石油炼制用催化剂、化学药剂及添加剂 在复杂的石油炼制过程中消耗多种催化剂、化学药剂和添加剂是为了更多地得到我们所需要的燃
石油炼制用催化剂、化学药剂及添加剂
在复杂的石油炼制过程中消耗多种催化剂、化学药剂和添加剂是为了更多地得到我们所需要的燃料、润滑油和其它化工产品,提高炼油效率和产品质量。伴随炼油行业中新技术的不断应用,生产规模的不断发展,与之配套的炼油用催化剂、化学药剂及添加剂也形成了一个新兴的行业,这个行业伴随着化学、材料和炼油等行业的发展而发展。
对于广大的炼油工作者来说,虽然和催化剂、化学药剂及添加剂经常接触,但由于炼油行业本身覆盖面广,生产过程复杂,专业分工越来越细,对于这个附属于炼油的化工催化剂化学品行业缺乏全面、深入的了解。本文阐述了当今世界及我国炼油工业的现状,从化学原理和反应机理上论述了主要催化剂、化学药剂及添加剂的主要性能,并介绍了炼油催化剂、化学药剂及添加剂的发展过程、技术进步和生产应用情况,给广大炼油工作者用好催化剂、化学药剂和添加剂有很好的指导作用。
第一章 炼油概况
截至2005年底,世界的炼油能力达到42.6亿吨/年,全球的石化工业已经形成了北美、亚太、西欧三足鼎立的市场格局。世界炼油厂总数从1999年的756座减少到了717座,炼厂平均规模从539万吨/年提高到2003年的572万吨/年。2005年,全球原油加工能力达到41.20亿吨/年,炼厂总数却从717座减少到674座,平均规模达到611万吨/年。
目前,世界炼油业形成了美亚并驾齐驱、西欧跟随的三足鼎立新格局。上述三地区2003年合计炼油能力占世界总能力的比例高达67.1%。亚太地区炼油能力占世界总能力的比重从1992年的18.3%增加到2000年以来的24.4%~24.9%。这表明,亚太地区炼油工业在世界炼油工业中已上升至重要的地位。
在亚太地区炼油工业中,中、日、韩、印度占有主导地位,2003年底这四国的合计炼油能力为6.95亿吨/年,占亚太地区总能力的69.4%。2002年底,中国原油一次加工能力已达2.895亿吨/年,超过日本和俄罗斯,居世界第二位,2004年达到了3.18亿吨。下表为2006年度世界最大炼油公司排名和最大炼厂排名次序。
2006年全球最大的25家炼油公司排名(万吨/年)
排名 | 公司 | 原油加工能力,桶/日历日 |
1 | 埃克森 美孚 | 5,690,000 |
2 | 皇家荷兰/壳牌 | 5,172,000 |
3 | BP | 3,871,000 |
4 | 中国石化(Sinopec) | 3,611,000 |
5 | Valero能源公司 | 2,830,000 |
6 | 委内瑞拉石油公司 | 2,792,000 |
7 | 道达尔 | 2738000 |
8 | 康菲公司 | 2659000 |
9 | 中国石油(CNPC) | 2440000 |
14 | 伊朗国家石油公司 | 1451000 |
15 | 俄国尤科斯公司 | 1182000 |
16 | 日本石油公司 | 1157000 |
20 | 印尼Pertamina公司 | 993000 |
24 | 韩国SK公司 | 817000 |
25 | 印度石油公司(IOC) | 777000 |
炼油能力前十名的国家
炼油能力(亿吨/年) | 炼厂数目(个) | 炼厂平均规模(万吨/年) | 能力所占比例(%) | |
全世界合计 | 41.03 | 717 | 572 | 100 |
美国 | 8.34 | 132 | 632 | 20.3 |
中国 | 3.04 | 122 | 249 | 7.4 |
俄罗斯 | 2.72 | 42 | 648 | 6.6 |
日本 | 2.35 | 33 | 712 | 5.7 |
韩国 | 1.27 | 6 | 2117 | 3.1 |
意大利 | 1.16 | 17 | 682 | 2.8 |
德国 | 1.14 | 16 | 713 | 2.8 |
印度 | 1.07 | 17 | 629 | 2.6 |
加拿大 | 0.99 | 21 | 471 | 2.4 |
法国 | 0.96 | 13 | 738 | 2.3 |
合计 | 23.04 | 419 | 550 | 56.2 |
我国炼油工业经过50年的发展,尤其是“十五”后,我国原油一次加工能力有了显着提高,特别是大幅度提高了高含硫原油加工能力。原油加工量由2.11亿吨提高到2005年的2.86亿吨,汽、煤、柴、润四大类成品油产量由1.24亿吨提高到1.80亿吨。
为了适应不断提高的汽、煤、柴等产品的质量要求和越来越重质化、劣质化的原油,炼油企业通过加大对二次加工装置的调整力度及提高加工深度,使汽柴油产品质量逐步提升,产品结构进一步优化,轻质油品收率大幅度上升,提高了加工负荷。
目前,汽油质量已经达到了无铅化和满足国家新颁布的质量标准要求,柴油质量全部满足新标准要求;生产的柴汽比由2000年的1.80调整为2005年的2.05,基本满足消费需要;轻油收率由2000年的70%左右提高到2005年的72%以上,其中汽煤柴润四大类油品收率由2000年的59%提高到2005年62.9%;全国炼厂平均加工负荷提高十几个百分点。
“十一五”期间,我国炼油工业将在现有13个千万吨级原油加工基地的基础上,通过改扩建或新建,形成20个左右千万吨级原油加工基地,加工能力占全国总能力的65%;企业平均规模达到570万吨,整体水平有较大提升。届时,炼油工业基本满足国内成品油市场需求,但需进口部分化工轻油以满足下游石化工业的需要。“十一五”期间,共新建原油一次加工能力9000多万吨,新增能力7000多万吨。
近期,国家已经先后核准了中海油南海惠州、青岛等新建大型炼油厂,以及中石油大连石化、大连西太平洋、独山子、中石化天津石化等炼油改扩建工程,并积极推进广西沿海大炼油、四川大炼油等项目的前期工作。蒸蒸日上的炼油工业发展时期,也是炼油催化剂化学工业的大好机遇,在今后的炼油生产中,我们将接触到更多的新型催化剂、化学药剂和添加剂。
第二章 催化剂化学品工业
催化剂化学品工业是指生产、销售催化剂和催化剂制造中所用载体以及所需特殊催化剂、化工原料的工业。
催化剂化学品工业早在19世纪末到20世纪初就逐渐形成,主要生产制造硫酸、油脂加氢、合成氨、合成甲醇、费托合成、煤焦油高压加氢等过程用的催化剂化学品,但大多是自产自用。后来由于石油炼制工业、化学工业、环境保护等发展的需要,出现了专门生产、销售催化剂的工业组织。由于催化剂化学品种类繁多,制造方法各异,服务行业不同,在催化剂化学品工业中形成多种经营方式的企业。
催化剂化学品生产组织主要包括:对原料的选择和质量控制,催化剂及其载体的制造,出厂前对催化剂特性评定,出厂后向客户提供技术服务。
催化剂分类
催化剂种类繁多,主要有金属催化剂、金属氧化物催化剂、硫化物催化剂、酸碱催化剂、络合催化剂、生物催化剂等,其制造方法也各异。
催化剂化学品工业中的主要产品种类有:石油炼制催化剂、石油化工催化剂(包括高分子合成中用的聚合催化剂)、无机化工催化剂(主要是制造氮肥和硫酸的催化剂)、环境保护催化剂等。
在外形和性能上,不仅要求具有一定化学组成和杂质限度,还要求具有一定形状、颗粒大小、强度、比表面、孔径等,以保证一定的催化活性、催化剂选择性、催化剂寿命,所以催化剂属于精细化工产品(见彩图)。
催化剂化学品产品的质量对于使用催化剂化学品的化工生产过程的效率具有重要意义。
炼油催化剂化学品工业
大宗的炼油催化剂有:烷基化、克劳斯硫磺回收、一氧化碳和氢气的有机合成、一氧化碳变换、裂化、脱烷基、脱水、脱氢、脱金属、脱氮、脱氧、脱硫、酶、气体脱硫脱氯、加氢、加氢处理、甲烷化、氧化和氨化氧化、聚合、重整、烃类蒸汽转化等催化剂共23类。
催化剂化学品生产是一个以技术为核心的行业,专业性强,有些催化剂化学品企业只生产一类催化剂化学品,或生产聚烯烃和聚合催化剂,或专营石油炼制的催化裂化催化剂,或专营酶催化剂等。而有些工厂主要生产石油炼制所用的催化裂化、催化重整、加氢精制等催化剂,或化肥工业所需的烃类蒸汽转化、一氧化碳变换、甲烷化等催化剂。有的公司以生产催化裂化催化剂著称,产量达十几万吨,还生产汽车排气净化催化剂等。有的公司以生产各种加氢精制催化剂为特色,还生产烯烃聚合、贵金属催化剂等。
多数催化剂化学品工厂也销售载体,并接受委托生产催化剂化学品,但也有专门生产载体或催化剂制备中特殊化工原料的工厂。有的工厂还专门从事再生催化剂化学品(见催化剂化学品再生)或回收贵金属。为了保护技术秘密,有的公司专设工厂生产自己发展的催化工艺中所用的催化剂,在用户购买工艺技术转让权后,才供应催化剂。也有的公司生产催化剂化学品自用,不销售。
1984年世界催化剂销售额达到27亿多美元,其中化工用催化剂占43%,石油炼制用占35%,环境保护用占22%。1989年达到了35亿美元,年平均增长率5%。
预计2008年,世界催化价值达到120亿美元/年,年增长率为3.7%,这主要是由于亚洲和拉美石化生产增长。欧洲、北美和日本以外地区的催化剂销售额年均增长率约为5%,2004年销售额为30亿美元;而北美的年均增长率为3%,2004年的销售额为42亿美元。
类别 | 化工 | 石油炼制 | 环境保护 |
比例(%) | 43 | 35 | 22 |
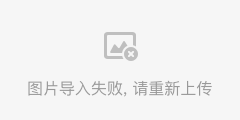
中国的炼油催化剂化学品工业
中华人民共和国成立之后,随着化肥、炼油、石油化工等工业的兴起而发展壮大。目前,化肥工业中所用的蒸汽转化、低温变换、中温变换、甲烷化、氨合成等催化剂均有一些工厂生产。炼油工业中所用的微球分子筛裂化催化剂、小球硅铝裂化催化剂、双金属重整催化剂、各种加氢精制催化剂、加氢裂化催化剂、迭合催化剂等也都大量生产,其中裂化催化剂年产量已达万吨以上。
石油化工中所用的裂解气加氢除炔烃、裂解汽油选择性加氢、二甲苯异构化、甲苯歧化等催化剂也均投入生产。此外,目前生产的还有丙烯氨化氧化、乙烯氧化制环氧乙烷以及乙烯聚合、丙烯聚合等各种催化剂。中国的催化剂化学品工厂多附属于化肥厂、炼油厂、石油化工厂,但所生产的催化剂化学品供应全国,并且还承担新催化剂的放大试制工作。还有一批专门生产氧化铝载体、氧化硅载体、活性炭载体以及分子筛的工厂。
催化剂化学品工业将随着石油炼制、化学工业、环境保护等有关行业的技术进步而发展。石油炼制工业迫切要求提高汽油辛烷值和进行渣油加工,催化剂化学品工业针对这些要求将推出一些新型催化剂化学品。化学工业要求发展适应原料变化、提高收率和节约能源的催化剂化学品,其中从煤制造一氧化碳和氢气,再生产各种有机化工原料的新型催化剂化学品正在发展。
第三章 炼油催化剂化学品
沸石系列催化剂
沸石是一族结晶型硅铝酸盐的总称。早在1756年,瑞典矿冶学家克朗斯提(B.Cronstedt)发现了一种低密度软性的结晶性硅铝酸盐矿石,主要由氧化硅、氧化铝与盐在水汽压力下作用所形成的。矿石结构中含有大约20%的水分,因水分会受热而失去,温度降低而再吸收,使得它在水中煮沸时会冒泡泡,故以希腊语“ZEO”(沸腾)和”litos”(石头)命名称为Zeolite(沸石)。
目前同天然产物具有相同结晶结构的沸石以及按分类属于非天然产的沸石,大多数都能够人工合成出来。天然产的沸石其化学组成是碱金属或碱土金属的硅铝酸盐,而合成沸石是硅铝酸钠。
在很长时间内,沸石仅作为吸水剂,后来又发现沸石有交换离子的性质。在本世纪初沸石用于净水,以除去硬水中的钙、镁等离子。到五十年代,沸石用于核能废水中阳离子处理剂、工业废气的吸收剂和工业废水的净化剂等。五十年代后期,莫比尔(Mobil)实验室首先发现在沸石结构内部能进行催化反应,六十年代,苇茨(Weisz)和弗里莱特(Frilette)在《物理化学》杂志上发表了关于合成沸石的催化作用。自此,沸石在催化领域的用途迅速扩大。
沸石分子筛的结构
沸石被广泛地应用为吸附剂、触媒及触媒载体缘于其结构的多孔性和极高的表面积。
沸石的微观结构是由(SiO4)四面体和(AlO4)四面体相互结合形成的立体网状结构,在网状结构中形成空洞,而且这些大空洞由纵横交错的孔道相互连通着。在这些空洞中含有结晶水和阳离子,这些阳离子用来中和(AlO4)四面体的负电荷,利用加热或减压的办法,可以比较容易地脱除一部分或全部结晶水,脱水后的沸石的结晶结构稳定,不会再发生本质上的变化。
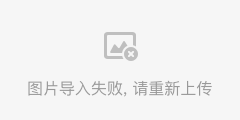
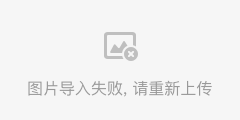
沸石的化学结构是以氧化硅或氧化铝的四面体为基本单元,以氧原子连接硅、铝的四面体而成的三度空间骨架结构。因铝原子为三价,呈AlO4四面体时,铝带负电荷,须仰赖阳离子来中和其电性。
分子筛的化学组成经验式为:
M2n·Al2O3·XSiO2·yH2O
式中M—分子筛中的金属离子,常见的阳离子有碱金、碱土、稀土金属、铵或氢离子;
n—金属离子的价数,
X—SiO2的mol数,
y—结晶水的mol数。
因两个AlO4四面体无法直接相连,沸石的硅/铝原子数比必须大于或等于1,即X≧1。
因沸石骨架结构中含有四、五、六、八、十、十二个四面体构成的环面,形成了大小不同的孔洞及管道,使得加热脱水处理过的沸石可以有选择性地吸附大小适当的分子,因此沸石又称为分子筛。
由于分子筛中Na2O,Al2O3,SiO2三者的数量比例不同而形成不同类型的分子筛,通常根据晶型和组成硅铝比的不同,把分子筛分为:A、X、Y、L…等类型,而根据孔径的大小又分为3A(在3微米左右),4A(比4略大),5A(比5略大)等型号。
几种常用分子筛的化学组成经验式对比:
4A分子筛Na2O·Al2O3·2SiO2
13X分子筛Na2O·Al2O3·2.5SiO2
Y型分子筛Na2O·Al2O3·5SiO2
丝光沸石Na2O·Al2O3·10iO2
由此可以看出,分子筛类型的不同主要是由于其组成中SiO2的含量不同。
为了适合分子筛的各种不同用途,特别是用作催化剂,需要把分子筛的Na+交换成其它阳离子。通常用Ca—X,Mg—X,Ca—Y,H—Y等表示交换后含有的阳离子。但这只表示它们含有的特种阳离子,并不意味着它们仅含有这些阳离子。
沸石的分类
到目前为止,应用最广的还是硅铝分子筛沸石,依其硅、铝的含量,可以分为三类:
l 低硅含量的;即Si/Al原子数比在1~1.5之间,如A及X沸石,多用于离子交换。
l 中等硅含量的;即Si/Al比在1.5~5.0之间,如Y及丝光沸石,用于石油炼制及石化工业的触媒作用。
l 高硅含量的;Si/Al比大于5,其中最著名的为H-ZSM-5(H代表质子),目前用于重油脱蜡、触媒重组等炼油工业,及由甲醇制造汽油、二甲苯异构化及甲苯不均化等石化工业。
一般而言,沸石的热稳定性及酸性强度因硅含量增加而增高,但是离子交换能力及酸性则随硅含量增加而减少。
部分研究沸石构造的学者,也依据沸石构造的基本单位来分类,如Y及X沸石与天然沸石同类,都是由双六员环(D6R)为基本连接单位,而ZSM-5和Beta沸石的基本结构单位为五员环。
沸石分子筛在石油化工中的应用
70年代莫比尔(Mobil)公司开发的以ZSM5为代表的高硅三维交叉直信道的新结构沸石,称之为第二代分子筛。这些高硅沸石分子筛水热稳定性高,亲油疏水,绝大多数孔径在0.6nm左右,在甲醇及烃类转化反应中有良好的活性及选择性。
80年代联合碳化公司(UCC)成功地开发了非硅、铝骨架的磷酸铝系列分子筛,这就是第三代分子筛。此类分子筛的开发,其科学价值在于给人们的启示:只要条件合适,其它非硅、铝元素也可形成具有类似硅、铝分子筛的结构,为新型分子筛的合成开辟了一条新途径。迄今为止,已经发现天然沸石分子筛40多种,人工合成的100多种。
目前,沸石催化剂目前已广泛地应用于石油化工领域,如用离子交换法将过渡金属担载在沸石上,再用氢气将其还原制备的催化剂,有很高的加氢活性。在具有固体硬性的沸石上担载过渡金属(主要是钯和铂)的双功能催化剂很早就运用于加氢裂化、重整、正构烷烃异构化等工业化过程中。
沸石的选择性吸附作用
由于分子筛的多样性和稳定性,其独特的选择与择形选择相结合的性能首先在吸附分离上得到工业应用。如空分、烷基苯料的烷烃分离、PX装置中芳烃分离。
沸石的选择性酸催化作用
液体形态的硫酸或氢氟酸等能催化一些反应如裂解(催化裂化),而固体形态的沸石,能提供质子,也能接受外来的电子对,而且也有与液体酸相同的酸催化效果,所以称之为固体酸。
沸石的酸根的来源是源自在氧化物的电荷不平衡,沸石分子结构中,Si是正四价,Al是正三价,两种元素周围都是四个负二价的氧,为维持整个结构电荷的平衡,在Al附近必需有一个正电来中和。如果此正电是H+,则可视为是质子的提供者,如果经加热脱除水分子则转成为电子对的接受者,总之,不论如何,氧化硅和氧化铝所形成的基团均成为一个酸基。
在催化反应中和液体酸比较,沸石作固体酸,另有如下好处:
(1) 具有高活性和选择性;
(2) 沸石固体酸不会腐蚀反应器和管线;
(3) 可以再生重复使用;
(4) 反应物及产物容易与固体酸分离;
(5) 处置废固体酸比废酸液容易。
沸石的形状选择性可分为
l 对反应物的选择性:反应物小于沸石孔洞口的才能进入沸石结构中进行反应。
l 对反应产物的选择性:产物中分子的形状及大小比沸石孔洞口小的,才有可能跑出来成为产物;若初步反应形成的产物尺寸太大,则必须再重组或转化成较小的分子。
l 过渡状态的选择性:在沸石孔洞内进行催化反应时,反应中间体的形成也受到沸石孔洞尺寸的限制,太大的中间体不易生成,以致由此种反应途径形成的产物也随之减少。
选择性裂化
在石油加工过程中应用ZSM5作催化剂进行选择性裂化反应,其中直链烷烃择形催化裂化为汽油馏分,在ZSM5中,链烷烃的裂化率随着链烷烃分子长度的增大而增加,随孔道的有效直径的减少而减少,这对辛烷值的提高是很理想的。X、Y、Z型的大孔径沸石和丝光沸石也可用作上述反应的催化剂,但失活较快。
在流化催化裂化工艺中,最初使用的是天然活性白土,后来开始使用合成硅酸铝、沸石催化剂。此外,还有人建议使用以氧化硅为主要成分含氧化镁、氧化硼、氧化铝等的催化剂。
流化催化裂化是最早应用沸石催化剂的,其主要目的是使生产能力和汽油馏分的辛烷值达到最大,并使副产物最少。在这类催化剂中,目前应用的主要是由稀土离子交换的具有较好的稳定性及较高硅铝比的Y型沸石。
这类催化剂颗粒大小及其分布对流化状态有较大影响。颗粒大小是流化开始时的重要因素,由于颗粒大小的不同,流化起始速度亦不同,显然颗粒大小对流化是一个重要因素。催化剂的最佳颗粒大小及其分布为:
30μm<DP<50ΜM
80μm以上……10%~20%
44μm以下……20%~40%
流化催化裂化催化剂还有氧化硅-氧化镁、氧化硅-氧化铝-氧化镁等。目前这类催化剂基本能满足工业生产的需求。但改善裂化催化剂的活性和稳定性、提高抗金属中毒性能、减低催化剂损失及耗用量、良好的选择性等方面的工作仍在发展中。
另外,由于产品的市场价格不同,催化裂化装置也在普通催化裂化催化剂中,增加部分新的催化裂化催化剂来得到更多的理想产品,如增产丙烯催化剂。
催化裂化装置采用基于ZSM5的助剂是低费用增产丙烯的有效途径,利用独特的基质技术,不仅可稳定ZSM5分子筛,使分子筛提供最大活性,而且可大大减少非选择性裂化,从而减少轻质烯烃产率。此外,这些助剂耐磨性极好,可减少损失。
目前采用的增丙催化剂(OlefinMax),其ZSM5助剂含ZSM5结晶25%,是炼油工业使用最广泛的ZSM5助剂,占所有ZSM5用户的近一半和FCC助剂市场的74%。
另外一种更高活性的催化剂(OlefinUltra)能提供最高的活性和极好的抗磨性能。可使炼厂新鲜催化剂消耗减少10%以上。该助剂已在全世界19座炼厂成功应用。
新一代的最大量增产丙烯催化剂,可使FCC装置丙烯产率超过15%(w)。
金属钝化剂
原油中的重金属(如镍、钒、铁等)几乎全部集中在渣油馏份中,随着渣油带入催化装置,在反应过程中沉积在催化剂上,使催化剂选择性变差,活性下降,产品分布变坏。严重时会威胁到催化裂化装置的安全和平稳运行。为了解决这个问题,最经济、方便和行之有效的方法为使用金属钝化剂。
为了防止FCC催化剂失活,工业上经常采用锑金属作钝化剂。催化裂化金属钝化剂是基于钝化剂有效组分随原料油一起沉积在催化剂表面,并和镍、铁、钒、钠等金属相互作用,或是形成金属盐或是以膜的形式覆盖在污染金属表面,改变污染金属的分散状态和存在形式,使其转变为稳定的、无污染活性的组分,抑制其对催化剂活性和选择性的破坏,提高平衡催化剂的活性和轻油收率。
助燃剂
由洛阳石油化工工程公司工程研究院开发的降低催化裂化再生烟气中氮氧化物含量的助剂LDN-1在中国石油天然气股份有限公司独山子石化分公司催化裂化装置上得到了成功应用,结果表明:该剂能够显着降低再生烟气中NOx含量并具有良好的CO助燃功能,在催化裂化主催化剂中加入质量分数为3%左右的LDN-1助剂。可使再生烟气中的NOx质量浓度从1400mg/m^3降至330mg/m3,NOx脱除率达75%。同时不会对产品分布和产品性质产生不良影响。
加氢裂化
加氢裂化是石油馏分在载有特种金属和具有酸功能的沸石催化剂存在下,在高氢分压下的裂化。大孔径Y,X型沸石和丝光沸石最适宜石脑油的加氢裂化,用稀土离子交换的高硅八面沸石适宜重质原料的加氢裂化。
用于加氢反应催化剂的主要金属,有周期表族的全部金属和B族的铜、铼、钼、钨和其它金属。
有研究表明:Ni-NaF-SiO2对1-己烯、环己烯、环十二碳三烯等加氢为饱和化合物的收率,几乎都是100%,催化剂的稳定性也很好。Pd-Al2O3催化剂在双烯加氢、丁烯醛加氢、乙炔加氢反应中均有较好的效果。Pd-CaCO3催化剂在2-丁炔-1,4-二醇和去氢沉香醇的加氢中得到工业应用。骨架镍(Ni2Al3和NiAl3)的合金可以制成高活性的催化剂。一般使用镍含量为30%~50%的合金。Ni和Pb催化剂在酚的加氢工业中也得到了应用。上述金属同时对羰基、醛、硝基、腈等也有很好的加氢效果。RuO2和Ru-C催化剂对脂肪酸和脂等的加氢的收率可以达到100%。
应用最广泛的加氢精制催化剂为铝-钴-钼催化剂,它是由在氧化铝上含2%~4%的CoO及9%~15%的MoO3所组成,当催化剂既含钴又含钼时,其活性比只含钴或只含钼时高得多(表2)。脱硫是在2MPa,380℃,供给原料空速为2.0h-1,供氢量为600标准m3/m3原料的条件下进行的。当改变Co∶Mo比值时,催化剂的活性亦发生变化。当催化剂中的原子数比Co∶Mo≈0.2∶1时,催化剂有最大的活性。氧化物与H2S及H2反应的结果使其从氧化态变成硫化态形式,部分氧化物还原成金属。此时催化剂的加氢活性大大提高。若原料中H2S含量低时,工业使用前最好先进行硫化,硫化是用含5%~10%的H2S的氢气在150~315℃时对催化剂进行处理。若在催化剂上有部分钴被镍所取代时,则含氮的有机化合物会较好地进行加氢。
催化重整
催化重整是炼油厂生产高辛烷值汽油组分的主要过程,也是为石油化工生产芳烃的主要过程。此过程是在双功能(酸与贵金属)催化剂上将低辛烷值的链烷烃和环烷烃转化为辛烷值的异构烷烃和芳烃。最常使用的催化剂是Pt/Ba/L型沸石催化剂,能高产率地将正构己烷和庚烷转化为苯和甲苯,这种催化剂对于象甲基环戊烷之类的常见毒物不敏感,但对硫很敏感。
由于双金属铂-铼催化剂(Pt-Re/γ-Al2O3)的优良性能,使铂铼催化剂几乎在世界各国炼油厂中得到推广应用。目前,我国开发出的双(多)金属重整催化剂有:
双金属
3741(Pt-Re/η-Al2O3)
3741-2(Pt-Re/γ-Al2O3)
CB-6(Pt-Re/γ-Al2O3)
3861(Pt-Sn/γ-Al2O3)
多金属
3752(Pt-Ir-Ce-Al/η-Al2O3)
CB-5(Pt-Re-Ti/γ-Al2O3)
重整催化剂属于双功能催化剂,其中一些反应是由于酸性催化剂在起作用(如异构化),另一些反应是由于金属催化剂在起作用(如脱氢)。现代重整催化剂的酸性功能由担体Al2O3和酸性组分氯提供的。在铂催化剂中常用的第二种金属有铼(Re)、铱(Ir)和锡(Sn)。其作用是阻止铂晶粒的增长,提高催化剂的容炭能力。但随着第二种金属的加入,致使重整油收率下降。为了解决这一问题又引入了第三种金属:钛、铅及金等。
国外现己开发了几种现代化催化重整催化剂:
l R-130系列:具有高的比表面积和稳定性,使用寿命长。现已有100多套CCR重整装置采用。这种高活性催化剂使用寿命可达5年(循环使用400余次)。
l R-170系列:与R-130比,C5+产率提高1% (v),有R-174、R-172等品种。有利于烷烃脱氢环化为芳烃,产氢也比R-130高出0.2% (w)。R-174己应用于奥地利斯韦夏特等炼油厂。操作工况为:分离器压力0.7MPa,重整生成油RONC为101,使用寿命超过5年。
l R-160系列:用于提高处理能力。R-162采用60%直馏石脑油扣40%裂化石脑油进料,操作压力1.2MPa。
l R-230系列:采用180℃干点石脑油进料,其活性和稳定性与R-130相媲美,C5+产率提高0.7w%,而且焦炭产率大大降低。
1965年,我国自行研究、设计、建设的第一套10万吨/年半再生催化重整在大庆炼油厂投产,使用国产第一个Pt/Al2O3催化剂(商业牌号3641)。随后,一系列双金属和多金属半再生和连续重整催化剂研制成功,并得到广泛应用。截至2003年3月,我国已建成投产的半再生式重整装置47套,总加工能力993.5万吨/年;连续重整装算18套,总加工能力1154万吨/年。
如何提高重整催化剂的活性、选择性、活性稳定性、水热稳定性是重整催化剂研究领域的技术核心。我国半再生重整催化剂的发展见下表。
我国半再生重整催化剂的发展
催化剂牌号 | 组成,Pt | Re | 其它% | 载体 | 相对稳定性 | 工业化年代 |
1226 | 0.3 | η-压片 | ||||
高铂小球 | 0.5 | η-小球 | 1965 | |||
3741 | 0.5 | 0.3 | η-小球 | 1974 | ||
Feb-41 | 0.5 | 0.45 | γ-小球 | 1984 | ||
3752 | 0.54 | Ir:0.1,Ce:0.22 | η-小球 | 1977 | ||
CB-5 | 0.5 | 0.3 | Ti:0.20 | η-小球 | 1983 | |
CB-5B | 0.5 | 0.3 | Ti:0.20 | γ-小球 | 1983 | |
CB-6 | 0.3 | 0.27 | γ-小球 | 1 | 1986 | |
CB-7 | 0.21 | 0.42 | γ-小球 | 1.5 | 1990 | |
CB-8 | 0.15 | 0.3 | γ-小球 | 1991 | ||
CB-9 | 0.25 | 0.25 | X | γ-小球 | 1 | 1997 |
3932 | 0.25 | 0.25 | γ-挤条 | 1 | 1995 | |
3933 | 0.21 | 0.46 | γ-挤条 | >1.5 | 1995 | |
PRT-A | 0.25 | 0.25 | X1 | GK条 | 1.15 | 2002 |
PRT-B | 0.21 | 0.48 | X1 | GK条 | >1.8 | 2003 |
表.我国半再生重整催化剂及其技术进步
催化剂牌号操作压力,MPa
单铂η-Al2O31226,
高铂小球,CB-31.5~2.0
双、多金属η-Al2O3CB-5~9,3932,3933<1.5
多金属γ-Al2O3PRT-A~D<1.2
1986年,我国第一个连续重整催化剂3861工业放大成功,法国IFP确认3861催化剂性能良好,可用于引进的使用法国IFP技术的连续重整工业装置。1991年在抚顺石油三厂引进的40万吨/年连续重整装置上首次应用成功。1994年,GCR-10催化剂在广州石化总厂的使用UOP技术的连续重整装置实现了工业化应用。随后,我国成功开发了一系列连续重整催化剂,见表3。
表我国开发的连续重整催化剂
催化剂商品名称首次应用特点
PS-Ⅱ38611990优良的活性、选择性、再生、抗磨损性能
PS-ⅢGCR-101994同上,但低铂
PS-Ⅳ39611996高水热稳定性
PS-ⅤGCR-1001998同上,但低铂
PS-ⅥRC0112001低积炭、高选择性
PS-Ⅶ2004同上,但高铂
截至2005年5月,我国共有连续重整装置18套,其中16套已完全采用国产PS系列催化剂,另外2套也采用国产连续重整催化剂作为补充剂。目前采用PS-Ⅲ催化剂1套,PS-Ⅳ催化剂3套,PS-Ⅴ催化剂8套,PS-Ⅵ催化剂4套。迄至目前,国产PS系列催化剂已在各类使用UOP和IFP技术的连续重整装置上得到成功应用,并且在使用我国开发的低压组合床技术的装置上也得到成功应用。
l PS-Ⅳ型
镇海炼化公司80万吨/年采用UOP公司第二代超低压连续重整装置用PS-Ⅳ型连续重整催化剂(工业牌号RCO11)工业应用试验表明,该催化剂具有良好的耐磨性能、水热稳定性和持氯性能,芳烃产率由65.40%提高到71.86%,提高了6.46个百分点;稳定汽油收率由86.87%提高到88.19%,提高了1.32个百分点;氢气产率由3.68%提高到4.03%,增加了9.5%;积炭速率降低了26.3%。
l PS-VI型
PS-VI型催化剂是我国自己研制开发的具有低积碳速率、高液体选择性特点的最新一代连续重整催化剂,铂、锡组元的基础上,引入新助剂,经过独特的工艺处理,在不降低比表面积的前提下,具有积碳速率低、选择性高、持氯能力强、活性稳定性好等特点。PS-VI型连续重整催化剂的主要组成是:Pt,0.28%;Sn,0.31%;Cl,1.10%;Si,79μg/g;Fe,98μg/g;Na,3μg/g。该催化剂的主要物理性质是:堆密度0.56ml/g,比表面积193平方米/g,孔隙体积0.71ml/g,1.4~2.0mm的粒径占99.8%,磨损率1.2%。
中国石化洛阳分公司70万吨/年连续重整装置采用法国石油研究院(IFP)第一代连续重整专利技术,原设计使用石化研究院研制的全氯型铂锡重整催化剂3861。该催化剂积炭速率较高、活性较低,运行效果不太理想。2002年5月在重整装置停工检修期间,将原3861重整催化剂更换为PS-VI型连续重整催化剂,取得了较好的效果。使用结果显示,在使用PS-VI催化剂时,尽管重整进料芳烃潜含量比使用3861催化剂时低了4.66个百分点,且在反应器入口温度降低15℃时,却能够获得RON为100.3的稳定汽油,说明PS-VI型催化剂活性高于3861催化剂。另外,稳定汽油的收率提高2.24个百分点;纯氢产率提高0.31个百分点;芳烃产率提高5.18个百分点;稳定汽油芳烃含量提高3.93个百分点,说明PS-VI催化剂比3861催化剂具有更好的选择性。PS-VI待生催化剂的碳含量为2.04%,而3861待生催化剂的碳含量为3%~4%,PS-VI催化剂的碳含量比3861催化剂降低了32%~49%,因此,PS-VI催化剂比3861催化剂具有更低的积炭速率。
l PS-Ⅶ型
由石科院研发、长岭炼化建长公司工业化生产的PS-Ⅶ型连续重整催化剂采用高铂含量、高Sn/Pt比、高比表面和二步浸渍法,并添加了A、B助剂,具有高选择性、低积炭率和高稳定性,具有良好的机械性能和烧焦再生性能。
l GCR-100
中石化广州分公司40万吨/年连续重整装置于1999年4月更换高水热稳定性的GCR-100催化剂。工业运转表明,GCR-100催化剂的再生性能、输送性能和抗磨性能良好,能满足UOP连续重整装置的工艺要求。天津石化公司化工厂连续重整装置采用GCR-100型重整催化剂生产高辛烷值芳烃原料。经过一年多的运转和装置考核表明,该催化剂具有良好的反应活性、选择性和稳定性。
l HDO-18
抚顺石油化工研究院研制开发的HDO-18催化重整生成油选择性加氢催化剂通过技术鉴定。鉴定认为,HDO-18催化剂的制备工艺成熟,无特殊环保问题,其性能达到国内同类催化剂先进水平。工业放大结果表明,HDO-18催化剂具有良好的活性、选择性和稳定性,可以满足工业装置长期稳定运转的使用要求,是一种催化重整生成油选择性加氢的理想催化剂,有着良好的推广前景。
二甲苯异构化
最简单的是苯环上的甲基重排,如二甲苯异构化反应,就是将来自重整装置或加氢汽油装置的C8芳烃转化为平衡的二甲苯混合物,然后分离出有价值的对二甲苯,若用(CVD法)Si沉积以收窄ZSM5孔道,产品中对二甲苯含量可增至95%。
甲苯歧化
甲苯歧化进行的是分子间的甲基重排,目前主要应用丝光沸石和ZSM5为催化剂,它们具有更高的稳定性,又可减少多甲苯的生成,如经镁或磷改性后对二甲苯的选择性可达83%。
乙苯合成
乙苯大约90%是通过苯与乙烯的酸催化烷基化而制成的,在ZSM5催化剂上进行乙烯与苯的烷基化反应,乙苯产率达99.6%,同时ZSM5催化剂能增加乙苯选择性及降低能耗。
对二甲苯的合成
这一类反应也是制备对二甲苯的途径,即甲醇与甲苯的烷基化,采用阳离子交换的八面沸石催化剂可生产50%对二甲苯,在ZSM5催化剂上对二甲苯选择性为90%。
碳碳键的生成
甲醇转化反应中,C—C键形成及分子增大的过程,利用ZSM5的孔道控制产物分子的截面积,选择适宜的反应条件以控制分子的长度,由此而发展了甲醇制汽油及甲醇制低碳烯过程。
异构化
C5/C6异物化
烷烃异构化是通过将原料中的C5/C6正构烷烃转化为相应的异构烃,从而提高汽油的前端辛烷值,使汽油具有均匀的抗爆性能。为解决汽油中不加四乙基铅而引起的辛烷值不足,许多炼油厂增加了戊烷和己烷异构化的能力,采用含贵金属的无定型SiO2Al2O3和沸石两种催化剂,在氢存在下和中压下进行操作。催化剂是用氧化铝为粘结剂的载有铂的丝光沸石,能抑制硫和水等杂质所引起的中毒。
催化剂是异构化技术的核心,目前已工业应用的异构化催化剂主要有低温及中温型两类,均以Pt作为活性金属组份,前者为Cl-Pt/Al2O3,反应温度低,活性高,但对原料中硫和水等杂质要求苛刻,不能再生;中温催化剂主要为Pt/分子筛,虽然活性略低,但对原料要求不高,可再生,在我国具有广泛的应用前景。
目前我国已有两套C5/C6烷烃异构化工业装置,均采用中温型分子筛催化剂,其中金陵分公司开发的NNI-1催化剂是世界上首次进行工业应用的载Pd分子筛催化剂,成本远低于Pt/分子筛催化剂,于2002年进行工业放大生产和应用,催化剂运行半年,一次通过辛烷值提高8-10个单位,达到80-82,性能达到载Pt分子筛催化剂水平。
金属催化剂
制氢
氧化铬-氧化铝、氧化铁、氧化钙-氧化镍、氧化锌等催化剂,广泛应用于烃类脱氢生产中。
合金、氧化锌、氧化铜和还原铜及骨架镍等催化剂广泛应用于醇类脱氢。
氧化钼、氧化钒、氧化碲及氧化锑等作为氧化催化剂得到广泛应用。许多研究指出,钴、钯、铂、铑、铱、钌等拥有对气态烃转化的活性。虽然有的贵金属的单位质量的活性比镍高些,但是对转化反应,镍的活性是足够的、最便宜的。所以,几十年来,镍一直被选为气态烃转化催化剂的最佳的主催化剂。
在制氨及制氢等工业生产中,常用的CO变换催化剂有Fe-Cr系(高变),Co-Mo-K系和Co-Mo-Mg系(耐硫低变),Cu-Zn系(低变)。甲烷化催化剂则以Ni为主要活性组分,助剂有Ca、Mg、La及Mo等。氨合成催化剂中主要组分是Fe3O4,助剂一般为铝、钾、钙、镁、钴等。Cu-Zn-Al催化剂则在甲醇工业生产中得到广泛应用。
树脂系列催化剂
MTBE树脂催化剂
甲基叔丁基醚(简称MTBE)是国内典型炼厂生产高辛烷值汽油组分的主要装置,只将炼厂气C4组份中异丁烯与工业甲醇在催化剂的作用下通过加成反应而生成甲基叔丁基醚(简称MTBE)。MTBE可用为添加剂来代替汽油中通常掺入的四乙基铅,达到提高汽油的辛烷值的目的,同时MTBE燃烧后对环境的影响污染要小得多。
MTBE装置按生产用途可分为炼油型及化工型两类。其中:炼油型生产的MTBE主要用于无铅汽油提高辛烷值的调和组分;化工型又分为丁烯-1精制、高纯度异丁烯生产和丁烯水合制甲乙酮等装置。从反应器设计分类又可分为外循环式固定床、膨胀床、混相床和催化蒸馏塔等。MTBE反应器床层反应温度30-60℃、异丁烯含量15%-50%、醇烯比0.95-1.05和空速2-5/h的工艺条件下,均有着优良的催化性能和较长的使用寿命。异丁烯转化率可达95%以上,最高可达99.9%,选择性可达98%以上,在正常操作条件下,每吨干剂催化树脂可产成品5000吨以上,最高可达10000吨。
MTBE树脂催化剂是用苯乙烯和二乙烯苯在特殊制孔剂的作用下经悬浮共聚成的珠体,再经磺化反应得到具有大孔网状、带有磺酸基团的高分子聚合物。
该催化剂的催化性能主要由交换容量和孔结构决定,物化指标如下表所示:
指标名称 | A-15(美) | A-35(美) | 国内催化剂A | 国内催化剂B | 催化剂D |
质量全交换容量mmol/g[H+] | 4.85 | 5.16 | 4.50 | 4.70 | ≥5.20 |
机械强度% | ≥95 | ||||
温视密度ml | 0.77 | 0.80 | 0.75~0.85 | 0.75~0.85 | |
湿真密度g/ml | 1.15~1.25 | ||||
平均孔径nm | 25 | 24 | 20~26 | 40 | 38~45 |
比表面积m2/g | 45 | 45 | 40~45 | 40~70 | 30-50 |
粒度%(0.355-1.25mm) | ≥95 | ||||
含水量% | 52~57 | 51~57 | 48~58 | 50~58 | 48~58 |
风干水份% | 45±3 | ||||
最高使用温度℃ | 120 | 120 | 120 | 120 | 120 |
出厂型式 | H或Na | H | H | ||
外观 | 深灰色 | 灰色 | 灰色 |
其它
汽油碱洗活化剂
单磺酸基酞菁钴和二磺酸基酞菁钴在不同浓度的碱溶液中,对不同硫醇的脱除效果,同时考察了7种活化剂对脱硫醇效果的影响.脱硫醇活化剂的有效成份是一种季铵类物质。在反应中:
1、 可以增加硫醇在活化剂中的溶解度,在反应器床层表面起表面活性作用;
2、 活化剂又起到碱催化作用,同时又起到活化效果,不需要硫醇分子发生相转移,即可发生氧化反应。因此对高级硫醇有较高的脱除率,使总的脱臭率增加率达到90-95%;
3、 可以作为清洁剂,将床层表面附的胶质,芳烃类物质洗涤下来,使催化剂维持高活性,长寿命;
4、 活化剂脱臭方法废碱液排放量小,环保意义明显。
技术指标
项目 | 质量指标 |
外观 | 淡黄至红棕色液体 |
活性组分(1)含量% | ≥8.0 |
活性组分(2)含量% | ≥1.5 |
密度(20℃),g/cm3 | 0.81-0.84 |
烷基化
利用加成或置换反应将烷基引入有机物分子中的反应过程。烷基化反应作为一种重要的合成手段﹐广泛应用于许多化工生产过程。
沿革1879年﹐德国人M.M.贝尔松首先用三氯化铝作催化剂由苯和乙烯制得乙苯﹐但直至20世纪40年代﹐此法才实现工业化。30年代末建立了第一套用硫酸作催化剂的异丁烷与丁烯的烷基化反应﹐生产高辛烷值汽油调合组分的工业装置﹔随着第二次世界大战对航空汽油的大量需要﹐该法迅速发展。40年代﹐美国壳牌公司开发了用硫酸作催化剂由丙烯与苯液相烷基化制异丙苯的生产装置﹐与此同时还开发了用磷酸硅藻土作催化剂的气相烷基化法。以后于1959年由美国环球油品公司开发的阿尔卡法和1975年由美国莫比尔石油公司开发的莫比尔-贝捷法﹐都是用气相催化法生产乙苯的烷基化装置。
反应类型烷基化反应可分为热烷基化和催化烷基化两种。由于热烷基化反应温度高﹐易产生热解等副反应﹐所以工业上都采用催化烷基化法。主要的催化烷基化有﹕
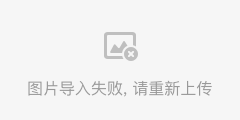
烷烃的烷基化﹐如用异丁烯使异丁烷烷基化得高辛烷值汽油组分﹕
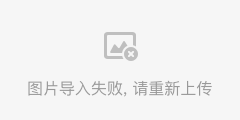
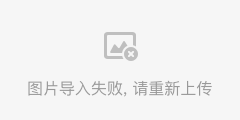
芳烃的烷基化﹐如用乙烯使苯烷基化﹕
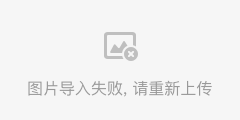
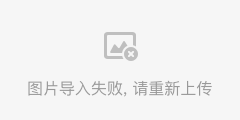
酚类的烷基化﹐如用异丁烯使对甲酚烷基化﹕
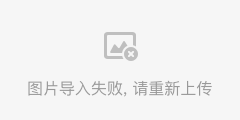
催化剂工业上催化烷基化过程可分为液相法和气相法两种﹐所用催化剂互不相同。
液相烷基化催化剂主要用酸催化剂和弗瑞德-克来福特催化剂。
常用的酸催化剂有硫酸和氢氟酸。异丁烷用丙烯﹑丁烯进行的烷基化﹐目前以应用氢氟酸为多。苯用高碳烯烃或用C10~C18的氯化烷进行的烷基化﹐以及酚类的烷基化﹐则以应用硫酸为多。
弗瑞德-克来福特催化剂有氯化铝-氯化氢和氟化硼-氟化氢等﹐常用于苯与乙烯﹑丙烯以及高碳烯烃的烷基化﹐以及酚类的烷基化等过程。
气相烷基化催化剂主要用固体酸催化剂、金属氧化物催化剂和分子筛催化剂。固体酸催化剂有磷酸硅藻土等﹐用于苯与乙烯﹑丙烯﹐萘与丙烯的烷基化﹔金属氧化物催化剂有氧化铝﹑氧化铝-氧化硅﹑镁和铁的氧化物以及活性白土等﹐常用于苯与乙烯﹑酚和甲醇进行烷基化反应等。分子筛催化剂有ZSM-5型分子筛催化剂﹐主要用于苯与乙烯进行烷基化的过程。
过程条件烷基化是放热反应﹐反应热一般为80~120kJ/mol﹐因此﹐反应热的转移至关重要。从热力学观点来看﹐在很宽的温度范围内﹐烷基化均可使反应接近完全﹐只在温度很高时﹐才有明显的逆反应。液相反应所用催化剂一般活性较高﹐反应可在较低温度(0~100℃)下进行。采用适当的压力是为了维持反应物呈液相以及调节反应温度。为了减少烯烃的聚合以及多烷基化物的生成﹐常采用较高的烷烯或苯烯摩尔比(5-14﹕1)以及较短的停留时间。工业上为了使苯和烷基化剂得到有效利用﹐常将多烷基化物循环送回反应器﹐使之与苯发生烷基转移反应﹐以生成一烷基苯。原料中的乙炔﹑硫化物和水对催化剂有害﹐应预先除去。气相烷基化所用催化剂活性一般较低﹐故须在较高温度(150~620℃下进行反应﹐压力通常在1.4~4.1MPa﹐苯烯摩尔比为3~20﹕1。原料中的硫化物及水易使催化剂中毒﹐必须预先脱除。
反应器液相烷基化可在卧式或塔式反应器内进行﹐反应热可由反应器(卧式)内的冷却管或蒸发制冷而移除。为了保证反应物和酸的充分混合以及控制一定的停留时间﹐可采用搅拌﹑循环﹑加挡板或采用多级串联式反应器。由于催化剂有腐蚀性﹐反应器须用耐腐蚀材料衬里。气相烷基化对设备无腐蚀﹐一般使用列管式固定床反应器﹐也可用多段激冷式绝热反应器。
工业应用在石油炼制工业中﹐烷基化过程主要用于生产高辛烷值汽油的调合组分。例如﹕异丁烷用丙烯或丁烯进行烷基化﹐得到烷基化油﹐这是烷基化过程的最早应用。苯用丙烯进行烷基化生产异丙苯﹐开始也是作为汽油的掺合剂﹐现在是生产苯酚和丙酮的主要原料。现在烷基化过程主要用于生成多种重要有机产品。例如﹕苯用乙烯进行烷基化生产乙苯﹐苯用C10~C18烯烃进行烷基化生产合成洗涤剂原料高碳数烷基苯。此外﹐甲苯用丙烯进行烷基化得到的甲基异丙苯﹐经过氧化及异构化可生产间甲酚﹔甲苯与乙烯反应可生产乙烯基甲苯。间二甲苯经异丁基化可生产二甲苯麝香。1﹐2﹐4-三甲苯用甲醇或氯甲烷进行烷基化﹐可生产1﹐2﹐4﹐5-四甲苯。苯酚用异丁烯进行烷基化可生成叔丁基苯酚﹐用二异丁烯进行烷基化可生成对辛基苯酚。
我国炼油企业的HF烷基化装置是从美国菲利浦斯(Phillips)石油公司引进专利技术,利用催化裂化装置液态烃中C4馏份作为原料,生产研究法辛烷值(RON94~97)的烷基化油,该油可与催化裂化汽油调合成无铜优质车用汽油,也可调合生产其它高辛烷值汽油或航空汽油。
烷基化装置所生产的汽油具有辛烷值高(RON94~97,MON92~94)敏感性小,调合性好,挥发性好和燃烧清洁等优点。因此,它是车用汽油的理想组份。
世界第一套HF烷基化装置是在1942年菲利浦斯石油公司所属的博格炼油厂建成的。经40多年的发展改进,菲利浦斯HF烷基化工艺日趋完善。
第四章 炼油化学药剂
原油电脱盐用破乳剂、脱钙剂
原油在开采之前,油与水在地下并不发生乳化。只是在原油从地下采出时要经过地层的空隙与水和空气混合在一起,又经过泵送的搅动,才形成乳化液。一般在油田都采取破乳剂进行了原油就地脱水脱盐的措施,使外输原油含水量达到一定的标准。如前苏联规定商品原油含水量不大于0.2%,含盐量不大于40mg/L;美国、加拿大和欧洲各国规定含水量不大于0.5%,含盐量不大于50mg/L;我国规定外输原油含水量不大于0.5%,含盐量不大于50mg/L。但是这仍然达不到炼油厂加工装置对原油质量的要求。因此在炼油厂的第一步加工工序,就是要进行原油的预处理——脱盐脱水。
另一个值得注意的动向是当前强化采油技术的应用。这一增产措施是采用表面活性剂或聚合物驱油,碱液驱油,使得表面活性剂或碱液进入油层,故形成的原油破乳液会按比例增加,增大了脱水脱盐的难度。随着油田热采技术(注热水、注蒸汽或火烧等)的开发和工业推广,我国稠油生产很快。稠油是指高粘度、高相对密度的重质原油,它的主要特征是胶质、沥青质和重金属含量高,形成的乳化液稳定性强,成了原油脱水脱盐不可忽视的课题。
盐在炼油过程中的危害:
原油中的盐分在经过蒸馏之后大多集中于重介质油中,在催化裂化装置中,钠等金属盐可以降低催化剂的水热稳定性,中和了催化剂的酸性。被钠污染的催化剂在再生过程中容易发生熔融,破坏分子筛晶格和筛孔,使催化剂的选择性变差。所以,生产中要求进料中钠离子不大于1mg/L。
原料中的盐份还可以造成其它如加氢裂化、加氢脱硫催化剂污染中毒;加速加热炉结焦;用于延迟焦化进料,会增加石油焦的灰分含量;用于溶剂脱沥青,会降低沥青的伸长度等。
我国各炼厂大都采用两级脱盐脱水流程。原油自油罐抽出后,先与淡水、破乳剂按比例混合,经加热到规定温度,送入一级脱盐罐,一级电脱盐的脱盐率在90%~95%之间,在进入二级脱盐之前,仍需注入淡水,一级注水是为了溶解悬浮的盐粒,二级注水是为了增大原油中的水量,以增大水滴的偶极聚结力。
以往原油脱盐只是作为一种防腐蚀、稳定操作的手段。现在脱盐技术要起到保护后续加工工艺所用催化剂不受污染的作用。
破乳剂
破乳剂的发展过程
从1914年,威士勃.尼契儿(WSBar.nichel)在乳化原油中加入了0.1%FeSO4溶液,发现了破乳现象以后,原油破乳剂的研究已有80多年的历史,其发展历程见表1。
年代 | 用量(×10-6) | 化学成分 |
20世纪20年代 | 1000 | 脂肪酸盐,环烷酸盐;芳香与烷基芳烃磺酸盐;磺化蓖麻油和蓖麻油 |
20世纪30年代 | 1000 | 石油磺酸盐,石油磺酸皂,氧化蓖麻油和硫代琥珀酸酯 |
自1935年起 | 500~1000 | 脂肪酸乙氧基化物,脂肪族醇和烷基酚 |
自1950年起 | 100 | 环氧乙烷与环氧丙烷共聚物,P-烷基酚,甲醛树脂+环氧乙烷与环氧丙烷及其变体 |
自1965年起 | 30~50 | 环氧化胺 |
自1976年起 | 10~30 | 环氧化的环状P-烷基酚,甲醛树脂与复杂变体 |
自1985年起 | 5~20 | 聚氨酯和掺合剂 |
破乳剂的合成路线及种类
破乳剂的研究思路
原油破乳剂是以非离子型的聚氧丙烯聚氧乙烯嵌段聚合物为主,其研究思路可以概括为10个字,即“改头、换尾、加骨、交联、复配”。
“改头”是指选择、设计、合成具有活泼氢的起始剂。例如OP型破乳剂是以烷基酚为起始剂,运用化学结构相似理论,可以将烷基酚与甲醛缩合而得到烷基苯酚甲醛树脂作为起始剂与环氧乙烷、环氧丙烷二段或三段聚合而得到新一类破乳剂(如AR或AF型)。
平平加或OP型
它是以高碳醇或烷基酚为起始剂与环氧乙烷的共聚物。
平平加型:R-O-(CH2CH2O)nH
OP型:
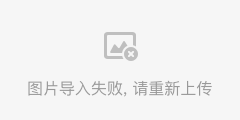
“换尾”是指利用化学方法改变嵌段聚合物的端基,将同类或不同类的嵌段聚合物端基进行酯化,而得到新一类的破乳剂化合物,此方法是增大破乳剂分子量的有效方法之一。
“交联”一般来讲,很多超高分子量的聚合物用作破乳剂,具有令人满意的效果。因此,采用二异氰酸酯等与具有数千分子量的聚氧乙烯聚氧丙烯嵌段聚合物交联,以达到增高分子量、提高破乳效果的目的。
“复配”是指应用表面活性剂的协同效应进行破乳剂的复配试验,即将两种或两种以上的破乳剂按适当比例复配,或在其中加入少量助剂,提高破乳脱水效果,改善脱出水的水色。
SP型
以高碳醇为起始剂与环氧乙烷、环氧丙烷的共聚物,如SP169:C18H37O(C3H6O)m(C2H4O)n(C3H6O)pH。
BE、BP型及其改性产品
以丙二醇为起始剂与环氧乙烷、环氧丙烷的二段或三段共聚物及其改性产品。
a. 聚氧丙烯聚氧乙烯丙二醇醚(BE型);
b. 聚氧丙烯聚氧乙烯聚氧丙烯丙二醇醚(BP型);
c. 聚氧乙烯聚氧丙烯丙二醇醚松香酸酯;
d. 聚氧乙烯聚氧丙烯丙二醇醚的二元羧酸扩链产物。
GP型
以丙三醇为起始剂的三段共聚物,聚氧丙烯聚氧乙烯聚氧丙烯丙三醇醚。
AR、AF型及其改性产品
以烷基苯酚醛树脂为起始剂的二元、三元共聚物及其改性产品。
a. 聚氧乙烯聚氧丙烯烷基苯酚甲醛树脂(AR型);
b. 聚氧丙烯聚氧乙烯聚氧丙烯烷基苯酚醛树脂(AF型);
c. 聚氧丙烯聚氧乙烯聚氧丙烯烷基苯酚醛树脂羧酸酯。
AE、AP型及其改性产品
从乙二胺或多乙烯多胺为起始剂的二元、三元共聚物及其改性产品
a. 聚氧乙烯聚氧丙烯乙二胺(AE型);
b. 聚氧丙烯聚氧乙烯聚氧丙烯二乙烯三胺(AP型);
c. 聚氧乙烯聚氧丙烯聚氧乙烯二乙烯三胺的二元羧酸扩链产物。
聚氧乙烯聚氧丙烯酚胺树脂(PFA)型
含硅破乳剂
聚氧乙烯聚氧丙烯甲基硅油
磷酸酯破乳剂
聚氧乙烯聚氧丙烯烷基磷酸酯
硼酸酯破乳剂
聚氧丙烯硼酸酯
此外,还有一些高分子非离子、阳离子和两性表面活性剂也可用作破乳剂。
破乳剂研究、生产和应用存在的问题及改进措施
l 破乳剂的破乳机理研究滞后于破乳剂的应用
院校及科研院所应紧密结合现场实际,加强破乳剂机理研究,为破乳剂的研究、生产和使用提供理论基础。
l 新型高效破乳剂的研究进展缓慢
尽管目前破乳剂的品种有200多个牌号,但原剂品种仅有40多个,众多的产品是复配剂。近几年来,研制者、生产厂家、用户均把复配看作能推出新品种、解决破乳难题的捷径,在相当程度上制约了新型高效多功能破乳剂的研究与应用。因此,新型破乳剂的研究可通过使用扩链剂提高传统破乳剂的分子量,并在新型高分子破乳剂中引入含硅、含磷、含硼的元素,使破乳剂能做到高效、低耗、一剂多效的功能。
l 反向破乳剂的开发和应用值得重视
反向破乳剂实质上是水包油型原油乳状液的破乳剂。随着三次采油技术的不断应用,水包油乳化原油破乳剂也越来越引起人们的重视。
l 破乳剂的筛选和使用浓度的优化方法有待进一步拓展
目前破乳剂的筛选和使用浓度的优化主要用瓶试法,但同时有许多学者提出的极性法、介电常数法和流动电位法值得重视,前两者用于油包水乳化原油破乳剂,后者用于水包油乳化原油破乳剂。
脱钙剂
羟基乙叉二膦酸二钠,分子式:C2H6O7P2Na2•;4H2O,分子量:322。
性能:螯合性能强,可与多种金属络合(如:铁、铜、铝、锌、钙、镁等)。在冷却水,锅炉水处理中做阻垢剂,化学稳定性好。耐高温,在200℃以下都能起良好作用,不分解.PH值可调性,可根据不同的用途调节PH值的酸碱性。在化学工业中,作为分离杂质的添加剂,掩蔽剂,过氧化物的稳定剂。是一种新的水质稳定剂,是EDTA的替代产品。
优点:螯合性能强、阻垢性能强、稳定性好、耐高温、PH值酸碱性可调。该产品外观为粉末状解决了液体酸碱反应沸锅、结晶析出等问题.避免了人员伤亡为企业生产安全方面提高了标准。且粒度可以调整,该产品为固体所以在运输及存放方面相当方便。
另外一种脱钙剂是在多聚磷酸、羟基喹啉等螯合剂中加入适量表面活性剂、季铵盐、季鏻盐或冠醚。组成如下:60~90%的螯合剂,其中螯合剂选自一元羧酸、二元羧酸、有机膦酸、氨基酸及其衍生物、多聚磷酸或羟基喹啉中的至少一种;1~30%的表面活性剂,其中表面活性剂为平均分子量为100~4000含1~18个碳原子的单醇或二醇的聚合物、季铵盐、季鏻盐或冠醚中的至少一种;0~15%的破乳剂或表面活性剂。
缓蚀剂
在石油工业中,研究和开发中性和酸性介质缓蚀剂,对保护钢铁设备具有重要的经济价值和现实意义。
缓蚀剂的加入抑制了金属在腐蚀介质中的电化学过程,减缓了电化学腐蚀速度。缓蚀剂的存在可能分别增大阴极极化或阳极极化,也可能同时增大阴极极化和阳极极化。
缓蚀剂能与金属或腐蚀介质的离子发生反应,在金属表面生成不溶或难溶的具有保护作用的各种膜层,阻止腐蚀过程,起到了缓蚀作用。
目前,许多有机缓蚀剂属于表面活性物质,其分子由亲水疏油的极性基和亲油疏水的非极性基组成。在介质中,极性基定向吸附排列在金属表面,从表面排除水分子和氢离子等致腐离子,使之难于接近金属表面,从而起到缓蚀作用。
常见的缓蚀剂包括咪唑啉型和非咪唑啉型等缓蚀剂,若按照缓蚀剂溶解性能的不同,还可以分成油溶型或水溶型。目前市场上油溶型的缓蚀剂比较多见,但油溶型缓蚀剂由于原材料成本高,加之由于油溶型缓蚀剂中含有大量的有机溶剂,在运输和使用过程中存在着较大的安全隐患。
水溶性缓蚀剂要求水中的溶解性良好,加入原油后,能在容器内壁吸附并形成多层保护膜,能有效防止原油炼制过程中产生的盐酸、硫化氢、二氧化碳以及矿物质对容器的腐蚀,使用后设备内表面无点蚀、坑蚀等现象,最好可在较宽的pH值及温度范围(<150℃)内使用,一般工业中的使用浓度为10-30ppm。另外要注意的是,常减压蒸馏的缓蚀剂在使用中不能影响后续炼油过程中的催化剂性能。
以合成的咪唑啉衍生物和炔氧甲基季铵盐为主要组分的缓蚀剂,能成功抑制HCI-H2S-H2O体系的腐蚀。生产实践证明,当pH值控制在6.0-8.0时,常减压蒸馏中的塔顶露点区的腐蚀率可以控制在0.06mm/a以下,远低于单纯注氨时的0.32mm/a的腐蚀速率,而且对汽油质量无不良影响。
在工业生产中,咪唑啉型缓蚀剂中还要添加分散剂、增效剂等其它助剂,用于低硫和高硫以及高酸原油的加工。
总之,缓蚀剂防腐在石油工业中已推广应用,并有良好的应用前景。具体操作时可参考上述经验初步选定缓蚀剂的类型,再经过实验确定缓蚀剂的具体种类及其配比。
高温缓蚀剂
目前所用的高温缓蚀剂是烷基苯基亚磷酸酯,能够在高温(250-350℃)部使用,是阳极抑制型缓蚀剂,可以遏止炼油过程中环烷酸在高温气相部位的环烷酸的腐蚀。在常减压蒸馏过程中的高温酸腐蚀部位如下图红色区域所示:
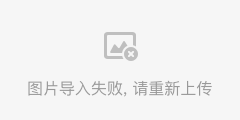
水处理剂
炼油行业既是能源生产大户,也是资源和能源消耗大户。尤其是在水消耗上,和国外相比,我国的炼油行业存在很大的差距,已经成为我国五大工业污水排放重点治理行业之一。
在炼厂水的管理中,由于循环水系统由于来回于生产装置之间。频繁的物料泄漏,使得系统水质和设备的严重污染,造成了系统中菌藻的大量繁殖,粘泥滋生,设备严重腐蚀,粘泥油污堵塞水冷器管束,为了处理物料泄漏,置换了大量的新水和排掉了大量的药剂,系统长期降低浓缩倍数运行,形成了循环水系统的恶性循环。
在水处理中经常用填加化学药剂的方法来改善水的品质,常用的化学药剂有絮凝剂、凝聚剂、阻垢分散剂、缓蚀剂、杀菌灭藻剂、污泥脱水剂、离子交换树脂、清洗剂、预膜剂、螯合剂、混凝脱色剂、脱磷剂、活性炭等。
絮凝剂
能使水溶液中的溶质、胶体或者悬浮颗粒产生絮状物沉淀的物质,可分为无机、有机和微生物三大类别。
无机絮凝剂:铝系(明矾、硫酸铝、铝酸钠、聚合氯化铝)、铁系等
聚合氯化铝
为无机高分子化合物,分子式:[AL2(OH)nCL6n]m,是介于氯化铝和氢氧化铝之间的产物,通过羟基而架桥聚合,分子中带有数量不等的羟基。无色或黄色树脂状固体。其溶液为无色或黄褐色透明液体,有时因含杂质而呈灰黑色粘液。液体产品中氧化铝含量为8%以上,固体产品中氧化铝含量为20%~40%。有较强的架桥吸附性能,易溶于水,水解过程中伴随有电化学、凝聚、吸附和沉淀等物理化学过程。有腐蚀性。
有机絮凝剂:
阴离子(聚丙烯酸钠、聚苯乙烯磺酸钠等)
阳离子(丙烯酰胺-甲基丙烯酸乙酯基三甲基氯化铵共聚物、丙烯酸胺-二甲基二烯丙基氯化铵共聚物)
非离子(聚乙烯醇、聚丙烯酰胺、聚氧化乙烯)
气体分离用MDEA
N-甲基二乙醇胺(MDEA),是一种叔胺类物质。分子式为CH3N(CH2CH2OH)2,分子量为119.16,比重1.0418,沸点247℃,在12℃时的粘度为101cP,凝固点–48℃,能全部溶于水中。本生产工艺采用国际上最先进的管道化反应,即环氧乙烷与纯一甲胺在管式反应器中,2.5MPa压力下进行反应,经蒸馏,精馏得到MDEA,纯度达到97%以上。
原油一次加工和二次加工的各生产装置都有气体产出,总称为炼厂气,就组成而言,主要有氢、甲烷、由2个碳原子组成的乙烷和乙烯、由3个碳原子组成的丙烷和丙烯、由4个碳原子组成的丁烷和丁烯等。它们的主要用途是作为生产汽油的原料和石油化工原料以及生产氢气和氨。发展炼油厂气加工的前提是要对炼厂气先分离后利用。炼厂气经分离作化工原料的比重增加,如分出较纯的乙烯可作乙苯;分出较纯的丙烯可作聚丙烯等
炼厂气体的脱硫,目前主要采用醇胺法,醇胺法脱硫开始应用的是一乙醇胺(MEA)、二乙醇胺(DEA),后来又在克劳斯尾气装置上使用二异丙醇胺(DIPA)。80年代我国研制开发了新型选择性脱硫溶剂N-甲基二乙醇胺(MDEA),开始在天然气脱硫装置上应用;进入90年代,MDEA在炼厂气脱硫装置上也开始应用。
MDEA是Fluor公司早年开发的脱硫溶剂。目前,它作为新一代脱硫溶剂已在天然气脱硫、煤气化脱硫以及炼厂脱硫中得到广泛应用。由于MDEA对H2S有很高的选择性和较低的能耗,被用于克劳斯原料气提浓,斯科特法尾气处理,低热值气体脱硫等过程。
从1993年开始,由于中国石化总公司系统内炼厂因加工能力提高,或因掺炼高硫原油,均出现过干气、液态烃脱硫深度不够的情况。在这种情况下以MDEA为主剂的高效脱硫剂充分显示出它硫容量大,选择性好的优点。由于该剂使用浓度可高达50%,因此它的循环量可大大减少,它可在高气液比或高液液比下吸收,MDEA的再生解吸热又比上述三种胺小,从而降低了再生耗热,总之,这些特点归纳一点,就是用MDEA脱酸性气可大幅降低能耗,最终降低操作成本。
南京化工研究院曾对二乙醇胺等五种溶剂作过对比试验,试验结果如下表所示。
五种脱硫剂对比试验
脱硫剂 | 脱H2S效率% | 再生气中H2S% |
二乙醇胺2.5克分子/升 | 40~50 | 8 |
二异丙醇胺2.5克分子/升 | 85~90 | 10~14 |
聚乙二醇二甲醚 | 95 | 25 |
65%聚乙二醇二甲醚+30%二异丙醇胺+5%水 | 80 | 5~8 |
N-甲基二乙醇胺MDEA | 94 | 33 |
从上表看出聚乙二醇二甲醚的各方面性能与MDEA比,不相上下。但须看到,用它做溶剂是一种物理吸收过程,要达到相同的处理能力,它的耗量比MDEA多,增加了脱硫成本。
除了炼厂气体脱硫外,MDEA在合成氨脱碳工艺上也有独特之处。MDEA的吸收CO2和再生耗能较单乙醇胺(MEA)为低,而且它对非极性气体如氢、氮、甲醇、甲烷及其它高级烃类化合物的溶解度极低,自身损失很少。MDEA与CO2反应仅生成碳酸氢盐而不生成氨基甲酸酯,吸收过程不会降解,日常补充量大大减少。MDEA对碳钢没有腐蚀,本身碱性很弱,且不产生热降解产物与化学降解产物,在再生解吸段出来的湿CO2因其温度不高(70℃左右),对碳钢的腐蚀是轻微的。目前国内有五套合成氨用MDEA脱碳,设备全部采用碳钢结构。由于MDEA本身的一些化学特征,使其用于合成气脱CO2过程中大大节约能耗;对于新建装置而言,由于脱碳系统可采用碳钢设备,故可使投资减小。再者脱出的CO2纯度最高可达99.9%,不管后续尿素装置,还是进一步利用CO2都是有利的。
环丁砜
又称二氧化四氢噻吩。常温下为无色、无臭固体,熔点28.5℃,能与水以任何比例混合,也溶于芳烃和醇类,是一种对质子非常稳定的工业溶剂。主要用作芳烃抽提的萃取剂,也用作天然气、炼厂气、合成气的净化、脱硫溶剂,以及橡胶、塑料的溶剂等。
环丁砜由丁二烯和二氧化硫反应制得,工业生产过程主要有两步:①由丁二烯和二氧化硫在少量阻聚剂(对苯二酚)存在下合成环丁烯砜,温度100~150℃,压力1.2~3.0MPa,反应时间2~3h。产物经精制除去未反应的丁二烯和二氧化硫,得到一定纯度的环丁烯砜。②在骨架镍催化剂存在下,用异丙醇或水作溶剂,环丁烯砜进行加氢、精制可得成品环丁砜。
阻垢剂
随着原油质量的变重变差,石油加工条件也变得更为苛刻,石油加工设备和管道的结垢问题日益突出。为此,国内外都进行了广泛的研究,提出了一系列减少结垢的方法,如改变操作条件,改进设备,在加工设备和管道时对其内表面进行化学钝化处理等。但是这些方法都有局限性,未能从根本上抑制结垢的产生。随着对结垢研究的深入,开发出了抑制结垢的阻垢剂。用阻垢剂来抑制石油加工设备和管道结垢的方法简便、有效、经济,因此在国内外得到了广泛的应用。
结垢原因
石油加工的很多设备和管道都存在结垢现象,如换热器、再生器、反应器、加热炉等,但是引起结垢的原因却有差别。经过对多种垢样组成的分析及与加工油料组成的比较,可以确定结垢物中含有有机物和无机物。导致无机物形成的原因有二个:一是盐类物质的析出;二是杂质颗粒的沉积。
无机垢的形成原因可由垢样的组成测试结果分析出来,其主要受油料性质和流速的影响。而有机垢的形成就比较复杂,也很难完全被鉴定。经分析后发现,有机垢分子式可表示为(CHm)n。在不同的设备和管道中有机垢形成的原因和过程有很大的差异,m和n的数值会在较大范围内变化,是化学反应和物理过程的综合结果。形成有机垢的化学反应有三类。第一类是自由基链反应,结果形成高分子聚合物;第二类是含有多环的烃类如重芳烃、胶质、沥青质在一定的温度条件下发生侧链断裂、多环缩合反应,生成大分子稠环物质;第三类是烃类的热分解反应。
温度对有机垢的形成有很大的影响。当油料处在较高的加工温度(500℃左右)时,高温使烃类发生热裂解反应,并使自由基链反应速度加快,生成焦炭和高分子聚合物,而设备和管道材质中的镍和铁又对脱氢生焦反应有催化作用,因此有机垢在设备和管道表面很快形成。此时形成的结垢比较坚硬,其碳氢比接近于焦炭,因此高温下的结垢常被称为结焦。当油料处在相对较低的加工温度(350℃左右)时,自由基链反应生成的大分子聚合物和因受热形成的大分子稠环芳烃,随着分子逐渐增大溶解度逐渐变小,沉积在设备和管道内表面,进一步的脱氢缩合形成有机垢,此种情况下生成的结垢较软,碳氢比较小。
阻垢剂种类和性能
国外阻垢剂一般可分成二类,一类用于温度为500℃左右的设备和管道,如热裂化、延迟焦化、焦化等装置,这类阻垢剂可抑制或减少高温时由烃类热裂解等反应引起的生焦,因此常被称为阻焦剂或防焦剂。另一类阻垢剂的使用温度相对较低,如:用于催化裂化油浆系统、减压塔底渣油系统等。但是也有一些阻垢剂可在250~550℃的温度范围内使用,即既能阻止高温结焦,也可阻止低温结垢。
国内的阻垢剂都是针对石油加工过程某个易结垢部位研制的,针对性强,阻垢效果也十分显着,因此阻垢剂一般按用途进行分类,分成催化裂化油浆阻垢剂、加氢裂化原料阻垢剂、减压渣油阻垢剂等。但是无论怎样,所有的阻垢剂都具有如下一种或几种性能。
(1)清净分散性。能阻止油料中的腐蚀产物、盐类和杂质颗粒聚集沉积,减少无机垢的生成。
(2)抗氧化性。与被氧化的烃自由基形成惰性分子,使链反应中止,不能形成大分子聚合物,减少有机垢的生成。
(3)阻聚合性。阻止烃分子的聚合,减少有机垢的生成。
(4)钝化金属表面性。使设备和管道的材质在高温下不能对脱氢生焦起催化作用。
(5)抗腐蚀性和表面改性功能,在设备和管道表面形成保护膜,减少腐蚀产物的生成,保持设备和管道的内表面的光洁。
除此之外,阻垢剂还应具有:油溶性,与加工油料能均匀混合;粘度小,易流动,便于使用;对后序加工工艺和产品性质不会产生不良的影响。在使用温度下不分解,以及无毒等理化性质。
阻垢剂产品及工业应用
3.1国外阻垢剂
美国是最早使用石油加工过程阻垢剂的国家,在70年代已将阻垢剂用于常减压蒸馏、加氢脱硫、加氢裂化、催化重整等装置的换热器等设备。80年代又将阻垢剂用于催化裂化油浆系统。在阻垢剂方面研究最多的是NalcoChemical公司和BatzProche公司,各自的阻垢剂产品有Nalco5262,5264,6265等;BatzAF12,AF18,AF114等。这些产品都有适用性广的特点,能用于不同性质的油料,有些为抗垢和抗焦的双功能阻垢剂,如NalcoChemical公司的9CR945,它既能抑制换热器结垢,又能减少加热炉内壁的结焦。但是这些阻垢剂产品基本上未进入国内市场。
国内曾引进过日本栗田水处理公司的Petrotech4030阻垢剂,据该公司介绍,该阻垢剂能用于加氢裂化原料换热器、催化油浆系统、延迟焦化装置等,其相对密度d420为1.00,闪点44℃,凝点-30℃,运动粘度(50℃)5.5mm2/s。在90年代初,金陵石油化工公司炼油厂和兰州炼油化工总厂曾短时间内使用过Petrotech4030阻垢剂。兰州炼油化工总厂将该阻垢剂用于催化裂化油浆系统,加入量为200μg/g。当分馏塔底温度小于370℃时,装置运行半年以上,油浆系统无结垢现象且热平衡调控自如。当分馏塔底温度大于370℃时,尽管在油浆系统注入200~500μg/g的Petrotech4030阻垢剂,但是装置运行了10~20天,油浆系统即出现结垢。表明当分馏塔底温度大于370℃时,Petrotech4030阻垢剂无阻垢作用。
金陵重油催化裂化装置曾在同一开工周期内使用过Petrotech4030和SF2(华东理工大学石油加工研究所研制)二种阻垢剂,二者的使用情况如表1。以油浆蒸汽发生器的油浆出口温度的变化来反映油浆系统结垢情况。可以看出,尽管在SF2阻垢剂使用期间,油浆的密度较大,系统温度较高,但SF2阻垢剂与Petrotech4030阻垢剂阻垢效果相同。而且,SF2阻垢剂经高桥石油化工公司上海炼油厂催化裂化装置使用后表明:分馏塔底温度在370℃以上还具有良好的抗垢性能,同时,在使用过程中不需要Petrotech4030阻垢剂那样要使用氮气保护。
3.2国内的阻垢剂产品及工业应用
近几年,国内阻垢剂发展很快,一般是多效复合剂,为易于流动的液体,可用泵直接注入加工油料,加入量为5~200μg/g。在使用阻垢剂时,建议在设备和管道开工后的前三、四周内,使用剂量加倍,那幺阻垢剂会在设备和管道表面形成一个良好的保护层,减少金属表面的腐蚀和对结垢的作用。
3.2.1催化裂化油浆阻垢剂
催化裂化油浆阻垢剂用于抑制重油催化裂化油浆系统的结垢,具有良好的分散性和抗沥青质缩合能力,是目前国内生产品种最多、使用最普遍的一种阻垢剂。除了上述品种外,催化裂化油浆阻垢剂主要有兰州炼油化工总厂的AF100、兰州西固吉野环境添加剂厂的GX03等。
目前国内大多数的大中型重油催化裂化装置都已使用阻垢剂。使用的效果说明,当油浆中注入阻垢剂后,换热效果随之明显好转,油浆返塔温度降低,蒸汽发生量增加。不仅如此,使用阻垢剂后,还使油浆系统压力降下降,油浆外甩量减少,轻质油收率增加。
抗焦剂
近年来,随着原油质量变重变差,石油加工过程中的设备和管线的结焦现象也越来越普遍和严重,结焦问题已日益成为影响安全生产和长周期操作的重要问题。结焦直接导致能耗,操作费用增加,也影响了装置的处理量,造成了很大的经济损失,更严重的是设备上的结焦,不仅增加了系统的压力,而且会使设备腐蚀、穿孔,给安全生产带来极大的危险。从目前国外]及国内近几年的研究和实践证明,在原料中加入微量抗焦剂来解决结焦问题是一个较为简便可行、经济有效的方法。国外研究出的抗焦剂已有多种类型,而国内对这方面的研究尚处于起步阶段,国内的抗焦剂与国外的相比,还存在很大差距,因此迫切需要研制出高效、对设备有缓蚀性的抗焦剂。
第五章 炼油添加剂
随着近代工业的发展,对石油产品质量的要求也在不断提高。由于石油中天然组分的局限性,单靠加工工艺本身,往往不能满足使用需要。为了提高石油产品的质量,以满足各种使用性能的要求,可加入一些特殊的油溶性有机化合物,这些化合物可以改善石油产品的各种性能,它们被称之为石油产品添加剂。采用加入添加剂来提高油品的使用性能,是既经济又有效的办法。
中华人民共和国标准局于1987年4月1日发布了石油添加剂分类专业标准(ZBE60003一87)以代替原石油部标准SY1981-73。该分类标准将石油添加剂分为四大类,80个组。四大类包括:润滑剂添加剂、燃料添加剂、复合添加剂、其它添加剂。
燃油添加剂
就是为了弥补燃油在某些性质上的缺陷并赋予燃油一些新的优良特性,在燃油中要加入的添加剂。其添加量从万分之几到百分之几。我们还可以从发动机的工作原理谈起。
燃油在发动机内的工作原理:经过滤清器除掉其中杂质,由油泵送到化油器或喷射装置中去燃烧做功,将其化学能转化为热能继而转化为机械能的过程。在燃油燃烧做功过程中,通常根据压力变化的发展特征将燃烧过程分为三个阶段:
诱导期:从电火花点燃到形成火焰中心,燃烧时间约占全部过程的15%。
明显燃烧期:从火焰中心形成到火焰传播至燃烧末端,明显燃烧期对发动机功率和经济性起决定作用的。
补燃期:燃油中残余油及不完全产物,继诱导期和明显燃烧期之后,从气缸压力下降到燃烧结束阶段。补燃期长,会使发动机经济效益降低。
燃油品质的高低对燃油消耗、尾气排放、动力性能至关重要。因为再好的燃料,在使用过程中也会有不完全燃烧的现象,尤其是随着电喷车的问世,由此产生的积碳如何清除的问题。如果使用了具有清洁作用的添加剂,就可以延缓这种现象,让燃料充分燃烧。而目前中国生产的燃油品质与国际上还有很大差异,因此在燃油中加入一些添加剂就有了必要,它可以更好地满足燃油的经济性、排放性、动力性,达到环保节能的作用。
燃油添加剂大体可分为供氧型添加剂、功能型添加剂和综合型添加剂三种.
1) 供氧型燃油添加剂
这种添加剂本身就是一种含氧的化合物(氧化剂),当其受热时会分解释放出氧参与燃烧.当气缸内出现火点(火花塞火花)或热点(柴油机压缩时的高温热点)时,其近处的添加剂受热即分解、放出O2,迅速同燃油分子结合燃烧,温度越高,分解越快,整体上加速燃烧过程的进行.其化学过程机理可能是添加剂中金属氧化物的氧有传递作用,能使燃料获得原子氧,进而产生大量自由基,从而促使燃料分子的链反应,实现燃料的迅速而完全的燃烧,高温使得这种过程更剧烈.
2) 功能型燃油添加剂
这种添加剂具有如下的功能.其一,可削弱燃油分子间的吸引力,使燃油分子团松化易分散开,从而增大燃油分子同空气的接触面,使油分子易于同空气中的O2结合,有利于实现迅速而完全的燃烧,如一些添加剂含有铝、镍、锰、铁等金属的有机盐,其离子能有效地降低燃油分子CH键的活化能,从而使燃料中活化分子数增多,这有利于燃油分子的分散和氧化燃烧.其二,可使燃油燃点降低,即促进燃油的着火.表1是两种燃油添加剂(分别称为1#、2#)使燃料燃点降低的试验结果.燃点降低,等于使燃油着火的温度降低,燃烧的滞燃期被缩短,促进燃料的着火,整个燃烧也被加速。
3) 综合型燃油添加剂
这种添加剂是供氧型和功能型两种添加剂的综合,具有供氧助燃、降低燃点、促进完全燃烧的综合功能.现今市场提供的燃油添加剂多属综合型添加剂.此外,随着环境保护意识的加强,对燃油添加剂的要求也越来越高,最新面市的一些添加剂,其功能不仅能提高发动机的动力与经济性能,而且还能降低内燃机排气中的CO、CH、NOx、SO2和SO3等有害物质的含量,这就要求添加剂既能缩短燃料的滞燃期并改善燃烧,又要促使燃气中的CO和CH争夺O2,变成无害的CO2和H2O,以阻止NO的形成和燃气中的NO与SO2向NO2和SO3的转化,因为后面这两种物质对环境的破坏性极大(如形成酸雨)。
使用燃油添加剂后的效果
一般来说市面上的添加剂都有降低油耗功效,另外还根据其特性配方不同还有保养发动机、清除积碳、环保等效果。下面我们就可以看看使用了燃油添加剂前后的部份汽车部件:化油器、汽缸盖、气门、喷油嘴的变化。
国内已经有很多的厂家和商家推出了自由品牌的燃油添加剂产品,从其检测报告和用户实际反应的情况来看,配兑了燃油添加剂后的汽柴油不仅能够充分燃烧降低排放污染,而且还能因为充分燃烧后感受到明显的动力增强,结合良好的驾驶习惯和操作更可以达到节油的效果。这些都是主观能够体会到的。还有一些则是在使用燃油添加剂后对发动机及油路的清洁效应。
以北京为例,机动车尾气排放对大气污染物中CO、HC、NOx的分担率分别为63.4%、73.5%和46%,非采暖期分担率更高。使用正确的燃油添加剂后,碳氢化合物HC下降26.6%,一氧化碳CO下降19.7%。不少省市已出台了要求推广和使用能有效清除积碳,减少尾气排放燃油添加剂的文件。在欧、美、日等发达国家在燃油质量监控、尾气排放达标等方面的管理十分严格,除遵循《世界燃油规范》的标准外,还提出更高的燃油标准。在这些国家,燃油添加剂的使用也非常普遍,要求也非常高,其目的就在于有效运用多种新型燃油添加剂的独特功能,使燃油成为不产生胶质、积碳并可以随时清除积碳的真正的清洁燃料。
汽油抗爆剂MMT
甲基环戊二烯三羰基锰简称MMT,1953年由雅富顿公司研制开发成功,1974年开始作为抗爆添加剂应用于美国含铅汽油中。1995年,美国EPA批准MMT可用于无铅汽油。
炼油界认为添加MMT可以有效、经济地提高汽油辛烷值,降低炼厂操作苛刻度,有助于减少汽油中芳烃、烯烃等含量,可以降低汽车CO、NOx等污染物排放。
雅富顿化学公司(AFTON)是全球领先的生产和销售燃油添加剂和润滑剂的跨国公司。该公司一直致力帮助客户提高和改进燃油添加剂和润滑剂的品质,进行了包括126辆汽车的行车试验和数千种包括MMT对发动机、汽车排放控制系统、对尾气催化器影响、人体健康、环境影响、锰的排放分析和暴露模型等试验。最终于1995年7月11日,美国环境保护局(EPA)批准雅富顿公司MMT用于传统无铅汽油的申请。清华大学泽华公司为雅富顿中国代理商
MMT在世界各地的发展
加拿大:加拿大是目前世界上MMT用量最大的国家,自1977年以来一直没有中断使用MMT,尽管在1997年6月由于汽车制造商的反对,发生了限制MMT贸易的禁令,但经过有关司法程序,加拿大政府在1998年解除了有关禁令,并赔偿了乙基公司在此期间的损失。MMT在加拿大二十多年的成功应用,为该添加剂在世界各地的推广树立了良好的典范。
俄罗斯:俄罗斯1997年颁布了无铅汽油国家标准ГОСТP51105-97,
于1998年1月1日起实施。标准规格中,标准80号汽油:锰含量≤50mg/L;普通91号汽油,高级95号汽油和超级98号汽油:锰含量≤18mg/L。
法国:法国环境部于1999年3月28日批准MMT用于铅替代汽油和无铅汽油。
英国:英国铅替代汽油BSI标准(草案)中,锰用量为7~36mg/L
中国:1996年,雅富顿公司开始在中国介绍MMT。1997年从年中开始,中国的各大城市陆续发布汽油无铅化公告,这给MMT在中国的应用带来机遇,也给炼油厂带来了可替代铅的抗爆剂选择。
1999年6月,中国国家环保总局发布车用汽油有害物质控制标准,规定车用汽油中的锰含量为不大于18mg/L。国家质量技术监督局于1999年12月28日发布了《车用无铅汽油GB17930》国家标准,标准中注明,无铅汽油中锰含量的检出限量为不大于0.018g/L。从环保方面和产品规格方面确认了MMT在我国无铅汽油中可以限量使用的合法性和科学性。
中国石油化工股份有限公司下发"石化股份科[2001]23号"文件中,明确提出"添加MMT是生产高标号车用无铅汽油可以采取的措施之一"。
中国石油天然气集团公司所属炼油厂大部分使用了MMT,从1998年下半年开始,大约有500万吨的无铅汽油中使用了MMT,使用MMT的炼油厂已获得了较好的经济效益。
另外,澳大利亚、印度、菲律宾、印度尼西亚等国家也开始使用,或者正在准备有关前期工作。
MMT对炼油工业的影响:
MMT可为炼油厂提供一种经济、有效的辛烷值改进剂。在无铅汽油中使用MMT不仅为炼油厂增加了汽油调合的灵活性,而且也提供了其它积极利益。预计MMT可为炼油工业提供下列利益:
1.增加汽油调合的灵活性
MMT使炼油厂在生产清洁燃料时,有更多的选择,减少对高辛烷值组份的依赖,增加了汽油调合的灵活性。有利于炼油厂增产高标号汽油。
2.较低的辛烷值改进成本
与MTBE相比,是极优良的调整介质。汽油中18mgMn/L限量浓度的MMT辛烷值增益相当于汽油中加入10%MTBE获得的辛烷值增益。
3.降低重整装置苛刻度
因为MMT提高了汽油的辛烷值,所以允许炼油厂在较低的苛刻度条件下操作重整装置,这样,就可以加大重整装置处理量,提高液收率。大约下降1个MON辛烷值,可提高1%液收率。
4.减少加热炉的排放
重整装置较低的苛刻度减少燃料的需要量约为3%,它也相应地减少了炼油厂的排放。
5.有助于降低汽油中的烯烃含量
在催化裂化装置中,降低汽油烯烃含量,提高柴油收率的措施有可能会降低辛烷值,汽油辛烷值降低的代价依靠MMT补偿。
6.减少原油的需要量
MMT的使用可以降低炼油厂对原油的精炼程度,提高了收率,降低了能耗,有利于炼油厂优化资源配置,这就节约了原油。采用MMT可以减少原油的需要量约1~2%,也是视MMT所加入的浓度而定。在美国,如果所有汽油都用MMT处理的话,估计节约原油82,000桶/天。估计去年中国已有500多万吨汽油调入MMT,若不使用MMT,而是依靠工艺方法达到相同的辛烷值的话,则要多消耗原油20万吨。
汽油抗氧剂
二次加工得到的燃料油含有较多的不饱和烃。这些烃类在光和温度的影响下,容易氧化生胶,从而造成发动机运转困难或效能低下,同时会损伤发动机部件,导致发动机故障。添加抗氧剂的主要目的是延长胶质含量达到影响使用之前的时间。我们用诱导期的大小来表示汽油在储存期间产生氧化和形成胶质的倾向,一般汽油的诱导期低于480min就要求添加抗氧剂。
十六烷值改进剂
十六烷值改进剂是一类极易产生自由基的化合物,可提高柴油在燃烧过程中的链引发速率,促进柴油的快速氧化,改善其点火性能。十六烷值改进剂的性能与基础燃料性质有关,通常加入0.1%的异辛基硝酸酯,柴油十六烷值可提高4~6个单位。基础燃料的十六烷值越低,含芳烃越多时,对十六烷值改进剂的感受性越差。此外,基础燃料的馏程也影响其对十六烷值改进剂的感受性。
柴油流动性改进剂
又称降凝剂,在柴油中加入该剂,可以改善柴油的低温使用性能,达到增产低凝固点柴油以提高炼厂生产的灵活性和经济效益。
当气温较低时,由于柴油被冷却,其蜡溶性开始下降,更重的正构烷烃组分以蜡晶的形式从溶液中析出。柴油流动性改进剂能在石蜡析出时与其共晶或吸附,抑制石蜡结晶长大,使蜡晶细化,从而改善柴油低温流动性能。
柴油稳定剂
二次加工柴油主要是催化柴油中存在大量烯烃、二烯烃以及硫、氮、氧化物等,容易引起的聚合反应、酸碱反应和酯化反应等,造成催化柴油颜色加深、氧化安定性不好。改善柴油的安定性一般通过加氢精制等工艺手段,但由于我国炼油工业加氢能力不足,且成本较高,因此许多炼厂通过添加稳定剂等非临氢精制的方法来改善部分二次加工柴油的安定性能。
航煤抗静电剂
喷气式飞机耗油量大,为了节省时间,机场采用高速加油。另外,航空煤油质量要求高,在生产、储运和加油过程中要经过严格的过滤。这样油品在过滤、混合、高速输油和喷雾过程中会因摩擦产生静电荷。由于航空煤油本身导电率低,大量静电荷就会聚集起来,引起火花放电而造成火灾或事故,因此需在航空煤油中加入少量的抗静电剂,以提高其导电率。
航煤抗磨剂
喷气式发动机是靠燃料本身作泵的润滑剂和冷却剂,如果燃料润滑性不好,就会增加燃料泵的磨损,降低其使用寿命,并危及飞行安全。而燃料润滑性取决于原油性质、加工工艺及其产品化学组成。一般硫化物对润滑性能有一定影响,硫化物含量多,润滑性能好,但随着油品加工深度增加,油品中酸性物和硫化物被除去,因而燃料的润滑性也会显着降低。为了提高燃料的润滑性能,通常在燃料中加入少量抗磨剂。
润滑剂添加剂
润滑剂添加剂按其作用的不同分为清净剂和分散剂、抗氧剂、极压抗磨剂、油性剂和摩擦改进剂、抗氧剂和金属减活剂、粘度指数改进剂、防锈剂、降凝剂、抗泡沫剂、其它润滑剂添加剂等共十大类。
复合添加剂类型
我国目前生产的复合添加剂的品种还很少,按其使用场合,可分为:汽油机油复合剂、柴油机油复合剂、通用汽车发动机油复合剂、二冲程汽油机油复合剂、铁路帆车油复合剂、船用发动机油复合剂、工业齿轮油复合剂、车辆齿轮油复合剂、通用齿轮油复合剂、液压油复合剂、工业润滑油复合剂、防锈油复合剂等共十二类。一般说来,向基础油中加入一定量的复合剂·便能同时改善它290的各种使用性能·即可得到所需要的相业的油品。这样既有利于简化油品生产过程,又有利于保证油品的质量。
清净分散剂类型几作用
清净剂和分散剂可统称为清净分散剂,它是发动机润滑油中用量最大的一种添加剂。按其化合物的类型分为:石油磺酸盐、合成磺酸盐、硫磷化聚异丁烯盐、烷基水杨酸盐、环烷酸盐、烯基丁二酚亚胺、硫化烷基酚盐。清净分散剂的统一符号为:“T1XX”。
清净分散剂有酸中和、增溶、分散、洗涤四个万面的作用:酸中和作用:清净分散剂具有碱性或高碱性,可以中和润滑油在高温使用过程中生成的酸性物质,防止进一步氧化缩合,减少漆膜与积炭的生成。增溶作用:清净分散剂都是油溶性表面活性剂,在油中它们郁以5-20个分子集合而成胶束,可以将一些油溶或油不溶的固体或液体溶解到胶束中心去,因而阻止进一步的氧化缩合,减少漆膜和积炭的生成。分散作用:清净分散剂能够将已经生成的漆膜和积炭等固体小颗粒加以吸附,分散在油中,防止它们凝聚起来形成大颗粒而粘附于机件上,或沉积为油泥。洗涤作用:清净分散剂对漆膜与积炭有很强的吸附性能·能将吸附在部件上的漆膜和积炭洗涤下来,分散在油中。
抗氧剂
抗氧剂具有抗氧化、抗腐蚀性能,并兼有抗磨作用,主要用于内燃机油,其次用于齿轮油、液压油等工业润滑油,其作用在于抑制润滑油的氧化过程,钝化金属的催化作用,减少油品氧化腐蚀,从而延长油品的使用寿命,同时保护机件金属表面不受酸的腐蚀等。在石油产品添加剂中抗氧剂的产量仅次于清净分散剂和粘度指数改进剂而居第三位。国内抗氧腐剂有:硫磷烷基酚锌盐、二烷基二硫代磷酸锌盐(简写ZDDP)等,抗氧剂的统一符号为:“T2XX”。
极压抗磨剂
极压抗磨剂主要是含硫、磷、氯的有机极性化合物,这类化合物在高的压力不能在金属表面形成比较牢固的化合物膜,它比金属的熔点低,当金属因为摩擦结点受压而温度升高时,这层化合膜就熔化,生成光滑的表面,减少金属表面的摩擦和磨损。极压抗磨剂的类型有:有机氯化物、有机硫化物、有机磷化物、有机金属盐等。极压抗磨剂的统一符号为:“T3XX”。
油性剂和摩擦改进剂
凡是能使润滑油在摩擦表面上形成定向吸附膜,从而改善摩擦性能,降低运动部件之间的摩擦和磨损的添加剂都叫油性剂和摩擦改进剂。常用的油性剂有:硫化鲸鱼油、硫化棉籽油、二聚酸、油酸乙二醇酪、硫化烯烃棉籽油、苯三挫脂肪酸胺盐等。油性剂和摩擦改进剂的统一符号为:“T4XX”。
粘度指数改进剂
粘度指数改进剂亦称增粘剂,是油溶性的链状高分子聚合物,其分子量由几万到几百万。在不同温度下具有不同形态,并对粘度产生不同影响,以增加粘度和改进粘温性能,即具有高的粘度指数。粘度指数改进剂主要用于调制多级内燃机油·其次用于调制低温性能好的液压油、液力传动油等。我国的粘度指数改进剂主要有,聚乙烯基正丁基醚、聚甲基丙烯酸醋、聚异丁烯、乙丙共聚物等。粘度指数改进刑的统一符号为:“T6XX”。
润滑油降凝剂
润滑油中一般均含有少量的石蜡,当油品温度下降到一定程度后,由于石蜡结晶析出,油就要失去流动性而凝固。降凝剂的作用主要是降低油品的凝点。降凝剂是一种化学合成的聚合或缩合产品,其分子中一般含有极性基团和与石蜡烃结构相似的烷基链,通过石蜡结晶表面的吸附或与其形成共晶的作用,改变蜡结晶的形状和尺寸,防止蜡晶粒间粘结形成三维网状结构,从而保恃油品在低温下的流动性。但是,如果润滑油中石蜡含量过多,大大超过了降凝剂所能起到的作用,那幺即使加了降凝剂也起不到降凝作用。我国降凝剂有:烷基萘、聚a烯烃、聚甲基丙烯酸酯等。降凝剂的统一符号为。T8XX"。
润滑油抗氧剂和金属减活剂
润滑油在使用过程中,在氧的存在下,受热、光、金属的催化作用,油品分子中结构最不牢的碳氢键受到破坏,发生自由基连锁反应,生成氧化物、过氧化物、水等。而后进一步聚合、缩合,形成胶质、油泥、漆膜等,使润滑油的使用性能变坏,使用寿命缩短。抗氧剂的用在于抑制油品的氧化,钝化金属的催化作用,减少油品的腐蚀,延长油品的使用寿命。它主要用于汽轮机油、工业齿轮油、抗磨液压油;变压器油、通用机床油等中。国内抗氧剂和金属减活剂有:2,6-二叔丁基对甲酚、N-苯基萘蔡胺、苯三唑衍生物、噻二唑衍生物等。抗氧剂和金属减活剂的统一符号为:“T5XX”。
防锈剂
防锈剂能在金属表面形成牢固的吸附膜,以抑制氧及水、特别是水对金属表面的接触,使金属不致锈蚀。防锈剂的分子结构应对金属有充分的吸附性·并对油的溶解性也好。常用的防锈剂有:烯基丁二酸、十七烯基眯唑琳烯基丁二酸盐、环烷酸锌、二壬基萘磺酸钡、苯并三氮唑、石油磺酸钡等等。防锈剂的统一符号为:“T7XX”。
抗泡沫剂
内燃机油及工业用油在发动机等设备中使用时,往往要喷散成雾状,这样就便润滑油中混进一部分空气,而形成比较稳定的泡沫流入曲轴箱内和润滑油箱中,结果就会使发动机不能正常操作。加入抗泡剂便可破坏润滑油与空气所形成的泡沫,降低泡沫吸附膜的稳定性,缩短泡沫存在的时间,从而保证设备正常运转。常用的抗泡沫剂有:甲基硅油、丙烯酸酪与醚共聚物等。抗泡沫剂的统一符号为:“T9XX”。
清净剂
清净剂是硫磷化聚异丁烯钡盐,按其碱值大小分为T108(中碱值)和T108A(高碱值)两种,主要由锦州炼油厂和兰州炼油化工总厂生产。该剂具有较好的高温清净能力及一定的酸中合能力。并具有一定的抗氧、抗磨、抗腐能力。缺点是热稳定性较差,不宜用于高档内燃机油中。可与其它添加剂配伍制备中低档内燃机油。1989年产品有出口。
抗氧剂
抗氧剂是不同原料的二烷基二硫代磷酸锌,它们具有良好的抗氧抗腐性及一定的抗磨性和极压性,以有效地防止轴承腐蚀和因高温氧化而使油品粘度增长,产品颜色浅,油溶性好,系国家专业标准产品,国内产品与国外OLOA267、OLOA3269A质虽相当。广泛用于调制内燃机油、工业用油及各类复合添加剂。T202主要用于汽油机油及工业用油中,国内牌号T203由于热安定性较好而主要用于柴油机油。主要生产单位有兰州炼油比工总厂及锦州炼油厂等。1989年产品有出口。
清净剂
清净剂是烷基水杨酸钙盐,它具有良好的高温清净性和酸中和能力,油溶性好,并具有一定的抗氧抗腐性能。国内产品T109产品与SHELL公司AC-60C质量相当。低剂量(2%~3%)可调制普通内燃机油,若与其它添加剂复合可以调制SC、SD、CC、CD等级别的中高挡内燃机油,1989年该产开始出口。
无灰分散剂
无灰分散剂分别是单烯基和双烯基丁二酰亚胺,具有良好低温和高温分散性,可与清净剂、抗氧抗腐蚀剂复合,油溶性优异。国内牌号T151、T152与国外OLOA-1200、OLOA-373水平相当。可调制SC、SD、CC、CD等级别的内燃机油。由兰州炼油化工总厂生产。另外,锦州炼油厂也生产类似的双烯基T154、多烯基T155分散剂,性能相同。一般来说,单烯基产品多用于汽油机油,双烯基和多烯基产品由于其热隐定性能好,多用于增压柴油机油中。
油性剂
油性剂是油酸乙二醇酶类型的油性剂。具有良好的油性、抗氧化性、抗乳化性及防锈性,与其它添加剂有较好的配武性。广泛用于调制工业齿轮油、导轨油、液压传动两用油。蜗轮蜗杆油及车辆齿轮油。
金属减活剂
金属减活剂是苯三唑衍生物,具有良好的改善油品抗氧化性能的功能,油溶性好。国内牌号T551金属减活剂与国外CIBAGEIGY公司Reomet38质量相当。可广泛用于汽轮机油、油膜轴承油、齿轮油、变压器油及俯环油中,以0.03%一O.1%的用量与其它剂复合使用、具有优异的抗氧增效作用。
第五章发展趋势
产品质量升级形势下新技术应用
随着经济的发展,汽车保有量不断增加,汽车排放造成的大气污染问题受到越来越多的关注,汽车排放的有害物质已成为世界各大城市大气污染的最大公害。据统计,目前世界上汽车保有量为6.6×107辆,按每辆轿车每天平均排放3.55kg的有害物质计算,每年汽车排向大气的有害物质高达8.58×108t。由于汽车排放的NOx、CO、碳氢化合物等会损害人的呼吸道系统或神经系统,必须严格控制汽车的尾气排放。表1列出了世界燃料规范中汽油的主要质量指标,我国车用汽油国家标准与国外先进标准相比尚有一定差距,新标准GB17930-1999规定硫含量小于0.08%;烯烃含量要求不大于35%;芳烃含量要求不大于40%,苯含量要求不大于2.5%;氧含量要求不大于2.7%。
世界燃料规范中汽油的主要质量指标
项目I类II类III类IV类
硫/(μg·g-1)<1000<200<300(<5~10)
烯烃,%(V)<20<10<10
芳烃,%(V)<50<40<35<35
苯体,%(V)<5.0<2.5<1.0<1.0
氧,%(V)<2.7<2.7<2.7<2.7
为了降低汽油中的硫、烯烃、苯和芳烃含量,生产清洁汽油,国内外的石油公司和研究单位都相继开发了针对性的清洁技术,这包括降低汽油中硫含量、烯烃含量、苯含量技术和提高汽油辛烷值的技术等。
降低汽油中硫含量的技术
据统计,汽油中90%的硫来自催化裂化,所以降硫技术主要集中在催化裂化汽油脱硫方面。目前相关的技术大体上可以分为两类:加氢脱硫和非加氢脱硫。加氢技术主要包括催化裂化进料加氢预处理技术、选择性加氢脱硫技术、非选择性加氢脱硫技术和催化蒸馏加氢脱硫技术;非加氢技术主要包括碱性抽提、吸附脱硫技术、生物脱硫技术和添加剂技术。
1.1催化裂化进料加氢预处理技术
对催化裂化进料中的含硫VGO和硫氮含量高的焦化HCGO加氢预处理,国内外都开发了相关的技术。炼油厂采用CH2O钼镍催化剂处理HCGO,能将硫含量从0189%降到0.04%;抚顺石化研究院用FDS4钼镍含硅氧化铝催化剂处理中东的VGO,能将硫含量从2.28%降到0118%;AKZO公司开发的三元金属(Ni、Co、Mo)催化剂902,能在维持NiCo催化剂的脱氮和芳烃饱和活性的同时,把VGO硫含量从0.3%降到01125%。
经验数据表明,催化裂化汽油的硫含量约为进料硫含量的6%~8%。因此,经加氢处理的催化裂化进料,其催化裂化汽油硫含量可达到II类汽油的标准。
1.2选择性加氢脱硫技术
由于常规的加氢脱硫工艺虽可以降低其硫含量,但辛烷值损失较大。针对这种情况发展了相应的选择性加氢技术。
Exxon/Mobil公司开发的Scanfining工艺采用AKZO公司的RT225催化剂,可将硫含量808~3340μg/g的LCN馏分经选择性加氢,硫含量降到10~20μg/g,脱硫率达99.0%~9918%,抗爆指数损失1.1~3.8个单位。此外,IFP的Prim-G,CDtech的两段脱硫等技术目前已实现了工业化,北京石油化工科学研究院(RIPP)开发的RSDS催化裂化汽油选择性加氢脱硫技术也通过了中试评议,现正进行工业化试验。
1.3非选择性加氢脱硫技术
OCTGain技术是Exxon/Mobil所开发的非选择性加氢脱硫技术,它主要采用了双功能催化剂。催化裂化汽油经第一催化剂加氢,使硫含量小于10μg/g,同时伴有饱和烯烃与辛烷值的降低,然后在同一反应器中在第二沸石催化剂上使低辛烷值分子裂化,恢复其辛烷值。从报道看,该技术对汽油重馏分脱硫效果较好,但处理全馏分时尚不够理想,主要是汽油抗爆指数损失较为严重。
Isal技术是UOP和Intevep公司所开发的。它采用的催化剂具有脱硫、脱氮、烯烃饱和及烷烃异构化等功能,在加氢脱硫过程中饱和烯烃,同时使烷烃异构化,以恢复损失的辛烷值。据1998年NPRA年会报道,对FCC重汽油,脱硫率大约99%、芳烃保持不变,而体积液收损失6%,辛烷值桶损失为7%。传统加氢法辛烷值桶损失为12%。
1.4催化蒸馏加氢脱硫技术
CDHYDRO技术和CDHDS技术是CDtech公司针对催化汽油轻、重馏分硫含量分布不同,而开发的催化汽油两段催化蒸馏加氢脱硫技术,它把加氢脱硫和蒸馏有机地结合在一起。CD2HYDRO技术是指在第一段催化蒸馏塔内对催化汽油轻馏分中的硫醇进行临氢硫醚化反应,形成高沸点的烯类硫化物。CDHDS技术是指把催化蒸馏塔底重馏分进行第二段催化蒸馏,也是加氢脱硫和蒸馏合在一个塔内完成,脱硫率可达95%以上,抗爆指数损失小于1个单位。
1.5碱性抽提
对汽油轻组分中的硫醇等含硫化合物进行加氢处理会使轻组分中的烯烃饱和,而且在经济上也是不可取的,解决这一问题的一个行之有效的办法就是用碱性抽提法除去含硫化合物。
Merichem公司发明的商品名为FIBER-FILMTM的接触器系统对于碱性抽提非常有效。在这种接触器中填充大量的金属纤维,由于毛细作用和表面张力,碱性水相被束缚在这些金属纤维上。当汽油流过接触器时,烃类与碱性水相之间的牵引力驱动水相沿着纤维丝向前流动,最后从分离器底部流出,进入水相收集器,由此使得起抽提作用的水相不断更新,而处理过的汽油流出接触器,进而从分离器顶部流出。
1.6吸附脱硫技术
IRVAD吸附脱硫技术是Black&VeatchPritchard公司和Alco工业化学品公司联合开发的,其工艺是在多段吸附塔内氧化铝基小球吸附剂与汽油逆流接触,废吸附剂经过热气体复活后返回塔内再用,经过吸附的汽油由塔顶排出。此外,由于吸附剂中添加有一种无机助剂,所以能脱除各种硫化物(硫醇、硫醚、噻吩、苯并噻吩)。中试结果表明,汽油硫含量可由1300μg/g降到70~80μg/g,氮含量可以由37μg/g降到0.3μg/g以下。
S-Zorb吸附脱硫技术是菲利浦斯石油公司开发的,其工艺是催化汽油通过装有专用吸附剂(锌和其它金属负载在一种载体上)在流化床吸附器进行吸附,吸附过程中排出的一部分待生剂送进再生器进行再生,循环操作。试验结果表明,催化全馏分汽油脱硫率可达97%以上,硫含量由800μg/g降到25μg/g以下,抗爆指数损失4个单位。第一套工业装置已于2001年初在美国得克萨斯州的博格炼油厂投产。
1.7生物脱硫技术
汽油生物脱硫技术尚处在开发阶段,目前对脱除催化裂化进料中的二苯并噻吩有了某些突破,已分出2种菌株,产生的酶能将二苯并噻吩中的硫选择性氧化为砜,然后再脱除砜中的硫,生产不含硫的联苯氧化衍生物和无机盐。对汽油馏分中的噻吩硫,迄今还没有发现能有效破坏噻吩的微生物。从汽油中脱除噻吩的关键是找到溶剂耐受性和催化速率较高的新生物催化剂。据美国能源部预计,生产硫含量低于50μg/g汽油的生物催化工艺在未来4~6年内可能实现工业化。
1.8添加剂技术
Grace公司开发的催化裂化GSR系列脱硫添加剂可以降低包括噻吩和烷基噻吩在内的各种有机硫化物的含量。其中GSR-1添加剂根据原料油、催化剂和操作条件的不同,能使催化汽油硫含量降低15%~25%,目前已在北美和欧洲10家炼油厂的催化裂化装置上使用。GSR-4添加剂作为Grace公司催化裂化催化剂SURCA家族的一种功能组分,已在北美的3套工业装置上使用,还有几套装置最近开始使用。工业使用的结果表明,用这种添加剂以后,催化汽油硫含量降低20%~30%。荷兰AKZO公司开发的Resolve添加剂,可使催化汽油硫含量降低20%。
降低汽油中烯烃含量的技术
成品汽油中的烯烃主要来自催化裂化汽油。因此,降低催化裂化汽油中烯烃含量是首要解决的问题,目前国内外相关的技术主要有以下几个方面。
2.1优化操作降低烯烃
通过优化操作可以降低催化裂化汽油烯烃含量,经验表明,如提升管出口温度每升高5.6℃,催化裂化汽油烯烃含量将增加1%;剂油比每增加1个单位,催化裂化汽油烯烃可降低1.5%~3.0%;反应温度一定,提高平衡催化剂活性,转化率提高,烯烃下降;深度稳定,控制汽油中液化气含量,烯烃下降等。
2.2降烯烃催化剂
Davison公司首先开发出的RFG催化剂,工业应用结果表明,可以降低25%~40%的烯烃,同时还能保持辛烷值和轻烯烃(C3、C4)产率不会下降,而且具有较好的焦炭选择性。RIPP开发的GOR系列降烯烃催化剂采用增加稀土含量、增加择形分子筛和经特殊处理的金属氧化物分子筛,从而提高了氢转移活性,补偿了辛烷值的损失,也有利于抑制焦炭的生成。
GOR-C催化剂在中石化股份公司洛阳分公司重油催化裂化装置上应用,烯烃下降10.6%。
另外,兰州石化科学研究院研制开发的新型降烯烃催化剂LBO-12可使汽油的烯烃含量下降6%~12%。AKZONOBEL公司推出的一种称为TAMCOBRA的催化剂技术能使烯烃含量下降7%左右。
2.3降烯烃助剂
洛阳石化工程公司炼制研究所开发的LAP助剂采用沸石选择性裂化的原理,选用特定金属改性的沸石制备而成,水热稳定性、抗磨性、活性稳定性都比较好,既能降低催化汽油的烯烃含量,又能保持辛烷值不降或略有提高。工业试验结果表明,当LAP添加剂占装置催化剂藏量的2.6%、5.3%和7.4%时,催化汽油中的烯烃含量分别降低6.3%、10.4%和12.8%,且液化气(特别是C3和C4烯烃)产率提高。
2.4催化裂化汽油的醚化技术
Snamprogetti公司开发的深度醚化技术(SPDET)以FCC轻汽油为原料,通过醚化反
应将活性的C=5~C=7转化为相应的甲基醚,同时采用烯烃骨架异构化工艺将n-C=5转化为i-C=5,并进一步醚化。烯烃转化率达42%。
芬兰Neste公司在Porvoo炼油厂建设一套FCC轻汽油醚化装置,采用FCC汽油分出的全部C5、C6馏分和一半的C7馏分为原料,经双烯选择性加氢后进行醚化,烃类的总转化率为1615%,约60%叔烯转化为醚,RON可增加到2%~3%。
降低汽油的苯含量的技术
在汽油总体中,75%以上的苯来自重整汽油。因此要降低苯含量最重要的是要降低重整油中的苯含量。
3.1重整进料预分馏技术
对重整进料进行预分馏可以除去苯的前身物,如甲基环戊烷和环己烷等,该技术可以降低重整油的苯体积含量的1%~2%,因此该法降低苯含量是有限的。
3.2溶剂抽提技术
对催化重整的苯抽提可采用液—液萃取法或萃取蒸馏法,液—液萃取法是利用苯与非苯在溶剂中溶解度的不同而进行的萃取分离,而萃取精馏是加入溶剂降低苯的蒸汽压,增大苯与非苯的相对挥发度,从而通过蒸馏使两者分离。溶剂抽提使用的溶剂一般为诸如环丁砜、三乙二醇醚、四乙二醇醚等。
3.3常规苯加氢饱和技术
该方法是把重整汽油中的含苯馏分分离出来进行加氢饱和转化为环己烷。在这一方面,IFP公司开发的技术反应条件温和,可采用非贵金属催化剂,且由于环己烷的比重小于苯,加氢后,体积产率增加,苯小于0.1%。另外,已工业应用的技术还有UOP公司的Bensat工艺以及Penex-plus工艺。
3.4催化蒸馏加氢脱苯技术
CDHYDRO苯加氢饱和技术是CDtech公司于20世纪90年代推出的一种催化蒸馏专利技术,该工艺的反应压力为0.24~0.6MPa,苯转化率为70%~90%,已有一套工业装置在运转。法国石油研究院开发的重整生成油催化蒸馏加氢脱苯技术(Benfree),以C5~C9重整生成油为原料,通过分馏塔使苯进行加氢生产环己烷,可以得到苯含量不大于1%的汽油。
提高汽油的辛烷值技术
目前对提高汽油的辛烷值技术的研究主要集中在烷基化和异构化技术方面。
4.1烷基化技术
烷基化油具有辛烷值高、敏感度好、蒸汽压低、沸点范围宽,是不含芳烃、硫和烯烃的饱和烃,是理想的高辛烷值清洁汽油组分。目前烷基化主要有液体酸烷基化技术、固体酸烷基化技术和拟烷基化技术。
长期以来,液体酸烷基化技术一直延用硫酸和HF作催化剂。由于腐蚀和环保问题,寻求一种固体酸催化剂替代硫酸和HF生产烷基化油就成了炼油工业的热门课题。
固体酸催化剂有杂多酸、沸石、离子交换树脂,无机氧化物上附载卤化物的固体酸等多种体系。目前开发较成熟的固体酸烷基化技术有UOP的Alkylene工艺。该工艺采用一种称为HAL-100TM的固相均相催化剂。该催化剂具有优化的颗粒分布和孔径,并能保证良好的传质,对异丁烯具有很高的烷基化活性。Topsoe公司开发的固体酸烷基化工艺采用固定床反应,所用催化剂是在载体上吸附的液体超强酸。
由于地下水污染问题,美国加州已下令2003年起禁用MTBE,预计21世纪初美国可能在汽油中禁用MTBE。面对这种形势,利用经过改造的MTBE装置和异丁烯原料通过二聚-加氢生产异辛烷来替代MTBE的拟烷基化工艺显示出魅力。目前已经工业应用和即将工业应用的工艺有UOP公司的InAlk、意大利斯纳姆普罗盖蒂公司的SP-Isooctane和凯洛格布朗-鲁特公司的NexOctane等工艺。
4.2异构化技术
异构化是提高整体汽油辛烷值最便宜的方法之一,可使轻直馏石脑油的辛烷值提高10%~22%。正构化烷烃进行异构化取决于所用催化剂,所以近几年对异构化的研究主要集中在烷基异构化及其催化剂的研究。
C5/C6异构化技术是比较成熟的烷基异构化技术,典型的技术有UOP/Shell的完全异构化技术(TIP),该工艺由异构化和分子筛吸附分离(ISOSIV)两部分组成。直馏C5、C6馏分,经异构化后RON可从68左右提高到79,然后用分子筛吸附,将正构烃分离出来进行循环异构化,RON可以提高到88~89。另外,UOP还推出了多代异构化技术,如基于HS-10分子筛催化剂的异构化、金属氧化物LPI-100催化剂的Pari2som技术和基于贵金属含氯氧化铝1-8催化剂的Penex技术等。
目前使用的异构化催化剂主要有两类。其一是无定形催化剂———Pt/Al2O3-Cl,使用此类催化剂时,反应温度较低(120~150℃),氢/烃比较低(小于0.1),不需要氢气循环,但对原料需进行严格的预处理和干燥。采用此类催化剂的有UOP公司的Penex工艺。其二是沸石类催化剂———Pt/丝光沸石或Ω沸石,使用此类催化剂时,反应温度较高(230~270℃),氢/烃比较大(大于1.0),因此需要氢气循环。采用此类催化剂的有UOP公司的TIP工艺。
我国的汽油质量现状及相应技术对策
总体来看,我国汽油的苯含量、烯烃含量、硫含量等指标与国际水平相比有一定的差距,其中突出的问题是:烯烃含量过高,平均烯烃含量约为50%;硫含量较高,大部分汽油中的硫含量小于0.05%,但部分企业生产的汽油硫含量大于011%;蒸汽压偏高。造成这一现状的主要因素是我国汽油组成比例不合理,以中国石化集团公司为例,催化汽油所占比例太大,达到了73.93%,而在美国、欧洲相应的比例分别只有36.2%和27%(见表2)。相反,我国汽油中重整、烷基化等高辛烷值组分太低。
车用汽油调和组分构成对比%
组分 中国石油天然气集团公司 美国 欧洲
催化汽油73.9336.2027100
重整汽油10.4126.6047100
直馏汽油10.80
烷基汽油0.306.104100
异构汽油5.105100
MTBE1.7411.708.50
其它2.8314.308.50
为了适应日益严格的环保要求,缩小与发达国家的标准,应该尽快做好我国汽油调和组分的结构调整,大力发展催化重整、烷基化和异构化等技术,以提供更多的高质量的汽油调和组分。鉴于我国催化裂化由于掺炼渣油和石蜡基原料密度过大造成烯烃含量过高的现状,应该优化操作条件、使用降烯烃催化剂和助剂,开发有效的催化汽油改质降烯烃技术,加快催化汽油的醚化技术的研究,满足2003年汽油烯烃含量小于35%的标准。另外,还应积极开发催化汽油的加氢脱硫技术、固体酸烷基化技术以及C5/C6异构化技术,为清洁汽油的生产提供技术支撑。
据美国《化学周刊》8月9日报道,为了满足日趋严格的环保法规,以及汽油需求不断增长,今年世界炼油催化剂的需求正经历着快速增长。据分析未来五年世界炼油催化剂需求还将继续保持较高增速。但是由于原材料成本不断升高,特别是金属和天然气价格增长较快,炼油催化剂行业也面临着巨大挑战。预计加氢工艺催化剂生产商可以轻松度过涨价关口,但流化催化裂化催化剂企业面临压力要大得多。
据美国CatalystGroup公司研究称,2005年世界炼油催化剂年销售额达26.9亿美元,预计未来五年还将继续以3.4%/年速度增长,到2011年销售额可达到32.4亿美元。其中加氢精制催化剂需求增长最为快速,预计增速平均为4.9%/年,2011年销售额可达12亿美元;未来五年催化裂化工艺催化剂需求增速预计为2.6%/年,2011年可达9.98亿美元;今后五年加氢裂化催化剂销售额预计将维持目前水平,由2005年的1.73亿美元增加至2011年的2.08亿美元,主要因为销售价格上涨。
欧洲、北美及日本以外地区催化剂销售额预计年增速为5%,这些地区2003年石油化工催化剂销售额约为28亿美元。同期,北美地区将由2003年的42亿美元继续保持3%/年增速增长;西欧未来3年平均增幅预计为3.7%/年,03年销售额33亿美元;日本将由2003年的17美元继续保持3.2%/年增速增长。
过去两年,由于世界燃料标准要求进一步降低硫含量,以及要求降低炼油厂二氧化氮和二氧化硫等排放量,炼油催化剂需求大幅增加,催化剂行业也在发生着各种变化。例如德国Süd-Chemie公司2005年炼油催化剂业务销售收入和盈利均出现大幅增长,涨幅超过20%。预计2006年公司炼油催化剂业务销售额和盈利还将增长15%以上。
丹麦托普索公司报告称2005年炼油催化剂及相关服务销售收入呈现强劲增长趋势,营业利润(Ebit)达5000万美元,2004年仅为900万美元,2005年销售额也增长了35%达7亿美元。其中销售额的一半来自加氢工艺催化剂,2005年托普索公司加氢催化剂销售量增加了70%。
炼油催化剂需求增长的主要推动力是燃料法规要求降低汽柴油的含硫量。比如美国自6月1日起生效的新的燃料标准,要求柴油硫含量由目前的500μg/g降低至15μg/g,汽油含硫量要求降低至10μg/g甚至更低,另一方面,炼油商则要求加工含硫量更高的劣质原油,所以加氢工艺催化剂需求更加广泛,包括催化裂化工艺之前的原料预加氢工艺、汽柴油产品加氢精制等工艺。
在催化裂化工艺催化剂方面,要求催化剂生产商开发助剂能够满足:降低硫含量、增加辛烷值并且具有丙烯最大产能。在这一领域的主要催化剂公司主要有——雅宝公司、Grace和恩格哈德公司,不过恩格哈德公司最近已由巴斯夫公司收购,并更名为巴斯夫催化剂公司。
为了满足市场需求不断增长,各大公司正在纷纷扩大产能。Grace和雪夫隆合资的加氢催化剂生产公司——先进炼油技术公司(ART)正在扩大芝加哥催化剂厂的产能30%。另一家主要加氢催化剂公司——CRICatalysts则在路易斯安娜州PortAllen新建一座世界规模的加氢催化剂厂。ART公司最近还宣布与科威特催化剂公司签署合作协议,由科威特公司为ART生产渣油加氢催化剂,满足阿拉伯地区市场需求。
UOP和雅宝公司在今年初宣布将联手合作为炼油行业提供加氢处理工艺技术,即由UOP提供加氢工艺授权,而雅宝公司提供催化剂,从而为炼油厂提供一站式服务。
由于原材料和天然气价格持续上涨,催化剂生产商面临压力不断增大。原材料烧碱、金属、氧化铝等价格持续上扬,而生产加氢催化剂的贵金属如钼、钴、镍价格上涨幅度更大。此外为了开发满足市场需求的高性能催化剂,催化剂公司不得不增加研发投资。据称,GraceDavison今年用于催化裂化工艺催化剂的投资增加了10%,将重点开发基础催化剂的活性和选择性,用于处理渣油原料以及精制原料。在加氢工艺催化剂方面,ART公司则集中于降低柴油的硫含量和实现氢耗最小,以及催化裂化预加氢处理催化剂的开发。
废剂再生和处理技术
催化剂再生技术是使催化作用效率已经衰退的催化剂重新恢复其效率的过程。再生过程不涉及催化剂整体结构的解体,仅仅是用适当的方法消除那些导致催化效能衰退的因素。
例如除去存留于催化剂上的毒质、覆盖于催化剂表面上的尘灰和由于副反应而生成于催化剂外表或孔隙内部的沉积物等,力图恢复催化剂的固有组成和构造。在有机催化反应中,由脱氢-聚合副反应生成高碳氢比的固体沉积物覆盖催化剂表面,是常见的失活原因之一。可用通入空气或贫氧空气的方法烧去碳沉积物,使催化剂再生;有些场合可用溶剂洗涤的方法使之再生。有些催化剂的再生作业可在原来的反应器中进行;有些催化剂的再生作业条件(如温度)与生产作业条件相差悬殊,必须在专门设计的再生器中再生。例如石油裂化过程中所用的铝硅酸盐催化剂再生时,为构成连续化的工业过程,可在一个流化床反应器中进行催化裂化,失活的催化剂连续地输入另一流化床反应器(再生器)中再生,再生催化剂连续地输送回裂化反应器。在裂化催化剂中,可加入少量的助燃催化剂(如负载有微量铂的氧化铝)以促进再生过程,使碳沉积物的清除更为彻底。此时排放气中的一氧化碳几乎可全部转化为二氧化碳,回收更多热量。
有些催化剂的再生过程较为复杂,非贵金属催化剂上积碳时,烧去碳沉积物后,多数尚需还原。
铂重整催化剂再生时,在烧去碳沉积物后尚需氯化更新,以提高活性金属组分的分散度。
近年来,为防止环境污染,减少反应器和再生设施投资和更好地恢复活性,特别是对用于加氢、加氢裂化的硫化物催化剂,建立了一批催化剂再生工厂,专门对催化剂进行器外再生。
可再生的催化剂经再生处理后,实际上其组成和结构并非能完全恢复原状,故再生催化剂的效能一般均低于新催化剂,经多次再生后,使用特性劣化到不能维持正常作业或催化过程的经济效益低于规定的指标,即表明催化剂寿命终止。有些催化过程中所用的催化剂失效后难以再生,例如载体的孔隙结构发生改变,活性成分由于烧结而分散度严重下降,或与毒质作用发生难以恢复的变化等。此时只能废弃,或从中回收某些原料,以重新制造催化剂。如加氢用的铂-氧化铝催化剂,失活后从废催化剂回收铂。
化学药剂的净化处理
劣化的环丁砜溶剂再生技术
生产显示,环丁砜的降解导致热稳态胺盐的积累,从而引起腐蚀。胺液脱硫装置的性能随着热稳态盐的增加而恶化,H2S的吸收变得不稳定、溶液中的铁增加、胺液过滤器寿命减短、设备腐蚀和堵塞,对芳烃抽提装置中运行的环丁砜溶剂及设备腐蚀残留物进行分析显示,环丁砜循环系统设备腐蚀是由于在环丁砜中累积的Cl-造成的氯腐蚀和由于环丁砜及杂质在运行中劣化产生的磺酸、丁基磺酸、硫酸等造成的硫腐蚀能导致不可预计的经济损失。
用阴离子交换树脂净化环丁砜,能显著降低环丁砜劣化产生的酸性阴离子和累积的Cl-的含量,有效地降低环丁砜对循环系统的设备腐蚀。加拿大ECO-TEC公司提供的一种胺液净化技术(AmiPur)就是采用这种方法,在富胺液的侧线安装净化装置可以使环丁砜脱硫的操作稳定又可靠,而且带来巨大的环境效益。这种持续性地去除热稳态盐的方法能够立即产生明显的效益:
l 降低了过滤费用;
l 不需要定期的吸收塔清洗;
l 提高了装置的气体处理能力;
l 不需要或减少了抑泡剂、中和剂和防腐剂的使用;
l 降低了原来去除HSS的费用。
FCC平衡剂磁分离回收处理技术
FCC平衡剂在线回收磁分离技术的特点:
1、超强分选磁场:表面场强达15000gauss,磁场梯度达15000gauss/cm;
2、逐级精选模式:针对弱磁性超细粉体的磁分离特点,采用不同的磁路组合方式,可达到较高的磁选效率,为NBMS工艺提供较大的调整范围;
3、密闭连续循环流程:磁选过程处于一个连续密闭的流程中
其原理是利用催化剂中保留金属Ni、Fe和V在磁场中的磁性进行分离。
在催化裂化生产过程中,原料油与催化剂接触反应时,原料油中的重金属(主要是Ni、Fe、V、Na、Ca、Cu等)及反应生成的焦碳一起沉积于催化剂颗粒上。催化剂再生时,催化剂颗粒上的焦碳被烧掉,而重金属却保留了下来。随着催化剂在系统内不断循环使用,重金属在催化剂上的沉积量不断增加,使催化剂受到污染而中毒,由于催化剂中毒导致其活性和选择性下降,产品分布变坏,液收下降。为了保持系统催化剂具有适当的活性和选择性就必须卸出一部分平衡剂,补充新鲜催化剂。
在卸出的平衡剂中含有使用寿命长短不一、重金属沉积多少不一的催化剂颗粒,重金属沉积量少的这部分催化剂仍具有较高的活性和选择性。如果把这部分催化剂与那些重金属污染较重的催化剂进行有效分离与回收,再返回装置继续使用,就能减少装置催化剂的消耗,减少废催化剂对环境的污染。
由于污染催化剂的重金属中的Ni、Fe和V属于铁磁性和顺磁性物质。在磁场中显示较强的磁性。因此在磁场中那些使用期短,重金属含量低的催化剂颗粒的磁性弱,而使用期长,重金属含量高的催化剂颗粒的磁性就强。在一定强度及梯度的磁场中,使后者被吸附,而前者不被吸附,从而实现两者的分离。把重金属含量低的这部分催化剂加以回收,可返回装置继续使用。这就是磁分离的基本原理。
2000年12月至2001年3月,济南炼油厂进行了催化剂磁分离工业应用试验(详见石油炼制与化工2003年第8期P20)。2001年5月至2001年7月,中石油大港石化也进行了工业验证试验(详见中国石油化工科技信息指南2002年上卷P45)。2002年12月,该技术在济南分公司首先实现了工业化应用,截止目前已在中石化、石油的八家炼厂得到了推广、应用。
参考文献
1张鸿仁.油田原油脱水.北京:石油工业出版社,1990
2丁德盘.油田化学,1998(1):82~86
3高惟宝.油田化学,1984(2):149~153
4魏竹波.日用化学工业,1995(3):19~22
5杨树德.国外油田工程,1992(5):20~24
6赵福麟.石油大学学报,1994(增刊):104~113
7魏国晟.油田化学,1995(2):188~190
8张宗愚.精细石油化工,1989(5):13~21
9 方洪波.石油技术,1992(3):85~92
CosynsJ,ChodorgeF,CommereucD.MaximizePropyleneProduction.HydrocarbonProcess,1998,77(3):61~64
陈平.轻烃资源优化及其效益分析.化工技术经济,2003,21(6):10~12
[3]ChauvinY,CommereucD.ProccsfortheMetathesisofOlefinswithanImprovedRheniumCatalyst.US5449852.1995
[4]CommereucD,HuguesF,SaussineL.ProcessforPreparingaRheniumandCesiumBasedMetathesisCatalyst.US6277781.2001
[5]ChodorgeJ,CommereucD,CosynsJ.ProcessandInstallationforConversionoftheOlefinC4-CutintoPolyisobuteneandPropylene.EP742234B1.2001
[6]FredericH,MegeP,CommereucD.ProcessforLiquid-PhaseConversionwithMoving-BedCatalystsUsingaStripper-Lift.US6284939.2001
[7]OliverH,CommereucD,ForestiereA.ProcessandUnitforCarryingoutaReactiononanOrganicFeed,suchasDimerizationorMetathesisinthePresenceofaPolarPhaseContainingaCatalysts.US6284937.2001
[8]SchwabP,HoehnA.PreparationofPropene.US6271430.2001
[9]SchwabP,BreitscheidelB,SchulzR.MetathesisCatalystsandItsPreparationandUse.US6130181.2001
[10]SchwabP,BreitscheidelB,SchulzR.PreparationofOlefins.US6166279.2000
[11]SchwabP,BreitscheidelB,OostC.ProcessforPreparingPropyleneand1-Butuene.DE19805716.1999
[12]SchwabP,HoehnA.ProcessforthePreparationofPropene.EP832867.1998
[13]SchwabPSchulzM.PropeneProductionGivingHighYieldandSelectivitybyDisproportionofButuene-1,ButueneandIsobutuene,UsingaMetathesisCatalystsBasedonTransitionMetal.DE19746040.1999
[14]BargerPT,LawsonRJ,VoraBV.ProcessforProducingLightOlefins.US5990369.1999
[15]白尔铮.四种增产丙烯催化工艺的技术经济比较.工业催化,2003,(5):7~11
[16]NkosiBS,SpamerA,SwartJ,etal.ProductionofPropylene.WO0014038.2000
[17]黄骏声,辛文杰,白杰等.钼负载型催化剂上乙烯与2-丁烯歧化制丙烯.石油化工,2003,32(3):191~194
[18]白杰,谢素娟,刘盛林等.用于乙烯和丁烯歧化制丙烯反应的催化剂及其制备方法.CN1403198.2003
[19]WangYangdong,ChenQingling,YangWeimin,etal.EffectofSupportNatureonWO3/SiO2StructureandButene-1Metathesis.ApplCatal,A,2003,25:25~37
[20]曹湘洪.增产丙烯,提高炼化企业盈利能力.化工进展,2003,22(9):911~919
[21]BoltHV,GlanzS.IncreasePropyleneYieldsCost-Effectively.HydrocarbonProcess,2002,12:77~80
[22]http://LiebnerW.Proplyur-anUpgradeofOlefin-byProduct.In:2002DewittPetrochemicalReview,HoustonTexasUSA:Willy&SonsPress,2002.19~21
[23]HarandiMN.FuildizerCatalyticProcessforUpgradingOlefins.US5164071.1992
[24]BlackA.UOPandATOFINAAnnounceNewOlefinCrackingProcees.UOPNewsRelease,2003-06-03
[25]PowersDH.ProcessforMakingPropyleneandEthylene.WO0026163.2000
[26]膝加伟,赵国良,谢在库等.碳四烯烃催化裂解生产丙烯催化剂及其工艺.见:C4的资源、利用途径及技术开发学术交流会议文集,呼和浩特:中国化工学会石油化工专业委员会,2002.147~151
[27]滕加伟,赵国良,谢在库等.烯烃催化裂解增产丙烯催化剂.石油化工,2004,33(2):100~103
[28]JohnsonDL,NarimanKE,WareR.CatalyticProductionofLightOlefinsRichinPropylene.CN1360623T.2002
[29]DrakeCA,WuA.ZeoliteMaterial,aProcessofMakingsuchZeoliteMaterial,aProductfromsuchProcess,andtheUsethereofintheConversionofHvdrocarbons.US6037294.2000
[30]高强,王滨,王小来等.碳四、碳五催化裂化制乙烯、丙烯.见:C4的资源、利用途径及技术开发学术交流会议文集,呼和浩特:中国化工学会石油化工专业委员会,2002.247~249
[31]张桂华.增产丙烯途径的技术经济比较.石油化工技术经济,2000,(1):27~30
[1]田永奎.金属腐蚀与防护.北京:机械工业出版社,1995:70~74
[2]魏宝明.金属腐蚀理论及应用.北京:化学工业出版社,1984:328~334
[3]间宫富士雄.缓蚀剂及其应用技术.北京:国防工业出版社,1984:54~176
C5/C6异构化技术的发展及其应用,聂晶,中国石化金陵分公司情报处,2001年12月
郭藩欣,C5/C6异构化工艺及催化剂,金陵石油化工,1993,3:34
苏虎,催化重整通讯,2002,2:62
黄国雄、李承烈,《烃类异构化》,中国石化出版社,1992
问:2023年锅炉价格/多少钱?
