发展历程固定床加压气化炉最早为德国鲁奇(Lurgi)公司开发,鲁奇气化技术由此得名,鲁奇气化技术发展是以鲁奇气化炉的改进为核心,鲁奇炉
- 发展历程
固定床加压气化炉最早为德国鲁奇(Lurgi)公司开发,鲁奇气化技术由此得名,鲁奇气化技术发展是以鲁奇气化炉的改进为核心,鲁奇炉的发展主要经历了3个阶段。
第一阶段(1930-1954年),第一代气化炉直径2.6米,主要用于生产城市煤气,气化炉的结构特点是有内衬和边置灰斗,不设膨胀冷凝器,汽化剂通过炉篦的主动轴送入,该炉型只能气化非粘结性煤,且气化强度较低,产气量每台5000-8000Nm³/h。
第二阶段(1954-1969年),第二代鲁奇炉扩大了用煤范围,可气化弱粘结性烟煤,取消了内衬,改进了布气方式和增加了破粘装置,边置灰斗调为中置灰斗,气化炉直径扩大到2.8米、3.7米两种,单炉生产能力得到提高,单炉产气量分别达到14000-17000Nm³/h和32000-45000Nm³/h。
第三阶段(1969年-至今),为了进一步扩大用煤范围,使之达到气化一般粘结性煤的目的,推出了Mark-IV型气化炉,改进了布煤器和破粘装置,可气化除焦煤外的所有煤种,气化强度进一步得到提高,单台气化炉直径3.8米,产气35000-65000Nm³/h,此后,南非萨索尔(Sasol)在1980年开发了Mark-V型气化炉,气化炉内径4.7米,单台产气量达10万m³/h。在此基础上,又推出第四代鲁奇炉Mark+(已于2010年8月完成该炉的基础工艺及机械设计)。同时,为满足气体排放标准,解决废水达标排放难题,鲁奇公司相继开发出高效的煤气化尾气处理和酚氨废水处理工艺技术。
- 工艺流程
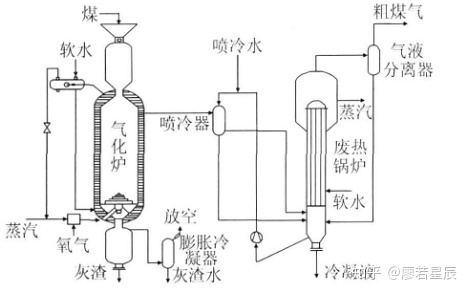
5-50 mm块煤经煤溜槽、煤锁进入气化炉。水、蒸气和氧气混合后从气化炉底部经炉篦进入气化炉,在3.0 MPa、1000 ℃的条件下,与煤发生气化反应。从气化炉出来的粗煤气,温度高达220-600 ℃,经喷冷器后温度降至200-210 ℃左右,进入废热锅炉回收余热,温度降至180 ℃左右,粗煤气经气液分离后进入下游工序。废热锅炉可产生0.5 MPa-0.6 MPa的低压蒸汽。从喷冷器洗涤下来的含焦油和尘的煤气水随煤气一起进入废热锅炉的底部的分离器,初步分离油水。一部分含尘煤气水由循环泵返回到洗涤冷却器,其余送煤气水分离单元。气化炉气化产生的灰渣周期性通过灰锁斗排出。
- 气化炉结构
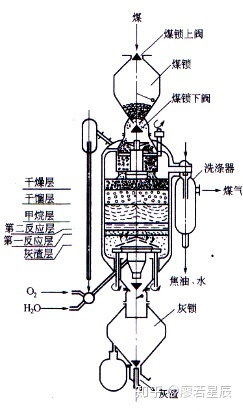
以Mark-IV型气化炉为例,其是夹套结构,主要部分有筒体、夹套、炉篦、煤锁和灰锁。现分述如下。
气化炉是双层夹套式圆形筒体,筒体外径为φ4000 mm,内径为φ3848 mm,高度12500 mm,内部容积为98 m³,夹套容积为13 m³,炉体总重量118.88吨(不包括内件炉篦重量40吨),操作重量243吨,操作压力为3.05 MPa(表压),操作温度范围1050~1100 ℃。
夹套在生产运行时充满高压锅炉给水并要保持足够高的液位,锅炉水吸热后产生高压饱和蒸汽,此蒸汽并入单台炉气化剂高压蒸汽管线,与氧气混合后返回气化炉内。夹套宽度为46 mm,总容积为13 m³,夹套内自产的高压饱和蒸汽,经过汽包顶部管线送出,在夹套上部空间设置有挡板,起汽液分离作用。
Mark-IV型气化炉采用塔形炉篦,分四层布气,气化剂由炉底进入炉篦中心管,然后由各层布气孔出去,通过炉篦各层间隙分布进入气化炉内,达到沿气化炉横断面均匀布气的效果。
炉篦的总高度为1200 mm,气化剂经各层炉篦通道进入炉内的气量分布大致为:I层~10 %,II层~20 %,III层~30 %,IV层~40 %。炉篦共有五层,为便于从气化炉顶部大法兰放入炉内进行安装,除一、二层是整体一块盖板外,其它层均是由几块组成:第三层4块,第四层4块,第五层6块盖板。各块之间采用螺栓连接。各层炉篦均固定在中心托板上,采用插入式咬合连接,中心托板上有挡块带动各层炉篦转动。炉篦整体由下部的止推盘支撑,止推盘下盘通过有水冷的支撑筋板固定在炉体内壳上。炉篦是通过两个对称布置传动的小齿轮带动的。炉外(两个)的小齿轮联结轴是由变速电机通过减速机传动而带动的,整个传动装置为6级传动,总速比为1:600,设计转速调整范围为1.0-12.0 r/h。
通常炉篦承受400-500 ℃的温度,在其顶部需保留约300-500毫米的灰层,以防止煤直接在炉篦上燃烧,烧坏炉篦,正常运行时,由于入炉的气化剂温度较低,气化剂对炉篦起到冷却保护,以防超温损坏。
在炉篦第五层下部设有排灰刮刀,可将大块灰渣挤压破碎,将灰渣并从炉内排至灰锁。
煤锁是用于向气化炉内部间歇加煤的压力容器,煤锁上、下部为圆锥型封头,中间为圆筒形,中间圆筒部分直径为Φ3000 mm,总高度为3800 mm,煤锁容积为12.10 M³,除去内件后煤锁有效容积为11.20 M³,设计压力为3.60 MPa,设计温度200 ℃,操作压力为3.0 MPa。
灰锁是用来将炉篦刮下的灰间歇排出炉外的压力容器,其上部是气化炉下灰室,下部与竖灰管相连,其外径为Φ2200 mm,总高约4000 mm,容积为12.2 m³,有效容积约为8.7 m³。其中间为圆柱形筒体,上部为凸形封头,下部为锥形封头,侧向有接管与膨胀冷凝器相通。其设计压力为3.6 MPa,设计温度为470 ℃,操作压力为3.0 MPa,材质选用15Mo3。由于灰锁内壁接触物料为灰渣,为延长其使用寿命,在灰锁内设置有耐磨护板。
- 煤种要求
气化用煤的指标有水分、灰分、挥发分、固定碳、灰熔点、焦渣特性等,其中煤的灰熔点和焦渣特性是鲁奇炉气化用煤的重要指标。
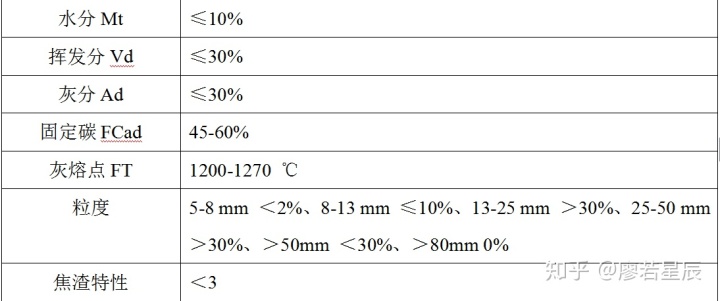
- 优势与劣势
优势
1.由于采用碎煤进料,相对气流床干粉或水煤浆进料,备煤系统简单,投资及运行费用大为降低,运行可靠性大幅提高。
2.气化剂与煤逆流接触,气化过程进行得比较完全,且热量利用合理,具有较高的热效率(最高可达94%),其冷煤气效率明显高于气流床。由于逆流运行,粗煤气及灰渣均以较低温度(典型值为400~700℃)离开气化炉,煤气与灰渣的热回收比干粉进料的废热锅炉流程简单可靠。
3.为防止结渣,气化采用高汽氧比,氧气消耗低于流化床及气流床,氧气单耗只为干粉气流床的50%~70%,显著降低空分设备投资。
4.粗煤气中甲烷含量高(10%或更高),特别适用于生产城市煤气和煤制天然气(SNG)。
5.粗煤气中H2/CO在2左右,当用褐煤为原料时,H2/CO可达2.7,高于气流床,对于F-T合成、甲醇合成、SNG的生产,可减轻煤气变换负荷。
6.技术成熟可靠,在无备用的情况下,单台气化炉年运转率超过93%,气化岛年运转率大于98%(在萨索尔塞康达工厂和大平原工厂得到验证)。设备本地化率高,投资省,对于相同的产品规模,气化岛加上配套空分的投资,约比水煤浆气化低20%。
劣势
1.出炉煤气中含焦油、酚等,污水处理和煤气净化工艺复杂、流程长、设备多,炉渣含碳5%左右。
2.水蒸汽消耗量大,但蒸汽分解率低,一般蒸汽分解率为40%,造成气化废水较多,后续煤气水分离负荷较重。
3.气化炉结复杂,炉内设有搅拌器和煤分布器、炉箅等转动设备,制造和维修费用大。
4.灰渣处理难度大:废渣为工业三废之一,煤燃烧后的炉渣,有细灰和渣块两种形态,无重复利用价值,处理难度大。随着环保处理难度大,随着国家环保的日益严格,废水、废渣的处理难度日益增加。
问:2023年锅炉价格/多少钱?

上一篇:无醇燃料真实可靠吗