工业炉窑是我国的能耗大户,每年耗能约占全国总能耗的1/4,其中燃煤约70%,其他为气体、液体燃料或电力等。由于我国工业炉窑种类多、数
工业炉窑是我国的能耗大户,每年耗能约占全国总能耗的1/4,其中燃煤约70%,其他为气体、液体燃料或电力等。由于我国工业炉窑种类多、数量大,在节能与环保等方面技术相对落后,从而造成产品综合能耗高、环境污染较严重等问题,因此从工业炉窑流程中的物质流、能量流分析角度入手,研究其节能原理与技术十分必要。
对于水泥炉窑的物质流与能量流研究主要关注的是预热器、分解炉、回转窑和篦冷机系统,对于余热利用单独进行分析,未考虑原燃材料的干燥系统。本文在此基础上,建立了一种可适用工业炉窑物质流与能量流分析的节点计算模型,研究了包含窑头余热锅炉(AQC炉)、篦冷机、回转窑、分解炉、五级悬浮预热器、窑尾余热锅炉(SP炉)、生料磨系统等主要装置的水泥炉窑系统能量流与㶲流分布情况,得到了能量与㶲损失的主要部位,对节能潜力进行了评估,为水泥炉窑节能管控技术提供了理论依据。
摘 要:工业炉窑是我国的能耗大户,每年耗能约占全国总能耗的1/4。在能源日益紧缺、环境污染严重的今天,工业炉窑节能减排工作十分紧迫。工业炉窑的生产是不同设备、不同工序协同生产的一个过程,包含物质与能量在各个系统之间的转换与转移,因此工业炉窑的物质流和能量流分析是炉窑实现高能效和低排放的基础。一般的方法主要从炉窑的产品用能或余热利用角度来分析,未将工业炉窑作为一个系统,整体来考察物质流和能量流状况。基于节点计算法,从工业炉窑整体系统出发,建立一种工业炉窑物质流与能量流匹配的数学模型,获得了典型工业炉窑不同部位的能量收支情况;同时采用热力学第二定律的㶲分析方法研究炉窑系统的㶲损失,明确了炉窑节能的重点部位。采用该方法开展了3 200 t/d典型水泥炉窑的物质流和能量流分析计算,结果表明,水泥炉窑的热量损失主要包含高温损失与低温损失,其中高温损失主要是炉窑壁面散热损失与煤粉未燃尽的碳热损失,分别占6.84%与1.95%,㶲损失分别为4.17%与2.59%,有较大的节能潜力;低温热损失包含烟道尾部烟气的排烟热损失、出冷却机熟料带出的显热等,AQC炉和SP炉的热量损失各占3.06%和6.19%,㶲损失分别为1.26%和1.45%,仍有利用价值。针对高温和低温热量损失的不同原因,对于炉窑的节能潜力进行了评估,提出采用先进保温、富氧煅烧、低温余热再利用等新技术,可进一步降低炉窑的煤耗;此外,也推荐了减少设备电耗的新技术,如采用高效风机以及永磁电机等,结合富余蒸汽拖动风机以及节能管控等技术,有望实现熟料烧成系统零电耗的目标。
1 工艺流程与数学模型
对于目前的新型干法水泥熟料生产工艺流程,从窑头至窑尾,除图1中的主要装备外,还包括生料磨、煤磨、高温风机、窑头与窑尾引风机、篦冷机风机等主要耗电设备。还给出了可能在水泥炉窑上使用的新技术,包括节能管控平台、富氧煅烧、分级燃烧、微细颗粒物与CO2减排等设备。
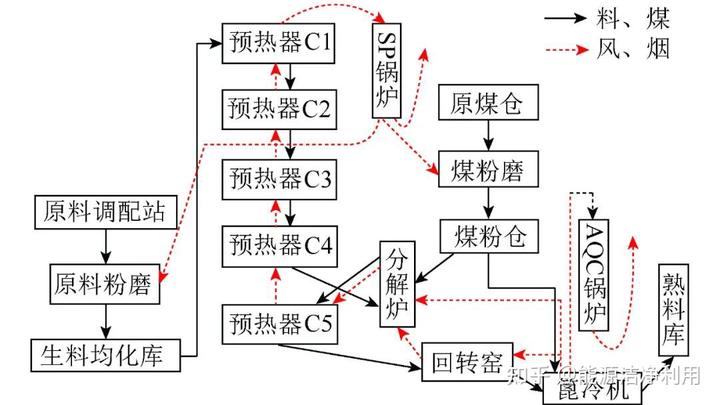
图1 新型干法水泥熟料生产线工艺流程
为了从数学上描述水泥熟料生产工艺流程的物质流与能量流,借鉴殷瑞钰院士提出的钢铁制造流程工序功能集合的解析思路,采用图2的流程网络来描述水泥炉窑,图中的节点代表具有不同功能的装置,连接线是指节点之间的连接方式。图2将水泥炉窑的7个主要装置简化为7个节点,节点间的关系表达了不同装置之间的联系。外围的框图将所研究的炉窑系统与外界分割开,进出炉窑系统的物质流及其伴随的能量流用实线描述。炉窑不同部位由于热能散失的能量流用虚线描述,计算时并入各附近的节点。
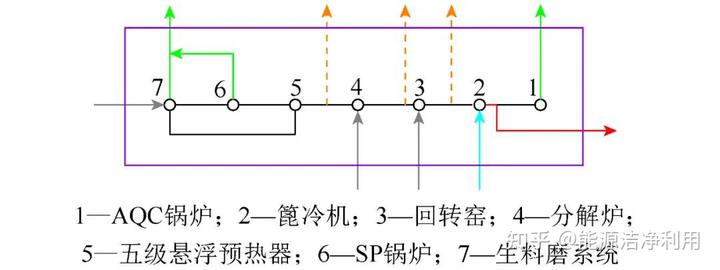
图2 水泥炉窑流程网络
2 结果与讨论
2.1 计算结果验证
对计算结果进行验证,测试数据来源于2017年国家建材工业水泥能效环保评价检验测试中心的现场测试报告,测试炉窑为金刚(集团)白山水泥有限公司3 200 t/d水泥熟料生产线。可以看出模型预测值较可靠。
2.2 炉窑系统的热量收支
首先计算了包含篦冷机、回转窑、分解炉、五级悬浮预热器等4个主要装置的水泥炉窑系统支出热量,该系统的4个节点对应图2的节点2~5,此方法与一般水泥炉窑的热平衡计算区域一致。在此基础上,计算的区域被扩大到包含AQC锅炉、篦冷机、回转窑、分解炉、五级悬浮预热器、SP锅炉、生料磨系统等7个主要装置的水泥炉窑系统支出热量(图2)。
图3为炉窑4个节点系统的收入热量与支出热量对比。炉窑系统的热量收入(黑色柱图)中,95.3%的热量来源于煤的燃烧热(Qf),其他为原燃材料与空气的显热(Q0)。有效热量支出(灰色柱图)中,熟料形成热(Qcl,f)最大,占总支出热量的53.38%(相当于1 742 kJ/kg);由于干燥后的生料与煤中残余水分占1%~2%,因此干燥后生料和煤粉进入炉窑,蒸发残余水分需热量(Qre,w)1.89%。预热器出口废气显热(Qpreh)和冷却机余风显热(Qc)分别占支出热量的18.86%和12.3%(白色柱图),其通过余热锅炉和生料、原煤的初始水分干燥过程,将得到进一步利用。其他支出热量(条纹柱图)包括:炉窑系统高温壁面散热(Qs,lo),占支出热量的6.84%(相当于220 kJ/kg);由于出冷却机的熟料温度较高(208 ℃,一般为110 ℃),因此出口熟料带走的显热(Qcl,out)占总支出热量的4.86%(相当于159 kJ/kg);煤粉的未燃尽碳热损失(Qub)占支出热量的1.95%(相当于63 kJ/kg)。
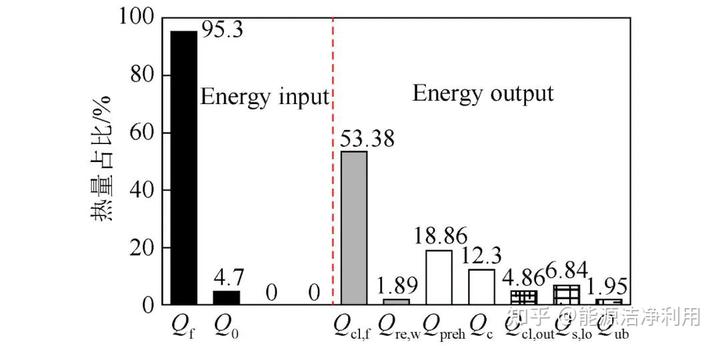
图3 炉窑4个节点系统的热量收入与支出对比
图4为炉窑7个节点系统的收入热量与支出热量对比。可见,热量收入与图3相同,而有效热量支出(5个灰色柱图)中,熟料形成热占53.5%(相当于1 742 kJ/kg),窑头与窑尾的烟气余热主要被AQC炉(QAQC,st)和SP炉(QSP,st)所吸收,产生蒸汽,该热量分别占总支出热量的9.27%和6.83%;SP炉出口的180 ℃烟气分别用于干燥生料和原煤的初始水分,该热量(Qdry)占支出的5.11%;蒸发残余水分需热量(Qre,w)1.89%。考虑余热利用和物料干燥后,热量利用的份额提升到76.6%,明显高于图3的结果。
热量损失(图4中6个白色柱图)中,高温炉壁(Qs,lo)所占的份额最大,占6.75%,具有可利用的潜力;煤粉的未燃尽碳热损失(Qub)占支出热量的1.95%;AQC炉(QAQC,lo)和SP炉(QSP,lo)的热量损失各占3.06%和6.19%,也仍有利用价值;出口熟料带走的显热(Qcl,out)占支出热量的4.87%,若降低熟料出口温度,还有进一步下降的可能性。
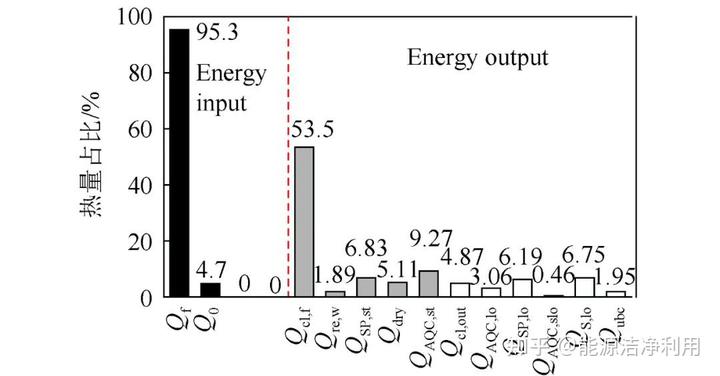
图4 炉窑7个节点系统的热量收入与支出对比
基于2017年国家建材工业水泥能效环保评价检验测试中心的现场测试报告的测试值对比,可以看出,基于节点的物质流与能量流计算模型预测值较可靠。
2.3 炉窑系统的㶲分析
为了从能量的品位角度分析热量的利用与损失情况,计算了炉窑7个节点系统的㶲支出对比(图5),其中熟料形成热引起的㶲支出最大,达71%。为了分析对比明显,图5仅给出除熟料形成热支出㶲外的其他㶲支出和㶲损失,可以看出,SP炉(ExSP,st)和AQC炉(ExAQC,st)的㶲支出分别占6.61% 和7.25%,是较大的㶲支出。另外,用于生料磨和煤磨的物料干燥(Exdry)和用于在预热器中物料残余水分干燥(Exre,w)的㶲支出分别占2.25%和1.84%。可见,这些用于熟料形成热以及余热锅炉吸热、物料干燥的有效㶲支出占88.95%,因此该炉窑的㶲效率相当高,这是因为随烟气温度降低,其㶲将被贬损。
图5还给出了炉窑7个节点系统的㶲损失,主要的损失来自于炉窑高温壁面散热(Exs,lo)和燃料的不完全燃烧(Exubc),分别占㶲损失的4.17%和2.59%;出冷却机熟料的剩余㶲(Excl,out)占1.32%;SP炉(ExSP,lo)的其他烟气(温度180 ℃)以及AQC炉(ExAQC,lo)出口烟气(温度110 ℃)还有一定的㶲损失,分别为1.45%和1.26%。从节能角度从发,这些损失都有可利用的价值,目前水泥炉窑节能需加以重视。
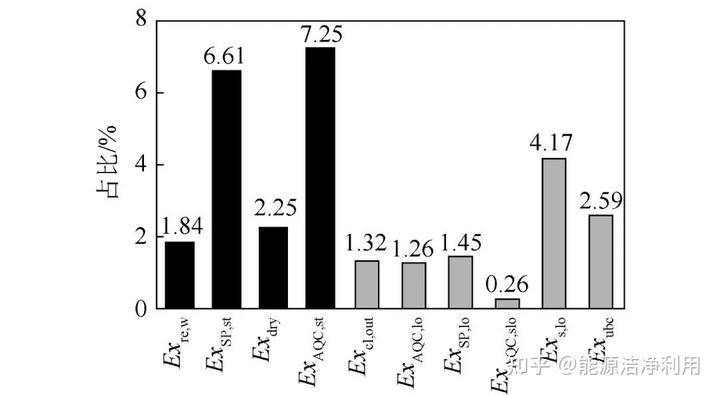
图5 炉窑7个节点系统的㶲收入与支出对比
2.4 炉窑的节能潜力评估与技术措施
从炉窑系统的㶲分析可见,高温炉壁散热引起的㶲损失最大,相当于浪费了220 kJ/kg的热量。另外,由于煤粉的未燃尽碳热损失为63 kJ/kg,这2项的热损失若换算为每吨熟料的标准煤热量,则相当于约9.7 kg/t。由于这2项㶲损失属于炉窑系统的高温损失,因此是炉窑系统节能的重点。在低温余热方面,由于出冷却机熟料的温度过高,其热量还可通过加大冷却机送风,增加利用约50%,即有79 kJ/kg的熟料显热;对于SP炉出口的180 ℃烟气,除用于物料干燥外,仍有51 kJ/kg的烟气余热可以利用;对于冷却机低温余风(208 ℃),也有69 kJ/kg的显热,这些低温余热(换算为每吨熟料的标准煤热量)相当于6.8 kg/t。若在实际工程中能够使得高温与低温余热得到有效利用,可减少煤耗5 kg/t以上。
从节能技术看,对于回转窑和三次风管等高温壁面的散热,可采用覆盖辐射换热器等措施回收热量,但更佳的方案是采用更先进的保温技术,减少散热。另外,对于炉窑高温段的密封也非常重要,可减少漏风引起的热损失。对于燃料的未燃尽碳热损失,可采用富氧燃烧等技术,提高低质煤的燃尽率和火焰着火温度,实现高效燃烧。
对于SP炉的烟气热损失,由于目前还有1/3左右的高温烟气热量未得到有效利用,因此需要在统筹物料干燥的基础上,尽量使高温烟气进入SP炉,产生更多的蒸汽。对于AQC炉出口的110 ℃烟气,可采用余风再循环方式,110 ℃烟气进入蓖冷机的二、三等低温段,提高冷却机的余风温度,可同时实现AQC炉出口烟气以及冷却机低温余风的热利用。
以上分析主要针对燃煤消耗的能量,未考虑电耗,一般研究的水泥炉窑电耗在60~65 kWh/t(换算为每吨熟料的电耗)。目前,也有一些新技术可减少电耗,针对3 200 t/d的熟料生产线,若采用生料磨采用高效辊压机可以减少5 kWh/t;采用高效风机以及永磁电机等技术可分别提高效率10%以上,相当于减少电耗10 kWh/t,结合富余蒸汽拖动风机以及节能管控技术采用新技术后,节电效果将更显著,加上余热电站的发电量(相当于35~38 kWh/t),可实现烧成系统零电耗的目标。
3 结 论
本文建立了一种基于节点法的工业炉窑物质流与能量流计算模型,可利用节能管控平台的监测数据,比较准确地预测炉窑的物质流与能量流状况,同时给出炉窑系统不同部位的㶲分析。通过研究包含AQC锅炉、篦冷机、回转窑、分解炉、五级悬浮预热器、SP锅炉、生料磨系统等主要装置的典型水泥炉窑系统能量流与㶲流分布,得到能量与㶲损失的主要部位,评估了节能的潜力。
1)高温炉壁散热引起的热量损失最大,达6.84%,其㶲损达4.17%;煤粉的未燃尽碳热损失相对较大,达1.95%,㶲损失达2.59%,这2项均属于高温能源浪费,具有较大的节约潜力。
2)窑头与窑尾的烟气余热主要被AQC炉(QAQC,st)和SP炉(QSP,st)吸收,该热量分别占总支出热量的9.27%和6.83%。但AQC和SP锅炉出口烟气温度分别为110 ℃和180 ℃,高于环境温度,还有一定的㶲损失。
3)采用更先进的保温技术,可减少高温炉壁散热损失;对于燃料的未燃尽碳热损失,可采用富氧燃烧等技术,实现高效燃烧;对于烟气低温热损失,可采用余风再循环,同时实现AQC炉出口烟气以及冷却机低温余风的热利用。
4)针对水泥厂节电措施,推荐采用高效辊压机、高效风机、永磁电机等技术,结合富余蒸汽拖动风机以及节能管控技术等,可取得显著的节电效果。
引用格式
魏小林,李慧鑫,李森,等.工业炉窑物质流和能量流匹配的节能原理分析[J].洁净煤技术,2020,26(5):11-19.
WEI Xiaolin,LI Huixin,LI Sen,et al.Principle analysis of energy saving of matched material and energy flows in the industrial furnace and kiln[J].Clean Coal Technology,2020,26(5):11-19.
请复制下方链接查看“洁净燃烧与工业炉窑节能减排技术”专刊全部论文
洁净燃烧与工业炉窑节能减排技术- 《洁净煤技术》联系我们:
电话:010-87986452/87986451
邮箱:jjmjs@263.net
网址:http://www.jjmjs.com.cn
微信客服:438351866
问:2023年锅炉价格/多少钱?

上一篇:脱硫脱硝厂家4吨生物质锅炉脱硝
下一篇:130t锅炉布袋除尘器技术方案