循环流化床锅炉全貌
水吸收炉膛燃烧火焰的辐射热,使水冷壁中的水饱和,沸腾,蒸发,这个过程密度下降,汽和水混合物自然上升;
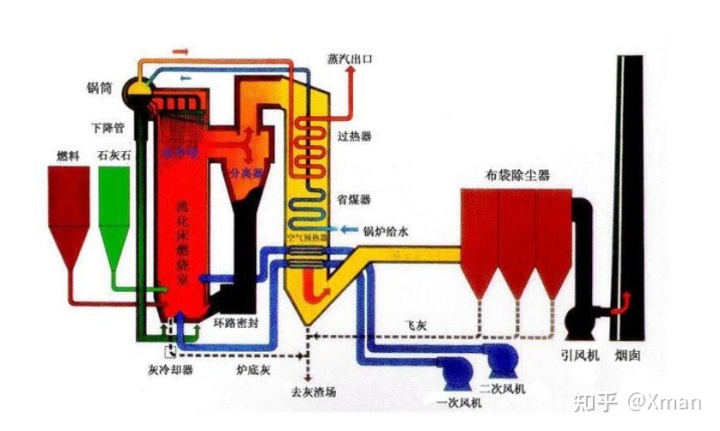
拆解过程-蒸汽产生

- 锅炉给水(高压)经过省煤器,对流管束热交换,未达到饱和状态的水,进入汽包;
- 锅炉汽包里的水经下降管,下联箱进入水冷壁(上升管);
- 水冷壁受到锅炉内燃烧过程的热辐射,沸腾产生的高温蒸汽(汽水混合物);
- 汽水混合物进入汽包后,汽水分离器(旋风分离器,波形板分离器,水的密度差进行重力分离)对蒸汽进行清洗,之后会进入高温过热器、再热器,进一步;
汽包
汽包和下联箱,将水加热成饱和水的加热过程;饱和水汽化成饱和蒸汽;饱和蒸汽加热成过热蒸汽;
作用:储能缓冲作用
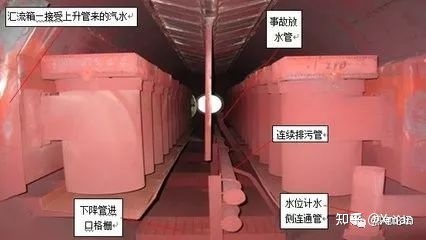
饱和蒸汽:当液体在密闭空间中蒸发时,液体分子通过液面进入上面成为蒸汽分子;由于蒸汽分子处于紊乱的热运动中,他们相互碰撞,并和容器壁以及页面发生碰撞,有的蒸汽分子被液体分子吸收,重新返回液体分子。
当单位时间内进入空间的分子数与返回液体中的分子数目相等时,则蒸发和凝结处于动态平衡状态,这时虽然蒸发和凝结仍在进行,但空间中蒸汽分子密度不再增大,此时状态称为饱和状态。
拆解过程-燃烧过程
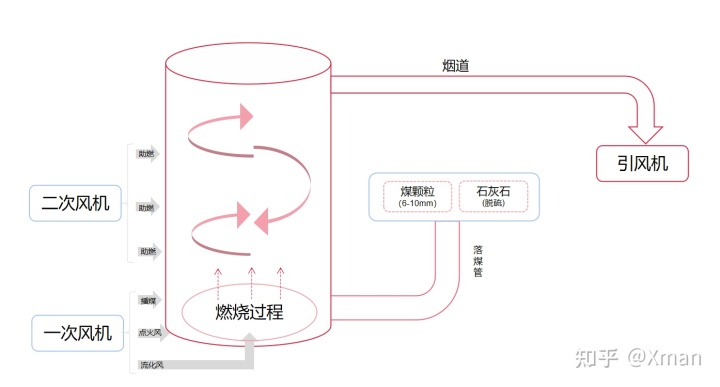
循环流化床得燃烧过程,即组织燃料按照一定方式进行燃烧,主要由燃烧器和炉膛两个部分构成:
- 石灰石 和 煤颗粒(6-10mm)通过助燃器送入炉膛,并组织一定气流结构(一次风和二次风);
- 煤颗粒和空气混合燃烧后,先以热辐射将大部分热量传送水冷壁l;
- 引风机,使炉膛内烟气上升进入烟道,气固分离器,烟气参与换热,除尘,排至烟筒;
强耦合
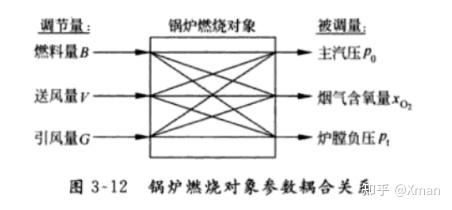
- 如果需要调节负荷,需要调节燃料,同时调整给风量,以使用风量和燃料量的比例;
- 如果需要调整烟气含氧量,需要调节送风量,同时需要调节燃料量;
- 如果需要调节炉膛负压,需要调节引风机,同时不能忽略送风量对其影响;
总风量
总风量 = 一次风量 + 二次风量
一次风
定义:一次风指的是从布风板下方送入炉膛、用来使料层充分流化、控制床温和保证初期流化燃烧所需的风。
一次风的作用
- 形成足够托举料层的气垫能力,保证料层炽热颗粒与新入炉燃料颗粒的快速传质,促进冷热颗粒混合,均匀床温,强化下部传热。
- 补充着火初期和燃烧过程前期的必要氧量,产生良好的初期稳定着火与还原区燃烧状态,保证粗颗粒层沸腾燃烧份额和燃尽率。
- 通过一次风的调节,实现对床温的良好控制,满足循环流化床锅炉料层温度在850~950℃范围内的燃烧要求。
- 在布风板均匀布风的作用下,实现料层的均匀流化,减少出现偏床、节涌、沟流等局部流化异常。
- 产生强烈的流态化燃烧过程,促进料层粗大颗粒的热态破裂,为密相区及其上方区域提供基本的细微颗粒群,形成粗颗粒向细颗粒的转移。
一次风的影响
一次风主要有两方面影响,床温和流化。
一次风量大小直接关系到流化质量的好坏。循环流化床锅炉在运行前都要进行冷态试验,并作出在不同料层厚度(料层差压)下的临界流化风量曲线,在运行时以此作为风量调整的下限,如果风量低于此值,料层就可能流化不好,时间稍长就会发生结焦。
当空气系数一定时,一次风偏大,床温会随之下降。
- 流化风的加强,会使密相区颗粒进入稀相区,密相区燃烧份额下降,耗氧量下降从而床温下降,而稀相区燃料浓度增加,耗氧量增加;
- 同时,飞灰含碳量升高,回料也会增多,和给煤一起是低温物质,同样会使床温下降;
当空气系数一定时,当一次风偏小,床温会分燃烧和流化有所不同,具体看比例:
- 燃烧,满足不了密相区的燃烧份额,床温下降(一次风小,燃烧放出的热,不满足冷物质吸收的热---------新进的煤和循环后返回床料的灰,就会引起床温下降);
- 流化,密相区向上燃料浓度的减少,床温增加(一次风小,流化时候吹响密相区的燃料浓度减少,会留在床料上发挥热量,使得床温升高);
经济性:一次风在保证床料充分流化的基础上,可适当降低,以减少热烟气带走的热量,保持较高的床温,提高燃烧效率。
一次风控制的难点:使用一次风控制床温,而一次风主要任务是建立稳定的循环流化状态,调节范围很窄,且要求稳定。但床温受煤质扰动(粒度,热值,挥发份)等因素的影响频繁变化,一次风频繁变化,会严重影响床料流化状态,威胁锅炉安全运行;
二次风
二次风主要指不参与床料层底部流化、用于稀相区和悬浮段物料颗粒燃烧的助燃风,富氧燃烧。二次风喷口一般沿炉膛高度方向上布置两层或三层。
二次风的设计要求要有足够的穿透能力,所以一般二次风布置是从炉膛短方向进入,形成射入炉膛燃烧室的强冲空气流,速度一般为50m/s以上。
二次风的作用
- 调节运行氧量,形成分级送风,在低温燃烧方式下进一步降低NO、SO,排放。
- 增加颗粒之间的相互运动、摩擦和撞击,便于剥离焦炭粒子表面灰壳,促进其与氧气的接触,确保悬浮段快速流化和气力输送区域燃料的燃烧效率,提高燃尽率。
- 高速二次风良好的穿透能力保证了炉膛横断面各处颗粒充分供应氧气,减少高浓度物料颗粒的贫氧区域。
- 二次风所产生的强烈扰动加速了颗粒的传质和载热过程,促进炉膛内部物料的温度平衡,强化了炉膛受热面的传热能力。
二次风的影响
稀相区的温度反映了稀相区燃烧的强度,其强度随着温度的升高而加强。但二次风量大时,其风压也高。所以二次风形成的射流其穿透性也越强,造成炉内扰动性也越强。稀相区细颗粒分布也均匀,与氧气混合的越好,燃烧的越充分,飞灰含碳量也随之减少。
当二次风过大,烟气流速增大,会导致飞灰含碳量升高,排烟热损失加大。同时,也造成受热面的磨损加剧;
二次风对锅炉经济性的影响
二次风的调整不仅对锅炉安全性有举足轻重的影响,而且对经济性的影响也非常明显。
本厂燃用的煤是品质较差的贫煤,平均煤质如下表所示:
发热量(KJ/Kg) 水分(%) 挥发分(%) 灰分(%)
21949 8.69 10.42 27.75
由于燃用煤种挥发份较低,所以在调整中应加大下部二次风份额,增加密相区空气量,增加煤在密相区的燃烧份额。在锅炉投运初期,满负荷运行时,二次风开度35%,在这种工况下,床温780℃左右,飞灰可燃物高达14%。经过摸索,加大二次风的开度,适当提高过量空气系数下,二次风开度在45%到55%之间视煤质情况进行调整。通过以上调整,稀相区的物料浓度降低,内循环物料量减少,密相区燃料燃烧放出的热量被返混物料吸收量减少,提高了密相区床层温度。床层温度的提高又提高了煤在密相区的燃烧份额,形成了良性循环。如此调整后,锅炉运行床温提高了15℃,飞灰可燃物降至9.5%,提高了锅炉运行的经济性。
一、二次风配比
由于循环流化床采用分段燃烧,在密相区为欠氧燃烧,会产生一氧化碳,一氧化碳在炉膛上部与二次风混合后,进一步燃烧放出热量,变为二氧化碳。这样就改变了密相区与稀相区的燃烧份额,使炉膛上部也保持较高的温度水平,更有利于炉膛上不得颗粒燃尽。
在某厂锅炉运行初期,由于排渣不畅,炉底大颗粒很多,流化不好,只能将一次风加大运行,为维持合理的过量空气系数,减少二次风的开度。由于二次风量较小,密相区燃烧份额减少,稀相区燃烧份额增大,n且上部物料浓度增大,不仅加剧了上部水冷壁磨损。同时,由于助燃的二次风量不足,使锅炉高温分离器内存在严重的后燃现象,即部分可燃物在高温分离器内燃烧,导致分离器出口烟气温度升高,出入口温差增大,n煤粒度变化时,旋风分离器出口温度达1000℃,温差甚至达到80℃左右。煤的后燃导致烟气温度上升,使得烟气对尾部对流受热面传热量增加,过热器出现超温,锅炉减温水量增大,严重影响了受热面的安全。nn 发现这些问题后,对锅炉作了如下调整nn (1)运行中在保证流化的前提下,尽量降低一次风,增大二次风。根据煤质及时做出调整,发现煤的粒度较细的时候,及时调整一、二次风的配比,增大二次风的比例,加大密相区燃烧份额,n降低上层物料浓度,减少磨损。在调整中,二次风最大可占总风量的45%。nn (2)试验表明,循环流化床锅炉存在核心贫氧区,这是造成后燃的重要原因。所以在调整中,注意调整二次风的风门开度,适当提高二次风风压,增加入炉二次风的刚度,以消除锅炉存在的中心贫氧区,n减少后燃的份额,减少尾部受热面吸热量,保证受热面的安全。
一、二次风配比总的原则
一次风率指从布风板低下加入的风量占总风量的比例;(二次风率同理)
一次风控制床温、流化;二次风调节氧量。一次风率对密相区的热量释放份额起决定性作用,在同样的燃料特性和流化速度条件下,一次风率越大,燃料在密相区热量释放份额越大。
在35%以下负荷一般保持点火时的固定一次风量不变,以保证超过或接近完全流化临界风量为准,此时,二次风原则上一般为 15%~30%。
负荷超过此值以后(35%-65%),开始根据流化程度、床温和氧量分别增加一次风量和二次风量。
当负荷已经增加到65%或更高时,锅炉受热面防磨;一次风量基本停止变化。在此之后再根据氧量和床温变化,不断增加二次风量,直至达到最大蒸发量下的对应风量。在床温适当的前提下,应尽量提高二次风率、降低一次风率,这有利于循环流化床锅炉高效分级燃烧,对NO、和 SO,减排也有利。
扩展内容:
https://www.zgypkj.com/support/glbk/884.html
https://patentimages.storage.googleapis.com/9f/cf/4a/a16584206006ab/CN101329582A.pdf
排烟氧含量
定义
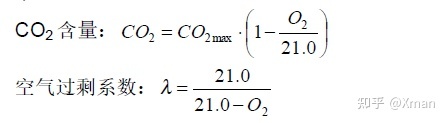
实际供给的空气量与理论空气量之比,称为过量空气系数。(http://news.eeworld.com.cn/MEMS/ic471492.html)
在各种炉子或燃烧室中,为使燃料尽可能燃烧完全,实际供入的空气量总要大于理论空气量(其超出部分称为“过剩空气量”),即过量空气系数必须大于1;
炉膛过量空气系数一般取1.3~1.4,即烟气氧含量控制在5%~6%。由于各方面的原因,在实际生产中将烟气中的氧含量控制在6%以下有较大的难度,一般燃用烟煤和无烟煤所要求的炉膛内过量空气系数为1.5左右,即把烟气氧含量控制在6%~8%作为链条锅炉经济运行指标。
寻找最佳燃烧效率点
摘自:全国金属学会2006年能源与热工学会年会论文集
因为供给加热炉,锅炉等设备的燃料燃烧热,并不是全部被利用了。以锅炉为例,有效热是为了使物料加热必须传入的热量,但这部分热量不好测量;
根据炉子热平衡可知:
N = 1 - (Q1+Q2+Q3+Q4)/Q
式中, Q———供给炉子的热量;
Q1 ———— 炉子烟气(废气)中过剩空气带走的物理热;
Q2 ————炉子烟气(废气)中燃料不完全燃烧而生成的或未燃烧的CO其带走的物理热;
Q3 ————炉子设备热损失(包括炉体散热,逸气损失,冷却水带走,热辐射等);
Q4 ————其他热损失;
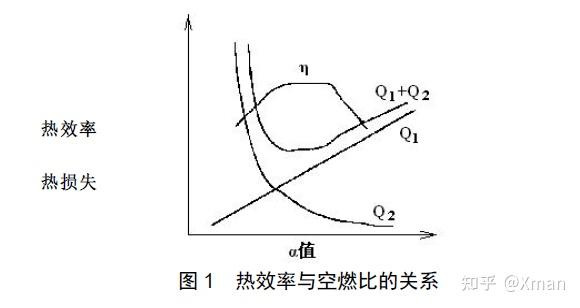
上图,显示了热效率和各项损失随着空燃比a的增加的变化规律。(空燃比,是混合气中空气与燃料之间的质量的比例。一般用每克燃料燃烧时所消耗的空气的克数来表示。)
当鼓风量过大时(即空燃比a偏大),虽然能使燃料充分燃烧,但烟气中过剩空气量偏大,表现为烟气中氧含量高,过剩空气带走的热损失Q1增大,导致热效率n 偏低。与此同时,过量扬起会与燃烧中的S,烟气中的氮反应生成有害物质。
当鼓风量偏低时(即空燃比a减小),表现为烟气中氧含量低,CO含量高,虽说排烟热损失小,但燃料没有完全燃烧,热损失Q2增大,热效率也将降低。另外,烟囱也会冒黑烟而污染环境。
所谓提高燃烧效率,就是要适量的燃料与适量的空气组成最佳比例进行燃烧。实验研究表明,图2为烟气中氧含量和CO含量与炉子能耗的关系。
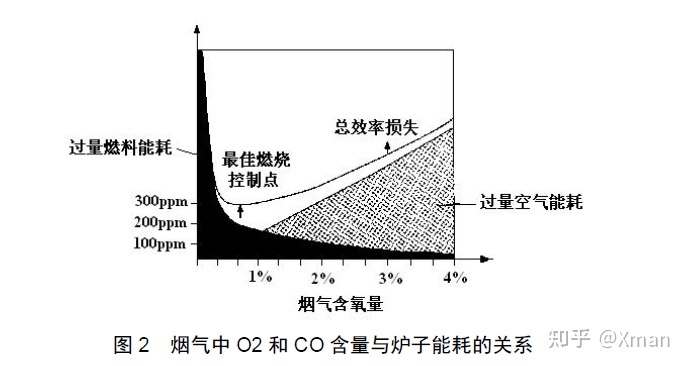
图2中,“过量空气能耗” 阴影面积表示富余的空气形成的能耗(或热损失),表征为烟气中氧气含量。“过量燃料能耗” 阴影面积表示有未完全燃烧的燃料所引起的能耗,表征为烟气中CO含量。
可以看出,若要降低这两部分能耗(同时亦可提高产品质量),必须降低烟气中氧含量和CO含量,但烟气中氧的含量和CO含量是相互制约的两个因素。若将上述两个阴影区叠加成另外一条曲线,即总效率损失曲线,其最小值即为最佳的燃料控制点,此处热损失最小,热效率最高,即烟气中氧含量约为1%。
由上文克制,热效率与烟气中的一氧化碳,氧气,二氧化碳含量以及排烟温度,供热负荷,雾化条件等因素有关。因此,可通过测量并控制烟道气体中一氧化碳,氧气,二氧化碳含量来调节空气消耗系数,来达到最高燃烧效率。
煤燃烧的滞后
- 煤进入炉内又一个受热,烘干,爆破,着火的过程,需要1-2min,这期间是吸热过程。弊端:当给煤增速太快时,可能出现先降温后升温的双向过程,给闭环控制带来不利。
- 给煤量改变,到锅炉主汽压力变化存在非常大的滞后,大概需要9-11分钟。弊端:经常容易导致过调现象,主汽压力大幅度摆动,而调节周期过长;
燃料粒度
我国循环流化床锅炉用煤为宽筛分物料,一般要求为0-8mm,燃料粒度的大小会引起送风量、燃烧份额和飞灰浓度的变化,从而影响汽温的变化。如燃煤的粒度大于8-10mm时,若维持在设计风量下运行有可能使粗颗粒沉积而引起事故(这是我国流化床锅炉不能长期稳定运行的主要原因之一)为使粗颗粒流化,必需加大送风量,结果造成颗粒扬析率增加,密相区内的燃烧份额降低,稀相区内的燃烧份额增加,同时增大送风量又使过热器区域的烟增加,使气温上升,严重时还可能使部分细颗粒煤在过热器区域燃烧,而造成汽温超限。
造成燃煤粒度不合要求的原因由以下几个方面,运行中应严格控制,保证锅炉的安全经济运行。
(1)制煤系统不合适,原煤未先经过筛分就进行破碎,造成细粉煤含量过多。
(2)筛子运行不正常,运行一段时间后特别当煤较湿时,筛孔发生部分堵塞,使煤的粒度越来越细。
(3)输煤系统上无吸铁装置或运行不正常,使铁钉、铁块等进入流化床中。
(4)破碎机运行不正常,破碎效果不佳,破碎后煤不过筛,都将造成大颗粒煤大量进入床中。
(5)筛子出现破损,使筛孔变大,造成粗颗粒煤大量进入床中。
床温
床层温度,指的密相区流动介质的平均温度。为保证良好的燃烧和传热,床温一般控制在850~950℃之间稳定运行。
- 在该温度下灰不会融化,从而减少了结渣的危险性;
- 该温度下具有较高的脱硫效率;
- 在该温度下燃烧气体的氮化物气体较少;
- 在该温度下煤中的碱金属不会升华,可以降低受热面的结渣;
影响床温的因素
主要有负荷、投煤量、返料量、风量及一二次风配比等,具体有以下几方面:
- 运行中煤种的变化时,发热量的改变会改变床内热平衡,从而影响燃烧、传热和负荷,也会影响排放量,易造成床温波动,发热量越高,床温就越高。
- 给煤量不均,时多时少,会使床温忽高忽低,尤其有时操作不慎或短时间断煤会使床温急剧下降。
- 负荷改变后,风煤配比未及时调整,如负荷增大、煤量、风量未相应增加,床温就会下降,反之,床温就会上升。
- 运行中给煤粒度控制不严或煤质太差,排渣不及时,会使流化层底部流化质量恶化,同时料层阻力增加使风量减少,风煤比失调,造成床温逐渐下降。
- 风煤比调整不当,给煤过多,风量过小时,煤在炉内不能良好燃烧,使床温降低。如果运行人员误认为煤量不够,继续增加煤量,会使风煤比严重失调,床温急剧下降。如果风量过大,则会使烟气带走粒子热量增加,也会使床温下降。
料层差压
料层差压是表征流化床料层高度的物理量,一定的料层高度对应一定的料层差压。因为在流化状态下,流化床的料层差压,同单位面积上布风板上流化物料的重力与流化床浮力之差大约相等,对于正在运行的流化床锅炉,根据燃用煤种和料层差压来估算料层厚度是十分有用的。
料层差压的影响
料层差压对流化床锅炉的稳定运行有很大影响,料层过薄,料层容易吹穿而产生沟流,流化不均而引起局部结渣,难以形成稳定的密相区,同时还会造成放渣含砒量高,燃烧不完全,增加了灰渣热损失
料层过厚会增加风机压头,气泡增大,扬析夹带量增大,流化质量下降,底部大颗粒物料沉积,危及安全运行,风机电耗増加,锅炉效率下降。因此,料层厚度应维持在适当的范围,一般认为500mm左右为好。
料层差压的控制
正常运行中,风门开度是不变的,如料层差压增加,说明料层增厚,可以采取排放冷渣来减薄料层,注意一次排放量不要太大,以免影响流化,排放后应将冷渣门关严以免漏入冷风引起冷渣管结渣,如有条件最好采取连续排渣。不同厂家料层差压的测量方式不同,一般采用风室静压,作为参照,风室静压等于布风机阻力加料层阻力。在冷态试验中测定不同风量下的布风板阻力,运行中可以通过风室静压,估算料层差压和料层厚度。
对于13mm的物料,为保证最低流化风量,风室静压要控制在8KPa以上,这时对应的料层差压为正常运行料层控制的最小值。循环流化床锅炉用一次风机、风压相对煤粉炉风机风压较高,运行中有风道撕裂现象,风机压头和风道的强度、风室的设计静压值也就决定了风室静压控制的最大值,正常运行中一般都要留有余量。以上最谈到的是料层差压控制的最小值和最大值,提供了控制的最大上下限,运行稳定后,应寻找控制的最佳值。料层差压随时间的变化曲线,斜率最小时对应的料层差压数值为最佳值。现在一般采用 DCS 控制,微机可以做出料层差压曲线,曲线斜率最小时,对应料层差压为最小。如果没有 DCS 微机控制,也可凭经验。
放渣后,床温升高,说明料层控制过厚;放渣后,床温下降,说明料层控制过薄。
炉膛差压
炉膛差压是表征流化床上部悬浮物料浓度的量,炉膛上部空间一定的物料浓度,对应一定的炉膛差压,对于同一煤种炉膛上部物料浓度增加,炉膛差压值越大,炉膛差压与锅炉循环灰量成正比。
炉膛差压的控制
流化床内物料粒子浓度是决定炉膛上部蒸发受热面传热强度的主要因素之一,试验表明,床、管之间放热系数随粒子浓度成直线关变化。因此,锅炉炉膛差压越高,锅炉循环灰量越大,将有更多的循环灰被带到炉膛上部悬浮段参加二次燃烧,锅炉出力也就越大。对于同一煤种,物料浓度增加,炉膛差压值增大,对炉膛上部蒸发受热传热强度越大,锅炉出力越强,反之锅炉出力越弱。循环流化床锅炉密相区中,燃料燃烧在密相区的燃烧热,有一部分由循环系统的返回料来吸收,带到炉膛上部放热,才能保持床温的稳定,如果循环量偏小,就会导致密相区放热过大,流化床温度过高,无法增加给煤量,带不上负荷,因此,足够的循坏灰量是控制床温的有效手段。
控制炉膛差压主要靠调整循环灰量来实现,当循环灰量少,炉膛差压小,床温偏高,不能满足负荷的需要时应适当增加二次风量及给煤量,这样炉膛上部颗粒浓度增加,燃烧份额也得到增加,水冷壁的吸热量增加,旋风分离器入口物料浓度增加,物料循环量增加,负荷增加。有时因燃料含灰量高,循坏量逐渐增大,床温过低燃烧无法维持,这时应放掉一部分循环灰,来降低炉膛差压。
氮氧化物
氮氧化物是造成大气污染的主要污染源之一。通常所说的氮氧化物NOx有多种不同形式:N2O、NO、NO2、N2O3、N2O4和 N2O5,其中NO和NO2是主要的大气污染物。我国氮氧化物的排放量中70%来自于煤炭的直接燃烧。
研究表明,氮氧化物的生成途径[2]有三种:
(1)热力型NOx,指空气中的氮气在高温下氧化而生成NOx;
(2)快速型NOx,指燃烧时空气中的氮和燃料中的碳氢离子团如CH等反应生成NOx;
(3)燃料型NOx,指燃料中含氮化合物在燃烧过程中进行热分解,继而进一步氧化而生成NOx;
在这三种形式中,快速型NOx所占比例不到5%;在温度低于1300℃时,几乎没有热力型NOx。对常规燃煤锅炉而言,NOx主要通过燃料型生成途径而产生。
氮氧化物的控制
低NOx燃烧技术主要有:分级燃烧、燃料再燃、低过剩空气燃烧和烟气再循环等几种方式。
空气分级燃烧
空气分级燃烧的基本原理为:将燃烧所需的空气量分成两级送入,使第一级燃烧区内过量空气系数在0.8左右,燃料先在缺氧的富燃料条件下燃烧,使得燃烧速度和温度降低,因而抑制了热力型NOx的生成。同时,燃烧生成的CO与NO进行还原反应,以及燃料N分解成中间产物(如NH、CN、HCN和NH3等)相互作用或与NO还原分解,抑制了燃料型NOx的生成。
在二级燃烧区内,将燃烧用的空气的剩余部分以二次空气输入,成为富氧燃烧区。此时空气量虽多,一些中间产物被氧化生成NO,但因火焰温度低,生成量不大,因而总的NOx生成量是降低的,最终空气分级燃烧可使NOx生成量降低30%~40%。当采用空气分级燃烧后,火焰温度峰值明显比不采用空气分级燃烧时降低,故热力型NOx降低。
燃料分级燃烧
在主燃烧器形成的初始燃烧区的上方喷入二次燃料,形成富燃料燃烧的再燃区,NOx进入本区将被还原成N2。为了保证再燃区不完全燃烧产物的燃尽,在再燃区的上面还需布置燃尽风喷口。改变再燃烧区的燃料与空气之比是控制NOx排放量的关键因素。存在问题是为了减少不完全燃烧损失,需加空气对再燃区烟气进行三级燃烧,配风系统比较复杂。
烟气再循环
除了空气和燃料分级降低NOx的排放量之外,目前使用较多的还有烟气再循环法。它是在锅炉的空气预热器前抽取一部分低温烟气直接送入炉内,或者是与一次风或二次风混合后送入炉内,这样不但可以降低燃烧温度,而且也降低了氧气浓度,因而可以降低NOx的排放浓度。
烟气再循环技术,其核心在于利用烟气所具有的低氧以及温度较低的特点,将部分烟气再循环喷人炉膛合适的位置,降低局部温度及形成局部还原性气氛,从而抑制NOx的生成。烟气再循环技术在很多情况下是被用来防止锅炉运行中的结焦问题。对于燃烧无烟煤等难燃煤种以及煤质不是很稳定的电站锅炉,则不宜采用烟气再循环技术。其原理为从空气预热器前抽取温度较低的烟气,通过再循环风机将抽取的烟气送入空气烟气混合器,和空气混合后一起送去炉内。
问:2023年锅炉价格/多少钱?
