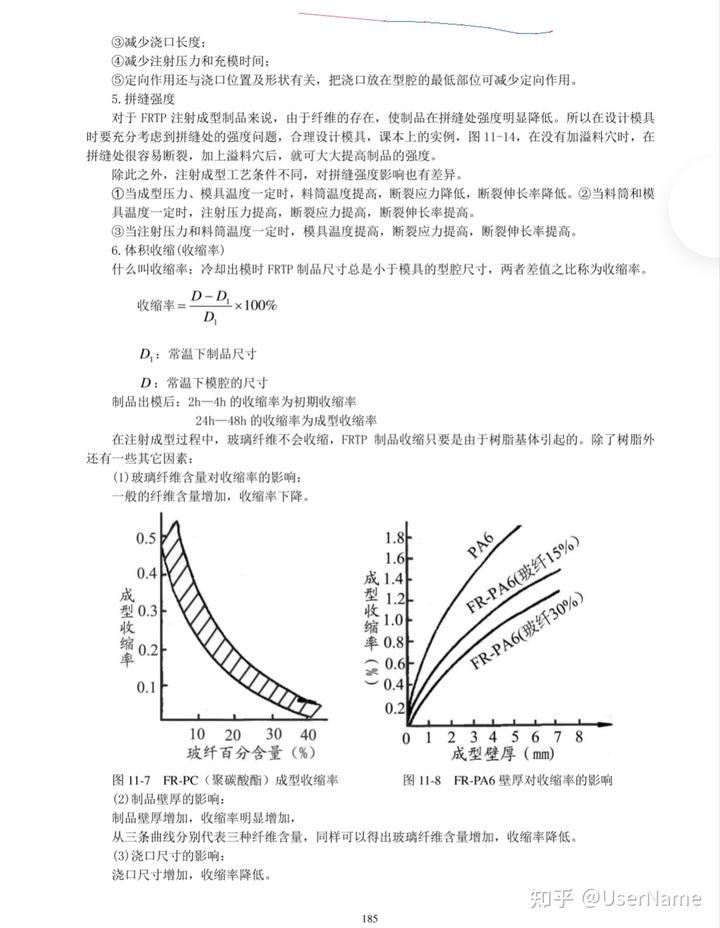
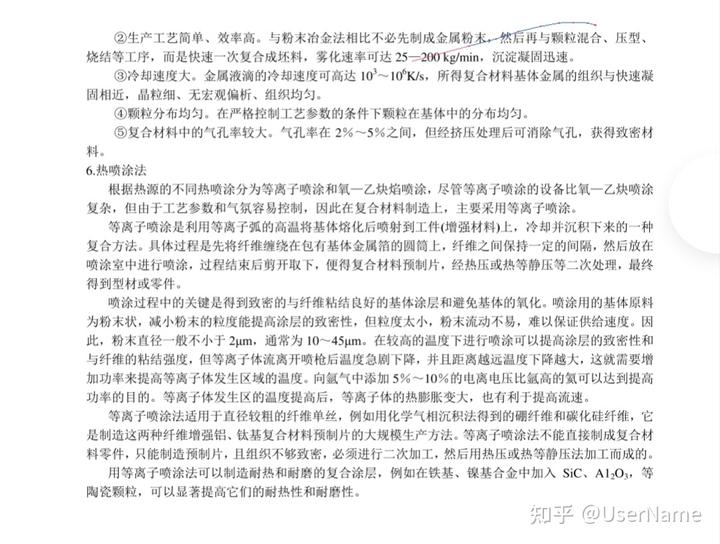
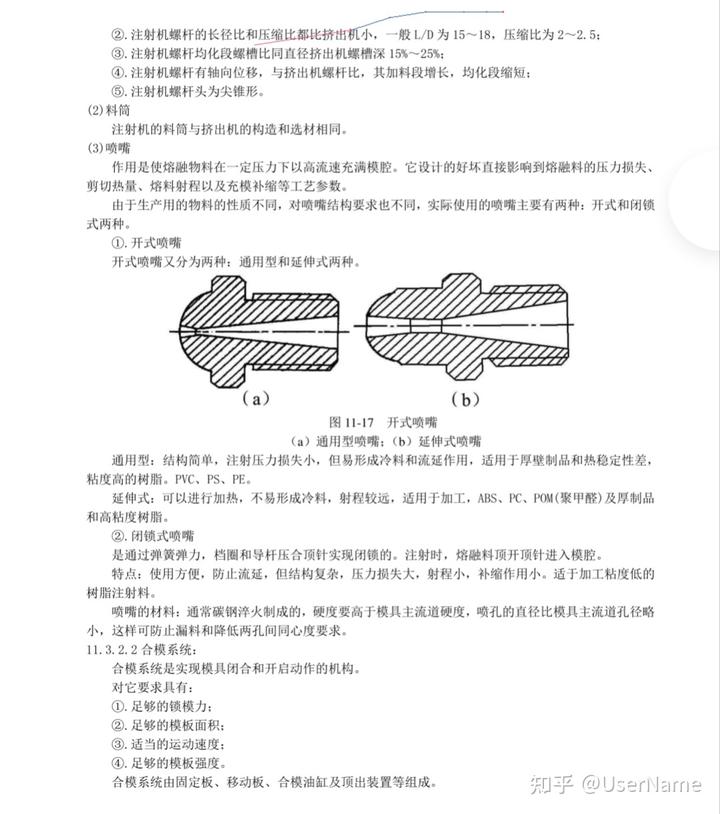
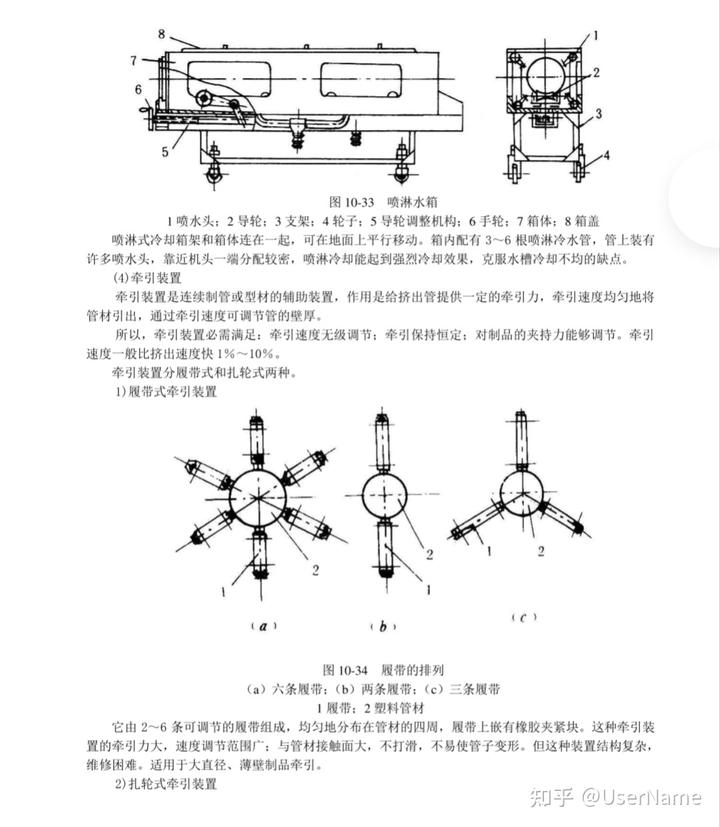
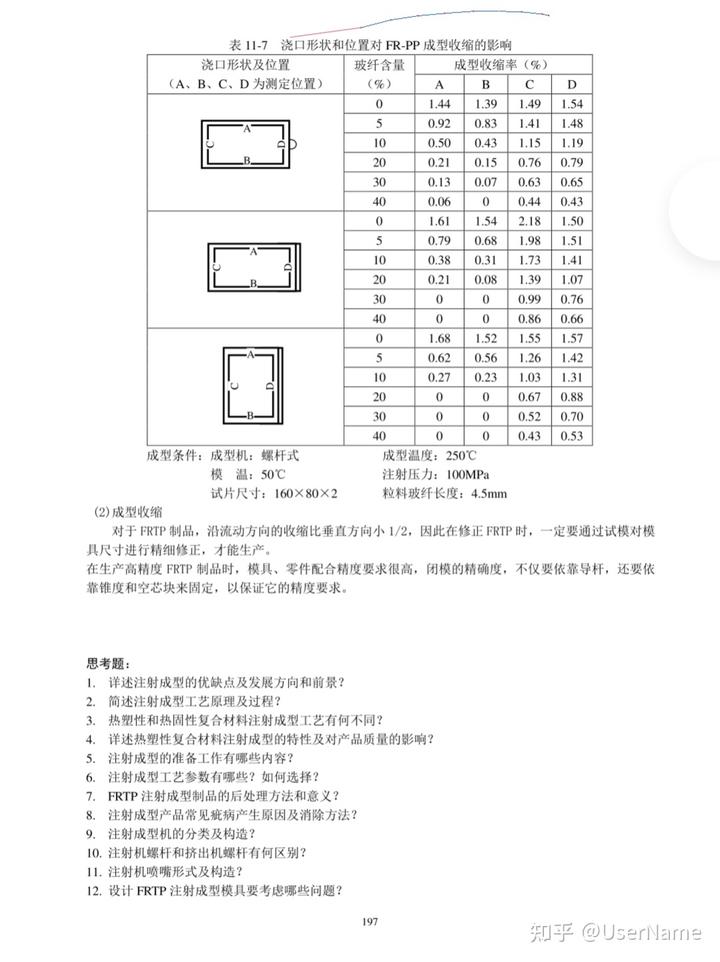
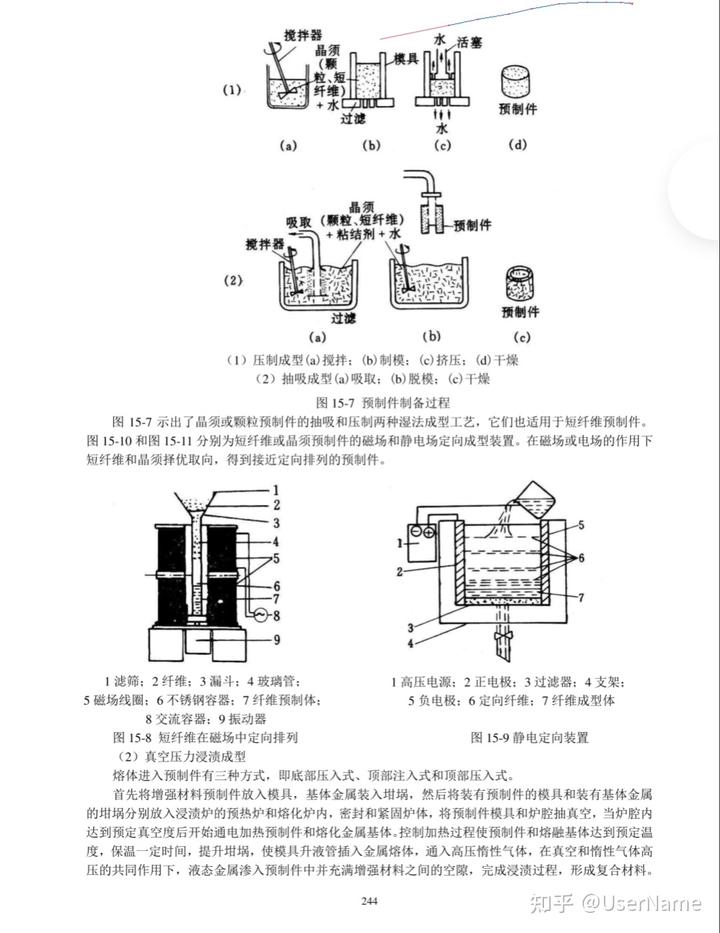
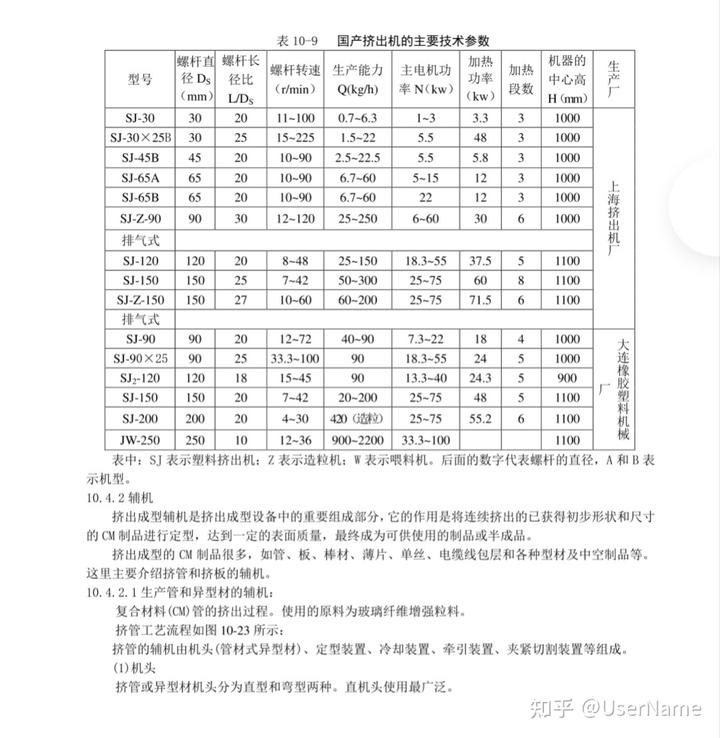
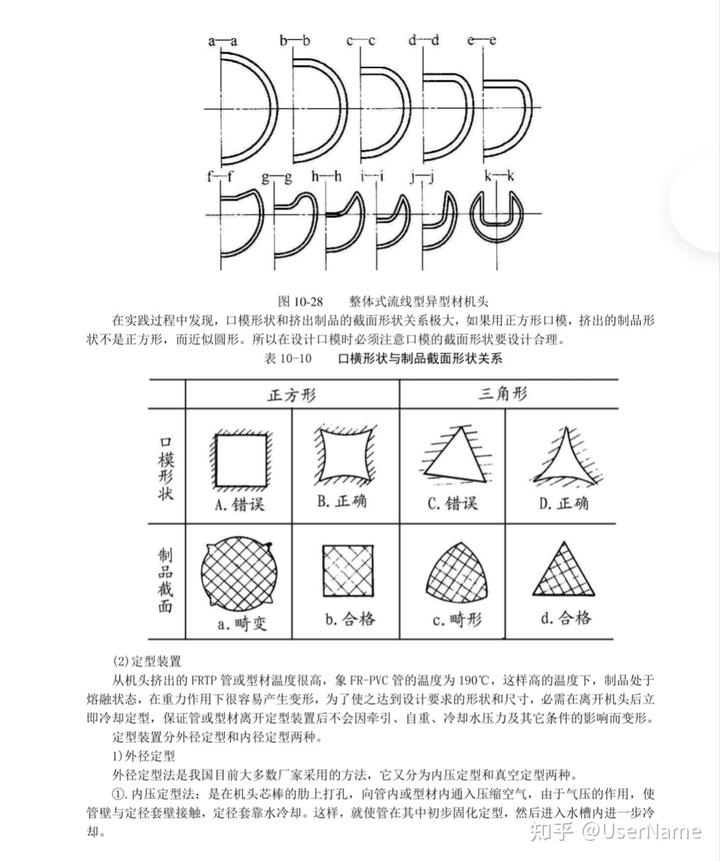
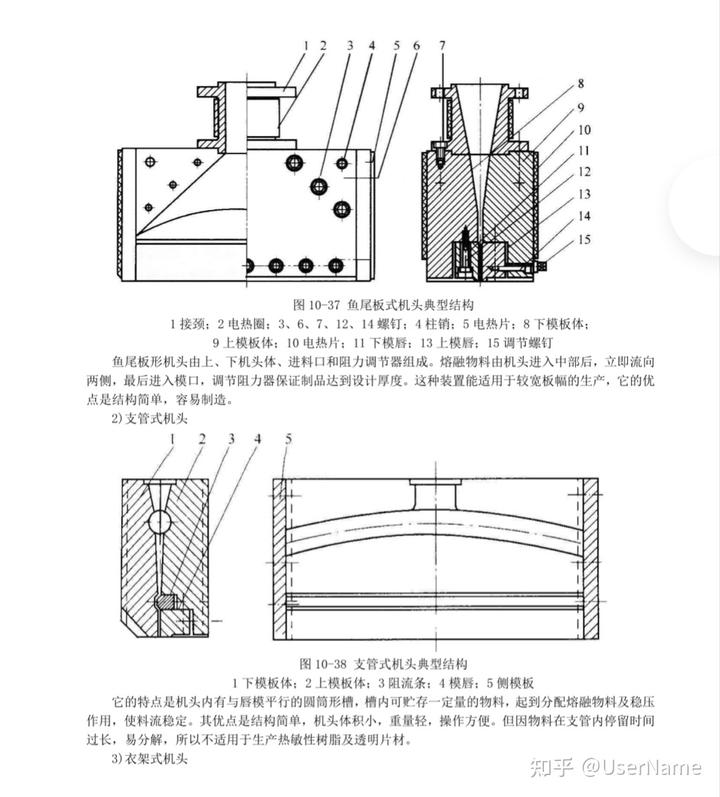
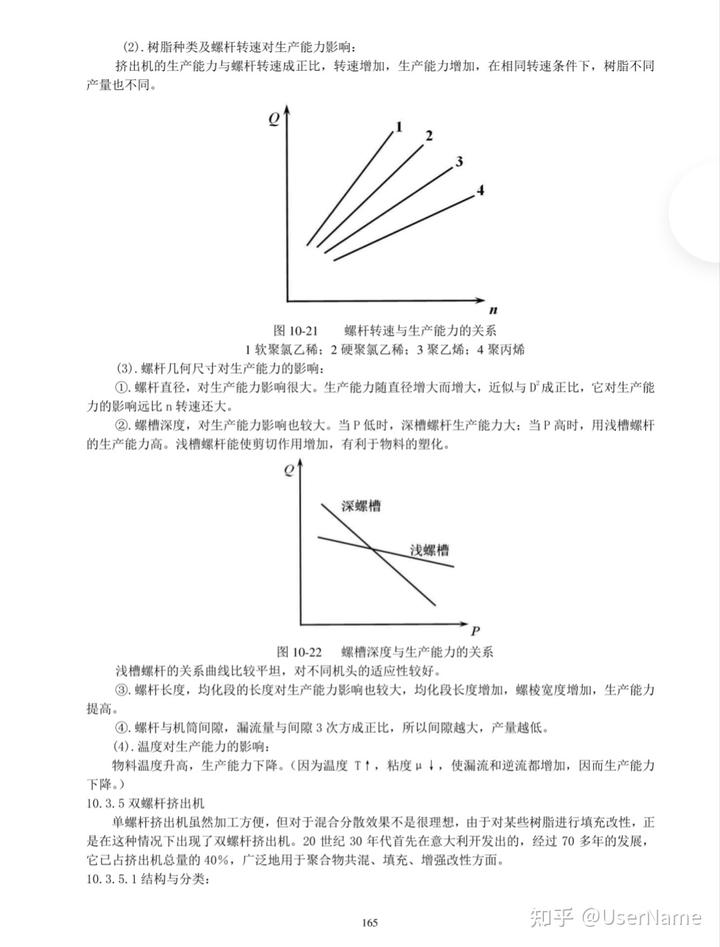
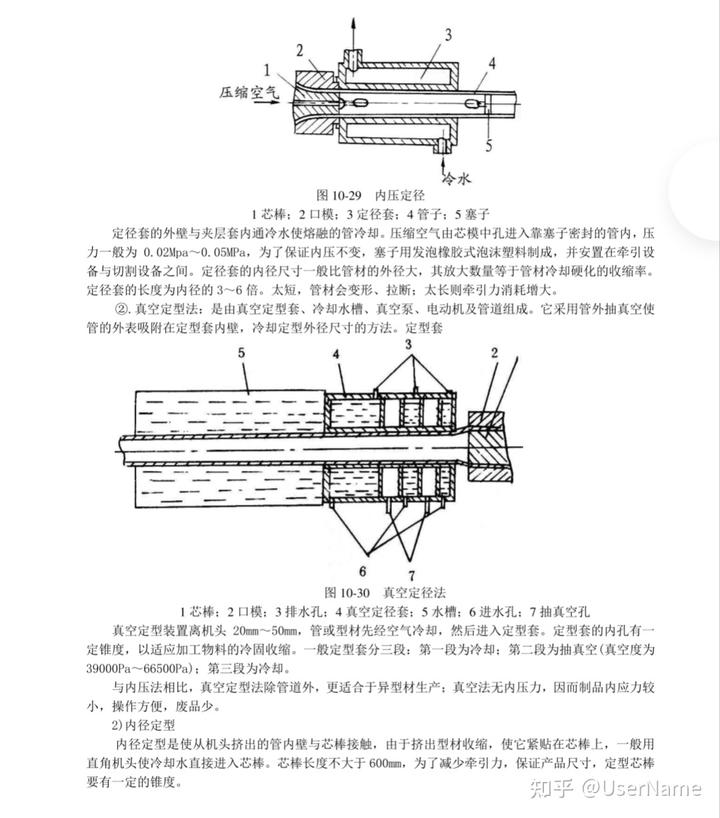
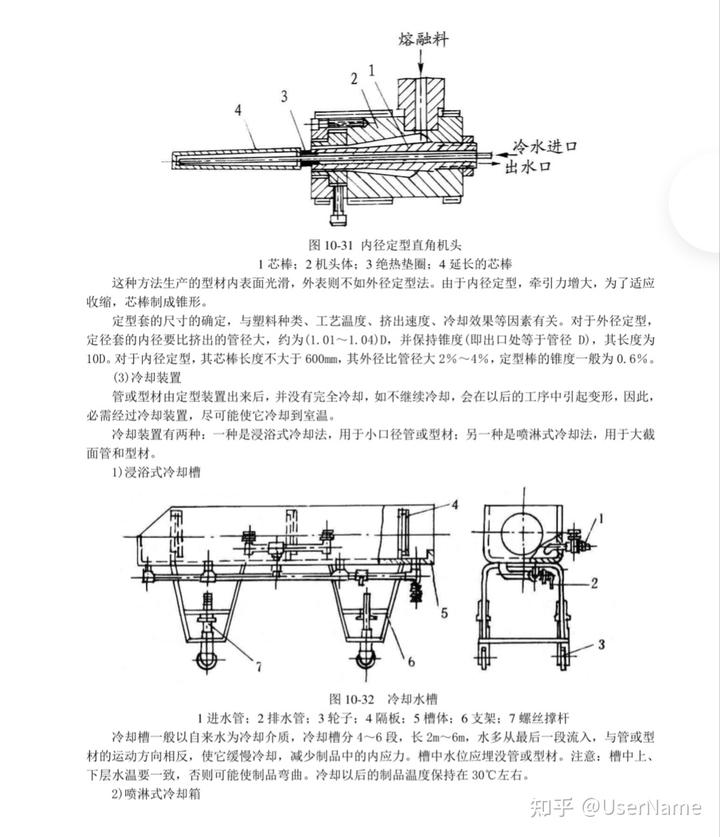
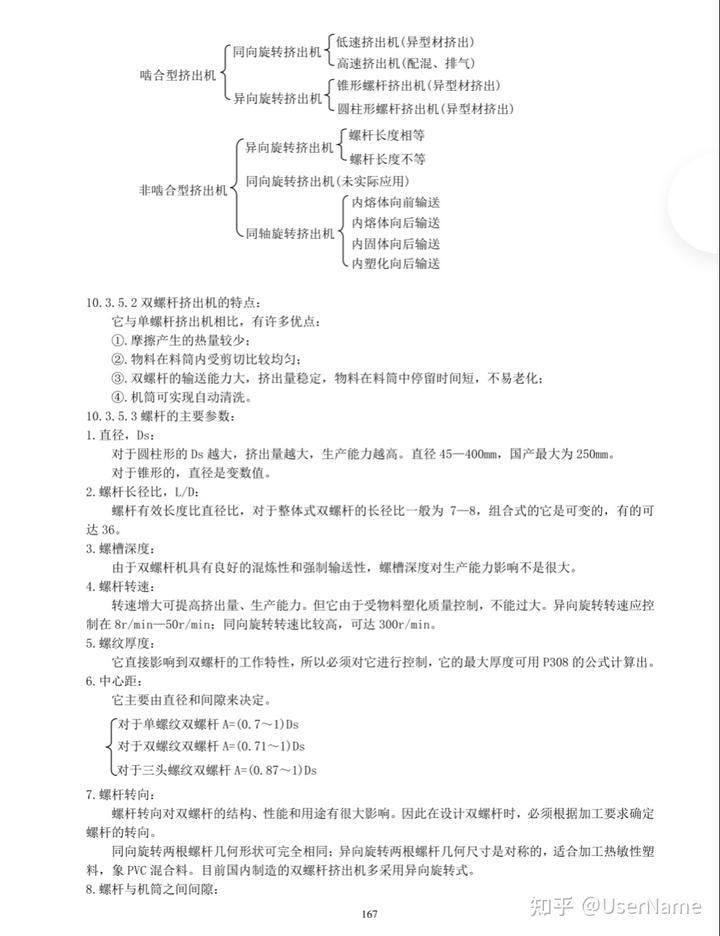
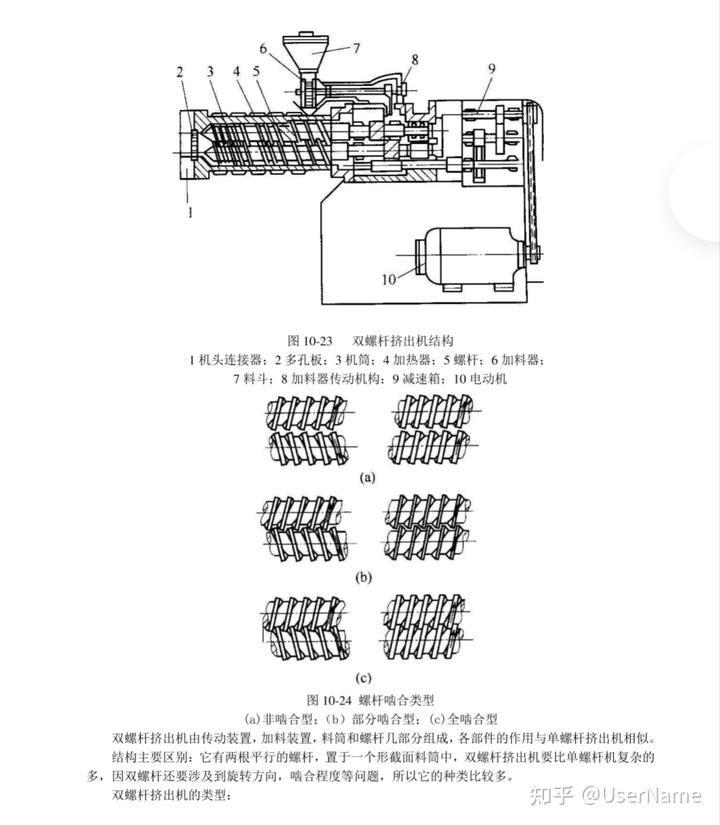
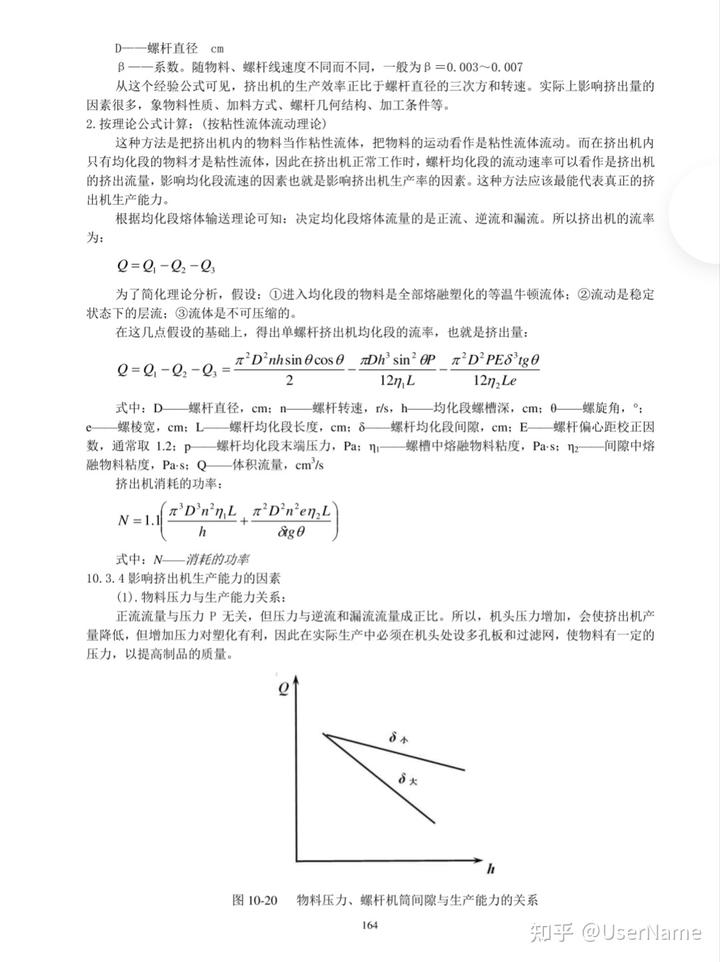
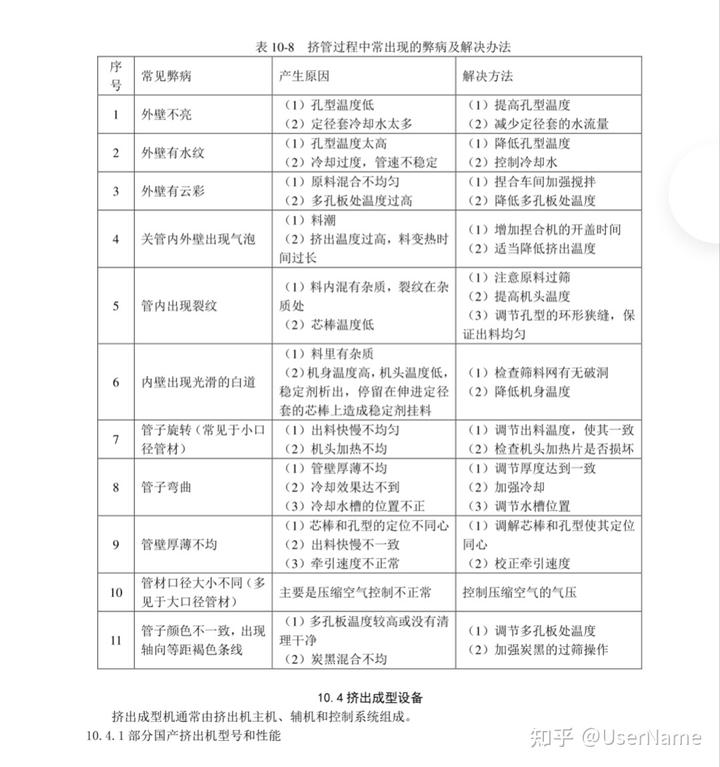
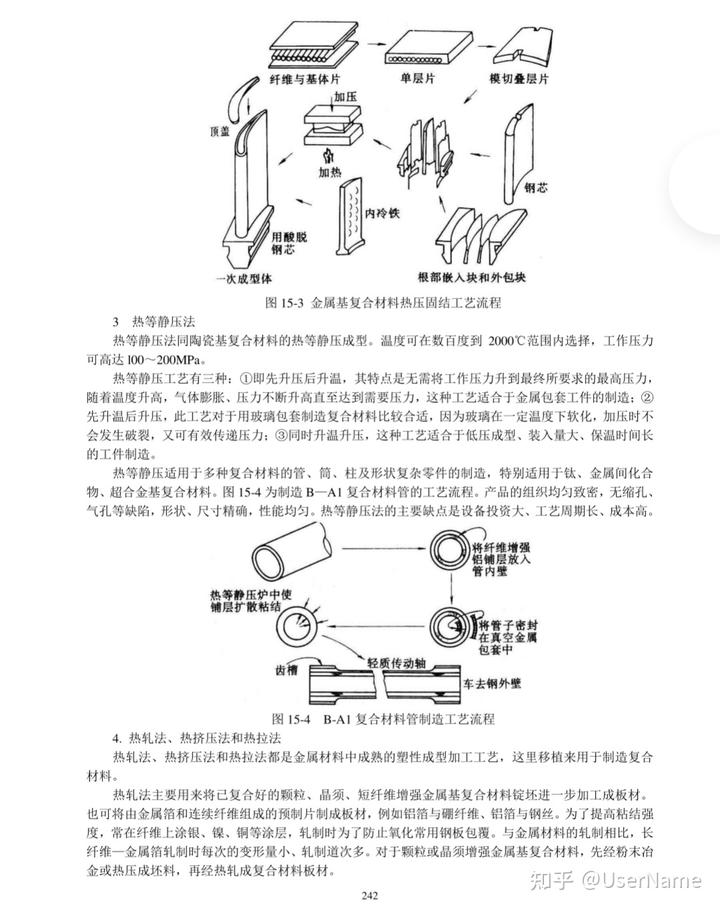
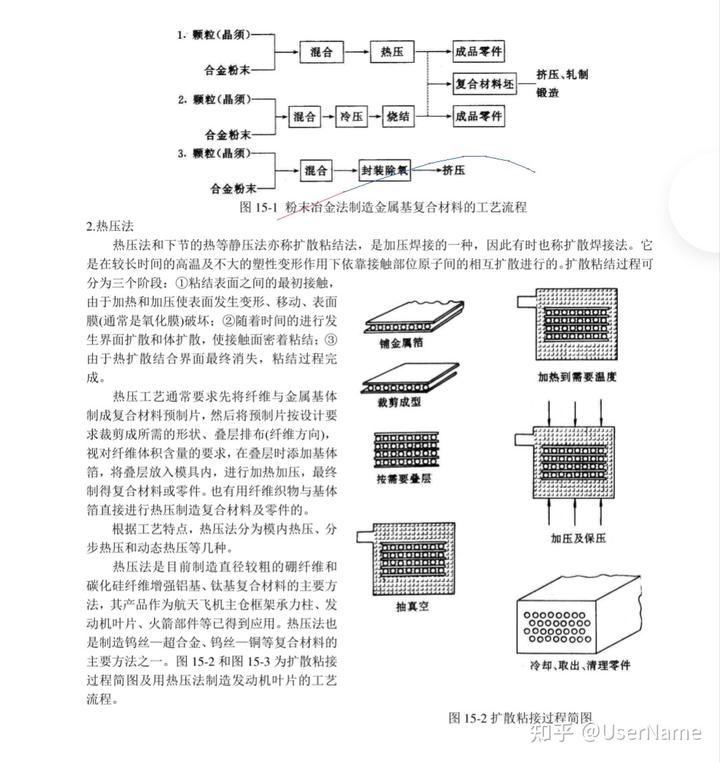
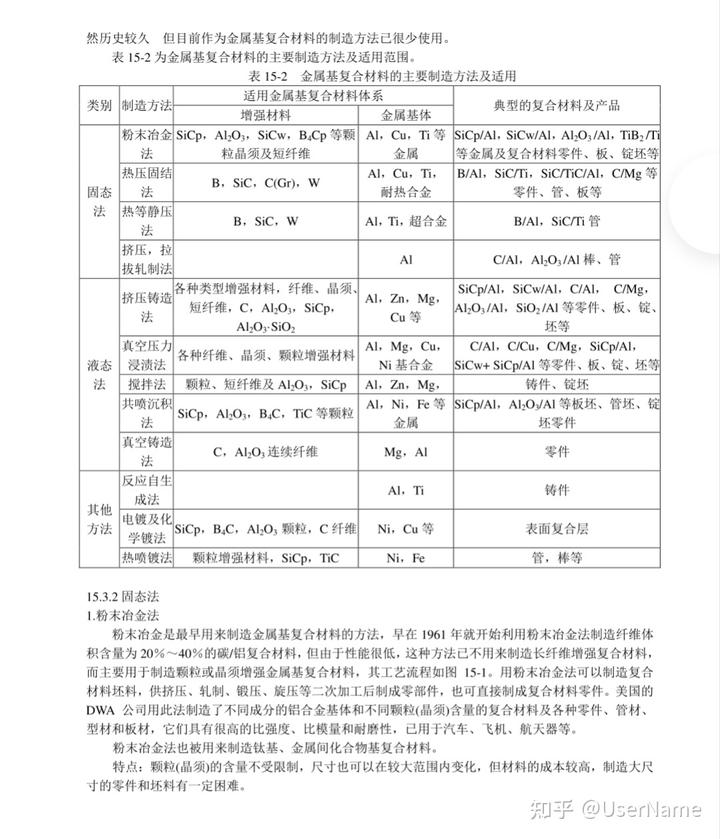
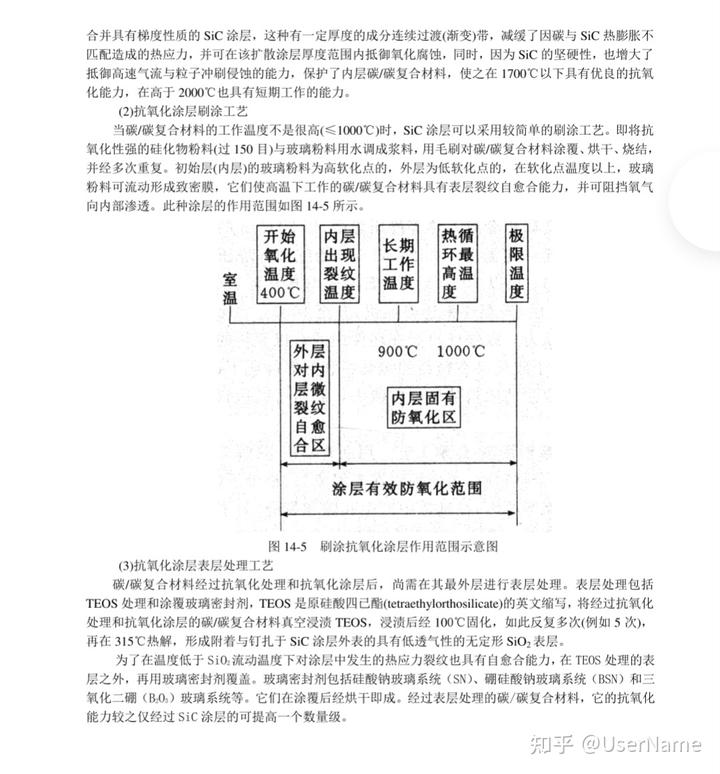
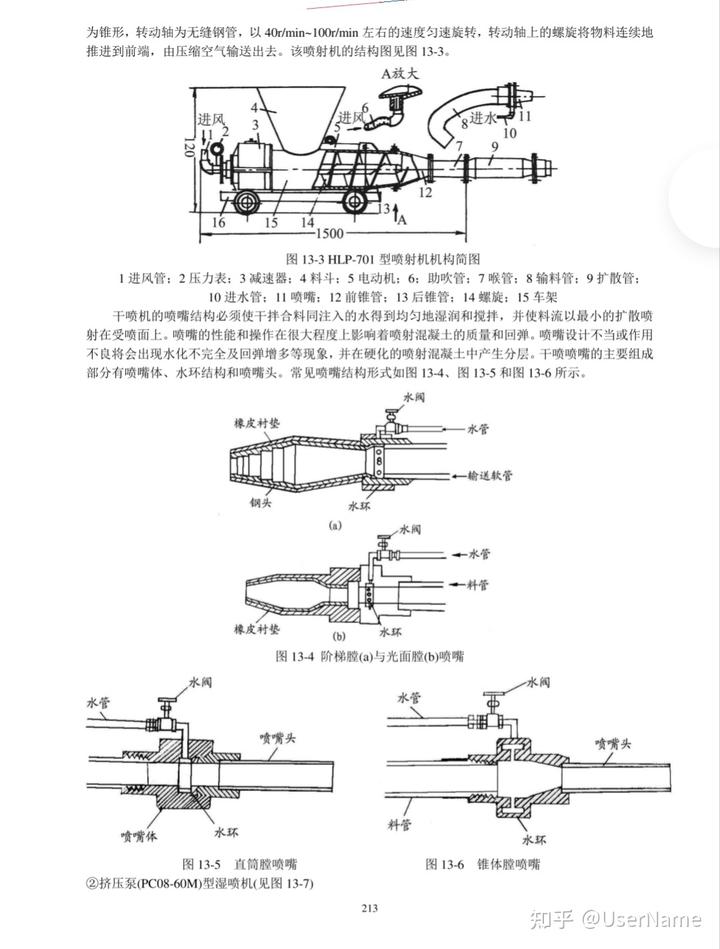
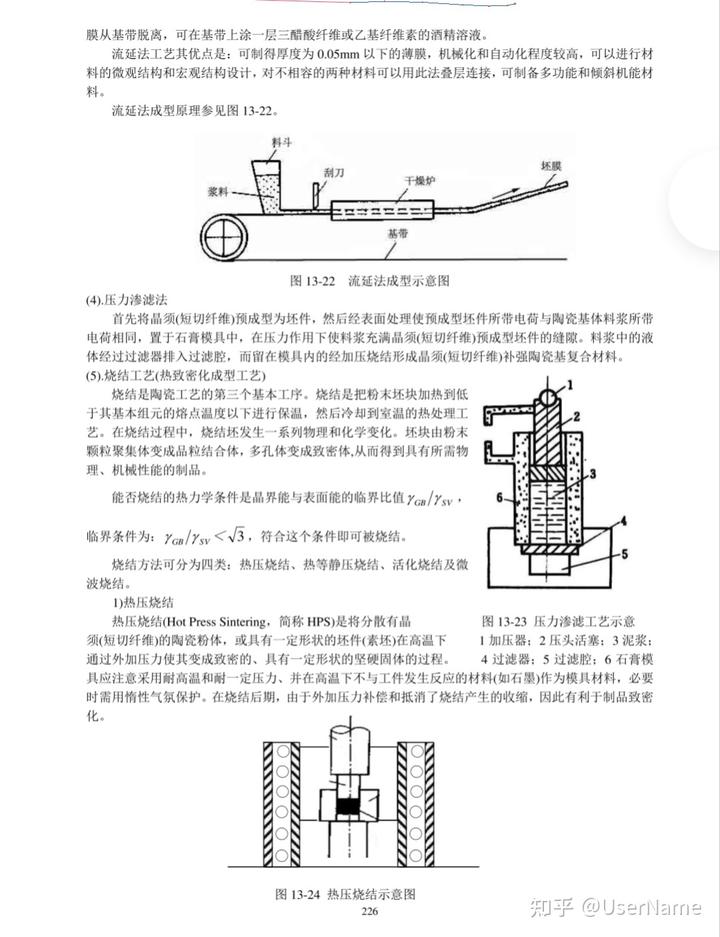
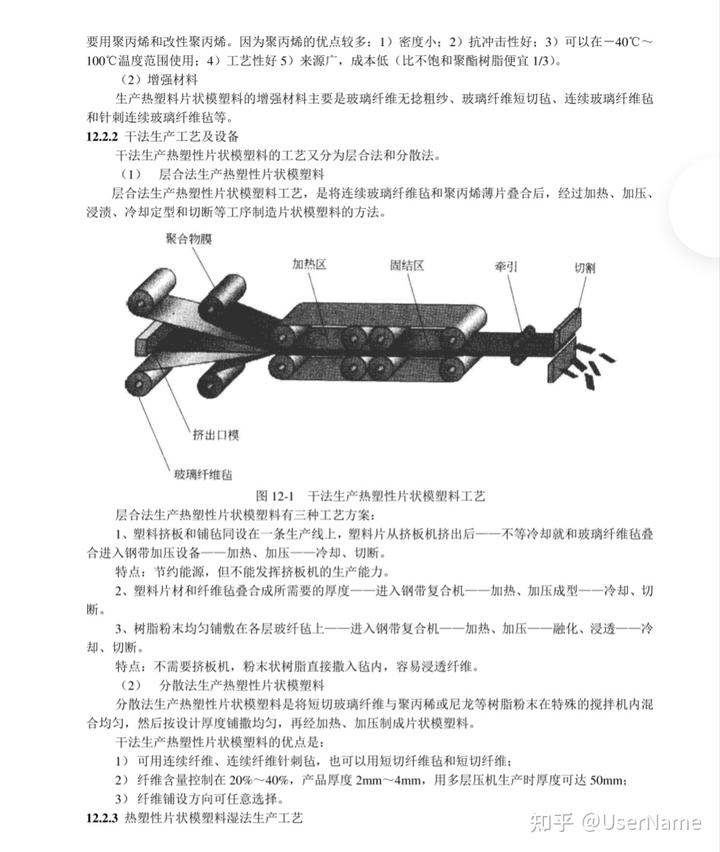
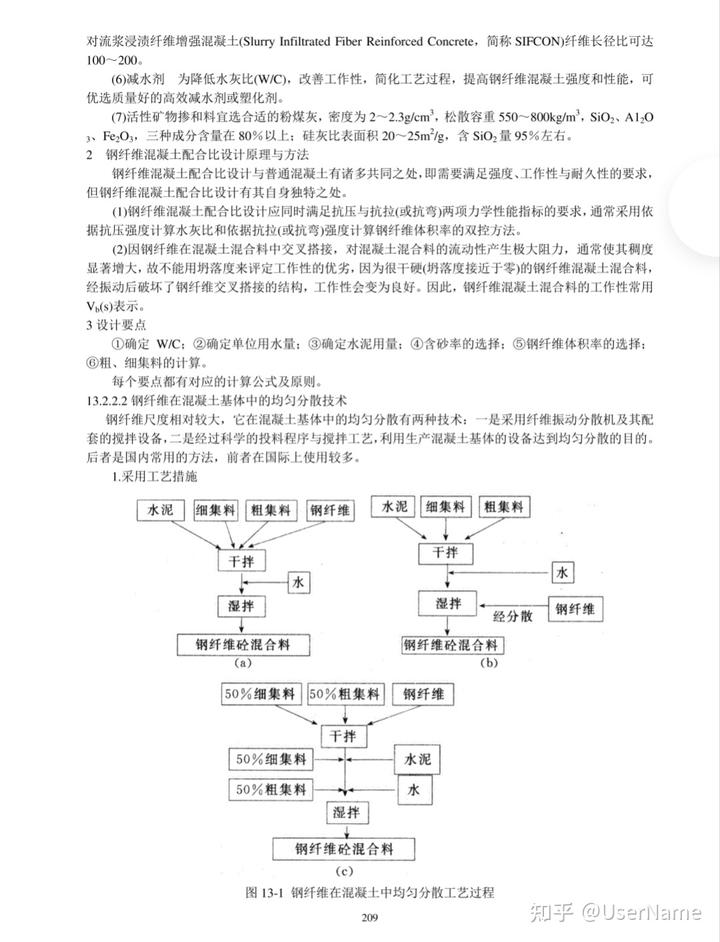
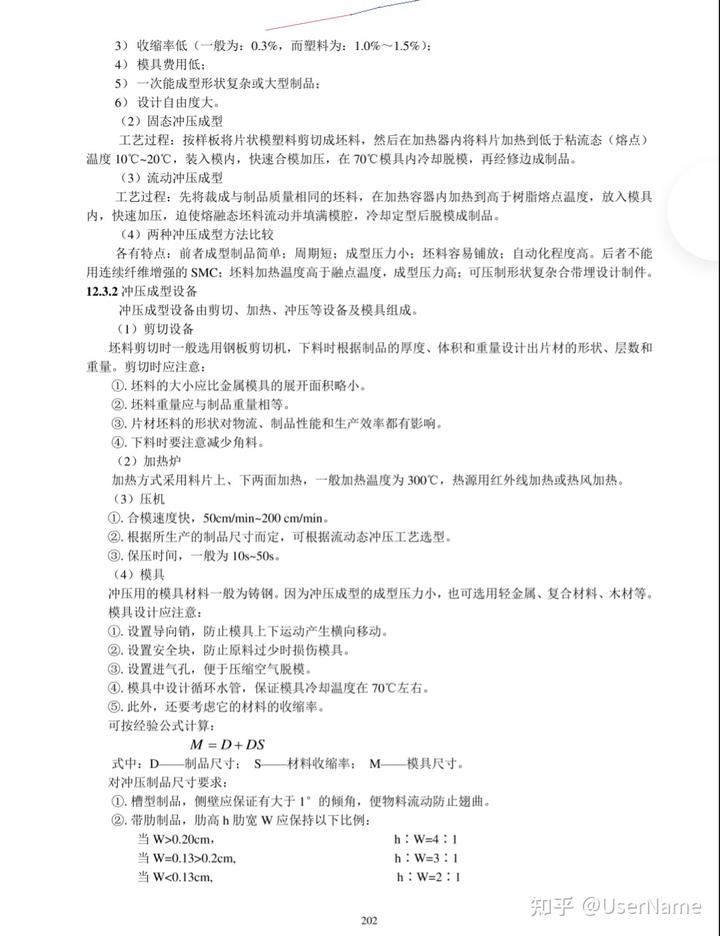
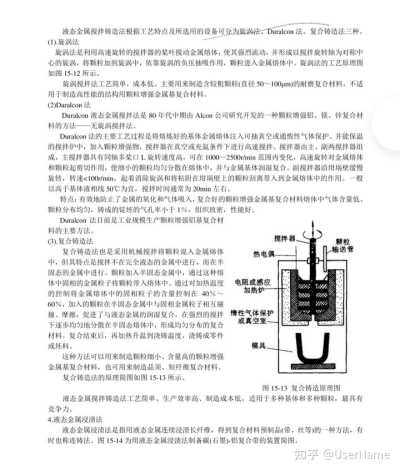
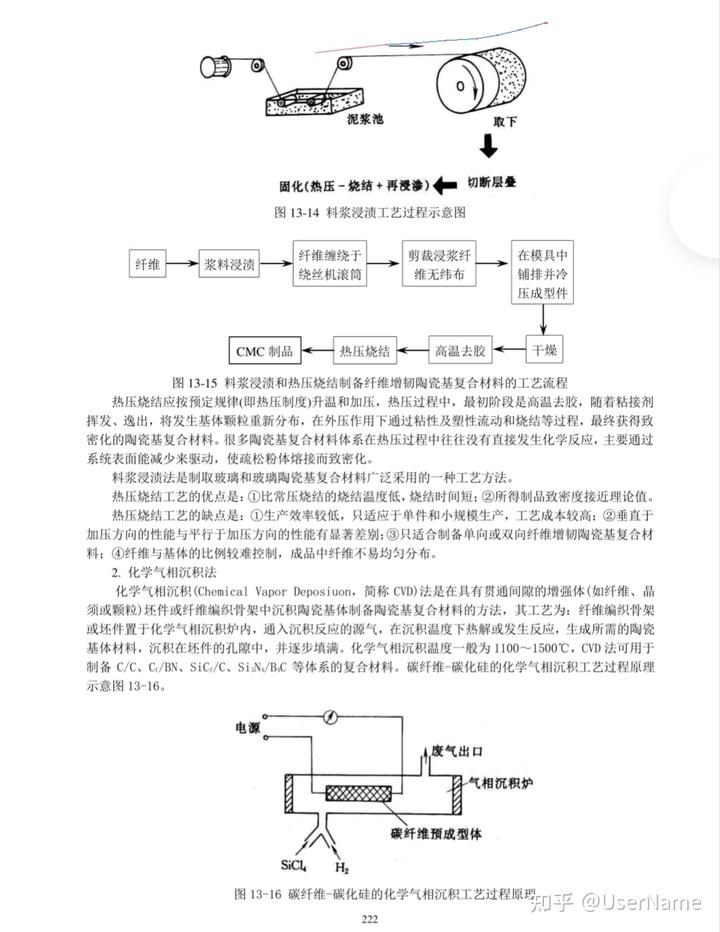
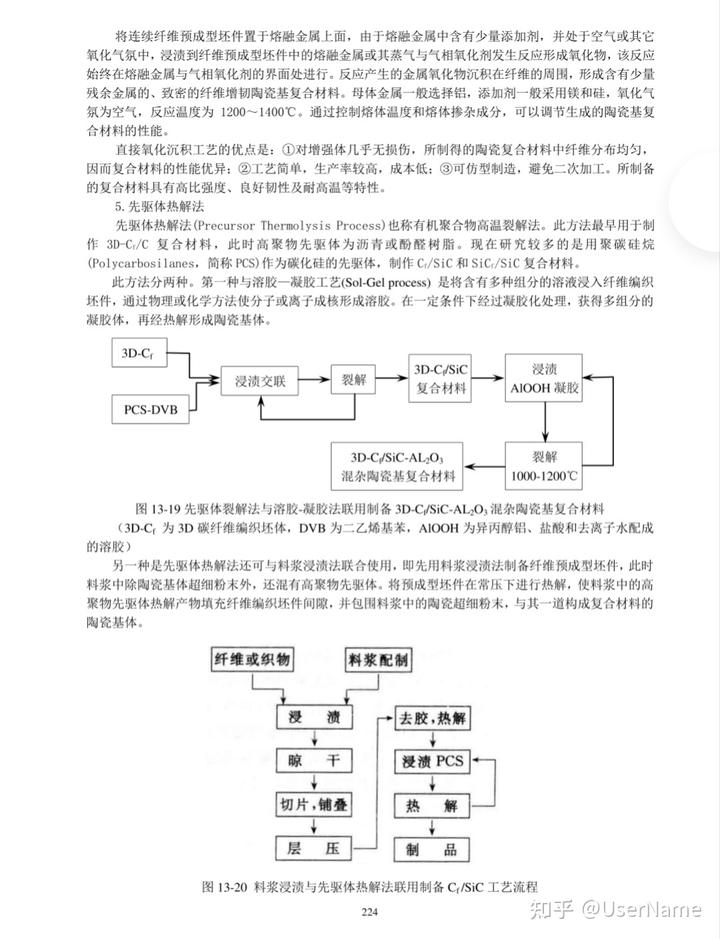
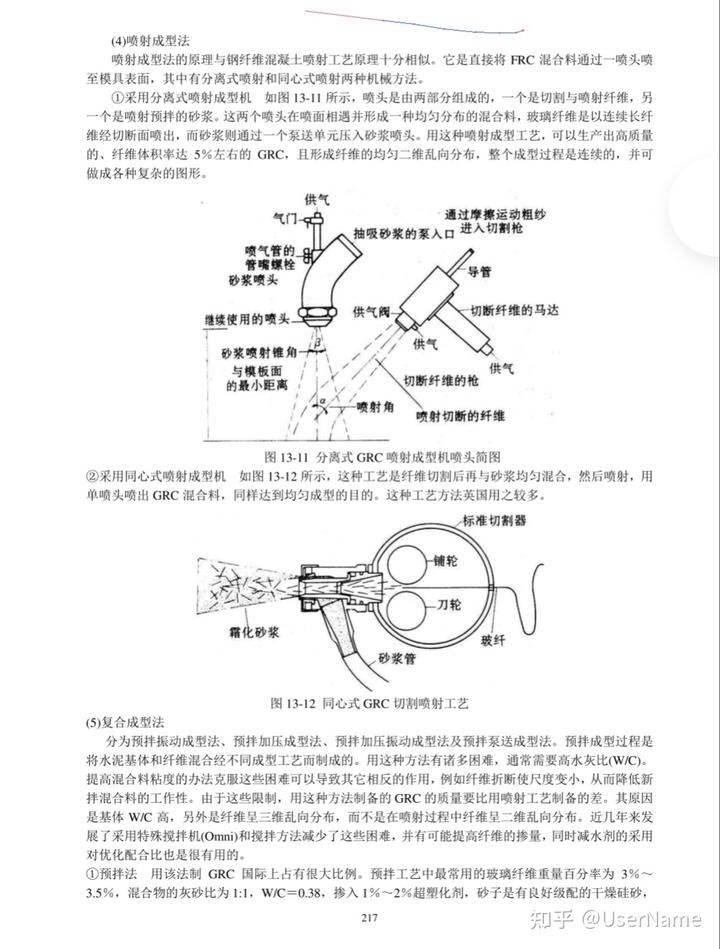
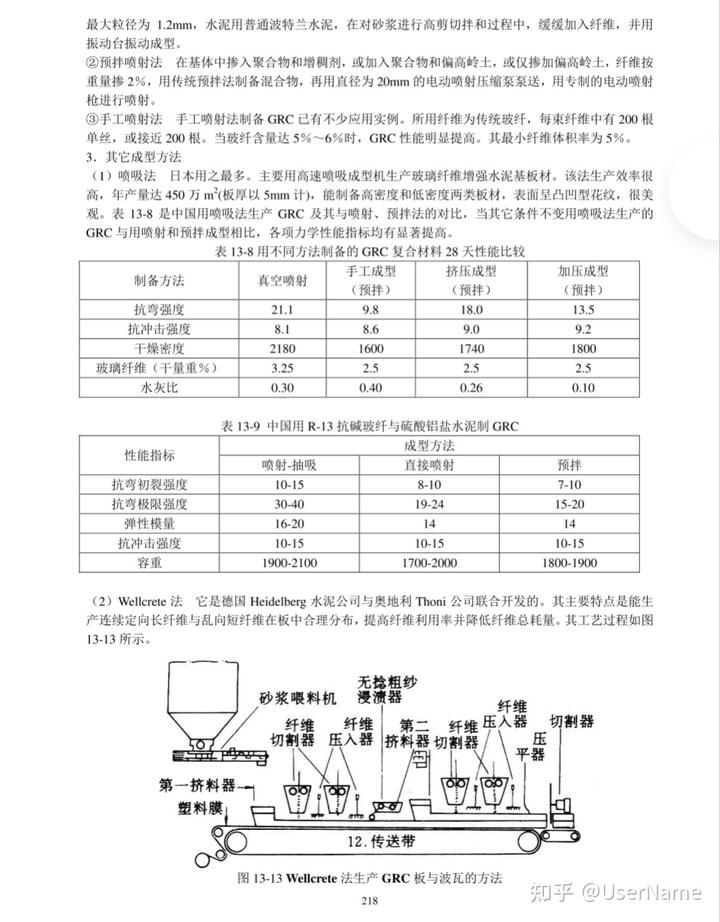
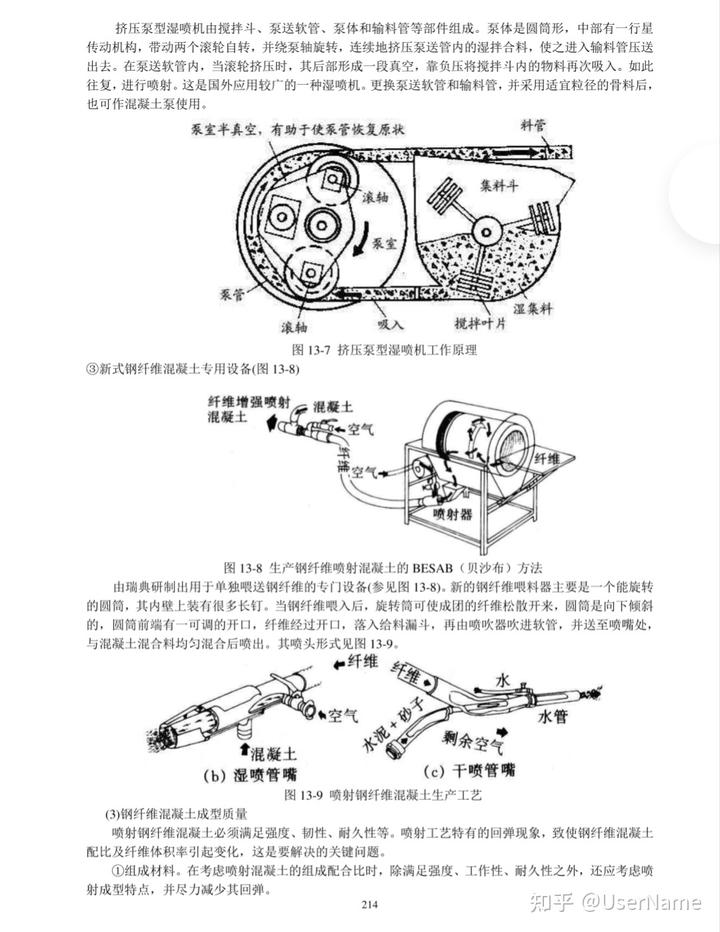
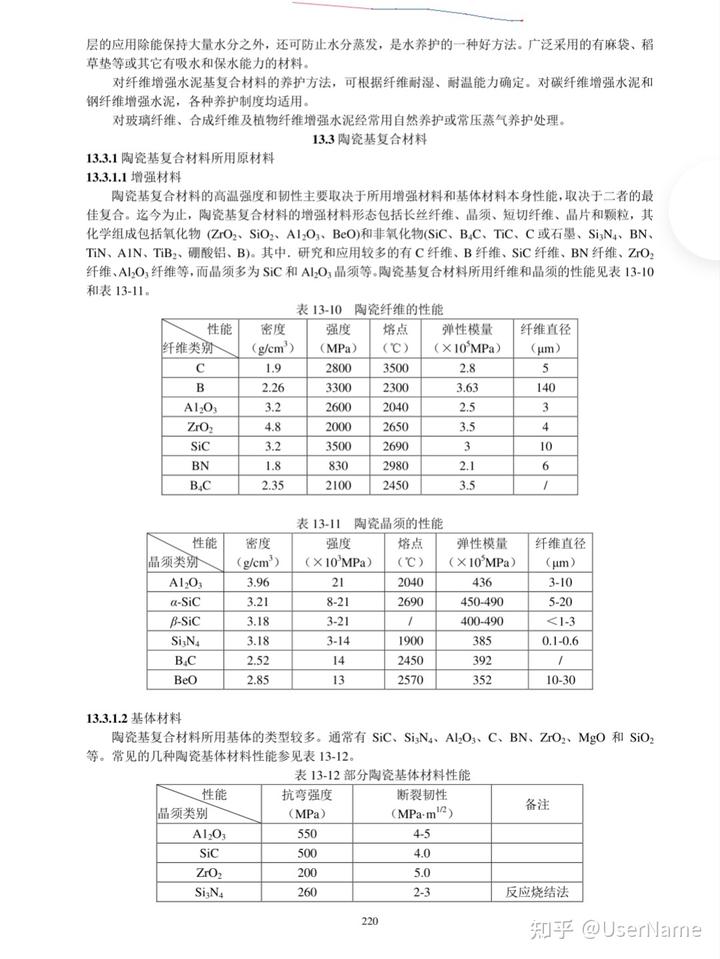
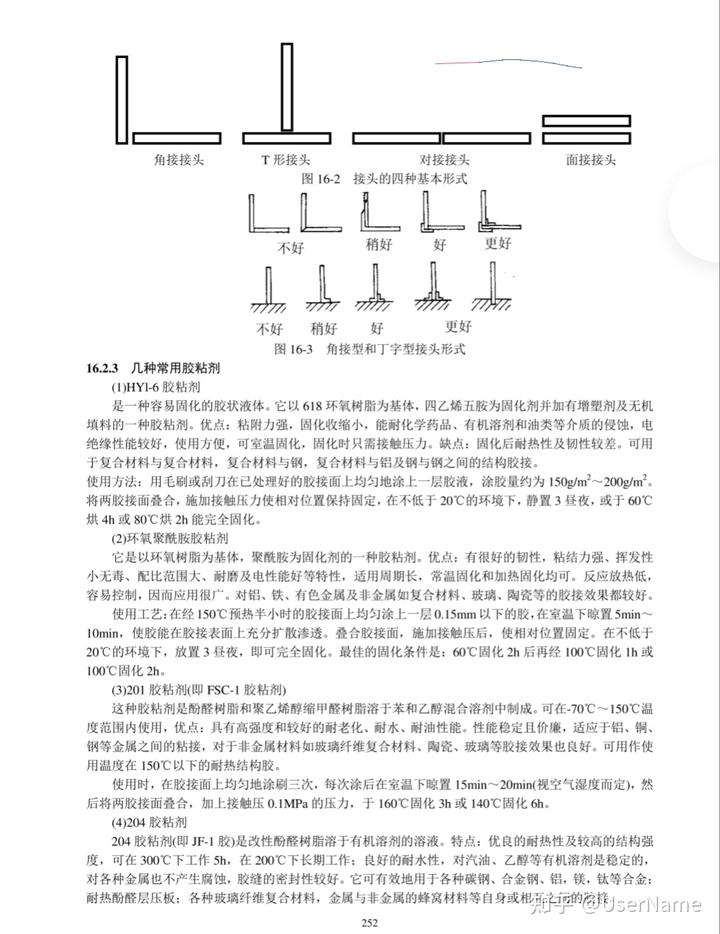
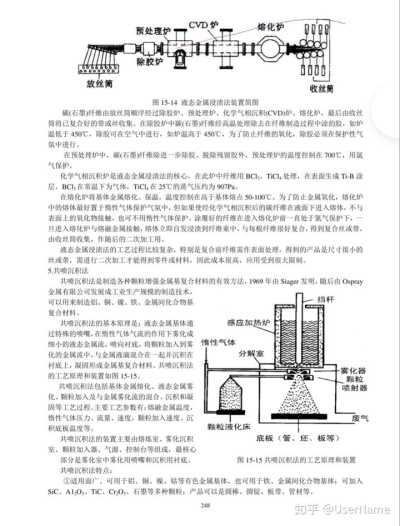
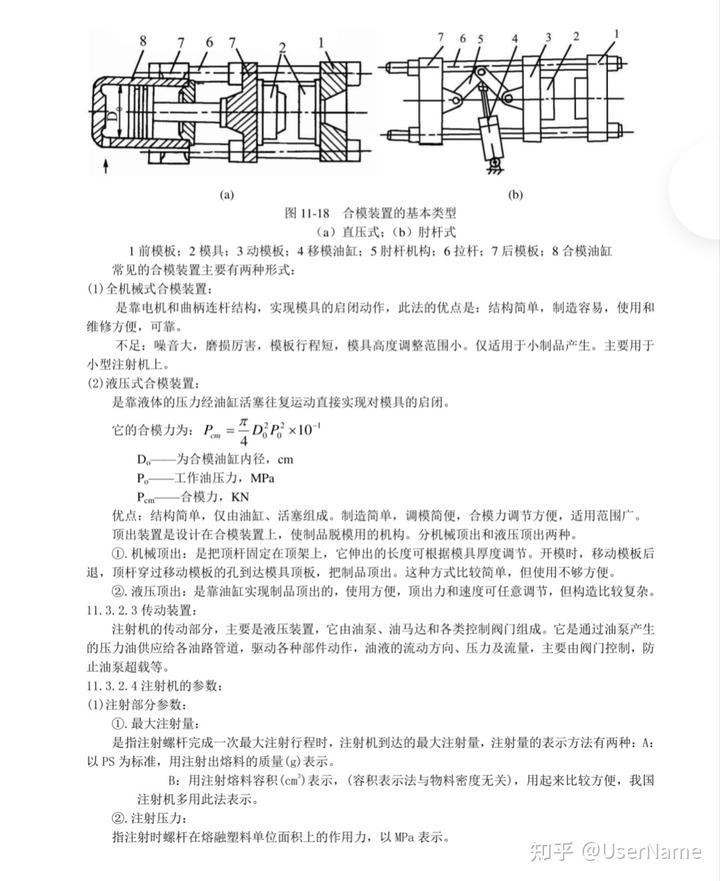
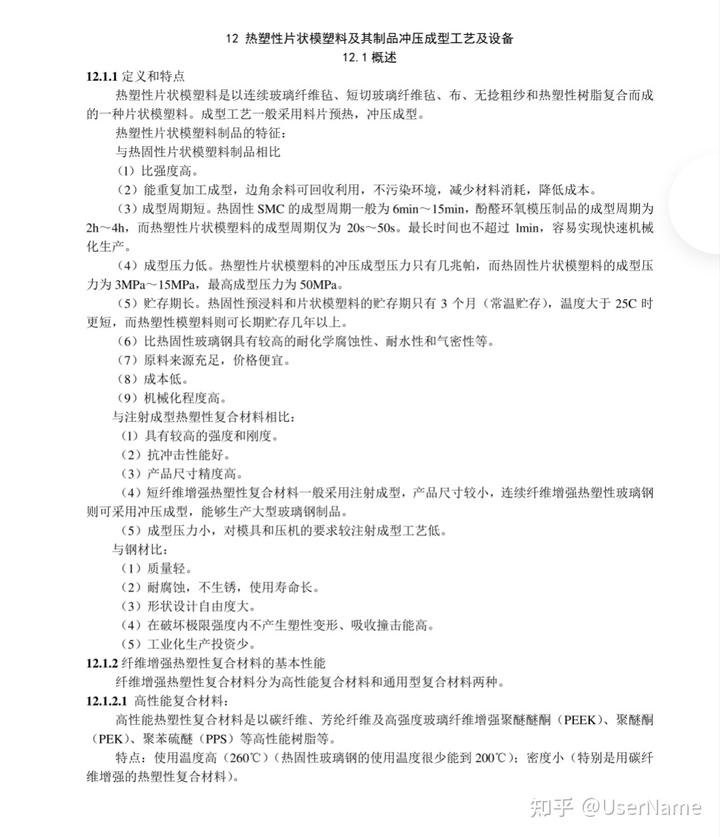
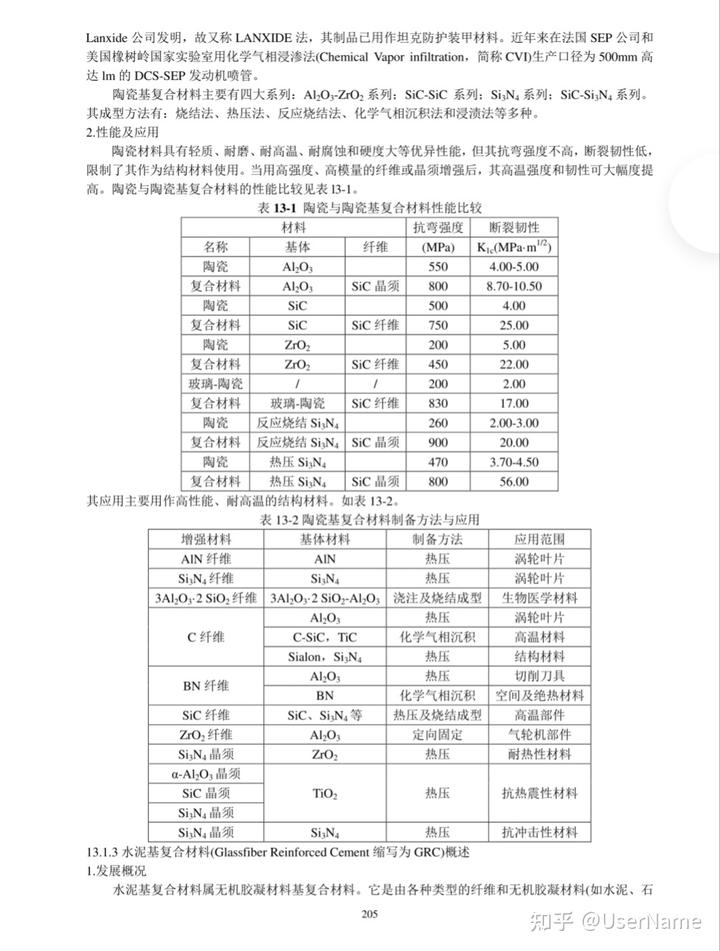
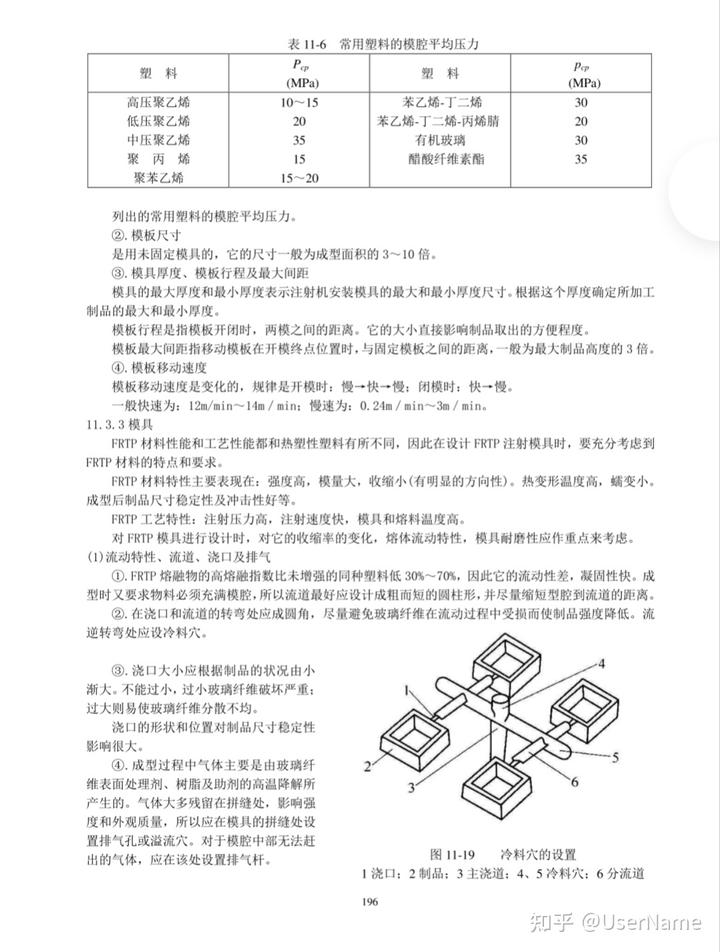
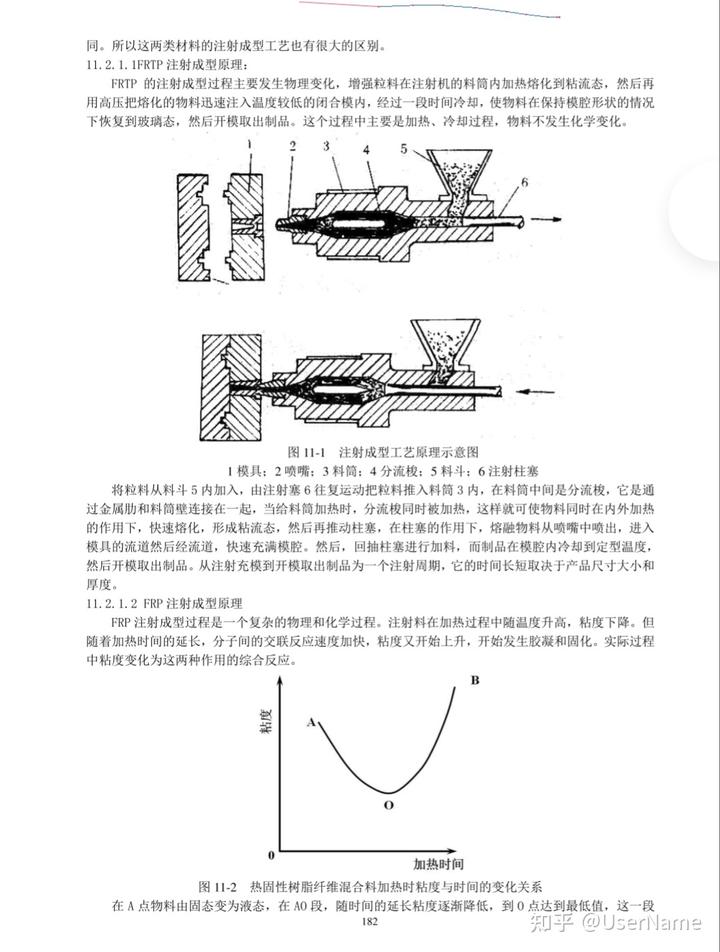
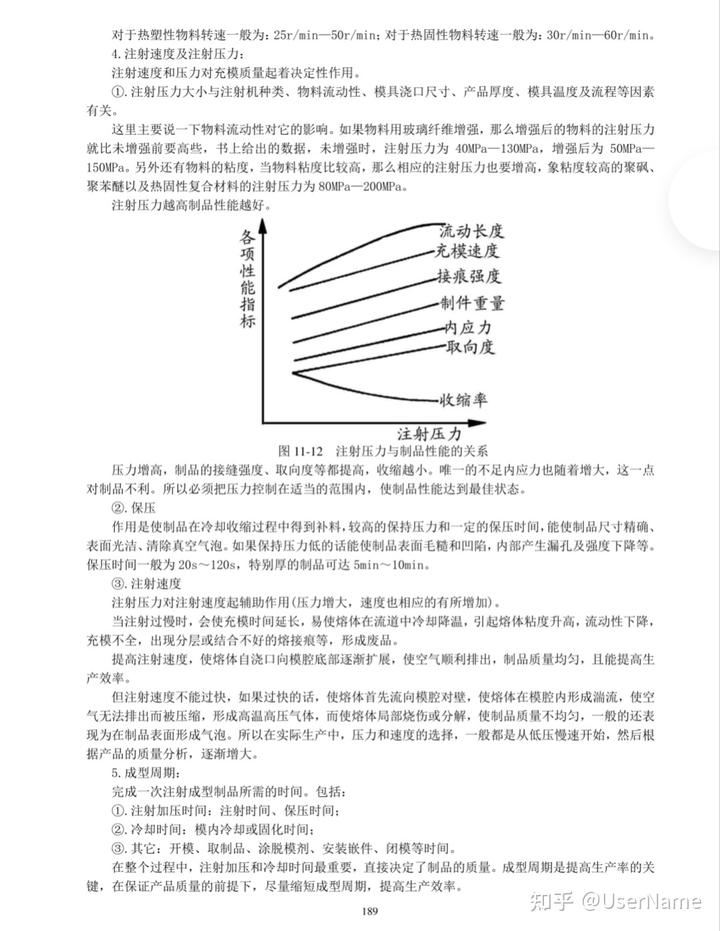
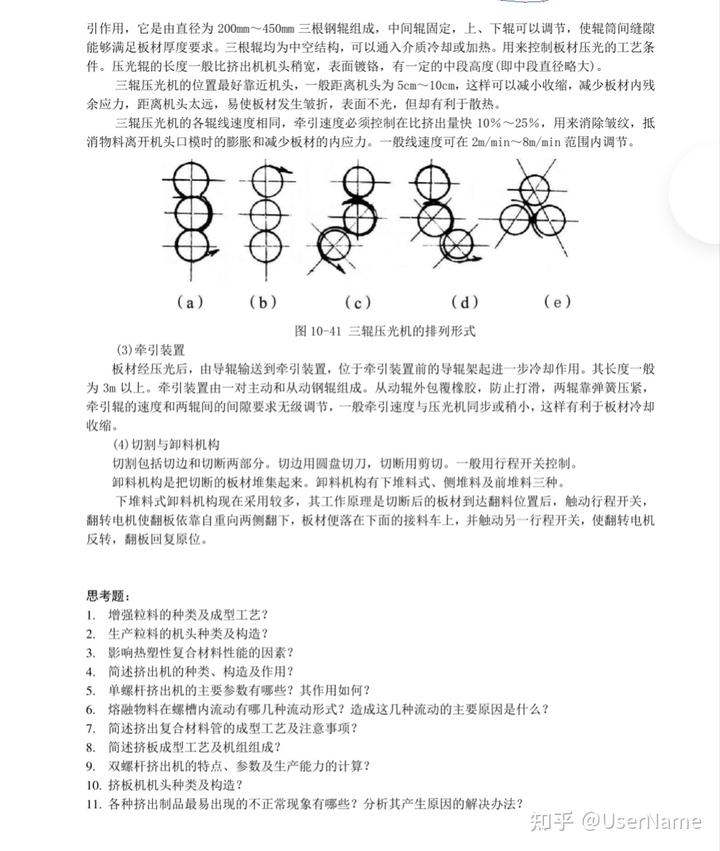
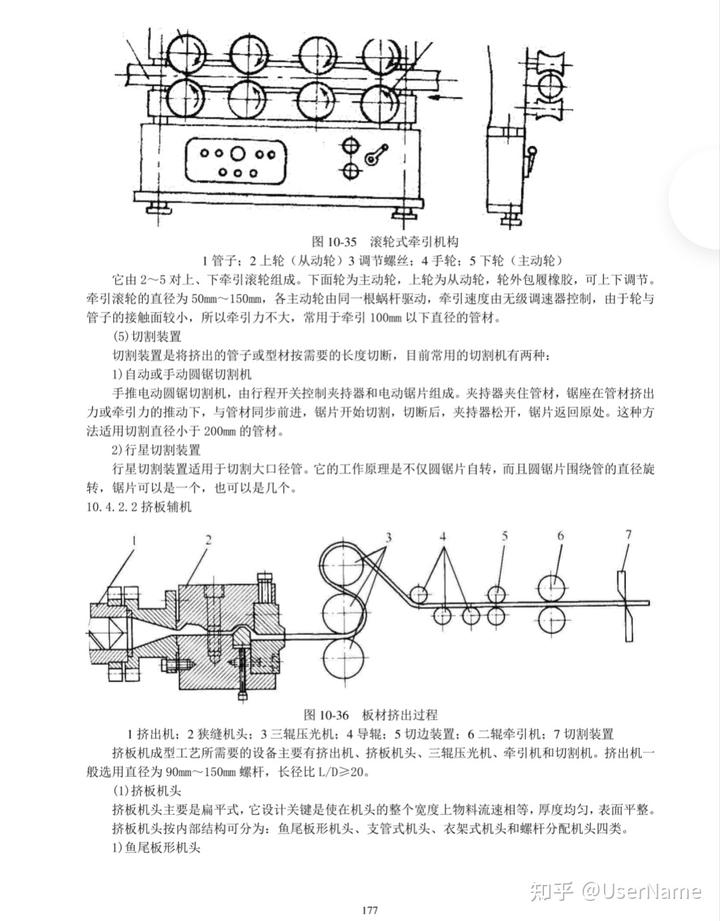
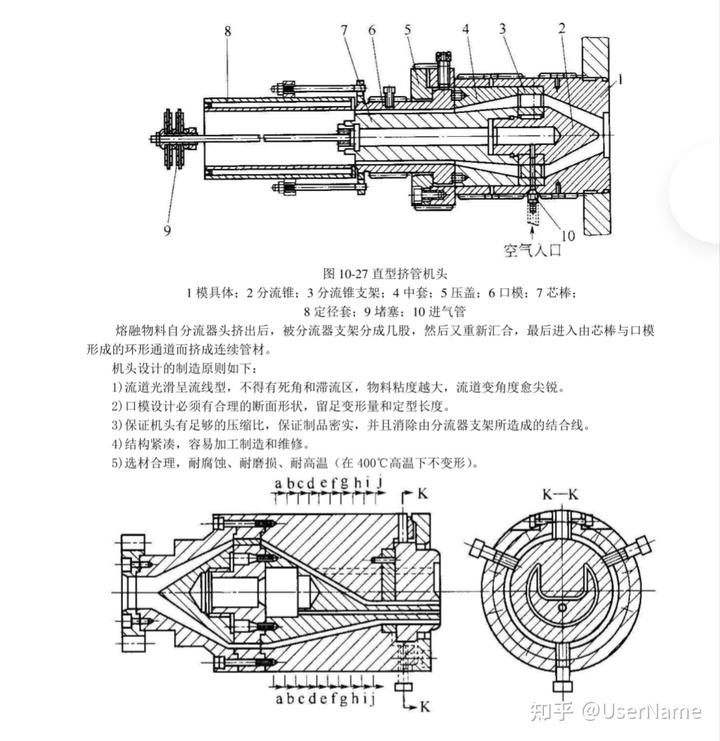
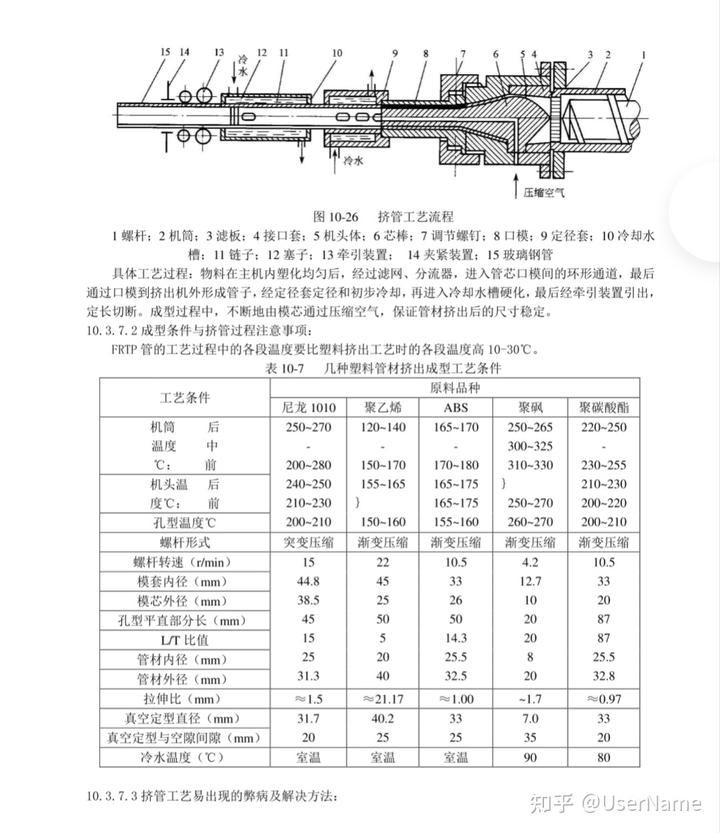
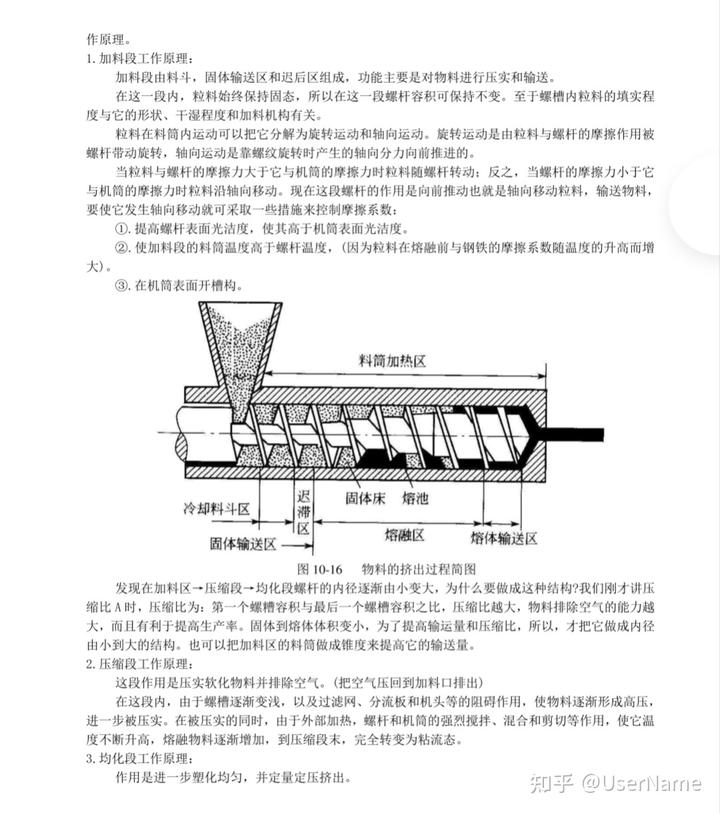
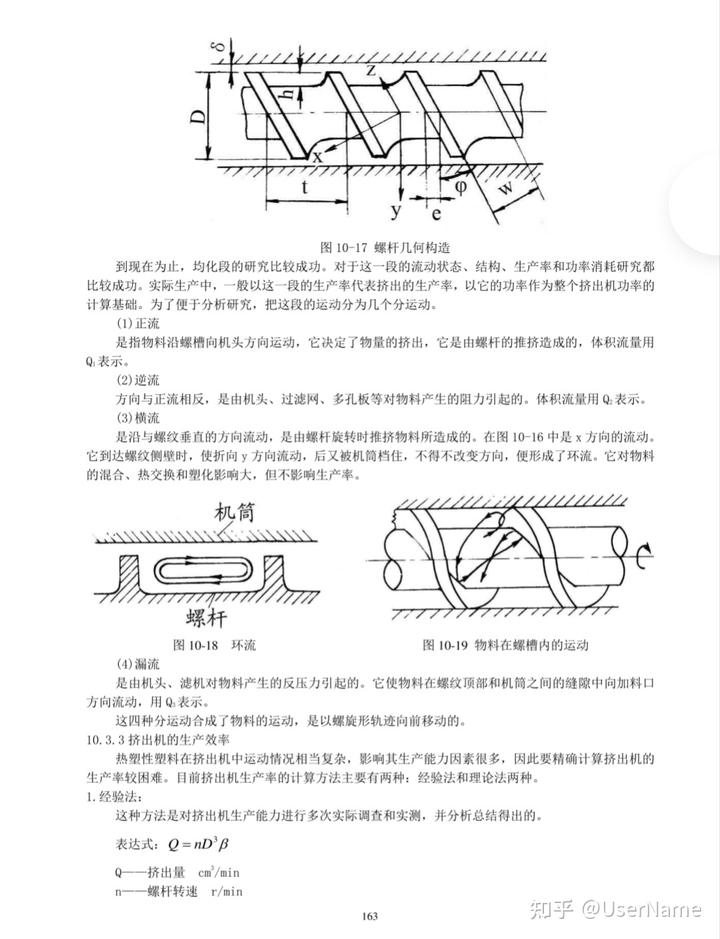
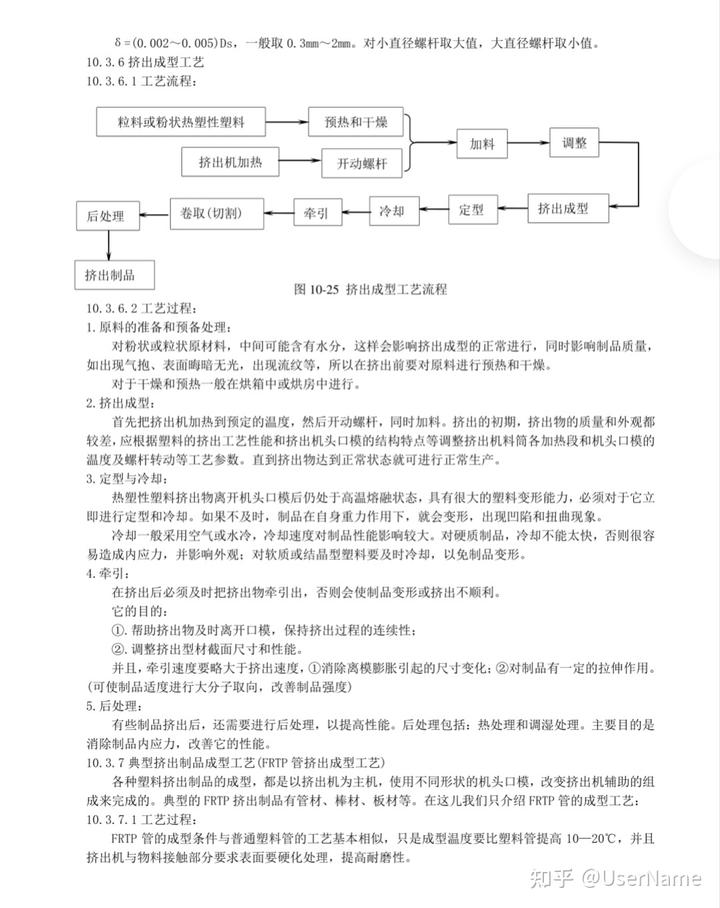
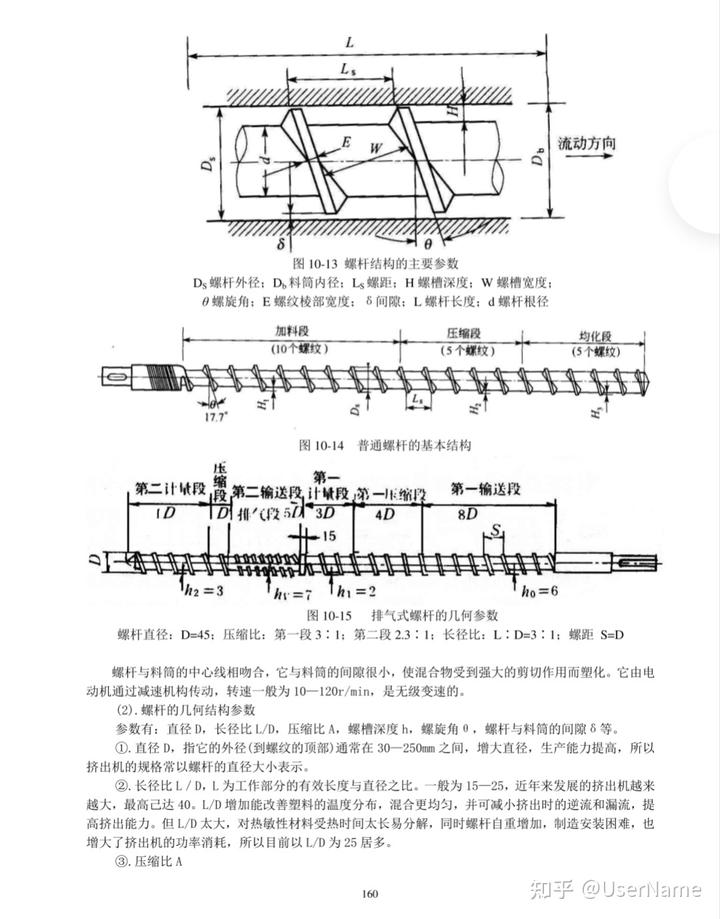
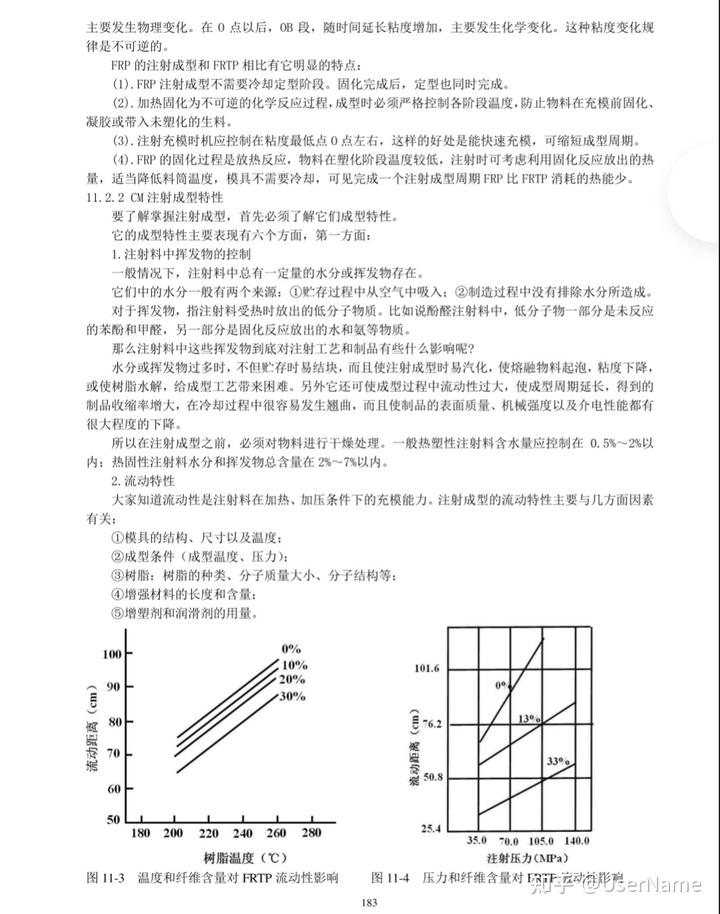
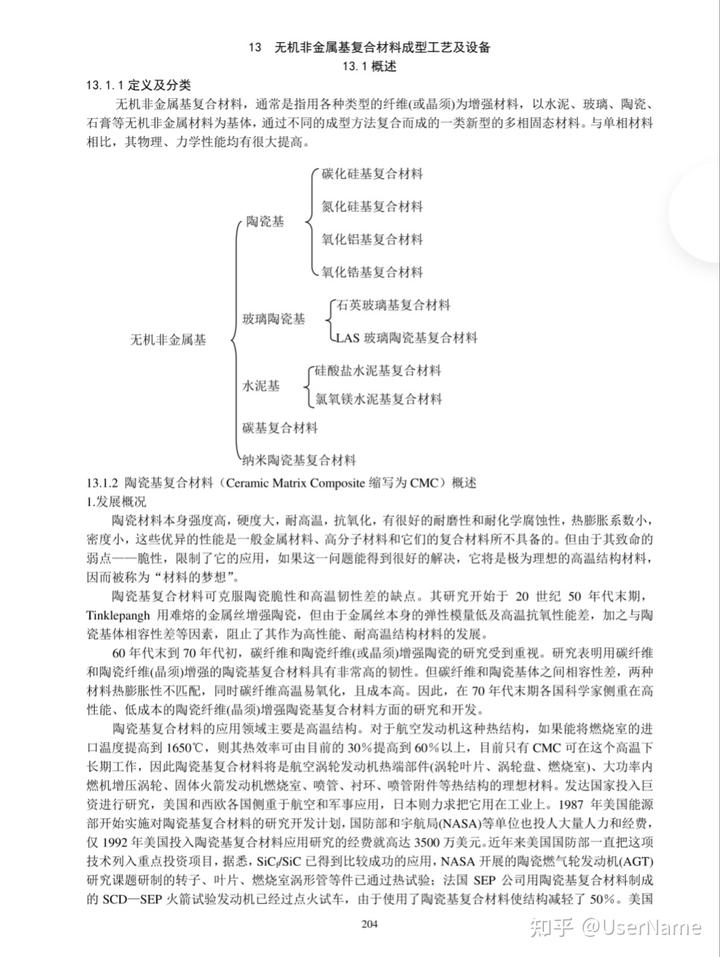
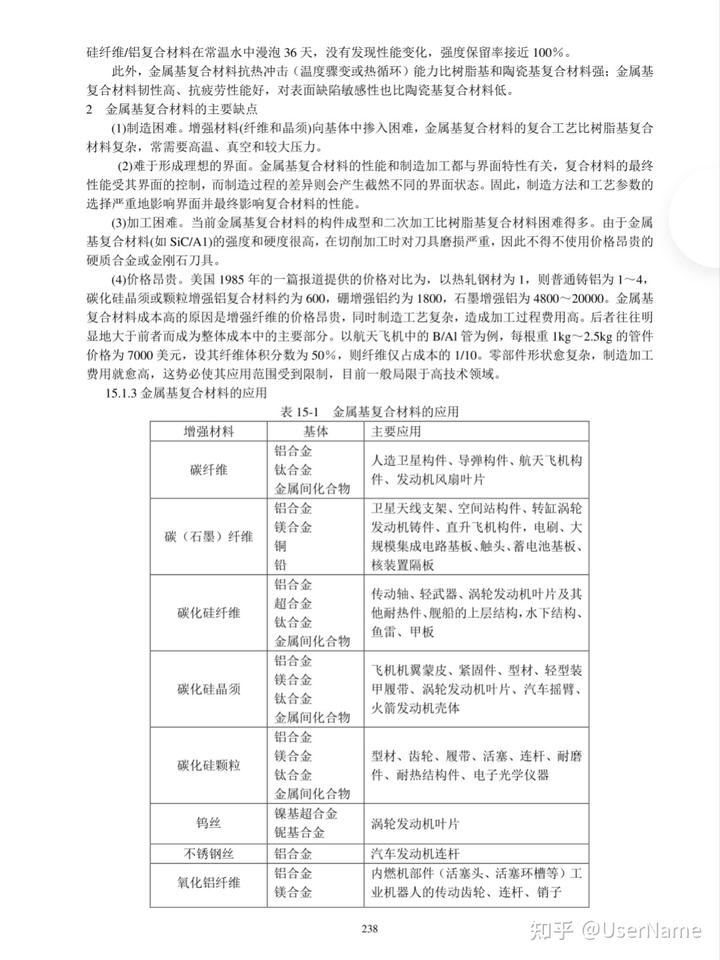
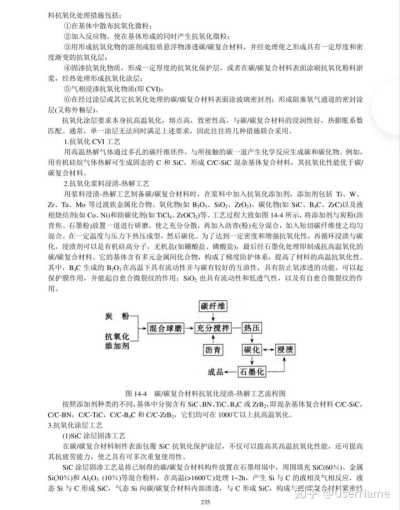
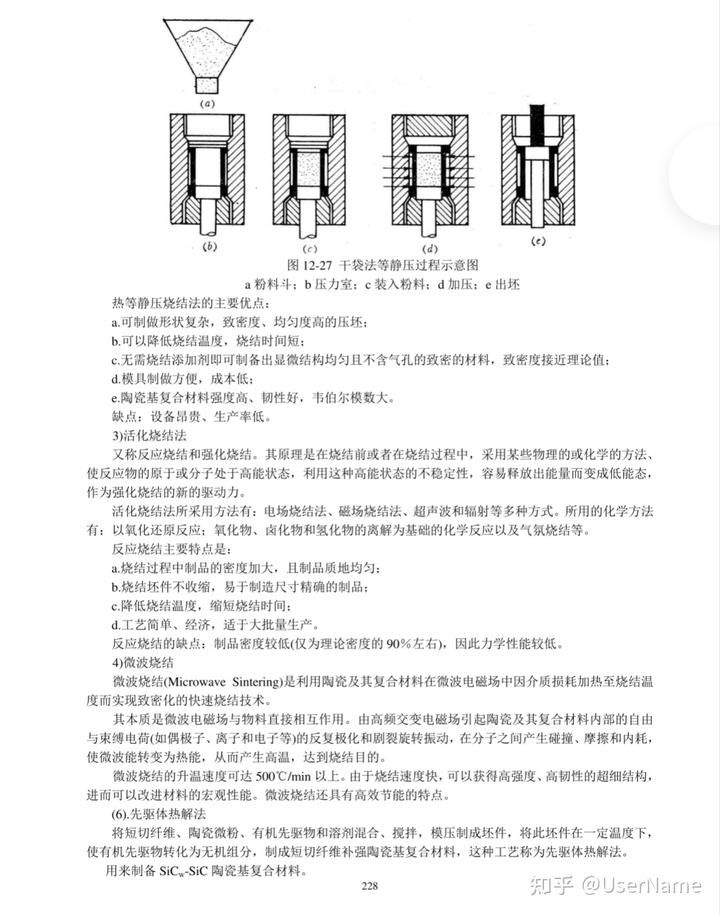

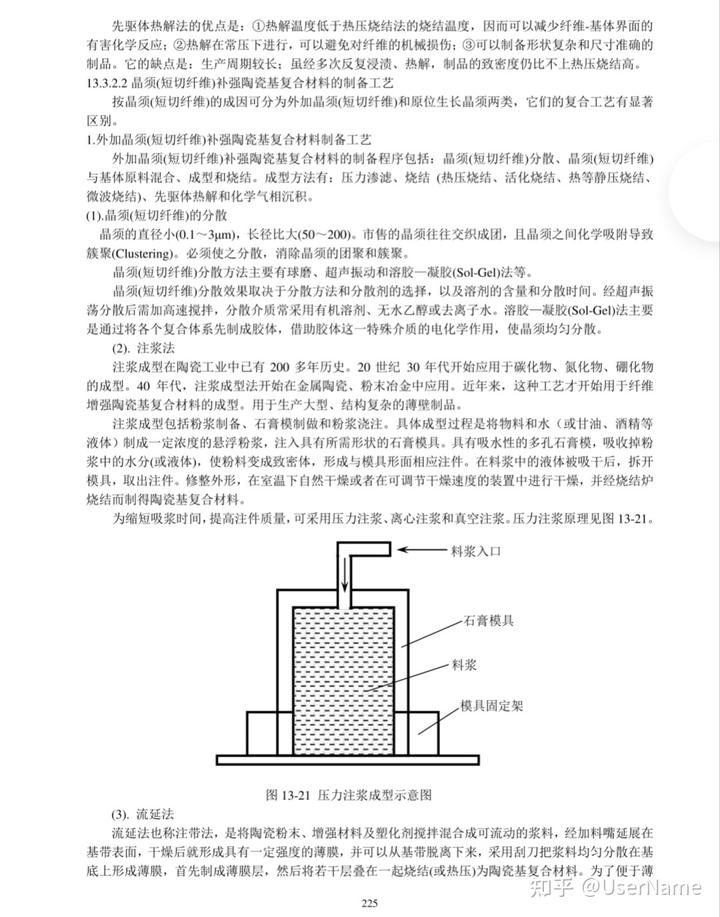
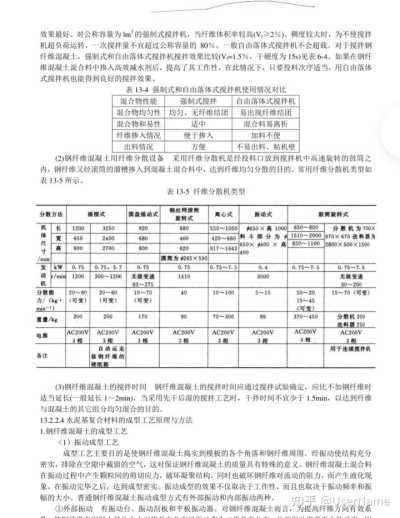
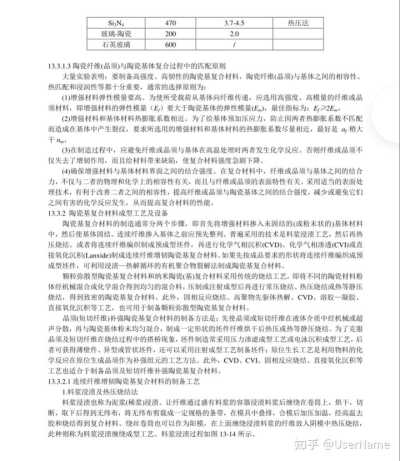
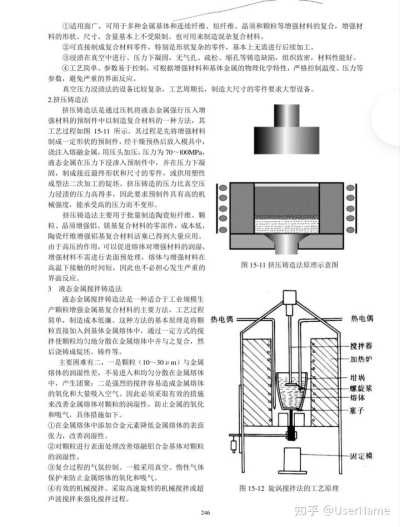
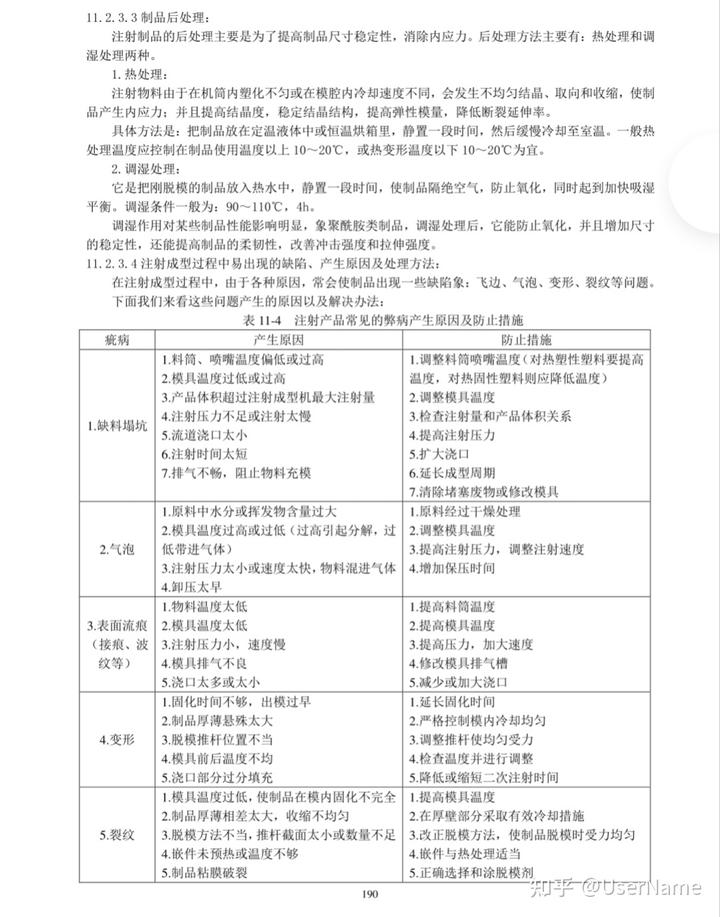
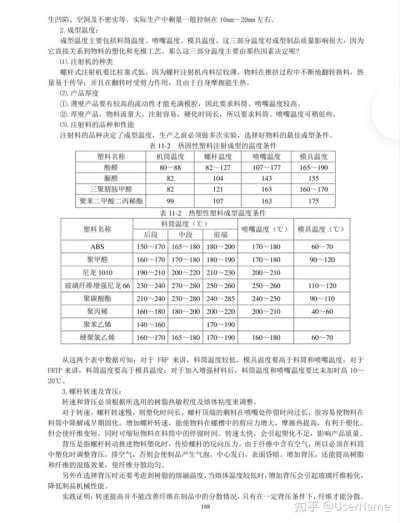
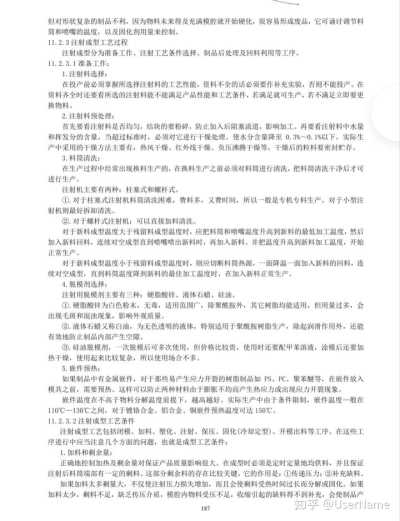
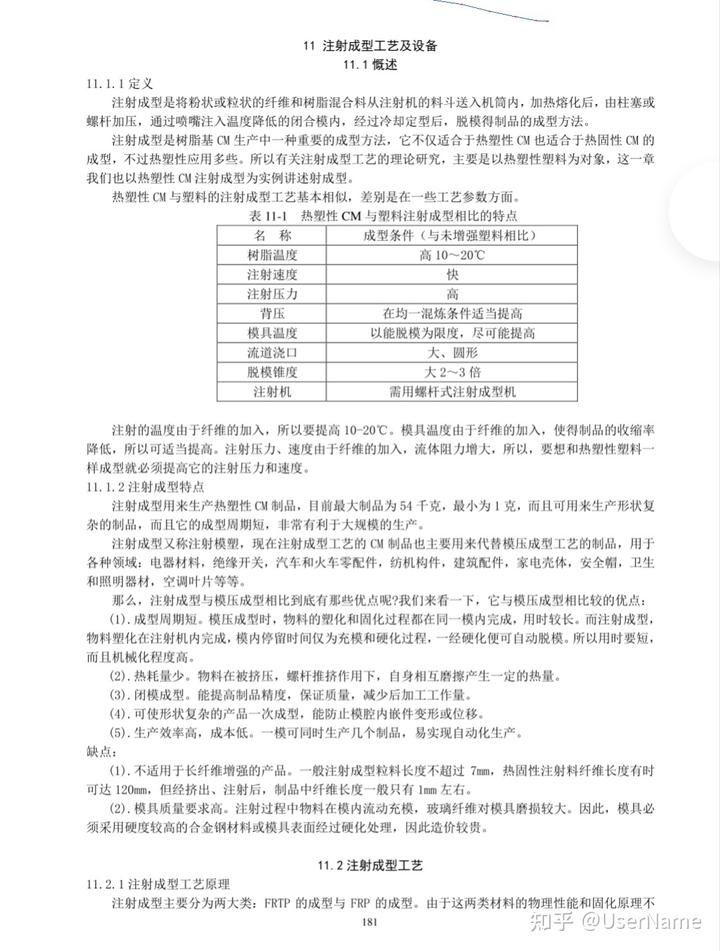
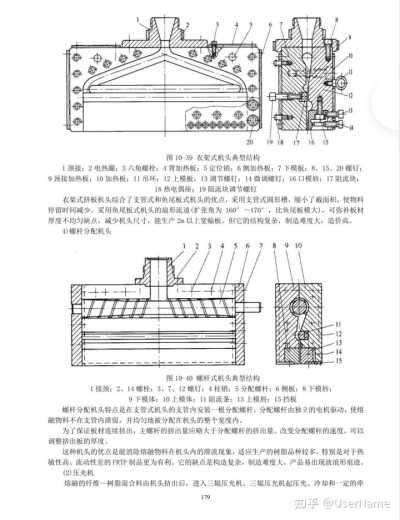
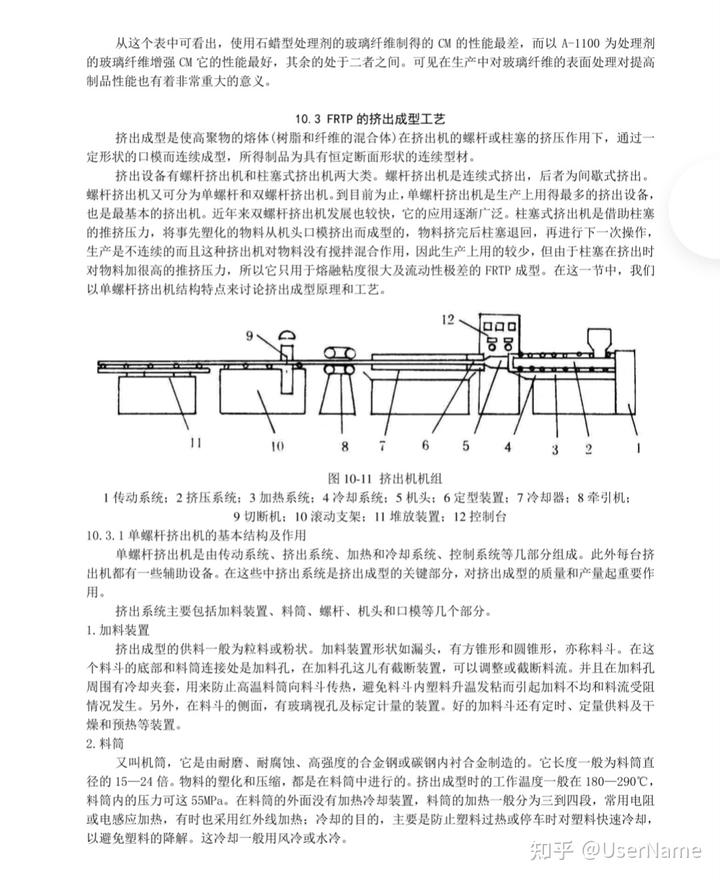
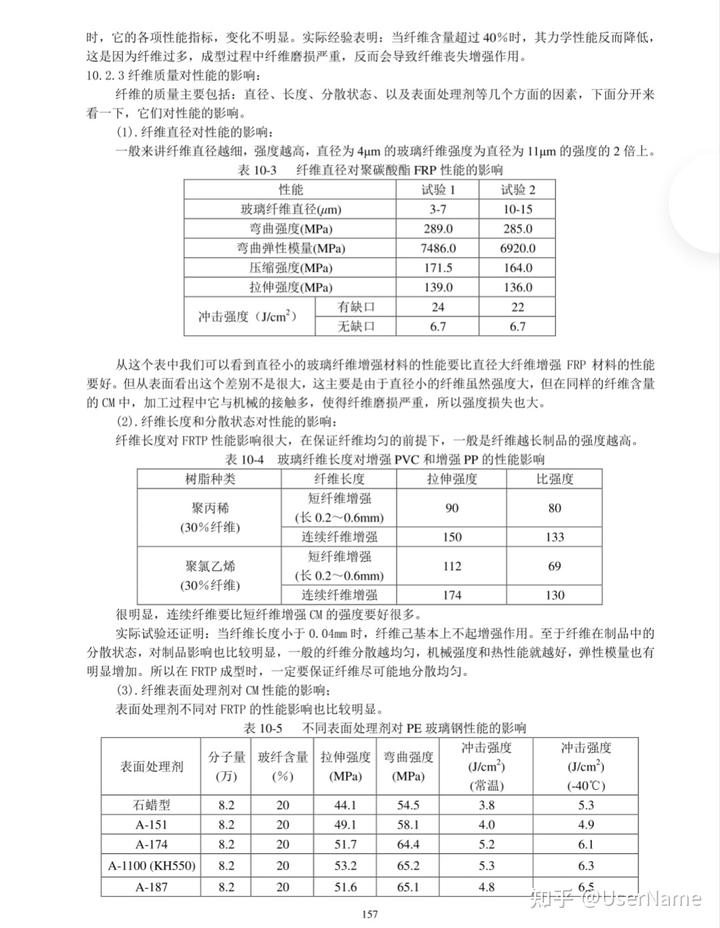
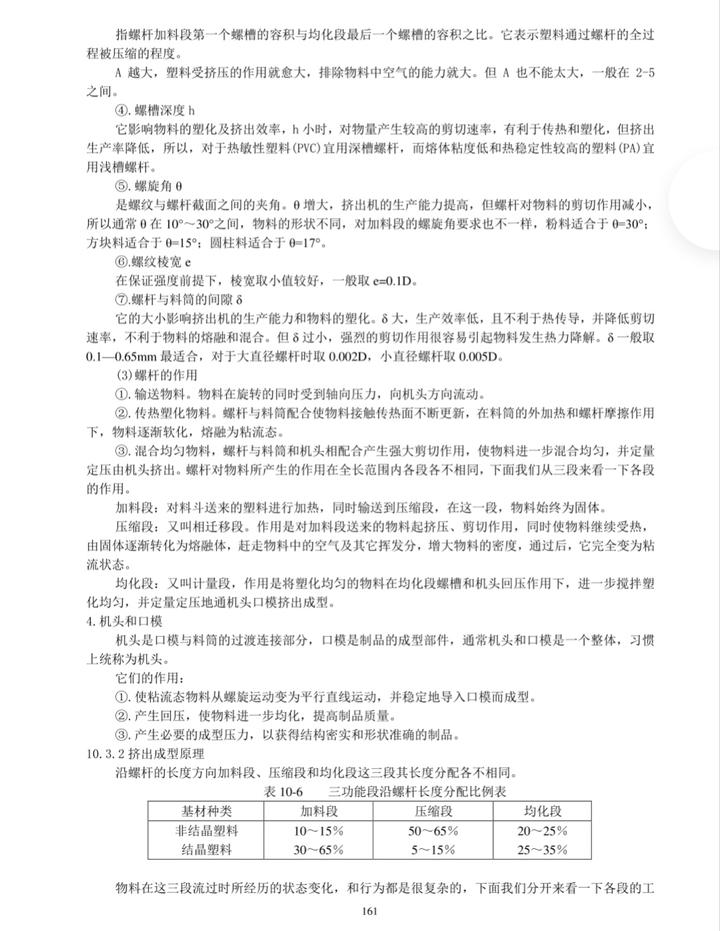
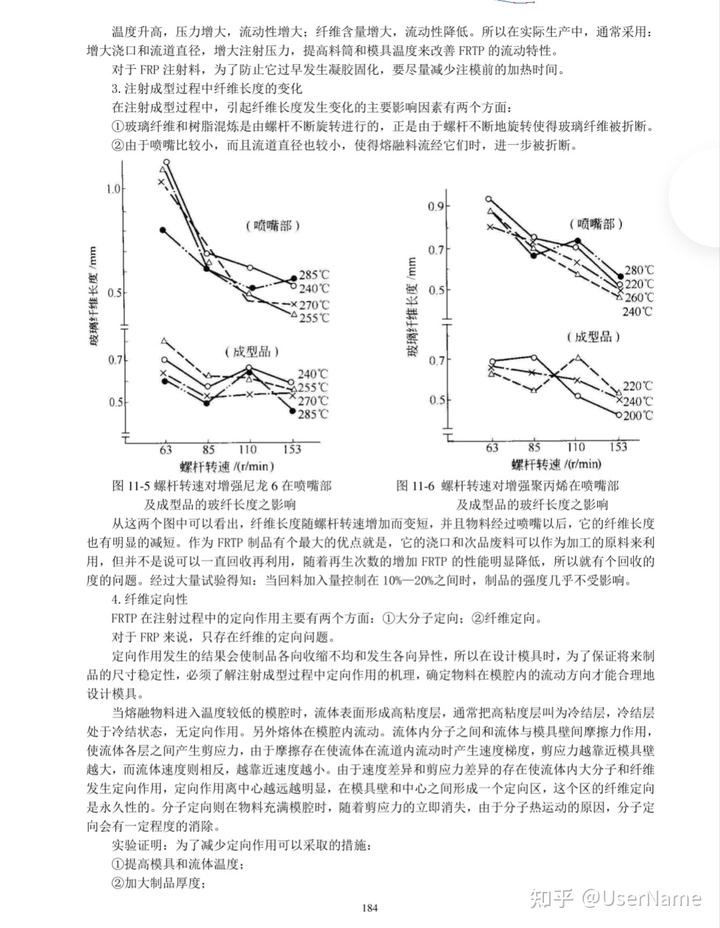
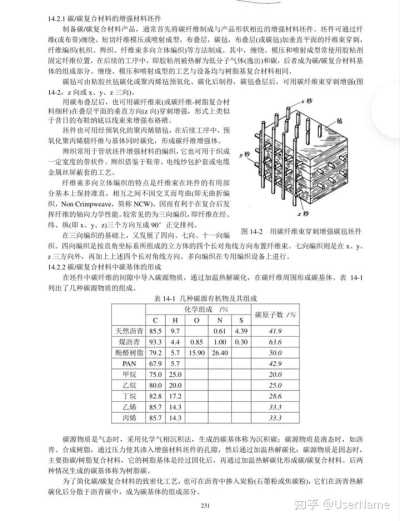
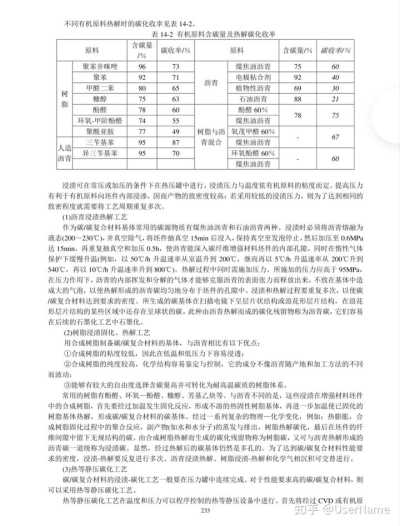
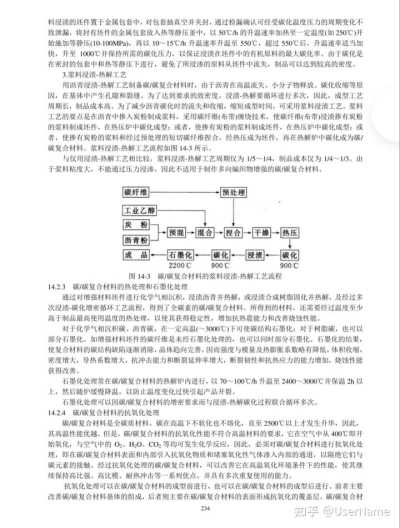
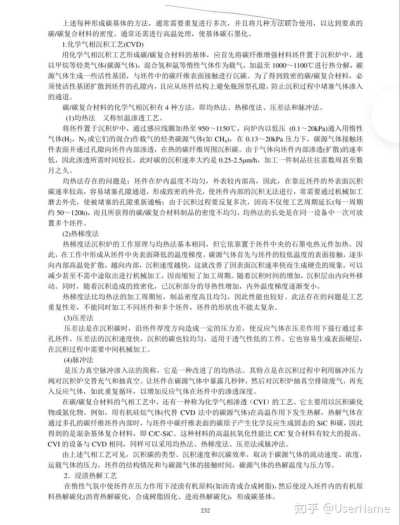
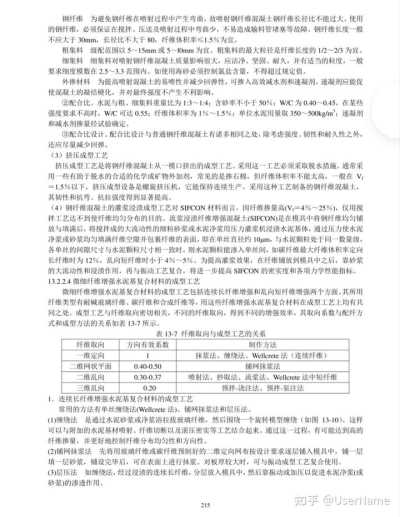
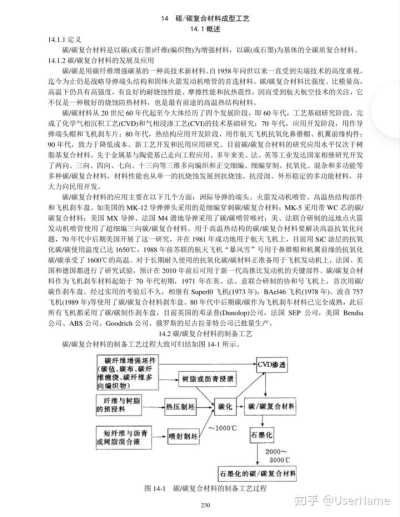
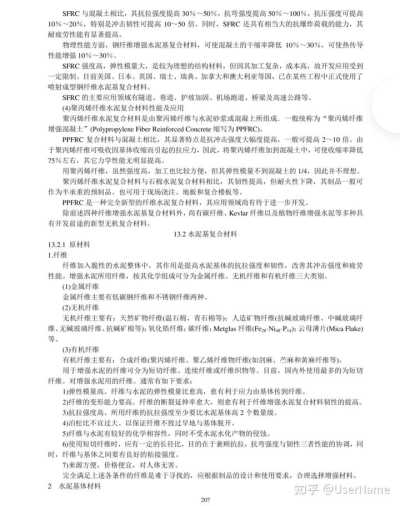
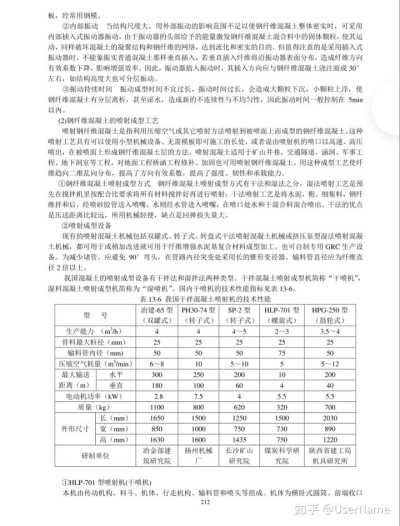
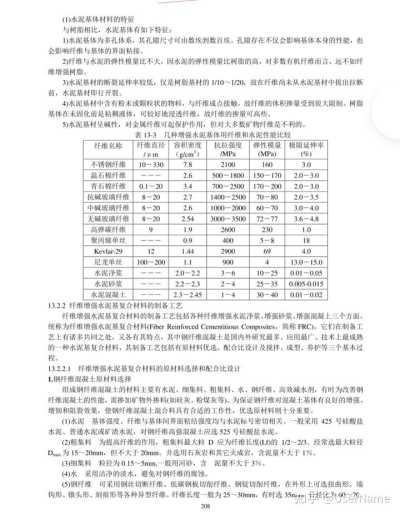
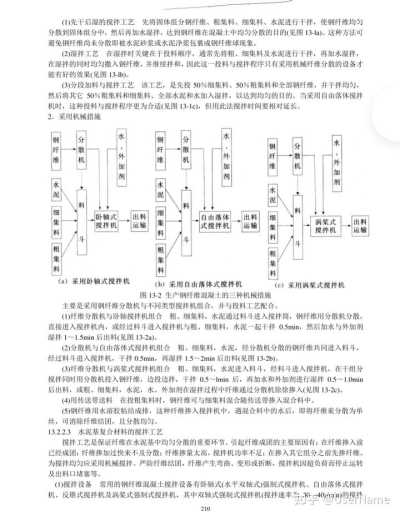
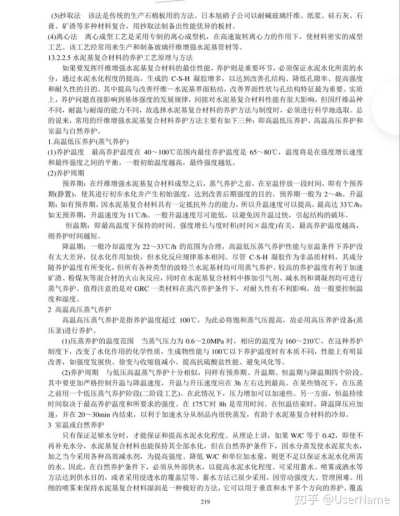
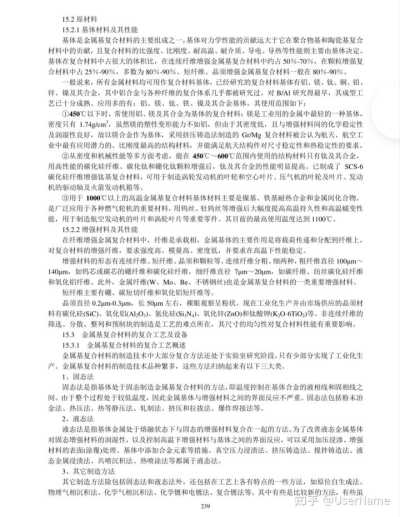
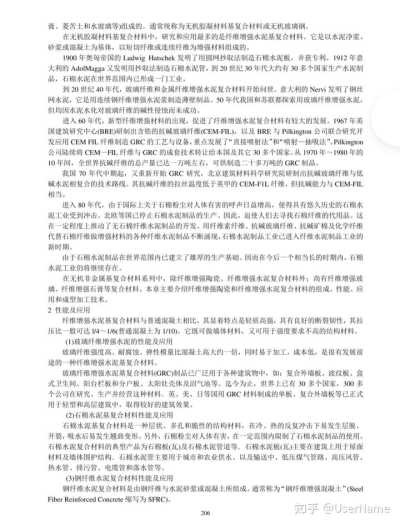
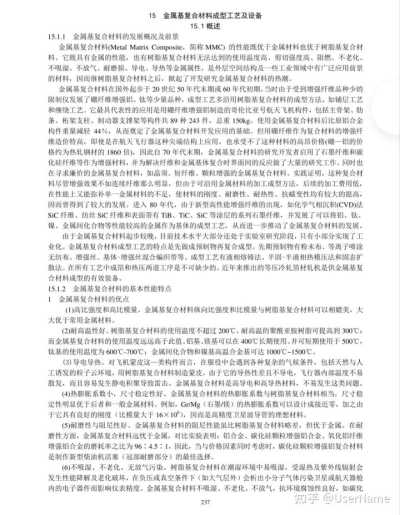
Si3N4470
3.7-4.5
热压法
玻璃-陶瓷200
2.0
石英玻璃600
13.3.1.3陶瓷纤维(晶须)与陶瓷基体复合过程中的匹配原则
大量实验表明:要制备高强度、高韧性的陶瓷基复合材料,陶瓷纤维(晶须)与基体之间的相容性、热匹配和浸润性等都十分重要,通常的选择原则为:
(1)增强材料弹性模量要高。为使所受载荷从基体向纤维传递,应选用高强度、高模量的纤维或晶须材料,即增强材料的弹性模量(E)要大于陶瓷基体的弹性模量(Em),最佳指标为:E≥2Em
(2)增强材料和基体材料热膨胀系数相近。为了给基体预加压应力,防止因两者热膨胀系数不匹配而造成在基体中产生裂纹,要求所选用的增强材料和基体材料的热膨胀系数尽量相近,最好是a稍大干am
(3)在制造过程中,应避免纤维或晶须与基体在高温处理时两者发生化学反应。否则纤维或晶须不仅失去了增韧作用,而且给材料带来缺陷,使复合材料强度急剧下降。
(4)确保增强材料与基体材料界面之间的结合强度。在复合材料中,纤维或晶须与基体之间的结合力,不仅与二者的物理和化学上的相容性有关,而且与纤维或晶须的表面特性有关。采用适当的表面处理技术,有利于改善二者之间的相容性,提高纤维或晶须与陶瓷基体之间的结合强度,减少或避免它们之间有害的化学反应发生,从而提高复合材料的性能。
13.3.2陶瓷基复合材料成型工艺及设备
陶瓷基复合材料的制造通常分两个步骤,即首先将增强材料掺入未固结的(或粉末状的)基体材料中,然后使基体固结。连续纤维掺入基体之前应预先整列。普遍采用的技术是料浆浸渍工艺,然后再热压烧结。或者将连续纤维编织制成预成型坯件,再进行化学气相沉积(CVD)、化学气相渗透(CVI)或直接氧化沉积(Lanxide)制成连续纤维增韧陶瓷基复合材料。如果先按成品要求的形状将连续纤维编织成预成型坯件,可利用浸渍一热解循环的有机聚合物裂解法制成陶瓷基复合材料。
颗粒弥散型陶瓷基复合材料和纳米陶瓷(基)复合材料采用传统的烧结工艺,即将不同的陶瓷材料粉体经机械混合或化学混合得到均匀的混合料,压制或注射成型后再进行常压烧结、热压烧结或热等静压烧结,得到致密的陶瓷基复合材料。此外,固相反应烧结、高聚物先驱体热解、CVD、溶胶一凝胶、直接氧化沉积等工艺,也可用于制备颗粒弥散型陶瓷基复合材料。
晶须(短切纤维)补强陶瓷基复合材料的制备方法是:先使晶须或短切纤维在液体介质中经机械或超声分散,再与陶瓷基体粉末均匀混合,制成一定形状的坯件纤维烘干后热压或热等静压烧结。为了克服晶须及短切纤维在烧结过程中的搭桥现象,坯件制造常采用压力渗滤成型工艺或电泳沉积成型工艺,后者可获得薄壁件、异型或管状坯件,还可以采用注射成型工艺制备坯件:原位生长工艺是利用物料的化学反应在原位生成晶须作为补强组元的工艺方法。此外,CVD、CVI、固相反应烧结、直接氧化沉积等工艺也适合于制备晶须及短切纤维补强陶瓷基复合材料。
13.3.2.1连续纤维增韧陶瓷基复合材料的制备工艺
1.料浆浸渍及热压烧结法
料浆浸渍也称为泥浆(稀浆)浸渍。让纤维通过盛有料浆的容器浸渍料浆后缠绕在卷筒上,烘干,切断,取下后得到无纬布,将无纬布剪裁成一定规格的条带,在模具中叠排,合模后加压加温,经高温去胶和烧结得到复合材料。绕丝卷筒也可以作为阳模,在上面缠绕浸渍料浆的纤维放入阴模中热压烧结,此种则称为料浆浸渍缠绕成型工艺。料浆浸渍过程如图13-14所示。
泥浆池取下
固化(热压-烧结+再浸渗)切断层叠
图13-14料浆浸渍工艺过程示意图
纤维缠绕于剪裁浸浆纤
在模具中
纤维浆料浸渍
绕丝机滚筒
维无纬布
铺排并冷
压成型件
CMC制品热压烧结
高温去胶
干燥
图13-15料浆浸渍和热压烧结制备纤维增韧陶瓷基复合材料的工艺流程
热压烧结应按预定规律(即热压制度)升温和加压,热压过程中,最初阶段是高温去胶,随着粘接剂
挥发、逸出,将发生基体颗粒重新分布,在外压作用下通过粘性及塑性流动和烧结等过程,最终获得致
密化的陶瓷基复合材料。很多陶瓷基复合材料体系在热压过程中往往没有直接发生化学反应,主要通过
系统表面能减少来驱动,使疏松粉体熔接而致密化。
料浆浸渍法是制取玻璃和玻璃陶瓷基复合材料广泛采用的一种工艺方法。
热压烧结工艺的优点是:①比常压烧结的烧结温度低,烧结时间短;②所得制品致密度接近理论值。热压烧结工艺的缺点是:①生产效率较低,只适应于单件和小规模生产,工艺成本较高;②垂直于
加压方向的性能与平行于加压方向的性能有显著差别:③只适合制备单向或双向纤维增韧陶瓷基复合材
料;④纤维与基体的比例较难控制,成品中纤维不易均匀分布。
2.化学气相沉积法
化学气相沉积(Chemical Vapor Deposiuon,简称CVD)法是在具有贯通间隙的增强体(如纤维、晶
须或颗粒)还件或纤维编织骨架中沉积陶瓷基体制备陶瓷基复合材料的方法,其工艺为:纤维编织骨架
或坯件置于化学气相沉积炉内,通入沉积反应的源气,在沉积温度下热解或发生反应,生成所需的陶瓷
基体材料,沉积在坯件的孔隙中,并逐步填满。化学气相沉积温度一般为1100~1500℃,CVD法可用于
制备C/C、C/BN、SiC/C、SiN/BC等体系的复合材料。碳纤维-碳化硅的化学气相沉积工艺过程原理
示意图13-16。电源
废气出口
气相沉积炉
碳纤维预成型体
SiClH2
图13-16碳纤维-碳化硅的化学气相沉积工艺过程原理
222
与热压烧结法相比,CVD法的优点是:①复合材料在制备过程中纤维受到的机械损伤和化学损伤小
②可以制备纤维多向排布、编织和复杂形状的制品;③可用于制备组成可调的梯度功能复合材料。CVD
法的不足是:①生产周期长,效率低,成本高:②坯件的间隙在CVD过程中容易堵塞或形成闭孔,即使
提高压强,源气也无法通入,因而难以获得高致密性的复合材料。
3.化学气相渗透法
化学气相渗透(Chemical Vapor Infiltration,简称CVI)法与CVD法一样,有均热法、温度梯度
法、压力梯度法和脉冲法等:CVI工艺与CVD不同的是:源气不仅热解和自身反应,而且还与坯件孔隙
表面的元素发生化学反应,并在坯件孔隙中沉积反应物。CVI法的工艺原理示意图13-17。
热区
加热元件热区1200℃
逸出的气体
带孔的挡环热表面
渗透的复合材料
冷表面
水冷底座纤维预成型体
源气
图13-17化学气相渗透(CVI)工艺原理示意图
将纤维预成型坯件置于底部及四周处于冷态而顶部处于热区的石墨坩埚中,预成型坯件的底部与
顶部的温度梯度很陡。从底部导入源气(反应物气体),当它通过预成型坯件的下部时,由于温度低而不
与之发生反应,直至到达预成型坯件顶部,即热区(1200℃)时,才发生热分解或化学反应,产生的固态
反应物沉积在热区的纤维周围形成基体。剩余的源气从开口挡环排出,由于出口处保持低压,形成的压
强梯度使源气自下而上穿过坯件。随着坯件顶部沉积部分的密度和导热率增加,使热区逐渐从顶部向下
移动,反应物沉积区也不断向下移动,直至整个坯件中的孔隙几乎全部被填满,最终获得高致密性的复
合材料。用这种方法制备的陶瓷基复合材料,其致密度达到理论密度的93%~94%。
CVI工艺的优点是:①制备陶瓷基复合材料的效率高、速率快,尺寸为50×13mm的SiC/SiC样
品,用CVD法需14~21天,而用CVI法仅需30h左右:②通过低温(1000℃-2000℃)成型,可沉积出熔
点高达3000℃的基体,同时避免了纤维-基体间的高温有害化学反应发生:③可仿形制造各种形状复杂、
大尺寸(例如投影面积1m以上)的陶瓷基复合材料部件:④可制取具有高强度、高韧性、高临界应变值
的陶瓷基复合材料。
4.直接氧化沉积法
直接氧化沉积(Direct Oxidating Deposition,简称DOD或LANXIDE)法,利用熔融金属直接与氧化
剂发生氧化反应来制备陶瓷基复合材料。此工艺最早被用来制备A1:0-A1复合材料,后推广于制备连续
纤维陶瓷基复合材料。LANXIDE法的工艺原理见图13-18。纤维
空气(氧化气氛)纤维/AO3复合材料
熔融A
耐火坩埚
图13-18LANXIDE法的工艺原理图
223
将连续纤维预成型坯件置于熔融金属上面,由于熔融金属中含有少量添加剂,并处于空气或其它
氧化气氛中,浸渍到纤维预成型坯件中的熔融金属或其蒸气与气相氧化剂发生反应形成氧化物,该反应
始终在熔融金属与气相氧化剂的界面处进行。反应产生的金属氧化物沉积在纤维的周围,形成含有少量
残余金属的、致密的纤维增韧陶瓷基复合材料。母体金属一般选择铝,添加剂一般采用镁和硅,氧化气
氛为空气,反应温度为1200~1400℃。通过控制熔体温度和熔体掺杂成分,可以调节生成的陶瓷基复
合材料的性能。
直接氧化沉积工艺的优点是:①对增强体几乎无损伤,所制得的陶瓷复合材料中纤维分布均匀,
因而复合材料的性能优异;②工艺简单,生产率较高,成本低;③可仿型制造,避免二次加工。所制备
的复合材料具有高比强度、良好韧性及耐高温等特性。
5.先驱体热解法
先驱体热解法(Precursor Thermolysis Process)也称有机聚合物高温裂解法。此方法最早用于制
作3D-C/C复合材料,此时高聚物先驱体为沥青或酚醛树脂。现在研究较多的是用聚碳硅烷
(Polycarbosilanes,简称PCS)作为碳化硅的先驱体,制作C/SiC和SiC/SiC复合材料。
此方法分两种。第一种与溶胶一凝胶工艺(Sol-Gelprocess)是将含有多种组分的溶液浸入纤维编织
坯件,通过物理或化学方法使分子或离子成核形成溶胶。在一定条件下经过凝胶化处理,获得多组分的
凝胶体,再经热解形成陶瓷基体。
3D-C3D-C/SiC
浸渍
浸渍交联裂解
复合材料
AOOH凝胶
PCS-DVB3D-C/SiC-AL2O3
裂解
混杂陶瓷基复合材料1000-1200℃
图13-19先驱体裂解法与溶胶-凝胶法联用制备3D-C/SiC-AL2O3混杂陶瓷基复合材料
(3D-C为3D碳纤维编织坯体,DVB为二乙烯基苯,AOOH为异丙醇铝、盐酸和去离子水配成
的溶胶)
另一种是先驱体热解法还可与料浆浸渍法联合使用,即先用料浆浸渍法制备纤维预成型坯件,此时
料浆中除陶瓷基体超细粉末外,还混有高聚物先驱体。将预成型坯件在常压下进行热解,使料浆中的高
聚物先驱体热解产物填充纤维编织坯件间隙,并包围料浆中的陶瓷超细粉末,与其一道构成复合材料的
陶瓷基体。纤维或织物
料浆配制
浸渍去胶,热解
晾干浸渍PCS
v
切片,铺叠热解
层压制品
图13-20料浆浸渍与先驱体热解法联用制备C/SiC工艺流程
224
先驱体热解法的优点是:①热解温度低于热压烧结法的烧结温度,因而可以减少纤维-基体界面的有害化学反应;②热解在常压下进行,可以避免对纤维的机械损伤:③可以制备形状复杂和尺寸准确的制品。它的缺点是:生产周期较长;虽经多次反复浸渍、热解,制品的致密度仍比不上热压烧结高。13.3.2.2晶须(短切纤维)补强陶瓷基复合材料的制备工艺
按晶须(短切纤维)的成因可分为外加晶须(短切纤维)和原位生长晶须两类,它们的复合工艺有显著区别。
1.外加晶须(短切纤维)补强陶瓷基复合材料制备工艺
外加晶须(短切纤维)补强陶瓷基复合材料的制备程序包括:晶须(短切纤维)分散、晶须(短切纤维)与基体原料混合、成型和烧结。成型方法有:压力渗滤、烧结(热压烧结、活化烧结、热等静压烧结、微波烧结)、先驱体热解和化学气相沉积。
(1).晶须(短切纤维)的分散
品须的直径小(0.1~3um),长径比大(50~200)。市售的品须往往交织成团,且品须之间化学吸附导致簇聚(Clustering)。必须使之分散,消除晶须的团聚和簇聚。
品须(短切纤维)分散方法主要有球磨、超声振动和溶胶一凝胶(Sol-Gel)法等。
晶须(短切纤维)分散效果取决于分散方法和分散剂的选择,以及溶剂的含量和分散时间。经超声振荡分散后需加高速搅拌,分散介质常采用有机溶剂、无水乙醇或去离子水。溶胶一凝胶(Sol-Gel)法主要是通过将各个复合体系先制成胶体,借助胶体这一特殊介质的电化学作用,使晶须均匀分散
(2).注浆法
注浆成型在陶瓷工业中已有200多年历史。20世纪30年代开始应用于碳化物、氮化物、硼化物的成型。40年代,注浆成型法开始在金属陶瓷、粉末冶金中应用。近年来,这种工艺才开始用于纤维增强陶瓷基复合材料的成型。用于生产大型、结构复杂的薄壁制品。
注浆成型包括粉浆制备、石膏模制做和粉浆浇注。具体成型过程是将物料和水(或甘油、酒精等液体)制成一定浓度的悬浮粉浆,注入具有所需形状的石膏模具。具有吸水性的多孔石膏模,吸收掉粉浆中的水分(或液体),使粉料变成致密体,形成与模具形面相应注件。在料浆中的液体被吸干后,拆开模具,取出注件。修整外形,在室温下自然干燥或者在可调节干燥速度的装置中进行干燥,并经烧结炉烧结而制得陶瓷基复合材料。
为缩短吸浆时间,提高注件质量,可采用压力注浆、离心注浆和真空注浆。压力注浆原理见图13-21。
料浆入口
石膏模具
料浆
模具固定架
图13-21压力注浆成型示意图
(3).流延法
流延法也称注带法,是将陶瓷粉末、增强材料及塑化剂搅拌混合成可流动的浆料,经加料嘴延展在基带表面,干燥后就形成具有一定强度的薄膜,并可以从基带脱离下来,采用刮刀把浆料均匀分散在基底上形成薄膜,首先制成薄膜层,然后将若干层叠在一起烧结(或热压)为陶瓷基复合材料。为了便于薄
225
膜从基带脱离,可在基带上涂一层三醋酸纤维或乙基纤维素的酒精溶液。
流延法工艺其优点是:可制得厚度为0.05mm以下的薄膜,机械化和自动化程度较高,可以进行材料的微观结构和宏观结构设计,对不相容的两种材料可以用此法叠层连接,可制备多功能和倾斜机能材料。流延法成型原理参见图13-22。
料斗刮刀
坯膜
干燥炉
浆料基带
图13-22流延法成型示意图
(4).压力渗滤法
首先将品须(短切纤维)预成型为坯件,然后经表面处理使预成型坯件所带电荷与陶瓷基体料浆所带电荷相同,置于石膏模具中,在压力作用下使料浆充满晶须(短切纤维)预成型坯件的缝隙。料浆中的液体经过过滤器排入过滤腔,而留在模具内的经加压烧结形成晶须(短切纤维)补强陶瓷基复合材料。
(5).烧结工艺(热致密化成型工艺)
烧结是陶瓷工艺的第三个基本工序。烧结是把粉末坯块加热到低
于其基本组元的熔点温度以下进行保温,然后冷却到室温的热处理工
艺。在烧结过程中,烧结坯发生一系列物理和化学变化。坯块由粉末
颗粒聚集体变成品粒结合体,多孔体变成致密体,从而得到具有所需物
理、机械性能的制品。
能否烧结的热力学条件是晶界能与表面能的临界比值GB/Ysv
临界条件为:Gn/Ysy <v3符合这个条件即可被烧结5
烧结方法可分为四类:热压烧结、热等静压烧结、活化烧结及微
波烧结。
1)热压烧结
热压烧结(Hot Press Sintering,简称HPS)是将分散有晶图13-23压力渗滤工艺示意
须(短切纤维)的陶瓷粉体,或具有一定形状的坯件(素坯)在高温下1加压器:2压头活塞:3泥浆;
通过外加压力使其变成致密的、具有一定形状的坚硬固体的过程。4过滤器:5过滤腔:6石膏模
具应注意采用耐高温和耐一定压力、并在高温下不与工件发生反应的材料(如石墨)作为模具材料,必要时需用惰性气氛保护。在烧结后期,由于外加压力补偿和抵消了烧结产生的收缩,因此有利于制品致密化。图13-24热压烧结示意图
226
热压烧结法的主要优点:
a.热压时,由于粉料处于热塑性状态,形变阻力小,易于塑性流动和致密化,所需的成型压力仅为
冷压法的1/10。
b.由于同时加温、加压,有助于粉末颗粒的接触和扩散、流动等传质过程,降低烧结温度和缩短烧
结时间,因而抑制了晶粒的长大。
c.热压法容易获得接近理论密度、气孔率接近于零的烧结体;容易得到细晶粒的组织和实现晶体的
取向效应及控制含有高蒸汽压成分的系统的组成变化,因而可获得具有良好机械性能、电性能的制品。d.可生产形状复杂、尺寸较精确的制品。
热压法的缺点是:生产效率低,成本高,且不便于批量生产。
2)热等静压烧结法
热等静压烧结(Hot Isostatic Press Sintering,简称HIPS)是将分散有晶须(短切纤维)、陶瓷基体粉末
的坯件或烧结体装入包套中,再置于等静压炉中,使其在加热过程中经受各向均衡的压力,在高温和高
压共同作用下烧结成陶瓷基复合材料的方法。又称高温等静压烧结(HighTemperatureIsostaticPress
Sintering, HIPS)高压缸
气瓶冷却水入口
巧工件
发热体
压力计热电偶
压缩机气体供给
超压排出
图13-25热等静压烧结示意图
所谓等静压成型,是使粉料在各向同时均匀受压的一种成型工艺,有干袋法和湿袋法两种。
a湿袋等静压法
(a】(b)
(c)
(d)
(c)
图12-26湿袋法等静压过程示意图
a装模;b封闭塞紧模具;c放入高压容器;d加压;e取模
b.干袋等静压法
(a)
(6)(c)
(d)
(c)
图12-27干袋法等静压过程示意图
a粉料斗;b压力室;c装入粉料;d加压:e出坯
热等静压烧结法的主要优点:
a.可制做形状复杂,致密度、均匀度高的压坯
b.可以降低烧结温度,烧结时间短:
c.无需烧结添加剂即可制备出显微结构均匀且不含气孔的致密的材料,致密度接近理论值
d.模具制做方便,成本低:
e.陶瓷基复合材料强度高、韧性好,韦伯尔模数大。
缺点:设备昂贵、生产率低。
3)活化烧结法
又称反应烧结和强化烧结。其原理是在烧结前或者在烧结过程中,采用某些物理的或化学的方法
使反应物的原于或分子处于高能状态,利用这种高能状态的不稳定性,容易释放出能量而变成低能态,
作为强化烧结的新的驱动力。
活化烧结法所采用方法有:电场烧结法、磁场烧结法、超声波和辐射等多种方式。所用的化学方法
有:以氧化还原反应;氧化物、卤化物和氢化物的离解为基础的化学反应以及气氛烧结等。
反应烧结主要特点是:
a.烧结过程中制品的密度加大,且制品质地均匀:
b.烧结坯件不收缩,易于制造尺寸精确的制品;
c.降低烧结温度,缩短烧结时间:
d.工艺简单、经济,适于大批量生产。
反应烧结的缺点:制品密度较低(仅为理论密度的90%左右),因此力学性能较低
4)微波烧结
微波烧结(Microwave Sintering)是利用陶瓷及其复合材料在微波电磁场中因介质损耗加热至烧结温
度而实现致密化的快速烧结技术。
其本质是微波电磁场与物料直接相互作用。由高频交变电磁场引起陶瓷及其复合材料内部的自由
与束缚电荷(如偶极子、离子和电子等)的反复极化和剧裂旋转振动,在分子之间产生碰撞、摩擦和内耗,
使微波能转变为热能,从而产生高温,达到烧结目的。
微波烧结的升温速度可达500℃/min以上。由于烧结速度快,可以获得高强度、高韧性的超细结构,
进而可以改进材料的宏观性能。微波烧结还具有高效节能的特点。
(6).先驱体热解法
将短切纤维、陶瓷微粉、有机先驱物和溶剂混合、搅拌,模压制成坯件,将此坯件在一定温度下,
使有机先驱物转化为无机组分,制成短切纤维补强陶瓷基复合材料,这种工艺称为先驱体热解法。
用来制备SiC-SiC陶瓷基复合材料。228
优点是成型容易、烧成温度低、工艺重复性高:其缺点是制品气孔率高,收缩变形大
(7).电泳沉积成型工艺(Electrophoretic Deposition Process)
陶瓷粉末和增强体(晶须或短切纤维)的悬浮溶液分散体系在直流电场作用下,荷电质点向电极迁移
并在电极上沉积成一定形状的坯件,经干燥、烧结后获得陶瓷基复合材料制品。
分散体系中由于质点离解或吸附使质点表面带电。分散介质可以用水或溶剂。电极材料用金属或
石墨等。体系中加入表面活性物质可以改变质点的荷电性质。
此工艺适宜制造薄壁异形筒(管)状和棒状、板状制品,以及层状复合材料和梯度功能复合材料。
2.原位生长晶须补强陶瓷基复合材料工艺
原位生长工艺(In-situ Growth Process)是通过化学反应在陶瓷基体中原位生成补强组元(晶须或高长
径比晶体),从而形成晶须补强陶瓷基复合材料的工艺。根据晶须生长的热力学,在陶瓷基体原料中掺
入可生成晶须的元素(或化合物),控制工艺条件,使在陶瓷基体致密化过程中在原位同时生长出晶须,
形成陶瓷基复合材料。
陶瓷液相烧结时某些晶相能够形成高长径比晶体,利用这一性质,控制烧结工艺使基体中生长出这
种起补强作用的晶体,形成陶瓷基自补强复合材料。
原位生长工艺的优点是:可以使用低价原料,环境污染小,工艺简单。
缺点是:难以制备完全致密的复合材料。
14碳/碳复合材料成型工艺
14.1概述
14.1.1定义
碳/碳复合材料是以碳(或石墨)纤维(编织物)为增强材料,以碳(或石墨)为基体的全碳质复合材料。14.1.2碳/碳复合材料的发展及应用
碳/碳是用碳纤维增强碳基的一种高技术新材料。自1958年问世以来一直受到尖端技术的高度重视,迄今为止仍是战略导弹端头结构和固体火箭发动机喷管的首选材料。碳/碳复合材料比强度、比模量高,高温下仍具有高强度,有良好的耐烧蚀性能、摩擦性能和抗热震性,因而受到航天航空技术的关注,它不仅是一种极好的烧蚀防热材料,也是最有前途的高温热结构材料。
碳/碳材料从20世纪60年代起至今大体经历了四个发展阶段,即60年代,工艺基础研究阶段,完成了化学气相沉积工艺(CVD)和气相浸渗工艺(CVI)的技术基础研究:70年代,应用开发阶段,用作导弹端头帽和飞机刹车片;80年代,热结构应用开发阶段,用作航天飞机抗氧化鼻锥帽、机翼前缘构件:90年代,致力于降低成本、新工艺开发和民用应用研究。目前碳/碳复合材料的研究应用水平仅次于树脂基复合材料,先于金属基与陶瓷基已走向工程应用。多年来美、法、英等工业发达国家相继研究开发了两向、三向、四向、七向、十三向等三维多向编织和正交细编、细编穿制、抗氧化、混杂和多功能等多种碳/碳复合材料,材料性能也从单一的抗烧蚀发展到抗烧蚀、抗浸沏、外形稳定的多功能材料,并大力向民用开发。
碳/碳复合材料的应用主要在以下几个方面:洲际导弹的端头、火箭发动机喷管、高温热结构部件和飞机刹车盘。如美国的MK-12导弹弹头采用的是细编穿刺碳/碳复合材料:MK-5采用带WC芯的碳/碳复合材料:美国MX导弹、法国M4潜地导弹采用了碳/碳喷管喉衬:美、法联合研制的远地点火箭发动机喷管使用了超细编三向碳/碳复合材料。用于高温热结构的碳/碳复合材料要解决高温抗氧化问题,70年代中后期美国开展了这一研究,并在1981年成功地用于航天飞机上,目前用SiC涂层的抗氧化碳/碳使用温度已达1650℃,1988年前苏联的航天飞机“暴风雪”号用于鼻锥帽和机翼前缘的抗氧化碳/碳承受了1600℃的高温。对于长期耐久使用的抗氧化碳/碳材料正准备用于飞机发动机上,法国、美国和德国都进行了研究试验,预计在2010年前后可用于新一代高推比发动机的关键部件。碳/碳复合材料作为飞机刹车材料起始于70年代初期,1971年在英、法、意联合研制的协和号飞机上,首次用碳/碳作刹车盘。经过实用的考验后不久,相继有Superl0飞机(1973年),BAel46飞机(1978年)、波音757飞机(1989年)等使用了碳/碳复合材料刹车盘。80年代中后期碳/碳作为飞机刹车材料已完全成熟,此后所有飞机都采用了碳/碳制作刹车盘,目前英国的邓录普(Dunolop)公司,法国SEP公司,美国Bendia公司、ABS公司、Goodrich公司、俄罗斯的尼古拉菲特公司已批量生产。
14.2碳/碳复合材料的制备工艺
碳/碳复合材料的制备工艺过程大致可归结如图14-1所示。
碳纤维增强坯件
(碳毡、碳布、碳纤CVD渗透
维缠绕、碳纤维多树脂或沥青浸渍
向编织物)
纤维与树脂
的预浸料热压制坯
碳化
碳/碳复合材料
~1000℃
短纤维与沥青喷射制坯
石墨化
或树脂混合液2000~
3000℃
石墨化的碳/碳复合材料
图14-1碳/碳复合材料的制备工艺过程
230
14.2.1碳/碳复合材料的增强材料坯件
制备碳/碳复合材料产品,通常首先将碳纤维制成与产品形状相近的增强材料坯件。坯件可通过纤维(或布带)缠绕、短切纤维模压或喷射成型,布叠层,碳毡,布叠层(或碳毡)加垂直平面的纤维束穿刺,纤维编织(机织、辫织、纤维束多向立体编织)等方法制成。其中,缠绕、模压和喷射成型常使用胶粘剂固定纤维位置,在后续的工序中,即胶粘剂被热解为低分子气体(逸出)和碳,后者成为碳/碳复合材料基体的组成部分。缠绕、模压和喷射成型的工艺与设备均与树脂基复合材料相同。
碳毡可由粘胶丝毡碳化或聚丙烯毡预氧化、碳化后制得,碳毡叠层后,可用碳纤维束穿刺增强(图14-2,z向或x、y、z三向)
用碳布叠层后,也可用碳纤维束(或碳纤维-树脂复合材z纱
料细杆)在叠层平面的垂直方向(z向)穿刺增强,形式上类似
于昔日的布鞋纳底以线束来增强布袼褙。毡
坯件也可用经预氧化的聚丙烯腈毡,在后续工序中,预
氧化聚丙烯腈纤维与基体同时碳化,形成碳纤维增强体。
辫织常用于管状坯件增强材料的编织,它也可用于织成y纱
一定宽度的带状件。辫织借鉴于鞋带、电线纱包护套或电缆
金属丝屏蔽套的工艺。
纤维束多向立体编织的特点是纤维束在坯件的有用部
分基本上保持准直,相互之间不因交叉而弯曲(即无曲折编
织,NonCrimpweave,简称NCW),因而有利于在复合后发
挥纤维的轴向力学性能。较常见的为三向编织,即纤维在经、纱
纬、纵(即x、y、z)三个方向互成90°正交排列。
在三向编织的基础上,又发展了四向、七向、十一向编图14-2用碳纤维束穿刺增强碳毡坯件
织。四向编织是按直角坐标系所组成的立方体的四个长对角线方向布置纤维束。七向编织则是在x、yz三方向外,再加上上述四个长对角线方向。多向编织在专用编织设备上进行。
14.2.2碳/碳复合材料中碳基体的形成
在坯件中碳纤维的间隙中导入碳源物质,通过加温热解碳化,在碳纤维周围形成碳基体。表14-1列出了几种碳源物质的组成。表14-1几种碳源有机物及其组成
化学组成/%碳原子数/%
CHN
天然沥青85.59.70.61
4.3941.9
煤沥青93.34.40.851.000.3063.6
酚醛树脂79.25.715.9026.4050.0
PAN67.95.742.9
甲烷75.025.020.0
乙烷80.020.025.0
丁烷82.817.228.6
乙烯85.714.333.3
丙烯85.714.333.3
碳源物质是气态时,采用化学气相沉积法,生成的碳基体称为沉积碳:碳源物质是液态时,如沥青、合成树脂,通过压力使其渗入增强材料坯件的孔隙,然后通过加温热解碳化;碳源物质是固态时,主要指碳/树脂复合材料,它的树脂基体是经过固化后,再通过加温热解碳化形成碳/碳复合材料。后两种情况生成的碳基体称为树脂碳。
为了简化碳/碳复合材料的致密化工艺,也可在沥青中掺入炭粉(石墨粉或焦碳粉),它们在沥青热解碳化后分散于沥青碳中,成为碳基体的组成部分。231
上述每种形成碳基体的方法,通常需要重复进行多次,并且将几种方法联合使用,以达到要求的碳/碳复合材料的密度。通常还需进行高温处理,使基体碳石墨化。
1.化学气相沉积工艺(CVD)
用化学气相沉积工艺形成碳/碳复合材料的基体,应首先将碳纤维增强材料坯件置于沉积炉中,通以甲烷等烃类气体(碳源气体),混合氢和氩等惰性气体作为载气,加温至1000~1100℃进行热分解,碳源气体生成一些活性基团,与坯件中的碳纤维表面接触进行沉碳。为了得到致密的碳/碳复合材料,必须使活性基团扩散到坯件的孔隙内,且应从坯件结构上避免瓶颈型孔隙,防止沉积过程中堵塞气体渗入的通道。
碳/碳复合材料的化学气相沉积有4种方法,即均热法、热梯度法、压差法和脉冲法。
(1)均热法又称恒温渗透工艺。
将坯件置于沉积炉中,通过感应线圈加热至950~1150℃,向炉内以低压(0.1~20kPa)通入用惰性气体(H2,N2或它们的混合)作载气的烃类碳源气体(如CH),在0.13~20kPa压力下,碳源气体接触坯件表面并通过孔隙向坯件内部渗透,在热的碳纤维周围沉积碳。由于气体向坯件内部渗透(扩散)的速率低,因此渗透所需时间较长,此时碳的沉积速率大约是0.25-2.5um/h,加工一件制品往往需数周甚至数月之久。
均热法存在的问题是:坯件在炉内温度不均匀,外表较内部高,因此,在靠近坯件的外表面沉积碳速率较高,容易堵塞孔隙通道,形成致密的外壳,使坯件内部的沉积无法进行,常需要通过机械加工磨去外壳,使被堵塞的孔隙重新通畅;由于沉积过程要反复多次,因而不仅使工艺周期延长(每一周期约50~120h),而且所获得的碳/碳复合材料制品的密度不均匀,均热法的长处是在同一设备中一次可放置多个坯件。
(2)热梯度法
热梯度法沉积炉的工作原理与均热法基本相同,但它依靠置于坯件中央的石墨电热元件加热。因此,在工作中形成从坯件中央表面降低的温度梯度。碳源气体首先与坯件的较低温度的表面接触,逐步向内部高温处扩散,越向内部,沉积速度越快,这就改善了因表面沉积速率快而生成硬壳的现象,可以减少甚至不需中途取出进行机械加工,因而缩短了加工周期。随着沉积时间的增加,沉积层由内向外移动。同时,随着沉积造成的致密化,已沉积部分的导热性增加,内外温度梯度逐渐变小。
热梯度法比均热法的加工周期短,制品密度高且均匀,因此性能也较好。此法存在的问题是工艺重复性差,不能同时加工不同坯件和多个坯件,坯件的形状也不能太复杂。
(3)压差法
压差法是在沉积碳时,沿坯件厚度方向造成一定的压力差,使反应气体在压差作用下强行通过多孔坯件。压差法的沉积速度快,沉积的碳也较均匀,适用于透气性低的工件。它也容易生成表面硬层,在沉积过程中需要中间机械加工。
(4)脉冲法
是压力真空脉冲渗入法的简称,它是一种改进了的均热法。其特点是在沉积过程中利用脉冲压力阀对沉积炉交替充气和抽真空。让坯件在碳源气体中暴露几秒钟,然后对沉积炉抽真空排除废气,再充入反应气体,如此重复循环,以增加反应气体在坯件中的渗透深度。
在碳/碳复合材料的气相工艺中,还有一种称为化学气相渗透(CVI)的工艺。它主要用以沉积碳化物或氮化物。例如,用有机硅烷气体(代替CVD法中的碳源气体)在高温作用下发生热解,热解气体在通过多孔的碳纤维坯件内部时,与坯件中碳纤维表面的碳原子产生化学反应生成固态的SiC和碳,因此得到的是混杂基体复合材料,即C/C-SiC。这种材料的高温抗氧化性能比C/C复合材料有较大的提高。CVI的设备与CVD相同,同样可以采用均热法、热梯度法、压差法或脉冲法。
由上述气相工艺可见,沉积碳的类型、沉积速度和沉碳效率,取决于碳源气体的流动速度、浓度,运载气体的压力,坯件的结构情况和与碳源气体的接触时间,碳源气体的热解温度与压力等。
2.浸渍热解工艺
在惰性气氛中使坯件在压力作用下浸渍有机原料(如沥青或合成树脂),然后使浸入坯件内的有机原料热解碳化(沥青热解碳化,合成树脂固化、进而热解碳化),形成碳基体。
232
不同有机原料热解时的碳化收率见表14-2
表14-2有机原料含碳量及热解碳化收率
原料含碳量
碳收率/%原料
含碳量/%
碳收率/%
1%
聚苯并咪唑96
73
煤焦油沥青
75
60
聚苯92
71
电极粘合剂
92
40
沥青
甲醛二苯80
65
植物性沥青
69
30
树脂糠醇
75
63
石油沥青
88
21
酚醛78
60
酚醛60%
78
75
环氧-甲阶酚醛74
55
煤焦油沥青
聚酰亚胺77
49
树脂与沥
氧茂甲醛60%67
三苄基苯95
87
青混合
煤焦油沥青
人造异三苄基苯95
70
环氧酚醛60%
沥青60
煤焦油沥青
浸渍可在常压或加压的条件下在热压罐中进行,浸渍压力与温度依有机原料的粘度而定。提高压力有利于有机原料向坯件内部浸渗,因而产物的致密度较高;若采用较低的浸渍压力,则为了达到相同的致密程度就需要将工艺周期重复多次。
(1)沥青浸渍热解工艺
作为碳/碳复合材料基体常用的碳源物质有煤焦油沥青和石油沥青两种。浸渍时必须将沥青熔融为液态(200~230℃),并真空除气,将坯件抽真空15min后浸入,保持真空至发泡停止,然后加压至0.6MPa达15min,再重复抽真空和加压0.5h,使沥青能深入碳纤维增强材料坯件的内部孔隙,同时在惰性气体保护下缓慢升温(例如,以50℃/h升温速率从室温升到200℃,继而再以5℃h升温速率从200℃升到540℃,再以10℃/h升温速率升到800℃)。热解过程中同时需施加压力。所施加的压力应高于95MPa,在压力作用下,沥青的内部挥发和分解的气体才能够克服沥青的表面张力而释放出来,不致在基体中造成大的气泡,以使热解形成的沥青碳均匀地分布于坯件的孔隙中。浸渍和热解过程要重复多次,以使碳碳复合材料达到要求的密度。所生成的碳基体在扫描电镜下呈层片状结构或浪花形层片结构,在浪花形层片结构的某些区域中还存在呈球状的碳,此种由沥青热解而成的碳化残留物称为沥青碳,它们容易在后续的石墨化工艺中石墨化。
(2)树脂浸渍固化、热解工艺
用合成树脂制备碳/碳复合材料的基体,与沥青相比有以下优点:
①合成树脂的粘度较低,因此在低温和低压力下容易浸透:
②合成树脂的纯度较高,化学结构容易鉴定与控制,它的成分不像沥青随产地和加工方法的不同而波动;
③能够有较大的自由度选择含碳量高并可转化为耐高温碳质的树脂体系。
常用的树脂有酚醛、环氧一酚醛、糠醇、芳基乙炔等。与沥青不同的是,这些浸渍在增强材料坯件中的合成树脂,首先要经过加温发生固化反应,形成不溶的热固性树脂基体,再进一步加温使已固化的树脂基体热解,形成碳/碳复合材料的碳基体。经过一系列复杂的物理一化学变化,例如:热膨胀,合成树脂固化过程中的聚合反应,副产物(如水和水分子)的蒸发与排出,树脂热解碳化,最后在坯件的纤维间隙中留下无规结构的碳。由合成树脂热解而生成的碳化残留物称为树脂碳,又可与沥青热解形成的沥青碳一道统称为浸渍碳。显然,经过热解后的碳基体仍然是多孔的。为了达到碳/碳复合材料性能要求的密度,浸渍-热解要反复进行多次。沥青浸渍热解、树脂浸渍-热解和化学气相沉积可交替进行。
(3)热等静压碳化工艺
碳/碳复合材料的浸渍-碳化工艺一般要在压力罐中连续完成。对于性能要求高的碳/碳复合材料,则可以采用热等静压碳化工艺。
热等静压碳化工艺在温度和压力可以程序控制的热等静压设备中进行。首先将经过CVD或有机原
233
料浸渍的坯件置于金属包套中,对包套抽真空并夹封,通过检漏确认可经受碳化温度压力的周期变化不致泄漏,将封有坯件的金属包套放入热等静压釜中,以50℃h的升温速率加热至一定温度(如250℃)开始施加等静压(10-100MPa),再以10~15℃/h升温速率升温至550℃,超过550℃后,升温速率适当加快,升至1000℃并保持所需的碳化压力,以保证浸渍在坯件中的有机原料的最大碳化率。由于碳化是在密封的包套中和热等静压下进行,避免了所浸渗的原料从坯件中流失,制品可以达到较高的密度。
3.浆料浸渍-热解工艺
用沥青浸渍-热解工艺制备碳/碳复合材料时,由于沥青在高温流失、小分子物释放、碳化收缩等原因,在基体中产生孔隙和裂缝。为了达到要求的致密度,浸渍-热解要循环进行多次,因此,成型工艺周期长,制品成本高。为了减少沥青碳化时的流失和收缩,缩短成型时间,可采用浆料浸渍工艺。浆料工艺的要点是在沥青中掺入炭粉制成浆料,采用碳纤维(布带)缠绕技术,使碳纤维(布带)浸渍掺有炭粉的浆料制成坯件,在热压炉中碳化成型:或者,使掺有炭粉的浆料制成坯件,在热压炉中碳化成型:或者,使掺有炭粉的浆料和经过预处理的短切碳纤维捏合,经热压成为坯件,再在热解炉中碳化成为碳碳复合材料。浆料浸渍-热解工艺流程如图14-3所示。
与仅用浸渍-热解工艺相比较,浆料浸渍-热解工艺周期仅为1/5~1/4,制品成本仅为1/4~1/3。由于浆料粘度大,不能通过压力浸渗,因此不适用于制作多向编织物增强的碳/碳复合材料。
碳纤维预处理
工业乙醇
炭粉预混
混合→捏合→干燥→热压
沥青粉
成品石墨化
碳化
浸渍
碳化
2200C900C
900C
图14-3碳/碳复合材料的浆料浸渍-热解工艺流程
14.2.3碳/碳复合材料的热处理和石墨化处理
通过对增强材料坯件进行化学气相沉积,浸渍沥青并热解,或浸渍合成树脂固化并热解,及经过多次浸渍-碳化增密循环工艺流程,得到了全碳素的碳/碳复合材料。所得到的材料,还需要经过温度至少高于制品最高使用温度的热处理,以使其获得稳定性,增加抗热震能力和改善烧蚀性能。
对于化学气相沉积碳、沥青碳,在一定高温(~3000℃)下可使碳结构石墨化:对于树脂碳,也可以部分石墨化。如增强材料坯件的碳纤维是未经石墨化处理的,也可以同时部分石墨化。石墨化的结果,使复合材料的碳结构缺陷逐渐消除,晶体趋向完善,因而强度与模量及热膨胀系数略有降低,体积收缩,密度增大,导热系数增大,抗冲击能力和断裂延伸率增大,断裂韧性和抗热应力的能力增加,烧蚀性能获得改善。
石墨化处理常在碳/碳复合材料的热解炉内进行,以70~100℃/h升温至2400~3000℃并保温2h以上,然后随炉缓慢降温,以防止温度变化过快引起产品开裂。
石墨化处理可以因碳/碳复合材料的增密要求而与浸渍-热解碳化过程联合循环多次。
14.2.4碳/碳复合材料的抗氧化处理
碳/碳复合材料是全碳质材料。碳在高温下不软化也不熔化,直至2500℃以上才发生升华,因此,其高温性能优越。但是,碳/碳复合材料的抗氧化性能不符合高温材料的要求,它在空气中从400℃即开始氧化,与空气中的O2、H2O、CO2等均可发生化学反应,因此,必须对碳/碳复合材料进行抗氧化处理,即在碳/碳复合材料表面和内部引入抗氧化物质和堵塞氧化性气体渗入内部的通道,以隔绝它们与碳元素的接触。经过抗氧化处理的碳/碳复合材料,可以改善它在高温氧化环境条件下的性能,使其继续保持高比强、高比模、耐热冲击等一系列优点,并具有多次重复使用的能力。
抗氧化处理可以在碳/碳复合材料的成型前进行,也可以在碳/碳复合材料的成型后进行。前者主要改善碳/碳复合材料基体的组成,后者则主要在碳/碳复合材料的表面形成抗氧化的覆盖层。碳/碳复合材
234
合并具有梯度性质的SiC涂层,这种有一定厚度的成分连续过渡(渐变)带,减缓了因碳与SiC热膨胀不匹配造成的热应力,并可在该扩散涂层厚度范围内抵御氧化腐蚀,同时,因为SiC的坚硬性,也增大了抵御高速气流与粒子冲刷侵蚀的能力,保护了内层碳/碳复合材料,使之在1700℃以下具有优良的抗氧化能力,在高于2000℃也具有短期工作的能力。
(2)抗氧化涂层刷涂工艺
当碳/碳复合材料的工作温度不是很高(≤1000℃)时,SiC涂层可以采用较简单的刷涂工艺。即将抗氧化性强的硅化物粉料(过150目)与玻璃粉料用水调成浆料,用毛刷对碳/碳复合材料涂覆、烘干、烧结,并经多次重复。初始层(内层)的玻璃粉料为高软化点的,外层为低软化点的,在软化点温度以上,玻璃粉料可流动形成致密膜,它们使高温下工作的碳/碳复合材料具有表层裂纹自愈合能力,并可阻挡氧气向内部渗透。此种涂层的作用范围如图14-5所示。
开始内层
氧化出现
长期
温度裂纹
工作
热环高
循最温
温度度
极限温度
400℃温度
外层900℃1000℃
对内
层微
裂纹内层固有
自愈防氧化区
合区涂层有效防氧化范围
图14-5刷涂抗氧化涂层作用范围示意图
(3)抗氧化涂层表层处理工艺
碳/碳复合材料经过抗氧化处理和抗氧化涂层后,尚需在其最外层进行表层处理。表层处理包括TEOS处理和涂覆玻璃密封剂,TEOS是原硅酸四已酯(tetraethylorthosilicate)的英文缩写,将经过抗氧化处理和抗氧化涂层的碳/碳复合材料真空浸渍TEOS,浸渍后经100℃固化,如此反复多次(例如5次),再在315℃热解,形成附着与钉扎于SiC涂层外表的具有低透气性的无定形SiO2表层
为了在温度低于Si0流动温度下对涂层中发生的热应力裂纹也具有自愈合能力,在TEOS处理的表层之外,再用玻璃密封剂覆盖。玻璃密封剂包括硅酸钠玻璃系统(SN)、硼硅酸钠玻璃系统(BSN)和三氧化二硼(B0)玻璃系统等。它们在涂覆后经烘干即成。经过表层处理的碳/碳复合材料,它的抗氧化能力较之仅经过SiC涂层的可提高一个数量级。
料抗氧化处理措施包括:
①在基体中散布抗氧化微粒:
②加入反应物,使在基体形成的同时产生抗氧化微粒;
③用形成抗氧化物的溶剂或胶质悬浮物渗透碳/碳复合材料,并经处理使之形成具有一定厚度和密度渐变的抗氧化层
④固渗抗氧化物质,形成一定厚度的抗氧化保护层,或者在碳/碳复合材料表面涂刷抗氧化粉料淤浆,经热处理形成抗氧化涂层:
⑤气相浸渗抗氧化物质(即CVI):
在经过涂层或其它抗氧化处理的碳/碳复合材料表面涂玻璃密封剂:形成阻塞氧气通道的密封涂层(又称外釉层)。
抗氧化涂层要求本身抗高温氧化,熔点高,致密性高,与碳/碳复合材料的浸润性好,热膨胀系数匹配。通常,单一涂层无法同时满足上述要求,因此往往将几种措施联合采用。
1.抗氧化CVI工艺
用高温热解气体通过多孔的碳纤维坯件,与所接触的碳一道产生化学反应生成碳和碳化物。例如,用有机硅烷气体热解可生成固态的C和SiC,形成C/C-SiC混杂基体复合材料,其抗氧化性能优于碳碳复合材料。
2.抗氧化浆料浸渍-热解工艺
用浆料浸渍-热解工艺制备碳/碳复合材料时,在浆料中加入抗氧化添加剂,添加剂包括Ti、W、Zr、Ta、Mo等过渡族金属化合物、氧化物(如B2O3、SiO2、ZrO2)、碳化物(如SiC、BC、ZrC)以及液相烧结剂(如Co、Ni)和助碳化剂(如TiCl、ZrOCl)等。工艺过程大致如图14-4所示,将添加剂与炭粉(沥青焦、石墨粉)放置一道进行研磨,使之充分分散,再加入沥青(粉)充分混合,加入短切碳纤维使之均匀混合。在一定温度与压力下热压成型,然后碳化。为了达到一定密度和增强抗氧化性,再循环浸渍与碳化,浸渍剂可以是有机硅高分子,无机盐(如硼酸盐、磷酸盐),最后经石墨化处理即制成抗高温氧化的碳/碳复合材料。它的基体含有多元金属间化合物,构成了梯度防护体系,提高了材料的高温抗氧化性。其中,BC生成的BO3在高温下具有流动性并与碳有较好的互溶性,具有防止氧渗透的功能,可以起保护膜作用,并能起自愈合微裂纹的作用;SiO2也具有流动性和低透气性,以及有自愈合微裂纹的作用。碳纤维
炭粉混合球磨
充分搅拌
热压
抗氧化
添加剂沥青
碳化
←→浸渍
成品石墨化
图14-4碳/碳复合材料抗氧化浸渍-热解工艺流程图
按照添加剂种类的不同,基体中分别含有SiC、BN、TiC、BC或ZrB2,即混杂基体复合材料C/C-SiC,C/C-BN,C/C-TiC,C/C-BC和C/C-ZrB2,它们均可在1000℃以上抗高温氧化。
3.抗氧化涂层工艺
(1)SiC涂层固渗工艺
在碳/碳复合材料制件表面包覆SiC抗氧化保护涂层,不仅可以提高其高温抗氧化性能,还可提高其抗疲劳能力,使之具有可多次重复使用性。
SiC涂层固渗工艺是将已制得的碳/碳复合材料构件放置在石墨坩埚中,周围填充SiC(60%)、金属Si(30%)和A103(10%)等混合粉料,在高温(>1600℃)处理1-2h,产生Si与C的液相及气相反应,液态Si与C形成SiC,气态Si向碳/碳复合材料内部渗透,与C形成SiC,构成与碳/碳复合材料紧密结
235
15金属基复合材料成型工艺及设备
15.1概述
15.1.1金属基复合材料的发展概况及前景
金属基复合材料(MetalMatrix Composite,简称MMC)的性能既优于金属材料也优于树脂基复合材料。它既具有金属的性能,也有树脂基复合材料无法达到的使用温度高、剪切强度高、阻燃、不老化、不吸湿、不放气、耐磨损、导电、导热等金属属性,是外层空间结构及一些工业领域中有广泛应用前景的材料,因而继树脂基复合材料之后,掀起了开发研究金属基复合材料的热潮。
金属基复合材料在国外起步于20世纪50年代末期或60年代初期。当时由于受到增强纤维品种少的限制仅发展了硼纤维增强铝、钛等少量品种,成型工艺多沿用树脂基复合材料的成型方法,如铺层工艺和缠绕工艺。它最具代表性的应用是用硼纤维增强铝制造的哥伦比亚号航天飞机构件,包括主骨架、肋条、桁架支柱、制动器支撑架等构件共89种243件,总重150kg。使用金属基复合材料后比原铝合金构件重量减轻44%,从而奠定了金属基复合材料开发应用的基础。但用硼纤维作为复合材料的增强纤维造价特高,即使是在航天飞行器这种尖端结构上应用,也承受不了这种材料的高昂价格(硼一铝的价格约为热轧钢材的1860倍),因此自70年代末期,金属基复合材料的研究开发者启用了石墨纤维和碳化硅纤维等作为增强材料,并为解决纤维和金属基体复合时界面间的反应做了大量的研究工作。同时也在寻求廉价的金属基复合材料,如晶须、短纤维、颗粒增强的金属基复合材料。实践证明,这种复合材料尽管增强效果不如连续纤维那么明显,但由于可沿用金属材料的加工成型方法,后续的加工费用低,在性能上又能弥补单一金属材料的不足,使材料的刚度、耐磨性、耐热性、抗蠕变性均有较大的提高,因而曾得到了较大的发展。进入80年代,由于新型高性能增强纤维的出现,如化学气相沉积(CVD)法SiC纤维、纺丝SiC纤维和表面带有TiB、TiC、SiC等涂层的系列石墨纤维,并发展了可以将铝、钛、镍、金属间化合物等性能较高的金属作为基体的成型工艺,从而进一步推动了金属基复合材料的发展。由于金属基复合材料起步较晚,目前技术水平大部分还处于实验室研究阶段,只有小部分实现了工业化。金属基复合材料成型工艺的特点是先做成预制物再复合成型。先期预制物有粉末布、等离子喷涂无纺布、增强丝、基体-增强丝混合编织带等。成型工艺有液相熔铸法、半固-半液相热模压法和固态扩散法。在所有工艺中成箔和热压两道工序是不可缺少的。近年来推出的等压冷轧箔材轧机是供金属基复合材料成型的有效装备。
15.1.2金属基复合材料的基本性能特点
1金属基复合材料的优点
(1)高比强度和高比模量,金属基复合材料纵向比强度和比模量与树脂基复合材料可以相媲美,大大优于常用金属材料。
(2)耐高温性好。树脂基复合材料的使用温度不超过200℃,耐高温的聚酰亚胺树脂可提高到300℃:而金属基复合材料的使用温度远远高于此值。铝基、镁基可以在400℃长期使用。并可短期使用于500℃,钛基的使用温度为600℃-700℃;金属间化合物和镍基高温合金基可达1000℃-1500℃。
(3)导电导热。对飞机蒙皮这一类构件而言,在服役中会遇到各种复杂的气候条件,包括天然与人工诱发的粒子云环境,用树脂基复合材料制造蒙皮,由于它的导热性差且不导电,飞行器内部温度不易散发,而且容易发生静电积聚导致雷击。金属基复合材料是高导电和高导热材料,不易发生这类问题。(4)热膨胀系数小,尺寸稳定性好。金属基复合材料的热膨胀系数与树脂基复合材料相当,尺寸稳定性明显优于后者和一般金属材料。例如,Gr/Mg(石墨/镁)的热膨胀系数可以设计成接近零,加之由于它具有良好的刚度(比模量大于16×10),因而是高精度卫星波导管的理想材料。
(5)耐磨性与阻尼性好。金属基复合材料的阻尼性能虽比树脂基复合材料略差,但优于金属。在耐磨性方面,金属基复合材料远忧于金属,对比实验表明:铝合金、碳化硅颗粒增强铝合金、氧化铝纤维增强铝合金的磨耗率之比为96:4.5:1,因此,当与价格因素同时考虑时,碳化硅颗粒增强铝复合材料是制作新型柴油机活塞(冠部耐磨部分)的最佳选择。
(6)不吸湿、不老化、无放气污染。树脂基复合材料在潮湿环境中易吸湿,受湿热及紫外线辐射会发生性能降解及老化破坏,在负压或真空条件下(如大气层外)会析出小分子气体污染卫星或航天器舱内的电子器件而影响仪表精度。金属基复合材料不吸湿、不老化、不放气,抗环境腐蚀性良好,如碳化
237
硅纤维/铝复合材料在常温水中漫泡36天,没有发现性能变化,强度保留率接近100%。
此外,金属基复合材料抗热冲击(温度骤变或热循环)能力比树脂基和陶瓷基复合材料强;金属基复合材料韧性高、抗疲劳性能好,对表面缺陷敏感性也比陶瓷基复合材料低。
2金属基复合材料的主要缺点
(1)制造困难。增强材料(纤维和晶须)向基体中掺入困难,金属基复合材料的复合工艺比树脂基复合材料复杂,常需要高温、真空和较大压力。
(2)难于形成理想的界面。金属基复合材料的性能和制造加工都与界面特性有关,复合材料的最终性能受其界面的控制,而制造过程的差异则会产生截然不同的界面状态。固此,制造方法和工艺参数的选择严重地影响界面并最终影响复合材料的性能。
(3)加工困难。当前金属基复合材料的构件成型和二次加工比树脂基复合材料困难得多。由于金属基复合材料(如SiC/A1)的强度和硬度很高,在切削加工时对刀具磨损严重,因此不得不使用价格昂贵的硬质合金或金刚石刀具。
(4)价格昂贵。美国1985年的一篇报道提供的价格对比为,以热轧钢材为1,则普通铸铝为1~4,碳化硅晶须或颗粒增强铝复合材料约为600,硼增强铝约为1800,石墨增强铝为4800~20000。金属基复合材料成本高的原因是增强纤维的价格昂贵,同时制造工艺复杂,造成加工过程费用高。后者往往明显地大于前者而成为整体成本中的主要部分。以航天飞机中的B/A管为例,每根重1kg~2.5kg的管件价格为7000美元,设其纤维体积分数为50%,则纤维仅占成本的1/10。零部件形状愈复杂,制造加工费用就愈高,这势必使其应用范围受到限制,目前一般局限于高技术领域。
15.1.3金属基复合材料的应用表15-1金属基复合材料的应用
增强材料基体
主要应用
铝合金人造卫星构件、导弹构件、航天飞机构
碳纤维钛合金
件、发动机风扇叶片
金属间化合物
铝合金卫星天线支架、空间站构件、转缸涡轮
镁合金发动机铸件、直升飞机构件,电刷、大
碳(石墨)纤维铜规模集成电路基板、触头、蓄电池基板、
铅核装置隔板
铝合金传动轴、轻武器、涡轮发动机叶片及其
超合金
碳化硅纤维他耐热件、舰船的上层结构,水下结构、
钛合金鱼雷、甲板
金属间化合物
铝合金飞机机翼蒙皮、紧固件、型材、轻型装
镁合金
碳化硅晶须甲履带、涡轮发动机叶片、汽车摇臂、
钛合金火箭发动机壳体
金属间化合物
铝合金
镁合金型材、齿轮、履带、活塞、连杆、耐磨
碳化硅颗粒钛合金
件、耐热结构件、电子光学仪器
金属间化合物
钨丝镍基超合金
涡轮发动机叶片
铌基合金
不锈钢丝铝合金
汽车发动机连杆
铝合金内燃机部件(活塞头、活塞环槽等)工
氧化铝纤维镁合金
业机器人的传动齿轮、连杆、销子
238
15.2原材料
15.2.1基体材料及其性能
基体是金属基复合材料的主要组成之一,基体对力学性能的贡献远大于它在聚合物基和陶瓷基复合材料中的贡献,且复合材料的比强度、比刚度、耐高温、耐介质、导电、导热等性能则主要由基体决定。基体在复合材料中占很大的体积比,在连续纤维增强金属基复合材料中约占50%-70%,在颗粒增强复合材料中占25%-90%,多数为80%-90%。短纤维、晶须增强金属基复合材料一般在80%-90%。
一般说来,所有金属材料均可用作复合材料基体,已经研究的复合材料基体有铝、镁、钛、铜、铅、锌、镍及其合金,其中铝合金与各种纤维的复合体系几乎都被研究过。对B/A研究得最早,其成型工艺已十分成熟。应用多的有:铝、镁、钛、铁、镍及其合金基体。其使用范围如下:
①450℃以下时,常使用铝、镁及其合金为基体的复合材料:镁是工业用的金属中最轻的一种基体,密度只有1.74g/cm3,虽然镁的塑性变形能力不如铝,但由于其密度低,且与增强材料间的化学稳定性及润湿性良好,故以镁合金作为基体,采用挤压铸造法制造的Gr/Mg复合材料被公认为航天、航空工业中最有应用潜力的、比刚度最高的结构材料,并能满足航天结构件对尺寸稳定性和热稳定性的要求。
②从密度和机械性能等多方面考虑,能在450℃~600℃范围内使用的结构材料只有钛及其合金,用高性能的碳化硅纤维、碳化钛和硼化钛颗粒增强后,钛及其合金的性能明显提高。已制成了SCS-6碳化硅纤维增强钛基复合材料,可用于制造涡轮发动机的叶轮和空心叶片、压气机的叶轮及叶片、发动机的驱动轴及火箭发动机箱等。
③用于1000℃以上的高温金属基复合材料基体材料主要是镍基、铁基耐热合金和金属间化合物。是广泛应用于各种燃气轮机的重要材料,用钨丝、钍钨丝等增强后大幅度提高高温持久性和高温蠕变性能,用于制造航空发动机的叶片和涡轮叶片等重要零件。其目前的最高使用温度达到1100℃。
15.2.2增强材料及其性能
在纤维增强金属复合材料中,纤维是承载相,金属基体的主要作用是将载荷传递和分配到纤维上。对复合材料的增强纤维,要求强度高、模量高、密度低,并要求在高温下性能稳定。
增强材料的形态有连续纤维、短纤维、晶须和颗粒等。连续纤维分粗、细两种,粗纤维直径100m~140m,如钨芯或碳芯的硼纤维和碳化硅纤维,细纤维直径7um~20m,如碳纤维、纺丝碳化硅纤维和氧化铝纤维。此外,金属纤维(W、Mo、Be、不锈钢丝)也是金属基复合材料的一类重要增强材料。
短纤维主要有硼、碳短切纤维和氧化铝短纤维等。
晶须直径0.2m-0.3m,长50um左右,裸眼观察呈粉状。现在工业化生产并由市场供应的晶须材料有碳化硅(SiC)、氧化铝(Al2O)、氮化硅(SiN4)、氧化锌(ZnO)和钛酸钾(KO-6TiO2)等。非连续纤维的筛选、分散、整列和预制块的制造是工艺的难点所在,其尺寸的均匀性对复合材料性能有重要影响。
15.3金属基复合材料的复合工艺及设备
15.3.1金属基复合材料的复合工艺概述
金属基复合材料的制造技术中大部分复合方法还处于实验室研究阶段,只有少部分实现了工业化生产。金属基复合材料的制造技术品种繁多,这些方法归纳起来有以下三大类。
1、固态法
固态法是指基体处于固态制造金属基复合材料的方法,即温度控制在基体合金的液相线和固相线之间。由于整个过程处于较低温度,因此金属基体与增强材料之间的界面反应不严重。固态法包括粉末冶金法、热压法、热等静压法、轧制法、挤压和拉拔法、爆炸焊接法等。
2、液态法
液态法是指基体金属处于熔融状态下与固态的增强材料复合在一起的方法。为了改善液态金属基体对固态增强材料的润湿性,以及控制高温下增强材料与基体之间的界面反应,可以采用加压浸渗、增强材料的表面(涂覆)处理、基体中添加合金元素等措施。真空压力浸渍法、挤压铸造法、搅拌铸造法、液态金属浸渍法、共喷沉积法、热喷涂法等都属于液态法。
3、其它制造方法
其它制造方法除包括固态法和液态法外,还包括在工艺上各有特点的一些方法,如原位自生成法、物理气相沉积法、化学气相沉积法、化学镀和电镀法、复合镀法等。其中有些是比较新的方法,有些虽
239
然历史较久但目前作为金属基复合材料的制造方法已很少使用。
表15-2为金属基复合材料的主要制造方法及适用范围。
表15-2金属基复合材料的主要制造方法及适用
适用金属基复合材料体系
类别制造方法典型的复合材料及产品
增强材料金属基体
粉末冶金SiCp,AO3,SiCw,B4Cp等颗Al,Cu,Ti等SiCp/Al, SiCw/Al, Al2O3/Al, TiB2/Ti
法粒晶须及短纤维
金属
等金属及复合材料零件、板、锭坯等
热压固结Al, Cu, Ti,
B/Al,SiC/Ti,SiC/TiC/Al,C/Mg固态法B,SiC,C(Gr),W
耐热合金
零件、管、板等
法热等静压B,SiC,W
Al,Ti,超合金
B/Al,SiC/Ti管
法
挤压,拉Al
C/AI,A2O3/A棒、管
拔轧制法各种类型增强材料,纤维、晶须、
挤压铸造SiCp/Al, SiCw/Al, C/Al, C/Mg,
短纤维,C,Al2O3,SiCp,Al, Zn, Mg,
法Cu等
A2O3/Al,SiO2/Al等零件、板、锭、
Al2O3-SiO2坯等
真空压力Al, Mg, Cu,
C/Al, C/Cu, C/Mg, SiCp/Al,
各种纤维、晶须、颗粒增强材料
液态浸渍法Ni基合金
SiCw+SiCp/Al等零件、板、锭、坯等
法搅拌法颗粒、短纤维及Al2O3,SiCpAl, Zn, Mg,铸件、锭坯
共喷沉积Al,Ni,Fe等
SiCp/Al,Al2O3/Al等板坯、管坯、锭
法SiCp,Al2O3,B4C,TiC等颗粒金属
坯零件
真空铸造C,Al2O3连续纤维
法Mg,Al
零件
反应自生Al, Ti
铸件
成法
其他电镀及化
方法SiCp,B4C,Al2O3颗粒,C纤维
Ni,Cu等表面复合层
学镀法
热喷镀法颗粒增强材料,SiCp,TiCNi,Fe
管,棒等
15.3.2固态法
1.粉末冶金法
粉末冶金是最早用来制造金属基复合材料的方法,早在1961年就开始利用粉末冶金法制造纤维体积含量为20%~40%的碳/铝复合材料,但由于性能很低,这种方法已不用来制造长纤维增强复合材料,而主要用于制造颗粒或晶须增强金属基复合材料,其工艺流程如图15-1。用粉末冶金法可以制造复合材料坯料,供挤压、轧制、锻压、旋压等二次加工后制成零部件,也可直接制成复合材料零件。美国的DWA公司用此法制造了不同成分的铝合金基体和不同颗粒(晶须)含量的复合材料及各种零件、管材、型材和板材,它们具有很高的比强度、比模量和耐磨性,已用于汽车、飞机、航天器等。
粉末冶金法也被用来制造钛基、金属间化合物基复合材料。
特点:颗粒(晶须)的含量不受限制,尺寸也可以在较大范围内变化,但材料的成本较高,制造大尺寸的零件和坯料有一定困难。
1.颗粒(晶须)混合
热压
成品零件
合金粉末挤压、轧制
复合材料坯
2.颗粒(晶须)锻造
混合冷压烧结成品零件
合金粉末
3.颗粒(晶须)混合
封装除氧
挤压
合金粉末
图15-1粉末冶金法制造金属基复合材料的工艺流程
2.热压法
热压法和下节的热等静压法亦称扩散粘结法,是加压焊接的一种,因此有时也称扩散焊接法。它是在较长时间的高温及不大的塑性变形作用下依靠接触部位原子间的相互扩散进行的。扩散粘结过程可分为三个阶段:①粘结表面之间的最初接触,
由于加热和加压使表面发生变形、移动、表面
膜(通常是氧化膜)破坏;②随着时间的进行发
生界面扩散和体扩散,使接触面密着粘结:③铺金属箔
由于热扩散结合界面最终消失,粘结过程完
成。加热到需要温度
热压工艺通常要求先将纤维与金属基体裁剪成型
制成复合材料预制片,然后将预制片按设计要
求裁剪成所需的形状、叠层排布(纤维方向),
视对纤维体积含量的要求,在叠层时添加基体
箔,将叠层放入模具内,进行加热加压,最终按需要叠层
制得复合材料或零件。也有用纤维织物与基体
箔直接进行热压制造复合材料及零件的。
根据工艺特点,热压法分为模内热压、分加压及保压
步热压和动态热压等几种。
热压法是目前制造直径较粗的硼纤维和
碳化硅纤维增强铝基、钛基复合材料的主要方
法,其产品作为航天飞机主仓框架承力柱、发抽真空
动机叶片、火箭部件等已得到应用。热压法也
是制造钨丝一超合金、钨丝一铜等复合材料的°°°°°°°°
主要方法之一。图15-2和图15-3为扩散粘接冷却、取出、清理零件
过程简图及用热压法制造发动机叶片的工艺
流程。图15-2扩散粘接过程简图
纤维与基体片单层片
模切叠层片
加压
顶盖加热
钢芯
)内冷铁
用酸脱
钢芯
一次成型体根部嵌入块和外包块
图15-3金属基复合材料热压固结工艺流程
3热等静压法
热等静压法同陶瓷基复合材料的热等静压成型。温度可在数百度到2000℃范围内选择,工作压力可高达100~200MPa。
热等静压工艺有三种:①即先升压后升温,其特点是无需将工作压力升到最终所要求的最高压力,随着温度升高,气体膨胀、压力不断升高直至达到需要压力,这种工艺适合于金属包套工件的制造;②先升温后升压,此工艺对于用玻璃包套制造复合材料比较合适,因为玻璃在一定温度下软化,加压时不会发生破裂,又可有效传递压力;③同时升温升压,这种工艺适合于低压成型、装入量大、保温时间长的工件制造。
热等静压适用于多种复合材料的管、筒、柱及形状复杂零件的制造,特别适用于钛、金属间化合物、超合金基复合材料。图15-4为制造B一A1复合材料管的工艺流程。产品的组织均匀致密,无缩孔、气孔等缺陷,形状、尺寸精确,性能均匀。热等静压法的主要缺点是设备投资大、工艺周期长、成本高。
将纤维增强
铝铺层放入
管内壁
热等静压炉中使
铺层扩散粘结将管子密封
在真空金属
包套中
齿槽轻质传动轴
车去钢外壁
图15-4B-A1复合材料管制造工艺流程
4.热轧法、热挤压法和热拉法
热轧法、热挤压法和热拉法都是金属材料中成熟的塑性成型加工工艺,这里移植来用于制造复合材料。
热轧法主要用来将已复合好的颗粒、晶须、短纤维增强金属基复合材料锭坯进一步加工成板材。也可将由金属箔和连续纤维组成的预制片制成板材,例如铝箔与硼纤维、铝箔与钢丝。为了提高粘结强度,常在纤维上涂银、镍、铜等涂层,轧制时为了防止氧化常用钢板包覆。与金属材料的轧制相比,长纤维一金属箔轧制时每次的变形量小、轧制道次多。对于颗粒或晶须增强金属基复合材料,先经粉末冶金或热压成坯料,再经热轧成复合材料板材。242
热挤压和热拉主要用于颗粒、晶须、短纤维增强金属基复合材料坯料的进一步加工,制成各种形状的管材、型材、棒材等。经挤压、拉拔后复合材料的组织变得均匀、缺陷减少或消除,性能明显提高,短纤维和晶须还有一定的择优取向,轴向抗拉强度提高很多。
热挤压和热拉对制造金属丝增强金属基复合材料是很有效的方法,具体做法是在基体金属坯料上钻长孔,将增强金属制成棒放入基体金属的孔中,密封后进行热挤压或热拉,增强金属棒变成丝。也有将颗粒或晶须与基体金属粉末混匀后装入金属管中,密封后直接热挤压或热拉成复合材料管材或棒材的。图15-5为热拉法制备金属基复合材料棒材的示意图。
热电偶
夹具夹具模具
真空
<阻挡块冷却套模具加热炉管状炉
绝缘体纤维砖
图15-5热拉金属基复合材料工艺示意图
5爆炸焊接法
爆炸焊接法是利用炸药爆炸产生的强大脉冲应力,通过使碰撞的材料发生塑性变形、粘结处金属的局部扰动以及热过程使材料焊接起来。注意:①基体和金属丝在焊前必须除去表面的氧化膜和污物。②底座材料的密度和隔音性能应尽可能与复合材料接近。
爆炸焊接的特点是作用时间短,材料的温度低,不必担心发生界面反应。用爆炸焊接可以制造形状复杂的零件和大尺寸的板材,需要时一次作业可得多块复合板。此法主要用来制造金属层合板和金属丝增强金属基复合材料,例如钢丝增强铝、铝丝或钨丝增强钛、钨丝增强镍等复合材料。图15-6为爆炸焊接示意图。4
5
6
3
200000000000000007
1(200000000000000
图15-6爆炸焊接示意图
1底座:2基板;3动板;4爆管;5炸药包:6缓冲层;7纤维
15.3.3液态法
1真空压力浸渍法
真空压力浸渍法是在真空和高压惰性气体共同作用下,将液态金属压入增强材料的预制件,制备金属基复合材料零件的一种方法。它兼备真空吸铸和压力铸造的优点,由美国的A1con公司于1960年最先发明的。
(1)预制件的制备,如图15-7所示。
搅拌器
晶须水活塞
(颗模具
粒、短
(1)纤维)
+水预制件
过滤水
(a)(b)
(c)
(d)
晶须
吸取(颗粒、短纤维)H
+粘结剂+水预制件
搅拌器
(2)过滤
预制件
(a)(b)
(c)
(1)压制成型(a)搅拌:(b)制模:(c)挤压;(d)干燥
(2)抽吸成型(a)吸取:(b)脱模:(c)干燥
图15-7预制件制备过程
图15-7示出了晶须或颗粒预制件的抽吸和压制两种湿法成型工艺,它们也适用于短纤维预制件。图15-10和图15-11分别为短纤维或晶须预制件的磁场和静电场定向成型装置。在磁场或电场的作用下短纤维和晶须择优取向,得到接近定向排列的预制件。
2
300
5
1
56
2
6三
7?
83
9
1滤筛;2纤维;3漏斗:4玻璃管;1高压电源:2正电极:3过滤器:4支架;
5磁场线圈:6不锈钢容器:7纤维预制体;5负电极:6定向纤维;7纤维成型体
8交流容器:9振动器
图15-8短纤维在磁场中定向排列图15-9静电定向装置
(2)真空压力浸渍成型
熔体进入预制件有三种方式,即底部压入式、顶部注入式和顶部压入式。
首先将增强材料预制件放入模具,基体金属装入坩埚,然后将装有预制件的模具和装有基体金属的坩埚分别放入浸渍炉的预热炉和熔化炉内,密封和紧固炉体,将预制件模具和炉腔抽真空,当炉腔内达到预定真空度后开始通电加热预制件和熔化金属基体。控制加热过程使预制件和熔融基体达到预定温度,保温一定时间,提升坩埚,使模具升液管插入金属熔体,通入高压惰性气体,在真空和惰性气体高压的共同作用下,液态金属渗入预制件中并充满增强材料之间的空隙,完成浸渍过程,形成复合材料。
244
降下坩埚,接通冷却系统,待完全凝固后,即可从模具中取出复合材料零件或坯料,凝固在压力下进行,无一般的铸造缺陷。真空压力浸渍法制备金属基复合材料的工艺过程如图15-10所示。
模具、预制件、熔体
快速通过管子抽真空
脱卸盖真空
抽真空管薄壁模具
预制件
凝固控制模具密封
压力容器
模具
加热炉升液管
熔体
加热炉基体
提升装置(a)(b)
(c)
真空真空
真空
真空管
入口已
0000100
凝固堵
模具内压力使模
塞
保持真空
0000具密封
提升坩埚
升液管浸
入熔体e666
开始加压
(d)(e)
(f)
真空真空
010H0100浸渍预制件
二开始定向凝固
补缩
88X
控制加压
888
。8。。。
保持高压
o66
88。
(g)(h)
(i)
(a)装入预制件;(b)装炉;(c)抽真空与熔化;(d)提升坩埚;(e)通入高压气体;
(f)进入模具;(g)浸渍;(h)凝固;(i)开炉
图15-10真空压力浸渍法制备金属基复合材料的工艺过程
真空压力浸渍法具有以下特点:245
①适用面广,可用于多种金属基体和连续纤维、短纤维、晶须和颗粒等增强材料的复合,增强材料的形状、尺寸、含量基本上不受限制。也可用来制造混杂复合材料。
②可直接制成复合材料零件,特别是形状复杂的零件,基本上无需进行后续加工。
③浸渍在真空中进行、压力下凝固,无气孔、疏松、缩孔等铸造缺陷,组织致密,材料性能好。④工艺简单、参数易于控制,可根据增强材料和基体金属的物理化学特性,严格控制温度、压力等参数,避免严重的界面反应。
真空压力浸渍法的设备比较复杂,工艺周期长,制造大尺寸的零件要求大型设备
2.挤压铸造法
挤压铸造法是通过压机将液态金属强行压入增
强材料的预制件中以制造复合材料的一种方法,其
工艺过程如图15-11所示。其过程是先将增强材料
制成一定形状的预制件,经干燥预热后放入模具中,
浇注入熔融金属,用压头加压,压力为70~100MPa,
液态金属在压力下浸渗入预制件中,并在压力下凝
固,制成接近最终形状和尺寸的零件,或供用塑性
成型法二次加工的锭坯。挤压铸造的压力比真空压
力浸渍的压力高得多,因此要求预制件具有高的机
械强度,能承受高的压力而不变形。
挤压铸造法主要用于批量制造陶瓷短纤维、颗
粒、晶须增强铝、镁基复合材料的零部件,成本低,●●●
陶瓷纤维增强铝基复合材料活塞已得到大量应用。
由于高压的作用,可以促进熔体对增强材料的润湿,
增强材料不需进行表面预处理,熔体与增强材料在
高温下接触的时间短,因此也不必担心发生严重的图15-11挤压铸造法原理示意图
界面反应。
3液态金属搅拌铸造法
液态金属搅拌铸造法是一种适合于工业规模生
产颗粒增强金属基复合材料的主要方法,工艺过程
简单,制造成本低廉。这种方法的基本原理是将颗热电偶热电偶
粒直接加入到基体金属熔体中,通过一定方式的搅
拌使颗粒均匀地分散在金属熔体中并与之复合,然搅拌器
后浇铸成锭坯、铸件等。
主要困难有二,一是颗粒(10~30μm)与金属加热炉
熔体的润湿性差,不易进入和均匀分散在金属熔体坩埚
中,产生团聚;二是强烈的搅拌容易造成金属熔体螺旋浆
的氧化和大量吸入空气。因此必须采取有效的措施熔体
来改善金属熔体对颗粒的润湿性,防止金属的氧化
和吸气,具体措施如下。塞子
①在金属熔体中添加合金元素降低金属熔体的表面
张力,改善润湿性。
②对颗粒进行表面处理改善熔融铝合金基体对颗粒
的润湿性。固定模
③复合过程的气氛控制。一般采用真空、惰性气体
保护来防止金属熔体的氧化和吸气。
④有效的机械搅拌。采取高速旋转的机械搅拌或超图15-12旋涡搅拌法的工艺原理
声波搅拌来强化搅拌过程。246
液态金属搅拌铸造法根据工艺特点及所选用的设备可分为旋涡法、Duralcon法、复合铸造法三种。(1).旋涡法
旋涡法是利用高速旋转的搅拌器的桨叶搅动金属熔体,使其强烈流动,并形成以搅拌旋转轴为对称中心的旋涡,将颗粒加到旋涡中,依靠旋涡的负压抽吸作用,颗粒进入金属熔体中。旋涡法的工艺原理图如图15-12所示。
旋涡搅拌法工艺简单,成本低。主要用来制造含较粗颗粒(直径50~100m)的耐磨复合材料,不适用于制造高性能的结构用颗粒增强金属基复合材料。
(2)Daralcon法
Duralcon液态金属搅拌法是80年代中期由Alcon公司研究开发的一种颗粒增强铝、镁、锌复合材料的方法——无旋涡搅拌法。
Duralcon法的主要工艺过程是将熔炼好的基体金属熔体注入可抽真空或通惰性气体保护、并能保温的搅拌炉中,加入颗粒增强物,搅拌器在真空或充氩条件下进行高速搅拌。搅拌器由主、副两搅拌器组成,主搅拌器具有同轴多桨口L旋转速度高,可在1000-2500r/min范围内变化,高速旋转对金属熔体和颗粒起剪切作用,使细小的颗粒均匀分散在熔体中,并与金属基体润湿复合。副搅拌器沿坩埚壁缓慢旋转,转速<100r/min,起着消除旋涡和将粘附在坩埚壁上的颗粒刮离带入到金属熔体中的作用。一般以高于基体液相线50℃为宜,搅拌时间通常为20min左右。
特点:有效地防止了金属的氧化和气体吸入,复合好的颗粒增强金属基复合材料熔体中气体含量低、颗粒分布均匀,铸成的锭坯的气孔率小于1%,组织致密,性能好。
Duralcon法前工规模产粒增强基复材
料的主要方法。
(3).复合铸造法搅拌器
颗粒
复合铸造法也是采用机械搅拌将颗粒混入金属熔体热电偶
输送管
中,但其特点是搅拌不在完全液态的金属中进行,而在半
固态的金属中进行。颗粒加入半固态金属中,通过这种熔
体中固相的金属粒子将颗粒带入熔体中。通过对加热温度电阻或感应
的控制将金属熔体中的固相粒子的含量控制在40%~加热炉
60%,加入的颗粒在半固态金属中与固相金属粒子相互碰
撞、摩擦,促进了与液态金属的润湿复合,在强烈的搅拌惰性气体保护
下逐步均匀地分散在半固态熔体中,形成均匀分布的复合或真空室
材料。复合结束后,再加热升温到浇铸温度,浇铸成零件
或坯料。模具
这种方法可以用来制造颗粒细小、含量高的颗粒增强
金属基复合材料,也可用来制造晶须、短纤维复合材料。
复合铸造法的原理简图如图15-13所示。图15-13复合铸造原理图
液态金属搅拌铸造法工艺简单、生产效率高、制造成本低,适用于多种基体和多种颗粒,最具有竞争力。
4.液态金属浸渍法
液态金属浸渍法是指用液态金属连续浸渍长纤维,得到复合材料预制品(带、丝等)的一种方法,有时也称连铸法。图15-14为用液态金属浸渍法制备碳(石墨)-铝复合带的装置简图。
预处理炉CVD炉
熔化炉
0000
除胶炉0000
放丝筒收丝筒
图15-14液态金属浸渍法装置简图
碳(石墨)纤维由放丝筒顺序经过除胶炉、预处理炉、化学气相沉积(CVD)炉、熔化炉,最后由收丝筒将已复合好的带或丝收集。在除胶炉中碳(石墨)纤维经高温处理除去在纤维制造过程中涂的胶,如炉温低于450℃,除胶可在空气中进行,如炉温高于450℃,为了防止纤维的氧化,除胶必须在保护性气氛中进行。
在预处理炉中,碳(石墨)纤维除进一步除胶、脱除残留胶外,预处理炉的温度控制在700℃,用氩气保护。
化学气相沉积炉是液态金属浸渍法的核心,在此炉中纤维用BCl1、TiCl处理,在表面生成Ti-B涂层。BCl3在常温下为气体,TiCL在25℃的蒸气压约为907Pa。
在熔化炉将基体金属熔化、保温,温度控制在高于基体熔点50-100℃。为了防止金属氧化,熔化炉中的熔体最好置于惰性气体保护气氛中,但如果使经化学气相沉积后的碳纤维在液面下进入熔体,不与表面上的氧化物接触,也可不用惰性气体保护。涂覆好的纤维在进入熔化炉前一直处于氮气保护下,一旦进入熔化炉与熔融金属接触,熔体立即自发浸渍到纤维束中,与每根纤维很好复合,得到复合丝或带,由收丝筒收集,作随后的二次加工用。
液态金属浸渍法的工艺过程比较复杂,特别是复合前纤维需作表面处理,得到的产品是尺寸很小的丝或带,需进行二次加工才能得到零件或材料,因此成本很高,应用受到很大限制
5.共喷沉积法
共喷沉积法是制造各种颗粒增强金属基复合材料的有效方法,1969年由Siager发明,随后由Ospray金属有限公司发展成工业生产规模的制造技术,
可以用来制造铝、铜、镍、铁、金属间化合物基挡杆
复合材料。
共喷沉积法的基本原理是:液态金属基体通感应加热炉
过特殊的喷嘴,在惰性气体气流的作用下雾化成
细小的液态金属流,喷向衬底,将颗粒加入到雾惰性气体
化的金属流中,与金属液滴混合在一起并沉积在分解室
衬底上,凝固形成金属基复合材料。共喷沉积法雾化器
的工艺原理和装置如图15-15。颗粒
共喷沉积法包括基体金属熔化、液态金属雾喷射器
化、颗粒加入及与金属雾化流的混合、沉积和凝
固等工艺过程。主要工艺参数有:熔融金属温度,
惰性气体压力、流量、速度,颗粒加入速度、沉废气
积底板温度等。颗粒液化床
共喷沉积法的装置主要由熔炼室、雾化沉积底板(管、坯、板等)
室、颗粒加入器、气源、控制台等组成,最核心
部分是雾化室中雾化用喷嘴和沉积用衬底。图15-15共喷沉积法的工艺原理和装置
共喷沉积法特点:
①适用面广。可用于铝、铜、镍、钴等有色金属基体,也可用于铁、金属间化合物基体;可加入SiC、A12O3、TiC、Cr2O3、石墨等多种颗粒;产品可以是圆棒、圆锭、板带、管材等。
248
②生产工艺简单、效率高。与粉末冶金法相比不必先制成金属粉末,然后再与颗粒混合、压型、烧结等工序,而是快速一次复合成坯料,雾化速率可达25-200kg/min,沉淀凝固迅速。
③冷却速度大。金属液滴的冷却速度可高达103~10K/s,所得复合材料基体金属的组织与快速凝固相近,晶粒细、无宏观偏析、组织均匀。
④颗粒分布均匀。在严格控制工艺参数的条件下颗粒在基体中的分布均匀。
⑤复合材料中的气孔率较大。气孔率在2%~5%之间,但经挤压处理后可消除气孔,获得致密材料
6.热喷涂法
根据热源的不同热喷涂分为等离子喷涂和氧一乙炔焰喷涂,尽管等离子喷涂的设备比氧一乙炔喷涂复杂,但由于工艺参数和气氛容易控制,因此在复合材料制造上,主要采用等离子喷涂。
等离子喷涂是利用等离子弧的高温将基体熔化后喷射到工件(增强材料)上,冷却并沉积下来的一种复合方法。具体过程是先将纤维缠绕在包有基体金属箔的圆筒上,纤维之间保持一定的间隔,然后放在喷涂室中进行喷涂,过程结束后剪开取下,便得复合材料预制片,经热压或热等静压等二次处理,最终得到型材或零件。
喷涂过程中的关键是得到致密的与纤维粘结良好的基体涂层和避免基体的氧化。喷涂用的基体原料为粉末状,减小粉末的粒度能提高涂层的致密性,但粒度太小,粉末流动不易,难以保证供给速度。因此,粉末直径一般不小于2μm,通常为10~45μm。在较高的温度下进行喷涂可以提高涂层的致密性和与纤维的粘结强度,但等离子体流离开喷枪后温度急剧下降,并且距离越远温度下降越大,这就需要增加功率来提高等离子体发生区域的温度。向氩气中添加5%~10%的电离电压比氩高的氦可以达到提高功率的目的。等离子体发生区的温度提高后,等离子体的热膨胀变大,也有利于提高流速。
等离子喷涂法适用于直径较粗的纤维单丝,例如用化学气相沉积法得到的硼纤维和碳化硅纤维,它是制造这两种纤维增强铝、钛基复合材料预制片的大规模生产方法。等离子喷涂法不能直接制成复合材料零件,只能制造预制片,且组织不够致密,必须进行二次加工,然后用热压或热等静压法加工而成的。用等离子喷涂法可以制造耐热和耐磨的复合涂层,例如在铁基、镍基合金中加入SiC、A12O3,等陶瓷颗粒,可以显著提高它们的耐热性和耐磨性。
16复合材料连接与机械加工
16.1概述
复合材料连接在复合材料结构设计中占有重要地位。合理的连接设计,不但能够满足使用要求,减轻结构质量,而且可以延长结构的使用寿命。否则可能首先在结构连接处产生破坏,甚至造成重大事故。复合材料连接的方法主要分成两大类:即胶接连接和机械连接。在连接设计中,采用胶接或者机械连接,要根据具体使用技术条件决定。一般来说,对于受力不大的薄壁结构,尤其对纤维增强树脂类复合材料元件,应尽量采用胶接连接。对于连接元件较厚;受力大的结构件,多采用螺接或铆接:在某些情况下,为了提高结构件的安全特性而采用混合连接,即胶一螺连接。
机械连接是指铆接、螺栓连接、销钉连接等。优点:易于检查、易于装拆。缺点:孔切断了纤维,削弱了受力截面,会引起应力集中,从而降低接头的疲劳强度,质量增加,密封性差,外观不好等。胶接连接优点:胶接结构质量轻、强度高,应力分布均匀;外形光滑整齐,工艺简单,周期短,可省功省时。
复合材料的机械加工,是借用切削金属和木材加工等方法对复合材料制品进行加工的总称。注意两点:机械加工不能影响产品质量,尽量为机械加工提供方便,必要时应在制品上留出加工余量。
16.2复合材料胶接连接
16.2.1胶粘剂的分类
(1)按成分分类
按成分分类主要有无机胶粘剂和有机胶粘剂。具体分类如下:
硅酸盐类
磷酸盐类
无机胶粘剂硫酸盐类
金属氧化物凝胶
玻璃陶瓷粘合剂
动物胶酚醛树脂
天然胶植物胶脲醛树脂
不饱和聚酯树脂
热固性树脂环氧树脂
有机硅
聚酰亚胺
树脂型聚苯丙咪唑
有机胶粘剂聚醋酸乙烯酯
氯乙烯醋酸乙烯酯
热塑性树脂丙烯酸酯
过氯乙烯树脂
聚氨酯
再生橡胶
丁苯橡胶
合成胶丁基橡胶
橡胶型氯丁橡胶
聚硫橡胶
聚氨酯橡胶
硅橡胶
酚醛一缩醛环氧一聚酰胺
酚醛一氯丁环氧—聚硫
混合型酚醛一丁腈酚醛一环氧
环氧一丁腈环氧一缩醛
250
(2)按胶接强度分类
按胶接强度分类,可分为结构型、次结构型和非结构胶粘剂。结构胶粘剂有较高的胶接强度,其胶接接头能够承受较大的载荷,可用来胶接各种承力构件。复合材料的胶接中主要用结构胶粘剂
(3)按固化形式分类
按固化形式分类,可分为溶剂挥发型、化学反应型及热熔型等三种。
(4)按外观分类
按胶粘剂的外观形式,可分为溶液型、乳液型、膏糊型、粉末型、固体型等五种。
16.2.2胶接工艺零件外形容差检验
预装配胶接件的表面制备
配置底胶
胶粘剂选择及复验涂底胶贴胶膜
剪裁胶膜胶接装配
直观检验胶接质量检验
固化
无损检验图16-1胶接工艺示意图
1各种材料的表面处理
(1)金属的表面处理
金属的表面处理方法有溶剂清洗、机械处理和化学处理。处理后的表面尽可能快地进行胶接。操作时应戴干净手套和使用干燥工具。
(2)复合材料的表面处理
未经加工的复合材料胶接表面,先用砂纸和铜丝刷打磨,以去除脱模剂及其它有机物,并使表面粗糙度在0.8um~3um范围内,经加工的复合材料胶接表面,用毛刷除去粉末,再用丙酮或四氯化碳做去尘脱脂处理,最后用风机吹干待用。
(3)塑料的表面处理
塑料首先用相应的溶剂去除污染物,然后才能进行机械处理或化学处理。
2胶粘剂的涂敷
涂胶的关键是保证胶层厚度合适,且均匀无气泡,无缺胶。涂敷方法主要有:刷涂法、自流法、喷涂法、滚涂法。
3胶粘剂的固化
加热和加压的方法很多,主要加热方式有:直接加热固化(电热、液体加热或蒸汽加热),辐射(红外或远红外线)加热固化,电热器加热、感应加热;高频电介质加热、超声波加热等方法。
胶粘剂固化采用的加压设备有:液压床或风动压床;气(液)压垫;重量加压;机械加压;真空加压,热压罐加压,热压机或热压板加压等。
4接头形式:
角接接头、T形接头、对接接头、面接接头。251
角接接头T形接头
对接接头
面接接头
图16-2接头的四种基本形式
不好稍好
好
更好
不好稍好好
更好
图16-3角接型和丁字型接头形式
16.2.3几种常用胶粘剂
(1)HY1-6胶粘剂
是一种容易固化的胶状液体。它以618环氧树脂为基体,四乙烯五胺为固化剂并加有增塑剂及无机填料的一种胶粘剂。优点:粘附力强,固化收缩小,能耐化学药品、有机溶剂和油类等介质的侵蚀,电绝缘性能较好,使用方便,可室温固化,固化时只需接触压力。缺点:固化后耐热性及韧性较差。可用于复合材料与复合材料,复合材料与钢,复合材料与铝及钢与钢之间的结构胶接。
使用方法:用毛刷或刮刀在已处理好的胶接面上均匀地涂上一层胶液,涂胶量约为150g/m2~200g/m2将两胶接面叠合,施加接触压力使相对位置保持固定,在不低于20℃的环境下,静置3昼夜,或于60℃烘4h或80℃烘2h能完全固化。
(2)环氧聚酰胺胶粘剂
它是以环氧树脂为基体,聚酰胺为固化剂的一种胶粘剂。优点:有很好的韧性,粘结力强、挥发性小无毒、配比范围大、耐磨及电性能好等特性,适用周期长,常温固化和加热固化均可。反应放热低,容易控制,因而应用很广。对铝、铁、有色金属及非金属如复合材料、玻璃、陶瓷等的胶接效果都较好。
使用工艺:在经150℃预热半小时的胶接面上均匀涂上一层0.15mm以下的胶,在室温下晾置5min~10min,使胶能在胶接表面上充分扩散渗透。叠合胶接面,施加接触压后,使相对位置固定。在不低于20℃的环境下,放置3昼夜,即可完全固化。最佳的固化条件是:60℃固化2h后再经100℃固化1h或100℃固化2h。
(3)201胶粘剂(即FSC-1胶粘剂)
这种胶粘剂是酚醛树脂和聚乙烯醇缩甲醛树脂溶于苯和乙醇混合溶剂中制成。可在-70℃~150℃温度范围内使用,优点:具有高强度和较好的耐老化、耐水、耐油性能。性能稳定且价廉,适应于铝、铜、钢等金属之间的粘接,对于非金属材料如玻璃纤维复合材料、陶瓷、玻璃等胶接效果也良好。可用作使用温度在150℃以下的耐热结构胶。
使用时,在胶接面上均匀地涂刷三次,每次涂后在室温下晾置15min~20min(视空气湿度而定),然后将两胶接面叠合,加上接触压0.1MPa的压力,于160℃固化3h或140℃固化6h。
(4)204胶粘剂
204胶粘剂(即JF-1胶)是改性酚醛树脂溶于有机溶剂的溶液。特点:优良的耐热性及较高的结构强度,可在300℃下工作5h,在200℃下长期工作;良好的耐水性,对汽油、乙醇等有机溶剂是稳定的,对各种金属也不产生腐蚀,胶缝的密封性较好。它可有效地用于各种碳钢、合金钢、铝,镁,钛等合金:耐热酚醛层压板;各种玻璃纤维复合材料,金属与非金属的蜂窝材料等自身或相互之间的胶接。
252
使用时,用毛刷进行涂胶,共涂三次,每次在湿度小于70%的清洁环境下晾置20min~30min,叠合,加0.1MPa~0.2MPa的压力,于180℃下固化2h或160℃下固化4h即可
16.3复合材料的机械连接
复合材料的机械连接,是指铆接、螺栓连接、销钉连接等。机械连接形式主要有搭接和对接两种,具体机械连接方式如图16-4:搭接
带锥度搭接
对接
带锥度对接
图16-4常用的机械连接
复合材料夹层结构连接中,大多采用胶接,但是对受力较大的构件之间的连接,则多采用胶接和螺接的混合形式。混合连接有胶一螺、胶铆和胶焊等混合连接形式。
根据工艺上的先后次序,混合连接可以有两种办法,拿胶一铆来说,一是将接头按正常的胶接工艺进行操作,待胶凝全部固化以后,再在需要的地方打几个铆钉。另一个办法是在胶接施工以前,先定好铆接位置,钻好孔,胶接以后,再进行铆接,最后固化。借助铆钉的压力进行加压,胶接零件相互位置的准确,但缺点是胶层厚薄不易控制,特别是当制件较薄的时候,有的地方就不容易加上压力,可能影响胶接质量。如果接头需要密封,可以在铆钉头上先涂上一些胶,再进行铆接。
16.4热塑性复合材料的焊接连接
焊接是塑料的主要加工方法之一,塑料焊接技术已成功地应用于很多工业部门。其也可以作为热塑性复合材料的一种连接方式。
塑料焊接,就是利用加热的方式,将塑料母材及焊条加热到流动点以上,使之成为粘流态,在一定的压力下填满焊缝,而使各零部件相互熔接在一起的方法。
塑料焊接的加热方式很多,分类方式如图16-5,其中气体加热法焊接是应用最多的。
加热方法
电加热火加热
摩擦加热
外热式热工具
加热
接触加热高频加热
气体加热
热空气加热热惰性气体加
热混合气体加
热热
图16-5塑料焊接加热方式分类
气体加热法焊接又叫热风焊接,或叫热空气焊接。该种方法焊接的实质是使压缩空气或压缩惰性
气体流过焊接装置上的电加热器或燃烧着的氢氧焰,空气或惰性气体被加热到焊接温度,然后再把被加
热的气体经喷嘴喷射封焊接点,将塑料母材的焊接部分和焊条都加热到焊接温度而进行焊接。焊接的主
要设备是焊枪。16.5复合材料的机械加工
复合材料机械加工基本上沿用了对金属材料的一套机械加工方法,如车、铣、、磨、钻等,它
可以在一般木材加工机床或金属切削机床上进行。
复合材料制品最好不要机械加工,如确实需要机械加工,也要在产品设计中考虑周到,加工量要
尽量少,且应在制品上留出加工余量。
机加工方式包括:车削加工,铣削加工,锯(磨)削,钻孔、攻丝和车螺纹。
16.5.1复合材料机械加工特点
(1)纤维复合材料是由硬度高的纤维增强材料和软质的树脂组成,切削加工时,是软硬相间,断续
切削,每分钟可达百万次以上冲击,致使切削条件恶化,刀具磨损严重。
(2)复合材料切削加工性比金属材料差,在切削过程中,金属刀具和复合材料摩擦所产生的热主要
传给刀具和制品,由于制品导热性能差,极易造成局部过热,致使刀具发生退火,硬度下降,加速刀具
的磨损,缩短使用寿命,因此,要求刀具耐热和耐磨性要好。
(3)复合材料的线膨胀系数比金属高(约为金属的1.5倍),弹性模量低(为钢材的1/10~1/20),所以
在切削加工时,制品加紧力要适当,要采用刀口锋利的刀具。
(4)复合材料在机械加工时,由于过热和震动,容易发生分层、起皮、撕裂等现象,所以要考虑切
削力方向,选择适当的切削速度。
(5)复合材料中的树脂不耐高温,高速切削时胶粘状的碎屑遇冷又硬化,碎屑极易粘刀,故切削速
度要适当,不能太高。
(6)复合材料制品在进行机械加工过程中,会产生大量粉尘,因此,必须采取有效的除尘通风措施。
16.4.2常用的机加工方式
1.车削加工
车削工序是复合材料切削加工中主要组成部分,绝大部分复合材料零件都离不开车削工序。
切削加工可进行车外圆、端面、内孔、切槽、切断、螺纹等。一般车削时侧面和前面的间隙必须比加工金属时略大一点,刀具安放的位置最好稍微偏中心线下方。切削速度要高,吃刀要浅,进刀要慢,
刀具必须保持锋利。在需要粗切削和高进刀速度时,应采用冷却剂。
2铣削加工
复合材料铣削加工,是复合材料层压件非常广泛的加工方法之一。它不仅可以铣削加工各种平面、
254
沟槽、台阶、螺旋槽、齿轮、螺纹、异形面,还可以加工各种异形试体。铣削时的切削速度为30m/min~50m/min左右。一般情况下,采用较低的转速是改善加工质量的有效途径。
3锯(磨)削
复合材料机械加工中,锯切是主要加工方法之一,应用很广。特点:生产效率很高。
复合材料锯(磨)削加工,常用的砂轮一般多采用黑色碳化硅和人造金刚石磨料,有时也用氧化铝微晶刚玉磨料(氧化铝)。砂轮磨料选择,一般情况下,脆性较大材料,如酚醛/玻璃纤维复合材料,应选择黑色碳化硅磨料,环氧和聚酯类复合材料选用氧化铝(白钢玉和微晶刚玉)。
锯(磨)削过程中,要特别注意防止因摩擦过热及振动使制品分层,要采用冷风或液体冷却剂。如果是干锯,则必须加除尘装置。
4钻孔、攻丝和车螺纹
钻孔在复合材料加工中应用非常广泛,工具是麻花钻。由于复合材料的导热系数小,而热膨张系数和弹性回复都较金属大,故钻孔时摩擦热很大,钻孔材料有一点收缩。因此,对精密孔应钻得略大一点。攻丝是指在孔眼内制出内螺牙。车螺纹则是在圆柱体上制出外螺牙。攻丝工具是丝锥。目前主要采用高速钢丝锥进行攻丝,特点:成本低,制造容易,但材料损坏严重。
车螺纹一般是在车床上进行,切削速度采用10m/min~20m/min,吃刀深度要严格控制,合理选择切削用量。
复合材料螺纹车削时,冷却除尘对切削效果有极大影响,除尘差不仅严重影响刀具的使用寿命,而且还明显地影响螺纹加工质量,因此,在生产实践中应充分冷却除尘。

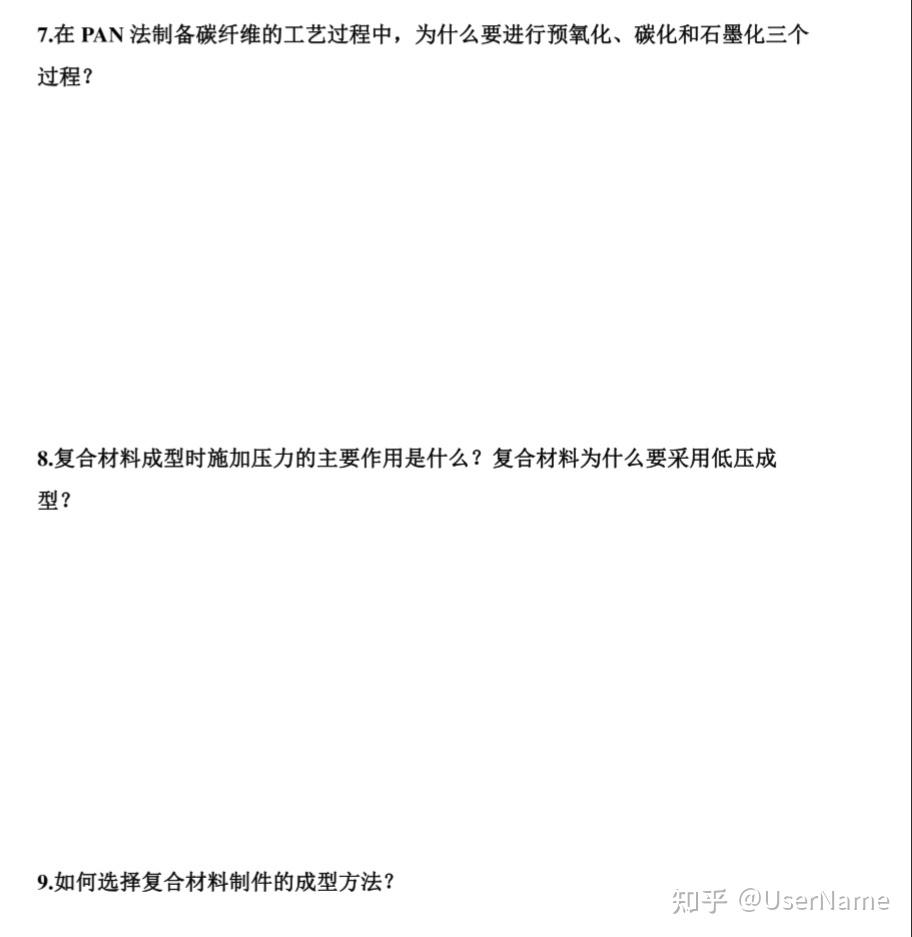
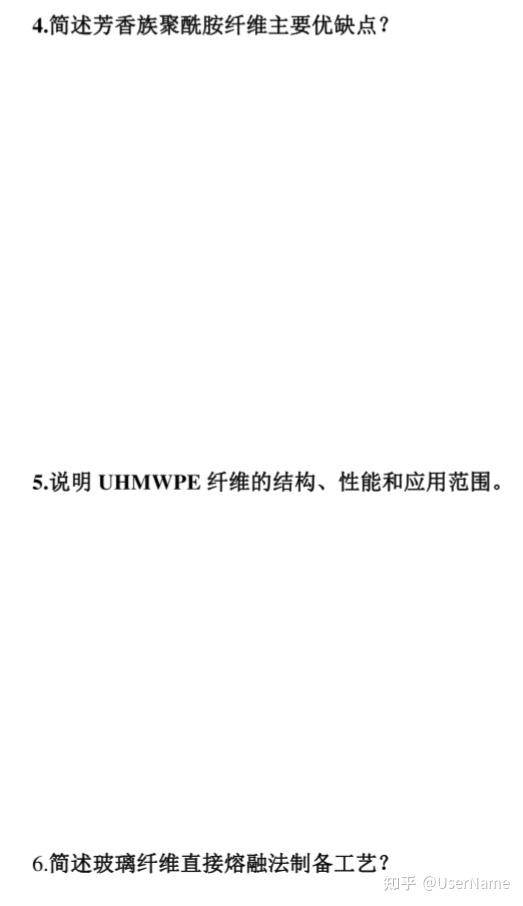
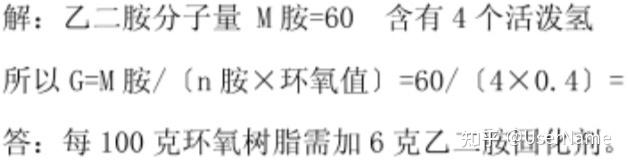
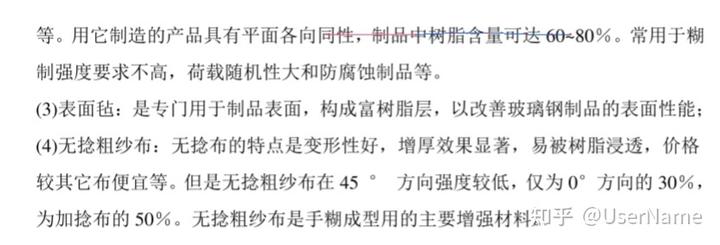
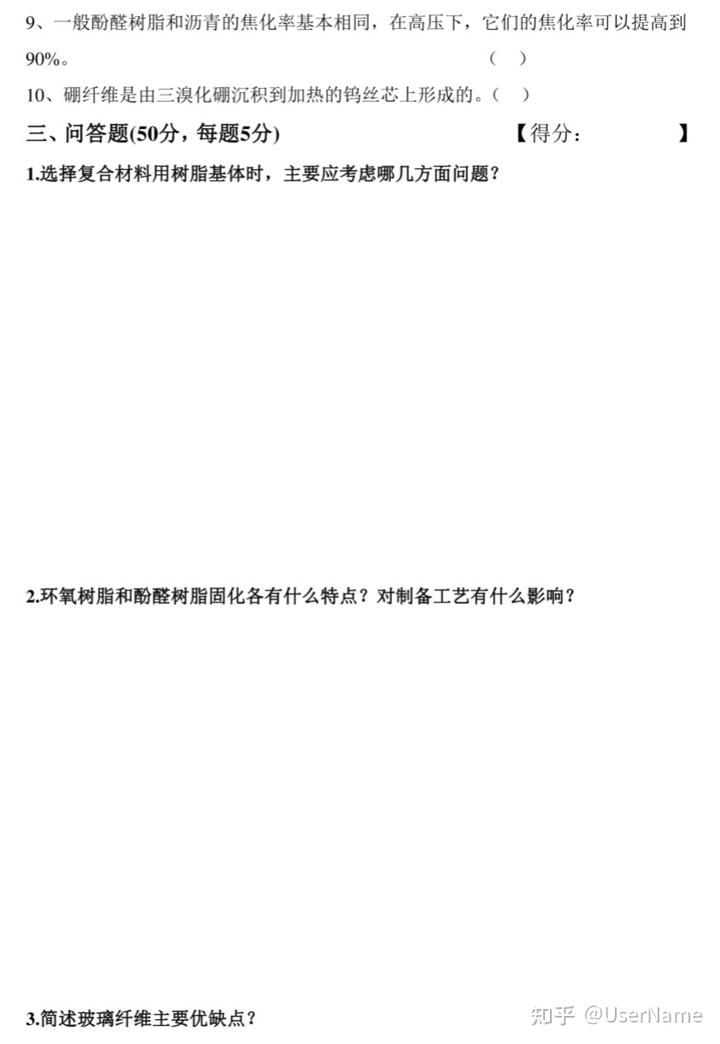
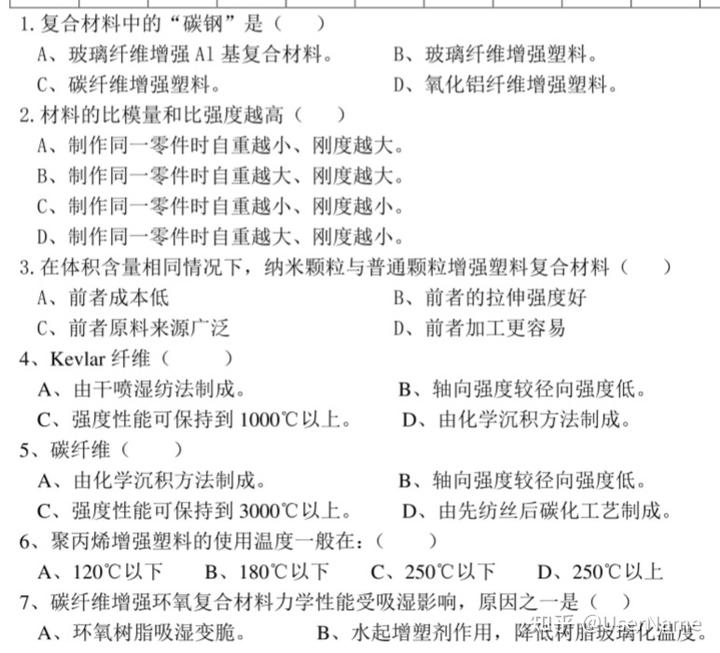
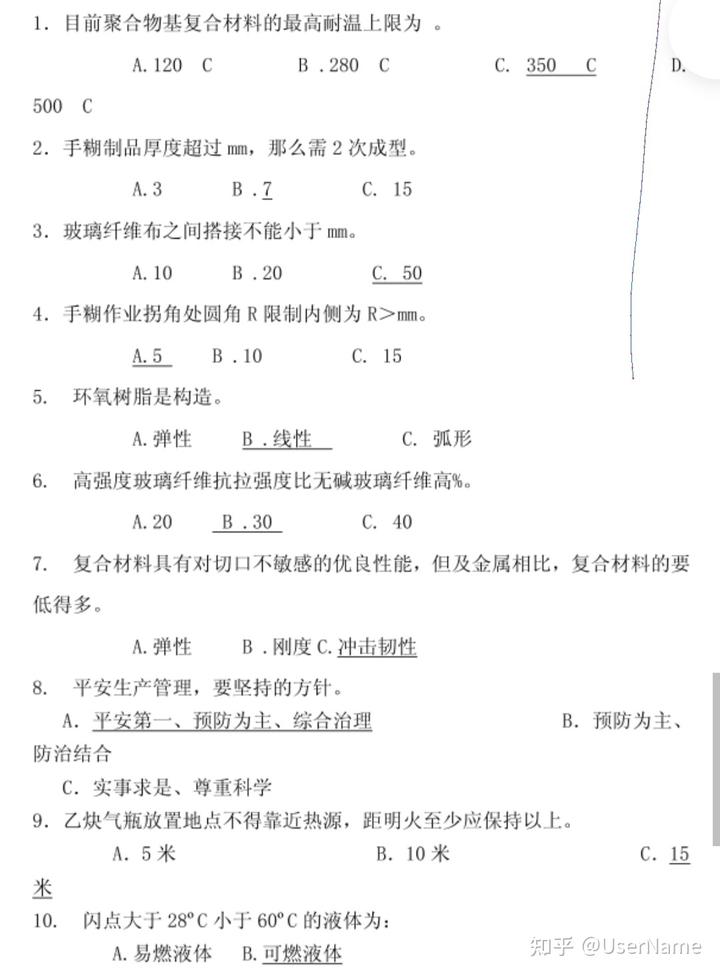
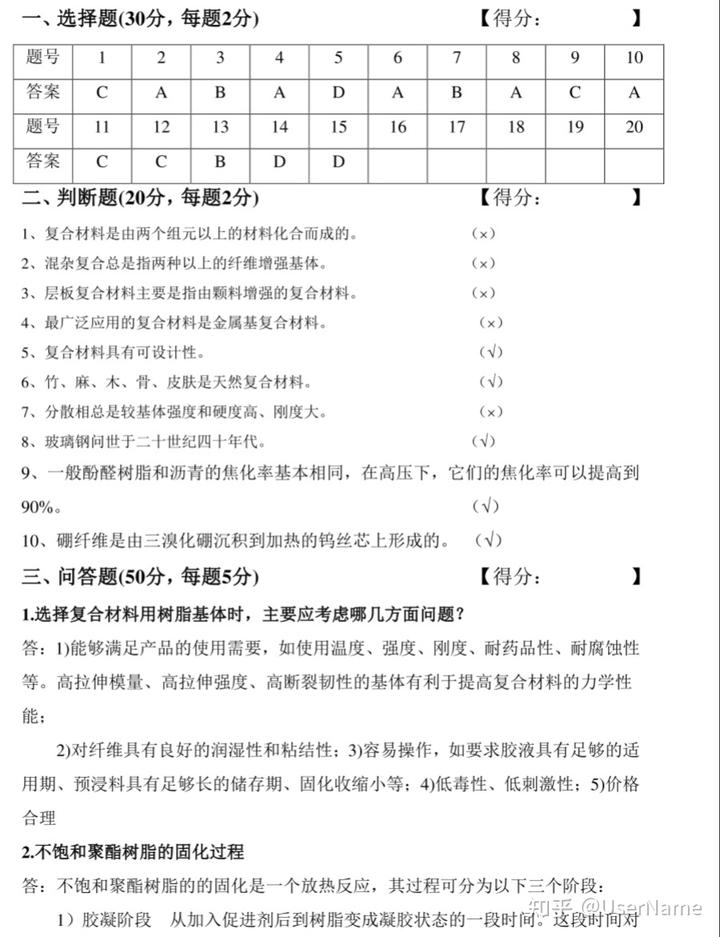
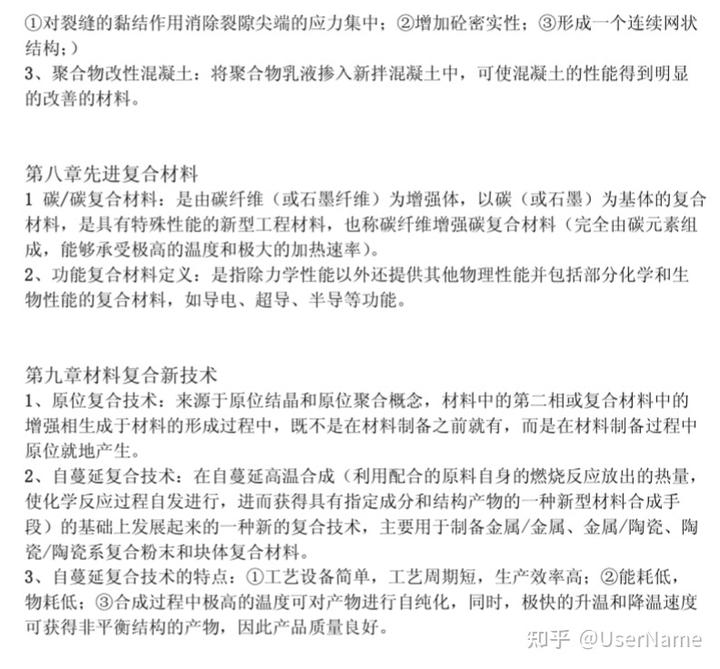
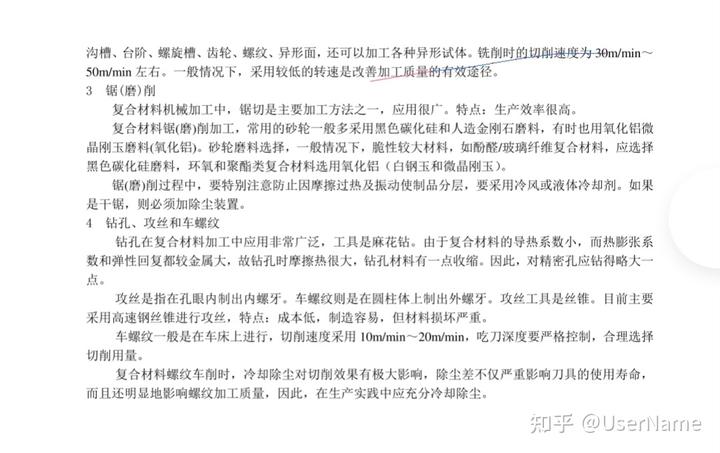
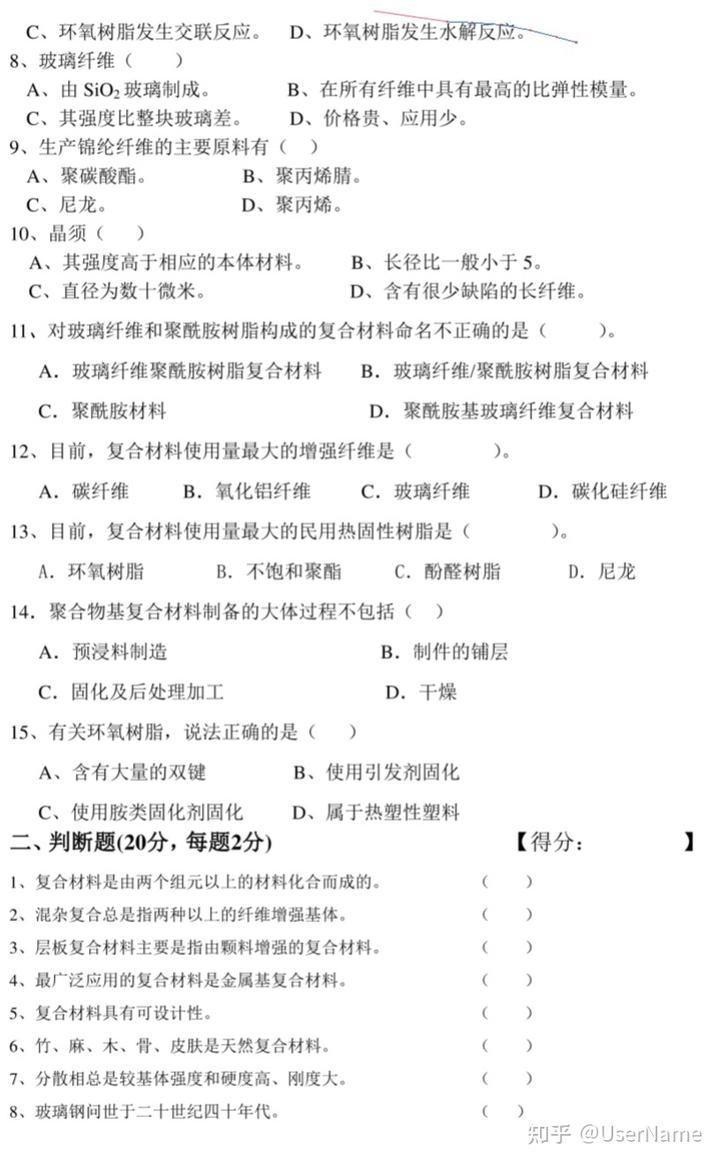
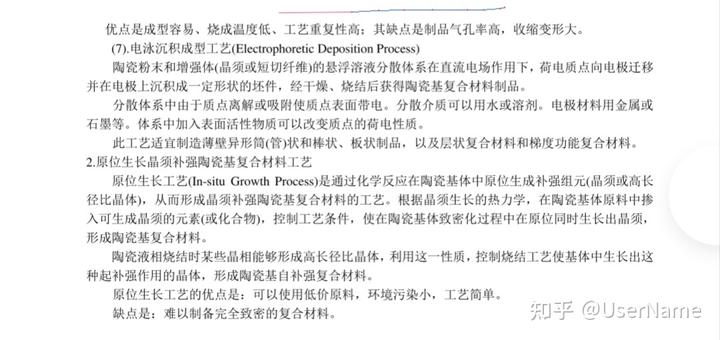
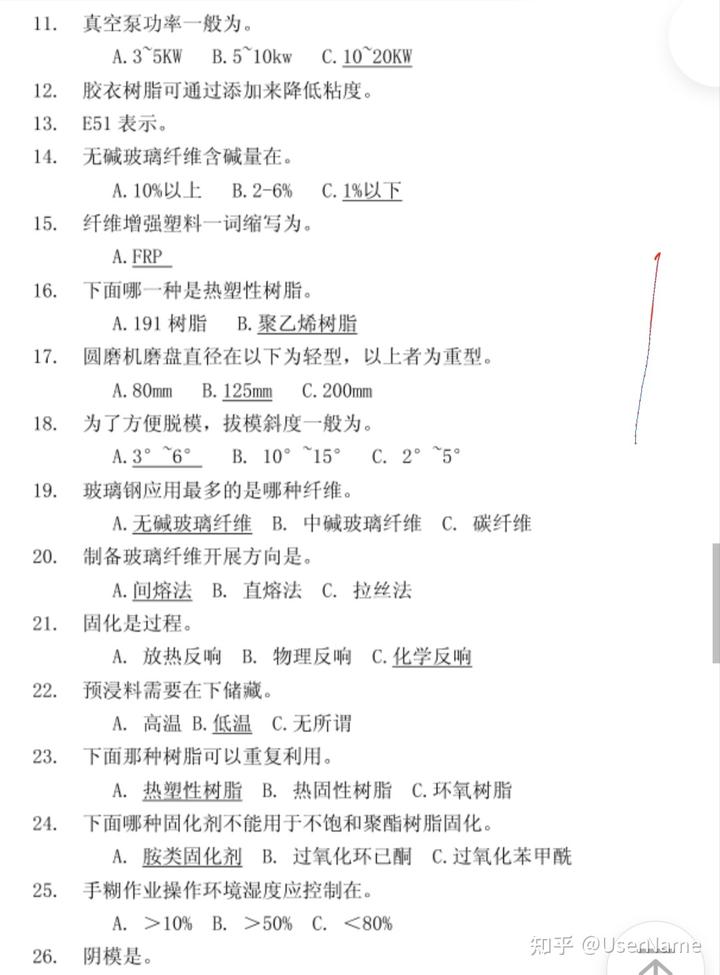
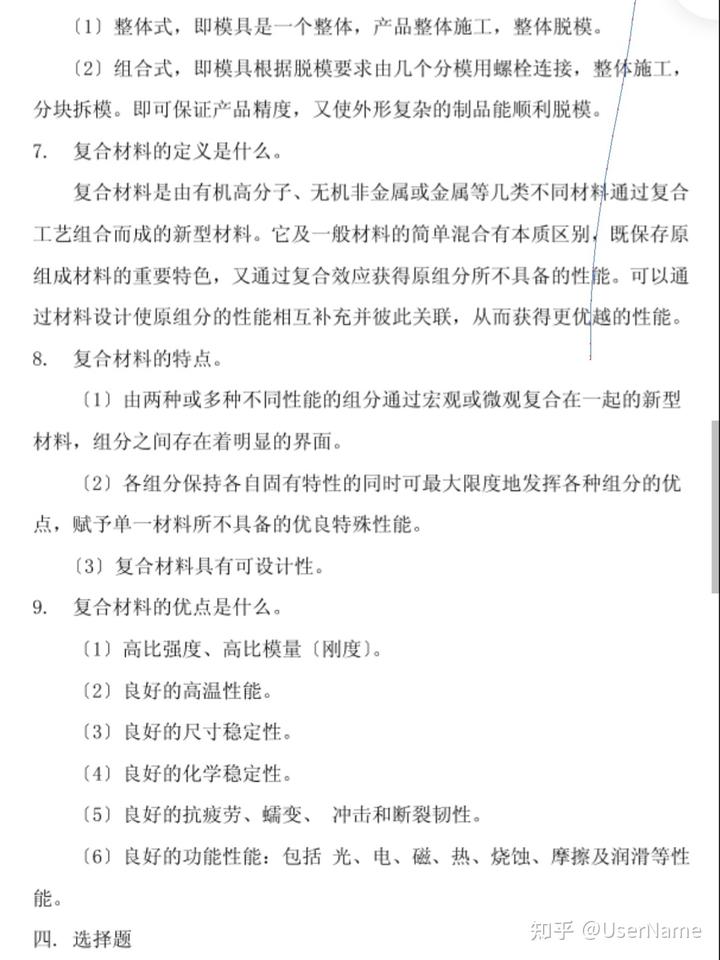
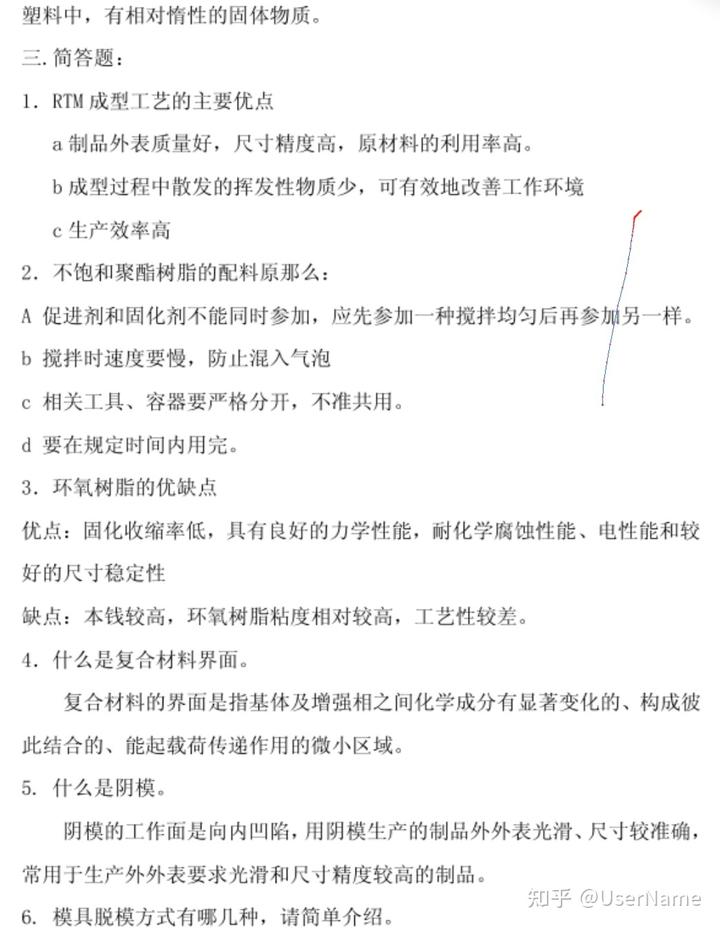
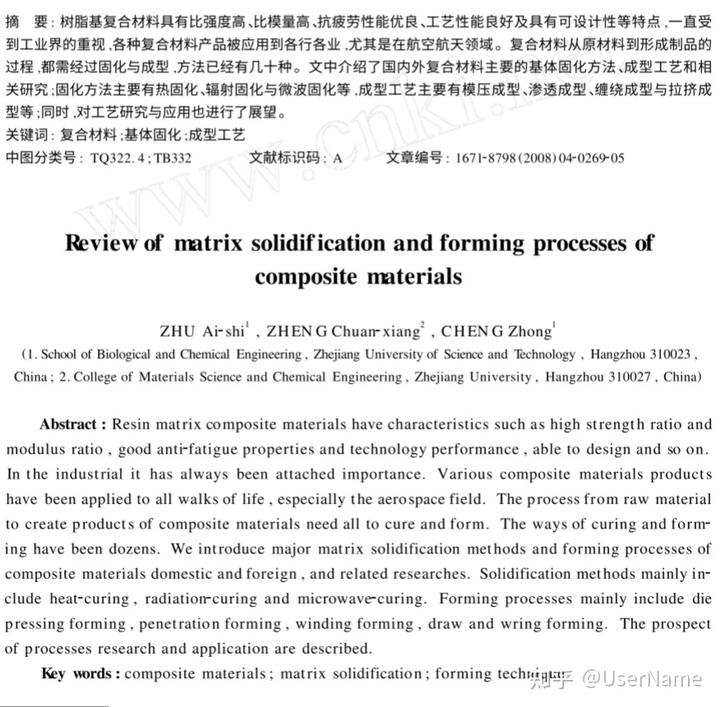
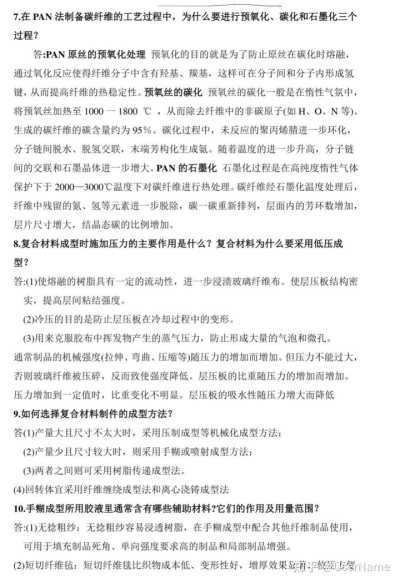
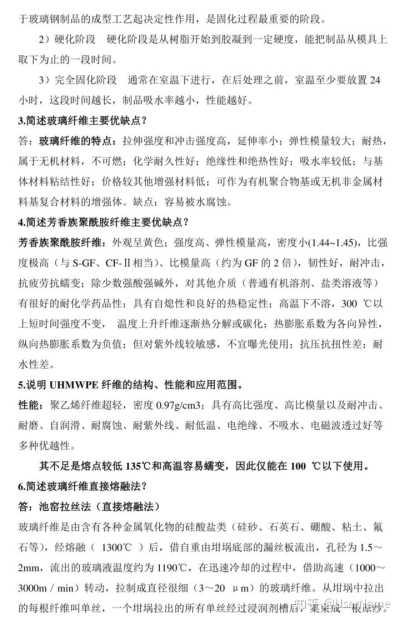
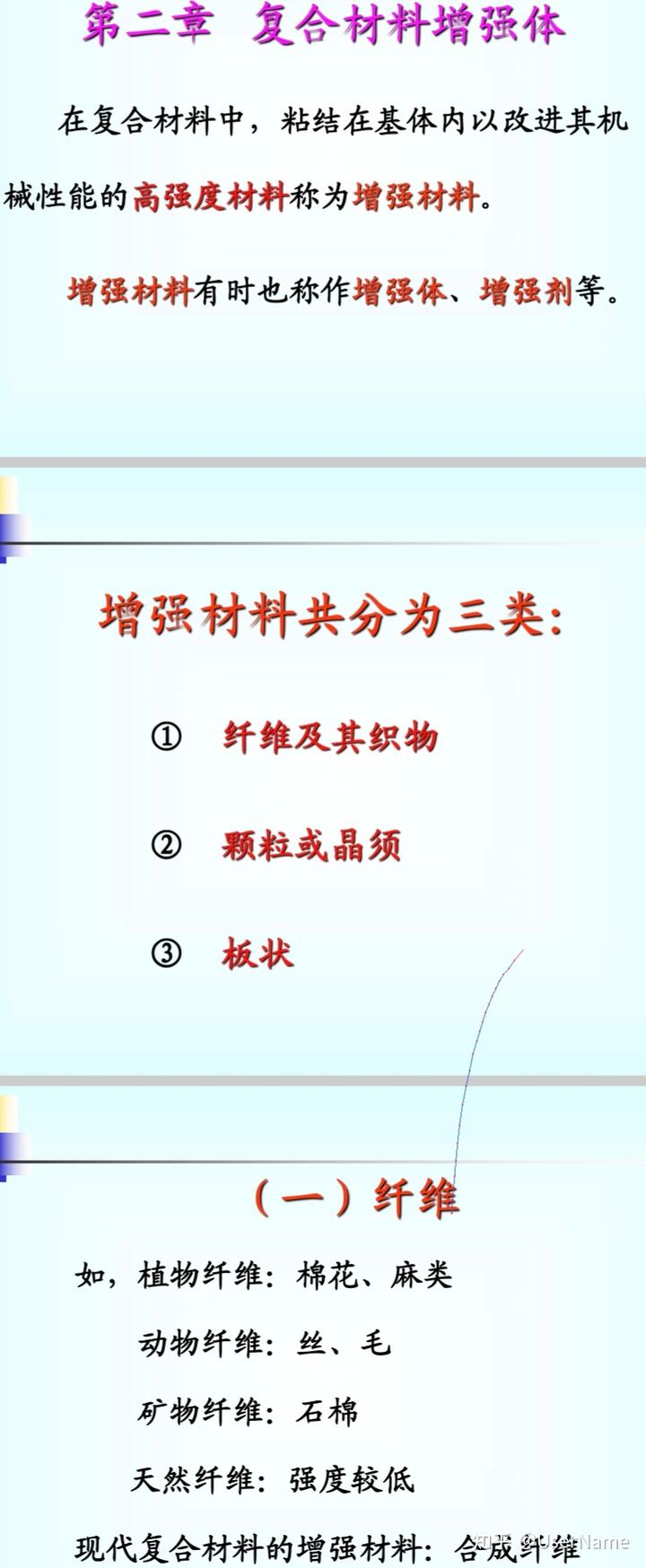
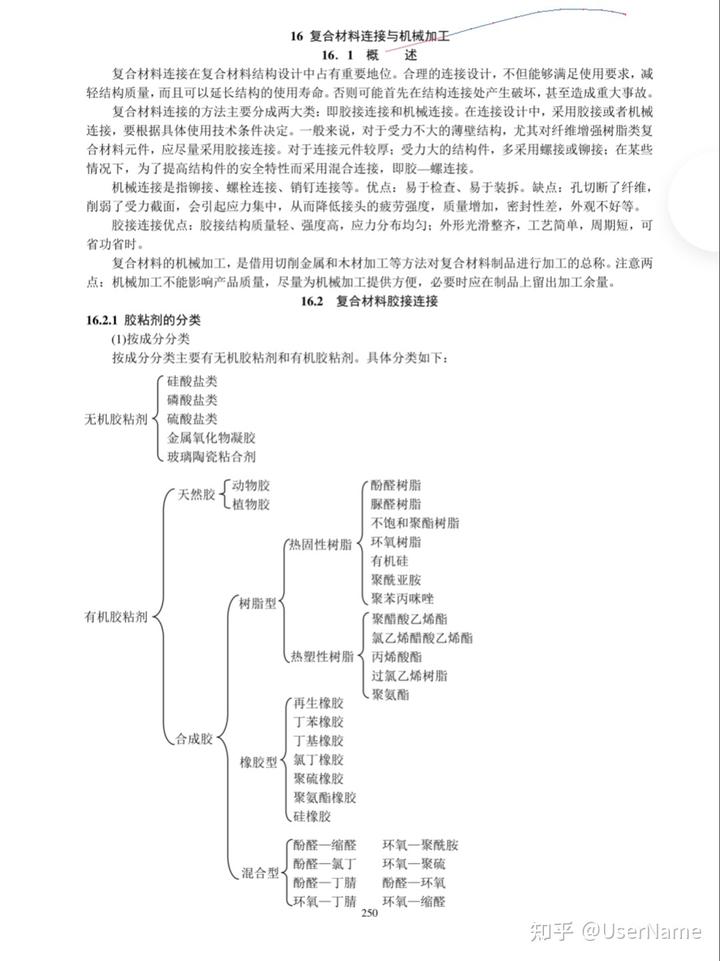
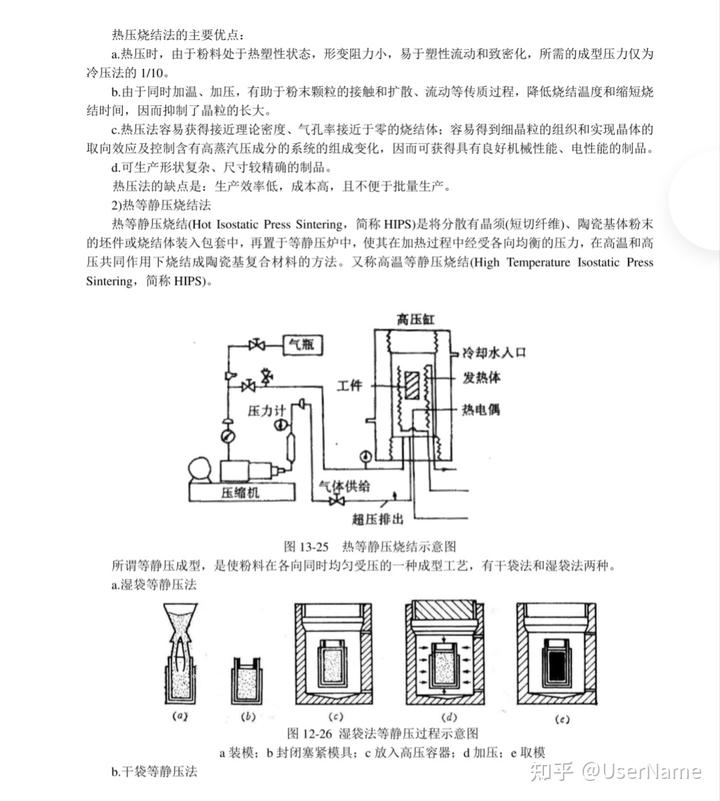
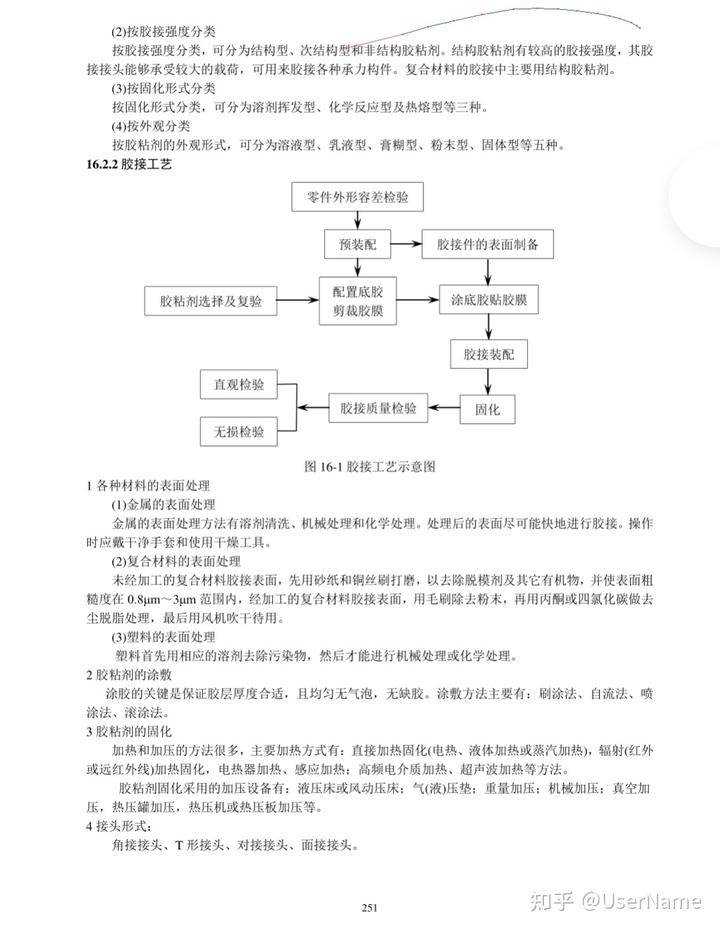
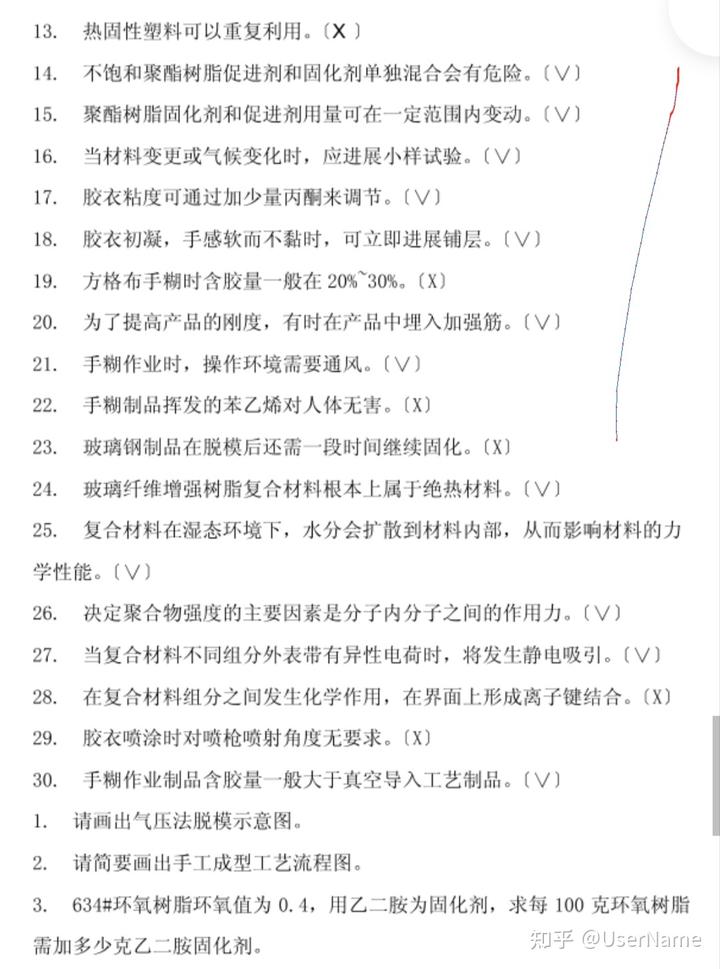
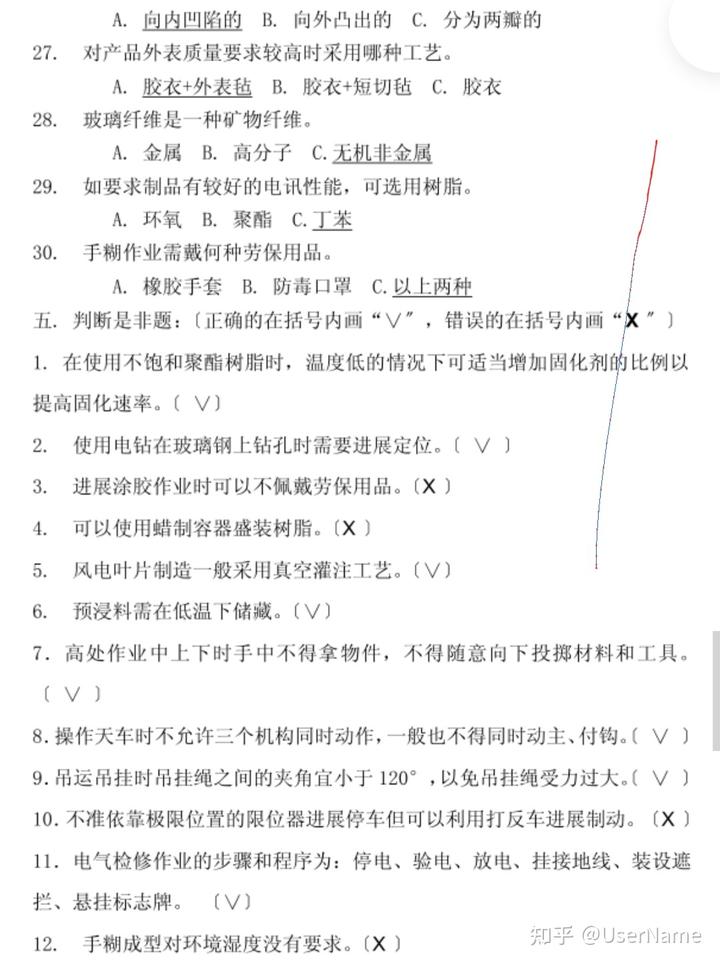
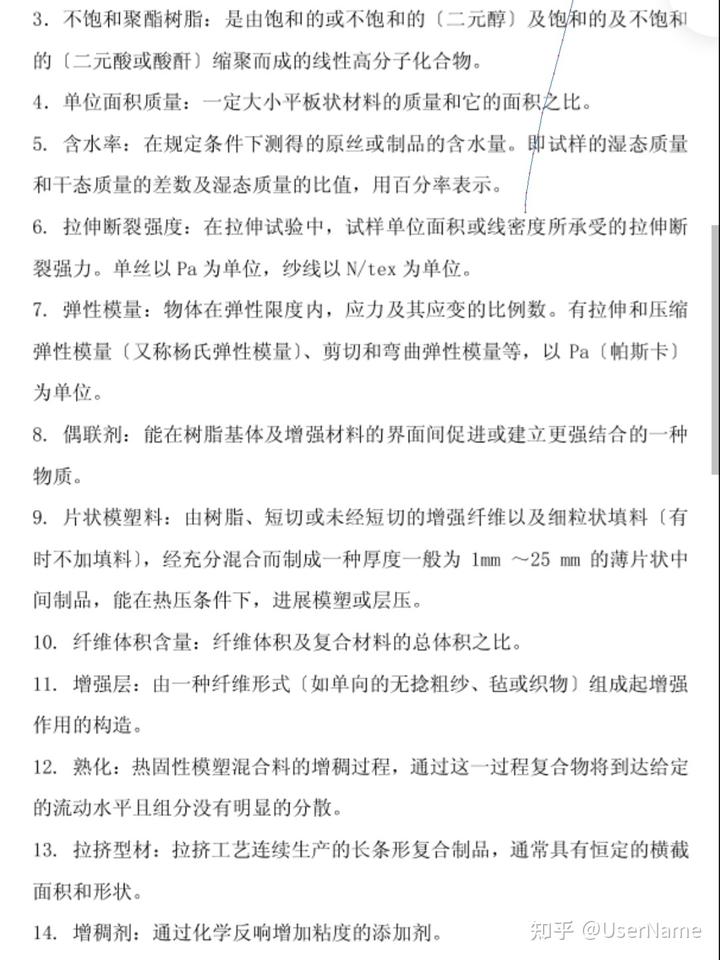
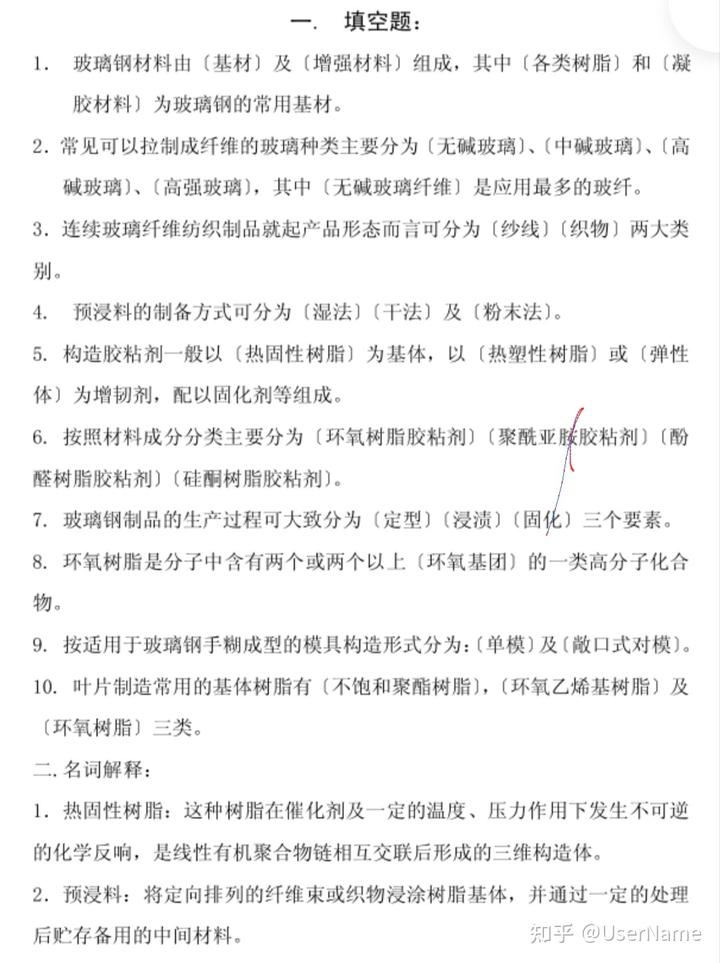
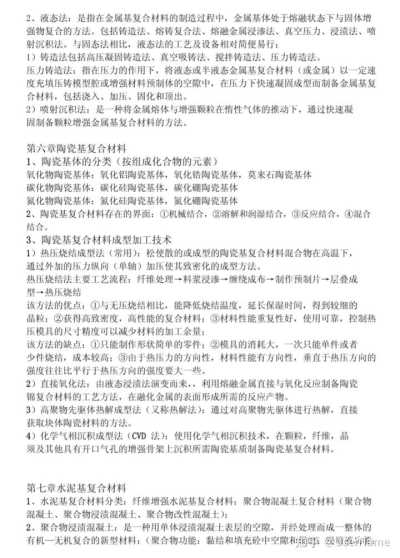
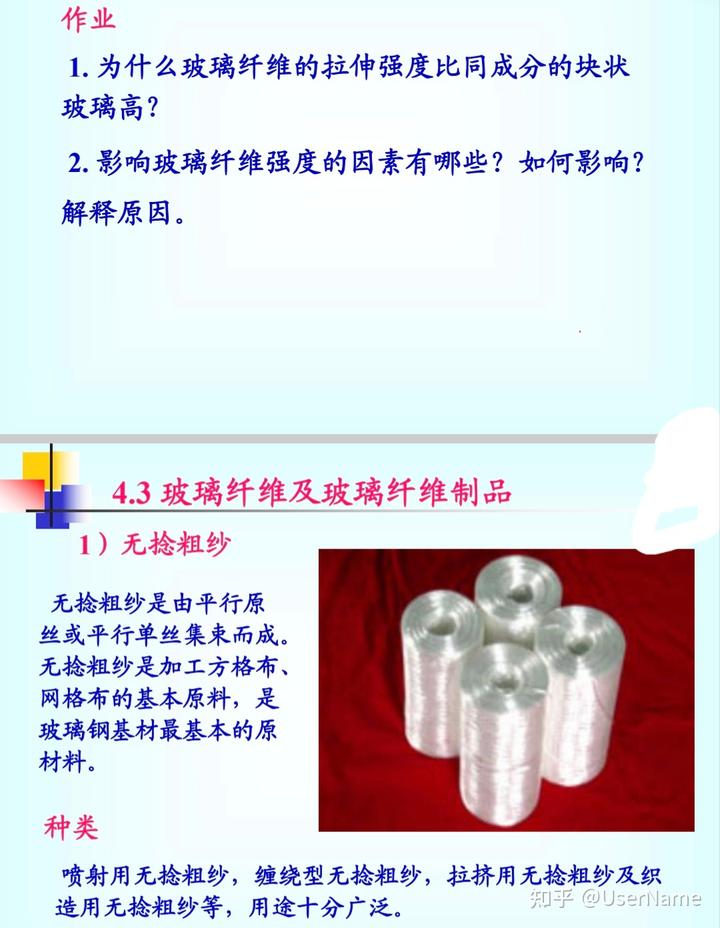
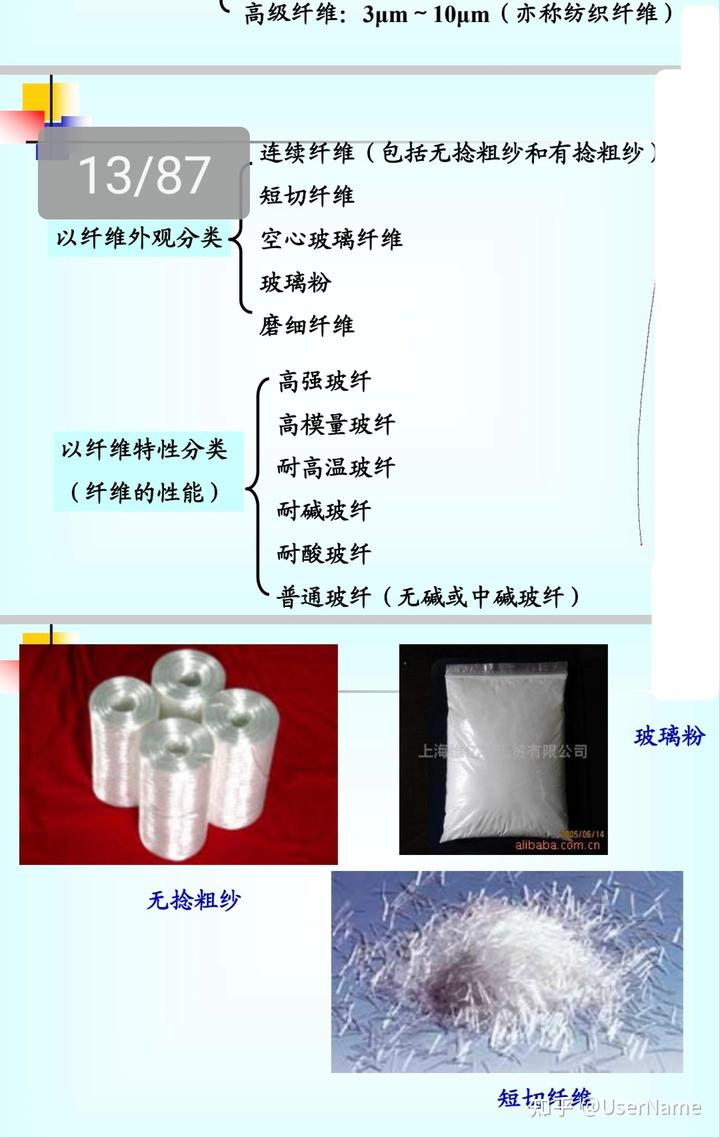
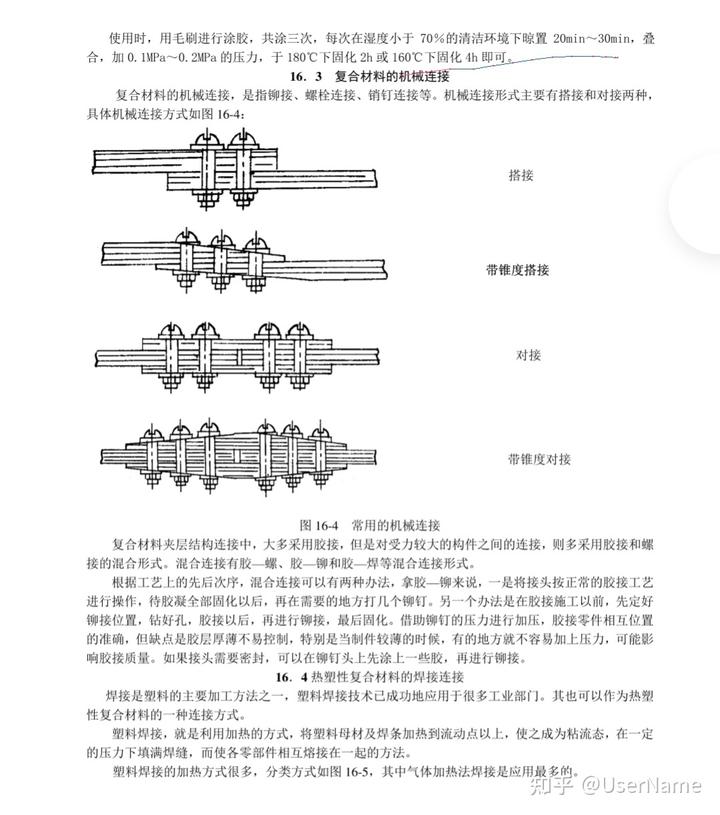
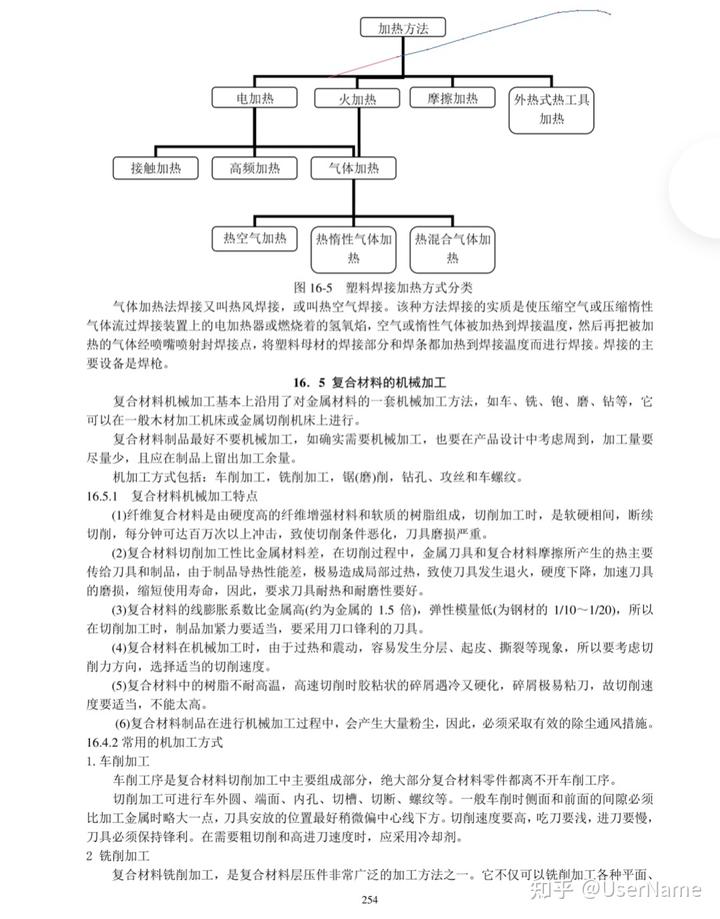
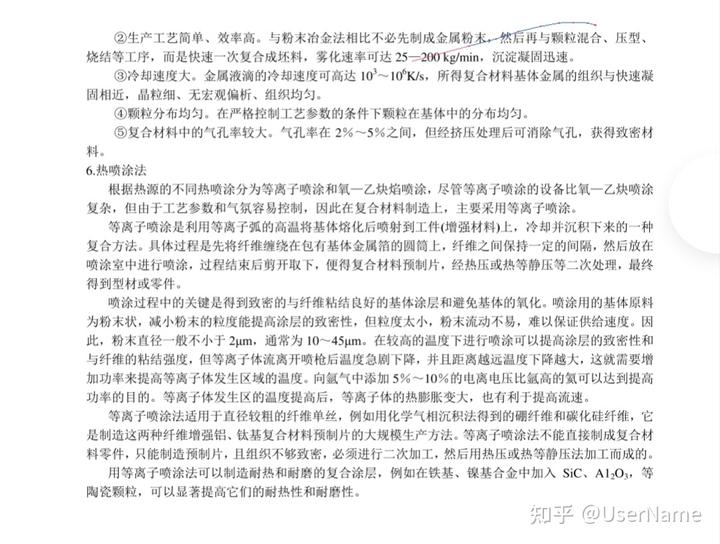
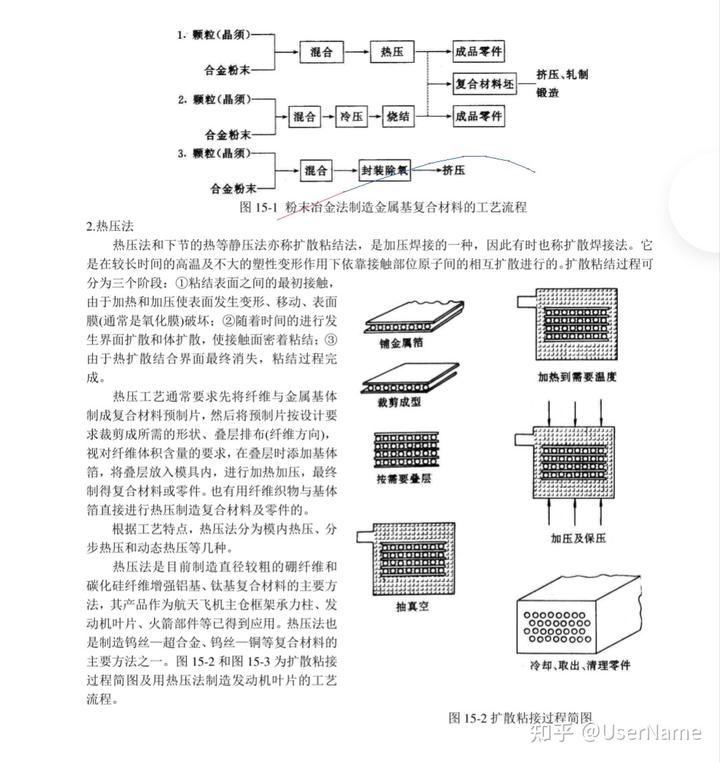
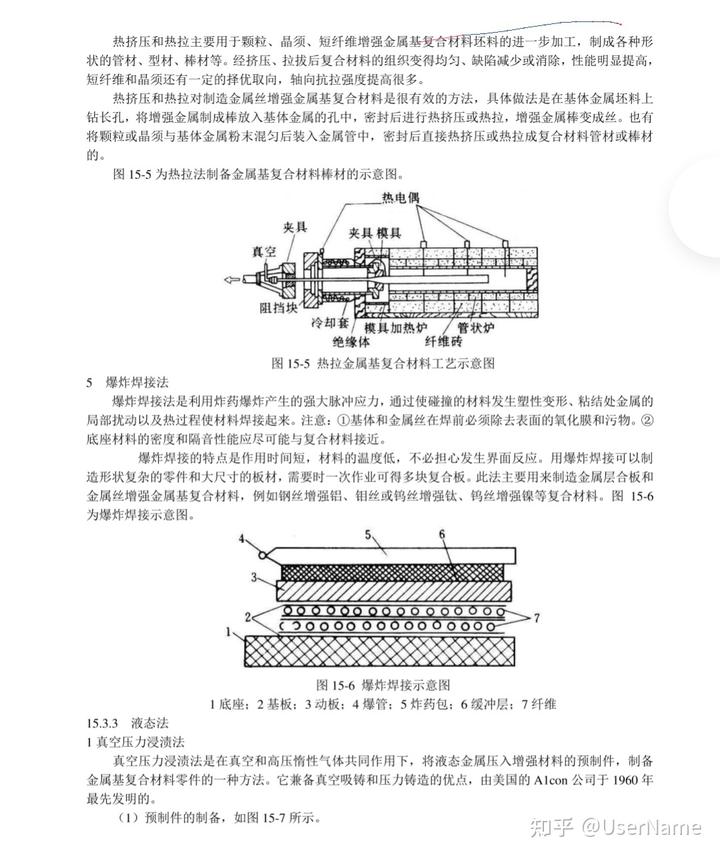
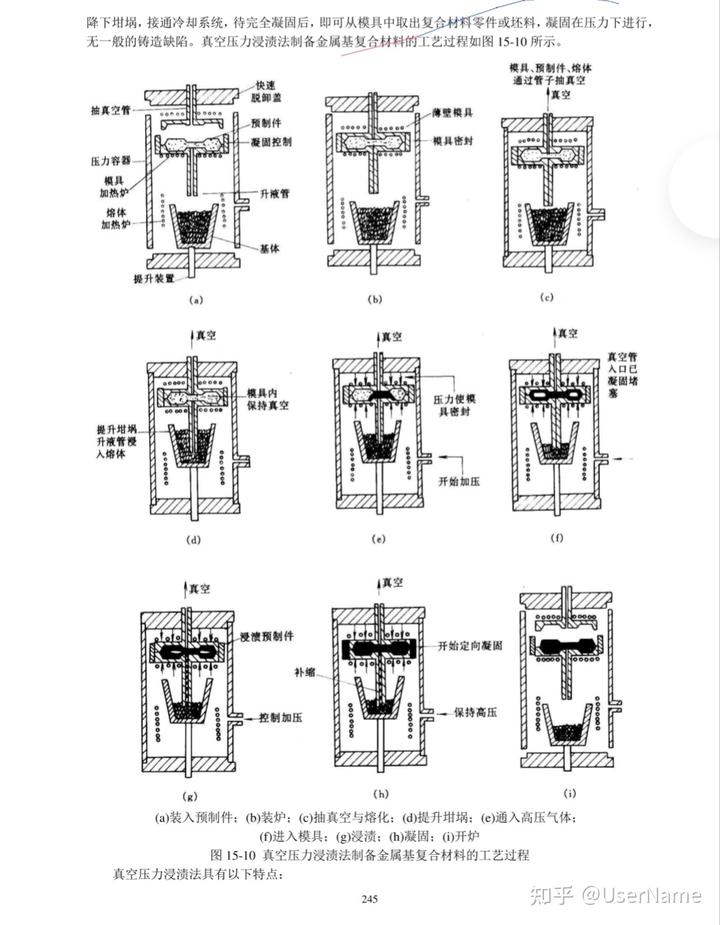
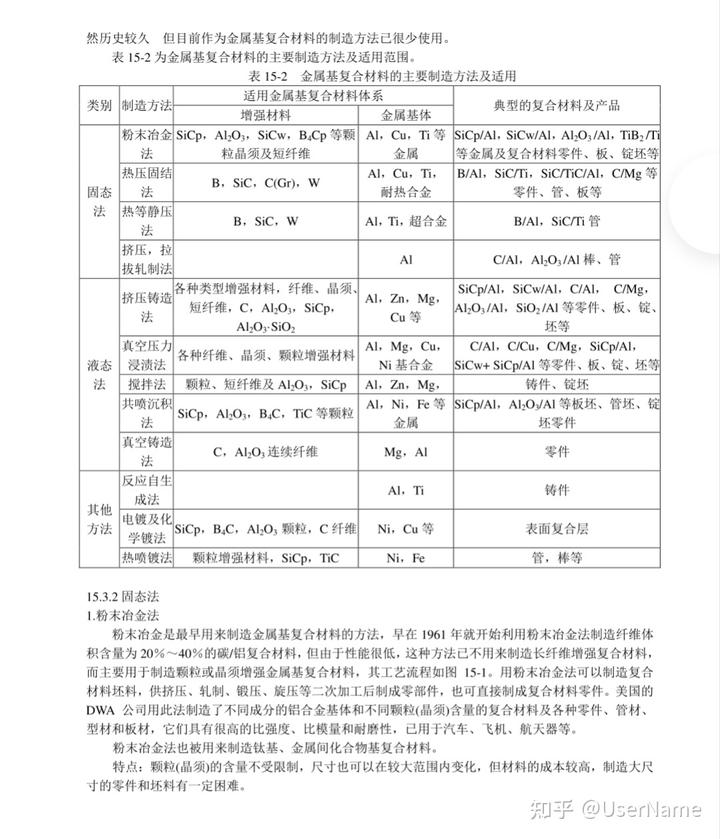
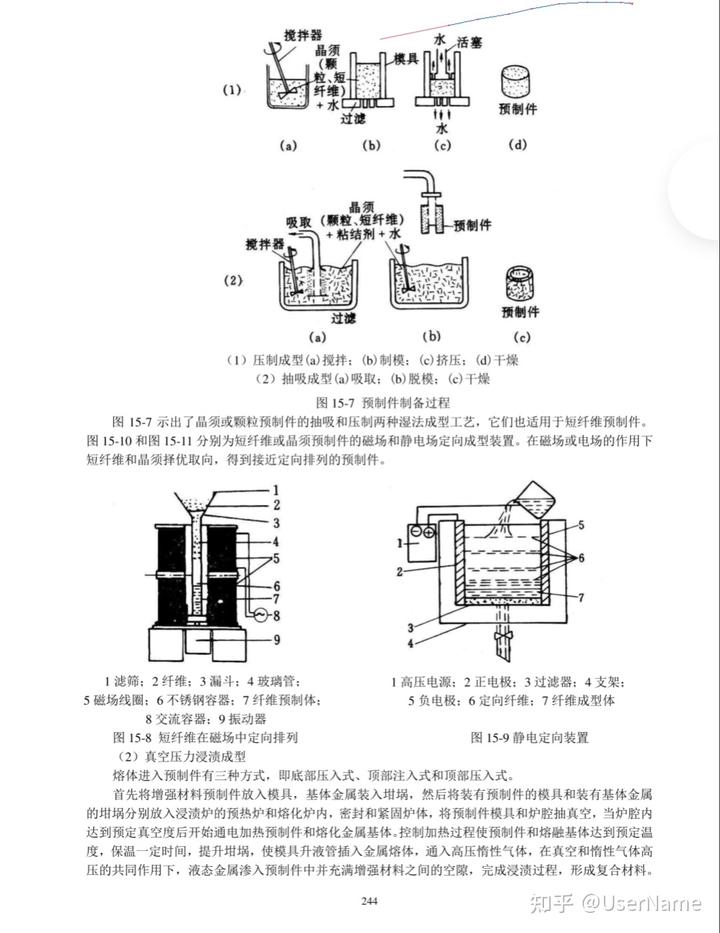
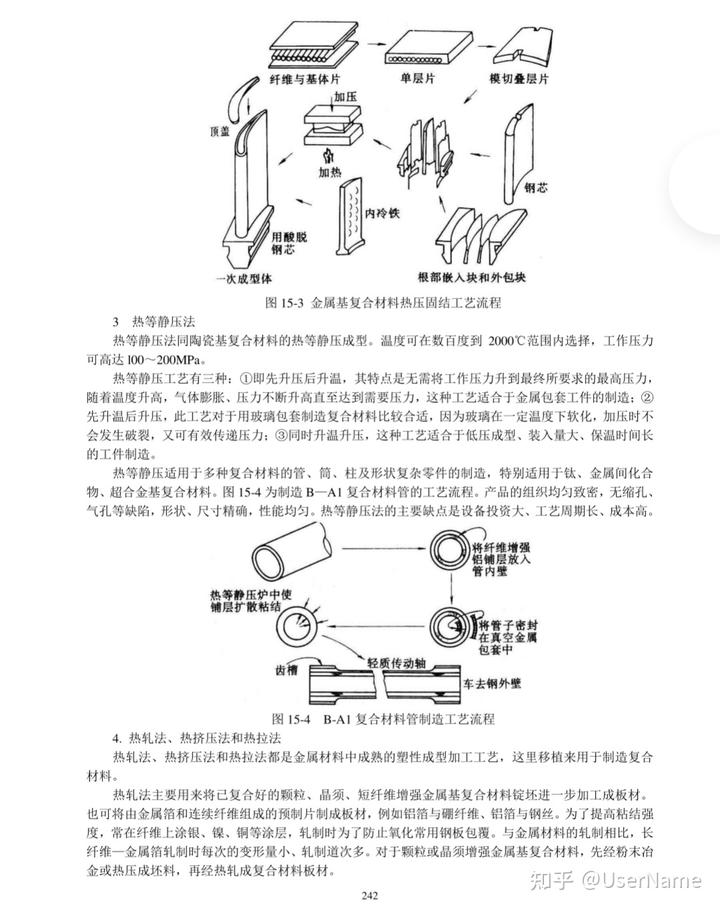
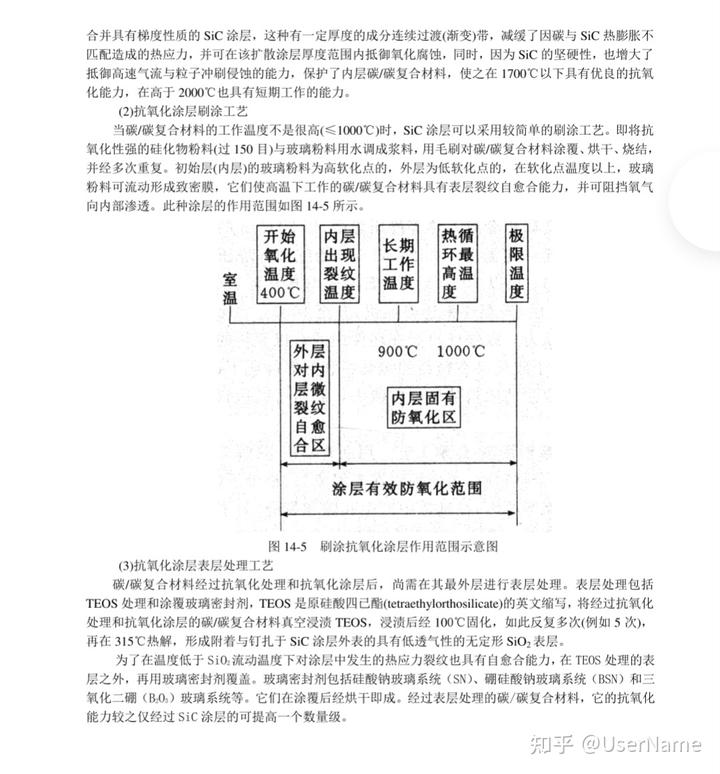
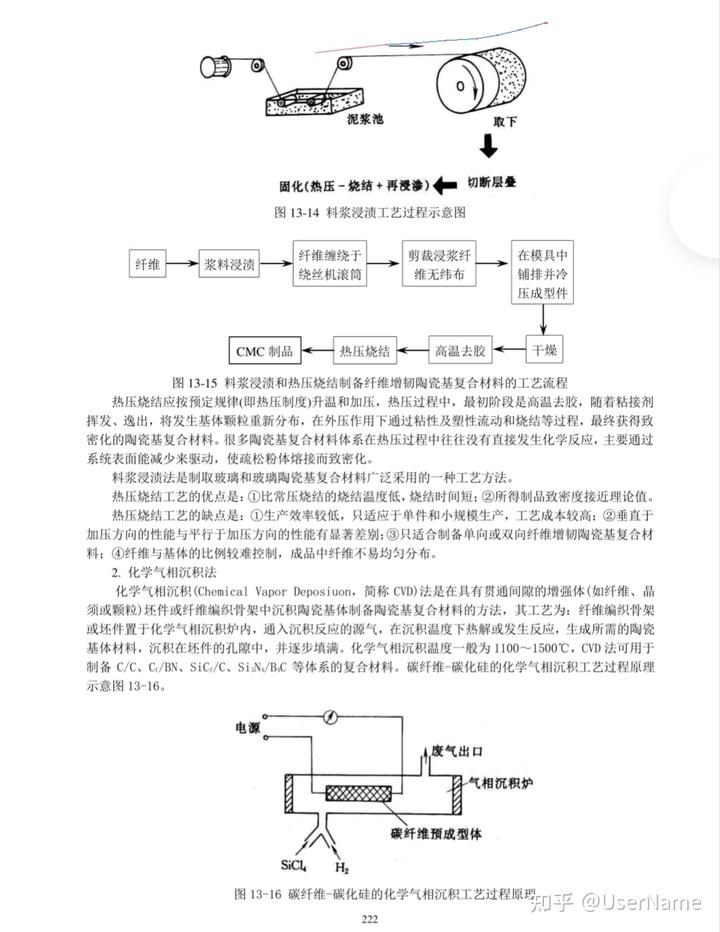
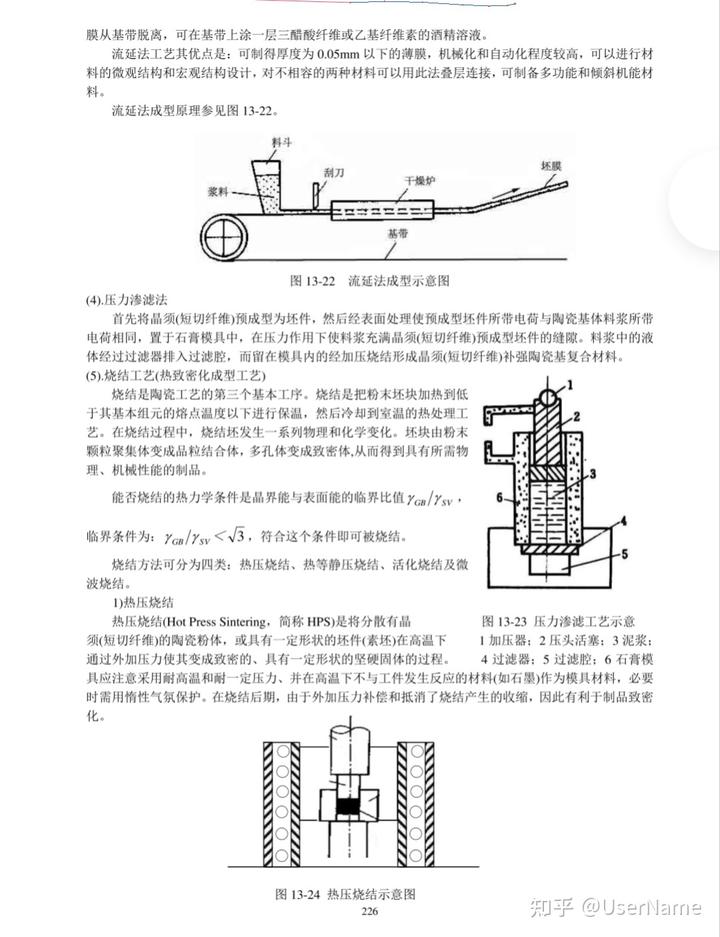
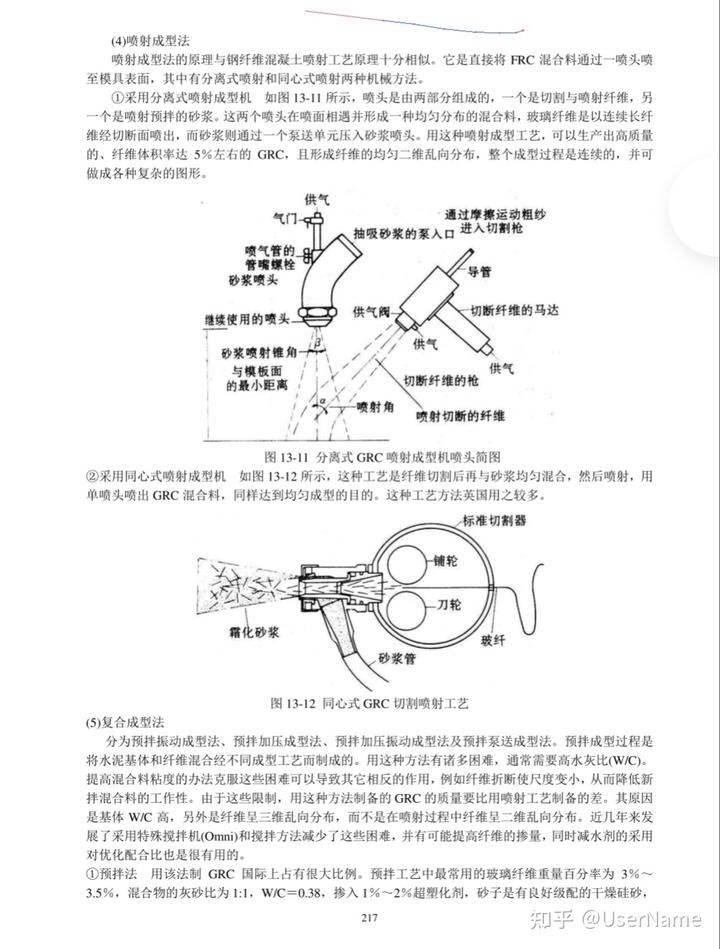
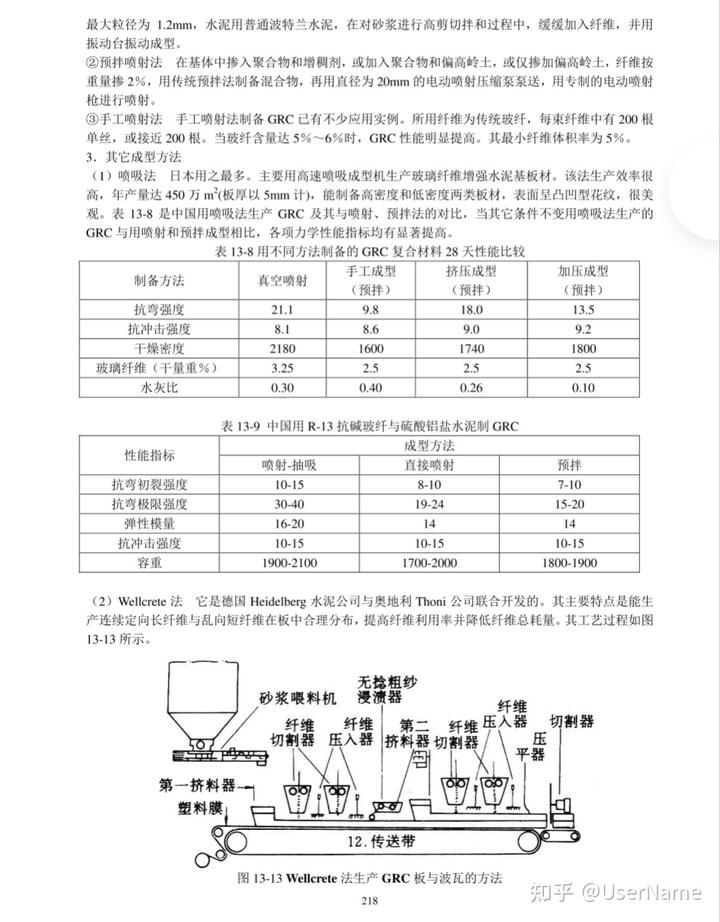
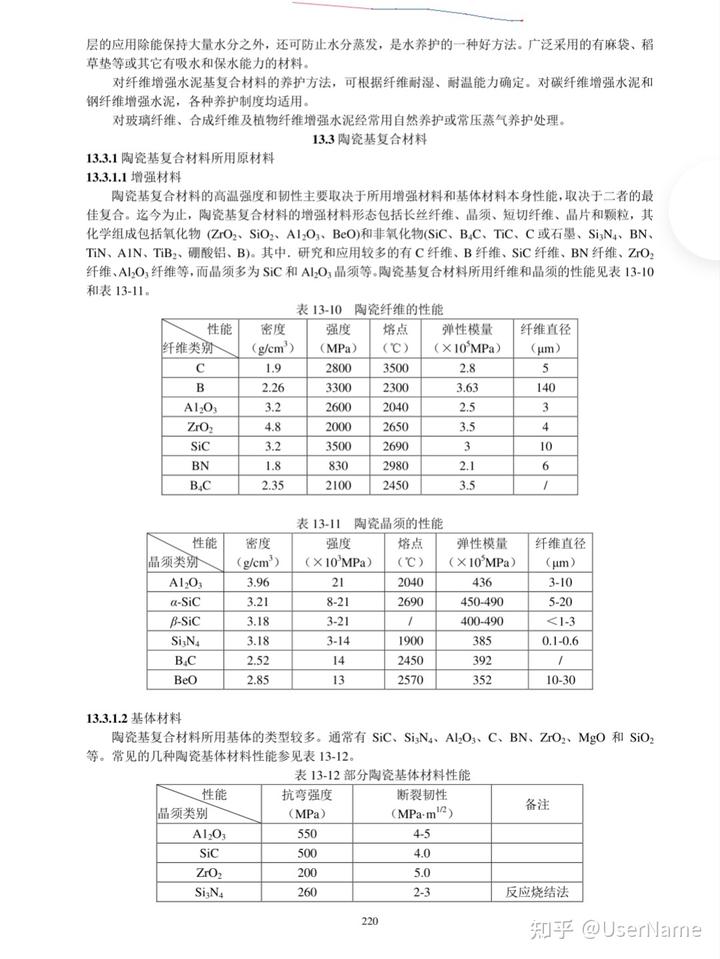
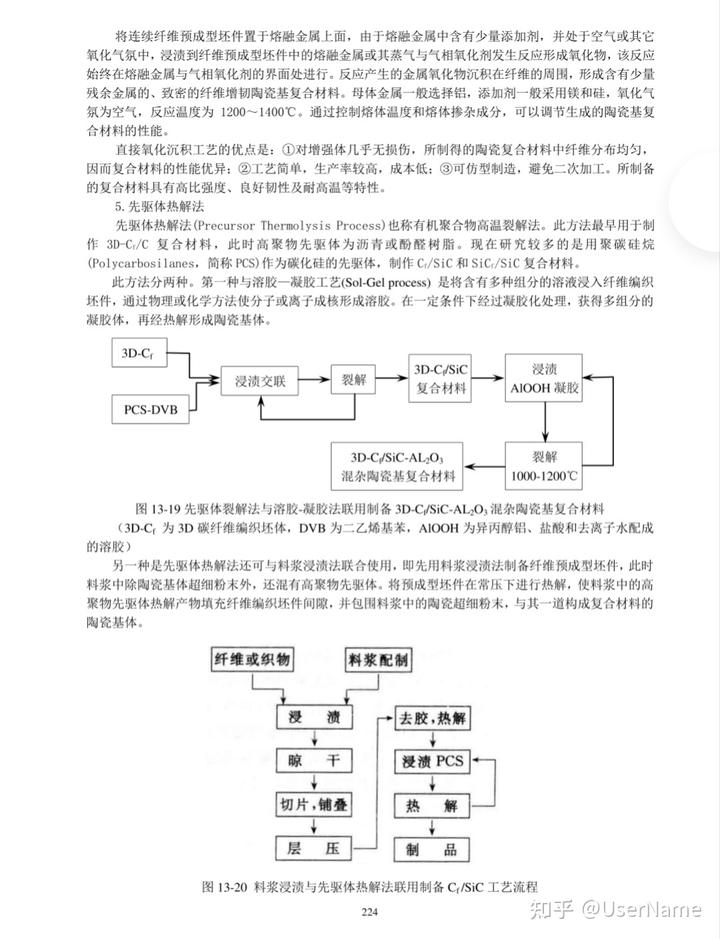
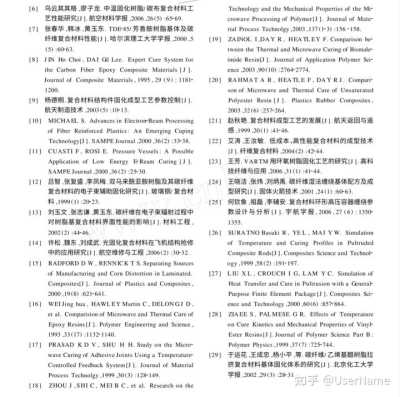
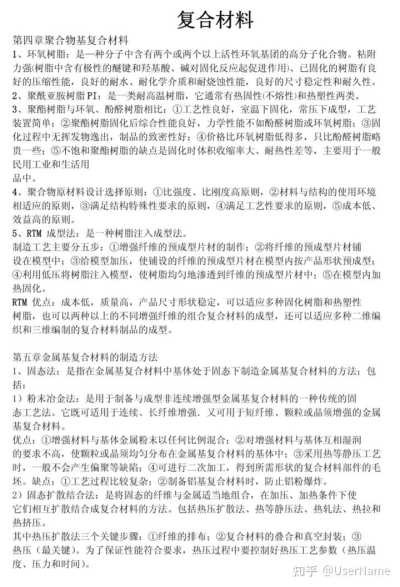
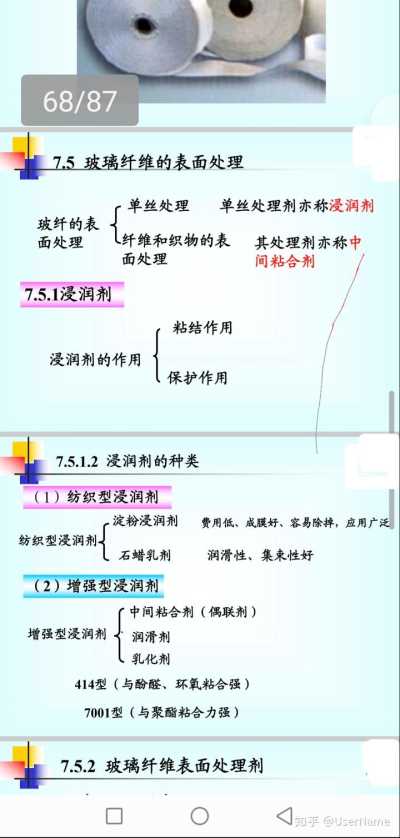
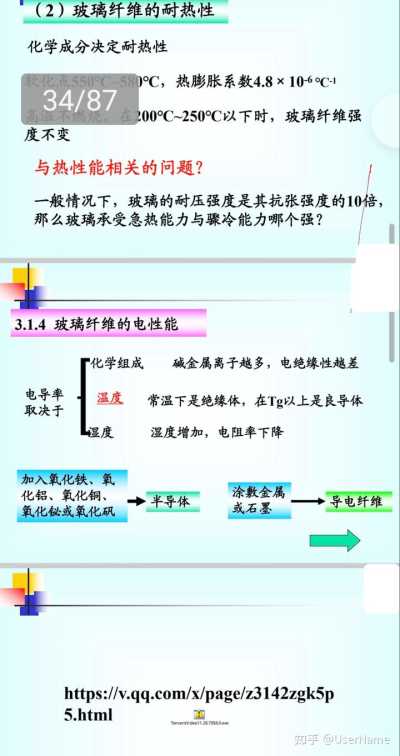
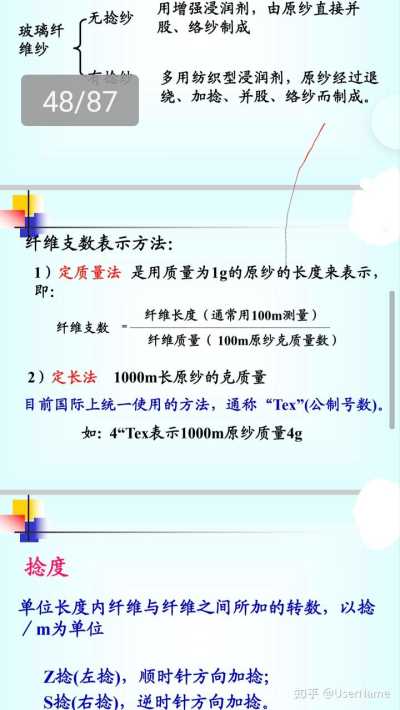
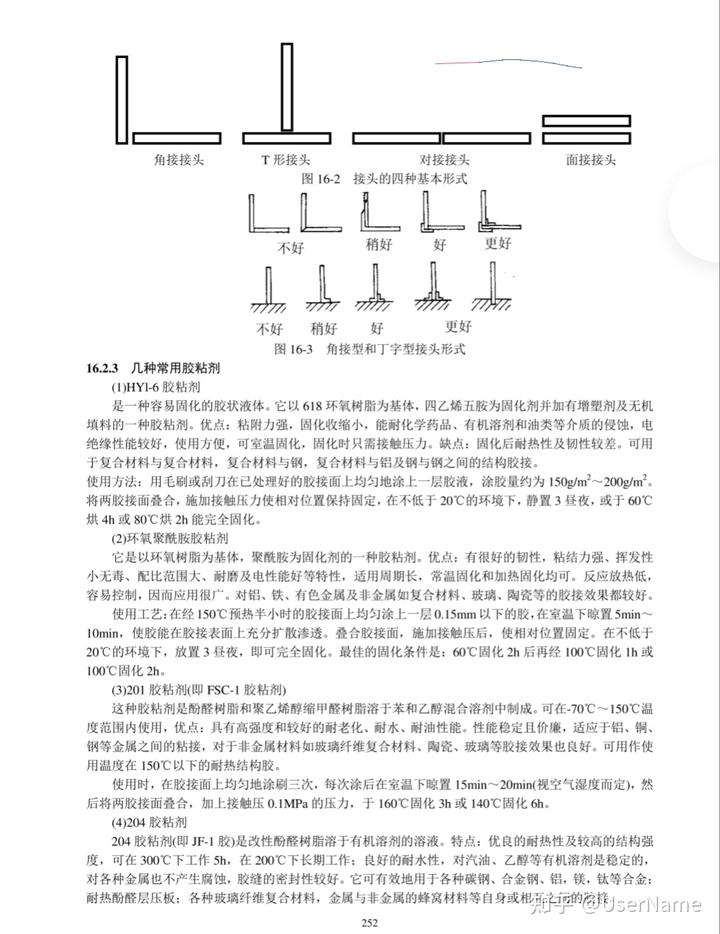
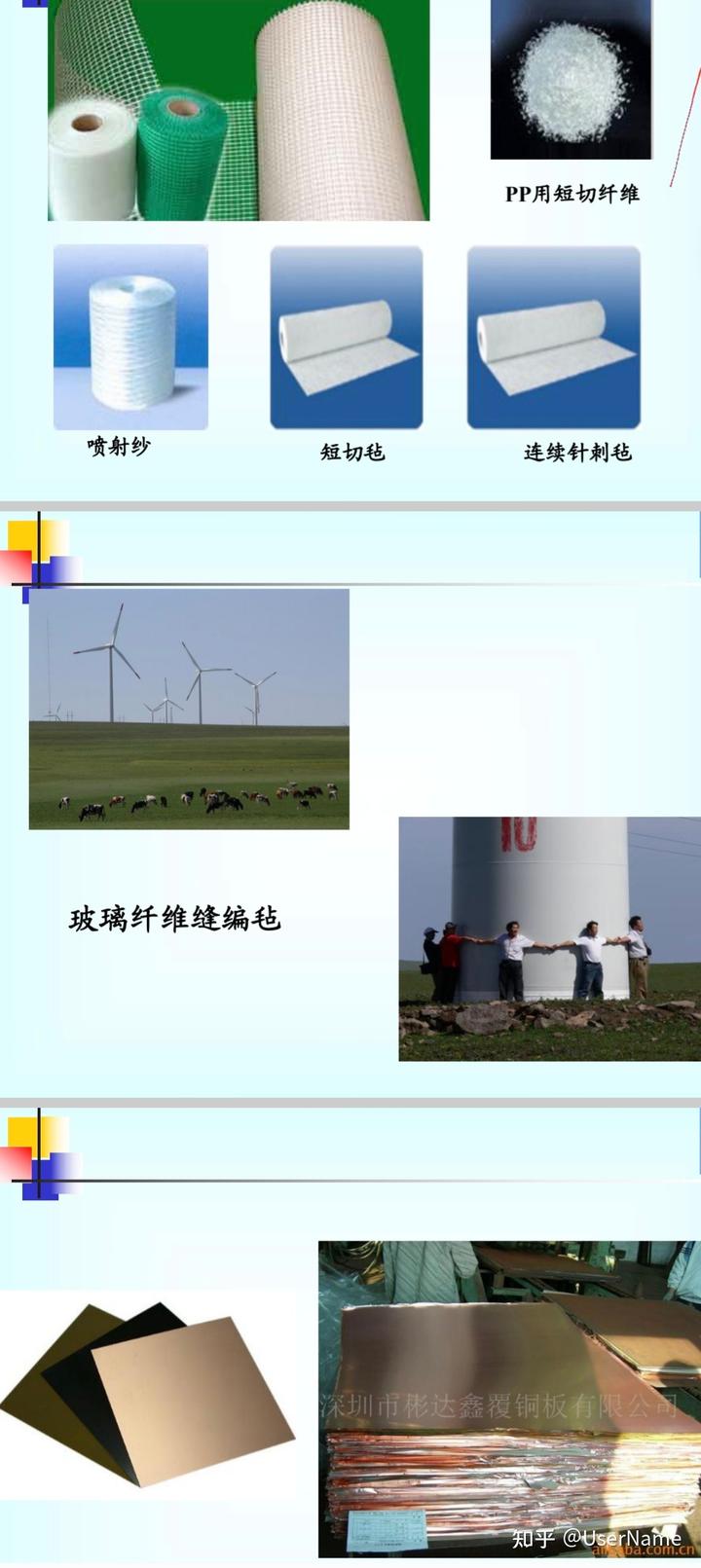
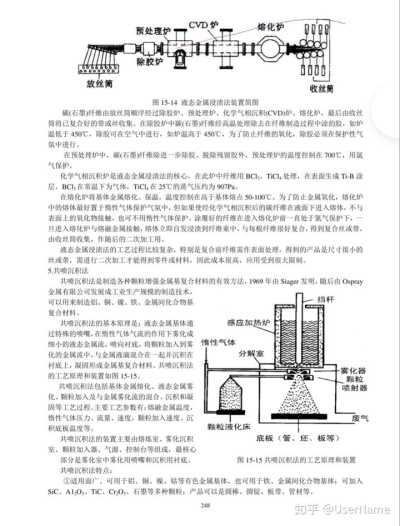
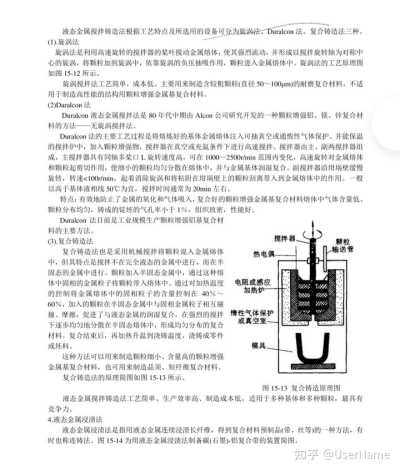
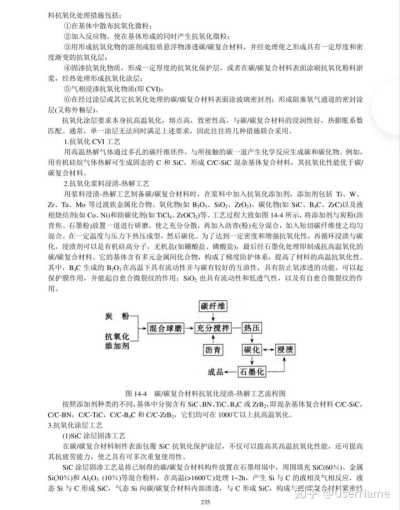
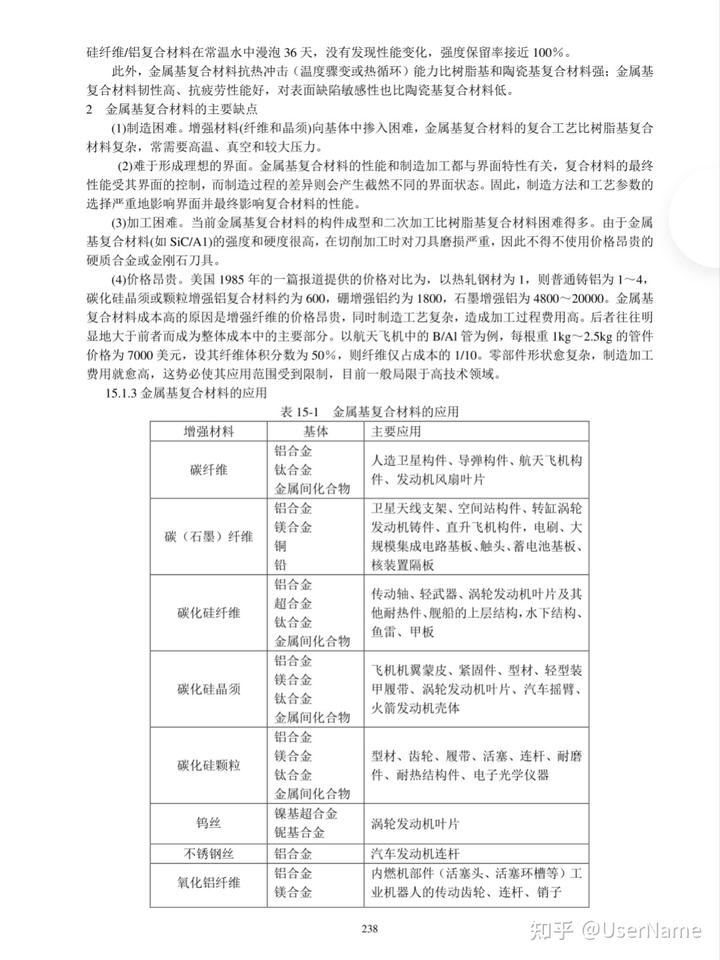
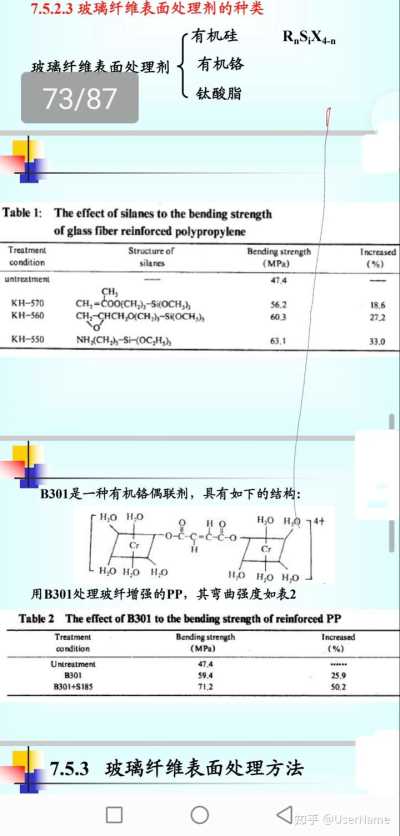

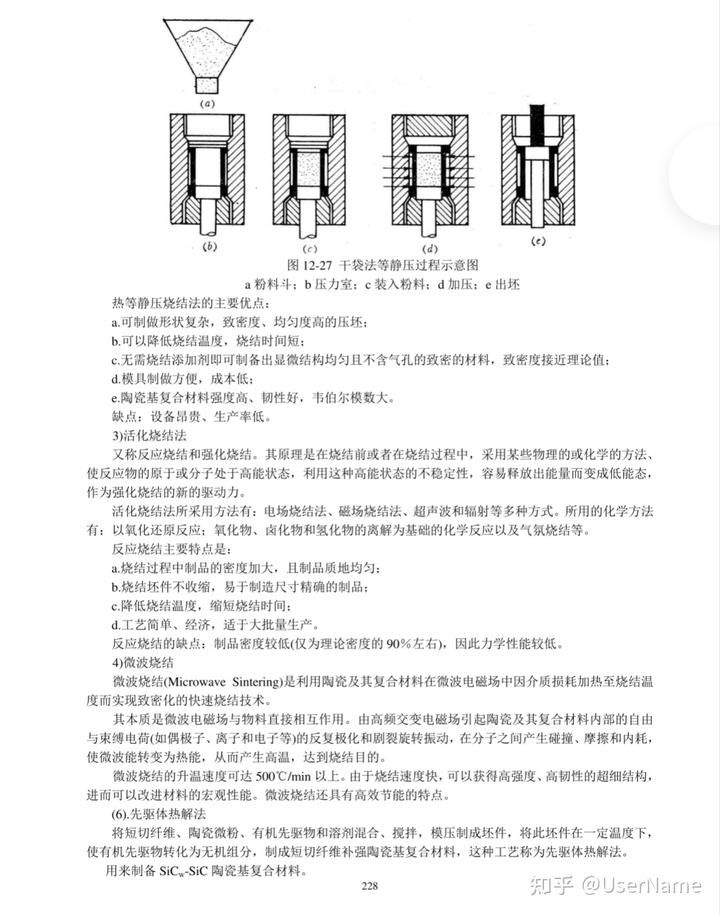
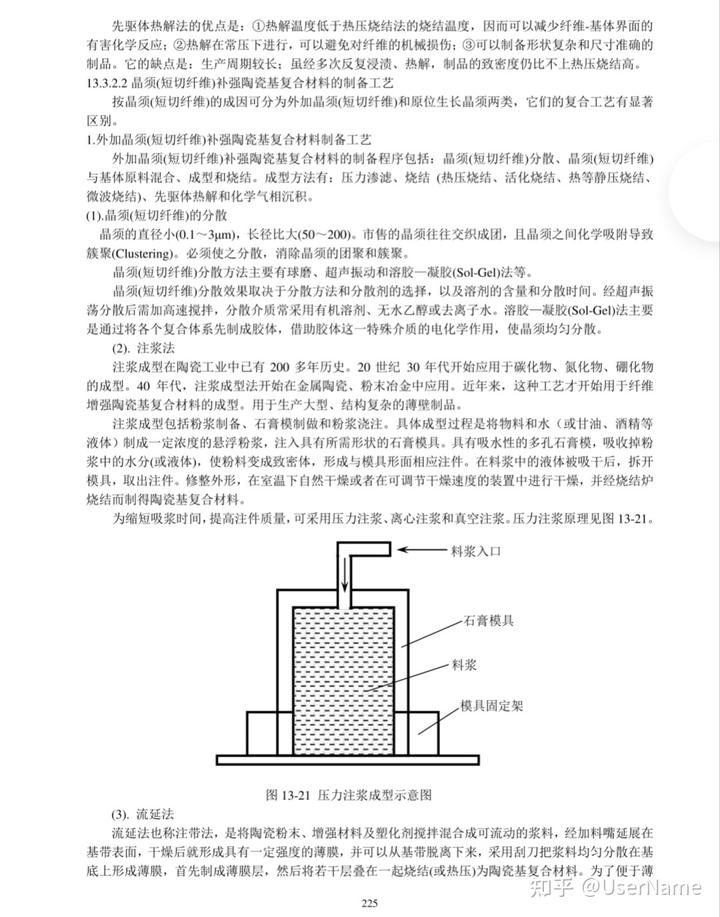
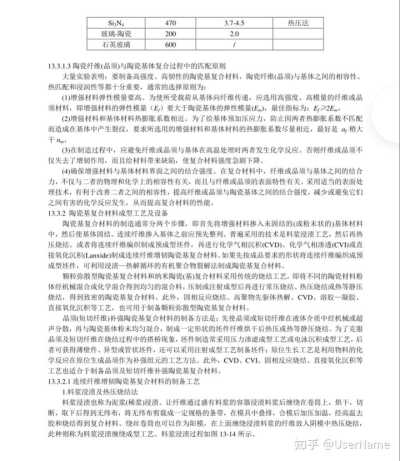
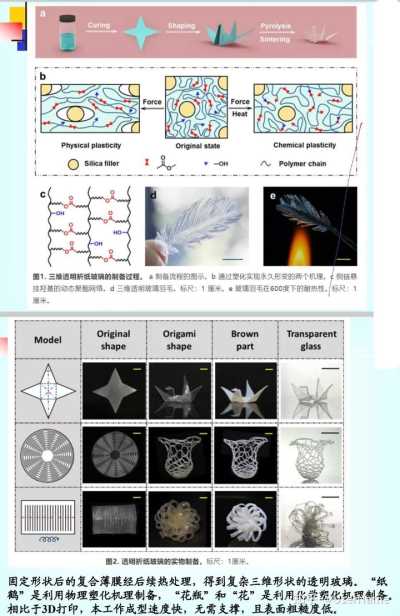
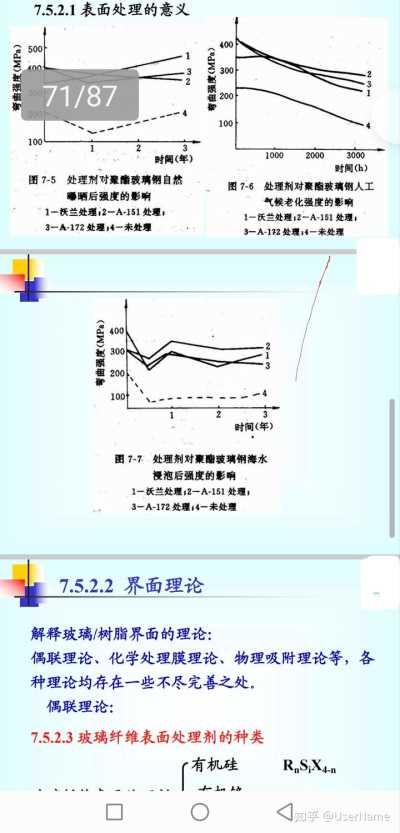
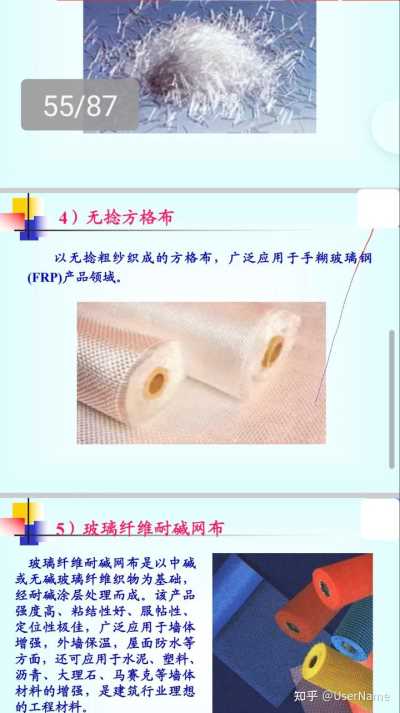
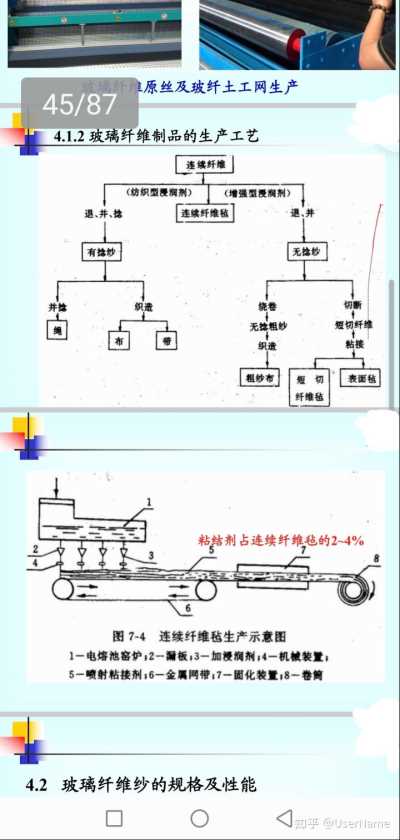
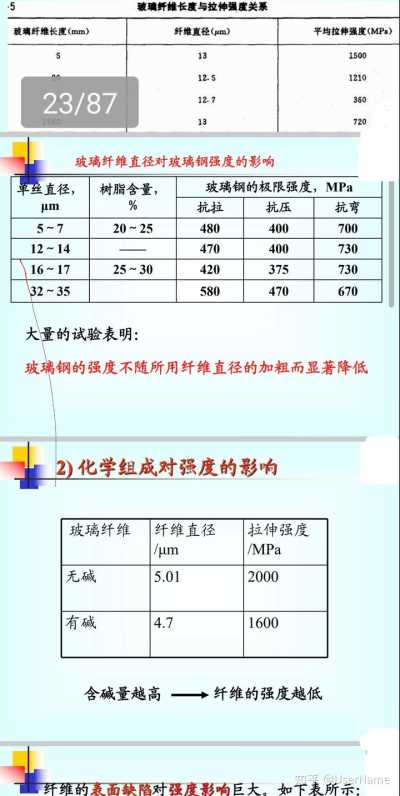
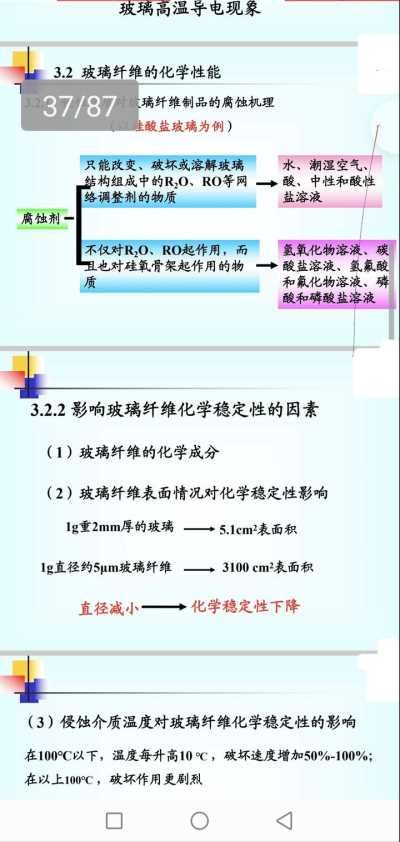
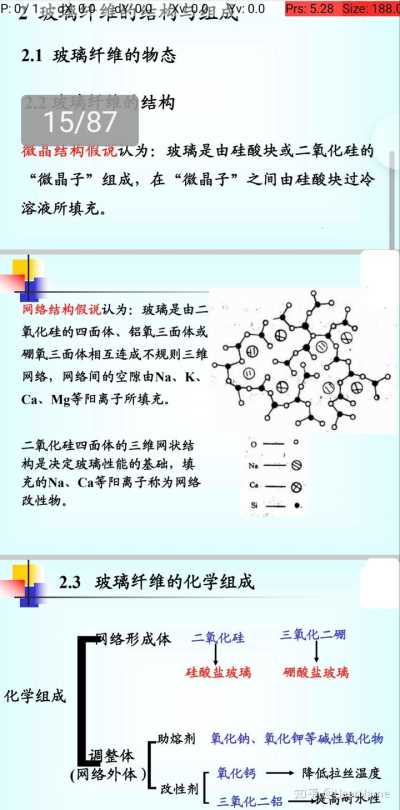
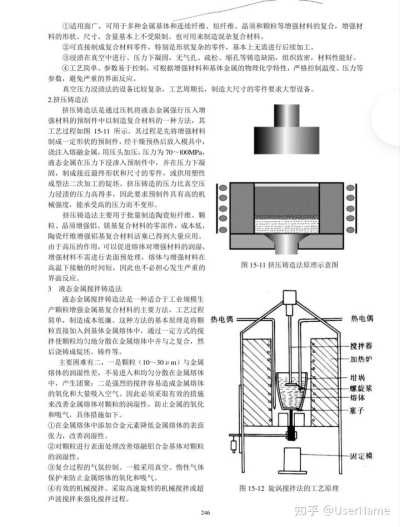
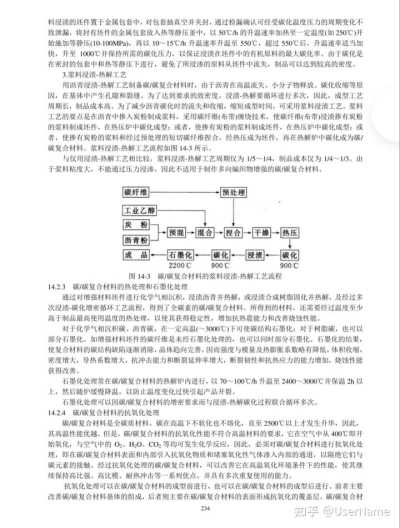
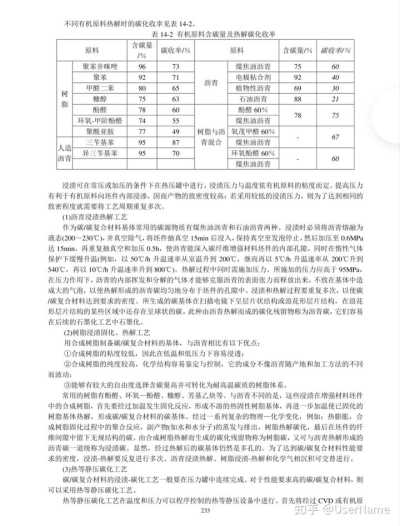
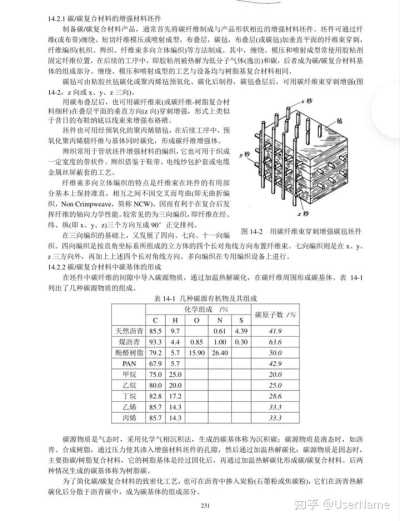
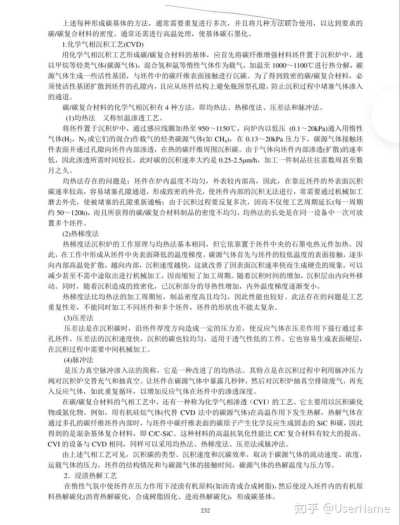
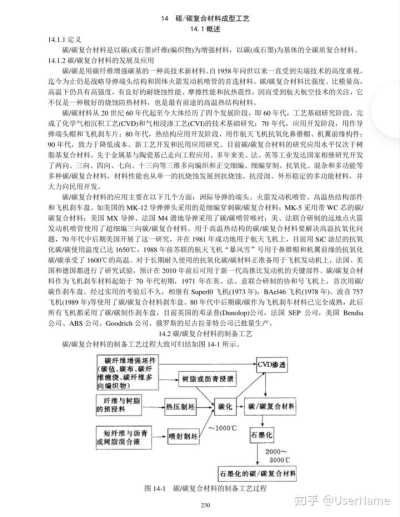
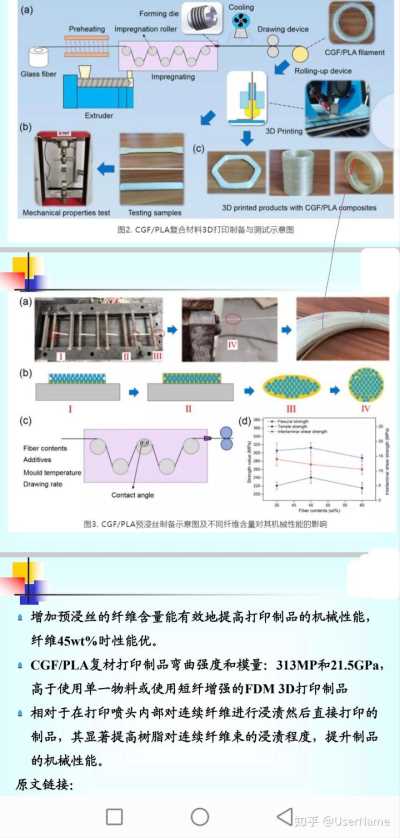
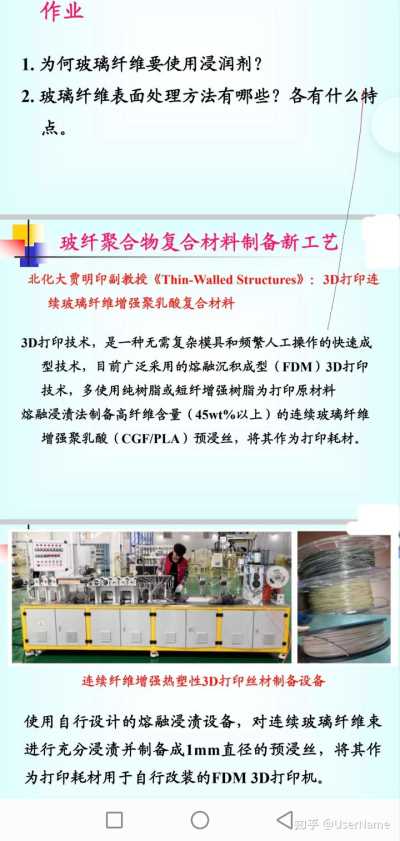
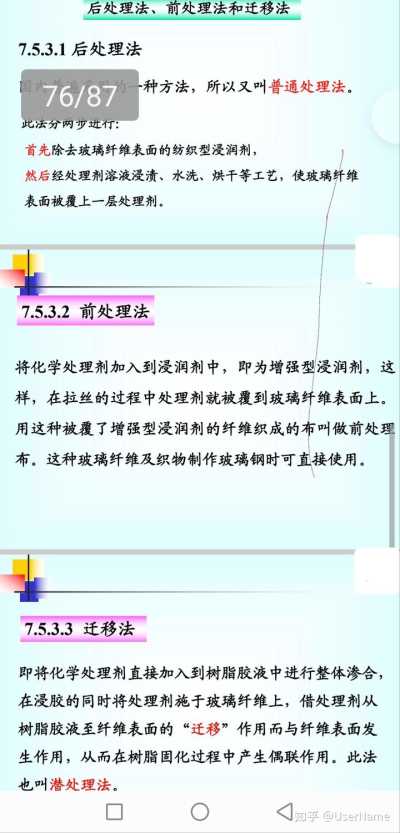
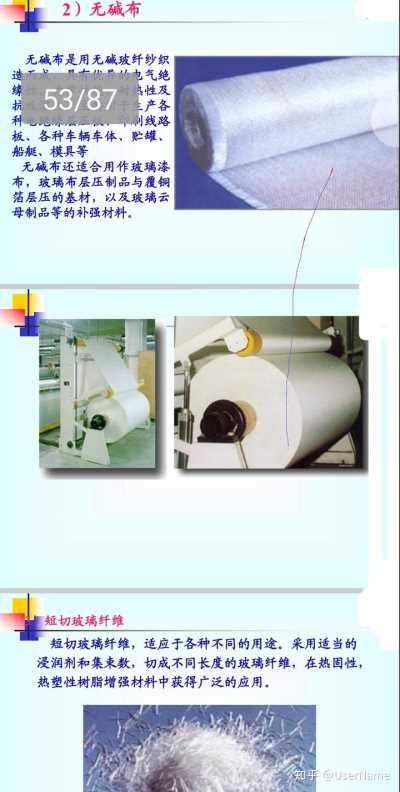
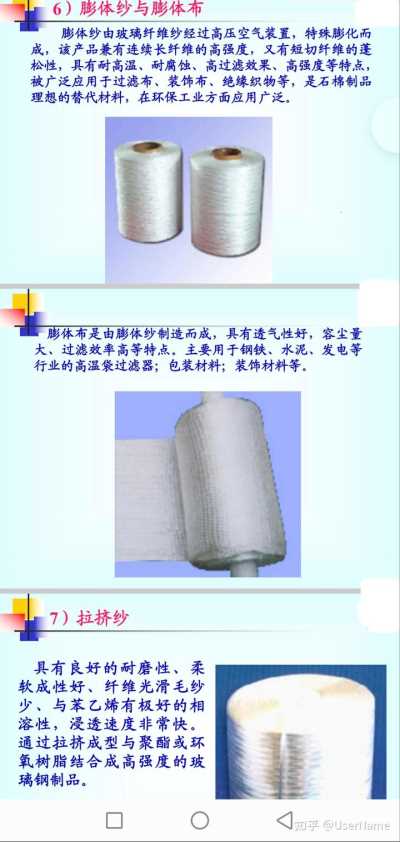
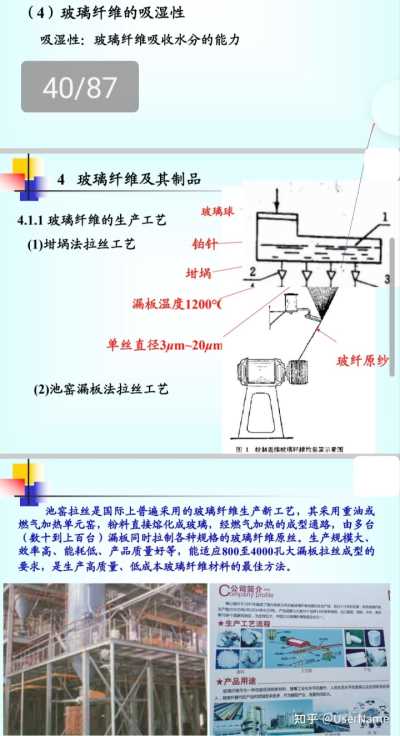
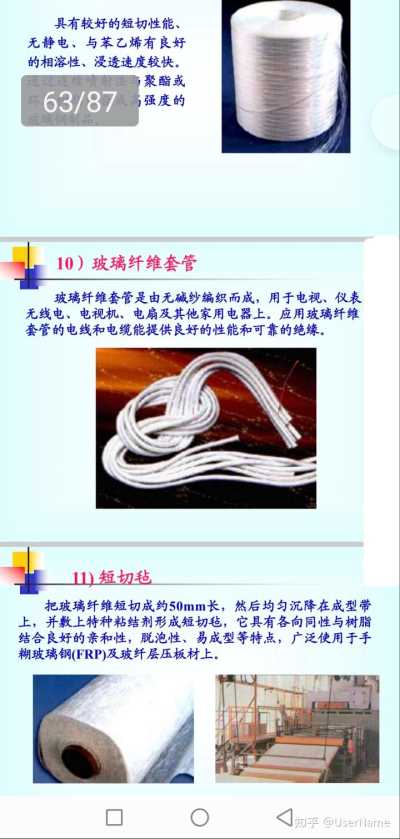
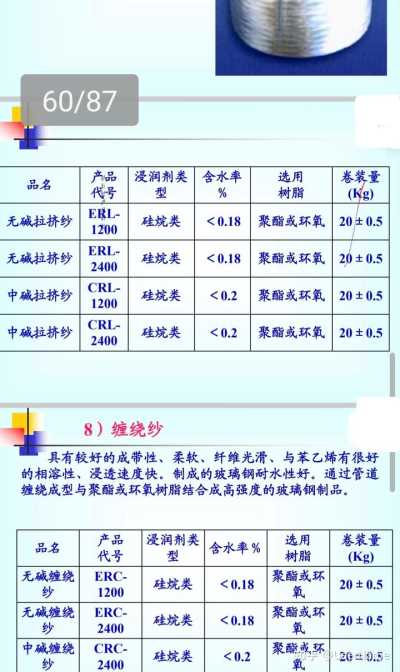
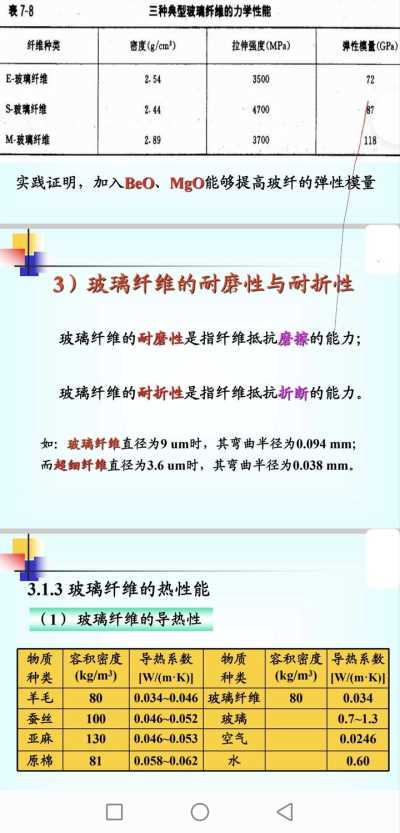
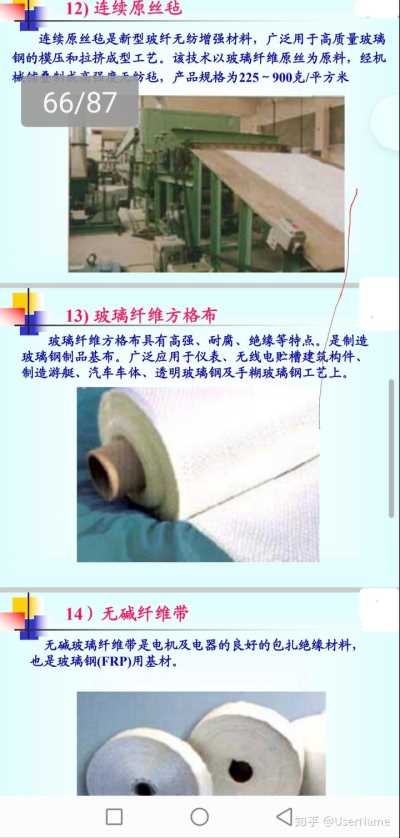
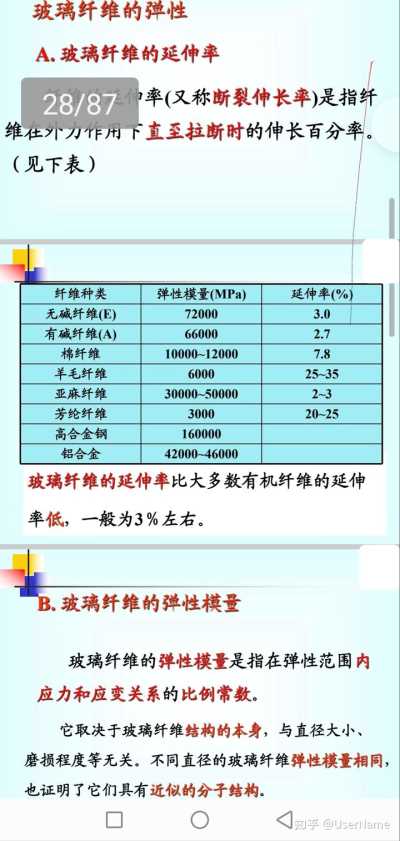
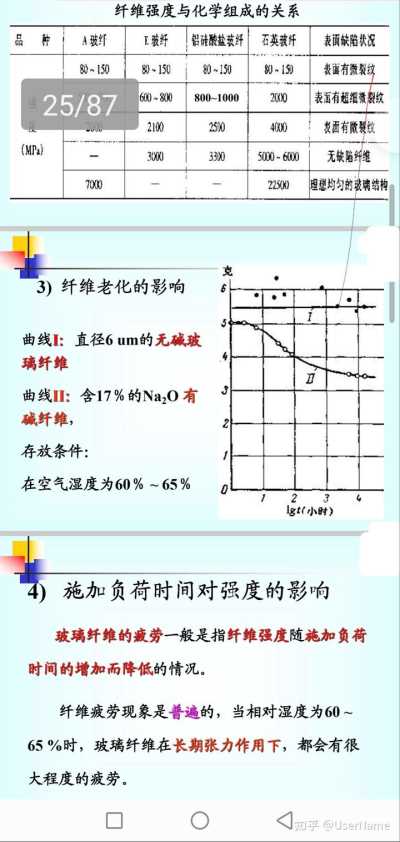
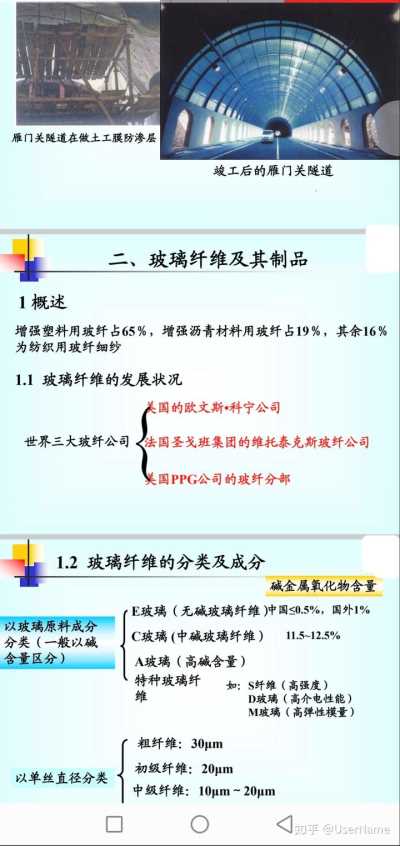
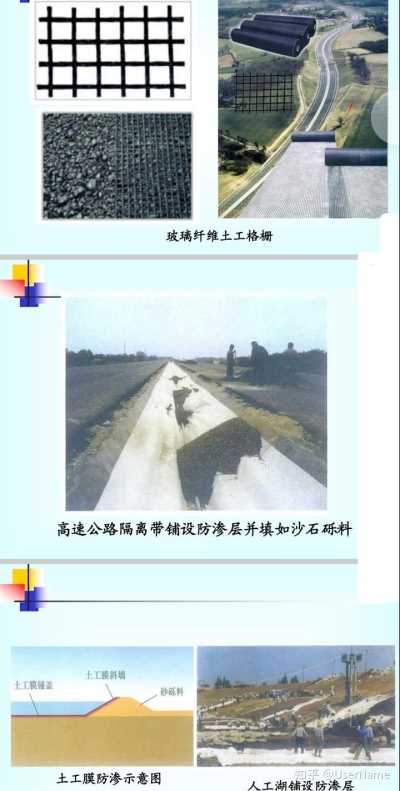
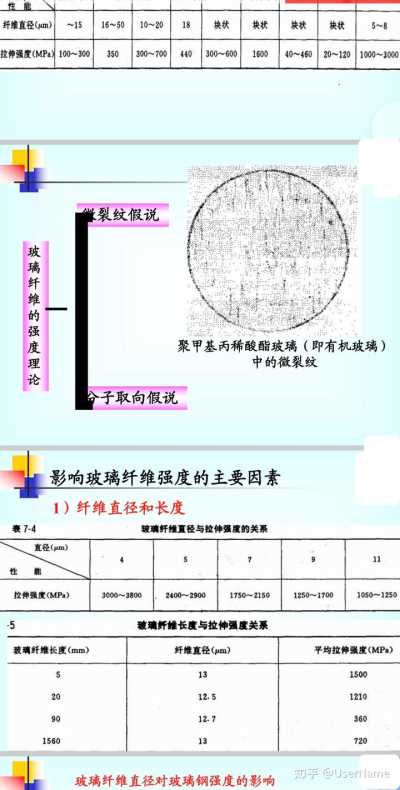
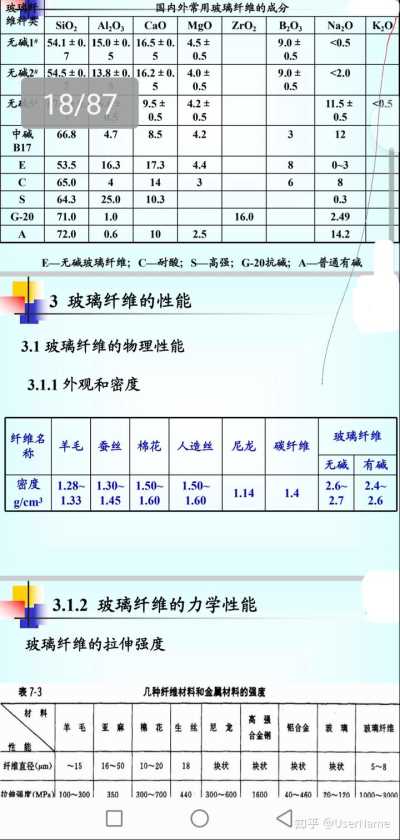
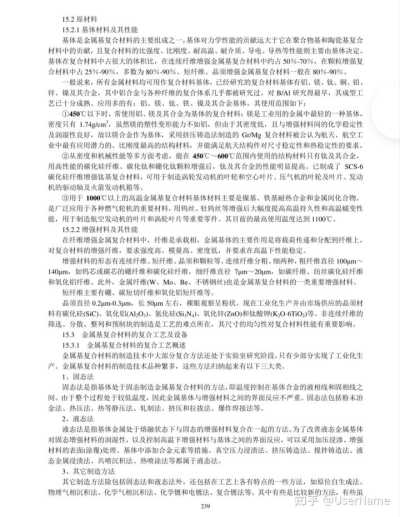
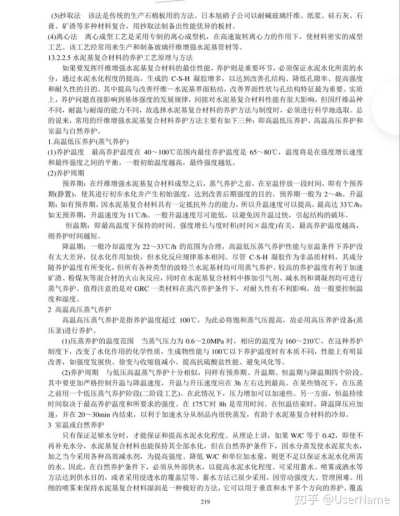
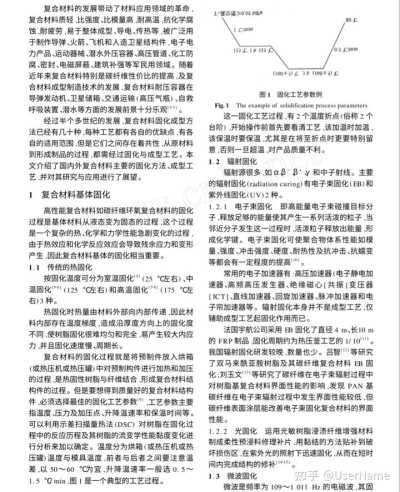
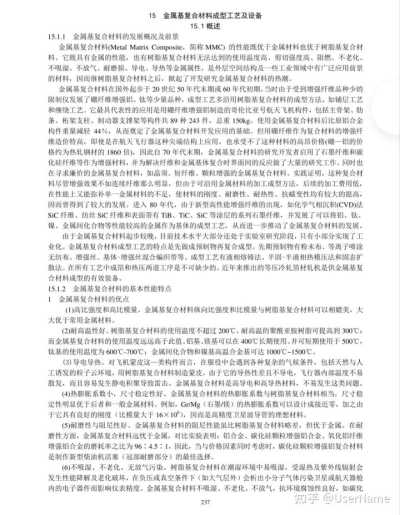
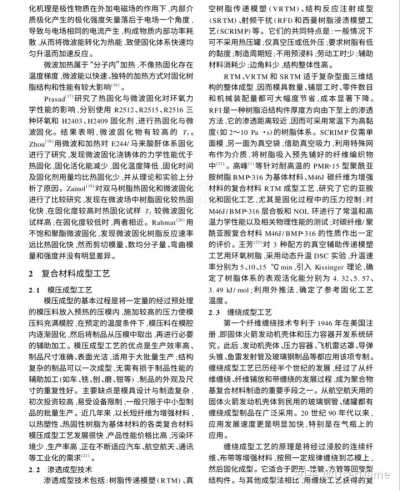
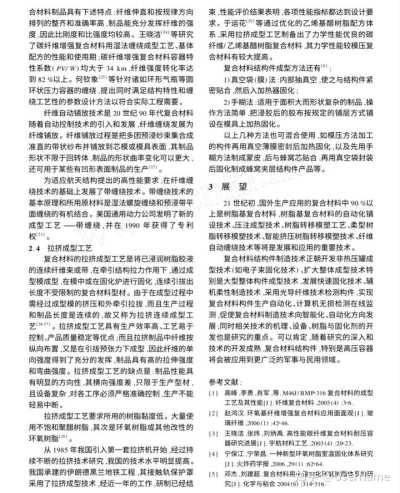
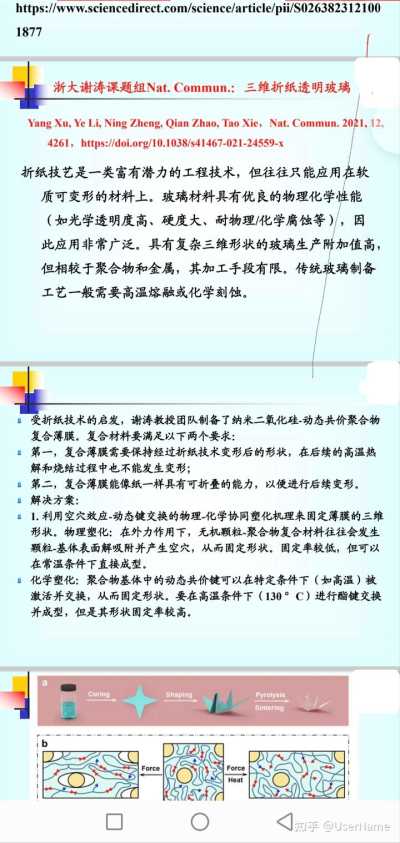
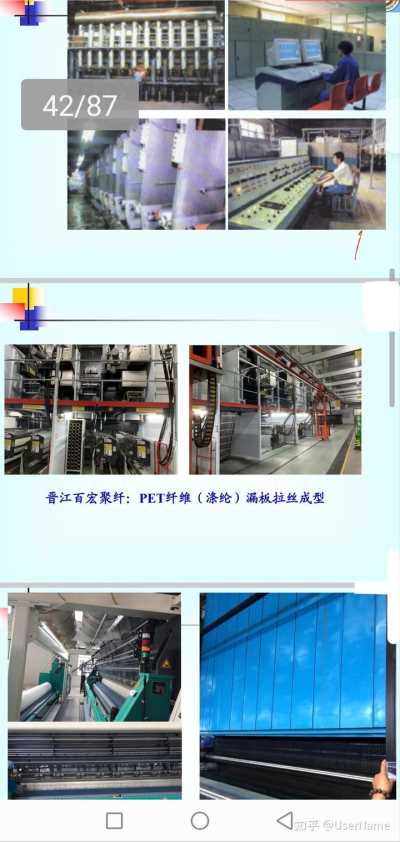
第二章复合材料增强体在复合材料中,粘结在基体内以改进其机械性能的高强度材料称为增强材料。
增强材料有时也称作增强体、增强剂等。增强材料共分为三类:
①纤维及其织物
②颗粒或晶须
③板状
(一)纤维
如,植物纤维:棉花、麻类
动物纤维:丝、毛
矿物纤维:石棉
天然纤维:强度较低
现代复合材料的增强材料:合成纤维
PP用短切纤维
喷射纱短切毡
连续针刺毡
玻璃纤维缝编毡深圳市彬达鑫覆铜板有限公司
bacom.cn
玻璃纤维土工格栅
高速公路隔离带铺设防渗层并填如沙石砾料土工膜斜墙
土工膜铺盖砂砾料
土工膜防渗示意图人工湖铺设防渗层
雁门关隧道在做土工膜防渗层竣工后的雁门关隧道
二、玻璃纤维及其制品
1概述
增强塑料用玻纤占65%,增强沥青材料用玻纤占19%,其余16%为纺织用玻纤细纱
1.1玻璃纤维的发展状况
美国的欧文斯·科宁公司
世界三大玻纤公司<法国圣戈班集团的维托泰克斯玻纤公司
美国PPG公司的玻纤分部
1.2玻璃纤维的分类及成分碱金属氧化物含量
E玻璃(无碱玻璃纤维)中国≤0.5%,国外1%以玻璃原料成分
分类(一般以碱C玻璃(中碱玻璃纤维)
11.5~12.5%
含量区分)A玻璃(高碱含量)
特种玻璃纤如:S纤维(高强度)
维D玻璃(高介电性能)
M玻璃(高弹性模量)
粗纤维:30μm
初级纤维:20μm
以单丝直径分类中级纤维:10μm~20μm
高级纤维:3μm~10μm(亦称纺织纤维)连续纤维(包括无捻粗纱和有捻粗纱)
13/87短切纤维
以纤维外观分类<空心玻璃纤维
玻璃粉
磨细纤维
高强玻纤
高模量玻纤
以纤维特性分类耐高温玻纤
(纤维的性能)耐碱玻纤
耐酸玻纤
普通玻纤(无碱或中碱玻纤)玻璃粉
上海限公司
alibaba.co
无捻粗纱短切纤维
P:01玻璃鲆维的结构写组成:0.0Prs: 5.28Size: 188.02.1玻璃纤维的物态
2.2玻璃纤维的结构
15/87
微晶结构假说认为:玻璃是由硅酸块或二氧化硅的“微晶子”组成,在“微晶子”之间由硅酸块过冷溶液所填充。
网络结构假说认为:玻璃是由二
氧化硅的四面体、铝氧三面体或
硼氧三面体相互连成不规则三维
网络,网络间的空隙由Na、K、
Ca、Mg等阳离子所填充。
二氧化硅四面体的三维网状结0
构是决定玻璃性能的基础,填Na
一
充的Na、Ca等阳离子称为网络Ca.
改性物。Si
2.3玻璃纤维的化学组成
网络形成体二氧化硅三氧化二硼
硅酸盐玻璃硼酸盐玻璃
化学组成助熔剂
氧化钠、氧化钾等碱性氧化物
调整体
(网络外体)氧化钙→降低拉丝温度
改性剂三氧化二铝提高耐水性
玻璃纤国内外常用玻璃纤维的成分
维种类SiO2AI2O3CaOMgOZrO2B2O3Na2O
K2O
无碱1#54.1±0.15.0±0.16.5±0.4.5±9.0±
<0.5
75
5
0.5
0.5
无碱2#54.5±0.13.8±0.16.2±0.4.0±9.0±
<2.0
50.5
0.5
无5#18/879.5±
4.2±11.5±
<0.5
50.5
0.5
0.5
中碱66.84.7
8.5
4.2
3
12
B17
E53.5
16.3
17.3
4.4
8
0~3
C65.0
4
14
3
6
8
S64.3
25.0
10.3
0.3
G-2071.01.0
16.0
2.49
A72.0
0.6
10
2.5
14.2
E—无碱玻璃纤维;C—耐酸;S—高强;G-20抗碱;A—普通有碱3玻璃纤维的性能
3.1玻璃纤维的物理性能
3.1.1外观和密度
纤维名玻璃纤维
称羊毛蚕丝棉花人造丝尼龙碳纤维无碱有碱
密度1.28~1.30~1.50~1.50~2.6~
2.4~
1.141.4
g/cm31.331.451.601.60
2.7
2.6
3.1.2玻璃纤维的力学性能
玻璃纤维的拉伸强度
表7-3几种纤维材料和金属材料的强度
材料高强
羊毛亚麻棉花生丝尼龙铝合金
玻璃玻璃纤维
合金钢
性能
纤维直径(μm)~1516~5010~2018块状块状块状块状5~8
拉伸强度(MPa)100~300350300~700440300~600160040~46020~1201000~3000
性能
纤维直径(μm)~1516~5010~2018块状块状块状块状5~8
拉伸强度(MPa)100~300350300~700440300~600160040~46020~1201000~3000
裂纹假说
玻璃纤维的强度理论聚甲基丙稀酸酯玻璃(即有机玻璃)
中的微裂纹
分子取向假说
影响玻璃纤维强度的主要因素
1)纤维直径和长度
表7-4玻璃纤维直径与拉伸强度的关系
直径(μm)5
7
11
性能
拉伸强度(MPa)3000~38002400~29001750~21501250~17001050~1250
-5玻璃纤维长度与拉伸强度关系
玻璃纤维长度(mm)纤维直径(μm)
平均拉伸强度(MPa)
513
1500
2012.5
1210
9012.7
360
156013
720
玻璃纤维直径对玻璃钢强度的影响
-5玻璃纤维长度与拉伸强度关系
玻璃纤维长度(mm)纤维直径(μm)
平均拉伸强度(MPa)
513
1500
12.51210
23/8712.7
360
156013
720
玻璃纤维直径对玻璃钢强度的影响
单丝直径,树脂含量,玻璃钢的极限强度,MPa
um%
抗拉
抗压
抗弯
5~720~25
480
400
700
12~14470
400
730
16~1725~30
420
375
730
32~35580
470
670
大量的试验表明:
玻璃钢的强度不随所用纤维直径的加粗而显著降低2)化学组成对强度的影响
玻璃纤维纤维直径拉伸强度
/um/MPa
无碱5.01
2000
有碱4.7
1600
含碱量越高—→纤维的强度越低
纤维的表面缺陷对强度影响巨大。如下表所示:
纤维强度与化学组成的关系
品一A玻纤E玻纤
铝硅酸盐玻纤石英玻纤表面缺陷状况
80~15080~15080~15080~150表面有微裂纹
强25/87600~800800~10002000表面有超细微裂纹
20002100
2500
4000
表面有微裂纹
(MPa)3000
3300
5000~6000无缺陷纤维
700022500
理想均匀的玻璃结构
克
3)纤维老化的影响6
5
曲线I:直径6um的无碱玻
璃纤维4
I
曲线II:含17%的Na2O有
碱纤维,2
存放条件:
在空气湿度为60%~65%012
lgt(小时)
4)施加负荷时间对强度的影响玻璃纤维的疲劳一般是指纤维强度随施加负荷时间的增加而降低的情况。
纤维疲劳现象是普遍的,当相对湿度为60~65%时,玻璃纤维在长期张力作用下,都会有很大程度的疲劳。
玻璃纤维的弹性
A.玻璃纤维的延伸率
28/87伸率(又称断裂伸长率)是指纤维在外力作用下直至拉断时的伸长百分率。(见下表)
纤维种类弹性模量(MPa)
延伸率(%)
无碱纤维(E)72000
3.0
有碱纤维(A)66000
2.7
棉纤维10000~12000
7.8
羊毛纤维6000
25~35
亚麻纤维30000~50000
2~3
芳纶纤维3000
20~25
高合金钢160000
铝合金42000~46000
玻璃纤维的延伸率比大多数有机纤维的延伸率低,一般为3%左右。
B.玻璃纤维的弹性模量
玻璃纤维的弹性模量是指在弹性范围内应力和应变关系的比例常数。
它取决于玻璃纤维结构的本身,与直径大小、磨损程度等无关。不同直径的玻璃纤维弹性模量相同,也证明了它们具有近似的分子结构。
表7-8三种典型玻璃纤维的力学性能
纤维种类密度(g/cm3)
拉伸强度(MPa)
弹性模量(GPa)
E-玻璃纤维2.54
3500
72
S玻璃纤维2.44
4700
87
M-玻璃纤维2.89
3700
118
实践证明,加入BeO、MgO能够提高玻纤的弹性模量3)玻璃纤维的耐磨性与耐折性
玻璃纤维的耐磨性是指纤维抵抗磨擦的能力;玻璃纤维的耐折性是指纤维抵抗折断的能力。如:玻璃纤维直径为9um时,其弯曲半径为0.094 mm;而超细纤维直径为3.6um时,其弯曲半径为0.038mm。3.1.3玻璃纤维的热性能
(1)玻璃纤维的导热性
物质容积密度导热系数物质
容积密度导热系数
种类(kg/m3)[W/(m-K)]种类
(kg/m3)
[W/(m·K)]
羊毛80
0.034~0.046
玻璃纤维80
0.034
蚕丝100
0.046~0.052
玻璃0.7~1.3
亚麻130
0.046~0.053
空气0.0246
原棉81
0.058~0.062
水
0.60
(2)玻璃纤维的耐热性
化学成分决定耐热性
软化点550℃-580℃,热膨胀系数4.8×10-6C-1
34/87
高温不燃烧。在200℃~250℃以下时,玻璃纤维强
度不变
与热性能相关的问题?
一般情况下,玻璃的耐压强度是其抗张强度的10倍,
那么玻璃承受急热能力与骤冷能力哪个强?
3.1.4玻璃纤维的电性能
化学组成碱金属离子越多,电绝缘性越差
电导率温度
常温下是绝缘体,在Tg以上是良导体
取决于湿度
湿度增加,电阻率下降
加入氧化铁、氧
化铝、氧化铜、半导体
涂敷金属
氧化铋或氧化矾或石墨
→
导电纤维
https:/http://v.qq.com/x/page/z3142zgk5p5.htmlTencentVideo11 28 7058 0 exe
玻璃高温导电现象
3.2玻璃纤维的化学性能
3.237/87
对玻璃纤维制品的腐蚀机理
以硅酸盐玻璃为例)
只能改变、破坏或溶解玻璃水、潮湿空气、
结构组成中的R2O、RO等网→酸、中性和酸性
络调整剂的物质盐溶液
腐蚀剂不仅对R2O、RO起作用,而
氢氧化物溶液、碳
且也对硅氧骨架起作用的物→酸盐溶液、氢氟酸
质和氟化物溶液、磷
酸和磷酸盐溶液
3.2.2影响玻璃纤维化学稳定性的因素
(1)玻璃纤维的化学成分
(2)玻璃纤维表面情况对化学稳定性影响
1g重2mm厚的玻璃→5.1cm2表面积
1g直径约5μm玻璃纤维 ___3100cm2表面积
直径减小化学稳定性下降
(3)侵蚀介质温度对玻璃纤维化学稳定性的影响在100℃以下,温度每升高10℃,破坏速度增加50%-100%;在以上100℃,破坏作用更剧烈
(4)玻璃纤维的吸湿性
吸湿性:玻璃纤维吸收水分的能力
40/87
玻璃纤维及其制品
玻璃球
.1.1玻璃纤维的生产r艺铂针
(1)坩埚法拉丝工艺君埚
漏板温度1200℃
丝直径3um~-2Uum玻纤原纱
(2)池窑漏极法拉丝工艺超1 秒制题技破璃糟的批国示量程
池客拉丝是国际上普进采用的玻璃纤维生产新工艺,其采用重油或
熬气加热单元窑,粉料直接林化成玻璃,经燃气加热的成型通路,由多台
(数十到上百台)漏扳同时粒制各种规格的玻璃纤维原丝,生产规模大、
效率高、能耗低、产品质量好等,能适应800王4000大漏极粒
要求,是生产高质量、低成本破璃纤维材的最佳方法.
品。鑫m。
~相mpany proile
平1HREHR责万n端EREhn1护电,中a+ianizE.t和ezjia上护严能财网万E=rma年imP可
Cseimn E1逼 m.. 电
fi-EFH·i省i五k.中I工大rHN语立1z.,
★生产工茅理n
a--h概.
一
_-t
工程
r“品用进
度国杆F控伟力一种柱能结和能新职,语工量化京平破开. AR在喜事国名精高重期喜起碍*议评智rt产品和据过也束中事,青为国gP),节通中让.
42/87
晋江百宏聚纤:PET纤维(涂轮)漏扳革丝成型
□1
原丝及玻纤土工网生产
45/87
4.1.2玻璃纤维制品的生产工艺
连续纤堆
(纺织s8浸润m)增强强浸润洲)
· . .
连续纤维毯
.、开、'
t
有0无0
智切纤草
粗纱布表西8
矩f
.tt纤锥毯
特结剂占连续纤 ,感的2~4%
图7-4连续纤维毯生产示意田
1- 电池窑护2-滑板3一 加漫酒剂+一机核装置5$一嗅射粘接剂;6-全展网带1一固化装量8-卷简
4.2玻璃纤维纱的规格及性能
用增强浸润剂,由原纱直接开
无抢纱股、络纱制成
玻璃纤
维纱多用纺织型没润剂,原纱经过退
人bh统、加粘、开股、纱而制成。
48/87
纤维支数表示方法:
1))定质量法是用质量为1g的原纱的长度来表示,即:纤维长度(通常用100m测量)
纤维支数纤维质量(100m原纱克质量毅)
2)定长法 1000m长原纱的克质量
目前国际上统一使用的方法,通称 “Tex”(公制号数).
如:4Tex表示1000m 原纱质量4g
抢度
单位长度内纤维与纤维之间所加的转效,以Vm为单位
7拾(左抢),顺时针方向加栓;
S(右),逆时针方向加t。
作业
1.为什么玻璃纤维的拉仲强度比同成分的块状玻璃高?
2.影响玻璃纤维强度的因素有哪些?如何影响?解原因。
4.3玻璃纤维及玻璃纤维制品
1)无抢粗纱
无粘粗纱是由平行原
丝或平行单丝集束而成。
无拾粗是加工方格布、
网格布的基本原料,是
玻璃钢基材最基本的原
材料。
种类
“喷射用无拾粗纱,缠绕型无拾粗纱,拉挤用无拾粗纱及织造用无粗纱等,用途十分广泛。
2)无破布
无破布是用无破玻纤纱织
造而影, 真有优学的也气绝
练性 R割 /Q7对春进及
我b3/ o于产备
种也地练会,A派,单刺线路
版、各种车辆车体、贮罐、
船粳、i头夺
无破布还造合用作玻璃漆
布,玻璃布层压制品与覆铜
名层压的基材,以及玻璃云
母制品等的补强材料。
短切玻璃纤维
粒切玻璃纤维,适应于各种不同的用途。采用适当的浸润剂和集束数,切成不同长度的玻璃纤维,在热国性,热塑性树脂增强材料中获得广泛的应用。
55/87
4)无抢方格布
以无拾粗纱织成的方格布,广泛应用于手糊玻璃铜(FRP)品领域。
5)玻纤维耐破网
玻璃纤维耐破网布是以中破
成无破玻璃纤维织物为基础,
经耐减涂层处理而成。该产品
虽度高、粘结性好、服粘性、
定位性极佳,广泛应用于墙体
增强,外播保湿,虚面防水等
方面,还可应用于水泥、塾料
万骨、大理石、马赛克导墙体
材料的增强,是建统行业理想
的工程材料。
6)膨体纱与膨体布
膨体纱由玻璃纤维纱经过高压空气获置,特殊膨化而成,该产品兼有连续长纤维的高强度,又有短切纤维的连松性,具有耐高温、耐腐蚀、高过浪效果、高强度等特点,被广泛应用于过浪布、表饰布、绝缘织物等,是石棉制品理想的替代材料,在环保工业方面应用广泛,
廖体布是由膨体纱制造而成,具有透气性好,客量大、过浪效率高等特点。主要用于钢铁、水泥、发电等行业的高温袋过滤器;包表材料; 表饰材料等.
7)拉挤纱
具有良好的耐磨性、柔
软成性好、纤维光滑毛
吵、与革U有极好的相
容性,没透速度非常快。
通过拉挤成型与聚酷或环
氧树脂结合成高强度的玻
璃钢制品.
60/87卷求量
严品没润剂类含水率选用
昂名代号
树脂
型(9)
%
ERL-
无碱扛挤纱硅烧类
< 0.18最醋或环氧20) ± 0.5
1200
ERL-
无破粒挤硅烧类
莱醋或环氧
≤0.1820 ± 0.5
2400
CRL-
中破粒挤纱硅烧类
聚酷或环氧
≤0.220 ± 0.5
1200
CRL-
中碱粒挤纱<0.2
秉苗或环氧
硅烧类20 ± 0.5
2400
8)缠绕纱
具有较好的成带性、柔软、纤锥光滑、与笨乙师有很好的相容性、浸透速度快。制成的玻璃钢耐水性奸.通过管道缠绕成型与秉醋或环氧树脂结合成高强度的玻璃钢制品。
品没洞剂类选用
卷表量
品名含水率%
代号树脂
(Kg)
业蹈或环
ERC.
无碱缠绕硅烧类
≤0.1820 ±0.5
纱1200
氧
秉或环
ERC.
无破缠统硅类
<0.1820 ±0.5
纱2400
氧
CRC-
中碱缠统莱蹈或环
硅烧类<0.220 ± 0.5
纱2400
具有较好的短切性能
无普电、与革乙 有良好
的相落性、浸透速度较快。
通过连续喷射法与莱酷或
63/ 87 猛度
10)玻璃纤维委管
玻璃纤维套管是由无减纱编织而成,用于电视、仪表无线电、电视机、电扇及其他家用电器上.应用玻璃纤维套管的电鲯和电纯能提供良好的性能和可靠的绝缘.
11)短切毡
把玻璃纤维短切成约50mm长,然后均匀沉降在成型带上,并软上特种粘结剂形成短切色,它具有各向同性与树脂结合良好的和性,脱泡性、易成型等特点,广泛使用于手糊玻璃钢(FRP)及玻纤县压极材上.
12) 迁续原丝构
连续原丝愁是新型玻纤无纺增强材料,广泛用于高质量玻璃
钢的模压和粒挤m型工艺.该技术以玻璃纤维原丝为原料,经机●
赫特m朴端青恐废天劳施,产品规格为225 -~900克平方来
66/87
13)玻纤维方格布
玻璃纤维方格布具有高强、耐腐、绝簿等特点。是制造玻璃钢制品基布。泛应用于仪表、无线电脑精建筑构件、制造游艇、汽车体、透明玻璃钢及子糊玻璃铜工艺上.
14 )无破纤维带
无破破璃纤维带是电机及电器的良好的色扎绝填材料,已是玻璃钢(FRP)用基材。<1
68/87
7.5玻璃纤维的表面处理
单丝处理剂亦称浸润剂
单丝处理
玻纤的表纤维和织物的表
面t理其处理剂亦称中
面处理间粘合剂
7.5.1浸润剂粘结作用
浸润剂的作用护作用
7.1.2没润剂的种类
(1)纺织型没润剂
粉浸润剂受用低、威膜奸、客易除样,应用广泛
纺织型浸润剂-问滑性、集束性好
石蜡乳剂
(2)增强型没润剂
中间粘合剂(偶联剂)
增强型浸润剂润滑剂
乳化剂
414型( 与酚苍、环氧粘合强)
7001型(与聚酷粘合力强)
7.2玻璃纤维表面处理剂
7.5.2.1表面处理的意义
"71/87200
100200u
3000
时间(年)1o00
时(h)
田7-5处理剂对聚音孩璃自然田7-6 处理剂对聚留教鞘锅人工
哪稻后投度的影响气快老化强度的影响
1-沃兰处理2-A-l151处理;-认三处上12-A-151处理)
3- A+172处理4=来处理w..3-A-l72 处理4-来处理
oo‘.-
t时间(年)
图7-7 处理剂对聚音玻璃海水
浸泡后强度的影响
1一沃兰处理2=A151处理
●T3=A-1z处理+=来处理
.+
7.5.2.2界面理论
解玻璃树脂界面的理论:
偶联理论、化学处理膜理论、物理吸附理论等,冬种理论均存在一些不尽完善之处.
偶联理论:
7.2.3玻璃纤维表面处理剂的种类
(有机硅R.->on4n
7.5.2.3我璃纤维表面处理剂的种类
有机硅R.>A4n
有机备
玻璃纤维表面处理剂饮酸脂
73/87
Table I: Thefect of silnes to the bending strength
of glass fiber reinforced polypropylene
Irealmentiructure of
Bending strength
ncreased
condition(MPa)
(%)
slanes
untreaimnenl47.4
—f
K-570Hy-coo(CHh-5i(OCH)},
1.6
S6.2
KH-S60HOHOctahsfoCHbh
27.2
603
KHl-50NH4(C-hs-(OCHh)
63.1
33.0
B301是一种有机格偶联剂,具有知下的结构:
HO IH040 Q1+
H0 o IOIBO HO HO
用B301处理玻纤增强的P,其弯曲强度如表
Thble 2 The eflet of B301 to the bendingstengthof rhihfored PP
TreatmentB-ending strength
Increased
(MPa)(%)
onafition7.4
Untreatmenl“t..
94253
E3011.2
B301+S18Ss0.2
7.3玻璃纤维表面处理方法
□O
后处理法、前处理法和迁移法
7.3.1后t理法
7k /Q7一种方法,所以又叫普通处理法.此法分网步过行:
首先除去玻璃纤维表面的纺织型浸润剂,
然后经处理剂落液没清、水洗、洪干等工艺,使玻璃纤维表面被覆上一层处理剂。
7.5.3.2前处理法
将化学处理剂加入到浸润剂中,即为增强型浸润剂,这
样,在拉丝的过程中处理剂就被覆到玻璃纤维表面上.用这种被覆了增强型浸润剂的纤维织成的布叫做前处理
布。这种玻璃纤维及织物制作玻璃钢时可直接使用。7.5.3.3迁移法
即将化学处理剂直接和入到树脂胶液中进行整体渗合,在浸胶的同时将处理剂施于玻璃纤维上,借处理剂从树脂肢液至纤维表面的“迁移”作用而与纤维表面而发生作用,从而在树脂国化过程中产生偶联作用。此法也叫港处理法。
作业
1.为何玻璃纤维要使用浸润剂?
2.玻璃纤维表面处理方法有哪些?各有什么特点。
玻纤聚合物复合材料制备新工艺
北化大黄明印副教授《'Thin-Walld Structures》 : 3D)打印连
续玻璃纤维增强聚乳酸复合材料
SD打印技术,是一种无需复杂模具和频繁人工操作的快速威型技术,目前广泛采用的熔秧沉积成型(DN/)3D打中技术,多使用绝树辟或短纤增强树黯为打印原材料
林融浸清法制务高纤维舍量(4Swt%以上) 的连续玻璃纤维增强聚乳酸(CGFPLA)预没丝,将其作为打即耗材。
连续纤维增强热塑性3D打印丝材制备设备
使用自行设计的林融浸清设备,对连续玻璃纤维束进行充分浸清并制备成lmm 直径的预浸丝,将其作为打印耗材用于自行改装的FDM 3D打印机。
(a)Cooling
Forming die
PreheatingImpregnation rollerDrawing device
()CGF/PLA filament
Glass fiberRolling-up device
Impregnating
Extruder
(b)KTT
3D Printing
(c)
Mechanical properties test3D printed products with CGF/PLA composites
Testing samples
图2.CGF/PLA复合材料3D打印制备与测试示意图
(a)IV
m
(b)3000000000
IV
(c)(d)
380Flexural strength
360Tesesteg
Fiber contents15
(edwd
Additives
Mould temperature
Drawing rateContact angle
200
354050
5560
Fiber contents(wt%)
图3.CGF/PLA预浸丝制备示意图及不同纤维含量对其机械性能的影响
增加预浸丝的纤维含量能有效地提高打印制品的机械性能,
纤维45wt%时性能优。
CGF/PLA复材打印制品弯曲强度和模量:313MP和21.5GPa,
高于使用单一物料或使用短纤增强的FDM 3D打印制品
相对于在打印喷头内部对连续纤维进行浸渍然后直接打印的
制品,其显著提高树脂对连续纤维束的浸渍程度,提升制品
的机械性能。
原文链接:
https:/http://www.sciencedirect.com/science/article/pii/S026382312100
1877浙大谢涛课题组Nat. Commun.: 三维折纸透明玻璃
Yang Xu, Ye Li, Ning Zheng, Qian Zhao, Tao Xie, Nat. Commun. 2021, 12,
4261, https:/http://doi.org/10.1038/s41467-021-24559-x
折纸技艺是一类富有潜力的工程技术,但往往只能应用在软
质可变形的材料上。玻璃材料具有优良的物理化学性能
(如光学透明度高、硬度大、耐物理/化学腐蚀等)/,因
此应用非常广泛。具有复杂三维形状的玻璃生产附加值高,
但相较于聚合物和金属,其加工手段有限。传统玻璃制备
工艺一般需要高温熔融或化学刻蚀。
受折纸技术的启发,谢涛教授团队制备了纳米二氧化硅-动态共价聚合物
复合薄膜。复合材料要满足以下两个要求:
第一,复合薄膜需要保持经过折纸技术变形后的形状,在后续的高温热
解和烧结过程中也不能发生变形;
第二,复合薄膜能像纸一样具有可折叠的能力,以便进行后续变形。
解决方案:
1.利用空穴效应-动态键交换的物理-化学协同塑化机理来固定薄膜的三维
形状。物理塑化:在外力作用下,无机颗粒-聚合物复合材料往往会发生
颗粒-基体表面解吸附并产生空穴,从而固定形状。固定率较低,但可以
在常温条件下直接成型。
化学塑化:聚合物基体中的动态共价键可以在特定条件下(如高温)被
激活并交换,从而固定形状。要在高温条件下(130°C)进行酯键交换
并成型,但是其形状固定率较高。
aCuring
Shaping
Pyrolysis
Sintering
bForce
Force
Heat
复合材料
第四章聚合物基复合材料
1、环氧树脂:是一种分子中含有两个或两个以上活性环氧基团的高分子化合物。粘附力强(树脂中含有极性的醚键和羟基酸、碱对固化反应起促进作用)、已固化的树脂有良好的压缩性能,良好的耐水、耐化学介质和耐烧蚀性能,良好的尺寸稳定性和耐久性。2、聚酰亚胺树脂PI:是一类耐高温树脂,它通常有热固性(不熔性)和热塑性两类。3、聚酯树脂与环氧、酚树脂相比:①工艺性良好,室温下固化,常压下成型,工艺装置简单;②聚酯树脂固化后综合性能良好,力学性能不如酚醛树脂或环氧树脂;③固化过程中无挥发物逸出,制品的致密性好:④价格比环氧树脂低得多,只比酚醛树脂略贵一些;⑤不饱和聚酯树脂的缺点是固化时体积收缩率大、耐热性差等,主要用于一般民用工业和生活用
品中。
4、聚合物原材料设计选择原则:①比强度、比刚度高原则,②材料与结构的使用环境相适应的原则,③满足结构特殊性要求的原则,④满足工艺性要求的原则,⑤成本低、效益高的原则。
5、RTM成型法:是一种树脂注入成型法。
制造工艺主要分五步:①增强纤维的预成型片材的制作:②将纤维的预成型片材铺设在模型中;③给模型加压,使铺设的纤维的预成型片材在模型内按产品形状预成型:④利用低压将树脂注入模型,使树脂均匀地渗透到纤维的预成型片材中;⑤在模型内加热固化。
RTM优点:成本低,质量高,产品尺寸形状稳定,可以适应多种固化树脂和热塑性树脂,也可以两种以上的不同增强纤维的组合复合材料的成型,还可以适应多种二维编织和三维编制的复合材料制品的成型。
第五章金属基复合材料的制造方法
1、固态法:是指在金属基复合材料中基体处于固态下制造金属基复合材料的方法;包括:
1)粉末冶金法:是用于制备与成型非连续增强型金属基复合材料的一种传统的固
态工艺法。它既可适用于连续、长纤维增强.又可用于短纤维、颗粒或晶须增强的金属基复合材料。
优点:①增强材料与基体金属粉末以任何比例混合:②对增强材料与基体互相湿润的要求不高,使颗粒或晶须均匀分布在金属基复合材料的基体中:③采用热等静压工艺时,一般不会产生偏聚等缺陷;④可进行二次加工,得到所需形状的复合材料部件的毛坯。缺点:①工艺过程比较复杂;②制备铝基复合材料时,防止铝粉爆炸。
2)固态扩散结合法:是将固态的纤维与金属适当地组合,在加压、加热条件下使它们相互扩散结合成复合材料的方法。包括热压扩散法、热等静压法、热轧法、热拉和热挤压。
其中热压扩散法三个关键步骤:①纤维的排布;②复合材料的叠合和真空封装;③热压(最关键)。为了保证性能符合要求,热压过程中要控制好热压工艺参数(热压温度、压力和时间)。
2、液态法:是指在金属基复合材料的制造过程中,金属基体处于熔融状态下与固体增强物复合的方法。包括铸造法、熔铸复合法、熔融金属浸渗法、真空压力、浸渍法、喷射沉积法。与固态法相比,液态法的工艺及设备相对简便易行;
1)铸造法包括高压凝固铸造法、真空吸铸法、搅拌铸造法、压力铸造法。
压力铸造法:指在压力的作用下,将液态或半液态金属基复合材料(或金属)以一定速度充填压铸模型腔或增强材料预制体的空隙中,在压力下快速凝固成型而制备金属基复合材料,包括浇入、加压、固化和顶出。
2)喷射沉积法:是一种将金属熔体与增强颗粒在惰性气体的推动下,通过快速凝固制备颗粒增强金属基复合材料的方法。
第六章陶瓷基复合材料
1、陶瓷基体的分类(按组成化合物的元素)
氧化物陶瓷基体:氧化铝陶瓷基体,氧化锆陶瓷基体,莫来石陶瓷基体
碳化物陶瓷基体:碳化硅陶瓷基体,碳化硼陶瓷基体
氮化物陶瓷基体:氮化硅陶瓷基体,氮化硼陶瓷基体
2、陶瓷基复合材料存在的界面:①机械结合,②溶解和润湿结合,③反应结合,④混合结合。
3、陶瓷基复合材料成型加工技术
1)热压烧结成型法(常用):松使散的或成型的陶瓷基复合材料混合物在高温下,
通过外加的压力纵向(单轴)加压使其致密化的成型方法。
热压烧结法主要工艺流程:纤维处理→料浆浸渗→缠绕成布→制作预制片→层叠成型→热压烧结
该方法的优点:①与无压烧结相比,能降低烧结温度,延长保湿时间,得到较细的品粒;②获得高致密度,高性能的复合材料;③材料性能重复性好,使用可靠,控制热压模具的尺寸精度可以减少材料的加工余量;
该方法的缺点:①只能制作形状简单的零件:②模具的消耗大,一次只能单件或者少件烧结,成本较高;③由于热压力的方向性,材料性能有方向性,垂直于热压方向的强度往往比平行于热压方向的强度要大一些。
2)直接氧化法:由液态浸渍法演变而来,利用熔融金属直接与氧化反应制备陶瓷锦复合材料的工艺方法,在融化金属的表面形成所需的反应产物。
3)高聚物先驱体热解成型法(又称热解法):通过对高聚物先驱体进行热解,直接获取块体陶瓷材料的方法。
4)化学气相沉积成型法(CVD法):使用化学气相沉积技术,在颗粒,纤维,晶
须及其他具有开口气孔的增强骨架上沉积所需陶瓷基质制备陶瓷基复合材料。
第七章水泥基复合材料
1、水泥基复合材料分类:纤维增强水泥基复合材料:聚合物混凝土复合材料(聚合物混凝土、聚合物浸渍混凝土、聚合物改性混凝土)
2、聚合物浸渍混凝土:是一种用单体浸渍混凝土表层的空隙,并经处理而成一整体的有机一无机复合的新型材料;(聚合物功能:黏结和填充砼中空隙和裂缝;浸渍液功能:
①对裂缝的黏结作用消除裂隙尖端的应力集中;②增加砼密实性:③形成一个连续网状结构;)
3、聚合物改性混凝土:将聚合物乳液掺入新拌混凝土中,可使混凝土的性能得到明显的改善的材料。
第八章先进复合材料
1碳/碳复合材料:是由碳纤维(或石墨纤维)为增强体,以碳(或石墨)为基体的复合材料,是具有特殊性能的新型工程材料,也称碳纤维增强碳复合材料(完全由碳元素组成,能够承受极高的温度和极大的加热速率)。
2、功能复合材料定义:是指除力学性能以外还提供其他物理性能并包括部分化学和生物性能的复合材料,如导电、超导、半导等功能。
第九章材料复合新技术
1、原位复合技术:来源于原位结晶和原位聚合概念,材料中的第二相或复合材料中的增强相生成于材料的形成过程中,既不是在材料制备之前就有,而是在材料制备过程中原位就地产生。
2、自蔓延复合技术:在自蔓延高温合成(利用配合的原料自身的燃烧反应放出的热量,使化学反应过程自发进行,进而获得具有指定成分和结构产物的一种新型材料合成手段)的基础上发展起来的一种新的复合技术,主要用于制备金属/金属、金属/陶瓷、陶瓷/陶瓷系复合粉末和块体复合材料。
3、自蔓延复合技术的特点:①工艺设备简单,工艺周期短,生产效率高:②能耗低,物耗低;③合成过程中极高的温度可对产物进行自纯化,同时,极快的升温和降温速度可获得非平衡结构的产物,因此产品质量良好。
摘要:树脂基复合材料具有比强度高、比模量高、抗疲劳性能优良、工艺性能良好及具有可设计性等特点,一直受
到工业界的重视,各种复合材料产品被应用到各行各业,尤其是在航空航天领域。复合材料从原材料到形成制品的
过程,都需经过固化与成型,方法已经有几十种。文中介绍了国内外复合材料主要的基体固化方法、成型工艺和相
关研究:固化方法主要有热固化、辐射固化与微波固化等、成型工艺主要有模压成型、渗透成型、缠绕成型与拉挤成
型等:同时,对工艺研究与应用也进行了展望。
关键词:复合材料:基体固化:成型工艺
中图分类号:TQ322.4:TB332文献标识码:A
文章编号:1671-8798(2008)04-0269-05
Review of matrix solidification and forming processes of
composite materials
ZHU Ai-shi', ZHEN G Chuan-xiang', CHEN G Zhong
(1. School of Biological and Chemical Engineering , Zhejiang University of Science and Technology , Hangzhou 310023,China; 2. College of Materials Science and Chemical Engineering, Zhejiang University, Hangzhou 310027, China)
Abstract: Resin matrix composite materials have characteristics such as high strength ratio and
modulus ratio, good anti-fatigue properties and technology performance, able to design and so on.
In the industrial it has always been attached importance. Various composite materials products
have been applied to all walks of life , especially the aerospace field. The process from raw material
to create products of composite materials need all to cure and form. The ways of curing and form
ing have been dozens. We introduce major matrix solidification methods and forming processes of
composite materials domestic and foreign , and related researches. Solidification methods mainly in-
clude heat-curing, radiation-curing and microwave-curing. Forming processes mainly include die
pressing forming, penetration forming , winding forming, draw and wring forming. The prospect
of processes research and application are described.
Key words: composite materials; matrix solidification; forming technique
复合材料的发展带动了材料应用领域的革命1-002
复合材料质轻,比强度、比模量高,耐高温,抗化学腐80C
蚀,耐疲劳,易于整体成型、导电、传热等,被广泛用I
于制作导弹、火箭、飞机和人造卫星结构件,电子电
力产品、运动器械、潜水外压容器、高压管道、化工防02
腐、密封、电磁屏蔽、建筑补强等军民用领域。随着
近年来复合材料特别是碳纤维性价比的提高,及复(102)C3(102)C
合材料成型制造技术的发展,复合材料耐压容器在
导弹发动机、卫星储箱、交通运输(高压气瓶)、自救图1固化工艺参数例
呼吸装置、潜水等方面的发展前景十分乐观。Fig. 1 The example of solidification process parameters
这一固化工艺过程,有2个温度折点(俗称2个
经过半个多世纪的发展,复合材料固化成型方台阶),开始操作前首先要看清工艺,该加温时加温,
法已经有几十种,每种工艺都有各自的优缺点,有各该保温时要保温,尤其是在将至折点时更要特别留
自的适用范围,但是它们之间存在着共性,从原材料意,否则一旦超温,对产品质量不利。
到形成制品的过程,都需经过固化与成型工艺。本
文介绍了国内外复合材料主要的固化方法、成型工1.2辐射固化
辐射源很多,如αββy和中子射线。主要
艺,并对其研究与应用进行了展望。的辐射固化(radiation curing)有电子束固化(EB)和
1复合材料基体固化紫外线固化(UV)2种。
高性能复合材料如碳纤维环氧复合材料的固化1.2.1电子束固化即高能量电子束碰撞目标分
子,释放足够的能量使其产生一系列活泼的粒子,当
过程是基体材料从液态变为固态的过程,这个过程邻近分子发生这一过程时,活泼粒子释放出能量,形
是一个复杂的热、化学和力学性能急剧变化的过程成化学键。电子束固化可使聚合物体系性能如模
由于热效应和化学反应效应会导致残余应力和变形量、强度、冲击强度、硬度、耐热性及抗冲击、抗蠕变
产生,因此复合材料基体的固化相当重要。等都会有一定程度的提高。
1.1传统的热固化常用的电子加速器有:高压加速器(电子静电加
按固化温度可分为室温固化(25C左右)、中速器、高频高压发生器、绝缘磁心[共振]变压器
温固化(125C左右)和高温固化(175C左
右)3种。[ICT]、直线加速器、回旋加速器、脉冲加速器和电
子帘加速器等。辐射固化本身并不是成型工艺仅
热固化时热量由材料外部向内部传递,因此材辅助成型工艺起固化作用而已。
料内部存在温度梯度,造成沿厚度方向上的固化度法国宇航公司采用EB固化了直径4m、长10m
不同,使树脂固化很难均匀和完全,易产生较大内应的FRP制品,固化周期约为热压釜工艺的1/10。
力,并且固化速度慢、周期长。我国辐射固化研发较晚,数量也少。吕智等研究
复合材料的固化过程就是将预制件放入烘箱了双马来酰亚胺树脂及其碳纤维复合材料EB固
(或热压机或热压罐)中对预制构件进行加热和加压化;刘玉文等研究了碳纤维在电子束辐射过程中
的过程,是热固性树脂与纤维结合,形成复合材料结对树脂基复合材料界面性能的影响,发现PAN基
构件的过程。但是要想得到质量好的复合材料结构碳纤维在电子束辐射过程中发生界面性能较低,但
件,必须选择最佳的固化工艺参数工艺参数主要碳纤维表面涂层能改善电子束固化复合材料的界面
指温度、压力及加压点、升降温速率和保温时间等。
可以利用示差扫描量热法(DSC)对树脂在固化过性能。
1.2.2光固化运用光敏树脂浸渍纤维增强材料
程中的反应历程及其树脂的流变学性能黏度变化进制成柔性预浸料修理补片,用黏结的方法贴补到破
行分析来加以确定。温度分为烘箱(或热压机或热坏损伤区,在紫外光的照射下迅速固化,从而在短时
压罐)温度与模具温度,前者与后者之间要注意温间内完成结构的修补1。
差,以50~60C为宜,升降温速率一般选0.5~1.3微波固化
1.5Cmin,图1是一个典型的工艺过程。微波是频率为109~1011Hz的电磁波,其固
化机理是极性物质在外加电磁场的作用下,内部介空树脂传递模塑(VRTM)、结构反应注射成型
质极化产生的极化强度矢量落后于电场一个角度(SRTM)、射频干扰(RFI)和西曼树脂浸渍模塑工
导致与电场相同的电流产生,构成物质内部功率耗艺(SCRIMP)等。它们的共同特点是:一般情况下
散,从而将微波能转化为热能,致使固化体系快速均可不采用热压罐;仅真空压或低外压;要求树脂有低
匀升温而加速反应。的黏度:制造周期短;不用预浸料;劳动工时少:辅助
微波加热属于“分子内”加热,不像热固化存在材料消耗少;边角料少,结构整体性高。
温度梯度,微波能以快速、独特的加热方式对固化树RTM、VRTM和SRTM适于复杂型面三维结
脂结构和性能有较大影响6构的整体成型,因而模具数量、铺层工时、零件数目
Prasad研究了热固化与微波固化对环氧力和机械装配量都可大幅度节省,成本显著下降。
学性能的影响,分别使用R2512、R2515、R2516三RFI是一种树脂沿结构件厚度方向由下至上的渗透
种环氧和H2403、H2409固化剂,进行热固化与微方法,它的渗透距离较近,因而可采用常温下为高黏
波固化。结果表明,微波固化物有较高的T。度(如2~10Pa·s)的树脂体系。SCRIMP仅需单
Zhou用微波和加热对E244/马来酸酐体系固化面模,另一面为真空袋,借助真空吸力,利用特殊网
进行了研究,发现微波固化浇铸体的力学性能优于布作为介质.将树脂吸入预先铺好的纤维编织物
热固化,固化活化能减少,固化温度降低,固化时间中。高峰等针对耐高温的PMR-15型聚酰亚
及固化剂用量均比热固化少,并从理论和实验上分胺树脂BMP-316为基体材料、M46J碳纤维为增强
析了原因。Zainol对双马树脂热固化和微波固化材料的复合材料RTM成型工艺,研究了它的亚胺
进行了比较研究,发现在微波场中树脂固化较热固化和固化工艺,尤其是固化过程中的压力控制:对
化快,在固化度较高时热固化试样T较微波固化M46J/BMP-316层合板和NOL环进行了常温和高
试样高;在固化度较低时,两者相近。Rahmat用温力学性能以及相关物理性能的测试:对碳纤维/聚
不饱和聚酯微波固化,发现微波固化树脂反应速率酰亚胺复合材料M46J/BMP-316的性质作出一定
远比热固化快然而剪切模量、数均分子量、弯曲模的评价。王芳对3种配方的真空辅助传递模塑
量和强度并没有明显差异。工艺用环氧树脂,采用动态升温DSC实验,升温速
率分别为5、10、15min,引入Kissinger理论,确
2复合材料成型工艺定了树脂体系的表观活化能分别为4.32、5.57、
2.1模压成型工艺3.49kJ/mol;利用外推法,确定了参考固化工艺
模压成型的基本过程是将一定量的经过预处理温度。
的模压料放入预热的压模内.施加较高的压力使模2.3缠绕成型工艺
压料充满模腔,在预定的温度条件下,模压料在模腔第一个纤维缠绕技术专利于1946年在美国注
内逐渐固化,然后将制品从压模中取出,再进行必要册,即固体火箭发动机壳体和压力容器开发系统研
的辅助加工。模压成型工艺的优点是生产效率高、究。此后,发动机壳体、压力容器、飞机雷达罩、导弹
制品尺寸准确、表面光洁,适用于大批量生产:结构头锥、鱼雷发射管及玻璃钢制品等都应用该项专制。
复杂的制品可以一次成型,无需有损于制品性能的缠绕成型工艺已历经半个世纪的发展,经过了从纤
辅助加工(如车、铣、刨、磨、钳等),制品的外观及尺维缠绕、纤维铺放和带缠绕的发展过程,成为聚合物
寸的重复性好。主要缺点是模具设计与制造复杂基复合材料制造的重要手段之一。从航空航天用的
初次投资较高,易受设备限制,一般只限于中小型制固体火箭发动机壳体到民用的玻璃钢管、储罐都有
品的批量生产。近几年来,以长短纤维为增强材料,缠绕成型制品在广泛采用。20世纪90年代以来,
以热塑性、热固性树脂为基体材料的各类复合材料应用发展速度更是明显加快,特别是在气瓶上的
模压成型工艺发展很快,产品性能价格比高,污染环应用。
境少,生产率高,正在不断适应汽车、航空航天、通讯缠绕成型工艺的原理是将经过浸胶的连续纤
等工业化的需求。维、布带等增强材料,按照一定规律缠绕到芯模上,
2.2渗透成型技术然后固化成型。它适合于圆形、锥管、方管等回旋型
渗透成型技术包括:树脂传递模塑(RTM)、真结构件。与其他成型法相比,用缠绕工艺获得的复
合材料制品具有下述特点:纤维伸直和按规律方向束性能评价结果表明各项性能指标都达到设计要
排列的整齐和准确率高,制品能充分发挥纤维的强求。于运花等通过优化的乙烯基醋树脂配方体
度,因此比刚度和比强度均较高。王晓洁等研究系,采用拉挤成型工艺制备出了力学性能优良的碳
了碳纤维增强复合材料用湿法缠绕成型工艺、基体纤维/乙烯基醋树脂复合材料,其力学性能较模压复
配方的性能和使用期:碳纤维增强复合材料容器特合材料有较大提高。
性系数(PV/W)均大于34km,纤维强度转化率达复合材料结构件成型方法还有
到82%以上。何钦象等针对诸如环形气瓶等圆1)真空袋(膜)法:内部抽真空,使之与结构件紧
环状压力容器的缠绕,提出同时满足结构特性和缠密贴合,然后入加热器固化;
绕工艺性的参数设计方法以符合实际工程需要。2)手糊法:适用于面积大而形状复杂的制品,操
纤维自动铺放技术是20世纪90年代复合材料作方法简单,把浸胶后的胶布按规定的铺层方式铺
随着自动控制技术的引入和发展,纤维缠绕发展为设在模具上加热固化。
纤维铺放。纤维铺放过程是把多团预浸纱束集合成以上几种方法也可混合使用,如模压方法加工
准直的带状纱布并铺放到芯模或模具表面,其制品的构件再用真空薄膜密封后加热固化,以及先用手
形状不限于回转体制品的形状曲率变化可以更大糊方法制成蒙皮,后与蜂窝芯贴合,再用真空袋封装
还可用于某些有凹形表面制品的生产。后固化制成蜂窝夹层结构件产品等。
为适应航天结构提出的高性能要求,在纤维缠
绕技术的基础上发展了带缠绕技术。带缠绕技术的3展望
基本原理和所用原材料是湿法螺旋缠绕和预浸带平21世纪初,国外生产应用的复合材料中90%以
面缠绕的有机结合。美国通用动力公司发明了新的上是树脂基复合材料,树脂基复合材料的自动化铺
成型工艺带缠绕,并在1990年获得了专利设技术、压注成型技术、树脂转移模塑工艺、柔型树
权。脂转移模塑技术、智能挤压树脂转移模塑技术、纤维
2.4拉挤成型工艺自动缠绕技术等将是发展和应用的重要技术。
复合材料的拉挤成型工艺是将已浸润树脂胶液复合材料结构件制造技术正朝开发非热压罐成
的连续纤维束或带,在牵引结构拉力作用下,通过成型技术(如电子束固化技术)、扩大整体成型技术特
型模成型,在模中或在固化炉进行固化,连续引拔出别是大型整体构件成型技术,发展快速固化技术、辅
长度不受限制的复合材料型材。由于在成型过程中机柔性制造技术采用光导纤维技术检测构件,实现
需经过成型模的挤压和外牵引拉拔,而且生产过程复合材料构件生产自动化、计算机无损检测在线监
和制品长度是连续的,故又称为拉挤连续成型工测促使复合材料制造技术向智能化、自动化方向发
艺。拉挤成型工艺具有生产效率高、工艺易于展:同时相关技术的机理、设备、树脂与固化剂的开
控制、产品质量稳定等优点;而且拉挤制品中纤维按发也是研究的重点。可以肯定,随着研究的深入和
纵向布置,又是在引拔预张力下成型,因此纤维的单技术的开发成熟,复合材料结构件,特别是高压容器
向强度得到了充分的发挥,制品具有高的拉伸强度将会被应用到更广泛的军事与民用领域。
和弯曲强度。拉挤成型工艺的缺点是:制品性能具
有明显的方向性,其横向强度差,只限于生产型材,参考文献:
且设备复杂,对各工序必须严格准确控制,生产不能[1]高峰,李勇,肖军,等.M46J/BMP-316复合材料的成型
轻易中断。工艺及其性能[J].纤维复合材料,2005(4):3-6.
拉挤成型工艺要求所用的树脂黏度低。大量使[2]赵鸿汉.环氧基纤维增强复合材料应用面面观[J].玻璃纤维,2006(1):42-46.
用不饱和聚醋树脂,其次是环氧树脂或其他改性的王晓洁,张炜,刘炳禹.高性能碳纤维复合材料耐压容
环氧树脂。[3]
器研究进展[].宇航材料工艺,2003(4):20-23.
从1985年我国引入第一套拉挤机开始,经过持[4]宁保江,宁荣昌.一种新型环氧树脂室温固化体系研究
续不断的拉挤技术研究,我国的技术水平明显提高。[J].火炸药学报,2006,29(1):62-64.
我国承建的伊朗德黑兰地铁工程,其接触轨保护罩[5]邓杰,刘建超.复合材料用中温固化环氧树脂体系的研
采用了拉挤成型技术,经近一年的工作,研制已经结究[J].化学与粘合2004(6):314-316.
[6]乌云其其格,廖子龙.中温固化树脂/碳布复合材料工Technology and the Mechanical Properties of the Mi-
艺性能研究[J].航空材料学报,2006,26(5):65-69.crowave Processing of Polymer[J ]. Journal of Mate-
[7]张春华,韩冰,黄玉东.TDE-85/芳香胺树脂基体及碳rial Process Technolgy,2003,137(1-3): 156-158.
纤维复合材料性能[J].哈尔滨理工大学学报,2000,5[19]
ZAINOL I,DAY R, HEATLEY F. Comparison be-
(5):60-63.tween the Thermal and Microwave Curing of Bismale-
[8] JIN Ho Choi, DAI Gil Lee. Expert Cure System forimide Resin[J ]. Journal of Application Polymer Sci-
the Carbon Fiber Epoxy Composite Materials [J ].ence,2003,90(10):2764-2774.
Journal of Composite Materials, 1995,29(9): 1181-[20]
RAHMAT A R, HEATLE F, DAY RJ. Compari-
1200.son of Microwave and Thermal Cure of Unsaturated
[9]杨德桐.复合材料结构件固化成型工艺参数控制[J]Polyester Resin [J ]. Plastics Rubber Composites,
航天制造技术,2003(5):10-13.2003,32(6):257-264.
[10] MICHAEL S. Advances in Electrom-Beam Processing[21]
赵秋艳.复合材料成型工艺的发展[J].航天返回与遥
of Fiber Reinforced Plastics: An Emerging Cuping感,1999,20(1):41-46.
Technology[J]. SAMPE Journal ,2000,36(2):33-38.[22]
艾涛,王汝敏.低成本、高性能复合材料的成型技术
[11] CUASTI F, ROSI E. Pressure Vessels: A Possible[J].纤维复合材料,2004(2):42-44.
Application of Low Energy E-Ream Curing [J].[23]
王芳.VARTM用环氧树脂固化工艺的研究[J].高科
SAMPE Journal,2000,36(2):25-30.技纤维与应用,2006,31(1):41-44.
[12]吕智,张复盛,李凤梅.双马来酰亚胺树脂及其碳纤维[24]
王晓洁,张炜刘炳禹,碳纤维湿法缠绕基体配方及成
复合材料的电子束辅助固化研究[J].玻璃钢/复合材型研究[J].固体火箭技术,2001.24(1):60-63.
料,1999(1):20-23.[25]
何钦象,祖磊,李辅安.复合材料环形高压容器缠绕参
[13]刘玉文,张志谦,黄玉东.碳纤维在电子束辐射过程中数设计与分析[J].宇航学报,2006,27(6):1350-
对树脂基复合材料界面性能的影响[J].材料工程,1355.
2002(2):44-46.[26] SURATNO Basuki R, YEL, MAIY W. Simulation
[14]许松,魏东,刘成武.光固化复合材料在飞机结构抢修of Temperature and Curing Profiles in Pultruded
中的应用研究[J].航空维修与工程,2006(2):30-32Composite Rods[J]. Composites Science and Technol-
[15] RADFORD D W, RENNICK T S. Separating Sourcesogy,1999,58(2): 191-197.
of Manufacturing and Corn Distortion in Laminated.[27]
LIU XL, CROUCH I G, LAM Y C. Simulation of
Composites[J ]. Journal of Plastics and Composites,Heat Transfer and Cure in Pultrusion with a General-
2000,19(8):621-641.Purpose Finite Element Package[J]. Composites Sci-
[16] WEIJing hua, HAWLEY Martin C, DELONGJ D,ence and Technology,2000,60(6):857-864.
et al. Comparision of Microwave and Thermal Cure of[28]
ZIAEE S, PALMESE G R. Effects of Temperature
Epoxy Resins[J ]. Polymer Engineering and Science,on Cure Kinetics and Mechanical Properties of Vinyl-
1993,33(17):1132-1140.Ester Resins[J ]. Journal of Polymer Science Part B:
[17] PRASAD K D V, SHU H H. Study on the Micro-Polymer Physics,1999,37(7): 725-744.
wave Curing of Adhesive Joints Using a Temperature[29]
于运花,王成忠,杨小平,等.碳纤维/乙烯基醋树脂拉
Controlled Feedback System[J]. Journal of Material挤复合材料基体固化体系的研究[J].北京化工大学
Process Technolgy,1999,30(3): 128-149.学报,2002,29(3):28-31.
[18] ZHOU J, SHI C, MEIB C, et al. Research on the
一填空题:
1.玻璃钢材料由(基材)及(增强材料)组成,其中(各类树脂)和(凝
胶材料)为玻璃钢的常用基材。
2.常见可以拉制成纤维的玻璃种类主要分为(无碱玻璃)、(中碱玻璃)、(高碱玻璃)、(高强玻璃),其中(无碱玻璃纤维)是应用最多的玻纤。
3.连续玻璃纤维纺织制品就起产品形态而言可分为(纱线)(织物)两大类别。
4.预浸料的制备方式可分为(湿法)(干法)及(粉末法)。
5.构造胶粘剂一般以(热固性树脂)为基体,以(热塑性树脂)或(弹性体)为增韧剂,配以固化剂等组成。
6.按照材料成分分类主要分为(环氧树脂胶粘剂)(聚酰亚胺胶粘剂)(酚醛树脂胶粘剂)(硅酮树脂胶粘剂)。
7.玻璃钢制品的生产过程可大致分为(定型)(浸渍)(固化)三个要素。8.环氧树脂是分子中含有两个或两个以上(环氧基团)的一类高分子化合物。
9.按适用于玻璃钢手糊成型的模具构造形式分为:(单模)及(敞口式对模)。10.叶片制造常用的基体树脂有(不饱和聚酯树脂),(环氧乙烯基树脂)及(环氧树脂)三类。
二.名词解释:
1.热固性树脂:这种树脂在催化剂及一定的温度、压力作用下发生不可逆的化学反响,是线性有机聚合物链相互交联后形成的三维构造体。
2.预浸料:将定向排列的纤维束或织物浸涂树脂基体,并通过一定的处理后贮存备用的中间材料。
3.不饱和聚酯树脂:是由饱和的或不饱和的(二元醇)及饱和的及不饱和的(二元酸或酸酐)缩聚而成的线性高分子化合物。
4.单位面积质量:一定大小平板状材料的质量和它的面积之比。
5.含水率:在规定条件下测得的原丝或制品的含水量。即试样的湿态质量和干态质量的差数及湿态质量的比值,用百分率表示。
6.拉伸断裂强度:在拉伸试验中,试样单位面积或线密度所承受的拉伸断裂强力。单丝以Pa为单位,纱线以N/tex为单位。
7.弹性模量:物体在弹性限度内,应力及其应变的比例数。有拉伸和压缩弹性模量(又称杨氏弹性模量)、剪切和弯曲弹性模量等,以Pa(帕斯卡)为单位。
8.偶联剂:能在树脂基体及增强材料的界面间促进或建立更强结合的一种物质。
9.片状模塑料:由树脂、短切或未经短切的增强纤维以及细粒状填料(有时不加填料),经充分混合而制成一种厚度一般为1mm~25mm的薄片状中间制品,能在热压条件下,进展模塑或层压。
10.纤维体积含量:纤维体积及复合材料的总体积之比。
11.增强层:由一种纤维形式(如单向的无捻粗纱、毡或织物)组成起增强作用的构造。
12.熟化:热固性模塑混合料的增稠过程,通过这一过程复合物将到达给定的流动水平且组分没有明显的分散。
13.拉挤型材:拉挤工艺连续生产的长条形复合制品,通常具有恒定的横截面积和形状。
14.增稠剂:通过化学反响增加粘度的添加剂。
塑料中,有相对惰性的固体物质。
三.简答题:
1.RTM成型工艺的主要优点
a制品外表质量好,尺寸精度高,原材料的利用率高。
b成型过程中散发的挥发性物质少,可有效地改善工作环境
c生产效率高
2.不饱和聚酯树脂的配料原那么
A促进剂和固化剂不能同时参加,应先参加一种搅拌均匀后再参加另一样。b搅拌时速度要慢,防止混入气泡
c相关工具、容器要严格分开,不准共用。
d要在规定时间内用完。
3.环氧树脂的优缺点
优点:固化收缩率低,具有良好的力学性能,耐化学腐蚀性能、电性能和较好的尺寸稳定性
缺点:本钱较高,环氧树脂粘度相对较高,工艺性较差。
4.什么是复合材料界面。
复合材料的界面是指基体及增强相之间化学成分有显著变化的、构成彼此结合的、能起载荷传递作用的微小区域。
5.什么是阴模。
阴模的工作面是向内凹陷,用阴模生产的制品外外表光滑、尺寸较准确,常用于生产外外表要求光滑和尺寸精度较高的制品。
6.模具脱模方式有哪几种,请简单介绍。
(1)整体式,即模具是一个整体,产品整体施工,整体脱模。
(2)组合式,即模具根据脱模要求由几个分模用螺栓连接,整体施工,分块拆模。即可保证产品精度,又使外形复杂的制品能顺利脱模。
7.复合材料的定义是什么。
复合材料是由有机高分子、无机非金属或金属等几类不同材料通过复合工艺组合而成的新型材料。它及一般材料的简单混合有本质区别,既保存原组成材料的重要特色,又通过复合效应获得原组分所不具备的性能。可以通过材料设计使原组分的性能相互补充并彼此关联,从而获得更优越的性能。8.复合材料的特点。
(1)由两种或多种不同性能的组分通过宏观或微观复合在一起的新型材料,组分之间存在着明显的界面。
(2)各组分保持各自固有特性的同时可最大限度地发挥各种组分的优点,赋予单一材料所不具备的优良特殊性能。
(3)复合材料具有可设计性。
9.复合材料的优点是什么。
(1)高比强度、高比模量(刚度)。
(2)良好的高温性能。
(3)良好的尺寸稳定性。
(4)良好的化学稳定性。
(5)良好的抗疲劳、蠕变、冲击和断裂韧性。
(6)良好的功能性能:包括光、电、磁、热、烧蚀、摩擦及润滑等性能。
四.选择题
1.目前聚合物基复合材料的最高耐温上限为。
A.120CB.280C
C.350C
D.
500C
2.手糊制品厚度超过mm,那么需2次成型。
A.3B.7
C.15
3.玻璃纤维布之间搭接不能小于mm。
A.10B.20
C.50
4.手糊作业拐角处圆角R限制内侧为R>mm。
A.5B.10
C.15
5.环氧树脂是构造。
A.弹性B.线性
C.弧形
6.高强度玻璃纤维抗拉强度比无碱玻璃纤维高%。
A.20B.30
C.40
7.复合材料具有对切口不敏感的优良性能,但及金属相比,复合材料的要低得多。A.弹性B.刚度C.冲击韧性
8.平安生产管理,要坚持的方针。
A.平安第一、预防为主、综合治理B.预防为主、
防治结合
C.实事求是、尊重科学
9.乙炔气瓶放置地点不得靠近热源,距明火至少应保持以上。
A.5米B.10米
C.15
米
10.闪点大于28°C小于60°C的液体为:
A.易燃液体B.可燃液体
11.真空泵功率一般为。
A.3~5KWB.5~10kwC.10~20KW
12.胶衣树脂可通过添加来降低粘度。
13.E51表示。
14.
无碱玻璃纤维含碱量在。
A.10%以上B.2-6%C.1%以下
15.纤维增强塑料一词缩写为。
A.FRP
16.下面哪一种是热塑性树脂。
A.191树脂B.聚乙烯树脂
17.圆磨机磨盘直径在以下为轻型,以上者为重型。
A.80mmB.125mmC.200mm
18.为了方便脱模,拔模斜度一般为。
A.3°~6°B.10°~15°C.2°~5°19.玻璃钢应用最多的是哪种纤维。
A.无碱玻璃纤维B.中碱玻璃纤维C.碳纤维
20.
制备玻璃纤维开展方向是。
A.间熔法B.直熔法C.拉丝法
21.固化是过程。
A.放热反响B.物理反响C.化学反响22.预浸料需要在下储藏。
A.高温B.低温C.无所谓
23.下面那种树脂可以重复利用。
A.热塑性树脂B.热固性树脂C.环氧树脂24.下面哪种固化剂不能用于不饱和聚酯树脂固化。
A.胺类固化剂B.过氧化环已酮C.过氧化苯甲酰
25.手糊作业操作环境湿度应控制在。
A.>10%B.>50%C.<80%
26.阴模是。
A.向内凹陷的B.向外凸出的C.分为两瓣的
27.对产品外表质量要求较高时采用哪种工艺。
A.胶衣+外表毡B.胶衣+短切毡C.胶衣
28.玻璃纤维是一种矿物纤维。
A.金属B.高分子C.无机非金属
29.如要求制品有较好的电讯性能,可选用树脂。
A.环氧B.聚酯C.丁苯
30.手糊作业需戴何种劳保用品。
A.橡胶手套B.防毒口罩C.以上两种
五.判断是非题:(正确的在括号内画“V”,错误的在括号内画“X”)1.在使用不饱和聚酯树脂时,温度低的情况下可适当增加固化剂的比例以提高固化速率。(V)
2.使用电钻在玻璃钢上钻孔时需要进展定位。(V)
3.进展涂胶作业时可以不佩戴劳保用品。(X)
4.可以使用蜡制容器盛装树脂。(X)
5.风电叶片制造一般采用真空灌注工艺。(V)
6.预浸料需在低温下储藏。(V)
7.高处作业中上下时手中不得拿物件,不得随意向下投掷材料和工具。(V)
8.操作天车时不允许三个机构同时动作,一般也不得同时动主、付钩。(V)9.吊运吊挂时吊挂绳之间的夹角宜小于120°,以免吊挂绳受力过大。(V)10.不准依靠极限位置的限位器进展停车但可以利用打反车进展制动。(X)11.电气检修作业的步骤和程序为:停电、验电、放电、挂接地线、装设遮拦、悬挂标志牌。(V)
12.手糊成型对环境湿度没有要求。(X)
13.热固性塑料可以重复利用。(X)
14.不饱和聚酯树脂促进剂和固化剂单独混合会有危险。(V)
15.聚酯树脂固化剂和促进剂用量可在一定范围内变动。(V)
16.当材料变更或气候变化时,应进展小样试验。(V)
17.胶衣粘度可通过加少量丙酮来调节。(V)
18.胶衣初凝,手感软而不黏时,可立即进展铺层。(V)
19.方格布手糊时含胶量一般在20%30%。(X)
20.为了提高产品的刚度,有时在产品中埋入加强筋。(V)
21.手糊作业时,操作环境需要通风。(V)
22.手糊制品挥发的苯乙烯对人体无害。(X)
23.玻璃钢制品在脱模后还需一段时间继续固化。(X)
24.玻璃纤维增强树脂复合材料根本上属于绝热材料。(V)
25.复合材料在湿态环境下,水分会扩散到材料内部,从而影响材料的力学性能。(V)
26.决定聚合物强度的主要因素是分子内分子之间的作用力。(V)
27.当复合材料不同组分外表带有异性电荷时,将发生静电吸引。(V)28.在复合材料组分之间发生化学作用,在界面上形成离子键结合。(X)29.胶衣喷涂时对喷枪喷射角度无要求。(X)
30.手糊作业制品含胶量一般大于真空导入工艺制品。(V)
1.请画出气压法脱模示意图。
2.请简要画出手工成型工艺流程图。
3.634#环氧树脂环氧值为0.4,用乙二胺为固化剂,求每100克环氧树脂需加多少克乙二胺固化剂。
解:乙二胺分子量M胺=60含有4个活泼氢所以G=M胺/(n胺×环氧值)=60/(4×0.4)=答:每100克环氧树脂需加6克乙二胺固化剂。
1.复合材料中的“碳钢”是()
A、玻璃纤维增强A1基复合材料。B、玻璃纤维增强塑料。
C、碳纤维增强塑料。D、氧化铝纤维增强塑料。
2.材料的比模量和比强度越高()
A、制作同一零件时自重越小、刚度越大。
B、制作同一零件时自重越大、刚度越大。
C、制作同一零件时自重越小、刚度越小。
D、制作同一零件时自重越大、刚度越小。
3.在体积含量相同情况下,纳米颗粒与普通颗粒增强塑料复合材料()A、前者成本低B、前者的拉伸强度好
C、前者原料来源广泛D、前者加工更容易
4、Kevlar纤维()
A、由干喷湿纺法制成。B、轴向强度较径向强度低。
C、强度性能可保持到1000℃以上。D、由化学沉积方法制成。
5、碳纤维()
A、由化学沉积方法制成。B、轴向强度较径向强度低。
C、强度性能可保持到3000℃以上。D、由先纺丝后碳化工艺制成。
6、聚丙烯增强塑料的使用温度一般在:()
A、120℃以下B、180℃以下
C、250℃以下D、250℃以上
7、碳纤维增强环氧复合材料力学性能受吸湿影响,原因之一是()A、环氧树脂吸湿变脆。B、水起增塑剂作用,降低树脂玻璃化温度。
C、环氧树脂发生交联反应。D、环氧树脂发生水解反应
8、玻璃纤维()
A、由SiO2玻璃制成。B、在所有纤维中具有最高的比弹性模量。
C、其强度比整块玻璃差。D、价格贵、应用少。
9、生产锦纶纤维的主要原料有()
A、聚碳酸酯。B、聚丙烯腈。
C、尼龙。D、聚丙烯。
10、晶须()
A、其强度高于相应的本体材料。B、长径比一般小于5。
C、直径为数十微米。D、含有很少缺陷的长纤维。
11、对玻璃纤维和聚酰胺树脂构成的复合材料命名不正确的是()。A.玻璃纤维聚酰胺树脂复合材料B.玻璃纤维/聚酰胺树脂复合材料C.聚酰胺材料D.聚酰胺基玻璃纤维复合材料
12、目前,复合材料使用量最大的增强纤维是()。
A.碳纤维B.氧化铝纤维
C.玻璃纤维
D.碳化硅纤维
13、目前,复合材料使用量最大的民用热固性树脂是(
)。
A.环氧树脂B.不饱和聚酯
C.酚醛树脂
D.尼龙
14.聚合物基复合材料制备的大体过程不包括()
A.预浸料制造B.制件的铺层
C.固化及后处理加工D.干燥
15、有关环氧树脂,说法正确的是()
A、含有大量的双键B、使用引发剂固化
C、使用胺类固化剂固化D、属于热塑性塑料
二、判断题(20分,每题2分)【得分:
】
1、复合材料是由两个组元以上的材料化合而成的。()
2、混杂复合总是指两种以上的纤维增强基体。()
3、层板复合材料主要是指由颗料增强的复合材料。()
4、最广泛应用的复合材料是金属基复合材料。()
5、复合材料具有可设计性。()
6、竹、麻、木、骨、皮肤是天然复合材料。()
7、分散相总是较基体强度和硬度高、刚度大。()
8、玻璃钢问世于二十世纪四十年代。()
9、一般酚醛树脂和沥青的焦化率基本相同,在高压下,它们的焦化率可以提高到90%。()
10、硼纤维是由三溴化硼沉积到加热的钨丝芯上形成的。()
三、问答题(50分,每题5分)【得分:
】
1.选择复合材料用树脂基体时,主要应考虑哪几方面问题?
2.环氧树脂和酚醛树脂固化各有什么特点?对制备工艺有什么影响?
3.简述玻璃纤维主要优缺点?
4.简述芳香族聚酰胺纤维主要优缺点?
5.说明UHMWPE纤维的结构、性能和应用范围。6.简述玻璃纤维直接熔融法制备工艺?
7.在PAN法制备碳纤维的工艺过程中,为什么要进行预氧化、碳化和石墨化三个过程?
8.复合材料成型时施加压力的主要作用是什么?复合材料为什么要采用低压成型?
9.如何选择复合材料制件的成型方法?
一、选择题(30分,每题2分)【得分:
】
题号12
3
4
5
6
7
8
9
10
答案A
B
A
D
A
B
A
A
题号1112
13
14
15
16
17
18
19
20
答案CB
D
D
二、判断题(20分,每题2分)【得分:
】
1、复合材料是由两个组元以上的材料化合而成的。(x)
2、混杂复合总是指两种以上的纤维增强基体。(x)
3、层板复合材料主要是指由颗料增强的复合材料。(x)
4、最广泛应用的复合材料是金属基复合材料。(x)
5、复合材料具有可设计性。()
6、竹、麻、木、骨、皮肤是天然复合材料。(V)
7、分散相总是较基体强度和硬度高、刚度大。(x)
8、玻璃钢问世于二十世纪四十年代。()
9、一般酚醛树脂和沥青的焦化率基本相同,在高压下,它们的焦化率可以提高到90%。(V)
10、硼纤维是由三溴化硼沉积到加热的钨丝芯上形成的。()
三、问答题(50分,每题5分)【得分:
】
1.选择复合材料用树脂基体时,主要应考虑哪几方面问题?
答:1)能够满足产品的使用需要,如使用温度、强度、刚度、耐药品性、耐腐蚀性等。高拉伸模量、高拉伸强度、高断裂韧性的基体有利于提高复合材料的力学性能:2)对纤维具有良好的润湿性和粘结性;3)容易操作,如要求胶液具有足够的适用期、预浸料具有足够长的储存期、固化收缩小等;4)低毒性、低刺激性;5)价格合理
2.不饱和聚酯树脂的固化过程
答:不饱和聚酯树脂的的固化是一个放热反应,其过程可分为以下三个阶段:
1)胶凝阶段从加入促进剂后到树脂变成凝胶状态的一段时间。这段时间对
于玻璃钢制品的成型工艺起决定性作用,是固化过程最重要的阶段。
2)硬化阶段硬化阶段是从树脂开始到胶凝到一定硬度,能把制品从模具上取下为止的一段时间。
3)完全固化阶段通常在室温下进行,在后处理之前,室温至少要放置24小时,这段时间越长,制品吸水率越小,性能越好。
3.简述玻璃纤维主要优缺点?
答:玻璃纤维的特点:拉伸强度和冲击强度高,延伸率小;弹性模量较大;耐热,属于无机材料,不可燃;化学耐久性好;绝缘性和绝热性好;吸水率较低;与基体材料粘结性好;价格较其他增强材料低;可作为有机聚合物基或无机非金属材料基复合材料的增强体。缺点:容易被水腐蚀。
4.简述芳香族聚酰胺纤维主要优缺点?
芳香族聚酰胺纤维:外观呈黄色;强度高、弹性模量高,密度小(1.44~1.45),比强度极高(与S-GF、CF-Ⅱ相当)、比模量高(约为GF的2倍),韧性好,耐冲击,抗疲劳抗蠕变;除少数强酸强碱外,对其他介质(普通有机溶剂、盐类溶液等)有很好的耐化学药品性;具有自熄性和良好的热稳定性;高温下不溶,300℃以上短时间强度不变,温度上升纤维逐渐热分解或碳化;热膨胀系数为各向异性,纵向热膨胀系数为负值;但对紫外线较敏感,不宜曝光使用;抗压抗扭性差;耐水性差。
5.说明UHMWPE纤维的结构、性能和应用范围。
性能:聚乙烯纤维超轻,密度0.97g/cm3;具有高比强度、高比模量以及耐冲击、耐磨、自润滑、耐腐蚀、耐紫外线、耐低温、电绝缘、不吸水、电磁波透过好等多种优越性。
其不足是熔点较低135℃和高温容易蠕变,因此仅能在100℃以下使用。
6.简述玻璃纤维直接熔融法?
答:池窑拉丝法(直接熔融法)
玻璃纤维是由含有各种金属氧化物的硅酸盐类(硅砂、石英石、硼酸、粘土、氟石等),经熔融(1300℃)后,借自重由坩埚底部的漏丝板流出,孔径为1.5~2mm,流出的玻璃液温度约为1190℃,在迅速冷却的过程中,借助高速(1000~3000m/min)转动,拉制成直径很细(3~20μm)的玻璃纤维。从坩埚中拉出的每根纤维叫单丝,一个坩埚拉出的所有单丝经过浸润剂槽后,集束成一根原纱。
7.在PAN法制备碳纤维的工艺过程中,为什么要进行预氧化、碳化和石墨化三个过程?
答:PAN原丝的预氧化处理预氧化的目的就是为了防止原丝在碳化时熔融,通过氧化反应使得纤维分子中含有羟基、羰基,这样可在分子间和分子内形成氢键,从而提高纤维的热稳定性。预氧丝的碳化预氧丝的碳化一般是在惰性气氛中,将预氧丝加热至1000-1800C,从而除去纤维中的非碳原子(如H、O、N等)。生成的碳纤维的碳含量约为95%。碳化过程中,未反应的聚丙烯腈进一步环化,分子链间脱水、脱氢交联,末端芳构化生成氨。随着温度的进一步升高,分子链间的交联和石墨晶体进一步增大。PAN的石墨化石墨化过程是在高纯度惰性气体保护下于2000-3000℃温度下对碳纤维进行热处理。碳纤维经石墨化温度处理后,纤维中残留的氮、氢等元素进一步脱除,碳一碳重新排列,层面内的芳环数增加,层片尺寸增大,结晶态碳的比例增加。
8.复合材料成型时施加压力的主要作用是什么?复合材料为什么要采用低压成型?
答:(1)使熔融的树脂具有一定的流动性,进一步浸渍玻璃纤维布。使层压板结构密实,提高层间粘结强度。
(2)冷压的目的是防止层压板在冷却过程中的变形。
(3)用来克服胶布中挥发物产生的蒸气压力,防止形成大量的气泡和微孔。
通常制品的机械强度(拉伸、弯曲、压缩等)随压力的增加而增加。但压力不能过大,否则玻璃纤维被压碎,反而致使强度降低。层压板的比重随压力的增加而增加。压力增加到一定值时,比重变化不明显。层压板的吸水性随压力增大而降低
9.如何选择复合材料制件的成型方法?
答(1)产量大且尺寸不太大时,采用压制成型等机械化成型方法;
(2)产量少且尺寸较大时,则采用手糊或喷射成型方法;
(3)两者之间则可采用树脂传递成型法。
(4)回转体宜采用纤维缠绕成型法和离心浇铸成型法
10.手糊成型所用胶液里通常含有哪些辅助材料?它们的作用及用量范围?
答:(1)无捻粗纱:无捻粗纱容易浸透树脂,在手糊成型中配合其他纤维制品使用,可用于填充制品死角、单向强度要求高的制品和局部制品增强。
(2)短切纤维毡:短切纤维毯比织物成本低、变形性好,增厚效果显著,使用方便
等。用它制造的产品具有平面各向同性,制品中树脂含量可达60~80%。常用于糊制强度要求不高,荷载随机性大和防腐蚀制品等。
(3)表面毡:是专门用于制品表面,构成富树脂层,以改善玻璃钢制品的表面性能;(4)无捻粗纱布:无捻布的特点是变形性好,增厚效果显著,易被树脂浸透,价格较其它布便宜等。但是无捻粗纱布在45°方向强度较低,仅为0°方向的30%,为加捻布的50%。无捻粗纱布是手糊成型用的主要增强材料。
aCuring
Shaping
Pyrolysis
Sintering
bForce
Force
Heat
Physical plasticityOriginal state
Chemical plasticity
Silica filler-OH
Polymer chain
Cd
e
OHO
HO
图1.三维透明折纸玻璃的制备过程。a制备流程的图示。b通过塑化实现永久形变的两个机理。c侧链悬挂羟基的动态聚酯网络。d三维透明玻璃羽毛。标尺:1厘米。e玻璃羽毛在600度下的耐热性。标尺:1厘米Brown
Transparent
ModelOriginal
Origami
shapeshape
part
glass
图2.透明折纸玻璃的实物制备。标尺:1厘米
固定形状后的复合薄膜经后续热处理,得到复杂三维形状的透明玻璃。“纸
鹤”是利用物理塑化机理制备,“花瓶”和“花”是利用化学塑化机理制备
相比于3D打印,本工作成型速度快,无需支撑,且表面粗糙度低。
10.手糊成型所用胶液里通常含有哪些辅助材料?它们的作用及用量范围?
问:2023年锅炉价格/多少钱?

上一篇:ASMB API